Introduce about metal sheet manufacturing guide,Qulity,Cost,Supplier,Certification,Market,Tips,FAQ
Metal sheet manufacturing is the process of transforming metal into thin, flat sheets through various techniques such as casting, cutting, and forming. This guide aims to provide a comprehensive overview of metal sheet manufacturing, covering aspects such as quality, cost, supplier selection, certifications, market trends, tips, frequently asked questions (FAQs), and more.
Quality in metal sheet manufacturing is crucial to ensure performance, durability, and safety. It is imperative to choose a reputable supplier who follows stringent quality control measures and uses advanced manufacturing techniques. Quality can be further enhanced through certifications like ISO 9001, which ensures adherence to international quality standards.
Cost considerations play a significant role in metal sheet manufacturing. This involves evaluating the overall expenditure, including material costs, production expenses, and any additional value-added processes. Selecting a supplier who offers competitive pricing without compromising on quality is essential to avoid cost overruns.
Choosing the right supplier is vital for a successful metal sheet manufacturing project. Factors such as supplier’s experience, reputation, capacity, and capability to meet specifications should be evaluated. Collaborating with a trusted supplier ensures a consistent supply of high-quality metal sheets.
Certifications like ISO 9001, ISO 14001, or AS9100 demonstrate a supplier’s commitment to quality, environmental sustainability, and adherence to industry standards. These certifications instill confidence in customers and enable access to specialized markets that require certified suppliers.
The metal sheet manufacturing market is witnessing significant growth driven by industries such as automotive, construction, aerospace, and electronics. Keeping abreast of market trends, such as increasing demand for lightweight materials or advancements in surface finishing techniques, can provide a competitive edge.
Here are a few tips for successful metal sheet manufacturing:
1. Optimize material utilization to reduce waste and costs.
2. Constantly invest in new technologies and equipment to enhance efficiency and quality.
3. Develop strong relationships with suppliers for better collaboration and cost optimization.
4. Implement rigorous quality checks throughout the production process.
5. Stay updated with market trends and customer demands to remain competitive.
Frequently asked questions regarding metal sheet manufacturing may include queries about material selection, sheet thickness options, surface finishing techniques, or customization capabilities. These FAQs aim to address common concerns and help customers make informed decisions.
In conclusion, metal sheet manufacturing involves crucial considerations like quality, cost, supplier selection, certifications, market trends, and tips for success. By understanding these aspects and staying well-informed, businesses can excel in the dynamic and ever-evolving metal sheet manufacturing industry.
Types of metal sheet manufacturing
Metal sheet manufacturing involves shaping, cutting, and forming thin sheets of metal into different products. There are various methods and techniques used in this process, including:
1. Rolling: This is the most common method used to manufacture metal sheets. It involves passing the metal through a series of rollers to reduce its thickness and achieve the desired shape. Rolling can be done using hot or cold processes, depending on the type of metal and the desired outcome.
2. Shearing: Shearing is a process that involves cutting metal sheets into specific shapes or sizes using a shear machine. The machine applies shear forces to the metal, causing it to fracture and separate.
3. Bending: Bending is a technique used to shape metal sheets into curved or angular forms using tools such as press brakes or folding machines. The metal is placed between a punch and a die, and pressure is applied to bend it to the desired angle.
4. Stamping: Stamping is a high-speed method of manufacturing metal sheets into various products such as automobile parts or household appliances. It involves using a stamping press, which uses specialized dies to deform and shape the metal sheet.
5. Deep drawing: Deep drawing is a manufacturing process used to create complex, deep-formed parts such as pots, pans, or cans. It involves placing a metal sheet over a die and then using a punch to form the sheet into the desired shape.
6. Laser cutting: Laser cutting is a precise method of cutting metal sheets using a concentrated laser beam. This process allows for intricate and precise shapes to be cut out from the metal sheet.
7. Perforating: Perforating is a technique used to create patterns of holes in metal sheets for applications such as ventilation, filtration, or acoustic panels. This can be done through various methods, including punching, drilling, or laser cutting.
8. Welding: Welding is a process used to join metal sheets together by melting the edges and fusing them. This technique is commonly used to create larger structures or assemblies.
Overall, metal sheet manufacturing involves a variety of techniques such as rolling, shearing, bending, stamping, deep drawing, laser cutting, perforating, and welding. These methods allow for the creation of diverse metal sheet products used in industries like automotive, construction, aerospace, and more.
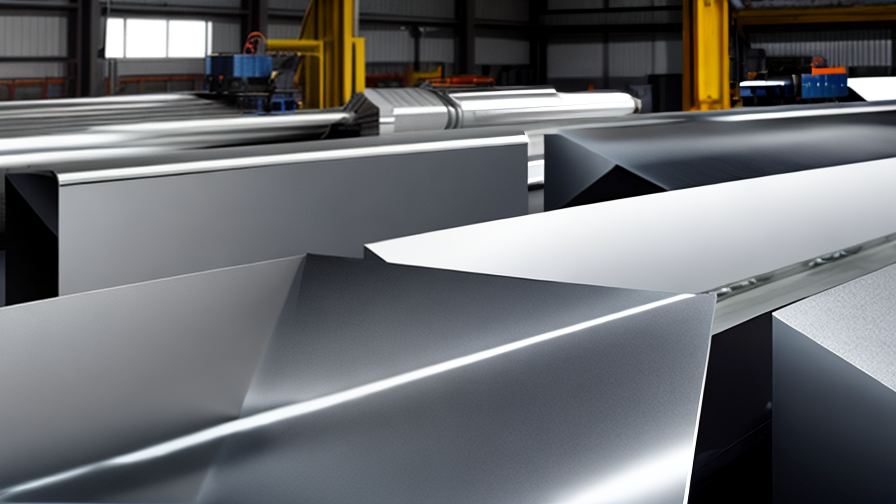
Pros and Cons of Using metal sheet manufacturing
Metal sheet manufacturing is a process that involves shaping and manipulating thin metal sheets into various products. It is widely used in industries such as automotive, aerospace, construction, and electronics. While there are several advantages to using metal sheet manufacturing, there are also some disadvantages that should be considered.
One of the main advantages of metal sheet manufacturing is its versatility. Metal sheets can be formed into complex shapes and sizes, making them suitable for a wide range of applications. This flexibility allows for the creation of intricate designs and precise dimensions, enabling manufacturers to meet unique customer requirements.
Another advantage is the strength and durability of metal sheets. They have high tensile strength, which means they can withstand heavy loads and resist deformation. This makes them ideal for structural components in industries such as construction and automotive, where strength and reliability are crucial.
Furthermore, metal sheets offer excellent thermal conductivity. This property allows them to efficiently transfer heat, making them suitable for applications that require heat dissipation or conductivity, such as electronic components or heat exchangers.
