Introduce about wafer manufacturing guide,Qulity,Cost,Supplier,Certification,Market,Tips,FAQ
The wafer manufacturing guide is a comprehensive manual that provides valuable knowledge and insights into the production process of wafers used in various industries. This guide covers several important aspects, including quality control, cost management, supplier selection, certification requirements, market trends, useful tips, and frequently asked questions.
Quality plays a crucial role in wafer manufacturing, as the final product must meet stringent standards for reliability and performance. The guide provides an overview of quality control practices, emphasizing the importance of inspecting the wafer’s dimensions, surface quality, and electrical properties. It also elaborates on testing methods and the significance of statistical process control to ensure consistent quality throughout the production cycle.
Cost management is another important aspect covered in the guide. It highlights strategies to optimize manufacturing costs without compromising quality. This includes streamlining production processes, optimizing resource utilization, and exploring cost-effective sourcing options for raw materials.
Selecting the right suppliers is vital in the wafer manufacturing industry. The guide offers insights on evaluating suppliers based on their technical capabilities, production capacity, financial stability, and delivery reliability. Additionally, it emphasizes the importance of developing strategic partnerships to foster long-term supply chain stability and continuous improvement.
Certification requirements are critical to demonstrate compliance with industry standards. The guide outlines commonly required certifications such as ISO 9001 for quality management systems and ISO 14001 for environmental management systems. It also explores specific certifications related to wafer manufacturing, such as cleanroom protocols (e.g., ISO 14644) and semiconductor equipment safety standards (e.g., SEMI S2).
Market trends and insights are provided to help manufacturers stay abreast of the latest developments, emerging technologies, and evolving customer demands. The guide explores market growth potential, key applications of wafers, and regional market dynamics.
The guide also includes helpful tips and recommendations gathered from industry experts. These insights cover various aspects ranging from process optimization and yield improvement to supply chain management and customer satisfaction.
Lastly, the guide answers frequently asked questions to address common concerns and provide clarity on specific topics related to wafer manufacturing.
In summary, the wafer manufacturing guide serves as a valuable resource for professionals, manufacturers, and researchers seeking to enhance their understanding of wafer manufacturing processes, improve product quality, manage costs, select reliable suppliers, comply with certifications, stay updated on market trends, and gain practical tips to optimize operations.
Types of wafer manufacturing
Wafer manufacturing refers to the process of creating wafers, which are thin slices of semiconductor materials used as the foundation for devices such as integrated circuits (ICs) and microelectromechanical systems (MEMS). There are several types of wafer manufacturing processes, each suited for different applications and desired outcomes.
1. Bulk Silicon Wafer Manufacturing: This is the most common type of wafer manufacturing and involves growing a crystalline silicon ingot, which is then sliced into thin circular wafers. The ingot is produced through the Czochralski method, where a seed crystal is dipped into molten silicon and slowly rotated to produce a cylindrical ingot. These wafers typically have a diameter ranging from 100 mm to 300 mm and are widely used in IC production.
2. Silicon on Insulator (SOI) Wafer Manufacturing: In SOI wafer manufacturing, two layers of silicon are created with a layer of insulating material (usually silicon dioxide) in between. This is achieved through techniques like wafer bonding or separation by implantation of oxygen (SIMOX). SOI wafers offer better isolation between components, reduced power consumption, and improved performance. They are commonly used in high-performance ICs, photonics, and radio frequency applications.
3. Compound Semiconductor Wafer Manufacturing: Compound semiconductors, such as gallium arsenide (GaAs) or indium phosphide (InP), are used to manufacture wafers for specialized applications. These materials offer properties that surpass silicon in terms of speed, power handling, and emission characteristics. Compound semiconductor wafers are commonly used in high-frequency electronics, optoelectronics (LEDs and lasers), and solar cells.
4. Epitaxial Wafer Manufacturing: Epitaxial growth involves depositing a layer of crystalline material on top of a substrate wafer. This is achieved through techniques like chemical vapor deposition (CVD) or molecular beam epitaxy (MBE). Epitaxial wafers are used to modify or enhance the properties of the substrate material, such as creating layers with different conductivity types or adding specific impurities. These wafers find applications in advanced ICs, power devices, and sensors.
5. Silicon Carbide (SiC) Wafer Manufacturing: SiC wafers are increasingly used due to their superior properties, including high-temperature tolerance, high power handling, and excellent thermal conductivity. The process involves using specialized methods like physical vapor transport or chemical vapor deposition to grow SiC crystals, which are then sliced into wafers. SiC wafers have applications in power electronics, high-frequency devices, and electric vehicles.
In conclusion, wafer manufacturing encompasses a range of techniques to produce semiconductor wafers suitable for various applications. The choice of manufacturing process depends on factors such as the desired semiconductor material, the required properties, and the intended use of the final devices.
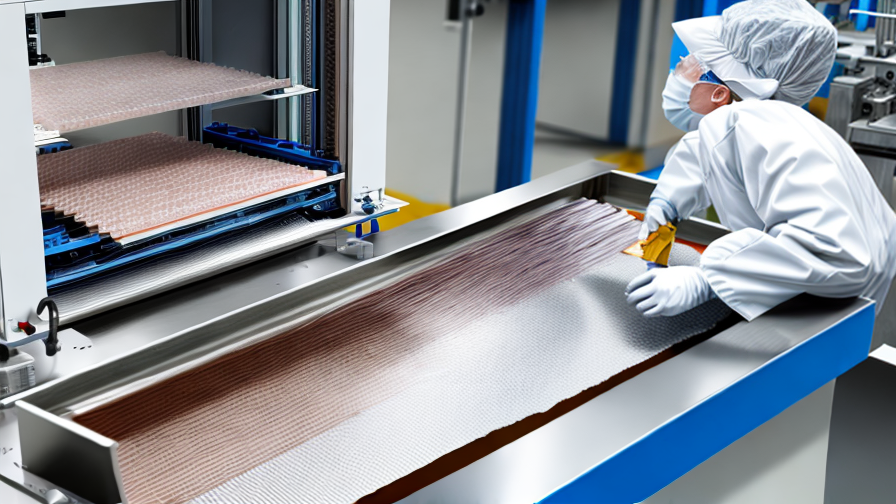
Pros and Cons of Using wafer manufacturing
Wafer manufacturing is the process of producing wafers, which are thin slices of semiconductor material, typically made of silicon. These wafers serve as the base for manufacturing various electronic devices such as microchips, integrated circuits, and solar cells. While wafer manufacturing enables the production of advanced technology, it also presents several pros and cons, as discussed below:
Pros:
1. Cost Efficiency: Wafer manufacturing allows for high-volume production, ensuring cost efficiency due to economies of scale. Large quantities of wafers can be produced simultaneously, reducing per-unit costs and making electronic devices more affordable.
2. Miniaturization: Wafers enable the production of small and compact electronic devices. With wafer manufacturing, microchips and integrated circuits can be fabricated with smaller dimensions, leading to the development of more advanced and portable technologies.
3. Performance and Functionality: Semiconductor wafers offer excellent electrical properties, enabling high-performance electronic devices. The controlled manufacturing process allows for precise doping and deposition techniques, resulting in enhanced functionality and improved operational capabilities of the devices.
4. Technological Advancement: Wafer manufacturing plays a vital role in driving technological advancements. It enables the production of cutting-edge devices, contributing to innovations in various sectors such as telecommunications, automotive, healthcare, and renewable energy.
Cons:
1. High Initial Investment: Establishing a wafer manufacturing facility requires substantial upfront investment in infrastructure, equipment, and skilled labor. The initial costs can be a barrier for companies or regions lacking the necessary resources.
