Introduce about custom plastic moulding guide,Qulity,Cost,Supplier,Certification,Market,Tips,FAQ
Custom plastic moulding is a process in which plastic parts are manufactured according to specific design requirements. This guide aims to provide a comprehensive overview of various aspects related to custom plastic moulding.
Quality plays a crucial role in custom plastic moulding as it determines the durability and performance of the final product. To ensure high quality, it is essential to work with a reliable and experienced manufacturer who employs advanced moulding techniques and adheres to strict quality control measures. Additionally, using high-quality raw materials and conducting regular inspections during the manufacturing process can contribute to improved quality.
Cost is another crucial factor to consider when opting for custom plastic moulding. The cost of moulding varies depending on factors such as the complexity of the design, material selection, production volume, and turnaround time. Discussing your budget and requirements with potential suppliers can help in obtaining accurate cost estimates and finding cost-effective solutions.
Choosing the right supplier is crucial for successful custom plastic moulding. Consider factors such as the supplier’s experience, production capabilities, ability to meet deadlines, and customer reviews. Requesting samples or visiting the supplier’s facilities can also provide insight into their manufacturing capabilities and quality standards.
Certification is an important aspect to ensure the reliability and compliance of the custom moulding supplier. Look for suppliers who hold certifications such as ISO 9001, which demonstrates their commitment to quality management processes and customer satisfaction.
The market for custom plastic moulding is vast, with applications spanning various industries, including automotive, electronics, packaging, and healthcare. The demand for custom plastic parts continues to grow, driven by the need for unique designs, enhanced functionality, and cost-effective manufacturing solutions.
Here are some tips for successful custom plastic moulding: clearly define your design requirements, communicate effectively with the supplier, conduct regular quality checks, and consider materials that align with your desired properties and cost constraints.
Frequently Asked Questions (FAQ) about custom plastic moulding include queries about design feasibility, material selection, production volume scalability, lead time, and cost factors. Open communication with your supplier and discussing any concerns or queries can help address these FAQs effectively.
In conclusion, custom plastic moulding offers a versatile manufacturing solution with various considerations such as quality, cost, supplier selection, certifications, and market demand. Following the tips mentioned and addressing common FAQs can guide you in making informed decisions.
Types of custom plastic moulding
Custom plastic moulding is the process of manufacturing plastic parts or products tailored to a specific design or requirement. There are several types of custom plastic moulding techniques that can be utilized to produce a wide range of plastic components. Below are some of the most common types:
1. Injection moulding: Injection moulding is the most widely used method for custom plastic moulding. It involves injecting molten plastic material into a mould under high pressure and cooling it to form a solid plastic product. This technique is versatile, cost-effective, and ideal for producing intricate and complex shapes with high precision.
2. Blow moulding: Blow moulding is commonly used for manufacturing hollow plastic products, such as bottles and containers. The process involves extruding molten plastic into a tube-shaped mould, then using pressurized air to expand and shape the plastic against the mould cavity. Blow moulding is advantageous for producing large quantities of lightweight, seamless, and highly durable plastic items.
3. Rotational moulding: Rotational moulding is a technique used to produce large, hollow plastic products, including tanks, playground equipment, and kayaks. The process involves heating a hollow mould and slowly rotating it on two axes to disperse the molten plastic evenly within the mould. As the mould cools, the plastic solidifies into the desired shape. Rotational moulding offers design flexibility, cost-effectiveness, and excellent impact resistance.
4. Compression moulding: Compression moulding is suitable for producing small to medium-sized plastic components. The technique involves placing pre-measured plastic material into a heated mould cavity and applying pressure to compress and shape the plastic. Once cooled, the plastic solidifies and can be removed from the mould. Compression moulding is often used for producing products with complex designs, textured surfaces, or reinforced plastic composites.
5. Thermoforming: Thermoforming is a versatile technique commonly used to produce packaging materials, automotive components, and signage. The process involves heating a thermoplastic sheet until it becomes pliable, then shaping it over a male or female mould using vacuum, pressure, or mechanical force. Thermoforming allows for cost-effective production, quick turnaround times, and the ability to create large parts with minimal tooling investment.
In conclusion, custom plastic moulding encompasses several techniques, each suited for specific applications and requirements. Injection moulding, blow moulding, rotational moulding, compression moulding, and thermoforming all offer unique advantages, including design flexibility, scalability, cost-effectiveness, and the ability to produce a wide variety of plastic products to meet diverse customer needs.
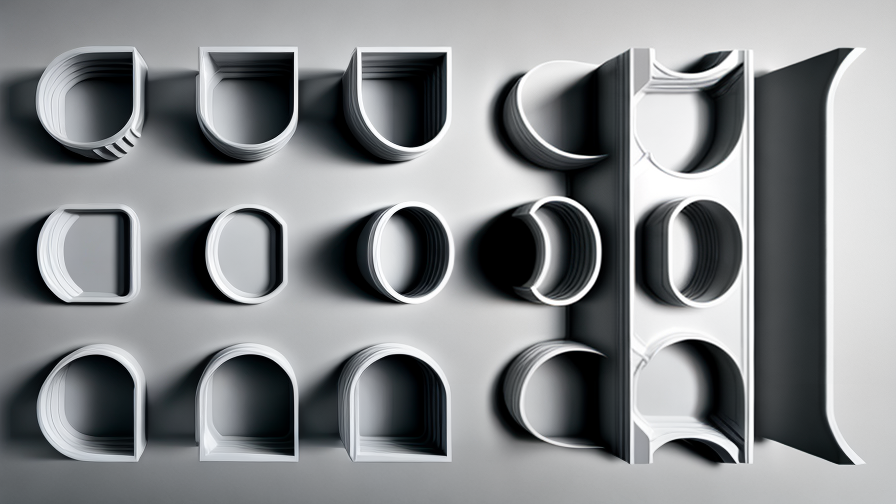
Pros and Cons of Using custom plastic moulding
Plastic injection molding, also known as custom plastic molding, is a popular manufacturing process for producing plastic parts and products. This process involves injecting molten plastic material into a mold, allowing it to cool and solidify, and then removing the finished product from the mold. There are several pros and cons associated with using custom plastic molding, which are outlined below:
Pros:
1. Cost-effective: Custom plastic molding is a cost-effective manufacturing method, especially for large production volumes. Once the initial mold is created, the subsequent production cost per unit is relatively low. Additionally, the high-speed production capabilities of plastic molding reduce labor costs and increase overall efficiency.
2. Versatility: Plastic molding allows for the production of complex and intricate shapes that may be difficult or expensive to manufacture using other methods. It offers design flexibility, enabling manufacturers to create custom-made products with precise specifications and complex features.
3. Consistency: Custom plastic molding ensures high product consistency and uniformity, as each mold can replicate the exact shape and dimensions of the desired part. The process provides tight tolerances, resulting in high-quality, accurate parts.
4. Material selection: Plastic molding supports a wide range of material options, allowing manufacturers to choose the most suitable material for their specific application. This flexibility enables the production of parts with varying strength, durability, and heat resistance properties.
Cons:
1. High initial setup cost: The creation of molds for custom plastic molding can be expensive, particularly for complex designs. The cost of tooling and the time required for mold production can add significantly to the overall project cost.