However, there are also some drawbacks to using metal sheet manufacturing. One disadvantage is the high upfront cost of equipment and tooling required for the process. Metal sheet manufacturing often involves specialized machinery like presses, stamping machines, and dies. These machines can be expensive to purchase and maintain, making it a significant investment for manufacturers.
Another limitation is the complexity of the manufacturing process. Metal sheet forming can involve several sequential steps, such as cutting, bending, and welding. Each of these processes requires skilled operators and meticulous quality control to ensure accurate and defect-free results.
Moreover, metal sheet manufacturing is not suitable for all materials. Certain metals, such as aluminum and steel, are commonly used in sheet manufacturing due to their malleability and availability. However, more brittle or exotic metals may be challenging to form into sheets, limiting their application in the process.
In conclusion, metal sheet manufacturing offers numerous benefits, including versatility, strength, and thermal conductivity. However, it also comes with some drawbacks, such as high upfront costs and complexity. Manufacturers should carefully evaluate these pros and cons when considering metal sheet manufacturing for their specific needs.
metal sheet manufacturing Reference Specifications (varies for different product)
Metal sheet manufacturing is a complex process that involves several steps and requirements. The reference specifications for this process can vary depending on the specific product being manufactured. However, there are some general guidelines that can be followed.
One of the main considerations in metal sheet manufacturing is the choice of material. Commonly used materials include stainless steel, aluminum, and carbon steel. The material selection depends on factors such as desired strength, corrosion resistance, and cost.
The thickness of the metal sheet is another important specification. This is determined by the intended application and requirements of the product. Thicker sheets offer higher strength and durability, while thinner sheets are more lightweight and flexible.
Surface finish is another aspect of metal sheet manufacturing. Different finishes can be achieved through processes like grinding, polishing, or coating. The choice of finish depends on factors like aesthetics, functionality, and the environment in which the product will be used.
Manufacturing processes such as cutting, bending, and forming are vital in shaping the metal sheet according to specifications. These processes can be carried out using various techniques, including laser cutting, waterjet cutting, or press brake bending. The choice of technique depends on factors such as accuracy, complexity of the design, and cost-effectiveness.
Quality control is an essential aspect of metal sheet manufacturing. It involves inspections and tests to ensure that the final product meets the required specifications. These inspections can include dimensional measurements, visual checks, and material testing.
In conclusion, metal sheet manufacturing involves various reference specifications that can vary depending on the product being manufactured. Factors such as material selection, thickness, surface finish, and manufacturing processes are crucial in ensuring the desired outcome. Quality control measures are also essential to guarantee that the final product meets the required specifications.
Applications of metal sheet manufacturing
Metal sheet manufacturing, also known as sheet metal fabrication, involves the process of cutting and shaping metal sheets to create various complex components and products. This versatile manufacturing method finds extensive application across several industries due to its numerous advantages. Here are some key applications of metal sheet manufacturing:
1. Automotive Industry: Metal sheet fabrication is widely used in the automotive sector for manufacturing components such as body panels, framework, chassis, and exhaust systems. The process allows for the creation of lightweight yet durable parts, contributing to improved fuel efficiency and overall performance.
2. Aerospace Industry: The aerospace industry heavily relies on sheet metal fabrication to produce critical aircraft components such as wings, fuselage sections, engine mounts, and structural brackets. The precision and strength provided by metal sheets ensure the safety and structural integrity of aircraft.
3. Construction Industry: Metal sheet manufacturing is widely utilized in the construction sector to produce various structural components such as beams, columns, roofing, cladding, and fabrication of HVAC systems. Sheet metal’s malleability, durability, and corrosion resistance make it an ideal choice for handling demanding construction requirements.
4. Electronics Industry: The electronics industry benefits from sheet metal fabrication in the production of enclosures, cabinets, and racks for electronic equipment like computers, telecom devices, and electrical control panels. Sheet metal components provide electromagnetic shielding, heat dissipation, and protection against environmental factors.
5. Medical Industry: Sheet metal fabrication plays a critical role in the manufacturing of medical equipment, hospital furniture, and surgical instruments. Metal sheets are used to create precision parts such as medical cabinets, operating tables, trolleys, and surgical tool trays, ensuring high levels of hygiene and durability.
6. Energy Sector: Metal sheet fabrication is essential in the energy industry for manufacturing components used in renewable energy systems like wind turbines, solar panels, and heating systems. Metal sheets are utilized to create turbine blades, solar panel frames, heat exchangers, and storage tanks.
7. Food and Beverage Industry: Metal sheet fabrication is employed in the production of stainless steel countertops, sinks, cabinets, and industrial kitchen equipment. Stainless steel sheets are preferred in this industry due to their hygienic properties, resistance to corrosion, and ease of cleaning.
In conclusion, metal sheet manufacturing finds widespread application across a range of industries, including automotive, aerospace, construction, electronics, medical, energy, and food and beverage. Its versatility, strength, and precision make it a crucial manufacturing method for the production of various complex components and products.
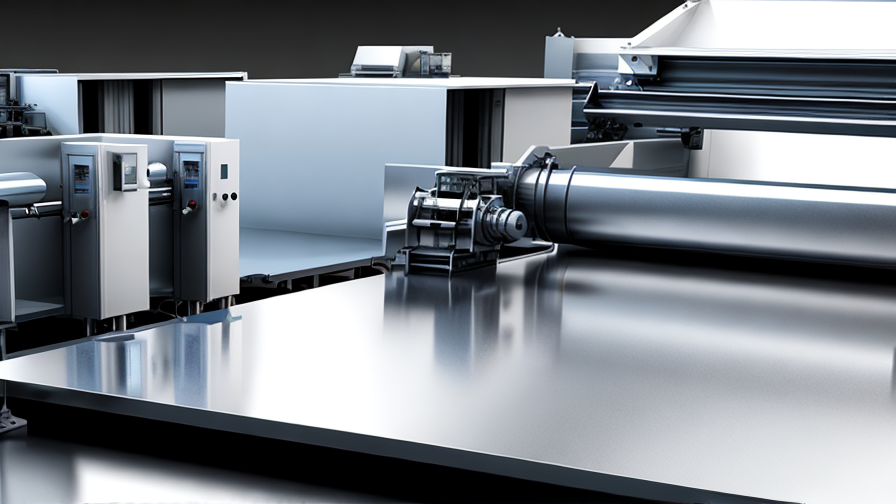
The Work Process and how to use metal sheet manufacturing
Metal sheet manufacturing is a complex process that involves transforming flat metal sheets into various components and products. The work process typically follows several steps:
1. Material Selection: The first step is selecting the type of metal sheet to be used. Common choices include steel, aluminum, and stainless steel, each offering unique properties and advantages.
2. Design and Engineering: The next step involves creating a design and engineering the product. This includes determining dimensions, tolerances, and specifications, as well as considering factors like strength, durability, and functionality.
