Types and Applications of cast steel valves
Cast steel valves are widely used across a range of industries including oil and gas, power generation, chemical processing, and water treatment. They remain a popular choice because of their durability, reliability, and versatility in extreme conditions. Here are some of the types and applications of cast steel valves.
1. Gate Valves
Gate valves are one of the most commonly used cast steel valves, owing to their ability to provide unrestricted flow. These valves are commonly used in pipelines transporting gases and liquids under high pressure.
2. Globe Valves
Globe valves are another popular type of cast steel valve. They are commonly used in applications that require precise control of flow rate and direction. They are used in pipelines transporting liquids and gases, and also in the steam-handling systems of power plants.
3. Ball Valves
Ball valves are designed to provide quick shutoff and have a compact design. They feature a spherical disc which rotates to control the flow of fluid through the valve. Ball valves are ideal for use in applications requiring tight shutoff and low pressure drop.
4. Check Valves
Check valves are designed to allow fluid flow in one direction only, preventing backflow. They are commonly used in applications such as pumps, compressors, and boilers, where backflow can cause damage to equipment or pose safety hazards.
5. Butterfly Valves
Butterfly valves are versatile and cost-effective. They feature a disc that rotates to control the flow of fluid through the valve. They are commonly used in applications such as fire protection systems, water treatment plants, and HVAC systems.
In conclusion, cast steel valves are used in diverse applications across a range of industries. The type of valve used will depend on factors such as fluid type, flow rate, pressure, temperature, and process requirements.
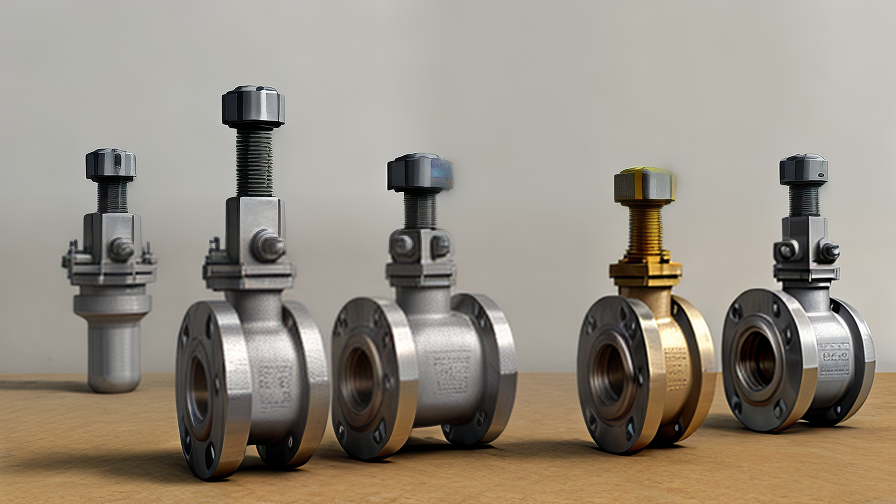
Benefits and Feature of Utilizing cast steel valves
Cast steel valves are a popular choice for industrial applications due to their durability, strength, and ability to withstand high pressures and temperatures. Here are some of the benefits and features of utilizing cast steel valves:
1. Durability: Cast steel valves are made from strong materials that are capable of enduring extreme conditions. This makes them suitable for use in harsh environments where other materials may not hold up.
2. Strength: Cast steel valves are known for their strength, making them ideal for use in industries such as oil and gas, chemical processing, and power generation where high-pressure and high-temperature applications are common.
3. Cost-effective: Cast steel valves are relatively cost-effective compared to other materials, making them a popular choice among manufacturers and industrial professionals.
4. Corrosion resistance: Many cast steel valves are designed to resist corrosion, which makes them an ideal choice for use in corrosive environments.
5. Enhanced lifespan: Cast steel valves can last for many years without the need for replacement or repair, making them an excellent choice for long-term use.
6. Variety of options: Cast steel valves are available in a wide range of sizes, shapes, and designs to suit different industrial applications.
7. Easy maintenance: Cast steel valves are easy to maintain, with many models requiring little more than regular cleaning and lubrication to keep them operating smoothly.
In summary, cast steel valves offer many benefits and features that make them an ideal choice for a range of industrial applications. These include durability, strength, cost-effectiveness, corrosion resistance, a long lifespan, a variety of options, and simple maintenance.
The Process of cast steel valves
The process of creating cast steel valves involves a series of steps to ensure the final product meets the required standards for use in various industries. The following is a brief overview of the process:
1. Pattern Creation: The process begins with the creation of a pattern that will be used to create the mold for the valve. The pattern is typically made from wood, plastic, or metal.
2. Mold Making: The pattern is used to create a mold from sand or a similar material. The mold is created in two halves, and the pattern is removed.
3. Melting: Steel is melted in a furnace, and the temperature is controlled to ensure consistency and quality.
4. Pouring: Molten steel is poured into the mold. The mold is then allowed to cool and solidify.
5. Deflasking: The solidified steel is removed from the mold by breaking open the mold. This process is known as deflasking.
6. Cleaning: The cast steel valve is then cleaned, removing any excess material or flash from the casting.
7. Machining: The valve is machined and polished to achieve the correct size, shape, and finish.
8. Quality Control: The finished valve is inspected to ensure it meets the required standard and specifications.
In conclusion, the process of creating cast steel valves involves pattern creation, mold making, melting, pouring, deflasking, cleaning, machining, and quality control. Each step is critical to ensure the final product is of high quality and meets the required standards.

