Introduce about welding machine types guide,Qulity,Cost,Supplier,Certification,Market,Tips,FAQ
Welding Machine Types: A Guide to Quality, Cost, Suppliers, Certifications, Market, Tips, FAQs
Welding machines are essential tools used in various industries to join metals and materials through the application of heat. This guide aims to provide an overview of different welding machine types, their quality, cost factors, reliable suppliers, relevant certifications, market trends, helpful tips, and frequently asked questions.
There are several types of welding machines available, including Stick or Arc Welding Machines, MIG Welding Machines, TIG Welding Machines, and Plasma Arc Welding Machines. Each type has its own set of advantages, applications, and suitable welding techniques. Understanding the requirements of your project or industry is crucial in selecting the right machine.
Quality is a significant consideration when investing in a welding machine. High-quality machines ensure durability, efficient performance, and extended lifespan. Key factors that determine quality include the brand reputation, manufacturing materials, technology, and reliability.
Cost is another crucial factor to consider during the purchasing process. The price of welding machines can vary based on the type, brand, specifications, and additional features. Comparing prices from different suppliers and considering long-term value for money is advisable.
Choosing a reliable supplier is essential for acquiring a welding machine that meets your requirements. Trusted suppliers provide genuine products, excellent customer service, and often offer warranty and after-sales support. Conducting thorough research, reading customer reviews, and seeking recommendations are beneficial in finding the right supplier.
Certifications play a significant role in ensuring the welding machine’s safety, quality, and compliance with industry standards. Look for machines that have obtained certifications such as ISO, CE, or UL, which validate their adherence to safety regulations.
Understanding the welding machine market trends can help in making informed decisions. Keep track of technological advancements, emerging brands, new features, and market demands to stay updated.
Here are some quick tips to consider when purchasing a welding machine: evaluate your specific needs, compare specifications, seek expert advice, budget your expenditure, consider additional accessories, and prioritize safety features.
Frequently Asked Questions (FAQs) may include queries related to the maintenance of welding machines, troubleshooting issues, selecting suitable welding techniques, and safety precautions. Refer to the manufacturer’s instructions or seek guidance from experts for specific queries.
In conclusion, investing in the right welding machine requires careful consideration of its type, quality, pricing, supplier reliability, certifications, market trends, and essential tips. By understanding these factors and conducting thorough research, you can make an informed decision that aligns with your needs and ensures optimal performance.
Types of welding machine types
Welding machines are used to join two or more pieces of metal by melting and fusing them together. There are several types of welding machines available, each designed for specific welding applications. Here are some of the most common types:
1. Stick Welding Machine (Shielded Metal Arc Welding – SMAW): This is the most basic and widely used type of welding machine. It uses a consumable electrode coated in flux to create an electric arc between the electrode and the workpiece, resulting in the deposition of metal.
2. MIG Welding Machine (Gas Metal Arc Welding – GMAW): This machine uses a wire electrode fed through a welding gun and an inert gas, typically argon or a mixture of argon and carbon dioxide, to shield the weld pool. MIG welding is fast, efficient, and suitable for welding thin to thick metal plates.
3. TIG Welding Machine (Gas Tungsten Arc Welding – GTAW): This machine uses a non-consumable tungsten electrode to create an arc and a separate filler metal, if needed. TIG welding produces high-quality, precise welds and is commonly used for stainless steel, aluminum, and exotic metals.
4. Flux-Cored Arc Welding Machine (FCAW): Similar to MIG welding, this machine uses a tubular wire filled with flux instead of a solid wire electrode. The flux provides the shielding gas and forms a slag that protects the weld pool. FCAW is versatile and suitable for both indoor and outdoor applications.
5. Plasma Arc Welding Machine (PAW): This machine uses a concentrated plasma arc to melt the metals being welded. It requires a high energy density and is often used for precision welding of thin materials or for welding in hard-to-reach areas.
6. Submerged Arc Welding Machine (SAW): In this process, the welding arc is completely submerged in a granular flux, which creates a protective layer and eliminates the need for a shielding gas. SAW is widely used in heavy fabrication, such as welding of large structures or pipes.
7. Laser Welding Machine: Laser welding uses a focused laser beam to weld metal parts. It offers high precision and speed, making it suitable for applications that require minimal heat input and minimal distortion.
These are just a few examples of the different types of welding machines available in the market. The choice of welding machine depends on factors such as the type of metal being welded, thickness, desired weld quality, and available power source. It is essential to choose the right welding machine for the specific welding application to ensure the best results are achieved.
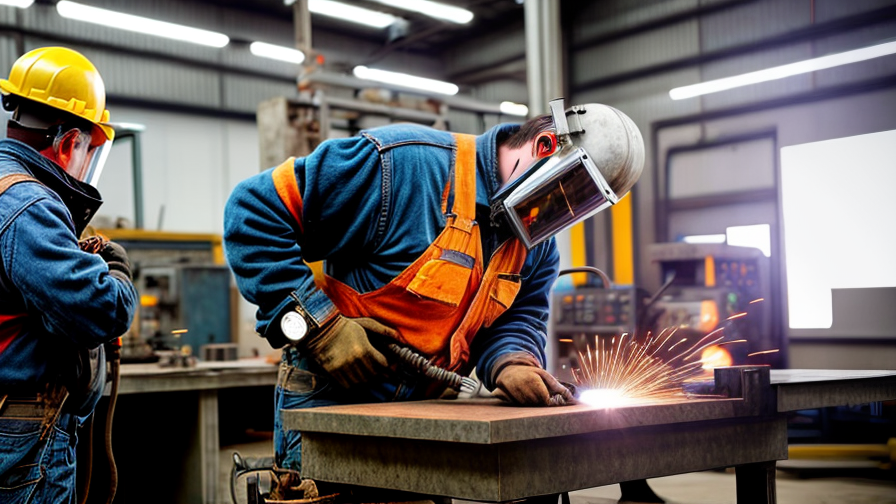
Pros and Cons of Using welding machine types
Pros of Using Welding Machine Types:
1. MIG Welding Machine:
– Easy to learn and use, hence suitable for beginners.
– Provides clean and precise welds.
– Can be used on a wide range of materials, including steel, aluminum, and stainless steel.
– High welding speed achieves faster completion of projects.
– Minimal spatter and low heat input, resulting in less distortion and better control over the welding process.
– Versatile, as it can be used for both thick and thin materials.
2. TIG Welding Machine:
– Produces high-quality welds with excellent precision and control.
– Suitable for welding thin materials and intricate designs.
– Ensures a clean weld without the need for additional cleanup.
– Provides excellent heat control, minimizing the risk of warping or damaging sensitive materials.
– Allows for welding various types of metals, including alloys and exotic materials.
– Can be used for welding in different positions, such as vertical and overhead.
3. Stick Welding Machine:
– Versatile, as it allows for welding on a wide range of materials, including stainless steel, cast iron, and carbon steel.
– Suitable for outdoor projects, as it can weld even in adverse weather conditions.
– Highly portable, making it convenient for on-site welding or remote locations.
