Introduce about custom plastic molding guide,Qulity,Cost,Supplier,Certification,Market,Tips,FAQ
Custom plastic molding is a manufacturing process that involves the production of plastic parts or components according to specific customer requirements. This comprehensive guide will provide an overview of various aspects related to custom plastic molding.
Quality is a crucial factor in custom plastic molding. It is essential to ensure that the supplier follows strict quality control measures and uses high-quality materials to meet the desired specifications. The process involves advanced techniques such as injection molding, blow molding, or rotational molding to achieve precise and consistent results.
Cost is another aspect to consider in custom plastic molding. The final cost depends on various factors such as the complexity of the product, the quantity required, material selection, and the manufacturing process itself. A reputable supplier should offer competitive pricing while maintaining exceptional quality standards.
Choosing the right supplier is vital to the success of your custom plastic molding project. Look for a supplier with extensive experience, a strong track record, and the ability to meet your specific requirements. They should also have a well-equipped manufacturing facility and a skilled workforce to deliver high-quality parts within the agreed timeline.
Certification is crucial for custom plastic molding suppliers as it demonstrates their commitment to meeting industry standards and regulations. Look for suppliers that hold certifications such as ISO 9001, ISO 14001, or any specific certifications related to your industry to ensure you are partnering with a trusted and reliable supplier.
The market for custom plastic molding is vast and diverse. It caters to industries such as automotive, aerospace, consumer goods, medical, electronics, and more. The ability to create customized parts makes this process widely sought after in various sectors.
Here are a few tips to consider when opting for custom plastic molding:
1. Clearly communicate your requirements to the supplier to avoid any misunderstandings or delays.
2. Request samples or prototypes to evaluate the product’s quality and suitability before proceeding with full-scale production.
3. Regularly communicate with the supplier throughout the manufacturing process to ensure everything is on track.
Frequently Asked Questions (FAQ):
1. How long does the custom plastic molding process typically take?
The time required depends on factors like product complexity, quantity, and the supplier’s production capacity. It can range from a few days to several weeks.
2. Can I customize the color and surface finish of the plastic parts?
Yes, custom plastic molding allows for various color options and surface finishes like matte, glossy, or textured.
In summary, custom plastic molding offers a versatile and tailored solution for various industries. By considering factors such as quality, cost, supplier selection, certifications, and market needs, you can successfully navigate the custom plastic molding process and achieve your desired outcomes.
Types of custom plastic molding
There are several types of custom plastic molding processes that are widely used in the manufacturing industry. These processes are chosen based on the desired shape, size, complexity, and volume of the plastic parts needed. Some of the common types of custom plastic molding include:
1. Injection Molding: Injection molding is the most widely used and versatile plastic molding process. It involves injecting molten plastic material into a mold cavity under high pressure. This process allows for the production of complex and intricate plastic parts with high precision and repeatability. Injection molding is suitable for high-volume production runs.
2. Blow Molding: Blow molding is primarily used for producing hollow plastic parts. This process involves heating a plastic parison (hollow tube) and then stretching and blowing it into the shape of a mold cavity. Blow molding is commonly used for manufacturing bottles, containers, and automotive components.
3. Rotational Molding: Rotational molding, also known as rotomolding, is a process where plastic material is heated in a mold that rotates on two perpendicular axes. As the mold rotates, the molten plastic coats the entire inner surface, forming a hollow part. Rotational molding is ideal for producing large, hollow, and seamless plastic parts with complex shapes, such as tanks, playground equipment, and automotive components.
4. Compression Molding: Compression molding is a process where plastic material is placed in a heated mold cavity and compressed under high pressure. The heat and pressure cause the plastic to soften and conform to the shape of the mold. Compression molding is typically used for producing components with intricate details, and it is commonly used in the automotive, aerospace, and electrical industries.
5. Thermoforming: Thermoforming is a process where a flat sheet of plastic is heated to a pliable forming temperature and then shaped against a mold using vacuum or pressure. This process is widely used for producing packaging materials, disposable cups, trays, and other thin-walled parts.
6. Insert Molding: Insert molding involves placing a preformed component, such as a metal insert or another plastic part, into the mold cavity before injecting the molten plastic. This process allows for the creation of composite parts that combine different materials or components.
Each of these custom plastic molding processes offers unique advantages and limitations. The selection of the appropriate process depends on the specific requirements and constraints of the desired plastic part. Manufacturers often consult with experts and engineers to determine the most suitable molding process for their needs.
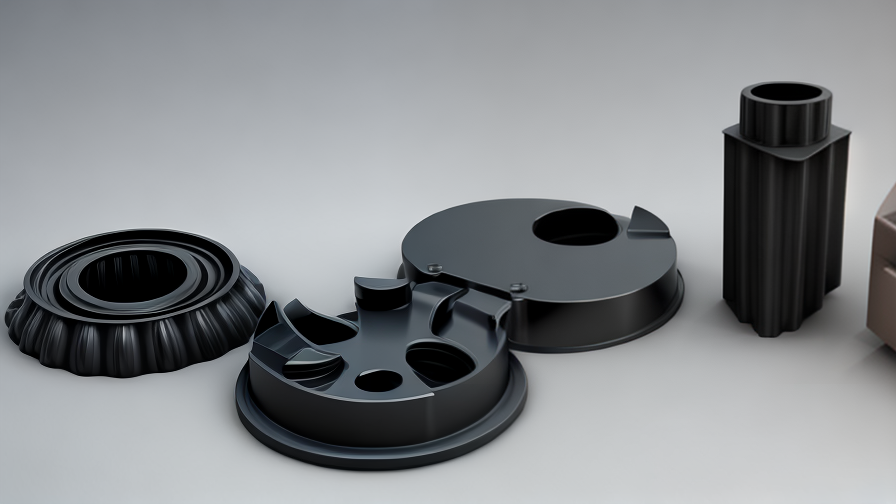
Pros and Cons of Using custom plastic molding
Custom plastic molding, also known as injection molding, is a manufacturing process that involves injecting molten plastic into a mold cavity. It is widely used in various industries for the production of plastic parts and products. Like any manufacturing technique, custom plastic molding has its own set of advantages and disadvantages.
Pros:
1. Cost-effective: Compared to other manufacturing processes, custom plastic molding can be more cost-effective, especially for large production runs. Once the initial mold is created, the cost per unit decreases significantly, making it an ideal option for mass production.
2. Design flexibility: Custom plastic molding allows for intricate and complex designs to be easily replicated. It provides flexibility in terms of shape, size, and features, offering endless possibilities for customization.
3. High-quality output: The use of injection molding ensures consistent and high-quality output. The molds are precision-engineered to produce accurate, detailed, and uniform parts with minimal dimensional variation.
4. Efficient production: The molding process is highly efficient and can produce a large number of parts in a relatively short period. With automated systems and minimal manual intervention, it offers faster production cycles and increased productivity.
Cons:
1. High initial investment: Setting up custom plastic molding requires a significant upfront investment. Designing and manufacturing molds can be costly, especially for complex or large-scale projects. This can pose a challenge for small businesses or startups with limited budgets.
