Introduce about cnc lathe machining guide,Qulity,Cost,Supplier,Certification,Market,Tips,FAQ
CNC lathe machining is a process that involves using computer numerical control (CNC) technology to operate a lathe machine with high precision and accuracy. It is widely used in the manufacturing industry for producing complex parts and components.
Quality is an essential aspect of CNC lathe machining. The use of advanced CNC technology ensures consistent and precise results, minimizing the chances of errors or defects in the final products. Quality control measures, such as regular maintenance and calibration of machines, are essential to ensure optimal performance.
Cost is another crucial factor in CNC lathe machining. The initial investment in CNC machines and related software can be significant. However, the automation and efficiency offered by CNC technology reduce labor costs and increase productivity, resulting in long-term cost savings for manufacturers.
Choosing the right supplier for CNC lathe machining is crucial to achieving high-quality results. A reliable supplier should have a track record of delivering precision machining services, a skilled workforce, and state-of-the-art equipment. Conducting research, reading customer reviews, and requesting samples can help evaluate the supplier’s capabilities.
Certification, such as ISO 9001, is an important factor to consider when selecting a CNC lathe machining supplier. Certification ensures that the supplier follows international standards for quality management systems, ensuring consistent and reliable production processes.
The market for CNC lathe machining is growing rapidly, driven by the increasing demand for precision parts across various industries such as automotive, aerospace, medical, and electronics. The ability to produce complex shapes and achieve tight tolerances makes CNC lathe machining a preferred choice for manufacturers in these sectors.
Here are some tips to enhance CNC lathe machining operations:
1. Regularly maintain and calibrate machines to ensure optimal performance.
2. Use high-quality cutting tools and materials to achieve better results.
3. Optimize cutting parameters and tool paths to improve efficiency.
4. Monitor and control temperatures to avoid thermal expansion and contraction.
In the FAQ section, common inquiries may include queries about the capabilities of CNC lathe machining, the materials that can be processed, turnaround times, and pricing structure.
To summarize, CNC lathe machining is a highly precise and efficient manufacturing process. When selecting a supplier, consider their quality, cost, certifications, and reputation. Stay updated with market trends, and follow the provided tips to optimize CNC lathe machining operations.
Types of cnc lathe machining
CNC lathe machining refers to the process of utilizing computer numerical control (CNC) technology to control and automate the operation of a lathe machine. This technology allows for precise and efficient fabrication of various parts and components. There are several types of CNC lathe machining that cater to different manufacturing requirements.
1. Turning: Turning is the most basic and commonly used type of CNC lathe machining. It involves rotating a workpiece while a cutting tool is traversed along the axis parallel to the workpiece rotation. This process is ideal for producing cylindrical parts, such as shafts, pins, and bushings.
2. Facing: Facing is another common type of CNC lathe machining, which involves removing material from the end surface of a workpiece to create a flat and smooth face. It is commonly used to produce squared or flat surfaces of parts.
3. Drilling: CNC lathes can also be used for drilling operations. Drilling involves creating holes in a workpiece through a rotating cutting tool. This process is crucial for producing parts that require precise and accurate holes, such as engine components or electronic enclosures.
4. Tapping: Tapping is a process used to create screw threads within holes. CNC lathes can be programmed to perform tapping operations, enabling the creation of threaded parts.
5. Chamfering: Chamfering involves removing sharp edges or bevelling the edges of a workpiece. CNC lathes can be programmed to perform chamfering operations, which are essential for reducing the risk of injuries caused by sharp edges and improving the aesthetic appearance of parts.
6. Knurling: Knurling is a process used to create a textured pattern on the surface of a workpiece. It can be used to improve grip or enhance aesthetics. CNC lathes can be programmed to perform knurling operations, producing precise and consistent patterns.
7. Grooving: Grooving involves cutting grooves into the surface of a workpiece. Grooves can serve various purposes, such as facilitating the installation of O-rings or improving the performance of a part. CNC lathes can be programmed to perform grooving operations with high accuracy and repeatability.
These are just a few examples of the various types of CNC lathe machining operations. The versatility and precision of CNC lathe machines make them an essential tool in modern manufacturing industries, allowing for efficient and reliable production of a wide range of products.
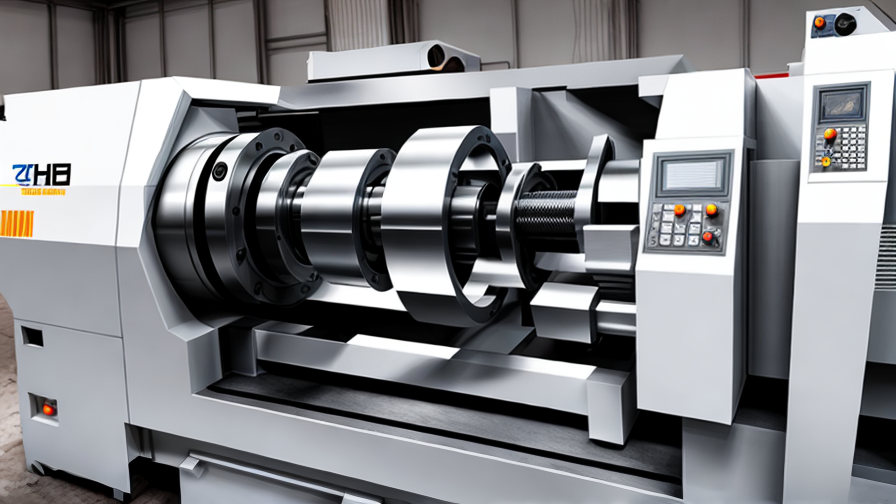
Pros and Cons of Using cnc lathe machining
CNC lathe machining, also known as computer numerical control lathe machining, is a manufacturing process in which computer software controls the movement and operation of a lathe machine. This technology offers several advantages and disadvantages, which are as follows.
Pros:
1. Precision: CNC lathe machining eliminates the possibility of human error and ensures high levels of precision and accuracy in producing intricate details and dimensions. It can consistently create identical parts, reducing the risk of variation or deviation.
2. Efficiency: CNC lathes can automate the entire machining process, which eliminates the need for manual labor and increases the production speed significantly. This improves overall efficiency and reduces costs associated with labor and time.
3. Flexibility: CNC lathes can easily switch between different parts and designs, making them highly versatile. They can handle various materials, sizes, and complex shapes, enabling manufacturers to explore a wider range of possibilities.
4. Cost-effectiveness: While CNC lathe machines may require a significant initial investment, they offer long-term cost benefits. Their automation reduces the need for manual intervention, leading to labor cost savings. Additionally, their precision reduces material waste, making the process more economical.
5. Better quality control: With CNC lathe machining, manufacturers can closely monitor and control the production process. Parameters such as speed, feed, and depth of cut can be precisely programmed, leading to better quality control and fewer defective products.
Cons:
1. Initial investment: Installing and setting up a CNC lathe machine requires a substantial investment. The cost includes not only the machine itself but also training, software, and maintenance expenses. Small businesses or startups may find it challenging to afford such an investment.
