Introduce about 3d printed titanium guide,Qulity,Cost,Supplier,Certification,Market,Tips,FAQ
Introduction:
3D printing technology has revolutionized various industries, and one such application is the production of 3D printed titanium guides. These guides play a vital role in various fields such as medical surgeries, engineering, and manufacturing. This introduction will provide insights into the quality, cost, suppliers, certifications, market demand, tips, frequently asked questions (FAQs), and more.
Quality:
3D printed titanium guides offer exceptional quality due to their precise manufacturing process. The use of titanium ensures high strength, durability, and biocompatibility. These guides are designed and fabricated using advanced computer-aided design (CAD) software, resulting in accurate and customized solutions for complex applications.
Cost:
Compared to traditional manufacturing methods, 3D printed titanium guides may initially seem more expensive. However, the cost-effectiveness lies in the reduced material waste, decreased production time, and the ability to produce complex geometries. Although initial costs may be higher, the overall costs can often be justified by the increased efficiency and improved outcomes.
Suppliers:
Several reputable suppliers specialize in 3D printed titanium guides. It is essential to choose a supplier with expertise in additive manufacturing, as they can ensure quality production, adhere to industry standards, and offer design assistance. Researching suppliers’ reputation, reviews, and certifications can help in selecting the most suitable supplier.
Certification:
When sourcing 3D printed titanium guides, certification is crucial. Look for suppliers who adhere to international standards such as ISO 13485 for medical applications. This certification ensures that the manufacturing processes and materials meet stringent quality requirements, providing confidence in the product’s safety and efficacy.
Market:
The demand for 3D printed titanium guides is escalating across various sectors. In healthcare, these guides aid in precise surgical interventions, patient-specific implants, and prosthetics. The aerospace and automotive industries benefit from lightweight, high-strength components, while engineering and manufacturing sectors utilize them for custom jigs, fixtures, and tooling.
Tips:
1. Collaborate with an experienced design team to ensure optimal geometry and functionality.
2. Communicate specific requirements and performance expectations to the supplier.
3. Request samples, prototypes, or test prints to evaluate quality before placing bulk orders.
FAQs:
Q: Can 3D printed titanium guides be sterilized?
A: Yes, titanium is highly resistant to corrosion and can withstand various sterilization methods.
Q: Can these guides be post-processed?
A: Yes, post-processing techniques like machining, polishing, or coating can be applied to enhance surface finish or add specific functionalities.
Q: Are these guides reusable?
A: It depends on the specific application and sterilization requirements. Consult with the supplier to determine reusability feasibility.
In conclusion, 3D printed titanium guides offer exceptional quality and unique customization opportunities. Though initially costlier, the advantages of reduced waste and increased efficiency make them a competitive option. It is important to choose certified suppliers and collaborate closely throughout the design and production process to ensure desired outcomes.
Types of 3d printed titanium
There are several types of 3D printed titanium alloys commonly used in various industries. These alloys possess unique properties that make them suitable for specific applications. Some of the most notable types include:
1. Ti6Al4V (also known as Grade 5 titanium): This is the most widely used titanium alloy due to its excellent strength-to-weight ratio, corrosion resistance, and biocompatibility. It is commonly used in aerospace, automotive, and medical industries for producing complex components.
2. Ti6Al2Sn4Zr2Mo: This alloy exhibits improved high-temperature tensile strength and creep resistance compared to Ti6Al4V. It is commonly used for components in aircraft engines, gas turbines, and oil and gas applications.
3. Ti6Al7Nb: This alloy is characterized by its high temperature resistance and excellent mechanical properties, including fatigue resistance. It is widely used in the medical industry for manufacturing implants such as hip and knee replacements.
4. Ti6Al2Sn4Zr6Mo: This alloy possesses extremely high strength and excellent corrosion resistance. It finds applications in aircraft structures, landing gear, and parts subjected to high stress and corrosive environments.
5. Ti5553: This alloy has a unique combination of high strength, lightweight, and excellent corrosion resistance. It is commonly utilized in aerospace applications, including aircraft structural components and landing gears.
6. Beta titanium alloys: These alloys, such as Ti15-3 and Ti15-3-3-3, display superior fatigue properties and high strength-to-weight ratios. They are used in automotive and sporting goods industries for applications like racing car components, bicycle frames, and golf clubs.
7. Porous titanium: 3D printing allows the creation of porous titanium structures with interconnected pores. These structures promote bone ingrowth and are used extensively in medical implants and orthopedic surgeries.
These are just a few examples of the wide range of 3D printed titanium alloys available. Each alloy offers unique characteristics and benefits that can be tailored to meet specific application requirements. The versatility of 3D printing technology enables the production of complex geometries with these alloys, unlocking new possibilities in various industries.

Pros and Cons of Using 3d printed titanium
One of the pros of using 3D printed titanium is its strength-to-weight ratio. Titanium is already known for its high strength and low density, and 3D printing technology allows for the creation of complex structures with optimized strength. This makes 3D printed titanium ideal for applications that require lightweight yet strong parts, such as aerospace components or biomedical implants.
Another advantage is the design flexibility provided by 3D printing. Traditional manufacturing methods often have limitations on the complexity of shapes that can be produced, but 3D printing allows for the creation of intricate geometries that were previously impossible. This capability enables engineers to design highly efficient and customized parts with improved performance.
Cost-effectiveness is also a potential benefit. While the initial investment in 3D printing equipment and materials can be significant, the ability to produce near-net-shape components reduces the need for additional machining or processing steps. This can result in cost savings, especially for low-volume production or prototyping.
However, there are also some drawbacks to using 3D printed titanium. One major concern is the quality control of 3D printed parts. The process involves layer-by-layer deposition of material, which can introduce defects such as voids or porosity. Ensuring the structural integrity and reliability of 3D printed titanium parts requires rigorous testing and quality assurance measures.
Additionally, the speed of production can be a limitation. 3D printing, especially for metals, can be a time-consuming process. The build time for complex or large-scale components can be significant, which may not be ideal for applications that require rapid production or high volume output.
Furthermore, the high cost of titanium itself is a barrier to its widespread use in 3D printing. Titanium is an expensive material, and the additional cost of acquiring and processing titanium powders suitable for 3D printing can further increase the overall production cost.
In summary, the pros of using 3D printed titanium include its excellent strength-to-weight ratio, design flexibility, and potential cost-effectiveness. However, concerns regarding quality control, slow production speed, and the high material cost are important considerations that may limit its applicability.
3d printed titanium Reference Specifications (varies for different product)
3D printing technology has revolutionized the manufacturing industry by enabling the production of complex and customized components with unmatched precision and efficiency. Among the various materials used in 3D printing, titanium stands out for its exceptional strength-to-weight ratio, corrosion resistance, and biocompatibility, making it a popular choice for a wide range of applications.
