Introduce about custom injection molded plastic guide,Qulity,Cost,Supplier,Certification,Market,Tips,FAQ
Custom injection molded plastic guides are small plastic components that are used to guide and direct the movement of various products and parts. These guides are designed specifically to meet the unique requirements of a particular application and are made through the process of injection molding, which involves injecting molten plastic into a mold cavity. This allows for the production of precise and consistent guides with complex geometries.
Quality is a crucial factor when it comes to custom injection molded plastic guides. High-quality guides should exhibit dimensional accuracy, excellent surface finish, and good mechanical properties. It is important to choose a reputable and experienced injection molding supplier who can deliver guides that meet your exact specifications.
Cost considerations are also important when opting for custom injection molded plastic guides. Factors like the complexity of the design, material selection, and production volume can impact the overall cost. Injection molding offers cost advantages for large production runs due to its high efficiency and repeatability.
When choosing a supplier for custom injection molded plastic guides, it is essential to ensure that they have the necessary certifications. ISO 9001 certification signifies that the supplier follows strict quality management systems, ensuring reliable and consistent products. Additionally, suppliers with certifications relevant to specific industries, such as automotive or medical, can provide added assurance.
The market for custom injection molded plastic guides is diverse and spans across various industries. They are commonly used in automotive, electronics, medical, consumer goods, and many other sectors. The demand for these guides is driven by the need for precise and efficient movement in products and assemblies.
Here are a few tips to consider when seeking custom injection molded plastic guides:
1. Clearly define your requirements, including dimensions, materials, and tolerances.
2. Work closely with your injection molding supplier to optimize the design for manufacturability and cost efficiency.
3. Request samples or prototypes to evaluate the quality and performance of the guides before committing to a larger production run.
Frequently Asked Questions (FAQ):
Q: Can custom injection molded plastic guides be made from different materials?
A: Yes, various plastics can be used, including ABS, polycarbonate, nylon, and polypropylene.
Q: What is the typical lead time for custom injection molded plastic guides?
A: Lead times can vary depending on the complexity and volume, but typically range from a few weeks to a few months.
Q: Are there any design limitations for custom injection molded plastic guides?
A: While injection molding allows for complex designs, it is important to consider factors like draft angles, wall thickness, and undercuts to ensure successful production.
In conclusion, custom injection molded plastic guides are high-quality, cost-effective components that play a critical role in directing the movement of products. It is essential to work with a reputable supplier and clearly define your requirements to achieve optimal results.
Types of custom injection molded plastic
Injection molding is a versatile manufacturing process for producing a wide range of custom plastic parts. This process involves injecting molten plastic into a mold cavity, allowing it to cool and solidify before being ejected from the mold. There are various types of custom injection molded plastics that can be produced, each offering unique properties, characteristics, and applications.
1. Polyethylene (PE): This is a widely used plastic known for its versatility, durability, and resistance to chemicals. It is commonly used in packaging materials, bottles, and toys.
2. Polypropylene (PP): PP is a thermoplastic with excellent chemical resistance and high tensile strength. It is used in various industries for products such as automotive parts, medical devices, and containers.
3. Acrylonitrile Butadiene Styrene (ABS): ABS is a lightweight and impact-resistant plastic that is commonly used in the automotive industry for interior and exterior trim components, as well as consumer electronics and toys.
4. Polycarbonate (PC): PC offers exceptional transparency, high impact resistance, and excellent thermal resistance. It is widely used in industries such as automotive, electronics, and medical for applications like safety glasses, lenses, and electrical components.
5. Polyethylene terephthalate (PET): PET is a strong, lightweight, and recyclable plastic used predominantly in the packaging industry for bottles, food containers, and polyester fibers for textiles.
6. Polyvinyl Chloride (PVC): PVC is a versatile plastic with a wide range of applications in construction, healthcare, and electrical industries. It is known for its resistance to chemicals, weathering, and fire.
7. Nylon (PA): Nylon is a durable and versatile thermoplastic with high mechanical strength and low friction. It is commonly used in applications such as gears, bearings, electrical connectors, and textiles.
8. Polystyrene (PS): PS is a lightweight and rigid plastic used in various applications such as packaging materials, disposable utensils, and insulation.
9. Polyoxymethylene (POM): POM, also known as acetal, is a strong and stiff plastic with excellent dimensional stability and low friction properties. It is commonly used in engineering applications like gears, bushings, and connectors.
These are just a few examples of the many types of custom injection molded plastics available. The choice of material depends on the specific requirements of the final product, including mechanical strength, chemical resistance, transparency, and temperature resistance. Injection molding allows for the production of complex shapes and precise dimensions, making it a preferred manufacturing process for numerous industries.
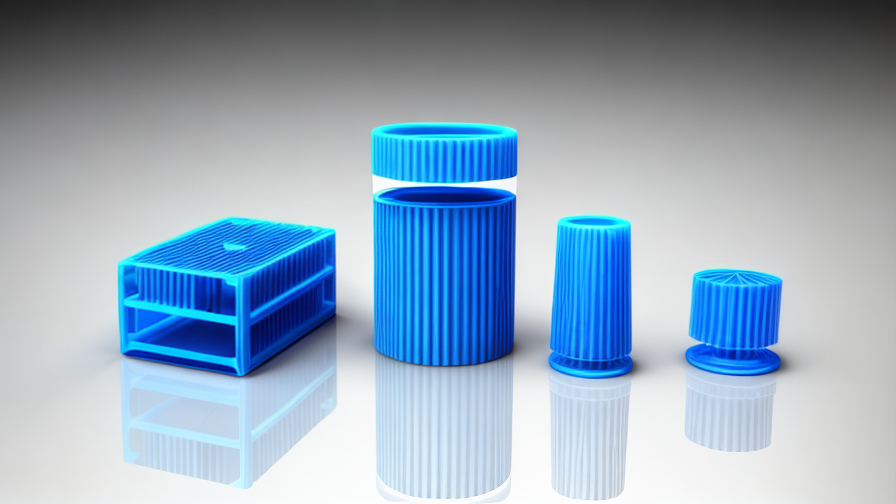
Pros and Cons of Using custom injection molded plastic
Custom injection molded plastic is widely used in various industries due to its versatility, durability, and cost-effectiveness. However, like any other manufacturing process, there are pros and cons to consider when deciding whether to use this method.
Pros:
1. Design flexibility: Custom injection molding allows for the production of complex and intricate shapes that may not be achievable with other manufacturing techniques. It offers a high degree of design freedom, allowing for the creation of customized parts that meet specific requirements.
2. Cost-effective for large volumes: Once the initial tooling and setup costs are covered, injection molding becomes a cost-effective option for large production runs. The per-unit cost decreases significantly as the volume of production increases, making it ideal for mass production.
3. Efficient production process: Injection molding is a highly automated and efficient process, enabling large quantities of parts to be produced quickly and consistently. The high-speed production capabilities of injection molding help meet tight project deadlines.
4. Material options: Injection molding allows for the use of a wide range of thermoplastic materials, each with unique properties. This flexibility in material selection makes it suitable for various applications across different industries.
Cons:
1. High initial setup costs: The tooling and mold costs associated with custom injection molding can be significant, especially for small production runs. The initial investment required for designing and manufacturing molds can deter small-scale operations.
