Introduce about smc manufacturing guide,Qulity,Cost,Supplier,Certification,Market,Tips,FAQ
SMC manufacturing, also known as Sheet Molding Compound manufacturing, is a process used to create lightweight, durable, and cost-effective products. This guide aims to provide an overview of key aspects related to SMC manufacturing, including quality, cost, suppliers, certifications, markets, tips, and frequently asked questions (FAQs).
Quality is a crucial factor in SMC manufacturing. The process involves combining different materials, such as polyester resin, chopped glass fibers, and fillers, to create a compound that is then molded into the desired shape. Ensuring high-quality materials and maintaining strict manufacturing standards is essential to produce SMC parts that meet customer requirements for strength, appearance, and dimensional accuracy.
Cost considerations play a significant role in SMC manufacturing. The cost of raw materials, machinery, and labor influence the overall production costs. However, SMC’s ability to be molded rapidly and efficiently reduces labor costs compared to traditional manufacturing methods. Additionally, the lightweight nature of SMC products contributes to cost savings in transportation and installation.
Finding reliable suppliers is crucial for successful SMC manufacturing. Suppliers should have expertise in producing high-quality SMC materials and be capable of meeting production volume requirements. It is advisable to select suppliers with a proven track record, adequate infrastructure, and a commitment to quality assurance to ensure a smooth manufacturing process.
Certifications are vital in SMC manufacturing, as they signify adherence to industry standards and quality control processes. Common certifications include ISO 9001 for quality management systems and ISO 14001 for environmental management systems. Other industry-specific certifications may also be required based on the targeted market or specific product applications.
The market for SMC products is diverse and extensive. SMC components find applications in various industries, including automotive, aerospace, electrical, and construction. The lightweight, corrosion-resistant, and high-strength properties of SMC make it an attractive choice for manufacturers across different sectors.
Here are some tips to consider when engaging in SMC manufacturing:
1. Conduct thorough research on material suppliers, their expertise, and track record.
2. Optimize the design and mold tooling to minimize material wastage during the manufacturing process.
3. Implement efficient quality control measures to ensure consistent product performance.
4. Stay updated on industry advancements, such as new materials or manufacturing technologies, to enhance product competitiveness.
Lastly, let’s address a few frequently asked questions (FAQs) regarding SMC manufacturing:
Q: Can SMC be painted or coated?
A: Yes, SMC parts can be painted or coated to enhance aesthetics and provide additional protection against external factors.
Q: Can SMC parts be recycled?
A: Yes, SMC parts can be recycled and used in various applications, contributing to sustainability efforts.
Q: Is SMC suitable for high-temperature environments?
A: Yes, SMC can withstand high temperatures and is often used in applications such as engine components or industrial equipment.
Overall, SMC manufacturing offers numerous advantages in terms of quality, cost, versatility, and sustainability. By understanding the key aspects highlighted in this guide, manufacturers can effectively leverage SMC for their specific manufacturing needs.
Types of smc manufacturing
There are several types of Surface Mounting Technology (SMT) manufacturing processes used in the electronics industry. SMT is a method of mounting electronic components directly onto the surface of a printed circuit board (PCB), without the need for through-hole connections. This manufacturing technique offers several advantages, including smaller and lighter designs, improved electrical performance, and faster production.
1. Surface Mount Technology (SMT): This is the most commonly used method for SMT manufacturing. In this process, components are mounted directly onto the surface of the PCB using automated pick-and-place machines. The components are held in place by solder paste, which is a mixture of powdered solder and flux, applied to the pads of the PCB. The PCB is then heated to melt the solder and create a reliable electrical connection.
2. Chip-on-Board (COB): COB manufacturing involves mounting integrated circuits directly onto the PCB, without the use of packaged components. The ICs are usually bare chips that are glued onto the PCB surface, wire bonded, and encapsulated with epoxy for protection. COB is often used in applications where space and weight considerations are critical, such as in portable electronic devices.
3. Ball Grid Array (BGA): BGA manufacturing involves mounting components onto the PCB using an array of small solder balls located on the component’s underside. The component is placed onto the PCB, and the solder balls make contact with corresponding pads on the PCB. The assembly is then heated to reflow the solder and create electrical connections. BGAs are commonly used for high-density and high-performance applications due to their excellent electrical and thermal properties.
4. Wafer Level Chip Scale Package (WLCSP): WLCSP manufacturing is a variation of BGA, where the packaged integrated circuit is directly mounted onto the PCB. WLCSPs have very small form factors, similar to bare chips, allowing for miniaturization of electronic devices. This process involves handling the IC on a wafer before dicing it into individual chips, applying solder bumps to the sensitive pads of the IC, and mounting it directly onto the PCB.
5. Package-on-Package (PoP): PoP manufacturing involves stacking multiple IC packages vertically, one on top of another, to achieve higher component density in a smaller footprint. This technique is often used in devices where both logic and memory functions need to be integrated into a single module.
These are just a few of the common types of SMT manufacturing processes used in the electronics industry. Each method offers unique advantages and is suited for specific applications, allowing manufacturers to create increasingly compact and advanced electronic devices.
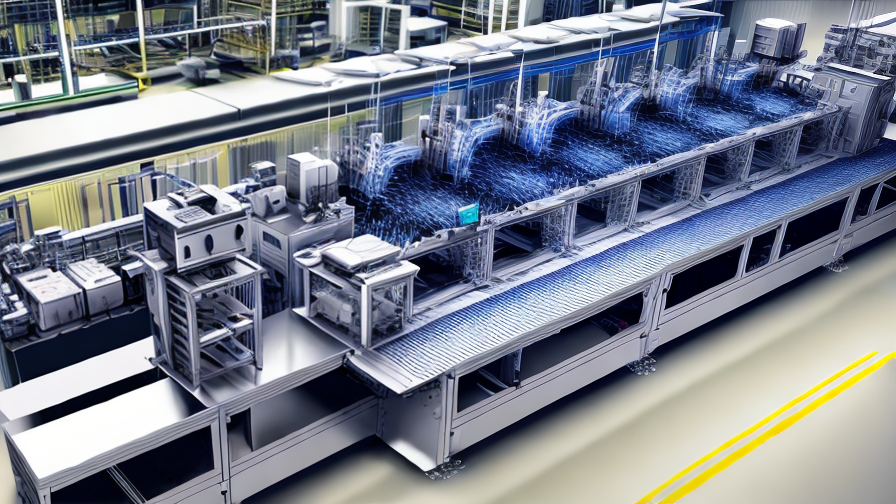
Pros and Cons of Using smc manufacturing
SMC (Sheet Molding Compound) manufacturing is a widely used technique in the production of various composite materials. It offers several advantages and disadvantages that should be considered before using it.
One of the major pros of SMC manufacturing is its versatility. SMC can be molded into complex shapes with high precision, allowing manufacturers to create intricate and customized components. This flexibility makes it suitable for a wide range of industries such as automotive, aerospace, and construction.
Another advantage of SMC manufacturing is the excellent strength-to-weight ratio it offers. SMC products are lightweight yet highly durable, making them ideal for applications where weight reduction is essential. This not only improves the overall product performance but also contributes to fuel efficiency and reduces transportation costs.
