Introduce about cutter metal machine guide,Qulity,Cost,Supplier,Certification,Market,Tips,FAQ
The Cutter Metal Machine Guide is a comprehensive manual that serves as a go-to resource for individuals or businesses seeking information on metal cutting machinery. It provides valuable insights into various aspects, including quality, cost, suppliers, certifications, market trends, and helpful tips.
Quality is a paramount consideration when selecting a metal cutting machine. The guide helps you understand the key parameters to assess the quality of a machine, such as material durability, precision, and efficiency. It also offers recommendations on reliable brands or models known for their superior performance.
Cost is another crucial factor discussed in the guide. It provides a breakdown of the typical pricing range for different types of metal cutting machines, assisting you in making an informed decision based on your budget and requirements. Additionally, it highlights cost-effective options and factors to consider to minimize operational expenses in the long run.
Finding a trustworthy supplier can be a daunting task. The guide offers insightful tips to identify reputable suppliers and provides a list of credible manufacturers or distributors globally. This information equips you with the necessary knowledge to make an informed decision and build a reliable supply chain for your metal cutting machinery needs.
Certifications play a vital role in guaranteeing the quality and safety of metal cutting machines. The guide outlines various certifications and standards relevant to the industry, helping you ensure that the machine you choose meets the necessary requirements and complies with safety regulations.
The market section of the guide sheds light on the current trends and developments in the metal cutting machinery industry. It provides an overview of the global market, regional analyses, growth projections, and emerging technologies. This information enables you to understand the market dynamics and make strategic decisions to stay competitive.
In addition to the above, the guide offers practical tips on machine maintenance, operation techniques, and troubleshooting common issues. It serves as a handy resource to optimize the performance of your metal cutting machine and extend its lifespan.
Furthermore, a FAQ section addresses common queries and concerns related to metal cutting machinery. It covers topics ranging from machine types and applications to maintenance tips and troubleshooting methods. This section provides quick answers to frequently asked questions, saving you time and effort in searching for information.
In summary, the Cutter Metal Machine Guide is a comprehensive resource that covers various aspects of metal cutting machinery. It assists readers in evaluating quality, understanding costs, finding reliable suppliers, knowing certifications, staying updated on market trends, obtaining practical tips, and addressing common queries. Utilizing the information provided, you can make well-informed decisions and optimize the performance of your metal cutting machines efficiently.
Types of cutter metal machine
There are several types of metal cutting machines available in the market that cater to specific cutting requirements. It is essential to choose the right type of cutter machine based on the type and thickness of the metal being cut. Here are some common types of cutter metal machines:
1. Bandsaw: It consists of a continuous metal band equipped with teeth that rotates on two or more wheels. Bandsaws are suitable for straight and curved cuts and are commonly used for cutting thick metal sheets or bars.
2. Laser Cutting Machine: This machine uses a high-powered laser to cut through metal. It provides precision cuts and is highly efficient for complex shapes and designs. Laser cutting machines are suitable for thin to medium metal sheets.
3. Plasma Cutting Machine: It uses a combination of high-velocity ionized gas (plasma) and an electrical arc to cut through metal. Plasma cutting machines can cut through thick metal sheets quickly and are commonly used in industrial settings.
4. Water Jet Cutting Machine: This machine utilizes a high-pressure jet of water mixed with abrasive materials to cut through metal. Water jet cutting machines can produce intricate and precise cuts on a wide range of metal thicknesses.
5. CNC Milling Machine: It uses computer numerical control (CNC) technology to cut metal. Milling machines can perform various cutting operations like drilling, slotting, and contouring. They are versatile and suitable for machining complex metal parts.
6. Shearing Machine: It is used to cut sheets of metal using a shearing action. Shearing machines can effectively cut straight lines but are not suitable for intricate or curved cuts. They are commonly used in metal fabrication workshops.
7. Plasma Arc Cutter: It uses a plasma torch to cut through metal. Plasma arc cutters are portable and can cut through both thin and thick metal sheets. They are widely used in construction, automotive, and DIY applications.
Remember that these are just a few examples of cutter metal machines, and there are many other specialized machines available for specific cutting requirements. It is crucial to select the right machine that suits your specific needs to ensure efficient metal cutting operations.
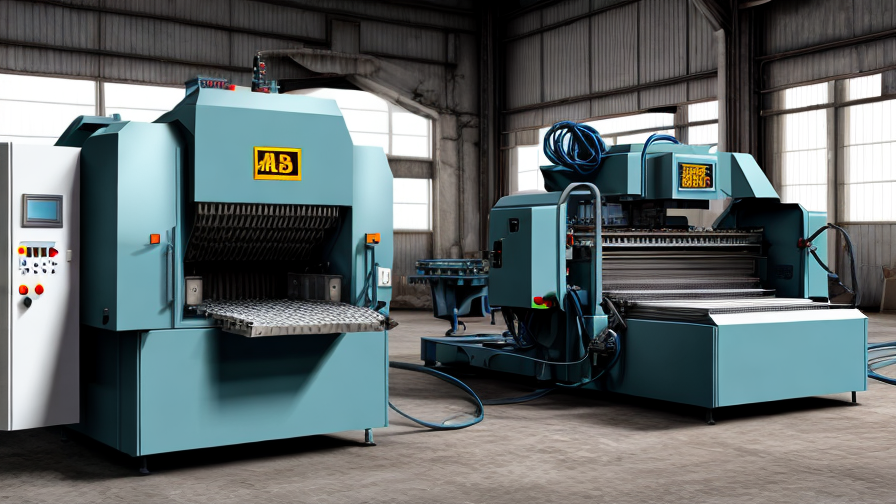
Pros and Cons of Using cutter metal machine
Pros:
1. Precision: Cutter metal machines are extremely accurate and can produce precise cuts, allowing for high-quality results.
2. Efficiency: These machines are designed for high-speed cutting, enabling faster production times and increased productivity.
3. Versatility: Cutter metal machines can handle various types of metal, including steel, aluminum, and brass, making them suitable for a wide range of applications.
4. Automation: Many cutter metal machines are automated, reducing the need for manual labor and increasing overall efficiency.
5. Cost-effective: While the initial cost of purchasing a cutter metal machine may be high, the long-term savings on labor costs and increased productivity make it a cost-effective investment.
6. Reduced waste: The accuracy of cutter metal machines minimizes material waste, resulting in cost savings and more sustainable manufacturing processes.
7. Customization: These machines can be programmed to perform various cutting patterns and designs, allowing for customization in metal fabrication projects.
Cons:
1. High initial cost: Purchasing a cutter metal machine can be costly, especially for smaller businesses or individuals.
2. Maintenance and repair: These machines require regular maintenance and occasional repair, which can add to the overall cost of ownership.
3. Training and skills: Operating a cutter metal machine requires specialized training and skills, which may necessitate additional training or hiring skilled operators.
4. Limited flexibility: Cutter metal machines are designed for specific purposes and may not be suitable for all cutting applications. This may limit the versatility of these machines.