2. Design limitations: While injection molding enables high design flexibility, certain design constraints must be considered. Factors such as draft angles, wall thickness, and undercuts may affect the feasibility of the design and increase costs.
3. Lead time: Developing molds and tooling can take weeks or even months, which may not be suitable for projects with tight timelines. The lead time associated with custom injection molding can delay product development and production.
4. Environmental impact: Plastic waste generated during the injection molding process can be a concern. The disposal and recycling of plastic materials require proper management to minimize environmental impact and ensure sustainability.
In conclusion, custom injection molded plastic offers numerous advantages in terms of design flexibility, cost-effectiveness for large volumes, efficient production, and material options. However, it is essential to consider the high initial setup costs, design limitations, lead time, and environmental impact associated with this manufacturing process.
custom injection molded plastic Reference Specifications (varies for different product)
Custom Injection Molded Plastic Reference Specifications (Varies for Different Product):
Injection molding is a widely used manufacturing process for producing plastic components in large quantities. The process involves injecting molten plastic material into a mold, which then cools and solidifies to form the desired shape. To ensure the successful production of custom injection molded plastic products, it is essential to establish reference specifications that vary depending on the specific product being manufactured.
1. Material Selection: The choice of the plastic material is crucial as it greatly impacts the product’s performance and properties. Factors such as strength, durability, chemical resistance, and temperature stability must be considered during material selection. Common plastics used in injection molding include polypropylene (PP), polystyrene (PS), polyethylene (PE), acrylonitrile-butadiene-styrene (ABS), and polyvinyl chloride (PVC).
2. Mold Design: The mold design should be tailored to the specific product requirements. Factors like complexity, parting line placement, wall thickness, gate location, and ejection method must be carefully considered. The mold design should facilitate proper filling of the cavity, minimize defects like warping and sink marks, and ensure easy ejection of the final product.
3. Injection Molding Machine: The selection of an appropriate injection molding machine is based on factors such as the required clamping force, shot size, and the type of plastic material being used. The machine should be capable of maintaining consistent melt temperature and injection pressure to produce high-quality parts.
4. Quality Control: To ensure consistent quality, various quality control measures should be implemented. This includes regular inspection of the molded parts for defects like flash, voids, sinks, and dimensional inaccuracies. Statistical process control (SPC) techniques can be employed to monitor key process parameters and identify any deviations from the desired specifications.
5. Post-Molding Operations: Some products may require additional post-molding operations such as trimming, painting, assembly, or packaging. These operations should be considered during the design phase and the necessary equipment and resources should be allocated accordingly.
In conclusion, custom injection molded plastic products require careful consideration of various specifications. These specifications vary depending on the specific product being manufactured and include aspects like material selection, mold design, injection molding machine choice, quality control measures, and post-molding operations. By adhering to these specifications, manufacturers can ensure the production of high-quality custom injection molded plastic products that meet the desired requirements.
Applications of custom injection molded plastic
Custom injection molded plastic has numerous applications across different industries due to its versatility, durability, and cost-effectiveness. Some of the major applications include:
1. Automotive Industry: Custom injection molded plastic is widely used in the automotive industry for manufacturing various components such as bumpers, interior trim, dashboards, door panels, and engine parts. Its lightweight properties, corrosion resistance, and ability to meet aesthetic requirements make it an ideal choice for automotive manufacturers.
2. Consumer Electronics: The electronics industry extensively utilizes custom injection molded plastic for the production of components like casings, covers, connectors, and buttons. Plastic’s electrical insulation properties, moldability, and ability to incorporate intricate details make it suitable for electronic devices.
3. Packaging Industry: Injection molded plastic is widely used in the packaging industry for the production of containers, lids, caps, and bottles. Its excellent moisture resistance, ability to preserve product integrity, and design flexibility make it a popular choice in the packaging of food, beverages, personal care products, and pharmaceuticals.
4. Medical and Healthcare: Custom injection molded plastic plays a crucial role in the medical and healthcare sector. It is used for manufacturing a wide range of products including syringes, IV components, medical device housings, surgical instruments, and drug delivery systems. The biocompatibility, sterilizability, and precision of injection molded plastic make it indispensable in this industry.
5. Aerospace and Defense: Injection molded plastic is extensively used in the aerospace and defense industries for the production of components like housings, brackets, connectors, and enclosures. Its lightweight properties, high strength-to-weight ratio, and ability to withstand extreme temperatures and conditions make it suitable for aerospace and defense applications.
6. Toys and Recreational Products: Many toys, games, and recreational products are made using custom injection molded plastic. Its flexibility, ability to replicate detailed features, and cost-effectiveness make it well-suited for the production of a wide range of toys and recreational items.
7. Industrial Equipment and Machinery: Injection molded plastic is utilized in the manufacturing of various industrial equipment and machinery components, including gears, handles, grips, and electrical connectors. Its ability to withstand high impact, resistance to chemicals and UV radiation, and excellent dimensional stability make it suitable for the demanding requirements of industrial applications.
In conclusion, custom injection molded plastic finds applications in diverse industries such as automotive, consumer electronics, packaging, medical, aerospace, toys, and industrial equipment. Its versatility, durability, cost-effectiveness, and ability to meet specific design requirements make it a favored choice for manufacturers across different sectors.
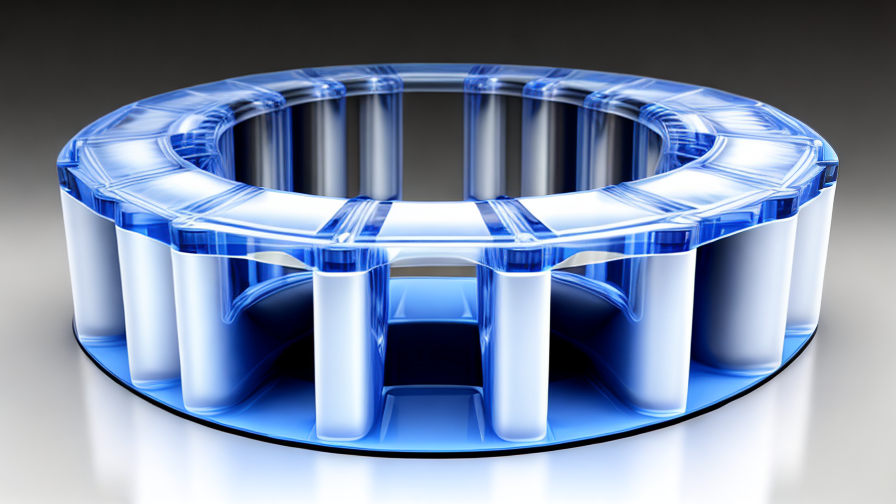
The Work Process and how to use custom injection molded plastic
The work process of custom injection molding involves several steps that begin with the design and end with the production of the final plastic product. Here is a brief overview of the process.
1. Design: The first step is to create a 3D CAD (Computer-Aided Design) model of the desired plastic product. This model will serve as a blueprint for the mold creation and production.
2. Mold Creation: Once the design is finalized, a mold is created. The mold is typically made from steel and is customized to match the exact specifications of the product. It consists of two halves – the cavity and the core – that fit together to form the desired shape of the plastic part.
3. Material Selection: The appropriate plastic material is chosen based on factors such as the product’s function, required strength, and desired aesthetics. Common materials used in injection molding include ABS, polypropylene, polycarbonate, and nylon.