2. Maintenance and repair: CNC lathe machines require regular maintenance to ensure optimal performance. Any breakdown or malfunctioning of the machine can disrupt the entire production process, resulting in downtime and additional repair costs.
3. Skilled operators: Operating a CNC lathe machine requires specific skills and knowledge of computer programming and machining techniques. It may take time and effort to train operators to efficiently utilize the machinery, and hiring skilled operators can add to labor costs.
4. Limited adaptability: CNC lathe machines may not be suitable for handling unconventional shapes or non-standard materials. The machines have limitations in terms of the size and shape of the parts they can produce. Additionally, they may not be as effective in certain applications that demand human creativity and decision-making.
In conclusion, CNC lathe machining offers numerous advantages, such as precision, efficiency, flexibility, cost-effectiveness, and improved quality control. However, it also has disadvantages like high initial investment, maintenance requirements, dependence on skilled operators, and limited adaptability. Before opting for CNC lathe machining, businesses should carefully assess their specific requirements and weigh these pros and cons to make an informed decision.
cnc lathe machining Reference Specifications (varies for different product)
CNC lathe machining is a manufacturing process that utilizes computer numerical control (CNC) technology to produce intricate and high-precision components. This process is commonly used in various industries, such as aerospace, automotive, electronics, and medical.
The reference specifications for CNC lathe machining may vary depending on the specific product being manufactured. However, there are some general guidelines and requirements that are typically followed to ensure the quality and accuracy of the machined parts.
Firstly, the dimensions and tolerances of the components are crucial specifications. The CNC lathe machine must be capable of accurately machining parts within the specified dimensions and tolerances, which are often specified in terms of millimeters or inches. These specifications ensure that the parts fit together properly and function as intended.
Another important specification is the material from which the components are made. CNC lathe machines can work with a wide range of materials, such as metals (aluminum, steel, titanium, etc.), plastics, and composites. The specific material being machined may dictate the type of cutting tools, speed, and feed rates used in the process.
Surface finish requirements are also vital specifications in CNC lathe machining. The finished parts may require a certain level of smoothness, texture, or roughness as per the product’s functional or aesthetic needs. This specification often dictates the type of cutting tools, machining techniques, and post-machining processes, such as polishing or coating.
Furthermore, the production volume is an essential consideration in CNC lathe machining. Depending on the product’s demand, the machining process may need to be optimized for high-volume production or lower-volume, custom production. This specification affects the selection of cutting tools, machining strategies, and production timelines.
Additionally, specific features like threads, chamfers, grooves, and undercuts may be required in certain components. These features add functionality or aid in assembly and may require specialized tooling or machining techniques.
Overall, CNC lathe machining reference specifications encompass dimensions, tolerances, materials, surface finishes, production volumes, and any specific features required for the product being manufactured. Adhering to these specifications ensures the production of high-quality, accurate, and functional components.
Applications of cnc lathe machining
CNC (Computer Numerical Control) lathe machining is a versatile manufacturing process that is used to produce a wide range of precision parts and components. Here are some of the applications of CNC lathe machining:
1. Production of Automobile Parts: CNC lathes are commonly used in the production of various automobile components such as crankshafts, camshafts, pistons, and valves. These machines allow for high precision machining, ensuring that the parts meet the strict requirements of the automotive industry.
2. Aerospace Industry: CNC lathes are extensively used in the aerospace industry for the production of critical components like turbine blades, engine parts, and landing gears. These parts require high accuracy and precision, which is easily achievable with CNC lathe machining.
3. Medical Devices: CNC lathe machining is also utilized in the production of medical devices such as implants, surgical tools, and prosthetics. The high precision and repeatability offered by CNC lathes ensure that these devices meet the stringent quality standards and provide optimal performance.
4. Electronics: CNC lathe machining plays a significant role in the production of electronic components like connectors, switches, and heat sinks. The ability of CNC lathes to produce complex designs with tight tolerances makes them ideal for the electronics industry.
5. Oil and Gas Industry: CNC lathes are employed in the oil and gas industry for the production of valves, fittings, and connectors used in drilling equipment, pipelines, and refineries. These parts require high durability and precision, which can be achieved efficiently using CNC lathe machining.
6. Defense Sector: CNC lathe machining is extensively used in the defense sector for the production of military hardware, including weapon components, aircraft parts, and naval equipment. The robustness and precision of CNC lathes make them suitable for meeting the strict requirements of defense applications.
7. General Manufacturing: CNC lathe machining is widely used in general manufacturing applications for producing a variety of parts and components ranging from fasteners to tooling. The versatility of CNC lathes allows manufacturers to efficiently process a wide range of materials, including metals, plastics, and composites.
In conclusion, CNC lathe machining finds applications in diverse industries, including automotive, aerospace, medical, electronics, oil and gas, defense, and general manufacturing sectors. The ability to produce high precision and complex parts makes CNC lathe machining an indispensable process in modern manufacturing processes.
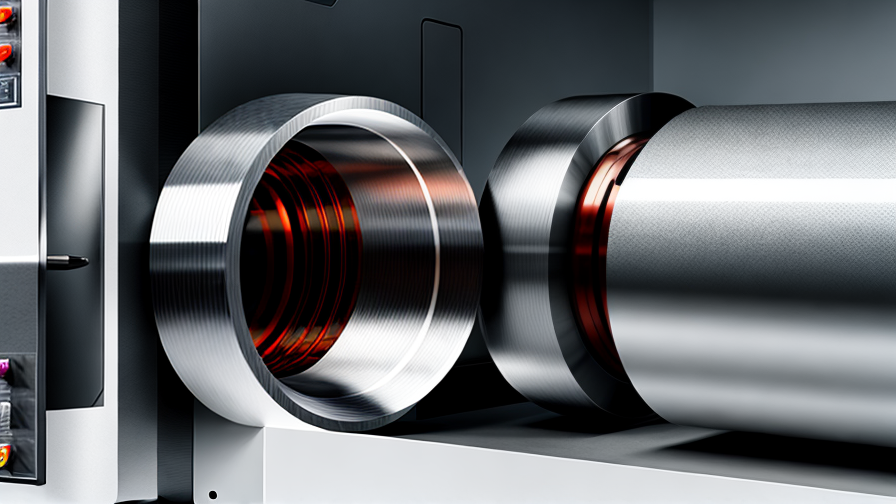
The Work Process and how to use cnc lathe machining
CNC lathe machining is a process used to shape and cut materials such as metal or wood using a computer-controlled lathe machine. The process involves several steps that ensure accurate and precise results.
The first step in CNC lathe machining is designing the part or component using computer-aided design (CAD) software. This software allows engineers to create a 3D model of the part, specifying its dimensions and features.
Once the design is complete, the CAD file is converted into a format that the CNC lathe machine can read. This is done using computer-aided manufacturing (CAM) software. CAM software generates the toolpaths and instructions necessary for the machine to accurately cut and shape the material.