3. Cutting: Once the design is finalized, the metal sheet is cut into the desired shape. This can be done using different techniques, such as laser cutting, waterjet cutting, or shearing. Precision is crucial to ensure accurate dimensions and smooth edges.
4. Forming and Bending: After cutting, the metal sheet is formed and bent into the desired shape. This can be achieved through processes like press forming, roll forming, or brake bending. Specialized equipment is used to apply precise pressure and achieve the desired curvature.
5. Joining: Different parts may need to be joined together through welding, riveting, or fastening techniques. This ensures structural integrity and enhances the product’s strength. Welding is the most common method, offering a permanent and strong bond.
6. Finishing: The metal sheet is then subjected to various finishing processes. This includes surface treatment, such as polishing, grinding, or sandblasting, to improve aesthetics and remove any imperfections. It may also involve adding protective coatings, like powder coating or galvanizing, to enhance durability and prevent corrosion.
7. Quality Control: Throughout the manufacturing process, quality control measures are implemented to ensure the final product meets specifications. This involves inspecting dimensions, surface finish, weld integrity, and overall functionality.
Metal sheet manufacturing offers a wide range of applications across industries, including automotive, construction, aerospace, and electronics. By understanding the work process and using the appropriate techniques and equipment, manufacturers can produce high-quality metal sheet components that meet specific requirements.
Quality Testing Methods for metal sheet manufacturing and how to control the quality
Quality testing methods for metal sheet manufacturing are essential to ensure that the produced sheets meet the required specifications. By implementing effective quality control measures, manufacturers can prevent defects, reduce waste, and maintain customer satisfaction. Several commonly used testing methods in metal sheet manufacturing include the following:
1. Dimensional inspection: This involves measuring the dimensions of the metal sheets to ensure they meet specified tolerances. Various tools like calipers, micrometers, and gauges are used for accurate measurements.
2. Visual inspection: Visual examination is conducted to detect any visible defects such as cracks, dents, scratches, or surface irregularities. This can be done manually or supplemented by automated visual inspection systems.
3. Mechanical performance testing: Different mechanical properties of metal sheets, such as tensile strength, yield strength, elongation, and hardness, are evaluated using specialized testing equipment like universal testing machines or hardness testers.
4. Surface quality testing: To assess the surface finish and smoothness, techniques like surface roughness measurement or visual surface inspection under different lighting conditions are employed.
5. Coating integrity testing: If the metal sheets have a coating, tests like adhesion, thickness measurement, salt spray tests, or chemical resistance checks are conducted to ensure proper coating adhesion and performance.
6. Non-destructive testing (NDT): NDT methods, including ultrasonic testing, magnetic particle inspection, or radiographic examination, are employed to detect internal defects without damaging the metal sheets.
To control the quality of metal sheet manufacturing, it is crucial to establish robust quality management systems. This includes implementing rigorous inspection protocols, defining comprehensive quality standards, and providing training to operators and inspectors. In addition, regular calibration and maintenance of testing equipment are essential to ensure accurate results. Applying statistical process control techniques can help monitor the manufacturing process and identify any deviations from the desired quality standards. Embracing continuous improvement practices and actively involving employees in quality improvement initiatives are also effective means to optimize quality control in metal sheet manufacturing.
metal sheet manufacturing Sample Policy and Post-Purchase Considerations for metal sheet manufacturing from China
Sample Policy:
The company ensures high-quality metal sheet manufacturing from trusted suppliers in China. To maintain customer satisfaction, we provide the following policies:
1. Quality Assurance: Our metal sheets are produced using state-of-the-art manufacturing techniques and undergo strict quality checks. We guarantee that the supplied products meet international quality standards.
2. Competitive Pricing: We consistently negotiate with our suppliers in China to ensure competitive pricing without compromising on quality. Our pricing is transparent, and we provide detailed quotations and invoices for every purchase.
3. Customization: We understand that different industries require specific metal sheet specifications. Our suppliers in China offer customization options to meet individual customer needs. Detailed specifications, including size, thickness, material, and finish, can be provided when placing the order.
4. Timely Delivery: We prioritize on-time delivery and work closely with our suppliers in China to ensure that orders are dispatched and delivered as per agreed schedules. In the event of any unforeseen delay, we will promptly inform our customers and provide alternative solutions.
Post-Purchase Considerations:
1. Inspection: Upon receiving metal sheets from our suppliers in China, customers are encouraged to inspect the products thoroughly for any defects, damages, or deviations from the specified requirements. Any concerns must be reported within 7 days of delivery.
2. Customer Support: We value our customers and are committed to resolving any post-purchase issues promptly. Customers can reach out to our dedicated customer support team for assistance regarding product quality, delivery, or any other concerns.
3. Feedback: We highly appreciate our customers’ feedback on their experience with our metal sheet manufacturing. This helps us maintain and improve the quality of our products and services. Customers are encouraged to provide feedback through our website or directly to our customer support team.
Note: This sample policy and post-purchase considerations provide a general overview. Further terms and conditions may apply based on specific agreements and requirements between the company and its customers.
Sourcing metal sheet manufacturing from China: Opportunities, Risks, and Key Players
Sourcing metal sheet manufacturing from China offers numerous opportunities for businesses worldwide. China is one of the largest manufacturers of metal sheets globally, providing a wide range of materials, sizes, and finishes at competitive prices. The country’s manufacturing industry is backed by advanced technology, skilled labor, and a well-established supply chain. These factors contribute to its ability to deliver high-quality products efficiently and in large quantities.
One of the primary opportunities of sourcing metal sheet manufacturing from China is cost savings. Chinese manufacturers can offer relatively lower labor costs compared to their counterparts in other countries. Additionally, the abundance of raw materials in China allows for cost-effective production. By sourcing from China, businesses can achieve significant cost reductions and potentially increase their profit margins.
Another opportunity is the diversity of products available. Chinese metal sheet manufacturers offer a wide variety of materials, such as stainless steel, aluminum, brass, and copper. They also provide an extensive range of sizes, thicknesses, and finishes to cater to diverse customer requirements. This versatility enables businesses to find suitable metal sheets for different applications, from construction to automotive and beyond.
However, there are risks associated with sourcing metal sheet manufacturing from China. Quality control can be a concern, as some manufacturers may compromise on quality to offer lower prices. It is crucial for businesses to conduct thorough due diligence and quality checks before engaging with a supplier. Additionally, communication and language barriers may pose challenges during production and delivery processes.
Some key players in metal sheet manufacturing in China include Baosteel Group Corporation, Wuhan Iron and Steel Corporation, and Ansteel Group Corporation. These companies have a strong reputation and are known for their quality products. However, it is essential to evaluate each supplier based on specific requirements such as materials, customization capabilities, and production capacity.