4. Injection Molding: The selected plastic material is heated until it reaches a molten state. It is then injected into the mold under high pressure. The molten plastic fills the cavity of the mold, conforming to its shape.
5. Cooling and Solidification: After the plastic is injected into the mold, it is allowed to cool and solidify. This typically takes a few seconds. Cooling can be accelerated using cooling channels within the mold.
6. Ejection: Once the plastic has solidified, the mold opens, and the plastic part is ejected. Ejector pins, located within the mold, push the part out of the mold.
7. Finishing: The ejected plastic part may require additional finishing processes such as trimming, sanding, or painting to achieve the desired final appearance. Any excess material or flash is removed.
Custom injection molded plastic is widely used in various industries, including automotive, electronics, medical, and consumer goods, among others. It offers numerous advantages such as high production volumes, precise and complex part geometries, cost-effectiveness, and fast production cycles. The versatility of injection molding allows for the production of a wide range of products, from small intricate components to large structural parts.
In conclusion, custom injection molding is a versatile manufacturing process that enables the production of complex plastic parts in high volumes. It involves designing a mold, selecting the appropriate material, injecting the molten plastic into the mold, cooling and solidifying the plastic, ejecting the final product, and finishing as required. The process is highly efficient and widely utilized in various industries.
Quality Testing Methods for custom injection molded plastic and how to control the quality
Quality testing methods for custom injection molded plastic are essential to ensure that the final product meets the desired specifications and standards. There are several key methods employed to control quality in injection molding:
1. Visual Inspection: A visual inspection is typically carried out to identify any visible defects such as surface imperfections, part deformation, or inconsistencies in color or texture. This method helps to identify any cosmetic defects that may affect the overall quality and appearance of the product.
2. Dimensional Inspection: Measurement tools such as calipers, micrometers, and gauges are used to verify the dimensional accuracy of the molded parts. This ensures that the product conforms to the specified dimensions and tolerances, minimizing any functional issues that may arise due to improper sizing.
3. Functional Testing: Functional testing involves assessing the performance of the molded parts under real-world conditions. This may include testing mechanical strength, flexibility, impact resistance, or any other specific functional requirements. Various machines and equipment may be used to simulate the product’s intended usage and evaluate its performance.
4. Material Analysis: Testing the material properties is crucial to ensure the quality of custom injection molded plastic. This includes analyzing the melt flow index (MFI), tensile strength, thermal properties, and other material characteristics. These tests help to verify that the chosen material meets the desired specifications and can withstand the intended applications.
5. Statistical Process Control (SPC): SPC involves continuously monitoring and controlling the injection molding process to optimize quality. Key process parameters including temperature, pressure, cooling time, and injection speed are regularly measured and analyzed through statistical methods to identify any variations or inconsistencies. By maintaining these parameters within specified limits, the process can be controlled to produce consistent, high-quality products.
To effectively control the quality of custom injection molded plastic, it is important to establish robust quality control procedures, including regular inspections during production, in-process checks, and final inspections before shipment. It is also crucial to train and educate the manufacturing team to identify potential defects and implement corrective actions promptly. Additionally, documentation and record keeping throughout the production process are vital to track and analyze quality data, enabling continuous improvement efforts.
By employing these quality testing methods and implementing effective control measures, manufacturers can ensure that custom injection molded plastic meets the required standards, resulting in customer satisfaction and product success.
custom injection molded plastic Sample Policy and Post-Purchase Considerations for custom injection molded plastic from China
Sample Policy:
When ordering custom injection molded plastic from China, it is essential to have a clear understanding of the sample policy offered by the supplier. The sample policy outlines the terms and conditions regarding the provision of samples before placing a bulk order. Typically, suppliers may charge for samples and shipping costs, but they may offer refunds or deduct the sample costs from the final order if the customer proceeds with the purchase. It is advisable to negotiate the sample policy beforehand to ensure both parties are clear on expectations and costs.
Post-Purchase Considerations:
After receiving the custom injection molded plastic from China, there are several post-purchase considerations to keep in mind:
1. Quality Assurance: Inspect the received plastic parts for any defects or discrepancies. Compare them to the approved samples and specifications. Contact the supplier immediately if there are any issues to discuss possible resolutions.
2. Packaging and Transportation: Evaluate the packaging quality and condition. If there are concerns about the packaging’s ability to protect the products during transportation, address them with the supplier. Proper packaging is crucial to avoid damages during transit.
3. Communication: Maintaining open lines of communication with the supplier is key. Promptly communicate any problems or concerns regarding the delivered products. Addressing issues at the earliest possible stage can increase the chances of finding suitable solutions.
4. Performance Testing: Conduct performance tests on the custom injection molded plastic to ensure they meet the required standards. This may include tests for durability, functionality, and compliance with regulations. Any issues found should be communicated to the supplier for resolution.
5. Feedback and Review: Provide constructive feedback to the supplier based on the products’ performance and overall experience. This helps improve the long-term relationship and encourages the supplier to rectify any issues promptly.
It is important to document all interactions and findings during the sample policy and post-purchase considerations process for future references and to assist in any potential dispute resolutions.
Sourcing custom injection molded plastic from China: Opportunities, Risks, and Key Players
Sourcing custom injection molded plastic from China presents both opportunities and risks for businesses. China is currently the largest producer of injection molded plastics in the world, providing a wide range of opportunities for companies looking to manufacture their products at a lower cost. The country has a well-developed infrastructure, a large pool of skilled labor, and a vast network of suppliers and manufacturers.
One key opportunity of sourcing from China is cost savings. Chinese manufacturers usually offer competitive pricing due to lower labor and operational costs. This allows businesses to reduce production expenses and stay competitive in the market. Moreover, companies can benefit from economies of scale as China has a vast manufacturing capacity, making it easier to meet larger order quantities.
However, there are risks associated with sourcing from China as well. Quality control can be a major concern, as some manufacturers may prioritize cost-cutting over ensuring high-quality products. Companies should thoroughly research and vet potential suppliers to ensure they possess the necessary certifications and quality control procedures. Regular inspections and strict quality control measures should be implemented to maintain product integrity.
Intellectual property (IP) protection is another risk in China. Despite efforts to strengthen IP laws, infringement cases still occur. Businesses should consider protecting their designs, patents, and trademarks before engaging with Chinese suppliers. Implementing legal contracts and Non-Disclosure Agreements (NDAs) with manufacturers can also help safeguard against IP theft.
When considering sourcing custom injection molded plastic from China, several key players dominate the market. Some prominent Chinese companies in the industry include Foxconn Technology Group, BYD Co. Ltd, and Midea Group. These companies have extensive manufacturing capabilities and experience in producing custom injection molded plastic products.
In conclusion, sourcing custom injection molded plastic from China presents significant opportunities for cost savings and manufacturing capabilities. However, businesses need to carefully assess the risks associated with quality control and IP protection. Conducting thorough due diligence and implementing necessary safeguards can help mitigate these risks and ensure successful sourcing from China.
How to find and select reliable custom injection molded plastic manufacturers in China,use google search manufacturers and suppliers
When looking for reliable custom injection molded plastic manufacturers in China, using Google search is indeed a good starting point. Here are some steps to follow to find and select the right manufacturer:
1. Conduct a Google search: Use specific keywords related to your requirements, such as “custom injection molded plastic manufacturers in China” or “reliable plastic injection molding suppliers.” This will help narrow down the results to manufacturers specializing in your desired products.