5. Noise and safety hazards: These machines can generate significant noise and pose safety risks, such as sharp metal parts and potential for accidents if not operated properly.
6. Size and space requirements: Some cutter metal machines can be large and require substantial space in the manufacturing facility or workshop.
7. Dependence on electricity: These machines rely on electricity to function, which can be a limitation in areas with unreliable or limited power supply.
In conclusion, using a cutter metal machine offers numerous benefits such as precision, efficiency, versatility, and customization options. However, it comes with drawbacks such as high initial cost, maintenance requirements, necessary skills, limited flexibility, safety hazards, space requirements, and dependence on electricity.
cutter metal machine Reference Specifications (varies for different product)
The reference specifications for a metal cutting machine can vary depending on the specific product. These machines are designed to cut various types of metal materials such as steel, aluminum, and copper. They are commonly used in industries such as manufacturing, construction, and automotive.
One key specification for a metal cutting machine is the cutting capacity. This refers to the maximum thickness of the metal that the machine can effectively cut. For example, a particular model may have a cutting capacity of up to 10mm for steel and 5mm for aluminum. It is essential to consider the intended use and required thickness of the materials when selecting a metal cutting machine.
Another important specification is the cutting speed. This refers to the rate at which the machine can cut through the metal. It is typically measured in meters per minute (m/min). The cutting speed can vary depending on the type of metal being cut and the specific machine model. Faster cutting speeds can improve productivity but may also require additional cooling or lubrication systems to prevent overheating or tool wear.
The power of the cutting machine is another significant factor. It is generally measured in watts (W) or kilowatts (kW). Higher power machines can handle more challenging cutting tasks and thicker materials. However, it is crucial to balance power requirements with energy consumption and operational costs.
The accuracy of the machine is another consideration. This refers to how precisely the machine can follow a predetermined cutting path. For metal cutting machines, accuracy is typically expressed in millimeters or micrometers. Higher accuracy ensures clean, consistent cuts, especially in applications that require tight tolerances.
Additionally, safety features play a critical role in metal cutting machines. These can include emergency stop buttons, safety curtains, and protective enclosures to prevent operator injuries. Compliance with safety standards and certifications is vital when selecting a metal cutting machine to ensure a safe working environment.
Other specifications that can vary for different products include the type of cutting technology used (such as plasma, laser, or waterjet), the size and weight of the machine, the control systems employed (such as CNC or manual), and additional features like automatic feeding systems or integrated material handling.
In conclusion, when referring to reference specifications for a metal cutting machine, factors like cutting capacity, cutting speed, power, accuracy, safety features, and technology are crucial considerations. These specifications will vary depending on the specific product and its intended applications.
Applications of cutter metal machine
A cutter metal machine is a versatile tool used in various applications across industries. With its ability to cut and shape metal materials accurately and efficiently, it has become an indispensable tool for many professionals. Here are some of the main applications of a cutter metal machine:
1. Metal fabrication: One of the primary uses of a cutter metal machine is in metal fabrication. It allows manufacturers and fabricators to cut, shape, and form metal sheets, rods, and tubes into desired sizes and shapes. This is crucial for the production of metal components used in various industries, such as automotive, aerospace, construction, and appliances.
2. Welding and construction: In welding and construction, a cutter metal machine is used to precisely cut metal plates, beams, and pipes. It ensures that the metal pieces fit together perfectly, facilitating a seamless welding process and resulting in robust and durable structures.
3. Signage and advertising: The signage and advertising industry heavily relies on cutter metal machines for creating attractive and eye-catching displays. These machines enable the precise cutting of metal sheets and letters, allowing for the production of intricate and customized signs, billboards, and other advertising materials.
4. Metal recycling: As part of the metal recycling process, a cutter metal machine is used to efficiently cut and shred metal scraps into smaller pieces. This facilitates the melting and reforming of the metal, making it easier to reuse in the production of new products.
5. Jewelry making: In the jewelry industry, a cutter metal machine is indispensable for cutting and shaping precious metals like gold, silver, and platinum. This enables jewelers to create intricate designs and customized jewelry pieces with precision and accuracy.
6. Prototyping and manufacturing: Manufacturers and product designers use cutter metal machines to create prototypes and small-scale production runs. These machines allow for the efficient and cost-effective fabrication of metal components, ensuring accuracy and consistency in the manufacturing process.
7. DIY and hobbyist projects: Enthusiasts and hobbyists often utilize cutter metal machines for their DIY projects. Whether it is for creating metal sculptures, home décor items, or custom furniture pieces, these machines offer the convenience of precise cutting and shaping of metal materials at a smaller scale.
In conclusion, a cutter metal machine finds applications in various industries and sectors. Its versatility, accuracy, and efficiency make it an essential tool for metal fabrication, welding, construction, signage, jewelry making, recycling, prototyping, manufacturing, and even DIY projects. With advancements in technology, cutter metal machines continue to evolve, providing enhanced capabilities and expanding their applications in the future.
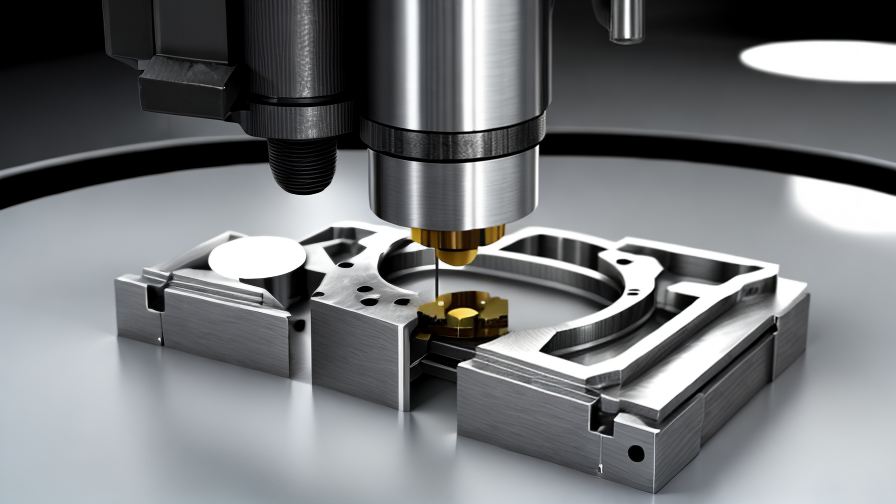
The Work Process and how to use cutter metal machine
The work process of using a cutter metal machine generally involves the following steps:
1. Safety Precautions: Before starting, ensure that you are wearing appropriate personal protective equipment such as safety goggles, gloves, and a face mask. Make sure the machine is in good working condition and all safety guards are in place.
2. Material Preparation: Choose the appropriate metal sheet or rod that needs to be cut. Measure and mark the desired dimensions using a ruler and a marking tool.
3. Machine Setup: Adjust the machine settings according to the material being cut, such as selecting the appropriate cutting tool (blade, disc, or abrasive wheel) and adjusting the cutting speed and depth.