The next step is setting up the machine. This involves mounting the material onto the lathe machine’s spindle and securing it in place. The machine also needs to be programmed with the appropriate cutting tools and settings.
After the setup is complete, the machine operator can start the machining process. The CNC lathe machine follows the programmed instructions, moving the cutting tool along the specified toolpaths to shape the material. The machine’s computer control ensures consistent and precise cuts.
During the machining process, the machine may need to pause for tool changes or to make adjustments to ensure accurate results. Once the machining is complete, the finished part or component is removed from the machine.
CNC lathe machining offers several advantages over traditional manual lathe machining. It allows for increased precision, faster production times, and the ability to create complex shapes and features. Additionally, CNC lathe machining reduces the risk of errors and inconsistencies due to human error, resulting in higher-quality parts.
In conclusion, CNC lathe machining is a process that uses computer-controlled machines to shape and cut materials. It involves designing the part using CAD software, programming the machine with CAM software, setting up the machine, and then running the machining process. CNC lathe machining offers increased precision, faster production times, and the ability to create complex shapes and features.
Quality Testing Methods for cnc lathe machining and how to control the quality
Quality control is essential in CNC lathe machining to ensure precision, accuracy, and consistency in the manufacturing process. There are various quality testing methods that can be employed to achieve this objective.
Firstly, visual inspection is a fundamental method used to check the overall quality of the machined components. This involves physically examining the product for any defects, such as surface imperfections, tool marks, or dimensional irregularities.
Secondly, dimensional measurement is crucial to assess the accuracy and precision of CNC lathe machining. It includes using calipers, micrometers, or coordinate measuring machines (CMM) to measure critical dimensions and tolerances. This ensures that the machined parts are within the specified limits.
Thirdly, surface finish testing is employed to evaluate the smoothness and texture of the machined surfaces. Techniques like profilometry or surface roughness measurement can be used to quantify the roughness parameters, ensuring that the desired surface finish is achieved.
Furthermore, functional testing is necessary to examine how well the machined components perform their intended tasks. This can involve assembling the parts and checking their functional interactions or subjecting them to simulated operational conditions to assess performance, reliability, and durability.
To control the quality in CNC lathe machining, the following measures can be implemented:
1. Regular maintenance and calibration of machines and tools to ensure their accuracy and reliability.
2. Implementation of standardized operating procedures to ensure consistency and repeatability in the machining process.
3. Utilization of statistical process control techniques to monitor and control variations in the manufacturing process.
4. Adoption of advanced quality management systems, such as ISO 9001, to establish comprehensive quality control protocols.
5. Continuous training and skill development of operators to enhance their knowledge of quality standards and machining techniques.
6. Implementing a rigorous inspection system at different stages of the manufacturing process to identify and eliminate defects before they propagate to the subsequent stages.
By combining these quality testing methods and control measures, CNC lathe machining can achieve a high level of quality assurance, resulting in superior product performance and customer satisfaction.
cnc lathe machining Sample Policy and Post-Purchase Considerations for cnc lathe machining from China
Sample Policy:
1. Request for Samples: Before making a bulk purchase, it is advisable to request samples from the CNC lathe machining supplier in China. This will help ensure the quality and accuracy of their products.
2. Sample Evaluation: Thoroughly evaluate the sample, checking for precision, finishing, durability, and any other specific requirements. This will help in determining whether the supplier meets your expectations and standards.
3. Quality Assurance: Ensure that the supplier has a quality assurance system in place to guarantee the consistency of their CNC lathe machining products. This can include ISO certification or other industry standards.
4. Customization Options: Discuss with the supplier their capabilities for customization. Understand their capabilities to adjust specifications, such as dimensions, materials, coatings, and tolerances, based on your specific needs.
Post-Purchase Considerations:
1. Quality Testing: Perform quality testing on the received CNC lathe machining products to ensure they meet the agreed specifications. Compare with the initial sample to check for any discrepancies.
2. Communication and Support: Maintain open communication with the supplier. If any issues arise, promptly address them and seek their assistance for resolution. Good suppliers provide reliable customer support.
3. Long-Term Partnership: Develop a long-term partnership with the supplier if they consistently provide quality CNC lathe machining products and reliable services. Building a strong relationship will ensure a seamless and efficient supply chain.
4. Market Feedback: Gather feedback from end-users or customers who utilize the CNC lathe machining products. This will help identify areas for improvement and provide insights for future orders.
5. Consider Multiple Suppliers: Evaluate multiple suppliers from China to compare their products and services. This can help ensure competitive pricing, product variety, and mitigate risks associated with relying on a single supplier.
In summary, when procuring CNC lathe machining products from China, it is essential to request and evaluate samples, ensure quality assurance, explore customization options, and establish a long-term partnership with a reliable supplier who offers excellent customer support. Regular quality testing, gathering market feedback, and considering multiple suppliers will contribute to a successful post-purchase experience.
Sourcing cnc lathe machining from China: Opportunities, Risks, and Key Players
Sourcing CNC lathe machining from China presents both opportunities and risks for businesses. One of the main opportunities is the cost-effectiveness of Chinese manufacturing. Chinese manufacturers often offer competitive pricing due to lower labor costs and economies of scale, making it an attractive option for businesses looking to optimize their production costs.
Additionally, China is known for its extensive manufacturing capabilities and infrastructure. The country has a well-established network of suppliers, which can provide a wide range of CNC lathe machining services, including precision machining, turning, milling, and more. This allows businesses to find the right manufacturer to meet their specific requirements.
However, there are also risks associated with sourcing CNC lathe machining from China. Quality control can be a challenge, as some Chinese manufacturers may not meet the same quality standards that businesses expect. It is crucial for businesses to thoroughly vet potential manufacturers and ensure they have quality control processes in place.
Intellectual property protection is another key concern. China has a history of intellectual property infringements, and businesses must take precautions to protect their proprietary designs and technologies. This can be done through non-disclosure agreements (NDAs) and careful selection of trusted manufacturers with a strong track record of protecting intellectual property.
Despite the risks, China is home to several key players in the CNC lathe machining industry. Some of the leading manufacturers in China include CKD Precision, Ningbo Kaibo, L.C. Technologies Inc., and Ningbo Haitian Precision Machinery Co., Ltd. These companies have a strong reputation for their manufacturing capabilities and can provide CNC lathe machining services to businesses globally.
In conclusion, sourcing CNC lathe machining from China offers cost-effective possibilities for businesses. However, it is essential to be aware of the associated risks, such as quality control and intellectual property protection. By carefully selecting trusted manufacturers and implementing precautionary measures, businesses can benefit from the opportunities that China’s manufacturing sector presents.
How to find and select reliable cnc lathe machining manufacturers in China,use google search manufacturers and suppliers
When searching for reliable CNC lathe machining manufacturers in China, Google can be a useful tool. Here’s a step-by-step approach to find and select the right manufacturer:
1. Identify your requirements: Determine the specific details you need for CNC lathe machining, such as material, desired specifications, and quantities required. Having clarity on your requirements will help you search more effectively.
