Introduce about 3d milling guide,Qulity,Cost,Supplier,Certification,Market,Tips,FAQ
3D milling is a comprehensive guide that assists users in understanding the process of milling three-dimensional objects. This guide covers various aspects such as quality, cost, suppliers, certifications, market trends, tips, frequently asked questions (FAQ) and more.
When it comes to quality, 3D milling ensures precision and accuracy, resulting in a high-quality finished product. This technology allows for intricate details and complex shapes to be milled with great precision, providing excellent surface finishes that meet or exceed industry standards.
In terms of cost, 3D milling can be a cost-effective solution. By utilizing computer-controlled machines, the process reduces human error and increases efficiency, saving time and money in production. Additionally, the use of 3D milling can eliminate the need for multiple setups, further reducing costs.
Choosing the right supplier is crucial to ensure the success of your 3D milling projects. It is advisable to partner with suppliers who have a solid reputation, extensive experience, and a track record of delivering high-quality milled products. Additionally, consider suppliers who offer excellent customer service, prompt delivery, and competitive pricing.
Certification is vital when selecting a supplier for 3D milling. Look for suppliers who hold relevant certifications, such as ISO 9001, which indicates their commitment to quality management systems. Certification ensures that the supplier adheres to strict standards, resulting in reliable and consistent quality.
The market for 3D milling is rapidly growing, with increasing demand across various industries such as aerospace, automotive, medical devices, and consumer goods. With advancements in technology, more companies are adopting 3D milling to improve efficiency, meet complex design requirements, and reduce lead times.
To maximize the benefits of 3D milling, here are a few tips to consider: optimize toolpaths for efficient milling, select appropriate materials for the desired application, use proper fixturing techniques for stability, and regularly maintain and calibrate milling machines for optimal performance.
Frequently Asked Questions (FAQ) typically revolve around topics such as the compatibility of different file formats, material selection, tolerance requirements, turnaround times, and pricing structures. Providing answers to these common concerns in the guide can help users understand and navigate the 3D milling process more effectively.
In conclusion, 3D milling is a comprehensive guide that covers various aspects of milling three-dimensional objects. This guide provides insights into quality, cost, suppliers, certifications, market trends, tips, and addresses frequently asked questions. Whether you are a beginner or an experienced professional, this guide serves as a valuable resource to enhance your understanding and proficiency in 3D milling.
Types of 3d milling
3D milling, also known as CNC (Computer Numerical Control) milling, is a subtractive manufacturing process that uses automated machines to remove material from a workpiece to create three-dimensional objects. There are several types of 3D milling techniques that vary in complexity and application. Let’s explore three commonly used types:
1. Ball End Milling: This type of milling utilizes a ball-nose cutter with a curved end to create contoured surfaces or features with rounded edges. Ball end milling is versatile and suitable for creating complex shapes, such as molds, dies, or artistic sculptural pieces. It is commonly used in industries like automotive, aerospace, and woodworking.
2. Face Milling: Face milling is suitable for creating large, flat surfaces on a workpiece. The cutting tool used in this technique has multiple cutting edges on its circumference and can remove material quickly and efficiently. Face milling is commonly used in the production of flat parts, machine components, and housing applications.
3. High-Speed Machining (HSM): High-speed machining involves using specialized tools and techniques to achieve high feed rates and cutting speeds. This technique is typically applied to reduce machining time and increase productivity. HSM is often used in industries like aerospace, automotive, and medical, where precision and speed are crucial.
In addition to these specific types, other variations of 3D milling include pocket milling, contouring, drilling, and roughing, each serving different purposes to achieve the desired final form of the workpiece. The choice of milling technique depends on factors such as the material being machined, the complexity of the design, and the desired surface finish.
3D milling has revolutionized manufacturing processes by enabling the production of highly intricate and precise parts. The use of computerized controls ensures minimal human error and allows for repeatability. This technology finds wide applications in various industries, including automotive, aerospace, electronics, and medical, where complex geometries and high precision are paramount.
In conclusion, the different types of 3D milling techniques serve diverse purposes in fabricating three-dimensional objects. From ball end milling for intricate contours to face milling for flat surfaces and high-speed machining for increased productivity, each method offers unique advantages for different applications. The extensive capabilities of 3D milling have ushered in a new era of precision manufacturing.
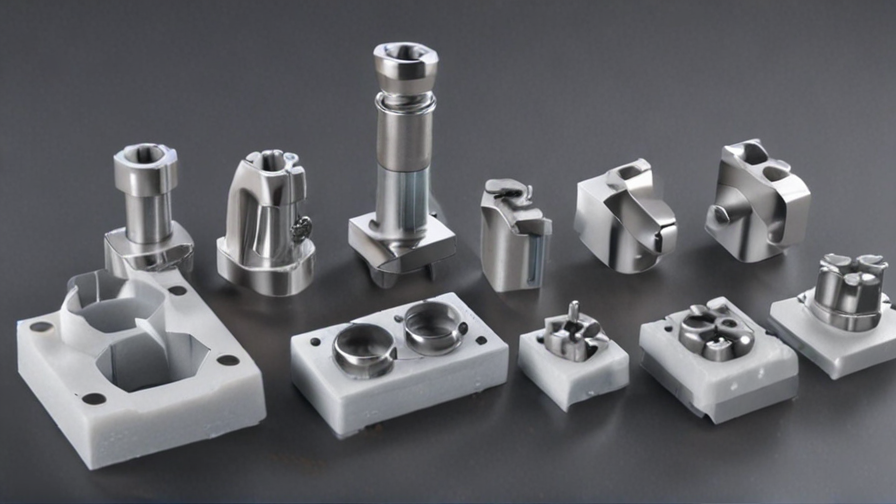
Pros and Cons of Using 3d milling
3D milling, also known as CNC milling, is the process of using computer-guided machinery to shape and cut materials into three-dimensional objects. It offers several advantages and disadvantages, as outlined below.
Pros:
1. Precision: 3D milling allows for high precision and accuracy, thanks to the computer-controlled machinery. This ensures that the final product is made exactly as specified, with highly intricate and detailed designs possible.
2. Versatility: With 3D milling, a wide variety of materials can be used, including metals, plastics, and wood. This makes it suitable for various industries, such as aerospace, automotive, and jewelry manufacturing.
3. Customization: The computer-aided design (CAD) technology used in 3D milling allows for easy customization of the object being created. It enables the production of unique, one-of-a-kind pieces tailored to specific requirements and preferences.
4. Efficiency: 3D milling is a relatively quick process, especially for small to medium-sized objects. It eliminates the need for manual cutting and shaping, which saves time and increases productivity.
5. Replication: Once a design is programmed into the milling machine, it can be replicated multiple times with consistent quality. This is particularly beneficial for mass production, reducing human error and ensuring uniformity across products.
Cons:
1. Cost: Setting up a 3D milling operation can be expensive, particularly for small businesses or individuals. The machinery, software, and training required to operate it can be a significant investment.
2. Complexity: Operating a 3D milling machine requires specialized skills and knowledge. The programming and maintenance of the machinery can be complex, making it challenging for those without expertise to use effectively.
3. Limited size: Conventional 3D milling machines typically have size limitations, which can restrict the size of objects that can be produced. Large-scale or oversized items may require alternative manufacturing processes.