– Robust and durable, with minimal maintenance requirements.
– Provides deep penetration, making it ideal for thick materials and heavy-duty applications.
– Offers superior weld strength and reliability.
Cons of Using Welding Machine Types:
1. MIG Welding Machine:
– Consumable wire and gas can increase operating costs.
– Limited to flat or horizontal welding positions.
– Not suitable for welding thick materials or large-scale structural projects.
2. TIG Welding Machine:
– Requires higher skill levels and more training to operate effectively.
– Slower welding speed compared to other methods.
– Higher costs due to the need for a shielding gas and filler rod.
3. Stick Welding Machine:
– Requires more skill and practice to achieve quality welds.
– Generates more spatter, resulting in additional cleanup.
– Limited to welding thick materials and less suitable for thin materials.
– Slower welding speed compared to other methods.
Overall, the choice of welding machine type depends on the specific application, skill level of the operator, and the materials being welded. Each type offers its own set of advantages and limitations, and considering these pros and cons is crucial in selecting the right welding machine for a particular task.
welding machine types Reference Specifications (varies for different product)
Welding machines are used to join two pieces of metal together by applying heat and pressure. There are various types of welding machines available in the market, each designed for specific applications and materials. The selection of a welding machine depends on factors such as the type of material, welding process, thickness of the materials to be joined, and the efficiency required.
Here are some common types of welding machines:
1. Arc Welding Machines: Also known as stick welders, these machines use an electric current to create an arc between the welding electrode and the base material. Arc welding machines are versatile and can be used for various materials like steel, stainless steel, cast iron, and aluminum.
2. MIG (Metal Inert Gas) Welding Machines: MIG welders are commonly used in automotive and industrial applications. They use a wire electrode that melts and fuses the base material together. MIG welding machines are known for their ease of use and produce clean welds.
3. TIG (Tungsten Inert Gas) Welding Machines: TIG welders are used for high-quality welding of thin and delicate materials such as aluminum, stainless steel, and copper. These machines create an arc between a non-consumable tungsten electrode and the base material, and the weld area is shielded with an inert gas.
4. Spot Welding Machines: This type of welding machine is used for joining two or more metal sheets together by applying heat and pressure at specific spots. Spot welding machines are commonly used in the automotive industry for joining sheet metals in the manufacturing of car bodies.
5. Plasma Arc Welding Machines: Plasma welding machines are used for precise and high-quality welding of materials such as stainless steel and aluminum. They use a high-velocity plasma jet to create the arc, resulting in a narrower and more focused weld.
6. Laser Welding Machines: Laser welding machines use a high-intensity laser beam to melt and join the materials together. These machines are highly accurate and are used for delicate and precision welding applications in industries like electronics and jewelry making.
7. Resistance Welding Machines: Resistance welding machines use electrical resistance to generate heat for joining metals. They are commonly used for spot welding, seam welding, and projection welding in industries like automotive and manufacturing.
It is important to refer to the specific product’s specifications and guidelines provided by the manufacturer for the proper use of welding machines. These machines come in various sizes, power ratings, and functionalities, so understanding the requirements of the welding project is crucial for selecting the right welding machine type.
Applications of welding machine types
Welding machines are essential tools used in various industries and applications to join and fabricate materials together. There are several types of welding machines, each with its own unique application.
1. Arc Welding Machines: Arc welding machines, such as shielded metal arc welding (SMAW) and gas metal arc welding (GMAW), are commonly used in construction and fabrication industries. They are ideal for joining steel, stainless steel, and aluminum, making them suitable for building structures, pipelines, and vehicle manufacturing.
2. Resistance Welding Machines: Resistance welding machines, including spot welding and seam welding, utilize electrical resistance to fuse materials together. They are widely used in the automotive industry for welding sheet metal components like car frames and body panels. These machines offer fast and efficient welding, making them suitable for high-volume manufacturing processes.
3. Gas Welding Machines: Gas welding machines, such as oxy-fuel welding and cutting, use a combination of oxygen and a fuel gas, typically acetylene, to produce a flame that melts the base metals. They are commonly used in metal fabrication, plumbing, and repair work. Gas welding machines are versatile and can join a wide range of materials, including steel, cast iron, copper, and brass.
4. Laser Welding Machines: Laser welding machines use a highly focused laser beam to heat and melt the materials, creating a strong weld joint. They are utilized in industries such as electronics, aerospace, and jewelry manufacturing. Laser welding offers precise and clean welds, making it ideal for intricate and delicate applications.
5. Ultrasonic Welding Machines: Ultrasonic welding machines create welds by using high-frequency vibrations to melt and bond materials together. They are commonly used in the plastics industry for joining thermoplastic materials. Ultrasonic welding is fast, energy-efficient, and produces strong welds, making it suitable for applications like packaging, automotive parts, and electrical components.
In summary, the applications of welding machine types are diverse and cater to various industries and materials. Arc welding machines are commonly used in construction and fabrication, while resistance welding machines are suitable for high-volume manufacturing. Gas welding machines are versatile and widely used in metal fabrication, and laser welding machines offer precise and clean welds for delicate applications. Lastly, ultrasonic welding machines are popular in the plastics industry for their speed and efficiency.
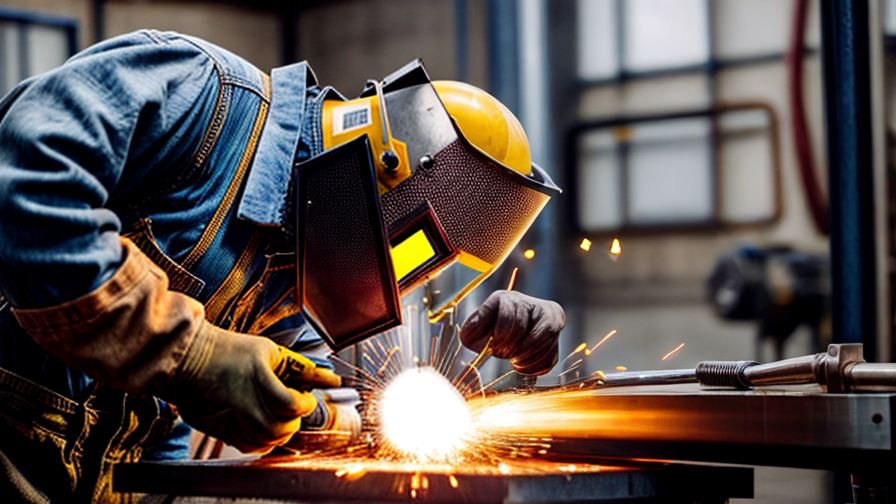
The Work Process and how to use welding machine types
The work process of welding involves joining two metal pieces together using high heat and pressure. This process requires the use of a welding machine, which comes in various types depending on the specific application.
The first step in using a welding machine is to ensure proper safety precautions. This includes wearing protective clothing, such as gloves, helmets, and goggles, to protect against sparks and UV radiation. It is also important to have a well-ventilated area to avoid inhaling toxic fumes.