SMC materials also exhibit good resistance to corrosion, chemical exposure, and UV radiation, making them suitable for harsh environments. Additionally, SMC parts have excellent electrical insulation properties, making them safe for use in electrical and electronic applications.
SMC manufacturing also enables cost savings. The production process is highly efficient, with reduced cycle times and minimal material wastage. Moreover, SMC materials have a long service life and require minimal maintenance, resulting in lower life-cycle costs.
However, there are also some cons to consider when using SMC manufacturing. One major drawback is the high initial setup costs. Specialized equipment and molds are required for SMC production, which can be expensive for small-scale manufacturers. Additionally, the curing process of SMC materials is time-consuming, which can lead to longer production lead times.
Another limitation of SMC manufacturing is the limited design flexibility compared to other manufacturing techniques such as injection molding. SMC parts may have restrictions on wall thickness, undercuts, and intricate details. This can restrict the design possibilities, especially for highly complex components.
Furthermore, the inconsistency of mechanical properties across different parts is a challenge in SMC manufacturing. Variations in fiber content, resin distribution, and curing conditions can lead to inconsistencies in part quality, resulting in strength variations.
In conclusion, SMC manufacturing offers numerous advantages such as versatility, lightweight properties, and resistance to environmental factors. It can also lead to cost savings in the long run. However, the high initial setup costs, limited design flexibility, and potential inconsistencies in mechanical properties should be recognized as potential drawbacks.
smc manufacturing Reference Specifications (varies for different product)
SMC Manufacturing is a leading company specializing in the production of various products, ranging from electronics to automotive components. We take pride in delivering high-quality products that meet and exceed industry standards. To ensure the finest manufacturing processes, we adhere to a set of reference specifications that vary depending on the product. Here are some commonly used reference specifications:
1. Material: We carefully select the materials for each product to ensure durability and performance. Common materials include metals (such as aluminum, steel, and copper), plastics, and composites. The choice of material depends on the intended use and specific product requirements.
2. Dimensional Accuracy: We prioritize precision in dimensions to ensure that each product fits perfectly into the desired assembly. Our reference specifications include tolerances that define the acceptable range for various measurements. This ensures uniformity and ease of use across different applications.
3. Surface Finish: The appearance and surface quality of our products are critical. We follow reference specifications to achieve the desired texture, smoothness, and aesthetic appeal. Techniques like polishing, painting, or anodizing may be employed to meet specific requirements.
4. Electrical and Mechanical Performance: Our products often require electrical and mechanical functionality. We have detailed reference specifications that outline the performance criteria such as voltage, current, power output, torque, and speed. These specifications ensure that our products meet the expectations of our customers and perform reliably.
5. Safety Standards: Safety is of utmost importance to us, and we strictly adhere to reference specifications to meet regulatory and industry safety standards. Our products undergo rigorous testing to verify compliance with these specifications, ensuring the well-being of our customers.
These reference specifications are essential in maintaining our commitment to producing high-quality products. They guide our manufacturing processes, ensuring consistency, reliability, and customer satisfaction. By adhering to these specifications, we guarantee that each product meets or exceeds the required standards. At SMC Manufacturing, we continuously update and improve our reference specifications to stay at the forefront of the industry and deliver products of the highest caliber.
Applications of smc manufacturing
SMC manufacturing, short for Sheet Molding Compound manufacturing, is a versatile and cost-effective process used in various industries. SMC is a composite material made up of chopped glass fibers, unsaturated polyester resin, and additives. This combination results in a high-strength, lightweight, and corrosion-resistant material, suitable for a wide range of applications. Let’s explore some of the key industries that benefit from SMC manufacturing.
1. Automotive Industry: SMC is extensively used in the automotive sector to produce lightweight components such as body panels, hoods, bumpers, and interior parts. The lightweight nature of SMC helps to reduce the overall weight of the vehicle, resulting in improved fuel efficiency and reduced emissions. Furthermore, SMC offers excellent design flexibility, allowing for complex and aerodynamic shapes.
2. Construction Industry: SMC is gaining popularity in the construction industry due to its durability, insulation properties, and resistance to harsh weather conditions. It is commonly used in the production of prefabricated building panels, bathroom modules, and utility enclosures. SMC-based products offer enhanced strength-to-weight ratios, reducing transportation costs and labor efforts during installation.
3. Electrical/Electronics Industry: SMC manufacturing finds applications in electrical and electronics components due to its excellent electrical insulation properties. It is used to produce cases for electrical equipment, enclosures for electrical distribution systems, insulating boards, and circuit breaker housings. SMC’s dimensional stability and resistance to high temperatures make it ideal for these applications, ensuring reliable performance and safety.
4. Aerospace Industry: SMC is widely utilized in the aerospace industry for parts that require strength, lightness, and resistance to corrosion. It is used to manufacture aircraft interior components, exterior panels, engine nacelles, and structural supports. The high strength-to-weight ratio of SMC enables the production of lightweight aircraft, improving fuel efficiency and reducing operating costs.
5. Consumer Goods: SMC manufacturing also plays a significant role in creating consumer goods such as furniture, household appliances, and recreational products. Manufacturers can leverage SMC’s ability to replicate various textures and finishes, allowing for appealing designs. SMC-based consumer goods offer advantages like reduced weight, increased durability, and resistance to impact and chemical exposure.
In conclusion, SMC manufacturing has a wide range of applications across industries due to its lightweight, sturdy, and corrosion-resistant properties. Its versatility and cost-effectiveness make it a preferred choice for producing various components, from automotive parts to aerospace structures and consumer goods. As technology and manufacturing processes continue to evolve, the applications of SMC are likely to expand further, contributing to enhanced product performance and sustainability.
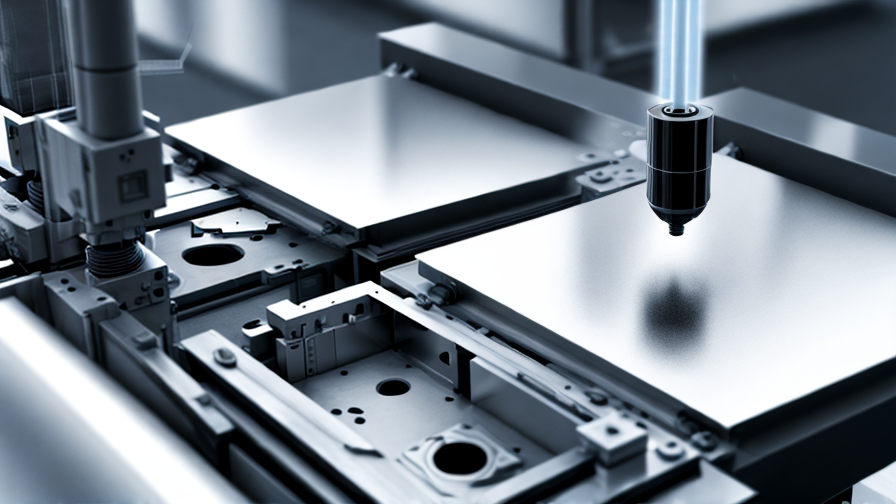
The Work Process and how to use smc manufacturing
SMC manufacturing, also known as Sheet Molding Compound manufacturing, is a process used in the production of various composite materials. It involves the compression and molding of resin and reinforcing fibers to create strong and lightweight finished products. Here is a simplified explanation of the work process involved in SMC manufacturing.