2. Use appropriate search terms: Go to Google and enter search terms like “CNC lathe machining manufacturers in China,” “CNC lathe suppliers China,” or specific keywords related to your requirements.
3. Check company websites: Visit the websites of the manufacturers listed in the search results. Look for comprehensive information about their experience, capabilities, certifications, and quality control measures. Reputable companies often have well-developed websites with clear product descriptions and contact details.
4. Evaluate manufacturers’ credibility: Look for signs of reliability and trustworthiness. This includes checking if the manufacturer has any industry certifications such as ISO 9001 or ISO 13485, which indicate adherence to international standards. Also, consider their years of experience, client testimonials or reviews, and the presence of company profiles on business directories.
5. Assess their capabilities: Review the manufacturer’s range of CNC lathe machining services, including whether they can handle your specific requirements. Look for information on their machinery, production capacity, and ability to provide customized solutions if needed. It is also essential to understand their quality control processes and if they have quality certifications.
6. Request quotes and samples: Contact the shortlisted manufacturers to request price quotes and, if possible, samples of their CNC lathe machined products. Pay attention to the clarity and promptness of their responses to gauge their level of professionalism and customer service.
7. Compare and select: Evaluate the quotes, samples, and overall impression of each manufacturer. Consider factors like price, quality, lead time, communication, and support services. Select the manufacturer that best aligns with your specific requirements and provides you with confidence in their reliability.
Remember to conduct due diligence by verifying the selected manufacturer’s credentials and reputation through online reviews, asking for references, or visiting manufacturing facilities if feasible. This thorough evaluation will help you find a trustworthy CNC lathe machining manufacturer in China.
How to check cnc lathe machining manufacturers website reliable,use google chrome SEOquake check if ranking in top 10M
To ensure the reliability of a CNC lathe machining manufacturer’s website, follow these steps using Google Chrome and SEOquake:
1. Install SEOquake: Install the SEOquake extension on your Google Chrome browser. SEOquake provides valuable information about a website’s search engine optimization metrics.
2. Search for the manufacturer: Open a new tab and enter the manufacturer’s name or related keywords in the Google search bar.
3. Analyze search results: Look for the manufacturer’s website in the search results. The higher the website ranks, the better its visibility and credibility usually are. Websites ranking in the top 10 million usually receive a moderate level of traffic.
4. Install SEOquake metrics: Click on the SEOquake icon in your browser’s toolbar, and a metrics panel will appear. Ensure that the “SEObar” and “SERP overlay” options are toggled on.
5. Check website metrics: After opening the manufacturer’s website, the SEObar will display metrics such as the website’s Google PageRank, Alexa rank, and backlink count. A higher PageRank, lower Alexa rank, and a good number of backlinks generally indicate a more reliable website.
6. Verify traffic: To get an estimate of the website’s traffic, click on the “SEMrush” button in the SEObar. SEMrush will provide the website’s estimated monthly organic search traffic, allowing you to gauge its popularity.
7. Analyze content quality: Navigate through the manufacturer’s website, paying attention to the quality of the information provided. Look for clear product descriptions, certifications, testimonials, and contact details. A well-structured and informative website is usually more reliable.
8. Read customer reviews: Search for customer reviews or testimonials about the manufacturer’s services or products. Positive reviews from reputed sources increase the website’s credibility.
By following these steps and utilizing the SEOquake extension in Google Chrome, you can assess the reliability of a CNC lathe machining manufacturer’s website within a concise 300-word explanation.
Top 10 cnc lathe machining manufacturers in China with each 160 words introduce products,then use markdown create table compare
1. Haas Automation China Co., Ltd. – Haas Automation is a leading manufacturer of CNC lathes in China, offering a wide range of lathe machines suitable for various industries. Their products include the ST series CNC lathes known for their high precision and productivity.
2. Yangzhou Euro Brother Machine & Tools Co., Ltd. – Specializing in CNC lathe production, Euro Brother offers a comprehensive range of lathe machines including flat bed and slant bed models. Their products feature advanced technology, high rigidity, and excellent precision.
3. Shandong Lu Young Machinery Co., Ltd. – Lu Young Machinery is known for its high-quality CNC lathe machines. Their product line includes various types of CNC lathes with exceptional performance, durability, and versatility. They cater to the needs of industries such as automotive, aerospace, and energy.
4. Ningbo Blin Machinery Co., Ltd. – Blin Machinery is a reliable manufacturer of CNC lathe machines, offering models suitable for both small and large-scale operations. Their products boast high precision and stability, making them ideal for precision turning and machining tasks.
5. Suzhou Huayuan CNC Machine Tool Co., Ltd. – Huayuan CNC is a renowned manufacturer of CNC lathe machines focusing on providing cost-effective solutions. Their products feature user-friendly interfaces, high efficiency, and accurate machining capabilities.
6. Wuxi Yiji Grinding Machine Manufacturing Co., Ltd. – Yiji Grinding Machine Manufacturing specializes in the production of CNC lathe machines designed for high precision processing. Their products are widely used in industries such as aerospace, automotive, and electronics.
7. Qingdao Victor International Trade Co., Ltd. – Victor International Trade offers a range of CNC lathe machines designed for different requirements. Their products are known for their superior quality, high speed, and precision machining capabilities.
8. Zhejiang Jingdian Numerical Control Equipment Co., Ltd. – Jingdian Numerical Control Equipment is a leading manufacturer of CNC lathe machines in China. Their products are known for their excellent stability, accuracy, and efficiency, making them suitable for various applications.
9. Taian Crystal Machinery Co., Ltd. – Crystal Machinery specializes in the production of CNC lathe machines known for their high precision and stability. Their products are widely used in industries such as automotive, electronics, and medical equipment manufacturing.
10. Dalian Guorui Machinery Co., Ltd. – Guorui Machinery offers a wide range of CNC lathe machines designed with advanced technology and precision. Their products are known for their excellent performance, reliability, and durability.
Table:
| Manufacturer | Notable Products |
|—————————————-|————————————————————————-|
| Haas Automation China Co., Ltd. | ST series CNC lathes |
| Yangzhou Euro Brother Machine & Tools | Flat bed and slant bed CNC lathes |
| Shandong Lu Young Machinery Co., Ltd. | Various high-quality CNC lathes |
| Ningbo Blin Machinery Co., Ltd. | CNC lathes for precision turning and machining |
| Suzhou Huayuan CNC Machine Tool Co., Ltd| Cost-effective CNC lathe machines |
| Wuxi Yiji Grinding Machine Mfg. | CNC lathes for high-precision processing |
| Qingdao Victor International Trade Co. | CNC lathes with superior quality and high speed |
| Zhejiang Jingdian Numerical Control | CNC lathes with excellent stability, accuracy, and efficiency |
| Taian Crystal Machinery Co., Ltd. | CNC lathes for automotive, electronics, and medical equipment industries |
| Dalian Guorui Machinery Co., Ltd. | CNC lathes with advanced technology and precision |
These top 10 CNC lathe machining manufacturers in China offer a diverse range of products with advanced features. By comparing their notable products, buyers can evaluate their specifications, precision, stability, and suitability for specific industries.
