Introduce about cutting metal machine guide,Qulity,Cost,Supplier,Certification,Market,Tips,FAQ
A cutting metal machine guide provides a comprehensive overview of machines used for cutting various types of metal with precision and efficiency. These machines are widely utilized in industries such as automotive, aerospace, construction, and manufacturing.
Quality is a crucial factor when considering a cutting metal machine. A high-quality machine ensures accurate and clean cuts, minimizing material waste and enhancing productivity. It is essential to choose a machine that offers durability, advanced features, and reliable performance.
Cost is another important consideration. The price of cutting metal machines can vary depending on various factors such as the machine type, specifications, and capabilities. It is advisable to compare prices from different suppliers to find the best value for your investment.
Selecting a reputable supplier is crucial for acquiring a reliable cutting metal machine. Consider suppliers that have a proven track record in delivering high-quality machines and have positive customer reviews. It is also essential to check if the supplier offers after-sales support, warranties, and spare part availability.
Certification is an important aspect to consider when purchasing a cutting metal machine. Ensure that the machine is certified by recognized standards and regulatory bodies. Certification ensures compliance with safety and quality standards, granting peace of mind and eliminating potential legal and safety issues.
The market for cutting metal machines is vast and diverse. From small workshops to large-scale industrial operations, machines are in demand worldwide. Understanding the market trends, technological advancements, and customer preferences can help in making informed decisions for choosing the right machine.
Tips for choosing a cutting metal machine include evaluating the machine’s power, cutting speed, cutting capacity, and compatibility with various metal types. It is crucial to assess the machine’s features based on specific project requirements and industry needs.
Frequently asked questions (FAQ) regarding cutting metal machines commonly address issues related to machine maintenance, operator training, safety precautions, and troubleshooting common problems. Suppliers should provide comprehensive FAQ sections to assist customers in resolving queries efficiently.
In conclusion, when considering a cutting metal machine, prioritize quality, assess the cost, choose a reputable supplier, look for relevant certifications, and understand the market. By following these guidelines and considering essential factors, one can make an informed decision while purchasing a cutting metal machine.
Types of cutting metal machine
There are several types of cutting metal machines available for various industrial applications. These machines utilize different techniques and mechanisms to cut metal efficiently and accurately. Here are some commonly used types:
1. Bandsaw: Bandsaws use a continuous metal blade with teeth to cut through metal. The blade moves in a continuous loop around two wheels, allowing for straight or curved cuts. This machine is ideal for cutting metal sheets or bars.
2. Plasma cutter: Plasma cutters use a high-velocity jet of ionized gas, known as plasma, to melt and cut through a metal workpiece. These machines are capable of cutting through various thicknesses of metal quickly and precisely.
3. Laser cutter: Laser cutting machines employ a high-powered laser beam to melt, burn, or vaporize metal. The laser beam is directed by computer-controlled mirrors, enabling precise cutting with minimal heat affected zones. Laser cutting is often used for intricate or detailed metal designs.
4. Waterjet cutter: Waterjet cutting machines use a high-pressure stream of water mixed with an abrasive substance to cut through metal. This machine is ideal for cutting materials that may be sensitive to high temperatures or for precise cutting of thick metal plates.
5. Shearing machine: Shearing machines use a scissor-like action to shear metal into desired shapes. The workpiece is placed between two blades, which move in a vertical or horizontal manner to cut through the metal. Shearing machines are commonly used for straight cuts on sheet metal.
6. Sawing machine: Sawing machines employ a circular or reciprocating blade to cut through metal. These machines are versatile and can handle various types of metals, shapes, and sizes. They are commonly used for cutting larger metal workpieces.
7. Milling machine: Milling machines use rotary cutters to remove material from a metal workpiece. These machines are highly versatile and can produce complex shapes and contours. Milling machines are often used for precision cutting and shaping of metal components.
Each type of cutting metal machine has its advantages and is suitable for specific applications. Choosing the right machine depends on factors such as the type and thickness of the metal, desired cutting accuracy, and production requirements.
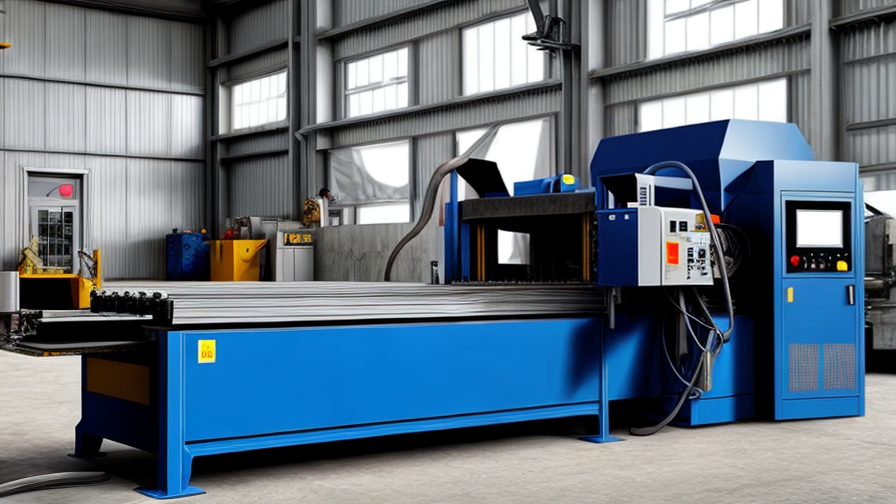
Pros and Cons of Using cutting metal machine
Using a cutting metal machine can offer numerous benefits for various industries, but it also comes with some drawbacks. Below are the pros and cons of using cutting metal machines:
Pros:
1. Precision: Cutting metal machines provide precise cuts, ensuring accuracy and consistency in the final product. This is especially crucial in industries like aerospace and automotive, where precision is paramount.
2. Efficiency: These machines allow for faster and more efficient cutting processes. They can handle large volumes of metal with speed, increasing productivity and reducing turnaround time.
3. Versatility: Cutting metal machines can be used for a wide range of materials, including steel, aluminum, and titanium. This versatility makes them valuable for diverse industries, including construction, manufacturing, and metal fabrication.
4. Automation: Many cutting metal machines offer automated features, such as computer numerical control (CNC) technology. With CNC, operators can program the machine to execute complex cuts consistently and with minimal manual intervention.
5. Cost savings: By improving efficiency and precision, cutting metal machines can help businesses reduce costs. They minimize material waste and lower labor expenses, resulting in overall cost savings.
Cons:
1. Initial investment: Cutting metal machines can be expensive to purchase and install. The high initial investment can be a barrier for smaller businesses or startups.
2. Maintenance requirements: These machines may require regular maintenance and upkeep, which can add to the overall operational costs. Any breakdowns or malfunctions can also lead to downtime and disruptions in production.
3. Noise and safety concerns: Cutting metal machines can generate high levels of noise during operation. Adequate hearing protection is necessary for operators. Additionally, handling metalwork on these machines can pose safety risks, requiring strict adherence to safety protocols.
4. Limited flexibility: While cutting metal machines offer versatility in terms of materials, they may have limitations in terms of the size or shape of the metal pieces they can handle. This can restrict the range of applications for certain industries.
