Introduce about custom injection molded plastics guide,Qulity,Cost,Supplier,Certification,Market,Tips,FAQ
Custom injection molded plastics are a widely used manufacturing process in which molten plastic material is injected into a mold cavity. This process allows for the production of complex and intricately shaped plastic products. In this guide, we will explore various aspects of custom injection molded plastics.
Quality is a crucial factor in custom injection molded plastics. High-quality molds ensure precision and consistency in the final products. Designs should be thoroughly inspected and tested to ensure they meet the required specifications. Quality control measures, such as regular inspections and stringent testing, should be implemented throughout the manufacturing process.
Cost is another important consideration. The cost of custom injection molded plastics depends on factors like material selection, mold design and production volume. Different materials have varying costs, and the complexity of the mold design and size affect costs too. Manufacturers should work closely with customers to determine the most cost-effective options.
Finding a reliable supplier is imperative in the custom injection molded plastics industry. Supplier reputation, experience, and technical capabilities are key factors to consider. Ensure they have a skilled and experienced team, state-of-the-art equipment, and a proven track record of delivering high-quality products on time.
Certification plays a crucial role in guaranteeing product quality and adherence to industry standards. Suppliers should hold certifications, such as ISO 9001, to demonstrate their commitment to quality management systems.
The market for custom injection molded plastics is vast. Industries such as automotive, electronics, medical, and packaging heavily rely on these products. The market is expected to grow further due to increasing demand for lightweight and durable plastic components.
Here are some useful tips for custom injection molded plastics: collaborate closely with suppliers for design optimization, choose the right materials for cost efficiency and functionality, prioritize quality control throughout the production process, and regularly update yourself with the latest industry trends and technological advancements.
Finally, a FAQ section addresses common queries. This may cover topics such as mold design and customization, material selection, production lead times, and pricing structures.
In conclusion, custom injection molded plastics are an integral part of various industries, offering versatility, precision, and cost-effective solutions. By understanding the key aspects mentioned in this guide, one can navigate the complexities of this manufacturing process successfully.
Types of custom injection molded plastics
Custom injection molding is a versatile manufacturing process that allows the production of a wide range of plastic components. There are numerous types of custom injection molded plastics available, each with its unique properties and applications. Here are some common types:
1. Acrylonitrile Butadiene Styrene (ABS): ABS is a widely used thermoplastic known for its strength, durability, and impact resistance. It is commonly used in automotive parts, electronic housings, and consumer goods.
2. Polypropylene (PP): PP is a versatile plastic with excellent chemical resistance, low density, and high stiffness. It is often used in packaging, automotive components, and medical devices.
3. Polyethylene (PE): PE is a lightweight, flexible plastic with excellent chemical resistance and moisture resistance. It is used in various applications, including packaging films, containers, and pipes.
4. Polyvinyl Chloride (PVC): PVC is a highly durable and cost-effective plastic that is resistant to weathering and chemicals. It is commonly used in construction, electrical insulation, and medical tubing.
5. Polycarbonate (PC): PC is a transparent plastic with high impact strength and heat resistance. It finds applications in safety glasses, electronics, and automotive components.
6. Nylon (PA): Nylon is a strong and wear-resistant plastic ideal for applications requiring high mechanical strength and good lubricity. It is commonly used in gears, bearings, and electrical connectors.
7. Thermoplastic Elastomers (TPE): TPEs are a class of versatile materials that combine the properties of rubber and plastic. They find applications in soft-touch grips, seals, and gaskets.
8. Polyethylene Terephthalate (PET): PET is a lightweight and transparent plastic commonly used in beverage bottles, food packaging, and textile fibers.
9. Polystyrene (PS): PS is a rigid and affordable plastic with good insulation properties. It is used in packaging, disposable cutlery, and insulation boards.
10. Polyoxymethylene (POM): POM, also known as acetal, is a strong and rigid plastic with excellent dimensional stability. It is used in precision gears, conveyor belts, and plumbing fittings.
These are just a few examples of the types of custom injection molded plastics available. Each plastic type has its specific advantages, making it suitable for different applications across various industries. The choice of material depends on factors like desired properties, cost-effectiveness, aesthetics, and regulatory requirements.
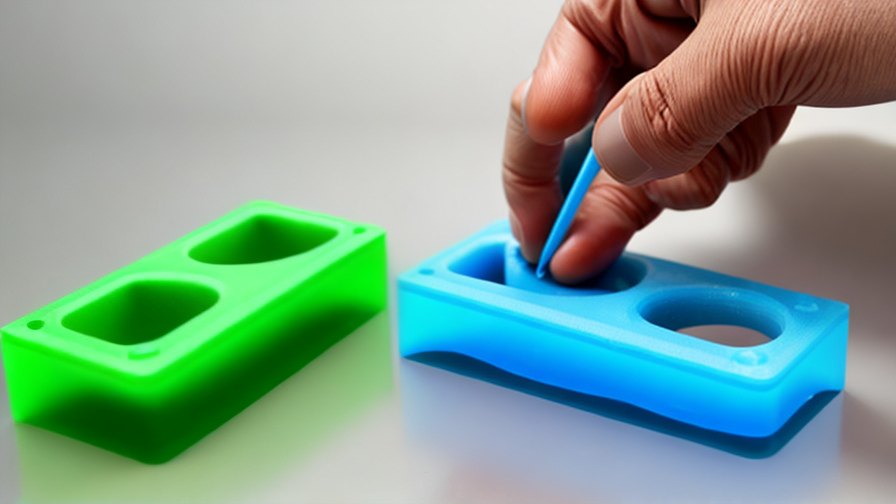
Pros and Cons of Using custom injection molded plastics
Custom injection molded plastics offer several advantages and disadvantages.
One of the primary pros of using custom injection molded plastics is cost-effectiveness. The process allows for high-volume production at a relatively lower cost per unit, making it suitable for large-scale manufacturing. Additionally, since injection molding is a highly automated process, it reduces labor costs compared to other techniques.
Another advantage is the versatility and design flexibility offered by custom injection molded plastics. This manufacturing method allows for intricate and complex shapes to be produced with precision. It enables the incorporation of various features, such as threads, hinges, undercuts, and graphics, directly into the molded part, eliminating the need for additional assembly steps.
Furthermore, custom injection molding offers excellent part repeatability and consistency. The process ensures uniformity in each produced item, reducing variations and defects. This makes injection molded plastics highly reliable for applications where consistency and dimensional accuracy are crucial.
However, there are also some cons associated with custom injection molded plastics. One of the major drawbacks is the initial tooling cost. The creation of molds can be expensive, especially for complex designs or unique shapes. Therefore, it may not be financially viable for small-scale productions or short runs.
Additionally, custom injection molding may have longer lead times, especially during the mold creation phase. The design, production, and testing of molds can take a significant amount of time before the actual production of parts can begin. As a result, injection molding may not be suitable for urgent or time-sensitive projects.
Moreover, the material selection for custom injection molded plastics may be limited. While many thermoplastic materials are compatible with injection molding, not all polymers can be processed using this technique. Some specialized or high-temperature materials may require alternative manufacturing methods.