Next, the appropriate welding machine type must be selected based on the project requirements. There are several common types of welding machines, including MIG (Metal Inert Gas), TIG (Tungsten Inert Gas), and Stick welding machines. Each machine works differently and offers unique advantages depending on the materials being welded, thickness, and precision required.
MIG welding is a popular choice for fast and efficient welding. It uses a wire electrode that is fed through a welding gun and melted into the joint. This method is ideal for welding thicker materials and is commonly used in automotive and construction industries.
TIG welding, on the other hand, is known for its precision and clean finish. It uses a non-consumable tungsten electrode to create the arc and requires the addition of filler material separately. TIG welding is commonly used in the aerospace and artistic industries, where intricate and precise welds are required.
Stick welding, or shielded metal arc welding, is the most basic type of welding. It uses a consumable electrode with a flux coating that creates a shield around the weld. Stick welding is versatile and can be used in various industries but requires more skill and practice compared to MIG or TIG welding.
Once the appropriate welding machine type is selected, the metal pieces to be joined must be prepared. This often involves cleaning the surfaces to be welded and ensuring they fit together tightly. The welding machine settings, such as heat and wire feed speed, should be adjusted based on the material thickness and welding technique.
When operating the welding machine, the welding gun or electrode should be held at the correct angle and moved steadily across the joint to create a strong and consistent weld. The welder must apply the right amount of pressure to ensure proper fusion between the metal pieces.
After completing the welds, it is important to inspect for any defects or imperfections. Strong welds should have good penetration, no porosity, and a smooth appearance. Any flaws should be corrected by re-welding if necessary.
In conclusion, the work process of welding involves selecting the appropriate welding machine type, preparing the metal surfaces, adjusting machine settings, and operating the machine correctly to create strong and high-quality welds. Safety precautions should always be followed to protect the welder and ensure a successful welding process.
Quality Testing Methods for welding machine types and how to control the quality
When it comes to quality testing methods for welding machines, there are several approaches that can be employed to ensure optimum performance and control the quality. Some of these methods include:
1. Visual Inspection: This involves carefully examining the welding machine for any visible defects such as cracks, deformities, loose parts, or poor surface finishes. It is a simple and effective method to identify any potential issues.
2. Non-Destructive Testing (NDT): NDT techniques like ultrasonic testing, magnetic particle testing, dye penetrant testing, or radiographic testing can be used to evaluate the internal structures of the welding machine without causing any damage. These methods help identify any hidden defects that may not be visible during visual inspections.
3. Performance Testing: This involves conducting various tests to evaluate the performance and functionality of the welding machine. For example, a weld test can be performed using prescribed welding parameters to verify that the machine produces sound and strong welds.
4. Load Testing: This method involves subjecting the welding machine to its maximum capacity or overload conditions to ensure that it can withstand the specified load without any malfunctions or failures. Load testing helps determine the machine’s durability and efficiency.
5. Environmental Testing: Environmental factors like temperature, humidity, vibrations, or exposure to dust and other contaminants can significantly impact the performance and longevity of welding machines. Therefore, subjecting the machine to various environmental conditions can help assess its ability to withstand such factors.
To control the quality of welding machines, the following steps should be undertaken:
1. Quality Assurance Procedures: Developing and implementing quality assurance procedures and guidelines ensures that the manufacturing process adheres to defined standards.
2. Calibration and Maintenance: Regular calibration and routine maintenance of welding machines are crucial to ensure accurate performance and prevent any deviations from quality standards.
3. Documentation and Traceability: It is important to maintain comprehensive documentation throughout the manufacturing process, detailing various parameters, quality checks, and test results. This documentation aids in traceability and serves as a reference for future quality control measures.
4. Training and Competence: Providing adequate training to machine operators and technicians is essential to ensure they possess the required skills and knowledge to operate and maintain welding machines effectively.
By employing these quality testing methods and implementing proper control measures, manufacturers can ensure that welding machines meet the desired quality standards, leading to enhanced performance, reliability, and customer satisfaction.
welding machine types Sample Policy and Post-Purchase Considerations for welding machine types from China
Sample Policy:
When purchasing welding machine types from China, it is important to have a well-defined sample policy in place. This policy should outline the process of acquiring samples from suppliers before making a bulk purchase. The sample policy should include the following:
1. Requesting Samples: Clearly define the method of requesting and receiving samples. Specify the quantity and quality requirements for the samples.
2. Cost and Timing: Include information on who bears the cost of samples and the expected turnaround time for receiving them.
3. Evaluation Criteria: Specify the evaluation criteria for the samples, such as performance, durability, reliability, and safety. This will help in objectively assessing the samples.
4. Feedback and Modifications: Outline the process of providing feedback on the samples to the supplier, including any required modifications or improvements.
5. Order Placement: Clearly state that the final order will only be placed after the samples meet the desired specifications and approval is given.
Post-Purchase Considerations:
After purchasing welding machine types from China, there are certain post-purchase considerations that should be taken into account. These considerations are essential to ensure smooth operations and long-term satisfaction. Some important post-purchase considerations include the following:
1. Warranty: Understand the warranty terms and conditions provided by the supplier. It is important to know what is covered, the duration of the warranty, and the process for claiming warranty services.
2. Technical Support: Determine the availability and responsiveness of technical support provided by the supplier. This includes assistance with installation, operation, maintenance, and troubleshooting.
3. Spare Parts: Confirm the availability and ease of sourcing spare parts for the welding machine types. This is crucial for minimizing downtime in case of any component failures.
4. Training and Documentation: Inquire about the availability of training programs and user manuals provided by the supplier. Adequate training and comprehensive documentation help in proper utilization and maintenance of the welding machines.
5. Supplier Reputation and Customer Reviews: Research and evaluate the supplier’s reputation in the market and consider customer reviews and experiences. This information can provide valuable insights into the quality and reliability of the welding machines.
By implementing a clear sample policy and considering these post-purchase aspects, businesses can ensure a satisfactory experience when purchasing welding machine types from China.
Sourcing welding machine types from China: Opportunities, Risks, and Key Players
China is a leading player in the global welding machine market, offering a wide range of opportunities for sourcing various types of welding machines. The Chinese welding machine market is highly developed, providing access to a diverse selection of machines at competitive prices. However, there are both opportunities and risks associated with sourcing welding machine types from China.
Opportunities:
1. Cost-effective: Chinese manufacturers often offer welding machines at lower prices due to lower production costs, providing an opportunity for cost savings.
2. Wide range of options: China offers a significant variety of welding machine types, including arc welding, resistance welding, and laser welding machines, among others. This allows buyers to find specific machines that suit their requirements.
3. Technological advancements: Chinese manufacturers have made significant technological advancements in recent years, allowing them to produce high-quality and technologically advanced welding machines.
4. Export-oriented production: Chinese manufacturers have extensive experience in exporting welding machines, ensuring they understand international quality standards and can cater to global markets.