2. Environmental Impact: The wafer manufacturing process involves the use of hazardous chemicals and generates significant waste. Improper disposal or mishandling of these chemicals can lead to environmental pollution and health risks.
3. Complexity and Technological Limitations: Wafer fabrication involves complex processes, including photolithography, etching, deposition, and testing. The complexity of these processes can result in high production costs, yield loss, and technical challenges, limiting the scalability and efficiency of wafer manufacturing.
4. Dependency on Global Supply Chains: The manufacturing of wafers often relies on a global supply chain for raw materials, equipment, and expertise. This dependency can be a concern during times of disruption, such as natural disasters or geopolitical tensions, impacting the availability and cost of essential resources.
In conclusion, wafer manufacturing presents significant advantages in terms of cost efficiency, miniaturization, performance, and technological advancements. However, challenges related to high initial investment, environmental impact, process complexity, and global supply chain dependency must be carefully considered and addressed to ensure the sustainable growth and development of the industry.
wafer manufacturing Reference Specifications (varies for different product)
Wafer manufacturing refers to the process of producing thin, flat slices of semiconductor material that are commonly used as the basis for integrated circuits (ICs), microchips, and electronic components. The specifications for wafer manufacturing may vary depending on the specific product being manufactured. Below are some general reference specifications for wafer manufacturing:
1. Wafer Size: Wafers come in various sizes, with the most common being 200mm (8 inches) and 300mm (12 inches) in diameter. The size of the wafer affects the number of ICs that can be produced, as larger wafers allow for more chips per wafer.
2. Wafer Material: Silicon is the most commonly used material for wafer manufacturing. The silicon wafers are typically made from highly pure single-crystal silicon ingots. Other materials like gallium arsenide may be used for specialized applications.
3. Wafer Thickness: The thickness of a wafer is crucial as it affects the stability, flexibility, and manufacturing cost. Common thicknesses range from 200-1200 micrometers, with thinner wafers being more delicate but enabling higher resolution in ICs.
4. Flatness and Surface Finishing: Wafer flatness is an important aspect of manufacturing, as it impacts the yield and performance of ICs. Typically, wafers have a surface flatness of around 1-2 micrometers. The surfaces are polished to achieve excellent smoothness, ensuring high-quality electronic performance.
5. Doping and Layering: Doping involves introducing impurities into the silicon wafer to modify its electrical properties. Different dopants, such as boron or phosphorus, are used to create p-doped or n-doped regions, essential for the design and functionality of ICs. Layering techniques, including oxidation and deposition, are employed to coat the wafer surface for optimal electrical conductivity.
6. Photolithography and Etching: This stage involves applying a light-sensitive material (photoresist) onto the wafer surface, exposing it to a mask, and then etching away the unwanted material. Photolithography enables the precise transfer of circuit patterns onto the wafer surface, while etching removes undesired material to form the desired circuitry.
7. Testing and Quality Control: After the manufacturing process, wafers undergo extensive testing to ensure their functionality and quality. This testing involves various electrical and physical inspections to detect any defects or failures that might compromise the performance of the finished ICs.
It should be noted that these specifications are just a general reference, and actual specifications for wafer manufacturing may vary depending on the specific product requirements, customer demands, and manufacturing capabilities.
Applications of wafer manufacturing
Wafer manufacturing is a critical process in the semiconductor industry that involves the fabrication of a thin slice of semiconductor material, typically made of silicon. These wafers serve as the foundation for the production of integrated circuits (ICs) used in various electronic devices. The applications of wafer manufacturing are numerous and diverse, ranging from consumer electronics to scientific research and industrial machinery.
One of the primary applications of wafer manufacturing is in the production of computer chips, which are the main components of electronic devices such as smartphones, tablets, laptops, and desktop computers. The wafers undergo a series of intricate processes, including deposition, etching, lithography, and doping, to create the necessary circuitry and pattern structures on the chips. The continuous advancement in wafer manufacturing technology has led to the development of smaller, faster, and more efficient computer chips, enabling the evolution of increasingly powerful and compact electronic devices.
Another crucial application of wafer manufacturing is in the field of renewable energy. Silicon wafers are widely used in the production of solar cells, which convert sunlight into electricity. The wafers are sliced into thin layers and then processed to create photovoltaic cells capable of capturing sunlight and generating electrical energy. With the growing demand for clean and sustainable sources of power, the wafer manufacturing industry plays a vital role in meeting the requirements of the solar energy market.
Furthermore, wafer manufacturing is essential in the development of advanced sensors and detectors used in a variety of industries. Silicon wafers are used as a base material to produce sensors for applications like automotive, aerospace, medical, and environmental monitoring. These sensors enable precise measurement, detection, and control of various parameters such as temperature, pressure, humidity, and gas concentration. They enhance the performance and reliability of critical systems and improve safety and efficiency in diverse industries.
Additionally, wafer manufacturing has applications in scientific research and development. Researchers rely on high-quality wafers to fabricate customized chips for experimental purposes. These chips enable the implementation of novel integrated circuits, microelectromechanical systems (MEMS), and nanoelectromechanical systems (NEMS). These advancements push the boundaries of scientific knowledge and contribute to breakthroughs in fields such as material science, biotechnology, quantum computing, and artificial intelligence.
In conclusion, wafer manufacturing is a fundamental process that underpins various technological advancements. Its applications span across industries, ranging from consumer electronics and renewable energy to sensors and scientific research. As the demand for smaller, faster, and more advanced electronic devices continues to rise, the importance of wafer manufacturing in driving innovation and progress cannot be overstated.
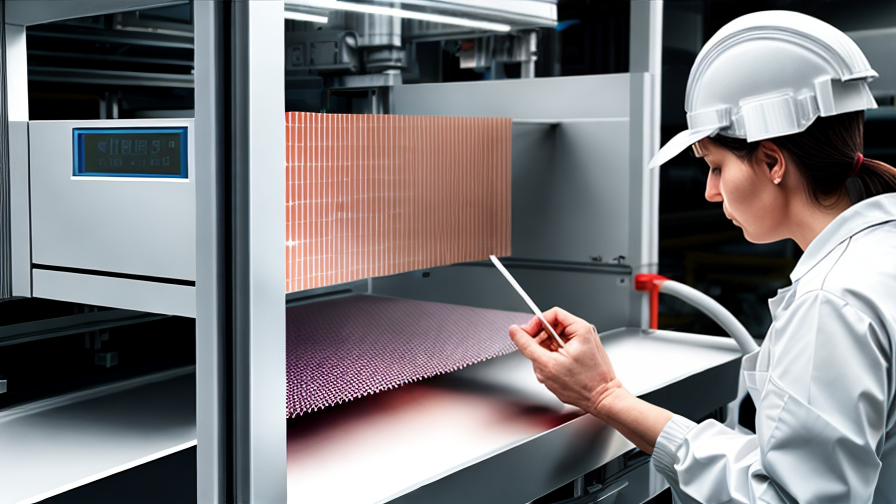
The Work Process and how to use wafer manufacturing
Wafer manufacturing is a complex process used to produce semiconductor devices, such as integrated circuits (ICs). The process involves several steps and requires the use of sophisticated equipment and precise control of various parameters. Below is an overview of the work process involved in wafer manufacturing:
1. Crystal Growth: The process begins with the growth of a single crystal ingot, usually made of silicon, through a method called Czochralski process or epitaxial growth. This step ensures the purity and uniformity of the semiconductor material.
2. Wafer Slicing: The ingot is then sliced into thin circular discs called wafers. Each wafer undergoes grinding and polishing to achieve a flat and smooth surface.