2. Evaluate the websites: Visit the websites of potential manufacturers to gather relevant information. Look for details like company background, manufacturing capabilities, product range, certifications, quality control measures, and customer reviews/testimonials. A well-designed and informative website can indicate a manufacturer’s professionalism and reliability.
3. Check experience and expertise: Look for manufacturers with considerable experience in the industry. A long track record suggests their ability to deliver consistent quality. Seek out companies that have expertise in your specific niche or industry, as they will likely have a better understanding of your requirements.
4. Assess production capabilities: Determine whether the manufacturer has the technological capabilities and equipment to produce the plastic components you need. Consider factors like mold size, injection molding machines, capacity, material availability, and types of plastic they can work with (e.g. ABS, PET, PVC, etc.).
5. Quality assurance: Ensure the manufacturer follows stringent quality control measures. Look for certifications such as ISO 9001, ISO 14001, or ISO/TS 16949, as they indicate adherence to international quality standards. Inquire about quality inspection processes, testing equipment, and certifications for raw materials.
6. Communication and support: Evaluate the manufacturer’s communication skills and responsiveness. Prompt and clear communication is essential to ensure your project requirements are understood and met. Look for manufacturers who can provide technical support, assist with design improvements if needed, and offer after-sales service.
7. Request quotes and samples: Shortlist a few manufacturers and request detailed quotes that include factors like mold costs, unit prices, lead times, and shipping options. It’s advisable to order product samples to evaluate the manufacturer’s product quality firsthand.
8. Verify supplier credibility: Cross-check the credibility of potential manufacturers by seeking references, customer reviews, or online ratings. You can also use supplier directories or platforms like Alibaba to check their reputation and credibility.
9. Payment terms and contracts: Clarify payment terms, such as deposits, milestone payments, and final payments. Ensure that a contract is in place, clearly defining product specifications, pricing, delivery timelines, quality standards, and intellectual property rights.
Remember, due diligence is crucial in vetting the reliability and credibility of manufacturers in China. Take time to research, gather information, and communicate effectively to find a trustworthy partner for your custom injection molded plastic needs.
How to check custom injection molded plastic manufacturers website reliable,use google chrome SEOquake check if ranking in top 10M
To check the reliability of a custom injection molded plastic manufacturer’s website, you can follow these steps:
1. Use Google Chrome: Start by opening the website in Google Chrome, which offers useful browser extensions for website analysis.
2. Install SEOquake: Install the SEOquake extension for Google Chrome, which provides valuable insights and data about a website’s SEO performance.
3. Check Rankings: With SEOquake installed, activate it by clicking on the SEOquake icon in your browser toolbar. Look for the “Density” tab and click on it.
4. Set Parameters: In the Density tab, select the parameters you want to analyze. To determine the website’s reliability, focus on the “Number of indexed pages” and the “Number of incoming links” to get an idea of their web presence.
5. Verify Rankings: Once the parameters are selected, scroll down to the bottom of the page and look for the “Number of results in Google” section. Here, you should find a figure indicating the website’s ranking position among the top 10 million websites on the internet, with 1 being the highest.
6. Interpret the Data: If the website’s rankings are within the top 10 million, it usually signifies good web presence and reliability. However, it’s important to consider other factors such as the quality and relevance of the website’s content, customer reviews, certifications, credentials, and industry reputation.
7. Utilize Additional Resources: It is recommended to conduct a thorough evaluation of the manufacturer by checking their customer feedback, testimonials, case studies, certifications (ISO, FDA, etc.), years of experience, and any other relevant details that can establish their credibility.
Remember, although checking a website’s rankings can provide an initial assessment of reliability, it is crucial to gather more information from various sources to make an informed decision about a custom injection molded plastic manufacturer.
Top 10 custom injection molded plastic manufacturers in China with each 160 words introduce products,then use markdown create table compare
1. Sinotech: With over 20 years of experience, Sinotech specializes in custom injection molding of plastic components. Their products range from automotive parts to consumer electronics, medical devices, and more. They emphasize quality control, innovative solutions, and competitive pricing.
2. Xiamen Better Silicone Rubber Co., Ltd: Focusing on silicone and plastic injection molding, Xiamen Better Silicone Rubber Co., Ltd offers a wide array of custom-made products. They cater to various industries such as electrical appliances, automotive, healthcare, and more. Their expertise lies in providing durable, precise, and cost-effective solutions.
3. Topworks Plastic Mold: Topworks is a leading plastic injection molding manufacturer, offering comprehensive services from design to production. They specialize in manufacturing high-quality, precision plastic parts for industries like electronics, automotive, household appliances, and more. Their commitment to professional service and customer satisfaction sets them apart.
4. HONGKAI: HONGKAI is a renowned custom injection molded plastic manufacturer in China. Their products span across industries such as automotive, electronics, medical, and more. They pride themselves on their competitive pricing, strict quality control measures, and efficient production processes.
5. JINGXIANG: With a focus on precision injection molding, JINGXIANG is a trusted manufacturer offering high-quality plastic parts. They serve industries such as automotive, electronics, telecommunications, and more. Their advanced production facilities and experienced team ensure reliable products and timely delivery.
6. STAR Prototype Manufacturing Co., Ltd: STAR Prototype is a leading provider of rapid injection molding services in China. They offer a wide range of plastic materials and finishes, catering to various industries like consumer electronics, medical devices, automotive, and more. Their emphasis on technological innovation and quick turnaround sets them apart.
7. Hord Plastic Mold Co., Ltd: Hord Plastic Mold specializes in custom injection molded plastic parts for industries like automotive, appliances, electronics, and more. Their vast production capabilities and quality assurance measures ensure the delivery of durable and precise products.
8. SPRING: SPRING is a trusted injection molding manufacturer in China, offering a diverse range of plastic parts. With expertise in design, production, and quality control, SPRING caters to industries including automotive, medical, electronics, and more. Their focus on customer satisfaction and cost-effective solutions distinguishes them in the market.
9. Bonamite Engineering Co., Ltd: Bonamite Engineering is committed to providing custom injection molded plastic products for sectors such as automotive, machinery, electronics, and more. With advanced facilities and comprehensive quality control, they offer reliable and cost-effective solutions.
10. Yuyao Dongxin Electric Appliance Co., Ltd: Specializing in plastic injection molded components, Yuyao Dongxin Electric Appliance offers a wide range of products for industries such as automobiles, household appliances, and electronics. Their experienced team and efficient production processes ensure high-quality and cost-effective solutions.
| Manufacturer | Expertise | Industries Served |
|—————————-|———————————————–|————————————————-|
| Sinotech | Automotive, consumer electronics, medical | Automotive, consumer electronics, medical |
| Xiamen Better Silicone | Silicone and plastic molding | Electrical appliances, automotive, healthcare |
| Topworks Plastic Mold | Plastic parts | Electronics, automotive, household appliances |
| HONGKAI | Custom molded plastic parts | Automotive, electronics, medical |
| JINGXIANG | Precision plastic parts production | Automotive, electronics, telecommunications |
| STAR Prototype | Rapid injection molding services | Consumer electronics, medical, automotive |
| Hord Plastic Mold | Injection molded plastic parts | Automotive, appliances, electronics |
| SPRING | Custom injection molding | Automotive, medical, electronics |
| Bonamite Engineering | Custom injection molded plastic products | Automotive, machinery, electronics |
| Yuyao Dongxin Electric | Plastic injection molded components | Automobiles, household appliances, electronics |
These top 10 custom injection molded plastic manufacturers in China offer a broad range of expertise, catering to diverse industries such as automotive, electronics, medical, and more. While each manufacturer possesses unique strengths, they share a commitment to quality control, precision manufacturing, and competitive pricing. By utilizing their advanced facilities and experienced teams, these manufacturers provide reliable and cost-effective solutions for various plastic molding needs.