Risks:
1. Quality concerns: While Chinese manufacturers have improved the quality of their welding machines, there may still be some concerns regarding product quality and reliability. Proper due diligence, including factory visits and product testing, is crucial to mitigate risks associated with quality.
2. Intellectual property issues: Intellectual property theft has been a concern in China. There is a risk that the design and technology of welding machines sourced from China may be replicated or counterfeited, leading to potential legal issues in the future.
3. Language and cultural barriers: Communication may be challenging due to language and cultural differences. This can result in misunderstandings or difficulties in clarifying requirements, potentially affecting the procurement process.
Key Players:
Some of the key players in the Chinese welding machine market include:
1. Huaheng Welding Co., Ltd
2. Shanghai Canon Welding Equipment Co., Ltd
3. Riland Industry Co., Ltd
4. Tianjin Xuzhi Machinery & Electrical Equipment Co., Ltd
5. Shenzhen Riland Industry Co., Ltd
In conclusion, sourcing welding machine types from China offers numerous opportunities, such as cost effectiveness, a wide range of options, and technological advancements. However, buyers should also be aware of potential risks, such as quality concerns, intellectual property issues, and language barriers. By being diligent in their research and selecting reputable manufacturers, buyers can mitigate these risks and benefit from the competitive advantages offered by China’s welding machine market.
How to find and select reliable welding machine types manufacturers in China,use google search manufacturers and suppliers
When looking to find and select reliable welding machine types manufacturers in China, using Google search can be an effective approach. Here are some steps to follow within 300 words:
1. Begin by searching for relevant keywords such as “welding machine manufacturers in China” or “welding machine suppliers in China”. This will generate a list of websites and directories that provide information on manufacturers in the welding machine industry.
2. Explore the websites that appear in the search results and make a shortlist of manufacturers that seem reputable and reliable. Look for indicators such as years of experience, certifications, customer reviews, and product range.
3. Narrow down the list to a few potential manufacturers and thoroughly research each one. Visit their official websites to learn more about their production capabilities, product quality, and certifications. Look for details about their manufacturing facilities, production processes, and quality control measures.
4. Look for online directories and B2B platforms that specialize in connecting buyers with suppliers from China. These platforms often provide detailed information about manufacturers, such as company profiles, product range, production capacity, and transaction history.
5. Utilize online forums and industry-specific communities to seek recommendations or information from professionals who have experience dealing with manufacturers in China. Their insights can help validate the reliability and reputation of potential manufacturers.
6. Contact the shortlisted manufacturers directly to inquire about their products, pricing, and any specific requirements you may have. Ask for product samples, certifications, and customer references to assess their quality and reliability.
7. Finally, assess the manufacturers’ customer service and responsiveness. Prompt and clear communication is essential for successful long-term partnerships.
By following these steps, you can find and select reliable welding machine types manufacturers in China using Google search and other online resources. Remember to conduct thorough research, verify credentials, and establish clear communication channels to ensure a satisfactory business partnership.
How to check welding machine types manufacturers website reliable,use google chrome SEOquake check if ranking in top 10M
To check the reliability of a welding machine manufacturer’s website, you can follow these steps:
1. Open the website using Google Chrome: Begin by accessing the manufacturer’s website using the Google Chrome web browser.
2. Install the SEOquake extension: Look for the SEOquake extension in the Chrome Web Store and install it on your browser. SEOquake is a popular tool used for SEO analysis that provides various metrics about a website.
3. Analyze the website’s ranking: Once installed, you can use SEOquake to check the website’s ranking. On the manufacturer’s website, click on the SEOquake icon in your browser’s toolbar, and it will display a variety of information. Look for the website’s “Alexa Rank” which indicates the website’s popularity compared to other sites on the web. Ensure that the website ranks within the top 10 million for a reasonably reliable indication.
4. Assess the domain age and authority: SEOquake also provides metrics like domain age and domain authority. These metrics can give you an idea of the website’s credibility. A older domain and higher domain authority generally indicate that the website has been around for a while and has earned a certain level of trust.
5. Check for relevant and accurate information: Browse through the website and evaluate the content. Look for comprehensive product descriptions, technical specifications, and customer reviews. Reliable manufacturers often provide detailed information about their products and have a user-friendly interface.
6. Look for certifications and affiliations: Reliable welding machine manufacturers often display certifications, affiliations, and quality standards on their website. These credentials can signify that the manufacturer adheres to certain industry norms and regulations.
7. Verify contact information: Check if the website provides proper contact details such as a physical address, phone number, and email address. Having verifiable contact information adds credibility to the manufacturer.
8. Search for customer feedback: Utilize search engines to find reviews or feedback about the manufacturer. Look for online forums, review sites, or social media platforms where customers discuss their experiences with the specific brand. This can help you gather more insights into the manufacturer’s reputation and the quality of their products.
By following these steps and using SEOquake to assess the website’s ranking and metrics, you can gain a better understanding of a welding machine manufacturer’s reliability.
Top 10 welding machine types manufacturers in China with each 160 words introduce products,then use markdown create table compare
1. Lincoln Electric: Lincoln Electric is a renowned manufacturer of welding machines in China. They offer a wide range of welding machines, including stick welders, MIG welders, TIG welders, and multi-process welders. Their products are known for their durability, performance, and user-friendly features.
2. ESAB: ESAB is another leading welding machine manufacturer in China. They specialize in producing cutting-edge welding machines such as MIG welders, TIG welders, and plasma cutters. Their machines are known for their high-quality construction and advanced technological features.
3. Miller Electric: Miller Electric is a trusted name in the welding industry. They offer a comprehensive range of welding machines, including MIG welders, TIG welders, stick welders, and multiprocess welders. Their products are known for their robustness, reliability, and excellent welding performance.
4. Kemppi: Kemppi is a well-established manufacturer of welding machines in China. They provide a wide range of welders, including MIG welders, TIG welders, and MMA welders. Kemppi machines are known for their excellent arc quality, energy efficiency, and innovative features.
5. Golden Spot Industry: Golden Spot Industry is a leading welding machine manufacturer in China. They specialize in producing high-quality MIG welders, TIG welders, plasma cutters, and spot welders. Their products are known for their precision, durability, and ease of use.
6. HUGONG: HUGONG is a reliable welding machine manufacturer in China. They offer a comprehensive range of welding machines, including MIG welders, TIG welders, and arc welders. HUGONG machines are known for their excellent welding performance, reliability, and cost-effectiveness.
7. Fronius: Fronius is a renowned manufacturer of welding machines in China. They provide a wide range of welders, including MIG welders, TIG welders, and robotic welding systems. Fronius machines are known for their advanced technology, high performance, and user-friendly interface.
8. Riland: Riland is a leading welding machine manufacturer in China. They specialize in producing MIG welders, TIG welders, plasma cutters, and arc welders. Riland machines are known for their affordability, reliability, and superior welding quality.
9. ProArc: ProArc is a trusted name in the welding industry. They offer a wide range of welding machines, including MIG welders, TIG welders, and submerged arc welding systems. ProArc machines are known for their precision, durability, and advanced welding controls.