4. Material limitations: While 3D milling supports a wide range of materials, some intricate or delicate materials, such as ceramics or glass, may not be suitable for this process. The machinery’s cutting tools may not be able to handle these materials without the risk of breakage.
5. Waste material: One potential drawback of 3D milling is the generation of waste material or scraps during the cutting and shaping process. Proper waste management becomes necessary to minimize environmental impact and reduce costs.
In conclusion, 3D milling offers numerous benefits, including precision, versatility, customization, efficiency, and replication. However, the disadvantages, such as cost, complexity, size limitations, material constraints, and waste generation, should be considered when deciding whether to utilize this manufacturing process.
3d milling Reference Specifications (varies for different product)
3D milling, also known as CNC milling, is a manufacturing process that uses computer numerical control (CNC) machines to remove material from a workpiece to create a three-dimensional object. The process involves using a rotating cutting tool to remove material from a solid block or workpiece in a series of precise movements. The reference specifications for 3D milling vary depending on the specific product being manufactured.
One important reference specification for 3D milling is the dimensional accuracy. This refers to the tolerance or the allowable variation in the dimensions of the final product. The dimensional accuracy depends on factors such as the machine precision, tool quality, and the complexity of the design. It is crucial to ensure that the final product meets the required dimensional accuracy to ensure proper fit and functionality.
Another reference specification for 3D milling is the surface finish. This refers to the quality of the surface of the milled object. The surface finish can be influenced by various factors, including the machine speed, tool sharpness, and the cutting strategy used. It is essential to achieve the desired surface finish to meet aesthetic requirements, functional requirements, or to ensure compatibility with other components.
Moreover, the material selection is a critical reference specification for 3D milling. Different materials may have varying cutting properties and may require specific tooling strategies and feeds and speeds. The material properties, such as hardness and brittleness, need to be considered to ensure optimal milling conditions and prevent tool wear or workpiece damage.
Additionally, the complexity of the design is another reference specification. Intricate and complex designs may require advanced milling techniques, such as multi-axis milling or simultaneous milling, to achieve the desired shape and accuracy. The complexity of the design also affects the machining time and cost.
Finally, the volume and batch size are crucial factors in determining the reference specifications for 3D milling. Mass production may require optimizing the cutting strategy, tooling, and machine setup to ensure efficient production rates and consistent quality across a large batch of products.
In conclusion, 3D milling reference specifications vary depending on the specific product being manufactured. These specifications include dimensional accuracy, surface finish, material selection, complexity of the design, and volume or batch size. Adhering to these specifications is vital to ensure the production of high-quality, precise, and functional 3D milled objects.
Applications of 3d milling
3D milling, also known as CNC milling, is a versatile manufacturing process that involves the removal of material from a workpiece using rotary cutters. This precise technique allows for the creation of complex and intricate shapes, making it suitable for a wide range of applications across various industries.
One of the primary applications of 3D milling is in the field of prototyping. It enables the creation of prototypes quickly and accurately, facilitating product development and testing. By milling a 3D model from a digital design, engineers and designers can physically visualize and evaluate the product before mass production, allowing for adjustments and improvements.
Another significant application of 3D milling is in the production of custom parts and components. This process is commonly employed in the aerospace and automotive industries, where intricate and precise parts are required. 3D milling ensures that the end products meet stringent quality standards, as it allows for high levels of precision and accuracy. This application extends to various other sectors, including medical devices, electronics, and consumer goods.
Artistic and architectural industries also make use of 3D milling for creating intricate sculptures, decorative elements, and architectural models. Whether it is replicating historical artifacts or constructing complex geometries in modern designs, 3D milling provides the necessary precision and control to bring these creations to life.
Additionally, 3D milling is utilized in mold making processes. The ability to mill complex geometries with tight tolerances makes it an ideal technique for generating molds for casting and forming operations. 3D milling allows for the production of highly detailed and accurate molds, resulting in high-quality finished products.
Furthermore, 3D milling plays a vital role in the production of medical and dental devices. It enables the precise fabrication of prosthetics, implant components, dental crowns, and orthopedic devices. The ability to customize these devices according to individual patient requirements greatly enhances the quality of care and patient comfort.
In conclusion, the applications of 3D milling are extensive and valuable across various industries. From prototyping and custom part production to art and architecture, mold making, and medical devices, 3D milling enables the creation of intricate and precise components, improving manufacturing processes and product quality.
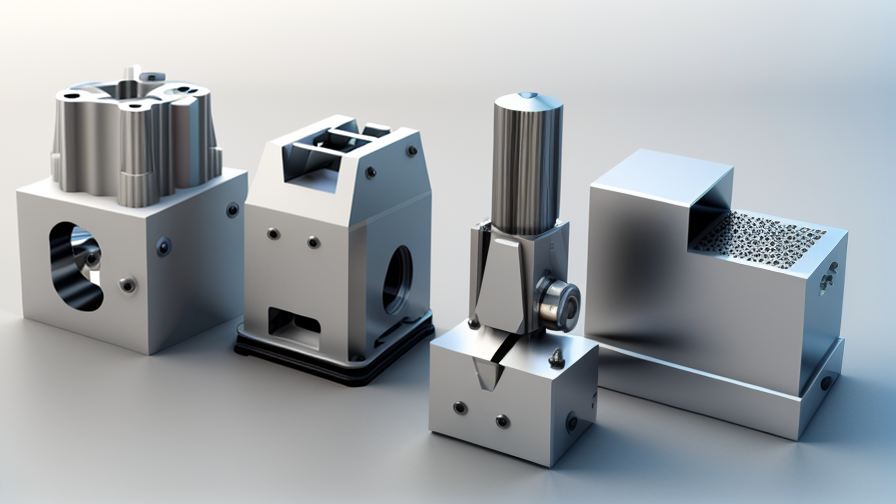
The Work Process and how to use 3d milling
3D milling is a machining process that involves cutting and shaping materials using a computer-controlled machine tool. It is widely used in various industries, including automotive, aerospace, and jewelry manufacturing. The work process of 3D milling typically involves the following steps:
1. Design: The first step is to create a 3D model or design of the desired object using computer-aided design (CAD) software. This design specifies the shape, dimensions, and features of the final product.
2. CAM Programming: After the design is complete, the next step is to generate toolpaths using computer-aided manufacturing (CAM) software. This involves determining the most efficient cutting strategy and tool movements that will achieve the desired shape and finish.
3. Material Preparation: Once the CAM programming is done, the material to be milled needs to be prepared. This usually involves selecting the appropriate raw material, such as metal or plastic, and securing it firmly on the milling machine’s worktable.
4. Machine Setup: The milling machine must be properly set up and calibrated before starting the milling process. This includes installing the required cutting tools, ensuring proper alignment, and configuring machine parameters based on the material and design specifications.
5. Milling Operation: With the setup complete, the milling machine is ready to start cutting the material. The machine moves the cutting tool along various axes (X, Y, Z) based on the programmed toolpaths, removing excess material and creating the desired shape.
6. Finishing: After the initial milling operation, the object may require additional operations for surface finish and detail. This can include techniques like sanding, polishing, or using additional cutting tools for finer details.