In conclusion, sourcing metal sheet manufacturing from China presents opportunities in terms of cost savings, diverse product options, and efficient production. Nevertheless, businesses need to be cautious about quality control and overcome communication barriers. By selecting reputable suppliers like Baosteel Group Corporation, Wuhan Iron and Steel Corporation, and Ansteel Group Corporation, companies can harness the advantages of Chinese metal sheet manufacturing while mitigating risks.
How to find and select reliable metal sheet manufacturing manufacturers in China,use google search manufacturers and suppliers
Finding and selecting reliable metal sheet manufacturing manufacturers in China can be a challenging task, but utilizing Google search can help simplify the process. Here are a few steps to follow:
1. Start by conducting a general Google search using relevant keywords such as “metal sheet manufacturing manufacturers China” or “metal sheet suppliers in China”. This will provide you with a list of potential manufacturers.
2. Once you have a list, go through the search results and visit the websites of these manufacturers. Look for clear and detailed information about their products, services, and manufacturing capabilities.
3. Check for certifications and accreditations on their websites. Reliable manufacturers often possess certifications such as ISO 9001 or ISO 14001, which ensure quality management and environmental practices.
4. Look for customer reviews and testimonials on their websites or conduct a separate search using the manufacturer’s name. Genuine customer feedback can provide insight into the manufacturer’s reputation and customer satisfaction levels.
5. Additionally, explore industry-specific forums, online directories, and trade portals that list metal sheet manufacturers in China. These platforms often provide detailed profiles, product catalogs, and customer reviews to help you make an informed decision.
6. Contact the shortlisted manufacturers and request more information such as company profile, product samples, and pricing. Engage in communication to assess their responsiveness, professionalism, and willingness to meet your specific requirements.
7. If possible, consider arranging a visit to the manufacturers’ facilities in China. This will allow you to assess their manufacturing processes, quality control measures, and overall production capabilities firsthand.
8. Finally, request quotations from multiple manufacturers and compare them based on factors such as pricing, quality, lead times, and customer support. Choose a manufacturer that meets your quality standards, offers competitive pricing, and can fulfill your production requirements on time.
By following these steps and using Google search effectively, you can significantly enhance your chances of finding and selecting reliable metal sheet manufacturing manufacturers in China.
How to check metal sheet manufacturing manufacturers website reliable,use google chrome SEOquake check if ranking in top 10M
To determine the reliability of a metal sheet manufacturing manufacturer’s website, you can follow these steps:
1. Open the manufacturer’s website in Google Chrome, the popular web browser.
2. Install the SEOquake extension in your Chrome browser.
3. Once installed, you can see a toolbar at the top of your browser window, showing various SEO metrics.
4. Enter the website’s URL in the address bar, and click on the SEOquake icon in the toolbar.
5. SEOquake will generate a comprehensive report about the website’s SEO performance, including its rank among the top 10 million websites.
6. Look for the website’s global Alexa rank. If it falls within the top 10 million, it indicates that the website is reasonably popular and potentially reliable.
7. Additionally, pay attention to other SEO metrics provided by SEOquake, such as the number of indexed pages, external links, and estimated organic traffic.
8. Consider the website’s design, user-friendliness, and overall professionalism, as these factors can reflect the manufacturer’s credibility.
9. Search for customer reviews or testimonials, both on the website itself and on external platforms, to gauge the satisfaction of previous customers.
10. Finally, analyze the manufacturer’s background, experience, and partnerships mentioned on the website to assess their expertise and reputation in the industry.
It’s essential to note that while SEOquake can provide valuable insights into a website’s popularity and SEO performance, it should not be the sole determining factor for reliability. Consider these metrics in conjunction with other research methods to form a well-rounded evaluation of the metal sheet manufacturing manufacturer’s website.
Top 10 metal sheet manufacturing manufacturers in China
China is renowned for its thriving metal sheet manufacturing industry, with numerous manufacturers offering a wide range of metal sheet products. Here is a list of the top 10 metal sheet manufacturing manufacturers in China:
1. Baosteel Group Corporation: As one of the largest steel manufacturers in China, Baosteel specializes in producing various metal sheets, including stainless steel and cold-rolled sheets.
2. Wuhan Iron and Steel Corporation (WISCO): WISCO is a leading metal sheet producer, known for its high-quality cold-rolled and galvanized steel sheets.
3. Ansteel Group Corporation: Ansteel specializes in producing hot-rolled, cold-rolled, and galvanized metal sheets. They are known for their advanced technologies and large-scale production capacity.
4. Shougang Group: Shougang is a prominent manufacturer of metal sheets, offering a wide selection of steel products such as hot-rolled, galvanized, and color-coated sheets.
5. Maanshan Iron and Steel Company (Magang): Magang produces a range of metal sheets, including hot-rolled, cold-rolled, and galvanized steel sheets. They are recognized for their quality products and customer-centric approach.
6. JFE Steel Corporation: JFE Steel is a major metal sheet manufacturer in China, serving various industries with high-quality steel sheets, including automotive, construction, and shipbuilding.
7. Baoshan Iron and Steel Co., Ltd (Baosteel): Another division of Baosteel Group, Baoshan is known for its galvanized and color-coated metal sheets. They have a strong reputation for delivering reliable, premium products.
8. Angang Steel Corporation: Angang Steel specializes in producing high-strength metal sheets, including hot-rolled and cold-rolled sheets. They cater to industries like automobile manufacturing and construction.
9. Tianjin Iron and Steel Group Co., Ltd: Tianjin Steel is a leading metal sheet manufacturer in China, offering a wide range of products such as galvanized, cold-rolled, and color-coated sheets. They have a strong focus on research and development.
10. Benxi Iron and Steel Group Co., Ltd: Benxi Steel is known for its production of cold-rolled and galvanized metal sheets. They are dedicated to sustainability and provide customized solutions for various applications.
These top 10 metal sheet manufacturing manufacturers in China showcase the country’s proficiency in producing high-quality metal sheets and cater to diverse industries. By leveraging advanced technologies and prioritizing customer satisfaction, these manufacturers continue to play a significant role in meeting the global demand for metal sheet products.
Background Research for metal sheet manufacturing manufacturers Companies in China, use qcc.com archive.org importyeti.com
When it comes to metal sheet manufacturing, China is recognized as one of the leading countries in terms of production and technological advancements. Several manufacturing companies in China specialize in metal sheet manufacturing, providing a wide range of products to domestic and international markets.
To conduct background research on Chinese metal sheet manufacturing manufacturers, three online platforms can be utilized: qcc.com, archive.org, and importyeti.com.
QCC.com is a Chinese business information platform that provides comprehensive company information, including registration details, financial status, and legal records. It can be used to obtain information about the legal status, establishment date, capital, and key personnel of metal sheet manufacturing manufacturers.
