Introduce about machines that cut metal guide,Qulity,Cost,Supplier,Certification,Market,Tips,FAQ
Metal cutting machines are advanced pieces of equipment used in various industries to precisely cut and shape metal materials. These machines offer several benefits, including increased productivity and accuracy. In this guide, we will explore important aspects such as quality, cost, suppliers, certifications, market trends, and FAQs.
Quality is a crucial factor while considering metal cutting machines. It is essential to invest in reliable, high-quality machines manufactured by reputable companies. These machines must provide precise and clean cuts, ensuring minimal material waste. Look for machines that incorporate advanced technologies and have a proven track record of delivering excellent performance.
When it comes to cost, metal cutting machines vary in price depending on factors such as size, features, and brand. It is important to compare prices from different suppliers to ensure a reasonable cost that aligns with your budget. While price is a consideration, it is equally important to evaluate the machine’s performance and durability.
Choosing a reputable supplier is crucial for obtaining a reliable metal cutting machine. Research different suppliers and their customer reviews to ensure you select one that provides optimal after-sales service and technical support. Trusted suppliers often offer warranties and maintenance services, ensuring long-term satisfaction with your purchase.
Certifications play a vital role in ensuring the quality and safety of metal cutting machines. Look for machines that comply with internationally recognized certifications such as ISO 9001, CE, and UL. These certifications affirm that the machines meet the required industry standards and regulations.
The market for metal cutting machines is witnessing steady growth due to increased demand across industries like automotive, aerospace, construction, and manufacturing. Advancements in technology, such as CNC (Computer Numerical Control), have revolutionized the metal cutting process, contributing to market expansion.
Here are some tips for choosing and using metal cutting machines:
1. Evaluate your specific cutting requirements and choose the machine accordingly.
2. Seek recommendations from experts or industry professionals.
3. Regularly maintain and calibrate the machine to ensure optimal performance.
4. Train operators to safely and efficiently operate the machine.
Frequently Asked Questions (FAQs):
– What types of metals can be cut using these machines?
Metal cutting machines can cut a wide range of metals, including steel, aluminum, copper, brass, and stainless steel.
– How precise are these machines in terms of cutting accuracy?
Modern metal cutting machines offer high precision, with cutting tolerances as low as 0.01mm.
– Can these machines handle thick metal sheets?
Yes, there are machines specifically designed to cut thick metal sheets, capable of handling varying thicknesses.
In conclusion, metal cutting machines are essential tools for precise and efficient metal cutting. By considering factors such as quality, cost, suppliers, certifications, market trends, and proper usage tips, you can find the ideal machine to meet your specific requirements.
Types of machines that cut metal
There are various types of machines used for cutting metal, each designed for specific purposes. These machines utilize different cutting methods to achieve desired precision and efficiency in metalworking processes. Here are some common types of metal cutting machines:
1. Bandsaw: A bandsaw is a power tool equipped with a continuously rotating toothed metal band. It is used for cutting various shapes and sizes of metal stock, such as bars, pipes, and sheets, by running the material through the band’s teeth.
2. Circular Saw: This machine uses a circular disc or blade with sharp teeth to cut through metal. It can be handheld or mounted on a table or bench to provide stability during cutting.
3. Lathe Machine: A lathe is a versatile machine used for shaping metal using rotation. It holds the workpiece in a spindle and cuts it using tools that move linearly or pivot on an axis. This machine is commonly used for turning, facing, threading, and other lathe operations.
4. Milling Machine: Milling machines use rotary cutting tools to remove material from a workpiece, creating complex shapes and profiles. They can cut metals in different directions, making them suitable for various machining operations like drilling, slotting, and contouring.
5. Plasma Cutter: Plasma cutters use a high-temperature plasma jet to slice through metal. The machine generates an electric arc between an electrode and the metal, creating a plasma stream that melts the material, which is blown away by high-velocity gas.
6. Waterjet Cutter: Waterjet cutting machines employ a high-pressure stream of water mixed with abrasive materials to erode metal, creating precise cuts. The water stream is directed by a computer-controlled nozzle, allowing for intricate shapes and tight tolerances.
Each of these metal cutting machines has its advantages and limitations, catering to different manufacturing requirements. The choice depends on factors like the type of metal, desired precision, complexity of the cut, material thickness, and production volume.
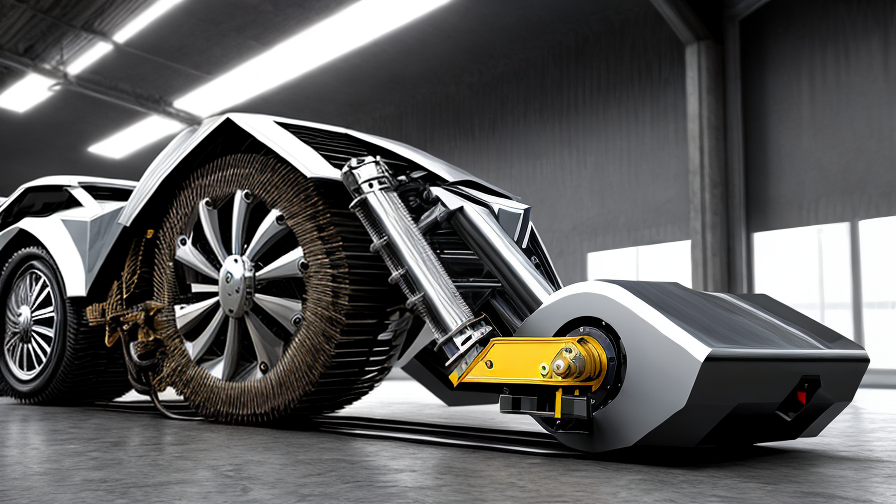
Pros and Cons of Using machines that cut metal
Pros:
1. Precision: Machines that cut metal offer high precision and accuracy. They can produce intricate shapes and designs with minimal error, ensuring consistent quality in the finished product.
2. Efficiency: These machines can cut through metal quickly, resulting in faster production times. This increased efficiency boosts overall productivity and reduces lead times, allowing manufacturers to meet deadlines and fulfill orders more effectively.
3. Cost-effective: Utilizing cutting machines can be cost-effective in the long run. While they may require a significant initial investment, they can save money over time by reducing labor costs, improving material utilization, and minimizing waste.
4. Flexibility: Metal cutting machines can be programmed to cut a wide range of materials, sizes, and shapes. This versatility makes them suitable for various industries, such as automotive, aerospace, construction, and manufacturing.
5. Safety: Modern metal-cutting machines are equipped with safety features to minimize the risk of accidents or injuries. They often include sensors, emergency stop buttons, and protective guards, ensuring the well-being of operators and minimizing human error.
Cons:
1. High initial cost: Investing in metal-cutting machines can be expensive, especially for small-scale businesses, startups, or those with limited budgets. The cost of purchasing, installing, and maintaining these machines might become a barrier for some companies.
