Types and Applications of air source treatment
Air source treatment is an essential process in ensuring the quality of compressed air used in different industrial applications. It involves the removal of moisture, oil, and other contaminants that can affect the efficiency and quality of compressed air. There are different types of air source treatments, including filters, regulators, lubricators, dryers, and condensate drains, each serving unique purposes.
Filters are commonly used for removing solid particles, liquid droplets, and oil and water mists from compressed air. This helps to prevent equipment failure, extend equipment life, and maintain compressed air quality. Filters are available in different grades, depending on the level of filtration required, and are suitable for use in various applications such as automotive, food and beverage, and pharmaceutical industries.
Regulators are used to regulate air pressure in compressed air systems. This ensures consistent air pressure, prevents equipment damage, and reduces energy consumption. Regulators are commonly used in industrial applications such as automotive, HVAC, and pneumatic systems.
Lubricators are used to add lubrication to compressed air systems to ensure smooth operation and prolong equipment life. They are commonly used in applications such as industrial machinery, petrochemicals, and compressed air systems.
Dryers are used to remove moisture from compressed air systems, which can cause corrosion, equipment failure, and loss of productivity. There are different types of dryers, including refrigerated, desiccant, and membrane dryers, which are suitable for various applications depending on the required level of dryness.
Condensate drains are used to remove condensate from compressed air systems. The condensate contains oil, water, and other contaminants that can affect equipment performance and system integrity. Condensate drains are available in different types, including electronic, timer-controlled, and zero-loss drains, each serving unique purposes.
Air source treatment is essential in ensuring the quality and efficiency of compressed air systems in different industrial applications. It helps prevent corrosion, equipment failure, and downtime, and reduces energy consumption and maintenance costs. Filters, regulators, lubricators, dryers, and condensate drains are all types of air source treatments that serve different purposes and are suitable for use in various applications.
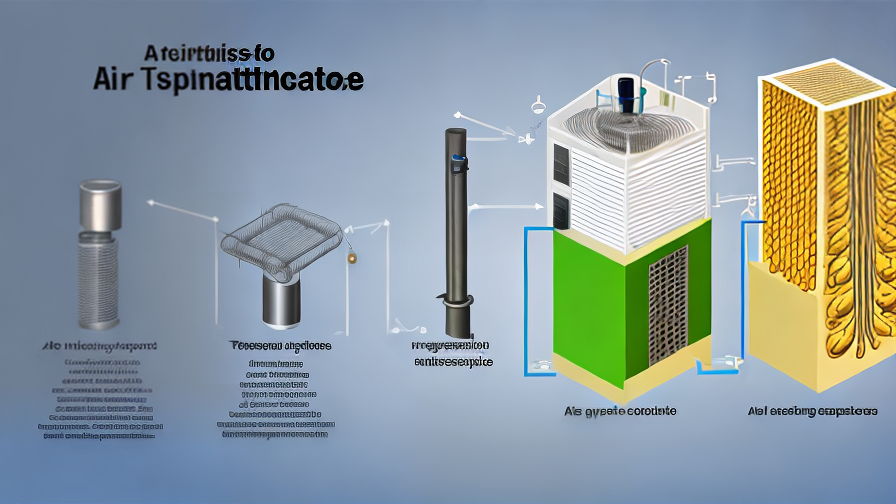
Benefits and Feature of Utilizing air source treatment
Air source treatment is an integral part of many industrial and manufacturing processes. Air source treatment helps to achieve the desired level of air quality necessary for these operations by filtering out particles, moisture, and oil from compressed air. Here are the essential benefits and features of utilizing air source treatment:
1. Extended Equipment Life: Air source treatment can help to extend the life of pneumatic equipment and tools by ensuring the air supply is clean, dry, and free of contaminants. Regular maintenance and filtration can prevent costly repairs resulting from system failures caused by dirty air.
2. Improved energy efficiency: Proper air source treatment reduces energy costs by minimizing pressure drops and reducing the frequency of equipment repair and replacement. Filtration and drying also result in more efficient air compressor operation and minimizes the possibility of air leaks or system malfunctions.