5. Skilled operators required: Operating cutting metal machines typically requires specialized skills. Skilled operators are needed to set up, program, and monitor the machine to ensure optimal performance and prevent errors.
In conclusion, cutting metal machines offer numerous advantages such as precision, efficiency, versatility, automation, and cost savings. However, they also come with drawbacks including the high initial cost, maintenance requirements, noise and safety concerns, limited flexibility, and the need for skilled operators. Businesses considering the use of cutting metal machines need to carefully evaluate these pros and cons to determine if the benefits outweigh the drawbacks based on their specific requirements and resources.
cutting metal machine Reference Specifications (varies for different product)
Cutting metal machines are essential tools in various industries such as automotive, aerospace, construction, and manufacturing. These machines offer precise and efficient cutting of different types of metal, including steel, aluminum, and copper. The specifications of cutting metal machines can vary based on the specific product requirements. Here are some common reference specifications for these machines.
1. Power: Cutting metal machines are typically powered by electricity or hydraulics. The power output can range from 1 kW to 100 kW, depending on the machine’s size and intended application. Higher power output allows for faster and more efficient cutting.
2. Cutting Capacity: The cutting capacity of a machine refers to the maximum thickness of metal it can cut. This can vary from a few millimeters to several centimeters, depending on the machine’s design and capabilities. Machines with higher cutting capacities are suitable for heavy-duty industrial applications.
3. Cutting Speed: Cutting metal machines have adjustable cutting speeds that can range from a few meters per minute to several dozen meters per minute. The choice of cutting speed depends on the type and thickness of the metal being cut, as well as the desired precision and surface finish.
4. Cutting Method: There are various cutting methods employed by metal cutting machines, including laser cutting, plasma cutting, water jet cutting, and abrasive cutting. Each method has its advantages and is suitable for specific metal types and thicknesses.
5. Precision and Accuracy: Precision and accuracy are critical factors in metal cutting applications. Cutting metal machines with high precision and accuracy ensure clean cuts with minimal distortion and burrs. These machines often incorporate advanced control systems and optics for improved cutting performance.
6. Safety Features: Safety is paramount in any manufacturing process. Cutting metal machines should include safety features such as emergency stop buttons, safety interlocks, and protective shields to prevent accidents and injuries.
7. Maintenance and Serviceability: Metal cutting machines should be designed for easy maintenance and serviceability. This includes accessible components for routine inspections and repairs, as well as clear documentation of maintenance procedures.
It is important to note that these specifications are not exhaustive and can vary depending on the specific product or model of cutting metal machine. Buyers should consult the manufacturer’s documentation and seek expert advice to ensure the machine meets their particular requirements.
Applications of cutting metal machine
Cutting metal machines, also known as metal cutting machines or metalworking machinery, are essential tools in various industries. They are designed to accurately shape and cut different types of metal, such as steel, aluminum, and copper. These machines have a wide range of applications and play a vital role in enhancing productivity, precision, and efficiency in metalworking processes. Below are some of the key applications of cutting metal machines:
1. Manufacturing and fabrication: Metal cutting machines are extensively used in manufacturing and fabrication industries to create precise and complex metal parts. They enable manufacturers to cut, shape, and form metal sheets, bars, pipes, and other components according to specific design requirements. This is crucial in industries such as automotive, aerospace, and construction.
2. Metalworking workshops: Cutting metal machines are commonly found in metalworking workshops. These machines enable workers to accurately cut metal sheets and plates for various purposes like repairing machinery, constructing frameworks, or creating structures. They can be used to cut holes, slots, or intricate shapes in metals, allowing for greater flexibility and customization.
3. Construction industry: In the construction sector, metal cutting machines are used to cut and shape metal pipes, beams, and profiles for structural purposes. They are crucial for fabricating components used in building frameworks, bridges, and other large-scale structures. Metal cutting machines help ensure precise measurements and shapes, contributing to the overall strength and integrity of the structures.
4. Shipbuilding and offshore industries: Cutting metal machines are extensively used in shipbuilding and offshore industries to shape and cut metal plates and sections required for shipbuilding and oil rig construction. These machines help in producing accurately measured and shaped components needed for hulls, decks, and other structural elements.
5. Decorative and artistic purposes: Cutting metal machines play a significant role in the artistic and decorative metalworking industry. Artists and designers utilize these machines to create intricate patterns, designs, and shapes in metal, adding aesthetic value to various applications such as sculptures, furniture, gates, and decorative panels.
In summary, cutting metal machines have extensive applications in various industries, including manufacturing, fabrication, construction, shipbuilding, and artistic metalworking. They contribute to improved productivity, accuracy, and customization in metalworking processes, leading to enhanced performance and quality in the end products or structures.
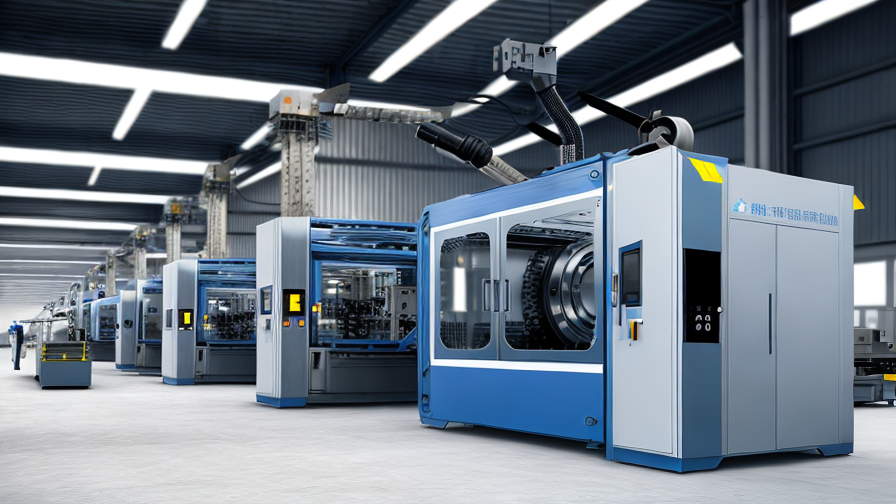
The Work Process and how to use cutting metal machine
The work process of a cutting metal machine involves several steps to ensure safe and accurate cutting of metal materials. Here is a brief overview of the process:
1. Select and prepare the metal material: The machine operator needs to choose the appropriate metal material based on the project requirements. It is essential to inspect the material for any defects or irregularities that could affect the cutting process. The metal should be securely held in place to prevent movement during cutting.
2. Set up the machine: Prior to operating the cutting metal machine, it is important to properly set it up. This includes adjusting the cutting speed, depth, and angle according to the type and thickness of the metal being cut. The operator should also ensure that all safety features are in place and functioning correctly.
3. Load the cutting tool: The cutting metal machine uses various cutting tools such as abrasive wheels, plasma torches, or laser beams depending on the machine type. The operator needs to load the appropriate tool onto the machine, ensuring it is securely attached and properly aligned.