2. Skilled operator requirement: Operating metal-cutting machines requires specialized knowledge and experience. Training operators to handle these machines effectively can be time-consuming and may require additional resources.
3. Maintenance and repairs: Machines may experience breakdowns or require regular maintenance to ensure optimal performance. Downtime during repairs or maintenance can disrupt production schedules, impacting overall productivity and potentially leading to financial losses.
4. Limited flexibility for complex cuts: While modern machines are versatile, they may have limitations when it comes to complex or unconventional cuts. Some shapes or designs may require manual cutting, which may add time and labor costs to the production process.
5. Environmental impact: Metal-cutting processes can generate a significant amount of waste, such as metal shavings and debris. Proper disposal or recycling of this waste is essential to minimize environmental impact, adding an additional responsibility for businesses.
In conclusion, metal-cutting machines offer numerous advantages such as precision, efficiency, cost-effectiveness, flexibility, and safety. However, they also have drawbacks like high initial costs, skilled operator requirements, maintenance needs, limited flexibility for complex cuts, and potential environmental impact.
machines that cut metal Reference Specifications (varies for different product)
Metal cutting machines are essential tools used in various industries for efficiently cutting and shaping metal materials. These machines are designed to deliver precise and accurate cuts, making them indispensable in manufacturing processes. They are available in different types and specifications, each tailored to meet specific cutting needs. Here are some common reference specifications for metal cutting machines:
1. Cutting method: Metal cutting machines employ various cutting techniques, including laser cutting, waterjet cutting, plasma cutting, and oxy-fuel cutting. Each method offers unique advantages in terms of speed, precision, and cost-effectiveness.
2. Cutting capacity: The cutting capacity of a machine refers to its ability to handle specific dimensions and thicknesses of metal materials. It is usually specified in terms of maximum length, width, and thickness that the machine can handle without compromising on the quality of the cut.
3. Cutting speed: This specification refers to the rate at which the machine can cut through the metal material. Cutting speed is typically measured in inches per minute (IPM) or meters per minute (MPM) and varies depending on the cutting method, metal type, and thickness.
4. Positioning accuracy: Metal cutting machines provide high positioning accuracy to ensure precise and consistent cutting results. This specification denotes the machine’s ability to position the cutting tool accurately along the intended cutting path, usually expressed in fractions of an inch or millimeters.
5. Repeatability: Repeatability is a crucial specification that determines the machine’s consistency in delivering the same cutting results when repeating a cutting operation. It represents the minimal deviation in the cutting path when performing subsequent cuts.
6. Power source: Metal cutting machines can be powered by electricity, hydraulics, or pneumatics, depending on the specific requirements of the application. The power source affects the machine’s performance, cutting speed, and versatility.
7. Automation and controls: Advanced metal cutting machines often feature automation and computer numerical control (CNC) systems. These systems allow for precise and automated cutting operations, offering enhanced efficiency, productivity, and ease of use.
It is essential to consider these reference specifications when selecting a metal cutting machine, as they directly impact the machine’s performance, efficiency, and suitability for specific applications. By understanding these specifications, manufacturers can make informed decisions and choose the most appropriate machine to meet their metal cutting needs.
Applications of machines that cut metal
Machines that cut metal have a wide range of applications across various industries. These cutting machines utilize different techniques to efficiently shape and separate metal materials. Here are some key applications of metal-cutting machines:
1. Manufacturing and Fabrication: Metal-cutting machines are extensively used in manufacturing and fabrication processes. These machines aid in creating precise and accurate components for products such as automobiles, aircraft, appliances, and machinery. They allow for the efficient cutting, shaping, and drilling of metal sheets, bars, pipes, and profiles, enabling the production of complex and intricate structures.
2. Construction Industry: Metal-cutting machines play a crucial role in the construction industry. They are used for cutting and fabricating metal components needed for structural frameworks, bridges, tunnels, pipelines, and various infrastructure projects. These machines can effectively cut through thick steel beams, channels, and plates, ensuring the accuracy and integrity of the construction process.
3. Metalworking and Metalforming: Metal-cutting machines are extensively used in metalworking industries. They enable the production of parts, tools, and equipment used in metal forming processes, such as stamping, bending, and forging. These machines facilitate the creation of precise molds, dies, and templates required in the production of metal components used in diverse applications.
4. Automotive and Aerospace Manufacturing: In the automotive and aerospace industries, metal-cutting machines are vital for the production of engine components, gears, shafts, brackets, and other metal parts. These machines allow for high-speed cutting, milling, turning, and drilling of various metals, enabling the production of lightweight yet durable components to meet the stringent requirements of these industries.
5. Metal Recycling: Metal-cutting machines are used in the metal recycling industry to efficiently dismantle and process scrap metal. These machines can easily cut through and separate metal materials, facilitating the recycling and reuse of valuable metals such as steel, aluminum, and copper.
6. Art and Design: Metal-cutting machines also find applications in artistic and design fields. Artists and designers use these machines to create intricate and unique metal sculptures, furniture, jewelry, and decorative items. These machines allow for precise cutting and engraving, enabling artists to express their creativity and bring their designs to life.
In summary, metal-cutting machines have diverse applications across industries, including manufacturing, construction, automotive, aerospace, metalworking, recycling, and art. These machines play a crucial role in shaping, fabricating, and transforming metal materials to meet various needs and requirements.
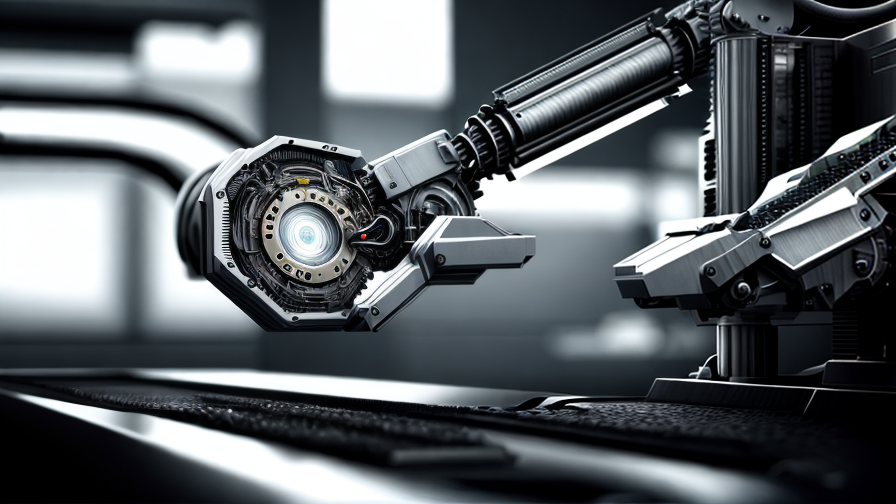
The Work Process and how to use machines that cut metal
The work process of using machines that cut metal involves various steps to ensure accurate and efficient results. Here is a general overview:
1. Planning: Start by understanding the specific requirements of the project, including the material, dimensions, and shapes needed. Create a detailed plan and select the appropriate cutting machine accordingly.