When it comes to 3D printed titanium, there are certain reference specifications that vary depending on the specific product and its intended use. Here are some key considerations:
1. Material: Titanium alloys, such as Ti6Al4V (Grade 5), are commonly used in 3D printing due to their favorable properties. These alloys consist of approximately 90% titanium, 6% aluminum, and 4% vanadium. The chemical composition may differ slightly based on the specific alloy used, but they generally offer high strength and good weldability.
2. Density: The density of 3D printed titanium components can vary depending on the printing process and parameters used. Typically, it ranges from 4.4 to 4.6 g/cm³, which is significantly lower than traditional manufacturing methods.
3. Mechanical properties: 3D printed titanium exhibits excellent mechanical properties, including high tensile strength, fatigue resistance, and toughness. The exact values depend on the specific alloy, part orientation during printing, and post-processing treatments. Generally, the minimum tensile strength of 3D printed titanium is around 950 MPa, with elongation values of approximately 10%-15%.
4. Surface finish: 3D printed titanium components usually have a rough surface finish directly after printing. However, various post-processing techniques like polishing and machining can be employed to achieve the desired smoothness, tolerances, and surface quality.
5. Dimensional accuracy: The dimensional accuracy of 3D printed titanium parts is affected by factors such as layer thickness, printer calibration, and thermal management. Typically, the achievable accuracy ranges from ± 0.1 mm to ± 0.2 mm, although tighter tolerances can be achieved with advanced printing techniques.
6. Heat treatment: Heat treatment processes, such as stress relief annealing and solution heat treatment, can be applied to 3D printed titanium to enhance its material properties and reduce residual stresses.
It should be noted that these reference specifications are not exhaustive and may differ based on the specific requirements of the application. Designers and manufacturers must work closely to determine the optimal specifications that balance structural integrity, functionality, and cost-effectiveness.
In conclusion, 3D printed titanium offers immense potential for the production of high-performance components across various industries. By understanding and optimizing the reference specifications, manufacturers can harness the benefits of this advanced material to create innovative and customized products.
Applications of 3d printed titanium
3D printed titanium has various applications across industries due to its unique properties, including high strength-to-weight ratio, corrosion resistance, and biocompatibility. Here are some notable applications of 3D printed titanium:
1. Aerospace Industry: Titanium’s strength and lightweight nature make it an ideal material for aerospace components. 3D printing allows the creation of complex geometries that are difficult to manufacture using traditional techniques. This includes turbine blades, engine components, brackets, and structural parts.
2. Medical Devices: Titanium’s biocompatibility and ability to fuse with bone make it a preferred material for orthopedic implants. 3D printing enables the production of patient-specific implants, such as hip and knee replacements, to ensure proper fit and reduce surgical time. Additionally, 3D printed titanium is used for dental implants, prosthetics, and surgical tools.
3. Automotive Industry: Titanium’s exceptional strength and weight reduction potential are advantageous in the automotive sector. 3D printed titanium allows for the creation of lightweight and durable components, including engine parts, exhaust systems, suspension components, and brackets, which enhance fuel efficiency and overall vehicle performance.
4. Defense and Military: 3D printed titanium finds applications in the defense sector, primarily for manufacturing lightweight armor and ballistic protection with complex designs. This provides better protection while reducing the weight burden for soldiers.
5. Energy Sector: Titanium’s corrosion resistance makes it suitable for applications in the energy sector. 3D printed titanium is used to produce components for power plants, including heat exchangers, valves, and pipes, as it can withstand high temperatures and aggressive environments.
6. Consumer Goods: 3D printed titanium is increasingly utilized in the production of high-end consumer goods like jewelry, watches, eyeglasses, and accessories. Its unique properties and ability to create intricate designs attract consumers seeking distinctive and durable products.
7. Industrial Equipment: Titanium’s strength and resistance to corrosion make it valuable in industrial settings. 3D printed titanium is utilized in machinery and equipment, such as aerospace tooling, jigs, fixtures, and molds, to enhance longevity, reduce costs, and improve efficiency.
The applications of 3D printed titanium continue to grow as advancements in additive manufacturing techniques and materials allow for increased complexity, customization, and reduced production costs. This promising technology has the potential to revolutionize various industries with its unique combination of properties and design freedom.
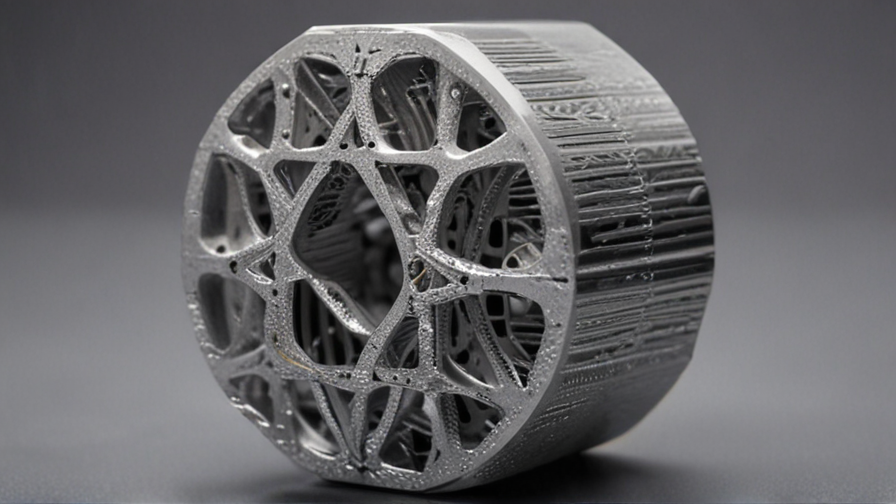
The Work Process and how to use 3d printed titanium
The work process for using 3D printed titanium involves several key steps. First, a digital 3D model of the desired object or part is created using computer-aided design (CAD) software. This model is then sliced into thin layers using slicing software, which generates the necessary instructions for the 3D printer.
Next, a layer-by-layer additive manufacturing technique called direct metal laser sintering (DMLS) is used to print the object. In this process, a high-powered laser selectively fuses titanium powder particles together based on the instructions from the slicing software. The printer’s build platform moves down after each layer is printed, allowing for the successive layers to be built upon each other until the entire object is formed.
Once the printing process is complete, the printed titanium part undergoes a post-processing stage. This typically involves removing support structures, which were added during the printing process to support overhanging sections of the design. This can be done manually or with the help of machining or chemical processes.
After the support structures are removed, the part may undergo additional treatments to improve its mechanical properties. These treatments can include stress relieving, heat treatment, or surface finishing techniques like sandblasting or polishing.
Finally, the printed titanium part is inspected for defects and quality assurance before being ready for use in various applications. This can involve visual inspection, dimensional measurements, or non-destructive testing methods like ultrasound or X-ray.
3D printed titanium offers numerous advantages, such as the ability to create complex and lightweight designs, reduced material waste, and faster production times. It finds applications in industries such as aerospace, automotive, medical, and even consumer goods.