Background Research for cnc lathe machining manufacturers Companies in China, use qcc.com archive.org importyeti.com
When seeking information on CNC lathe machining manufacturers in China, there are several reliable sources that can be utilized for background research. These include qcc.com, archive.org, and importyeti.com.
qcc.com is a comprehensive business database that provides information on companies in China. It allows users to search for specific companies and access their profiles, including contact details, business scope, registration status, and more. This platform is particularly helpful for obtaining basic information on CNC lathe machining manufacturers and verifying their legitimacy.
archive.org, also known as the Internet Archive, is a digital library that offers free access to historical collections of websites, videos, books, and other digital materials. By searching for specific websites or company names, researchers can access old versions of webpages and review any publicly available information on CNC lathe machining manufacturers in China. This can be useful for tracking the historical development, changes, or reputation of these companies.
importyeti.com is an import/export data platform that provides information about the trading activities of companies. By searching for specific products or company names, researchers can identify potential CNC lathe machining manufacturers in China and gain insight into their export activities. This platform allows users to track shipment records, monitor market trends, and analyze the import/export data of CNC lathe machining manufacturers.
By utilizing the above-mentioned sources, researchers can gather background information on CNC lathe machining manufacturers in China. These platforms provide access to company profiles, historical data, and import/export records, enabling researchers to evaluate the legitimacy, track record, and market presence of potential manufacturers. However, it is important to critically analyze the obtained information and cross-reference with other reliable sources to ensure accuracy and make informed decisions.
Leveraging Trade Shows and Expos for cnc lathe machining Sourcing in China
Trade shows and expos provide excellent opportunities for sourcing CNC lathe machining services in China. These events bring together manufacturers, suppliers, and buyers, allowing them to connect and build business relationships. By leveraging trade shows and expos, companies can access a large pool of potential suppliers, compare offerings, and make informed decisions.
Participating in trade shows and expos dedicated to CNC lathe machining in China is beneficial for several reasons. Firstly, these events provide a platform for meeting and interacting with a wide range of suppliers in one location. This saves time and resources that would otherwise be spent on individual supplier visits. Moreover, it enables businesses to gather information about the latest technologies, trends, and innovations in the industry.
During trade shows and expos, companies can evaluate different suppliers based on their capabilities, quality standards, pricing, and production capacity. They can examine samples of products and assess the suppliers’ ability to adhere to specifications and meet desired quality levels. This firsthand evaluation helps in finding the most suitable supplier for CNC lathe machining needs.
Additionally, trade shows and expos allow businesses to network with industry experts, gain insights into market dynamics, and develop a better understanding of the competitive landscape. These events often feature seminars, workshops, and panel discussions, enabling attendees to acquire valuable knowledge and learn about best practices in CNC lathe machining.
To make the most out of trade shows and expos, companies should have clear objectives and a well-defined sourcing strategy. It’s essential to conduct thorough research before attending these events to identify the most relevant ones and arrange meetings with potential suppliers in advance. Making a checklist of specific requirements, such as capacity, certifications, and service offerings, will streamline the evaluation process and aid decision-making.
In conclusion, trade shows and expos provide a unique opportunity for sourcing CNC lathe machining services in China. By leveraging these events, companies can access a wide range of suppliers, evaluate their capabilities, and make informed sourcing decisions. With careful preparation and a focused approach, businesses can efficiently navigate these events and find the most suitable CNC lathe machining partner in China.
The Role of Agents and Sourcing Companies in Facilitating cnc lathe machining Purchases from China
Agents and sourcing companies play a crucial role in facilitating CNC lathe machining purchases from China. These intermediaries help businesses identify and connect with reliable manufacturers in the country, ensuring a smooth procurement process.
Firstly, agents and sourcing companies have extensive local knowledge and expertise, allowing them to identify reputable CNC lathe machining manufacturers in China. They maintain a database of reliable suppliers and possess industry-specific knowledge to find the most suitable ones for a particular business’s requirements. This saves considerable time, effort, and resources for businesses that would otherwise have to conduct extensive research on their own.
Furthermore, these intermediaries can communicate effectively with Chinese manufacturers, overcoming any language and cultural barriers. They are fluent in Chinese and have a deep understanding of Chinese business practices, ensuring clear and accurate communication between buyers and suppliers. This simplifies the process for businesses and minimizes misunderstandings, leading to a more efficient purchasing experience.
Agents and sourcing companies also provide comprehensive quality control and inspection services. They can conduct factory audits to assess the manufacturers’ capabilities, production facilities, and quality control processes. This helps businesses ensure that the CNC lathe machining products they purchase meet their standards and specifications. Additionally, these intermediaries can arrange for product inspections at various stages of production, reducing the risk of receiving defective products.
Moreover, agents and sourcing companies assist with logistics and shipping arrangements. They have in-depth knowledge of local shipping regulations and can negotiate the best rates and terms with freight forwarders or shipping companies. This ensures prompt and cost-effective delivery of the purchased CNC lathe machining products to the buyer’s location.
Overall, agents and sourcing companies serve as reliable intermediaries, streamlining the process of purchasing CNC lathe machining products from China. Their expertise, local knowledge, and comprehensive services help businesses find trustworthy suppliers, communicate effectively, ensure product quality, and handle logistics efficiently.
Price Cost Research for cnc lathe machining manufacturers Companies in China, use temu.com and 1688.com
When conducting price cost research for CNC lathe machining manufacturers in China, two reliable platforms to gather information from are temu.com and 1688.com. These websites are widely used in China’s manufacturing industry to connect buyers with different suppliers.
Temu.com is an online platform that facilitates direct communication between buyers and suppliers. It provides detailed information on the capabilities, production capacity, and qualifications of CNC lathe machining manufacturers. Users can browse through various listings and contact potential suppliers directly to inquire about product prices and related costs. It is important to ensure that the suppliers you are interested in have the necessary certifications and the ability to meet your specific requirements.
Another valuable platform is 1688.com, which is a B2B (business-to-business) website widely used by manufacturers and suppliers in China. It offers a vast array of products, including CNC lathe machining services. The platform allows users to search for manufacturers based on location, product specifications, and other relevant factors. It also provides pricing information, including the unit price and minimum order quantity. In addition, 1688.com offers a messaging system that enables communication between buyers and suppliers, facilitating further discussions regarding pricing, customization, and other details.
When utilizing these platforms for price cost research, it is recommended to:
1. Clearly define your specific requirements, including technical specifications, quantity, and desired quality standards.
2. Compare multiple suppliers to ensure competitive pricing and evaluate the capabilities of different manufacturers.
3. Communicate directly with the suppliers to request detailed quotations and obtain a comprehensive understanding of their pricing structures, including any additional costs (e.g., shipping, taxes, or customization fees).
4. Take into consideration the supplier’s reputation, certifications, and customer reviews to ensure reliability and quality.