10. Jasic: Jasic is a well-established manufacturer of welding machines in China. They provide a comprehensive range of welders, including MIG welders, TIG welders, and plasma cutters. Jasic machines are known for their excellent welding performance, energy efficiency, and user-friendly design.
| Manufacturer | Welding Machine Types |
|———————–|———————————-|
| Lincoln Electric | Stick welders, MIG welders, TIG welders, multi-process welders |
| ESAB | MIG welders, TIG welders, plasma cutters |
| Miller Electric | MIG welders, TIG welders, stick welders, multiprocess welders |
| Kemppi | MIG welders, TIG welders, MMA welders |
| Golden Spot Industry | MIG welders, TIG welders, plasma cutters, spot welders |
| HUGONG | MIG welders, TIG welders, arc welders |
| Fronius | MIG welders, TIG welders, robotic welding systems |
| Riland | MIG welders, TIG welders, plasma cutters, arc welders |
| ProArc | MIG welders, TIG welders, submerged arc welding systems |
| Jasic | MIG welders, TIG welders, plasma cutters |
Background Research for welding machine types manufacturers Companies in China, use qcc.com archive.org importyeti.com
When researching welding machine types manufacturers in China, several online platforms can provide valuable information. Websites like qcc.com, archive.org, and importyeti.com can be useful resources.
Qcc.com is a Chinese business information platform that offers comprehensive information about companies in various industries. It allows users to search for specific companies or browse through different categories, including welding machine manufacturers. By utilizing qcc.com, researchers can access company profiles, contact details, product information, and other relevant data.
Archive.org, commonly known as the Wayback Machine, is a digital archive of web pages. This platform enables researchers to view historical snapshots of websites and track their development over time. By inputting the websites of specific welding machine manufacturers from China, users can retrieve past information, such as product catalogs, corporate announcements, and previous company details.
Importyeti.com is an import-export business directory that provides data on international trade activities. This platform focuses on import and export records, offering insights into the shipment details of various products. By searching for welding machine manufacturers on importyeti.com, researchers can gather information on their export volumes, destinations, and importers’ identities, providing a broader perspective on their market presence and global reach.
In summary, by utilizing qcc.com, archive.org, and importyeti.com, researchers can access a comprehensive range of information on welding machine types manufacturers in China. These online platforms provide company profiles, contact details, historical data, export records, and other valuable insights, contributing to a well-rounded background research of the manufacturers.
Leveraging Trade Shows and Expos for welding machine types Sourcing in China
Trade shows and expos can be excellent platforms for sourcing welding machine types from China. These events bring together manufacturers, suppliers, and buyers in one location, making it convenient to explore a wide range of options and build connections. By leveraging these opportunities effectively, businesses can benefit in several ways.
Firstly, trade shows and expos provide a vast selection of welding machine types. China is known for its manufacturing capabilities, and trade shows allow attendees to explore a plethora of machines, including MIG, TIG, plasma cutters, and more. This extensive variety enables buyers to compare features, quality, and prices, helping them make informed decisions based on their specific requirements.
Secondly, these events offer the chance to connect directly with manufacturers and suppliers. In China, many manufacturers often exhibit at trade shows, allowing buyers to establish direct relationships with them. This direct interaction facilitates better communication, negotiation of prices, customization options, and future collaborations.
Furthermore, trade shows and expos provide an opportunity to stay updated with the latest welding machine trends and innovations. Manufacturers display their newest models and technologies, allowing buyers to stay ahead of the competition. By attending industry-specific seminars, workshops, or product demonstrations, businesses can gain valuable insights and knowledge about the advancements in welding machines, helping them make informed choices for their sourcing needs.
To maximize the benefits of trade shows and expos, preparation and planning are crucial. It is essential to research beforehand, identify events that highlight welding machine types, and prepare a list of desired suppliers or manufacturers to visit. Additionally, businesses should bring along their specifications and requirements to discuss with potential suppliers, ensuring a more tailored sourcing experience.
In conclusion, trade shows and expos offer an excellent opportunity for sourcing welding machine types in China. These events showcase a wide range of machines, enable direct connections with manufacturers, and provide insights into the latest trends. By effectively leveraging trade shows and expos, businesses can find suitable suppliers, negotiate better pricing, and stay up-to-date with advancements in the welding machine industry.
The Role of Agents and Sourcing Companies in Facilitating welding machine types Purchases from China
Agents and sourcing companies play a crucial role in facilitating purchases of welding machine types from China. These entities act as intermediaries between buyers and manufacturers, helping to streamline the procurement process and ensure a smooth transaction. Their involvement can greatly benefit businesses looking to source welding machines from China in several ways.
Firstly, agents and sourcing companies possess expertise and knowledge about the local market in China. They have extensive networks and connections with various manufacturers and suppliers, allowing them to identify and source high-quality welding machine types at competitive prices. By leveraging their industry knowledge, these intermediaries can help businesses find reliable and reputable manufacturers that meet their specific requirements.
Secondly, language and cultural barriers are common obstacles when dealing with overseas suppliers. Agents and sourcing companies are proficient in both the local language, typically Mandarin, and English, bridging the communication gap between buyers and manufacturers. This ensures that specifications, technical details, and any other pertinent information are accurately conveyed to the supplier, minimizing the risks of miscommunication or misunderstandings.
Moreover, agents and sourcing companies can conduct thorough inspections and quality control checks on behalf of the buyers. They can assess the production facilities and verify the quality standards and certifications of the welding machines. This helps buyers to ensure that they are procuring reliable and well-made products, reducing the chance of receiving substandard or defective goods.
Additionally, agents and sourcing companies can handle the logistics and shipping arrangements. They have experience in shipping goods internationally and can assist with customs clearance, documentation, and tracking of shipments. This aids in the efficient and timely delivery of welding machines, providing buyers with peace of mind and convenience during the process.
Finally, agents and sourcing companies can also negotiate pricing and terms with the manufacturers on behalf of the buyers. Their familiarity with the local market and industry norms allows them to navigate negotiations effectively and secure favorable deals. This can help buyers obtain competitive prices and reasonable payment terms, ensuring a cost-effective sourcing process.
Overall, agents and sourcing companies are essential facilitators in purchasing welding machine types from China. Their market knowledge, language abilities, quality control capabilities, logistics expertise, and negotiation skills make them valuable partners for buyers seeking to source welding machines efficiently and successfully from China.
Price Cost Research for welding machine types manufacturers Companies in China, use temu.com and 1688.com
When researching the price and cost of welding machine types in China, two reliable online platforms to consider are temu.com and 1688.com. These platforms offer a wide range of manufacturers and companies specializing in welding machines. The objective is to gather essential information while keeping the description within 300 words.
temu.com is an online marketplace that provides access to various manufacturers and suppliers of welding machines. To conduct price and cost research, users can search for specific welding machine types, such as MIG, TIG, or arc welders. The platform allows direct communication with manufacturers, enabling users to inquire about prices, minimum order quantities, and customization options. It also provides information on product specifications, certifications, and shipping details, helping users estimate overall costs. temu.com offers a variety of welding machine types suitable for different applications, including industrial, automotive, and DIY usage.