In conclusion, custom injection molded plastics offer cost-effectiveness, design versatility, and consistent part quality. However, the initial tooling cost, longer lead times, and limited material selection should also be considered when deciding whether to use this manufacturing method.
custom injection molded plastics Reference Specifications (varies for different product)
Reference Specifications for Custom Injection Molded Plastics (Varies for Different Products)
1. Material: The choice of material for custom injection molded plastics depends on the desired properties such as strength, flexibility, chemical resistance, and temperature stability. Commonly used materials include thermoplastics like polyethylene (PE), polypropylene (PP), polystyrene (PS), polyvinyl chloride (PVC), and engineering resins like acrylonitrile butadiene styrene (ABS), polycarbonate (PC), and nylon.
2. Dimensions: The specifications for custom injection molded plastics should include the desired dimensions of the product. This includes the length, width, and height of the part, as well as any specific tolerances that need to be met.
3. Wall Thickness: The wall thickness of the custom injection molded plastics is an important consideration to ensure structural integrity and proper filling during the injection molding process. The thickness should be specified based on the material and the application requirements.
4. Surface Finish: The desired surface finish for the custom injection molded plastics should be specified. It can range from a smooth, polished surface to a textured or matte finish depending on the aesthetic and functional requirements of the product.
5. Color: The color of the custom injection molded plastics can be chosen based on the desired appearance or for specific identification purposes. It is important to specify the color accurately, either by referencing a standard color system (such as Pantone or RAL) or by providing a physical sample.
6. Inserts and Overmolding: If the product requires inserts or overmolding, it should be clearly specified. This includes any metal or plastic inserts that need to be incorporated into the molded part or additional materials for two-shot or multi-shot molding processes.
7. Strength and Performance Requirements: Any specific strength, rigidity, or performance requirements should be outlined. This can include load-bearing capacity, resistance to impact or environmental factors, as well as compliance with industry standards or certifications.
8. Quantity: The desired quantity of custom injection molded plastics should be indicated, as it can affect the selection of the molding process (such as mass production or rapid prototyping), tooling requirements, and production timelines.
9. Regulatory Compliance: If the product needs to comply with specific regulations or standards (such as RoHS, REACH, or FDA regulations), these requirements should be stated to ensure the materials and manufacturing processes meet the necessary criteria.
10. Packaging and Shipping: The packaging and shipping requirements, including any specific packaging materials, labeling, or handling instructions, should be provided to ensure safe delivery of the custom injection molded plastics.
It is important to note that these specifications may vary depending on the specific product and application. Custom injection molded plastics offer a wide range of possibilities, and collaborating with a trusted manufacturer or supplier can help to ensure the specifications meet the intended purpose and requirements.
Applications of custom injection molded plastics
Custom injection molded plastics have a wide range of applications in various industries, due to their versatility, durability, and cost-effectiveness. Here are some key applications of these plastics:
1. Automotive Industry: Injection molded plastics are extensively used in the automotive industry for various components such as dashboards, interior trims, door panels, instrument panels, and exterior parts like bumpers and grilles. These plastics provide design flexibility, weight reduction, and improved efficiency in manufacturing.
2. Medical Industry: Custom injection molded plastics play a significant role in the medical sector. They are used to produce a variety of medical devices and equipment, including surgical instruments, drug delivery devices, diagnostic equipment, and disposable medical supplies like syringes and vials. These plastics offer excellent sterilization properties, biocompatibility, and precision manufacturing capabilities.
3. Consumer Products: Injection molded plastics are widely utilized in the production of consumer products. This includes items such as toys, kitchenware, electronic enclosures, packaging materials, and cosmetic containers. The ability to create intricate designs, color variations, and lightweight products makes injection molded plastics the preferred choice for many consumer goods.
4. Electronics Industry: The electronics industry heavily relies on custom injection molded plastics for the production of electronic components and housing. These plastics provide exceptional insulation properties, dimensional stability, and resistance to heat and chemicals. They are commonly used for manufacturing connectors, sockets, switches, enclosures, and other electronic device components.
5. Aerospace Industry: The aerospace industry utilizes injection molded plastics to produce lightweight and high-performance parts. These parts include air ducts, brackets, interior fixtures, and structural components. The benefits of using injection molded plastics in aerospace applications include weight reduction, enhanced fuel efficiency, and cost-effectiveness compared to traditional metal components.
6. Industrial Equipment: Injection molded plastics find applications in various industrial equipment, ranging from machinery components to safety devices. These plastics offer resistance to extreme temperatures, corrosion, and impact, making them suitable for manufacturing gears, bearings, valves, conveyor components, and safety guards.
In summary, the applications of custom injection molded plastics are vast and varied across industries such as automotive, medical, consumer products, electronics, aerospace, and industrial equipment. The ability to produce complex shapes, cost-effectiveness, and material properties make these plastics a preferred choice for many manufacturers seeking durable and functional solutions.
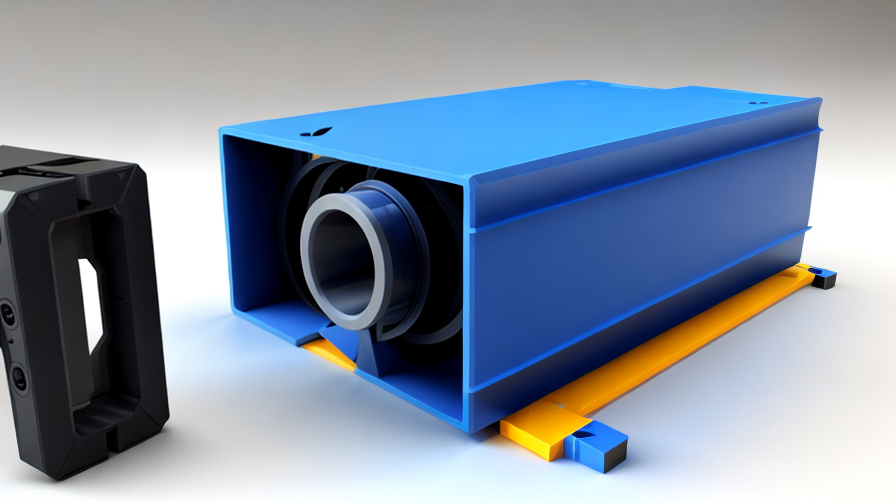
The Work Process and how to use custom injection molded plastics
The work process for using custom injection molded plastics involves several steps.
First, a design for the plastic part is created using CAD software. This design includes the shape, dimensions, and features of the desired part.
Next, a mold for the part is created. The mold is typically made from steel and consists of two halves that fit together. One half of the mold contains a cavity in the shape of the desired part, while the other half has a mechanism for injecting molten plastic into the cavity.
Once the mold is prepared, the plastic material is selected. Various types of plastics can be used for injection molding, including ABS, polypropylene, and polycarbonate. The plastic material is fed into a heated barrel and melted, forming a liquid resin.
The liquid resin is then injected into the mold cavity under high pressure. This pressure ensures that the resin completely fills the cavity and forms the desired shape. The resin is left to cool and solidify within the mold, which typically takes a few seconds to a few minutes depending on the size and complexity of the part.
