Introduce about custom plastic mold guide,Qulity,Cost,Supplier,Certification,Market,Tips,FAQ
Custom plastic mold guide is a comprehensive manual that provides essential information about designing, manufacturing, and sourcing plastic molds tailored to specific requirements. It aims to assist manufacturers, engineers, and businesses in understanding the process and making informed decisions to achieve high-quality molds at an optimal cost.
Quality is crucial in plastic mold production as it directly impacts the final product’s performance and durability. Manufacturers should prioritize quality control measures throughout the manufacturing process to ensure precision, accuracy, and consistency.
Cost is another critical factor to consider when procuring custom plastic molds. The cost involves various components such as mold design, raw materials, production, and tooling. It is imperative to work closely with suppliers to identify cost-effective solutions without compromising on quality.
Choosing the right plastic mold supplier is essential for successful mold production. Suppliers should have extensive experience, a proven track record, and state-of-the-art facilities. Evaluating supplier capabilities, quality management systems, and client reviews can assist in selection.
Certification is an important aspect when working with custom plastic mold suppliers. It ensures that the supplier adheres to international quality standards and regulations. Certifications such as ISO 9001 validate the supplier’s commitment to delivering top-notch quality molds.
The market for custom plastic molds is vast and diverse, catering to numerous industries such as automotive, consumer goods, electronics, and medical devices. It is crucial to understand market trends, technology advancements, and emerging materials to stay competitive and meet industry demands effectively.
Tips for successful custom plastic mold production include thorough design validation, regular communication with suppliers, leveraging the expertise of mold engineers, and an in-depth understanding of the molding process and materials used.
Frequently Asked Questions (FAQ) typically revolve around topics like mold material selection, surface finishes, lead times, production volume capabilities, and cost considerations. Having access to a well-structured FAQ section in the custom plastic mold guide can help address common queries promptly.
In conclusion, the custom plastic mold guide is a valuable resource that offers comprehensive information on quality, cost, suppliers, certifications, market trends, useful tips, and frequently asked questions related to custom plastic mold production. This guide aids manufacturers and businesses in making informed decisions throughout the mold manufacturing process while ensuring high-quality molds at an optimal cost.
Types of custom plastic mold
There are several types of custom plastic molds that are used in various industries for different purposes. These molds are designed to create specific shapes and forms of plastic products. Here are some common types of custom plastic molds:
1. Injection Molds: Injection molds are the most commonly used molds in the plastic manufacturing industry. They are used to produce a wide range of plastic products, such as automotive parts, consumer products, packaging materials, and more. This type of mold consists of two main parts – a mold cavity and a mold core. The plastic material is injected into the mold cavity, where it takes the shape of the desired product.
2. Blow Molds: Blow molds are used to create hollow plastic products, such as bottles, containers, and tubes. This type of mold is designed with a cavity and a core, similar to injection molds. However, blow molds use the blowing technique to shape the plastic material, rather than injecting it. The plastic material is heated and inflated, causing it to expand and take the shape of the mold cavity.
3. Compression Molds: Compression molds are used to manufacture large, solid plastic parts with complex shapes. This type of mold consists of two halves – the upper half and the lower half. The plastic material is placed in between these halves and is heated under pressure until it takes the desired shape. Compression molds are commonly used for products like electrical components, appliance parts, and machine housings.
4. Rotational Molds: Rotational molds, also known as rotomolds, are used to produce large, durable plastic products. This type of mold is rotated in an oven while the plastic material inside melts and coats the inner surface of the mold. As the mold continues to rotate, the material cools and solidifies, forming the desired product. Rotational molds are used for manufacturing products such as playground equipment, storage tanks, and road safety barriers.
5. Thermoforming Molds: Thermoforming molds are used in the thermoforming process, which involves heating a sheet of plastic until it becomes pliable and then forming it over a mold to create a specific shape. This type of mold is typically made of aluminum or wood and is used to manufacture products like cups, trays, and packaging materials.
In conclusion, these are some common types of custom plastic molds used in various industries. Each type of mold has its own advantages and is designed to create specific shapes and forms of plastic products. The choice of mold depends on the product requirements, production volume, and cost considerations.
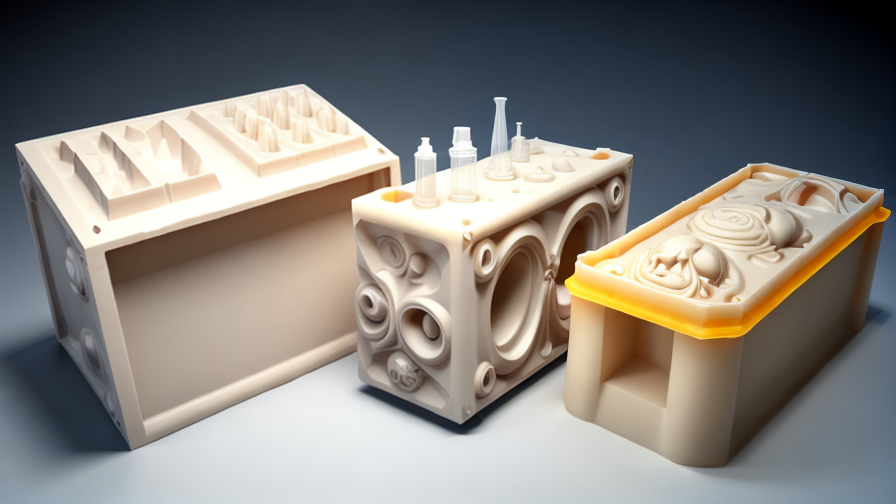
Pros and Cons of Using custom plastic mold
Custom plastic molding is a manufacturing process that involves creating plastic parts and products by using a custom-designed mold. This method offers a variety of advantages and disadvantages, which are important to consider for businesses that are looking to use this manufacturing technique.
Pros of Using Custom Plastic Molding:
1. Cost-effective: Custom plastic molding enables high-volume production, which can significantly reduce the cost per part. This is particularly beneficial for businesses that require large quantities of plastic parts.
2. Flexibility in design: One of the major advantages of custom plastic molding is the ability to create complex shapes and intricate designs. The molds can be customized to meet specific requirements, allowing for greater design flexibility.
3. Shorter production cycles: Compared to other manufacturing methods, custom plastic molding has relatively short production cycles. Once the mold is created, the production process becomes more efficient, reducing lead times and ensuring faster product delivery.
4. High precision and accuracy: Custom plastic molding allows for tight tolerances and consistent shapes, ensuring high levels of precision and accuracy. This is especially crucial for industries that require complex and precise parts, such as medical, automotive, and aerospace.
5. Material versatility: The process of custom plastic molding supports a wide range of plastic resin materials, including high-performance plastics. Businesses can choose the most suitable material for their application, considering factors like strength, flexibility, temperature resistance, and chemical resistance.
Cons of Using Custom Plastic Molding:
1. High upfront investment: The creation of custom molds requires an initial investment, which can be relatively high. This may pose a challenge for small businesses or companies with limited budgets.
2. Limited design changes: Once the mold is produced, making design changes can be costly and time-consuming. Therefore, it is essential to finalize the design before creating the mold to avoid additional expenses and delays.
