Types and Applications of magnesia carbon brick
Magnesia carbon brick is a refractory material used in a wide range of high-temperature applications, such as steelmaking, nonferrous metallurgy, cement kilns, and glass furnaces. It is composed of magnesia and carbon materials, which provide excellent resistance to erosion, thermal shock, and slag corrosion.
There are three types of magnesia carbon brick:
1. Direct-bonded: This type of brick has a high-density magnesia matrix, in which carbon is bonded directly to the magnesia grains. Direct-bonded brick has good resistance to slag erosion and thermal spalling, making it an ideal choice for steelmaking.
2. Resin-bonded: In this type of brick, a resin binder is used to bond the magnesia and carbon materials. Resin-bonded brick has a lower porosity and higher strength than direct-bonded brick, making it suitable for use in ladle linings and other high-stress applications.
3. Oxidation-resistant: This type of brick contains additional additives, such as aluminum oxide, to improve its resistance to oxidizing atmospheres. Oxidation-resistant brick is used in industries such as glass and carbon.
Magnesia carbon brick has various applications, including:
1. Steelmaking: Magnesia carbon brick is used in steelmaking to line the furnaces and ladles used to melt and pour molten steel. The refractory lining protects the steel structure from damage caused by high temperatures and corrosion.
2. Nonferrous metallurgy: The high resistance to chemical corrosion and erosion makes magnesia carbon brick ideal for use in nonferrous metallurgy. It is used to line converters, anode furnaces, and other high-temperature equipment.
3. Cement production: Magnesia carbon brick is used in the kilns used to produce cement. The refractory lining protects the kiln walls from chemical reactions and thermal stress caused by the high temperatures required for cement production.
4. Glass furnaces: Magnesia carbon brick is used to line the walls and roofs of glass furnaces. The refractory lining withstands the high temperatures and chemical reactions that occur during glass production.
In conclusion, magnesia carbon brick is an essential refractory material used in many high-temperature applications. The three types of magnesia carbon brick have unique properties that make them suitable for different industries and applications. The high resistance to corrosion, erosion, and thermal stress makes magnesia carbon brick a valuable material for industries such as steelmaking, nonferrous metallurgy, cement production, and glass manufacturing.
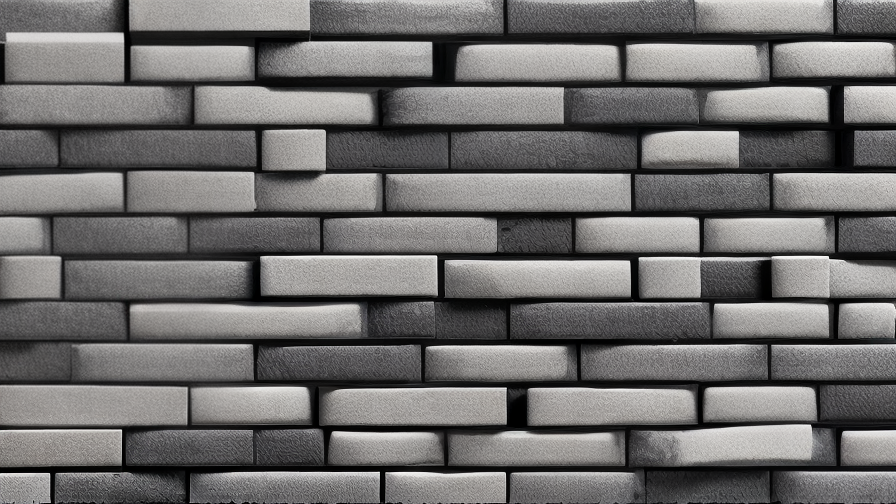
Benefits and Feature of Utilizing magnesia carbon brick
Magnesia carbon brick is a type of refractory brick commonly used in high-temperature applications. These bricks are made from magnesium oxide and carbon and are known for their excellent corrosion resistance, thermal shock resistance, and high-temperature strength. Here are some benefits and features of utilizing magnesia carbon bricks:
1. Corrosion resistance: Magnesia carbon bricks are highly resistant to corrosion and can withstand aggressive chemical environments.
