Introduce about 3d print titanium guide,Qulity,Cost,Supplier,Certification,Market,Tips,FAQ
The 3D printing of titanium has revolutionized the manufacturing industry by offering a multitude of benefits. This guide aims to provide an overview of key aspects related to the 3D printing of titanium, including quality, cost, suppliers, certification, market trends, tips, and frequently asked questions.
Quality is a vital consideration when using 3D printed titanium. The process ensures the production of intricate designs with high precision and accuracy. The material’s superior strength-to-weight ratio makes it ideal for applications that require lightweight yet sturdy components. 3D printed titanium parts also exhibit excellent corrosion resistance, making them suitable for various industries.
Cost is a significant factor in any manufacturing process. While the initial investment for 3D printing titanium can be high, the technology offers cost advantages in several areas. It eliminates the need for expensive tooling or molds, reduces material waste, and enables the production of complex designs in a single manufacturing step. These factors contribute to overall cost savings and increased efficiency.
Finding reliable suppliers is crucial for obtaining high-quality 3D printed titanium products. Several reputable companies specialize in this field, providing expertise and the necessary production capabilities. It is advisable to select suppliers with a proven track record, exceptional customer reviews, and a wide range of certification.
Certification ensures that the 3D printed titanium parts meet industry standards and quality requirements. Suppliers that hold certifications such as ISO 9001 or AS9100 demonstrate their commitment to quality management systems, ensuring consistent and reliable products. It is vital to verify certifications before partnering with a supplier.
The market for 3D printed titanium continues to grow rapidly. Industries such as aerospace, automotive, medical, and defense are increasingly incorporating this technology. The ability to manufacture lightweight yet robust components with intricate designs has opened up new possibilities and applications.
Here are some tips for successful 3D printing of titanium:
1. Optimize the design for additive manufacturing, leveraging the unique capabilities of this technology.
2. Ensure proper equipment calibration, material handling, and post-processing to achieve the desired quality.
3. Collaborate with suppliers and utilize their expertise to refine designs and identify cost-saving opportunities.
Frequently Asked Questions:
1. Can 3D printing produce complex shapes with titanium?
Yes, one of the significant advantages of 3D printing titanium is the capability to manufacture complex and intricate designs.
2. Is 3D printed titanium as strong as traditionally manufactured titanium?
Yes, 3D printed titanium exhibits similar strength properties to traditionally manufactured titanium.
3. Are there any limitations of 3D printing titanium?
Some limitations include high initial costs, limited material choices, and size constraints. However, these limitations continue to improve as technology advances.
In conclusion, 3D printing titanium offers numerous benefits, including high quality, cost savings, and design flexibility. With the growing demand for titanium-based components, it is essential to partner with reliable suppliers holding necessary certifications. By understanding the market trends, implementing best practices, and considering design optimizations, businesses can leverage the advantages of 3D printed titanium effectively.
Types of 3d print titanium
When it comes to 3D printing with titanium, there are several types of titanium alloys that are commonly used. These alloys possess different properties and are suitable for various applications. Here are some of the most popular types of 3D print titanium:
1. Ti6Al4V (also known as Grade 5 titanium): This is the most commonly used titanium alloy in additive manufacturing. It consists of approximately 90% titanium, 6% aluminum, and 4% vanadium. Ti6Al4V offers excellent mechanical properties, high strength-to-weight ratio, corrosion resistance, and biocompatibility. It is widely used in aerospace, automotive, medical, and industrial applications.
2. Ti6Al4V ELI (Extra Low Interstitials): This variant of Ti6Al4V is specifically designed for biomedical applications due to its improved compatibility with human tissues. It has lower levels of interstitial elements like oxygen, nitrogen, and carbon, which makes it more biocompatible and reduces the risk of adverse reactions in the human body.
3. Beta C (Ti-15V-3Cr-3Sn-3Al): This titanium alloy is known for its excellent biocompatibility and superior strength-to-weight ratio. It offers good corrosion resistance and is suitable for applications in the aerospace, medical, and chemical industries.
4. Pure titanium (Grade 2): This is commercially pure titanium and is typically used when high ductility and formability are required. Although it has lower strength compared to titanium alloys, it boasts excellent corrosion resistance and is often used in marine, chemical, and architecture applications.
5. Alpha + Beta alloys: These alloys, such as Ti-6Al-2Sn-4Zr-2Mo, offer excellent strength and hardness combined with good toughness. They are primarily used in aerospace, automotive, and marine applications that require high-performance materials.
Apart from these commonly used titanium alloys, there are ongoing research and development efforts to create advanced titanium composites with enhanced properties. These include alloys with improved fatigue resistance, higher thermal conductivity, and specific compositions tailored for specific applications.
In conclusion, the various types of 3D print titanium alloys available offer a wide range of mechanical, thermal, and chemical properties suitable for diverse industries and applications. The choice of the alloy depends on specific requirements, such as mechanical strength, corrosion resistance, and biocompatibility. 3D printing with titanium has opened up new possibilities in manufacturing, as it enables the production of complex geometries and lightweight structures that were previously difficult to achieve using traditional manufacturing methods.
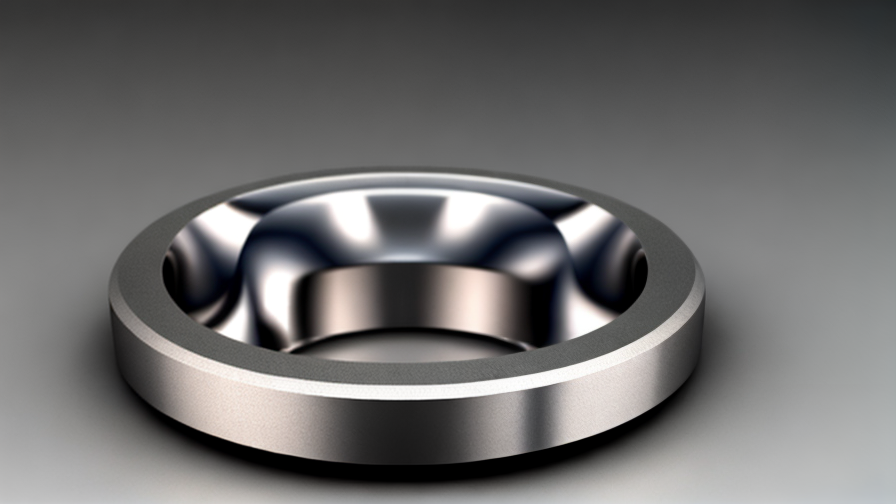
Pros and Cons of Using 3d print titanium
Using 3D print titanium offers several advantages over traditional manufacturing methods, but it also comes with a few drawbacks. Here are some pros and cons of utilizing 3D printed titanium:
Pros:
1. Design Flexibility: 3D printing allows for the creation of complex geometries and intricate designs that are difficult or even impossible to achieve using conventional manufacturing techniques. This level of design flexibility enables the production of lightweight and optimized structures, ultimately reducing material waste.