2. Long lead time: The design, development, and testing of molds take time, which could cause delays in production. Custom plastic molding is not suitable for urgent or time-sensitive projects, as it typically requires a longer lead time.
3. Limited material options: While custom plastic molding offers a wide range of plastic materials to choose from, the options may be limited compared to other manufacturing processes. Some specialized or exotic materials may not be suitable for injection molding.
4. Environmental concerns: Plastic waste and pollution are growing global concerns. Custom plastic molding contributes to this issue due to its reliance on plastic materials. Companies must take responsibility for proper disposal, recycling, or reuse of plastic waste to minimize its environmental impact.
In conclusion, custom plastic molding has numerous benefits such as cost-effectiveness, design flexibility, high-quality output, and efficient production. However, it also has disadvantages, including high initial investment, long lead time, limited material options, and environmental concerns. Ultimately, the decision to use custom plastic molding should be based on the specific requirements and priorities of the project.
custom plastic molding Reference Specifications (varies for different product)
Custom plastic molding is a manufacturing process used to produce plastic components tailored to specific customer requirements. The reference specifications for custom plastic molding can vary depending on the product being produced. Below are a few key specifications commonly considered in the custom plastic molding process.
1. Dimensional requirements: The dimensions and tolerances of the plastic component are crucial. Reference specifications outline the exact measurements and limits for length, width, height, and other critical dimensions. These specifications ensure that the final product meets the desired specifications and can function properly.
2. Material selection: Different plastic materials have unique properties, such as strength, flexibility, heat resistance, and chemical resistance. Reference specifications help in identifying the appropriate plastic material for the specific application. Factors such as the environment in which the component will operate, industry regulations, and customer preferences are considered to determine the appropriate material type and grade.
3. Surface finish: The appearance and texture of the plastic component can be specified in terms of surface finish requirements. Reference specifications may specify the desired surface smoothness, gloss level, or any other texture requirement. These specifications help achieve the desired aesthetic appeal and functionality of the final product.
4. Color requirements: Custom plastic molding allows for a wide range of color options. Reference specifications may outline the desired color or color code for the plastic component. Special color effects, such as metallic or pearl finishes, can also be specified to meet specific design needs.
5. Strength and durability: The mechanical properties of the plastic component, including tensile strength, impact resistance, and load-bearing capacity, are vital considerations in custom plastic molding. Reference specifications may provide performance criteria and test methods to ensure that the plastic component meets the required strength and durability standards.
6. Additional features: Reference specifications may also include details on any additional features, such as inserts, threads, surface textures, logos, or special markings required in the plastic component. These specifications ensure that all necessary elements are included in the molding process.
In summary, custom plastic molding requires well-defined reference specifications to achieve the desired product. These specifications encompass dimensional requirements, material selection, surface finish, color requirements, strength and durability criteria, and other specific features. Adhering to these reference specifications ensures that the final product meets customer expectations, regulatory requirements, and industry standards.
Applications of custom plastic molding
Custom plastic molding has a wide range of applications in various industries, thanks to its versatility and cost-effectiveness. Here are some key applications of custom plastic molding:
1. Automotive Industry: Custom plastic molding is extensively used in the automotive industry for manufacturing various components such as dashboards, door panels, bumpers, grilles, and interior trim parts. The ability to mold complex shapes and design flexibility makes it ideal for automotive applications.
2. Consumer Goods: Custom plastic molding is widely used in the consumer goods industry for producing items such as toys, kitchen utensils, bottles, and packaging materials. Plastic molding allows for the customization of products, ensuring high-quality and cost-effective production.
3. Medical and Healthcare: The medical industry relies on custom plastic molding for the production of medical devices and equipment. This includes items such as syringes, surgical instruments, IV components, and diagnostic equipment. Plastic molding offers the advantage of producing sterile products, as well as being lightweight and durable.
4. Electronics and Electrical Appliances: Custom plastic molding is used in the manufacturing of various electronic components, including computer and smartphone cases, connectors, switches, and battery housings. The ability to mold intricate designs allows for efficient production of these components.
5. Industrial Applications: Custom plastic molding finds applications in various industries for producing components that require high strength, corrosion resistance, and precise dimensions. This includes parts for machinery, pumps, valves, and filtration systems.
6. Furniture and Home Decor: Custom plastic molding is utilized in the furniture and home decor industry for producing items such as chairs, tables, cabinets, and decorative pieces. Plastic offers design flexibility and can mimic other materials like wood or metal, while being lightweight and cost-effective.
7. Aerospace and Defense: Custom plastic molding plays a significant role in the aerospace and defense sectors by producing components such as interior panels, aircraft interiors, and military equipment. Plastic molding allows for lightweight and durable parts, contributing to weight reduction and fuel efficiency.
8. Construction Industry: Custom plastic molding is used in the construction industry for producing fittings, connectors, and fixtures. Plastic components offer advantages such as rust resistance, insulation, and ease of installation, making them suitable for both interior and exterior applications.
In conclusion, custom plastic molding finds applications across various industries, including automotive, consumer goods, medical, electronics, industrial, furniture, aerospace, defense, and construction. Its versatility, design flexibility, and cost-effectiveness make it a preferred choice for many manufacturers.
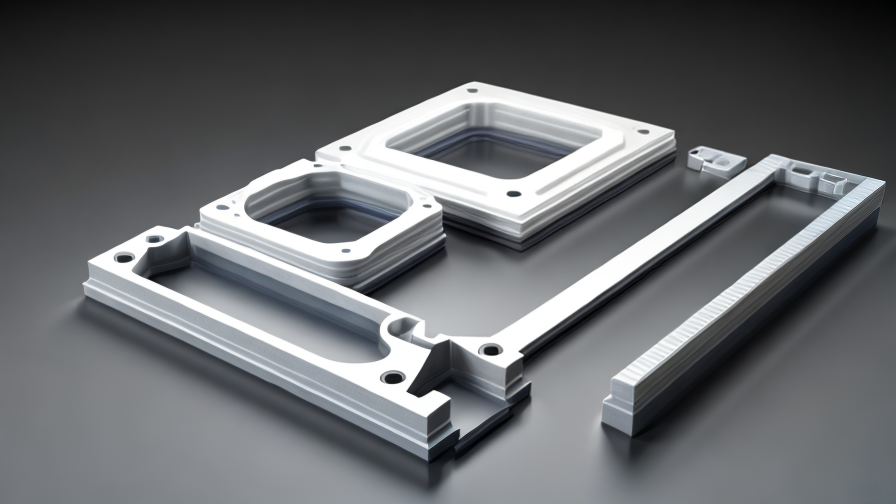
The Work Process and how to use custom plastic molding
Custom plastic molding is a manufacturing process that involves creating plastic parts and products based on unique designs and specifications. It is widely utilized in various industries including automotive, consumer goods, electronics, healthcare, and more. This process offers numerous benefits such as cost-effectiveness, versatility, and high production efficiency.