As with any sourcing process, it is recommended to exercise due diligence and thoroughly assess potential suppliers to mitigate any risks and ensure a successful collaboration.
Shipping Cost for cnc lathe machining import from China
The shipping cost for CNC lathe machining imports from China can vary depending on several factors. The main factors that influence the shipping cost are the weight and dimensions of the cargo, the distance it needs to travel, the mode of transportation used, and any additional services required.
For small-scale imports, air freight is a popular choice due to its fast delivery time. The cost of air freight is typically determined by the chargeable weight, which is either the actual weight or the volumetric weight, whichever is higher. Additional charges may apply for customs clearance, handling fees, and documentation.
For larger shipments, sea freight is often more cost-effective. The shipping cost for sea freight is usually calculated based on the volume of the cargo in cubic meters (CBM) or the weight in metric tons. Other charges, such as port fees, customs duties, and insurance, may also apply.
To get a more accurate estimate of the shipping cost, it is advisable to contact freight forwarders or shipping agents who specialize in China imports. They can provide specific rates based on your requirements and negotiate with shipping lines for the best possible price.
It is important to consider other factors as well, such as the delivery time, reliability of the shipping carrier, and any additional services required, such as packaging, customs clearance, and inland transportation.
Lastly, it is worth mentioning that the shipping cost is just one aspect to consider when importing CNC lathe machining from China. It is equally important to ensure the product’s quality, compliance with regulations, and the reputation of the manufacturer or supplier.
Compare China and Other cnc lathe machining Markets: Products Quality and Price,Visible and Hidden Costs
China is renowned for its vast manufacturing capabilities, including the production of CNC lathe machined products. When comparing China’s CNC lathe machining market with others, several factors come into play, such as products quality, price, and visible and hidden costs.
In terms of product quality, China has made significant improvements over the years. Initially known for producing lower-quality items, Chinese manufacturers have invested in advanced technology and improved their manufacturing processes. As a result, the quality of CNC lathe machined products from China has greatly improved and can now compete with products from other markets. However, it is crucial to note that quality can vary depending on the manufacturer, and thorough research is necessary to ensure that the desired quality standards are met.
Price is a key factor when considering CNC lathe machining markets. China has the advantage of low labor costs, which often leads to competitive pricing for its products. This makes China an attractive option for buyers looking for cost-effective solutions. However, it is worth considering that price alone does not guarantee value for money. The overall cost should also encompass other factors, such as quality, reliability, and customer service.
Visible costs refer to the readily apparent expenses associated with outsourcing CNC lathe machining to a particular market. These include the cost of the product, shipping, and any applicable taxes or tariffs. In this regard, China’s manufacturing capabilities and well-established logistics infrastructure make it a convenient option.
Hidden costs, on the other hand, are not immediately apparent and can add up over time. These costs include poor product quality leading to rejections, long lead times, communication challenges, cultural differences, and intellectual property risks. When evaluating China’s CNC lathe machining market, buyers should carefully consider these hidden costs and potential risks.
In summary, China’s CNC lathe machining market has progressed significantly in terms of product quality, offering products that can compete with those from other markets. Its advantageous low labor costs make it a cost-effective option, especially for price-sensitive buyers. However, it is essential to consider both visible and hidden costs associated with manufacturing in China. Evaluating quality, reliability, and potential risks should be a priority to ensure a successful outsourcing experience.
Understanding Pricing and Payment Terms for cnc lathe machining: A Comparative Guide to Get the Best Deal
When it comes to acquiring CNC lathe machining services, understanding pricing and payment terms is essential to ensure you get the best deal. This comparative guide aims to provide insights into the factors that influence pricing and payment structures in the CNC machining industry, helping you make an informed decision.
Pricing in CNC lathe machining typically depends on several key factors. Firstly, the complexity and intricacy of the required design greatly impact the cost. More complex designs usually require additional labor, tooling, and programming time, which may result in higher prices. Additionally, the size and volume of the project also play a role. Larger projects often require more materials and machining time, leading to increased costs.
Material selection is another crucial consideration. Different materials have varying costs and machining requirements. Metals like aluminum and steel are generally more affordable compared to exotic alloys or plastics, which can be more expensive. Moreover, the size and weight of the material can influence pricing, as heavy or oversized parts may require specialized equipment or additional operator assistance.
The quantity and frequency of the parts required can also affect pricing. Machining companies often offer volume discounts, making it more cost-effective to order larger quantities. Furthermore, recurring orders or long-term contracts might enable negotiable pricing, providing significant savings in the long run.
Payment terms vary among CNC machining service providers. Many companies require an upfront deposit before commencing the project, with the remaining balance payable upon completion. Others may establish milestone payments for longer projects. It is important to discuss and clarify payment terms with potential vendors to avoid any misunderstandings or surprises.
To get the best deal, it is advisable to obtain multiple quotes from different CNC machining service providers. This allows you to compare prices, quality, lead times, and customer reviews. Keep in mind that selecting the cheapest option may not always be the best choice; instead, focus on value for money and the supplier’s reputation in terms of quality and reliability.
In conclusion, understanding pricing and payment terms is crucial when seeking CNC lathe machining services. Consider the complexity, size, and material of the project, as well as the quantity and frequency of parts required. Obtain multiple quotes and compare factors beyond price alone. By doing so, you can ensure you secure the best deal while maintaining high-quality standards for your CNC lathe machining needs.
Chinese Regulations and Industry Standards Certifications for cnc lathe machining,Import Regulations and Customs for cnc lathe machining from China
In China, there are specific regulations and industry standards certifications for CNC lathe machining. These regulations ensure the quality, safety, and reliability of CNC lathe machines produced and exported from China.
One of the key certifications for CNC lathe machining in China is the ISO 9001 certification. This certification indicates that the manufacturer has established and implemented a quality management system that meets international standards. It ensures that the manufacturer follows strict quality control processes throughout the production of CNC lathe machines.
Another important certification is the CE certification, which is required for CNC lathe machining products exported to many countries in Europe. This certification indicates that the product meets the essential health, safety, and environmental protection requirements set by the European Union.
Additionally, the China Compulsory Certification (CCC) is mandatory for certain CNC lathe machining products sold in the Chinese domestic market. This certification ensures that the products comply with the quality, safety, and environmental protection standards set by the Chinese government.
When importing CNC lathe machining products from China, it is essential to comply with import regulations and customs procedures. The importer should ensure that the supplier is properly certified, and the products meet the relevant standards and certifications required by their country.
Importers should also be aware of customs duties, taxes, and other import charges that may apply when bringing CNC lathe machining products into their country. They should consult the customs authorities of their country to understand the specific regulations and procedures for importing these products.
To summarize, Chinese regulations and industry standards certifications, such as ISO 9001, CE, and CCC, ensure the quality and safety of CNC lathe machining products. Importers should adhere to import regulations and customs procedures, considering certifications and consulting with customs authorities to ensure a smooth importation process.