After solidification, the mold is opened, and the newly formed plastic part is ejected. The part may require additional finishing processes such as trimming excess material or adding surface textures or colors.
Custom injection molded plastics offer several benefits over other manufacturing processes. Injection molding allows for high production volumes and fast cycle times, making it cost-effective for large-scale production. The process also enables the creation of complex shapes and intricate details with high precision and consistency.
In summary, the work process for using custom injection molded plastics involves designing the part, creating a mold, melting and injecting the plastic, cooling and solidifying the part, and adding finishing touches as required. This process allows for the efficient production of high-quality plastic parts with various shapes, sizes, and features.
Quality Testing Methods for custom injection molded plastics and how to control the quality
Quality testing methods for custom injection molded plastics include visual inspection, dimensional measurement, mechanical testing, and material analysis. Visual inspection involves examining the surface of the molded plastic for any defects, such as cracks, bubbles, or warping. This can be performed manually or with the help of automated systems that can detect and categorize defects based on predefined criteria.
Dimensional measurement is done to ensure that the molded parts comply with the required specifications. This can be achieved using tools like calipers, gauges, coordinate measuring machines (CMM), or optical measurement systems. It verifies critical dimensions such as length, width, height, and tolerances.
Mechanical testing involves subjecting the molded plastic parts to various forces, pressures, or stresses to assess their strength and durability. This can include tests like tensile strength, impact resistance, fatigue testing, or flexural testing. These tests help determine if the parts can withstand the intended use and meet the performance requirements.
Material analysis is essential to ensure that the injection molded plastic is made from the correct material and that the material properties meet the required specifications. Techniques like Fourier transform infrared spectroscopy (FTIR), differential scanning calorimetry (DSC), or melt flow index (MFI) testing are used to analyze the material composition, thermal characteristics, or flow properties.
To control the quality of custom injection molded plastics, several steps can be taken. Firstly, a comprehensive quality management system should be established, including documented quality control procedures and standards. The manufacturing process should be closely monitored and controlled, with regular inspections and tests at different stages, from raw material verification to final product inspection.
Implementing statistical process control (SPC) techniques can help identify and address any process variations or deviations that may impact the quality of the molded plastics. This involves collecting and analyzing data from the manufacturing process to detect trends or patterns that could lead to defects or inconsistencies.
Regular training programs for employees should be conducted to ensure they understand the quality requirements and can perform their tasks effectively. Additionally, feedback from customers or end-users should be gathered to identify any issues or concerns and to continuously improve the quality of the injection molded plastics.
Through a combination of rigorous testing methods and effective quality control measures, manufacturers can ensure the production of high-quality custom injection molded plastics that meet customer expectations and industry standards.
custom injection molded plastics Sample Policy and Post-Purchase Considerations for custom injection molded plastics from China
Sample Policy:
When it comes to custom injection molded plastics from China, it is important to establish a clear sample policy with the supplier. This policy should outline the terms and conditions regarding the production and delivery of product samples.
The first step in the sample policy is to establish the cost and payment terms for samples. It is common for customers to bear the cost of the samples, including shipping fees. The supplier may refund or credit the sample cost if an order is eventually placed.
Next, the sample lead time should be clearly stated to ensure both parties have a clear understanding of the production timeline. This includes the production time, as well as the time it takes for the samples to be delivered to the customer.
It is essential to define the specifications and expectations for the samples. This can include details such as material type, color, size, and any specific features or finishes required. This will avoid any misunderstandings or discrepancies in the final product.
Finally, the sample policy should outline the communication process between the customer and the supplier during the sample production stage. Regular updates and feedback should be provided to ensure the samples meet the customer’s requirements.
Post-Purchase Considerations:
Once the custom injection molded plastics have been purchased from China, there are several post-purchase considerations to keep in mind.
Firstly, it is important to review the quality of the final product upon delivery. Thoroughly inspect the injection molded parts to ensure they meet the agreed-upon specifications. Any defects or discrepancies should be promptly communicated to the supplier for resolution.
Communication with the supplier should continue even after the purchase. Maintaining an open line of communication is crucial for addressing any post-purchase issues that may arise. Timely responses and effective problem-solving will help maintain a healthy business relationship.
Regularly evaluate the performance and durability of the injected molded plastics. Assess whether they meet the intended purpose and if any modifications or improvements need to be made for future orders.
Consider monitoring the supplier’s production processes and practices to ensure they maintain consistent quality standards. Regular audits or inspections can help identify any potential issues or deviations from the agreed-upon quality.
Lastly, document any post-purchase considerations, including feedback, issues, and resolutions. This will help in future negotiations and ensure a smoother process for subsequent orders.
By establishing a clear sample policy and considering these post-purchase factors, customers can navigate the custom injection molded plastics market in China more effectively and efficiently.
Sourcing custom injection molded plastics from China: Opportunities, Risks, and Key Players
Sourcing custom injection molded plastics from China can offer both opportunities and challenges for businesses. One of the main advantages is the cost-effectiveness of production in China, as labor and manufacturing costs tend to be lower compared to other countries. This can result in significant cost savings, making it an attractive option for businesses looking to manufacture plastic components or products.
Moreover, China has a well-established and efficient supply chain ecosystem for plastic injection molding. The country has a vast network of manufacturers, designers, and mold makers with extensive experience in producing custom plastic parts. This allows businesses to have access to a wide range of options in terms of materials, colors, sizes, and shapes for their products.
However, there are some risks associated with sourcing custom injection molded plastics from China. Quality control can be a major concern, as not all manufacturers prioritize high-quality production. Working with a reliable and reputable supplier is crucial to ensure that the end products meet the required standards and specifications.
Another risk is intellectual property (IP) protection. China has faced criticism for its lax enforcement of IP rights, and there have been instances of counterfeiting and unauthorized production of patented products. It is essential for businesses to have proper legal protections in place and work with suppliers who are committed to respecting IP rights.
When it comes to key players in the custom injection molding industry in China, there are numerous manufacturers and suppliers to choose from. Some well-known companies include China Plastic Injection Molding, HQMOULD, Sositar Mould, and 3ERP. It is important to conduct research and due diligence to select a supplier that aligns with a business’s specific requirements and can offer reliable production and timely delivery.
Overall, sourcing custom injection molded plastics from China provides significant opportunities for cost savings and a wide range of options. However, it is essential to carefully consider the risks associated with quality control and IP protection and choose reliable suppliers to ensure a successful sourcing experience.
How to find and select reliable custom injection molded plastics manufacturers in China,use google search manufacturers and suppliers
Finding and selecting reliable custom injection molded plastics manufacturers in China requires careful research and evaluation. One effective method is to use Google search and follow these steps:
1. Begin by typing in relevant keywords such as “custom injection molded plastics manufacturers China” or specific product requirements in the Google search bar.
2. Review the search results and visit the websites of potential manufacturers. Look for companies that specialize in plastic injection molding and have a strong presence and credibility.