2. Customization: 3D printing allows for easy customization, making it suitable for producing one-off or small-batch parts tailored to specific requirements. This technology eliminates the need for expensive molds or tooling, making it more cost-effective for prototypes and personalized products.
3. Enhanced Product Performance: Titanium is known for its excellent strength-to-weight ratio, corrosion resistance, and biocompatibility. The 3D printing process allows for precise control over the internal structure of the titanium part, optimizing its mechanical properties. This leads to improved product performance in industries such as aerospace, automotive, and medical.
4. Reduced Lead Times: Traditional manufacturing methods often involve time-consuming steps, such as manufacturing tooling and fixtures. With 3D printing, parts can be produced more quickly and efficiently, which is especially advantageous for urgent or time-sensitive projects.
Cons:
1. High Initial Costs: The equipment and materials used in 3D printing titanium can be expensive. Additionally, the pre-processing software and expertise required for preparation and printing necessitate additional investments. These initial costs may limit access to 3D printing technology for some organizations.
2. Limited Size and Scale: The build volume of most 3D printers is restricted compared to conventional manufacturing equipment. Large-scale production of titanium parts using 3D printing is technically challenging and financially demanding. Therefore, it may not be suitable for applications requiring large or oversized components.
3. Material Limitations: While titanium is a suitable material for 3D printing, its usage can be restricted due to the limited number of available titanium alloys. This reduces the material choices available to designers and manufacturers compared to other manufacturing methods.
4. Post-Processing Challenges: After the initial 3D printing process, titanium parts often require additional post-processing steps, such as heat treatment, surface finishing, and machining, to achieve the desired final properties or dimensions. These extra steps increase the overall production time and cost.
In summary, 3D printing titanium provides numerous advantages such as design flexibility, customization options, enhanced product performance, and reduced lead times. However, the technology also has drawbacks including high initial costs, limited size and scale capabilities, material limitations, and additional post-processing requirements. Organizations considering the adoption of 3D printed titanium should carefully evaluate these pros and cons to determine its suitability for their specific applications and requirements.
3d print titanium Reference Specifications (varies for different product)
3D printing with titanium offers a range of possibilities due to the material’s excellent properties, such as high strength-to-weight ratio, corrosion resistance, and biocompatibility. However, the reference specifications for 3D printing titanium can vary depending on the specific product and its intended use.
Typically, the minimum wall thickness for a 3D printed titanium part can be around 0.5 mm, but this can vary depending on the geometry and size of the design. The minimum feature size is often around 0.25 mm, ensuring intricate details can be accurately reproduced. Additionally, the maximum build size differs for different 3D printing machines but can extend up to several meters, allowing for various sizes of titanium parts to be produced.
Regarding mechanical properties, the minimum tensile strength is generally around 900 MPa, while the minimum yield strength can be approximately 800 MPa. The minimum elongation at break is typically 10%, indicating the material’s ability to deform before fracture. These properties make titanium an attractive choice for applications where structural integrity is crucial.
It is worth mentioning that the process used for 3D printing titanium can impact the final product’s specifications. For example, powder bed fusion techniques, like selective laser melting or electron beam melting, can provide high precision and excellent mechanical properties. The powder size used for these processes typically ranges between 20 to 200 microns, for optimal resolution.
Post-processing techniques like stress relieving and hot isostatic pressing might be applied to improve the material’s mechanical properties further. These additional steps can enhance the overall density, reduce residual stresses, and enhance the ductility of the 3D printed titanium parts.
As for surface finish, the as-printed surfaces may exhibit a certain degree of roughness due to the layer-by-layer manufacturing process. However, these surfaces can be post-processed through milling, grinding, or polishing to achieve the desired aesthetic and functional requirements.
In conclusion, the reference specifications for 3D printing titanium can vary depending on the specific product requirements. Design considerations, such as wall thickness and feature size, along with mechanical properties like tensile strength and yield strength, play crucial roles when determining the ideal parameters for successful 3D printing. Considering the versatility and exceptional properties of titanium, it continues to be an incredible material for additive manufacturing in various industries.
Applications of 3d print titanium
3D printing, also known as additive manufacturing, has revolutionized the production processes across various industries. One highly sought-after application of 3D printing technology is the production of titanium components. Titanium, renowned for its high strength-to-weight ratio, excellent corrosion resistance, and biocompatibility, offers numerous possibilities for 3D printing applications. Let’s explore some of the key areas where 3D printed titanium is making a significant impact.
1. Aerospace Industry: Titanium parts can be custom-designed and produced using 3D printing techniques, making them lighter, more durable, and cost-effective. Application areas include aircraft structural components, engine parts, equipment brackets, fuel system components, and airframe components.
2. Medical and Dental: 3D printed titanium has found extensive application in the medical field. It allows for the creation of patient-specific implants, prosthetics, and surgical instruments. Custom implants, such as hip, knee, or cranial implants, are generated using patient-specific data, leading to improved patient outcomes. Additionally, dental industries benefit from 3D printed titanium in the fabrication of crowns, bridges, and orthodontic appliances.
3. Automotive Industry: 3D printed titanium offers potential applications in the automotive sector, including lightweight structural components, suspension parts, engine components, and exhaust systems. Utilizing 3D printing technology enables designers to optimize part geometries and reduce overall weight, leading to enhanced fuel efficiency and improved performance.
4. Industrial Manufacturing: Titanium parts with complex geometries and intricate designs can be produced using 3D printing technology, enabling greater flexibility and customization. Applications in this sector range from tooling and jigs to specialty components used in chemical processing, oil and gas, and heavy machinery.
5. Sports and Recreation: 3D printed titanium enables the production of lightweight and high-performance sporting goods such as bicycle frames, golf clubs, tennis racket frames, and helmets. The ability to create complex geometries and tailor designs leads to superior performance and customization in sports equipment.
6. Defense and Military: 3D printed titanium components find use in defense applications, including aerospace and naval defense systems. High-strength and lightweight titanium parts can be produced for armored vehicles, missiles, drones, and satellite systems, optimizing performance and reducing costs.
7. Architecture and Design: Architectural firms explore the possibilities of 3D printed titanium for unique building structures. The lightweight nature of titanium paired with its strength allows for the creation of intricate and sustainable designs that were previously impossible.
The applications of 3D printed titanium extend beyond these areas, with ongoing research and development driving further innovation. The technology’s ability to produce complex and lightweight parts with unique geometric features, coupled with titanium’s exceptional properties, offers significant advantages in various industries, resulting in optimized performance, cost savings, and improved product design.