Background Research for custom injection molded plastic manufacturers Companies in China, use qcc.com archive.org importyeti.com
When looking for custom injection molded plastic manufacturers in China, a few websites can provide useful background research. Qcc.com, archive.org, and importyeti.com are reliable platforms that can offer valuable information about the companies.
Qcc.com is an online business directory that provides comprehensive data about Chinese enterprises. It offers details such as company profiles, contact information, legal status, credit history, and even their production capacity. This platform can be extremely beneficial in gauging the credibility and trustworthiness of potential manufacturers. Users can search for specific manufacturers, view their information, and verify their authenticity by checking their legal status and credit history.
Archive.org is a digital library that provides access to archived web pages. This can be particularly useful for researching the manufacturers’ websites and tracking their historical changes. By comparing different versions of their websites over time, one can gain insights into the development of the company, its portfolio, and its reputation. This can help in assessing how the manufacturer has evolved and whether they have consistently maintained a good standard.
Importyeti.com is an import/export data platform that offers access to shipment records and customs data. It allows users to search for specific products and discover the manufacturers who have been exporting them. This platform can provide valuable information about manufacturers’ export history, their product range, and the countries they have been exporting to. Examining the data can help in assessing the experience and expertise of the manufacturer in the specific field of custom injection molded plastics.
By utilizing these platforms, researchers can gather comprehensive information about custom injection molded plastic manufacturers in China. This background research can assist in shortlisting potential manufacturers and making informed decisions based on the credibility, performance history, and expertise of the companies.
Leveraging Trade Shows and Expos for custom injection molded plastic Sourcing in China
Trade shows and expos are valuable platforms for sourcing custom injection molded plastics in China. These events offer an opportunity for businesses to connect with manufacturers, explore product samples, and establish reliable partnerships.
China is renowned for its strong manufacturing capabilities and expertise in injection molding. By attending trade shows and expos in the country, businesses can gain access to a wide range of suppliers and manufacturers specializing in plastic injection molding. These events act as a hub for industry professionals to showcase their products, technology, and expertise.
One of the key advantages of trade shows and expos is the ability to see and evaluate product samples firsthand. This allows businesses to assess the quality, design, and functionality of injection molded plastics. By physically inspecting and testing samples, companies can make informed decisions about the suitability of a supplier or manufacturer.
Trade shows and expos also provide an opportunity for face-to-face interactions with potential suppliers. Engaging in direct discussions allows businesses to establish personal connections, address concerns, and negotiate favorable terms. Building relationships with manufacturers is essential to ensure a reliable supply chain and timely delivery of custom injection molded plastics.
Additionally, these events often feature seminars, workshops, and demonstrations that offer insights into the latest technology and trends in injection molding. Keeping up with industry advancements can help businesses identify innovative solutions and stay competitive in the market.
To maximize the benefits of trade shows and expos in China, businesses should thoroughly research and plan their attendance. It is crucial to identify relevant exhibitions, pre-register, and prepare a list of potential suppliers to visit. Companies should also set clear objectives, such as sourcing new suppliers, exploring product options, or gathering market intelligence.
In conclusion, trade shows and expos in China present an excellent opportunity for businesses to source custom injection molded plastics. By attending these events, companies can connect with manufacturers, assess product samples, establish relationships, and stay updated on industry trends. Leveraging trade shows and expos can ultimately contribute to successful sourcing and manufacturing operations in China.
The Role of Agents and Sourcing Companies in Facilitating custom injection molded plastic Purchases from China
Agents and sourcing companies play a crucial role in facilitating custom injection molded plastic purchases from China. These entities act as intermediaries, connecting buyers with reliable and reputable manufacturers in China. They assist in various aspects of the purchasing process, ensuring a smooth and successful transaction.
One of the primary functions of agents and sourcing companies is to conduct supplier identification and selection. They have an in-depth understanding of the market and can help buyers find suitable manufacturers that meet their specific requirements in terms of quality, price, and production capabilities. This saves buyers time and effort in searching for suppliers themselves.
Agents also provide guidance on product development and design. They possess knowledge about the injection molding process and can advise buyers on aspects such as design feasibility and material selection. Their expertise helps to ensure that the final product meets the buyer’s expectations and performs its intended function effectively.
Another crucial role agents play is negotiating prices and terms with suppliers. They have established relationships with manufacturers and possess a deep understanding of the local market conditions. This allows them to negotiate favorable deals on behalf of the buyer, helping to secure competitive pricing and favorable terms of trade.
Agents and sourcing companies also oversee the production process. They monitor manufacturing timelines, quality control procedures, and ensure compliance with buyer specifications. This ensures that the injection molded plastic products meet the required standards and are delivered on time.
Lastly, agents and sourcing companies handle logistics and shipping arrangements. They have experience in navigating the complexities of international shipping and can coordinate the transportation of the products from China to the buyer’s location. This includes managing customs clearance, documentation, and any necessary certifications or inspections.
In summary, agents and sourcing companies in China play a vital role in facilitating custom injection molded plastic purchases. They assist with supplier identification, product development, negotiation, production oversight, and logistics. Their expertise and local knowledge help to streamline the purchasing process and ensure successful outcomes for buyers.
Price Cost Research for custom injection molded plastic manufacturers Companies in China, use temu.com and 1688.com
When it comes to finding custom injection molded plastic manufacturers in China, two popular platforms to consider are temu.com and 1688.com. These platforms offer a wide range of companies and suppliers that specialize in injection molding.
Both temu.com and 1688.com are user-friendly websites that allow buyers to explore various manufacturers and compare their products and services. By searching for custom injection molded plastic manufacturers on these platforms, you can find a plethora of options to suit your specific needs.
One advantage of using temu.com is its efficient search engine that allows you to filter suppliers based on criteria such as location, certification, and product type. This makes it easier to find manufacturers that meet your requirements. Moreover, temu.com provides a convenient messaging system that enables direct communication with suppliers to discuss your custom injection molding needs and negotiate prices.
On the other hand, 1688.com is a wholesale marketplace where you can find a wide range of manufacturers and suppliers, including injection molding companies. Although the website is primarily in Chinese, it offers a translation feature that allows non-Chinese speakers to navigate through the platform. Furthermore, the vast number of listings on 1688.com provides a greater chance of finding a manufacturer that fits your budget and desired production volume.
When researching prices for custom injection molded plastic manufacturers on these platforms, it is essential to consider factors such as material quality, production volume, tooling costs, and shipping fees. Additionally, requesting and comparing multiple quotes from different suppliers will help you make a more informed decision.