3. Pay attention to the manufacturer’s website design, content quality, and professionalism. Reputable manufacturers usually invest in presenting their capabilities, certifications, factory information, and product details clearly and comprehensively.
4. Look for certifications and quality standards such as ISO 9001, TS 16949, or ISO 13485. These certifications indicate that the manufacturer adheres to strict quality control processes and provides consistent product quality.
5. Explore their production capabilities, including the range of molds they can produce, the raw materials they use, the machinery and technology they employ, and any customization options available.
6. Check their past project portfolio or case studies to assess their experience and expertise. Look for relevant industries or applications that match your requirements.
7. Verify their credibility and reputation by searching for online reviews, testimonials, or feedback from other customers. Engage in forums or social media platforms to gather information and insights about their reputation.
8. Contact the manufacturers directly and inquire about their services, production capacity, lead times, and pricing models. Professional and reliable manufacturers should respond promptly with detailed answers and provide clear communication throughout the process.
9. Request samples or prototypes to evaluate the manufacturer’s product quality, finishing, and accuracy. This step can help you assess if their capabilities align with your expectations.
10. Consider visiting the factories or arranging video conferences to have a better understanding of their production facilities, quality control processes, and to establish personal connections.
Ultimately, the key to finding and selecting reliable custom injection molded plastics manufacturers in China lies in conducting thorough research, evaluating their capabilities and reputation, requesting samples, and maintaining clear communication throughout the process.
How to check custom injection molded plastics manufacturers website reliable,use google chrome SEOquake check if ranking in top 10M
To determine the reliability of a custom injection molded plastics manufacturer’s website, you can follow these steps:
1. Use Google Chrome: Open the manufacturer’s website using Google Chrome browser, as it offers various SEO tools and extensions that can assist in evaluating a website’s reliability.
2. Install SEOquake Extension: Add the SEOquake extension to your Chrome browser. This powerful SEO tool provides crucial insights about a website’s ranking, traffic, and other relevant details.
3. Check the Website’s Alexa Rank: Once the SEOquake extension is installed, activate it by clicking on its icon in the toolbar. Look for the website’s Alexa Rank, which provides an indication of the website’s popularity and traffic. Websites with lower Alexa ranks generally receive higher traffic and have a good online presence.
4. Analyze Organic Traffic: SEOquake also shows the estimated monthly organic traffic for a website. Check the organic traffic figure to determine if the manufacturer’s website is attracting a good number of visitors. Higher organic traffic suggests that the website is valuable and trusted by users, indicating reliability.
5. Verify Search Engine Rankings: SEOquake can also display the website’s search engine rankings. Check if the manufacturer’s website ranks within the top 10 million search results on Google. This indicates that the website has established a certain level of online visibility and is more likely to be reliable.
6. Assess Website Design and Content: While evaluating the website’s reliability, also consider its design and content. A professional and well-designed website with clear information about their products, certifications, quality control processes, and customer testimonials can indicate a trustworthy manufacturer.
7. Consider Communication Channels: Reliable manufacturers often provide multiple ways to contact them, such as phone numbers, email addresses, contact forms, or live chat options. Check if the website offers these channels to ensure easy communication.
Remember, in addition to these steps, it is always recommended to conduct thorough research on the manufacturer, read reviews from previous customers, and check their certifications to make an informed decision.
Top 10 custom injection molded plastics manufacturers in China with each 160 words introduce products,then use markdown create table compare
1. Win Industry Company: Win Industry specializes in custom injection molding for a wide range of industries, including automotive, electronics, and packaging. Their product line includes plastic containers, electrical connectors, and automotive parts. With advanced facilities and a team of experienced engineers, they are able to provide high-quality molded plastic products.
2. Dongguan Riteng Industrial: Dongguan Riteng offers custom injection molding solutions for various industries like automotive, medical, and electronics. Their product portfolio includes plastic parts for automotive interiors, medical equipment, and electrical appliances. They are known for their precision molding technology and efficient production processes.
3. Xiamen Stick Industry: Xiamen Stick Industry is a leading manufacturer of custom injection molded plastics, serving industries such as electronics, packaging, and household appliances. Their product line includes plastic enclosures, covers, and components. They are known for their expertise in tooling design and production, ensuring high-quality and cost-effective solutions.
4. Realhao Precision: Realhao Precision specializes in custom injection molding for consumer electronics, automotive, and medical industries. Their product range includes plastic components, housings, and connectors. With ISO 9001 certification, they strive to provide durable and precise mold designs and injection molding processes.
5. Ningbo Haishu Lijing Plastic Electrical Appliance: Ningbo Haishu Lijing is a leading manufacturer of custom injection molded plastics in China. They offer a wide range of products, including plastic parts for electrical appliances, automotive components, and home appliances. With a strong focus on innovation and quality, they have gained recognition from international clients.
6. Shanghai WWA Moulding: Shanghai WWA Moulding is a renowned manufacturer of custom injection molded plastics, serving industries such as automotive, electronics, and medical. They provide solutions for plastic enclosures, connectors, and various components. With a state-of-the-art facility and advanced technologies, they ensure precise and efficient production processes.
7. HKY Mould: HKY Mould specializes in custom injection molding for industries like automotive, medical, and consumer electronics. Their product line includes plastic parts, enclosures, and components. With a dedicated team of engineers and advanced equipment, they offer high-quality and cost-effective solutions.
8. Topworks Plastic Mold: Topworks Plastic Mold is a leading manufacturer of custom injection molded plastics, serving industries such as automotive, electronics, and packaging. They provide solutions for plastic components, enclosures, and packaging materials. With a focus on precision and durability, they have established long-term partnerships with clients worldwide.
9. Foshan Mogel Hardware and Plastic: Foshan Mogel specializes in custom injection molding for various industries like automotive, electronics, and furniture. Their product line includes plastic parts, knobs, and handles. They are known for their expertise in plastic mold design and production, ensuring high-quality and efficient manufacturing processes.
10. Plastocon China: Plastocon China offers custom injection molded plastics for industries like automotive, electronics, and consumer goods. They provide solutions for plastic components, enclosures, and packaging materials. With a focus on innovation and sustainability, they aim to deliver eco-friendly and cost-effective solutions.
| Manufacturer | Industries Served | Product Range |
|——————————-|———————|————————————————————————————————-|
| Win Industry Company | Automotive, Electronics, Packaging | Plastic containers, Electrical connectors, Automotive parts |
| Dongguan Riteng Industrial | Automotive, Medical, Electronics | Plastic parts for automotive interiors, Medical equipment, Electrical appliances |
| Xiamen Stick Industry | Electronics, Packaging, Household Appliances | Plastic enclosures, Covers, Components |
| Realhao Precision | Consumer Electronics, Automotive, Medical | Plastic components, Housings, Connectors |
| Ningbo Haishu Lijing Plastic Electrical Appliance | Electrical Appliances, Automotive, Home Appliances | Plastic parts for electrical appliances, Automotive components, Home appliances |
| Shanghai WWA Moulding | Automotive, Electronics, Medical | Plastic enclosures, Connectors, Components |
| HKY Mould | Automotive, Medical, Consumer Electronics | Plastic parts, Enclosures, Components |
| Topworks Plastic Mold | Automotive, Electronics, Packaging | Plastic components, Enclosures, Packaging materials |
| Foshan Mogel Hardware and Plastic | Automotive, Electronics, Furniture | Plastic parts, Knobs, Handles |
| Plastocon China | Automotive, Electronics, Consumer Goods | Plastic components, Enclosures, Packaging materials |
Background Research for custom injection molded plastics manufacturers Companies in China, use qcc.com archive.org importyeti.com
When looking for custom injection molded plastics manufacturers in China, there are several resources that can be utilized to gather background research. Three useful platforms are qcc.com, archive.org, and importyeti.com.