4. Machine Operation: Securely fasten the metal piece to the machine’s worktable or clamp it in place using a vice. Switch on the metal cutter machine, ensuring you’re following the manufacturer’s instructions. Slowly feed the metal piece into the cutter using a controlled motion, applying light, consistent pressure.
5. Cutting Process: Allow the machine to do the cutting, applying only minimal force yourself. Keep the metal piece against the guide or fence throughout the cutting process to ensure straight, accurate cuts. Avoid excessive heat buildup by intermittently withdrawing the metal piece to allow it to cool.
6. Finishing Touches: Once the cutting is complete, switch off the machine and let it come to a complete stop. Inspect the cut edges for any roughness or burrs. If required, use a deburring tool or sandpaper to smoothen the edges.
7. Clean Up: Remove any metal scraps or debris from the machine and work area. Store the cutting tools safely.
It is important to familiarize yourself with the specific guidelines and safety precautions provided by the manufacturer of the metal cutter machine you are using. Always consult the user manual and seek proper training if necessary to ensure safe and effective operation of the machine.
Quality Testing Methods for cutter metal machine and how to control the quality
When it comes to quality testing methods for cutter metal machines, there are several approaches that can be adopted to ensure the desired level of quality and performance. Some key methods include:
1. Visual Inspection: This involves examining the cutter metal machine for any visible defects such as cracks, dents, or missing parts. Visual inspection helps identify any potential issues that may affect the quality of the machine.
2. Dimensional Measurement: Accurate measurements of the key dimensions of the machine parts can be performed using precision tools such as vernier calipers or micrometers. This ensures that the machine components meet the required specifications and tolerances.
3. Functional Tests: Performing functional tests involves running the cutter metal machine under various operating conditions to assess its performance. This includes testing the machine for its cutting accuracy, speed, power, and overall functionality. It helps identify any performance issues or limitations.
4. Material Testing: Evaluating the composition and properties of the metal used in the machine is crucial to ensure its quality and durability. This can be done through various material testing methods such as hardness testing, chemical analysis, or tensile testing.
To control the quality of cutter metal machines, it is important to implement effective quality control measures throughout the manufacturing process. This can include:
1. Supplier Qualification: Collaborating with trusted suppliers who provide high-quality raw materials and components is essential. Supplier qualification processes should be in place to evaluate the reliability and quality of the materials supplied.
2. Quality Assurance Plan: Developing a comprehensive quality assurance plan that outlines the specific quality requirements, inspection criteria, and testing procedures is vital. This plan should cover all stages of manufacturing, from raw material inspection to final assembly.
3. Process Control: Implementing strict process controls ensures that each manufacturing step is carried out consistently and accurately. Regular audits and inspections should be conducted to identify any deviations or non-conformities in the manufacturing processes.
4. Training and Skill Development: Regular training programs should be organized to enhance the skills and knowledge of the manufacturing personnel. This helps to ensure that they are equipped with the necessary expertise to maintain and control the quality of the cutter metal machines.
By implementing these quality testing methods and control measures, manufacturers can ensure that the cutter metal machines meet the required standards and provide reliable and accurate cutting performance.
cutter metal machine Sample Policy and Post-Purchase Considerations for cutter metal machine from China
Sample Policy:
When purchasing a cutter metal machine from China, it is advisable to request a sample before making a bulk order. This allows you to evaluate the quality, functionality, and performance of the machine. Some suppliers may offer free samples, while others may charge a nominal fee or request you to cover the shipping costs.
When requesting a sample, specify your requirements, such as the machine model, specifications, voltage compatibility, and any additional features you desire. Ensure that the supplier understands your expectations clearly and provides a sample that meets your specifications.
Post-Purchase Considerations:
After receiving the sample and judging its suitability for your needs, there are a few post-purchase considerations to keep in mind:
1. Quality Control: Check the sample thoroughly for defects or any deviations from your requirements. Ensure that the machine functions properly and meets the expected standards. If any issues are found, communicate them to the supplier immediately.
2. Certification and Compliance: Verify if the machine complies with safety and quality standards, such as CE certification. This is particularly important, as non-compliant machines may not meet the safety standards of your country, potentially causing harm to workers or violating regulations.
3. Warranty and After-Sales Service: Inquire about the warranty period offered by the supplier and their after-sales service. A reliable supplier should provide a reasonable warranty period and be responsive to queries or issues that may arise during or after the machine’s operation.
4. Spare Parts and Components: Check if the supplier offers readily available spare parts and components for the machine. This ensures that in case of any future repairs or replacements, you can easily access the required parts without delays or complications.
5. Feedback and Reviews: Research the supplier’s reputation by reading customer feedback and reviews. Look for positive experiences and customer satisfaction in terms of product quality, timely delivery, and customer support.
In conclusion, requesting a sample before placing a bulk order for a metal cutter machine from China allows you to assess its quality and suitability. Ensure compliance with safety standards, consider warranty and after-sales service, and seek customer feedback to make an informed purchase decision.
Sourcing cutter metal machine from China: Opportunities, Risks, and Key Players
Sourcing cutter metal machines from China presents numerous opportunities to businesses in terms of cost-effectiveness and availability of a wide range of options. China has emerged as a major player in the manufacturing industry and has been offering competitive prices for various machinery and equipment. The metal cutting industry in China is no exception.
One of the main advantages of sourcing cutter metal machines from China is the cost advantage. Chinese manufacturers generally offer lower prices compared to their counterparts in other countries, making it an attractive option for businesses looking to optimize their costs. Additionally, China has a well-established supply chain and a vast network of suppliers, ensuring a wide range of options to choose from. This enables businesses to find the most suitable cutter metal machine to meet their specific requirements.
However, there are certain risks associated with sourcing from China. Quality control can be a concern, especially when dealing with unknown or unreliable suppliers. It is essential to conduct thorough research and due diligence on potential suppliers, ensuring they have a track record of delivering high-quality products. Communication and language barriers can also pose challenges, which may impact the efficiency of the sourcing process.
When sourcing cutter metal machines from China, it is important to identify key players in the industry. Some prominent Chinese manufacturers of metal cutting machinery include Bodor Laser, Bystronic, Amada, Trumpf, and Jinan Senfeng Technology. These companies have established themselves as leaders in the field, offering advanced technology, reliable products, and efficient after-sales services.
In conclusion, sourcing cutter metal machines from China provides significant opportunities for businesses due to competitive pricing and a wide range of options. However, it is crucial to carefully navigate the risks associated with quality control and communication. Identifying key players in the industry ensures access to reliable and technologically advanced products. Overall, with proper research and due diligence, businesses can successfully leverage the benefits of sourcing cutter metal machines from China.
How to find and select reliable cutter metal machine manufacturers in China,use google search manufacturers and suppliers
To find and select reliable metal cutter machine manufacturers in China, you can follow these steps:
1. Start by conducting a Google search: Use relevant keywords such as “metal cutter machine manufacturers in China” or “reliable metal cutting machine suppliers in China.” This will generate a list of manufacturers and suppliers.