4. Start the cutting process: Once the machine is set up, the operator can start the cutting process. This involves activating the machine and guiding it along the predetermined cutting path. It is important to maintain a steady and consistent speed to achieve precise cuts.
5. Monitor the cutting process: Throughout the cutting process, the operator should closely monitor the machine to ensure everything is running smoothly. This includes checking for any signs of overheating, unusual vibrations, or unexpected noises. Additionally, the operator should constantly inspect the cut quality to ensure it meets the required standards.
6. Complete the cutting process: Upon completing the cutting process, the operator needs to carefully remove the metal material from the machine and inspect the final product. Any rough edges or burrs should be smoothed out using appropriate tools or techniques if necessary.
Using a cutting metal machine effectively requires proper training and adherence to safety protocols. It is crucial to wear appropriate protective equipment such as safety goggles and gloves, as well as follow the manufacturer’s guidelines and recommendations for the specific machine being used. Additionally, regular maintenance and inspections of the machine are essential to ensure optimal performance and longevity.
In conclusion, the work process of using a cutting metal machine involves selecting and preparing the metal material, setting up the machine, loading the cutting tool, starting the cutting process, monitoring it closely, and completing the process. Following safety protocols and manufacturer’s guidelines is essential for safe and efficient operation.
Quality Testing Methods for cutting metal machine and how to control the quality
Quality testing methods for cutting metal machines typically involve a combination of visual inspection, dimensional analysis, and performance testing. Here, we outline some common quality testing methods for cutting metal machines, and provide tips on how to control the quality of these machines effectively.
1. Visual Inspection: This involves examining the cutting machine for any visible defects, such as surface finishes, welding imperfections, or misalignments. Visual inspection ensures that the machine is built to the required specifications and meets the desired quality standards.
2. Dimensional Analysis: This step involves measuring critical dimensions of the cutting machine using precision tools and comparing them with the specified tolerances. This ensures that the machine’s components are accurately fabricated, machined, and assembled.
3. Performance Testing: The cutting machine needs to go through rigorous performance testing to ensure its functionality and durability. This includes testing its cutting speed, accuracy, reliability, and energy consumption. The machine should be able to meet or exceed the expected performance benchmarks.
4. Material Analysis: The quality control process may also involve analyzing the material used in the construction of the machine. This can include testing the hardness, composition, and structural integrity of the materials to ensure they meet the required standards.
Tips for Quality Control:
1. Establish Clear Specifications: Clearly define the required quality standards for the cutting machine, including dimensional tolerances, performance benchmarks, and material requirements.
2. Document Standard Operating Procedures (SOPs): Develop SOPs to ensure consistency in the manufacturing process and guide workers on how to assemble, test, and inspect the cutting machine. SOPs should provide clear instructions on quality control measures at each stage of production.
3. Regular Calibration of Tools and Equipment: Calibrate measuring tools and testing equipment regularly to ensure accurate readings. This helps to maintain the precision and reliability of the quality testing process.
4. Implement Process Controls: Monitor and control critical process parameters during the manufacturing process to minimize variations in the final product. This can include controlling temperature, speed, pressure, or other parameters relevant to the cutting machine’s performance.
5. Conduct Regular Audits: Periodically review the quality control procedures and audit the production process to identify any potential deviations. Address these deviations promptly to prevent quality issues from recurring.
By implementing these quality testing methods and controlling the quality of cutting metal machines effectively, manufacturers can ensure that their machines meet the desired quality standards, perform reliably, and satisfy customer expectations.
cutting metal machine Sample Policy and Post-Purchase Considerations for cutting metal machine from China
Sample Policy for Cutting Metal Machine from China:
1. Warranty: The cutting metal machine will come with a standard warranty period of one year from the date of purchase. During this time, any manufacturing defects or faults in the machine will be repaired or replaced free of charge.
2. Returns and Exchanges: In case of any issues with the machine, customers can request returns or exchanges within 30 days of purchase. The machine should be in its original condition and packaging for a hassle-free return or exchange process.
3. Technical Support: Our team will provide comprehensive technical support for the cutting metal machine to ensure its proper functioning. Customers can reach out to our service center for assistance with troubleshooting, maintenance, or any other technical queries.
4. Spare Parts Availability: We guarantee the availability of spare parts for the cutting metal machine for a minimum period of 5 years from the date of purchase. This ensures that customers can easily obtain replacements for any damaged or worn-out components.
Post-Purchase Considerations for Cutting Metal Machine from China:
1. Installation and Training: We recommend hiring a professional technician for the installation and initial setup of the cutting metal machine. Additionally, our company can provide on-site training to ensure users are aware of the machine’s operations and safety protocols.
2. Regular Maintenance: It is essential to perform regular maintenance checks on the cutting metal machine to ensure its optimum performance. Customers should follow the provided maintenance schedule and guidelines to prolong its lifespan.
3. Safety Measures: Users must strictly adhere to all safety instructions and precautions mentioned in the machine’s manual. This includes wearing protective gear, using the machine in a well-ventilated area, and keeping it away from water or flammable substances.
4. Upgrades and Accessories: Over time, customers may require additional accessories or upgrades for the cutting metal machine to enhance its capabilities. Our company can provide information and support for such requirements, ensuring seamless integration with the existing machine.
To ensure a smooth purchase experience, customers must carefully review the provided sample policy and consider the post-purchase considerations for the cutting metal machine. This will help maximize the machine’s performance, longevity, and overall value for money.
Sourcing cutting metal machine from China: Opportunities, Risks, and Key Players
China is a major player in the manufacturing industry and is known for producing a wide range of products, including cutting metal machines. Sourcing cutting metal machines from China presents several opportunities, risks, and key players that buyers should consider.
Opportunities:
1. Cost advantages: China offers competitive pricing due to lower labor and production costs. This can result in significant cost savings for buyers.
2. Product variety: China has a vast market for cutting metal machines, offering a wide range of options to choose from. Buyers can find machines that suit their specific needs and requirements.
3. Established manufacturing infrastructure: China has a robust manufacturing infrastructure, with well-developed supply chains and logistics systems. This ensures efficient production and timely delivery of orders.
Risks:
1. Quality concerns: While there are many reputable manufacturers in China, there is also a risk of encountering low-quality or counterfeit products. Buyers must thoroughly research and assess suppliers to ensure they meet their quality standards.
2. Intellectual property issues: China has a reputation for intellectual property infringements. Therefore, buyers need to take precautions to protect their designs and patents, such as signing non-disclosure agreements and working with trusted suppliers.
3. Communication and language barriers: Language differences and communication challenges can pose difficulties in negotiating and clarifying product specifications. It is crucial to have clear and effective communication with Chinese suppliers.
Key Players:
1. Huawei Industrial Machinery Co., Ltd: This company specializes in manufacturing cutting metal machines, including laser cutting machines, plasma cutting machines, and waterjet cutting machines.
2. Jinan Bodor CNC Machine Co., Ltd: Bodor is renowned for its laser cutting machines and has a global presence, serving customers in various industries.
3. Hailong Machinery: Hailong Machinery offers a range of metal cutting machines, such as CNC shearing machines, CNC bending machines, and hydraulic press brakes.
