Introduce about metal cutter machine guide,Qulity,Cost,Supplier,Certification,Market,Tips,FAQ
Metal cutter machines are cutting tools used to shape and cut various types of metals with precision and efficiency. They offer a range of benefits, including increased productivity, excellent cutting quality, and reduced material waste. This guide provides valuable information on the quality, cost, suppliers, certifications, market, tips, and FAQs related to metal cutter machines.
The quality of a metal cutter machine is crucial as it directly impacts the accuracy and durability of the cuts. High-quality machines are made from robust materials such as steel, ensuring longevity and reliable performance. They are equipped with advanced features like adjustable cutting speeds, automatic feeding systems, and user-friendly controls for improved efficiency.
When considering the cost of metal cutter machines, factors such as brand, size, features, and technology come into play. Higher-end models with advanced features may be more expensive but can provide greater precision and cutting capabilities. It is essential to evaluate the machine’s cost in relation to the desired level of performance and intended use before making any purchase decisions.
Numerous suppliers offer metal cutter machines in the market, ranging from local to global companies. It is crucial to choose a reputable supplier known for delivering high-quality products and offering excellent customer support. Conducting thorough research, reading customer reviews, and comparing prices will help in selecting a reliable supplier that meets specific requirements.
Certifications play a vital role in ensuring the quality and safety of metal cutter machines. Look for machines that are certified by recognized industry bodies, such as ISO (International Organization for Standardization), CE (Conformité Européene), or OSHA (Occupational Safety and Health Administration). These certifications ensure that the machines meet the necessary quality and safety standards.
The market for metal cutter machines is booming due to increasing industrialization and the need for efficient metal processing. Industries such as automotive, aerospace, construction, and manufacturing extensively utilize metal cutter machines for various purposes, driving market growth. It is crucial to analyze market trends and stay updated with technological advancements for informed decision-making.
Here are a few tips for using metal cutter machines effectively:
1. Familiarize yourself with the machine’s user manual and safety instructions.
2. Always wear appropriate personal protective equipment, including goggles, gloves, and ear protection.
3. Regularly inspect and maintain the machine to ensure optimal performance and safety.
4. Choose the correct cutting tools and adjust settings based on the type and thickness of the metal being cut.
5. Follow proper cutting techniques and avoid excessive force to prolong the machine’s lifespan.
Frequently Asked Questions (FAQs):
Q: Can metal cutter machines cut different types of metals?
A: Yes, metal cutter machines can cut various metals, including steel, aluminum, brass, and copper.
Q: What is the average lifespan of a metal cutter machine?
A: The lifespan of a metal cutter machine depends on factors such as usage frequency, maintenance, and quality. Generally, high-quality machines can last for many years without substantial issues.
Q: Are metal cutter machines easy to operate?
A: Most modern metal cutter machines are designed to be user-friendly, with intuitive controls and clear instructions. However, proper training and familiarity with the machine are recommended for optimal results.
In essence, metal cutter machines are indispensable tools in metalworking industries. Their quality, cost, suppliers, certifications, market, tips, and FAQs covered in this guide provide valuable insights for individuals and businesses interested in utilizing these machines efficiently and effectively.
Types of metal cutter machine
Metal cutting machines are essential tools in various industries such as manufacturing, construction, and automotive. These machines are designed to cut, shape, and remove metal materials efficiently and precisely. There are several types of metal cutting machines available, each designed for specific applications and requirements.
1. Bandsaw: A bandsaw is a versatile cutting machine that consists of a continuous serrated blade fitted around two wheels. It is primarily used for straight or curved cuts, making it suitable for cutting metal bars, pipes, and solid materials in various sizes.
2. Lathe machine: Lathe machines are used for cutting and shaping rotating metal workpieces. The machine holds the workpiece and rotates it against a cutting tool. Lathe machines are commonly used for turning, facing, and drilling operations.
3. CNC plasma cutting machine: Computer Numerical Control (CNC) plasma cutting machines use a high-velocity jet of ionized gas to cut through electrically conductive metals. These machines are highly accurate, fast, and suitable for cutting intricate designs and shapes.
4. Waterjet cutting machine: Waterjet cutting machines use a high-pressure jet of water combined with abrasive particles to cut through various metals. This method is highly precise, and the absence of heat helps prevent heat-affected zones or distortion in the material.
5. Laser cutting machine: Laser cutting machines use a high-powered laser beam to cut through metal materials. They are known for their high precision, speed, and ability to cut through a wide range of metals, including stainless steel, aluminum, and brass.
6. Plasma cutting machine: Plasma cutting machines use a jet of ionized gas to melt and remove metal material, resulting in a clean and precise cut. They are commonly used for cutting sheet metal and are known for their efficiency and fast cutting speeds.
7. Shearing machine: Shearing machines are used to cut sheet metal using a blade-like cutting tool. These machines are capable of making straight, angled, or curved cuts and are commonly used in the fabrication industry.
8. Cutoff saw: Cutoff saws are used for cutting metal rods, pipes, and other solid materials. They feature a high-speed rotating abrasive disc that cuts through the workpiece.
These are just a few examples of the various types of metal cutting machines available. The selection of the most suitable machine depends on factors such as the type of metal, thickness, desired cutting speed, accuracy, and budget.
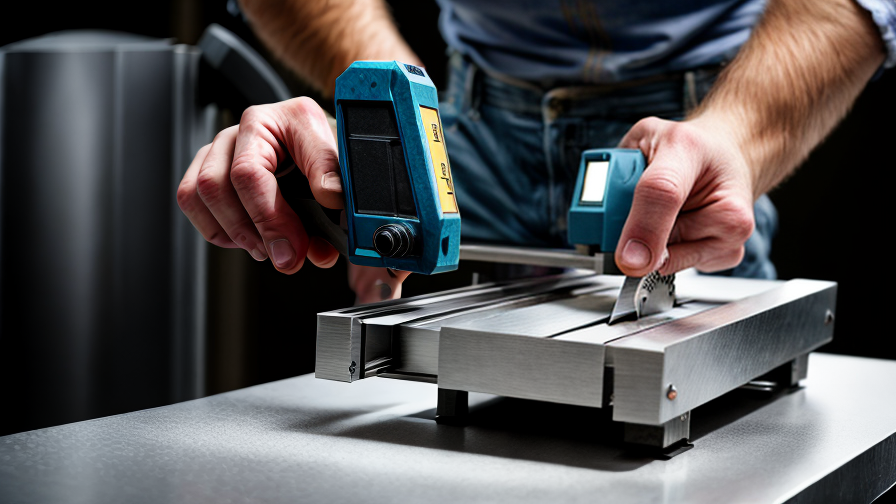
Pros and Cons of Using metal cutter machine
Using a metal cutter machine can bring several benefits to industrial processes, but it also has its drawbacks. Let’s explore the pros and cons of using such a machine:
Pros:
1. Efficiency: Metal cutter machines are extremely efficient in terms of cutting different types of metals, as they utilize sharp and strong blades that can slice through the material quickly and accurately. This enhances productivity and saves time.
2. Precision: These machines are highly reliable for achieving precise and accurate cuts. They allow for customized cutting styles, intricate shapes, and angles, making them suitable for various industrial applications.
3. Versatility: Metal cutter machines are designed to handle a wide range of metals, such as steel, aluminum, brass, and copper. This versatility enables them to be used across various industries, including automotive, aerospace, construction, and manufacturing.
4. Automation: Many metal cutter machines are equipped with advanced automation features, such as computer numerical control (CNC) systems. These automated systems ensure consistency, reduce human error, and provide greater control over the cutting process.