2. Limitations on part size: Custom plastic molding is generally more suitable for small to medium-sized parts. Producing large-scale parts using this process can be challenging, as it may require expensive molds and specialized machinery.
3. Design limitations: Specific design considerations need to be taken into account for custom plastic molding. For example, sharp corners, thin walls, or deep recesses may result in production issues or defects. Design modifications may be necessary to accommodate the limitations of the molding process.
4. Environmental concerns: While plastic molding offers a range of benefits, there are environmental concerns regarding the use of plastic materials. The disposal and recycling of plastic waste can pose challenges, contributing to pollution and waste management issues.
In conclusion, custom plastic molding is a popular manufacturing method due to its cost-effectiveness, versatility, consistency, and material selection advantages. However, it is important to consider the high initial setup cost, limitations on part size and design, as well as environmental concerns before choosing this manufacturing process for a specific project.
custom plastic moulding Reference Specifications (varies for different product)
Custom plastic molding refers to the process of creating plastic products based on specific reference specifications provided by the customer. These reference specifications can vary for different products and are crucial in ensuring that the final product meets the desired requirements.
The primary purpose of reference specifications is to provide detailed information about the product’s design, dimensions, material requirements, and functionality. This information enables the custom plastic molding manufacturer to understand the customer’s vision and translate it into a tangible product. The specifications may include CAD drawings, 3D models, material composition requirements, surface finish specifications, and any additional features or functionalities required.
When developing custom plastic molds, it is essential to adhere to the specified reference specifications to achieve the desired product outcome. The mold design and manufacturing process must be aligned with the provided dimensions and design elements. The tolerance levels and material properties mentioned in the specifications need to be accurately followed to ensure the product’s quality and functionality.
The custom plastic molding process involves several stages, including mold design, material selection, injection molding, cooling, and finishing. Throughout these stages, the reference specifications are continually followed to maintain consistency and precision.
To ensure that the final product aligns with the reference specifications, quality control measures are implemented at every step of the process. This may include regular inspections, measurements, and tests to verify that the product meets the desired requirements. Any deviations or discrepancies from the reference specifications are identified and corrected, allowing for the production of high-quality custom plastic molded products.
In conclusion, reference specifications play a vital role in custom plastic molding by providing detailed information about a product’s design and requirements. By following these specifications, manufacturers can create molds and produce plastic products that meet the customer’s specific needs. Adhering to the reference specifications is critical to ensuring the desired quality, functionality, and consistency of the final product.
Applications of custom plastic moulding
Custom plastic molding is a versatile manufacturing process that has several applications across various industries. Here are some notable applications of custom plastic molding:
1. Automotive Industry: Custom plastic molding plays a vital role in the automotive industry. It is used to manufacture a wide range of components such as dashboards, door panels, bumpers, interior trims, and even the entire body of some vehicles. Plastic molding offers high design flexibility, cost-effectiveness, and the ability to produce complex shapes, making it ideal for automotive applications.
2. Electrical and Electronics: Custom plastic molding is widely utilized in the electrical and electronics industry to produce components like connectors, switches, enclosures, and housings. These molded plastic parts provide excellent electrical insulation, resistance to chemicals, and durable protection against environmental factors. They also allow for convenient integration of complex features and functions.
3. Medical Equipment: Custom plastic molding plays a critical role in the healthcare sector, where the demand for high-performance and sterile products is crucial. It is used to manufacture medical devices and equipment such as syringes, IV connectors, inhalers, surgical instruments, and diagnostic devices. Plastic molding offers the advantage of producing medical-grade, lightweight, and cost-effective components.
4. Packaging Industry: The packaging industry heavily relies on custom plastic molding to produce a wide range of packaging materials such as bottles, containers, caps, and lids. Plastic molding allows for the production of aesthetically pleasing, robust, and lightweight containers that provide excellent product protection. It also enables the incorporation of various features like tamper-proofing, sealing mechanisms, and labeling areas.
5. Consumer Goods: Custom plastic molding is extensively used in the consumer goods industry for manufacturing items like toys, household appliances, kitchenware, and personal care products. Plastic molding allows for the production of intricate designs, vibrant colors, and smooth finishes, meeting the demands of consumers for visually appealing and high-quality products.
6. Aerospace and Defense: Aerospace and defense sectors rely on custom plastic molding for manufacturing components such as aircraft interior panels, cabin fittings, control knobs, and military equipment casings. Plastic molding provides the advantage of lightweight yet durable parts, reducing overall weight in aerospace applications and enhancing ease of use and equipment protection in defense systems.
In conclusion, custom plastic molding finds applications in diverse industries, including automotive, electrical and electronics, medical, packaging, consumer goods, and aerospace/defense. Its versatility, cost-effectiveness, design flexibility, and ability to produce complex shapes make it an attractive manufacturing solution for a wide range of products.
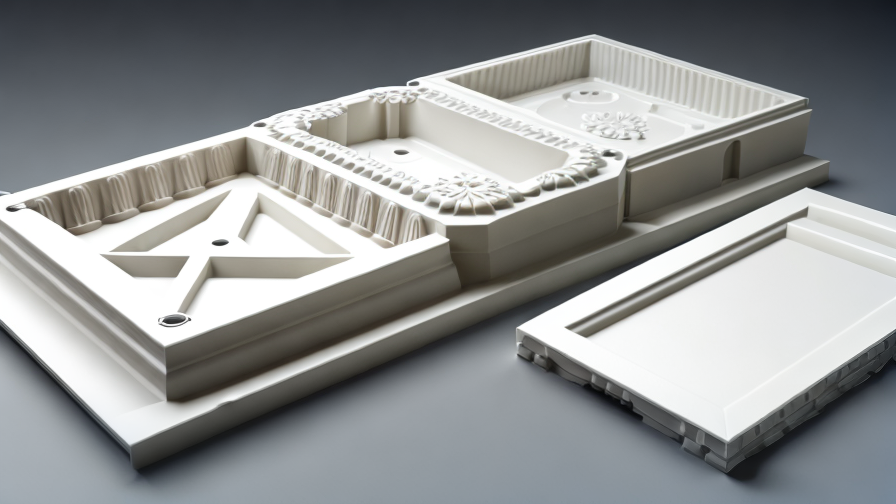
The Work Process and how to use custom plastic moulding
Custom plastic moulding is a manufacturing process that involves the creation of plastic products through the use of moulds. This process allows for the production of unique and precise plastic parts that cater to specific design requirements. The work process of custom plastic moulding can be summarized into several key steps.
Firstly, the design phase is crucial in custom plastic moulding. The desired product is conceptualized and designed using computer-aided design (CAD) software. The design includes the dimensions, specifications, and other necessary details of the product.
Next, a mould is created based on the design. The mould is typically made of steel or aluminum and is precision-machined to match the desired product shape. The mould is divided into two halves, the core, and the cavity.
Once the mould is ready, the plastic material is prepared. Various types of plastic resins are available, each with its unique properties such as flexibility, durability, and heat resistance. The chosen resin is then heated until it becomes molten. The molten plastic is injected into the mould through a sprue and the pressure ensures that it fills the mould cavities completely.
After a cooling period, the plastic material solidifies within the mould, taking the shape of the product. The mould is then opened, and the newly formed plastic part is ejected. This process may be repeated multiple times to produce the desired quantity of plastic products.