In conclusion, temu.com and 1688.com are valuable resources for finding custom injection molded plastic manufacturers in China. With their extensive supplier databases and user-friendly interfaces, you can explore various options, compare prices, and communicate directly with manufacturers to ensure you get the best possible pricing and production services for your specific requirements.
Shipping Cost for custom injection molded plastic import from China
The shipping cost for custom injection molded plastic imports from China can vary depending on several factors such as weight, volume, distance, and mode of transportation. Generally, there are two main options for shipping: air freight and sea freight.
Air freight is the faster option, but it can be more expensive. The cost is usually calculated based on the weight and volume of the shipment. Air shipping can be ideal for smaller or urgent orders, but it may not be cost-effective for larger or heavier shipments.
Sea freight, on the other hand, is a more economical option for larger volumes. The cost is usually calculated based on the shipping container’s size, either full container load (FCL) or less than container load (LCL). FCL is more cost-effective if you have a significant amount of goods, while LCL is suitable for smaller orders.
Additional costs to consider are customs duties, taxes, and import fees. These vary based on the destination country’s regulations. Importers may also need to consider hiring a customs broker to assist with the customs clearance process, which incurs additional costs.
To get accurate shipping quotes, it is important to provide detailed information about the shipment, such as the product dimensions, weight, number of units, and destination. It is recommended to work with reliable shipping companies or freight forwarders to ensure efficient and secure transportation.
In conclusion, the shipping cost for custom injection molded plastic imports from China depends on multiple factors, including the transportation mode, shipment size, and destination. Proper planning and research are crucial to find the most suitable and cost-effective shipping solution for your specific needs.
Compare China and Other custom injection molded plastic Markets: Products Quality and Price,Visible and Hidden Costs
China and other custom injection molded plastic markets have both similarities and differences in terms of product quality and price, as well as visible and hidden costs.
In terms of product quality, China has made significant progress over the years and now offers a wide range of high-quality injection molded plastic products. Chinese manufacturers have invested heavily in advanced technology and machinery, allowing them to produce products that meet international quality standards. Other custom injection molded plastic markets, such as those in Europe and the United States, have a long-standing reputation for producing high-quality products. These markets often have stricter quality control measures in place and prioritize precision and durability.
When it comes to price, China has traditionally been known for offering competitive rates due to its large-scale manufacturing capabilities and lower labor costs. Chinese manufacturers can leverage economies of scale to produce injection molded plastic products at a lower cost compared to other markets. This has made China a popular destination for outsourcing manufacturing operations. However, other custom injection molded plastic markets may have higher manufacturing costs due to factors such as higher labor costs, stricter regulations, and smaller production volumes.
Visible costs, such as the initial product price and shipping costs, may vary between China and other markets. China’s manufacturing advantages allow for competitive pricing on products, making them attractive to buyers looking for cost-effectiveness. However, shipping costs from China may be higher due to the distance and associated logistical requirements.
Hidden costs, on the other hand, may also differ between China and other markets. These costs include factors like intellectual property protection, product quality control, and communication challenges. Other markets often prioritize intellectual property rights and have a more robust legal framework in place, reducing the risk of counterfeiting or other intellectual property infringements. Quality control measures in other markets may also be more stringent, resulting in lower product rejection rates and potential cost savings in the long run. Additionally, communicating with Chinese manufacturers who may have language barriers or cultural differences can sometimes lead to inefficiencies and potential problems.
In summary, China and other custom injection molded plastic markets have their own advantages and considerations. China offers competitive pricing and has made significant strides in product quality, although there may be some hidden costs associated with outsourcing to China. Other markets, on the other hand, often prioritize higher quality and have stricter regulations, potentially leading to higher visible costs but potentially lower hidden costs. Ultimately, buyers must carefully evaluate their specific requirements and the trade-offs they are willing to make.
Understanding Pricing and Payment Terms for custom injection molded plastic: A Comparative Guide to Get the Best Deal
Pricing and payment terms for custom injection molded plastic can vary significantly depending on various factors such as the complexity of the design, the type and quantity of materials used, tooling costs, manufacturing processes, and the level of customization required. To secure the best deal, it is essential to have a clear understanding of these elements and explore different suppliers. In this comparative guide, we will highlight key considerations when negotiating pricing and payment terms.
1. Design Complexity: Intricate molds and complex designs require more time, expertise, and specialized equipment, leading to higher costs. Simplifying the design can help reduce pricing.
2. Material Selection: Different plastics have unique properties and costs. Discuss with suppliers to determine the most suitable material for your application that balances cost, durability, and performance.
3. Quantity: Economies of scale apply to injection molding. Larger quantities often lead to lower unit costs as fixed overheads are spread across more parts. Negotiate volume discounts when possible.
4. Tooling Costs: Injection mold tooling can be a substantial initial investment. Compare tooling quotes from multiple suppliers and consider long-term production requirements before selecting a supplier.
5. Lead Time: Urgency may affect pricing. Longer lead times often offer better pricing since suppliers can optimize production schedules, reducing rush charges.
6. Annual Volume Commitments: Committing to a specific annual volume can lead to better pricing by assuring manufacturers of consistent revenue. Explore options for additional cost savings through agreements like blanket orders.
7. Payment Terms: Negotiate favorable payment terms, such as partial payments or credit, to improve cash flow. However, note that some suppliers may charge additional fees for accommodating non-standard terms.
8. Quality Assurance: Evaluate suppliers based on their quality track record and certifications. Non-compliant parts add costs through rework or rejects, impacting overall pricing.
9. Hidden Costs: Consider costs beyond the unit price, such as packaging, shipping, and potential post-production services. These can affect the overall deal.
10. Multiple Quotes: Obtain quotes from multiple suppliers to compare pricing, payment terms, lead times, and additional services. This will help identify the best overall value.
Negotiating pricing and payment terms for custom injection molded plastic requires a thorough understanding of the factors influencing costs and careful evaluation of various suppliers. By considering the key points mentioned in this guide, you can ensure you secure the best deal suited to your requirements.
Chinese Regulations and Industry Standards Certifications for custom injection molded plastic,Import Regulations and Customs for custom injection molded plastic from China
Chinese Regulations and Industry Standards Certifications for custom injection molded plastic
In China, the custom injection molded plastic industry is regulated by various regulations and industry standards certifications to ensure quality and safety. Some of the key regulations and certifications are as follows:
1. National Standards: China has established a set of national standards for custom injection molded plastic products. These standards cover various aspects such as material selection, production process, dimensional tolerances, and product performance.
2. Quality Management System Certification: Many injection molding companies in China obtain certifications such as ISO 9001:2015, which demonstrates their adherence to quality management principles and continuous improvement.
3. Environmental Regulations: China has strict regulations for controlling pollution and promoting environmental sustainability. Injection molding companies need to comply with environmental standards and obtain relevant certifications such as ISO 14001 to ensure proper waste management and reduce the environmental impact of their operations.
4. Safety Regulations: Chinese regulations require injection molding companies to follow safety guidelines and obtain certifications such as CE (Conformité Européene) marking for products exported to European markets. This ensures that the products meet the necessary safety requirements.
Import Regulations and Customs for custom injection molded plastic from China
When importing custom injection molded plastic from China, it is important to consider the following import regulations and customs procedures:
1. Customs Documentation: Proper documentation is essential for importing goods into any country. Importers need to prepare commercial invoices, packing lists, bill of lading/airway bill, and any other required documents according to the destination country’s customs requirements.