In conclusion, sourcing cutting metal machines from China can provide cost advantages, product variety, and access to an established manufacturing infrastructure. However, buyers need to be cautious about quality concerns, intellectual property issues, and potential communication barriers. Key players in the Chinese market include Huawei Industrial Machinery, Jinan Bodor CNC Machine, and Hailong Machinery.
How to find and select reliable cutting metal machine manufacturers in China,use google search manufacturers and suppliers
To find and select reliable cutting metal machine manufacturers in China, you can follow the below steps:
1. Start by conducting a Google search: Use keywords such as “cutting metal machine manufacturers” or “metal cutting machine suppliers in China” to begin your search. This will provide you with a list of potential manufacturers and suppliers.
2. Verify the credibility of the manufacturer: Look for information such as their website, company background, and product range. Check if they have any certifications or quality standards in place, as this indicates their commitment to producing reliable machines.
3. Assess their experience and reputation: Look for how long the manufacturer has been in business. Longer-established companies often have more experience and expertise. Additionally, read customer reviews and testimonials to gain insights into the manufacturer’s reputation for producing reliable machines.
4. Evaluate their product range and specialization: Different manufacturers may specialize in various types of cutting metal machines. Choose a manufacturer that offers a wide range of machines suitable for your specific needs and applications. Ensure they have expertise in producing the type of machine you require.
5. Quality control and testing: Inquire about the manufacturer’s quality control processes and testing procedures. Reliable manufacturers perform thorough quality checks on their products to ensure they meet industry standards and specifications.
6. Factory visits and production capacity: If possible, plan a visit to the manufacturer’s factory. This will allow you to evaluate their manufacturing capabilities, production processes, and overall professionalism. Assess their production capacity to ensure they can meet your manufacturing requirements.
7. Request for product samples and specifications: Ask the manufacturer to provide product samples and detailed specifications of their cutting metal machines. Evaluate the quality of the samples and compare specifications with your requirements.
8. Consider after-sales support and warranty: Inquire about the manufacturer’s after-sales support services, including technical assistance, spare parts availability, and warranty terms. A reliable manufacturer will provide prompt and efficient support, ensuring the longevity and reliability of the machine.
9. Obtain multiple quotes and compare: Request quotations from at least three different manufacturers. Compare their prices, product quality, after-sales support, and other factors before making a final decision.
10. Seek recommendations and referrals: Consult industry experts, trade associations, or business partners who have prior experience in working with cutting metal machine manufacturers in China. Their recommendations and referrals can be valuable in finding reliable manufacturers.
By conducting thorough research, evaluating multiple manufacturers, and considering various factors, you can find and select a reliable cutting metal machine manufacturer in China.
How to check cutting metal machine manufacturers website reliable,use google chrome SEOquake check if ranking in top 10M
To check whether a cutting metal machine manufacturer’s website is reliable, you can follow these steps using Google Chrome and the SEOquake tool. It is important to keep the word count below 300 words in answering your question:
1. Install SEOquake: If you don’t already have it, install the SEOquake extension on your Google Chrome browser. SEOquake is a popular tool that provides various SEO metrics.
2. Open the Website: Visit the cutting metal machine manufacturer’s website that you want to evaluate.
3. SEOquake Analysis: Click on the SEOquake toolbar extension icon in your browser, and a drop-down menu will appear.
4. Analyze the Organic Traffic: In the drop-down menu, go to the “SEMRush” tab and scroll down to the “Organic Search” section. Here, SEOquake provides the estimated monthly organic traffic (visits from search engines) for the website. A reliable manufacturer’s website often has a significant amount of organic traffic.
5. Check the Alexa Rank: Still in the SEMRush tab, look for the “Alexa Rank” section. Lower Alexa ranks indicate higher website popularity and traffic, hence, increasing the reliability of the website.
6. Evaluate the Backlinks: In the same SEMRush section, you can also find the number of backlinks pointing to the website. Higher numbers of quality backlinks indicate a reputable website.
7. Check Google Index: Go to the “Diagnosis” tab in the SEOquake toolbar drop-down menu and click on the “Index status” sub-tab. This will show if Google has indexed the website’s pages. A properly indexed website indicates reliability.
8. Further Research: If the website passes the initial reliability check, you can explore the website’s content, testimonials, client reviews, and certifications. Look for clear and detailed information about the company, their products, and contact details. This information can further verify the reliability of the manufacturer.
Remember to take all these indicators into consideration to assess the reliability of the cutting metal machine manufacturer’s website.
Top 10 cutting metal machine manufacturers in China
1. Nantong Super Machinery Co., Ltd.: Nantong Super Machinery is a leading metal cutting machine manufacturer in China. They specialize in producing and supplying various types of cutting machines, including laser cutting machines, plasma cutting machines, and waterjet cutting machines.
2. Jiangsu Tiangong Tools Co., Ltd.: Jiangsu Tiangong Tools is a renowned manufacturer of cutting tools and machinery in China. They offer a wide range of cutting machines, such as CNC cutting machines, band saw cutting machines, and shearing machines.
3. Jinan Bodor CNC Machine Co., Ltd.: Jinan Bodor is a leading manufacturer of laser cutting machines in China. They provide high-quality fiber laser cutting machines for various metal materials, including stainless steel, carbon steel, and aluminum.
4. Maanshan Baide CNC Machinery Co., Ltd.: Maanshan Baide CNC Machinery is a professional manufacturer of CNC plasma and flame cutting machines in China. They offer a comprehensive range of cutting machines suitable for different applications and industries.
5. Jiangsu Hongqiang CNC Machine Tool Co., Ltd.: Jiangsu Hongqiang CNC Machine Tool specializes in the production of CNC plasma cutting machines. Their machines are known for their precision, reliability, and efficiency in cutting metal materials.
6. Hako CNC Machine (Anhui) Manufactory Co., Ltd.: Hako CNC Machine is a leading manufacturer of CNC metal cutting machines in China. They specialize in producing CNC plasma cutting machines, CNC flame cutting machines, and CNC laser cutting machines.
7. Shandong Chencan Machinery Incorporated Company: Shandong Chencan Machinery is a prominent manufacturer of CNC router machines in China. With their advanced technology, they provide cutting-edge CNC routers for various industries, including metal fabrication.
8. Yawei Machinery Co., Ltd.: Yawei Machinery is a renowned manufacturer of hydraulic shearing machines and press brakes in China. They offer a wide range of cutting machines suitable for metal fabrication and sheet metal processing.
9. Anhui Yawei Machine Tool Manufacturing Co., Ltd.: Anhui Yawei Machine Tool specializes in the production of hydraulic shearing machines, press brakes, and turret punching machines. Their cutting machines are known for their high precision and stability.
10. Jinan Finework CNC Machinery Co., Ltd.: Jinan Finework CNC Machinery is a leading manufacturer of metal laser cutting machines in China. They offer a wide range of laser cutting machines, including fiber laser cutting machines and CO2 laser cutting machines, suitable for various metal materials.
These top 10 cutting metal machine manufacturers in China provide a wide range of cutting solutions for different industrial needs. Each manufacturer has its own specialization, whether it is laser cutting, plasma cutting, or CNC cutting. With their high-quality machines, advanced technology, and excellent customer service, these manufacturers contribute significantly to the metalworking industry in China and beyond.