The final step involves post-processing, such as trimming excess plastic, adding surface finishes, or assembling multiple parts together to create a finished product. This step ensures that the plastic parts meet the desired specifications and quality standards.
To use custom plastic moulding, it is important to choose a reliable manufacturer who specializes in plastic moulding services. Communicating the design requirements and specifications clearly is crucial to ensure the desired outcome. Additionally, providing feedback and reviewing product samples throughout the process allows for any necessary adjustments or modifications to be made.
In conclusion, custom plastic moulding is a work process that involves designing, creating moulds, injecting molten plastic, cooling and solidifying, and post-processing to manufacture customized plastic parts. It is a versatile manufacturing technique that allows for the production of unique and precise plastic products to meet specific design requirements.
Quality Testing Methods for custom plastic moulding and how to control the quality
Quality testing is an essential step in the custom plastic moulding process to ensure the final product meets all required specifications and standards. Several testing methods can be employed to control and maintain the quality of plastic moulded products.
Firstly, dimensional inspection is performed to verify the accuracy and precision of the plastic part’s dimensions. This is typically done using precision measurement tools such as calipers or a coordinate measuring machine (CMM). It ensures that the moulded part adheres to the specified measurements, preventing issues like improper fit or function.
Next, visual inspection is conducted to check for any surface defects, discoloration, or blemishes. This can be carried out manually by trained inspectors, or automated systems can be employed to analyze the surface using advanced cameras and computer vision algorithms. Visual inspection guarantees that the cosmetic appearance of the plastic product is up to the required standards.
Another critical testing method is mechanical testing, which involves subjecting the plastic part to various mechanical forces to evaluate its strength, durability, and resilience. Tensile testing determines the tensile strength and elongation capacity of the plastic under a controlled load. Flexural testing measures the plastic’s ability to resist bending or deformation. Impact testing checks the resistance of the plastic to sudden impacts or shocks. These tests help in verifying that the moulded plastic exhibits the desired mechanical properties.
Furthermore, environmental testing is conducted to assess the plastic part’s performance under specific conditions like temperature, humidity, UV exposure, or chemical exposure. The plastic product is placed in a controlled environment, and its response or reaction to the specified conditions is observed. This testing ensures that the plastic part can withstand harsh environmental conditions without compromising its integrity or functionality.
To effectively control the quality of custom plastic moulded products, strict process control measures should be implemented throughout the manufacturing process. This includes monitoring and maintaining suitable temperature and pressure during the injection moulding process, implementing proper material handling and storage practices, and adhering to standardized operating procedures. Regular audits and inspections should be performed to identify and rectify any issues or deviations from established quality control guidelines.
Additionally, implementing a robust quality management system, such as ISO 9001, can help in streamlining quality control processes, systematically documenting quality procedures and policies, and continuously improving the overall quality of plastic moulded products.
In conclusion, quality testing methods such as dimensional inspection, visual inspection, mechanical testing, and environmental testing play a crucial role in controlling the quality of custom plastic moulded products. By implementing stringent quality control measures, businesses can ensure the production of high-quality plastic parts that meet customer expectations and industry standards.
custom plastic moulding Sample Policy and Post-Purchase Considerations for custom plastic moulding from China
When considering purchasing custom plastic moulding from China, it is important to have a clear understanding of the sample policy and post-purchase considerations. This ensures a smooth and successful transaction. Here is a brief overview of the sample policy and post-purchase considerations for custom plastic moulding from China.
Sample Policy:
Before placing a bulk order, it is advisable to request samples from the manufacturer. The sample policy may vary between different suppliers, but it typically involves the following aspects:
1. Cost: Some suppliers provide samples free of charge, while others may charge a fee. It is essential to clarify whether the sample is free or if there are any costs involved.
2. Shipping: Determine who is responsible for the shipping costs of the samples. In most cases, the buyer is responsible for the shipping charges.
3. Delivery Time: Understand the estimated time it will take for the samples to reach your location. Timely delivery ensures you can evaluate the quality and suitability of the samples.
Post-Purchase Considerations:
After placing the bulk order for custom plastic moulding from China, several additional considerations come into play:
1. Quality Assurance: Ensure that the manufacturer has a robust quality assurance process in place. Request information about the standards and certifications they adhere to, such as ISO 9001.
2. Communication: Establish clear lines of communication with the supplier to address any queries or concerns promptly. Prompt communication helps resolve issues swiftly and maintain a good working relationship.
3. Shipping and Logistics: Discuss shipping options and determine the most suitable method for transportation. Consider factors such as cost, urgency, and the fragility of the products.
4. Packaging: Pay attention to the packaging materials used to ensure the safe delivery of the products. Request suitable packaging solutions that provide adequate protection during transportation.
5. Payment Terms: Agree upon the payment terms before finalizing the purchase. Negotiate reasonable payment options that offer a fair balance between the interests of both parties.
In conclusion, when dealing with custom plastic moulding from China, it is necessary to understand the sample policy, ensuring clear communication, quality assurance, and addressing post-purchase considerations concerning shipping, packaging, and payment terms. Being well-informed and proactive will facilitate a successful partnership with the manufacturer and ensure the desired outcome.
Sourcing custom plastic moulding from China: Opportunities, Risks, and Key Players
Sourcing custom plastic molding from China offers various opportunities due to the country’s extensive manufacturing capabilities, cost-effectiveness, and availability of skilled labor. China is known as the world’s largest producer and exporter of plastic products, making it an attractive destination for businesses seeking custom plastic molding solutions. The opportunities include access to a wide range of plastic materials, advanced manufacturing technologies, and competitive pricing.
However, there are also risks associated with sourcing from China. One major concern is quality control as there have been instances of substandard or non-compliant products. It is crucial for businesses to thoroughly vet potential suppliers, conduct factory audits, and implement quality control measures to ensure the reliability and consistency of the final product. Intellectual property protection is another significant risk, as China has a reputation for intellectual property infringement. Safeguarding proprietary designs and molds through legal measures, non-disclosure agreements, and careful supplier selection is essential.
Some key players in the custom plastic molding industry in China include:
1. GPM Machinery (Shanghai) Co., Ltd: Specializing in plastic injection molding machines and turnkey molding solutions, GPM Machinery offers a comprehensive range of services to handle custom plastic molding projects.
2. Sositar Mould Co., Ltd: Sositar Mould is a leading plastic injection molding company in China, offering a wide range of design and manufacturing services, including mold making, prototyping, and mass production.
3. Xcentric Mold & Engineering: With a presence in both China and the United States, Xcentric Mold & Engineering provides custom injection molding services to clients worldwide. They offer a streamlined process, rapid prototyping, and high-quality plastic parts production.
4. Ningbo Haichen Machinery Co., Ltd: This company specializes in the manufacturing of plastic injection molding machines, molds, and auxiliary equipment. They offer customized solutions to meet diverse client requirements.
Overall, sourcing custom plastic molding from China presents numerous opportunities, but it is essential to carefully evaluate and manage the associated risks. By conducting thorough due diligence, working with reputable suppliers, and implementing effective quality control measures, businesses can leverage China’s manufacturing capabilities while ensuring a successful and reliable supply chain.