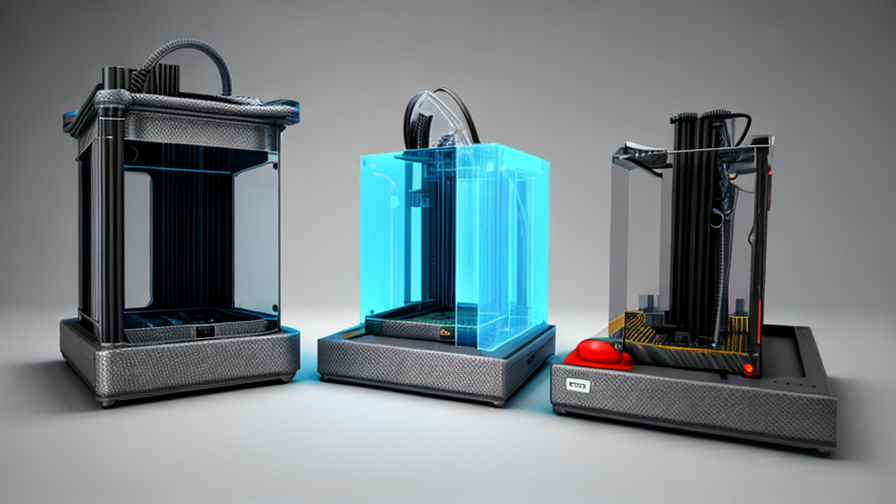
The Work Process and how to use 3d print titanium
The process of 3D printing with titanium involves several steps. The first step is to create a 3D model of the desired object using computer-aided design (CAD) software. This model is then sliced into thin layers using specialized software.
Next, the sliced model is sent to a 3D printer that is capable of printing with titanium. The 3D printer uses a nozzle or a laser to selectively melt and fuse titanium powder together layer by layer, following the sliced model.
During the printing process, a build platform moves downwards as each layer is completed. This allows for the creation of complex and intricate geometries. Additionally, support structures may be printed alongside the object to provide stability during the printing process.
Once the printing is complete, the object is removed from the printer. However, it is still attached to the support structures and needs to be post-processed. The object is placed in a furnace where it undergoes a process called sintering. This involves heating the object to a specific temperature to fully bond the layers of titanium together.
After sintering, the excess support structures are removed by hand or using mechanical means. The object may then undergo additional post-processing steps such as polishing or sandblasting to achieve the desired surface finish.
Using 3D printing to create objects with titanium offers several benefits. It allows for the production of highly complex and customized parts that would be difficult or impossible to manufacture using traditional methods. It also reduces waste material, as only the required amount of titanium powder is used.
However, it is worth noting that 3D printing with titanium can be a challenging process due to the high melting point and reactivity of the material. It requires specialized 3D printers, as well as careful control of factors such as temperature, oxygen levels, and layer thickness.
In conclusion, the process of 3D printing with titanium involves creating a 3D model, slicing it into layers, and then selectively melting and fusing titanium powder to build up the object layer by layer. Post-processing steps such as sintering and support structure removal are essential to achieve the final desired product.
Quality Testing Methods for 3d print titanium and how to control the quality
When it comes to quality testing methods for 3D printed titanium, there are several techniques that can be employed to ensure the desired standards are met. The primary focus is on controlling the quality of the printed parts and identifying any potential defects. Here are some commonly used methods:
1. Visual Inspection: The simplest and most fundamental method is visual inspection, which involves a thorough examination of the printed part for any visible defects such as surface imperfections, cracks, or warping. This manual inspection helps in identifying any obvious defects that may compromise the quality of the part.
2. Dimensional Accuracy Testing: To ensure the printed part meets the required specifications, dimensional accuracy testing is performed. This involves measuring the critical dimensions of the part using precision tools such as calipers or coordinate measuring machines. Deviations from the design specifications can indicate quality issues.
3. Microstructure Analysis: Examination of the microstructure of the 3D printed titanium is crucial to assess the material’s integrity. Optical microscopy, electron microscopy, or X-ray diffraction techniques can be utilized to study grain structure, porosity, and assess the presence of any defects.
4. Mechanical Testing: Mechanical properties such as tensile strength, elasticity, and fatigue resistance need to be evaluated to ensure the printed titanium part can withstand the intended use. Standard mechanical tests like tensile testing, hardness testing, and impact testing are typically performed according to relevant standards.
5. Non-Destructive Testing (NDT): NDT methods can be employed to inspect the quality of the 3D printed titanium parts without causing any damage. Techniques like ultrasonic testing, X-ray inspection, or dye penetrant testing can detect internal defects, discontinuities, or inclusions that may affect the structural integrity of the part.
To control the quality of 3D printed titanium, it is essential to implement quality management systems. This may involve documenting and following standardized procedures, maintaining traceability, validating printing parameters, and conducting regular equipment calibration. Moreover, continuous monitoring and process control are necessary to identify any deviations or variations that may impact the quality of the final product. By employing these quality testing methods and implementing robust quality control measures, manufacturers can ensure the 3D printed titanium parts meet the required standards and specifications.
3d print titanium Sample Policy and Post-Purchase Considerations for 3d print titanium from China
Sample Policy:
When purchasing 3D printed titanium products from China, it is important to consider the supplier’s sample policy. Before committing to a bulk order, it is advisable to request samples to evaluate the quality, finish, and accuracy of the 3D printed titanium items.
The supplier may have different sample policies, such as providing free samples, charging a nominal fee, or offering sample discounts that can be applied to the subsequent order. It is crucial to clarify these details with the supplier before proceeding.
Examining the samples closely allows for an assessment of the supplier’s manufacturing capabilities, precision, and attention to detail. Comparing different samples from various suppliers can aid in making an informed decision regarding the chosen supplier. The samples should be thoroughly inspected to ensure that they meet the desired specifications and quality standards.
Post-Purchase Considerations:
After purchasing 3D printed titanium products from China, several post-purchase considerations should be taken into account:
1. Quality Verification: Upon receiving the bulk order, it is essential to inspect the products to confirm that they match the approved samples both in terms of material quality and dimensional accuracy.
2. Communication: Maintain open lines of communication with the supplier to address any concerns or issues that may arise. Promptly reporting any quality problems is crucial for finding an appropriate resolution.
3. Warranty and Returns: Review the supplier’s warranty policy to understand the coverage and process for returning defective or unsatisfactory products. Clear communication regarding return procedures can help in avoiding misunderstandings.
4. Customs and Shipping: Be aware of any potential customs regulations, import duties, or shipping requirements when importing 3D printed titanium products from China. Ensuring compliance with these regulations can prevent unexpected delays or additional costs.
5. Feedback: Share feedback with the supplier once the product has been received and evaluated. This helps build a better working relationship and encourages the supplier to address any issues promptly.
By carefully considering the sample policy and taking post-purchase considerations into account, buyers can ensure a smoother purchase experience when ordering 3D printed titanium products from China.
Sourcing 3d print titanium from China: Opportunities, Risks, and Key Players
China is a leading player in the global 3D printing market and offers various opportunities for sourcing 3D printed titanium. One of the significant advantages of sourcing from China is its cost-effectiveness. Chinese manufacturers offer competitive pricing due to low labor and production costs.
China’s 3D printing industry has witnessed significant growth, primarily driven by its robust manufacturing capabilities and technological advancements. The abundant availability of raw materials, including titanium, allows Chinese manufacturers to meet the increasing demand for 3D printed titanium products.