Another valuable platform is 1688.com, which is a comprehensive online marketplace based in China. It serves as a directory of manufacturers, suppliers, and wholesalers of various products, including welding machines. When searching for welding machine types on 1688.com, users can filter results by product specifications, price range, and supplier location. The platform displays detailed product listings, allowing users to compare prices, learn about different features, and access ratings and reviews from other customers. Users can communicate directly with suppliers through the messaging system, requesting price quotations and negotiating discounts. 1688.com also provides supplier information, allowing users to verify credentials, assess manufacturing capabilities, and estimate shipping costs.
By utilizing temu.com and 1688.com, users can conduct thorough research on welding machine types in China. These platforms offer a broad selection of manufacturers and companies, providing valuable insights into pricing, costs, and product specifications. Users can efficiently compare options, evaluate supplier credentials, and gather all essential information necessary for making informed purchasing decisions.
Shipping Cost for welding machine types import from China
The shipping costs for importing welding machines from China vary depending on several factors including the type of welding machine, its weight and dimensions, the shipping method chosen, and the destination country.
For smaller welding machines such as handheld or portable models, shipping costs can range from $100 to $500 per unit. These machines are usually lightweight and smaller in size, making them more cost-effective to ship.
On the other hand, larger welding machines such as industrial or heavy-duty models can have higher shipping costs due to their weight and size. The shipping cost for these machines can range from $500 to several thousand dollars per unit.
When it comes to shipping methods, there are several options to consider. Air freight is usually faster but more expensive, while sea freight is cheaper but takes longer. The choice of shipping method depends on the urgency of delivery and budget constraints.
It is important to note that these shipping costs are estimates and can vary depending on the shipping company and other factors such as insurance, customs fees, and taxes. Additionally, it is advisable to work with a reputable shipping agent or freight forwarder who can provide accurate cost estimates and handle the logistics of the import process.
In conclusion, the shipping costs for importing welding machines from China can range from $100 to several thousand dollars depending on the type of machine, its weight and dimensions, shipping method chosen, and destination country. It is crucial to do thorough research, work with trusted shipping partners, and consider all associated costs to ensure a smooth and cost-effective import process.
Compare China and Other welding machine types Markets: Products Quality and Price,Visible and Hidden Costs
China’s welding machine market is known for its wide range of products, competitive prices, and varying quality. When comparing it to other welding machine markets, several factors, such as product quality, price, visible and hidden costs, come into play.
In terms of product quality, China offers a wide array of options catering to different customer requirements. While some Chinese welding machines provide excellent performance and durability, others may have lower quality components. On the other hand, alternative markets often specialize in specific types of welding machines, resulting in a narrower product range, but potentially better quality control.
Price is a crucial aspect in any market comparison. China’s welding machine market is highly competitive, offering products at significantly lower prices compared to other markets. This affordability makes Chinese welding machines more accessible to a larger consumer base. In contrast, alternative markets may offer higher-priced machines due to factors such as a focus on specialized or niche products or different manufacturing costs.
Visible costs, including the product’s selling price, are relatively transparent in the Chinese market. Customers can easily compare prices and choose the most suitable option. Conversely, in alternative markets, due to a narrower product range, potential buyers might encounter difficulty finding the desired products, leading to higher visible costs.
Hidden costs, such as maintenance, repair, and long-term durability, are critical considerations. While Chinese welding machines generally offer cost-effective solutions, some may lack longevity and require more frequent maintenance or repair, resulting in hidden costs over time. In comparison, alternative markets often prioritize product durability, resulting in reduced hidden costs.
To summarize, the Chinese welding machine market offers a diverse product range and competitive prices. However, quality and hidden costs may pose challenges. Alternative markets specialize in certain welding machine types, potentially ensuring better quality control. Nonetheless, their higher prices and often limited product selection might deter some customers. Overall, buyers must carefully evaluate their specific requirements and consider the trade-offs between product quality, price, and visible and hidden costs before making a purchase decision.
Understanding Pricing and Payment Terms for welding machine types: A Comparative Guide to Get the Best Deal
Pricing and payment terms play a crucial role when considering the purchase of welding machines. To make well-informed decisions and secure the best possible deal, it is important to understand the different types of welding machines available in the market and their associated pricing structures.
There are several types of welding machines, including stick welders, MIG welders, TIG welders, and plasma cutters. Stick welders are typically the most affordable option, followed by MIG welders, TIG welders, and plasma cutters, which tend to be more expensive due to their advanced features and capabilities. It is essential to assess your specific welding needs and consider the complexity of the projects you’ll be working on to determine the most suitable machine type.
When it comes to pricing, it is crucial to compare prices from different manufacturers and suppliers. However, it’s equally important to consider the quality and reliability of the machines along with their pricing. Opting for a cheaper machine might save money upfront but may lead to increased repair costs or reduced productivity in the long run. Therefore, it is recommended to balance affordability with durability and functionality to ensure a cost-effective investment.
Payment terms can vary depending on the supplier or manufacturer. Some companies offer flexible payment options, such as installment plans or financing, which can spread out the cost of the machine over time. It is essential to evaluate these payment terms and consider your budget and cash flow before making a decision.
Another key aspect to consider is warranty and after-sales service. Ensure that the welding machine comes with a warranty period and inquire about the manufacturer’s service and support policies. This can provide peace of mind and minimize any potential disruptions in case of machine failure or malfunction.
In conclusion, understanding the pricing and payment terms of different welding machine types is essential to secure the best deal. Conducting thorough research, comparing prices, evaluating payment options, and considering the warranty and after-sales service will help ensure a wise investment that meets your welding needs while being cost-effective in the long run.
Chinese Regulations and Industry Standards Certifications for welding machine types,Import Regulations and Customs for welding machine types from China
China has implemented certain regulations and industry standards certifications for welding machine types to ensure their quality, safety, and environmental sustainability. One of the main certifications is the China Compulsory Certification (CCC), which is required for certain types of welding machines to be sold in the Chinese market. It ensures that the products meet the defined quality and safety standards set by the government.
The CCC certification process involves conducting tests and assessments of the welding machine types, including performance, safety, electromagnetic compatibility, energy efficiency, and environmental protection. Upon successful evaluation, the manufacturer is granted a CCC mark, allowing them to legally sell their products in China.
In addition to the CCC certification, there are various industry standards relevant to welding machines that manufacturers should adhere to. These standards include GB/T 15579-2008, which outlines the general requirements for welding equipment, and GB/T 8117-2008, which specifies the safety requirements for welding transformers, welding reactors, and welding power sources.
When importing welding machine types from China, it is essential to comply with the relevant regulations and customs procedures. Firstly, importers should ensure that the products being imported have obtained the necessary certifications, such as CCC and other applicable standards. Failure to comply with these regulations may result in import restrictions or legal issues.