7. Inspection and Quality Control: Once the milling process is complete, the finished object is inspected for accuracy, dimensional precision, and surface quality. This ensures that it meets the required specifications and tolerances.
3D milling offers several advantages over traditional machining methods, such as increased accuracy, reduced material wastage, and improved productivity. It allows for the production of complex shapes and intricate designs with high precision and repeatability.
In conclusion, the work process of 3D milling involves designing a 3D model, programming toolpaths through CAM software, preparing the material, setting up the milling machine, performing the milling operation, finishing as needed, and inspecting the final product. By following these steps, manufacturers can harness the capabilities of 3D milling to produce high-quality, custom-made parts and products efficiently.
Quality Testing Methods for 3d milling and how to control the quality
Quality testing methods for 3D milling involve a systematic approach to ensure that the final product meets the required quality standards. Here are some common quality testing methods and techniques for 3D milling:
1. Dimensional Accuracy: This involves measuring the dimensions of the milled object using precise tools such as calipers or coordinate measuring machines (CMMs). The measured dimensions are compared against the specified tolerances to detect any deviations.
2. Surface Finish Analysis: Surface roughness testers are used to assess the quality of the milled surface. By measuring parameters such as Ra (average roughness) or Rz (mean roughness depth), the surface finish can be evaluated against the desired specifications.
3. Geometric Integrity: This testing method verifies if the milled object matches the intended design. It involves using 3D scanning techniques or CMMs to digitally compare the milled product with the CAD model. Deviations can be identified and analyzed for corrective actions.
4. Material Properties: If specific material properties are critical to the success of the milled part, various material testing methods can be employed. These may include tensile testing, hardness testing, impact testing, or metallographic analysis, depending on the requirements.
5. Functional Testing: This method involves testing the milled part’s functional performance. For example, if the part is a mechanical component, it can be put through simulated mechanical loads or tests to ensure it meets the functional requirements.
To control the quality of 3D milling, several practices can be implemented:
1. Calibration: Regular calibration of milling machines, sensors, and measuring tools is essential to maintain accuracy and repeatability.
2. Operator Training: Well-trained operators can significantly impact the quality of the milled parts. Providing training on machine operation and quality control procedures enhances their understanding and competency.
3. Process Monitoring: Monitoring the milling process in real-time can help identify deviations and prevent potential quality issues. Variables such as cutting forces, tool wear, and feed rates can be monitored and controlled to optimize quality.
4. Standard Operating Procedures (SOPs): Defining and adhering to standardized procedures ensures consistency and quality across different milling operations. SOPs should cover aspects such as tooling selection, machine settings, and inspection protocols.
5. Continuous Improvement: Implementing a continuous improvement approach encourages the identification of areas for enhancement through feedback, data analysis, and learning from defects or non-conformance.
By employing these quality testing methods and following effective quality control measures, manufacturers can ensure the production of high-quality milled parts with minimal deviations from the required specifications.
3d milling Sample Policy and Post-Purchase Considerations for 3d milling from China
Sample Policy:
When purchasing 3D milling from China, it is important to consider the following sample policy:
1. Quality Assurance: Prioritize suppliers who provide high-quality products. Request samples before making a bulk order to ensure the milling meets your standards and requirements.
2. Manufacturing Time: Discuss and agree upon a suitable manufacturing time with the supplier. Ensure they have the capacity to deliver within your desired timeline.
3. Customization: If you require specific customization or design alterations, clearly communicate your needs to the supplier. Confirm their ability to accommodate such requests before finalizing the purchase.
4. Packaging and Shipping: Confirm the packaging methods and materials used to protect the milling during transit. Discuss shipping options to optimize cost and delivery time.
5. Payment Terms: Clarify payment terms, such as the accepted methods (e.g., bank transfer, PayPal), down payment requirements, and balance payment terms, ensuring they are mutually acceptable.
Post-Purchase Considerations:
After the purchase, consider the following actions to ensure a successful 3D milling purchase from China:
1. Inspection: Thoroughly inspect the received products upon arrival. Check for any damages or deviations from the agreed specifications. Promptly raise any concerns with the supplier to resolve issues.
2. Quality Testing: Conduct quality testing on a sample of the received milling to ensure it meets the expected standards. If any faults are identified, communicate them to the supplier for resolution or replacement.
3. Feedback and Review: Share your experience and provide feedback to the supplier. This contributes to their continuous improvement and helps potential buyers make informed decisions.
4. Long-term Relationship: If satisfied with the purchase, maintaining a long-term relationship with the supplier can be beneficial. Continuity simplifies future orders and enables better customization options based on familiarity with your requirements.
5. Recommended Supplier: Should you have a positive experience, consider recommending the supplier to others, strengthening the supplier’s reputation and fostering trust in their products and services.
By following these sample policies and post-purchase considerations, you can enhance the likelihood of a successful 3D milling purchase from China.
Sourcing 3d milling from China: Opportunities, Risks, and Key Players
Sourcing 3D milling services from China can present several opportunities, risks, and key players in the market. China has emerged as a global manufacturing hub offering competitive pricing, advanced technology, and a wide range of industrial capabilities. However, there are also risks associated with sourcing from China, such as quality control issues, intellectual property concerns, and geopolitical uncertainties.
Opportunities:
1. Competitive Pricing: Chinese manufacturers often offer lower production costs compared to other countries, allowing businesses to reduce their expenses and increase profitability.
2. Advanced Technology: China has made significant investments in advanced manufacturing technologies, including 3D milling. Chinese companies often possess the capabilities to provide high-quality, precision engineering.
3. Wide Industrial Capabilities: China has diversified industrial capabilities, enabling businesses to find suitable 3D milling services for various sectors, including automotive, aerospace, electronics, and medical devices.
Risks:
1. Quality Control: Ensuring consistent quality can pose a challenge when sourcing from China. It is crucial to thoroughly vet potential suppliers, conduct regular quality inspections, and establish clear quality control standards to mitigate this risk.
2. Intellectual Property Protection: Protecting intellectual property remains a concern when sourcing from China. Companies should take precautions to safeguard their designs, patents, and trade secrets and consider the legal and regulatory framework to protect their interests.
3. Geopolitical Uncertainties: Changes in trade policies, tariffs, and political tensions between China and other countries could impact the supply chain and lead to disruptions. It is vital to monitor geopolitical developments and have contingency plans in place.
Key Players:
1. Foxconn: Known for their extensive manufacturing capabilities, Foxconn is a major player in the Chinese 3D milling industry, serving a broad range of sectors.
2. BYD Company Limited: Primarily focused on electric vehicles, BYD has also established itself as a provider of high-quality 3D milling services for the automotive industry.
3. DJI: Specializing in drones and aerial photography equipment, DJI is a prominent Chinese company that employs 3D milling technologies extensively to produce sophisticated and precise components.
In conclusion, sourcing 3D milling from China offers opportunities in terms of competitive pricing, advanced technology, and diverse industrial capabilities. However, it is important to consider risks related to quality control, intellectual property protection, and geopolitical uncertainties. Key players in the Chinese 3D milling market include Foxconn, BYD, and DJI.