Sustainability and Environmental Considerations in cnc lathe machining Manufacturing
Sustainability and environmental considerations in CNC lathe machining manufacturing are becoming increasingly important in today’s industrial landscape. As the world focuses on reducing energy consumption, minimizing waste generation, and mitigating the environmental impact of manufacturing processes, CNC lathe machining companies must adopt sustainable practices to ensure long-term viability.
One area of concern is energy consumption. CNC lathe machining involves the use of heavy machinery and power-intensive operations. To address this, manufacturers can invest in energy-efficient equipment that has better power management systems and consumes less electricity. Additionally, implementing machine monitoring and optimization techniques can help identify energy-wasting processes and reduce overall energy consumption.
Waste generation is another critical issue. CNC lathe machining typically involves the use of lubricants, coolants, and cutting fluids, which can create significant amounts of waste. To minimize waste, manufacturers can switch to using environmentally friendly lubricants and cutting fluids that can be recycled or disposed of safely. Implementing proper waste management practices, such as segregating and recycling waste materials, can also help reduce the environmental impact.
Furthermore, material usage should be optimized. CNC lathe machining often involves the removal of excess material, resulting in a significant amount of waste. Implementing efficient material management practices, such as optimizing toolpaths and minimizing the amount of material removed, can help reduce waste generation.
To ensure sustainability, manufacturers should also consider the life cycle of their products. This involves assessing the environmental impact of raw material extraction, production, transportation, use, and end-of-life disposal. By using sustainable materials, reducing the use of harmful substances, and designing products for easy disassembly and recycling, manufacturers can minimize the overall environmental impact.
In conclusion, sustainability and environmental considerations are crucial for CNC lathe machining manufacturing. Energy-efficient equipment, waste reduction strategies, material optimization, and product life cycle assessment are key approaches to achieving sustainability. By integrating these principles into their operations, CNC lathe machining companies can contribute to a more sustainable and environmentally conscious manufacturing industry.
List The Evolution history of “cnc lathe machining”
CNC (Computer Numerical Control) lathe machining has evolved significantly over the years, revolutionizing the manufacturing industry. Here is a brief history of its evolution:
1. Early 1950s: The birth of numerical control (NC) machines marked the start of automated machining. These machines were controlled by punched paper tapes that provided instructions to the machine tools.
2. Late 1950s: MIT researchers developed the concept of electronically controlling machine tools using punched cards. This led to the development of the first CNC lathe in the late 1950s, combining computer technology and machining.
3. 1960s: The industry witnessed various advancements in CNC technology. The introduction of minicomputers allowed for greater programming capabilities and improved accuracy in machining. This decade also saw the first use of CAD (Computer-Aided Design) systems to generate part designs.
4. 1970s: Microprocessors were introduced, making CNC systems more compact and affordable. This led to a wider adoption of CNC machines, making them more accessible to small and medium-sized manufacturers.
5. 1980s: CNC technology became more powerful and versatile. The integration of computer systems with CNC machines allowed for real-time monitoring and increased automation. Multi-axis capabilities were also introduced, enabling complex machining operations.
6. 1990s: CNC lathe machining experienced significant advancements in software and hardware. CAD/CAM (Computer-Aided Manufacturing) systems became more sophisticated, enabling seamless integration between design and manufacturing processes.
7. 2000s: CNC machines became more intelligent with the integration of advanced sensors and feedback systems. This led to improved precision, accuracy, and automated tool control. Additionally, networking capabilities allowed for remote monitoring and programming.
8. Present day: CNC lathe machining continues to evolve with advancements in robotics, artificial intelligence, and data analytics. Smart manufacturing concepts, such as the Internet of Things (IoT) and Industry 4.0, are being integrated into CNC systems, enabling increased efficiency, productivity, and flexibility.
Today, CNC lathe machining has transformed the manufacturing landscape, offering precise and automated solutions for a wide range of industries. Continuous advancements in technology will further enhance its capabilities, making CNC machines even more efficient, intelligent, and adaptable.
The Evolution and Market Trends in cnc lathe machining Industry
The CNC lathe machining industry has undergone significant evolution and market trends in recent years. CNC (Computer Numerical Control) technology has revolutionized the way lathes are operated, resulting in increased precision, efficiency, and automation.
One major evolution in the industry is the shift towards multi-axis CNC lathes. Traditional lathes typically operated on two axes (X and Z), but advancements in technology have allowed for the development of lathes that can operate on multiple axes simultaneously. Multi-axis lathes offer greater flexibility and versatility, enabling manufacturers to produce more complex and intricate parts.
Another important evolution is the integration of CAD/CAM (Computer-Aided Design/Computer-Aided Manufacturing) software in CNC lathe machining. CAD/CAM software allows manufacturers to create detailed, 3D models of the desired part, which can then be translated into machine instructions for the CNC lathe. This integration streamlines the manufacturing process, reduces human error, and enables faster prototyping and production.
Market trends in the CNC lathe machining industry reflect the increasing demand for precision and efficiency. Industries such as aerospace, automotive, and medical device manufacturing require high levels of precision in their machined parts, which can be achieved through CNC lathe machining. As a result, there is a growing market for CNC lathe machines that can deliver on these requirements.
Automation is another significant market trend in the industry. CNC lathe machines can be programmed to run continuously, minimizing the need for human intervention and reducing production time. Additionally, the integration of robotics and other automation technologies in CNC lathe machining further enhances the efficiency and productivity of the manufacturing process.
An emerging market trend is the rise of smart manufacturing in the CNC lathe machining industry. This involves the use of Internet of Things (IoT) technology to connect machines, sensors, and software for real-time data collection and analysis. Smart manufacturing allows for predictive maintenance, remote monitoring, and optimization of production processes, leading to improved productivity and reduced downtime.
In conclusion, the CNC lathe machining industry has evolved significantly in recent years, with advancements in technology and market trends shaping the way manufacturers operate. The shift towards multi-axis lathes, integration of CAD/CAM software, increasing demand for precision, automation, and the rise of smart manufacturing are all notable developments in the industry. These trends are likely to continue shaping the future of CNC lathe machining, driving further advancements in precision, efficiency, and productivity.
Custom Private Labeling and Branding Opportunities with Chinese cnc lathe machining Manufacturers
Custom private labeling and branding opportunities with Chinese CNC lathe machining manufacturers provide businesses the chance to establish their unique brand identity and gain a competitive edge in the market. With a vast network of CNC lathe machining manufacturers in China, businesses can find ample opportunities to customize their products and showcase their brand effectively.
By collaborating with Chinese CNC lathe machining manufacturers, businesses can create products specifically tailored to their target market’s needs and preferences. Manufacturers offer various customization options, including designing the shape, size, color, materials, and finishes of the products. This allows businesses to create distinctive and high-quality products that resonate with their brand image and customer base.
In addition to product customization, Chinese manufacturers also provide private labeling services. This enables businesses to showcase their logo, brand name, and other essential details on the products. By having their brand prominently labeled, businesses can increase brand recognition and customer loyalty. Moreover, private labeling also helps in preventing counterfeit products and strengthens the authenticity of the brand.