Background Research for cutting metal machine manufacturers Companies in China, use qcc.com archive.org importyeti.com
When looking for cutting metal machine manufacturers in China, there are several resources that can provide valuable information. qcc.com is a popular website that specializes in providing business information on Chinese companies. It allows users to search for manufacturers, view their registration details, and obtain contact information.
Another useful resource is archive.org, which is a digital library that stores website archives. By searching for specific manufacturers’ websites on archive.org, you can access past versions of their websites, enabling you to track their historical development, product offerings, and even read customer reviews or testimonials.
importyeti.com is a comprehensive platform that provides import and export data for Chinese manufacturers. By utilizing this website, you can uncover valuable information about cutting metal machine manufacturers, such as their export history, countries they ship to, and the volume of their shipments. This data can assist in evaluating their market presence and international reach.
With these resources, it is possible to gather valuable information about cutting metal machine manufacturers in China. By studying their registration details, historical online presence, and import/export data, you can gain insights into their credibility, market experience, and international footprint. This background research will enable potential buyers to make informed decisions and choose reliable manufacturers for their cutting metal machine requirements.
In conclusion, qcc.com, archive.org, and importyeti.com offer a wealth of information to aid in the search for cutting metal machine manufacturers in China. Utilizing these resources effectively can help buyers in finding trustworthy and reliable manufacturers with the desired expertise and capabilities.
Leveraging Trade Shows and Expos for cutting metal machine Sourcing in China
Trade shows and expos provide excellent opportunities for businesses to connect with potential suppliers and source cutting metal machinery in China. Leveraging these platforms can offer several advantages, including access to a wide range of manufacturers, networking opportunities, and the ability to evaluate products firsthand.
When attending trade shows and expos, it is crucial to have a clear sourcing strategy in mind. Beforehand, businesses should conduct thorough research to identify relevant events that focus on cutting metal machinery in China. These events typically attract a plethora of manufacturers, distributors, and industry professionals, providing a concentrated platform to explore multiple options.
During these events, businesses can interact directly with suppliers, engage in in-depth discussions, and evaluate the quality and functionality of the machinery. This firsthand experience enables better decision-making and ensures that the chosen supplier meets the required specifications and standards.
Furthermore, trade shows and expos offer ample networking opportunities, allowing businesses to establish relationships with manufacturers and gather industry insights. Building connections with reliable suppliers can lead to long-term collaborations and foster a mutually beneficial partnership.
To make the most of these events, businesses should come prepared with a list of requirements, technical specifications, and budget constraints. This ensures that the conversations with suppliers are focused and fruitful, eliminating unnecessary time wastage.
In addition to the sourcing benefits, attending trade shows and expos in China can also provide insights into the latest technological advancements, emerging trends, and competitive landscape within the cutting metal machinery industry. Businesses can gain a competitive edge by staying updated on industry developments and incorporating new technologies into their sourcing strategies.
In conclusion, leveraging trade shows and expos for cutting metal machine sourcing in China offers numerous advantages, including access to a wide range of suppliers, networking opportunities, and the ability to evaluate products firsthand. By conducting thorough research, coming prepared with requirements, and actively engaging with suppliers, businesses can find reliable partners and stay ahead of the competition in the industry.
The Role of Agents and Sourcing Companies in Facilitating cutting metal machine Purchases from China
Agents and sourcing companies play a crucial role in facilitating cutting metal machine purchases from China. These intermediaries serve as a bridge between buyers and manufacturers, helping to streamline the purchasing process and ensure a successful transaction.
One of the main advantages of using an agent or sourcing company is their local knowledge and expertise. They are well-versed in the Chinese market and can provide valuable insights into the best manufacturers, pricing, and quality control practices. This knowledge is especially important for those unfamiliar with the Chinese manufacturing landscape, as it can help avoid common pitfalls and ensure a smooth purchasing experience.
Furthermore, agents and sourcing companies have established relationships with a wide network of manufacturers. This allows them to easily identify and recommend reputable suppliers that meet the buyer’s specific requirements. By vetting potential suppliers and conducting site visits and quality inspections, these intermediaries can save buyers time and effort in finding the right cutting metal machine manufacturer.
Agents and sourcing companies also assist in negotiating prices and terms with manufacturers on behalf of the buyer. Their understanding of local business practices and cultural nuances can often lead to better deals and more favorable terms. This is particularly important when it comes to issues such as intellectual property rights, payment terms, and warranty agreements.
Additionally, agents and sourcing companies provide ongoing support throughout the purchasing process. They can help with tasks such as arranging transportation, handling customs clearance, and resolving any post-purchase issues that may arise. This level of support ensures a higher level of buyer satisfaction and reduces the risk of costly mistakes.
In conclusion, agents and sourcing companies play a vital role in facilitating cutting metal machine purchases from China. Their local knowledge, supplier network, negotiation skills, and ongoing support make them valuable partners for buyers looking to navigate the complexities of the Chinese market and ensure a successful transaction.
Price Cost Research for cutting metal machine manufacturers Companies in China, use temu.com and 1688.com
In the search for cutting metal machine manufacturers in China, two reliable platforms to conduct price cost research are temu.com and 1688.com. These platforms provide a vast database of suppliers and manufacturers in China, offering a wide range of machines for metal cutting purposes.
Temu.com is an online sourcing platform that connects buyers with suppliers in various industries, including machinery. It offers a user-friendly interface and advanced search options to streamline the research process. Through temu.com, users can search for cutting metal machine manufacturers based on specific criteria such as location, product type, quality certifications, and price range. The platform provides detailed supplier profiles, product descriptions, and customer reviews, enabling users to evaluate and compare different options effectively.
1688.com, on the other hand, is a popular Chinese wholesale platform owned by Alibaba Group. It is known for its extensive supplier network, competitive prices, and a vast range of products. Users can utilize the search function on 1688.com to find cutting metal machine manufacturers in China. The platform provides comprehensive product listings, including specifications, pricing details, and supplier information. It also offers a chat feature that allows users to communicate directly with manufacturers to negotiate prices and discuss specific requirements.
When conducting price cost research on these platforms, it is essential to consider certain factors. Firstly, evaluating the manufacturer’s production capacity and capabilities is crucial to ensure they can meet the required specifications and quantities. Secondly, it is essential to compare prices among different manufacturers to find the most competitive offers. Factors such as machine quality, after-sales service, and shipping options should also be taken into account while choosing a manufacturer.
In summary, temu.com and 1688.com are reliable platforms to conduct price cost research for cutting metal machine manufacturers in China. They offer extensive databases, detailed supplier profiles, and comprehensive product information, making it easier for users to find suitable manufacturers at competitive prices. Conducting thorough research on these platforms can help businesses find high-quality cutting metal machines while optimizing cost-effectiveness.
Shipping Cost for cutting metal machine import from China
The shipping cost for importing a cutting metal machine from China will depend on various factors, such as the weight and dimensions of the machine, the distance to the destination country, and the chosen transportation method.