The work process of custom plastic molding generally involves the following steps:
1. Design and Engineering: The process starts with the creation of a design for the plastic part or product. This can be done using computer-aided design (CAD) software. Design engineers ensure that the design meets the desired specifications in terms of shape, size, functionality, and aesthetics.
2. Mold Fabrication: Once the design is finalized, a mold is fabricated. The mold is typically made of steel or aluminum and consists of two halves, an injection side, and an ejector side. The mold is engineered to precisely shape the molten plastic material as it cools and solidifies.
3. Material Selection: The appropriate plastic resin material is chosen based on the specific requirements of the part or product. Factors such as strength, temperature resistance, flexibility, and color are considered during material selection.
4. Injection Molding: The mold halves are clamped together, and the chosen plastic resin is melted and injected into the mold under high pressure. The molten plastic fills the cavity, taking the shape of the mold.
5. Cooling and Solidification: After the mold is filled, the plastic is allowed to cool and solidify. The cooling process may be accelerated using cooling systems or water channels built into the mold. This ensures that the plastic part or product maintains its desired shape and dimensions.
6. Part Ejection and Finishing: Once the plastic has solidified, the mold is opened, and the part is ejected. Any excess plastic or flash is trimmed off, and additional finishing processes such as polishing, painting, or assembly may be performed to achieve the final desired appearance and functionality.
In conclusion, custom plastic molding is a versatile manufacturing process that enables the production of tailor-made plastic parts and products. By following a systematic work process involving design and engineering, mold fabrication, material selection, injection molding, cooling, part ejection, and finishing, manufacturers can effectively utilize custom plastic molding to meet specific requirements.
Quality Testing Methods for custom plastic molding and how to control the quality
Quality testing methods for custom plastic molding include visual inspection, dimensional inspection, and performance testing. These methods help to ensure that the final product meets the required quality standards.
Visual inspection is a basic and essential quality testing method. It involves visually examining the molded plastic parts for any visual defects such as cracks, surface imperfections, or color variation. Skilled inspectors can detect and reject any defective parts during this inspection process.
Dimensional inspection is another crucial method to ensure the accuracy of the molded parts. It involves measuring the dimensions of the molded plastic parts using precise tools such as calipers, micrometers, or coordinate measuring machines (CMMs). This helps to ensure that the products meet the required specifications and fit properly with other components.
Performance testing is conducted to evaluate the functional attributes of the plastic parts. This may involve subjecting the parts to different environmental conditions such as temperature, humidity, or pressure to measure their durability and performance. Performance testing ensures that the molded plastic parts can withstand the intended applications without any failure or compromise in quality.
To control the quality of custom plastic molding, several measures can be implemented. Firstly, it is crucial to establish clear quality control standards and procedures. This includes defining the acceptable tolerances, visual standards, and performance requirements for the molded parts.
Additionally, implementing a robust inspection plan is essential. This involves conducting regular inspections during the molding process to identify any potential quality issues early on. This can include inspecting raw materials, monitoring the molding process parameters, and inspecting the finished parts.
Furthermore, it is important to train and educate the employees involved in the plastic molding process about quality control techniques and standards. This will help them understand the importance of quality and enable them to identify any potential defects or non-conformances.
Lastly, implementing a feedback loop system is crucial. This involves collecting feedback from customers, conducting internal audits, and addressing any quality issues promptly. This feedback loop helps to continuously improve the quality of the custom plastic molding process and ensures that customer expectations are met.
In conclusion, quality testing methods such as visual inspection, dimensional inspection, and performance testing are essential to control the quality of custom plastic molding. Implementing clear quality control standards, conducting regular inspections, training employees, and maintaining a feedback loop system are crucial in maintaining high-quality standards in custom plastic molding.
custom plastic molding Sample Policy and Post-Purchase Considerations for custom plastic molding from China
Sample Policy:
When ordering custom plastic molding from China, it is important to request a sample before placing a bulk order. Most suppliers are willing to provide samples, either free of charge or for a nominal fee. However, it is recommended to clarify the sample policy with the supplier beforehand.
The sample policy should include details such as the number of samples provided, whether they are fully functional products or just prototypes, and any additional costs involved, such as shipping fees. It is also important to inquire about the lead time for receiving the samples.
By requesting samples, buyers can ensure that the quality of the custom plastic molding meets their requirements and specifications. It allows them to evaluate the product’s design, durability, and functionality before committing to a large order.
Post-Purchase Considerations:
After receiving the samples and finalizing the order, there are several post-purchase considerations to keep in mind:
1. Quality Assurance: Establish clear quality control procedures with the supplier to ensure consistent quality throughout the manufacturing process. Regular inspections and testing of the custom plastic molding can help identify any defects or issues early on.
2. Communication and Updates: Maintain open and regular communication with the supplier, providing any necessary updates or changes in specifications. This helps prevent misunderstandings and ensures that the final product aligns with expectations.
3. Shipping and Logistics: Discuss shipping arrangements with the supplier, including packaging specifications, transportation methods, and delivery schedules. Clarify responsibilities and costs associated with shipping to avoid any unexpected expenses.
4. Payment Terms: Agree on payment terms and methods with the supplier in advance. This includes discussing the payment schedule, currency, and any applicable fees or taxes. It is advisable to use secure payment methods and consider using a reputable international trade platform or escrow service for added protection.
5. Feedback and Continuous Improvement: Provide feedback to the supplier after receiving the custom plastic molding. This helps foster a long-term partnership and allows the supplier to improve their manufacturing processes based on customer requirements.
In conclusion, requesting samples and establishing clear post-purchase considerations are essential when ordering custom plastic molding from China. These practices help ensure product quality, communication, and overall satisfaction with the purchase.
Sourcing custom plastic molding from China: Opportunities, Risks, and Key Players
Sourcing custom plastic molding from China offers numerous opportunities for businesses around the world. China has become a dominant player in the global manufacturing industry due to its low labor costs, vast production capabilities, and advanced technology.
One of the main advantages of sourcing custom plastic molding from China is cost-effectiveness. The lower labor costs in China compared to many other countries allow businesses to achieve significant cost savings. In addition, China’s extensive supply chain capabilities enable efficient production and potential economies of scale.
China’s advanced technology and expertise in plastic molding also present opportunities for businesses. Chinese manufacturers have invested heavily in cutting-edge equipment and technology, allowing them to produce high-quality plastic components and products. Moreover, the large number of experienced engineers and technicians in China’s manufacturing sector keeps it at the forefront of innovation.
However, there are inherent risks associated with sourcing custom plastic molding from China. One primary concern is the potential for intellectual property theft and counterfeiting. Protecting proprietary designs and molds is crucial when collaborating with Chinese manufacturers. Careful selection of trusted partners and the use of legal protections are essential to mitigate this risk.
Another challenge is language and cultural barriers, as effective communication is crucial for successful collaboration. Understanding each party’s expectations, technical specifications, and quality standards is essential to ensure the final products meet the desired requirements.
Key players in the Chinese custom plastic molding industry include well-established companies like Foxconn, Hutchinson Technology Inc., and Amphenol. These companies have a solid track record of delivering high-quality plastic molded products and have established long-lasting relationships with clients worldwide.