2. Evaluate the websites: Go through the websites of the listed manufacturers and suppliers to gather initial information. Look for key indicators of reliability such as years in operation, certifications, quality control measures, and experience in the industry.
3. Verify business legitimacy: Check if the company has a valid business license and proper documentation. You can also search for their company registration number to ensure they are legally registered.
4. Assess manufacturing capabilities: Look for information about their manufacturing facilities, equipment, and production capacity. A well-equipped and modern facility indicates that the manufacturer is capable of producing high-quality cutting machines.
5. Check product quality: Look for any certifications or accreditations that ensure the quality of their products. Also, read customer reviews and testimonials to gauge their reputation and satisfaction levels.
6. Inquire about customization and technical support: If you require specific customization options or technical assistance, contact the manufacturers to inquire about their capabilities in these areas. A reliable manufacturer will have a responsive customer service team that can address your queries promptly.
7. Pricing and payment terms: Request price quotes from multiple manufacturers to compare costs. Be cautious of unusually low prices, as they may indicate subpar quality. Also, discuss payment terms and any additional fees or charges associated with the purchase.
8. Communication and language proficiency: Check if the manufacturer has proficient English communication skills to ensure smooth communication throughout the process. Prompt and clear communication is essential for a successful business relationship.
9. Consider a factory visit: If feasible, plan a visit to the manufacturer’s facility to assess their manufacturing process, quality control measures, and overall operations. This will provide firsthand information to make an informed decision.
10. Request samples and warranties: Finally, ask for product samples to assess the quality firsthand. Also, inquire about warranties and after-sales support, which are indicative of a manufacturer’s confidence in their products.
By following these steps, you can thoroughly evaluate and select reliable metal cutter machine manufacturers in China that meet your requirements.
How to check cutter metal machine manufacturers website reliable,use google chrome SEOquake check if ranking in top 10M
To check the reliability of a cutter metal machine manufacturer’s website, you can follow these steps:
1. Open Google Chrome: Launch your Google Chrome web browser, which is widely used and supports various reliable tools for website analysis.
2. Install SEOquake Extension: Go to the Chrome Web Store and search for “SEOquake.” Install the extension developed by Semrush to gather relevant data about the website’s ranking and other useful information.
3. Activate SEOquake Extension: Once installed, activate the SEOquake extension by clicking on its icon in your browser’s toolbar.
4. Enter the Manufacturer’s Website URL: Type the URL of the cutter metal machine manufacturer’s website in the address bar of your browser.
5. Analyze Website’s SEO Data: SEOquake will automatically display a result bar at the top of the manufacturer’s website. Look for the “Google Index” metric, which indicates the website’s ranking position among the top 10 million websites.
6. Check Google Index Rank: If the website’s Google Index rank is below 10 million, it means that the website falls within the top 10 million websites globally. This indicates that the website has a relatively high level of exposure and could be considered more reliable.
7. Further Research: While SEOquake helps determine the website’s ranking, it is advisable to conduct additional research to assess the overall credibility of the manufacturer. Look for customer reviews, industry certifications, and any other relevant information available on the website.
By using these steps and the SEOquake extension, you can quickly evaluate the reliability of a cutter metal machine manufacturer’s website. Remember to consider other factors besides ranking, such as customer reviews and industry reputation, to make a well-informed decision.
Top 10 cutter metal machine manufacturers in China
China is renowned for its manufacturing capabilities, and the metal cutting machine industry is no exception. The following is a list of the top 10 metal cutting machine manufacturers in China.
1. Ji’nan Bodor CNC Machine Co., Ltd. – Bodor specializes in the research, development, and production of fiber laser cutting machines, offering high-quality machines with advanced technology and excellent performance.
2. Wuhan Hans GS Laser Technology Co., Ltd. – Hans GS Laser is a leading manufacturer of laser engraving and cutting machines. They offer a wide range of machines suitable for various metal cutting applications.
3. Shanghai Fenghe Intelligent Technology Co., Ltd. – Fenghe Intelligent Technology is a well-known manufacturer of CNC plasma and flame cutting machines. They provide precision cutting solutions for various metal materials.
4. Shandong CCI Co., Ltd. – CCI is a professional manufacturer of plasma cutting machines. Their product range includes portable plasma cutting machines, CNC plasma cutting machines, and more.
5. Jinan Finework CNC Machinery Co., Ltd. – Finework specializes in the production of plasma cutters, laser cutting machines, and other CNC machines. They offer high-quality machines suitable for different metal cutting requirements.
6. Nanjing Boduan CNC Machine Tool Co., Ltd. – Boduan CNC Machine Tool is known for its CNC engraving and milling machines, as well as laser cutting machines. Their machines are widely used in the metalworking industry.
7. Guangzhou Dragon Diamond Technology Co., Ltd. – Dragon Diamond Technology focuses on the production of laser cutting machines, offering a wide range of solutions for metal cutting applications.
8. Suzhou Naiwei CNC Technology Co., Ltd. – Naiwei CNC Technology specializes in the production of CNC milling machines, engraving machines, and laser cutting machines.
9. Wuhan Optical Valley Laser Equipments Co., Ltd. – Optical Valley Laser Equipments is a prominent manufacturer of laser cutting machines, laser engraving machines, and other laser equipment for metal cutting.
10. Ningbo Maxtors CNC Machinery Co., Ltd. – Maxtors CNC Machinery offers a comprehensive range of metal cutting machines, including laser cutting machines, plasma cutting machines, and more.
These top 10 metal cutting machine manufacturers in China deliver high-quality machines that meet international standards. From fiber laser cutting machines to plasma cutting machines, they provide solutions to cater to various metal cutting requirements.
Background Research for cutter metal machine manufacturers Companies in China, use qcc.com archive.org importyeti.com
In China, there are several manufacturers of cutter metal machines that offer reliable and cost-effective solutions for cutting various types of metals. Some prominent manufacturers in this industry include Jinan Bodor CNC Machine Co., Ltd., Hako CNC Machine (Anhui) Manufactory Co., Ltd., and Perfect Laser (Wuhan) Co., Ltd.
Jinan Bodor CNC Machine Co., Ltd. is a leading manufacturer of CNC metal cutting machines with a wide range of products, including fiber laser cutting machines, CO2 laser cutting machines, and plasma cutting machines. The company has a well-established reputation for producing high-quality machines and providing excellent after-sales service.
Hako CNC Machine (Anhui) Manufactory Co., Ltd. specializes in the production of CNC cutting machines, including fiber laser cutting machines, plasma cutting machines, and flame cutting machines. With extensive experience in the industry, Hako CNC has gained a strong presence both in the domestic and international markets.
Perfect Laser (Wuhan) Co., Ltd. is another prominent manufacturer of metal cutting machines in China. The company offers a comprehensive range of machines, including fiber laser cutting machines, CO2 laser cutting machines, and plasma cutting machines. Perfect Laser is known for its advanced technology, precision, and durability of its machines.