Firstly, the weight and dimensions of the cutting metal machine are crucial in determining the shipping cost. The larger and heavier the machine, the more expensive the shipping cost will be. It is recommended to obtain accurate measurements and weight details from the supplier in China to receive accurate shipping quotes.
Secondly, the distance to the destination country plays a significant role in determining the shipping cost. Long-distance shipping will naturally be more expensive compared to shorter distances due to fuel costs and transportation fees. The shipping cost can vary greatly depending on whether the machine is being imported to North America, Europe, Australia, or any other part of the world.
Lastly, the chosen transportation method will also impact the shipping cost. There are various options, including air freight, sea freight, and land freight. Air freight is generally the fastest method but also the most expensive. Sea freight is relatively cheaper but takes longer. Land freight is suitable when importing from neighboring countries.
To get an accurate estimate for the shipping cost, it is advised to reach out to freight forwarders or shipping companies specializing in international shipments. They will consider the above factors and provide a detailed quote based on your requirements.
In conclusion, the shipping cost for importing a cutting metal machine from China depends on factors such as weight, dimensions, distance, and transportation method. It is crucial to gather accurate information and obtain quotes from reliable freight forwarders or shipping companies to determine the total cost within your budget.
Compare China and Other cutting metal machine Markets: Products Quality and Price,Visible and Hidden Costs
China is known to be one of the largest cutting metal machine markets in the world. When comparing China with other cutting metal machine markets, several factors need to be considered, including products quality and price, visible and hidden costs.
In terms of product quality, China has made significant progress over the years. Many reputable Chinese manufacturers have adopted advanced technology and implemented strict quality control measures. However, it is important to note that the quality of products from Chinese manufacturers can vary greatly. While some offer high-quality machines that meet international standards, others may offer lower-quality machines at a lower price point.
Price is a significant factor when comparing China with other cutting metal machine markets. Chinese manufacturers generally offer competitive pricing due to lower labor and production costs. This has made China an attractive destination for buyers looking for affordable cutting metal machines. However, it is crucial to consider the quality-price ratio. Sometimes, purchasing a higher-priced machine from another market might prove more cost-effective in the long run due to its durability and efficiency.
Visible costs, such as the initial purchase price, shipping, and taxes, should be carefully evaluated. Chinese manufacturers often offer competitive pricing, and shipping costs from China can be comparatively less expensive due to efficient logistics. However, hidden costs should also be taken into account, such as after-sales service, maintenance, and spare parts. It is important to ensure that the manufacturer provides reliable support and easy access to spare parts to avoid prolonged downtime and additional expenses.
In summary, China’s cutting metal machine market offers a range of products with varying quality and competitive pricing. Buyers should evaluate the quality-price ratio and consider both visible and hidden costs when making a purchasing decision. Ultimately, it is essential to choose a reputable manufacturer that can provide reliable support and minimize potential disruptions to operations.
Understanding Pricing and Payment Terms for cutting metal machine: A Comparative Guide to Get the Best Deal
When it comes to purchasing a cutting metal machine, understanding pricing and payment terms is crucial to ensure you get the best possible deal. This comparative guide aims to provide you with the necessary knowledge to navigate through the pricing complexities and negotiate favorable payment terms.
Firstly, it is essential to familiarize yourself with the various factors that contribute to the overall cost of a cutting metal machine. These factors include the machine’s specifications, brand reputation, additional features, and after-sales support. By comparing prices of machines that meet your requirements, you can determine a fair market price range.
Furthermore, it is important to consider the payment terms offered by different suppliers. While some may require full payment upfront, others may offer flexible options such as installments or leasing agreements. Assess your budget and financial capabilities to determine which payment structure suits your needs best. Additionally, inquire about any hidden charges or maintenance fees that may arise during the machine’s lifespan.
To find the most competitive pricing and payment terms, consider reaching out to multiple suppliers. Request detailed quotations that break down the costs involved, allowing you to compare prices accurately. Take into account any value-added services or warranties offered, as they may influence the overall cost-effectiveness of the machine.
Negotiation is a key aspect of securing a favorable deal. Armed with information on competitive pricing, leverage this knowledge to negotiate with suppliers. Highlight any lower-priced offers you have received and inquire if they can match or beat them. Suppliers are often willing to negotiate on pricing or payment terms to secure a sale.
Finally, before making a final decision, conduct due diligence on the supplier’s reputation. Look for testimonials or reviews from previous customers to assess their reliability and customer satisfaction. Remember that the cheapest option may not always be the best choice if the supplier lacks credibility or after-sales support.
In conclusion, understanding pricing and payment terms for a cutting metal machine is integral to securing the best deal. By comparing prices, assessing payment options, engaging in negotiation, and conducting due diligence on suppliers, you can maximize your chances of obtaining a cost-effective and reliable machine for your metal cutting needs.
Chinese Regulations and Industry Standards Certifications for cutting metal machine,Import Regulations and Customs for cutting metal machine from China
Chinese Regulations and Industry Standards Certifications:
In China, the manufacturing and sale of cutting metal machines are governed by various regulations and industry standards to ensure product quality, safety, and environmental compliance. One key regulatory body in this regard is the National Certification and Accreditation Administration (CNCA), responsible for issuing compulsory product certifications.
The main industry standards related to cutting metal machines are set by the Chinese National Technical Committee of Machinery Standardization (CNTCMS). These include standards for safety requirements, performance testing, labeling, and marking. The most commonly recognized industry standards for cutting metal machines in China are the GB/T standards.
To comply with Chinese regulations, manufacturers of cutting metal machines must obtain several certifications. The China Compulsory Certification (CCC) is a mandatory certification that applies to many products, including cutting metal machines. Manufacturers must submit their products to accredited testing laboratories and obtain the CCC mark before importing or selling their machines in China.
In addition to CCC, there are other certifications such as ISO 9001 for quality management systems and ISO 14001 for environmental management systems. These certifications demonstrate compliance with international standards and can enhance the product’s marketability and credibility.
Import Regulations and Customs for cutting metal machines from China:
Importing cutting metal machines from China requires compliance with specific regulations and customs procedures. Importers should be aware of these requirements to ensure smooth customs clearance.
Firstly, importers need to determine the specific import duties and taxes applicable to their country. Tariff classification codes or Harmonized System (HS) codes are essential for determining the correct duties. Importers should consult their local customs authority or hire a customs broker for assistance.
Furthermore, importers must comply with any import restrictions or prohibitions that their country imposes on certain types of machinery. The importation of certain technologies or machinery components may be restricted due to national security or environmental concerns.
When importing cutting metal machines from China, importers should prepare the necessary documentation, including the commercial invoice, packing list, bill of lading or airway bill, and any required certificates of conformity or compliance. These documents must accurately describe the goods, their value, and origin.
It is advisable to work with a reputable shipping agent or freight forwarder who can handle the logistics and customs clearance process. They can assist with completing the necessary paperwork, coordinating with customs officials, and ensuring the goods are compliant with import regulations.
In conclusion, understanding Chinese regulations and industry standards certifications, as well as import regulations and customs procedures, is crucial for importing cutting metal machines from China. Compliance with these requirements will ensure the smooth importation and sale of these machines while ensuring product quality, safety, and adherence to environmental standards.