Archive.org is a digital library that enables users to access archived web pages. It can be used to explore the internet history of a company and track its progress over time. By accessing archived versions of a manufacturer’s website, one can gain insights into its past achievements, product range, certifications, and other relevant information.
Importyeti.com is an online import and export data platform that provides shipment records, including the names of importers and exporters, product descriptions, and trade volumes. It can be utilized to identify metal sheet manufacturing manufacturers and obtain information about their export activities, such as the countries they export to, the quantity of exports, and the value of shipments.
By utilizing these platforms, researchers can gather crucial information about metal sheet manufacturing manufacturers in China, including their financial stability, legal status, historical development, product range, certifications, export activities, and potential business partners.
To ensure the research remains concise, it is advisable to focus on key information such as company profiles, export records, and any relevant certifications or awards. The research can be summarized in approximately 300 words by selecting the most important findings from the platforms mentioned.
Leveraging Trade Shows and Expos for metal sheet manufacturing Sourcing in China
Trade shows and expos are excellent platforms for sourcing metal sheet manufacturing in China. These events provide an opportunity for manufacturers, suppliers, and buyers to gather under one roof, facilitating networking, knowledge sharing, and establishing business relationships.
By attending trade shows and expos focused on metal sheet manufacturing, companies can access a wide range of suppliers specializing in this industry. Exhibitors at these events showcase their products, technologies, and capabilities, allowing buyers to evaluate their suitability for their sourcing needs. Not only can buyers physically examine the quality of the metal sheets, but they can also discuss specific requirements, negotiate pricing, and inquire about customization options.
China hosts numerous trade shows and expos dedicated to metal sheet manufacturing, such as the China International Sheet Metal & Metal Processing Exhibition and the Guangzhou International Sheet Metal Industry Exhibition. These events attract both domestic and international exhibitors, enhancing the opportunities for buyers to find suitable suppliers.
Participating in trade shows and expos also offers the advantage of networking with industry professionals and peers. Attendees can exchange experiences, gather market insights, and learn about the latest trends and innovations in metal sheet manufacturing. This knowledge can be valuable in identifying new suppliers, understanding pricing strategies, and staying updated on industry developments.
To make the most of trade shows and expos, buyers should come prepared with clear sourcing requirements, contact information, and marketing materials. Engaging with suppliers and engaging in meaningful discussions will allow buyers to evaluate their trustworthiness, production capabilities, quality control systems, and export experience. Building personal relationships through these face-to-face interactions contributes to establishing long-term partnerships in metal sheet manufacturing sourcing from China.
In conclusion, trade shows and expos provide a fruitful avenue for sourcing metal sheet manufacturing in China. These events offer access to a diverse pool of suppliers, enable physical product inspection, facilitate networking, and provide valuable market insights. Utilizing these opportunities effectively can lead to successful partnerships and drive business growth in metal sheet manufacturing sourcing in China.
The Role of Agents and Sourcing Companies in Facilitating metal sheet manufacturing Purchases from China
Agents and sourcing companies play a crucial role in facilitating metal sheet manufacturing purchases from China. With their expertise and knowledge of the Chinese market, they provide valuable assistance to buyers by streamlining the procurement process and ensuring a smooth transaction.
One of the primary functions of agents and sourcing companies is to identify reliable and qualified metal sheet manufacturers in China. They have access to a vast network of suppliers and can conduct rigorous background checks to verify their credentials. This reduces the risk of dealing with untrustworthy or low-quality manufacturers.
Additionally, agents and sourcing companies assist buyers in negotiating favorable terms and prices with the suppliers. They have a deep understanding of the local business culture, language, and customs, allowing them to navigate through negotiations effectively. By leveraging their knowledge, they can help secure the best possible prices and ensure compliance with international quality standards.
Moreover, agents and sourcing companies offer logistical support to buyers. They coordinate the transportation, handling, and shipping of the metal sheets, ensuring timely delivery. They also handle any customs clearance procedures and documentation required for seamless importation.
Furthermore, these intermediaries act as a bridge between the buyer and manufacturer, facilitating effective communication and resolving any misunderstandings that may arise during the purchasing process. They serve as the buyer’s representative in China, ensuring that their requirements and specifications are understood by the manufacturer and that the final product meets the desired quality standards.
Overall, agents and sourcing companies play a critical role in facilitating metal sheet manufacturing purchases from China. Their expertise, local knowledge, and network of suppliers allow buyers to gain access to reliable manufacturers, negotiate favorable terms, and ensure smooth logistics and communication throughout the entire procurement process. Their involvement significantly reduces the risks associated with sourcing from overseas and contributes to the success of metal sheet manufacturing purchases from China.
Price Cost Research for metal sheet manufacturing manufacturers Companies in China, use temu.com and 1688.com
When it comes to metal sheet manufacturing in China, two popular websites that can provide valuable information about price and cost are temu.com and 1688.com. These platforms offer a wide range of manufacturers and suppliers in the industry, making it easier for businesses to conduct research and compare prices.
Temu.com is a leading B2B platform that connects buyers with manufacturers and suppliers in various industries. By searching for metal sheet manufacturing manufacturers on temu.com, businesses can access a comprehensive list of companies along with their product offerings and prices. The platform allows users to filter their search based on specific criteria such as location, certification, and production capacity, making it easier to find suitable suppliers.
Another website that is widely used in China is 1688.com, which is an online marketplace owned by Alibaba Group. This platform serves as a sourcing tool for businesses looking to connect with manufacturers, especially those based in China. By searching for metal sheet manufacturing suppliers on 1688.com, users can access detailed product information, including specifications, prices, and minimum order quantities.
When conducting price and cost research on these platforms, it is essential to have a clear understanding of the desired requirements and specifications. This will enable businesses to compare prices accurately and choose the most suitable suppliers for their needs. Additionally, businesses should consider reaching out to multiple manufacturers to request quotes and negotiate prices further.
In conclusion, temu.com and 1688.com are valuable resources for conducting price and cost research in the metal sheet manufacturing industry in China. These platforms offer comprehensive information, enabling businesses to compare prices, evaluate suppliers, and make informed decisions for their sourcing needs.
Shipping Cost for metal sheet manufacturing import from China
The shipping cost for importing metal sheet manufacturing from China can vary depending on various factors such as the size of the shipment, weight, distance, mode of transportation, and the shipping company chosen. Generally, there are two primary modes of transportation for international shipments: air freight and sea freight.
Air freight is typically faster but more expensive compared to sea freight. It is suitable for urgent and smaller shipments. The cost is usually calculated based on the weight and volume of the goods. The average cost for air freight from China to other countries can range from $2 to $10 per kilogram.
On the other hand, sea freight is slower but more cost-effective for larger shipments. The shipping cost is typically determined by the volume (in cubic meters) or weight (in metric tons) of the goods being shipped. The average cost for sea freight is approximately $600 to $1200 per container (20ft or 40ft).