3. Longer setup time: Custom plastic molding may require significant setup time, especially when creating a new mold. This can delay the production process, particularly for companies with tight deadlines.
4. Environmental considerations: Plastic production and disposal can have negative environmental impacts. It is crucial for businesses to implement sustainable practices and consider alternative materials or recycling options to mitigate these concerns.
In conclusion, the usage of custom plastic molding offers numerous advantages, including cost-effectiveness, design flexibility, shorter production cycles, high precision, and material versatility. However, businesses should also consider the cons, such as high upfront investment, limited design changes, longer setup time, and environmental considerations, when evaluating whether this manufacturing method is suitable for their specific needs.
custom plastic mold Reference Specifications (varies for different product)
Custom plastic mold reference specifications vary depending on the specific product requirements. These specifications outline the necessary details and parameters for designing and manufacturing a custom plastic mold to meet the client’s needs. Below is a brief overview of some commonly considered reference specifications:
1. Dimensions: The dimensions of the custom plastic mold are specified to ensure that the final product will have the desired shape and size. This includes both the exterior dimensions of the mold itself and the internal dimensions for the part to be produced.
2. Material: The choice of material for the custom plastic mold is crucial as it determines the durability, heat resistance, and other properties required for the molding process. The material selection is based on factors such as the type of plastic being used, the expected production volume, and cost considerations.
3. Parting line and gates: The parting line is the separation line between the two halves of the mold. It is critical to determine the appropriate location of the parting line to prevent any undesirable marking on the final product. The gates, or entry points for plastic material, are also specified to ensure proper flow and distribution during the injection molding process.
4. Cooling system: Efficient cooling is essential for ensuring the durability and quality of the plastic mold. Reference specifications include the design and placement of cooling channels or systems within the mold to control the cooling process effectively. This helps in achieving faster cycle times and minimizing defects in the final product.
5. Ejection system: The ejection system is responsible for removing the molded parts from the mold once the injection molding cycle is complete. The reference specifications define the type and location of ejector pins or other mechanisms necessary for safe and efficient part ejection.
6. Surface finish and texture: The desired surface finish and texture of the final product should be considered during the mold design phase. Specifications may include requirements for gloss, texture, grain patterns, or other surface details of the custom plastic part.
7. Tolerances: Tolerances define the range of acceptable deviation from the desired dimensions for the final product. Reference specifications include the tolerance limits for critical dimensions to ensure that the custom plastic mold produces parts within the required specifications.
By adhering to these custom plastic mold reference specifications, manufacturers can successfully design and produce molds that meet the clients’ unique product requirements. These specifications play a crucial role in achieving both efficiency and quality in the injection molding process.
Applications of custom plastic mold
Custom plastic molds have a wide range of applications across various industries due to their versatility, cost-effectiveness, and ease of production. Here are a few noteworthy applications of custom plastic molds:
1. Automotive Industry: Custom plastic molds are extensively used in the automotive industry for manufacturing various parts and components. These molds can be designed to produce precise and complex shapes, allowing for the production of customized car interiors, dashboard panels, engine components, and exterior parts such as bumpers and grills.
2. Medical Equipment: Custom plastic molds play a crucial role in the production of medical equipment, devices, and components. From surgical instruments and implantable devices to medical packaging and drug delivery systems, plastic molds enable the manufacturing of sterile, reliable, and cost-effective medical products.
3. Consumer Electronics: In the consumer electronics industry, custom plastic molds are used to manufacture casing and enclosures for various devices, including smartphones, laptops, cameras, and home appliances. These molds allow for the creation of sleek and durable products, while also accommodating functional features such as buttons, connectors, and displays.
4. Packaging Materials: Custom plastic molds are extensively utilized in the production of packaging materials such as bottles, containers, and caps. The ability to create molds in different shapes, sizes, and designs enables efficient packaging solutions for industries ranging from beverages and cosmetics to pharmaceuticals and food products.
5. Aerospace Industry: The aerospace industry relies on custom plastic molds for manufacturing lightweight and precise components used in aircraft interiors, cockpit panels, seating, and cabin parts. These molds enable the production of strong and durable plastic parts that meet strict safety and performance standards.
6. Toys and Games: Custom plastic molds are widely used in the production of toys and games, allowing for the creation of intricate and appealing designs. From action figures and dolls to building blocks and puzzles, these molds enable the mass production of toys with consistent quality and details.
7. Industrial Components: Custom plastic molds find applications in the production of various industrial components, including machine parts, fittings, gears, and housings. The use of plastic molds provides cost-effective solutions compared to traditional metal machining processes, while also offering design flexibility and corrosion resistance.
In conclusion, custom plastic molds have numerous applications across industries such as automotive, medical, electronics, packaging, aerospace, toy manufacturing, and industrial component production. The versatility and cost-effectiveness of these molds make them vital for producing a wide range of plastic products efficiently and with high quality.
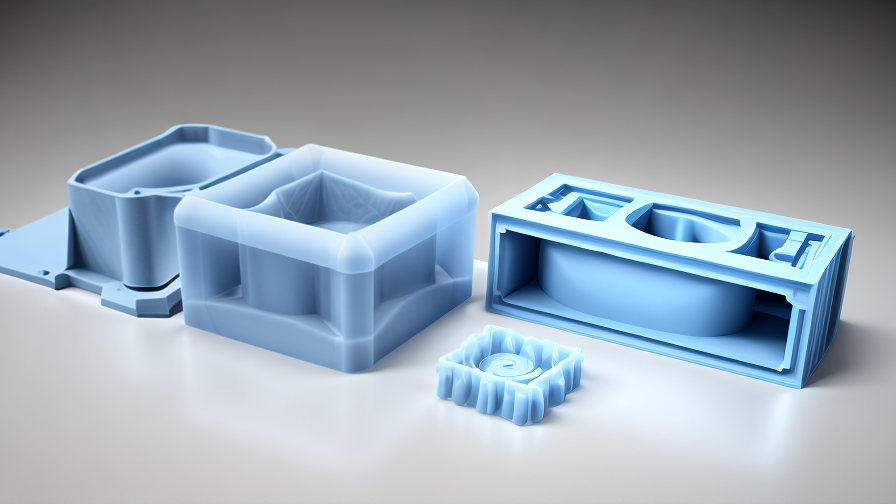
The Work Process and how to use custom plastic mold
The work process for creating custom plastic molds involves several steps to ensure a successful outcome. Here is a brief overview of the process:
1. Design: The first step is to create a design for the plastic mold. This is typically done using computer-aided design (CAD) software. The design will include the specific shape and dimensions of the mold, as well as any intricate details or special features required.
2. Material Selection: Once the design is finalized, the next step is to select the appropriate material for the mold. Factors such as cost, durability, and compatibility with the intended application need to be considered. Common materials used for custom plastic molds include polyethylene, polypropylene, and polycarbonate.
3. Mold Making: After the material is chosen, the mold making process begins. This involves using specialized equipment, such as CNC machines or 3D printers, to create the mold. The design is translated into a physical mold by cutting, shaping, or additive manufacturing methods.