Regarding customs procedures, importers need to provide necessary documentation, such as commercial invoices, packing lists, and a bill of lading or airway bill. The goods should be properly classified based on the Harmonized System (HS) codes, which categorize products for customs purposes. It is essential to accurately declare the value of the goods and pay any applicable customs duties or tariffs.
Importers should also be aware of any specific import restrictions or import licensing requirements imposed by their respective countries or regions. Authorities may conduct inspections to verify the compliance of imported welding machines with regulatory standards.
In conclusion, Chinese regulations require welding machine manufacturers to obtain certifications like CCC, and adhere to relevant industry standards. Importers need to comply with customs procedures and ensure the necessary certifications and documentation are in order when importing welding machine types from China.
Sustainability and Environmental Considerations in welding machine types Manufacturing
When it comes to welding machine manufacturing, sustainability and environmental considerations play a crucial role in minimizing the environmental impact of the manufacturing process as well as the operation of the machines themselves.
In the manufacturing phase, efforts can be made to optimize energy consumption, reduce material waste, and minimize water usage. Implementing energy-efficient manufacturing processes, such as using advanced technologies and equipment, can significantly reduce energy consumption and lower greenhouse gas emissions. Additionally, waste reduction strategies, such as recycling and reusing materials, can minimize the amount of waste generated during the manufacturing process.
Furthermore, considering the environmental impacts of the materials used in the manufacturing of welding machines is essential. Using sustainable materials, such as recycled metals or bio-based plastics, can help reduce the reliance on non-renewable resources and minimize the carbon footprint associated with the production of these machines.
In terms of the operation of welding machines, energy efficiency is a key factor. By designing and manufacturing machines that are more energy-efficient, less electricity will be required to power them during use, reducing both operational costs and the associated environmental impact. Implementing features like automatic shut-off when not in use or utilizing energy-saving modes can further enhance energy efficiency.
Moreover, the maintenance and disposal of welding machines should also be considered in terms of sustainability. By designing machines that are easy to maintain and repair, the lifespan of the equipment can be extended, reducing the need for frequent replacements and minimizing waste generation. Additionally, ensuring proper disposal and recycling practices for welding machines at the end of their life cycle is essential to prevent them from ending up in landfills and contributing to environmental pollution.
In conclusion, the manufacturing of welding machines should prioritize sustainability and environmental considerations. By incorporating energy-efficient manufacturing processes, using sustainable materials, focusing on energy-efficient operation, and promoting proper maintenance and disposal practices, the environmental impact of welding machines can be significantly reduced, contributing to a more sustainable and eco-friendly industry.
List The Evolution history of “welding machine types”
Welding is the process of joining two or more materials together, typically metals, to create a strong and permanent bond. Over time, welding techniques and equipment have evolved significantly to meet the ever-increasing demands of various industries. Here is a brief overview of the evolution history of welding machine types:
1. Forge Welding: The earliest form of welding, forge welding, dates back to ancient times. It involved heating the ends of two metal pieces and hammering them together. This method required skilled craftsmen and was limited in its application.
2. Carbon Arc Welding: In the late 19th century, the carbon arc welding technique was developed. It used a carbon electrode to create an electric arc between the electrode and the workpiece, melting the metals at the joint. While effective, this method had limitations, including high electrode consumption and inconsistent quality.
3. Metal Inert Gas (MIG) Welding: In the 1940s, MIG welding was introduced. It utilized a continuously fed wire electrode and an inert gas shield to protect the weld pool from atmospheric contamination. MIG welding became popular due to its versatility, speed, and ease of use.
4. Tungsten Inert Gas (TIG) Welding: Developed during World War II, TIG welding involved using a non-consumable tungsten electrode and an inert gas shield to create the arc. TIG welding offered precise control over the weld and worked well for thin and delicate materials.
5. Submerged Arc Welding (SAW): In the 1940s, SAW was developed for welding thick materials, mainly in the shipbuilding industry. It involved creating an arc beneath a layer of granular flux, which protected the weld pool and reduced spatter.
6. Plasma Arc Welding (PAW): Initially developed for aerospace applications in the 1960s, PAW utilized a highly concentrated plasma arc for welding. It provided better control and higher precision than other welding methods.
7. Laser Beam Welding (LBW): In the 1970s, LBW emerged as a highly advanced welding technique. It used a focused laser beam to melt and join the materials together. LBW offered exceptional precision, minimized heat input, and was ideal for automation.
8. Resistance Spot Welding (RSW): RSW, introduced in the early 20th century, involved passing an electric current through two overlapping sheets of metal, generating resistance and producing localized welds. This technique became widely used in automotive manufacturing.
9. Electron Beam Welding (EBW): Developed in the 1940s, EBW utilized a high-velocity electron beam to melt and join metals. It offered deep penetration and high welding speeds, primarily used in aerospace and nuclear industries.
These are just a few examples of the evolution of welding machine types. As technology continues to advance, new welding techniques and machines are constantly being developed to meet the demands of modern industries.
The Evolution and Market Trends in welding machine types Industry
The welding machine industry has come a long way in terms of technological advancements and market trends. In the past, welding machines were large and stationary, requiring a dedicated space and operator expertise. However, with the evolution of technology, welding machines have become more compact, portable, and user-friendly.
One of the major advancements in the welding machine industry is the introduction of inverter-based welding machines. These machines utilize advanced electronics to provide a higher level of efficiency, precision, and control. Inverter-based machines are smaller, lighter, and more flexible, allowing for easy transportation and operation in different environments. They also offer improved power factor correction, resulting in increased energy efficiency and reduced power consumption.
Another notable development in the industry is the rise of automated welding systems. These systems utilize robotic technology to perform welding tasks with minimal human intervention. Automated welding systems offer several advantages, such as increased productivity, quality control, and worker safety. They are especially popular in industries that require repetitive and high-volume welding operations, such as automotive, aerospace, and manufacturing.
Market trends in the welding machine industry are primarily driven by the growing demand for infrastructure development, construction, and manufacturing activities. Rapid urbanization and industrialization in emerging economies have led to increased investments in construction projects and manufacturing facilities, driving the adoption of welding machines. Additionally, the expansion of the automotive and aerospace sectors has created a demand for advanced welding solutions to meet the stringent quality requirements of these industries.
Environmental sustainability has also emerged as a significant market trend in the welding machine industry. Manufacturers are increasingly focusing on developing eco-friendly welding machines that consume less energy and produce lower emissions. This trend is driven by the need to reduce carbon footprint and comply with government regulations on environmental conservation.
In conclusion, the welding machine industry has witnessed significant evolution and market trends. The introduction of inverter-based machines and automated welding systems has revolutionized the industry by offering higher efficiency, flexibility, and precision. The market trends are driven by infrastructure development, manufacturing growth, and the need for sustainable welding solutions. As technology continues to advance, the welding machine industry is expected to further innovate and cater to the evolving needs of various sectors.
Custom Private Labeling and Branding Opportunities with Chinese welding machine types Manufacturers
Chinese welding machine manufacturers offer excellent custom private labeling and branding opportunities for businesses looking to enter or expand in the welding industry. These manufacturers specialize in producing various types of welding machines, including MIG welders, TIG welders, stick welders, and plasma cutters, among others.