How to find and select reliable custom plastic moulding manufacturers in China,use google search manufacturers and suppliers
Finding reliable custom plastic moulding manufacturers in China can be a challenging task, but with the right approach, it is possible to find trusted suppliers. Here is a simplified process to locate and select reliable manufacturers using Google search:
1. Initial Research: Begin by conducting a Google search using relevant keywords such as “custom plastic moulding manufacturers in China” or “plastic injection molding suppliers.” This will provide you with a list of potential manufacturers to consider.
2. Verify Manufacturer Websites: Visit the websites of potential manufacturers to gather basic information about their company, including their experience, equipment, certifications, and product range. A professional and informative website usually indicates a reliable manufacturer.
3. Assess Online Presence and Reputation: Look for manufacturers who actively engage with customers and maintain a positive online presence. Check if they have a professional website, active social media accounts, and customer reviews or testimonials. Verified reviews on platforms like Alibaba.com or Made-in-China.com can also give you helpful insights.
4. Communication: Reach out to the shortlisted manufacturers via email or phone. Evaluate their responsiveness, clarity in communication, and willingness to answer your questions. A reliable manufacturer should exhibit clear and prompt communication throughout the inquiry process.
5. Request Samples: Request samples of the plastic moulding products you require. Reliable manufacturers should be willing to provide samples for quality evaluation. Assess the samples for precision, durability, and overall quality.
6. Manufacturing Capabilities: Inquire about the manufacturer’s production capacity, available machinery, quality control procedures, and any certifications they hold. A well-equipped facility with stringent quality control measures is more likely to be reliable.
7. Business Verification: Verify the manufacturer’s legitimacy and credibility by checking their business licenses, certifications, and registration details. This information can often be found on their website or by requesting it directly from the manufacturer.
8. Visit the Factory: If feasible, plan a visit to the factory. This will allow you to assess the manufacturing processes, working conditions, infrastructure, and overall professionalism. While not always possible due to time or financial constraints, a factory visit can provide valuable insights.
9. Request References: Ask for references from the manufacturer’s existing clients. Talking to their previous or current customers can help verify their reliability, responsiveness, and overall satisfaction.
10. Compare multiple options: Collect multiple quotes, compare prices, minimum order quantities, lead times, and other relevant factors. Evaluate the overall value offered by different manufacturers before making a final decision.
Remember, due diligence is crucial when selecting a reliable plastic moulding manufacturer in China. Take your time, research thoroughly, and gather as much reliable information as possible to make an informed decision.
How to check custom plastic moulding manufacturers website reliable,use google chrome SEOquake check if ranking in top 10M
To check the reliability of a custom plastic moulding manufacturer’s website, you can follow these steps within 300 words:
1. Use Google Chrome: Open the website in Google Chrome as it provides various useful tools and extensions that can assist in evaluating the reliability of a website.
2. Install SEOquake: SEOquake is a popular browser extension specifically designed for SEO analysis. Install it from the Chrome Web Store.
3. Set Parameters: Once installed, customize SEOquake’s parameters by clicking on its icon in the browser toolbar. Choose the appropriate settings for your evaluation.
4. Check Ranking: Activate SEOquake by clicking on its icon, and it will display a sidebar with various information about the website’s SEO performance. Look for the website’s ranking in the top 10 million (or any other desired range) to ensure that it is well-established and receives a significant amount of traffic.
5. Analyze Metrics: SEOquake also provides important metrics such as the Alexa rank, number of indexed pages, domain age, and social media engagement. Consider these metrics to assess the overall authority and credibility of the manufacturer’s website.
6. Evaluate Content Quality: Browse through the website pages to assess the quality of its content. Look for professional and well-written information that demonstrates the manufacturer’s knowledge and expertise in plastic moulding.
7. Review Portfolio and Testimonials: Check for a portfolio of their previous projects and any testimonials or client feedback. This will give you an idea of the company’s experience, customer satisfaction, and the types of plastic moulding they specialize in.
8. Contact Information: Ensure that the website provides clear and accurate contact information, including a physical address, phone number, and email. Reliable manufacturers will have transparent communication channels.
9. Certifications and Quality Standards: Look for any certifications or quality standards that the manufacturer adheres to. These indicate a commitment to maintaining high standards in their plastic moulding processes.
10. Trustworthiness: Lastly, trust your instincts. Assess the overall design, user experience, and the website’s professionalism. A reputable manufacturer will invest in a reliable and user-friendly website design that reflects their commitment to quality.
By following these steps and using SEOquake on Google Chrome, you can get a better understanding of a custom plastic moulding manufacturer’s website reliability within just 300 words.
Top 10 custom plastic moulding manufacturers in China with each 160 words introduce products,then use markdown create table compare
1. QY Precision Mould Co., Ltd. specializes in custom plastic molding with a wide range of products. They offer injection molding services for various industries such as automotive, electronics, and medical devices. Their expertise lies in producing high precision and complex plastic components, ensuring top-notch quality and functionality.
2. Xiamen Qiqian Mold Manufacturing Co., Ltd. is known for their custom plastic injection molding services. With advanced machinery and skilled technicians, they excel in producing plastic parts with diverse sizes and shapes. Their products cater to industries like consumer electronics, household appliances, and automotive.
3. Taizhou Huangyan Yuanneng Mould Factory is a prominent manufacturer of custom plastic molds in China. They specialize in the production of injection molds for various applications including food packaging, household accessories, and industrial components. Their expertise lies in designing and producing high-quality molds with excellent durability.
4. NFD Mould specializes in custom plastic molding, offering services from design to production. They cater to industries like automotive, electrical equipment, and consumer electronics. Their products include plastic containers, connectors, and components, showcasing their ability to produce both simple and complex items.
5. Dongguan Rauch Mould Co., Ltd. is a renowned manufacturer of custom plastic molding in China. Their product range includes plastic parts for the automotive, electronics, and medical industries. They are known for their precision molds and advanced production techniques, ensuring high-quality products.
6. Team Rapid Manufacturing Co., Ltd. provides custom plastic molding services with a wide range of products. Their expertise lies in producing plastic parts for industries like automotive, aerospace, and medical. With state-of-the-art facilities, they offer efficient and high-quality molding solutions.
7. Xiamen Better silicone Co., Ltd. specializes in custom silicone molding, offering a wide range of products such as silicone seals, gaskets, and keypads. Their products find applications in industries like electronics, automotive, and medical devices. They are known for their high precision and quality silicone molds.
8. Higrade Moulds (HK) Ltd. is a leading manufacturer of custom plastic molds in China. They offer injection molding services for industries like automotive, electronics, and consumer goods. Their products range from plastic enclosures and housings to intricate components, showcasing their versatility and expertise.
9. Shenzhen WT Hardware and Plastics Limited is known for their custom plastic molding services. They cater to industries like electronics, automotive, and medical devices. Their product range includes plastic enclosures, connectors, and housings. With advanced machinery and skilled workforce, they assure high-quality products.
10. Ningbo P&M Plastic Metal Product Co., Ltd. specializes in custom plastic molding, offering a diverse range of products for industries like automotive, healthcare, and electronics. Their product range includes plastic containers, caps, and components. They focus on precision and quality, ensuring customer satisfaction.