4. Mold Testing and Refinement: Once the mold is created, it is important to test its performance. This is done by injecting molten plastic into the mold and evaluating the quality of the resulting plastic parts. Any issues or defects are identified and addressed to refine the mold design if necessary.
5. Production: Once the mold is tested and refined, it can be used for mass production. The mold is mounted onto a plastic injection molding machine, where the molten plastic is injected into the mold cavity. The mold is then cooled, and the finished plastic part is ejected. This process allows for the production of a large quantity of identical plastic parts.
Using a custom plastic mold involves careful planning and coordination. The mold should be properly maintained and cleaned to ensure its longevity and performance. It is also important to consider factors such as the type of plastic material being used, the desired production volume, and any specific requirements for the finished plastic parts.
In summary, the work process for using a custom plastic mold involves design, material selection, mold making, testing and refinement, and finally, mass production. By following these steps and paying attention to the details, quality plastic parts can be efficiently and consistently manufactured.
Quality Testing Methods for custom plastic mold and how to control the quality
Quality testing methods for custom plastic molds are essential to ensure that the final product meets the specified requirements. Here are some commonly used testing methods for custom plastic molds and how to control quality during the manufacturing process.
1. Visual Inspection: The first step is to visually inspect the mold for any visible defects or imperfections. This includes checking for surface imperfections, cracks, or any inconsistencies in the mold.
2. Dimensional Inspection: It is crucial to verify that the mold’s dimensions conform to the specifications and tolerances. This can be done using precision measuring tools such as calipers, micrometers, or optical comparators.
3. Material Testing: The integrity of the plastic materials used in the mold is essential. Material testing can include analyzing the physical properties, such as tensile strength, impact resistance, or heat resistance, to ensure they meet the required standards.
4. Mold Functionality: The mold must be tested for its functionality, including how well it produces the desired plastic parts. This can be done by running trial production runs and analyzing the output for any defects or inconsistencies.
5. Mold Flow Analysis: Before proceeding with production, a mold flow analysis can be conducted using specialized software to simulate the flow of plastic material inside the mold cavity. This helps identify potential issues such as uneven filling or air traps.
To control the quality of custom plastic molds, the following measures should be implemented:
1. Clearly defined specifications: Clearly establish the requirements and specifications for the molds, including dimensions, tolerances, and material properties. This provides a basis for quality control throughout the manufacturing process.
2. Regular inspection and maintenance: Conduct regular inspections of the mold to identify any wear or damage that may affect the quality. Routine maintenance can help prevent issues and ensure optimal mold performance.
3. Process monitoring: Implement a process monitoring system to track various parameters such as temperature, pressure, or cooling time during the mold manufacturing process. This allows for immediate detection of any abnormalities or variations that may affect quality.
4. Training and expertise: Ensure that operators and technicians involved in the mold manufacturing process are adequately trained and possess the necessary expertise to identify and address quality-related issues.
Ultimately, quality control methods for custom plastic molds aim to minimize defects, maintain consistent production, and optimize the performance of the mold. Implementing these methods and maintaining strict quality control measures will help ensure the production of high-quality custom plastic molds.
custom plastic mold Sample Policy and Post-Purchase Considerations for custom plastic mold from China
Sample Policy:
When ordering custom plastic molds from China, it is essential to have a clear understanding of the sample policy to ensure that the final product meets your expectations. It is typical for manufacturers to provide samples before starting mass production. The following points should be considered regarding the sample policy:
1. Sample Cost: Determine who will bear the sample cost. In some cases, manufacturers may offer free samples, but the customer usually needs to cover shipping charges. Alternatively, both the sample and shipping costs can be negotiated.
2. Sample Lead Time: Discuss the expected lead time for receiving the samples. This time frame may vary depending on the complexity of the mold and the manufacturer’s workload.
3. Sample Specifications: Clearly communicate your requirements for materials, dimensions, colors, surface finishes, and any other specific details. This will help ensure that the samples accurately represent the final product.
4. Modifications and Revisions: Understand the manufacturer’s policy regarding modifications and revisions to the initial sample. It is common to have multiple rounds of revisions before finalizing the mold design.
Post-Purchase Considerations:
After receiving the samples, several important considerations should be taken into account before proceeding with the bulk order:
1. Quality Assessment: Carefully evaluate the samples to determine if they meet your quality expectations. Check for consistent mold dimensions, accurate details, and any defects that may affect functionality.
2. Communication with the Manufacturer: Maintain open and clear communication with the manufacturer to discuss any concerns or necessary modifications based on the sample evaluation. Ensure that both parties have a mutual understanding of the desired product.
3. Mass Production Agreement: Once the sample is approved, finalize the terms and conditions for the bulk order, including the mold’s production lead time, payment terms, and logistics arrangements.
4. Quality Control Measures: Request information about the manufacturer’s quality control procedures and certification. This will help ensure that the production process meets international standards and the final product will be of the desired quality.
By carefully considering the sample policy and adhering to post-purchase considerations, you can mitigate potential risks and ensure a smooth and successful collaboration with your China-based custom plastic mold manufacturer.
Sourcing custom plastic mold from China: Opportunities, Risks, and Key Players
Sourcing custom plastic molds from China offers various opportunities for businesses. Firstly, China is recognized as one of the largest manufacturers of plastic molds globally, providing a vast selection of options to choose from. The country has an extensive network of suppliers and manufacturers, ranging from small-scale workshops to large-scale production facilities, allowing for flexibility in meeting different production needs.
Additionally, Chinese plastic mold manufacturers often offer competitive pricing compared to those in other countries. This cost-effectiveness can significantly benefit businesses looking to reduce production costs, especially when ordering large quantities or complex custom molds. Moreover, China’s specialization in plastic mold manufacturing has led to the development of expertise and advanced technologies, ensuring high precision and quality in the production process.
However, there are risks associated with sourcing from China as well. One primary concern is quality control. Some manufacturers might prioritize cost reduction over quality, resulting in the production of molds that may not meet the required standards. It is essential to conduct thorough research and due diligence when selecting a supplier to mitigate this risk. This can involve requesting samples, visiting manufacturing facilities, and requesting references from previous clients.
Another risk is the possibility of intellectual property infringement. China has faced criticism for its lax enforcement of intellectual property rights in the past. Businesses should take necessary precautions to protect their designs and molds by working with trusted suppliers and employing legal measures, such as patents or non-disclosure agreements.
When sourcing custom plastic molds from China, some key players in the industry include LKM Group, Dongguan Yixun Industrial Co., Ltd., Ningbo Beilun Saige Machine Co., Ltd., and Dongguan Haibo Precision Plastic & Hardware Products Co., Ltd. These companies have established a strong reputation and have experience in manufacturing high-quality plastic molds.
Overall, sourcing custom plastic molds from China can present significant opportunities for businesses, including a wide selection of suppliers, competitive pricing, and advanced manufacturing technologies. However, careful consideration of risks, such as quality control and intellectual property protection, is crucial when choosing and working with suppliers.
How to find and select reliable custom plastic mold manufacturers in China,use google search manufacturers and suppliers
When searching for reliable custom plastic mold manufacturers in China, using Google search can be an effective method. To start, use relevant keywords such as “custom plastic mold manufacturers in China” or “plastic injection molding suppliers.” This will provide you with a list of potential manufacturers and suppliers to consider.