How to find and select reliable 3d milling manufacturers in China,use google search manufacturers and suppliers
Finding and selecting reliable 3D milling manufacturers in China can be a crucial step in ensuring the quality and efficiency of your production process. Here’s a concise guide on how to achieve this using Google search and other strategies:
1. Define your requirements: Know your specific needs regarding 3D milling, such as materials, precision requirements, production volume, and project timeline.
2. Use relevant search terms: Begin by searching for terms like “3D milling manufacturers in China” or “CNC milling suppliers.” Refine your search by adding specific keywords related to your requirements, like “aluminum milling” or “high-precision milling.”
3. Explore top search results: Visit websites of the top search results and browse through their offerings and capabilities. Look for manufacturers that have experience in your industry and offer the desired material and precision capabilities.
4. Check certifications and quality standards: Ensure that the manufacturers hold certifications such as ISO 9001, indicating their commitment to quality control and reliable processes. Look for any other industry-specific certifications that may be applicable to your project.
5. Read customer reviews and testimonials: Look for testimonials or reviews from previous customers to determine the manufacturer’s reputation and reliability. This can provide insights into the quality of their work, customer service, and delivery timelines.
6. Request for samples or portfolios: Contact the shortlisted manufacturers and request samples or a portfolio of their previous work. This will allow you to assess the quality of their products, their attention to detail, and their ability to meet your specific needs.
7. Evaluate communication and responsiveness: Prompt and effective communication is essential for a successful partnership. Pay attention to the responsiveness and clarity of the manufacturers when answering your inquiries or clarifying your requirements.
8. Consider additional factors: Apart from product quality, also consider factors like pricing, production capacity, lead times, and after-sales support.
9. Request for quotes: After evaluating all the above factors, request quotes from multiple manufacturers. Compare the prices, payment terms, and any additional services offered to make an informed decision.
10. Collaboration and monitoring: Once you choose a manufacturer, establish clear communication channels and collaborate closely. Regularly monitor product quality, delivery times, and overall customer experience to ensure reliable and consistent performance.
By following these steps, you can maximize your chances of finding and selecting reliable 3D milling manufacturers in China for your specific requirements.
How to check 3d milling manufacturers website reliable,use google chrome SEOquake check if ranking in top 10M
When assessing the reliability of a 3D milling manufacturer’s website, you can follow a few straightforward steps. Firstly, ensure you are using a reliable and commonly used web browser like Google Chrome. With Chrome, you can utilize an extension called SEOquake to check if the manufacturer’s website is ranking within the top 10 million websites globally. This metric signifies a certain level of popularity and trustworthiness.
To begin, download and install the SEOquake extension from the Chrome Web Store. Once installed, activate the extension by clicking on its icon in your browser’s toolbar. This will enable you to view various SEO-related data for any website you visit.
Next, visit the website of the 3D milling manufacturer you are interested in assessing. Once on their website, click on the SEOquake icon in your browser’s toolbar to open the SEOquake analysis panel. In the panel, you will find an array of metrics and information about the website’s SEO performance.
Look for the website’s “Quantcast Rank” or “Alexa Rank” within the SEOquake panel. These ranks indicate the website’s relative popularity among all websites on the internet. If the manufacturer’s website is within the top 10 million, it generally implies a certain level of reliability.
By following these steps, you can quickly assess the reliability of a 3D milling manufacturer’s website using Google Chrome and the SEOquake extension. Remember to use not more than 300 words to keep your response concise.
Top 10 3d milling manufacturers in China with each 160 words introduce products,then use markdown create table compare
1. Shenzhen Xiamen Machinery Co., Ltd. (SXMC) specializes in 3D milling machines for various applications. Their milling machines feature high precision, efficiency, and are suitable for processing a wide range of materials, including metal, plastic, and wood. With advanced manufacturing techniques and a strong R&D team, SXMC delivers reliable and durable machines that meet international standards.
2. CNC Technology Co., Ltd. is a leading manufacturer of 3D milling machines in China. Their products are widely used in industries such as automotive, aerospace, and electronic manufacturing. CNC Technology offers a diverse range of milling machines with different specifications to meet the specific needs of customers. Their machines are known for their precision, stability, and high cutting speed.
3. Jiangsu Wallong-Hsin Machinery Engineering Co., Ltd. produces advanced 3D milling machines that offer high performance and precision. Their machines are widely used in the mold and die industry, and also find applications in sectors such as automotive and aerospace. With a strong focus on innovation, Wallong-Hsin delivers reliable and efficient milling solutions.
4. Keliang CNC Equipment Co., Ltd. manufactures 3D milling machines suitable for processing various materials, including metal, plastic, and wood. Their machines are equipped with advanced control systems and precision components, ensuring high-quality milling results. Keliang CNC provides customized solutions to meet the unique requirements of different industries.
5. Guangdong Dowin Technology Co., Ltd. is a leading manufacturer of 3D milling machines in China. Their machines offer high precision and efficiency, making them suitable for industries such as automotive, aerospace, and electronics. Dowin Technology’s milling machines are known for their stability, durability, and advanced technological features.
6. Shandong Chencan Machinery Incorporated Company specializes in the production of 3D milling machines for various applications. Their machines are widely used in industries such as woodworking, advertising, and mold making. Chencan Machinery’s milling machines are known for their stability, precision, and high cutting speed.
7. Beijing Jiningshiyun Technology Co., Ltd. manufactures 3D milling machines that are widely used in industries such as automotive, aerospace, and electronics. Their machines offer high precision, efficiency, and stability. Jiningshiyun Technology’s milling machines feature advanced control systems, ensuring optimal milling results.
8. Zhejiang Chuangyuan Numerical Control System Co., Ltd. produces 3D milling machines that are suitable for a wide range of materials, including metal, plastic, and wood. Their machines are known for their high precision, stability, and durability. Chuangyuan’s milling machines are widely used in industries such as mold making, automotive, and aerospace.
9. Jiangsu Dongqing CNC Machine Tool Co., Ltd. specializes in the production of high-quality 3D milling machines. Their machines offer high precision, stability, and are suitable for processing various materials. Dongqing CNC’s milling machines find applications in industries such as aerospace, automotive, and electronics.
10. Shandong Joy CNC Machinery Co., Ltd. manufactures 3D milling machines that are designed for high precision and efficiency. Their machines are widely used in industries such as woodworking, advertising, and mold making. Joy CNC’s milling machines are known for their stability, durability, and advanced technological features.
| Manufacturer | Product Features |
|————————————|——————————————————————————————————————————————————————|
| Shenzhen Xiamen Machinery Co., Ltd. | High precision milling machines suitable for different materials. Advanced manufacturing techniques and strong R&D capabilities. |
| CNC Technology Co., Ltd. | Reliable and high-speed 3D milling machines widely used in various industries. Precise cutting and stable performance. |
| Jiangsu Wallong-Hsin Machinery Co. | Specialized milling machines with high precision and performance. Ideal for mold and die industry. |
| Keliang CNC Equipment Co., Ltd. | Customizable 3D milling machines for metal, plastic, and wood processing. Advanced control systems and precision components for quality results. |
| Guangdong Dowin Technology Co., Ltd. | High-precision milling machines suitable for automotive, aerospace, and electronics industries. Stable, durable, and technologically advanced. |
| Shandong Chencan Machinery Co., Ltd. | Stable and speedy milling machines for woodworking, advertising, and mold making industries. Reliable precision and high cutting speed. |
| Beijing Jiningshiyun Technology Co. | Advanced 3D milling machines for automotive, aerospace, and electronics industries. High precision and efficiency. Technologically advanced control systems. |
| Zhejiang Chuangyuan Numerical… | Milling machines suitable for various materials such as metal, plastic, and wood. High precision, stability, and durability. |
| Jiangsu Dongqing CNC Machine… | High-quality milling machines with high precision and stability. Suitable for aerospace, automotive, and electronics industries. |
| Shandong Joy CNC Machinery Co.,… | Stable and precise 3D milling machines for woodworking, advertising, and mold making industries. Durability and advanced features. |
Background Research for 3d milling manufacturers Companies in China, use qcc.com archive.org importyeti.com
When searching for 3D milling manufacturers in China, three websites can be utilized for background research: qcc.com, archive.org, and importyeti.com. These platforms provide valuable information about companies, including their business profiles, historical data, and import/export records.