Sourcing titanium from China presents an opportunity for businesses to access a wide range of 3D printing technologies, such as Selective Laser Melting (SLM) and Electron Beam Melting (EBM). These technologies ensure high precision and quality in manufacturing titanium components, making them suitable for various industries like aerospace, medical, and automotive.
However, there are some risks associated with sourcing 3D printed titanium from China. Quality control remains a concern as not all manufacturers may adhere to international quality standards. Collaborating with reputable and certified suppliers can mitigate this risk. Intellectual property protection is another challenge in China, as copying and counterfeiting of designs and technologies is prevalent. It is essential to take necessary precautions such as signing non-disclosure agreements (NDAs) to protect intellectual property rights.
Key players in the Chinese market for 3D printed titanium include companies like Tiertime, Shining 3D, and Farsoon Technologies. Tiertime is known for its advanced desktop 3D printers, catering to a wide range of industries. Shining 3D offers industrial-grade 3D printing solutions, including metal 3D printers suited for titanium printing. Farsoon Technologies specializes in high-speed production-grade metal 3D printers, providing cost-effective options for sourcing titanium components.
Overall, China presents valuable opportunities for sourcing 3D printed titanium due to its competitive pricing, advanced manufacturing capabilities, and a wide range of technologies. However, businesses must be cautious of quality control and intellectual property risks, ensuring collaboration with reputable suppliers. Key players like Tiertime, Shining 3D, and Farsoon Technologies contribute to the growth and development of the Chinese 3D printing industry.
How to find and select reliable 3d print titanium manufacturers in China,use google search manufacturers and suppliers
1. Start by conducting a Google search using relevant keywords such as “3D print titanium manufacturers in China” or “reliable titanium suppliers in China.”
2. Look for established manufacturers: Check for well-known and reputable manufacturers that have been in the industry for a considerable amount of time. Companies with long track records often have more experience and reliable processes.
3. Evaluate the manufacturer’s website: Visit the websites of potential manufacturers to gather relevant information about their capabilities, expertise, and certifications. Look for details about their experience in 3D printing, their production capabilities, certifications such as ISO, and any customer testimonials or case studies.
4. Verify their manufacturing facilities: Ensure that the manufacturer has advanced and well-maintained manufacturing facilities equipped with modern 3D printing technology. Facilities with state-of-the-art machinery and quality control measures are more likely to deliver reliable products.
5. Request samples and references: Contact the shortlisted manufacturers and request product samples to assess their quality firsthand. Additionally, ask for references from their previous or current clients to get real-world feedback on their performance, reliability, and consistency.
6. Consider certifications and quality control: Look for manufacturers that comply with global quality standards and have certifications such as ISO 9001. This ensures that they follow strict quality control measures, resulting in consistent and reliable prints.
7. Inquire about material sourcing: Ask the manufacturers about their sources of titanium materials. Reliable manufacturers often have established relationships with reputable material suppliers, ensuring the quality and authenticity of the materials used.
8. Communication and support: Evaluate the responsiveness and professionalism of the manufacturers during the communication process. A reliable manufacturer will be prompt, responsive, and willing to answer all your queries.
9. Compare pricing and lead time: Collect quotes from multiple manufacturers and compare their pricing and lead time. However, be cautious of extremely low prices, as it may indicate compromises in quality. Consider a balance between cost-effectiveness and reliability.
10. Secure agreements and terms: Once you have selected a reliable manufacturer, ensure to establish clear agreements regarding pricing, lead time, quality control measures, and any other relevant terms. This will help in managing expectations and ensuring a smooth collaboration.
By following these steps and being diligent in your research and evaluation, you can find and select reliable 3D print titanium manufacturers in China.
How to check 3d print titanium manufacturers website reliable,use google chrome SEOquake check if ranking in top 10M
To determine the reliability of a 3D print titanium manufacturer’s website, you can follow these steps:
1. Use Google Chrome: Start by opening up the Google Chrome browser on your computer.
2. Install SEOquake: Go to the Chrome Web Store and search for “SEOquake.” Install the SEOquake extension by clicking on the “Add to Chrome” button and following the on-screen instructions.
3. Search for the Manufacturer: Enter the name of the 3D print titanium manufacturer in the Google search bar. Hit Enter to perform the search.
4. Check Website Ranking: After the search results appear, look for the manufacturer’s website URL in the top 10 million results. This indicates that the website receives a decent amount of traffic. If the website appears within the top 10 million, it is likely a reputable and reliable manufacturer.
5. Analyze Additional Information: Click on the SEOquake extension icon in your browser’s toolbar after loading the manufacturer’s website. This will display various SEO metrics, such as the website’s Google PageRank, SEMrush rank, Alexa rank, and other valuable information. These metrics can help further assess the website’s credibility.
6. Evaluate Website Design and Content: Take a closer look at the website’s design, layout, user interface, and overall professionalism. Check if the website contains relevant and accurate information about the manufacturer, their products, certifications, contact details, and any customer reviews or testimonials.
7. Look for Social Proof: Additionally, search for the manufacturer’s presence on social media platforms, such as Facebook, Instagram, LinkedIn, or Twitter. Observe the engagement, customer interactions, and feedback to gauge their reputation among customers.
By following these steps, you can get a better idea of a 3D print titanium manufacturer’s website reliability, ensuring a more informed decision before engaging with their services or purchasing their products.
Top 10 3d print titanium manufacturers in China
China is known for its manufacturing prowess and has emerged as a major player in the global 3D printing industry. When it comes to 3D printing with titanium, several Chinese manufacturers stand out for their expertise, quality, and innovation. Here are the top 10 3D print titanium manufacturers in China:
1. Xi’an Bright Laser Technologies Co., Ltd. – Known for its high-precision metal 3D printing technology, Bright Laser provides reliable titanium additive manufacturing solutions.
2. Beijing Longyuan Automated Fabrication System Co., Ltd. – Longyuan specializes in large-scale industrial 3D printing and offers advanced titanium printing services.
3. Shanghai Union-tek Advanced Material Technology Co., Ltd. – Union-tek focuses on titanium powder production, offering high-quality titanium alloy powders for 3D printing applications.
4. Tongtai Machine & Tool Co., Ltd. – With its advanced manufacturing equipment, Tongtai offers titanium 3D printing services and has a reputation for delivering precise and intricate designs.
5. Xi’an Saite Metal Materials Development Co., Ltd. – Saite Metal Materials develops and supplies titanium alloy materials, including powder, for customers engaged in 3D printing and other industries.
6. Beijing Longyuan Aerospace Technology Co., Ltd. – Part of the Longyuan group, this company specializes in aerospace-grade 3D printing, including titanium components.
7. Xi’an Brightway International Trading Inc. – Brightway is a leading distributor of titanium materials for 3D printing, catering to the needs of various industries.
8. Hunan Farsoon High-tech Co., Ltd. – Farsoon offers a range of industrial 3D printers capable of printing with titanium materials, enabling the production of complex components.