3. Wafer Cleaning: The wafers are thoroughly cleaned to remove any impurities or particles that could affect the manufacturing process. This step involves rinsing, chemical treatment, and drying.
4. Photolithography: The wafers are coated with a photosensitive material called photoresist. A photomask, containing the desired circuit pattern, is aligned and exposed onto the wafer using ultraviolet light. This step is repeated multiple times to create various layers of patterns.
5. Etching: Chemical or dry etching is used to selectively remove the exposed or unprotected areas of the wafer, as defined by the photolithography step. This process is essential for creating the desired circuit patterns and structures.
6. Thin Film Deposition: Thin films of various materials, such as conductor, insulator, or semiconductor, are deposited onto the wafer using techniques like physical vapor deposition or chemical vapor deposition. These films play a crucial role in forming specific components or layers of the semiconductor device.
7. Diffusion and Ion Implantation: These processes introduce impurities called dopants into the semiconductor material to alter its electrical properties. Diffusion involves heating the wafer in a controlled environment, while ion implantation uses high-energy ions to selectively implant dopants into the wafer.
8. Metallization: Metal layers are deposited onto the wafer to establish electrical connections between different components or to provide interconnects. These metal layers can be patterned using photolithography and etching techniques.
9. Testing and Packaging: After fabrication, the wafers are subjected to electrical and functional testing to ensure their performance meets the required specifications. If deemed functional and reliable, the wafers are then cut into individual chips and packaged to protect them.
Overall, wafer manufacturing involves a series of complex and precise steps, each contributing to the creation of high-quality semiconductor devices. It requires a combination of advanced equipment, skilled personnel, and strict quality control measures to ensure the successful production of ICs.
Quality Testing Methods for wafer manufacturing and how to control the quality
Quality testing methods for wafer manufacturing involve a combination of physical, electrical, and visual inspections to ensure the wafers meet the desired standards. These methods encompass both in-process testing and final inspection.
In-process testing methods include wafer surface inspection, where a visual examination is conducted to identify scratches, particles, or other defects. Optical microscopy and scanning electron microscopy (SEM) are also employed to examine wafer patterns and detect issues such as pattern deviations or misalignments. Electrical testing, using techniques like probe testing or automatic test equipment, assesses the electrical characteristics of the circuits on the wafers. This helps identify any faulty or weak components that may impact functionality. Additionally, thickness measurements, performed using profilometers or interferometers, are used to ensure the wafers meet precise thickness specifications.
Final inspection techniques involve more comprehensive testing. Wafer mapping examines the entire wafer to identify any defects, irregularities, or impurities across the surface. Wafer flatness is also assessed to ensure uniformity. Electrical testing is performed again at the final stage to verify the integrity of the circuits and measure essential parameters like resistivity or capacitance. X-ray analysis is adopted to evaluate the presence of any structural abnormalities and to determine the composition of the materials used. Finally, wafer yield analysis is conducted to calculate the proportion of wafers that meet the required standards, further evaluating the manufacturing quality.
To control the quality during wafer manufacturing, strict process control measures are implemented. This includes using advanced equipment with precise calibration and maintaining a controlled environment to minimize contamination risks. Regular equipment maintenance and periodic calibration checks are conducted to ensure accurate measurements. Implementing statistical process control techniques helps monitor and control the manufacturing process, allowing timely adjustments to prevent defects. Additionally, inspection sampling plans are implemented to ensure a representative assessment of wafers without excessive testing, which can be time and resource-consuming.
Effective communication and collaboration between different departments, such as engineering, manufacturing, and quality control, facilitates early detection and resolution of quality issues. Continuous employee training programs ensure the workforce is equipped with the necessary skills and knowledge to maintain quality standards. Regular internal audits are also conducted to assess adherence to quality processes and identify areas for improvement.
In conclusion, wafer manufacturing quality testing methods involve various physical, electrical, and visual inspections, both during the manufacturing process and at the final inspection stage. By implementing strict process controls, utilizing advanced equipment, conducting regular testing and inspections, and fostering effective communication and collaboration, manufacturers can ensure the production of high-quality wafers essential for the electronics industry.
wafer manufacturing Sample Policy and Post-Purchase Considerations for wafer manufacturing from China
Sample Policy and Post-Purchase Considerations for Wafer Manufacturing from China
1. Quality Assurance Policy:
Our company is committed to delivering high-quality wafer products to our customers. We expect our manufacturing partner in China to adhere to the following quality assurance policies:
a. Strict adherence to international quality standards and regulations.
b. Implementation of robust quality control measures throughout the manufacturing process.
c. Regular inspection and testing of wafer products to ensure optimal performance.
d. Continuous improvement initiatives to enhance product quality and reliability.
e. Prompt resolution of quality-related issues or disputes.
2. Intellectual Property Protection:
We respect intellectual property rights and expect our manufacturers to do the same. The following measures should be taken:
a. Properly handle and protect confidential information, trade secrets, and patents.
b. Ensure that all wafer manufacturing processes are compliant with intellectual property laws.
c. Transparent communication and documentation to establish a mutual understanding of intellectual property rights.
3. Communication and Collaboration:
Effective communication between our company and the manufacturing partner is crucial for a successful collaboration. It is essential to establish clear lines of communication and engage in regular updates to ensure:
a. Prompt response to queries, concerns, or requests for information.
b. Timely feedback on sample approval, production progress, and shipping schedules.
c. Efficient resolution of any issues or challenges encountered during the manufacturing process.
d. A collaborative approach to address possible improvements and suggestions.
4. Shipping and Logistics:
Reliable and timely delivery of wafer products is vital for our business. The manufacturer should meet the following criteria:
a. Accurate documentation and compliance with all relevant export and import regulations.
b. Collaboration with reputable shipping companies to ensure the secure transportation of goods.
c. Efficient handling of customs procedures and coordination of logistics.
d. Timely provision of shipping updates, tracking information, and delivery confirmation.
5. Post-Purchase Support:
Our company expects post-purchase support from the manufacturer to ensure customer satisfaction. This includes:
a. Warranty policies for defective or non-compliant products.
b. After-sales technical support and guidance for product installation or troubleshooting.
c. Timely and efficient handling of product returns, replacements, or repairs.
In conclusion, when engaging in wafer manufacturing partnerships with Chinese manufacturers, it is crucial to establish a comprehensive policy focusing on quality assurance, intellectual property protection, communication, shipping, and post-purchase support. These considerations will promote a successful and mutually beneficial collaboration while ensuring customer satisfaction.
Sourcing wafer manufacturing from China: Opportunities, Risks, and Key Players
China is a prominent player in the global wafer manufacturing industry. The country offers numerous opportunities, but also comes with certain risks. Understanding these aspects is crucial for businesses considering sourcing wafer manufacturing from China.
Opportunities:
1. Cost Advantage: China’s low labor and operational costs give it a competitive edge over other countries. This makes sourcing wafer manufacturing from China economically attractive.
2. Infrastructure: China has invested heavily in its infrastructure, particularly in technological development and research facilities. This facilitates the availability of advanced equipment and skilled labor for wafer manufacturing.
3. Growing Market Demand: As a global manufacturing hub, China offers access to a massive market. The country’s domestic market demand for wafers is also expanding due to increasing consumer electronics and semiconductor applications.
4. Supply Chain Integration: China has a well-developed supply chain network, enabling seamless integration of various manufacturing processes. This creates efficiencies and reduces lead times.
Risks:
1. Intellectual Property Protection: China has faced criticism for inadequate enforcement of intellectual property rights, making it essential for businesses to protect their technologies and patents.
2. Regulatory Compliance: China’s regulatory environment may pose challenges for foreign companies in terms of meeting compliance standards and obtaining necessary permits and licenses.