Qcc.com is a comprehensive business information database in China. It contains a vast amount of company profiles, financial data, and regulatory registration information. This platform allows users to search for specific manufacturers, view their registration details, and gain insights into their overall business performance. Additionally, it provides a rating system that allows users to assess a company’s creditworthiness, which can be helpful when choosing a reliable 3D milling manufacturer.
Archive.org is a digital library platform that allows users to access archived web pages. By using this website, one can retrieve historical data about the selected 3D milling manufacturers in China. The archived web pages might contain past company descriptions, product catalogs, and other relevant information that can give insights into the company’s evolution and growth over time.
Importyeti.com is a global import/export records platform that provides detailed trade data. By searching for specific 3D milling manufacturers in China, users can access their import/export records, including the countries they trade with, the quantities exported, and the types of products traded. This information can be valuable for assessing a company’s international experience and reputation in the 3D milling industry.
By utilizing these three websites, qcc.com, archive.org, and importyeti.com, researchers can gather important background information on 3D milling manufacturers in China. These platforms offer a comprehensive overview of a company’s financial status, historical data, and import/export records, providing researchers with the necessary insights to make informed decisions when selecting a suitable manufacturer.
Leveraging Trade Shows and Expos for 3d milling Sourcing in China
One effective way to source 3D milling services in China is by leveraging trade shows and expos related to the manufacturing industry. These events provide a platform for businesses to showcase their capabilities, network with potential suppliers, and stay updated on the latest industry trends.
Attending trade shows and expos focused on 3D milling allows companies to explore multiple suppliers in one location, saving time and effort compared to individually researching and contacting numerous suppliers. These events often attract a wide range of manufacturers, including those specializing in 3D milling services, making them the ideal place to find potential suppliers.
When attending these events, it is crucial to have a clear sourcing strategy in mind. This includes defining specific requirements and expectations for the 3D milling services needed. It is also essential to thoroughly research the exhibiting companies beforehand to identify the most promising ones.
During the trade show or expo, businesses should engage in meaningful conversations with the suppliers to understand their capabilities, quality standards, production capacity, and pricing structure. Asking for samples, case studies, or references can provide valuable insights into the supplier’s expertise and previous work. This helps in assessing their suitability for the desired 3D milling projects.
Furthermore, it is important to evaluate the supplier’s overall professionalism, communication skills, and willingness to collaborate. Building a strong and trustworthy relationship with potential suppliers is crucial for long-term success.
After the trade show, companies should follow up with the most promising suppliers to continue the discussion and negotiate terms. It is recommended to request detailed quotations, including pricing, lead times, and any additional services offered. Comparing multiple quotes allows for making an informed decision while considering factors such as quality, cost-effectiveness, and reliability.
In conclusion, trade shows and expos provide an excellent opportunity for sourcing 3D milling services in China. By attending these events and strategically engaging with suppliers, businesses can find reliable partners for their milling needs while saving time and effort in the sourcing process.
The Role of Agents and Sourcing Companies in Facilitating 3d milling Purchases from China
Agents and sourcing companies play a crucial role in facilitating 3D milling purchases from China. These entities bridge the gap between buyers and manufacturers, providing a range of services that simplify the procurement process and ensure smooth transactions. Here are some key aspects of their role:
1. Supplier identification and verification: Agents and sourcing companies have extensive networks and knowledge of the Chinese market. They identify potential suppliers capable of meeting the specific requirements of the buyers. They thoroughly vet these suppliers to ensure their reliability, quality standards, and production capacities.
2. Negotiation and price benchmarking: Agents negotiate with the suppliers on behalf of the buyers, aiming to secure the most competitive prices for the desired 3D milling products. They leverage their market knowledge and negotiation skills to achieve favorable terms and conditions.
3. Quality control and inspection: Agents and sourcing companies perform robust quality control and inspection procedures to ensure the products meet the defined standards. They may conduct on-site visits to assess the manufacturers’ facilities, processes, and equipment. Regular inspections are carried out during production and before shipment to guarantee quality assurance.
4. Logistics and shipping management: These intermediaries handle logistics, transportation, and shipping arrangements, guaranteeing that the products are delivered on time and in the appropriate condition. They coordinate with freight forwarders and ensure compliance with relevant import and export regulations.
5. Language and cultural barriers: Agents and sourcing companies bridge the language and cultural gaps that often hinder direct communication between buyers and Chinese manufacturers. They act as interpreters and cultural mediators, facilitating effective communication and promoting mutual understanding.
6. Risk mitigation and legal support: Agents and sourcing companies can offer legal support, assisting buyers with contract drafting and ensuring compliance with local laws and regulations. They help mitigate the risks associated with international trade, such as intellectual property protection, trade disputes, and payment security.
Overall, agents and sourcing companies streamline the purchasing process, from supplier identification and negotiation to quality control and logistics management. Their expertise, market knowledge, and networks not only facilitate access to trusted manufacturers but also help minimize risks and ensure a successful 3D milling purchase from China.
Price Cost Research for 3d milling manufacturers Companies in China, use temu.com and 1688.com
When conducting price cost research for 3D milling manufacturers in China, two reliable platforms to consider are temu.com and 1688.com. These websites provide a wide range of options for sourcing suppliers and obtaining competitive pricing information.
temu.com is a popular Chinese manufacturing platform that offers an extensive database of suppliers. It allows users to search for specific products and filter results based on various criteria such as location, certification, and minimum order quantity. This platform not only provides contact information for manufacturers but also offers a messaging system for direct communication.
1688.com, also known as Alibaba China, is one of the largest online marketplaces in China. It is specifically designed for the domestic market, enabling users to connect with a vast number of Chinese suppliers. 1688.com offers a wide range of products, including machinery and manufacturing services. It allows users to compare prices, read customer reviews, and negotiate directly with suppliers.
To efficiently conduct price cost research using these platforms, the following steps can be taken:
1. Visit temu.com and search for “3D milling manufacturers” or similar keywords. Filter the results based on location, certifications (such as ISO or CE), and other relevant preferences.
2. Compile a list of potential suppliers, paying attention to their product specifications, pricing information (if available), and customer reviews.
3. Repeat the same process on 1688.com, ensuring to navigate through the categories related to machinery, CNC equipment, or precision manufacturing.