2. Customs Duties and Taxes: Importers should be familiar with the applicable customs duties and taxes imposed by their country on imported injection molded plastic products. They need to ensure accurate valuation and classification of the goods for smooth customs clearance.
3. Product Compliance: It is crucial to ensure that the imported injection molded plastic products comply with the importing country’s regulations and standards. This may involve testing and certification processes to demonstrate compliance with safety, quality, and performance requirements.
4. Customs Clearance: Importers need to engage a customs clearance agent or handle the process directly to facilitate the smooth entry of the goods into their country. This involves submitting the required documentation, paying customs duties and taxes, and complying with other customs procedures.
In summary, importing custom injection molded plastic from China requires compliance with both Chinese regulations and industry standards certifications, as well as understanding and adhering to the import regulations and customs procedures of the destination country.
Sustainability and Environmental Considerations in custom injection molded plastic Manufacturing
Sustainability and environmental considerations are becoming increasingly important in the manufacturing industry, including custom injection molded plastic manufacturing. This process involves the production of various plastic components by injecting molten plastic into a mold cavity, which then cools and solidifies to form the desired shape. However, the traditional methods of plastic manufacturing can have significant negative impacts on the environment.
To address these concerns, manufacturers are adopting several practices to improve sustainability and reduce their environmental footprint. One approach is the use of eco-friendly materials such as biodegradable or recyclable plastics. This allows for the reduction of non-biodegradable waste and promotes the use of materials that can be recycled or safely disposed of after use.
Another important consideration is energy consumption. Custom injection molding often requires the use of heating elements and machinery, resulting in significant energy consumption. Manufacturers are now investing in energy-efficient equipment to minimize energy consumption and reduce greenhouse gas emissions.
Additionally, waste management is crucial in plastic manufacturing. Companies are implementing sustainable waste management practices by implementing recycling programs and reusing excess materials. By regrinding and reusing plastic scrap, manufacturers can reduce waste and minimize the consumption of new raw materials.
Water conservation is also a critical aspect of sustainable manufacturing. Injection molding processes typically require the use of cooling water, which can lead to significant water consumption. Manufacturers are now implementing closed-loop water systems that reduce water usage by recycling and reusing water in the manufacturing process.
Furthermore, transportation and packaging play a role in the overall sustainability of injection molding processes. By optimizing transportation routes and using eco-friendly packaging materials, manufacturers can minimize carbon emissions associated with the transportation and storage of plastic components.
Overall, sustainability and environmental considerations in custom injection molded plastic manufacturing involve the adoption of eco-friendly materials, energy-efficient equipment, waste management practices, water conservation, and sustainable transportation and packaging. By implementing these measures, manufacturers can reduce their environmental impact and contribute to a more sustainable future.
List The Evolution history of “custom injection molded plastic”
Custom injection molded plastic has evolved significantly over the years, from its inception to the advanced techniques used in modern manufacturing processes. The history of this particular material can be traced back to the mid-19th century when Alexander Parkes introduced the first man-made plastic, called Parkesine, in 1856. However, the industrial-scale production of injection molded plastic began in the 1940s.
In the early days, injection molding was mainly used for producing simple objects like buttons and combs. The process involved heating plastic granules into a molten state and injecting them into a mold under pressure. This technique proved to be cost-effective and efficient in mass production, leading to its widespread adoption in various industries.
During the 1950s, advancements in polymer technology led to the introduction of more diverse materials for injection molding. For instance, polyethylene and polypropylene became popular due to their enhanced properties, such as strength, flexibility, and resistance to chemicals. This expansion of available materials greatly expanded the possibilities for custom injection molded plastic applications.
With the rise of computer-aided design (CAD) and computer-aided manufacturing (CAM) technologies in the 1980s, injection molding entered a new era of precision and complexity. These advancements allowed for the creation of more intricate molds and designs, making it possible to produce highly detailed and complex parts. The integration of robotics and automation further improved efficiency and accuracy in the injection molding process.
In recent years, sustainability and environmental concerns have driven the development of eco-friendly plastic materials for injection molding. Biodegradable and recycled plastics have gained popularity, reducing the environmental impact of custom injection molded plastic products.
Additionally, advancements in 3D printing technology have had an impact on injection molding. The ability to prototype complex designs quickly and cost-effectively using 3D printing has been utilized to refine molds and test new designs before committing to full-scale production.
In summary, the history of custom injection molded plastic showcases a progression from simple and limited applications to sophisticated, intricate designs. From the introduction of Parkesine in the mid-19th century to the modern-day integration of sustainable materials and 3D printing, custom injection molded plastic has continually evolved to meet the demands of diverse industries.
The Evolution and Market Trends in custom injection molded plastic Industry
The custom injection molded plastic industry has witnessed significant evolution and market trends over the years. Injection molding is a manufacturing process used to produce plastic parts by injecting molten material into a mold, which then cools and solidifies to form the desired shape. This process offers numerous advantages, including high production rates, complex part designs, and cost-effectiveness.
One key evolution in the custom injection molded plastic industry is the advancement in technology. With the introduction of computer-aided design (CAD) software and computer numerical control (CNC) machining, manufacturers can now create intricate and complex designs with high precision. This has opened up new possibilities for product development and design flexibility.
Market trends in the industry have also been influenced by various factors. Increasing demand for lightweight and durable plastic components in industries such as automotive, aerospace, and electronics has driven the growth of the custom injection molded plastic market. Manufacturers are now focusing on producing components that meet stringent quality and performance standards while reducing weight and cost.
Furthermore, sustainability and environmental concerns have become significant market trends. As consumers and regulatory bodies demand more environmentally friendly solutions, manufacturers are adopting sustainable practices in their injection molding processes. This includes the use of bio-based and recycled materials, as well as implementing energy-efficient manufacturing techniques.
Another trend in the custom injection molded plastic industry is the integration of automation and robotics. Automation has improved efficiency, reduced labor costs, and increased production rates. Robots are now utilized for various tasks, including part handling, assembly, and quality control, leading to improved overall productivity and consistency.
Additionally, the industry has experienced a shift towards global outsourcing. Many companies are now opting to outsource their injection molding needs to countries with lower labor costs, such as China and India. This allows for cost savings and quicker turnaround times.
In conclusion, the custom injection molded plastic industry has evolved significantly, driven by advancements in technology, increasing demand for lightweight and eco-friendly solutions, automation, and global outsourcing. These trends have shaped the market and will continue to influence the industry in the future.
Custom Private Labeling and Branding Opportunities with Chinese custom injection molded plastic Manufacturers
Chinese custom injection molded plastic manufacturers offer a wide range of opportunities for custom private labeling and branding. With their expertise in plastic molding, these manufacturers can help businesses create unique, branded plastic products that are tailored to their specific needs.
One of the main advantages of working with Chinese manufacturers is the ability to customize every aspect of the product. From the design and dimensions to the color, texture, and finish, businesses have complete control over the final look and feel of their plastic products. This allows them to create a distinct brand identity and stand out in a crowded market.
Moreover, Chinese manufacturers offer cost-effective solutions for private labeling and branding. By leveraging their advanced injection molding technology and economies of scale, businesses can minimize production costs without compromising on quality. This makes it easier for them to introduce new products or expand their product lines while maintaining competitive pricing.