To gather more information on these companies, one can refer to websites such as qcc.com, archive.org, and importyeti.com. Qcc.com provides company profiles, product information, and contact details of various manufacturers in China. Archive.org offers a platform to explore archived web pages, which can provide insights into the historical development and reputation of these companies. Importyeti.com allows users to search for import/export records of companies, which can give an idea of their international business operations.
By utilizing these resources, one can gain a comprehensive understanding of the leading cutter metal machine manufacturers in China, their product offerings, market presence, and reputation in the industry.
Leveraging Trade Shows and Expos for cutter metal machine Sourcing in China
Trade shows and expos are excellent platforms for sourcing cutter metal machines in China. By attending these events, businesses can connect with a wide range of suppliers and manufacturers, gather valuable market intelligence, and explore the latest advancements in the industry.
One of the key advantages of attending trade shows and expos is the opportunity to meet face-to-face with potential suppliers. This allows businesses to establish personal relationships, evaluate the quality of products, and negotiate terms and prices. Meeting suppliers directly also enables businesses to gain a better understanding of their capabilities, production processes, and quality control procedures.
Furthermore, trade shows and expos provide businesses with an extensive selection of cutter metal machines. This allows for a comprehensive comparison of different suppliers and their products, helping businesses make informed decisions. By seeing the machines in action and experiencing their performance firsthand, businesses can better assess their suitability for their specific needs.
Trade shows and expos also provide a platform for networking and learning from industry experts. Seminars, workshops, and panel discussions offer valuable insights into the latest trends, technologies, and best practices in the cutter metal machine industry. By engaging in these educational sessions, businesses can stay updated on industry developments and gain a competitive edge.
In addition, trade shows and expos allow businesses to gather market intelligence. By observing competitors’ offerings, pricing strategies, and marketing tactics, businesses can gain insights into the overall market dynamics. This information can help businesses refine their sourcing strategies, identify gaps in the market, and make informed decisions about potential suppliers.
To make the most out of trade shows and expos, businesses should come prepared. Conducting thorough research beforehand, setting clear objectives, and scheduling meetings with desired suppliers can maximize the efficiency of the sourcing process. Following up with suppliers after the event is also crucial to build and maintain strong relationships.
In conclusion, trade shows and expos provide invaluable opportunities for businesses to source cutter metal machines in China. By attending these events, businesses can connect with suppliers, compare products, gather market intelligence, and stay updated on industry trends. With proper preparation and follow-up, trade shows and expos can significantly enhance the sourcing process.
The Role of Agents and Sourcing Companies in Facilitating cutter metal machine Purchases from China
Agents and sourcing companies play a crucial role in facilitating cutter metal machine purchases from China. They act as intermediaries between buyers and manufacturers, helping to bridge language and cultural barriers, provide market knowledge, and ensure smooth transactions. Here are the key ways in which agents and sourcing companies facilitate cutter metal machine purchases:
1. Supplier Identification: Agents and sourcing companies have extensive networks and relationships with various manufacturers in China. They leverage their industry knowledge and expertise to identify reliable and suitable suppliers for cutter metal machines. This ensures that buyers have access to a wide range of options and can choose from high-quality manufacturers.
2. Negotiation and Communication: Due to language barriers, it can be challenging for international buyers to communicate their requirements, negotiate prices, and resolve any issues that may arise during the purchasing process. Agents and sourcing companies act as translators and negotiators, ensuring smooth communication between buyers and manufacturers. They facilitate discussions, clarify specifications, and resolve misunderstandings, thus streamlining the purchasing process.
3. Quality Control and Inspection: Agents and sourcing companies play a crucial role in ensuring the quality of cutter metal machines. They conduct factory audits, quality inspections, and pre-shipment inspections to verify the product’s quality, reliability, and compliance with the buyer’s specifications. This minimizes the risk of receiving substandard or faulty machines.
4. Logistics and Shipping: International shipping and logistics can be complex and time-consuming. Agents and sourcing companies take care of the logistical aspects, including packaging, documentation, transportation, and customs clearance. They ensure that the cutter metal machines are safely delivered to the buyer’s location, taking care of all the necessary paperwork and complying with import regulations.
5. Payment and Financial Security: Agents and sourcing companies also help buyers navigate payment processes and ensure financial security. They provide guidance on payment terms, facilitate secure transactions, and help resolve any payment-related issues. By acting as trusted intermediaries, they reduce the risk of fraud or financial losses.
In summary, agents and sourcing companies streamline the process of purchasing cutter metal machines from China by identifying reliable suppliers, facilitating communication, ensuring quality control, managing logistics, and providing financial security. Their expertise and assistance make it easier and more efficient for buyers to source cutter metal machines from China, ultimately contributing to a successful and smooth purchasing experience.
Price Cost Research for cutter metal machine manufacturers Companies in China, use temu.com and 1688.com
When it comes to researching the price and cost of cutter metal machine manufacturers in China, two reliable online platforms that can be utilized are temu.com and 1688.com.
Temu.com is a comprehensive platform that offers access to various Chinese suppliers and manufacturers. It allows users to search for specific products, including cutter metal machines, and provides detailed product descriptions and price information. The platform also enables direct communication with suppliers, facilitating negotiations and inquiries about cost and pricing details. Additionally, users can analyze the reputation and customer reviews of different manufacturers on temu.com, ensuring the selection of high-quality suppliers at competitive prices.
1688.com, also known as Alibaba’s domestic platform, is another resourceful site for researching cutter metal machine manufacturers in China. It provides a wide range of products offered by numerous manufacturers. Similar to temu.com, this platform offers detailed product descriptions, pricing information, and the ability to contact suppliers directly for inquiries and negotiations. However, it is important to note that 1688.com is primarily in Chinese, so users may require translation tools or assistance to navigate the platform effectively.
Conducting price and cost research on both temu.com and 1688.com allows users to compare offerings from different manufacturers, assess quality certifications, and evaluate customer reviews and ratings. Moreover, these platforms often provide additional information about shipping terms, payment methods, and after-sales services, which can be crucial factors to consider when determining the overall cost of purchasing cutter metal machines from China.
In summary, temu.com and 1688.com are valuable online platforms for conducting research on cutter metal machine manufacturers in China. Their extensive product listings, detailed descriptions, pricing information, and direct communication capabilities enable users to make informed decisions about suppliers and negotiate competitive pricing.
Shipping Cost for cutter metal machine import from China
The shipping cost for importing a metal cutter machine from China varies based on several factors such as the weight and dimensions of the machine, the shipping method chosen, and the destination country. Typically, there are two main shipping methods: air freight and sea freight.
If you opt for air freight, the shipping cost will be higher but the delivery time will be faster. The cost is usually calculated based on the chargeable weight, which is the higher value between the actual weight and volumetric weight. The volumetric weight is determined by calculating the size of the package using its length, width, and height. Additionally, there may be extra charges for customs clearance, handling fees, and insurance. It is recommended to obtain quotes from multiple freight forwarders or shipping agents to get the best rates.