2. Thermal shock resistance: These bricks can withstand rapid temperature changes without cracking or spalling, making them ideal for applications where heating and cooling cycles are frequent.
3. High-temperature strength: Magnesia carbon bricks can withstand high temperatures up to 2000°C, making them ideal for use in furnace linings, kilns, and other high-temperature applications.
4. Wear resistance: These bricks are highly resistant to wear and abrasion, making them ideal for use in cement kilns, steelmaking furnaces, and other applications where high abrasion resistance is required.
5. Low porosity: Magnesia carbon bricks have a low porosity, which makes them highly resistant to thermal shock and chemical attacks.
6. Easy installation: These bricks are easy to install and can be easily cut and shaped to fit any application.
7. Cost-effective: Magnesia carbon bricks are cost-effective compared to other refractory materials, making them a popular choice for a wide range of high-temperature applications.
8. Longer service life: Magnesia carbon bricks have a longer service life compared to other refractory materials, which reduces maintenance costs and downtime.
In conclusion, utilizing magnesia carbon brick provides several benefits and features, such as corrosion resistance, thermal shock resistance, high-temperature strength, wear resistance, low porosity, easy installation, cost-effectiveness, and longer service life. These qualities make magnesia carbon bricks the ideal choice for various high-temperature applications, including steelmaking, cement production, and furnace linings.
The Process of magnesia carbon brick
Magnesia carbon brick is a type of refractory brick that is widely used in industries where extreme high temperatures are required. It is primarily composed of magnesia and graphite, which provides high thermal conductivity and excellent resistance to heat, erosion, and corrosion.
The process of making magnesia carbon bricks begins by selecting high-purity magnesite and graphite as raw materials. The magnesite is then crushed, ground, and mixed with the graphite powder in a specific ratio in a ball mill or a mixer.
The resulting mixture is then molded into bricks of various shapes and sizes, using hydraulic presses. After the molding process, the green bricks are dried and baked in a kiln at high temperatures to remove any residual moisture and to further increase their strength and density.
Once the firing process is complete, the bricks undergo carbonization, where they are heated in a controlled environment to around 1000°C. The carbonization process results in the formation of a protective layer of graphite on the surface of the magnesia grains, which makes the bricks more resistant to oxidation and corrosion.
After carbonization, the bricks are calibrated and polished to ensure their dimensional accuracy and surface finish. Finally, the finished bricks undergo rigorous quality control testing to ensure that they meet the required specifications for use in high-temperature applications.
In conclusion, the process of making magnesia carbon brick involves selecting high-quality raw materials, mixing, molding, drying, firing, carbonization, calibration, polishing, and quality control testing. This process results in a highly durable and reliable refractory brick that is well-suited for use in extreme industrial environments.

How to use magnesia carbon brick
Magnesia carbon brick is a refractory material made of magnesium oxide and carbon materials. It is widely used in various industrial applications, such as steel making, non-ferrous metal smelting, casting, and cement production. This type of brick has excellent resistance to high temperatures, chemical corrosion, and mechanical wear, making it an ideal material for high-temperature furnaces and other applications that require resistance to extreme heat and chemical exposure.
The use of magnesia carbon brick consists of several steps. Firstly, the brick should be chosen according to the specific application. Different types of bricks have different properties, such as thermal conductivity, thermal shock resistance, and chemical resistance. The appropriate brick should be selected based on the requirements of the application.
Next, the brick should be laid in the furnace or other application in a certain pattern. The brick should be bonded together using a suitable refractory mortar to ensure stable performance and prevent cracks and damage from occurring due to thermal expansion and contraction.
During use, the magnesia carbon brick should be carefully monitored for any signs of wear or damage. Any cracks or defects should be remedied immediately to ensure the continued safety and effectiveness of the brick.