2. Machine Setup: Ensure the machine is properly installed, calibrated, and inspected for any defects. Adjust the settings based on the material being cut, including the feed rate, cutting speed, and tooling.
3. Material Preparation: Prepare the metal stock by measuring and marking the desired dimensions. Use tools like rulers, calipers, or protractors for accurate measurements.
4. Machine Programming: If using a computer-controlled cutting machine, program the desired cuts into the machine’s software. This includes specifying the cutting path, depth, and any additional parameters required for the particular machine.
5. Machine Operation: Load the metal stock onto the cutting machine bed, ensuring it is securely clamped. Activate the machine and monitor the cutting process. Regularly check for any abnormalities, including unusual sounds, vibrations, or tool wear.
6. Tool Maintenance: Regularly inspect and replace cutting tools as required, ensuring they remain sharp. Follow the machine manufacturer’s guidelines for proper maintenance and lubrication.
7. Quality Control: Inspect the cut pieces for accuracy and any deviations from the desired shape or dimensions. Use measuring tools like micrometers or gauges to verify the final results.
8. Finishing Operations: After cutting, additional finishing operations may be needed, such as deburring, sanding, or surface treatment. Perform these tasks as required to achieve the desired final product.
9. Safety Precautions: Follow all safety guidelines while operating the cutting machine. Wear appropriate protective equipment, such as safety goggles, gloves, and ear protection. Keep the work area clean and organized to minimize the risk of accidents.
By following these guidelines, the work process of using machines to cut metal can be safely and effectively executed, resulting in high-quality finished products. Remember to always consult machine-specific manuals and guidelines for the best outcomes.
Quality Testing Methods for machines that cut metal and how to control the quality
When it comes to quality testing methods for machines that cut metal, there are several essential approaches to consider. The first step is to establish a comprehensive quality control plan that focuses on the specific requirements and specifications set for the metal-cutting machines.
One crucial method is the implementation of regular inspections and maintenance schedules to ensure that the machines are functioning correctly and efficiently. This includes checking for any signs of wear or damage on the cutting tools, as well as ensuring proper alignment and calibration of the machine components.
Secondly, conducting periodic performance testing is vital to validate the quality of metal cutting. This can be done by taking random samples of the cut metal and conducting material analysis tests, such as tensile strength and hardness testing, to ensure that the machines are delivering the desired results consistently.
Furthermore, employing non-destructive testing methods, such as ultrasonic or magnetic particle inspection, is beneficial in identifying any potential defects or flaws in the metal cutting process. These methods allow for early detection of any issues that could compromise the quality of the cut metal.
To control the quality of metal cutting machines effectively, it is crucial to implement a robust data-driven approach. This involves collecting and analyzing data related to the cutting process, such as cutting speed, feed rate, and tool wear. By monitoring these parameters, it becomes possible to identify trends or deviations that may indicate a decline in the quality of the cut metal. This data-driven approach also enables predictive maintenance, allowing for proactive adjustments or repairs to be made before any significant issues arise.
Lastly, ensuring that operators are adequately trained and following standardized procedures is essential. Implementing training programs that cover machine operation, maintenance, and quality control can significantly contribute to maintaining high-quality standards.
In conclusion, an effective quality control plan for machines that cut metal involves regular inspections, periodic performance testing, non-destructive testing, data-driven analysis, and comprehensive operator training. By implementing these methods, manufacturers can achieve consistent, high-quality metal cutting while minimizing the risk of defects or compromised performance.
machines that cut metal Sample Policy and Post-Purchase Considerations for machines that cut metal from China
Sample Policy:
When dealing with the purchase of machines that cut metal from China, it is essential to have a well-defined sample policy in place. This policy should outline the following considerations:
1. Quality Assurance: The supplier should provide a sample machine that accurately represents the quality and specifications of the final product. It should be thoroughly tested to ensure it meets the required standards and performs efficiently.
2. Inspection and Evaluation: The buyer must have the opportunity to inspect and evaluate the sample machine before making a purchase decision. This may include conducting tests, checking for any defects or issues, and verifying if it meets the specific requirements for metal cutting applications.
3. Documentation: The supplier should provide all necessary documentation related to the sample machine, including operation manuals, maintenance instructions, and warranty details. This documentation should be accurate, clear, and in English or the buyer’s preferred language.
4. Return Policy: If the sample machine fails to meet the required quality standards or specifications, the buyer should be entitled to return it and receive a refund or an alternative machine that meets the required criteria. The return policy should clearly state the conditions and timeframe for returns.
Post-Purchase Considerations:
After purchasing a machine that cuts metal from China, the following post-purchase considerations should be taken into account:
1. Installation and Training: The supplier should offer assistance with installation, setup, and training of operators to ensure the machine is correctly implemented and operated. This includes providing clear instructions or on-site support if required.
2. Warranty and Support: The machine should come with a comprehensive warranty period, typically covering a minimum of one year. The buyer should also have access to technical support services, including troubleshooting assistance and spare parts availability.
3. Performance Monitoring: Regular monitoring of the machine’s performance is crucial to detect any issues or potential problems early on. This can be accomplished through periodic inspections, maintenance checks, and performance evaluation against the initial sample machine.
4. Feedback and Communication: Maintaining an open line of communication with the supplier is essential. Any concerns, questions, or feedback regarding the machine’s performance or any issues should be promptly conveyed to the supplier for resolution.
By implementing a thorough sample policy and considering these post-purchase aspects, buyers can ensure a smoother experience when purchasing machines that cut metal from China, minimizing the risk of quality issues and maximizing the value of their investment.
Sourcing machines that cut metal from China: Opportunities, Risks, and Key Players
China is a dominant player in the global market when it comes to sourcing machines that cut metal. The country offers numerous opportunities for businesses seeking efficient and cost-effective metal cutting solutions. However, there are also risks associated with sourcing from China, including quality control issues and intellectual property concerns. Let’s explore these opportunities, risks, and key players in the Chinese metal-cutting machine market.
Opportunities:
1. Cost-Effective Solutions: Chinese metal-cutting machines are often more affordable compared to their counterparts from other countries. This enables businesses to lower their manufacturing costs and remain competitive in the market.
2. Wide Range of Options: China offers a diverse range of metal-cutting machines, including laser cutting machines, plasma cutting machines, waterjet cutting machines, and more. Buyers can choose from various models that suit their specific requirements.
3. Technological Advancements: Chinese manufacturers have been investing in research and development, leading to continuous technological advancements in metal-cutting machines. These advancements enhance precision, speed, and efficiency, contributing to increased productivity for businesses.
Risks:
1. Quality Control: Some Chinese manufacturers may compromise quality to reduce costs, resulting in unreliable and less durable metal-cutting machines. Buyers must conduct thorough due diligence and quality inspections before committing to a supplier.