On the other hand, sea freight is a more cost-effective shipping option, especially for larger and heavier machines. The cost is usually determined by the volume or the container size required. There are different types of containers available, such as Full Container Load (FCL) or Less than Container Load (LCL), depending on the size and quantity of the machines. Sea freight generally takes longer than air freight, ranging from a few weeks to a couple of months, depending on the distance and customs procedures at the destination port.
Apart from the shipping cost, it is important to consider other costs associated with importing the cutter metal machine. These may include customs duties, import taxes, inland transportation costs, destination port fees, and handling charges. It is advisable to consult with a customs broker or freight forwarder who can help estimate these additional costs accurately based on the specific details of the machine.
In conclusion, the shipping cost for importing a metal cutter machine from China varies based on factors like weight, dimensions, shipping method, and destination. It is recommended to obtain quotes from multiple shipping agents or freight forwarders and consider all additional costs related to customs and inland transportation before finalizing the import.
Compare China and Other cutter metal machine Markets: Products Quality and Price,Visible and Hidden Costs
China is one of the major players in the global cutter metal machine market. When it comes to product quality, China has made significant strides in recent years. Many Chinese manufacturers have invested in advanced technology and have enhanced their production processes to improve the quality of their cutter metal machines. However, it is important to note that the quality of products in China can vary widely depending on the manufacturer and the level of investment in quality control measures. Other cutter metal machine markets, such as Germany and Japan, are known for their high-quality products, as they have a long-standing reputation for precision engineering and stringent quality standards.
Price is another important factor to consider when comparing China with other cutter metal machine markets. China is known for its competitive pricing, thanks to its low labor and production costs. As a result, Chinese cutter metal machines are generally more affordable compared to those from other countries. However, it is worth noting that price should not be the sole determining factor, as lower-priced machines may sometimes compromise on quality.
Visible costs, which include the initial purchase price and freight charges, are often transparent and can be easily calculated. In this regard, Chinese manufacturers are generally able to offer competitive prices due to lower labor and production costs. On the other hand, other cutter metal machine markets, such as Germany and Japan, may have higher visible costs due to higher labor and production expenses.
Hidden costs, on the other hand, can be more challenging to assess. These costs include factors such as maintenance, repairs, and downtime, which can impact the long-term cost-effectiveness of a cutter metal machine. While Chinese machines may have a lower initial price, they may also have higher hidden costs due to potential issues with quality, reliability, and after-sales service. In contrast, machines from other markets may have higher initial prices but lower hidden costs due to their superior quality and reliability.
In conclusion, China has emerged as a key player in the cutter metal machine market, offering competitive prices and improving product quality. However, comparing China with other cutter metal machine markets highlights the need to consider factors beyond just price, such as product quality and hidden costs. It is important for buyers to carefully evaluate their unique requirements and consider the trade-offs between price and quality when making a purchasing decision.
Understanding Pricing and Payment Terms for cutter metal machine: A Comparative Guide to Get the Best Deal
When it comes to purchasing a cutter metal machine, understanding the pricing and payment terms is crucial to ensure you get the best deal. By comparing various options, you can make an informed decision and maximize the value of your investment. Here is a comparative guide to help you get the best deal in no more than 300 words.
1. Research and Compare Pricing:
Start by researching different brands and suppliers of cutter metal machines. Look for models that meet your specific requirements and compare their prices across various sellers. Take note of any additional features or accessories included in the price, as this can impact the overall value.
2. Consider Quality and Reliability:
While it’s important to look for competitive pricing, don’t compromise on quality and reliability. A machine that requires frequent repairs or has a shorter lifespan can end up costing you more in the long run. Consider customer reviews and ratings to gauge the performance and durability of the machine before making a decision solely based on price.
3. Negotiate and Leverage Competition:
Once you have shortlisted potential suppliers, reach out to them and negotiate the pricing. Use the competitive landscape to your advantage by sharing quotes from other sellers. This can encourage the suppliers to offer a better deal or additional benefits, such as discounted maintenance services or extended warranties.
4. Payment Terms and Financing Options:
Examine the payment terms offered by each supplier. Some may provide flexible payment options, such as installments or leasing arrangements, which can help you manage cash flow. Compare the interest rates and fees associated with financing options to ensure they align with your budget and long-term financial goals.
5. Warranty and After-Sales Support:
A cutter metal machine is a significant investment, so it’s important to consider the warranty and after-sales support provided. Compare the length of the warranty offered by different sellers and the availability of technical support. A comprehensive warranty and reliable customer service can provide peace of mind and potentially save you money on repairs and maintenance.
6. Consider Total Cost of Ownership:
Don’t solely focus on the upfront price of the machine. Take into account the total cost of ownership, including operational costs, consumables, and maintenance expenses. A machine with higher efficiency or lower operating costs may be more cost-effective in the long term, even if the initial price is slightly higher.
In conclusion, finding the best deal on a cutter metal machine requires thorough research and comparison. By considering factors such as pricing, quality, payment terms, warranties, and total cost of ownership, you can make an informed decision and secure a machine that meets your needs without breaking your budget.
Chinese Regulations and Industry Standards Certifications for cutter metal machine,Import Regulations and Customs for cutter metal machine from China
Chinese Regulations and Industry Standards Certifications for cutter metal machines:
In China, the manufacturing and sale of cutter metal machines are regulated by several government agencies and industry bodies. The main regulatory body is the State Administration for Market Regulation (SAMR), which is responsible for setting and enforcing product standards and certifications.
The most important industry standard certification for cutter metal machines in China is the China Compulsory Certification (CCC) mark. This certification ensures that the product meets safety, quality, and environmental protection requirements. It is mandatory for a wide range of products, including cutter metal machines, before they can be sold in the Chinese market.
In addition to the CCC mark, there are other industry standards and certifications that are commonly required for cutter metal machines. These include the ISO 9001 certification for quality management systems, ISO 14001 for environmental management, and ISO 45001 for occupational health and safety management.
Import Regulations and Customs for cutter metal machines from China:
When importing cutter metal machines from China, it is important to comply with the import regulations and customs procedures of the importing country. These regulations may vary depending on the country, but some common requirements include:
1. Custom duties and taxes: Importers need to be aware of the custom duties and taxes applicable to cutter metal machines in their country. These fees vary and must be paid before the goods can be cleared by customs.
2. Documentation: Importers should ensure that they have all the necessary documentation, including invoices, packing lists, and bill of lading, to provide to customs authorities.
3. Product compliance: Importers should ensure that the cutter metal machines they are importing comply with the safety and quality standards of their country. This may require obtaining certifications or test reports from recognized testing laboratories.
4. Customs clearance: Importers need to file the necessary customs declarations and go through the customs clearance process. This may include providing additional information or documentation as requested by customs authorities.
5. Licensing and permits: Some countries may require importers to obtain specific licenses or permits for importing cutter metal machines. Importers should check with the relevant authorities to determine if any additional licenses or permits are required.