1. Material Preparation: The process begins with the preparation of raw materials, which include resin, reinforcing fibers (such as glass or carbon fibers), fillers, and additives. These materials are carefully measured and mixed to create a homogenous mixture known as the SMC.
2. Molding: The SMC is then placed into a mold cavity that is pre-treated with a release agent to prevent sticking. The mold is typically made of two halves that fit together precisely. The SMC is spread evenly and accurately within the mold to ensure consistent quality.
3. Compression: The mold halves are closed and clamped tightly, applying pressure to the SMC. The pressure ensures proper flow and compaction of the materials to eliminate voids and air bubbles. The amount and duration of compression vary depending on the desired characteristics of the final product.
4. Curing: After compression, the mold is heated to initiate the curing process. Heat causes the resin to react and harden, bonding the reinforcing fibers together. The curing temperature and time are carefully controlled to achieve the desired physical and mechanical properties of the product.
5. Demolding: Once cured, the mold is opened, and the finished product is removed. The demolding process requires precision to prevent any damage or deformation to the part. In some cases, additional post-processing steps such as trimming, drilling, or painting may be carried out to achieve the desired final product.
SMC manufacturing offers several advantages, including high strength-to-weight ratio, corrosion resistance, and complex shape capabilities. It is commonly used in various industries, such as automotive, aerospace, construction, and electrical applications.
In conclusion, SMC manufacturing involves the preparation of SMC materials, molding the SMC mixture in a precisely pre-treated mold, compressing it under pressure, curing it through heating, and finally demolding the finished product. Understanding this process can help businesses make informed decisions when choosing SMC manufacturing for their composite material needs.
Quality Testing Methods for smc manufacturing and how to control the quality
Quality testing methods for SMC (Sheet Molding Compound) manufacturing involve a range of techniques to ensure that the final product meets the required quality standards. SMC is a composite material commonly used in industries like automotive, aerospace, and construction due to its excellent mechanical properties and high strength-to-weight ratio. Effective quality control measures are essential to guarantee the reliability and performance of SMC products.
One commonly used testing method is visual inspection, which involves carefully examining the surface of the SMC components for any visible defects such as cracks, voids, or surface imperfections. This method is relatively simple and inexpensive, providing immediate feedback on the quality of the components.
Another important quality testing method for SMC manufacturing is mechanical testing. This involves subjecting the SMC components to various mechanical stresses to evaluate their strength, stiffness, and impact resistance. Tensile, flexural, and impact tests are commonly conducted to verify if the material meets the required specifications and performance criteria.
Furthermore, dimensional inspection is crucial to ensure that the SMC components are manufactured within the acceptable tolerances. This involves using precise measuring tools to verify the dimensions of the components are within the specified ranges. Any deviations from the desired dimensions can affect the functionality and fitment of the SMC parts.
Additionally, chemical analysis can be carried out to verify the composition of SMC materials and ensure that they meet the required chemical specifications. This analysis helps identify any impurities or variations in the raw materials that may affect the quality and performance of the final product.
To control the quality of SMC manufacturing, it is essential to implement a comprehensive quality management system. This includes defining clear quality standards, establishing process controls, conducting regular inspections, and implementing corrective and preventive actions to address any deviations or non-conformities. Proper documentation and record-keeping of test results, process parameters, and material specifications are also vital for traceability and quality assurance purposes.
Ensuring the competence and training of personnel involved in SMC manufacturing is crucial for achieving consistent quality. Ongoing training programs and performance evaluations can help maintain a skilled workforce capable of carrying out quality tests and implementing quality control measures effectively.
By utilizing a combination of visual inspection, mechanical testing, dimensional inspection, and chemical analysis, coupled with a robust quality management system and well-trained personnel, SMC manufacturers can control the quality of their products throughout the manufacturing process.
smc manufacturing Sample Policy and Post-Purchase Considerations for smc manufacturing from China
Sample Policy:
At smc manufacturing, our goal is to ensure customer satisfaction by providing high-quality products from our trusted manufacturing partners in China. We understand that occasionally issues may arise after purchasing our products, and we have developed the following policies to address any concerns:
1. Return and Exchange Policy: If you encounter any defects or damages in the products purchased from smc manufacturing, please notify us within 7 days of receiving the shipment. We will arrange for the return or exchange of the faulty items at no additional cost.
2. Warranty Policy: All products from smc manufacturing come with a 1-year limited warranty. If any defects occur within this time frame, we will repair or replace the item free of charge.
3. Communication and Support: Our customer service team is always available to assist you with any post-purchase questions or concerns. You can reach us via email, phone, or our online chat platform.
Post-Purchase Considerations:
When purchasing products from smc manufacturing in China, it is essential to consider the following factors:
1. Quality Control: We maintain a rigorous quality control process to ensure that all products meet our high standards before shipment. However, it is recommended to check the product upon arrival to address any potential issues promptly.
2. Shipping and Importation: smc manufacturing takes care of the shipping and importation process from China to minimize any inconvenience for our customers. However, it is important to be aware of any specific import regulations or customs duties in your country.
3. Language and Cultural Differences: Communication with our manufacturing partners in China may require patience due to language and cultural differences. We ensure effective communication between all parties to avoid any misunderstandings.
4. Feedback: We highly appreciate customer feedback regarding their experience with our products and services. Your feedback helps us continuously improve our offerings and address any areas of concern.
smc manufacturing strives to provide a seamless experience for our customers, from the initial purchase to after-sales support. We are committed to resolving any concerns promptly and ensuring your satisfaction with our products from China.
Sourcing smc manufacturing from China: Opportunities, Risks, and Key Players
Sourcing SMC manufacturing from China offers both opportunities and risks for businesses. China is known for its efficient and cost-effective manufacturing capabilities, making it an attractive option for companies looking to produce SMC (Sheet Molding Compound) products. The country has a large pool of skilled labor, a well-established supply chain, and advanced manufacturing technologies.
One key opportunity of sourcing SMC manufacturing from China is the cost advantage. Chinese manufacturers often offer competitive pricing due to lower labor and production costs. This cost advantage allows businesses to reduce their overall production expenses and potentially increase profit margins.
Additionally, China’s vast manufacturing infrastructure provides companies with access to a wide range of suppliers and materials. This enables businesses to have a diverse range of options and flexibility in sourcing different components required in SMC manufacturing. Moreover, Chinese manufacturers usually have quick turnaround times, allowing businesses to meet tight production deadlines.
However, there are also risks associated with sourcing SMC manufacturing from China. Quality control can be a concern as some manufacturers may prioritize cost-cutting measures, resulting in lower quality products. Verifying the quality and reliability of potential suppliers is crucial to avoid product defects or inconsistencies.
Another risk is intellectual property protection. China has faced criticism in the past for intellectual property theft, and businesses must take necessary precautions to protect their designs and patents when sourcing from China. Conducting due diligence, signing non-disclosure agreements, and protecting intellectual property rights are important steps in mitigating these risks.