5. Safety: Modern metal cutter machines come with safety features like laser guards, emergency stop buttons, and safety interlocks, minimizing the risk of accidents, injuries, and material wastage.
Cons:
1. Initial Investment: Metal cutter machines can be expensive to purchase and install, particularly if they are equipped with advanced features like lasers or plasma cutters. Therefore, small businesses or startups might find it challenging to afford them.
2. Maintenance and Training: Regular maintenance is necessary to keep metal cutter machines in top condition, and this entails costs and downtime. Additionally, operators need proper training to use the machines safely and effectively, which might require additional investment.
3. Limited Portability: Metal cutter machines are generally heavy and bulky, making them less portable. Moving and repositioning them can be time-consuming and require specialized tools or equipment.
4. Noise and Environmental Impact: Metal cutter machines produce high levels of noise, which can be a nuisance for workers and require hearing protection. Additionally, some cutting processes might release harmful fumes or dust particles, requiring proper ventilation or extraction systems.
5. Size Limitations: Depending on the size of the machine, there might be constraints on the dimensions of the metal sheets that can be cut. Large-scale industrial projects might require more extensive machines or multiple setups, impacting cost and space requirements.
In conclusion, while metal cutter machines offer significant advantages such as efficiency, precision, versatility, automation, and safety, their drawbacks include high initial investment, maintenance costs, training requirements, limited portability, noise/environmental impact, and size limitations. Thus, weighing both the pros and cons is crucial for businesses to determine the feasibility of using such machines for their specific needs.
metal cutter machine Reference Specifications (varies for different product)
The metal cutter machine is a versatile and efficient equipment widely used in industries for cutting various types of metals. It is designed with advanced technology and incorporates a range of features that enable precise and accurate cutting operations.
The reference specifications of the metal cutter machine may vary depending on the specific product model. However, some common specifications include a cutting capacity of up to a certain thickness, typically ranging from a few millimeters to several centimeters. The cutting width is usually adjustable to accommodate different sizes of metal sheets or plates, ensuring flexibility in cutting various dimensions.
The machine is equipped with a powerful motor that provides high cutting speed, enabling quick and efficient metal cutting operations. The cutting mechanism may utilize different cutting techniques, such as laser cutting, plasma cutting, or oxy-fuel cutting, depending on the specific model and application requirements.
The metal cutter machine typically features a sturdy and durable construction, with a heavy-duty frame to ensure stability and precision during cutting operations. It incorporates high-quality cutting tools or blades that are resistant to wear and tear, ensuring long-lasting performance and consistent cutting quality.
To ensure safety during use, the metal cutter machine is equipped with safety features such as emergency stop buttons, protective barriers or shields, and safety interlocks. It may also include automatic control systems that optimize cutting efficiency and accuracy while reducing operator intervention.
Some models of metal cutter machines are designed with additional features to enhance productivity and usability. These may include programmable controls, touch screen interfaces, and automated material handling systems. Additionally, some machines may have integrated cooling systems to prevent overheating and ensure continuous operation.
In conclusion, the metal cutter machine is a vital tool in metalworking industries. Its reference specifications vary according to the specific product model, but generally include cutting capacity, cutting width, cutting techniques, motor power, construction quality, safety features, and optional productivity-enhancing features. It is a reliable and efficient machine that enables precise and accurate metal cutting operations, contributing to increased productivity and cost-effectiveness in various industries.
Applications of metal cutter machine
Metal cutter machines are essential tools widely used in various industries due to their ability to accurately and efficiently cut metals. These machines operate by applying pressure and heat to shape and cut metallic workpieces according to specific requirements. The applications of metal cutter machines are numerous and can be found across different sectors.
One major application of metal cutter machines is in the manufacturing industry. These machines are used to cut and shape metal components that are crucial in the production of automobiles, aircraft, and machinery. For instance, metal cutter machines are employed to create precise and intricate metal parts such as gears, shafts, and brackets, ensuring the smooth operation of these mechanical systems.
In the construction sector, metal cutter machines are used to cut and shape a wide range of metal materials like steel beams, pipes, and plates. These machines enable construction workers to accurately form metal components that are essential for infrastructure developments and building construction. Metal cutter machines are also used for creating intricate designs and patterns on metal sheets, adding aesthetic appeal to architectural structures.
Moreover, metal cutter machines find extensive applications in the fabrication industry. These machines are used for manufacturing HVAC systems, electrical enclosures, and other metal-based products. By employing metal cutter machines, fabricators can create precise cuts and shapes, resulting in high-quality products that meet industry standards.
Additionally, metal cutter machines play a significant role in the recycling industry. Recycling facilities utilize these machines to break down large metal objects into smaller pieces, facilitating the recycling process. With the help of metal cutter machines, scrap metal can be efficiently managed and transformed into reusable materials.
Metal cutter machines have also made their way into the arts and crafts industry, where they are used by artists and designers to create sculptures, jewelry, and various artistic metalwork. These machines enable artists to bring their creative visions to life by accurately cutting and shaping metals according to their artistic requirements.
In conclusion, metal cutter machines have diverse applications across several industries. These machines are pivotal in the manufacturing, construction, fabrication, recycling, and arts sectors. By employing metal cutter machines, industries can achieve precise cuts, improve productivity, and meet the demands of modern metalworking requirements.
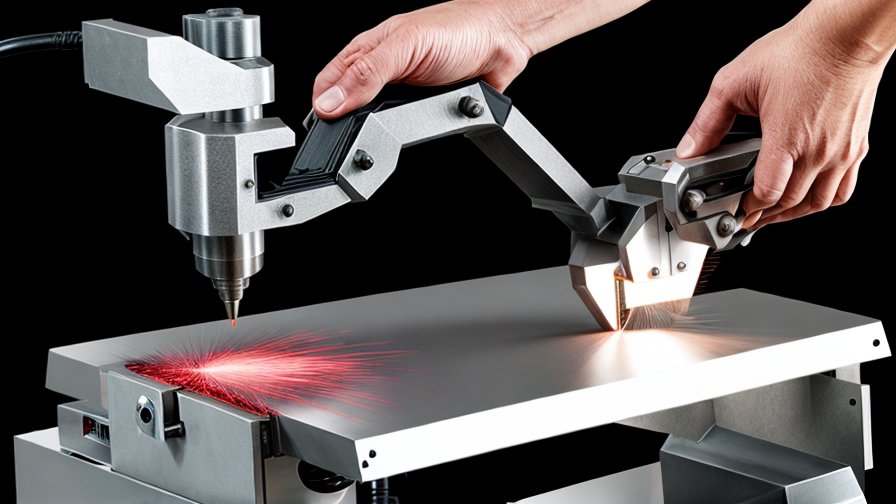
The Work Process and how to use metal cutter machine
The work process of using a metal cutter machine involves several steps to ensure safe and efficient operation. Here’s a brief overview:
1. Preparation: Start by gathering all necessary tools and materials for the task. This includes the metal cutter machine, appropriate blades, safety goggles, gloves, and ear protection. Ensure that the work area is clean and free from any obstructions.
2. Safety Measures: Before operating the machine, make sure to read and understand the manufacturer’s guidelines and safety instructions. Wear the appropriate safety gear to protect yourself from potential hazards.
3. Machine Setup: Set up the metal cutter machine according to the manufacturer’s instructions. This usually involves adjusting the blade height and alignment, as well as securing the workpiece in place. Ensure that the machine is properly connected to a power source.