In conclusion, complying with Chinese regulations and industry standards certifications, as well as understanding the import regulations and customs procedures of the importing country, are crucial when importing cutter metal machines from China. It is advisable to consult with customs brokers or trade experts for thorough guidance throughout the import process.
Sustainability and Environmental Considerations in cutter metal machine Manufacturing
Sustainability and environmental considerations are important factors in the manufacturing of cutter metal machines. These machines are widely used in various industries, including automotive, aerospace, and construction. While they play a vital role in increasing productivity and efficiency, their manufacturing process can have significant environmental impacts.
One of the key environmental concerns in cutter metal machine manufacturing is energy consumption. These machines require large amounts of energy to operate, and the production process itself can also be energy-intensive. To address this, manufacturers can implement energy-efficient technologies, such as using high-efficiency motors and optimizing production processes to minimize energy waste.
Another major environmental consideration is the use of raw materials. Cutter metal machines are typically made from steel, which has a high carbon footprint due to the energy-intensive processes involved in its production. Manufacturers can explore alternatives, such as using recycled steel or lightweight materials that require less energy to produce.
Waste generation is also a significant issue in the manufacturing process. Metal shavings and other waste materials are produced during the cutting and shaping of metal parts. To minimize waste, manufacturers can implement recycling programs to reuse or sell scrap metal. They can also adopt lean manufacturing principles to reduce material waste and optimize production efficiency.
Water usage is another environmental concern in cutter metal machine manufacturing. Many manufacturing processes require the use of water for cooling and lubrication. Implementing water-saving technologies and recycling systems can help reduce water consumption and minimize the impact on local water resources.
To ensure sustainability in cutter metal machine manufacturing, manufacturers should also consider the environmental impact throughout the machine’s lifecycle. This includes designing machines for longer lifespans, making them easier to repair and upgrade, and ensuring proper disposal or recycling at the end of their useful life.
In conclusion, sustainability and environmental considerations are crucial in cutter metal machine manufacturing. By implementing energy-efficient technologies, reducing waste generation, conserving water, and considering the entire lifecycle of the machine, manufacturers can minimize their environmental impact and contribute to a more sustainable future.
List The Evolution history of “cutter metal machine”
The evolution of metal cutting machines, also known as cutter metal machines, spans several centuries, starting with simple hand-operated tools to the sophisticated computer-controlled machines we see today.
1. Early Hand Tools: The earliest form of metal cutting was done manually with hand tools like chisels and saws. This method required significant physical effort and was limited in terms of precision and speed.
2. Industrial Revolution: The Industrial Revolution brought significant advancements in metal cutting technology. In the late 18th and early 19th centuries, machines such as the lathe and shaper were introduced. These powered devices allowed for more precise and faster metal cutting, enhancing manufacturing processes.
3. Introduction of Power Tools: With the spread of electricity in the late 19th century, power tools became popular. Machines like the drill press, bandsaw, and milling machine revolutionized metal cutting, enabling greater precision and automation.
4. Numerical Control (NC): In the mid-20th century, NC technology emerged. NC machines were capable of performing metal cutting operations based on pre-programmed instructions, eliminating the need for manual control. These machines used punched cards or magnetic tapes to store instructions.
5. Computer Numerical Control (CNC): CNC machines, an advancement of NC technology, were developed in the 1970s. These machines utilized computers to control the metal cutting process. CNC systems allowed for more complex operations, higher precision, and faster production.
6. Automation and Robotics: In recent decades, automation and robotics have further transformed metal cutting machines. Computer-controlled systems, combined with artificial intelligence, have enabled machines to operate autonomously and handle complex tasks. Industrial robots now perform metal cutting operations with exceptional speed and precision.
7. Laser and Plasma Cutting: Laser and plasma cutting technologies have emerged as powerful alternatives to traditional metal cutting methods. These utilize highly concentrated energy beams to melt or vaporize metal, allowing for more precise and efficient cutting.
8. 3D Printing and Additive Manufacturing: The latest trend in metal cutting machines is the incorporation of 3D printing and additive manufacturing technologies. These machines build three-dimensional objects layer by layer, including metal components. This approach offers new possibilities for complex and customized metal cutting and manufacturing.
In conclusion, cutter metal machines have evolved significantly over time, from primitive hand tools to advanced CNC, robotics, laser cutting, and additive manufacturing technologies. These developments have driven greater precision, speed, and automation in the metal cutting industry.
The Evolution and Market Trends in cutter metal machine Industry
Over the past few decades, the cutter metal machine industry has witnessed remarkable evolution and significant market trends. These advancements have revolutionized the manufacturing processes across various sectors.
One of the key developments in this industry is the integration of computer numerical control (CNC) technology. CNC cutting machines have replaced conventional manual machines due to their accuracy and efficiency. These machines are capable of executing precise cutting operations with minimal human intervention, thereby reducing production time and improving product quality.
Another notable evolution is the introduction of advanced cutting techniques. Laser cutting machines, for example, utilize highly focused laser beams to melt, vaporize, or burn through different metals with high precision. Plasma cutting machines use ionized gases to cut through metals, providing speed and versatility. Waterjet cutting machines employ a high-pressure stream of water mixed with abrasive materials to cut through metals. These advancements in cutting techniques have significantly expanded the range of cutting capabilities and improved overall productivity.
Furthermore, market trends in the cutter metal machine industry reflect the growing demand for automation and operational efficiency. Manufacturers are increasingly adopting robotic cutting systems to streamline production and optimize resource allocation. Robotic cutters offer increased precision and speed while reducing labor costs and human error. Additionally, the rise in digitalization and Industry 4.0 has led to the integration of various sensors and data analytics tools, enabling real-time monitoring and predictive maintenance of cutter machines.
In terms of market growth, the cutter metal machine industry is witnessing a surge in demand from various sectors. The automotive industry extensively utilizes cutter machines for producing components and chassis. The aerospace industry relies on these machines for intricate cutting operations on aircraft parts. The construction industry relies on cutter machines for precise cutting of metal structures. Moreover, the growing adoption of renewable energy sources, such as wind turbines and solar panels, has led to increased demand for cutter machines in the renewable energy sector.
In conclusion, the cutter metal machine industry has undergone significant evolution driven by advancements in technology and market demands. The integration of CNC technology, advanced cutting techniques, and automation has transformed the industry, leading to improved efficiency, accuracy, and productivity. Additionally, the market trends demonstrate the increasing demand for cutter machines in various sectors such as automotive, aerospace, construction, and renewable energy.
Custom Private Labeling and Branding Opportunities with Chinese cutter metal machine Manufacturers
Chinese cutter metal machine manufacturers offer excellent custom private labeling and branding opportunities for businesses looking to market their own products. These manufacturers have extensive experience in producing high-quality cutter metal machines and can help businesses create a unique and branded product line.
With custom private labeling, businesses can create their own brand name and logo to be printed on the machines. This adds a professional and personalized touch to the products, making them stand out in the market. Chinese manufacturers are adept at working with businesses to design and customize packaging, labels, and even manuals, ensuring a cohesive and consistent branding strategy.