9. Xi’an Zukun Technology Co., Ltd. – Zukun Technology provides expertise in designing and manufacturing titanium parts using advanced 3D printing technology.
10. Hengye 3D Tech Co., Ltd. – Hengye focuses on developing and producing titanium alloy powders for 3D printing, supplying materials to both domestic and international markets.
These top 10 3D print titanium manufacturers in China showcase the country’s growing expertise in titanium additive manufacturing. By delivering high-quality products and services, these companies are contributing to the advancement of 3D printing technology and its applications across various industries.
Background Research for 3d print titanium manufacturers Companies in China, use qcc.com archive.org importyeti.com
When researching 3D print titanium manufacturers in China, several platforms such as qcc.com, archive.org, and importyeti.com can be utilized. These platforms provide valuable information on companies operating in the industry. Below is a brief background research on 3D print titanium manufacturers in China, within the given word limit of 300 words.
Qcc.com is a reliable platform that provides information on Chinese enterprises. Conducting a search on the website, a number of 3D print titanium manufacturers in China can be found. The information includes company names, contact details, business scope, and registration information. This platform can help identify potential manufacturers and gather further information about their operations.
Archive.org is a digital library that allows users to access web pages and information from the past. By utilizing this platform, one can track the development and changes of companies over time. This can be particularly useful in assessing the growth, reputation, and evolution of 3D print titanium manufacturers in China.
Import Yeti is a platform that specializes in tracking Chinese exporters and provides a comprehensive database of companies. By searching for 3D print titanium manufacturers, one can obtain vital details such as company profiles, product information, shipment records, and more. This data allows for a better understanding of a manufacturer’s capabilities and export history.
Through the combination of these platforms, researchers can gather relevant information about 3D print titanium manufacturers in China. This includes company profiles, contact details, capabilities, export history, and changes over time. It is crucial to utilize these platforms to ensure the selection of a reputable and reliable manufacturer for titanium 3D printing needs.
Leveraging Trade Shows and Expos for 3d print titanium Sourcing in China
Trade shows and expos are excellent platforms for sourcing 3D print titanium products from China. These events provide unique opportunities for businesses to connect and build relationships with suppliers, manufacturers, and industry experts. With careful planning and preparation, trade shows can significantly aid in finding reliable sources for 3D print titanium sourcing in China.
One of the key benefits of attending trade shows is the ability to meet suppliers face-to-face. In-person interactions allow for better communication and understanding of the supplier’s capabilities, product quality, and manufacturing processes. This can help businesses assess whether a supplier is a suitable partner for sourcing 3D print titanium products.
Trade shows and expos also give businesses the chance to explore a wide range of options. Numerous suppliers and manufacturers showcase their products and services in one place, allowing attendees to compare and evaluate different offerings. This helps businesses identify potential suppliers that meet their specific requirements, such as product specifications, pricing, and manufacturing capabilities.
Moreover, trade shows often feature informative conferences and seminars conducted by industry experts. These sessions can provide valuable insights into the latest trends, technological advancements, and best practices in 3D printing titanium. Attendees can gain valuable knowledge about the industry, which can help them make informed decisions when selecting suppliers and negotiating contracts.
To make the most of trade shows and expos, businesses should prepare well in advance. Researching and identifying potential suppliers before the event can help focus efforts on connecting with the most suitable partners. Pre-scheduling meetings with suppliers and preparing a list of questions can facilitate productive discussions during the event.
In conclusion, leveraging trade shows and expos for 3D print titanium sourcing in China can offer businesses numerous advantages. These events provide opportunities for face-to-face interactions with suppliers, allow for product comparisons, and offer valuable industry insights. By effectively utilizing these platforms, businesses can find reliable and trustworthy suppliers for their 3D print titanium needs.
The Role of Agents and Sourcing Companies in Facilitating 3d print titanium Purchases from China
Agents and sourcing companies play a crucial role in facilitating 3D print titanium purchases from China. With their expertise and local knowledge, they navigate the complexities of the Chinese market and offer valuable assistance to buyers looking to source high-quality titanium products.
One of the main advantages of working with agents or sourcing companies is their ability to connect buyers with reliable and trustworthy suppliers in China. They have established networks and relationships with various manufacturers, ensuring a wide range of options for buyers. This saves buyers the hassle of searching for suppliers themselves and reduces the risk of dealing with unscrupulous or unreliable companies.
Agents and sourcing companies also provide important support throughout the purchasing process. They conduct due diligence on suppliers, verifying their certifications, licenses, and quality control procedures. This helps buyers ensure that they are dealing with reputable suppliers who can deliver the desired 3D print titanium products.
Furthermore, agents can help facilitate communication between buyers and suppliers. They act as a bridge to overcome language and cultural barriers, ensuring clear and effective communication. They can also assist in negotiating contracts, terms, and pricing, helping buyers secure better deals.
Another role of agents and sourcing companies is quality control. They can visit the supplier’s facilities to inspect the manufacturing process, ensuring that the titanium products meet the required standards. This helps buyers have confidence in the quality of the purchased products and avoid potential issues or discrepancies.
Finally, agents and sourcing companies provide logistical support. They coordinate the shipping and transportation of the purchased products, ensuring timely delivery to the buyer’s location. They also handle customs clearance and necessary documentation, simplifying the import process.
In summary, agents and sourcing companies play a vital role in facilitating 3D print titanium purchases from China. They connect buyers with reliable suppliers, provide support throughout the purchasing process, assist in quality control, and handle logistics. Their expertise and local knowledge greatly benefit buyers looking to source titanium products from China.
Price Cost Research for 3d print titanium manufacturers Companies in China, use temu.com and 1688.com
When conducting price cost research for 3D print titanium manufacturers in China, two popular online platforms to explore are Temu.com and 1688.com.
Temu.com is an online marketplace that specializes in connecting buyers and suppliers in the industrial manufacturing sector. It provides a platform for companies to showcase their capabilities and products. By using the search function on Temu.com and entering relevant keywords such as “3D print titanium manufacturers,” one can access a comprehensive list of suppliers in China. The platform allows users to filter search results based on factors such as location, product category, and company size. This helps to narrow down the options and find suitable manufacturers.
1688.com, on the other hand, is a leading Chinese wholesale marketplace owned by Alibaba Group. It offers a wide range of products, including industrial components and materials. By searching for “3D print titanium” on 1688.com, users can find numerous manufacturers, suppliers, and distributors in China. The platform allows users to compare prices, specifications, and certifications of different products. This information aids in making informed decisions regarding cost and quality.
When analyzing the pricing information provided on Temu.com and 1688.com, it is important to consider multiple factors. The unit price of the 3D print titanium product is crucial, but other costs such as shipping, packaging, and minimum order quantity (MOQ) should also be taken into account. Requesting quotations directly from the manufacturers is recommended, as it allows for negotiation and customization according to specific requirements.