3. Quality Control: Ensuring consistent quality can be a concern as China’s manufacturing sector is vast, and maintaining stringent quality control in every facility may be difficult.
4. Geopolitical Uncertainties: Rapidly changing political dynamics and trade tensions can impact supply chain stability and trade relations with other countries.
Key Players:
1. Taiwan Semiconductor Manufacturing Company (TSMC): While technically not located in China, TSMC has a significant presence in the country due to its advanced manufacturing facilities catering to the global demand for semiconductor wafers.
2. Semiconductor Manufacturing International Corporation (SMIC): As China’s largest and most advanced semiconductor foundry, SMIC plays a crucial role in meeting the domestic demand for wafers while expanding its presence in the global market.
3. Hua Hong Semiconductor: Specializing in the design, development, and manufacturing of integrated circuits, Hua Hong Semiconductor is another major player in China’s wafer manufacturing industry.
In conclusion, sourcing wafer manufacturing from China presents opportunities in terms of cost advantages, infrastructure, market demand, and supply chain integration. However, businesses should also consider risks related to intellectual property protection, regulatory compliance, quality control, and geopolitical uncertainties. Understanding the key players, such as TSMC, SMIC, and Hua Hong Semiconductor, can help companies navigate the Chinese wafer manufacturing landscape effectively.
How to find and select reliable wafer manufacturing manufacturers in China,use google search manufacturers and suppliers
Finding and selecting reliable wafer manufacturing manufacturers in China can be a daunting task, but it can be simplified with the help of Google search and careful evaluation. Here are some steps to follow:
1. Start by conducting a Google search for “wafer manufacturing manufacturers in China.” This will provide you with a list of various companies in this industry.
2. Visit the websites of these manufacturers and explore their background, capabilities, and experience. Look for information such as the number of years they have been in business, their production capacity, certifications, and any notable clients they have worked with.
3. Evaluate the company’s reputation and reliability. Look for online reviews and testimonials from other clients or industry experts. This can give you an insight into their overall performance and customer satisfaction.
4. Check if the manufacturer has relevant certifications such as ISO 9001, ISO 14001, or other industry-specific certifications that ensure quality control and environmental standards.
5. Contact the shortlisted manufacturers and request samples of their wafer products. Evaluate the samples for quality, precision, and adherence to your specifications.
6. Inquire about the manufacturer’s production process, quality control measures, and their ability to handle customization requests.
7. Consider visiting the manufacturing facility or schedule a video call to get a better understanding of their operations, equipment, and overall production capabilities.
8. Ask for references from the manufacturer and get in touch with their existing clients to gather feedback on their experience working with the manufacturer.
9. Evaluate the pricing and payment terms offered by the manufacturer. Ensure that the price is reasonable considering the quality and capabilities of the manufacturer.
10. Finally, choose a manufacturer that meets your requirements in terms of quality, reliability, price, and capability to deliver on time.
By using Google search and applying a thorough evaluation process, you can identify and select reliable wafer manufacturing manufacturers in China that align with your specific needs.
How to check wafer manufacturing manufacturers website reliable,use google chrome SEOquake check if ranking in top 10M
To check the reliability of a wafer manufacturing manufacturer’s website, you can follow these steps:
1. Use Google Chrome: Open the website in Google Chrome, as it allows for a more in-depth analysis through various extensions.
2. Install SEOquake extension: Install the SEOquake extension in your Google Chrome browser. It provides a wealth of information about a website’s performance and ranking.
3. Check for website ranking: Once the extension is installed, click on the SEOquake icon in the toolbar and select “Page Info”. This will provide detailed insights on the website’s ranking.
4. Look for Alexa Rank: SEOquake will display the website’s Alexa Rank, which is a measure of its popularity and traffic. Check if it is ranked within the top 10 million websites. A higher Alexa Rank signifies better reliability and credibility.
5. Verify domain age: SEOquake also displays the domain age of the website. Generally, older domains are considered more reliable, as they have established themselves over time.
6. Assess backlinks and indexed pages: SEOquake will show the number of backlinks pointing to the website and the number of indexed pages. A higher number of backlinks and indexed pages generally indicate a stronger website presence and reliability.
7. Evaluate overall website design and content: Analyze the website’s design and quality of content. Look for professional design elements, clear information about the manufacturing process, comprehensive product descriptions, and contact information. A well-designed, informative website is more likely to be reliable.
By following these steps and using SEOquake extension in Google Chrome, you can gain valuable insights into the reliability of a wafer manufacturing manufacturer’s website. Remember, the information provided by SEOquake should be used as a starting point, and additional research and verification may be necessary to make a final judgment.
Top 10 wafer manufacturing manufacturers in China
1. Jiangsu Hengtai Electronics Technology Co., Ltd.: Established in 1997, Hengtai Electronics is a leading manufacturer of silicon wafers in China. They specialize in the production of 2-6 inch wafers for various applications, including microelectronics and solar energy.
2. Tongfu Microelectronics Co., Ltd.: Tongfu Microelectronics is one of the largest wafer manufacturers in China. They have a wide range of wafer sizes available, from 1 inch to 8 inches, and offer customization options to meet specific customer requirements.
3. Zhonghuan Semiconductor Co., Ltd.: Founded in 2001, Zhonghuan Semiconductor is a major player in the Chinese wafer manufacturing industry. They produce high-quality silicon wafers with sizes ranging from 2 to 12 inches, catering to the needs of the semiconductor, solar, and LED sectors.
4. Shanghai Simgui Technology Co., Ltd.: Simgui Technology specializes in the production of 2-8 inch silicon wafers. They offer a comprehensive range of wafer types, such as single-side polished, double-side polished, and epitaxial wafers, and serve industries like semiconductors, MEMS, and optoelectronics.
5. Sino-American Silicon Products Inc. (SAS): SAS is a joint venture between China and the United States, known for manufacturing 3-8 inch silicon wafers. They have a strong focus on research and development, ensuring technological advancements and high-quality products.
6. Jiangsu Jingrui Semiconductor Co., Ltd.: Jingrui Semiconductor specializes in the production of 2-8 inch silicon wafers for the semiconductor and solar industries. They are known for their advanced manufacturing equipment and stringent quality control, ensuring reliable and consistent wafer production.
7. Inner Mongolia Photovoltaic Technology Co., Ltd. (IMPV): As a leading photovoltaic wafer manufacturer, IMPV provides high-quality silicon wafers for solar cell production. They have a diverse product portfolio, ranging from 2-8 inch wafers, and focus on sustainable and eco-friendly manufacturing practices.
8. Jiangxi LDK Solar High-Tech Co., Ltd.: LDK Solar is a major player in China’s solar wafer manufacturing industry. They produce high-efficiency monocrystalline and polycrystalline silicon wafers for solar module production, catering to both domestic and international markets.
9. JA Solar Holdings Co., Ltd.: JA Solar is a prominent solar wafer manufacturer in China. They produce high-quality wafers for solar cells using advanced manufacturing techniques. With a wide range of wafer sizes available, they cater to the ever-growing solar energy market.
10. Anhui Jingli Optoelectronics Technology Co., Ltd.: Jingli Optoelectronics specializes in the production of silicon wafers for the LED industry. They offer comprehensive solutions for LED wafer manufacturing, including epitaxial growth, slicing, polishing, and inspection, ensuring precise and reliable wafer production.
These top 10 wafer manufacturing manufacturers in China showcase the country’s significant capabilities in wafer production for various industries, including semiconductors, solar energy, and LED technologies.