3. Compliance with regulatory standards: Many industries have specific air quality standards they must meet for industrial processes. Air source treatment ensures air quality standards are met, reducing the risk of work-site environmental pollution violations.
4. Increased productivity: By removing contaminants, air source treatment ensures that equipment operates at top performance levels, avoiding costly downtime caused by routine maintenance or unexpected system failures.
5. Health and Safety: Workplace air quality is a significant concern for employees. Proper use of air source treatment ensures that employees are not exposed to contaminated or unhealthy air, promoting better health and safety practices in the workplace.
In summary, the use of air source treatment offers tangible benefits and features that enhance productivity, promote quality control, improve equipment longevity, and ensure worker safety. Therefore, it is essential to ensure that air source treatment is integrated into air compression systems for efficient operation and improved production output.
The Process of air source treatment
Air source treatment is the process of treating compressed air sourced from the atmosphere before it is used in industrial and commercial applications. The treatment process is essential in ensuring the air is free from contaminants that can compromise product quality or damage machinery. The typical air source treatment process involves four stages, namely, filtration, drying, lubrication, and regulation.
Filtration is the first stage of air source treatment and involves removing solid and liquid contaminants from the compressed air. The process is necessary to prevent damage to downstream equipment and processes and improve the quality of the compressed air. The filtration stage typically involves the use of filters that remove contaminants based on their size and particle shape.
The second stage is drying, where the compressed air is heated and cooled to remove moisture and achieve a predetermined dew point. The control of moisture in compressed air is essential as excessive moisture can lead to corrosion of equipment and damage to pneumatic tools. The drying process can be achieved through refrigeration or adsorption techniques, depending on the application requirements.
After drying, lubrication is necessary to ensure smooth operation of pneumatic machinery. The lubrication process involves introducing minute quantities of lubricants, such as oil or grease, into the compressed air stream to protect the machinery and other components from wear and tear.
Finally, the last stage of air source treatment is regulation, where the pressure and flow rate of the air are regulated to meet the requirements of the application. Pressure regulators and flow control valves are used to maintain consistent air pressure levels and flow rates, thus enabling optimal performance of the pneumatic machinery.
In summary, the air source treatment process is essential in ensuring the compressed air used in industrial and commercial applications is free from contaminants, moisture, and is appropriately lubricated to extend the life of the machinery and improve product quality. The four-stage process of filtration, drying, lubrication, and regulation ensures the compressed air meets the demands of modern production requirements.

How to use air source treatment
Air source treatment is an essential step in many industrial applications where compressed air is used. The process enables the removal of impurities, moisture, and oil from the air before it is used, thereby enhancing the efficiency and longevity of the pneumatic equipment. This guide provides an overview of how to use air source treatment correctly.
Firstly, it’s essential to ensure that the air source treatment system is appropriately sized for the pneumatic equipment. Generally, the compressor and air treatment system should be chosen together to ensure optimal operation. The components of the air source treatment system include an air filter, a pressure regulator, an oil mist separator, and a dryer.
Secondly, check the air filter to ensure that the element is not clogged. The air filter should be cleaned or replaced regularly to ensure optimal operation. The water trap should also be emptied of any collected water periodically.
Thirdly, set the pressure regulator to meet the pressure requirements of the pneumatic equipment. The regulator should be adjusted to maintain a stable pressure to enhance the operation of the equipment.
Fourthly, ensure that the oil mist separator is functioning correctly to prevent damage to downstream components and contamination of products.
Finally, maintain the dryer by checking the desiccant regularly and replacing it per the manufacturer’s instructions. The dryer should also be serviced periodically to ensure that it continues to function correctly.
In conclusion, air source treatment is an essential process that should be performed regularly and correctly to ensure optimal operation and longevity of pneumatic equipment. Proper maintenance, cleaning, and replacement of components are crucial in this process.
air source treatment Manufacturer,Supplier and Wholesale
An air source treatment manufacturer is a company that provides a range of products designed to regulate and filter compressed air. The primary function of air source treatment is to ensure that compressed air systems are free of contaminants and moisture. This is crucial in industries such as food and beverage processing, pharmaceuticals, and electronics manufacturing.