2. Intellectual Property Concerns: China has long been criticized for intellectual property violations. Companies should be cautious when sharing proprietary designs or technology, ensuring that their intellectual property rights are protected.
3. Communication Challenges: Language and cultural differences can create communication barriers between Chinese manufacturers and foreign buyers. Miscommunication may lead to misunderstandings, delays, or incorrect specifications, impacting the sourcing process.
Key Players:
1. Bystronic: Bystronic is a renowned Swiss-headquartered company with production facilities in China. It specializes in laser cutting and bending machines and has a significant presence in the Chinese market.
2. Amada: As a global player, Amada Corporation from Japan also has a strong presence in China. They offer a wide range of cutting and fabrication machines, including laser cutting systems.
3. TRUMPF: This German company has a subsidiary in China and is known for its innovative laser cutting machines. TRUMPF is recognized as a leading player in the global metal fabrication industry.
In conclusion, sourcing machines that cut metal from China offers opportunities for cost-effective solutions, a diverse range of options, and technological advancements. However, businesses should be aware of risks concerning quality control, intellectual property, and communication challenges. Key players in the Chinese market include Bystronic, Amada, and TRUMPF. Careful evaluation and due diligence are crucial while sourcing metal-cutting machines from China to ensure reliable quality and satisfactory business outcomes.
How to find and select reliable machines that cut metal manufacturers in China,use google search manufacturers and suppliers
When searching for reliable metal cutting machine manufacturers in China, Google search can be a useful tool. Here are a few steps to follow:
1. Begin by conducting a generic search using keywords like “metal cutting machine manufacturers in China” or “metal cutting machine suppliers in China.” This will provide you with a list of potential manufacturers.
2. Visit the websites of various manufacturers that appear in the search results. Look for information on their history, experience, certifications, and product range. This will give you an initial idea of whether they are reliable and suitable for your needs.
3. Verify the manufacturer’s reputation and credibility by checking customer reviews and testimonials. Look for feedback from previous customers regarding the quality of their machines, customer service, and overall satisfaction.
4. Consider the manufacturer’s experience and specialization. Look for companies that have been in the industry for a considerable period and have a strong track record in manufacturing metal cutting machines. Additionally, some manufacturers may specialize in specific types or sizes of metal cutting machines, so ensure they can meet your requirements.
5. Consider the manufacturer’s certifications and quality control measures. Look for certifications such as ISO 9001, which ensures that the organization follows strict quality standards. This indicates that the manufacturer is committed to delivering high-quality products.
6. Request product catalogs, specifications, and catalogs from potential manufacturers. Compare the features, specifications, and prices of different machines offered by various manufacturers to determine which best suits your needs and budget.
7. Communicate directly with the shortlisted manufacturers. Ask questions about the machines, warranty, after-sales service, spare parts availability, and any customization options you may require.
8. Lastly, consider visiting trade shows or exhibitions related to metal cutting machines in China. This will allow you to meet manufacturers in person, examine their machines, and discuss your requirements face-to-face.
By following these steps and conducting thorough research, you can find and select reliable metal cutting machine manufacturers in China. Remember to prioritize manufacturers with positive reviews, relevant experience, appropriate certifications, and good customer service.
How to check machines that cut metal manufacturers website reliable,use google chrome SEOquake check if ranking in top 10M
To determine the reliability of a machine manufacturer’s website, you can use various methods, including checking its ranking on Google Chrome with SEOquake. By following a few steps, you can quickly assess the website’s credibility within a specified word limit.
1. Install SEOquake: Add the SEOquake extension to your Google Chrome browser by searching for it in the Chrome Web Store and clicking on “Add to Chrome.” Follow the steps to complete the installation.
2. Perform a Google search: Open Google Chrome and search for the machine manufacturer’s name or related keywords.
3. Analyze search results: Look for the manufacturer’s website among the search results. If it appears within the top 10 million websites, it indicates a reasonably significant online presence.
4. Use SEOquake for ranking analysis: Click on the SEOquake icon in the browser’s toolbar to activate it. A pop-up window will appear with various metrics. Locate the “SEMRush Rank” and check if the manufacturer’s website falls within the top 10 million websites. If it does, it suggests a relatively reliable online presence.
5. Evaluate website quality: Visit the manufacturer’s website and assess its overall quality. Ensure that the site contains detailed information about their machines, such as specifications, technical details, certifications, and contact information. Take note of the website’s design, ease of navigation, and professionalism. Look for customer testimonials or case studies to verify their credibility further.
By following these steps, you can quickly determine the reliability of a metal cutting machine manufacturer’s website. Remember, the word limit should not exceed 300 words to maintain a concise response.
Top 10 machines that cut metal manufacturers in China
China is well-known for its manufacturing industry, and when it comes to machines that cut metal, there are several leading manufacturers in the country. Here is a list of the top 10 machine manufacturers in China that specialize in cutting metal:
1. Shenyang Machine Tool Co. Ltd. (SMTCL): With a history of over 70 years, SMTCL is a major player in the Chinese machine tool industry. They offer a wide range of metal cutting machines, including CNC lathes, milling machines, and machining centers.
2. Dalian Machine Tool Group (DMTG): DMTG is one of the largest machine tool manufacturers in China. They provide various cutting solutions, including CNC milling and turning machines, as well as drilling and grinding machines.
3. Jiangsu Yangli Group: Yangli Group is renowned for producing high-quality machine tools. Their metal cutting machines include hydraulic guillotine shears, hydraulic swing beam shears, and CNC press brakes.
4. Amada (China): Being a subsidiary of the renowned Japanese company, Amada, Amada (China) offers a vast array of metal cutting machines such as laser cutting machines, turret punch presses, and bending machines.
5. Jinan Bodor CNC Machine Co. Ltd.: Bodor CNC specializes in laser cutting machines. They offer a wide range of models suitable for different metal cutting requirements, such as flatbed laser cutting machines and tube laser cutting machines.
6. Bystronic (China) Co. Ltd.: Bystronic China is a subsidiary of the Swiss company, Bystronic. They provide advanced technology in the form of laser cutting systems, waterjet cutting machines, and press brakes.
7. TRUMPF (China): TRUMPF is a prominent global manufacturer of machine tools. Their Chinese subsidiary offers an extensive range of metal cutting machines, including laser cutting systems, punching machines, and bending machines.
8. Shandong Fin CNC Machine Co. Ltd.: Specializing in CNC drilling machines, Fin CNC produces high-quality solutions for metal cutting needs. Their products are widely used in industries such as aerospace, automotive, and shipbuilding.
9. Maanshan Press & Shear Machinery Co. Ltd.: This company focuses on producing hydraulic press machines and shearing machines for metal cutting purposes. They offer a wide variety of models suitable for different applications.