QCC.com is a popular Chinese business database that provides information on various companies registered in China. It allows users to search for specific company names and provides details such as the company’s registration number, business scope, registered capital, and contact information. This platform can be helpful in verifying the legitimacy and basic information of custom injection molded plastics manufacturers in China.
Archive.org is a valuable tool that allows users to access archived versions of websites. This can be useful when researching companies’ websites or online presence. By typing in the URL of a specific custom injection molded plastics manufacturer’s website, users can view previous versions of the site, allowing them to track any changes in the company’s history, offerings, and credibility over time. Archive.org can provide insight into a company’s past performance, product catalog, and overall online presence.
Importyeti.com is a platform specifically designed to help users find suppliers in China. It provides a database of import and export records, allowing users to search for specific products, such as custom injection molded plastics, and track which companies have been involved in their production and export. Importyeti.com can provide valuable information on the capacity, experience, and track record of various manufacturers, enabling potential buyers to assess their suitability.
Gathering information from these three sources can be a comprehensive way to conduct background research on custom injection molded plastics manufacturers in China. While qcc.com provides basic company information and registry details, archive.org offers insights into a company’s history and online presence. Importyeti.com complements the research process by providing data on a manufacturer’s export activity, allowing buyers to assess their credibility and experience within the industry.
Leveraging Trade Shows and Expos for custom injection molded plastics Sourcing in China
Trade shows and expos are excellent opportunities for sourcing custom injection molded plastics in China. These events bring together manufacturers, suppliers, and industry professionals from around the world, providing a platform for networking, knowledge sharing, and business development.
Attending trade shows and expos allows buyers to connect with multiple suppliers in one location, saving time and effort in the sourcing process. In the case of custom injection molded plastics, these events provide access to a wide range of Chinese manufacturers specializing in this field. Buyers can interact with exhibitors, view product samples, and discuss specific requirements face to face.
One key advantage of attending trade shows and expos is the ability to evaluate the quality and capabilities of potential suppliers. The ability to see and touch product samples gives buyers a better understanding of the manufacturers’ capabilities and helps in assessing their ability to meet specific design criteria and quality standards. This direct interaction also allows buyers to discuss customization options, pricing, lead times, and other critical aspects of the sourcing process.
Furthermore, trade shows and expos often feature industry-specific seminars, workshops, and presentations where buyers can learn about the latest trends, technologies, and best practices in custom injection molding. This knowledge can be invaluable in identifying innovative solutions and staying ahead of the competition.
To maximize the benefits of trade shows and expos, it is essential to plan ahead and set clear objectives. Buyers should research the exhibitor list and identify potential suppliers that meet their requirements. It is also important to schedule meetings in advance to ensure dedicated time with each supplier. Following up after the event is crucial for maintaining relationships and negotiating contracts.
In conclusion, leveraging trade shows and expos for sourcing custom injection molded plastics in China provides a unique opportunity to connect with a wide range of manufacturers, evaluate their capabilities, and stay updated with industry trends. The personal interaction and access to product samples make these events invaluable for successful sourcing in this sector.
The Role of Agents and Sourcing Companies in Facilitating custom injection molded plastics Purchases from China
Agents and sourcing companies play a crucial role in facilitating custom injection molded plastics purchases from China. These intermediaries act as a bridge between buyers and manufacturers, ensuring a seamless and efficient procurement process.
One of the key responsibilities of agents and sourcing companies is supplier identification and validation. They have extensive networks and knowledge of the Chinese manufacturing landscape, allowing them to connect buyers with reputable and reliable manufacturers of custom injection molded plastics. Through thorough vetting and assessment, these intermediaries ensure that buyers are connected with manufacturers that meet their specific requirements in terms of quality, pricing, and capacity.
Furthermore, agents and sourcing companies assist buyers throughout the entire purchasing process. They help negotiate favorable pricing and contractual terms with manufacturers, ensuring that buyers achieve the best value for their investments. These intermediaries also manage the logistics and coordination aspects of the procurement process, including quality control, sampling, production monitoring, and shipping arrangements. By handling these complex tasks, agents and sourcing companies streamline the procurement process, saving buyers both time and effort.
Agents and sourcing companies also play a critical role in mitigating risks associated with sourcing from China. They have a deep understanding of local market conditions, regulations, and cultural nuances, helping buyers navigate potential pitfalls and challenges. This expertise is especially important when dealing with customs, tariffs, and compliance issues, ensuring that buyers can import their custom injection molded plastics smoothly and with minimal delays.
In summary, agents and sourcing companies are indispensable in facilitating custom injection molded plastics purchases from China. Their vast networks, industry knowledge, and expertise enable buyers to connect with reputable manufacturers, negotiate favorable terms, and navigate the complexities of international procurement. By leveraging these intermediaries, buyers can streamline their purchasing process, reduce risks, and ultimately achieve successful and cost-effective procurement outcomes.
Price Cost Research for custom injection molded plastics manufacturers Companies in China, use temu.com and 1688.com
When it comes to sourcing custom injection molded plastics manufacturers in China, two popular online platforms are TEMU.com and 1688.com. These platforms provide a wide range of options for businesses looking to find reliable suppliers and obtain competitive pricing for their manufacturing needs.
TEMU.com is a B2B platform that connects global buyers with verified Chinese manufacturers. It offers a user-friendly interface and a variety of features to simplify the sourcing process. With its extensive database of suppliers, TEMU.com allows businesses to search for manufacturers specializing in custom injection molding, ensuring that specific requirements are met. The platform also provides detailed product information, company profiles, and customer reviews, enabling buyers to make informed decisions.
On the other hand, 1688.com is a Chinese B2B e-commerce platform owned by Alibaba Group. It is predominantly used by domestic buyers but is increasingly popular among international businesses due to the large number of Chinese suppliers available. The site allows users to search for custom injection molded plastics manufacturers and provides detailed product listings, including specifications, prices, and MOQs (minimum order quantities). 1688.com offers a direct communication channel with suppliers, allowing buyers to negotiate prices and discuss customization options.
To conduct price cost research on TEMU.com and 1688.com, it is essential to enter relevant keywords and filters to narrow down the search results. For example, specifying the desired material, product specifications, production volume, and quality standards can help obtain more accurate pricing information. It is advisable to compare prices and minimum order quantities from multiple suppliers to ensure getting the best deal while maintaining quality standards.