To ensure reliability, follow these steps:
1. Evaluate the website: Look for a professional and well-designed website that provides detailed information about the company, their experience, services, and certifications. A reputable manufacturer will showcase their expertise and professionalism through their website.
2. Check company background: Look for information on the company’s history, experience, and reputation. Consider how long they have been in business and if they have a positive track record. Membership in industry associations or certifications can also be indicators of reliability.
3. Read customer reviews and testimonials: Search for customer reviews and testimonials about the manufacturer you are considering. This will give you insights into their quality, responsiveness, and overall customer satisfaction. Beware of fake reviews or extreme biases and consider the overall sentiment.
4. Request samples and certifications: Contact the manufacturer and ask for product samples or case studies related to products similar to yours. This will demonstrate their capabilities and quality. Additionally, inquire about their certifications, such as ISO 9001, which ensures adherence to strict quality control standards.
5. Communication and responsiveness: Contact the manufacturer and assess their communication skills, responsiveness, and willingness to provide information and answer your queries. Reliable manufacturers will be prompt and transparent in their communication.
6. Request a quotation and compare: Obtain quotations from multiple manufacturers and compare their pricing, lead times, and quality. However, remember that the cheapest option does not necessarily mean the best, so consider the overall value offered.
7. Visit the facility if possible: If feasible, plan a visit to the manufacturer’s facility to assess their capabilities, quality control processes, and overall manufacturing environment. This personal assessment will help you make a more informed decision.
Ultimately, finding and selecting reliable custom plastic mold manufacturers in China requires thorough research, careful evaluation, and open communication. Taking these steps will help you find a manufacturer that meets your quality and production requirements.
How to check custom plastic mold manufacturers website reliable,use google chrome SEOquake check if ranking in top 10M
When determining the reliability of a custom plastic mold manufacturer’s website, follow these steps:
1. Use Google Chrome: Open the website in Google Chrome browser as it offers several tools for analyzing websites.
2. Install SEOquake: Add the SEOquake extension to your Google Chrome browser. This is a useful SEO tool that provides various metrics and insights about a website.
3. Check the Website’s Ranking: Use SEOquake’s feature to check the website’s ranking. Type the website’s URL into the search bar and click on the “Search” button. Check if the website is ranked within the top 10 million websites. Websites with higher rankings are generally more established and trustworthy.
4. Analyze Metrics: SEOquake provides various metrics like Alexa rank, Google index, domain age, and more. Analyze these metrics to assess the credibility and reliability of the manufacturer’s website.
5. Check Domain Age: Look for the domain age of the website. Older domains are usually more reliable. You can find the domain age in SEOquake’s metrics or by using a separate domain age checking website.
6. User-Friendly Design: Evaluate the website’s design and user-friendliness. A well-designed and easy-to-navigate website demonstrates professionalism and credibility.
7. Verify Contact Information: Ensure that the website provides clear and reliable contact information, including phone numbers, email addresses, and physical addresses. Lack of contact information can be a red flag indicating an unreliable manufacturer.
8. Look for Certifications: Look for any certifications or affiliations displayed on the website. Certifications from recognized organizations indicate the manufacturer’s commitment to quality and reliability.
9. Customer Testimonials: Check for customer testimonials or reviews on the website. Positive testimonials can give you an idea about the manufacturer’s reputation and reliability.
10. Industry Experience: Check if the manufacturer has relevant industry experience and expertise in plastic mold manufacturing. Look for information about their history, clientele, and past projects.
Remember, while these steps can help you assess a custom plastic mold manufacturer’s website reliability, it’s always recommended to conduct further research, read reviews, and reach out to the manufacturer directly for more information before making any commitments.
Top 10 custom plastic mold manufacturers in China with each 160 words introduce products,then use markdown create table compare
1. Dongguan SINCERE Tech Co., Ltd.: SINCERE Tech specializes in custom plastic mold manufacturing for various industries including automotive, household appliances, electronics, and more. They offer high precision molds, quick turnaround times, and competitive prices. Their products include injection molds, blow molds, insert molds, and over-molding.
2. HTI Plastics: HTI Plastics is a leading custom plastic mold manufacturer in China. They provide innovative and high-quality molds for the medical, packaging, and consumer goods industries. Their product range includes injection molds, prototype molds, and complex molds with advanced features.
3. Creative Rubber & Plastic Products: With over 20 years of experience, Creative Rubber & Plastic Products is a trusted Chinese manufacturer of custom plastic molds. They specialize in producing molds for the automotive, electronics, and industrial sectors. Their products are known for their durability, precision, and cost-effectiveness.
4. Xiamen Qiqiangsheng Moulds Co., Ltd.: Qiqiangsheng Moulds is a leading manufacturer of custom plastic molds in China. They offer a wide range of molds for industries such as automotive, home appliances, and medical devices. Their products are known for their superior quality, advanced design features, and competitive pricing.
5. Shanghai DECK Precision Tool&Die Co., Ltd.: DECK Precision Tool&Die is a reputable Chinese manufacturer specializing in custom plastic molds for the automotive, electronics, and medical device industries. They provide high-quality molds with precise designs and quick turnaround times.
6. Foshan Sanlong Plastic Mold Co., Ltd.: Sanlong Plastic Mold is a reliable Chinese manufacturer offering a diverse range of custom plastic molds. They cater to industries such as automotive, electronics, household appliances, and more. Their molds are known for their excellent quality, precise dimensions, and long lifespan.
7. Shenzhen Hengzhan Mold Co., Ltd.: Hengzhan Mold is a trusted custom plastic mold manufacturer in China. They have expertise in producing molds for the packaging, consumer goods, and automotive industries. Their products are known for their high precision, durability, and reasonable prices.
8. Ningbo Kaili Plastic Machinery Co., Ltd.: Kaili Plastic Machinery is a renowned manufacturer of custom plastic molds in China. They offer a wide range of molds for industries such as automotive, electronics, and household appliances. Their products are characterized by their high accuracy, durability, and competitive pricing.
9. Suzhou FCE Precision Electronics Co., Ltd.: FCE Precision Electronics is a leading Chinese manufacturer of custom plastic molds for the electronics, automotive, and medical device industries. They provide high-quality molds with exceptional precision and advanced design features.