In conclusion, the work process of using 3D printed titanium involves creating a digital model, slicing it into layers, 3D printing the layers using DMLS technology, post-processing the printed part, inspecting for quality, and using it in various applications. This innovative approach allows for the creation of intricate designs with enhanced performance characteristics, making it a promising technology for the future.
Quality Testing Methods for 3d printed titanium and how to control the quality
Quality testing methods for 3D printed titanium components are essential to ensure that the printed parts meet the desired specifications and possess the required mechanical properties. Here are some commonly used quality testing methods for 3D printed titanium:
1. Visual Inspection: This is the simplest and most basic test, which involves visually examining the printed part for defects such as cracks, warping, or surface imperfections.
2. Dimensional Analysis: Using precision measuring tools, the printed parts are checked against the CAD model to verify if they meet the specified dimensions within the acceptable tolerance limits.
3. Density Measurement: This method involves determining the density of the 3D printed part by comparing it to the theoretical density. Any deviation from the expected value can indicate voids or porosity within the printed part.
4. Tensile Testing: Tensile strength is a critical mechanical property for evaluating the strength of 3D printed titanium components. Tensile tests are performed by applying a controlled force to the printed part until it fractures, allowing the determination of ultimate tensile strength, yield strength, and elongation at break.
5. Microscopic Analysis: This method involves using a microscope to examine the microstructure of the 3D printed titanium part. It helps identify any structural defects, such as lack of fusion, voids, or uneven grain structure.
To control the quality of 3D printed titanium components, the following measures should be considered:
1. Material Selection: Ensure the use of high-quality titanium powders specifically designed for 3D printing, which meet relevant industry standards.
2. Printer Calibration: Regularly calibrate the 3D printer to maintain accuracy and precision during the printing process.
3. Process Optimization: Optimize the printing parameters, such as print speed, temperature, and layer thickness, to obtain the desired part quality and mechanical properties.
4. Post-Processing: Employ appropriate post-processing techniques like heat treatment or surface finishing to enhance the mechanical properties and surface quality of the printed components.
5. Quality Control Checks: Implement rigorous quality control checks at various stages of the production process, including raw material inspection, in-process monitoring, and final inspection.
By utilizing these testing methods and implementing stringent quality control measures, the quality of 3D printed titanium components can be effectively controlled to meet the desired specifications and industry standards.
3d printed titanium Sample Policy and Post-Purchase Considerations for 3d printed titanium from China
Sample Policy:
When ordering 3D printed titanium products from China, it is important to establish a clear sample policy to ensure customer satisfaction. The following guidelines can be considered:
1. Sample Request: Customers should be encouraged to request product samples before placing bulk orders. This allows them to inspect the quality, accuracy, and finish of the 3D printed titanium parts.
2. Free Sample: Consider offering free samples to build trust with potential customers. This demonstrates confidence in the product’s quality and gives them an opportunity to assess its suitability for their needs.
3. Sample Cost: If offering free samples is not feasible, a nominal fee can be charged to cover the manufacturing and shipping costs. This can be refunded or adjusted against the final order, creating an incentive for customers to proceed with their purchase.
4. Sample Options: Provide a diverse range of sample options, such as different designs, finishes, or tolerances, depending on the product’s complexity. This allows customers to choose the most appropriate sample for their requirements.
5. Production Lead Time: Clearly communicate the lead time required for sample production. This ensures that customers have realistic expectations and can factor in this duration when making decisions and placing orders.
Post-Purchase Considerations:
After purchasing 3D printed titanium products from China, customers should keep the following considerations in mind:
1. Quality Assurance: Thoroughly inspect the received products to ensure they meet the required quality standards. Verify that the 3D printed titanium parts match the approved sample in terms of accuracy, finish, and overall appearance.
2. Testing and Validation: Conduct necessary tests and validation procedures to determine if the 3D printed titanium parts perform as intended. This step is vital, especially for applications involving critical performance or safety requirements.
3. Communication Channel: Maintain an open communication channel with the Chinese supplier for any post-purchase inquiries, clarifications, or assistance. Promptly address any concerns or issues related to the 3D printed titanium products.
4. Feedback: Provide feedback to the supplier about the product’s performance, quality, or any suggestions for improvement. This fosters a collaborative relationship and encourages the supplier to constantly enhance their offerings.
5. Future Orders: Evaluate the supplier’s reliability, responsiveness, and overall performance. This assessment will help determine whether to continue sourcing 3D printed titanium products from this supplier or explore alternative options in the future.
By implementing a well-defined sample policy and considering post-purchase factors, customers can optimize their experience when ordering 3D printed titanium products from China while ensuring quality and customer satisfaction.
Sourcing 3d printed titanium from China: Opportunities, Risks, and Key Players
Sourcing 3D printed titanium from China offers several opportunities for businesses. Firstly, China is one of the leading manufacturers of 3D printing equipment, materials, and technology. This means that companies can find a wide range of suppliers and service providers with expertise in 3D printing titanium. Additionally, China has a strong manufacturing base, enabling cost-effective production of titanium products using 3D printing technology.
However, there are certain risks associated with sourcing 3D printed titanium from China. Quality control can be a concern, as not all Chinese manufacturers may meet international standards. It is crucial for businesses to thoroughly vet and select reputable suppliers with appropriate certifications and a proven track record. Intellectual property protection can also be a risk, as some Chinese manufacturers have been accused of copyright infringement and counterfeiting. Companies should ensure they have robust agreements and legal protections in place to safeguard their designs and intellectual property.
Several key players in the Chinese market provide 3D printed titanium products and services. Winbo 3D Printers, a leading Chinese manufacturer, offers a range of industrial-grade 3D printers capable of printing with titanium materials. Additionally, Huaxia 3D, a Chinese metal 3D printing service provider, specializes in titanium parts for various industries such as aerospace and medical. Other notable players include Shining 3D, Farsoon Technologies, and UnionTech.
In conclusion, sourcing 3D printed titanium from China presents opportunities for businesses due to the country’s manufacturing expertise and cost-effective production capabilities. However, it is essential to assess the risks related to quality control and intellectual property protection. By carefully selecting reputable suppliers and implementing robust legal safeguards, businesses can benefit from the advantages that Chinese 3D printing titanium market offers.
How to find and select reliable 3d printed titanium manufacturers in China,use google search manufacturers and suppliers
Finding reliable 3D printed titanium manufacturers in China can be done using Google search by following these steps:
1. Start by searching for “3D printed titanium manufacturers in China” or similar keywords. Make sure to include specific phrases that indicate titanium manufacturing expertise.
2. Evaluate the first few search results, as they are usually the most relevant and reputable manufacturers. Look for manufacturers that have a well-designed, professional website with detailed information about their services and products.