In conclusion, TEMU.com and 1688.com are valuable online platforms for conducting price cost research for custom injection molded plastics manufacturers in China. These platforms not only provide access to a vast supplier database but also offer essential information, product details, and direct communication channels, facilitating the sourcing and negotiation process. By leveraging these platforms, businesses can find reliable suppliers and obtain competitive pricing, ultimately enhancing their supply chain efficiency.
Shipping Cost for custom injection molded plastics import from China
When importing custom injection molded plastics from China, the shipping cost is influenced by several factors. The first aspect to consider is the volume or weight of the shipment. Larger or heavier goods will incur higher shipping costs compared to smaller or lighter ones. Additionally, the distance between the supplier in China and the destination country is another factor affecting shipping costs.
There are different transportation options available, including air freight, sea freight, and railway transportation. Air freight is the fastest but most expensive option. It is suitable for urgent orders or small-sized shipments. On the other hand, sea freight is cost-effective for larger quantities of goods. However, it takes longer to transport the products. Railway transportation can be considered as a middle ground, providing a balance between cost and speed, especially for landlocked countries.
In terms of the specific cost, it is difficult to provide an exact figure without knowing the shipment details, such as the size, weight, and destination. Nonetheless, various charges contribute to the overall shipping cost, including freight charges, handling fees, customs duties, insurance, and documentation fees. It is recommended to obtain quotations from different shipping providers or freight forwarders to compare prices and choose the most suitable option based on the shipment’s requirements.
To keep shipping costs low, it is advisable to optimize the packaging to minimize dimensions and weight while ensuring the safety of the products. Consolidating multiple orders into one shipment or utilizing the services of a freight forwarder who specializes in China imports can also help reduce costs. Finally, staying informed about any applicable customs regulations and ensuring proper documentation can prevent additional charges at the destination port.
In conclusion, the shipping cost for importing custom injection molded plastics from China depends on various factors, such as the size and weight of the shipment, transportation mode, distance, and associated charges. Optimizing packaging, consolidating orders, and understanding customs regulations can help keep shipping costs within budget.
Compare China and Other custom injection molded plastics Markets: Products Quality and Price,Visible and Hidden Costs
China is known as the world’s largest producer and exporter of custom injection molded plastics. Its vast manufacturing capabilities have helped it establish a dominant position in the market compared to other countries. One key aspect when comparing China’s custom injection molded plastics market to others is the quality of products.
Chinese manufacturers have made substantial progress in improving the quality of their injection molded products. They have invested in advanced technology and production processes, resulting in products that meet international standards. However, it is important to note that quality can vary across manufacturers. While some Chinese companies offer high-quality products, others may not meet the same standards. On the other hand, the products from other markets may also have varying quality levels.
Price is another significant factor when considering China’s custom injection molded plastics market against other markets. China is often associated with low-cost manufacturing, which can be attributed to its lower labor and production costs compared to countries like the United States or Germany. However, price competitiveness can vary depending on the specific product and order quantity. Other markets may have higher production costs, leading to relatively higher prices.
When discussing visible and hidden costs, China’s market has its advantages and challenges. Visible costs such as material, labor, and tooling costs are generally lower in China, contributing to its competitive pricing. However, there are hidden costs that customers should consider, such as potential shipping delays, communication barriers, intellectual property risks, and quality control issues. These hidden costs can impact the overall cost-effectiveness of sourcing from China.
In summary, China’s custom injection molded plastics market offers competitive quality and pricing compared to other markets. While China has made significant strides in improving product quality, there can still be variations across manufacturers. The country’s lower production costs contribute to its price advantage but hidden costs should also be considered. Evaluating the specific needs of the project and conducting thorough due diligence is crucial when comparing the custom injection molded plastics market in China to other markets.
Understanding Pricing and Payment Terms for custom injection molded plastics: A Comparative Guide to Get the Best Deal
When it comes to acquiring custom injection molded plastics, understanding pricing and payment terms is crucial to ensure getting the best deal. This comparative guide aims to shed light on these aspects, providing valuable insights in less than 300 words.
Pricing for custom injection molded plastics typically depends on several factors. The complexity of the part design, the required mold tooling, the quantity of parts needed, and the chosen material all play a role in determining the price. High complexity designs or intricate molds can drive up costs, while larger quantities often lead to per-unit price reductions. The choice of material is also important, as different plastics have varying costs.
Payment terms for custom injection molded plastics can vary among suppliers. Common payment methods include upfront payment, milestone payments, or a combination of both. Upfront payment requires paying the full amount before production begins, while milestone payments involve dividing the project into stages and paying accordingly. Alternatively, some suppliers offer flexible payment plans, allowing for a percentage of the payment upfront and the rest upon delivery or over a specified timeframe.
To secure the best deal, it is advisable to request quotes from multiple suppliers. By comparing prices, payment terms, and the overall value offered, one can determine the most favorable option. It is important to consider not only the pricing but also the supplier’s reputation, quality of their products, lead times, and customer service.
Additionally, negotiating with suppliers can help achieve better pricing and payment terms. Some suppliers may be open to adjusting their prices or offering discounts for larger orders. Building a strong, long-term relationship with a reputable supplier can also lead to more favorable pricing and payment conditions.
In conclusion, understanding pricing and payment terms for custom injection molded plastics is essential to secure the best deal. Considering factors such as part complexity, mold requirements, material choice, and quantities can help estimate pricing accurately. Exploring various payment options, comparing quotes, and negotiating with suppliers can further enhance the outcome. By following this comparative guide, customers can navigate the pricing and payment landscape effectively and obtain highly cost-effective custom injection molded plastics.
Chinese Regulations and Industry Standards Certifications for custom injection molded plastics,Import Regulations and Customs for custom injection molded plastics from China
China has several regulations and industry standards certifications in place for custom injection molded plastics. These regulations ensure product safety, quality control, and environmental protection. The following certifications are commonly required:
1. ISO 9001: This certification ensures that the manufacturer has implemented a quality management system to consistently provide products that meet customer and regulatory requirements.
2. ISO 14001: This certification ensures that the manufacturer has an effective environmental management system in place to minimize environmental impact and comply with relevant regulations.
3. RoHS: Restriction of Hazardous Substances Directive restricts the use of certain hazardous substances in electrical and electronic equipment. It ensures that custom injection molded plastics do not contain harmful materials.
4. REACH: Registration, Evaluation, Authorization, and Restriction of Chemicals is a regulation that applies to the use and production of chemicals. Custom injection molded plastics need to comply with REACH requirements to ensure the safety of consumers and workers.
5. UL94: Underwriters Laboratories 94 classifies plastic materials based on their flammability. Injection molded plastics must meet specific flammability ratings to ensure they are suitable for use in different applications.
When importing custom injection molded plastics from China, it is important to comply with import regulations and customs requirements. These regulations are country-specific and may vary, but some common considerations include:
1. Import duties and taxes: Understanding the applicable import duties and taxes is crucial for accurate costing and a smooth customs clearance process. Consult with a customs broker or research the rates beforehand.
2. Customs documentation: Prepare all necessary documentation for customs clearance, including commercial invoices, packing lists, bill of lading or airway bill, and any specific certificates required for the products.