10. Zhejiang Huangyan Jinnuo Mould Co., Ltd.: Jinnuo Mould is a trusted manufacturer of custom plastic molds in China. They specialize in producing molds for the automotive, electronics, and packaging sectors. Their products are known for their superior quality, precision, and competitive pricing.
| Manufacturer | Products Offered |
|———————————|——————————————–|
| Dongguan SINCERE Tech Co., Ltd. | Injection molds, blow molds, insert molds, and over-molding |
| HTI Plastics | Injection molds, prototype molds, and complex molds|
| Creative Rubber & Plastic Products | Custom molds for automotive, electronics, and industrial sectors |
| Xiamen Qiqiangsheng Moulds Co., Ltd. | Custom molds for automotive, home appliances, and medical devices |
| Shanghai DECK Precision Tool&Die Co., Ltd. | Custom molds for automotive, electronics, and medical device industries |
| Foshan Sanlong Plastic Mold Co., Ltd. | Mold manufacturing for automotive, electronics, and household appliances |
| Shenzhen Hengzhan Mold Co., Ltd. | Custom molds for packaging, consumer goods, and automotive industries |
| Ningbo Kaili Plastic Machinery Co., Ltd. | Custom molds for automotive, electronics, and household appliances |
| Suzhou FCE Precision Electronics Co., Ltd. | Custom molds for electronics, automotive, and medical device industries |
| Zhejiang Huangyan Jinnuo Mould Co., Ltd. | Mold manufacturing for automotive, electronics, and packaging sectors |
In summary, these top 10 custom plastic mold manufacturers in China offer a wide range of high-quality molds for various industries. From injection molds to complex molds with advanced features, they excel in precision, durability, and competitive pricing. Whether it is for automotive, electronics, household appliances, or medical devices, these manufacturers have proven expertise in delivering customized molds to meet the specific requirements of their clients.
Background Research for custom plastic mold manufacturers Companies in China, use qcc.com archive.org importyeti.com
When it comes to sourcing custom plastic molds, China has established itself as a major player in the industry. There are several reputable companies in China that specialize in manufacturing plastic molds to cater to the specific needs of businesses worldwide. To conduct background research on such companies, key resources include qcc.com, archive.org, and importyeti.com.
Qcc.com is a comprehensive business database in China that provides information on companies registered in the country. It allows users to search for specific companies and view their details such as contact information, registration status, capital, and business scope. This platform can be utilized to verify the authenticity and credibility of potential custom plastic mold manufacturers in China.
Archive.org, also known as the Wayback Machine, is a digital archive of the World Wide Web. It allows users to access archived web pages, providing a historical perspective on a company’s online presence. By analyzing the past website designs, product offerings, and customer testimonials of custom plastic mold manufacturers, researchers can gain insights into their evolution and track record.
Importyeti.com is a platform that focuses on the import and export industry in China. It provides information on companies’ trade activities, shipment records, and customs data. By utilizing this platform, users can verify the export history and performance of custom plastic mold manufacturers. This can be particularly useful in identifying reliable suppliers with a track record of successfully exporting their products.
By leveraging these three resources, researchers can gather crucial information on custom plastic mold manufacturers in China, including their registration status, historical performance, evolution, and export records. This background research will aid in identifying trustworthy and competent suppliers for businesses seeking custom plastic mold manufacturing services from China.
Leveraging Trade Shows and Expos for custom plastic mold Sourcing in China
Trade shows and expos are excellent platforms for sourcing custom plastic molds in China. These events bring together manufacturers, suppliers, and industry professionals from all around the world, providing a unique opportunity to connect and engage with potential suppliers.
China is known for its expertise in plastic mold manufacturing, and attending trade shows and expos in the country allows buyers to see firsthand the latest advancements, technologies, and capabilities in the industry. These events offer a wide range of benefits for sourcing custom plastic molds, including:
1. Networking: Trade shows and expos provide a unique opportunity to meet and network with suppliers, allowing buyers to establish valuable connections. Engaging in face-to-face discussions can help in building trust and understanding between the buyer and the supplier.
2. Showcase of products: Manufacturers and suppliers often showcase their products and capabilities at trade shows and expos. This provides buyers with an opportunity to evaluate the quality, functionality, and design of the plastic molds. By examining physical samples and prototypes, buyers can make informed decisions about potential suppliers.
3. Industry insights: Attending trade shows and expos allows buyers to stay informed about the latest trends, innovations, and industry developments. This knowledge can be valuable in assessing the expertise and competitiveness of suppliers. Learning about new materials, technologies, and processes can also lead to improved manufacturing and cost-saving opportunities.
4. Supplier diversity: Trade shows and expos attract a wide range of suppliers, both large and small, offering buyers a diverse pool of options. This allows buyers to compare price quotes, production capabilities, and quality standards, ensuring the best fit for their custom plastic mold requirements.
To capitalize on these opportunities, buyers should prepare in advance by conducting research on participating suppliers and identifying their specific needs and requirements. Setting clear objectives, such as identifying potential suppliers for long-term partnerships or obtaining competitive price quotes, can further streamline the sourcing process.
Overall, trade shows and expos serve as bustling marketplaces, bringing together buyers and suppliers in the plastic mold industry. By leveraging these events, buyers can establish valuable connections, evaluate products, gain industry insights, and select the most suitable suppliers in China for their custom plastic mold needs.
The Role of Agents and Sourcing Companies in Facilitating custom plastic mold Purchases from China
Agents and sourcing companies play a crucial role in facilitating custom plastic mold purchases from China. With China being a major hub for manufacturing and having a vast network of suppliers, their expertise and knowledge of the local market are invaluable for international buyers.
Firstly, agents and sourcing companies act as the link between buyers and suppliers. They have established relationships and a deep understanding of the capabilities, strengths, and weaknesses of different mold manufacturers in China. This enables them to identify the most suitable suppliers based on the buyer’s specific requirements, such as cost, quality, lead time, and capacity.
Moreover, agents and sourcing companies provide support throughout the purchasing process. They assist in supplier selection, negotiate pricing and terms, handle all communication and documentation, and ensure that the buyer’s specifications are met. This reduces the buyer’s risk and saves valuable time and resources.
Agents and sourcing companies also provide quality control and assurance services. They conduct regular factory visits, perform inspections, and ensure that the molds meet the buyer’s quality standards. This is especially important when dealing with custom plastic molds, as any defects or deviations from specifications can cause significant problems during production.
Furthermore, agents and sourcing companies assist with logistics and shipping arrangements. They have extensive experience in navigating the complex logistics involved in international trade and can help buyers select the most cost-effective and reliable shipping options.
Lastly, agents and sourcing companies offer valuable insights into the Chinese market. They stay updated on industry trends, technological advancements, and regulatory changes, providing buyers with a competitive advantage and enabling them to make informed decisions.
In summary, agents and sourcing companies play a vital role in facilitating custom plastic mold purchases from China. Their expertise, network, and support throughout the purchasing process help buyers find reliable suppliers, ensure quality control, handle logistics, and stay informed about the market. By leveraging these services, international buyers can navigate the complexities of sourcing molds from China more efficiently and effectively.
Price Cost Research for custom plastic mold manufacturers Companies in China, use temu.com and 1688.com
When it comes to sourcing custom plastic mold manufacturers in China, two popular platforms to consider are temu.com and 1688.com. These platforms offer extensive options and allow you to find the most suitable manufacturers for your needs. Conducting price cost research on these platforms can help you determine the most cost-effective solutions for your project.
Temu.com is an online platform that connects global buyers with Chinese manufacturers. It provides a vast database of trusted suppliers, including custom plastic mold manufacturers. The platform allows buyers to submit inquiries, receive quotations, and compare prices from multiple suppliers. It also provides a transparent system for evaluating suppliers’ reputation, quality, and response time. Through temu.com, you can directly communicate with manufacturers and negotiate cost-effective deals.