10. Hako CNC Machine (Anhui) Manufactory Co. Ltd.: Hako CNC provides a range of metal cutting machines, including CNC shearing machines, hydraulic guillotine shears, and CNC press brakes. They are known for their efficient and precision-oriented products.
These top 10 machine manufacturers in China offer a wide variety of cutting solutions to cater to different industrial requirements. From CNC lathes and laser cutting machines to hydraulic guillotine shears and drilling machines, these manufacturers provide cutting-edge technology to meet the diverse needs of the metalworking industry.
Background Research for machines that cut metal manufacturers Companies in China, use qcc.com archive.org importyeti.com
QCC.com, Archive.org, and Importyeti.com are valuable sources to conduct background research on manufacturers of metal-cutting machines in China. These platforms provide comprehensive information on companies, their products, and related activities within the industry. Here is an overview of what these sources offer:
1. QCC.com: QCC.com is a Chinese business search engine that offers detailed company profiles and background information. It provides data such as company registration details, legal representatives, financial status, and operational history. By searching for specific keywords like “metal-cutting machines” or “machine tool manufacturers,” valuable insights can be gained on companies operating in this sector. Additionally, QCC.com also provides contact details, including phone numbers and addresses, which can be helpful for further inquiries or collaboration prospects.
2. Archive.org: Archive.org is a digital library that stores snapshots of websites over time. It can be used to access historical data on manufacturers’ websites and track their progress and evolution. By searching for specific company websites, interested parties can view the content that was available on those websites during different periods. This can help evaluate the company’s growth, product range, and technological advancements over time. Archive.org can also offer insights into the company’s past projects, partnerships, and achievements through their website’s content.
3. Importyeti.com: Importyeti.com is a platform that provides import and export data for businesses engaged in global trade. It offers information on import/export activities, shipment records, and customs data. This can be used to identify manufacturers of metal-cutting machines in China, their export destinations, and potential overseas clients. Importyeti.com enables users to search by specific keywords, company names, or product categories. Additionally, the platform provides contact details for the companies involved in import/export activities, which can aid in establishing business connections.
By utilizing these sources, researchers can gain valuable insights into the manufacturing landscape of metal-cutting machines in China. This information can assist in identifying potential suppliers, evaluating their capabilities, and understanding the overall competitiveness of the industry. It is important to analyze the data available on these platforms to make informed decisions and ensure successful business collaborations.
Leveraging Trade Shows and Expos for machines that cut metal Sourcing in China
Trade shows and expos provide a valuable platform for businesses sourcing machines that cut metal in China. These events offer numerous benefits that can be leveraged to meet sourcing needs effectively.
One major advantage is the opportunity to explore a wide range of suppliers and products under a single roof. Trade shows gather exhibitors from various regions and industries, enabling buyers to compare and assess different machinery options in a highly efficient manner. This allows businesses to save time and effort by avoiding the need for separate visits to multiple suppliers.
Furthermore, trade shows facilitate direct interaction between buyers and manufacturers. This direct engagement helps to establish a personal connection and build trust, which is crucial when sourcing machinery from China. It allows buyers to meet face-to-face with suppliers, discuss specific requirements, negotiate prices, and evaluate the quality of the products being offered. The ability to ask questions on the spot and receive immediate answers can significantly enhance the decision-making process.
Trade shows also serve as a platform for staying updated on the latest industry trends and technological advancements. Exhibitors often showcase their latest products, innovations, and technologies, providing valuable insights into the capabilities and advancements in metal-cutting machinery. This knowledge can aid in selecting the most suitable machine for specific cutting requirements and stay ahead of competitors by adopting cutting-edge technologies.
Additionally, trade shows foster connections with industry peers and professionals. Networking with other buyers, experts, and industry leaders can provide valuable advice, recommendations, and references for sourcing metal-cutting machines in China. It can also lead to collaborations, partnerships, or sharing of best practices, enabling businesses to expand their sourcing network and gain insights from experienced individuals.
In summary, trade shows and expos offer a unique opportunity for businesses to efficiently source machines that cut metal in China. Leveraging these events allows for a comprehensive exploration of suppliers and products, direct interaction with manufacturers, access to the latest industry trends, and networking with professionals. By capitalizing on these benefits, businesses can optimize their sourcing efforts and make informed decisions while cutting down on time and costs.
The Role of Agents and Sourcing Companies in Facilitating machines that cut metal Purchases from China
When it comes to purchasing machines that cut metal from China, agents and sourcing companies play a crucial role in facilitating the entire process. These professionals possess in-depth knowledge of the Chinese market, its manufacturers, and the expertise required to navigate the complexities associated with international trade. Their primary aim is to ensure that buyers find reliable suppliers and obtain high-quality products at competitive prices.
Agents act as intermediaries between buyers and suppliers. They have extensive networks and established relationships with manufacturers, which allows them to identify suitable suppliers that meet the buyer’s requirements. They help buyers in vetting potential suppliers through factory visits, product inspections, and quality control processes. Agents understand the technical specifications and standards required for machines that cut metal, enabling them to accurately assess the capabilities of suppliers.
Sourcing companies, on the other hand, provide a comprehensive solution for buyers. They offer a range of services, including supplier identification, negotiation, project management, quality control, and logistics. Sourcing companies have a team of professionals specialized in different areas, such as engineering, quality assurance, and supply chain management, allowing them to handle every aspect of the purchasing process efficiently.
These agents and sourcing companies also play a significant role in communication and language barriers. They bridge the gap between buyers and suppliers, translating technical specifications and requirements accurately. They ensure clear and effective communication, reducing the risk of misunderstandings and facilitating a smooth business relationship.
Moreover, agents and sourcing companies help buyers in negotiating favorable pricing and contract terms. They leverage their knowledge of the local market, industry trends, and supplier relationships to secure competitive prices. By handling negotiations, they ensure that buyers get the best value for their money.
In summary, agents and sourcing companies are indispensable in facilitating purchases of machines that cut metal from China. Their expertise, market knowledge, and network of suppliers enable buyers to find reliable manufacturers, obtain quality products, negotiate favorable terms, and successfully navigate the complexities of international trade, ultimately fostering a smooth and successful business transaction.
Price Cost Research for machines that cut metal manufacturers Companies in China, use temu.com and 1688.com
When it comes to finding manufacturers of machines that cut metal in China, two popular platforms for conducting price and cost research are temu.com and 1688.com. These platforms provide extensive information on various manufacturers, allowing businesses to compare prices, features, and specifications before making a purchasing decision.
Temu.com is a B2B online platform that offers a wide range of industrial machinery and equipment. The website features a dedicated section for metal-cutting machines, where businesses can browse through numerous manufacturers, their products, and related information. Users can extract details on machine specifications, cutting capabilities, and performance to evaluate the most suitable options for their specific needs. Additionally, temu.com provides pricing details, including unit prices, minimum order quantities, and shipping costs, enabling users to estimate the total expenditure involved.