3. Product compliance: Ensure that the custom injection molded plastics meet all necessary product safety and quality standards required by the importing country. This may involve obtaining relevant certifications or testing reports.
4. Packaging and labeling: Follow the importing country’s packaging and labeling regulations to ensure compliance. Proper labeling should include product descriptions, country of origin, and any other necessary information.
5. Import restrictions or permits: Some countries may have import restrictions or require specific import permits for certain types of products. Research the regulations of the importing country to ensure compliance.
By understanding and adhering to these regulations and requirements, importers can ensure the smooth importation of custom injection molded plastics from China.
Sustainability and Environmental Considerations in custom injection molded plastics Manufacturing
In the manufacturing industry, sustainability and environmental considerations are becoming increasingly important, particularly in the field of custom injection molded plastics. Injection molding is a widely used manufacturing process for producing high volumes of identical plastic components. However, the production of plastic materials and products can have significant environmental impacts, including the depletion of fossil fuel resources and the generation of plastic waste.
One key aspect of sustainability in custom injection molded plastics manufacturing is the choice of materials. Manufacturers are increasingly opting for bio-based or recycled plastics, which are derived from renewable sources or made from recycled plastic waste. These materials reduce the reliance on fossil fuels and minimize the overall environmental footprint of the production process.
Another important consideration is energy consumption. Injection molding requires a significant amount of energy for heating, melting, and shaping the plastic materials. Manufacturers are investing in energy-efficient machinery and technologies, such as electric injection molding machines, to minimize energy consumption and reduce greenhouse gas emissions associated with the manufacturing process.
Furthermore, waste management is crucial in ensuring sustainability in custom injection molded plastics manufacturing. By implementing recycling and waste reduction measures, manufacturers can minimize the amount of plastic waste generated during production. This can include reusing scrap materials, implementing closed-loop recycling systems, or partnering with recycling facilities to ensure proper disposal and recycling of waste materials.
Water conservation is also an important environmental consideration. Injection molding requires water for cooling the plastic materials and machinery. Manufacturers are adopting water-saving technologies, such as closed-loop cooling systems and water recycling, to minimize water consumption and reduce the strain on local water resources.
In conclusion, sustainability and environmental considerations are vital in custom injection molded plastics manufacturing. By choosing sustainable materials, optimizing energy consumption, implementing waste management strategies, and conserving water, manufacturers can minimize the environmental impact and promote a more sustainable manufacturing process. These efforts not only benefit the environment but also contribute to the growing demand for environmentally friendly and socially responsible products in the market.
List The Evolution history of “custom injection molded plastics”
Custom injection molded plastics have evolved significantly over the years, driven by technological advancements and changing customer needs. The history of this process can be traced back to the mid-19th century when plastics were first developed.
The early days of custom injection molding were marked by slow and labor-intensive processes. Initially, celluloid, a highly flammable material, was used as the raw material, limiting the applications of injection molded plastics. However, in the 1920s, the advent of more advanced thermoplastics, such as polyethylene and polypropylene, revolutionized the industry. These materials were safer and offered improved properties, making them suitable for a wider range of applications.
As the demand for plastic products increased in the mid-20th century, injection molding technology progressed. The 1950s saw the introduction of screw injection machines, which allowed for more precise control of the molding process. This innovation led to increased production efficiency and consistency in part quality.
In the 1960s, computer numerical control (CNC) machines were integrated into the injection molding process. CNC technology enabled better control of mold cavity pressure and temperature, resulting in higher-quality finished products. Additionally, the integration of automation in the 1970s further improved production speed and reduced labor costs.
The 1980s witnessed the development of advanced materials, such as engineering plastics, which brought even more options for custom injection molding. These materials offered enhanced mechanical properties, chemical resistance, and heat resistance, allowing for the production of parts for demanding applications.
In recent years, the industry has been focused on reducing environmental impact. Sustainable alternatives, like biodegradable and recycled plastics, have gained popularity. Additionally, advancements in design and modeling software have made it easier to create complex and precise molds, allowing for greater customization and innovation.
Today, custom injection molded plastics continue to evolve with the introduction of technologies like additive manufacturing (3D printing). 3D printing enables the rapid prototyping of molds, reducing lead times and costs. Furthermore, the integration of IoT (Internet of Things) in injection molding machines has improved process monitoring and optimization.
In conclusion, the evolution of custom injection molded plastics has been shaped by advancements in materials, machinery, automation, and sustainability. From the labor-intensive processes of the past to the high-precision, customizable manufacturing technologies of today, injection molded plastics have transformed numerous industries and continue to play a vital role in modern manufacturing.
The Evolution and Market Trends in custom injection molded plastics Industry
The custom injection molded plastics industry has undergone significant evolution and witnessed several market trends over the years. This industry involves the manufacturing of plastic parts through the process of injection molding, where molten plastic is injected into a mold and cooled to form a solid shape.
One major evolution in this industry is the advancement in technology and equipment used for injection molding. Automation and computer-aided design (CAD) have revolutionized the manufacturing process, making it faster, more efficient, and highly accurate. Computer numerical control (CNC) machines, robotics, and 3D printing have also played significant roles in shaping the industry.
Another evolution is the shift towards sustainable and eco-friendly manufacturing practices. With increasing environmental concerns, there has been a growing demand for biodegradable and recyclable plastics. Manufacturers are now focusing on using sustainable materials and implementing energy-efficient processes to reduce the carbon footprint of their operations.
In terms of market trends, one prominent trend is the increasing demand for lightweight and durable plastic products across various industries. Lightweight plastics are replacing traditional materials like metal and glass, offering better performance, cost-effectiveness, and design flexibility. This trend is particularly evident in industries such as automotive, consumer electronics, packaging, and healthcare.
Another trend is the growing customization in plastic parts. Consumers and businesses are seeking unique and personalized products, which has led to a rise in custom injection molding. Manufacturers are now capable of producing highly intricate and specific designs, enabling them to cater to individual specifications and requirements.
Additionally, the global market for custom injection molded plastics is witnessing significant growth due to factors like urbanization, industrialization, and rising disposable incomes. Emerging economies, particularly in Asia-Pacific, are experiencing high demand for plastic products, creating more opportunities for manufacturers in the custom injection molding industry.
In conclusion, the custom injection molded plastics industry has evolved through technological advancements and a growing focus on sustainability. Market trends include the demand for lightweight and durable plastic products, growing customization, and the expanding global market. These trends are expected to continue shaping the industry in the coming years.
Custom Private Labeling and Branding Opportunities with Chinese custom injection molded plastics Manufacturers
Chinese custom injection molded plastics manufacturers offer excellent opportunities for custom private labeling and branding. With their expertise and advanced manufacturing capabilities, these manufacturers can help businesses create unique and customized plastic products that bear the company’s branding and design.
Private labeling is a strategic approach that allows businesses to sell products under their own brand name, creating a sense of exclusivity among customers. Chinese manufacturers can provide the necessary support to ensure that the custom injection molded plastics product matches the brand’s image and values.