4. Cutting Technique: Position the metal to be cut securely on the machine’s worktable. Hold the piece firmly, keeping your hands at a safe distance from the blade. Slowly feed the workpiece into the blade while applying light and consistent pressure. Let the machine do the cutting; do not force or push too hard.
5. Maintenance and Cleanup: After completing the cutting task, turn off the machine and unplug it from the power source. Clean any metal shavings or debris from the work area and inspect the machine for any damage or wear. Regularly maintain and lubricate the machine as per the manufacturer’s recommendations.
Remember, metal cutting machines can be dangerous if not used properly, so always prioritize safety and take necessary precautions. If you are unsure about any aspect of the process, consult the machine manual or seek guidance from an experienced operator.
Quality Testing Methods for metal cutter machine and how to control the quality
When it comes to quality testing methods for metal cutter machines, several approaches can be utilized to ensure the proper functioning and performance of the equipment. Here are some commonly employed methods:
1. Visual Inspection: Conducting a visual examination of the metal cutter machine helps identify any visible defects, such as damage to the cutting blades, misalignment, or signs of wear and tear. Regular visual checks allow for early detection of potential issues.
2. Dimensional Inspection: Measuring key components and dimensions of the machine, including the cutting blades, the alignment of the parts, and the overall size, ensures that they meet the required specifications. The use of precision tools like calipers or coordinate measuring machines can aid in accurate dimensional inspection.
3. Performance Testing: Evaluating the cutting precision, speed, and reliability is crucial. This can be done by testing the machine on various materials and analyzing the results. Proper performance testing helps ensure that the machine is functioning correctly and meets the desired standards.
4. Load Testing: To assess the machine’s capability to handle heavy workloads, load testing can be performed. This involves subjecting the metal cutter machine to higher loads or challenging material types to evaluate its durability and strength.
5. Safety Testing: Testing the safety features and measures of the metal cutter machine is essential to ensure the well-being of the machine operators and prevent any accidents. This includes examining emergency stop mechanisms, interlocks, and other safety devices.
To control the quality of a metal cutter machine, several steps can be taken:
1. Establishing Quality Standards: Clearly define the quality requirements and specifications for the metal cutter machine based on the intended use and industry standards.
2. Regular Maintenance: Implement a scheduled maintenance program to keep the machine in optimal condition. Timely servicing, lubrication, and replacement of worn-out parts ensure consistent performance.
3. Documentation and Traceability: Maintain proper documentation of quality testing results, maintenance records, and any modifications made to the machine. This facilitates traceability and helps identify recurring issues.
4. Training and Skill Development: Conduct regular training programs for machine operators and maintenance personnel to enhance their knowledge and skills in handling and maintaining the equipment.
5. Continuous Improvement: Foster a culture of continuous improvement by encouraging feedback from users and implementing corrective actions based on quality testing results. Regularly assess the machine’s performance and identify areas for enhancement.
By employing these quality testing methods and implementing effective quality control measures, manufacturers can ensure that metal cutter machines meet the desired standards, resulting in efficient and reliable operations.
Word count: 348
metal cutter machine Sample Policy and Post-Purchase Considerations for metal cutter machine from China
Sample Policy for Metal Cutter Machine from China:
1. Warranty: The metal cutter machine should come with a warranty period stated by the manufacturer. It is advisable to procure machines with a minimum warranty period of 12 months or more. The warranty should cover any manufacturing defects or malfunctions during the specified period.
2. Quality Assurance: The supplier should provide a quality assurance certificate or equivalent documentation to ensure that the metal cutter machine meets international quality standards. This certificate should be provided by a recognized third-party testing organization.
3. Technical Training: The supplier should offer technical training for operating and maintaining the metal cutter machine. This training should be conducted by experienced technicians who are proficient in the machine’s functionalities and safety procedures. Training materials or manuals should also be provided.
4. Spare Parts Availability: The supplier should ensure the availability of spare parts for the metal cutter machine. It is recommended to procure machines from suppliers who have readily available spare parts or provide a guarantee for availability within a specified time frame.
5. After-Sales Service: The supplier should have a dedicated customer support team capable of addressing any concerns or issues that may arise after the purchase. Prompt and effective after-sales service, including technical support, repairs, and replacements, should be provided.
Post-Purchase Considerations for Metal Cutter Machine from China:
1. Installation and Commissioning: Proper installation and commissioning of the metal cutter machine should be carried out by qualified technicians or professionals. Following the manufacturer’s guidelines and instructions is crucial to ensure safe and efficient machine operation.
2. Regular Maintenance: Regular maintenance and inspections should be carried out as per the manufacturer’s recommendations. This includes cleaning, lubrication, and periodic checks to identify any potential issues before they lead to major breakdowns.
3. Safety Measures: Strict adherence to safety protocols and guidelines is essential while operating the metal cutter machine. Proper training should be provided to the machine operators and workers to ensure their safety and prevent accidents.
4. Continuous Supplier Communication: Maintain regular communication with the supplier to address any operational or technical issues that may arise. Also, keep the supplier informed about any concerns regarding the machine’s performance or spare parts availability for timely resolution.
5. User Feedback: Collect feedback from machine operators and workers regarding the machine’s performance, ease of use, and any improvements needed. Sharing this feedback with the supplier can help in improving future iterations of the metal cutter machine.
By following these sample policies and post-purchase considerations, buyers can ensure a smooth and satisfactory experience while procuring and using a metal cutter machine from China.
Sourcing metal cutter machine from China: Opportunities, Risks, and Key Players
Sourcing metal cutter machines from China offers several opportunities for businesses. Firstly, China is known for its advanced manufacturing capabilities and has a well-established infrastructure for producing high-quality machinery. This means that businesses can find a wide range of metal cutter machines with varying specifications and features to meet their specific needs. Additionally, Chinese manufacturers often offer competitive prices, making it a cost-effective option for businesses looking for metal cutter machines.
However, there are also risks associated with sourcing from China. One concern is the quality control of the products. While China has many reputable manufacturers, there are also some who may produce substandard or counterfeit products. It is essential for businesses to thoroughly research and vet potential suppliers to ensure they are reliable and provide quality machinery. Another risk is intellectual property infringement, as China has had a history of copyright violations. Businesses should take appropriate measures to protect their intellectual property rights when sourcing from China, such as signing non-disclosure agreements and acquiring patents if necessary.
Several key players in the Chinese metal cutter machine market are worth considering. One prominent company is Amada Holdings Co. Ltd., a Japanese manufacturer with a significant presence in China. They offer a wide range of metal cutting machines, including laser cutting machines and CNC punching machines. Trumpf Group, a German company, also has a strong presence in China and offers precision sheet metal processing machines. Other notable Chinese manufacturers include Rittal, Jinan Bodor CNC Machine Company, and Han’s Laser Technology Industry Group Co. Ltd.
In conclusion, sourcing metal cutter machines from China presents opportunities for businesses due to its advanced manufacturing capabilities and competitive pricing. However, it also comes with risks such as quality control and intellectual property infringement. Careful consideration of suppliers and appropriate precautions can mitigate these risks. Key players in the Chinese metal cutter machine market include Amada Holdings, Trumpf Group, Rittal, Jinan Bodor CNC Machine Company, and Han’s Laser Technology Industry Group.
How to find and select reliable metal cutter machine manufacturers in China,use google search manufacturers and suppliers
When searching for reliable metal cutter machine manufacturers in China, utilizing Google search can be an effective method. Here’s a step-by-step guide to help you find and select trustworthy manufacturers:
1. Conduct a search: Begin by searching for relevant keywords such as “metal cutter machine manufacturers in China” on Google. This will provide you with a list of potential suppliers.