In addition to customization and cost-effectiveness, Chinese manufacturers also provide efficient production and timely delivery. They have well-established supply chains and logistics networks, ensuring that products are manufactured and delivered within the specified timeframe. This is crucial for businesses that want to meet market demands and keep up with consumer expectations.
To take advantage of these opportunities, businesses should partner with reputable Chinese custom injection molded plastic manufacturers. Conducting thorough research and due diligence is essential to ensure that the manufacturer has a track record of delivering high-quality products and excellent customer service.
In summary, Chinese custom injection molded plastic manufacturers offer businesses the opportunity to create unique, branded plastic products through private labeling and branding. With their customization capabilities, cost-effective solutions, and efficient production processes, these manufacturers are a valuable partner for businesses looking to enhance their brand identity and grow their product range.
Tips for Procurement and Considerations when Purchasing custom injection molded plastic
When it comes to purchasing custom injection molded plastic, there are several tips and considerations that can help ensure a successful procurement process.
Firstly, it is crucial to understand the specific requirements of the project. This includes factors such as the desired shape, size, and material for the injection molded plastic parts. Clear and detailed specifications will help in finding a supplier that is capable of meeting these requirements.
Finding a reliable and reputable supplier is another essential tip. Look for suppliers that have experience and expertise in injection molding and have a track record of delivering high-quality products. Check for certifications and customer reviews to ensure credibility.
Comparing quotes from multiple suppliers is also important. This allows for price and quality comparisons. While cost is a crucial aspect, it should not be the sole determining factor. Consider the supplier’s capabilities, manufacturing processes, and quality control measures.
Consideration should also be given to the lead time and availability of the supplier. Evaluate whether they have the capacity to meet the required production quantities within the desired time frame. Communication is vital during the procurement process, so choose a supplier that is responsive and keeps you updated on the progress.
Quality control is of utmost importance when purchasing custom injection molded plastic. Ensure the supplier has robust quality control processes in place to ensure consistent and defect-free products. This may include inspecting samples or requesting documentation of quality standards.
Closely review the supplier’s terms and conditions, including payment terms, warranties, and return policies. It is also recommended to have a written agreement in place to protect both parties’ interests.
Lastly, consider the environmental impact of the injection molding process and the materials used. Look for suppliers that prioritize sustainability and offer eco-friendly options.
By following these tips and considerations, you can streamline the procurement process and ensure that you find a reliable supplier capable of delivering high-quality custom injection molded plastic parts.
FAQs on Sourcing and Manufacturing custom injection molded plastic in China
1. Why should I consider sourcing and manufacturing custom injection molded plastic in China?
Sourcing and manufacturing custom injection molded plastic in China can offer several advantages. China has a large manufacturing industry with a vast pool of experienced workers and advanced equipment, resulting in competitive pricing and high production capacity. Additionally, many Chinese manufacturers have specialized in injection molding, making them experts in the field. China’s extensive supply chain also ensures easy access to materials and components, reducing lead times and facilitating efficient production.
2. What is the process of sourcing custom injection molded plastic in China?
The sourcing process typically involves identifying potential manufacturers and gathering quotes. This can be done through online platforms, trade shows, or engaging with sourcing agents. It’s essential to assess the manufacturer’s capabilities, quality control measures, and ensure they have experience in the specific type of plastic molding required. Once a suitable manufacturer is identified, samples are requested for validation. If the samples meet the quality expectations, a manufacturing agreement is negotiated and production commences.
3. How can I ensure manufacturing quality and avoid potential issues?
To ensure manufacturing quality, it is crucial to work with reputable manufacturers who have established quality control processes. This can be verified through certifications such as ISO 9001. Regular inspections can be conducted during production or before shipment to maintain quality standards. Communication with the manufacturer is essential, providing clear and detailed specifications, including material requirements, dimensions, and tolerances. It is also recommended to conduct independent quality control inspections or hire third-party inspection services to ensure adherence to specifications.
4. What are the typical MOQs (Minimum Order Quantities) for custom injection molded plastic in China?
Minimum Order Quantities can vary depending on the manufacturer and complexity of the project. However, many Chinese manufacturers are willing to accept smaller MOQs, ranging from hundreds to a few thousand units. It is crucial to discuss MOQ requirements and negotiate with the manufacturer to reach a mutually beneficial agreement.
5. How long does the production process typically take in China?
Production lead times can vary depending on factors such as product complexity, quantity, and availability of materials. However, Chinese manufacturers are often capable of completing production within 4-8 weeks. Communication and coordination with the manufacturer, as well as efficient logistics planning, can help expedite the process.
6. Are there any intellectual property concerns when sourcing custom injection molded plastic in China?
Intellectual property protection is a recurring concern when sourcing from any country, including China. It is recommended to work with manufacturers who respect intellectual property rights and sign appropriate non-disclosure agreements, manufacturing agreements, or contracts that safeguard your ideas and designs. Conducting due diligence and utilizing legal advice can further help protect your intellectual property interests.
7. Can I visit the manufacturer and conduct on-site inspections in China?
Yes, it is possible to visit manufacturers in China and conduct on-site inspections. It is advisable to schedule visits in advance and communicate the purpose of the visit. On-site inspections offer an opportunity to assess the manufacturing facility, equipment, and quality control measures. Additionally, direct interaction with the manufacturer can enhance communication and strengthen the business relationship.
Please note that these answers provide a general overview and must be adapted to individual circumstances and requirements when sourcing and manufacturing custom injection molded plastic in China.
Why contact sourcifychina.com get free quota from reliable custom injection molded plastic suppliers?
SourceifyChina.com provides a platform for businesses to connect with reliable custom injection molded plastic suppliers in China. The company offers a free quota to encourage businesses to explore the potential of sourcing their plastic injection molding needs from China.
One of the main reasons to contact SourceifyChina.com for a free quota is to tap into the vast network of reliable suppliers the platform has established. China is known for its extensive manufacturing capabilities, including injection molding, and there are numerous suppliers offering competitive pricing and high-quality products. By utilizing SourceifyChina.com, businesses can access these suppliers without the need for extensive research and vetting, saving them time and effort.
The free quota allows businesses to request quotes for their specific plastic injection molding requirements without any financial commitment. This helps them understand the cost implications of sourcing from China and evaluate the potential savings they can achieve. By comparing the quotes received from different suppliers, businesses can make informed decisions regarding their sourcing strategy and choose the most cost-effective option.
SourceifyChina.com ensures that the suppliers on its platform are reliable and trustworthy. The company conducts a comprehensive screening process to verify the suppliers’ credentials, manufacturing facilities, quality control measures, and production capabilities. This minimizes the risk for businesses and increases the likelihood of finding a supplier that meets their requirements.
Additionally, SourceifyChina.com provides support throughout the sourcing process, including communication, negotiation, and quality control. They act as a bridge between businesses and suppliers, ensuring smooth communication and streamlining the procurement process.
In conclusion, businesses should contact SourceifyChina.com to get a free quota from reliable custom injection molded plastic suppliers in China because it offers access to a wide network of suppliers, helps to evaluate cost savings, ensures supplier reliability, and provides comprehensive support throughout the sourcing process. It allows businesses to make informed decisions and find the right supplier to meet their plastic injection molding needs.