Background Research for wafer manufacturing manufacturers Companies in China, use qcc.com archive.org importyeti.com
When it comes to wafer manufacturing in China, several companies have made a significant impact in the industry. In this background research, information from qcc.com, archive.org, and importyeti.com will be gathered to provide an overview of some of the top wafer manufacturing manufacturers in China.
1. Wuhan Xinxin Semiconductor Manufacturing Corp. (XMC)
XMC is a leading wafer manufacturing company based in Wuhan, China. Founded in 2006, the company specializes in the design, development, and production of 300mm silicon wafers. XMC invests heavily in research and development to meet the growing demands of the semiconductor industry.
2. GlobalFoundries China
GlobalFoundries China is a prominent semiconductor foundry company with wafer manufacturing facilities in multiple locations, including Chengdu, Chongqing, and Shanghai. The company offers advanced wafer manufacturing solutions, including 12nm and 22nm process technology nodes, serving a wide range of industries such as automotive, communication, and consumer electronics.
3. Semiconductor Manufacturing International Corporation (SMIC)
SMIC is one of the largest and most advanced wafer foundries in China. The company provides integrated circuit (IC) manufacturing services, including design, research and development, and manufacturing services for both wafer fabrication and assembly. SMIC offers a broad portfolio of technology nodes, ranging from 0.35um to 14nm.
4. Huada Semiconductor Co., Ltd.
Huada Semiconductor is a well-established wafer manufacturer based in Wuxi, China. The company specializes in the production of 8-inch and 12-inch silicon wafers, offering a comprehensive product line for various applications, including microcontrollers, sensors, and power devices.
5. Shanghai Huali Microelectronics Corporation (HLMC)
HLMC is a leading wafer foundry in China, focusing on the design, development, and manufacturing of 200mm silicon wafers. The company provides comprehensive foundry services, supporting a range of technology nodes from 1.0um to 90nm. HLMC’s advanced wafer fabrication capabilities cater to the needs of sectors like automotive, industrial, and internet of things (IoT).
Please note that the information provided is a brief overview, and further research is recommended for specific details and up-to-date information on the mentioned companies.
Leveraging Trade Shows and Expos for wafer manufacturing Sourcing in China
Trade shows and expos are a powerful tool for businesses looking to source wafer manufacturing services in China. These events provide a platform for networking, acquiring new customers, and exploring potential partnerships. Leveraging trade shows and expos effectively can help companies gather valuable insights into the Chinese wafer manufacturing market.
Attending trade shows and expos in China allows businesses to directly engage with industry professionals and gain visibility within the wafer manufacturing sector. It provides an opportunity to observe the latest technological advancements, new products, and market trends. Companies can also familiarize themselves with the key players in the industry, including manufacturers, suppliers, and service providers.
Trade shows and expos offer a platform for businesses to showcase their own product or service offerings. Companies specializing in wafer manufacturing can set up booths or participate in speaking engagements to demonstrate their capabilities, establish brand presence, and generate leads. This enables them to connect with potential clients or collaborate with other industry players to expand their network.
In addition, these events facilitate face-to-face meetings and communication, which helps in building trust and strengthening relationships with Chinese manufacturers. It allows businesses to evaluate potential suppliers by assessing their equipment, production processes, quality control measures, and certifications. Attending trade shows and expos in China also provides an opportunity for on-site inspections and negotiations, ensuring that the chosen manufacturing partner meets the desired standards.
Moreover, trade shows and expos often feature workshops, seminars, and conferences, where industry experts and thought leaders share valuable insights and knowledge. Businesses can attend these sessions to stay updated on the latest advancements, industry regulations, and market dynamics relevant to wafer manufacturing in China.
In conclusion, leveraging trade shows and expos for wafer manufacturing sourcing in China offers numerous benefits. These events serve as a platform for networking, gaining industry knowledge, exploring business opportunities, and establishing partnerships. By attending trade shows and expos, businesses can effectively identify and connect with reliable suppliers while staying abreast of market trends and innovations.
The Role of Agents and Sourcing Companies in Facilitating wafer manufacturing Purchases from China
Agents and sourcing companies play a crucial role in facilitating wafer manufacturing purchases from China. These intermediaries act as a bridge between the buyer and the supplier, ensuring a smooth and efficient procurement process. Here are some key functions they perform:
1. Supplier identification and vetting: Agents and sourcing companies have extensive networks and knowledge about the local market. They help buyers identify and evaluate potential suppliers in China. This involves conducting background checks, verifying credentials, and assessing manufacturing capabilities.
2. Price negotiation: Negotiating favorable terms and pricing is a critical aspect of any purchase. Agents and sourcing companies leverage their expertise and experience to secure competitive prices on behalf of the buyers. They have a deep understanding of the local cost structure and market dynamics, enabling them to achieve the best possible deals.
3. Quality assurance: Maintaining quality standards is paramount in the manufacturing industry. Agents and sourcing companies play a crucial role in ensuring that Chinese suppliers meet the required quality criteria. They carry out regular inspections and audits, oversee production processes, and conduct rigorous quality checks before shipments.
4. Logistics and shipping coordination: Managing logistics and shipping can be complex for international buyers. Agents and sourcing companies handle all the necessary documentation, customs clearance, and transportation arrangements, ensuring a seamless flow of goods from China to the buyer’s location.
5. Cultural and language expertise: Doing business in a foreign country like China can present language and cultural barriers. Agents and sourcing companies act as intermediaries, effectively communicating buyer requirements to the suppliers. They bridge the gap between different languages, cultures, and business practices, facilitating smooth communication and understanding between both parties.
In summary, agents and sourcing companies play a vital role in facilitating wafer manufacturing purchases from China. Their expertise in supplier identification, price negotiation, quality assurance, logistics coordination, and cultural understanding streamline the procurement process, providing buyers with efficient and reliable sourcing solutions.
Price Cost Research for wafer manufacturing manufacturers Companies in China, use temu.com and 1688.com
When conducting price cost research for wafer manufacturing manufacturers in China, two popular platforms that can be utilized are temu.com and 1688.com. With a focus on efficiency, it’s essential to provide a concise summary within the limit of 300 words.
temu.com is an online platform that serves as a comprehensive marketplace connecting international buyers with Chinese manufacturers. It provides a wide range of products related to wafer manufacturing, including silicon wafers, slicing machines, and wafer testing equipment. The platform offers a simple and user-friendly interface, making it easy for users to navigate through the different categories, compare prices, and connect with suppliers directly.
1688.com, on the other hand, is a business-to-business platform owned by Alibaba Group, specifically designed for the domestic Chinese market. It hosts a multitude of suppliers and manufacturers offering various wafer manufacturing products. This platform allows users to search for specific products, obtain price quotations, and assess supplier profiles. With its vast supplier network, 1688.com allows buyers to access a wide range of wafer manufacturing manufacturers in China.
By utilizing these platforms for price cost research, buyers can gain insights into the pricing trends and the average costs of wafer manufacturing products. They can compare prices from multiple suppliers, evaluate different product specifications, and make more informed decisions based on their budget and requirements. Additionally, users can leverage the feedback and ratings from previous customers to assess the reliability and credibility of the manufacturers.
In conclusion, temu.com and 1688.com are two valuable platforms for conducting price cost research for wafer manufacturing manufacturers in China. Their extensive supplier networks, user-friendly interfaces, and competitive pricing information make them excellent resources for buyers looking to source products in this sector. By utilizing these platforms effectively, buyers can identify affordable and reliable manufacturers that meet their specific needs.
Shipping Cost for wafer manufacturing import from China
The shipping cost for wafer manufacturing imports from China can vary depending on several factors. Firstly, the distance between the origin and destination plays a crucial role in determining the price. The longer the distance, the higher the shipping cost will generally be. Additionally, the mode of transportation chosen also influences the cost. There are three common methods of shipping: air freight, sea freight, and land freight.