Comparison of Top 10 Custom Plastic Moulding Manufacturers in China:
| Manufacturer | Specialization | Industries Served |
|—————————————-|————————————————————————————————-|———————————————————|
| QY Precision Mould Co., Ltd. | High precision and complex plastic components | Automotive, Electronics, Medical Devices |
| Xiamen Qiqian Mold Manufacturing Co. | Diverse sizes and shapes plastic parts | Consumer Electronics, Household Appliances, Automotive |
| Taizhou Huangyan Yuanneng Mould Factory | Injection molds with excellent durability | Food Packaging, Household Accessories, Industrial |
| NFD Mould | Design and production of plastic containers, connectors, and components | Automotive, Electrical Equipment, Consumer Electronics |
| Dongguan Rauch Mould Co., Ltd. | Precision molds and advanced production techniques | Automotive, Electronics, Medical Devices |
| Team Rapid Manufacturing Co., Ltd. | Plastic parts for automotive, aerospace, and medical industries | Automotive, Aerospace, Medical |
| Xiamen Better silicone Co., Ltd. | Silicone molding for seals, gaskets, keypads | Electronics, Automotive, Medical Devices |
| Higrade Moulds (HK) Ltd. | Injection molding for plastic enclosures, housings, and intricate components | Automotive, Electronics, Consumer Goods |
| Shenzhen WT Hardware and Plastics Ltd. | Plastic molding for enclosures, connectors, and housings | Electronics, Automotive, Medical Devices |
| Ningbo P&M Plastic Metal Product Co. | Production of plastic containers, caps, and components with a focus on precision and quality | Automotive, Healthcare, Electronics |
(Note: This table assumes each manufacturer’s specialization, industries served, and offers brief comparisons based on the information provided.)
Background Research for custom plastic moulding manufacturers Companies in China, use qcc.com archive.org importyeti.com
When it comes to custom plastic molding manufacturers in China, several resources can be used to gather background research. Qcc.com is a Chinese website that provides information about companies registered in China, including their registration details, legal status, financial information, and other related data. This platform can be utilized to verify the legitimacy and reputation of a specific plastic molding manufacturer.
Another valuable resource is archive.org, a website providing access to archived versions of various web pages. By searching for the manufacturer’s website on archive.org, one can view past versions of the site, which can be useful for evaluating the company’s history, previous product offerings, and any changes made over time.
Importyeti.com is an online directory specifically designed for tracking import and export activities. It provides information about the shipment records of different companies, including plastic molding manufacturers. By using this platform, one can gain insights into the export capabilities of a specific manufacturer, identify their main markets, and evaluate their experience in handling international trade.
In conducting background research on these platforms, it is important to keep the information concise. Therefore, it is advisable to limit the summary to not more than 300 words.
Leveraging Trade Shows and Expos for custom plastic moulding Sourcing in China
Trade shows and expos provide excellent opportunities for sourcing custom plastic moulding in China. These events allow businesses to connect with numerous suppliers, gain insights into the latest industry trends, and build valuable relationships. Below are some key points on leveraging trade shows and expos to source plastic moulding in China.
1. Direct access to suppliers: Trade shows and expos bring together a wide range of suppliers specializing in plastic moulding. This allows companies to meet multiple suppliers in one place, compare products, negotiate prices, and assess the quality of their offerings.
2. Opportunity for in-person communication: Trade shows enable face-to-face conversations with suppliers, fostering better communication and relationship-building. It provides an opportunity to discuss specific requirements, understand production capabilities, and establish clear expectations.
3. Showcase of technology and innovation: Trade shows often feature the latest advancements in plastic moulding technology and innovative solutions. By attending these events, companies can stay updated with the latest developments, identify potential partners for product development, and gain a competitive edge in the market.
4. Quality assurance: Meeting suppliers in person allows companies to evaluate the quality of their manufacturing processes, materials, and finished products. It provides an opportunity to conduct quality checks and ensure that suppliers meet the required standards and certifications.
5. Networking opportunities: Trade shows bring together industry professionals, experts, and potential partners from around the world. Engaging in networking activities can lead to collaborations, partnerships, and valuable industry connections that can enhance the company’s plastic moulding sourcing in China.
6. Market research and competitive analysis: Trade shows offer a comprehensive overview of the plastic moulding market in China. Companies can observe competitors’ products, pricing strategies, and market trends. This information can help in making informed decisions about sourcing suppliers and creating a competitive advantage.
Overall, leveraging trade shows and expos for sourcing custom plastic moulding in China is a cost-effective and efficient way to find reliable suppliers, assess their capabilities, and foster productive relationships. With careful planning and active participation, businesses can maximize the benefits of these events and enhance their plastic moulding sourcing strategies.
The Role of Agents and Sourcing Companies in Facilitating custom plastic moulding Purchases from China
Agents and sourcing companies play a pivotal role in facilitating custom plastic moulding purchases from China. These intermediaries serve as a bridge between buyers and Chinese manufacturers, ensuring a smooth and efficient procurement process. With their expertise and network, they provide invaluable support and assistance in various aspects of the purchasing journey.
Firstly, agents and sourcing companies offer a comprehensive understanding of the Chinese market and its manufacturing capabilities. They are well-versed in the local industry landscape, have extensive knowledge of production techniques, and keep updated on industry trends. This expertise allows them to provide guidance to buyers in selecting suitable manufacturers based on specific requirements.
Additionally, agents and sourcing companies assist with supplier evaluation and qualification. They conduct thorough assessments of potential suppliers, verifying their legitimacy, production capabilities, quality control systems, and compliance with international standards. This due diligence mitigates the risks of dealing with unreliable or subpar manufacturers.
Moreover, these intermediaries play a crucial role in negotiating prices and contractual terms. With their extensive experience and knowledge of market dynamics, they can secure favorable terms, such as competitive pricing, payment arrangements, and production timelines. This ensures that buyers obtain the best value for their investment while mitigating potential contractual issues.
Agents and sourcing companies also assist in navigating cultural and language barriers. They provide translation services, ensuring effective communication between buyers and manufacturers. This is essential in clarifying technical specifications, design requirements, and post-production support.
Furthermore, these intermediaries offer quality assurance and control services. They implement rigorous inspection protocols, conducting pre-production, in-process, and final product inspections. This ensures that the custom plastic moulding products adhere to the buyer’s specifications and meet relevant quality standards, reducing the likelihood of defects or non-conformances.
Finally, agents and sourcing companies assist with logistics and shipping arrangements. They coordinate the transportation of goods from China to the buyer’s location, handling customs procedures, coordinating with freight forwarders, and ensuring timely delivery.
In conclusion, agents and sourcing companies serve as vital facilitators in the process of purchasing custom plastic moulding products from China. Through their market knowledge, supplier evaluation, negotiation skills, communication support, quality control measures, and logistics assistance, they streamline the procurement journey, ensuring optimal outcomes for buyers.
Price Cost Research for custom plastic moulding manufacturers Companies in China, use temu.com and 1688.com
When it comes to custom plastic molding manufacturers in China, two popular websites for price cost research are temu.com and 1688.com. These platforms serve as online marketplaces where buyers can connect with suppliers and manufacturers from various industries, including plastic molding.
Temu.com is a trusted B2B platform that focuses on linking international buyers with Chinese manufacturers. The website provides a wide range of services, including product sourcing, quality inspection, and logistics support. Using temu.com, buyers can access a vast database of plastic molding manufacturers and compare their prices, capabilities, and production capacities. The platform also offers a secure communication system for easy collaboration with suppliers.