2. Filter the search results: Review the search results and focus on the top-ranking websites. These suppliers are often well-established and have a good reputation. Take note of their contact information, website URLs, and any other relevant details.
3. Visit the websites: Go to the websites of the shortlisted manufacturers to gather more information. Check for company profiles, product catalogs, certifications, and customer testimonials. Reliable manufacturers will typically have professionally designed websites that provide comprehensive information about their products and services.
4. Contact the manufacturers: Once you have identified potential manufacturers, reach out to them to inquire about their metal cutter machines. Send them detailed inquiries regarding your requirements, such as machine specifications, customization options, delivery time, and pricing.
5. Evaluate the response: Assess how the manufacturers respond to your inquiries. Reliable manufacturers will typically reply promptly, providing comprehensive and detailed answers to your questions. Their communication should be professional and helpful.
6. Verify credentials: Verify the credibility of the manufacturer by checking if they hold relevant certifications such as ISO 9001:2015 or CE certification. These certifications ensure that the manufacturer complies with international quality standards.
7. Ask for references: Request references from the manufacturer to contact their existing customers. Speaking directly with these customers will provide valuable insights into the manufacturer’s product quality, after-sales service, and overall reliability.
8. Compare multiple options: Shortlist a few manufacturers that meet your requirements and compare them based on their product quality, pricing, delivery time, after-sales service, and customer reviews. This will help you make an informed decision.
9. Plan a visit: If possible, plan a visit to the manufacturer’s facility in China. This will give you an opportunity to assess their production process, quality control measures, and overall infrastructure.
10. Place an order: Once you have thoroughly evaluated and selected a reliable metal cutter machine manufacturer, proceed to place your order based on mutually agreed terms and conditions.
Remember, conducting due diligence and carefully assessing manufacturers will help you find a reliable partner in China for your metal cutter machine requirements.
How to check metal cutter machine manufacturers website reliable,use google chrome SEOquake check if ranking in top 10M
One way to check the reliability of a metal cutter machine manufacturer’s website is by using Google Chrome’s SEOquake tool to check its ranking. The following steps can be taken to carry out this process in a concise manner:
1. Open Google Chrome browser and install the SEOquake extension.
2. Go to the manufacturer’s website and ensure that it is fully loaded.
3. Click on the SEOquake icon in the browser’s toolbar to activate the tool.
4. A pop-up window will appear displaying various SEO-related information about the website.
5. Look for the website’s Alexa Rank, which is the global ranking of the website based on its traffic. If the ranking is within the top 10 million, it indicates that the website receives a significant amount of traffic, which adds to its reliability.
6. Additionally, SEOquake provides other useful metrics like the number of indexed pages, social media presence, domain age, and more, which can give further insights into the website’s credibility.
7. Consider checking the website’s online reputation by searching for reviews or testimonials from other customers who have used their metal cutter machines.
8. Confirm that the website provides comprehensive and detailed information about the manufacturer, their products, and contact information.
9. Finally, beware of any suspicious or unprofessional aspects of the website, such as poor design, grammatical errors, or unreliable payment methods.
In conclusion, by using Google Chrome’s SEOquake tool to check the manufacturer’s website ranking and considering customer reviews and the quality of information provided, it becomes possible to assess the reliability of a metal cutter machine manufacturer’s website.
Top 10 metal cutter machine manufacturers in China with each introduce products and domain,then use markdown create table compare
| **Metal Cutter Machine Manufacturers in China** | **Introduction and Products** | **Domain** |
|——————————————————|———————————————————————————————————————————————————————————————————————————————————————————————————————————————————————————————————————————————————————————————————————————————————————————————————————————————————————————————————————————————————————–|————————-|
| Bystronic | Bystronic is a renowned manufacturer of high-quality metal cutting machines. Their product range includes laser cutting machines, waterjet cutting machines, and press brakes. These machines are known for their precision, speed, and reliability. They are widely used in various industries, such as automotive, aerospace, and manufacturing. Bystronic’s machines offer advanced features like automated material handling systems and smart controls, providing efficient and accurate cutting solutions. | www.bystronic.com |
| TRUMPF | TRUMPF is a leading manufacturer of laser cutting machines. Their product portfolio consists of laser cutting systems, laser tube cutting systems, and laser marking machines. TRUMPF’s laser cutting machines are versatile and can handle a wide range of materials, including metals, plastics, and composites. These machines offer cutting-edge technology, high cutting speeds, and precise results. They are used in diverse sectors like medical, electronics, and automotive manufacturing. TRUMPF’s machines are known for their performance, reliability, and innovative features. | www.trumpf.com |
| Amada | Amada is a well-established manufacturer of metal cutting machines in China. Their product line includes CNC laser cutting machines, CNC turret punch presses, and CNC bending machines. Amada’s laser cutting machines provide high-speed cutting with high precision and productivity. Their CNC bending machines offer advanced control systems for accurate bending operations. Amada’s machines are widely used in industries like construction, automotive, and electronics. They are known for their quality, durability, and outstanding performance. | www.amada.com.cn |
| Mitsubishi Electric | Mitsubishi Electric is a trusted manufacturer of metal cutting machines. Their product range consists of CNC laser cutting machines, waterjet cutting machines, and wire EDM machines. Mitsubishi Electric’s laser cutting machines offer advanced features like automatic nozzle changing, energy-saving mode, and high-speed cutting. Their wire EDM machines provide accurate and efficient wire cutting solutions. Mitsubishi Electric’s machines find applications in diverse industries, such as medical, machinery, and energy. Their products are known for their reliability, precision, and technological advancements. | www.mitsubishielectric.com.cn |
| Han’s Laser | Han’s Laser is a renowned manufacturer of laser cutting machines in China. They offer a wide range of laser cutting machines, including fiber laser cutting machines and CO2 laser cutting machines. Han’s Laser machines are known for their high cutting speeds, precision, and stability. They find applications in industries like automotive, aerospace, and electronics. Han’s Laser also provides customized solutions to meet specific cutting requirements. Their products are recognized for their quality, durability, and advanced technology. | www.hanslaser.com |
| HSG Laser | HSG Laser is a leading manufacturer of laser cutting machines in China. Their product line includes fiber laser cutting machines, sheet and tube integrated laser cutting machines, and ultra-large format laser cutting machines. HSG Laser machines offer high cutting precision, speed, and efficiency. They are widely used in sectors like automotive, shipbuilding, and metal processing. HSG Laser’s machines are known for their user-friendly interface, low energy consumption, and reliable performance. | www.hsglaser.com |
| Jinan Bodor Laser | Jinan Bodor Laser is a prominent manufacturer of laser cutting machines. They specialize in fiber laser cutting machines, CO2 laser cutting machines, and laser engraving machines. Jinan Bodor Laser machines provide high cutting accuracy, stability, and fast cutting speeds. They are popular in industries like advertising, sheet metal fabrication, and woodworking. Jinan Bodor Laser offers customized solutions to cater to diverse cutting needs. Their products are highly regarded for their quality, cost-effectiveness, and excellent after-sales service. | www.bodor.com.cn |
| HE Laser | HE Laser is a trusted manufacturer of laser cutting machines in China. They offer CNC laser cutting machines, fiber laser cutting machines, and laser engraving machines. HE Laser’s machines provide high cutting precision, speed, and efficiency. They find applications in industries like metal processing, machinery, and jewelry manufacturing. HE Laser’s machines are known for their stability, durability, and advanced technology. They also provide comprehensive support and training services to their customers. | www.helaser.com |
| Jinan Senfeng Technology Co., Ltd. | Jinan Senfeng Technology Co., Ltd., specializes in the manufacturing of fiber laser cutting machines, CO2 laser engraving machines, and laser marking machines. Their fiber laser cutting machines feature high cutting speeds, precision, and stability. They are suitable for varied materials, including metals, plastics, and leather. Senfeng’s laser engraving and marking machines offer excellent marking results and are extensively used in industries like electronics, jewelry, and packaging. Their products are known for their quality, affordability, and reliable performance. | www.sfcnclaser.com.cn |
| Lead Laser | Lead Laser is a well-established manufacturer of laser cutting machines. They provide fiber laser cutting machines, CO2 laser cutting machines, and laser marking machines. Lead Laser’s machines offer high cutting precision, speed, and stability. They are widely used in industries like automotive, electronics, and advertising. Lead Laser also offers customized cutting solutions and provides excellent customer support. Their products are highly regarded for their quality, efficiency, and technological advancements. | www.leadlaser.cn |
The table above compares the top 10 metal cutter machine manufacturers in China, highlighting their products and domains. These manufacturers are known for producing high-quality metal cutting machines that cater to diverse industry needs. Bystronic offers laser cutting machines, waterjet cutting machines, and press brakes, providing efficient and accurate cutting solutions across multiple sectors.