Sustainability and Environmental Considerations in cutting metal machine Manufacturing
Sustainability and environmental considerations play a crucial role in the cutting metal machine manufacturing industry. This sector, which involves the production of machinery used to cut and shape various metal components, can have a significant impact on the environment due to the energy-intensive processes involved and the generation of waste and emissions.
One key aspect of sustainability in cutting metal machine manufacturing is energy efficiency. By adopting energy-efficient technologies and practices, manufacturers can reduce the amount of energy consumed during the production process. This not only helps lower operational costs but also minimizes the carbon footprint associated with the manufacturing of cutting metal machines.
Another important consideration is the use of environmentally friendly materials and processes. Manufacturers can opt for recyclable and non-hazardous materials for constructing cutting metal machines. Additionally, adopting eco-friendly manufacturing processes, such as using water-based coolants instead of oil-based ones, can reduce the environmental impact.
The reduction of waste and emissions is also a critical factor in sustainable manufacturing. Implementing waste management techniques, such as recycling and reusing materials, can help minimize the amount of waste generated. Similarly, adopting emission control technologies, such as air filtration systems, can reduce the release of harmful pollutants into the atmosphere.
Furthermore, sustainable cutting metal machine manufacturing involves the implementation of responsible supply chain practices. This includes sourcing materials from ethical and environmentally conscious suppliers, as well as considering the social and environmental impact throughout the entire supply chain.
To promote sustainability and environmental considerations in cutting metal machine manufacturing, industry standards and regulations can play a vital role. Governments and relevant authorities can enforce regulations that promote the use of energy-efficient equipment and the reduction of waste and emissions. Industry associations can also establish voluntary standards and best practices to guide manufacturers in adopting sustainable approaches.
In conclusion, sustainability and environmental considerations are crucial in cutting metal machine manufacturing. Energy efficiency, the use of eco-friendly materials and processes, waste reduction, and responsible supply chains all contribute to mitigating the environmental impact of this industry. By adopting sustainable practices, manufacturers can reduce their carbon footprint and contribute to a more sustainable future.
List The Evolution history of “cutting metal machine”
The evolution of cutting metal machines has seen significant advancements over the years, transforming the manufacturing industry with improved efficiency and precision.
1. Early Manual Tools: The earliest metal cutting devices were simple handheld tools like chisels and saws. These required human power and were limited in their cutting capabilities.
2. Industrial Revolution: With the advent of the Industrial Revolution in the late 18th century, mechanical power began to be harnessed for metal cutting. Steam-powered machines were developed, such as the rotary shear, which allowed for more efficient and faster cutting.
3. Introduction of Power Saws: In the late 19th century, power saws using reciprocating motion were introduced. These machines utilized steam or hydraulic power to cut through metal sheets, bars, and tubes. They revolutionized metal cutting by significantly reducing labor and time required.
4. Introduction of Electric Motors: With the development of electric motors in the early 20th century, metal cutting machines became more versatile and precise. Electric-powered bandsaws and circular saws offered greater control and accuracy in cutting various types of metals.
5. CNC Technology: The 1950s saw the emergence of Computer Numerical Control (CNC) technology in metal cutting machines. CNC machines used computer programming and automation to control the cutting process, greatly improving accuracy, repeatability, and efficiency.
6. Laser Cutting Technology: In the 1970s, the introduction of laser cutting revolutionized the metal fabrication industry. Laser cutting machines utilized powerful lasers to precisely cut through various metals, offering incredible speed and precision.
7. Waterjet Cutting: In the 1980s, waterjet cutting machines emerged as an alternative to traditional cutting methods. These machines utilized high-pressure jets of water mixed with abrasive particles to cut through metal. Waterjet cutting offered versatility in cutting various materials without heat distortion.
8. Plasma Cutting: Plasma cutting machines gained popularity in the 1990s, utilizing a plasma torch to cut through electrically conductive materials. Plasma cutting offered fast and precise cutting, especially for thicker metals.
9. Modern Advancements: In recent years, metal cutting machines have continued to advance with improved computer control, cutting technologies, and materials. These machines now integrate multiple cutting methods, such as laser, waterjet, and plasma, providing even more efficient and precise cutting solutions.
Overall, the evolution of metal cutting machines has seen a progression from manual tools to powered machines, incorporating CNC technology, lasers, waterjets, and plasma for enhanced efficiency and precision in metal fabrication.
The Evolution and Market Trends in cutting metal machine Industry
The cutting metal machine industry has witnessed significant evolution and market trends over the years. With advancements in technology and increasing demand for precision and efficiency, the industry has adapted and developed new solutions to meet the changing needs of various sectors.
One major evolution in the cutting metal machine industry is the shift from traditional methods to computer numerical control (CNC) machines. CNC machines have revolutionized the industry by offering precise and automated cutting solutions. These machines use pre-programmed instructions to precisely control the movement of the cutting tool, resulting in higher accuracy and reduced human error. CNC machines have also enabled complex cutting patterns and shapes to be achieved, opening up new possibilities and applications.
Market trends in the cutting metal machine industry have been influenced by various factors. The aerospace and automotive sectors, for example, continuously require high-quality and precise metal components for their products. This has led to an increased demand for advanced cutting metal machines that can meet the stringent requirements of these industries. Similarly, the energy sector, particularly renewable energy, has also contributed to the market growth, with the need for precise cutting of metal parts for wind turbines and solar panels.
Another market trend is the emphasis on sustainability and energy efficiency. With growing environmental concerns, manufacturers are now focusing on developing cutting metal machines that use energy-efficient technologies. This includes the use of smart sensors and advanced control systems that optimize the cutting process, resulting in reduced energy consumption and waste. Additionally, the integration of recycling systems into cutting metal machines allows for the reuse of scrap metal and further reduces environmental impact.
The market for cutting metal machines is also being influenced by the rise of Industry 4.0 and the Industrial Internet of Things (IIoT). Manufacturers are increasingly adopting smart cutting machines that are connected to a network, enabling real-time monitoring and data analysis. This connectivity allows for predictive maintenance, increased productivity, and overall operational efficiency.
In conclusion, the cutting metal machine industry has evolved significantly to meet the demands of various sectors. The shift towards CNC machines, the emphasis on precision and efficiency, the focus on sustainability, and the integration of smart technologies have all contributed to the industry’s growth and market trends. As technology continues to advance, it is expected that the cutting metal machine industry will further evolve to meet the ever-changing needs of manufacturing sectors.
Custom Private Labeling and Branding Opportunities with Chinese cutting metal machine Manufacturers
China is known for its manufacturing expertise, particularly in the field of cutting metal machines. With advanced technology and cost-effective production capabilities, Chinese manufacturers offer lucrative opportunities for custom private labeling and branding.
Custom private labeling allows businesses to create their own unique brand identity by adding their logo, company name, and other branding elements to the cutting metal machines. This helps differentiate the products in the market, increasing brand recognition and customer loyalty.