In conclusion, sourcing custom plastic molding from China offers attractive opportunities due to cost-effectiveness, advanced technology, and vast production capabilities. However, businesses need to be aware of the risks involved, such as intellectual property theft and communication challenges. By choosing reputable partners and implementing appropriate protective measures, companies can tap into China’s thriving manufacturing industry and benefit from its expertise and resources.
How to find and select reliable custom plastic molding manufacturers in China,use google search manufacturers and suppliers
When looking for reliable custom plastic molding manufacturers in China, using Google search can be an effective method. Here’s a step-by-step guide:
1. Start by typing relevant keywords in the Google search bar, such as “custom plastic molding manufacturers China” or “plastic injection molding suppliers China.”
2. Review the search results carefully, as they will provide a list of potential manufacturers. Pay attention to the organic listings and avoid focusing solely on paid advertisements.
3. Visit the websites of the companies that appear in the search results. Look for information about the company’s history, experience, production capabilities, certifications, quality control, and customer reviews/testimonials.
4. Evaluate the company’s communication channels. Check if they have a working phone number, email address, or live chat support. Reach out to them with any initial questions or inquiries and assess how promptly they respond and the level of professionalism in their communication.
5. Look for independent reviews and ratings about the manufacturer. Online platforms like Alibaba, Global Sources, or Made-in-China often have customer reviews and ratings that can provide insights into the manufacturer’s reputation and reliability.
6. Consider requesting samples or prototypes of the plastic parts you require. This can help you assess the manufacturer’s quality of work, attention to detail, and adherence to your specific requirements.
7. Evaluate the manufacturer’s pricing and payment terms. Request quotes from multiple manufacturers and compare them to ensure fair pricing.
8. Check if the manufacturer has experience exporting products to your location. Inquire about their shipping and delivery options, as well as their ability to handle customs requirements and documentation.
9. It is advisable to narrow down your options to two or three potential manufacturers. Arrange video or phone calls to discuss further details, clarify any doubts, and assess their level of responsiveness and willingness to accommodate your requirements.
10. Finally, make an informed decision based on all the gathered information, considering factors like price, quality, lead time, and overall reliability.
Remember that due diligence is crucial when selecting a reliable custom plastic molding manufacturer. Taking the time to research and evaluate various options will increase the likelihood of finding a trustworthy and suitable supplier in China.
How to check custom plastic molding manufacturers website reliable,use google chrome SEOquake check if ranking in top 10M
When evaluating the reliability of a custom plastic molding manufacturer’s website, utilizing Google Chrome with the SEOquake extension can be a useful tool. Here’s a step-by-step guide:
1. Install SEOquake: Add the SEOquake extension to your Google Chrome browser. This can be done by searching for “SEOquake Chrome extension” in the Chrome Web Store and clicking on the “Add to Chrome” button.
2. Search for the manufacturer: Open a new tab and search for the custom plastic molding manufacturer using relevant keywords like “custom plastic molding manufacturer + [company name].”
3. Analyze the search results: Look for the manufacturer’s website in the search results. Click on the website link to open it.
4. Check SEOquake data: Once the website loads, you should see multiple SEOquake icons and data on the browser toolbar or in the bottom right corner of the screen. If it is not visible, click on the SEOquake icon in your browser toolbar to display the data.
5. Examine the website ranking: In the SEOquake data, locate the “Alexa Rank” or “Global Rank” value. If the website has a ranking within the top 10 million, it indicates that the website is relatively popular and receives a significant amount of traffic.
6. Consider other factors: While website ranking is a useful metric to assess its reliability, it should not be the sole determining factor. Review the website for other indicators of reliability like a professional design, clear contact information, certifications, testimonials, and an established presence in the industry.
By following these steps, you can use Google Chrome with SEOquake to check if a custom plastic molding manufacturer’s website is reliable. Remember to assess multiple factors beyond just the website ranking to make an informed decision.
Top 10 custom plastic molding manufacturers in China with each 160 words introduce products,then use markdown create table compare
1. Xiamen Lisen Mold & Plastic Engineering Co., Ltd. is a leading company in China specializing in custom plastic molding. They offer a wide range of products, including injection molded plastic parts, blow molded products, and custom plastic molds. With advanced equipment and skilled technicians, they ensure high-quality products that meet international standards.
2. Located in Dongguan, China, Kysen Mould is a professional plastic injection molding manufacturer. They provide a range of services, such as product design, mold manufacturing, and plastic injection molding. Their products include automotive parts, household appliances, and industrial components. With strict quality control measures, they guarantee the durability and precision of their plastic molded products.
3. Sositar Mold Co., Limited is a trustworthy name in the plastic molding industry in China. Their product portfolio includes custom plastic molds, injection molded parts, and CNC machining components. With years of experience, they have gained expertise in manufacturing high-quality plastic products for various industries, like automotive, electronics, and medical equipment.
4. Located in Shenzhen, China, Moldflow Plastic Co., Limited specializes in custom plastic injection molding. They offer a wide range of products, including electronic enclosures, automotive parts, and consumer goods. With a strong focus on quality and innovation, they provide efficient solutions to meet their customers’ specific requirements.
5. Dongguan Longeron Mold Technology Co., Ltd. is a leading plastic molding manufacturer based in China. Their products encompass injection molded plastic parts, blow molded items, and custom plastic molds. With their state-of-the-art facilities and experienced team, they deliver exceptional products that adhere to international quality standards.
6. Hengyue Precision Mould Limited is known for its top-quality plastic molds and injection molding solutions. They offer a diverse range of products, including automotive parts, electrical appliances, and medical devices. With advanced machinery and a dedicated team, they ensure precise and efficient manufacturing processes.
7. Located in Ningbo, China, FHZ Mould & Plastic Co., Ltd. specializes in plastic injection molding and mold making. Their products span multiple industries, such as electronics, household appliances, and medical equipment. With their strong emphasis on precision and quality, they have established a solid reputation in the plastic molding market.
8. Sunsky Tooling & Injection Moulding Co., Ltd. is a professional plastic injection molding manufacturer based in China. They pride themselves on providing high-quality plastic products, including automotive components, consumer electronics, and industrial parts. With their advanced equipment and stringent quality control system, they meet the diverse needs of their customers.
9. Zhiyuan Plastic Mould Co., Ltd. offers comprehensive plastic molding solutions for various industries. They specialize in injection molding, blow molding, and custom plastic molds. Their product range includes automotive parts, household goods, and electronic enclosures. With a focus on quality and reliability, they have built a strong reputation as a reliable plastic molding manufacturer.