1688.com, owned by Alibaba Group, is a leading Chinese wholesale platform. It primarily caters to the domestic market but offers a wide range of products, including custom plastic molds. While the website is predominantly in Chinese, you can use online translation tools to navigate through the platform and communicate with suppliers. 1688.com enables you to compare prices, view product specifications, and contact manufacturers directly. This platform provides an opportunity to find manufacturers that may not be visible on other international platforms.
In your quest for cost-effective options, it’s crucial to consider factors beyond the listed prices. Quality assurance, manufacturing capabilities, lead time, and communication skills should be thoroughly evaluated. Requesting samples and conducting due diligence is essential to ensure that your chosen manufacturer meets your requirements.
With temu.com and 1688.com, you have the convenience of harnessing the extensive network of Chinese custom plastic mold manufacturers to find competitive prices. However, always exercise caution and thoroughly research potential suppliers to secure the best possible deal without compromising quality.
Shipping Cost for custom plastic mold import from China
The shipping cost for importing a custom plastic mold from China depends on several factors such as the size and weight of the mold, the distance it needs to travel, the mode of transportation, and any additional services required.
Usually, molds are quite heavy and bulky, which means they need to be shipped through sea freight. Shipping by sea is generally the most cost-effective method for large and heavy items. The cost is typically calculated based on the volume of the shipment in cubic meters (CBM), which is determined by multiplying the length, width, and height of the mold.
For example, let’s assume the custom plastic mold has dimensions of 1.5 meters length, 1 meter width, and 0.8 meters height. Multiplying these dimensions gives us a total volume of 1.2 CBM.
The average cost of shipping goods by sea from China to the US or Europe is around $200-$300 per CBM. Using this estimate, the shipping cost for the custom plastic mold would be approximately $240-$360.
In addition to the base shipping cost, there might be additional charges such as customs duties, port handling fees, and documentation fees. These fees can vary depending on the specific country and port of destination. It is essential to consult with a customs broker or freight forwarder to determine the exact charges for the importation of the plastic mold.
It’s worth noting that if the mold needs to be transported urgently, air freight can be an option, but it is significantly more expensive compared to sea freight. The cost of air freight is typically calculated based on the weight of the shipment.
To have a precise shipping cost for importing a custom plastic mold from China, it is recommended to get quotes from shipping companies or freight forwarders who specialize in international shipping. They can provide accurate pricing based on the specific requirements and route of your shipment.
Compare China and Other custom plastic mold Markets: Products Quality and Price,Visible and Hidden Costs
China is known as a prominent player in the custom plastic mold market, but it is essential to compare it with other markets in terms of product quality and price, as well as visible and hidden costs.
Product Quality: China’s custom plastic mold market has made significant advancements in product quality over the years. Many Chinese manufacturers have invested in modern machinery and equipment, allowing them to produce high-quality molds that meet international standards. However, other markets, such as Germany and Japan, are renowned for their precision engineering and exceptional product quality. These markets often prioritize stringent quality control measures, resulting in molds that offer superior performance and durability compared to Chinese counterparts.
Price: China has a competitive advantage in terms of price in the custom plastic mold market. Chinese manufacturers benefit from lower labor and production costs, enabling them to offer molds at lower prices compared to other markets. While some manufacturers in Germany and Japan may produce molds of superior quality, they generally come at a higher price due to higher labor costs and strict quality control standards. Thus, for those seeking cost-effectiveness, China may be a more attractive option.
Visible and Hidden Costs: When considering the total cost of acquiring custom plastic molds, it is crucial to examine both visible and hidden costs. In terms of visible costs, China’s lower labor and production costs can result in more affordable prices for molds. However, there could be hidden costs involved, such as import duties, shipping charges, and quality control inspections. These additional costs, if not properly accounted for, can impact the overall affordability of molds sourced from China. On the other hand, markets like Germany and Japan may have higher upfront costs, but they often ensure transparent pricing with minimal hidden costs, providing a more accurate understanding of the total investment required.
In conclusion, China’s custom plastic mold market offers competitive prices and improving product quality, making it a preferred choice for those seeking cost-effectiveness. However, markets like Germany and Japan maintain an edge in terms of superior product quality. It is crucial to consider visible and hidden costs associated with each market. Ultimately, the specific requirements and priorities of the customer will determine the most appropriate market to source custom plastic molds from.
Understanding Pricing and Payment Terms for custom plastic mold: A Comparative Guide to Get the Best Deal
When it comes to getting a custom plastic mold made, understanding the pricing and payment terms is crucial to securing the best deal. This comparative guide will provide insights into the key factors that affect pricing and offer tips to negotiate favorable payment terms.
The pricing of custom plastic molds can vary significantly depending on several factors. Firstly, the complexity and size of the mold will play a major role in determining cost. Intricate designs or larger molds typically require more materials and a longer production time, leading to higher prices. Additionally, the type of plastic material used can also impact cost, with specialized or high-quality materials often commanding a premium.
Another crucial factor in pricing is the quantity of molds ordered. Manufacturers often provide quantity-based discounts, meaning that ordering larger quantities may result in a lower per-unit price. Therefore, it is vital to understand your production requirements and consider volume when negotiating pricing.
Payment terms are equally important when seeking the best deal for custom plastic molds. Generally, manufacturers require an upfront deposit before commencing production to cover material costs and ensure commitment. However, be cautious of excessively high upfront payments, as they may indicate a lack of trustworthiness.
To negotiate favorable payment terms, it is advisable to request milestone-based payments. This means breaking down the total cost into several installments payable at different stages of the production process. For instance, an initial deposit, followed by payments at the completion of design, tooling, and final delivery stages. This approach ensures regular progress is being made and reduces the risk of paying for incomplete or unsatisfactory work.
Furthermore, exploring different manufacturers and comparing their pricing and payment terms is essential. Requesting quotes from several suppliers allows you to compare prices and negotiate more effectively. Ensure that you thoroughly evaluate each manufacturer’s reputation, quality of work, and production capabilities to make an informed decision.
In conclusion, understanding the factors influencing pricing and negotiating favorable payment terms are crucial steps to securing the best deal for a custom plastic mold. Consider the complexity, size, and quantity required when evaluating pricing, and aim for milestone-based payments to ensure progress and minimize risk. By utilizing this comparative guide, you can navigate the pricing and payment landscape confidently and secure a beneficial agreement.
Chinese Regulations and Industry Standards Certifications for custom plastic mold,Import Regulations and Customs for custom plastic mold from China
China is known for being a major player in the plastic mold industry, and the country has established regulations and industry standards certifications to ensure the quality and safety of custom plastic molds. These regulations and certifications are crucial for both manufacturers and importers to understand and comply with when dealing with custom plastic molds from China.
One of the key regulations in China for the plastic mold industry is the GB/T 27699-2011 standard, which specifies the classification, technical requirements, test methods, and marking of plastic molds. This standard covers various aspects such as design, materials, dimensions, processing, and testing, ensuring that the molds meet the necessary standards for quality and performance.
In addition to the GB/T 27699-2011 standard, there are also industry certifications and labels that manufacturers can obtain to demonstrate compliance with certain standards. One of the most well-known certifications is the ISO 9001:2015, which ensures that a manufacturer has implemented a quality management system and meets customer and regulatory requirements consistently.