In conclusion, the use of magnesia carbon brick requires careful selection, installation, and maintenance to ensure optimal performance and prevent damage or wear. The properties of the brick should be carefully evaluated to ensure that it is appropriate for the specific application, and any defects or wear should be addressed promptly to ensure the continued safety and effectiveness of the material.
magnesia carbon brick Manufacturer,Supplier and Wholesale
Magnesia carbon brick is a type of refractory brick that is widely used in the steel industry due to its high thermal conductivity and excellent resistance to corrosion, erosion, and oxidation. These bricks are made by mixing high-purity magnesia and high-carbon graphite, which are then compacted and fired at high temperatures. As a result, they have a high density, low porosity, and excellent mechanical strength, making them ideal for use in harsh environments.
As a leading magnesia carbon brick manufacturer, supplier, and wholesale, we provide high-quality refractory bricks that meet the highest standards of the industry. Our products are characterized by their excellent thermal shock resistance, high-temperature strength, and low thermal expansion, making them the preferred choice of many steel-making facilities around the world.
Our production process involves the use of advanced technology and strict quality control measures to ensure that our products meet the needs of our customers in a cost-effective and reliable way. We work closely with our clients to understand their specific requirements and provide customized solutions that meet their needs, whether they need a small quantity of bricks or a large volume of bricks.
Our magnesia carbon brick products are widely used in the steel industry for applications such as EAF roofs, tapping channels, blast furnace linings, ladle linings, and other high-temperature applications. Our products are known for their outstanding performance, durability, and resistance to wear.
At our manufacturing facility, we have a team of skilled technicians and engineers who are dedicated to producing high-quality magnesia carbon bricks that meet the most demanding standards of the industry. We are committed to providing our customers with superior products and services that exceed their expectations, and we strive to be a reliable and trustworthy partner for all their refractory needs.

magnesia carbon brick Price
Magnesia carbon brick is a type of refractory material that is used in high-temperature applications such as steelmaking and other industrial processes. This type of brick is made from a combination of magnesia and carbon and has excellent resistance to high temperatures, corrosion, and erosion.
The price of magnesia carbon brick can vary depending on several factors such as the size, shape, and quality of the brick. Generally, magnesia carbon brick is more expensive than other refractory materials due to the combination of raw materials used, but the total cost will depend on the quantity and the supplier.
For example, a standard size 230x114x65 mm magnesia carbon brick can range in price from $50 to $100 depending on the manufacturer and the order quantity, while larger bricks such as 500x500x1000 mm can cost several thousand dollars.
It is also important to consider the quality of the magnesia carbon brick when making a purchase as lower quality bricks may require more frequent replacement, ultimately increasing the total cost of the project. High-quality magnesia carbon bricks can withstand higher temperatures, have better resistance to wear and corrosion, and have a longer lifespan, making them more cost-effective in the long run.
In conclusion, the price of magnesia carbon brick can vary based on several factors, but it is generally more expensive than other refractory materials due to its unique combination of raw materials. It is important to consider both the price and the quality of the brick when making a purchase to ensure the most cost-effective solution for your high-temperature application needs.
FAQ sourcing magnesia carbon brick manufacturer from China with multiple answers
Q: What is magnesia carbon brick?
A: Magnesia carbon brick is a type of refractory material that is used in high temperature furnaces and kilns due to its high resistance to corrosion and wear.
Q: Why source magnesia carbon brick from China?
A: China is one of the largest producers of magnesia carbon bricks in the world, with a competitive market and high-quality products at reasonable prices.
Q: How to find a reliable magnesia carbon brick manufacturer in China?
A: There are various ways to find a reliable manufacturer, including online directories, trade shows, referrals from industry professionals, and conducting a background check on the company.
Q: What are the advantages of sourcing magnesia carbon brick from China?
A: Some advantages include cost-effectiveness, high-quality products, streamlined production, and access to a wide range of suppliers.
Q: What should I consider when selecting a magnesia carbon brick manufacturer in China?
A: Consider the company’s experience in manufacturing and exporting, production capacity, quality control measures, certifications, and customer reviews and feedback.
Q: Are there any risks associated with sourcing magnesia carbon brick from China?
A: Like with any international trade, there are risks involved such as language barriers, cultural differences, regulatory compliance, and logistics challenges. However, working with a reputable and established manufacturer can help mitigate these risks.