How to use cast steel valves
Cast steel valves are high-quality valves that are commonly used in numerous industrial processes. They offer excellent performance and durability, which makes them the ideal choice for industrial applications that require high levels of strength, reliability, and resistance to harsh conditions.
These valves are designed to handle a wide range of applications, including corrosive and high-temperature environments. Cast steel valves are commonly used in industries such as oil and gas, petrochemicals, and power generation.
To use cast steel valves, it is essential to ensure that the valve is installed correctly. The installation process should be carried out by a qualified professional who has experience with valve installation. The installation process should also include adequate support to prevent any damage to the valve.
The valve should be regularly maintained to ensure proper functioning. Regular maintenance involves checking for leaks and corrosion and replacing any worn or damaged parts. It is recommended to follow the manufacturer’s maintenance schedule for optimal valve performance.
In conclusion, to use cast steel valves, it is critical to ensure proper installation, regular maintenance, and following the manufacturer’s guidelines. These valves offer excellent performance and are essential components in numerous industrial applications.
cast steel valves Manufacturer,Supplier and Wholesale
Cast steel valves are a fundamental component in the effective functioning of various industrial processes like chemical plants, oil and gas pipelines, water treatment plants, and power generation plants. These valves are made up of high-quality steel that offers long-lasting durability, strength, and excellent corrosion resistance, making them suitable for use in harsh environments.
At present, there are numerous manufacturers, suppliers, and wholesale distributors of cast steel valves worldwide, offering a range of cast steel valves in various designs, specifications, and sizes. However, not all cast steel valve manufacturers are equal, and it is essential to choose a reputable and reliable one to avoid any issues with the product.
A reputable cast steel valve manufacturer offers high-quality valves that meet the required international standards, including API, ANSI, and ISO. They incorporate advanced technology and high-quality materials to manufacture valves that will perform effectively and stand the test of time.
Moreover, a good cast steel valve supplier must provide an extensive range of valves to cater to various industrial applications. They must offer ball valves, gate valves, globe valves, check valves, butterfly valves, and other types of valves to cater to different industrial requirements.
In addition, a trustworthy cast steel valve wholesale distributor must offer fair and competitive prices that are commensurate with the quality of their products. A good supplier must also provide excellent customer support, including technical support and after-sales services.
In conclusion, cast steel valve manufacturers, suppliers, and wholesale distributors play a crucial role in meeting industrial needs. Quality and reliability are essential traits that one should consider when selecting a manufacturer or supplier to ensure that the cast steel valve you purchase is capable of meeting the specific needs of your industry.

cast steel valves Price
Cast steel valves are widely used in various industries such as oil and gas, chemical, petrochemical, and power generation. These valves are highly durable and resistant to corrosion, making them ideal for high-pressure and high-temperature applications. The price of cast steel valves varies based on their size, material, type, and design.
The cost of cast steel valves typically ranges from $50 to $10,000, depending on their size and type. The smaller valves used in domestic applications, such as in residential heating systems, are relatively less expensive. On the other hand, larger industrial valves used in oil and gas pipelines or power generation plants can cost several thousand dollars. The materials used to manufacture the valves also affect their price. Steel alloys that include elements such as chromium, nickel, and molybdenum enhance the valves’ durability and resistance to corrosion, but also increase their cost.
The type and design of the valve also determine its price. A basic ball valve or gate valve is relatively inexpensive, while a specialized valve such as a globe valve or butterfly valve can be more expensive. Similarly, valves with advanced features such as pressure relief or flow control mechanisms are typically more costly than simpler models.
In summary, the price of cast steel valves varies based on their size, material, type, and design. It is essential to consider the specific requirements of the application when determining which valve to purchase. Valves that are of higher quality and more durable may cost more upfront but could ultimately save money in maintenance costs and downtime.
FAQ sourcing cast steel valves manufacturer from China with multiple answers
1. What is the minimum order quantity for cast steel valves from China?
Most manufacturers in China have a minimum order requirement of 50 to 100 pieces per model. However, this can vary depending on the size and complexity of the valve.
2. What certifications do Chinese cast steel valve manufacturers have?
Most Chinese manufacturers are certified by ISO, CE, API, and other standards. It is important to verify the certifications and quality control measures before making a purchase, as some manufacturers may not be fully compliant.
3. Can I get custom designs for cast steel valves from China?
Yes, Chinese manufacturers can provide custom designs based on customer specifications. It is important to provide detailed information such as valve size, material, pressure rating, and other requirements to ensure the manufacturer can produce the desired product.
4. What is the lead time for cast steel valves from China?
The lead time varies depending on the manufacturer, quantity, and complexity of the product. Generally, it ranges from 4 to 12 weeks. It is important to confirm the lead times with the manufacturer before placing an order.
5. What is the pricing for cast steel valves from China?
Prices vary depending on the manufacturer, quantity, and product specifications. On average, prices for cast steel valves from China are 20-30% lower than those from Western countries. However, pricing should not be the only factor considered when selecting a manufacturer, as quality and reliability are also important.
6. How do I ensure quality when sourcing cast steel valves from China?
It is important to work with a reputable manufacturer that has the necessary certifications and quality control measures in place. It is also recommended to conduct a thorough inspection of the products before shipment or work with a third-party inspection company. This can help ensure that the products meet the desired specifications and quality standards.