Custom private labeling allows businesses to have their own logo, design, and brand name displayed on the welding machines, offering a unique identity and increasing brand recognition. Chinese manufacturers are experienced in customizing welding machines according to specific requirements, enabling businesses to create a distinct line of products tailored to their target market.
Branding opportunities with Chinese manufacturers extend beyond customization. They can also help businesses in designing packaging for the welding machines, including boxes, labels, and instruction manuals. This customization and branding allow companies to build a strong brand image and command higher market value.
Chinese manufacturers offer competitive pricing options compared to other countries, allowing businesses to enjoy cost advantages and increase profit margins. These manufacturers have well-established supply chains, efficient production processes, and access to high-quality materials. This ensures that the welding machines produced are of the highest standards, meeting international quality certifications and regulations.
To maximize the private labeling and branding opportunities, businesses must consider partnering with reliable and reputable Chinese welding machine manufacturers. Thorough research, background checks, and thorough communication are vital before finalizing partnerships. A trusted manufacturer will provide assistance in navigating various aspects like product customization, quality control, logistics, and after-sales service.
In conclusion, Chinese welding machine manufacturers offer excellent custom private labeling and branding opportunities, allowing businesses to create their unique line of welding machines. With their competitive pricing, high-quality products, and extensive experience in customization, partnering with Chinese manufacturers can be a secure and profitable option for businesses in the welding industry.
Tips for Procurement and Considerations when Purchasing welding machine types
When it comes to procurement of welding machines, there are several factors to consider to ensure you make the right purchase decision. Here are some tips and considerations:
1. Identify your welding needs: Determine the type and level of welding you will be performing. This will help you choose the appropriate welding machine for your specific requirements. Consider factors like materials to be welded, thickness, and the types of joints you will be working with.
2. Power requirements: Evaluate the power available in your facility. Different welding machines have varying power needs, so ensure that your facility can handle the required power supply.
3. Welding process: Understand the different welding processes such as MIG, TIG, stick, or flux-cored welding. Each process has its own advantages and is suitable for specific applications. Choose a welding machine that supports the welding process you need.
4. Budget: Define your budget for the welding machine. Consider the long-term costs as well, including maintenance, training, and consumables. Opting for a cheap machine may save money upfront but can result in higher costs over time due to frequent repairs or low-quality welds.
5. Quality and reliability: Look for reputable brands known for their quality and reliability. Research customer reviews and consider recommendations from experienced welders to ensure you purchase a machine that will provide satisfactory performance and durability.
6. Size and portability: Determine the size and portability requirements of your welding machine. If you need to transport it frequently or work in different locations, consider compact and lightweight options.
7. Safety features: Check for essential safety features in the welding machine, such as auto-shutdown in case of overheating or overloading, voltage protection, and thermal overload protection. Safety should be a top priority when purchasing welding equipment.
8. Service and warranty: Evaluate the warranty, after-sales service, and availability of spare parts for the welding machine. A reliable service network will ensure timely maintenance and repairs, minimizing downtime.
9. Training and support: Consider the availability of training and support resources for the chosen welding machine. Proper training will help optimize its usage and ensure safe operation.
10. Future-proofing: Anticipate future welding needs and growth. Invest in a machine that allows for upgrades or additional features to accommodate evolving requirements.
By considering these tips and taking into account your specific needs and constraints, you can make an informed procurement decision and select a welding machine that offers excellent performance and value for your money.
FAQs on Sourcing and Manufacturing welding machine types in China
Q: Can I source welding machine types from China?
A: Yes, China is one of the largest suppliers of welding machines in the world. They offer a wide range of welding machine types, including MIG, TIG, ARC, plasma cutters, spot welders, and more.
Q: How can I find manufacturers of welding machines in China?
A: There are several ways to find manufacturers in China. One option is to attend trade shows and exhibitions related to welding and manufacturing. These events often attract a large number of Chinese suppliers. Additionally, you can use online platforms, such as Alibaba, Global Sources, or Made-in-China, to search for manufacturers. It is important to do thorough research, check their credibility, and request samples or visit their factories before making a final decision.
Q: Are China-made welding machines of good quality?
A: China has a reputation for producing a wide range of quality levels. While there are many high-quality manufacturers in China, there are also some low-quality ones. It is crucial to conduct due diligence and evaluate the manufacturer’s reputation, certifications, production processes, and quality control measures before choosing a supplier. Requesting samples or visiting the factory can help assess the quality of their products.
Q: What are the advantages of sourcing welding machines from China?
A: One of the main advantages is the cost-effectiveness. China offers competitive prices due to their large-scale production capabilities, cost-efficient labor, and access to raw materials. Moreover, there is a wide variety of welding machine types available, allowing you to find the most suitable product for your specific needs. Additionally, Chinese manufacturers are often open to customization and can provide flexible manufacturing options.
Q: What should I consider when sourcing welding machines from China?
A: It is important to consider factors such as product quality, reputation of the manufacturer, certifications, production capacity, lead time, shipping options, and after-sales service. Effective communication is also crucial to ensure that your requirements are understood and met. It is recommended to work with a sourcing agent or engage in thorough research to mitigate potential risks and ensure a successful sourcing experience.
In conclusion, China offers a wide range of welding machine types and is a popular destination for sourcing. By conducting diligent research, evaluating manufacturers, and assessing quality, it is possible to find reliable suppliers and benefit from the cost-effectiveness and variety of products available.
Why contact sourcifychina.com get free quota from reliable welding machine types suppliers?
Sourcifychina.com may receive a free quota from reliable welding machine types suppliers for several reasons.
Firstly, Sourcifychina.com may have established a strong and reputable relationship with these suppliers over time. The platform could have consistently sourced high-quality welding machines from these suppliers in the past and maintained a good business relationship. As a result, the suppliers might offer a certain amount of free quota as a gesture of goodwill and appreciation for the ongoing business.
Secondly, Sourcifychina.com might guarantee a certain volume of orders or a specific long-term partnership with the suppliers. By giving a free quota, the suppliers can ensure a consistent stream of business from Sourcifychina.com. This could help the suppliers secure a stable customer and revenue source, ultimately benefiting them in the long run.
Moreover, offering a free quota could be a strategic move by suppliers to attract new customers through Sourcifychina.com. By providing a certain amount of products or services for free, suppliers offer an incentive for potential buyers to try their welding machines. This can help improve brand visibility, generate positive reviews, and potentially lead to a long-term business relationship with new customers.
Finally, Sourcifychina.com may have negotiated special terms or pricing arrangements with these suppliers. This could include discounted rates or exclusive privileges for using their platform to source welding machines. As a result, the suppliers might offer a free quota as part of these negotiated terms, aiming to build a stronger partnership with Sourcifychina.com.
In conclusion, Sourcifychina.com could receive a free quota from reliable welding machine types suppliers due to a strong existing relationship, ensuring a consistent volume of business, attracting new customers, or being part of special negotiated terms.