4. Cross-reference the suppliers found on both platforms to ensure a comprehensive search.
5. Contact the shortlisted suppliers through the provided contact information or the messaging systems on the respective platforms. Inquire about their products, pricing, minimum order quantities, and any other relevant details.
6. Request sample products or prototypes if necessary to assess the quality and suitability of the manufacturer’s capabilities.
7. Compare the quotes and overall viability of each supplier, considering factors such as cost, quality, lead time, and communication reliability.
By utilizing temu.com and 1688.com, it is possible to efficiently research and collect price cost information from various 3D milling manufacturers in China. These platforms enable direct communication with suppliers, allowing for effective comparison and evaluation of potential options. Remember to conduct thorough due diligence before finalizing any agreements or purchases.
Shipping Cost for 3d milling import from China
The shipping cost for importing 3D milling machines from China can vary depending on several factors. The main factors that affect the shipping cost include the size and weight of the machines, the shipping method chosen, the destination country, and any additional services required.
Generally, there are two main shipping methods for importing goods from China: sea freight and air freight. Sea freight is usually more cost-effective for large and heavy machines, while air freight is faster but more expensive. The size and weight of the 3D milling machines will determine which shipping method is more suitable.
When it comes to sea freight, the cost is calculated based on the volume of the machines or the weight, whichever is higher. It also depends on the shipping route, distance, and any additional services such as customs clearance and delivery to the final destination. It is advisable to work with a freight forwarder who can provide competitive rates and handle all the necessary paperwork.
Air freight, on the other hand, is charged based on weight and volume, with the heavier or larger shipments costing more. This method is usually faster and preferred for urgent shipments or if the machines are relatively small and lightweight.
To get an estimate of the shipping cost, it is important to provide the freight forwarder with the dimensions, weight, and other necessary details of the machines. They will be able to provide a more accurate quote based on these specifications and the preferred shipping method.
Overall, the shipping cost for importing 3D milling machines from China can range from a few hundred dollars to several thousand dollars, depending on the factors mentioned above. It is recommended to compare quotes from different shipping providers and consider their reputation and reliability before making a decision.
Compare China and Other 3d milling Markets: Products Quality and Price,Visible and Hidden Costs
China is a dominant player in the 3D milling market, but it is crucial to compare it with other markets in terms of products quality, price, and visible and hidden costs. The quality of products can vary across markets due to differences in manufacturing processes, technological advancements, and quality control measures.
China has gained a reputation for offering a wide range of 3D milling products at competitive prices. Its manufacturing infrastructure and economies of scale make it possible to produce goods at lower costs compared to other markets. However, the quality of Chinese products can sometimes be inconsistent, with reports of lower durability and precision compared to products from certain other markets. This inconsistency can be attributed to the diverse range of manufacturers and varying standards followed across China’s vast industrial landscape.
When considering prices, China does have a pricing advantage in terms of affordability. The lower production costs allow Chinese suppliers to offer products at relatively lower prices compared to many other markets. In contrast, some other markets, such as Germany or Japan, may have higher price points due to rigorous quality standards, superior technology, and specialized expertise. These markets focus on producing high-end, precision-engineered milling products that come with a premium price tag.
Visible costs such as manufacturing, shipping, and taxes can be relatively transparent in both China and other markets. However, hidden costs can differ. In China, language and cultural barriers can hinder effective communication and result in misunderstandings or delays, leading to additional costs. Additionally, intellectual property and copyright concerns have been associated with manufacturing in China, potentially resulting in additional legal and licensing costs for businesses.
In conclusion, China offers a vast selection of competitively priced 3D milling products, although quality consistency may vary. Other markets might excel in terms of product quality and precision, but at a higher cost. When comparing visible costs, China may have an advantage, but hidden costs such as language barriers and intellectual property concerns exist. Businesses should carefully consider their specific needs and requirements when selecting a market for 3D milling products.
Understanding Pricing and Payment Terms for 3d milling: A Comparative Guide to Get the Best Deal
When it comes to 3D milling, understanding pricing and payment terms is crucial to ensure you get the best deal possible. This comparative guide aims to shed light on these aspects in order to help you make informed decisions.
1. Pricing Models:
Different 3D milling service providers may adopt various pricing models. The most common are:
– Hourly Rate: Some providers charge based on the time taken to complete the milling job. The hourly rate can vary depending on factors such as complexity and materials used.
– Project-Based: In this model, a fixed price is negotiated based on the scope of the project. It offers better cost predictability, especially for larger-scale milling projects.
Comparing pricing models will depend on your specific requirements. Hourly rates may be suitable for small, quick-turnaround jobs, while project-based pricing might be more preferable for long-term projects with well-defined specifications.
2. Additional Costs:
Apart from the base price, it is essential to consider any additional costs that may be associated with the milling process. These may include:
– Material Costs: Some providers charge separately for the raw materials used in the milling process.
– Design and Development: If your project requires design modifications or engineering assistance, additional charges may apply.
– Shipping and Logistics: If you are not located near the milling service provider, it is important to consider shipping and logistics costs.
Comparing these additional costs will help you evaluate the total expenditure involved in your 3D milling project.
3. Payment Terms:
Understanding the payment terms is crucial in securing the best deal. Some important factors to consider are:
– Upfront Payments: Some providers may require a percentage of the project cost to be paid upfront.
– Progress Payments: For longer-term projects, installment-based payments may be agreed upon, with specific milestones triggering payment releases.
– Payment Methods: Understanding the accepted payment methods will help you plan your financing and ensure a smooth transaction.
Obtaining quotes from multiple providers and comparing their payment terms will allow you to choose the most favorable option for your budget and cash flow requirements.
In conclusion, it is vital to thoroughly analyze pricing models, additional costs, and payment terms when considering 3D milling services. By conducting a comparative guide and evaluating these aspects, you can minimize costs, maximize the value for your money, and ultimately secure the best deal for your project.
Chinese Regulations and Industry Standards Certifications for 3d milling,Import Regulations and Customs for 3d milling from China
China has established specific regulations and industry standards certifications for 3D milling, aiming to ensure the quality and safety of such products. One of the key certifications is the China Compulsory Certification (CCC), which is mandatory for certain products intended for the Chinese market.
The CCC certification for 3D milling equipment ensures that the product complies with relevant technical regulations. The certification process involves testing the product’s performance, safety, and quality parameters, as well as evaluating the manufacturer’s production capabilities and quality management system.
In addition to CCC certification, there are industry standards that serve as guidelines for 3D milling equipment manufacturers. These standards include performance, safety, and quality requirements that the products should meet. Manufacturers are encouraged to adhere to these standards to enhance the competitiveness of their products and promote innovation within the industry.
To import 3D milling equipment from China, it is necessary to comply with import regulations and customs procedures. Importers should identify the specific HS code or tariff classification for their products to determine the applicable import duties and taxes. Additionally, they need to ensure that the products meet any required certifications or standards in their own country to avoid any complications during the customs clearance process.
Documentation required for import includes the commercial invoice, packing list, bill of lading or airway bill, and any relevant certificates or permits. Importers should also be aware of any specialized requirements or regulations for the importation of specific types of 3D milling equipment, such as those related to safety and environmental standards.