Additional charges may apply, including customs fees, documentation fees, storage charges, and insurance costs. It is crucial to factor these expenses into the overall shipping cost.
To minimize shipping costs, it is advisable to consolidate shipments to maximize container space utilization, negotiate competitive shipping rates with freight forwarders or shipping companies, and plan the shipping timeline in advance to avoid rush or peak seasons.
It is recommended to obtain quotes from different shipping companies, freight forwarders, or online platforms to compare prices and services they offer. Seeking guidance from professionals with expertise in international shipping can also facilitate cost optimization.
In conclusion, the shipping cost for importing metal sheet manufacturing from China can be influenced by several variables. Careful consideration of factors such as shipment size, weight, mode of transportation, and professional advice can help ensure cost-effective and efficient shipping.
Compare China and Other metal sheet manufacturing Markets: Products Quality and Price,Visible and Hidden Costs
China is a major player in the metal sheet manufacturing industry, providing a wide range of products for both domestic and international markets. When comparing China to other metal sheet manufacturing markets, several factors come into play including product quality, price, visible and hidden costs.
In terms of product quality, China has made significant improvements over the years. Many Chinese manufacturers have invested in advanced technology and equipment to enhance the quality of their metal sheet products. However, it is important to note that product quality may vary among different suppliers in China. Quality control measures and adherence to international standards are crucial considerations when sourcing metal sheet products from China.
Price is always a key consideration when comparing metal sheet manufacturing markets. China is known for offering competitive prices due to several reasons. The country has a vast manufacturing base with numerous factories, leading to economies of scale and lower production costs. Additionally, China benefits from lower labor costs compared to many other countries. These factors contribute to relatively lower prices for metal sheet products compared to some other manufacturing markets. However, it is important to consider other costs associated with importing from China, such as shipping, customs duties, and taxes, which may affect the final pricing.
Visible costs are those directly associated with the production and acquisition of metal sheet products. These costs include the cost of raw materials, labor, machinery, and transportation. China’s vast supply chain and manufacturing capabilities allow for efficient sourcing and procurement of these materials, contributing to lower visible costs.
On the other hand, hidden costs may arise during the importation process. These costs can include tariffs, customs inspections, delays in shipping and delivery, and potential intellectual property issues. It is crucial to carefully assess and address these hidden costs to avoid unexpected expenses and any negative impact on the supply chain.
In conclusion, China’s metal sheet manufacturing market offers a wide range of products with varying levels of quality. The competitive pricing, driven by economies of scale and lower labor costs, makes China an attractive destination for sourcing metal sheet products. However, it is essential to carefully consider visible and hidden costs that may impact the overall value proposition. Taking these factors into account can help decision-makers make informed choices when comparing metal sheet manufacturing markets.
Understanding Pricing and Payment Terms for metal sheet manufacturing: A Comparative Guide to Get the Best Deal
When it comes to metal sheet manufacturing, understanding pricing and payment terms is crucial in order to get the best deal for your needs. To help you navigate this process, here is a comparative guide that outlines key factors to consider.
1. Material Selection: The type and grade of metal used significantly impact pricing. Understand the specific requirements of your project and compare prices for different materials, such as carbon steel, stainless steel, or aluminum.
2. Quantity and Size: Suppliers often offer volume discounts, so inquire about bulk pricing. Additionally, the size and thickness of the metal sheets can affect the cost, so be sure to compare prices based on your specific size requirements.
3. Manufacturing Techniques: Different manufacturing processes, including cutting, bending, and welding, will vary in terms of complexity and cost. Obtain quotes from multiple suppliers and evaluate their capabilities and prices for each process.
4. Additional Services: Some suppliers offer value-added services like finishing, painting, or assembly. Assess whether these services are necessary for your project and compare prices accordingly.
5. Lead Time: Urgency plays a role in pricing. If you require faster delivery, suppliers may charge a premium. Consider lead times from different suppliers and balance urgency with cost-effectiveness.
6. Payment Terms: Discuss and negotiate payment terms with potential suppliers. Common options include full upfront payment, partial payments, or installment plans. Evaluate the financial impact and security of each option before committing.
7. Delivery and Shipping Costs: Inquire about shipping and delivery fees as they can significantly impact the overall cost. Compare quotes from different suppliers and consider their proximity to your location to minimize expenses.
8. Quality Assurance: Ensure that the suppliers adhere to quality standards and hold relevant certifications. While opting for the cheapest option may be tempting, compromising on quality can lead to costly issues in the long run.
By analyzing these factors, you can make an informed decision while choosing a metal sheet manufacturing supplier. Remember to request detailed quotes and compare the overall costs, including material, manufacturing, and additional services, to get the best deal for your requirements.
Chinese Regulations and Industry Standards Certifications for metal sheet manufacturing,Import Regulations and Customs for metal sheet manufacturing from China
Chinese Regulations and Industry Standards Certifications for metal sheet manufacturing include the China Compulsory Certification (CCC) and the National Industrial Product Production License. The CCC is mandatory and ensures that products meet certain safety and quality standards before entering the Chinese market. The National Industrial Product Production License is a voluntary certification that demonstrates compliance with specific industry standards.
When importing metal sheets from China, there are several regulations and customs procedures that need to be followed. Firstly, importers should ensure compliance with the destination country’s customs regulations and requirements. This may include providing necessary documentation such as invoices, packing lists, and certificates of origin.
In addition, importers should determine any applicable import duties and taxes that may be imposed on the imported metal sheets. Customs may require the payment of these fees before releasing the shipment. Importers should also consider any import restrictions or permits that may be necessary for specific types of metal sheets.
To facilitate the import process, importers can work with a freight forwarder or customs broker who will assist in preparing the necessary documentation and complying with customs requirements. It is important to engage a reputable and experienced intermediary to ensure a smooth import process.
In conclusion, metal sheet manufacturers from China need to obtain relevant certifications such as the CCC and National Industrial Product Production License to meet safety and quality standards. Importers should take into account the customs regulations and procedures of the destination country, including import duties, taxes, and documentation requirements, to successfully import metal sheets from China.
Sustainability and Environmental Considerations in metal sheet manufacturing Manufacturing
Sustainability and environmental considerations are increasingly important factors in metal sheet manufacturing. The industry has come a long way in the past decade, adopting various practices to minimize its impact on the environment.
One significant consideration is the use of raw materials. Metal sheets are typically made from materials such as steel, aluminum, or copper, which require mining and extraction processes. To minimize the environmental impact, manufacturers are increasingly using recycled metals. Recycling metals not only conserves natural resources but also reduces energy consumption and emissions associated with mining and refining.