Air freight is the fastest option, but it is also the most expensive. It is suitable for urgent shipments or small consignments. Sea freight, on the other hand, is more cost-effective for larger quantities of goods but has a longer transit time. It is the preferred choice for most wafer manufacturing imports due to the industry’s relatively large volumes. Land freight is generally utilized when the origin and destination countries are geographically connected, such as in bordering territories.
To estimate the shipping cost, factors like the weight, volume, and dimensions of the wafer manufacturing goods must be considered. These aspects affect the space utilized in the shipping container, which influences the cost. Furthermore, customs duties, taxes, and other import/export fees should be taken into account when calculating the overall expenses associated with shipping. These costs vary depending on the countries involved and the specific regulations governing the trade.
It is essential to obtain quotes from multiple shipping companies or freight forwarders to compare prices and services. Some companies may offer additional services like customs clearance or insurance, which could affect the overall cost but provide added convenience and security. To avoid unexpected expenses or delays, it is advisable to work with reputable shipping agents or companies with experience in handling wafer manufacturing imports.
In conclusion, the shipping cost for wafer manufacturing imports from China depends on factors such as the distance, chosen mode of transportation, weight, volume, dimensions, customs duties, taxes, and other fees. Obtaining quotes from various shipping providers is crucial to ensure a cost-effective and reliable logistics solution.
Compare China and Other wafer manufacturing Markets: Products Quality and Price,Visible and Hidden Costs
When comparing China with other wafer manufacturing markets, several factors come into play, including product quality, price, and visible and hidden costs.
In terms of product quality, China has made significant advancements in recent years. With technological advancements and investment in research and development, Chinese wafer manufacturers have been able to produce high-quality products that meet international standards. However, it is important to note that quality can vary among different manufacturers in China, so thorough due diligence is necessary when selecting a supplier.
In terms of price, Chinese wafer manufacturers often have a competitive edge due to lower labor costs and economies of scale. This makes China an attractive option for companies looking for cost-effective solutions. Additionally, the abundant availability of raw materials in China further contributes to lower manufacturing costs.
When it comes to visible costs, such as manufacturing and transportation expenses, China generally offers competitive rates due to its well-developed infrastructure and logistics network. This enables efficient production and delivery of wafer products to global markets.
However, there are also hidden costs associated with manufacturing in China. These include intellectual property risks, potential language and cultural barriers, and regulatory compliance challenges. Protecting intellectual property can be a concern, as China has faced accusations of intellectual property infringement in the past. Language and cultural differences can also pose challenges in communication and collaboration with Chinese manufacturers. Additionally, navigating regulatory processes and ensuring compliance with local regulations can be time-consuming and costly.
In summary, China has made significant strides in wafer manufacturing with improved product quality and competitive pricing. However, companies should carefully consider both visible and hidden costs before making a decision. Thorough supplier evaluation, including quality checks and risk assessments, is crucial to ensure a successful and cost-effective partnership with Chinese wafer manufacturers.
Understanding Pricing and Payment Terms for wafer manufacturing: A Comparative Guide to Get the Best Deal
Pricing and payment terms play a crucial role in any business transaction, and wafer manufacturing is no exception. As a buyer, understanding these factors is essential to get the best deal and ensure a profitable and smooth operation. This comparative guide aims to shed light on some key aspects to consider when negotiating pricing and payment terms in the wafer manufacturing industry.
1. Cost Structure:
It is necessary to have a clear understanding of the cost structure involved in wafer manufacturing. This includes analyzing the cost of raw materials, production equipment, labor, overhead expenses, and any potential additional charges. By doing so, buyers can accurately determine the supplier’s pricing strategy and identify any cost-saving opportunities.
2. Volume and Timing:
The volume of wafer production and the required timing can significantly impact pricing. Typically, suppliers offer lower prices for larger order volumes due to economies of scale. Additionally, buyers may negotiate better pricing by committing to long-term contracts or by placing orders during non-peak periods when suppliers may have excess capacity.
3. Quality Requirements:
Quality requirements and specifications can also influence pricing. Higher quality standards often result in increased manufacturing costs, which may be reflected in the pricing offered by suppliers. Buyers should carefully evaluate their quality requirements and strike a balance between cost and desired product quality.
4. Payment Terms:
Flexible payment terms can offer advantages to both buyers and suppliers. Common payment methods include upfront payment, partial payments, or payment upon delivery. Negotiating extended payment terms or installment plans may improve cash flow for buyers, while suppliers might offer discounts for prompt payments or larger upfront payments.
5. Contractual Agreements:
Having a comprehensive agreement is vital to protect the interests of both parties. The contract should clearly stipulate the pricing structure, payment terms, quality specifications, delivery schedules, penalties for late delivery, and other relevant terms and conditions. Consulting legal professionals specializing in commercial contracts can help ensure a fair and enforceable agreement.
6. Competitive Analysis:
Conducting a competitive analysis is crucial to gauge the prevailing market prices and terms. Buyers should thoroughly research and compare multiple wafer manufacturers, their pricing structures, payment terms, and reputation. This information can be leveraged during negotiations to obtain competitive pricing and favorable payment terms.
In conclusion, understanding the various aspects of pricing and payment terms in wafer manufacturing is indispensable for securing the best deal. Analyzing the cost structure, volume, timing, quality requirements, and payment preferences of both parties, along with careful contract drafting and competitive analysis, can significantly contribute to successful negotiations and a mutually beneficial partnership.
Chinese Regulations and Industry Standards Certifications for wafer manufacturing,Import Regulations and Customs for wafer manufacturing from China
In China, the wafer manufacturing industry is regulated by several government organizations to ensure quality standards, safety, and environmental protection. The primary regulatory bodies involved in wafer manufacturing are the Ministry of Industry and Information Technology (MIIT), the National Development and Reform Commission (NDRC), and the China Semiconductor Industry Association (CSIA).
The MIIT is responsible for formulating regulations and standards for the wafer manufacturing industry. These regulations cover various aspects, including equipment requirements, production processes, and quality control. The MIIT also works closely with the CSIA to develop industry standards for wafer manufacturing.
Industry standards certifications play a crucial role in the wafer manufacturing sector. The most prominent certification in China is the China Compulsory Certification (CCC), which is mandatory for certain products to enter the Chinese market. However, wafer manufacturing might not fall under CCC certification requirements, as it is mainly applicable to finished products intended for consumer use. Instead, the industry focuses on other certifications such as ISO 9001:2015 for quality management system and ISO 14001:2015 for environmental management system.
When importing wafer manufacturing equipment or products from China, it is essential to comply with import regulations and customs procedures. Importers should consult with the General Administration of Customs (GAC) to understand the specific requirements for their products and ensure smooth customs clearance. It is generally necessary to provide relevant documentation, including a commercial invoice, bill of lading/airway bill, packing list, and certificates of origin.
Furthermore, certain wafer manufacturing equipment may require additional certifications or approvals. For instance, semiconductor manufacturing equipment might need the China Compulsory Product Certification (CCAP) or the China Certification of Approval (CA) before importation.
In summary, Chinese regulations and industry standards certifications ensure quality, safety, and environmental compliance in the wafer manufacturing industry. Importers of wafer manufacturing equipment or products from China should familiarize themselves with import regulations and customs procedures to facilitate a smooth import process.
Sustainability and Environmental Considerations in wafer manufacturing Manufacturing
Sustainability and environmental considerations in wafer manufacturing are crucial due to the potential negative impacts associated with this industry. Wafer manufacturing involves several processes, such as raw material extraction, chemical usage, and energy consumption, all of which can contribute to environmental degradation and resource depletion.