3. Check if the manufacturer has certifications or partnerships that demonstrate their commitment to quality and reliability. Look for certifications such as ISO 9001, ISO 13485 (for medical devices), or AS9100 (for aerospace).
4. Read through their company profiles, about us section, and any available customer reviews or testimonials. This will give you an idea of their experience, capabilities, and reputation.
5. Contact the shortlisted manufacturers via email or phone to inquire about their services, production processes, turnaround time, pricing, and any other specific requirements you may have. Observe their responsiveness, willingness to address your queries, and professionalism in their communication.
6. Request samples or a portfolio of their previous work, particularly if you want to ensure their quality and capabilities in 3D printed titanium manufacturing. Check if they have successfully completed projects similar to yours.
7. If possible, visit the manufacturer’s facility or schedule a video call to get a better understanding of their production capabilities, equipment, and quality control processes. This will help you assess whether they can meet your specific requirements.
8. Ensure that the chosen manufacturer offers clear terms and conditions, including price, delivery, payment terms, and any specific guarantees or warranties.
9. Obtain quotations from multiple manufacturers to compare pricing, lead times, and other factors that are crucial for your project’s success.
10. Finally, make an informed decision by considering factors such as reputation, experience, capabilities, responsiveness, pricing, and communication.
By following these steps, you can identify and select reliable 3D printed titanium manufacturers in China to meet your specific needs.
How to check 3d printed titanium manufacturers website reliable,use google chrome SEOquake check if ranking in top 10M
When assessing the reliability of a 3D printed titanium manufacturer’s website, here are a few steps using Google Chrome and the SEOquake extension:
1. Install the SEOquake extension: Visit the Chrome Web Store and install the SEOquake extension for your Google Chrome browser. This extension provides various SEO metrics and insights for websites you visit.
2. Access the manufacturer’s website: Open Google Chrome and navigate to the website of the 3D printed titanium manufacturer you wish to evaluate.
3. Activate SEOquake: Once the website loads, click on the SEOquake extension icon in your browser’s toolbar to activate it. This will enable you to analyze the website’s metrics.
4. Check if the website ranks in the top 10M: With SEOquake active, scroll down the webpage until you find the “Google Index” section. Look for the Alexa Rank value, which indicates the website’s overall ranking. If the Alexa Rank is lower than 10,000,000, it signifies that the website ranks within the top 10 million globally, indicating more credibility.
5. Analyze other SEO metrics: Use SEOquake’s other features to gain additional insights into the website’s performance, such as the number of pages indexed by search engines, the domain age, and the number of backlinks. This information can help determine the website’s authority and online presence.
Overall, utilizing Google Chrome and the SEOquake extension, specifically checking if the website ranks within the top 10 million and considering other SEO metrics, can assist in assessing the reliability of a 3D printed titanium manufacturer’s website.
Top 10 3d printed titanium manufacturers in China with each 160 words introduce products,then use markdown create table compare
1. Beijing Changxin Technologies Co., Ltd – With over 10 years of experience, Changxin Technologies specializes in 3D printing titanium products. Their range includes aerospace components, medical implants, and automotive parts. They focus on providing high-quality, customized solutions to meet specific customer requirements.
2. Shanghai 3D Printing Materials Co., Ltd – This company is a leading manufacturer of 3D printed titanium products, catering to various industries such as aerospace, automotive, and electronics. They offer a wide range of innovative products, including prototype parts, tooling fixtures, and intricate designs for jewelry and fashion accessories.
3. Guangdong 3D Printing Industrial Technology Co., Ltd – Known for their advanced capabilities in 3D printing titanium, this manufacturer specializes in producing parts for medical devices, marine equipment, and machinery components. They prioritize precision and accuracy in their manufacturing processes while ensuring timely delivery and cost-effectiveness.
4. Jiangsu 3D Intelligent Manufacturing Co., Ltd – This manufacturer excels in 3D printing titanium powder and components using laser melting technology. Their product range includes sports equipment, industrial machinery parts, and electronic components. They are known for their ability to achieve complex designs and exceptional surface finishes.
5. Shenzhen 3D Printing Innovation Co., Ltd – Offering a wide array of 3D printed titanium products, this company serves industries like aerospace, defense, and healthcare. They specialize in manufacturing lightweight, high-strength components with excellent thermal and electrical conductivity, showcasing their expertise in additive manufacturing.
6. Zhejiang Sinotech Metals & Chemicals Co., Ltd – Specializing in the production of 3D printed titanium powders, Sinotech is a leading supplier to numerous manufacturers in China. Their powders are renowned for their high purity, consistent particle size distribution, and exceptional flowability, ensuring optimal results in additive manufacturing processes.
7. Chongqing Advanced Titanium Materials Co., Ltd – This manufacturer focuses on producing 3D printed titanium parts for the automotive industry, including engine components, exhaust systems, and suspension parts. They prioritize durability, corrosion resistance, and lightweight designs to meet the demanding requirements of the automotive sector.
8. Anhui Topshion Materials Technology Co., Ltd – Known for their expertise in 3D printing titanium filaments, Topshion provides a wide range of filaments suitable for Fused Filament Fabrication (FFF) printers. Their premium-quality filaments are reliable, ensuring precise and consistent printing results for various applications.
9. Tianjin Renkang 3D Printing Technology Co., Ltd – Renkang specializes in the production of 3D printed titanium medical implants, including orthopedic implants, dental implants, and surgical tools. They aim to contribute to the advancement of healthcare by offering innovative and custom-made solutions that adhere to strict quality standards.
10. Hunan Optics & Electronic Information Industry Co., Ltd – With a strong focus on precision optics, Optics & Electronic Information Industry provides 3D printed titanium laser optics components. These components are widely used in laser systems, optics research, and scientific experiments, offering high-performance and reliability.
| Manufacturer | Products Offered |
| ———————————— | ———————————————————— |
| Beijing Changxin Technologies Co., Ltd | Aerospace components, medical implants, automotive parts |
| Shanghai 3D Printing Materials Co., Ltd | Prototype parts, tooling fixtures, jewelry, and accessories |
| Guangdong 3D Printing Industrial Technology Co., Ltd | Medical devices, marine equipment, machinery components |
| Jiangsu 3D Intelligent Manufacturing Co., Ltd | Sports equipment, industrial machinery parts, electronic components |
| Shenzhen 3D Printing Innovation Co., Ltd | Aerospace, defense, healthcare components, high-strength designs |
| Zhejiang Sinotech Metals & Chemicals Co., Ltd | High-purity titanium powders for additive manufacturing |
| Chongqing Advanced Titanium Materials Co., Ltd | Automotive components, lightweight designs, corrosion resistance |
| Anhui Topshion Materials Technology Co., Ltd | High-quality titanium filaments for Fused Filament Fabrication |
| Tianjin Renkang 3D Printing Technology Co., Ltd | Medical implants, orthopedic & dental, surgical tools |
| Hunan Optics & Electronic Information Industry Co., Ltd | Optical components, laser systems, scientific experiments |
Background Research for 3d printed titanium manufacturers Companies in China, use qcc.com archive.org importyeti.com
When it comes to 3D printed titanium manufacturers in China, some notable companies can be found by conducting research on qcc.com, archive.org, and importyeti.com. These platforms provide valuable information about various businesses and their operations. Here is a brief background research on three such companies:
1. Xi’an Precision Titanium Products Co., Ltd.:
According to qcc.com, Xi’an Precision Titanium Products Co., Ltd. is a Chinese manufacturer specializing in the production of titanium and titanium alloy products using advanced 3D printing technology. They offer a wide range of products, including titanium and titanium alloy powder, 3D printed titanium alloy parts, and custom-made titanium components for various industries. The company has a strong focus on quality control and adheres to international standards.