Some key players in SMC manufacturing in China include Polynt, AOC, and Tianma Group. These manufacturers have extensive experience in producing SMC products and possess the necessary certifications and standards required for international markets. It is essential to conduct research and verify the track record and reputation of potential manufacturers before entering into a partnership.
In conclusion, sourcing SMC manufacturing from China presents opportunities in terms of cost advantage, diverse supplier options, and quick production turnaround. However, businesses must also be aware of the risks associated with quality control and intellectual property protection. Conducting thorough research, due diligence, and selecting reputable manufacturers are vital steps to ensure a successful sourcing process.
How to find and select reliable smc manufacturing manufacturers in China,use google search manufacturers and suppliers
Finding and selecting reliable SMC manufacturing manufacturers in China can be a challenging task, but by following certain steps, it is possible to narrow down the options and make an informed choice.
One of the most effective ways to start the search is through Google. By typing in relevant keywords like “reliable SMC manufacturing manufacturers in China,” a list of potential suppliers will appear. It is important to carefully review the top search results and shortlist a few manufacturers based on their website, reputation, and relevant information.
Once a list of potential suppliers is created, it is essential to assess their credibility and reliability. This can be done by taking several factors into consideration:
1. Company Profile: Carefully review the company’s website to gather information about their history, experience, production capabilities, certifications, and any accolades they may have received.
2. Product Quality: Look for reviews or feedback from other clients to gauge the product quality and reliability of the manufacturer. Check for any product certifications or quality control processes they follow.
3. Manufacturing Facilities: Determine whether the manufacturer has advanced manufacturing facilities with modern machinery and equipment. This ensures their ability to meet production requirements and maintain quality standards.
4. Communication and Customer Support: Evaluate the manufacturer’s responsiveness and willingness to answer queries promptly. Good communication is vital for a successful business relationship.
5. Samples and Prototypes: Request samples or prototypes of the desired SMC products to assess their quality and suitability. This step helps in verifying the manufacturer’s capabilities.
6. Price and Payment Terms: Compare the prices offered by different manufacturers, considering factors like production time, packaging, shipping costs, and payment terms. Remember that the cheapest option may not always be the most reliable.
7. Visit the Factory: If possible, plan a visit to the shortlisted manufacturers to see their manufacturing facilities, meet their team, and get a better understanding of their operations. This step can provide valuable insights into their reliability and professionalism.
By following these steps and conducting thorough research, it is possible to find and select reliable SMC manufacturing manufacturers in China. It is essential to invest time in the selection process to ensure a successful and long-term partnership.
How to check smc manufacturing manufacturers website reliable,use google chrome SEOquake check if ranking in top 10M
To determine the reliability of an SMC manufacturing manufacturer’s website, you can follow these steps using Google Chrome and the SEOquake extension:
1. Install SEOquake: Go to the Chrome Web Store and search for “SEOquake.” Click on the “Add to Chrome” button to install the extension.
2. Visit the manufacturer’s website: Open a new tab in Google Chrome and enter the URL of the manufacturer’s website.
3. Activate SEOquake: On the top-right corner of your browser, you will find the SEOquake icon. Click on it to activate the extension.
4. Check for top 10M ranking: Once SEOquake is activated, a toolbar will appear at the top of your browser window with various options. Look for the “SEM” tab and click on it. Then, within SEM’s submenu, select “Google Index” and choose “Top 10M.”
5. Analyze the ranking: After selecting “Top 10M,” the SEOquake extension will display the ranking of the manufacturer’s website. If it falls within the top 10 million websites according to Google, it indicates that the website receives a reasonable level of traffic and is likely more reliable.
6. Additional considerations: While the top 10M ranking provides a certain level of reliability, it is not the only factor to consider. You may also evaluate other aspects such as the website’s design, user interface, content quality, customer testimonials, and any certifications or partnerships displayed on the site. Additionally, it’s recommended to verify the company’s contact information, such as physical address and phone number, for further authentication.
By using SEOquake and paying attention to the website’s ranking and other reliability indicators, you can assess the trustworthiness of an SMC manufacturing manufacturer’s website.
Top 10 smc manufacturing manufacturers in China
China is renowned for its robust manufacturing industry, and the production of Sheet Molding Compounds (SMC) is no exception. SMC manufacturing refers to the fabrication process for composite materials that are commonly used in various industries such as automotive, aerospace, construction, and electrical, among others. Here is a list of the top 10 SMC manufacturing manufacturers in China:
1. Zhejiang Yueqing SMC/BMC Manufacturing Co., Ltd.: This company specializes in producing SMC/BMC products for electrical and automotive applications, known for their excellent quality and competitive prices.
2. Beijing Composites Technology Co., Ltd.: With a focus on research and development, this company supplies high-quality SMC products to meet specific customer requirements.
3. AOC (China) Co., Ltd.: AOC is a global leader in SMC manufacturing, providing a wide range of composite products for various industries such as transportation, infrastructure, and consumer goods.
4. PlastiComp (Suzhou) Co., Ltd.: This company excels in producing SMC composite materials with high-performance properties, catering to industries like automotive, construction, and renewable energy.
5. Royalstar Precise Composite Materials Co., Ltd.: Known for its advanced manufacturing technology, this company specializes in SMC sheet production and related composite materials used in industries like transportation and aerospace.
6. Qidi Composite Co., Ltd.: Qidi offers comprehensive solutions for SMC manufacturing, including product design, tooling, and fabrication, serving industries such as automotive, electrical, and construction.
7. Hsin-Yi Composite Materials Co., Ltd.: Hsin-Yi focuses on producing SMC materials for automotive components, providing lightweight yet durable solutions for vehicle manufacturers.
8. Toho Tenax Co., Ltd.: As a leading supplier of carbon fiber SMC, Tenax provides highly advanced composite materials used in aerospace, automotive, and sporting goods industries.
9. Shanghai PRET Composite Material Co., Ltd.: PRET specializes in producing SMC materials for electrical and electronic applications, providing insulation and heat resistance properties required in these sectors.
10. Ningbo Huayuan FRP Electrical Appliance Manufacture Co., Ltd.: This company focuses on SMC/BMC manufacturing for electrical equipment, offering a wide range of composite products suitable for power distribution and transmission applications.
These top 10 SMC manufacturing manufacturers in China represent a diverse range of companies that excel in producing high-quality SMC materials for various industries. With their advanced manufacturing technologies and commitment to innovation, they contribute significantly to China’s position as a global leader in composite manufacturing.
Background Research for smc manufacturing manufacturers Companies in China, use qcc.com archive.org importyeti.com
SMC (Sheet Molding Compounds) manufacturing is a process widely used in the production of various composite materials. While China is known for its manufacturing capabilities, locating specific information on SMC manufacturing manufacturers in the country can be challenging. However, by utilizing various online resources like qcc.com, archive.org, and importyeti.com, it is possible to gather background information on this industry in China.
Qcc.com is a Chinese business information database that provides insights into companies operating in China. By searching for SMC manufacturing manufacturers on qcc.com, one can obtain information such as company name, address, registration date, registered capital, and business scope. This data can provide a preliminary understanding of the companies in the SMC manufacturing industry.