In summary, utilizing platforms like Temu.com and 1688.com can help in conducting price cost research for 3D print titanium manufacturers in China. These platforms provide access to a wide range of suppliers, allowing for a comprehensive evaluation of prices, specifications, and other relevant details. It is important to consider factors beyond the unit price, such as additional costs and MOQ, and to engage in direct communication with manufacturers for accurate quotations and negotiations.
Shipping Cost for 3d print titanium import from China
The shipping cost for importing a 3D printed titanium product from China can vary depending on several factors. These factors include the size and weight of the product, the shipping method chosen, and the destination country.
If the 3D printed titanium product is small and lightweight, it can be shipped using international courier services such as DHL or FedEx. These services offer fast and reliable shipping, but they can be quite expensive. The cost of shipping via courier can range from $50 to $200, depending on the size and weight of the package.
For larger and heavier 3D printed titanium products, shipping through sea freight is a more cost-effective option. Sea freight is generally cheaper but takes longer compared to courier services. The cost of sea freight can vary greatly depending on the size and weight of the shipment, as well as the departure and arrival ports. On average, shipping a medium-sized package via sea freight could cost anywhere from $300 to $1000.
It is important to note that additional charges such as customs duties and taxes may apply when importing products from China. These charges vary depending on the destination country’s import regulations and tariff rates. Importers should consider these charges when calculating the total shipping cost.
To ensure the most accurate shipping cost estimate, it is recommended to contact shipping companies or freight forwarders who specialize in international logistics. These professionals can provide specific quotes based on the product’s specifications, shipping method, and destination country. Additionally, they can also assist with necessary paperwork, customs clearance, and other shipping-related services to streamline the import process.
Compare China and Other 3d print titanium Markets: Products Quality and Price,Visible and Hidden Costs
China is currently the largest and one of the most rapidly growing markets for 3D print titanium, while several other countries including the United States, Germany, and Japan also have a significant presence in this market. When comparing the products quality and price between China and these markets, there are both similarities and differences.
In terms of products quality, titanium 3D printed parts manufactured in China are known for their high standards. Chinese companies have made significant progress in improving the quality of their products, and many have obtained ISO certifications and other quality accreditations. Similarly, companies in the other markets mentioned also prioritize product quality and adhere to strict quality control measures. However, some consumers may still perceive products from countries such as the United States, Germany, or Japan to have a slightly higher quality due to their reputation for precision engineering and advanced manufacturing technologies.
In terms of price, China has traditionally been known for its cost-effective manufacturing capabilities, and this is reflected in the price of its 3D print titanium products. Chinese manufacturers can offer competitive prices due to lower labor and operating costs. On the other hand, products from the other markets mentioned may have higher price tags due to higher production costs, including labor, overheads, and research and development investment.
When it comes to visible and hidden costs, there are a few factors to consider. China’s 3D print titanium market benefits from economies of scale and a mature supply chain, resulting in lower visible costs for raw materials and production processes. However, there may be hidden costs associated with intellectual property rights and potential risks of counterfeit products. In contrast, countries such as the United States, Germany, or Japan may have higher visible costs due to higher labor and material costs, but they generally have stronger intellectual property protection measures, reducing the risk of counterfeit products and potential legal pitfalls.
In summary, while China has made significant progress in terms of product quality and price competitiveness in the 3D print titanium market, it is still seen as a cost-effective option with slightly lower visible costs. However, countries like the United States, Germany, and Japan have a reputation for higher-quality products, and their higher visible costs can be attributed to their advanced manufacturing technologies and stringent quality control measures. Additionally, these markets often provide stronger intellectual property protection, which can be a significant advantage in terms of mitigating hidden costs and potential risks.
Understanding Pricing and Payment Terms for 3d print titanium: A Comparative Guide to Get the Best Deal
When it comes to 3D printing with titanium, understanding pricing and payment terms is essential to ensure you get the best deal. Titanium is a highly sought-after material due to its strength, durability, and lightweight properties. However, it is also a relatively expensive material compared to other options. To optimize your cost savings, consider the following comparative guide.
Firstly, it’s crucial to compare pricing across different 3D printing service providers. Request quotes from various companies and examine their pricing structures. Some companies charge based on the weight of the titanium used, while others follow an hourly rate or a combination of both. By comparing these pricing models, you can determine which option best suits your project’s requirements and budget.
Secondly, consider the additional costs associated with 3D printing titanium. These can include pre-processing costs, such as design optimization and file preparation, as well as post-processing costs for finishing touches like polishing or heat treating. Ensure that you account for these additional charges when comparing prices across different providers.
In addition to pricing, understanding the payment terms is essential. Some companies may require full payment upfront, while others offer flexibility with payment options. Evaluate your financial situation and project timeline to determine which payment terms are most favorable for you. Additionally, inquire about any potential discounts or bulk order benefits that may be available, as this could significantly impact the overall pricing and payment terms.
Lastly, consider the quality and reputation of the 3D printing service provider. While cost savings are important, it should not come at the expense of quality. Research customer reviews, ask for sample prints, and investigate the provider’s experience in printing with titanium. Opting for a reputable and experienced company ensures a higher likelihood of receiving a superior end product.
In conclusion, to obtain the best deal when 3D printing with titanium, it is imperative to understand pricing structures, additional costs, payment terms, and the reputation of the service provider. By comparing quotes and considering these factors, you can make an informed decision that strikes the right balance between cost-efficiency and high-quality results.
Chinese Regulations and Industry Standards Certifications for 3d print titanium,Import Regulations and Customs for 3d print titanium from China
Chinese Regulations and Industry Standards Certifications for 3D Printed Titanium:
In China, the regulations and industry standards certifications for 3D printed titanium are governed by several key authorities. These regulations ensure the product’s quality, safety, and compliance with industry standards.
The primary authority responsible for regulating 3D printing in China is the National Standards Committee. They establish and enforce standards for manufacturing processes, product quality, and safety. The standards cover aspects such as material composition, mechanical properties, surface finish, and dimensional accuracy.
Additionally, the China Food and Drug Administration (CFDA) oversees the regulations for medical-grade 3D printed titanium products. CFDA certification is required for any 3D printed titanium medical devices to ensure their safety and efficacy.
Other important industry standards certifications for 3D printed titanium in China include ISO 13485 for medical devices, ISO 9001 for general quality management systems, and ISO 14001 for environmental management systems.
Import Regulations and Customs for 3D Printed Titanium from China:
When importing 3D printed titanium from China, it is crucial to comply with the country’s import regulations and customs procedures. These ensure smooth and legal entry of the goods into the importing country.
Firstly, the importer should check whether any import restrictions or special permits are required for 3D printed titanium. Some countries may have specific regulations regarding the import of certain materials, especially in medical, aerospace, or defense-related sectors.
Customs documentation is also essential. The importer must provide accurate and complete information regarding the imported products, including detailed descriptions, quantities, and values. This information is crucial for customs clearance and valuation purposes.
Import duties and taxes are another consideration. The importer should be aware of the applicable tariff rates and any additional taxes or fees imposed on 3D printed titanium imports. These can vary depending on the nature of the product and the importing country.