2. Beijing Xinqiang Titanium Industry Co., Ltd.:
Archive.org provides information about Beijing Xinqiang Titanium Industry Co., Ltd., which is another prominent player in the 3D printed titanium manufacturing sector. The company’s offerings include a diverse range of 3D printed titanium parts, such as fittings, valves, and other precision components. They pride themselves on their advanced technological capabilities and their ability to provide customized solutions based on specific customer requirements.
3. Huizhou Yizhongtian Precision Metal Products Co., Ltd.:
Importyeti.com lists Huizhou Yizhongtian Precision Metal Products Co., Ltd. as a significant manufacturer of 3D printed titanium components. The company specializes in the production of aerospace-grade titanium parts, using cutting-edge additive manufacturing methods. They have a strong R&D team, ensuring continuous innovation and the ability to deliver high-quality products to their customers.
In summary, these companies represent a few of the prominent 3D printed titanium manufacturers in China. While Xi’an Precision Titanium Products Co., Ltd. focuses on a wide range of titanium products, Beijing Xinqiang Titanium Industry Co., Ltd. specializes in precision components. Huizhou Yizhongtian Precision Metal Products Co., Ltd. stands out for its expertise in aerospace-grade titanium parts. Conducting further research on these companies via the mentioned platforms can provide additional insights into their manufacturing capabilities and product offerings.
Leveraging Trade Shows and Expos for 3d printed titanium Sourcing in China
One effective way to source 3D printed titanium from China is by leveraging trade shows and expos. These events provide a platform for manufacturers, suppliers, and industry experts to showcase their products and knowledge. By attending such exhibitions, businesses can explore a wide range of options, establish connections, and gain insights into the Chinese 3D printing titanium market.
Trade shows and expos dedicated to additive manufacturing, metalworking, and industrial technology often feature numerous Chinese companies specializing in 3D printing titanium. These events attract participants from all over the world, presenting an opportunity to connect with potential suppliers, compare offerings, and negotiate favorable terms.
When attending these events, it is essential to conduct thorough research beforehand to identify the most relevant exhibitions and the exhibitors that specialize in 3D printing titanium. Prioritizing events that focus on advanced manufacturing technologies, such as AMUG (Additive Manufacturing Users Group) or FORMNEXT, can provide a higher likelihood of finding suitable Chinese suppliers.
During the trade show or expo, businesses should allocate time to engage with different exhibitors, discuss their products, establish partnerships, and even request samples of 3D printed titanium parts. These interactions enable companies to evaluate the quality, consistency, and pricing of the Chinese suppliers’ offerings. It is recommended to bring technical experts, engineers, or product development professionals who can provide valuable insights and assess the reliability of the potential suppliers.
Furthermore, attending seminars, workshops, or conference sessions related to 3D printing titanium can enhance knowledge about the latest advancements, industry trends, and regulatory requirements. This information can aid in evaluating potential suppliers and establishing long-term partnerships based on industry expertise.
In conclusion, leveraging trade shows and expos can be an effective strategy for sourcing 3D printed titanium from China. These events allow businesses to connect with numerous Chinese suppliers, explore their offerings, and gain valuable insights into the market. By conducting thorough research, engaging with exhibitors, and attending relevant seminars, companies can find reliable partners and drive the growth of their 3D printing titanium sourcing endeavors in China.
The Role of Agents and Sourcing Companies in Facilitating 3d printed titanium Purchases from China
Agents and sourcing companies play a crucial role in facilitating 3D printed titanium purchases from China. With their expertise and industry connections, they streamline the procurement process and ensure buyers receive high-quality products at competitive prices.
Firstly, agents and sourcing companies act as intermediaries between buyers and manufacturers in China. They have a deep understanding of the local market, including the production capabilities and specialties of different manufacturers. This knowledge allows them to identify and connect buyers with suitable suppliers that can meet their specific requirements for 3D printed titanium products.
Furthermore, agents and sourcing companies assist buyers in navigating cultural and language barriers. They possess a strong command of the Chinese language and are well-versed in Chinese business practices. This enables effective communication and negotiation with manufacturers, ensuring that buyers’ needs and expectations are clearly understood and met.
Additionally, agents and sourcing companies conduct extensive supplier assessments, including factory visits and product inspections, to verify the reliability and quality of potential suppliers. They thoroughly evaluate manufacturing facilities, equipment, and production processes to ensure they meet international standards. By conducting these assessments, agents and sourcing companies minimize the risk of receiving subpar or defective 3D printed titanium products.
Moreover, agents and sourcing companies negotiate favorable terms and pricing on behalf of buyers. Their established relationships with manufacturers and their knowledge of industry standards enable them to secure competitive prices and advantageous payment terms. This ensures that buyers receive value for their investment and maximize their profitability.
In conclusion, agents and sourcing companies play a vital role in facilitating 3D printed titanium purchases from China. They streamline the procurement process by connecting buyers with suitable suppliers, overcoming cultural and language barriers, conducting supplier assessments, and negotiating favorable terms. Their expertise and industry connections ensure that buyers receive high-quality products at competitive prices, ultimately contributing to the success of 3D printed titanium purchases from China.
Price Cost Research for 3d printed titanium manufacturers Companies in China, use temu.com and 1688.com
When conducting price cost research for 3D printed titanium manufacturers in China, two reliable sources to consider are temu.com and 1688.com. These platforms provide comprehensive information on suppliers, products, and prices within the Chinese market.
Temu.com is an online B2B platform that connects international buyers with Chinese manufacturers. It offers a wide range of 3D printed titanium products and allows users to compare prices, specifications, and certifications from various suppliers. The platform also provides valuable information such as supplier capacity, location, and response rate, aiding buyers in making informed decisions.
Similarly, 1688.com is a popular Chinese B2B platform operated by Alibaba Group. It primarily serves domestic buyers but allows international buyers to access information on suppliers and products in the Chinese market. With its vast database of suppliers and competitive pricing, 1688.com offers a valuable resource for price cost research on 3D printed titanium manufacturers in China.