10. Taizhou Huangyan JMT Mould Co., Ltd. is a leading plastic injection molding manufacturer in China. They provide a wide range of plastic molded products for industries like automotive, packaging, and medical devices. With their cutting-edge technology and experienced team, they ensure top-quality products that meet strict industry standards.
|**Company**|**Product Portfolio**|**Quality Assurance**|
|:-|:-|:-|
|Xiamen Lisen Mold & Plastic Engineering Co., Ltd.|Injection molded plastic parts, blow molded products, custom plastic molds|Adherence to international standards|
|Kysen Mould|Automotive parts, household appliances, industrial components|Strict quality control measures|
|Sositar Mold Co., Limited|Custom plastic molds, injection molded parts, CNC machining components|Expertise in various industries|
|Moldflow Plastic Co., Limited|Electronic enclosures, automotive parts, consumer goods|Focus on quality and innovation|
|Dongguan Longeron Mold Technology Co., Ltd.|Injection molded plastic parts, blow molded items, custom plastic molds|State-of-the-art facilities and experienced team|
|Hengyue Precision Mould Limited|Automotive parts, electrical appliances, medical devices|Advanced machinery for precision molding|
|FHZ Mould & Plastic Co., Ltd.|Plastic injection molding, mold making|Precision and quality assurance|
|Sunsky Tooling & Injection Moulding Co., Ltd.|Automotive components, consumer electronics, industrial parts|Advanced equipment and stringent quality control|
|Zhiyuan Plastic Mould Co., Ltd.|Injection molding, blow molding, custom plastic molds|Quality and reliability focus|
|Taizhou Huangyan JMT Mould Co., Ltd.|Plastic injection molding, automotive parts, packaging, medical devices|Cutting-edge technology and experienced team|
Background Research for custom plastic molding manufacturers Companies in China, use qcc.com archive.org importyeti.com
There are several custom plastic molding manufacturers in China providing a wide range of services. By conducting research on qcc.com, archive.org, and importyeti.com, you can gather valuable information about these companies.
QCC.com is a popular business database in China. It allows you to search for companies based on various criteria such as industry, location, and company size. By using this platform, you can find custom plastic molding manufacturers in China along with their contact information and basic company profiles.
Archive.org is an internet archive that provides access to historical versions of websites. This platform can be useful for retrieving information about the development and evolution of these manufacturers. You may find previous versions of the companies’ websites, which can provide insights into their history, products, and services.
Importyeti.com is a useful website that provides import and export data for various products and industries. By searching for custom plastic molding manufacturers on this platform, you can access data related to their import and export activities. This data can include information about their trade partners, shipment details, and product categories.
By utilizing these platforms, you can gain a comprehensive understanding of different custom plastic molding manufacturers in China. Furthermore, you can collect vital information such as their contact details, company profiles, trade history, and more. This background research will assist you in making informed decisions about potential partnerships or suppliers.
Leveraging Trade Shows and Expos for custom plastic molding Sourcing in China
Trade shows and expos are valuable platforms for businesses in sourcing custom plastic molding in China. These events provide opportunities to connect with suppliers, gain industry insights, and explore the latest trends and technologies in plastic molding.
Attending trade shows and expos in China allows businesses to network and establish relationships with a wide range of plastic molding suppliers. These events bring together numerous manufacturers, enabling businesses to meet face-to-face, discuss their requirements, and assess the capabilities and quality of potential suppliers. This direct interaction helps in building trust and ensuring a good fit between the supplier and the business.
In addition to networking, trade shows also offer the chance to gain valuable industry insights. Exhibitors often showcase their latest products, technologies, and innovations in plastic molding. By attending these demonstrations and presentations, businesses can stay up-to-date with the latest advancements in the field, ensuring they select suppliers that offer cutting-edge solutions.
Trade shows and expos further allow businesses to assess the credibility and reliability of Chinese plastic molding suppliers. Exhibitors are usually required to meet certain standards and certifications, giving businesses the assurance that their potential suppliers are reputable and capable of meeting their specific requirements. Furthermore, trade show organizers often vet the participating suppliers, adding an extra layer of credibility to the businesses they introduce.
Overall, leveraging trade shows and expos for custom plastic molding sourcing in China is an effective and efficient strategy. These events enable businesses to connect with a wide network of suppliers, gain industry insights, and evaluate the credibility and capabilities of potential partners. By attending these events, businesses can optimize their sourcing process and ensure they find the right plastic molding supplier in China.
The Role of Agents and Sourcing Companies in Facilitating custom plastic molding Purchases from China
Agents and sourcing companies play a crucial role in facilitating custom plastic molding purchases from China. They act as intermediaries between buyers and manufacturers, ensuring a smooth and successful transaction. With their knowledge of the Chinese market and expertise in the plastic molding industry, they provide valuable support and assistance throughout the purchasing process.
One of the main responsibilities of agents and sourcing companies is supplier identification and qualification. They have extensive networks and connections with reliable and reputable manufacturers in China. This enables them to identify the most suitable suppliers for custom plastic molding based on the buyer’s requirements, such as the type of plastic material, design specifications, and production volume. By conducting thorough background checks and quality assessments, agents and sourcing companies ensure that buyers collaborate with trustworthy and capable manufacturers.
Furthermore, agents and sourcing companies assist with negotiations and price bargaining. They have in-depth knowledge of the prevailing market rates and industry standards, ensuring that buyers get a fair price for their custom plastic molding orders. They also help in overcoming language and cultural barriers between buyers and manufacturers, facilitating effective communication and ensuring that all specifications and terms are clearly understood.
Agents and sourcing companies also oversee the production process and provide quality control. They act as the buyer’s representative in China, monitoring production schedules, inspecting the quality of the molded products, and ensuring that all requirements are met. This reduces the risks of potential delays, defects, or deviations from the buyer’s specifications.
Lastly, agents and sourcing companies handle logistics and shipping arrangements. They have expertise in international freight and customs regulations, ensuring that the custom plastic molding products are shipped safely and efficiently to the buyer’s location. They coordinate with logistics providers, handle documentation, and track the shipment to ensure timely delivery.
In conclusion, agents and sourcing companies are instrumental in facilitating custom plastic molding purchases from China. From supplier identification and qualification to negotiations, production oversight, and logistics management, they provide comprehensive support and expertise, ensuring a smooth and successful purchasing experience for buyers.
Price Cost Research for custom plastic molding manufacturers Companies in China, use temu.com and 1688.com
When conducting price cost research for custom plastic molding manufacturers in China, two reliable sources to consider are temu.com and 1688.com. These platforms provide a wide range of options and allow you to contact suppliers directly. To make the most of your research, it is recommended to follow these steps:
1. Start by visiting temu.com, which is a B2B online marketplace that connects buyers and suppliers. Utilize their search function to find custom plastic molding manufacturers in China. You can filter the search results based on location, certification, and other preferences.
2. Once you have identified potential suppliers on Temu, begin evaluating their profiles. Look for details such as company size, production capability, certifications (ISO 9001, ISO 14001, etc.), and any customer reviews or ratings available on the platform. This information will help you shortlist the most suitable candidates.
3. After shortlisting, take note of the supplier’s contact details and reach out to them directly via email or phone. Inquire about their price range, minimum order quantity (MOQ), production lead time, and any other specific requirements you may have. It is advisable to contact multiple suppliers to compare their offerings.
4. Additionally, consider visiting 1688.com, a popular wholesale marketplace in China. Although it is primarily in Chinese language, you can utilize online translation tools or seek assistance from a translator to navigate the platform effectively. 1688.com provides an extensive range of suppliers, including plastic molding manufacturers, offering competitive prices.