When importing custom plastic molds from China, importers need to comply with the country’s import regulations and customs procedures. The import of plastic molds may require certain documentation, such as a commercial invoice, packing list, bill of lading, and import license. These documents facilitate customs clearance and provide necessary information about the imported products.
Importers should also be aware of any specific regulations or restrictions in their destination country regarding the importation of custom plastic molds. This may include compliance with safety standards, inspections, and potential tariffs or duties. It is essential to consult with the customs authorities or seek assistance from a customs broker to ensure compliance and smooth importation.
In summary, China has established regulations and industry standards certifications to ensure the quality of custom plastic molds. Compliance with these regulations and certifications is crucial for both manufacturers and importers. Importers also need to be familiar with import regulations and customs procedures to facilitate the smooth importation of custom plastic molds from China.
Sustainability and Environmental Considerations in custom plastic mold Manufacturing
In custom plastic mold manufacturing, sustainability and environmental considerations play a crucial role in minimizing the industry’s impact on the environment. By focusing on green practices and adopting sustainable solutions, manufacturers can reduce waste, conserve resources, and promote a more environmentally friendly approach.
One significant aspect of sustainability in plastic mold manufacturing is the efficient use of materials. Minimizing waste during the manufacturing process by optimizing the design, reducing scrap, and reusing or recycling materials is essential. Using computer-aided design and manufacturing (CAD/CAM) software can facilitate the development of efficient mold designs, reducing the amount of plastic used and minimizing waste. Additionally, incorporating recycling programs for excess plastic and implementing closed-loop systems for reusing plastic can significantly decrease the environmental footprint.
Moreover, energy conservation is another important consideration. Manufacturers can employ energy-efficient machinery and technologies to minimize power consumption during the production process. This can include using energy-efficient motors, sensors, and controls, as well as implementing automation and streamlining production to reduce energy usage. Utilizing renewable sources of energy, such as solar or wind power, can further enhance the sustainability of the manufacturing process.
Reducing emissions and controlling pollution is also critical in custom plastic mold manufacturing. Implementing proper waste management protocols, including the responsible disposal of hazardous materials and the treatment of waste water, ensures compliance with environmental regulations. Moreover, adopting filtration and air purification systems can help mitigate air pollution caused by the production process. Monitoring and controlling emissions, especially volatile organic compounds (VOCs), is important to minimize the environmental impact.
Lastly, manufacturers can foster a culture of sustainability by engaging employees in environmentally friendly practices and raising awareness about the importance of environmental stewardship. Training programs and regular communication can help employees understand and implement sustainable practices in their day-to-day activities.
By prioritizing sustainability and incorporating environmental considerations in custom plastic mold manufacturing, manufacturers can play a significant role in reducing the industry’s environmental impact and promoting a more sustainable future.
List The Evolution history of “custom plastic mold”
The evolution history of custom plastic molds can be traced back to the early 20th century. Initially, molds were primarily made of metal, such as steel or aluminum, which were expensive and time-consuming to create. However, with advancements in technology, the use of plastics became more prevalent in various industries, driving the need for custom plastic molds.
In the 1920s, the first plastic injection molding machines were developed. These machines allowed for the rapid and efficient production of plastic products, leading to the increased demand for custom plastic molds. Shapes and sizes of molds became more diverse, enabling manufacturers to create complex and intricate plastic parts.
In the 1940s, the development of thermoplastics revolutionized the custom plastic molding industry. Thermoplastics are polymers that can be melted and reformed multiple times without losing their properties. This breakthrough enabled molds to be reused, reducing costs and increasing production efficiency.
With the advancements in computer technology in the 1980s, computer-aided design (CAD) systems were introduced, making it easier and quicker to design custom plastic molds. CAD software allowed designers to create digital 3D models of molds, eliminating the need for manual drafting and reducing errors.
In the late 1990s and early 2000s, the use of computer numerical control (CNC) machines for mold making became more widespread. CNC machines could accurately and precisely shape molds based on the CAD designs, further improving the quality and efficiency of custom plastic mold production.
In recent years, additive manufacturing, or 3D printing, has made its way into the custom plastic mold industry. 3D printing enables the production of molds with complex geometries that were previously difficult or impossible to achieve using traditional methods. This technology has significantly reduced lead times and costs for prototyping and small-scale production runs.
Today, custom plastic molds continue to evolve with the advancements in technology. From traditional metal molds to computer-aided design and high-precision CNC machines to the disruptive innovation of 3D printing, the custom plastic mold industry has come a long way in meeting the ever-changing demands of various industries.
The Evolution and Market Trends in custom plastic mold Industry
The custom plastic mold industry has witnessed significant evolution and market trends over the years. With advancements in technology and changing consumer demands, this industry has adapted to stay relevant and competitive.
One notable evolution in the custom plastic mold industry is the shift towards automation and digitization. Manufacturers are now utilizing advanced software systems and robotics to design and produce molds more efficiently. This not only reduces human error but also increases production speed and accuracy.
Moreover, market trends have shown a growing preference for eco-friendly and sustainable solutions. As consumers become more environmentally conscious, there is an increased demand for custom plastic molds that incorporate recycled materials or are biodegradable. Manufacturers in this industry are responding by developing innovative molds that align with these sustainability goals.
Another market trend is the increasing use of additive manufacturing, commonly known as 3D printing, in custom plastic mold production. This technology offers flexibility and design freedom, allowing manufacturers to create complex and intricate molds. This trend has significantly reduced production time and costs, making it a preferred choice for many in the industry.
Additionally, the custom plastic mold industry has experienced a rise in demand for personalized and unique products. Consumers are now looking for customized designs and shapes that cater to their specific needs and preferences. This trend has prompted manufacturers to invest in advanced machinery and equipment to create highly customized molds.
Furthermore, the industry has witnessed a shift in market dynamics, with a growing number of small and medium-sized enterprises (SMEs) entering the market. These companies are offering customized solutions at competitive prices, challenging the dominance of larger players. This trend has created a more fragmented market, leading to an increased focus on innovation and differentiation.
In conclusion, the custom plastic mold industry has transformed in response to evolving consumer demands and technological advancements. The adoption of automation, the focus on sustainability, the incorporation of additive manufacturing, the rise of customization, and the emergence of SMEs are all contributing to the industry’s growth and development. It is crucial for businesses operating in this industry to stay abreast of these trends in order to remain competitive and meet the evolving needs of consumers.
Custom Private Labeling and Branding Opportunities with Chinese custom plastic mold Manufacturers
Chinese custom plastic mold manufacturers offer excellent opportunities for custom private labeling and branding. With their expertise and cost-effective manufacturing capabilities, businesses can create unique products and establish their own brand identity.
One significant advantage of working with Chinese custom plastic mold manufacturers is the ability to create custom designs. These manufacturers have experienced design teams that can translate a business’s ideas and requirements into high-quality plastic molds. This allows businesses to create products tailored to their specific needs, giving them a competitive edge in the market.