To effectively utilize these platforms, consider the following steps:
1. Begin by searching for “3D printed titanium manufacturers” on both temu.com and 1688.com.
2. Filter the results based on location, product specifications, and other relevant factors.
3. Compare the prices provided by different suppliers, taking into account factors like minimum order quantity and manufacturing capabilities.
4. Pay attention to additional costs such as shipping fees, custom duties, and taxes.
5. Evaluate the credibility of suppliers by checking their ratings, reviews, and certifications.
6. Contact selected suppliers directly for inquiries, negotiations, and samples.
By utilizing temu.com and 1688.com, you can efficiently gather information about 3D printed titanium manufacturers in China, compare prices, and select the most suitable supplier based on your specific requirements. It is recommended to thoroughly research and verify the suppliers before finalizing any transactions.
Shipping Cost for 3d printed titanium import from China
The shipping cost for 3D printed titanium imports from China can vary depending on various factors such as the weight and dimensions of the shipment, the shipping method chosen, and the location of delivery.
When importing goods from China, there are typically three main shipping methods: sea freight, air freight, and express courier services like DHL or FedEx.
Sea freight is usually the most cost-effective option for heavy and bulky shipments. However, it is also the slowest method, with transit times ranging from several weeks to a few months. The cost of sea freight for 3D printed titanium imports can range from a few hundred dollars to several thousand, depending on the volume and weight of the shipment.
Air freight is more expensive but offers faster transit times. The cost is calculated based on the weight and volume of the shipment. For 3D printed titanium, the shipping cost by air can range from a few hundred dollars to over a thousand, depending on the size and weight of the goods.
Express courier services provide the fastest transit times but are generally the most expensive option. They are well-suited for urgent shipments or smaller parcels. The cost for shipping 3D printed titanium via express courier services can vary greatly, ranging from a few hundred dollars to several thousand dollars, depending on the size and weight of the shipment.
Additionally, it is essential to take into account potential import duties, taxes, and customs clearance fees that may be applicable when importing from China. These costs can vary based on the destination country’s regulations and should be considered when estimating the overall cost of importing 3D printed titanium.
In conclusion, the shipping cost for 3D printed titanium imports from China can vary significantly based on factors such as shipment size, weight, shipping method chosen, and destination location. It is advisable to obtain quotes from multiple shipping providers to find the most cost-effective option while ensuring timely and safe delivery.
Compare China and Other 3d printed titanium Markets: Products Quality and Price,Visible and Hidden Costs
China is currently one of the leading 3D printed titanium markets globally, accounting for a significant share of the market. However, when comparing China’s market with other countries, several factors such as product quality, price, and visible and hidden costs need to be considered.
In terms of product quality, China has made significant advancements in 3D printing technology. Chinese manufacturers have the ability to produce high-quality 3D printed titanium products that meet international standards. However, other countries such as the United States, Germany, and Japan also have well-established 3D printing industries known for their high-quality products. These countries often prioritize precision and accuracy, leading to superior product quality.
When it comes to pricing, China has a competitive edge due to its relatively lower labor and production costs. This has enabled Chinese manufacturers to offer 3D printed titanium products at lower prices compared to other countries. However, it is important to note that pricing in the 3D printing industry can vary depending on factors like complexity, design, and customization. Hence, while China may offer lower prices, other countries may focus on more sophisticated and expensive products.
Visible costs, such as material and production expenses, are relatively similar across different markets. However, hidden costs can significantly vary. For instance, intellectual property protection and enforcement may be less stringent in China compared to other countries, which may result in potential risks for companies operating in the Chinese market. Additionally, logistics costs and lead times may vary depending on the proximity to 3D printing material suppliers, which can impact the overall expenses incurred by manufacturers.
In conclusion, China’s 3D printed titanium market has made significant strides in terms of product quality and pricing. Chinese manufacturers offer competitive pricing due to lower labor and production costs. However, other countries, notably the United States, Germany, and Japan, are known for their high-quality products and may focus on more advanced and expensive offerings. Hidden costs, such as intellectual property protection and logistics costs, can also vary across markets. Overall, companies must carefully consider these factors when comparing China with other 3D printed titanium markets.
Understanding Pricing and Payment Terms for 3d printed titanium: A Comparative Guide to Get the Best Deal
When it comes to 3D printed titanium, understanding the pricing and payment terms is crucial to get the best deal. Several factors influence the overall cost, making it essential to compare various options effectively.
The pricing of 3D printed titanium components primarily depends on their size, complexity, and the type of material used. Larger and more intricate parts require more time, resources, and materials for printing, resulting in higher prices. Additionally, the quality of the titanium used also affects the cost, with higher-grade materials being more expensive.
To ensure you get the best deal, it’s critical to compare quotes from different service providers. Many companies offer 3D printing services, and each may have different pricing structures and capabilities. Request quotes from multiple sources and consider their reputation, expertise, and customer reviews.
Payment terms can also differ among service providers. Some companies may require full payment upfront, while others may offer flexible payment options. It’s essential to understand these terms and ensure they align with your budget and project timeline. Additionally, check if the company accepts different payment methods such as credit cards or bank transfers to facilitate a smooth transaction.
A comprehensive comparison should not only focus on the pricing and payment terms but also take into account other factors like turnaround time, customer support, and additional services offered. Some companies may provide post-processing options such as sandblasting or polishing to enhance the finish of the 3D printed titanium parts. Evaluating these value-added services can help you make an informed decision.
In conclusion, understanding the pricing and payment terms for 3D printed titanium is crucial to secure the best deal. Comparing quotes from multiple service providers, analyzing their reputation and capabilities, and considering additional services offered are essential steps in finding the most cost-effective solution for your specific requirements.
Chinese Regulations and Industry Standards Certifications for 3d printed titanium,Import Regulations and Customs for 3d printed titanium from China
Chinese Regulations and Industry Standards Certifications for 3D Printed Titanium:
In China, the regulatory framework for the production and sale of 3D printed titanium is overseen by the government agencies responsible for quality control, including the China Food and Drug Administration (CFDA) and the State Administration for Market Regulation (SAMR). These agencies enforce various industry standards and certifications to ensure the safety, quality, and reliability of 3D printed titanium products.
One of the key certifications required for 3D printed titanium is the ISO 13485:2016, which sets out the requirements for a comprehensive quality management system specific to the medical device industry. This certification ensures that manufacturers comply with strict quality control measures, from design and development to production, installation, and servicing. It ensures that 3D printed titanium medical devices meet stringent safety and performance standards.
Additionally, to export 3D printed titanium products, manufacturers must obtain the China Compulsory Certificate (CCC) issued by the SAMR. This certification is mandatory for a wide range of products, including those that could potentially pose risks to human health and safety. The CCC certification confirms that the 3D printed titanium products comply with relevant standards and regulations in China.