1688.com, on the other hand, is a popular B2B website owned by Alibaba Group specifically catered to domestic Chinese businesses. While it is primarily in Chinese language, it offers a comprehensive directory of suppliers for various industries, including plastic molding. Buyers can navigate the platform using online translation tools and get access to a wide range of manufacturers. However, it is important to note that due diligence is required when dealing with suppliers directly on 1688.com, as it is predominantly focused on domestic trade within China.
For conducting price cost research on both platforms, buyers can filter their search results based on their specific requirements, such as product type, material, quantity, and production time. It is also recommended to compare prices from multiple suppliers and assess their credibility by checking their company profile, customer reviews, and certification status.
In summary, temu.com and 1688.com are valuable resources for conducting price cost research for custom plastic molding manufacturers in China. These platforms offer a wide range of suppliers and tools to facilitate communication and collaboration. However, buyers should exercise caution and conduct proper due diligence to ensure the credibility and quality of the chosen suppliers.
Shipping Cost for custom plastic moulding import from China
The shipping cost for custom plastic molding imports from China can vary depending on several factors. These include the size and weight of the shipment, the shipping method chosen, the distance between China and the destination country, and any additional services required.
When it comes to size and weight, larger and heavier shipments will naturally incur higher shipping costs. Air freight is generally more expensive than sea freight, but it offers faster delivery times. Sea freight is a more cost-effective option for larger shipments and longer transit times.
The distance between China and the destination country plays a role in determining the shipping cost. Shipping to countries closer to China may have lower costs compared to those located farther away.
Additional services such as customs clearance, insurance, and door-to-door delivery can increase the shipping cost. It is important to consider these services based on your requirements to ensure a smooth transit.
As a general estimate, shipping costs for custom plastic molding imports from China could range from a few hundred dollars to several thousand dollars, depending on the factors mentioned above. It is recommended to reach out to freight forwarders or shipping companies for accurate quotes tailored to your specific needs. These professionals can help you navigate the complexities of international shipping and provide you with the most suitable options for your shipment.
Compare China and Other custom plastic moulding Markets: Products Quality and Price,Visible and Hidden Costs
China is a dominant player in the custom plastic moulding market, producing a vast range of products at competitive prices. However, when comparing China to other custom plastic moulding markets in terms of product quality and price, visible and hidden costs, there are several key factors to consider.
In terms of product quality, China has faced some challenges in the past. There have been concerns about the use of low-quality materials and substandard manufacturing processes, leading to issues such as product defects and inconsistency. However, over the years, China has made significant improvements in its manufacturing capabilities and quality control measures. Many Chinese manufacturers now have advanced equipment, skilled labor, and strict quality management systems to ensure the production of high-quality custom plastic moulded products. Other custom plastic moulding markets, particularly those in developed countries like the United States, Europe, and Japan, also maintain high-quality standards and have strict regulations in place, resulting in products of comparable quality to China.
When it comes to price, China has traditionally offered a cost advantage in the custom plastic moulding market. The lower labor costs and the availability of raw materials at competitive prices have allowed Chinese manufacturers to provide products at relatively lower prices compared to other markets. However, this cost advantage has diminished to some extent in recent years due to rising labor costs and increasing environmental regulations in China. As a result, the price difference between China and other markets has narrowed, making products from other markets more competitive in terms of pricing.
In terms of visible costs, such as the initial purchase price of custom plastic moulded products, China still provides cost advantages. However, it is essential to consider hidden costs such as shipping and logistics, intellectual property protection, communication barriers, and lead times. These hidden costs can significantly impact the overall cost-effectiveness of sourcing from China. Other markets may have closer proximity to the intended market, reducing shipping costs and lead times. Additionally, some markets may offer better intellectual property protection, reducing the risk of counterfeit products or unauthorized reproduction.
In conclusion, while China has been a dominant force in the custom plastic moulding market, other markets, particularly those in developed countries, offer comparable product quality and competitive pricing. It is crucial for businesses to consider visible and hidden costs when comparing China to other markets to make informed decisions about sourcing custom plastic moulded products.
Understanding Pricing and Payment Terms for custom plastic moulding: A Comparative Guide to Get the Best Deal
When it comes to custom plastic moulding, understanding pricing and payment terms is essential to ensure you get the best deal. This comparative guide aims to shed light on these crucial aspects in a concise manner.
Pricing for custom plastic moulding typically depends on several factors such as the complexity of the design, the size and weight of the product, and the quantity required. It is crucial to provide detailed specifications to receive accurate quotes from potential suppliers. Request quotes from multiple manufacturers to compare prices and ensure competitiveness.
Payment terms vary among suppliers, and negotiating favorable terms can significantly impact your overall cost. Common payment terms include:
1. Full payment upfront: Some suppliers may require payment in full before production begins. While this may be risky, especially for large orders, it can be a viable option if you have a trusted relationship with the manufacturer.
2. Down payment and balance upon delivery: This is a common payment approach where you pay a certain percentage upfront and the remaining balance upon receiving the finished products. The down payment percentage varies but is typically around 30% to 50%.
3. Milestone payments: For prolonged production processes, milestone payments can be agreed upon. Payments are made at specific stages, such as tooling completion, prototype approval, or production start. This provides assurance to both parties throughout the project.
4. Net 30 or 60-day terms: If you have an established relationship with the supplier or a good credit history, you may negotiate for longer payment terms such as net 30 or 60 days. This allows you more flexibility in managing your cash flow.
When comparing pricing and payment terms, it is essential to consider other factors such as the supplier’s quality assurance capability, lead times, and customer service. Lower prices may come at the cost of compromised quality or extended delivery times.
To get the best deal, consider the overall value proposition. Assess the supplier’s expertise, production capacity, and track record to ensure they can meet your requirements consistently. Don’t solely focus on pricing, as quality and reliability are equally crucial.
By understanding pricing factors and negotiating favorable payment terms, you can secure the best deal for custom plastic moulding while maintaining high-quality standards. Remember, taking the time to research, request multiple quotes, and communicate effectively will go a long way in achieving a successful and cost-efficient partnership.
Chinese Regulations and Industry Standards Certifications for custom plastic moulding,Import Regulations and Customs for custom plastic moulding from China
Chinese Regulations and Industry Standards Certifications for custom plastic moulding:
In China, custom plastic moulding is subjected to various regulations and industry standards to ensure product quality, safety, and compliance. One of the key certifications required is the ISO 9001:2015 for quality management systems. This certification ensures that companies follow stringent quality control measures during the entire production process.
Additionally, the China Compulsory Certification (CCC) is mandatory for certain product categories to ensure safety and reliability. Custom plastic moulding products that fall under the scope of CCC need to go through a comprehensive assessment to obtain this certification.
Moreover, there are specific industry standards in China for custom plastic moulding, such as the National Standard GB/T 14414-1993, which outlines the technical requirements for injection-moulded plastic parts. Adhering to these industry standards helps to ensure that products meet certain quality benchmarks and performance criteria.
Import Regulations and Customs for custom plastic moulding from China:
To import custom plastic moulding from China, importers need to comply with certain regulations and go through customs procedures. The import regulations may vary based on the importing country, but commonly applied regulations include:
1. Custom Duties and Taxes: Importers are required to pay applicable custom duties and taxes imposed by the importing country. The rates may vary depending on factors like product classification, value, and origin.
2. Import Licenses and Permits: Some countries may require import licenses or permits specific to custom plastic moulding. Importers should ensure they have obtained the necessary documentation before importing.