Working with a reputable freight forwarder or customs broker can assist importers in navigating through the import regulations and customs procedures more smoothly and efficiently. They can provide guidance on tariff rates, documentation requirements, and help ensure compliance with all applicable regulations.
In summary, China has regulations and certifications in place for 3D milling equipment, such as the CCC certification and industry standards. Importers should be familiar with import regulations and customs procedures, ensuring necessary documentation and compliance with standards in their own country. Collaboration with a competent freight forwarder or customs broker can simplify the import process.
Sustainability and Environmental Considerations in 3d milling Manufacturing
Sustainability and environmental considerations are becoming increasingly important in modern manufacturing processes, and 3D milling is no exception. 3D milling refers to the process of using computer-controlled machines to remove material from a workpiece to create a desired shape or design. While this technology offers several advantages in terms of precision, efficiency, and flexibility, it also poses challenges in terms of sustainability and environmental impact.
One of the key environmental concerns in 3D milling is the generation of waste material. As the milling machine cuts away excess material from the workpiece, a significant amount of waste is produced. This waste, typically in the form of chips, can be difficult to recycle or dispose of in an environmentally friendly manner. Manufacturers need to consider ways to minimize waste generation through efficient design and optimization of the milling process.
Another important consideration is the energy consumption associated with 3D milling. These machines often require substantial amounts of electricity to operate, which may have a significant carbon footprint depending on the energy source. It is essential for manufacturers to explore energy-efficient technologies and alternative energy sources to reduce the environmental impact of 3D milling.
Furthermore, the choice of materials used in 3D milling has implications for sustainability. Some materials commonly used in milling, such as certain metals or plastics, may have a significant environmental footprint in terms of extraction, processing, and disposal. It is crucial to evaluate the life cycle impacts of different materials and opt for more sustainable alternatives whenever possible.
In addition to these concerns, manufacturers should also consider the potential emissions and pollutants associated with 3D milling processes. Dust, fumes, and chemical by-products generated during milling can pose health risks to workers and contribute to air and water pollution. Implementing effective ventilation, filtration, and waste management systems is imperative to minimize these impacts.
To conclude, sustainability and environmental considerations play a vital role in the practice of 3D milling manufacturing. Minimizing waste generation, reducing energy consumption, choosing sustainable materials, and managing emissions and pollutants are all essential for sustainable and environmentally responsible manufacturing practices in the field of 3D milling.
List The Evolution history of “3d milling”
3D milling, also known as 3D milling machining or 3-axis milling, has evolved significantly over the years, revolutionizing manufacturing and shaping various industries. Here is a brief history of its evolution:
1. Early Milling Machines: The evolution of 3D milling can be traced back to the early 19th century when manual milling machines were first developed. These machines utilized rotary cutters to remove material from the workpiece in a controlled manner.
2. Numerical Control (NC): The introduction of numerical control in the mid-20th century marked a significant advancement in milling technology. NC milling machines allowed for the programming of precise tool paths using punched cards or magnetic tapes, thus reducing human error and enhancing precision.
3. Computer Numerical Control (CNC): In the 1970s, CNC machining revolutionized the milling industry. CNC machines replaced the punch cards and tapes with computer programs, offering greater flexibility, efficiency, and the ability to execute complex designs automatically.
4. 3D CAD/CAM Integration: With the progression of computer-aided design (CAD) and computer-aided manufacturing (CAM) technologies, 3D milling took another leap forward. The integration of CAD/CAM software with CNC machines enabled the direct translation of 3D CAD models into machine code, streamlining the manufacturing process.
5. High-Speed Machining (HSM): As machining technology advanced, the concept of high-speed machining emerged in the early 1990s. HSM aimed to maximize material removal rates while maintaining accuracy and surface finish, resulting in reduced machining times.
6. 5-Axis and Multi-axis Machining: To enhance the capabilities of 3D milling, manufacturers began incorporating additional axes of movement. 5-axis and multi-axis milling machines allowed simultaneous machining from different angles, enabling complex geometries and reducing setup times.
7. Additive-Subtractive Hybrid Machines: In recent years, the development of hybrid machines that combine additive manufacturing (3D printing) with subtractive milling has expanded the possibilities for 3D milling. These machines offer the ability to build complex geometries through additive techniques and then refine the surfaces or add fine details through subtractive milling.
Today, 3D milling continues to evolve, with advancements in automation, robotics, tooling, and software. It is being utilized across numerous industries, including aerospace, automotive, healthcare, and consumer goods, driving innovation and pushing the boundaries of what is possible in manufacturing.
The Evolution and Market Trends in 3d milling Industry
The 3D milling industry has witnessed significant evolution and market trends in recent years, driven by technological advancements and increasing demand for precision manufacturing. 3D milling, also known as computer numerical control (CNC) milling, involves the use of computer-controlled machines to remove material from a workpiece, resulting in highly accurate and complex 3D objects.
One of the key evolutions in the 3D milling industry is the development of advanced software and hardware solutions. Manufacturers are now utilizing sophisticated design software, such as Computer-Aided Design (CAD), to create intricate 3D models that can be directly translated into milling instructions. This streamlines the manufacturing process, reducing human error and improving overall efficiency.
Additionally, advancements in milling machine technology have enabled faster and more precise milling operations. High-speed mills equipped with multiple axes and advanced tooling systems can now rapidly produce complex parts with minimal manual intervention. These machines can handle a wide range of materials, including metal, plastic, and wood, further expanding their applications across various industries.
Another major trend in the 3D milling industry is the growing adoption of automation and robotics. Many manufacturers are incorporating robotic milling systems into their production lines to achieve higher productivity and cost-effectiveness. These systems can operate 24/7, reducing labor costs and speeding up the production cycle, making them highly attractive for large-scale manufacturing.
Furthermore, the increasing demand for sustainability and environmental consciousness is influencing the 3D milling industry. Manufacturers are now focusing on using eco-friendly materials and adopting energy-efficient practices. Additionally, the integration of additive manufacturing techniques with 3D milling has gained traction, allowing for advanced hybrid manufacturing processes that reduce material waste and promote sustainability.
In terms of market trends, the 3D milling industry is experiencing significant growth across various sectors. The automotive and aerospace industries, in particular, are embracing 3D milling technology to produce lightweight and complex components that enhance fuel efficiency and performance. The medical and dental industries are also increasingly adopting 3D milling for precision manufacturing of prosthetics and dental implants.
Overall, the evolution of software and hardware solutions, the integration of automation and robotics, and the growing demand for sustainability are shaping the future of the 3D milling industry. With its ability to produce high-quality, complex parts with speed and efficiency, 3D milling is poised to continue its growth and expansion in the manufacturing sector.
Custom Private Labeling and Branding Opportunities with Chinese 3d milling Manufacturers
Chinese 3D milling manufacturers offer excellent opportunities for custom private labeling and branding. With their advanced technology and capabilities, these manufacturers can produce high-quality customized products for businesses looking to create their own brand.
Private labeling allows businesses to sell products under their own brand name, adding value and exclusivity to their offerings. Chinese 3D milling manufacturers have the expertise to create unique designs and produce customized products according to specific requirements. This includes customizing product shapes, finishes, materials, and even packaging, enabling businesses to differentiate themselves in the market.