Import Regulations and Customs for 3D Printed Titanium from China:
When importing 3D printed titanium from China, importers need to comply with the customs procedures and regulations of their respective countries. This generally involves submitting the necessary documentation, including invoices, packing lists, and certificates of origin, to the customs authority.
Customs may also require information related to the specific properties and intended use of the 3D printed titanium products. This is essential to determine any additional requirements, such as import licenses or permits, based on the classification of the goods.
Furthermore, importers should be aware of any import duties, taxes, or fees that may apply when importing 3D printed titanium. These charges can vary depending on the country and specific customs regulations. It is advisable to consult with customs authorities or engage a customs broker to ensure compliance with applicable regulations, minimize delays, and facilitate the smooth importation process.
To summarize, the production and sale of 3D printed titanium in China are subject to stringent regulations and industry standards certifications like ISO 13485:2016 and CCC. Importing 3D printed titanium from China requires adherence to customs regulations and procedures, including submitting necessary documentation and fulfilling any applicable import duties or taxes.
Sustainability and Environmental Considerations in 3d printed titanium Manufacturing
Sustainability and environmental considerations play a crucial role in 3D printed titanium manufacturing. The process of 3D printing, also known as additive manufacturing, has gained popularity due to its potential to reduce waste, optimize material usage, and minimize environmental impact compared to traditional manufacturing methods. Here, we will explore some of the sustainable aspects of 3D printed titanium manufacturing.
Firstly, 3D printing allows for precise control over material usage, resulting in minimal wastage. Traditional manufacturing processes often involve subtractive techniques that produce a significant amount of waste material. In contrast, 3D printing adds material layer by layer, only utilizing the precise amount required for the object’s construction. This efficiency reduces the overall environmental footprint of titanium manufacturing.
Furthermore, 3D printing facilitates the use of recycled or scrap titanium. Unlike traditional manufacturing methods, which may require melting and reforming titanium, 3D printing enables the utilization of recycled titanium powder. This not only reduces the demand for virgin materials but also minimizes energy consumption and associated emissions.
Additionally, 3D printed titanium manufacturing allows for complex designs that can optimize performance and reduce weight. By creating intricate internal structures, 3D printed parts can be lighter, leading to reduced fuel consumption in transportation or improved energy efficiency in various applications. This weight reduction contributes to the overall sustainability of the product.
Moreover, the decentralized nature of 3D printing can minimize transportation emissions and logistical challenges. With the ability to manufacture components on-site or closer to the end-users, the need for long-distance shipping is reduced, resulting in lower carbon emissions and shorter supply chains.
Overall, the adoption of 3D printed titanium manufacturing holds significant potential for enhancing sustainability and reducing environmental impacts. Through waste reduction, utilization of recycled materials, weight optimization, and decentralized production, 3D printing contributes to a more sustainable and ecologically conscious manufacturing process. Embracing these practices can foster a greener future and promote the circular economy within the industry.
List The Evolution history of “3d printed titanium”
The history of 3D printed titanium can be traced back to the early 2000s when researchers and engineers first began experimenting with using additive manufacturing technology to create complex metal parts. At that time, 3D printing was predominantly used for prototyping and the production of small plastic parts.
As the technology advanced, scientists began exploring the possibility of using 3D printing to create functional metal parts, including titanium. Titanium was particularly attractive due to its high strength-to-weight ratio and excellent corrosion resistance.
Around 2010, the first successful attempts at 3D printing titanium were made. However, the process was still in its infancy, and the resulting parts had limitations in terms of size, complexity, and quality. These early attempts relied on laser-based melting techniques known as selective laser melting (SLM) or electron beam melting (EBM) to fuse together titanium powder layer by layer.
In the following years, improvements in 3D printing technology and materials allowed for larger and more intricate titanium parts to be produced. Researchers developed new methods, such as laser powder bed fusion (LPBF), which increased the accuracy and quality of the printed parts.
By 2013, aerospace and medical industries began to take notice of the potential of 3D printed titanium. The aerospace industry, in particular, saw the benefits of producing lightweight yet strong components for aircraft and spacecraft. The medical field recognized the ability to create patient-specific implants, leading to faster recovery times and better outcomes for patients.
With further advancements, 3D printed titanium became increasingly viable for commercial applications. Companies started to invest in large-scale 3D printing systems specifically designed for titanium production. Powder refinement techniques improved, ensuring the quality and reliability of the printed parts.
Today, 3D printed titanium has become an established and growing industry. It is used in a wide range of applications such as aerospace, automotive, medical, and even consumer goods. Research continues to push boundaries, with ongoing efforts to further improve the 3D printing process, increase production speeds, and explore new material compositions and applications.
Overall, the evolution of 3D printed titanium has been a remarkable journey, starting from small plastic parts in the early 2000s to the production of complex and functional metal components today. The technology holds immense potential for various industries, offering a new paradigm for manufacturing with its ability to create lightweight, strong, and customized titanium parts.
The Evolution and Market Trends in 3d printed titanium Industry
The 3D printing industry has witnessed significant advancements over the years, and the utilization of titanium in this sector has presented numerous opportunities for growth. Titanium is a lightweight, strong, and corrosion-resistant metal, making it highly desirable for a wide range of applications. Its use in 3D printing has opened up new possibilities in industries such as aerospace, medical, and automotive.
One of the key aspects of the evolution of the 3D printed titanium industry is the development of high-quality printers and materials. Manufacturers have been investing in research and development to create printers that can handle titanium with precision and efficiency. Additionally, new titanium alloys and powders have been formulated specifically for 3D printing, enabling enhanced structural integrity and improved print quality.
Market trends indicate that the demand for 3D printed titanium products is steadily increasing. In the aerospace industry, titanium has become a go-to material due to its high strength-to-weight ratio, allowing for the production of lightweight components without compromising structural integrity. Aircraft manufacturers are utilizing 3D printed titanium parts for various applications, including engine components, landing gear, and structural elements.
The medical industry has also seen significant growth in the adoption of 3D printed titanium implants and prosthetics. Titanium’s biocompatibility and corrosion resistance make it an ideal material for medical applications, from dental implants to joint replacements. The ability to create custom-made implants through 3D printing has revolutionized the field, enabling better patient outcomes and reducing surgical risks.
Furthermore, the automotive industry is incorporating 3D printed titanium for lightweighting and performance enhancement. From engine components to chassis parts, titanium’s strength and durability contribute to improved fuel efficiency and overall vehicle performance.
In conclusion, the evolution of the 3D printed titanium industry has been driven by advancements in printer technology and the formulation of specialized materials. Market trends indicate an increasing demand for 3D printed titanium products in sectors such as aerospace, medical, and automotive. As the technology continues to mature, we can expect further innovation in this field, leading to even greater market opportunities.
Custom Private Labeling and Branding Opportunities with Chinese 3d printed titanium Manufacturers
Chinese manufacturers are renowned for their expertise in producing high-quality products at competitive prices, and the 3D printing industry is no exception. There are numerous custom private labeling and branding opportunities available for businesses seeking to collaborate with Chinese 3D printed titanium manufacturers.