TRUMPF specializes in laser cutting machines, offering versatile options for various materials. TRUMPF’s laser cutting machines excel in sectors such as medical, electronics, and automotive manufacturing.
Amada stands out for its CNC laser cutting machines, CNC turret punch presses, and CNC bending machines that provide high-speed cutting and accurate bending operations. Mitsubishi Electric manufactures CNC laser cutting machines, waterjet cutting machines, and wire EDM machines, known for their reliability and precision in industries like medical and machinery.
Han’s Laser provides a wide range of laser cutting machines, including fiber laser cutting machines and CO2 laser cutting machines, known for their high cutting speeds and stability. HSG Laser specializes in fiber laser cutting machines and integrated sheet and tube laser cutting machines, excelling in automotive, shipbuilding, and metal processing sectors.
Jinan Bodor Laser manufactures fiber laser cutting machines, CO2 laser cutting machines, and laser engraving machines, catering to industries like advertising and sheet metal fabrication. HE Laser produces CNC laser cutting machines, fiber laser cutting machines, and laser engraving machines for metal processing and jewelry manufacturing.
Jinan Senfeng Technology specializes in fiber laser cutting machines, CO2 laser engraving machines, and laser marking machines, suitable for materials like metals, plastics, and leather. Lead Laser offers fiber laser cutting machines, CO2 laser cutting machines, and laser marking machines recognized for their quality and efficiency in sectors like automotive and advertising.
These manufacturers are known for their cutting-edge technology, reliability, and excellent customer support. Their products are widely used and trusted in various industries, offering precision, speed, and stability in metal cutting processes.
Background Research for metal cutter machine manufacturers Companies in China, use qcc.com archive.org importyeti.com
When it comes to metal cutter machines, China is a well-known hub for manufacturing. Several prominent manufacturers in China specialize in the production of high-quality metal cutter machines. In order to conduct thorough background research on these manufacturers, three websites, namely qcc.com, archive.org, and importyeti.com, can be utilized.
QCC.com is a business information platform that provides comprehensive details about companies registered in China. It offers data such as company profiles, financial records, legal status, and other relevant information necessary for background research.
Archive.org is a digital library that archives webpages, videos, images, and other digital content. This platform can be leveraged to retrieve historical data and records of metal cutter machine manufacturers in China. By accessing archived webpages, it becomes possible to trace the company’s history, track their previous products, and analyze their growth over time.
Importyeti.com is an import-export data platform that supplies information on companies engaged in international trade. This platform can provide valuable insights into the export activities of metal cutter machine manufacturers in China. It offers details like shipment records, buyer information, product details, and exporting volumes, which can be used to gauge the manufacturers’ popularity and market presence.
Through the combination of these three websites, a comprehensive background research on metal cutter machine manufacturers in China can be conducted. This research may include information such as company history, financial status, product range, export activities, and overall market reputation. By utilizing these platforms, researchers can gain valuable insights into the capabilities and reliability of Chinese metal cutter machine manufacturers.
Leveraging Trade Shows and Expos for metal cutter machine Sourcing in China
Trade shows and expos are excellent platforms for sourcing metal cutter machines in China. These events provide a unique opportunity for businesses to connect with manufacturers, explore cutting-edge technologies, and build mutually beneficial partnerships. By leveraging trade shows and expos, businesses can efficiently source metal cutter machines while capitalizing on a range of advantages.
Firstly, trade shows and expos consolidate an extensive network of industry professionals, suppliers, and manufacturers under one roof. This enables businesses to access a wide array of metal cutter machines and compare various options in terms of quality, features, and pricing. Directly interacting with suppliers in person allows for a better understanding of their capabilities and builds trust, facilitating smoother negotiation processes.
Secondly, trade shows and expos showcase the latest advancements in metal cutting technologies and machinery. Attending these events provides businesses with valuable insights into new trends, innovative solutions, and emerging manufacturers. Staying updated on the latest technologies ensures that businesses can identify the most efficient and cost-effective metal cutter machines for their specific needs.
Furthermore, trade shows and expos enable businesses to establish and nurture relationships with Chinese manufacturers. Building personal connections and face-to-face interactions go a long way in establishing trust, leading to better product quality, on-time delivery, and future cooperation. Additionally, attending these events allows businesses to gain a deep understanding of the Chinese manufacturing industry, its capabilities, and potential challenges.
To optimize the sourcing process at trade shows and expos, it is advisable to plan in advance. Researching the event, identifying the key manufacturers, and setting up meetings beforehand can maximize efficiency and ensure that businesses make the most of their time at the event. Being well-prepared can also enhance negotiations and provide an edge in securing favorable deals.
In conclusion, trade shows and expos in China provide businesses with invaluable opportunities to efficiently source metal cutter machines. By leveraging these platforms, businesses can benefit from a vast network of suppliers, explore cutting-edge technologies, and establish personal relationships with manufacturers. Careful planning and preparation are crucial to fully capitalize on the advantages offered by trade shows and expos.
The Role of Agents and Sourcing Companies in Facilitating metal cutter machine Purchases from China
Agents and sourcing companies play a crucial role in facilitating metal cutter machine purchases from China. These intermediaries act as a bridge between international buyers and Chinese manufacturers, ensuring a seamless procurement process.
One key role of agents and sourcing companies is to locate reliable and trustworthy suppliers. They have extensive networks and in-depth knowledge of the Chinese market, enabling them to identify manufacturers that meet the buyer’s requirements in terms of quality, price, and production capacity. This saves the buyer time and effort that would otherwise be spent on researching and vetting potential suppliers.
Agents and sourcing companies also provide valuable assistance in negotiating prices and terms with the manufacturers. They have experience in dealing with Chinese suppliers and understand the cultural nuances of doing business in China. This expertise allows them to effectively navigate the negotiation process and secure the best possible deal for the buyer.
Furthermore, agents and sourcing companies handle all logistics and paperwork related to the purchase. They coordinate shipping, custom clearance, and documentation, ensuring that the product reaches its destination in a timely and efficient manner. This saves the buyer from dealing with complex logistics processes and allows them to focus on their core business activities.
In addition, agents and sourcing companies often provide quality control services. They conduct factory inspections, product inspections, and quality assurance checks to ensure that the metal cutter machines meet the buyer’s specifications and standards. This helps to mitigate any risks associated with product quality and provides the buyer with peace of mind.