5. On 1688.com, search using specific keywords related to custom plastic molding and filter the results based on your preferences (e.g., location, certification, etc.). Evaluate the suppliers’ profiles, ratings, and reviews, paying attention to their capabilities and production capacity.
6. Once you have identified potential suppliers, proceed with the same approach as on Temu. Capture the supplier’s contact details and initiate direct communication to request quotations and gather relevant information.
By utilizing temu.com and 1688.com, you can efficiently gather price cost information from diverse custom plastic molding manufacturers in China. Remember to consider factors such as product quality, manufacturing capabilities, certifications, and customer reviews when making an informed decision.
Shipping Cost for custom plastic molding import from China
The shipping cost for custom plastic molding imported from China can vary depending on several factors such as the weight and volume of the goods, the shipping method chosen, and the destination country.
When it comes to shipping methods, there are two popular options: air freight and sea freight. Air freight is generally faster but more expensive, while sea freight is slower but cost-effective for large shipments.
Air freight rates for custom plastic molding from China can range from $2 to $10 per kilogram, depending on the volume and urgency of the shipment. This means that for a 500-kilogram shipment, the shipping cost by air could be anywhere between $1,000 and $5,000.
On the other hand, sea freight rates are usually calculated based on the volume or weight of the shipment, whichever is higher. The cost per cubic meter (CBM) for sea freight can range from $200 to $1,000, again depending on the urgency and the specific route.
For example, for a shipment of custom plastic molding with a volume of 3 CBM, the sea freight cost could range from $600 to $3,000.
In addition to the freight charges, it is important to consider other potential costs such as customs duties, import taxes, insurance, and destination fees. These costs vary from country to country and need to be considered while calculating the overall shipping cost.
To get an accurate estimate of the shipping cost for custom plastic molding, it is recommended to contact freight forwarders or shipping agents who can provide you with specific quotes based on your requirements. They can guide you through the process and help you choose the most cost-effective shipping method.
Compare China and Other custom plastic molding Markets: Products Quality and Price,Visible and Hidden Costs
China is widely recognized as a significant player in the custom plastic molding market due to its vast manufacturing capabilities and competitive pricing. When comparing China to other custom plastic molding markets, several factors come into play, including product quality and price, visible and hidden costs.
In terms of product quality, China has made significant advancements over the years. Many manufacturers in China have adopted advanced technology and equipment to improve the quality of their products. However, it is essential to note that there can be variations in product quality among different Chinese manufacturers. While some companies prioritize quality and adhere to stringent standards, others may focus more on cost optimization, resulting in lower quality products.
Price is one of the key advantages that China offers in the custom plastic molding market. Chinese manufacturers are known for their cost competitiveness, offering lower prices compared to other regions. This is primarily due to China’s well-established infrastructure, abundant raw materials, and a vast labor force. However, it is crucial to consider factors such as transportation costs when comparing prices across different markets.
Visible costs in custom plastic molding include components like manufacturing labor costs, material costs, and overhead expenses, which can vary across different markets. China’s labor costs, although increasing in recent years, are still relatively lower than many other countries. This helps keep visible costs, such as labor, at a competitive level in the Chinese market.
Hidden costs, on the other hand, pertain to factors that are not immediately apparent but can impact the overall cost of the product. These costs can include intellectual property protection, quality control, production lead time, and after-sales service. When doing business in China, it is crucial to carefully consider and manage these hidden costs to mitigate any potential risks.
In conclusion, China has emerged as a dominant player in the custom plastic molding market due to its competitive pricing and improving product quality. However, it is essential to thoroughly evaluate factors such as visible and hidden costs, product quality, and after-sales service when comparing China to other custom plastic molding markets. Such considerations will help businesses make informed decisions based on their specific requirements and priorities.
Understanding Pricing and Payment Terms for custom plastic molding: A Comparative Guide to Get the Best Deal
Pricing and payment terms for custom plastic molding can vary greatly depending on various factors such as the complexity of the mold design, material used, production volume, and additional services required. To secure the best deal, it is crucial to understand and compare the pricing structures and payment terms offered by different molding companies.
Pricing structures in custom plastic molding often involve three main components: tooling costs, unit costs, and any additional charges. Tooling costs cover the expenses in creating the mold, including design, engineering, and manufacturing. This cost can be a significant upfront investment but is usually a one-time expense. Unit costs, on the other hand, refer to the price per unit molded, which varies based on factors like material type, part complexity, and quantity produced. Additional charges may include labor costs, special finishes, secondary operations, and shipping costs.
Payment terms are another essential aspect to consider. Different suppliers may offer varied payment options, such as full upfront payment, partial payments, or payment upon a specific milestone achievement. It’s important to evaluate your financial capabilities and discuss payment terms that best suit your budget and project timeline. Suppliers may also offer discounts for larger production volumes or extended payment terms, so it is essential to negotiate favorable terms that align with your business needs.
When comparing pricing and payment terms, it is vital to gather multiple quotes from different suppliers, ensuring they provide detailed breakdowns of costs. This enables a comprehensive understanding of what is included in the pricing structure and helps identify any hidden charges or potential cost-saving opportunities. Evaluating the reputation and experience of different suppliers is also essential, as it assures a reliable partnership and high-quality end products.
Additionally, it’s important to consider the overall value offered by a supplier beyond just the pricing and payment terms. Factors like production lead times, quality control measures, technical support, and customer service should also be taken into account to ensure a successful and cost-effective molding experience.
In conclusion, understanding pricing and payment terms is crucial to securing the best deal for custom plastic molding. By comparing pricing structures, evaluating payment options, and considering other value-added services offered by different suppliers, businesses can make informed decisions and ensure a successful partnership with a molding company.
Chinese Regulations and Industry Standards Certifications for custom plastic molding,Import Regulations and Customs for custom plastic molding from China
China is known for its thriving custom plastic molding industry, which supplies a wide range of products globally. However, stringent regulations and industry standards certifications are in place to ensure the quality and safety of these products.
In China, custom plastic molding manufacturers must comply with several regulations and obtain industry standard certifications. One such certification is the ISO 9001:2015, which ensures that the manufacturer follows a quality management system and meets customer requirements consistently. It covers various aspects such as design, production, installation, and servicing.
Additionally, custom plastic molding manufacturers must also comply with the China Compulsory Certification (CCC). This certification is mandatory for products involving safety, health, and environmental protection. It covers a wide range of products, including electrical and electronic equipment, automotive parts, and toys, ensuring that they meet the specified standards.
When importing custom plastic molding from China, importers must adhere to the applicable import regulations and customs procedures. Firstly, it is essential to identify any specific regulations imposed by the destination country. This may involve complying with safety standards, labeling requirements, and import permits, among others.
Importers must also consider the customs procedures when importing custom plastic molding. This typically involves providing necessary documents like commercial invoices, packing lists, and bill of lading. It is crucial to declare the correct product classification, value, and origin to prevent any customs issues or delays.