1688.com, on the other hand, is a popular online marketplace in China for bulk wholesale purchases. It offers a vast array of products, including metal-cutting machines. Businesses can search for manufacturers, compare prices, and directly contact suppliers. 1688.com also provides detailed product descriptions, specifications, and customer reviews, which aid in evaluating the quality and reliability of the machines.
To conduct efficient price and cost research, businesses can start by searching for “metal-cutting machine manufacturers” on both temu.com and 1688.com. They can narrow down their search by filtering results based on machine types, specifications, and pricing options. Factors to consider while comparing prices include the cutting accuracy, power, durability, and customer service offered by different manufacturers.
In conclusion, temu.com and 1688.com are valuable resources for businesses seeking manufacturers of machines that cut metal in China. These platforms provide detailed information on product specifications, pricing, and supplier details, facilitating effective price and cost research. By utilizing these platforms, businesses can make informed decisions based on their specific requirements and budget constraints.
Shipping Cost for machines that cut metal import from China
The shipping cost for machines that cut metal imported from China can vary depending on factors such as weight, dimensions, shipping method, and destination. Generally, there are two primary shipping methods: air freight and ocean freight.
Air freight is the fastest option for shipping machines from China. The cost is determined by the weight and dimensions of the packages. Typically, machines that cut metal are heavy, so the air freight charges can be relatively high. However, air freight offers quicker delivery times, which can be beneficial for urgent orders.
Ocean freight is a more economical option for shipping heavy machinery. The cost is calculated based on the volume or weight of the cargo, referred to as chargeable weight. The dimensions and destination also impact the cost. However, ocean freight has longer transit times compared to air freight, ranging from a few weeks to several months depending on the port of origin and destination.
Additionally, other factors such as customs duties, taxes, and handling fees should be considered when calculating the overall shipping cost. It is advisable to consult with a freight forwarder or shipping agent experienced in handling machinery imports to determine the most cost-effective shipping method and ensure compliance with customs regulations.
In conclusion, the shipping cost for machines that cut metal imported from China can vary depending on factors such as weight, dimensions, shipping method, and destination. It is recommended to compare different shipping options and consult with experts to minimize costs and ensure smooth importation.
Compare China and Other machines that cut metal Markets: Products Quality and Price,Visible and Hidden Costs
China is widely known for its dominance in the manufacturing industry, including the market for machines that cut metal. When comparing China to other markets in terms of products quality and price, visible and hidden costs, a few key differences and insights arise.
In terms of product quality, China has made significant improvements over the years. However, it is still commonly perceived that machines from other markets, such as Germany or Japan, offer higher quality and precision. These machines often come with advanced technologies, superior workmanship, and strict quality control processes, ensuring their reliability and longevity. On the other hand, China’s machines may be perceived as having lower quality due to inconsistent standards and occasional issues with reliability and durability.
Price is often a key factor when businesses consider purchasing machines that cut metal. China’s market is characterized by competitive pricing, with machines generally being more affordable compared to those from other markets. This is primarily due to lower labor and production costs in China. However, it is important to note that price alone does not determine the overall value of a machine. Businesses should also consider factors such as productivity, durability, and long-term maintenance costs when assessing the true cost of ownership.
Visible and hidden costs are crucial considerations when comparing China to other markets for metal-cutting machines. Visible costs include the initial purchase price, installation, and training expenses. In this aspect, China’s offerings often have an advantage due to lower initial costs. However, hidden costs, such as maintenance, repairs, and downtime, can add up in the long run. It is essential to evaluate the availability and cost of spare parts, local technical support, and the overall reliability of the machine to mitigate these hidden costs.
In conclusion, China’s market for machines that cut metal has gained significant traction in recent years, yet it still faces challenges in terms of product quality perception. While China frequently offers competitive pricing, machines from other markets like Germany or Japan may be perceived as higher quality. When making purchasing decisions, businesses must carefully evaluate both visible and hidden costs to determine the true value of the machine. By considering factors such as longevity, productivity, maintenance, and local support, businesses can make informed decisions that suit their specific needs and goals.
Understanding Pricing and Payment Terms for machines that cut metal: A Comparative Guide to Get the Best Deal
When purchasing machines that cut metal, it is crucial to have a clear understanding of the pricing and payment terms in order to secure the best possible deal. This comparative guide aims to provide insights and tips to ensure a successful purchase within a limited word count of 300.
Firstly, it is important to research and compare prices from different suppliers and manufacturers. A price comparison will help you gauge the market range and identify potential outliers. It is recommended to obtain quotes from various sources, both local and international, to get a comprehensive understanding of the pricing landscape.
While considering the pricing, it is equally essential to evaluate the quality and specifications of the cutting machines. Comparing the features and capabilities offered by different manufacturers will help assess the value for money and avoid overpaying for unnecessary functionalities.
When negotiating with suppliers, understanding the payment terms is crucial. This includes determining the upfront payment, installment options, and any financing alternatives available. Some suppliers may offer discounts for full upfront payments, while others may provide more flexibility in payment schedules. Evaluating the financial implications of different payment terms will help make an informed decision that suits your budget and cash flow requirements.
Furthermore, it is advisable to consider the potential maintenance costs and availability of spare parts. In some cases, manufacturers offering slightly more expensive machines could provide better after-sales service or offer longer warranties, which may offset additional costs in the long term.
Lastly, it is essential to inquire about any additional costs that may arise, such as shipping, installation, or training fees. These expenses should be accounted for and compared across different suppliers to have a true cost comparison.
In conclusion, understanding the pricing and payment terms for machines that cut metal is crucial for securing the best deal. Proper research, price comparisons, evaluation of specifications, and careful consideration of the payment options and related costs are all pivotal steps in ensuring a successful purchase.
Chinese Regulations and Industry Standards Certifications for machines that cut metal,Import Regulations and Customs for machines that cut metal from China
Chinese Regulations and Industry Standards Certifications for machines that cut metal play a crucial role in ensuring the safety, quality, and compliance of such equipment. The main regulatory body overseeing this industry is the State Administration for Market Regulation (SAMR), which sets guidelines and standards for manufacturing and importing metal cutting machines.
To ensure compliance with Chinese regulations, manufacturers and importers must obtain various certifications. The most important certification for metal cutting machines is the China Compulsory Certification (CCC). This certification ensures that the machine meets mandatory safety and quality requirements. Other certifications that manufacturers can obtain include ISO 9001 for quality management and ISO 14001 for environmental management.
Moreover, industry-specific standards and certifications are also highly regarded in China, such as the National Standard for Machine Tool Safety and Performance. This standard covers aspects like safety features, precision, and performance requirements. Adhering to such standards enhances the competitiveness and credibility of the machines.
When it comes to importing metal cutting machines from China, importers must also comply with specific regulations and customs requirements. Importing machinery requires obtaining an Import License from China’s Ministry of Commerce or its authorized agencies. Additionally, customs documentation, including commercial invoices, packing lists, and bills of lading, must be properly completed and submitted.