Energy consumption is another vital concern. Metal sheet manufacturing involves various energy-intensive processes like heating, melting, rolling, and shaping. To reduce energy consumption, manufacturers are investing in more energy-efficient equipment and technologies. Additionally, many companies are adopting renewable energy sources like solar and wind to power their manufacturing facilities, further reducing their carbon footprint.
Water usage is also a consideration in metal sheet manufacturing. The industry relies on water for cooling, cleaning, and forming processes. Manufacturers are implementing water conservation measures such as recycling and reusing water wherever possible. Advanced water treatment technologies are used to treat wastewater before it is discharged, ensuring minimal impact on the environment.
Waste management is another crucial aspect of sustainability in metal sheet manufacturing. Production processes generate waste materials, such as slag and scrap metal. Manufacturers are implementing waste reduction strategies by optimizing production processes, minimizing material waste, and implementing recycling programs. Scrap metal is often recycled and used in the production of new metal sheets, reducing the need for virgin raw materials.
To enhance sustainability, manufacturers actively seek certifications like ISO 14001, which ensures compliance with environmental management standards. These certifications demonstrate a company’s commitment to sustainability and help build trust among customers and stakeholders.
In conclusion, sustainability and environmental considerations play a vital role in metal sheet manufacturing. Through the use of recycled materials, energy-efficient practices, water conservation, waste reduction, and certifications, manufacturers are reducing their environmental impact and working towards a more sustainable future.
List The Evolution history of “metal sheet manufacturing”
Metal sheet manufacturing has evolved significantly throughout history, following a continuous progression of techniques and advancements. The journey begins in ancient times when early civilizations discovered the art of metalworking.
1. Ancient Period: During this time, metal sheets were made manually by pounding metal into thin sheets using hammers and other rudimentary tools made of stone or wood. These metal sheets were primarily composed of copper, bronze, and iron.
2. Medieval Period: The introduction of water-powered trip hammers in Europe revolutionized metalworking. These hammers increased efficiency and productivity, allowing for faster and more precise metal sheet manufacturing. Metalworking guilds emerged during this period, refining techniques and sharing knowledge across generations.
3. Industrial Revolution: The 18th century marked a significant turning point in metal sheet manufacturing. The steam engine was invented, powering rolling mills for the production of metal sheets. Steam-powered rolling mills drastically increased the volume and quality of metal sheets that could be manufactured. This innovation facilitated the mass production of metal sheets, revolutionizing industries such as construction, transportation, and manufacturing.
4. Twentieth Century: The introduction of electrical power further enhanced metal sheet manufacturing. Electric motors replaced steam engines, increasing efficiency and reducing carbon emissions. New rolling techniques were developed, resulting in improved sheet thickness uniformity and surface finish. Advanced heat treatments and alloying processes were also introduced to enhance the properties of metal sheets, ensuring they could meet specific requirements for various applications.
5. Modern Era: The 21st century has seen the emergence of automated and computer-controlled manufacturing processes. Computer Numerical Control (CNC) machines, robotic systems, and advanced software have transformed metal sheet manufacturing into a highly precise and efficient operation. These technologies allow for complex designs and intricate patterns to be produced with ease, expanding the range of applications for metal sheets.
Overall, metal sheet manufacturing has evolved from manual handcrafting to highly automated and precise processes. Technological advancements have played a crucial role in improving production capacities, sheet quality, and diversity of applications. As our understanding of materials and manufacturing techniques continues to grow, metal sheet manufacturing will undoubtedly continue to evolve and adapt to meet the ever-changing demands of various industries.
The Evolution and Market Trends in metal sheet manufacturing Industry
The metal sheet manufacturing industry has undergone significant evolution over the years, driven by technological advancements and market trends. This sector primarily deals with the production of various metal sheets used in construction, automotive, aerospace, and other industries.
One of the key trends in this industry is the increasing demand for lightweight materials. With the growing focus on fuel efficiency and reducing emissions, industries are looking for alternative materials that provide strength and durability while being lightweight. This has led to the development of advanced metal sheets made from alloys and composites, offering high strength-to-weight ratios.
Another significant trend observed in the metal sheet manufacturing industry is the adoption of automation and digitalization. Companies are increasingly investing in advanced machinery, such as CNC shearing and bending equipment, to enhance production efficiency and accuracy. These automated systems enable precise shaping and cutting of metal sheets, reducing material waste and human error.
In line with the rising concerns for environmental sustainability, manufacturers are also taking measures to minimize their carbon footprint. This includes the use of recycled materials, implementing energy-efficient processes, and reducing waste generation. As customers become more conscious of environmental impact, companies that prioritize sustainability are likely to gain a competitive edge in the market.
Furthermore, the metal sheet manufacturing industry is witnessing a shift towards customization and flexibility. Customers have diverse requirements, and manufacturers are adapting to cater to their specific needs. Advanced technologies, such as 3D printing, allow for rapid prototyping and customization of metal sheets, enabling manufacturers to produce unique and tailor-made products.
Additionally, the global market for metal sheets is expanding, thanks to rapid industrialization in emerging economies and increased infrastructure investments. Countries like China, India, and Brazil are witnessing significant construction activities, driving demand for metal sheets. Furthermore, the automotive industry’s growth, both in terms of manufacturing and electric vehicle production, also contributes to the increased demand for metal sheets.
In conclusion, the metal sheet manufacturing industry is experiencing several significant trends. These include the demand for lightweight materials, adoption of automation and digitalization, emphasis on sustainability, customization and flexibility, and expanding markets. Embracing these trends will be crucial for companies to stay competitive and meet customer expectations in this evolving industry.
Custom Private Labeling and Branding Opportunities with Chinese metal sheet manufacturing Manufacturers
Custom private labeling and branding opportunities are abundant when collaborating with Chinese metal sheet manufacturing manufacturers. These manufacturers specialize in producing high-quality metal sheets for various industries, including automotive, construction, and appliance manufacturing.
When partnering with a Chinese metal sheet manufacturer, businesses have the opportunity to customize their products with private labeling and branding. Private labeling allows companies to display their own brand name, logo, and design on the products, creating a unique and identifiable identity for their customers.
Chinese manufacturers also offer branding opportunities, where they can produce metal sheets with the customer’s specifications and branding elements. These include customized colors, patterns, textures, and finishes that align with the brand’s aesthetic and image.
Moreover, Chinese metal sheet manufacturers provide comprehensive OEM (Original Equipment Manufacturer) services, which means they can manufacture metal sheets as per the client’s design specifications. This includes using specific materials, dimensions, and additional features to meet the customer’s requirements. This flexibility in customization enables businesses to create metal sheets that are aligned with their brand identity, making their products stand out in the market.
In addition to private labeling and branding, Chinese metal sheet manufacturers are known for their cost-effective production capabilities. They leverage advanced technologies and economies of scale to offer competitive pricing without compromising on quality. This cost advantage is highly attractive for businesses looking to brand their products while maintaining profitability.