One important aspect to consider is the sourcing of raw materials. The extraction of minerals and other materials required for wafer production can have significant environmental consequences, including deforestation, habitat destruction, and water pollution. Therefore, it is essential for wafer manufacturers to prioritize responsible sourcing practices, such as obtaining materials from ethical and sustainable sources.
Chemical usage is another critical area where sustainability measures should be implemented. Wafer manufacturing involves the use of various chemicals, such as solvents, acids, and dopants. Improper handling and disposal of these chemicals can lead to air and water pollution, as well as soil contamination. Manufacturers should adopt strategies to minimize the use of hazardous chemicals and properly manage their disposal through recycling or safe treatment methods.
Energy consumption is a significant contributor to the environmental footprint of wafer manufacturing. The high energy requirements for processes like crystal growth, wafer slicing, and epitaxy contribute to greenhouse gas emissions and climate change. Manufacturers should implement energy-efficient equipment and technologies, such as advanced cooling systems and process optimization, to reduce energy consumption and minimize their carbon footprint.
Additionally, waste management is an integral part of sustainable wafer manufacturing. This industry generates significant amounts of waste, including silicon particles, chemicals, and wastewater. Implementing recycling programs for silicon waste can help reduce the environmental impact. Proper treatment and recycling of wastewater, along with the implementation of water conservation measures, can also minimize the strain on local water resources.
To ensure sustainability in wafer manufacturing, industry stakeholders should consider implementing eco-design principles. This involves designing products and processes that minimize environmental impacts throughout the product lifecycle, from material extraction to end-of-life disposal. Collaborative efforts between wafer manufacturers, suppliers, and customers are essential to advance sustainable practices and promote a circular economy within the industry.
In conclusion, sustainability and environmental considerations in wafer manufacturing are vital to mitigate the potential negative impacts on the environment. Responsible sourcing, minimizing chemical usage, reducing energy consumption, implementing waste management strategies, and embracing eco-design principles are some of the key practices that can contribute to a more sustainable and environmentally friendly wafer manufacturing industry.
List The Evolution history of “wafer manufacturing”
Wafer manufacturing has undergone significant evolution since its inception, with advancements in technology, materials, and processes enabling the production of smaller, faster, and more advanced electronic devices. The evolution history of wafer manufacturing can be summarized as follows:
1. Silicon Ingot Growth (1950s-1960s): The earliest wafer manufacturing involved growing cylindrical silicon ingots using the Czochralski method. These ingots were then sliced into wafers using wire saws.
2. Lapping and Polishing (1960s-1970s): In this period, the wafers were lapped and polished to achieve the desired thickness and flatness. Chemical mechanical polishing (CMP) was introduced to improve accuracy.
3. Photolithography (1960s-1970s): Photolithography revolutionized wafer manufacturing by enabling the transfer of desired patterns onto the wafer’s surface. This involved coating the wafer with a light-sensitive material (photoresist), exposing it to UV light through a mask, and selectively etching to create patterns.
4. Doping and Oxidation (1970s-1980s): To modify the conductivity of silicon, dopants such as boron or phosphorus were introduced by diffusing or implanting them into the wafer. Thermal oxidation was also employed to form insulating layers on the wafer’s surface.
5. Etching and Deposition (1980s-1990s): Chemical and plasma etching techniques were developed to selectively remove or add materials to create complex structures. Physical vapor deposition (PVD) and chemical vapor deposition (CVD) allowed for precise deposition of various materials onto the wafer’s surface.
6. Copper Interconnects (1990s-2000s): As chip complexity increased, copper replaced aluminum for interconnects due to its lower resistance. This required the development of new processes such as copper electroplating and chemical mechanical planarization (CMP).
7. 3D Integration (2000s-Present): To increase device density, wafer manufacturing shifted towards 3D integration techniques such as through-silicon vias (TSVs) and wafer bonding. This enabled stacking multiple chips vertically, reducing interconnect lengths and improving performance.
8. Advanced Materials (Present): The evolution of wafer manufacturing continues with the integration of advanced materials like gallium nitride (GaN) and silicon carbide (SiC), enabling the development of power devices that offer higher efficiency and better thermal performance.
In conclusion, wafer manufacturing has undergone a remarkable evolutionary journey from simple silicon wafers to complex structures involving advanced materials, intricate patterning techniques, and 3D integration. This continuous innovation has been instrumental in the development of increasingly powerful and efficient electronic devices that shape our modern world.
The Evolution and Market Trends in wafer manufacturing Industry
The wafer manufacturing industry has undergone significant evolution and witnessed various market trends over the years. A wafer is a thin slice of semiconductor material, typically silicon, used as a base for the fabrication of integrated circuits (ICs) and other electronic components.
One major evolution in the industry is the continuous reduction in wafer size. The transition from larger diameter wafers (e.g., 200mm) to smaller ones (e.g., 300mm) has enabled the production of more chips from a single wafer, increasing efficiency and reducing manufacturing costs. This trend has been driven by the need for higher chip density and performance in electronic devices.
Another important development in wafer manufacturing is the shift towards more advanced semiconductor materials. While silicon remains the dominant material in the industry, there is a growing demand for compound semiconductors such as gallium arsenide (GaAs), gallium nitride (GaN), and silicon carbide (SiC). These materials offer superior properties for specific applications, such as high-frequency power devices and LEDs.
In terms of market trends, one notable aspect is the increasing demand for wafer foundry services. Many fabless semiconductor companies prefer to outsource wafer fabrication to specialized foundries rather than investing in their own manufacturing facilities. This trend has given rise to the emergence of foundry giants like TSMC and GlobalFoundries, which cater to the diverse needs of the semiconductor industry.
Moreover, the adoption of advanced packaging technologies, such as 2.5D and 3D integration, has gained significant momentum in recent years. These packaging techniques enable the integration of multiple chips or die within a single package, offering improved performance in terms of speed, power efficiency, and form factor. This trend is driven by the demand for compact and high-performance electronic devices, including smartphones, wearables, and automotive electronics.
Additionally, the wafer manufacturing industry is witnessing a surge in demand for specialized chips and devices to support emerging technologies like 5G, Internet of Things (IoT), and Artificial Intelligence (AI). These technologies require specific ICs and sensors, driving the need for wafer manufacturing companies to adapt their processes and develop new capabilities.
In conclusion, the wafer manufacturing industry has evolved significantly over time, with trends focusing on smaller wafer sizes, advanced semiconductor materials, and increased outsourcing to foundries. Market trends include the adoption of advanced packaging technologies and the growing demand for chips supporting emerging technologies. The industry’s evolution and market trends continue to shape the development of electronic devices and drive innovation in the semiconductor landscape.
Custom Private Labeling and Branding Opportunities with Chinese wafer manufacturing Manufacturers
Chinese wafer manufacturing manufacturers offer a wide range of opportunities for custom private labeling and branding. With their advanced technologies and expertise in wafer production, they can help businesses create unique and high-quality products that align with their brand identity.
One major benefit of working with Chinese wafer manufacturing manufacturers is the ability to customize packaging and labeling. Businesses can design their own packaging materials, such as boxes, trays, or bags, and incorporate their logo, brand colors, and other branding elements. This allows them to create a strong brand presence on the market and enhance product recognition.
Furthermore, Chinese manufacturers offer various printing options, including printing on the wafer itself. This enables businesses to add their logo or brand name directly onto the wafer, providing a seamless branding experience for consumers. This also helps to prevent counterfeiting and ensures that products are easily identifiable as authentic.