The role of an air source treatment manufacturer is to provide products that are reliable, efficient, and tailored to the specific needs of their customers. This includes a range of products such as filters, regulators, lubricators, and dryers. These products work together to ensure that compressed air is clean, dry, and at the correct pressure.
The benefits of using air source treatment products include improved efficiency, reduced maintenance costs, and increased system lifespan. By removing contaminants and moisture from compressed air, the risk of equipment failure and production downtime is significantly reduced. This results in increased productivity, improved product quality, and a safer working environment for employees.
In addition to air source treatment products, manufacturers may also provide installation, maintenance, and repair services. This ensures that their customers have access to expert knowledge and support throughout the lifespan of their compressed air system.
As a supplier and wholesale distributor, they can provide reliable products for a range of industries. They can also offer competitive pricing and flexible delivery options to meet the needs of their customers.
Overall, an air source treatment manufacturer plays a critical role in ensuring that compressed air systems are efficient, reliable, and provide a high-quality end product. Their products and services are essential for industries that rely on compressed air, and they provide peace of mind for businesses that need to ensure that their systems are running smoothly.

air source treatment Price
Air source treatment is a process that involves removing impurities such as moisture, oil, and other particles from compressed air. It is vital to ensure that the compressed air is clean and dry to prevent equipment damage, contamination, and health hazards. The cost of air source treatment depends on various factors, including the type of treatment required and the size of the equipment.
Air filters are one of the most common forms of air source treatment used to remove impurities from compressed air. The prices of air filters vary depending on the filter’s efficiency and size. Smaller filters are generally cheaper than larger filters, and high-efficiency filters cost more than low-efficiency filters. Prices for air filters can range from as low as $20 to as high as $500.
Refrigerated air dryers are used to remove moisture from compressed air and prevent equipment damage and corrosion. The cost of refrigerated air dryers varies depending on the size of the equipment and its capabilities. Prices for refrigerated air dryers can range from around $500 to over $10,000.
Desiccant air dryers are another type of air source treatment used to remove moisture from compressed air. These dryers use desiccants to extract water vapor from the air. The cost of desiccant air dryers depends on the size of the equipment and the type of desiccant used. Prices for desiccant air dryers can range from around $1,000 to over $20,000.
Overall, the cost of air source treatment depends on the specific needs of the buyer. However, it is essential to consider the benefits of air source treatment, such as improving equipment efficiency, reducing maintenance costs, and preventing product contamination. Investing in air source treatment is a worthwhile investment that can save money in the long run.
FAQ sourcing air source treatment manufacturer from China with multiple answers
Q: Why should I source air source treatment from China?
A: China is known for its affordable labor and raw materials. It also has a large air treatment industry with a wide range of manufacturers, making it easier to find the right supplier for your needs.
Q: How can I find reliable air source treatment manufacturers in China?
A: One way is to look for manufacturers that have passed various certifications such as ISO 9001. You can also ask for references and read online reviews from previous customers. Lastly, you can visit trade shows in China where you can meet with different manufacturers and compare their products and prices.
Q: Can I request for customized air source treatment products from Chinese manufacturers?
A: Yes, most manufacturers in China are willing to produce customized products according to your specifications. You just need to provide them with the necessary details and requirements.
Q: How long does it take to receive shipments from Chinese air source treatment manufacturers?
A: The delivery time can vary depending on the manufacturer and the shipping method you choose. It can take as little as a few days or up to several weeks if the product needs to be manufactured first.
Q: Are there any risks of sourcing air source treatment from China?
A: Yes, there are risks such as language barriers, cultural differences, quality control issues, and supply chain disruptions. However, these risks can be minimized by working with reputable manufacturers and using secure payment methods.
Q: Can I negotiate prices with Chinese air source treatment manufacturers?
A: Yes, negotiating prices is common in China. It is important to have a clear understanding of the product specifications and the market prices before negotiating with the manufacturer.