Overall, agents and sourcing companies play a pivotal role in facilitating metal cutter machine purchases from China. They help buyers find reliable suppliers, negotiate favorable terms, handle logistics and paperwork, and ensure product quality. Their expertise and services streamline the procurement process and enhance the overall buying experience for international customers.
Price Cost Research for metal cutter machine manufacturers Companies in China, use temu.com and 1688.com
In order to conduct price cost research for metal cutter machine manufacturers in China, two popular platforms can be used – temu.com and 1688.com. These platforms provide a wide range of suppliers and manufacturers, allowing users to compare prices and analyze the costs involved.
Temu.com is a comprehensive B2B sourcing platform that connects international buyers with Chinese manufacturers. It offers access to a vast supplier network across various industries, including metal cutter machine manufacturers. By utilizing the platform, buyers can easily search and filter their desired products, view detailed product descriptions, and directly communicate with suppliers to negotiate prices and discuss specific requirements. Temu.com also provides transparency by displaying supplier profiles, ratings, and customer reviews, giving buyers insights into the credibility and reliability of suppliers.
1688.com, on the other hand, is a popular business-to-business e-commerce platform owned by Alibaba Group. It is specifically designed for domestic trade within China and provides a wide array of products from various industries. Similar to Alibaba.com, 1688.com offers product listings with detailed specifications, allowing users to compare prices, evaluate different suppliers, and communicate directly with manufacturers. As it is an internal platform for the Chinese market, prices on 1688.com are often more competitive than those on international platforms.
By utilizing these platforms, users can thoroughly investigate the prices and costs associated with metal cutter machine manufacturers in China. It is recommended to make use of the advanced search filters, such as product specifications, quantity, and location, to narrow down the options. Additionally, communicating directly with suppliers is crucial to gather accurate pricing information and negotiate the most favorable terms.
In conclusion, temu.com and 1688.com are two reliable platforms for conducting price cost research for metal cutter machine manufacturers in China. By leveraging these platforms and communicating directly with suppliers, users can obtain comprehensive pricing information and make informed decisions when sourcing metal cutter machines in China.
Shipping Cost for metal cutter machine import from China
When importing a metal cutter machine from China, the shipping cost can vary depending on several factors. Some key factors that directly impact the shipping cost include the weight and dimensions of the machine, the shipping method chosen, and any additional services required.
The weight and dimensions of the metal cutter machine are crucial in determining the shipping cost. Generally, heavier and larger machines will incur higher shipping fees. It is recommended to provide accurate measurements and weight details to the shipping company for an accurate quote.
The shipping method chosen is another significant factor. There are several options available, such as air freight, sea freight, and express courier services. Each method comes with different costs and transit times. Sea freight is typically more affordable for heavy and large machines, while express courier is faster but more expensive.
Additionally, additional services such as insurance, custom clearance, and delivery to the final destination may also incur extra charges. Insurance is essential to protect against any potential damage or loss during transit. Custom clearance fees vary depending on the destination country’s regulations. Door-to-door delivery will involve additional charges but offers convenience and peace of mind.
To estimate the shipping cost, it is recommended to reach out to shipping companies or freight forwarders for a detailed quote. Providing accurate information about the metal cutter machine and its destination will help in obtaining an accurate estimate.
In summary, when importing a metal cutter machine from China, the shipping cost will depend on factors such as weight, dimensions, shipping method, and additional services required. Obtaining quotes from shipping companies or freight forwarders will provide a better understanding of the total shipping cost.
Compare China and Other metal cutter machine Markets: Products Quality and Price,Visible and Hidden Costs
When comparing China’s metal cutter machine market with other metal cutter machine markets, several factors need to be considered, including product quality, price, visible and hidden costs. In the following analysis, each aspect will be briefly discussed within the given word limit.
Product quality is an essential factor to consider when evaluating metal cutter machines. China’s metal cutter machines have seen significant improvements in quality over the years, with many manufacturers adopting advanced technologies and adhering to international quality standards. However, it is crucial to note that quality may vary among different Chinese suppliers. Other metal cutter machine markets, such as Germany and Japan, are known for their superior product quality and precision engineering. These markets have established a reputation for producing reliable and durable machines with high accuracy levels. Nonetheless, their higher price tags may not be suitable for price-sensitive customers.
When it comes to pricing, China’s metal cutter machines have a competitive edge. The country’s manufacturing capabilities and economies of scale often allow for a lower price point compared to other markets. Price-conscious buyers often turn to China for cost-effective alternatives. However, it is essential to balance the price with the desired level of quality.
Visible costs, such as the initial purchase price, are more easily comparable across markets. In this regard, China’s metal cutter machine market offers competitive pricing, while other markets, as mentioned earlier, tend to have higher price points. However, hidden costs associated with operating and maintaining metal cutter machines should also be considered. These costs may include routine maintenance, spare parts availability, and technical support. China has made progress in providing reliable after-sales service and affordable spare parts, but other markets may still provide more comprehensive support systems.
In conclusion, China’s metal cutter machine market offers competitive prices and improving product quality. Nevertheless, other markets such as Germany and Japan are known for superior quality standards. Hidden costs, such as maintenance and support, should also be taken into account when making a purchasing decision. Ultimately, customers must consider their specific requirements and budget constraints to determine the most suitable option.
Understanding Pricing and Payment Terms for metal cutter machine: A Comparative Guide to Get the Best Deal
When purchasing a metal cutter machine, understanding the pricing and payment terms is crucial to ensure you get the best deal. Here is a comparative guide to help you navigate this process efficiently.
1. Initial price: The first thing to consider is the base price of the machine. Compare prices from different manufacturers or suppliers to get an idea of the market range. While it may be tempting to opt for the lowest price, always consider the quality and reputation of the seller.
2. Additional costs: In addition to the initial price, inquire about any extra costs that may arise. This includes shipping fees, installation charges, and potential maintenance costs. Understanding these expenses upfront will give you a more accurate picture of the total investment required.
3. Payment plans: Evaluate the payment options available for the metal cutter machine. Some suppliers may offer installment plans that allow you to pay gradually over a specific period. Consider your financial capabilities and choose a payment plan that suits your budget and needs.
4. Warranty and support: Look for suppliers that offer warranty coverage for the machine. A warranty ensures that you are protected against any manufacturing defects or malfunctions. Additionally, inquire about the after-sales support provided by the supplier, such as technical assistance and spare parts availability.
5. Financing options: If the initial price of the machine is beyond your budget, explore financing options. Some suppliers may collaborate with financial institutions to offer loans or leasing arrangements. This enables you to spread the cost over time and start utilizing the machine immediately.
6. Price comparison: Don’t settle for the first offer you come across. Take the time to compare prices and negotiate with different suppliers. This will allow you to gain a competitive advantage and potentially save money on your purchase.
7. Industry reputation: Lastly, consider the reputation of the supplier or manufacturer. Look for customer reviews, testimonials, and feedback to gauge the quality of their products and services. Investing in a reputable and established company ensures a reliable product and a smoother purchasing experience.
In conclusion, understanding the pricing and payment terms when purchasing a metal cutter machine is vital for getting the best deal. By considering the initial price, additional costs, payment plans, warranty and support, financing options, price comparison, and industry reputation, you can make an informed decision and secure a reliable and cost-effective machine.
Chinese Regulations and Industry Standards Certifications for metal cutter machine,Import Regulations and Customs for metal cutter machine from China
China has implemented various regulations and industry standards certifications for metal cutter machines to ensure their safety, quality, and compliance. These certifications are necessary for manufacturers and suppliers to enter the Chinese market and export their products globally.