Archive.org is a digital library that offers access to archived versions of websites. It can be helpful for researching historical information or previously available data about SMC manufacturing manufacturers. By exploring archived versions of industry-related websites or company profiles, researchers can gather valuable insights into the development and evolution of the SMC manufacturing industry in China.
Importyeti.com is a specialized platform that provides import/export data. Utilizing this database can offer insights into the trading activities of SMC manufacturing manufacturers. Researchers can access information like the volume, value, and origin/destination of imports and exports related to SMC materials and products. By understanding the import/export trends, it is possible to gauge the market dynamics and the competitiveness of Chinese SMC manufacturers.
In summary, conducting background research on SMC manufacturing manufacturers in China requires utilizing online resources such as qcc.com, archive.org, and importyeti.com. These platforms enable researchers to gather information about companies, historical data, and import/export activities related to the SMC manufacturing industry. By leveraging these sources, valuable insights can be obtained within a 300-word limit.
Leveraging Trade Shows and Expos for smc manufacturing Sourcing in China
Trade shows and expos can be valuable resources for sourcing small and medium-sized manufacturing (SMC) in China. These events provide an opportunity for buyers to connect with numerous suppliers, gain insights into the industry trends, and evaluate the quality and capabilities of manufacturers. With strategic planning and utilization, leveraging trade shows and expos can greatly benefit SMC manufacturing sourcing in China.
Firstly, trade shows and expos serve as a platform to establish direct communication with potential suppliers. Rather than relying solely on internet searches or third-party platforms, attending these events allows buyers to engage in face-to-face discussions, learn more about manufacturers’ offerings, and negotiate terms directly. This personal interaction not only provides a better understanding of the supplier’s capabilities but also helps to establish a foundation for a long-term business relationship.
Secondly, trade shows and expos enable buyers to witness the latest technological advancements and industry trends. China’s manufacturing sector is known for its continuous innovation and development. By attending these events, buyers can stay up-to-date with the latest production techniques, machinery, and materials in SMC manufacturing. This knowledge can contribute to identifying potential suppliers who are at the forefront of technology and can offer innovative solutions for their manufacturing needs.
Furthermore, trade shows and expos offer an opportunity to evaluate the quality and reliability of potential suppliers. Buyers can physically inspect product samples, review manufacturing processes, and assess the suppliers’ overall capabilities. This firsthand evaluation is crucial, particularly for SMC manufacturing, where quality control plays a significant role in ensuring the products meet the desired specifications.
To maximize the benefits of trade shows and expos, buyers should engage in thorough research and preparation beforehand. This includes identifying specific objectives, researching and shortlisting potential suppliers, and creating a detailed schedule to navigate through the event. Additionally, networking and attending seminars or presentations relevant to SMC manufacturing in China can provide valuable insights and connections.
In summary, trade shows and expos offer a wealth of opportunities for sourcing SMC manufacturing in China. They provide direct communication with suppliers, showcase the latest technological advancements, and allow for firsthand evaluation of products and capabilities. By leveraging these events strategically, buyers can effectively identify reliable suppliers, stay informed about industry trends, and ultimately, streamline their sourcing process in China.
The Role of Agents and Sourcing Companies in Facilitating smc manufacturing Purchases from China
Agents and sourcing companies play a crucial role in facilitating small and medium-sized company (SMC) manufacturing purchases from China. With their expertise, knowledge, and local presence, they can effectively bridge the gap between SMCs and Chinese manufacturers, overcoming language and cultural barriers, as well as ensuring the smooth execution of orders.
One of the main roles of agents and sourcing companies is to identify and select suitable manufacturers in China for SMCs. They have an extensive network and understanding of the manufacturing landscape, enabling them to shortlist potential suppliers based on the SMCs’ specific product requirements, quality standards, and budget constraints. This helps SMCs save time and effort in finding reliable suppliers and ensures a higher chance of successful cooperation.
Moreover, agents and sourcing companies negotiate on behalf of SMCs with Chinese manufacturers to secure favorable pricing and terms. They are experienced in vendor management and have the necessary skills to drive a hard bargain and achieve competitive pricing for SMCs. Additionally, they ensure that contracts and agreements are properly drafted to protect the interests of both parties, minimizing the risks for SMCs.
Furthermore, these intermediaries provide quality control services throughout the manufacturing process. They conduct regular inspections and audits to ensure that the products meet the SMCs’ specifications and adhere to international quality standards. Inspections can encompass raw material inspection, in-process inspection, and finished product inspection. By having a local presence, agents and sourcing companies can quickly identify and rectify any manufacturing issues, thereby minimizing potential disruptions and delays.
Lastly, agents and sourcing companies handle logistics and shipping arrangements for SMCs. They have a good understanding of transportation requirements, customs regulations, and documentation needed for international shipments. This ensures that the products ordered from Chinese manufacturers are efficiently transported to the SMCs’ designated location, minimizing any logistics challenges and avoiding unnecessary complications.
In conclusion, agents and sourcing companies play a vital role in facilitating SMC manufacturing purchases from China. They assist SMCs in identifying suitable manufacturers, negotiating favorable terms, ensuring quality control, and handling logistics. Their expertise and local presence significantly contribute to the success of SMCs’ sourcing initiatives, enabling them to tap into the vast manufacturing capabilities China has to offer.
Price Cost Research for smc manufacturing manufacturers Companies in China, use temu.com and 1688.com
When conducting price cost research for SMC (Sheet Molding Compound) manufacturing companies in China, two popular online platforms to explore are temu.com and 1688.com. Both platforms provide a wide range of options and valuable information for finding manufacturers that specialize in SMC production.
Temu.com is an online marketplace that connects global buyers with Chinese suppliers. It offers a comprehensive database of manufacturers, allowing users to browse through various product categories. To conduct price cost research on temu.com, one can filter the search results to specifically target SMC manufacturers in China. This will help in obtaining a list of potential suppliers and comparing their pricing and production capabilities.
1688.com, often referred to as the Chinese version of Alibaba, is another effective platform for researching SMC manufacturers in China. It is primarily used by domestic businesses and trading companies. The website provides a vast array of SMC manufacturing companies from different provinces in China. Although the platform is in Chinese, it can be easily navigated using translation tools such as Google Translate or other browser extensions.
When conducting price cost research, it is recommended to consider factors such as product quality, manufacturing capability, production capacity, and after-sales service. Comparing price quotes from multiple suppliers is crucial to finding the most competitive rates. However, it is equally important to assess the credibility and reputation of the suppliers by reviewing their company profiles, certifications, and customer reviews.
In conclusion, temu.com and 1688.com are valuable online platforms for conducting price cost research on SMC manufacturing companies in China. Utilizing these platforms, and taking into account key factors, can help identify reliable suppliers with competitive pricing.
Shipping Cost for smc manufacturing import from China
When importing from China, it is essential to consider the shipping cost for SMC (Sheet Molding Compound) manufacturing materials. The total shipping cost depends on various factors such as the volume of the shipment, weight, packaging, transportation mode, and distance traveled.
The two main transportation options for importing goods from China are by sea or air. Shipping by sea is typically the most cost-effective option for bulky and heavy shipments, such as SMC materials. It is recommended to use Full Container Load (FCL) or Less than Container Load (LCL) services.