Moreover, Chinese manufacturers provide private labeling options, allowing businesses to brand their products with their own logos, names, and designs. Custom private labeling is an effective way to build brand recognition and loyalty among customers. It creates a consistent and professional image, helping businesses stand out from competitors.
Chinese custom plastic mold manufacturers also offer cost-effective solutions. The lower labor and production costs in China allow businesses to manufacture high-quality products at competitive prices. This enables businesses to maximize their profit margins while delivering value to their customers.
Additionally, working with Chinese manufacturers provides businesses with access to a vast range of plastic materials and production techniques. Manufacturers in China have expertise in working with various materials like polyethylene, polypropylene, PVC, ABS, and more. They also possess advanced machinery and technologies, including injection molding, blow molding, and rotational molding.
In conclusion, collaborating with Chinese custom plastic mold manufacturers offers immense opportunities for custom private labeling and branding. Businesses can leverage their expertise, affordable manufacturing costs, and diverse production capabilities to create unique, high-quality products that resonate with their target markets.
Tips for Procurement and Considerations when Purchasing custom plastic mold
When purchasing a custom plastic mold, there are several important considerations and tips to keep in mind to ensure a successful procurement process. Here are some key points to consider:
1. Define your requirements: Clearly articulate your specific needs and requirements for the custom plastic mold. Consider factors such as size, shape, material, functionality, and any specific design features required.
2. Research potential suppliers: Look for reputable suppliers with experience and expertise in manufacturing custom plastic molds. Check their track record, customer reviews, and certifications to ensure quality and reliability.
3. Request multiple quotes: Obtain quotes from multiple suppliers to compare prices, lead times, and capabilities. Don’t solely focus on the lowest price; consider the supplier’s reputation and quality of their previous work.
4. Material selection: Carefully consider the type of plastic material required for your mold. Factors such as durability, flexibility, cost, and compatibility with the intended product should be taken into account.
5. Mold longevity: Discuss with the supplier the expected lifespan of the custom plastic mold. Consider factors such as the number of cycles it can withstand and any maintenance that may be required.
6. Prototype testing: Before finalizing the production of the custom mold, ask the supplier to provide a prototype for testing purposes. This will help identify any design flaws or required modifications, saving time and costs in the long run.
7. Quality control: Ensure the supplier has a robust quality control process in place. Ask for details on how they inspect and test the molds to meet your specifications and standards.
8. Lead time and production capacity: Discuss lead times and ensure the supplier has sufficient production capacity to meet your required quantity within the desired timeframe.
9. Logistics and shipping: Clarify shipping arrangements and responsibilities. Ensure the supplier can handle packaging, labeling, and transport to your desired location, considering any potential customs regulations or certifications required.
10. Communication and collaboration: Establish clear lines of communication with the supplier throughout the procurement process. Regular updates and open dialogue can help address any issues promptly.
By considering these tips and conducting thorough research, you can ensure a successful purchasing process for your custom plastic mold, leading to a high-quality end product.
FAQs on Sourcing and Manufacturing custom plastic mold in China
1. Why should I consider sourcing and manufacturing custom plastic molds in China?
China has long been a global leader in plastic manufacturing due to its cost-effective labor and advanced infrastructure. Choosing to source and manufacture custom plastic molds in China can lead to significant cost savings without compromising on quality. Chinese manufacturers often offer competitive pricing and have the capability to deliver large quantities within short lead times.
2. How do I select a reliable manufacturer in China for my custom plastic mold?
It is crucial to conduct thorough research and due diligence before partnering with a manufacturer in China. Look for companies with a solid reputation, extensive experience, and a track record of delivering high-quality products. Checking customer reviews, certifications, and visiting their facilities can help evaluate their capabilities and reliability. Working with a trusted sourcing agent or hiring a quality control inspector can also provide added assurance.
3. What steps are involved in custom plastic mold manufacturing in China?
The process typically starts with concept development and design, followed by prototyping and testing. Once the design is finalized, the actual mold manufacturing begins. This involves milling, turning, and heat treatment processes. Mold trials are conducted to ensure functionality and quality before mass production. The manufacturer then proceeds with injection molding, trimming, assembly, and packaging. Quality control processes, such as inspections and tests, are undertaken at every stage to maintain product consistency.
4. Are there any language barriers or communication challenges when working with Chinese manufacturers?
While language barriers can exist, many Chinese manufacturers are proficient in English or have translators available. Communicating expectations, specifications, and requirements in a clear and detailed manner is crucial to avoid misunderstandings. Utilizing visual aids like drawings, blueprints, and 3D renderings can facilitate effective communication throughout the manufacturing process.
5. How can I ensure product quality when sourcing plastic molds from China?
To ensure product quality, it is recommended to define strict quality requirements and specifications prior to production. Regular communication with the manufacturer, conducting product inspections at various stages, and reviewing samples are essential. Engaging a third-party quality control company to conduct independent inspections and audits can help verify compliance with quality standards and specifications.
6. How long does it take to manufacture custom plastic molds in China?
The manufacturing timeframe can vary depending on the complexity of the mold, its size, and the quantity required. Generally, the entire process, including design, prototyping, mold manufacturing, and production, can range from a few weeks to a few months. Efficient communication and working with experienced manufacturers can help streamline the timeline.
7. What are the shipping options for receiving plastic molds from China?
Most manufacturers in China offer various shipping options, including air, sea, or even courier services. The choice of shipping method depends on factors like budget, urgency, and quantity of molds. Sea freight is often the most cost-effective option for larger shipments, while air freight is ideal for urgent or smaller orders. Deciding on the most suitable shipping method should be based on individual requirements and cost considerations.
In conclusion, sourcing and manufacturing custom plastic molds in China can be a cost-efficient option without compromising on quality. Careful supplier selection, effective communication, and robust quality control measures can help ensure a successful partnership and timely delivery of high-quality products.
Why contact sourcifychina.com get free quota from reliable custom plastic mold suppliers?
Sourcifychina.com is likely to offer a free quota from reliable custom plastic mold suppliers for several reasons. Firstly, by providing a free quota, Sourcifychina.com aims to attract potential customers and build trust in their services. In a competitive market, offering a free quota can be an effective strategy to showcase their expertise and commitment to delivering high-quality service.
Moreover, Sourcifychina.com understands that customers may be hesitant to invest in custom plastic molds without assessing their cost implications. By offering a free quota, they allow customers to evaluate the feasibility of their projects and make informed decisions without any financial commitment.
Additionally, Sourcifychina.com may have established longstanding partnerships with reliable custom plastic mold suppliers. These suppliers trust Sourcifychina.com’s judgment and expertise in identifying potential customers, thereby offering quotas free of charge. This trust is crucial for both parties as it ensures smooth communication, timely delivery, and overall customer satisfaction.
Furthermore, the free quota allows Sourcifychina.com to gather essential details about the customer’s requirements, project scope, and budget. This information enables them to accurately assess the project’s complexity, determine the most suitable plastic mold suppliers, and provide a comprehensive quotation that meets the client’s needs.
Overall, by offering a free quota from reliable custom plastic mold suppliers, Sourcifychina.com endeavors to attract customers, build trust, and provide an accurate and competitive pricing evaluation for custom plastic mold projects.