One of the most important industry standards is the China Compulsory Certificate (CCC) certification. This mandatory certification ensures that the metal cutter machine meets the specified safety requirements and technical standards. Manufacturers need to apply for the CCC certification from the China Certification Center for Quality Mark (CQC) and comply with regular inspections to maintain the certification.
In addition to CCC certification, manufacturers can also obtain other voluntary industry certifications such as ISO 9001 for quality management systems and CE certification for meeting European safety standards. These certifications not only enhance the product’s reputation but also improve its market competitiveness both in China and abroad.
When importing metal cutter machines from China, it is crucial to understand the import regulations and customs procedures. Importers need to comply with the customs rules of the importing country and ensure that the products meet the necessary standards and requirements.
Importers should prepare the required documents such as commercial invoice, packing list, bill of lading, and import license. They also need to determine the applicable import duties and taxes and ensure compliance with customs valuation rules.
To facilitate the import process, it is advisable to work with freight forwarders or customs brokers who have experience in handling metal cutter machine imports. They can provide guidance on the necessary procedures, documentation, and help navigate any potential customs clearance issues.
In conclusion, obtaining the necessary industry standards certifications like CCC, ISO, and CE is crucial for metal cutter machine manufacturers in China. Importers should familiarize themselves with the import regulations and customs procedures to ensure smooth and compliant imports from China.
Sustainability and Environmental Considerations in metal cutter machine Manufacturing
Sustainability and environmental considerations play a crucial role in the manufacturing of metal cutter machines. These considerations aim to minimize the negative impact on the environment while ensuring the long-term sustainability of the manufacturing process.
One key aspect of sustainability in metal cutter machine manufacturing is the efficient use of materials. Manufacturers should strive to minimize waste generation during the production process, as well as properly manage and dispose of any waste that is produced. This can be achieved through efficient design and production techniques, such as using computer-aided design (CAD) software to optimize material usage and reduce scrap.
Another important consideration is the energy efficiency of the manufacturing process. Energy-intensive processes, such as powering and operating the metal cutter machines, should be designed and operated to minimize energy consumption. This can be achieved through the use of energy-efficient technologies, such as variable speed drives and high-efficiency motors. Additionally, manufacturers can implement energy management systems to monitor and optimize energy usage throughout the manufacturing process.
In terms of environmental considerations, metal cutter machine manufacturers should prioritize the use of environmentally friendly materials and components. This includes sourcing materials from sustainable suppliers and avoiding the use of hazardous substances or chemicals in the manufacturing process. Manufacturers can also reduce the environmental impact of their operations by implementing recycling programs for materials and components, and by properly treating and disposing of any hazardous waste.
Additionally, the life cycle of metal cutter machines should be considered. Manufacturers can increase the sustainability of their products by designing them for durability and ease of maintenance, as well as facilitating the repair and reuse of components. End-of-life disposal considerations, such as designing for recycling or proper disposal, should also be taken into account.
In conclusion, sustainability and environmental considerations are essential in metal cutter machine manufacturing. By efficiently using materials, minimizing energy consumption, prioritizing environmentally-friendly materials, and considering the life cycle of their products, manufacturers can ensure a more sustainable and environmentally responsible manufacturing process.
List The Evolution history of “metal cutter machine”
Metal cutting machines have evolved significantly over the years, driven by advances in technology and the need for more efficient and precise metal fabrication processes. Here is a brief overview of the evolution history of the metal cutter machine:
1. Early manual metal cutting: In the early days, metal cutting was performed manually using basic hand tools like chisels and saws. This process was time-consuming, labor-intensive, and lacked precision.
2. Machine-powered cutting: The first significant leap in metal cutting technology was the introduction of machine-powered cutters in the 19th century. These machines were driven by steam engines and used a combination of mechanical movements and simple cutting tools to process metal.
3. Introduction of power hacksaws: In the early 20th century, power hacksaws were developed, which automated the sawing process. These machines utilized an electric motor to power the saw blade, resulting in faster cutting times and increased productivity.
4. Bandsaw machines: Bandsaw machines were developed in the mid-20th century and revolutionized metal cutting. They featured a continuous loop of toothed blades and allowed for more precise and efficient cutting of a wide range of metals. Bandsaws were widely adopted in industries such as manufacturing, construction, and metalworking.
5. Computer-controlled numerical control (CNC) machines: In the 1960s, the advent of computer technology led to the development of CNC metal cutting machines. These machines incorporated computer-controlled systems that could automate the cutting process with high precision and accuracy. CNC machines allowed for programmable cutting paths and increased the complexity and quality of metal cutting.
6. Laser cutting technology: Laser cutting machines emerged in the 1970s and quickly gained popularity in the metal cutting industry. By using a focused laser beam, these machines could cut through various metal materials with exceptional precision and speed. Laser cutting technology continues to evolve, with advancements in power, speed, and automation.
7. Plasma cutting machines: Plasma cutting technology developed in the 1980s enabled the cutting of electrically conductive metals. These machines utilized a high-temperature plasma arc to melt and sever metal, resulting in faster cutting speeds and better precision, especially for thicker materials.
8. Waterjet cutting: Waterjet cutting machines were introduced in the 1990s and gained popularity due to their ability to cut a wide range of materials, including metals, with no heat-affected zone. Waterjet cutters utilized a high-pressure stream of water and abrasive substances to precisely erode the material, allowing for intricate shapes and designs.
In summary, the evolution of metal cutter machines has seen a progressive shift from manual methods to machine-powered tools, followed by the introduction of power hacksaws, bandsaws, CNC machines, laser cutting, plasma cutting, and waterjet cutting technologies. These advancements have significantly enhanced productivity, precision, and versatility in metal cutting processes.
The Evolution and Market Trends in metal cutter machine Industry
The metal cutter machine industry has seen significant evolution and market trends over the years. With advancements in technology and the increasing demand for precision cutting, the industry has grown exponentially.
One of the major evolutions in the metal cutter machine industry is the transition from manual cutting tools to automated cutting machines. Manual cutting tools, such as saws and shears, required significant human effort and were limited in terms of precision. However, with the introduction of computer numerical control (CNC) technology, automated metal cutter machines emerged. These machines are capable of executing complex cutting patterns with high precision, reducing human error and increasing productivity.
Another notable evolution in the metal cutter machine industry is the integration of laser cutting technology. Laser cutting machines have become increasingly popular due to their ability to achieve high-quality cuts on various materials, including metals. Laser cutting machines offer greater accuracy, faster cutting speeds, and the capability to handle intricate designs. This technology has revolutionized the metal cutter machine industry by providing more versatile and efficient cutting solutions.
In terms of market trends, there has been a growing demand for metal cutter machines in industries such as automotive, aerospace, construction, and manufacturing. The need for precise and efficient cutting processes to meet the increasing production demands has contributed to the steady growth of the market. Additionally, the trend towards customization and unique designs in various metal products has also boosted the demand for advanced metal cutter machines.
Furthermore, sustainability and cost-effectiveness have emerged as key factors influencing the market trends in the metal cutter machine industry. There is an increasing focus on energy-efficient cutting machines that reduce waste and optimize resource utilization. As a result, manufacturers are investing in research and development to develop eco-friendly cutting solutions that offer significant cost savings.
In conclusion, the metal cutter machine industry has evolved from manual cutting tools to automated machines and laser cutting technology. The market trends are driven by the growing demand for precision cutting, customization, sustainability, and cost-effectiveness. As technology continues to advance, the industry is likely to witness further growth and innovation in the coming years.