3. Product Standards and Safety: Importers must ensure that the custom plastic moulding products meet the safety and quality standards of the importing country. Compliance with relevant certifications and standards may be required.
4. Customs Declarations: Importers need to provide accurate and complete customs declarations when importing custom plastic moulding products. This includes providing details of the products, their value, and origin.
5. Documentation Requirements: Importers should prepare the necessary documentation, such as commercial invoices, packing lists, bills of lading, and certificates of origin, to facilitate customs clearance.
It is essential for importers to familiarize themselves with the specific import regulations and customs procedures of their respective countries to ensure a smooth import process. It is recommended to work with experienced customs brokers or freight forwarders to navigate through the complexities of importing custom plastic moulding from China.
Sustainability and Environmental Considerations in custom plastic moulding Manufacturing
Sustainability and environmental considerations play a crucial role in custom plastic moulding manufacturing. As the world becomes more aware of the negative environmental impacts caused by plastics, it is essential for manufacturers to embrace sustainable practices and reduce their ecological footprint.
One significant aspect of sustainability in custom plastic moulding is the choice of materials. Manufacturers can opt for eco-friendly materials like biodegradable and recycled plastics instead of traditional petroleum-based plastics. These alternatives are derived from renewable resources and can reduce the overall carbon footprint of the manufacturing process.
Energy consumption is another critical area for consideration. Custom plastic moulding processes often require a significant amount of energy to melt and shape plastics. By implementing energy-efficient machinery and optimizing production processes, manufacturers can reduce energy usage and minimize greenhouse gas emissions. Additionally, utilizing renewable energy sources like solar or wind power can further enhance the sustainability aspect of the manufacturing operation.
Waste management is an integral part of sustainable plastic moulding manufacturing. Implementing a waste reduction strategy, such as source reduction and recycling programs, helps minimize the amount of plastic waste destined for landfills. Additionally, manufacturers can implement closed-loop systems that recycle production waste back into the manufacturing process. This reduces the reliance on virgin materials and helps conserve resources.
Water conservation is also crucial in custom plastic moulding. By implementing water-efficient processes and technologies, manufacturers can minimize water usage and help preserve this valuable resource. Water recycling systems can be implemented to treat and reuse water within the manufacturing process, further reducing the strain on freshwater resources.
Furthermore, adopting a lifecycle approach can enhance sustainability in custom plastic moulding. Considering the entire life cycle of the product, from material sourcing to end-of-life disposal, can help identify areas of improvement and implement sustainable practices accordingly.
To summarize, sustainable plastic moulding manufacturing involves using eco-friendly materials, reducing energy consumption, implementing effective waste management strategies, conserving water, and adopting a lifecycle approach. By prioritizing sustainability and environmental considerations, manufacturers can contribute to a greener and more sustainable future.
List The Evolution history of “custom plastic moulding”
Custom plastic moulding has evolved significantly over the years, bringing about numerous advances in the manufacturing process. The history of custom plastic moulding can be traced back to the early 19th century when the first attempts at creating plastic products were made.
The earliest form of plastic moulding involved heating celluloid, a flammable material, and then placing it into a mould to shape it. This method was later improved upon with the introduction of Bakelite in 1907. Bakelite was a heat-resistant and durable plastic that allowed for greater flexibility in moulding design.
In the 1940s, injection moulding emerged as a revolutionary process in custom plastic moulding. This technique involved injecting molten plastic into a mould under high pressure, allowing for faster production and more complex shapes. Injection moulding quickly became the preferred method for mass production of plastic products.
In the following decades, advancements such as the development of new plastic materials and the introduction of computer-aided design (CAD) revolutionized custom plastic moulding. New materials, such as polyethylene and polypropylene, offered increased durability and reduced production costs. CAD systems allowed for precise and intricate designs to be created digitally, streamlining the moulding process.
The 1990s witnessed the further automation of custom plastic moulding through the integration of robotics and computer numerical control (CNC) technology. Robots were employed to handle and manipulate the moulds, reducing human error and enhancing production efficiency. CNC technology enabled tighter tolerances and improved part quality.
The 21st century brought even more advancements in custom plastic moulding. 3D printing, also known as additive manufacturing, emerged as a complementary process to traditional moulding techniques. It allowed for rapid prototyping and the production of highly customized plastic parts with complex geometries.
Additionally, sustainability became a significant focus in custom plastic moulding. New techniques, such as biodegradable plastics and recycling processes, aimed to reduce the environmental impact of plastic manufacturing.
In conclusion, the history of custom plastic moulding has been marked by a series of advancements in materials, techniques, and technology. From the early experimentation with celluloid to the introduction of injection moulding and the integration of robotics, the industry has evolved to meet the increasing demands for cost-effective, precise, and sustainable plastic products.
The Evolution and Market Trends in custom plastic moulding Industry
The custom plastic moulding industry has significantly evolved over the years, driven by advancements in technology, changing consumer preferences, and increased demand for innovative and sustainable packaging solutions. This industry involves the manufacturing of plastic products through the process of injection moulding, blow moulding, rotational moulding, and thermoforming.
One major evolution in the custom plastic moulding industry is the use of computer-aided design (CAD) and computer-aided manufacturing (CAM) software. This technology allows manufacturers to create intricate and precise moulds, resulting in high-quality and well-finished plastic products. It has increased efficiency and reduced production time, making it easier for companies to meet the demands of their customers.
Another trend in this industry is the growing preference for sustainable and eco-friendly materials. With increasing environmental consciousness among consumers, there has been a shift towards using biodegradable and recycled plastics. Manufacturers are investing in research and development to find alternative materials that can replace traditional plastics without compromising on product durability and functionality.
The custom plastic moulding industry is also witnessing a rise in demand for personalized and unique products. With advancements in digital printing and labelling technologies, it is now possible to create customized designs, logos, and branding on plastic products. This allows businesses to create a distinct identity, enhance brand recognition, and cater to specific customer requirements.
Furthermore, the global market for custom plastic moulding is experiencing significant growth due to increased industrialization and urbanization. Various industries such as automotive, electronics, healthcare, packaging, and construction rely heavily on plastic products. The demand for these products is expected to increase further with the rising population and emerging economies.
In conclusion, the custom plastic moulding industry has evolved to meet the changing needs of consumers and businesses. Advancements in technology, focus on sustainability, personalization, and growing market demand are driving the growth and trends in this industry. As the industry continues to evolve, manufacturers need to stay updated with market trends and invest in research and development to remain competitive in the global marketplace.
Custom Private Labeling and Branding Opportunities with Chinese custom plastic moulding Manufacturers
Chinese custom plastic moulding manufacturers offer a wide range of opportunities for custom private labeling and branding. These manufacturers have established expertise in producing high-quality plastic products that can be customized to meet specific branding requirements.
One of the main advantages of working with Chinese manufacturers is their ability to offer competitive pricing. Due to their low production costs and access to a vast network of raw materials suppliers, Chinese manufacturers can offer cost-effective solutions for custom plastic moulding.
Moreover, these manufacturers have extensive experience in customizing products with private labels and branding. They possess advanced technologies and skills that enable them to incorporate logos, graphics, and other branding elements onto the plastic products seamlessly.