Chinese CNC lathe machining manufacturers are equipped with advanced technology and extensive industry expertise. They possess the capability to meet bulk production requirements while maintaining superior quality. With affordable production costs and a competitive pricing structure, businesses can maximize their profit margins while delivering value to customers.
Furthermore, collaborating with Chinese manufacturers offers businesses flexibility in scaling their production. As the demand for products increases, manufacturers can quickly adapt and increase production capacities to meet the growing needs of the business. This ensures uninterrupted supply and faster time-to-market, providing a significant advantage over competitors.
In conclusion, custom private labeling and branding opportunities with Chinese CNC lathe machining manufacturers present businesses with a lucrative avenue to create distinctive products and establish a strong brand presence. By leveraging the expertise of Chinese manufacturers, businesses can effectively meet their target market’s requirements, enhance brand recognition, and drive business growth.
Tips for Procurement and Considerations when Purchasing cnc lathe machining
When purchasing a CNC lathe machine, there are several important factors to consider to ensure you make the best procurement decision. Here are some tips and considerations to help you in the process:
1. Requirement Analysis: Determine your specific requirements for the CNC lathe machine. Consider factors like the size and weight of the components to be machined, the level of precision required, the material type, and the production volume. This will help you identify the right specifications for your machine.
2. Machine Type: Choose between a horizontal or vertical CNC lathe machine based on your specific needs. Horizontal machines are suitable for large and heavy workpieces, while vertical machines are ideal for smaller and lighter workpieces.
3. Accuracy and Precision: Look for a machine that offers high accuracy and precision. Check the machine’s repeatability, resolution, and positioning accuracy to ensure it meets your quality requirements.
4. Control System: Opt for a CNC lathe machine with a user-friendly and intuitive control system. This will make it easier for your operators to quickly learn and optimize the machine’s capabilities.
5. Tooling and Spindle Speed: Consider the machine’s tooling options and spindle speed capabilities. Ensure that the machine can accommodate your required tooling configurations and offers sufficient spindle speed for the material and operations you will be performing.
6. Maintenance and Support: Investigate the availability of spare parts, maintenance requirements, and technical support for the machine. Choose a manufacturer or supplier with a good reputation for after-sales service and support.
7. Cost and Return on Investment: Evaluate the total cost of ownership, including the machine price, installation, training, and maintenance costs. Consider the expected return on investment based on increased productivity, reduced labor costs, and improved product quality.
8. Supplier Reputation: Research and choose a reputable supplier with a track record of delivering quality CNC lathe machines. Read customer reviews and testimonials to gain insights into their reliability, service, and product performance.
By carefully considering these tips and considerations, you can make an informed decision when purchasing a CNC lathe machine that best suits your specific requirements and maximizes your productivity and profitability.
FAQs on Sourcing and Manufacturing cnc lathe machining in China
Q: Why should I consider sourcing and manufacturing CNC lathe machining in China?
A: China has a well-established manufacturing industry, and is known for its expertise in CNC machining. Sourcing and manufacturing CNC lathe machining in China offers significant cost savings due to lower labor and production costs compared to many other countries. Additionally, China has a vast network of suppliers and manufacturers, providing a wide range of options to choose from. The country’s infrastructure and logistics capabilities also make exporting products more efficient.
Q: How can I find reliable suppliers for CNC lathe machining in China?
A: There are several ways to find reliable suppliers in China. One option is to attend trade shows and exhibitions where Chinese manufacturers showcase their products and services. This allows you to meet suppliers face-to-face and assess their capabilities. Another option is to use online sourcing platforms, such as Alibaba or Global Sources, which allow you to search for and contact suppliers directly. It is important to thoroughly research and vet potential suppliers, checking their certifications, quality control processes, and customer reviews.
Q: What are the advantages of CNC lathe machining in China?
A: CNC lathe machining in China offers several advantages. Firstly, Chinese manufacturers have extensive experience and expertise in CNC machining, ensuring high-quality production. Secondly, China has a vast pool of skilled labor, enabling faster production turnaround times. Moreover, China operates at a large scale, allowing for economies of scale, meaning that production costs can be significantly lower compared to other countries. Finally, China’s manufacturing sector is known for its flexibility and ability to handle complex projects, accommodating various customization requirements.
Q: How can I ensure quality control when manufacturing CNC lathe machining in China?
A: Quality control is crucial when manufacturing in China. To ensure quality, it is essential to clearly communicate your specific requirements and specifications to the supplier. Requesting samples or prototypes before placing a large order is also recommended. Additionally, performing factory inspections and audits can help verify the supplier’s facilities, capabilities, and quality control processes. Implementing a comprehensive quality control plan and conducting regular inspections throughout the production process can further ensure that the final products meet your standards. It is advisable to seek suppliers who have relevant certifications, such as ISO 9001, as it demonstrates their commitment to quality management.
Q: What are the typical lead times for CNC lathe machining in China?
A: Lead times for CNC lathe machining in China can vary depending on several factors, including product complexity, order quantity, and the supplier’s workload. Generally, lead times range from a few weeks to a few months. Communicating your required delivery date and having a clear understanding of the supplier’s production capacity can help manage expectations and plan accordingly. Tighter deadlines may be achievable but may require additional costs or negotiation with the supplier.
Why contact sourcifychina.com get free quota from reliable cnc lathe machining suppliers?
Sourcifychina.com, a sourcing platform, offers free quota from reliable CNC lathe machining suppliers as part of their business strategy to attract and retain customers. This approach serves both the suppliers and the buyers by providing a mutually beneficial arrangement.
Firstly, by providing a free quota, Sourcifychina.com enables potential buyers to assess the capabilities and pricing of different CNC lathe machining suppliers without any financial commitment. This allows them to evaluate the quality of the products, the supplier’s responsiveness, and their ability to meet specific requirements. By offering this service, Sourcifychina.com helps buyers make informed decisions, increasing their chances of finding a suitable supplier.
Secondly, this business strategy benefits the CNC lathe machining suppliers by giving them exposure to a larger customer base. By participating in the free quota system, suppliers gain the opportunity to showcase their skills, quality control measures, and competitive pricing to potential buyers who may not have considered them otherwise. This helps suppliers expand their market reach and secure new business partnerships.
Furthermore, by offering a free quota, Sourcifychina.com is positioning itself as a trusted intermediary in the sourcing process. This builds trust with both buyers and suppliers and establishes the platform as a reliable source for finding reputable CNC lathe machining suppliers in China. As a result, more suppliers are likely to join the platform, increasing the options available to buyers.
In conclusion, the provision of free quotas from reliable CNC lathe machining suppliers by Sourcifychina.com is a strategic decision aimed at attracting and retaining both buyers and suppliers. This approach benefits buyers by allowing them to assess potential suppliers without financial risk, while also benefiting suppliers by gaining exposure to a wider customer base. Ultimately, Sourcifychina.com aims to become a trusted and go-to platform for sourcing CNC lathe machining suppliers in China.