In addition to packaging and labeling customization, Chinese wafer manufacturers often provide assistance in creating custom flavors and recipes. They have a wide range of flavors, fillings, and textures to choose from, allowing businesses to create unique and appealing products that stand out in the market. By offering exclusive flavors, businesses can attract a specific target audience and establish a niche within the wafer industry.
Another advantage of partnering with Chinese wafer manufacturers is their ability to offer competitive pricing without compromising quality. China has a robust manufacturing industry, resulting in lower production costs compared to other countries. This cost-effectiveness allows businesses to maximize their profit margins and invest more in marketing and branding activities.
Overall, Chinese wafer manufacturing manufacturers offer a range of opportunities for custom private labeling and branding. From customizable packaging and labeling options to unique flavors and recipes, businesses can create products that accurately represent their brand identity and resonate with their target market. Moreover, the competitive pricing ensures that businesses can achieve profitability while maintaining high-quality products.
Tips for Procurement and Considerations when Purchasing wafer manufacturing
Procurement of wafer manufacturing equipment involves several considerations to ensure a smooth and efficient manufacturing process. Here are some tips and essential factors to consider when purchasing wafer manufacturing equipment:
1. Reliability and quality: Prioritize the procurement of equipment from trusted and reputable suppliers. Look for manufacturers with a proven track record and positive customer reviews, as it indicates high reliability and quality.
2. Technology advancement: Consider the latest technological advancements in wafer manufacturing equipment. Up-to-date equipment offers improved efficiency, accuracy, and productivity, resulting in higher-quality wafers and reduced downtime.
3. Customization options: Look for suppliers who provide customizable equipment. Each manufacturing facility has unique requirements, so having the flexibility to tailor the equipment to your specific needs can significantly improve overall performance.
4. Cost: Analyze your budget and the total cost of ownership (TCO) when considering equipment procurement. It’s not just about the initial purchasing cost, but also ongoing maintenance, operational costs, and potential upgrades. Ensure that the equipment offers long-term value for your investment.
5. Energy efficiency: Consider the energy consumption of the equipment. Energy-efficient systems can help reduce operational costs and contribute to sustainability goals. Look for equipment with features like automatic shut-off and power-saving modes.
6. Supplier support and training: Evaluate the level of support and training offered by the equipment supplier. As wafer manufacturing technology evolves, regular training and support are crucial to optimize equipment utilization and to keep up with any software or hardware updates.
7. Scalability of equipment: If you have plans for future expansion, consider the scalability of the equipment. Ensure that it can accommodate increased production volumes or new advanced processes, so you can avoid disruptions as your business grows.
8. Compliance with standards: Verify that the equipment meets all relevant industry standards and certifications. Compliance ensures operational safety, quality control, and facilitates the integration of the equipment with existing manufacturing processes.
9. Warranty and maintenance: Understand the warranty terms and after-sales services provided by the supplier. Robust warranty coverage and maintenance agreements help mitigate risks and ensure continued equipment performance.
10. Long-term partnerships: Consider establishing long-term partnerships with equipment suppliers who can provide ongoing technical support, spare parts availability, and continuous improvement or upgrade options.
In summary, careful consideration of reliability, customization options, cost, energy efficiency, support, scalability, compliance, warranty, and long-term partnerships can greatly influence the procurement process for wafer manufacturing equipment.
FAQs on Sourcing and Manufacturing wafer manufacturing in China
Q1: What is wafer manufacturing?
Wafer manufacturing is the process of producing thin, round slices of semiconductor material, typically made from silicon. These wafers serve as the foundation for the production of integrated circuits (ICs) and other microdevices used in electronic devices.
Q2: Why source wafer manufacturing from China?
China is a prominent global hub for manufacturing, and sourcing wafer manufacturing from China offers several advantages. Firstly, the country has a well-established semiconductor industry, with numerous factories equipped with advanced technology and skilled labor. China also has a vast domestic market for electronic devices, driving the demand for wafer manufacturing capabilities. Additionally, sourcing from China often provides cost advantages due to lower production costs, competitive wages, and access to raw materials.
Q3: What are the key considerations when sourcing wafer manufacturing in China?
When sourcing wafer manufacturing in China, several factors must be considered. Firstly, it is imperative to research and select a reputable and experienced manufacturing company with a proven track record in wafer manufacturing. This includes assessing their certifications, quality control processes, and adherence to industry standards. Intellectual property protection measures should also be evaluated to ensure the safety of proprietary designs and technologies.
Moreover, communication and language barriers should be addressed by working with manufacturers that have efficient English-speaking staff or hiring local translators. It is crucial to establish clear agreements on pricing, delivery schedules, and quality control measures to avoid misunderstandings and ensure a smooth production process.
Q4: Are there any potential challenges when sourcing wafer manufacturing from China?
While sourcing wafer manufacturing from China has its advantages, there are potential challenges that need to be considered. These include intellectual property protection concerns, quality control issues, and long-distance logistics. It is crucial to implement contractual agreements and protection measures to safeguard intellectual property rights. Quality control processes should be closely monitored, and frequent inspections and audits may be required to ensure adherence to specifications and standards. Additionally, managing logistics and transportation can be complex due to the distance involved, necessitating careful planning and coordination.
Q5: What are the steps involved in wafer manufacturing?
Wafer manufacturing involves several steps, including crystal growth, wafering, surface preparation, doping, lithography, etching, deposition, and packaging. Crystal growth involves melting and growing the semiconductor material to form a cylindrical ingot, which is then sliced into thin wafers. The wafers undergo surface preparation, wherein impurities and defects are removed. Doping introduces specific impurities to create desired electronic properties. Lithography, etching, and deposition processes are used to pattern and modify the wafer surface, creating microcircuits. Finally, the wafers are packaged and tested for functionality and quality assurance.
In conclusion, wafer manufacturing in China offers significant advantages in terms of cost-effectiveness, skilled labor, and a well-established semiconductor industry. However, potential challenges include ensuring intellectual property protection, maintaining quality control standards, and managing logistics. Thorough research and due diligence are essential when sourcing from China to ensure a successful wafer manufacturing partnership.
Why contact sourcifychina.com get free quota from reliable wafer manufacturing suppliers?
Sourcifychina.com offers free quota to its users from reliable wafer manufacturing suppliers for several reasons. Firstly, providing free quotas allows Sourcifychina.com to attract more potential customers and expand its user base. By offering a valuable service at no cost, they can generate interest and capture a larger market share.
Secondly, wafer manufacturing suppliers may offer free quotas as a promotional strategy. By providing a certain amount of their products or services for free, suppliers can showcase the quality of their wafers and demonstrate the benefits of working with them. This can help build trust and encourage potential customers to consider purchasing from these suppliers in the future.
Additionally, obtaining a free quota from reliable wafer manufacturing suppliers allows businesses to test the quality, compatibility, and suitability of the wafers for their specific applications without committing to a large purchase. This enables them to assess whether the supplier’s products meet their requirements and align with their overall business goals. It helps businesses avoid potential risks and losses associated with investing in large quantities of wafers upfront without prior evaluation.
Moreover, offering free quotas can foster long-term relationships between suppliers and potential customers. It provides an opportunity for both parties to establish a connection, communicate effectively, and develop trust. This can lead to future collaborations, partnerships, and a mutually beneficial business relationship.
In conclusion, Sourcifychina.com offers free quotas from reliable wafer manufacturing suppliers as a means to attract customers, promote the suppliers’ products, allow businesses to test the quality of the wafers, and foster long-term relationships. This strategy benefits both the users and the wafer manufacturing suppliers, creating a win-win situation for all parties involved.