Moreover, importers may also need to pay import duties, taxes, or fees imposed by the destination country. The importation process may also involve customs inspections or necessary certifications to ensure compliance with the destination country’s regulations.
To summarize, the custom plastic molding industry in China is subject to various regulations and industry standards certifications. Manufacturers must comply with certifications like ISO 9001:2015 and CCC to guarantee the quality and safety of their products. Importers, on the other hand, must follow the import regulations and customs procedures of the destination country when importing custom plastic molding from China. Adhering to these regulations and certifications guarantees the smooth importation and compliance of custom plastic molding products.
Sustainability and Environmental Considerations in custom plastic molding Manufacturing
In recent years, sustainability and environmental considerations have become critical factors in the manufacturing industry, including custom plastic molding. Companies are increasingly aware of the need to reduce their environmental impact and adopt sustainable practices throughout the manufacturing process.
One of the primary areas of focus for sustainability in custom plastic molding is the use of eco-friendly materials. Many manufacturers are now opting for biodegradable or recyclable plastics instead of traditional petroleum-based plastics. By using these materials, companies can minimize the amount of plastic waste that ends up in landfills or oceans, reducing their environmental footprint.
Furthermore, energy consumption is another crucial aspect to consider. Custom plastic molding often requires significant amounts of energy, particularly during the heating and cooling stages. To address this, manufacturers are implementing energy-efficient technologies to reduce energy consumption. This may include using energy-efficient machinery, optimizing production processes, and adopting renewable energy sources to power their operations.
Water usage is also an important consideration in plastic molding. Manufacturers are implementing strategies to minimize water consumption by implementing closed-loop systems that recycle and reuse water within the production process. Additionally, companies are focusing on reducing or eliminating the use of hazardous chemicals and pollutants in the manufacturing process to ensure the protection of the environment and worker safety.
Waste management is a critical component of sustainability in custom plastic molding. Manufacturers are developing effective recycling programs to minimize waste and maximize the reuse of materials. They are also exploring innovative techniques such as reclaiming excess plastic and incorporating it back into the production process, thus reducing the overall waste output.
Moreover, companies are improving the transportation and distribution of their products to minimize carbon emissions. Implementing efficient logistics strategies, utilizing alternative fuel vehicles, and optimizing packaging sizes are some of the measures being taken to reduce the environmental impact of transportation.
In conclusion, sustainability and environmental considerations play a vital role in the custom plastic molding industry. Manufacturers are working towards using eco-friendly materials, minimizing energy and water consumption, reducing waste, and implementing sustainable logistics practices. By adopting these measures, custom plastic molding companies can contribute to a greener and more sustainable future.
List The Evolution history of “custom plastic molding”
Custom plastic molding is a manufacturing process that involves shaping plastic materials into specific forms or designs based on the requirements of the product. Its evolution history can be summarized as follows.
1. Early Days: Custom plastic molding originated in the early 19th century with the development of the first plastics. Initially, the process involved manual shaping of plastic materials through methods such as hand molding, blow molding, and compression molding.
2. Injection Molding: The breakthrough in custom plastic molding came in the 1940s with the invention of injection molding. This technique revolutionized the industry by enabling mass production of plastic products in a more efficient and cost-effective manner. Injection molding involves injecting molten plastic into a mold cavity, allowing it to cool and solidify.
3. Advancements in Materials: In the following decades, there were advancements in plastic materials, with the introduction of new types such as polyethylene, polypropylene, and polystyrene. These materials offered improved properties like increased strength, durability, and heat resistance, expanding the possibilities for custom plastic molding.
4. Automation and Technology: The 1980s marked a significant milestone in the evolution of custom plastic molding with the introduction of computer-aided design (CAD) and computer-aided manufacturing (CAM) technologies. These advancements facilitated more precise designs, greater accuracy, and faster production times.
5. Specialized Techniques: As the demand for custom plastic molding grew, specialized techniques emerged to meet specific requirements. These include rotational molding, which allows for the production of large, hollow products, and blow molding, commonly used for creating bottles and containers.
6. Sustainable Practices: In recent years, the focus on sustainability has impacted the custom plastic molding industry. Manufacturers have started using biodegradable and recycled plastic materials, as well as implementing more energy-efficient processes to reduce their environmental impact.
7. Digital Manufacturing: The advent of 3D printing and additive manufacturing has brought another dimension to the custom plastic molding field. It allows for rapid prototyping, on-demand production, and intricate designs, changing the way products are developed and manufactured.
In conclusion, custom plastic molding has gone through a transformative journey from traditional hand molding techniques to highly advanced and automated processes. The focus on improving materials, technology, and sustainability has positioned custom plastic molding as a vital manufacturing method across various industries today.
The Evolution and Market Trends in custom plastic molding Industry
The custom plastic molding industry has undergone significant evolution and experienced various market trends over the years. This industry involves the manufacturing of plastic products, components, and parts according to specific customer requirements.
One major evolution in the custom plastic molding industry is the advancement in technology and techniques. With the introduction of computer-aided design (CAD) software and computer-aided manufacturing (CAM) systems, manufacturers now have the ability to create complex and intricate plastic molds with high precision and efficiency. This has significantly reduced production time and costs while improving the overall quality of the final products.
Another evolution is the increasing demand for environmentally friendly and sustainable plastic materials. As consumers become more conscious of the impact of plastic waste on the environment, there is a growing need for manufacturers to adopt eco-friendly practices. This includes using biodegradable and recyclable plastics, as well as implementing efficient waste management and recycling processes.
In terms of market trends, customization has become a key driving factor. Customers now expect personalized plastic products that cater to their specific needs and preferences. This trend has led to an increased demand for custom plastic molding services, as manufacturers strive to provide unique solutions to meet individual customer requirements.
Additionally, there is a growing emphasis on cost-effectiveness and efficiency. Manufacturers are continuously looking for ways to optimize their production processes, minimize material waste, and reduce overall manufacturing costs. This trend has led to the adoption of lean manufacturing principles, automation, and the use of advanced technologies.
Moreover, globalization has had a significant impact on the custom plastic molding industry. With the rise of international trade and the ability to easily source materials and components from different parts of the world, manufacturers have expanded their reach to global markets. This has resulted in increased competition, but also opportunities for growth and expansion.
In conclusion, the custom plastic molding industry has evolved due to technological advancements, growing demand for sustainable materials, and changing customer expectations. Customization, cost-effectiveness, and globalization are some of the key market trends shaping this industry. As the demand for plastic products continues to grow, manufacturers will need to stay adaptable, innovative, and environmentally conscious to remain competitive in this evolving market.
Custom Private Labeling and Branding Opportunities with Chinese custom plastic molding Manufacturers
Chinese custom plastic molding manufacturers offer a range of private labeling and branding opportunities for businesses looking to customize their plastic products. With their expertise and capabilities, these manufacturers can help businesses create unique products that reflect their brand identity.
Private labeling involves placing the business’s own brand name and logo on the plastic products, giving them a distinct identity. Chinese custom plastic molding manufacturers can imprint or engrave the brand name and logo on the products using various techniques such as screen printing, pad printing, or hot stamping. This allows businesses to build brand recognition and loyalty among their customers.
