Types and Applications of alumina magnesia carbon bricks
Alumina magnesia carbon bricks (AMC) are refractory bricks that consist of alumina, magnesia, and carbon. These bricks are widely used in high-temperature applications such as steelmaking, cement production, and non-ferrous metal refining.
There are mainly two types of AMC bricks: direct-bonded AMC and spinel-bonded AMC. Direct-bonded AMC bricks are made by pressing raw materials, followed by firing and bonding without using any intermediate phases. These bricks have excellent corrosion resistance against slag and metal penetration, making them ideal for use in steel ladles, converters, and other high-temperature applications. Spin-bonded AMC bricks are created by introducing a spinel phase in the raw materials and then firing them at high temperatures. These bricks have superior thermal shock resistance and less erosion by molten metal and slag.
The applications of AMC bricks are diverse and can be used in a wide range of industries. In steelmaking, they are used for various applications such as hot metal pretreatment, ladles, tundishes, converters, and electric arc furnaces. In cement production, they are utilized in the kiln and cooler zones, where extreme temperatures are encountered. In non-ferrous metal refining, AMC bricks find application in copper, lead, and zinc production.
In conclusion, alumina magnesia carbon bricks are essential refractory materials for high-temperature applications. They possess excellent properties such as corrosion and thermal shock resistance, making them ideal for applications in industries such as steelmaking, cement production, and non-ferrous metal refining.
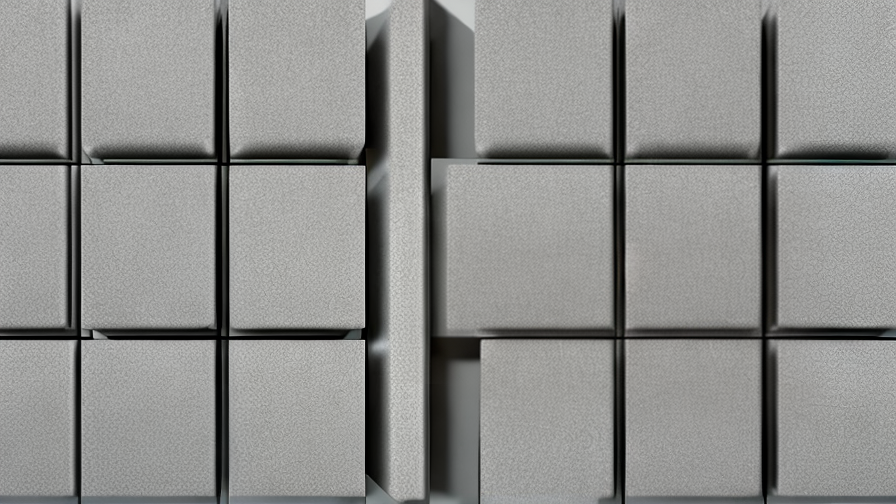
Benefits and Feature of Utilizing alumina magnesia carbon bricks
Alumina Magnesia Carbon (AMC) bricks are widely used in high-temperature industrial applications due to their high resistance to thermal shock and high temperatures. These bricks are composed of high-grade magnesia, alumina, graphite, and antioxidants that enhance the brick’s mechanical and thermal properties. Below are some of the benefits and features of using AMC bricks:
1. High Thermal Properties – AMC bricks can withstand extremely high temperatures of up to 1700℃ without showing signs of deterioration. Their high thermal conductivity helps to transfer heat away from the source much faster than other materials such as conventional firebricks.
2. Excellent Corrosion Resistance – Alumina magnesia carbon bricks have a high resistance to acidic and alkaline environments, making them ideal for use in furnaces or kilns where acidic gases or alkaline substances are present.
3. High Thermal Shock Resistance – These bricks exhibit excellent thermal shock resistance, making them suitable for use in applications where they are exposed to rapid temperature changes such as in the steelmaking industry.