Finally, compliance with customs authorities’ requirements is critical. The importer should ensure that the 3D printed titanium meets all necessary quality and safety standards and has the required certifications. Non-compliance could lead to delays or even rejection at the customs border.
In conclusion, understanding the Chinese regulations and industry standards certifications for 3D printed titanium, as well as complying with import regulations and customs procedures, is vital for importing these products from China. Failing to adhere to these requirements could lead to legal issues, delays, or the rejection of imported goods.
Sustainability and Environmental Considerations in 3d print titanium Manufacturing
Sustainability and environmental considerations are essential in 3D printing titanium manufacturing processes due to their potential impact on resource consumption, waste generation, and greenhouse gas emissions. While titanium additive manufacturing offers various advantages, including reduced material waste and design flexibility, it is crucial to assess and mitigate its potential environmental consequences.
One key aspect of sustainability in 3D print titanium manufacturing is resource efficiency. Titanium is a valuable and relatively scarce material, so optimizing its usage is critical to minimize waste and ensure long-term availability. Manufacturers can employ design-for-additive-manufacturing approaches to reduce the amount of titanium required, optimize part geometries, and minimize support material usage.
Another environmental aspect is the energy consumption associated with 3D printing processes. While additive manufacturing inherently uses less energy than traditional subtractive methods, involving high-powered lasers or electron beams can still result in significant energy requirements. Therefore, implementing energy-efficient technologies, using renewable energy sources for processing, and maximizing equipment utilization can help minimize the environmental impact.
Furthermore, the disposal of waste generated during 3D print titanium manufacturing must be considered. Leftover titanium powder, failed prints, and post-processing chemicals can contribute to waste if not handled appropriately. Implementing comprehensive recycling programs, such as powder recovery systems and reclaiming techniques, can reduce waste generation and support circular economy principles.
In terms of greenhouse gas emissions, the energy-intensive nature of 3D printing processes can result in carbon dioxide and other emissions. Choosing low-emission energy sources and using energy-efficient machinery can help mitigate these emissions. Additionally, adopting lightweight designs made possible by additive manufacturing can reduce the overall carbon footprint of parts, especially in industries like aerospace and automotive where weight reduction can lead to fuel savings during operation.
In conclusion, sustainability and environmental considerations are crucial when engaging in 3D print titanium manufacturing. Optimizing resource efficiency, minimizing waste generation, reducing energy consumption, and mitigating greenhouse gas emissions are vital to ensure the long-term viability of this manufacturing process and its positive contribution to a sustainable future.
List The Evolution history of “3d print titanium”
The evolution of 3D printing using titanium can be traced back to the early 2000s when researchers and engineers started experimenting with the concept of using this advanced material in additive manufacturing. At that time, the technology was still in its infancy, and the use of titanium presented numerous challenges and limitations.
In the initial stages, the main focus was on improving the 3D printing process itself to achieve higher precision and resolution. Researchers worked on developing specialized printers and software that could handle the complex properties of titanium. They had to tackle issues such as the high melting point of the metal and its tendency to oxidize, which affected the structural integrity of the printed objects.
Significant breakthroughs came in the mid-2000s when advancements in laser technology allowed for more precise and efficient melting of titanium powders. Laser beam melting (LBM) and electron beam melting (EBM) emerged as the dominant techniques for 3D printing titanium. These techniques utilized lasers or electron beams to selectively melt and fuse titanium powders layer by layer to form solid objects.
As the technology progressed, researchers began to explore the potential applications of 3D printed titanium. Initially, it found use primarily in the aerospace and medical industries due to its excellent strength-to-weight ratio and biocompatibility. Complex aerospace components like turbine blades and structural parts could be manufactured with greater design freedom and reduced material waste. In the medical field, titanium implants and prosthetics could be custom-made for patients, improving their fit and functionality.
Over time, advancements in 3D printer capabilities and materials development expanded the range of applications for 3D printed titanium. Industries such as automotive, defense, and architecture started utilizing this technology to create lightweight yet robust components. The ability to print intricate designs and complex geometries opened up new possibilities for product development and optimization.
In recent years, 3D printed titanium has become more accessible, thanks to improved affordability and scalability of the technology. As a result, it has gained popularity among small businesses, designers, and even hobbyists. Today, 3D printed titanium is being used in various industries, pushing the boundaries of innovation and fabrication.
In conclusion, the evolution of 3D printing with titanium has come a long way from its early stages of development. By overcoming technical challenges and exploring its potential applications, the technology has revolutionized manufacturing across diverse industries, paving the way for a new era of design and production possibilities.
The Evolution and Market Trends in 3d print titanium Industry
The 3D printing of titanium has witnessed significant evolution and market trends over the years. Titanium, a lightweight and strong metal with excellent corrosion resistance, has become increasingly popular in various industries, including aerospace, healthcare, automotive, and consumer goods.
Initially, 3D printing of titanium faced challenges due to the metal’s high melting point and reactive nature. However, advancements in additive manufacturing technologies, such as selective laser melting (SLM) and electron beam melting (EBM), have greatly improved the feasibility and quality of 3D printed titanium components. These technologies allow for precise control over the printing process, resulting in complex geometries and high strength-to-weight ratio structures.
The market for 3D printed titanium has been expanding rapidly. In the aerospace industry, companies like Boeing and Airbus are increasingly adopting titanium 3D printing to reduce weight and improve fuel efficiency in aircraft components. Additionally, the healthcare sector has embraced this technique to fabricate customized medical implants, prosthetics, and dental applications. The automotive industry also shows potential, as titanium 3D printing can enable the production of lightweight and high-performance automotive parts.
One of the key market trends in the 3D print titanium industry is the growing demand for sustainable and eco-friendly manufacturing. Titanium’s lightweight properties reduce fuel consumption and emissions in transportation applications. Moreover, 3D printing eliminates waste by using only the required amount of material, making it a sustainable alternative to traditional subtractive manufacturing processes.
Another trend is the increasing accessibility of 3D printing technology, resulting in a broader range of applications and more affordable production costs. This accessibility, combined with ongoing research and development efforts, has accelerated innovation in the design and manufacturing of titanium components.
In summary, the evolution of 3D print titanium has overcome initial challenges to emerge as a viable solution for various industries. The market trends indicate a growing demand for lightweight, high-strength, and sustainable components. As technology continues to advance, the 3D print titanium industry is poised for further growth and innovation.
Custom Private Labeling and Branding Opportunities with Chinese 3d print titanium Manufacturers
Chinese manufacturers of 3D print titanium offer excellent custom private labeling and branding opportunities for businesses. With their advanced technology and expertise, these manufacturers can produce high-quality titanium products according to the specific requirements of the brand.
Custom private labeling allows businesses to have their logo, brand name, and other desired branding elements on the titanium products. This enhances brand visibility and recognition, creating a professional and cohesive image for the business. Furthermore, custom labeling helps prevent counterfeiting and builds trust with customers.