For FCL shipments, the shipping cost is determined by the container size (20ft or 40ft), the starting and ending ports, and the delivery location. Generally, FCL offers lower overall costs as it eliminates the need to share the container with other importers.
On the other hand, LCL shipments are suitable for smaller quantities when it is not feasible to fill a complete container. LCL charges are based on the volume of goods being shipped and any additional charges for loading and unloading the cargo.
Shipping by air is a faster but more expensive option. It is suitable for urgent or time-sensitive shipments. The air freight cost depends on the weight and volume of the goods, as well as the departure and arrival airports.
To estimate the shipping cost accurately, it is recommended to contact shipping agents or freight forwarders. They can provide detailed quotations based on the specific shipment parameters. Additionally, it is crucial to consider other costs involved in importing, such as customs duties, taxes, and any other fees required by the importing country.
In summary, the shipping cost for SMC manufacturing materials imported from China varies based on factors such as shipment volume, weight, packaging, transportation mode, and distance. To get an accurate estimation, it is advisable to consult with shipping agents or freight forwarders.
Compare China and Other smc manufacturing Markets: Products Quality and Price,Visible and Hidden Costs
When comparing China to other SMC (Sheet Molding Compound) manufacturing markets, key factors to consider include product quality and price, as well as visible and hidden costs.
Product quality in China has historically been a concern due to issues such as counterfeit products and lack of adherence to strict quality standards. However, in recent years, Chinese manufacturers have made significant improvements in quality control and have become more competitive in terms of product standards. Other SMC manufacturing markets, such as Germany, the United States, and Japan, have traditionally had a reputation for higher quality products. These markets often have stricter regulations and quality control measures in place, resulting in products that meet higher standards. However, it is worth noting that there are Chinese manufacturers who have also achieved internationally recognized quality certifications, narrowing the gap with these leading markets.
In terms of price, China has long been known for its low-cost manufacturing advantage. The country’s large-scale production capabilities, abundant labor force, and relatively low overhead costs have enabled manufacturers to offer competitive pricing. This price advantage has been a significant factor in China’s dominance in global manufacturing. However, other SMC manufacturing markets, particularly in Eastern Europe and Southeast Asia, have emerged as cost-effective alternatives to China. These markets offer lower labor costs and, in some cases, competitive manufacturing capabilities, leading to lower prices. The price differentials between China and these markets can vary depending on factors such as product complexity and production volume.
Visible costs, such as labor, material, and transportation costs, are generally lower in China compared to many other SMC manufacturing markets. However, hidden costs, such as intellectual property risks, supply chain disruptions, and potential quality issues, can add significant expenses in the long run. Intellectual property risks, including counterfeiting and unauthorized use of proprietary technology, have been a concern for companies manufacturing in China. Companies may need to invest in additional security measures and legal protections to mitigate these risks. Supply chain disruptions, such as delays in shipping or material shortages, can also result in additional costs or lost business opportunities. Furthermore, quality issues, such as product recalls or customer complaints, can damage a company’s reputation and lead to financial repercussions.
In summary, China’s manufacturing market has made significant improvements in product quality but still faces challenges in comparison to more established markets. However, China’s advantage in terms of lower pricing remains a compelling factor for many companies. When considering manufacturing options, it is crucial to evaluate both visible and hidden costs alongside quality and price to make an informed decision.
Understanding Pricing and Payment Terms for smc manufacturing: A Comparative Guide to Get the Best Deal
When it comes to manufacturing, understanding pricing and payment terms is crucial in order to get the best deal for your company. This is particularly true for SMC (Sheet Molding Compound) manufacturing, which involves a unique process of molding fiber-reinforced thermosetting resin materials.
The first step in obtaining the best pricing is to gather quotes from multiple SMC manufacturers. By comparing these quotes, you can identify any variations in pricing, which may be attributed to factors such as the manufacturer’s experience, facility size, or production capabilities. It is also important to consider the quality of the SMC materials provided by each manufacturer, as this can directly impact the final product’s durability and performance.
Payment terms are another crucial aspect to consider. Negotiating favorable payment terms can help manage your company’s cash flow. Common payment terms for SMC manufacturing include:
1. Up-front payment: Some SMC manufacturers may require full payment upfront, especially for smaller orders or to cover the cost of raw materials. While this option may be less favorable, it could be necessary when dealing with a new or less established manufacturer.
2. Down payment plus installments: A more flexible option involves paying a down payment upfront, followed by installment payments throughout the manufacturing process. This option allows you to mitigate risks while also providing some financial flexibility.
3. Net payment terms: Established companies with a good credit history may negotiate net payment terms, allowing them to pay for the SMC materials after a certain number of days or weeks from the invoice date. This option is beneficial for managing cash flow, as it provides more time for the company to generate revenue before making the payment.
To secure the best deal, it is highly recommended to negotiate both pricing and payment terms. You can leverage factors such as the volume of your order, the length of your business relationship, and your company’s overall financial stability to negotiate better prices and favorable payment terms.
In summary, to get the best deal for SMC manufacturing, it is essential to gather quotes from multiple manufacturers, compare pricing and quality, and negotiate advantageous payment terms. By doing so, your company can lower costs, properly manage cash flow, and ensure the highest quality SMC products for your manufacturing needs.
Chinese Regulations and Industry Standards Certifications for smc manufacturing,Import Regulations and Customs for smc manufacturing from China
When it comes to SMC (Sheet Molding Compound) manufacturing, China has regulations and industry standards that need to be adhered to. Additionally, there are import regulations and customs procedures that should be considered when importing SMC products from China.
In terms of regulations and industry standards certifications for SMC manufacturing, one important requirement is the China Compulsory Certification (CCC). This certification is mandatory for various products, including electrical and electronic equipment, and it ensures that the products meet the safety, health, and environmental protection standards set by the Chinese government. SMC manufacturers need to ensure that their products comply with CCC requirements before exporting them to China or any other country that requires CCC certification.
In addition to CCC, SMC manufacturers should also adhere to industry standards such as the GB/T 22240-2008 standard, which specifies the technical requirements for SMC materials used in electrical applications. This standard covers aspects such as mechanical properties, electrical properties, and resistance to heat and chemicals. Adhering to these standards ensures the quality and safety of SMC products manufactured in China.
When importing SMC products from China, it is essential to understand and comply with the import regulations and customs procedures. The first step is to determine the import classification of SMC products according to the Harmonized System (HS) codes. This classification will determine the applicable import duties and taxes.
Importers should also ensure that they have the necessary documentation, such as a commercial invoice, packing list, bill of lading, and a certificate of origin. These documents are required for customs clearance and to demonstrate the authenticity and value of the imported SMC products.
Moreover, observing specific import restrictions, if any, is crucial. For instance, certain SMC products may be subject to import quotas, licensing requirements, or quality inspections. Importers should keep themselves updated with the latest regulations and requirements to avoid any complications during the import process.
In conclusion, SMC manufacturing in China requires compliance with regulations and industry standards certifications such as CCC and GB/T 22240-2008. Importing SMC products from China necessitates understanding import regulations, customs procedures, and documentation requirements. By following these guidelines, businesses can ensure smooth operations and meet the necessary legal requirements.