Importers should also be aware of applicable import duties and taxes. Tariff rates for machinery can vary depending on the product category, and it is advisable to consult China’s Customs Tariff Commission or a customs broker to determine the correct rates. Importers might also need to comply with import inspection and quarantine procedures, especially for machinery that involves potential risks.
To summarize, compliance with Chinese regulations and industry standards certifications is necessary when dealing with metal cutting machines. Importers should be familiar with the required certifications, such as CCC, and ensure proper documentation and adherence to customs regulations while importing machinery from China. Seeking guidance from experienced customs brokers or consultants can greatly facilitate the import process.
Sustainability and Environmental Considerations in machines that cut metal Manufacturing
Sustainability and environmental considerations play a crucial role in the manufacturing industry, including machines that cut metal. These considerations focus on minimizing the environmental impact of the manufacturing process, reducing waste generation, and optimizing energy efficiency.
One approach to achieving sustainability in metal cutting machines is through the implementation of cleaner and more efficient technologies. For instance, using advanced laser cutting technology can significantly reduce material waste and energy consumption compared to traditional machining methods. Laser cutting machines utilize high-intensity lasers to precisely cut metal, minimizing material loss and lowering energy requirements.
Another aspect to consider is the use of sustainable materials in the construction of the machines. Opting for eco-friendly materials, such as recycled metals or components made from bio-based materials, can reduce the overall environmental footprint of the machines. Additionally, using materials that are easily recyclable at the end of their lifecycle can contribute to the circular economy.
Energy efficiency is a key concern in the manufacturing industry. Metal cutting machines should be designed with energy-saving features such as variable speed drives, which enable the machines to operate at optimal energy levels based on the specific workload. Implementing smart energy management systems can also monitor and control energy consumption, identifying areas for improvement and reducing overall energy wastage.
Furthermore, proper waste management is critical in the metal cutting manufacturing process. Implementing recycling programs for metal scraps can help minimize waste generation and promote resource conservation. Additionally, ensuring proper disposal of hazardous waste and using environmentally friendly lubricants and cooling fluids are important measures to reduce the negative impact on the environment.
In conclusion, sustainability and environmental considerations in metal cutting machine manufacturing involve the adoption of cleaner technologies, the use of sustainable materials, optimizing energy efficiency, and implementing effective waste management practices. By incorporating these considerations, manufacturers can contribute to a more sustainable and environmentally friendly manufacturing industry.
List The Evolution history of “machines that cut metal”
The evolution of machines that cut metal can be traced back to ancient times when early humans used primitive tools like stones to shape and cut materials. However, it was during the Industrial Revolution in the late 18th century that significant advancements in machining technology began to occur.
The first notable machine that cut metal was the lathe, which originated in ancient Egypt. This device allowed for the rotation of a workpiece while a cutting tool shaped it. The lathe underwent several improvements over the centuries, with Leonardo da Vinci making significant contributions in the 15th century.
In the early 19th century, the milling machine was invented, which allowed for the removal of material from a workpiece by rotating multiple cutting tools. This innovation increased efficiency and accuracy in metal cutting.
Another crucial development was the introduction of the steam-powered metal cutting machine in the early 19th century. This machine utilized steam power to drive the cutting tools, enabling faster and more efficient metal cutting processes.
The 20th century witnessed a series of transformative innovations in metal cutting machines. The advent of electric power led to the replacement of steam engines, making machines more compact and easier to operate. Further advancements included the introduction of automated and computer numerical control (CNC) machines, which revolutionized metal cutting processes by providing precise control and reducing human error.
In recent years, the rise of additive manufacturing technologies, commonly known as 3D printing, has impacted metal cutting. This technique allows for the creation of intricate metal parts by layering material, eliminating the need for cutting in some cases.
From ancient lathes to modern CNC machines and additive manufacturing, the evolution of machines that cut metal has been a story of continuous progress driven by human ingenuity and technological advancements. These machines have played a pivotal role in shaping the industrial landscape and advancing various fields, from manufacturing to aerospace.
The Evolution and Market Trends in machines that cut metal Industry
The machines that cut metal industry has witnessed significant evolution over the years, driven by advancements in technology and changing market trends. From traditional mechanical cutting machines to sophisticated computerized systems, the industry has transformed to enhance efficiency, accuracy, and productivity.
One of the key factors driving the evolution in this industry is the increasing demand for precision and customization. With the rise of industries like aerospace, automotive, and electronics, there is a growing need for machines that can cut complex shapes and contours with utmost precision. This has led to the development of advanced computer numerical control (CNC) machines and laser cutting systems that offer high precision and accuracy in metal cutting.
Additionally, automation and integration have played a crucial role in shaping the market trends in this industry. Manufacturers are increasingly adopting automated metal cutting systems to improve productivity and reduce labor costs. These systems incorporate robotic arms, conveyor belts, and other automated components to streamline the metal cutting process, resulting in higher throughput and improved production efficiency.
Another important trend in this industry is the integration of data analytics and connectivity. Manufacturers are leveraging the power of IoT (Internet of Things) and cloud computing to gather real-time data from cutting machines, analyze performance metrics, and optimize operations. This allows for predictive maintenance, remote monitoring, and improved overall equipment effectiveness.
Furthermore, sustainability and environmental concerns are influencing the market trends in the machines that cut metal industry. With a greater focus on reducing energy consumption and waste generation, manufacturers are developing eco-friendly cutting machines that consume less power and utilize advanced filtration systems to minimize emissions and waste.
In conclusion, the machines that cut metal industry has evolved significantly to meet the increasing demand for precision, customization, automation, and sustainability. The integration of advanced technologies, such as CNC, laser cutting, automation, and data analytics, has revolutionized the industry, driving improved efficiency, accuracy, and productivity. As the industry continues to advance, it is expected that further innovations will be seen to cater to the evolving market demands.
Custom Private Labeling and Branding Opportunities with Chinese machines that cut metal Manufacturers
China is known for its expertise in manufacturing machinery, including cutting machines for metal. If you are a business looking to leverage the potential of custom private labeling and branding opportunities with Chinese manufacturers in this industry, there are several advantages to consider.
Firstly, Chinese manufacturers offer cost-effective solutions that can significantly reduce production expenses. They often have access to advanced production technology and materials at competitive prices, enabling them to offer affordable options for custom private labeling and branding.
Moreover, Chinese manufacturers are widely experienced in catering to diverse customization needs. With their expertise in engineering, they can tailor cutting machines to meet specific requirements, ensuring optimal performance and efficiency for different metal cutting applications. This flexibility allows businesses to establish a unique brand identity through customized labeling, branding, and features.
Additionally, Chinese manufacturers are known for their ability to deliver products quickly. Speedy production processes combined with efficient logistics ensure that businesses can swiftly bring their branded cutting machines to market, meeting consumer demand and gaining a competitive edge.