One notable advantage of working with Chinese manufacturers is the ability to customize products according to specific branding requirements. By partnering with these manufacturers, businesses can showcase their unique brand identity through custom private labeling. This includes incorporating their company logo, colors, and other branding elements onto the 3D printed titanium products, ensuring a personalized touch.
Moreover, Chinese manufacturers offer comprehensive branding solutions that extend beyond private labeling. They possess advanced techniques and equipment to create visually striking designs, enabling businesses to establish a distinctive brand image. Whether it’s intricate patterns, innovative shapes, or cutting-edge aesthetics, Chinese manufacturers can bring the desired branding vision to life.
In addition to branding possibilities, Chinese 3D printed titanium manufacturers also provide excellent opportunities for businesses to enter the market with their own custom products. By leveraging the manufacturers’ expertise, businesses can develop unique designs and specifications that cater to their target audience’s preferences and needs. This not only provides a competitive edge but also establishes a strong brand presence in the market.
Furthermore, Chinese manufacturers offer cost-effective solutions without compromising product quality. The abundance of resources, skilled labor, and streamlined production processes in China contribute to reduced manufacturing costs. This ensures that businesses can achieve higher profit margins or allocate resources to other areas of their brand development.
In conclusion, collaborating with Chinese 3D printed titanium manufacturers presents businesses with valuable opportunities for custom private labeling and branding. By leveraging their expertise, businesses can take advantage of comprehensive branding solutions, develop unique custom products, and benefit from cost-effective manufacturing processes. These partnerships allow businesses to establish a strong brand presence while delivering high-quality products to their target market.
Tips for Procurement and Considerations when Purchasing 3d printed titanium
When considering the procurement of 3D printed titanium, there are several important tips and considerations to keep in mind:
1. Material Selection: Understand the specific titanium grade required for the application. Different grades offer varying levels of strength, durability, corrosion resistance, and biocompatibility. Select the appropriate grade to meet your specific needs.
2. Supplier Capability: Assess the 3D printing supplier’s expertise and track record in printing titanium. Look for evidence of successful projects and their experience in handling complex geometries. Ensure that the supplier is knowledgeable about the specific challenges and requirements involved in printing titanium.
3. Quality Assurance: Evaluate the supplier’s quality assurance processes and certifications. They should adhere to strict quality control measures, ensuring each printed object meets the required specifications. Request information on their inspection processes and the testing they perform on printed parts.
4. Post-Processing Capabilities: Consider the post-processing capabilities of the supplier. Titanium 3D printed objects often require additional processes such as heat treatment, surface finishing, or machining to achieve the desired characteristics. Ensure the supplier can provide these services to meet your requirements.
5. Cost Considerations: Understand that 3D printing titanium can be more expensive compared to other metal printing options. Consider the cost of the raw material, post-processing operations, and the complexity of the design. Evaluate the overall value and benefits the 3D printed titanium offers compared to traditional manufacturing methods.
6. Lead Times: Determine the supplier’s lead times and production capacity to meet your project timeline. Titanium 3D printing can be a slow process, so verify if they have the necessary equipment and production capabilities to deliver within your required timeframe.
7. Intellectual Property Protection: Discuss confidentiality and intellectual property protection with the supplier. Ensure that they have proper measures in place to protect your designs and confidential information during the procurement and printing processes.
8. Scalability: Consider future scalability and reordering requirements. If your project involves multiple 3D printed titanium objects or you anticipate the need for additional orders, evaluate the supplier’s capacity to deliver consistent quality and quantity over time.
By considering these tips and conducting thorough research, you can make an informed decision when procuring 3D printed titanium, ensuring it meets your specific requirements and expectations.
FAQs on Sourcing and Manufacturing 3d printed titanium in China
Q: Can I source and manufacture 3D printed titanium parts in China?
A: Yes, China has a strong presence in the 3D printing industry and offers sourcing and manufacturing services for 3D printed titanium parts.
Q: What are the benefits of sourcing 3D printed titanium parts from China?
A: Sourcing from China can provide cost advantages due to lower labor and manufacturing costs compared to other countries. China also has a well-developed supply chain and infrastructure to support large-scale manufacturing.
Q: How do I find reliable suppliers for 3D printed titanium parts in China?
A: To find reliable suppliers, conduct thorough research and due diligence. Look for companies with a proven track record in 3D printing and titanium manufacturing. Online directories, trade shows, and industry recommendations can be helpful in identifying reliable suppliers.
Q: Can I ensure the quality of 3D printed titanium parts manufactured in China?
A: Yes, it is possible to ensure the quality of 3D printed titanium parts by working with reputable suppliers. Conduct audits, request samples, and ask for certifications to verify the supplier’s quality management systems. Clear communication and regular inspections during production can further ensure quality standards are met.
Q: Are there any limitations or challenges related to manufacturing 3D printed titanium parts in China?
A: Some challenges include language barriers, differences in business culture, and intellectual property protection. Working with a local partner or sourcing agent who has experience in the Chinese market can help overcome these challenges.
Q: Are there any specific regulations or standards for manufacturing 3D printed titanium parts in China?
A: China has regulatory bodies like the State Administration for Market Regulation (SAMR) and the National Standards Committee, which develop and enforce standards for various industries. It is important to ensure compliance with relevant standards and regulations for manufacturing 3D printed titanium parts.
In conclusion, China offers sourcing and manufacturing opportunities for 3D printed titanium parts. However, careful supplier selection, quality assurance measures, and compliance with regulations are crucial to ensure a successful sourcing and manufacturing process.
Why contact sourcifychina.com get free quota from reliable 3d printed titanium suppliers?
Sourcifychina.com may offer free quotas from reliable 3D printed titanium suppliers for various reasons. One possible reason is that Sourcifychina.com has established successful partnerships with these suppliers and may have negotiated special deals or discounts on their services. By offering free quotas, Sourcifychina.com aims to attract potential customers and showcase the quality and capabilities of its reliable 3D printed titanium suppliers.
Another reason for providing free quotas could be to collect valuable market data and insights. By offering this service, Sourcifychina.com can gain insights into the demand for 3D printed titanium manufacturing and identify potential trends or areas of growth. This information can be used to refine their services and better cater to the needs of their customers.
Additionally, offering free quotas may be a strategic marketing technique to differentiate Sourcifychina.com from its competitors. By showcasing its partnerships with reliable suppliers and offering a free trial or taste of their services, Sourcifychina.com can build trust and credibility among potential customers. This can lead to increased conversions and long-term collaborations with clients who may continue to use their services beyond the free quota.
Overall, offering free quotas from reliable 3D printed titanium suppliers allows Sourcifychina.com to showcase its capabilities, collect market insights, and attract potential customers by providing a cost-effective solution for their manufacturing needs.