Sustainability and Environmental Considerations in smc manufacturing Manufacturing
Sustainability and environmental considerations play a crucial role in the manufacturing of Sheet Molding Compound (SMC), as it is essential to minimize the impact on the environment throughout the production process. SMC manufacturing involves the use of raw materials, energy, and water, all of which have implications for sustainability.
One aspect of sustainability in SMC manufacturing is the sourcing of raw materials. The primary components of SMC are glass fibers, resin, and fillers. These materials should be obtained from sustainable sources, minimizing deforestation and promoting responsible resource management. Additionally, efforts should be made to use recycled or reclaimed materials whenever possible, reducing the overall environmental footprint of the manufacturing process.
Energy consumption is another significant aspect of sustainability in SMC manufacturing. The production of SMC requires a considerable amount of energy, mainly for heating, mixing, and curing processes. To minimize energy usage, manufacturers should explore energy-efficient technologies and equipment, as well as renewable energy sources such as solar or wind power. Implementing energy management systems and optimizing production schedules can also help reduce energy consumption and associated greenhouse gas emissions.
Water usage and wastewater management are important environmental considerations in SMC manufacturing. Water is used for various purposes, including cleaning, cooling, and mixing. Manufacturers should strive to reduce water consumption through process optimization and recycling techniques. Proper wastewater treatment is vital to prevent pollution of water sources. Implementing effective filtration and treatment systems can remove contaminants and minimize the impact on aquatic ecosystems.
Waste management is critical in SMC manufacturing to minimize the generation of solid waste and hazardous materials. Recycling of scrap materials should be prioritized, and waste disposal should comply with strict regulations to prevent environmental contamination. Implementing lean manufacturing principles and process optimization can help reduce waste generation and increase resource efficiency.
In conclusion, sustainability and environmental considerations in SMC manufacturing require a holistic approach that encompasses the selection of raw materials, energy management, water usage, waste management, and compliance with regulations. By implementing these measures, manufacturers can minimize their environmental impact and contribute to a more sustainable future.
List The Evolution history of “smc manufacturing”
SMC manufacturing, also known as sheet molding compound manufacturing, has experienced significant advancements and evolution over the years. This composite material manufacturing process involves a mixture of resins, reinforcements, and fillers to create a versatile and strong product. Here is a brief overview of the evolution history of SMC manufacturing:
1. Development: SMC manufacturing originated in the 1960s as engineers sought alternative materials for automotive parts. The early development focused on combining thermosetting resins, such as polyester, with reinforcing fillers, usually glass fibers.
2. Advancements in Formulation: In the 1970s, manufacturers began experimenting with different resin systems, such as vinyl ester and epoxy, to enhance the mechanical properties and resistance of SMC components.
3. Automation and Productivity: By the 1980s, automation technologies were introduced to improve the efficiency and productivity of SMC manufacturing. Automated SMC lines facilitated faster mixing, molding, and curing processes, enabling mass production of composite parts.
4. Improved Physical and Mechanical Properties: In the 1990s, advancements in reinforcing fillers, such as carbon fibers and aramid fibers, provided SMC products with higher strength-to-weight ratios and improved resistance to heat, chemical, and impact.
5. Surface Aesthetics: In the early 2000s, manufacturers focused on improving the surface finish and appearance of SMC components. Techniques such as the inclusion of visible carbon fibers, painting technologies, and the application of gel coats resulted in a more visually appealing final product.
6. Customization and Integration: In recent years, SMC manufacturing has evolved to meet the demands of diverse industries. The ability to incorporate additional functionalities, such as electrical conductivity, acoustics, or fire resistance, has made SMC a popular choice for applications in aerospace, construction, consumer goods, and more.
7. Sustainability: With the growing importance of environmental sustainability, the SMC manufacturing industry has been exploring bioresins and biofillers derived from renewable sources. These advancements aim to reduce the carbon footprint associated with the production of SMC components.
Overall, the evolution of SMC manufacturing has seen progress in formulation, production processes, surface aesthetics, customization, and sustainability, making it a versatile and efficient solution for various industries seeking lightweight, durable, and visually appealing composite materials.
The Evolution and Market Trends in smc manufacturing Industry
The manufacturing industry has undergone significant evolution in recent years, particularly in the field of Sheet Molding Compound (SMC) manufacturing. SMC is a composite material used primarily in automotive, aerospace, and construction industries due to its high strength-to-weight ratio, excellent corrosion resistance, and low production costs. The evolution of the SMC manufacturing industry can be attributed to several key factors.
Firstly, advancements in technology have played a vital role in the evolution of the SMC manufacturing industry. Automation and robotics have enabled manufacturers to streamline production processes, resulting in increased efficiency and lower production costs. This has also led to improved product quality and consistency, meeting the stringent requirements of end-users.
Secondly, market trends have also influenced the evolution of the SMC manufacturing industry. The growing demand for lightweight, fuel-efficient vehicles has driven the adoption of SMC in automaking. The aerospace industry has also embraced SMC due to its ability to replace traditional materials like aluminum and steel, resulting in lighter aircraft and improved fuel efficiency. Furthermore, the construction industry has utilized SMC for its durability and ability to withstand harsh environmental conditions.
Additionally, environmental concerns and regulations have shaped the evolution of the SMC manufacturing industry. The industry has made significant advancements in developing sustainable and eco-friendly manufacturing processes. Manufacturers are now focusing on reducing energy consumption, minimizing waste, and utilizing recyclable materials in the production of SMC.
Furthermore, market trends indicate a growing preference for customization and personalized products. This has led to the development of innovative SMC manufacturing techniques, such as 3D printing, which allows for complex geometries and unique designs. Manufacturers are also exploring the use of SMC in emerging markets such as renewable energy, electrical, and electronics sectors.
In conclusion, the SMC manufacturing industry has experienced significant evolution due to advancements in technology, market trends, and environmental concerns. The industry has adapted to meet the growing demand for lightweight, durable, and eco-friendly materials in various industries. With continued innovation, the SMC manufacturing industry is poised for further growth and expansion in the coming years.
Custom Private Labeling and Branding Opportunities with Chinese smc manufacturing Manufacturers
Chinese smc manufacturing manufacturers offer multiple opportunities for custom private labeling and branding. With their expertise in the production of smc (Sheet Molding Compound) products, they can help businesses create unique and customized products that are perfectly branded to meet their specific needs.
One of the key advantages of working with Chinese smc manufacturers is their ability to offer private labeling options. This means that businesses can have their own logo, tags, and labels applied to the products they order, giving them a personalized touch and helping to build brand recognition. This feature is especially beneficial for businesses that aim to establish their own unique identity and differentiate themselves from competitors.
Moreover, Chinese smc manufacturers also provide branding opportunities. They can assist businesses in creating custom molds, designs, and color variations for their products. This allows brands to add distinctive features to their products, enhancing their market appeal and making them stand out on the shelves. By working closely with Chinese smc manufacturers, businesses can ensure that their products are precisely tailored to their brand image, customer preferences, and marketing strategies.