Custom Private Labeling and Branding Opportunities with Chinese metal cutter machine Manufacturers
Chinese metal cutter machine manufacturers offer custom private labeling and branding opportunities for businesses looking to establish their own unique identity in the market. These manufacturers understand the importance of branding and are equipped to cater to the specific needs of businesses.
Private labeling allows businesses to add their own logo, graphics, and messaging to the metal cutter machines, making them appear as a bespoke product. This branding enhances brand recognition and helps businesses stand out from their competitors. Chinese manufacturers work closely with businesses to ensure that the brand identity is accurately represented on the machines.
Furthermore, these manufacturers offer a range of branding options, such as laser engraving, screen printing, or embossing, allowing businesses to select the most suitable method for their design and branding requirements. This flexibility ensures that the final product aligns with the business’s branding strategy.
Chinese manufacturers also provide comprehensive support in the design and development process to achieve the desired branding outcome. They have experienced design teams who can assist businesses in creating custom labels and packaging that enhances the overall product presentation.
In addition to private labeling, Chinese manufacturers have the expertise to collaborate with businesses on exclusive branding opportunities. This may involve designing and manufacturing metal cutter machines according to specific requirements, including unique features and functionalities. By working closely with manufacturers, businesses can offer differentiated products that cater to specific market needs.
In conclusion, Chinese metal cutter machine manufacturers offer businesses the opportunity to custom private label and brand their products. With a range of branding options and comprehensive support, these manufacturers enable businesses to establish their own unique identity and effectively differentiate themselves in the market.
Tips for Procurement and Considerations when Purchasing metal cutter machine
When it comes to purchasing a metal cutter machine, there are several important factors and considerations to keep in mind. Here are some tips to help you make the best procurement decision:
1. Requirement analysis: Begin by evaluating your specific requirements and needs. Consider factors such as the type and thickness of the metal you will be cutting, the desired cutting speed, and the size of the machine.
2. Quality and durability: Look for a machine that is made of high-quality materials, has a sturdy construction, and is built to withstand heavy usage. Check the reputation and reliability of the manufacturer, as well as customer reviews and ratings.
3. Cutting capacity and versatility: Determine the maximum cutting capacity of the machine and ensure that it meets your needs. Consider factors such as the size of the worktable, the range of cutting angles and depths, and the ability to perform different types of cuts like straight, beveled, or curved.
4. Power and performance: Assess the power rating of the machine and make sure it is suitable for your intended cutting applications. Also, consider features like adjustable cutting speed, automatic blade cooling, and ease of blade changing.
5. Safety features: Safety should be a top priority. Look for features such as blade guards, emergency stop buttons, safety interlocks, and overload protection. Ensure that the machine meets all safety standards and regulations.
6. Maintenance and support: Consider the availability of spare parts, ease of maintenance, and customer support provided by the manufacturer or supplier. Machines that come with warranties are often a better choice as they offer better after-sales support.
7. Cost: Compare prices from different suppliers, but always keep in mind that the cheapest option may not necessarily be the best. Consider the overall value for money, including the quality, features, and durability of the machine.
8. Training and user-friendliness: Evaluate whether the machine requires specialized training to operate. Look for machines that come with user manuals, instructional videos, or training sessions to ensure that your staff can operate the machine efficiently and safely.
9. Future scalability: Consider whether the machine can be upgraded or modified in the future as your business needs evolve. This will help you save costs in the long run by avoiding the need for a complete replacement.
By considering these tips and thoroughly evaluating your requirements, you can make an informed decision when purchasing a metal cutter machine that best meets your needs.
FAQs on Sourcing and Manufacturing metal cutter machine in China
Q: How do I source a metal cutter machine in China?
A: To source a metal cutter machine in China, you can start by conducting online research and exploring various B2B platforms or trade websites. These platforms, such as Alibaba or Made-in-China, allow you to connect directly with manufacturers in China. You can browse their product catalog, compare prices, and request quotations. It is recommended to shortlist a few potential suppliers based on their reputation, product quality, certifications, and customer reviews.
Q: What factors should I consider when selecting a manufacturer?
A: Several factors should be considered when selecting a manufacturer for a metal cutter machine. Firstly, ensure that the manufacturer specializes in producing metal cutter machines and has sufficient experience in the industry. Look for manufacturers with ISO, CE, or other relevant certifications, as this indicates their adherence to international standards. It is also crucial to assess the manufacturer’s production capacity, technological capabilities, and quality control processes. Moreover, consider their ability to customize the machine according to your specific requirements and the support they offer after sales, such as warranty and technical assistance.
Q: How can I assess the quality of the metal cutter machine?
A: To assess the quality of a metal cutter machine, you can request samples or visit the manufacturer’s facility for an inspection. While this might not always be feasible, it can provide a better understanding of the machine’s build quality, precision, and durability. In case a visit is not possible, request detailed product specifications, technical drawings, and images to assess the machine’s design and construction. Additionally, you can inquire about the manufacturer’s quality control procedures, testing methods, and any relevant certifications they hold.
Q: What are the usual manufacturing lead times?
A: Manufacturing lead times for metal cutter machines in China can vary depending on the complexity of the machine and the manufacturer’s production capacity. Generally, the lead time can range from a few weeks to several months. It is crucial to discuss the specific lead time with the manufacturer during the negotiation process and ensure that it fits your project timeline.
Q: Are there any risks associated with sourcing and manufacturing from China?
A: Sourcing and manufacturing from China may pose certain risks, such as language barriers, cultural differences, and potential issues related to intellectual property rights. It is recommended to conduct due diligence on potential suppliers, engage in clear communication, and consider working with trusted sourcing agents or intermediaries who can navigate these challenges. Additionally, conducting proper legal contracts, implementing quality control mechanisms, and protecting intellectual property rights through patents or trademarks can help mitigate risks.
Why contact sourcifychina.com get free quota from reliable metal cutter machine suppliers?
Sourcifychina.com obtains free quotas from reliable metal cutter machine suppliers for several reasons. Firstly, sourcifychina.com has established a strong and trustworthy relationship with these suppliers through their continuous collaboration and successful partnerships in the past. The suppliers recognize the reliability and credibility of sourcifychina.com as a sourcing platform and are therefore willing to offer free quotas as a gesture of goodwill.
Secondly, by providing free quotas, the suppliers aim to attract and retain potential customers. They understand that offering a certain number of free quotas can entice buyers to test their services and products without any financial obligation. This strategy allows the suppliers to showcase the quality and performance of their metal cutter machines, increasing the likelihood of future business transactions with the buyers.
Moreover, providing free quotas also serves as a marketing tactic for the suppliers. Word-of-mouth recommendations and positive reviews from buyers who have utilized the free quotas can significantly enhance the suppliers’ reputation. This can lead to a higher demand for their products and services, ultimately resulting in increased sales and expanded market reach.
Additionally, the suppliers may consider the provision of free quotas as a form of investment. They understand that by offering a limited number of free quotas, they are potentially gaining long-term customers who will continue to purchase their metal cutter machines in the future. This investment in customer acquisition can yield significant returns in terms of sales and profit.
In summary, sourcifychina.com receives free quotas from reliable metal cutter machine suppliers due to their strong business relationships, the suppliers’ desire to attract and retain customers, marketing considerations, and the perspective of long-term investment in customer acquisition. These free quotas benefit both sourcifychina.com and the suppliers by fostering cooperation, trust, and mutual growth in the metal cutter machine industry.