In addition to private labeling, Chinese manufacturers also offer branding opportunities by providing custom molds and designs. They can work closely with businesses to create customized plastic products that align with their brand image. Whether it’s a unique shape, color, or texture, these manufacturers have the expertise to bring ideas to life.
Moreover, Chinese custom plastic molding manufacturers often offer packaging and labeling services, which further enhance the branding opportunities. They can package the products with customized labels, tags, or stickers that showcase the business’s logo and brand message. This attention to detail helps businesses create a cohesive and professional brand image.
By leveraging the services of Chinese custom plastic molding manufacturers, businesses can tap into a wide range of private labeling and branding opportunities. These manufacturers provide the necessary expertise, technology, and resources to create customized plastic products that reflect the brand identity. With their attention to detail and commitment to quality, Chinese manufacturers offer a cost-effective solution for businesses looking to strengthen their brand presence in the market.
Tips for Procurement and Considerations when Purchasing custom plastic molding
When purchasing custom plastic molding for your procurement needs, it is important to consider several factors to ensure you make an informed decision. Here are some tips and considerations to keep in mind:
1. Identify your requirements: Determine your specific needs, such as the type of plastic material required, the dimensions of the mold, and any additional features or specifications.
2. Quality control measures: Look for a supplier who has stringent quality control procedures in place. This ensures that the plastic molding meets your desired standards and specifications.
3. Supplier expertise and experience: Choose a supplier that specializes in custom plastic molding and has extensive experience in the industry. This ensures that they have the technical know-how and can provide valuable insights throughout the procurement process.
4. Material selection: Consider the type of plastic material best suited for your product. Common materials include polypropylene, polyethylene, and ABS. Consult with the supplier to determine the ideal material based on your requirements, such as durability, flexibility, or heat resistance.
5. Production capabilities: Evaluate the supplier’s production capabilities and capacity to meet your required volume and delivery timeline. Review their manufacturing facilities, equipment, and production processes to ensure they can handle your project efficiently.
6. Cost considerations: While price is an important factor, it should not be the sole determining factor. Consider the entire cost of ownership, which includes quality, durability, maintenance, and long-term use of the plastic molding.
7. Communication and collaboration: Ensure effective communication with the supplier throughout the procurement process. Regular updates, progress reports, and open communication channels will help address any issues or concerns promptly.
8. Testing and validation: Request samples or prototypes to test the plastic molding’s functionality, fit, and overall quality. This step allows you to identify any potential issues or areas for improvement before committing to a larger production run.
9. Supplier reliability and trustworthiness: Research and evaluate the supplier’s reputation and track record. Read customer reviews, request references, and verify their certifications and compliance with industry standards.
10. After-sales support: Inquire about the supplier’s after-sales support, warranty policies, and maintenance services. A reliable supplier should provide ongoing support and assistance even after the procurement process is completed.
By considering these tips and factors, you can ensure a successful procurement process for custom plastic molding that meets your specific requirements and expectations.
FAQs on Sourcing and Manufacturing custom plastic molding in China
1. Why should I consider sourcing and manufacturing custom plastic molding in China?
Sourcing and manufacturing custom plastic molding in China can offer significant cost savings compared to other countries. The lower labor costs and extensive supply chains in China make it an attractive option for businesses looking to produce plastic molded products at a competitive price. Additionally, China has a strong manufacturing infrastructure and years of experience in plastic molding, ensuring high quality and reliable production.
2. How do I find a reliable plastic molding manufacturer in China?
To find a reliable plastic molding manufacturer in China, thorough research and due diligence are necessary. Online directories, trade shows, and referrals from trusted sources can help in identifying potential manufacturers. Evaluate the manufacturer’s experience, certifications, production capabilities, and quality control processes. It is recommended to visit the manufacturer’s facilities in person to assess their operations and capabilities firsthand.
3. What are the factors to consider when selecting a plastic molding manufacturer in China?
Several factors should be considered when selecting a plastic molding manufacturer in China. These include the manufacturer’s production capacity, lead times, quality control procedures, communication capabilities, and compatibility with your specific requirements. It is also essential to ensure that the manufacturer is compliant with international standards and regulations.
4. How can I ensure the quality of the plastic molded products?
To ensure the quality of the plastic molded products, it is crucial to establish clear and detailed specifications with the manufacturer. Regular communication, sample approvals, and periodic quality inspections or certifications during production are essential. Working with a reputable manufacturer that has quality control measures in place and is willing to provide documentation and samples can help maintain the desired quality standards.
5. What are the shipping and logistics considerations when sourcing from China?
When sourcing plastic molding from China, it is important to consider shipping and logistics. Calculate the shipping costs, transit times, and any import duties or regulations that may apply in your country. Work closely with your manufacturer to plan and coordinate shipping arrangements, ensuring proper packaging and delivery methods. Engaging reliable freight forwarders or logistics providers with experience in importing from China can help streamline the shipping process.
In summary, sourcing and manufacturing custom plastic molding in China can offer cost savings, but thorough research and due diligence are necessary to find a reliable manufacturer. Factors to consider include a manufacturer’s experience, production capabilities, quality control, and compliance with standards. Ensuring product quality and coordinating shipping logistics are also crucial for a successful sourcing experience.
Why contact sourcifychina.com get free quota from reliable custom plastic molding suppliers?
Sourcifychina.com offers free quota from reliable custom plastic molding suppliers for a variety of reasons.
Firstly, Sourcifychina.com aims to provide a platform that connects businesses with reliable and trustworthy suppliers. By offering a free quota, they attract a large pool of suppliers who are willing to showcase their capabilities and quality to potential customers. This allows businesses to access a wide range of options and select the most suitable supplier based on their specific requirements.
Secondly, the free quota helps mitigate the risk for businesses. Plastic molding is a complex process that requires expertise and precision. By obtaining a free quota, businesses can assess the supplier’s capabilities, quality standards, and production capabilities without incurring any financial obligations. This allows for a thorough evaluation of the supplier’s capabilities and enables businesses to make informed decisions about partnering with a particular supplier.
Furthermore, Sourcifychina.com recognizes the importance of transparency and accountability in supplier selection. By offering a free quota, businesses can gain insights into the supplier’s communication efficiency, responsiveness, and overall professionalism. This helps businesses assess the supplier’s ability to meet their specific needs and deliver on time, ensuring a smooth and efficient partnership.
Additionally, providing a free quota allows Sourcifychina.com to establish trust and credibility among businesses and suppliers. By facilitating connections and offering a risk-free evaluation process, Sourcifychina.com positions itself as a reliable and trustworthy platform for sourcing custom plastic molding suppliers. This encourages businesses to rely on Sourcifychina.com as a dependable resource for their sourcing needs.
In conclusion, Sourcifychina.com offers free quota from reliable custom plastic molding suppliers to provide businesses with a wide range of options, mitigate risk, ensure transparency, and establish trust and credibility. By doing so, they facilitate a seamless and efficient sourcing process for businesses seeking plastic molding suppliers in China.