Furthermore, Chinese smc manufacturers often offer a variety of product customization options. These can range from size and shape variations to surface finishes and detailing choices. Such versatility allows businesses to create products that align with their branding guidelines and specifications. Whether it is aesthetics, functionality, or quality, Chinese smc manufacturers can accommodate different customization requests, enabling businesses to offer unique and exclusive products to their customers.
In conclusion, Chinese smc manufacturing manufacturers present excellent opportunities for businesses to engage in custom private labeling and branding. With their expertise, businesses can collaborate closely with the manufacturers to create personalized products that align with their branding guidelines and customer demands. By taking advantage of these opportunities, businesses can strengthen their brand identity, increase market appeal, and ultimately boost their competitive advantage.
Tips for Procurement and Considerations when Purchasing smc manufacturing
When it comes to procurement and purchasing of SMC manufacturing, there are several tips and considerations that can help ensure a smooth and successful process.
1. Clearly define your requirements: Before approaching any potential suppliers, it is crucial to have a clear understanding of your requirements. Determine the specific characteristics, dimensions, tolerances, and quality standards you expect from the SMC manufacturing.
2. Research potential suppliers: Conduct thorough research to identify potential suppliers who specialize in SMC manufacturing. Look for suppliers with a strong track record, experience, and positive customer reviews. Consider factors such as their capacity, certifications, and ability to meet your specific needs.
3. Request for proposals (RFPs): Create a detailed Request for Proposal (RFP) that outlines your requirements and seeks relevant information from potential suppliers. This helps streamline the process by allowing you to compare and evaluate different offers objectively.
4. Quality assurance and certifications: Ensure that potential suppliers have appropriate quality assurance processes in place. Look for suppliers who hold relevant certifications such as ISO 9001 or ISO/TS 16949, as these indicate their commitment to quality management systems.
5. Cost considerations: While cost is an important factor, it should not be the sole determining factor. Consider the total cost of ownership, taking into account factors such as quality, lead times, after-sales support, and any potential risks associated with cheaper options.
6. Supplier evaluation: Conduct thorough evaluations of potential suppliers before making a decision. Evaluate their financial stability, production capabilities, delivery timelines, and references from previous customers.
7. Communication and collaboration: Establish clear communication channels with the supplier to ensure both parties have a shared understanding of requirements, timelines, and deliverables. Collaborate closely with the supplier to address any concerns or issues that may arise during the procurement process.
8. Contract and legal considerations: Develop a comprehensive contract that includes important terms and conditions such as pricing, delivery schedules, quality standards, intellectual property rights, and dispute resolution mechanisms. Engage legal counsel to review the contract to protect your interests.
9. Continuous supplier management: Once a supplier is selected, establish a framework for ongoing supplier management. Regularly review performance metrics, conduct audits, and maintain open lines of communication to ensure a productive and successful relationship.
By following these tips and considerations, you can enhance the procurement and purchasing process for SMC manufacturing, leading to successful outcomes and a mutually beneficial relationship with your supplier.
FAQs on Sourcing and Manufacturing smc manufacturing in China
1. Why should I consider sourcing and manufacturing in China for my SMC products?
Sourcing and manufacturing in China can offer numerous advantages. China has a well-established manufacturing infrastructure, with a vast network of suppliers and factories specializing in various industries, including SMC manufacturing. The cost of labor in China is typically lower than in many other countries, allowing for cost-efficient production. Additionally, China’s strong industrial capabilities, technical expertise, and advanced machinery further contribute to the quality and efficiency of SMC manufacturing.
2. How can I find a reliable SMC manufacturer in China?
Finding a reliable SMC manufacturer in China involves thorough research and due diligence. Online sourcing platforms like Alibaba, Made-in-China, and Global Sources can be useful starting points. Look for manufacturers with extensive experience in SMC production, relevant certifications (such as ISO 9001), and positive customer reviews. Conducting factory audits and requesting samples can also help evaluate a manufacturer’s capabilities and product quality.
3. Are there any potential challenges or risks associated with sourcing and manufacturing SMC products in China?
While China offers numerous advantages, there are potential challenges to be aware of. Language and cultural barriers can sometimes hamper effective communication and understanding. Intellectual property protection can also be a concern, so it is vital to work with manufacturers that respect intellectual property rights and sign non-disclosure agreements. Lastly, distance can impact lead times and logistics, but this can be mitigated by effective planning and communication.
4. What are the payment terms and methods commonly used for sourcing and manufacturing in China?
Payment terms vary depending on the manufacturer and nature of the project. Common options include Letters of Credit (LC), Telegraphic Transfer (T/T), and PayPal. Manufacturers may request a deposit upfront, with the balance upon completion or pre-shipment inspection. It is crucial to establish clear payment terms and timelines in the contract and work with reputable manufacturers to ensure payment security.
5. How can I ensure quality control during the manufacturing process?
Implementing effective quality control measures is essential when sourcing and manufacturing in China. Conducting regular inspections and audits, either by visiting the factory or hiring a third-party inspection company, can help ensure adherence to specifications and standards. Detailed product specifications, quality requirements, and testing protocols should be clearly communicated to the manufacturer. Regular communication and building a good working relationship can also contribute to better quality control.
Overall, sourcing and manufacturing SMC products in China can provide cost-efficient production, technical expertise, and a wide range of suppliers. However, proper due diligence and communication are crucial to mitigate risks and ensure successful manufacturing.
Why contact sourcifychina.com get free quota from reliable smc manufacturing suppliers?
Sourcifychina.com offers a free quota from reliable SMC manufacturing suppliers for a variety of reasons. Here are some key points explaining why:
1. Building trust and credibility: Sourcifychina.com aims to establish itself as a reliable platform for sourcing in China. By offering a free quota from trusted SMC manufacturing suppliers, they demonstrate their commitment to connecting businesses with reputable suppliers.
2. Encouraging engagement: Providing a free quota motivates potential buyers to actively interact with the platform. It allows them to explore sourcing options without any financial commitment, boosting engagement levels and attracting a larger pool of clients.
3. Helping businesses save costs: SMC manufacturing involves significant financial investments. By obtaining a free quota, businesses can save on initial expenses that would otherwise be incurred in the sourcing process. This can be particularly beneficial for startups or small businesses with limited budgets.
4. Ensuring supplier quality: Sourcifychina.com only partners with reliable SMC manufacturing suppliers who meet certain quality standards. By offering a free quota only from these trusted suppliers, they ensure that businesses receive quotations from manufacturers with a proven track record of delivering high-quality products.
5. Facilitating informed decision-making: Providing a free quota allows businesses to compare and evaluate different suppliers’ pricing and capabilities. This enables them to make informed decisions based on important factors like cost-effectiveness, production capacity, lead times, and quality assurance.
6. Establishing long-term relationships: Sourcifychina.com understands the importance of fostering long-term partnerships between buyers and suppliers. By providing a free quota, they aim to initiate a positive engagement that can lead to fruitful collaborations and ongoing business transactions.
Overall, offering a free quota from reliable SMC manufacturing suppliers benefits both Sourcifychina.com and businesses in search of sourcing solutions. It helps build trust, reduces costs, promotes engagement, ensures quality, facilitates decision-making, and supports the establishment of long-term business relationships.