These manufacturers offer a wide range of options for customization. They can create custom molds based on the brand’s specifications, allowing businesses to have complete control over the product’s design and features. This includes selecting various colors, textures, finishes, and even adding logos or brand names directly on the plastic parts.
Moreover, Chinese manufacturers can help businesses incorporate branding elements such as embossing, engraving, or debossing to ensure the product’s appearance is aligned with the brand’s image. These branding opportunities contribute to enhancing product recognition and customer loyalty.
Additionally, Chinese manufacturers often offer flexible manufacturing quantities, allowing businesses to order small or large quantities of custom injection molded plastic products. This is beneficial for companies looking to start with smaller production runs or experimental marketing campaigns.
Working with Chinese custom injection molded plastics manufacturers for private labeling and branding provides businesses with cost-effective solutions. The competitive pricing in China, combined with high-quality manufacturing standards, enables businesses to establish their brand’s presence in the market without compromising on quality or their budget.
In conclusion, partnering with Chinese custom injection molded plastics manufacturers offers businesses the opportunity to create unique products that can be private labeled and branded. With their expertise, advanced manufacturing capabilities, and cost-effective solutions, these manufacturers enable businesses to stand out and build a strong brand presence in the market.
Tips for Procurement and Considerations when Purchasing custom injection molded plastics
When purchasing custom injection molded plastics, there are several key considerations that can help ensure a successful procurement process. Here are some tips to guide you through the process:
1. Define your requirements: Clearly understand your specific needs and requirements for the custom injection molded plastics. This includes the intended use, dimensions, desired material, color, and any specific technical specifications.
2. Choose a reliable supplier: Research and select a reputable supplier with a proven track record in producing high-quality custom injection molded plastics. Look for certifications, experience, and customer reviews to ensure their reliability and expertise.
3. Material selection: Consider the intended application, environment, and any regulatory requirements when selecting the appropriate material for your needs. Consult with the supplier or a material specialist to ensure the chosen material can meet the desired performance and durability.
4. Quality control: Insist on stringent quality control measures throughout the manufacturing process. This includes material inspection, mold maintenance, process monitoring, and final product inspection. Quality control ensures that the finished products meet your specifications and regulatory standards.
5. Mold design and tooling: Work closely with the supplier on mold design and tooling to ensure that the customized plastic parts can be produced accurately and cost-effectively. Collaborate on factors like mold cavity layout, gate placement, and ejection system, as these can impact the quality and cost of the final product.
6. Cost considerations: Obtain detailed quotes from multiple suppliers to compare pricing, lead time, and any additional costs such as tooling. However, beware of choosing solely based on the lowest price, as it may compromise quality. Consider the overall value, including reliability, quality, reputation, and delivery times.
7. Communication and collaboration: Maintain open and frequent communication with the supplier throughout the procurement process. Regularly update them on any changes or modifications and address any concerns or challenges promptly. Effective collaboration helps avoid misunderstandings and ensures the final product meets your expectations.
8. Supply chain resilience: Evaluate the supplier’s ability to handle unexpected disruptions, such as natural disasters or fluctuations in demand. Assess their contingency plans, alternate sourcing options, and risk management strategies to ensure a resilient supply chain.
By considering these tips, you can ensure a successful procurement process when purchasing custom injection molded plastics. It is essential to establish clear requirements, choose a reliable supplier, carefully select materials, maintain quality control, collaborate effectively, evaluate costs, and prioritize a resilient supply chain.
FAQs on Sourcing and Manufacturing custom injection molded plastics in China
1. Why should I source custom injection molded plastics from China?
Sourcing custom injection molded plastics from China offers several advantages, including cost savings. China has a large manufacturing base that can produce high-quality products at a lower cost compared to many other countries. Additionally, China has a well-established supply chain for plastic injection molding, ensuring quick turnaround times and efficient production.
2. How do I find a reliable manufacturer for custom injection molded plastics in China?
To find a reliable manufacturer, you can start by conducting thorough research on different manufacturers. Look for companies with a proven track record of producing quality plastic injection molded products. Verify their certifications and check if they comply with international quality standards. Reading reviews and testimonials from previous customers can also help in assessing the manufacturer’s reputation.
3. What is the typical lead time for custom injection molded plastics from China?
The lead time for custom injection molded plastics can vary depending on various factors, including the complexity of the design, the quantity required, and the manufacturing capabilities of the chosen manufacturer. However, in general, lead times can range from a few weeks to a few months. It is advisable to discuss and confirm the lead time with your chosen manufacturer before placing an order.
4. Can I get samples before placing a bulk order?
Yes, most manufacturers in China offer the provision to provide samples of custom injection molded plastics before placing a bulk order. It allows you to evaluate the quality, functionality, and suitability of the product for your specific requirements. Discuss the sampling process with the manufacturer and clarify any associated costs or fees.
5. What are the quality control measures followed during manufacturing?
Reputable manufacturers in China implement stringent quality control measures to ensure the production of high-quality custom injection molded plastics. This may include thorough quality checks at every stage of production, inspections of incoming raw materials, and testing of finished products. Good manufacturers often provide transparency in their quality control processes and may even offer certifications, such as ISO 9001, to demonstrate their commitment to quality.
In conclusion, sourcing custom injection molded plastics in China offers cost benefits, a well-established supply chain, and efficient production. Finding a reliable manufacturer, understanding lead times, acquiring samples, and verifying quality control measures are crucial considerations when engaging in this process.
Why contact sourcifychina.com get free quota from reliable custom injection molded plastics suppliers?
Sourcifychina.com is able to obtain free quotas from reliable custom injection molded plastics suppliers due to several reasons. Firstly, Sourcifychina.com has established strong partnerships and collaborative relationships with these suppliers. As a trusted sourcing platform, they have built a reputation of delivering high-quality products and services, ensuring that the suppliers benefit from a steady stream of customers. Consequently, the suppliers are willing to offer free quotas as a way to attract potential buyers and maintain their partnership with Sourcifychina.com.
Secondly, Sourcifychina.com has a streamlined and efficient sourcing process, which minimizes overhead costs and reduces the overall production expenses for the suppliers. By utilizing their extensive network and expertise in sourcing, they can negotiate favorable terms with the suppliers and achieve cost savings. The suppliers are more likely to offer free quotas as they already benefit from an optimized production process, allowing them to accommodate additional orders without significantly impacting their costs.
Additionally, Sourcifychina.com has a large customer base and frequent orders, which provides suppliers with a consistent and reliable source of revenue. When suppliers receive a steady flow of orders through Sourcifychina.com, they are more willing to offer free quotas as a strategic marketing initiative to capture potential long-term customers. Moreover, these suppliers understand the value of establishing strong relationships with reliable partners like Sourcifychina.com, as it enables them to expand their business opportunities and improve their market presence.
To sum up, Sourcifychina.com secures free quotas from reliable custom injection molded plastics suppliers by building strong partnerships, optimizing the sourcing process, and offering suppliers a consistent revenue stream. By leveraging their reputation and network, Sourcifychina.com creates a mutually beneficial environment, ensuring suppliers are motivated to provide free quotas to attract potential customers.