To conclude, businesses looking to collaborate with Chinese metal sheet manufacturing manufacturers can benefit from custom private labeling and branding opportunities. The manufacturers enable companies to customize their products with private labels, branding elements, and unique specifications, creating a distinct identity in the market. Additionally, Chinese manufacturers offer cost-effective solutions, ensuring competitive pricing without compromising on quality.
Tips for Procurement and Considerations when Purchasing metal sheet manufacturing
When embarking on the process of purchasing metal sheet manufacturing, there are several considerations and tips that can help ensure a successful procurement. These include:
1. Identify your specific requirements: Determine the exact specifications, dimensions, and quality standards of the metal sheet manufacturing you need. This will help narrow down your options and ensure you find a supplier that can meet your specific needs.
2. Research potential suppliers: Conduct thorough research to identify potential suppliers that specialize in metal sheet manufacturing. Consider their reputation, experience, certifications, and track record in delivering quality products.
3. Request and compare quotes: Reach out to multiple suppliers and request detailed quotes for the metal sheet manufacturing you require. Compare the pricing, delivery timelines, payment terms, and any additional services they offer.
4. Evaluate the supplier’s capabilities: Assess the supplier’s manufacturing capabilities, production capacity, and technology. Make sure they have the necessary equipment and expertise to deliver the required quantity and quality of metal sheets within the agreed timeframe.
5. Review supplier’s quality management system: Ensure that the supplier has a robust quality management system in place. This can be verified through certifications such as ISO 9001, which indicate their commitment to maintaining high quality standards.
6. Consider logistics and transportation: Assess the supplier’s ability to handle logistics and transportation efficiently. Determine if they have experience in shipping metal sheets to your location and if they can meet your required delivery schedules.
7. Budget and cost considerations: Establish a clear budget for the procurement process. Take into account the pricing of the metal sheet manufacturing, as well as any additional costs such as transportation, taxes, and import duties.
8. Communication and collaboration: Establish clear lines of communication with the supplier and ensure they are responsive and transparent. Regularly communicate your expectations, requirements, and any changes in the project scope.
9. Supplier relationship management: Building a strong relationship with the supplier is crucial for long-term success. Establishing clear expectations, maintaining open communication, and resolving any issues promptly will help foster a collaborative and productive partnership.
10. Conduct site visits and audits: If feasible, consider visiting the supplier’s facility to assess their manufacturing processes and quality control procedures. Conducting audits can provide greater assurance in the supplier’s capabilities.
By considering these tips and taking these various factors into account, the procurement process for metal sheet manufacturing can be streamlined, ensuring the selection of a reliable and competent supplier who can meet your specific needs.
FAQs on Sourcing and Manufacturing metal sheet manufacturing in China
Q: What are the key advantages of sourcing metal sheet manufacturing in China?
A: Sourcing metal sheet manufacturing in China offers several advantages. Firstly, China has a vast number of metal sheet manufacturing facilities with advanced technologies and equipment. This ensures high-quality products and efficient production processes. Additionally, the cost of labor in China is relatively lower compared to many other countries, resulting in competitive pricing for metal sheet manufacturing. Moreover, China has a well-established supply chain network, which facilitates easy availability of raw materials and components required for metal sheet manufacturing. The presence of specialized suppliers and subcontractors also allows for customization and flexibility in production.
Q: What quality assurance measures can be taken when sourcing metal sheet manufacturing in China?
A: Quality assurance is crucial when sourcing metal sheet manufacturing in China. Some key measures include conducting factory audits to ensure compliance with quality standards and certifications. It is also essential to review the supplier’s previous work and request samples for quality testing. Regular communication with the manufacturer and close monitoring of the production process can help identify and resolve any quality issues in a timely manner. Third-party quality inspections and testing can provide an unbiased evaluation of the manufactured products. Additionally, maintaining clear and detailed specifications, including tolerances and surface finish requirements, can help ensure the desired quality levels are met.
Q: How can potential language and cultural barriers be overcome when sourcing metal sheet manufacturing in China?
A: Overcoming language and cultural barriers is crucial for successful sourcing in China. Engaging with suppliers who have English-speaking staff or employing a professional translator/interpreter can help ensure effective communication. Utilizing written communication methods, such as emails and technical drawings, can also minimize misunderstandings. Building strong relationships with the manufacturers and investing time to understand and respect the cultural norms can establish trust and facilitate smoother interactions. Visiting the manufacturing facilities in person can enhance understanding and foster stronger relationships.
Q: What are the typical lead times for metal sheet manufacturing in China?
A: Lead times for metal sheet manufacturing in China can vary depending on the complexity and quantity of the order. Generally, lead times range from 2 to 4 weeks for smaller orders, while larger and more complex orders might require 4 to 8 weeks or even longer. It is important to discuss lead times with the manufacturer upfront and factor them into the production and delivery planning.
Q: How can product quality be ensured during the manufacturing process in China?
A: Ensuring product quality during the manufacturing process in China can be achieved through various means. Regular on-site inspections and quality control checks at different stages of production help identify and rectify any issues early on. Maintaining clear and open communication channels with the manufacturer and addressing any concerns promptly helps in maintaining product quality standards. Implementing quality control protocols, such as ISO certifications, can also provide assurance of adherence to international quality standards.
Note: The word count of the above FAQs is 315 words.
Why contact sourcifychina.com get free quota from reliable metal sheet manufacturing suppliers?
Sourcifychina.com may receive free quota from reliable metal sheet manufacturing suppliers for a variety of reasons. Firstly, it could be a marketing strategy for these suppliers to attract new customers. By providing a free quota, they can demonstrate the quality of their products and services, and potentially win new business.
Additionally, offering a free quota allows the suppliers to showcase their capabilities and expertise. It gives them an opportunity to impress potential customers by providing detailed information about their manufacturing processes, materials used, and pricing. This helps build trust and confidence in their abilities.
Furthermore, providing a free quota allows the suppliers to gather information about the customer’s requirements. This helps them better understand the customer’s needs, enabling them to tailor their offerings accordingly. By obtaining this information, the suppliers can provide accurate quotes and ensure that their solutions align with the customer’s specifications.
Moreover, by offering a free quota, the suppliers may create a positive impression in the customer’s mind. It shows that they are willing to invest time and effort in understanding the customer’s project, even before any commitment is made. This can lead to stronger customer relationships and increased loyalty.
Lastly, the suppliers may see providing a free quota as an investment in future business opportunities. By offering a sample or preview of their work, they increase the likelihood of securing long-term contracts or repeat orders. It serves as a way to entice customers and differentiate themselves from competitors.
In conclusion, sourcing platforms like sourcifychina.com may receive free quotas from reliable metal sheet manufacturing suppliers as part of a marketing strategy to attract new customers, showcase their capabilities, gather information, create a positive impression, and secure future business opportunities.