Branding opportunities are abundant with Chinese 3D print titanium manufacturers as they offer a range of customization options. Businesses can choose from various product designs, finishes, and even create unique shapes that align with their brand identity. Manufacturers can work closely with businesses to customize the product to meet specific requirements, ensuring that it reflects the brand’s vision and values.
Chinese 3D print titanium manufacturers excel in quality control, ensuring that the branded products meet or exceed industry standards. They employ strict quality assurance processes and utilize advanced machinery to deliver products of the highest quality. This quality control extends to the private labeling and branding process, ensuring that businesses receive products that are consistent, durable, and visually appealing.
Collaborating with Chinese manufacturers also offers cost advantages. Due to their expertise in 3D printing technology, these manufacturers can optimize production processes, resulting in cost savings that can be passed on to the businesses. This makes custom private labeling and branding more affordable, allowing businesses to invest in enhancing their product’s identity without exceeding their budget.
To conclude, Chinese 3D print titanium manufacturers present a plethora of custom private labeling and branding opportunities for businesses. With their advanced technology, commitment to quality, and cost advantages, businesses can confidently partner with these manufacturers to create branded titanium products that are unique, visually appealing, and of the highest quality.
Tips for Procurement and Considerations when Purchasing 3d print titanium
When it comes to procuring and purchasing 3D printed titanium, there are several considerations to keep in mind to ensure a successful and cost-effective process. These tips can help guide you through the procurement process:
1. Material Specifications: Understand the specific requirements for the titanium material you need. Consider factors such as grade, strength, corrosion resistance, and desired surface finish to ensure the material meets your intended application.
2. Supplier Evaluation: Research and evaluate potential suppliers for 3D printed titanium. Look for suppliers with a good track record, experience in 3D printing titanium, and advanced manufacturing capabilities. Consider asking for samples or prototypes to assess their quality.
3. Quality Control: Ensure that the supplier follows strict quality control measures. Ask about certifications, quality standards, and inspection processes that they have in place to maintain consistent material properties and dimensional accuracy.
4. Cost and Lead Time: Obtain multiple quotes from different suppliers to compare their prices and lead times. Consider the supplier’s proximity to your location or target market, as this can affect shipping costs and delivery time.
5. Design Optimization: Collaborate with the supplier to optimize your 3D design for titanium printing. This can help reduce material waste, improve part performance, and minimize manufacturing challenges.
6. Intellectual Property Protection: Ensure that the supplier has protocols in place to safeguard your intellectual property. Discuss confidentiality agreements or non-disclosure agreements to protect your designs and proprietary information.
7. Post-Processing Options: Inquire about the availability of post-processing options such as heat treatment, surface finishing, or machining. Some applications may require additional processing to meet specific requirements.
8. Scalability and Capacity: Consider the supplier’s production capacity, inventory availability, and ability to scale up production if needed. This is important for long-term partnerships and potential future orders.
9. Regulatory Compliance: Ensure that the supplier follows relevant regulations and standards for the production of 3D printed titanium parts. This includes compliance with safety standards, material traceability, and any industry-specific certifications.
10. Collaboration and Support: Establish good communication channels with the supplier to facilitate a smooth procurement process. Regular communication can help address any concerns, update delivery dates, and collaborate on design changes if required.
In summary, successful procurement of 3D printed titanium involves evaluating suppliers for quality, cost, and lead time; optimizing designs for additive manufacturing; considering post-processing options; and ensuring regulatory compliance and intellectual property protection.
FAQs on Sourcing and Manufacturing 3d print titanium in China
Q: Can I source and manufacture 3D printed titanium in China?
A: Yes, China offers sourcing and manufacturing options for 3D printed titanium products. The country has a strong and well-established manufacturing industry and is known for its cost-effective production capabilities.
Q: How can I find reliable suppliers for 3D printed titanium in China?
A: It is recommended to do thorough research and due diligence to find reliable suppliers. Utilize online platforms such as Alibaba, Global Sources, and Made-in-China, which provide access to a wide range of suppliers. Additionally, attending trade shows and exhibitions like the Canton Fair can offer opportunities to meet potential suppliers face-to-face.
Q: Are there any specific challenges associated with sourcing 3D printed titanium in China?
A: While China offers numerous advantages for sourcing and manufacturing, there may be some challenges to consider. Quality control can be a concern, so it is crucial to conduct proper supplier vetting and inspections. Language and communication barriers can also arise, but several suppliers have English-speaking sales representatives to assist.
Q: What are the costs involved in manufacturing 3D printed titanium in China?
A: Manufacturing costs in China can be relatively lower compared to many other countries. However, the actual cost will depend on various factors, including the complexity of the design, the quantity ordered, and the expertise required. Obtaining quotes from multiple suppliers and comparing them will help in evaluating the costs.
Q: Are there any specific regulations or certifications for manufacturing 3D printed titanium in China?
A: China has its own regulatory bodies and standards for manufacturing processes and products. It is essential to ensure that the chosen supplier meets the necessary certifications and standards, such as ISO 9001 for quality management. Additionally, complying with export regulations and intellectual property rights protection is crucial.
Q: What is the typical lead time for manufacturing 3D printed titanium in China?
A: The lead time can vary based on the complexity and quantity of the order, as well as the availability of raw materials. However, Chinese manufacturers generally have efficient production capabilities, and lead times can range from a few weeks to a few months.
Q: Can I customize the design and dimensions for 3D printed titanium products in China?
A: Yes, Chinese manufacturers typically offer customization options for 3D printed titanium products. They can work from provided designs or help develop custom designs based on specific requirements. Collaborating and communicating the desired design specifications with the chosen supplier is vital.
In summary, sourcing and manufacturing 3D printed titanium in China is feasible and cost-effective. However, careful supplier selection, quality control, and adherence to relevant regulations are crucial for a successful business engagement.
Why contact sourcifychina.com get free quota from reliable 3d print titanium suppliers?
Sourcifychina.com may offer free quota from reliable 3D print titanium suppliers for several reasons. First, by providing a free quota, Sourcifychina.com aims to attract potential customers and build trust with them. Offering a free quota allows businesses to assess the capabilities and pricing of different suppliers without any financial commitment.
Second, by partnering with reliable 3D print titanium suppliers, Sourcifychina.com can ensure that customers receive high-quality products. Working with trustworthy suppliers helps to maintain the reputation of Sourcifychina.com as a reliable sourcing platform.
Third, by offering a free quota, Sourcifychina.com encourages businesses to explore 3D print titanium as a viable option. Titanium is a versatile metal with numerous applications, and showcasing its potential through a free quota can pique the interest of businesses that may not have considered it before.
Furthermore, Sourcifychina.com may have established relationships with these suppliers, allowing them to negotiate favorable pricing. By passing on these benefits to customers through free quotas, Sourcifychina.com aims to attract more potential buyers and generate more business for the suppliers.
Overall, offering a free quota from reliable 3D print titanium suppliers allows Sourcifychina.com to attract and build trust with customers, promote the use of titanium, and benefit from their partnership with reliable suppliers.