However, it is crucial to conduct thorough due diligence when selecting a partner for private labeling and branding. Verifying a manufacturer’s reputation, quality control measures, and compliance with international standards is essential to ensure reliable delivery of high-quality products.
In conclusion, Chinese manufacturers offer excellent opportunities for custom private labeling and branding of cutting machines for metal applications. With their cost-effective solutions, customization expertise, quick production, and delivery capabilities, businesses can establish themselves as value-added suppliers in the market.
Tips for Procurement and Considerations when Purchasing machines that cut metal
When it comes to purchasing machines that cut metal, there are several key considerations and tips for procurement that can help ensure you make the right choice. Here are some:
1. Define your requirements: Before starting the procurement process, clearly define your needs, including the type of metal, thickness, and desired output. This will help you shortlist machines that are capable of meeting your specific requirements.
2. Research different options: Conduct thorough research and explore different suppliers, manufacturers, and models available in the market. Consider factors like reputation, reliability, performance, and after-sales service to identify potential suppliers.
3. Quality and durability: Look for machines that are built with high-quality materials and have a reputation for durability. Cutting metal can be a demanding task, so opting for well-built machines will ensure efficient and long-lasting performance.
4. Accuracy and precision: Precision is crucial in metal cutting, so consider machines that offer accurate cutting capabilities. Look for features like laser guidance or computer numerical control (CNC) systems that ensure precise cuts.
5. Speed and efficiency: Evaluate the cutting speed and efficiency of the machines. Production requirements, turnaround time, and the volume of work will help determine the desired speed of the machine.
6. Safety features: Safety is paramount in any industrial environment. Look for machines equipped with safety features like emergency stop buttons, protective guards, and automatic shut-off mechanisms to prevent accidents.
7. Cost and budget: While cost is a significant factor, it should not be the sole determining factor. Consider the overall value for money, including productivity, durability, and after-sales support, rather than focusing purely on the initial purchase price.
8. Training and support: Check if the supplier offers training for machine operators and ongoing technical support. Adequate training ensures optimal machine utilization, while reliable support ensures quick resolution of any technical issues.
9. Review customer feedback: Read customer reviews and testimonials to gain insights into the experiences of other buyers. This can provide valuable information about the machine’s performance, reliability, and customer service of the supplier.
10. Warranty and maintenance: Understand the warranty terms and conditions provided by the supplier, along with the availability of maintenance and spare parts. This will help you plan for routine maintenance and ensure continued operations.
By following these tips and considering the important factors discussed above, you can make an informed decision when purchasing machines for metal cutting, aligning them with your specific requirements and maximizing productivity.
FAQs on Sourcing and Manufacturing machines that cut metal in China
1. What types of metal cutting machines are available in China?
China offers a wide range of metal cutting machines, including laser cutting machines, plasma cutting machines, waterjet cutting machines, CNC milling machines, and CNC lathe machines. These machines are designed to cut various metals such as steel, aluminum, brass, and more.
2. How can I find reliable manufacturers of metal cutting machines in China?
To find reliable manufacturers in China, you can start by conducting online research through platforms like Alibaba, GlobalSources, or Made-in-China. These platforms allow you to browse through a list of verified manufacturers, read customer reviews, and compare prices. Another option is to attend exhibitions or trade fairs held in China, like the China International Industry Fair or the Canton Fair, where you can interact directly with manufacturers and inspect their machines.
3. What factors should I consider when sourcing metal cutting machines from China?
When sourcing machines from China, it is crucial to consider factors such as the manufacturer’s reputation, quality certifications (ISO, CE), production capabilities, product warranty, and after-sales service. Requesting samples or visiting the manufacturing facility to inspect the machines in person can also help ensure their quality.
4. Are Chinese metal cutting machines affordable compared to those from other countries?
China is renowned for its cost-effective manufacturing capabilities, making metal cutting machines from China generally more affordable compared to those from other countries. However, it’s crucial to weigh the cost against other factors like quality and reliability to make an informed decision.
5. Can Chinese manufacturers customize metal cutting machines based on specific requirements?
Yes, many Chinese manufacturers offer customization services for metal cutting machines. This allows you to tailor the machines to your specific needs, such as cutting dimensions, power requirements, or additional features. It’s advisable to discuss your requirements with the manufacturer and ensure they have the necessary expertise to fulfill your customization requests.
6. How can I ensure the quality of metal cutting machines sourced from China?
To ensure the quality of metal cutting machines sourced from China, it is important to conduct due diligence. This involves verifying the manufacturer’s reputation, requesting product samples for testing, checking for quality certifications, and seeking feedback from other customers. It’s also advisable to establish a direct line of communication with the manufacturer to address any concerns or queries promptly.
In conclusion, sourcing and manufacturing metal cutting machines from China offer a wide range of options at competitive prices. However, it is crucial to conduct thorough research, consider various factors, and verify the manufacturer’s reliability to ensure the quality of the machines and a smooth sourcing process.
Why contact sourcifychina.com get free quota from reliable machines that cut metal suppliers?
SourcifyChina.com offers a free quota to reliable machines that cut metal suppliers for several reasons. By providing a free quota, SourcifyChina.com aims to attract potential customers and develop a mutually beneficial relationship with suppliers.
Firstly, the free quota allows SourcifyChina.com to showcase their services to potential customers. By offering a limited amount of free quota, customers can evaluate the quality and efficiency of the machines that cut metal suppliers. This trial period allows customers to gain hands-on experience and assess whether the suppliers meet their specific requirements and standards.
Secondly, SourcifyChina.com benefits from providing a free quota by establishing trust and credibility in the market. By collaborating with reliable suppliers, SourcifyChina.com ensures the quality of the machines used for metal cutting, thereby enhancing their reputation in the industry. This trust-building strategy is essential in an increasingly competitive market, where customers are cautious and seek reassurance regarding the capabilities of suppliers.
Furthermore, the free quota serves as a marketing tool, attracting potential customers who might be hesitant to engage with suppliers directly. By offering a risk-free opportunity to try the services of reliable machines that cut metal suppliers, SourcifyChina.com eliminates the barriers to entry and encourages customers to explore the possibilities without incurring any financial commitment upfront. This strategy effectively expands the customer base and increases the chances of securing long-term partnerships.
Finally, the free quota allows SourcifyChina.com to gather valuable data and feedback from customers. By monitoring the usage patterns and satisfaction levels during the free quota period, SourcifyChina.com can fine-tune their services and tailor them to the specific needs of their clientele. This data-driven approach ensures continual improvements and enhances customer satisfaction, ultimately leading to long-lasting partnerships in the industry.
Overall, providing a free quota to reliable machines that cut metal suppliers is a strategic move for SourcifyChina.com. It allows them to showcase their services, build trust, attract potential customers, and collect valuable feedback. This approach not only benefits SourcifyChina.com but also facilitates efficient and reliable sourcing solutions for customers in need of metal cutting services.