Moreover, Chinese cutter metal machine manufacturers can also offer custom branding opportunities. This allows businesses to create an entirely new product line with specific features, design elements, and functionalities. Whether it is a unique cutting mechanism or specialized software, these manufacturers can work closely with businesses to bring their branding ideas to life.
By partnering with Chinese manufacturers for custom private labeling and branding, businesses can benefit from their expertise, cost-effectiveness, and production capabilities. These manufacturers typically have state-of-the-art facilities, modern machinery, and skilled labor that can deliver high-quality customized products at competitive prices.
In conclusion, Chinese cutter metal machine manufacturers provide excellent opportunities for businesses to customize and brand their products. Through custom private labeling and branding, businesses can create their own unique product lines, adding value to their brand and ultimately enhancing their market position. With their expertise and cost-effective manufacturing capabilities, Chinese manufacturers are a reliable choice for businesses seeking to establish a strong presence in the cutter metal machine market.
Tips for Procurement and Considerations when Purchasing cutter metal machine
When purchasing a cutter metal machine for procurement, there are several considerations to keep in mind to make an informed decision. Here are some tips and factors to consider.
1. Machine Specifications: Look for a cutter metal machine that meets your specific requirements in terms of cutting capacity, bed size, cutting speed, cutting accuracy, and power consumption. Ensure that it can handle the type and thickness of metal you work with.
2. Quality and Durability: Invest in a machine built with high-quality materials and components to ensure durability and long-term performance. Check for industry certifications and customer reviews to gauge the machine’s quality.
3. Supplier Reputation: Choose a reputable supplier with a track record of delivering quality products and excellent customer service. Verify their experience and expertise in manufacturing cutter metal machines.
4. Pricing and Value for Money: Compare prices from different suppliers while considering the machine’s features, quality, and after-sales support. Look for the best value for your money rather than the cheapest option.
5. Maintenance and Training: Consider the availability of spare parts and service support from the supplier. Ensure they offer training and technical assistance to operators for efficient and safe machine operation.
6. Safety Features: Safety should be a top priority. Ensure the machine is equipped with safety features like emergency stop buttons, safety interlocks, and protective guarding to prevent accidents.
7. Energy Efficiency: Opt for a cutter metal machine that is energy-efficient to minimize operating costs and reduce environmental impact.
8. Warranty and After-sales Support: Check the warranty period offered by the supplier and understand the terms and conditions. Additionally, inquire about the availability of after-sales support, technical assistance, and spare parts.
9. Compatibility and Integration: If you have existing equipment or software for design or manufacturing processes, ensure compatibility and integration with the cutter metal machine to streamline operations.
10. Future Expansion and Upgrades: Consider the machine’s capability to accommodate future expansions or upgrades to meet changing business needs.
Remember to conduct a thorough evaluation of your requirements, comparing various options, and consulting with industry experts before making a final decision.
FAQs on Sourcing and Manufacturing cutter metal machine in China
Q: Why should I consider sourcing and manufacturing cutter metal machines in China?
A: China has emerged as a leading global manufacturing hub due to its competitive pricing, skilled labor force, and extensive manufacturing capabilities. Sourcing cutter metal machines in China can result in cost savings, as labor and production costs are generally lower compared to other countries. Additionally, China offers a wide range of factories and suppliers specializing in cutter metal machines, ensuring a variety of options to meet specific requirements.
Q: How can I find a reliable manufacturer for cutter metal machines in China?
A: Finding a reliable manufacturer in China can be achieved through various methods. Firstly, conducting thorough research and due diligence is essential. Online platforms like Alibaba and Made-in-China can provide a comprehensive list of manufacturers. It is advisable to review their product catalogs, company information, and client feedback to assess their reliability. Additionally, attending trade shows and exhibitions related to metalworking technologies in China can enable direct interaction with potential suppliers and assist in building trust.
Q: How can I ensure the quality of cutter metal machines sourced from China?
A: Quality control is crucial when sourcing cutter metal machines from China. One effective way is to request samples from prospective suppliers before making a final decision. By inspecting the sample for build quality, precision, and overall performance, you can assess if their products meet your requirements. It is also recommended to conduct factory visits or engage third-party inspection agencies to verify the manufacturer’s capabilities and adherence to quality standards.
Q: What are the potential challenges when sourcing cutter metal machines from China?
A: Language and cultural differences can pose initial communication challenges when dealing with Chinese manufacturers. Time zone differences may also affect real-time communication. Moreover, intellectual property protection can be a concern. To mitigate these challenges, engaging with sourcing agents or manufacturing specialists who are familiar with the Chinese market can streamline communication and provide guidance on legal protection.
Q: Are there any specific regulations or certifications to consider when importing cutter metal machines from China?
A: Yes, it is important to ensure that the cutter metal machines meet your local regulations and safety standards. Depending on your country, certifications such as CE, ISO, or UL may be required. Working closely with manufacturers to understand their compliance procedures and obtaining relevant certifications can ensure the machines’ legality and safety.
In conclusion, sourcing and manufacturing cutter metal machines in China can offer cost advantages, a wide range of suppliers, and competitive production capabilities. However, thorough research, quality control measures, and consideration of challenges like cultural and language differences, intellectual property protection, and compliance with regulations are crucial for a successful sourcing process.
Why contact sourcifychina.com get free quota from reliable cutter metal machine suppliers?
Sourcifychina.com, as a platform connecting buyers with Chinese suppliers, offers a variety of services to ensure a smooth sourcing process. One of the benefits they provide to buyers is free quota from reliable cutter metal machine suppliers. This initiative aims to facilitate the sourcing of cutter metal machines for businesses looking to expand their operations or upgrade their machinery.
Obtaining free quota from reliable cutter metal machine suppliers offers several advantages. Firstly, it allows buyers to compare and evaluate different suppliers without incurring any costs. This helps in finding the most suitable supplier that meets their specific requirements and budget. By offering this service, Sourcifychina.com eliminates the initial financial investment that buyers would typically have to make to obtain quotations.
Secondly, by connecting buyers with reliable cutter metal machine suppliers, Sourcifychina.com ensures that the suppliers have a proven track record of delivering quality products and maintaining good business practices. This saves buyers from the hassle of researching and verifying the credibility of various suppliers. The platform’s pre-vetting process ensures that only reliable and trustworthy suppliers are listed, giving buyers peace of mind.
Furthermore, the free quota service encourages competition among cutter metal machine suppliers, leading to improved pricing and terms for the buyers. Suppliers may offer more competitive pricing and value-added services in order to secure the buyer’s business. This benefits the buyer by providing better options and potentially reducing overall costs.
In conclusion, Sourcifychina.com offers free quota from reliable cutter metal machine suppliers to simplify the sourcing process for buyers. This service enables buyers to evaluate different suppliers, eliminates the financial burden of obtaining quotations, ensures the credibility of suppliers, and promotes competitiveness among suppliers. By leveraging this service, businesses can efficiently source high-quality cutter metal machines while minimizing costs and risks.