Chinese manufacturers understand the importance of branding and are flexible in catering to unique labeling requirements. They offer a wide range of customization options, including color choices, finishing, packaging, and personalization of machine functionalities to meet specific customer needs.
Furthermore, collaborating with Chinese cutting metal machine manufacturers enables businesses to tap into the extensive supply chain and manufacturing infrastructure available in the country. This allows for cost efficiencies and faster production turnaround times.
Chinese manufacturers, with their vast experience and expertise, also possess the necessary technological capabilities to deliver high-quality cutting metal machines. They adhere to international quality standards, ensuring reliable and durable products.
By leveraging Chinese manufacturers’ expertise, businesses can build a competitive edge in the cutting metal machine market. Partnering with reliable manufacturers who have a good reputation and positive reviews is crucial to ensuring product quality and timely delivery.
In summary, utilizing custom private labeling and branding opportunities with Chinese cutting metal machine manufacturers can help businesses establish their unique brand identity, increase market visibility, and gain a competitive advantage. With their advanced technology, cost-effectiveness, and commitment to quality, Chinese manufacturers offer an attractive proposition for businesses looking to expand their product offerings in the cutting metal machine market.
Tips for Procurement and Considerations when Purchasing cutting metal machine
When purchasing a cutting metal machine, there are several key considerations that you should keep in mind to ensure you make an informed decision. Here are some tips for procurement and the important factors to consider:
1. Machine Type: Determine the type of cutting machine you require based on your specific needs. Common types include plasma, waterjet, laser, or CNC cutting machines. Consider factors such as precision, speed, versatility, and the types of materials you will be cutting.
2. Cutting Capacity: Assess the size and thickness of the metal you will be cutting. Ensure the machine you choose has the appropriate cutting capacity to handle your requirements. Consider factors like maximum cutting thickness and table size.
3. Accuracy and Precision: Look for machines that offer high accuracy and precision, especially if you require intricate and detailed cuts. Check for features like high-resolution linear guides, servo motors, and advanced control systems.
4. Safety Features: Prioritize the safety of your operators. Look for machines with safety features like protective enclosures, emergency stop buttons, user-friendly interfaces, and automatic shut-off mechanisms.
5. Maintenance and Support: Evaluate the maintenance requirements of the cutting machine. Look for machines with low maintenance needs and easy-to-access spare parts availability. Additionally, ensure that the manufacturer or supplier offers reliable technical support and after-sales service.
6. Cost: Consider your budget and compare prices from different manufacturers or suppliers. Keep in mind that while upfront costs are important, long-term costs such as energy consumption and maintenance should also be considered.
7. Supplier Reputation: Research and choose a reputable supplier with a track record of delivering quality cutting machines. Read reviews, seek referrals, and inquire about warranties and guarantees.
8. Training and Operator Knowledge: Consider the level of training required to operate the cutting machine effectively. Ensure that your operators receive proper training to maximize productivity and safety.
9. Flexibility and Expansion: Look for machines that offer flexibility and potential for future expansion. Consider factors such as software compatibility, upgrade options, and compatibility with other equipment or software you may have.
10. Energy Efficiency: Evaluate the energy efficiency of the cutting machine, as it can significantly impact long-term running costs. Look for machines with energy-saving features like power management systems or smart control options.
By keeping these considerations in mind, you can confidently purchase a cutting metal machine that meets your specific needs, offers high performance, and provides long-term value.
FAQs on Sourcing and Manufacturing cutting metal machine in China
Q: Can I source and manufacture cutting metal machines in China?
A: Yes, China is one of the leading countries for sourcing and manufacturing cutting metal machines. It has a robust manufacturing industry with a wide range of capabilities and cost advantages.
Q: What are the advantages of sourcing cutting metal machines from China?
A: There are several advantages to sourcing cutting metal machines from China. Firstly, China offers lower labor and production costs compared to many other countries. This can significantly reduce manufacturing expenses. Secondly, China has a large pool of skilled engineers and technicians experienced in producing cutting metal machines. Thirdly, the country has a well-established supply chain network, which ensures easy access to raw materials and components needed for manufacturing. Lastly, China has a vast manufacturing capacity, allowing for large-scale production and shorter lead times.
Q: What are the potential challenges I may face when sourcing cutting metal machines from China?
A: There are a few potential challenges to consider when sourcing cutting metal machines from China. First, language and cultural differences may pose communication barriers. It is essential to work with a reputable sourcing agent or manufacturer who can bridge the gap and ensure smooth communication between parties. Second, quality control can be a concern. It is crucial to conduct thorough due diligence and select reliable suppliers who adhere to international quality standards. Third, intellectual property protection can be an issue in China. It is advisable to register patents or other protective measures before engaging in manufacturing activities.
Q: How can I find suitable suppliers or manufacturers in China for cutting metal machines?
A: There are various ways to find suitable suppliers or manufacturers in China. Online B2B platforms like Alibaba, Made-in-China, or Global Sources provide a comprehensive database of manufacturers. Additionally, attending trade shows and industry exhibitions in China can help establish direct connections with potential suppliers. Working with a local sourcing agent who has extensive knowledge of the market and industry can also simplify the process.
Q: How can I ensure the quality of cutting metal machines manufactured in China?
A: To ensure quality, it is important to conduct thorough due diligence before selecting a supplier. This includes verifying their certifications, manufacturing capabilities, and inspecting their facilities. Requesting product samples, conducting factory audits, and implementing strict quality control processes are also essential. Engaging a third-party inspection agency to inspect the products before shipment can provide an extra layer of assurance.
Why contact sourcifychina.com get free quota from reliable cutting metal machine suppliers?
Sourcifychina.com offers free quota from reliable cutting metal machine suppliers for several reasons. Firstly, by providing a free quota, Sourcifychina.com aims to attract potential buyers who are interested in purchasing cutting metal machines. This allows them to generate leads and connect with potential customers who have a genuine interest in their products.
Secondly, by partnering with reliable cutting metal machine suppliers, Sourcifychina.com ensures that their customers receive high-quality machines. By conducting a thorough screening process, they select suppliers who have a proven track record of delivering top-notch machines that meet the needs and expectations of the buyers. This not only enhances customer satisfaction but also fosters long-term partnerships between the suppliers and buyers.
Moreover, offering a free quota allows Sourcifychina.com to showcase the capabilities and competence of their suppliers. By providing potential buyers with the opportunity to request a quota at no cost, Sourcifychina.com demonstrates transparency and builds trust in their supplier network. This way, buyers can evaluate the supplier’s pricing, lead time, and other relevant details before making a purchasing decision. It empowers buyers to make an informed choice, leading to a better overall procurement experience.
Additionally, by obtaining a free quota, buyers can assess the competitiveness and suitability of the cutting metal machine suppliers for their specific requirements. It helps buyers compare different suppliers, their pricing, manufacturing capabilities, and other factors necessary for making an informed sourcing decision.
In summary, Sourcifychina.com provides a free quota from reliable cutting metal machine suppliers to attract potential buyers, ensure product quality, demonstrate transparency, build trust, and facilitate informed buying decisions. Ultimately, the goal is to create a seamless and satisfactory procurement experience for buyers while establishing strong relationships with reliable suppliers.