4. Low Porosity – AMC bricks have a low porosity, which means they do not absorb moisture or gases, making them an ideal material for lining furnaces, ladles, and torpedo cars.
5. Good Mechanical Properties – The magnesium oxide and alumina contents in the bricks result in superior mechanical properties, including high strength, hardness, and toughness.
6. Energy Efficiency – AMC bricks can help to improve energy efficiency in high-temperature applications by reducing energy consumption and enhancing the performance of thermal processes, leading to significant cost savings.
In summary, Alumina Magnesia Carbon (AMC) bricks deliver a range of features and benefits that make them an ideal material for use in industrial applications where high temperatures, mechanical strength, and chemical resistance are required.
The Process of alumina magnesia carbon bricks
Alumina magnesia carbon bricks are a type of refractory bricks made from raw materials such as alumina, magnesite, flake graphite, and various additives. The process involves several steps, including mixing, molding, drying, and firing.
First, the raw materials are weighed and mixed in the appropriate proportions to achieve the desired composition and properties of the bricks. The mixing process is critical to ensure uniformity and homogeneity of the mixture.
Next, the mixture is compressed and molded into the desired shape and size using a hydraulic press or extrusion machine. The molds can be customized to meet specific requirements, such as curved or angled shapes.
After molding, the bricks are allowed to dry at room temperature for several days to remove any excess moisture and improve their strength. The drying process is crucial to prevent cracking and warping during firing.
Finally, the dried bricks are fired in a high-temperature kiln at temperatures ranging from 1350°C to 1650°C. The firing process chemically bonds the raw materials, creating a strong and durable aggregate structure. The carbon in the bricks provides additional strength and resistance to thermal shock.
Alumina magnesia carbon bricks have excellent corrosion and erosion resistance, high thermal conductivity, and low thermal expansion, making them ideal for use in steelmaking and other high-temperature applications. The manufacturing process of these bricks involves precision and control to ensure their performance and longevity.

How to use alumina magnesia carbon bricks
Alumina magnesia carbon (AMC) bricks are highly specialized materials used in the steelmaking industry for the construction of furnaces and other high-temperature applications. These bricks are made by combining alumina, magnesia, and graphite, which results in a material with excellent thermal conductivity, high resistance to thermal shock, and good mechanical strength.
To use AMC bricks, it is important to follow several steps. Firstly, the bricks should be inspected for any damage or defects. This is especially important for bricks that will be exposed to high temperatures, as any cracks or other damage can compromise their structural integrity and cause them to fail prematurely.
Once the bricks have been inspected, they can be installed using a range of techniques such as dry precast, gunning, or ramming. The precise method used will depend on the specific application and design of the furnace or other equipment. It is essential that the installation is carried out carefully to ensure that all joints are tightly sealed and that the bricks are correctly positioned to avoid any weak points or thermal stresses.
After installation, the AMC bricks will need to be carefully cured to ensure that they reach their full strength. This typically involves gradually raising the temperature to the working temperature while monitoring the condition of the bricks. Any issues should be addressed promptly to prevent further damage.
Overall, the use of AMC bricks is essential for high-temperature applications, and proper installation and maintenance are critical to their long-term performance. By following these steps, the bricks can provide excellent performance and durability, helping to ensure safe, efficient, and reliable steel production.
alumina magnesia carbon bricks Manufacturer,Supplier and Wholesale
We are a leading manufacturer and supplier of Alumina Magnesia Carbon (AMC) bricks, which are widely used in various high-temperature applications, including steelmaking, cement kiln linings, and non-ferrous metal furnaces. Our AMC bricks are made of high-quality raw materials such as alumina, magnesia, graphite, and other additives, which ensure their superior thermal shock resistance and excellent resistance to corrosion and erosion.
Our AMC bricks are designed to provide superior performance and durability even in the most challenging environments, where other refractory materials may fail. Our state-of-the-art production facilities and skilled workforce ensure that our products meet the highest standards of quality and consistency. We use advanced manufacturing techniques such as high-pressure molding, dry pressing, and isostatic pressing to produce AMC bricks of different shapes and sizes as per customer requirements.