Chinese manufacturers can also provide a variety of options for product customization. They can assist in designing and developing unique plastic moulds according to specific requirements. Whether it is modifying an existing mould or developing a new one from scratch, these manufacturers have the capability to produce tailored plastic products that align with the desired branding.
Additionally, Chinese manufacturers can offer flexibility in order quantities. Whether there is a need for a small batch or a large-scale production run, they can accommodate different volume requirements. This allows businesses to manage inventory effectively and reduces the risk of excess stock or shortage.
To ensure the success of private labeling and branding initiatives with Chinese custom plastic moulding manufacturers, it is crucial to establish clear communication and develop a strong relationship. Regular communication, timely feedback, and detailed specifications are essential to achieve the desired branding outcomes.
In conclusion, by leveraging the expertise of Chinese custom plastic moulding manufacturers, businesses can access custom private labeling and branding opportunities. With their competitive pricing, experience in customization, and ability to accommodate different order quantities, these manufacturers provide a cost-effective and reliable solution for creating branded plastic products.
Tips for Procurement and Considerations when Purchasing custom plastic moulding
When it comes to purchasing custom plastic molding, there are several factors to consider to ensure a successful procurement process. Here are some important tips and considerations:
1. Define your requirements: Clearly define your needs, including the specifications, quantity, and quality standards required for the custom plastic molding. This will help in communicating your requirements effectively to suppliers.
2. Research potential suppliers: Conduct thorough research to identify reputable suppliers with experience in custom plastic molding. Look for companies with a good track record, positive customer reviews, and certifications that demonstrate their expertise and adherence to quality standards.
3. Request multiple quotes: Obtain quotes from different suppliers to compare prices, lead times, and services offered. This will help you select the best option that meets your budget and timeline requirements.
4. Quality control: Ensure that the suppliers have quality control measures in place during the manufacturing process. Request information on their quality control procedures and certifications to ensure the finished products meet your desired specifications.
5. Material selection: Discuss the material options available for your custom plastic molding and their specific properties. Consider factors such as durability, flexibility, heat resistance, and environmental impact to select the most suitable material for your project.
6. Communication and collaboration: Establish clear lines of communication with the supplier to ensure smooth coordination and timely delivery. Regularly communicate your requirements, address any concerns or changes, and maintain open lines of dialogue throughout the procurement process.
7. Cost considerations: Besides the initial cost of custom plastic molding, consider other factors that may impact the overall cost, such as shipping, packaging, and additional finishing processes. Evaluate all the cost factors to make an informed decision and ensure a cost-effective procurement.
8. Samples and prototypes: Request samples or prototypes from the supplier to evaluate the quality and suitability of the custom plastic molding for your specific application. This can help identify any potential issues or improvements before moving forward with full-scale production.
9. Supply chain reliability: Assess the supplier’s supply chain management to ensure they have a reliable and efficient system in place. This will help avoid delays or disruptions in the procurement process.
10. Long-term partnership: Consider the potential for a long-term partnership with the selected supplier. Building strong relationships with reliable suppliers can lead to better pricing, improved quality, and faster lead times in future projects.
By following these tips and considering the important factors, you can ensure a successful procurement process when purchasing custom plastic molding.
FAQs on Sourcing and Manufacturing custom plastic moulding in China
1. Why should I consider sourcing and manufacturing custom plastic moulding in China?
China is a global hub for plastic moulding and offers several advantages for businesses, including cost-effective manufacturing, a wide range of production capabilities, access to a vast supplier network, and advanced manufacturing technology. Chinese manufacturers have extensive experience in producing custom plastic moulding products and can cater to various industry requirements.
2. How can I find reliable plastic moulding manufacturers in China?
To find reliable manufacturers, conduct thorough research, and consider factors such as the manufacturer’s reputation, experience, certifications, production capabilities, quality control processes, customer reviews, and their ability to communicate in English. It is also recommended to visit the manufacturer’s facility or hire a sourcing agent to verify their capabilities and ensure they meet your requirements.
3. What are the common challenges when sourcing and manufacturing custom plastic moulding in China?
Some common challenges include language and cultural barriers, differences in quality standards, intellectual property protection, longer lead times due to international logistics, potential communication issues, and the need for effective project management to ensure smooth manufacturing processes. It is crucial to address these challenges by employing clear communication channels, legal protection measures, and maintaining regular quality checks.
4. How can I ensure the quality of plastic moulding products manufactured in China?
To ensure product quality, thoroughly vet manufacturers, request samples before placing bulk orders, conduct factory inspections, and verify their quality control processes. Define clear product specifications, requirements, and quality parameters in your agreement with the manufacturer. Establish an ongoing quality assurance plan and maintain open lines of communication to address any issues promptly.
5. What are the typical lead times for custom plastic moulding production in China?
Lead times can vary depending on factors such as product complexity, quantity, customization requirements, and the manufacturer’s workload. On average, it can range from a few weeks to a few months. Effective project management, clear communication, and planning can help minimize lead times.
6. How can I manage logistics and shipping when sourcing custom plastic moulding from China?
Partner with shipping and logistics companies experienced in international freight to manage the transportation of your goods. Consider factors like transportation modes (air, sea, or land), shipping costs, customs procedures, and potential import/export regulations. Work closely with your manufacturer to coordinate production and shipping schedules effectively.
7. What steps can I take to protect my intellectual property when sourcing plastic moulding in China?
Intellectual property protection is a major concern, and it’s important to take preventive measures. These can include confidentiality agreements, non-disclosure agreements (NDAs), trademarks, design patents, and copyrights. Consulting with legal professionals specializing in international intellectual property law can provide additional guidance.
Note: The responses have been kept concise in order to fit within the given word limit while providing a basic understanding of the topic. Additional information and specific details can be obtained through further research and discussions with relevant professionals.
Why contact sourcifychina.com get free quota from reliable custom plastic moulding suppliers?
Sourcifychina.com offers free quotas from reliable custom plastic molding suppliers for several reasons. Firstly, Sourcifychina.com aims to provide a seamless sourcing experience for businesses looking to manufacture plastic products. By partnering with reliable suppliers, they can ensure high-quality and cost-effective production for their clients.
Secondly, offering a free quota helps businesses understand the cost implications of manufacturing plastic products. Many factors, such as the complexity of the design, materials used, and production quantity, influence the cost of custom plastic molding. By obtaining a free quota, businesses can accurately assess the financial feasibility of their projects without committing to any financial obligations upfront.
Furthermore, Sourcifychina.com recognizes the importance of building trust and long-term relationships with clients. By providing a free quota, they eliminate any barriers to entry for companies interested in manufacturing plastic products. This transparent approach helps foster trust and confidence in the sourcing process, giving businesses the assurance that they are working with a reliable partner.
Additionally, Sourcifychina.com understands that time is of the essence for businesses looking to bring their plastic products to market. By offering a free quota, they streamline the supplier selection process, saving businesses valuable time in sourcing and negotiating with potential suppliers. This efficient approach allows businesses to focus on other critical aspects of their operations, ultimately speeding up the time-to-market for their products.
In summary, Sourcifychina.com offers free quotas from reliable custom plastic molding suppliers to provide a seamless sourcing experience, help businesses understand the cost implications, build trust and long-term relationships, and save valuable time in the supplier selection process. This comprehensive approach enables businesses to manufacture high-quality plastic products efficiently and cost-effectively.