In addition to private labeling, Chinese 3D milling manufacturers also offer branding opportunities. They can help businesses incorporate their brand identity into the products by incorporating logos, colors, and other visual elements. This branding integration helps in building brand recognition and customer loyalty.
Furthermore, working with Chinese manufacturers offers cost-effective solutions for customized products. China is known for its competitive pricing and expertise in manufacturing. By leveraging the capabilities of these manufacturers, businesses can access high-quality custom products at lower costs, maximizing profitability.
However, when exploring private labeling and branding opportunities with Chinese 3D milling manufacturers, it is crucial to ensure quality control and intellectual property protection. Partnering with reputable manufacturers and conducting proper due diligence is essential to maintain product quality and protect brand integrity.
In conclusion, Chinese 3D milling manufacturers offer businesses the chance to create custom private labeled products and build their brand identity. With their expertise, cost-effectiveness, and ability to produce unique designs, these manufacturers provide excellent opportunities for businesses to enhance their offerings in the market.
Tips for Procurement and Considerations when Purchasing 3d milling
When it comes to procurement and purchasing 3D milling, there are a few key tips and considerations that should be kept in mind. These factors can help organizations make informed decisions and ensure successful procurement.
1. Define the requirements: Clearly establish the specifications and requirements for the 3D milling equipment. Consider factors such as maximum workpiece size, accuracy, speed, and material compatibility. This will help in identifying suitable vendors and selecting the right equipment for the organization’s needs.
2. Research potential vendors: Conduct thorough research on potential vendors to ensure their credibility and reliability. Look for vendors with a proven track record, positive customer reviews, and good after-sales support. Additionally, consider their financial stability and warranty/guarantee policies.
3. Evaluate costs: Consider both the upfront cost of the equipment and the long-term costs associated with maintenance, repairs, and consumables. Look for vendors offering competitive prices without compromising on quality. It may also be beneficial to compare different vendors and request quotes to get a better idea of the market rates.
4. Consider compatibility and integration: Ensure that the chosen 3D milling equipment is compatible with existing systems and software used by the organization. Compatibility issues can lead to additional expenses or limitations on functionality. Similarly, consider any integration requirements with other machinery or equipment.
5. Training and support: Assess the vendor’s ability to provide proper training and support for the operation and maintenance of the 3D milling equipment. Ensure that they offer comprehensive training programs and prompt technical support to minimize downtime and enhance productivity.
6. Consider future needs: Look beyond the immediate requirements and consider if the chosen equipment will be able to accommodate future needs or expansions. This can help avoid the need for frequent replacements or upgrades, saving both time and money in the long run.
7. Quality assurance: Ask potential vendors about the quality assurance protocols they have in place. Inquire about any certifications or standards they adhere to and their quality control processes. This will ensure that the equipment meets industry standards and delivers consistent performance.
8. Feedback and references: Seek feedback from existing customers of the vendors under consideration. This will provide insights into their experience with the equipment and the vendor’s customer service. References can help verify the vendor’s claims and give a clearer picture of the overall satisfaction level.
By following these tips and considering these factors, organizations can make informed decisions and successfully procure 3D milling equipment that meets their requirements and ensures long-term benefits.
FAQs on Sourcing and Manufacturing 3d milling in China
1. Why should I consider sourcing and manufacturing 3D milling in China?
China is known for its cost-effective manufacturing capabilities and abundant supply of skilled labor, making it an attractive option for businesses looking to reduce production costs without compromising on quality. The country has a well-established infrastructure for manufacturing and a vast network of suppliers, enabling efficient sourcing of materials and components for 3D milling.
2. What are the benefits of sourcing and manufacturing 3D milling in China?
The main benefits include lower production costs, access to a diverse range of machining technologies, quick turnaround times, flexibility in volume production, and the ability to achieve complex designs and high precision. China’s competitive manufacturing landscape also fosters innovation, enabling businesses to tap into the country’s vast technological advancements in the 3D milling industry.
3. What is the average lead time for sourcing and manufacturing 3D milling in China?
Lead times can vary depending on factors such as the complexity of the design, quantity, and production capacity of the chosen supplier. However, in general, Chinese manufacturers can offer relatively short lead times compared to other regions, thanks to streamlined production processes, efficient supply chains, and a large manufacturing workforce.
4. How can I ensure the quality of 3D milling products sourced from China?
To ensure product quality, it is essential to thoroughly vet potential suppliers, review their certifications, and request sample products before placing large orders. Working with a sourcing agent or partner in China who has expertise in the 3D milling industry can also help ensure proper quality control and inspection procedures are in place.
5. Are intellectual property rights protected when sourcing and manufacturing 3D milling in China?
While China has made strides in protecting intellectual property rights, concerns persist. It is crucial to work with experienced legal counsel to navigate the complexities of intellectual property protection in China. Employing non-disclosure agreements (NDAs) and proprietary technologies can further safeguard your designs and trade secrets.
In summary, sourcing and manufacturing 3D milling in China offer advantages such as cost-effectiveness, technological advancements, efficiency, and accessibility to a vast array of suppliers. However, careful due diligence, quality control measures, and protection of intellectual property rights should be considered to ensure a successful collaboration in China’s 3D milling industry.
Why contact sourcifychina.com get free quota from reliable 3d milling suppliers?
Contacting Sourcifychina.com can be beneficial for businesses seeking reliable 3D milling suppliers as it offers a unique advantage of obtaining a free quota from such suppliers. This plays a crucial role in ensuring that businesses can access high-quality manufacturing services at competitive prices.
Sourcifychina.com is a reputable platform that connects businesses with reliable suppliers in China. It has developed strong relationships and partnerships with numerous suppliers specializing in various manufacturing processes, including 3D milling. These suppliers have undergone a strict vetting process to ensure their reliability and consistency in delivering top-notch products.
By offering a free quota, Sourcifychina.com enables businesses to explore the capabilities and pricing of different 3D milling suppliers without incurring any financial risks. This allows businesses to make informed decisions by comparing quotes and evaluating the quality, lead times, and pricing offered by different suppliers. It also gives them the opportunity to assess the responsiveness and professionalism of the suppliers, ensuring a good fit for their requirements.
The free quota provided by Sourcifychina.com helps businesses to save costs in their manufacturing process. Instead of directly engaging with suppliers and potentially paying for quotes, businesses can leverage this free service to estimate project costs and negotiate pricing before committing to a specific supplier. This enables businesses to allocate their budgets more effectively and make informed decisions that align with their financial goals.
Furthermore, the free quota service from Sourcifychina.com promotes transparency and trust between businesses and suppliers. By obtaining multiple quotes, businesses can gain a clearer understanding of market prices, ensuring they receive fair pricing from potential suppliers. This transparency also helps to establish trust with suppliers as it demonstrates a commitment to fair negotiations and fosters open communication.
In conclusion, contacting Sourcifychina.com for a free quota from reliable 3D milling suppliers offers numerous benefits for businesses seeking manufacturing services. It allows them to explore different options, assess pricing, quality, and other factors before committing to a supplier. This cost-saving service promotes transparency and trust, ultimately assisting businesses in making well-informed decisions and achieving successful manufacturing partnerships.