We offer an extensive range of AMC bricks, including Alumina Carbon Bricks, Magnesia Carbon Bricks, Alumina Magnesia Carbon Bricks, and Chrome Magnesia Carbon Bricks, among others. Our AMC bricks are available in several grades, including high-alumina, mid-alumina, and low-alumina, to provide customers with a wide range of options to choose from.
We are committed to providing the best quality products and services to our customers, and we continuously upgrade our facilities and processes to ensure that our customers receive the most advanced and reliable products. With our vast experience and knowledge in the field of refractories, we are confident that we can provide our customers with the best quality AMC bricks at competitive prices.
In summary, if you are looking for a reliable and experienced manufacturer, supplier, and wholesaler of Alumina Magnesia Carbon (AMC) bricks, look no further than us. Contact us today to discuss your requirements or to request a quote.

alumina magnesia carbon bricks Price
Alumina magnesia carbon (AMC) bricks are widely used in the steel industry for their excellent performance in challenging environments. They are primarily used in the lining of steelmaking furnaces and ladles, where they have to withstand extreme temperatures, chemical attacks, and mechanical stresses. The price of AMC bricks primarily depends on their composition, quality, and size.
The price range of AMC bricks varies widely based on the alumina and magnesia content, carbon content, and binder type. The higher the alumina and magnesia content, the higher the price. The carbon content also affects the price, as higher carbon content makes the bricks more resistant to thermal and mechanical stress, but also increases their cost.
AMC bricks are available in different sizes and shapes to cater to different requirements. The larger the size, the more expensive the bricks become due to the use of more raw materials and higher production costs. The quality of AMC bricks also affects their price. High-quality bricks that are durable, resistant to corrosion, and have a longer service life are more expensive than lower quality bricks.
In summary, the price of AMC bricks can range from $400 to $1200 per tonne, depending on the composition, quality, and size. It is recommended to choose a reliable supplier that provides high-quality bricks at a reasonable price to ensure the best value for money.
FAQ sourcing alumina magnesia carbon bricks manufacturer from China with multiple answers
1. What is alumina magnesia carbon brick?
Alumina magnesia carbon brick is a type of refractory brick that is made from a mix of high-purity alumina, magnesia, and carbon. It is used in high-temperature applications where thermal shock resistance, corrosion resistance, and high mechanical strength are essential.
2. What are the advantages of using alumina magnesia carbon brick?
The advantages of using alumina magnesia carbon bricks include high thermal conductivity, excellent resistance to thermal shock and corrosion, high resistance to abrasion, and long service life. They are ideal for use in steelmaking furnaces, ladles, and tundishes.
3. What is the sourcing process for alumina magnesia carbon bricks manufacturers in China?
To source an alumina magnesia carbon brick manufacturer in China, you can search online directories and databases to find suppliers. You may also attend trade shows or conferences to connect with manufacturers and distributors. It is important to thoroughly research the manufacturer and their products, including their certifications and quality management systems, before making a purchase.
4. What factors should be considered when choosing a supplier of alumina magnesia carbon bricks in China?
When choosing a supplier of alumina magnesia carbon bricks, factors such as price, quality, delivery time, minimum order quantity, and after-sales service should be considered. It is essential to work with a reliable and experienced supplier that can meet your specific requirements and provide support throughout the procurement process and beyond.
5. How do I ensure quality when purchasing alumina magnesia carbon bricks from a Chinese supplier?
To ensure quality when purchasing alumina magnesia carbon bricks from a Chinese supplier, you should conduct a thorough evaluation of their manufacturing process, quality control systems, and certifications. You may also request product samples and conduct on-site inspections to verify the quality and consistency of the products. A clear and detailed quality control agreement should also be established to ensure that the products meet your specific requirements.