Introduce about machining design guide,Qulity,Cost,Supplier,Certification,Market,Tips,FAQ
The machining design guide is a comprehensive resource that provides essential information and guidelines for designing and implementing effective machining processes. It covers various aspects, including quality, cost, supplier selection, certification requirements, market analysis, tips, frequently asked questions (FAQs), and much more.
Quality is a vital consideration in machining design, as it directly impacts the final product’s performance and reliability. The guide outlines key quality control measures, such as selecting appropriate materials, implementing precise machining tolerances, and conducting thorough inspections. It also emphasizes the importance of collaboration with suppliers and adherence to industry standards to ensure consistent quality.
Cost is another crucial factor in machining design, and the guide offers insights into cost-effective strategies. It provides techniques for reducing material waste, optimizing production processes, and streamlining tooling and equipment selection. By implementing these cost-saving measures, manufacturers can enhance their competitiveness while maintaining high-quality standards.
Supplier selection is a critical aspect covered in the guide. It offers valuable tips on evaluating potential suppliers based on their expertise, industry experience, technological capabilities, and supply chain management. Additionally, it emphasizes the significance of establishing strong partnerships with reliable suppliers to ensure a smooth and efficient machining process.
Certification requirements are often necessary for compliance with industry standards and customer expectations. The machining design guide provides information about various certifications, such as ISO 9001, AS9100, or ISO/TS 16949. It outlines the benefits of obtaining these certifications, which enhance credibility and demonstrate commitment to quality and continuous improvement.
Market analysis is crucial for understanding the competitive landscape and identifying potential opportunities and challenges. The guide offers insights into market trends, customer preferences, and upcoming developments in the machining industry. This information can help manufacturers make informed decisions and develop innovative solutions for their target markets.
The guide also includes practical tips for optimizing machining design, such as selecting appropriate cutting tools, determining the ideal cutting parameters, and implementing efficient programming techniques. These tips maximize productivity, minimize errors, and improve overall machining performance.
Frequently asked questions (FAQs) provide additional clarity on common topics related to machining design, such as material compatibility, surface finishes, or design for manufacturability. The guide addresses these FAQs to assist designers and engineers in overcoming potential obstacles and making informed decisions.
In summary, the machining design guide is a comprehensive resource that covers various aspects of machining design, including quality, cost, supplier selection, certification requirements, market analysis, tips, and FAQs. It offers valuable insights and practical information to assist manufacturers in developing effective machining processes, optimizing productivity, and ensuring customer satisfaction.
Types of machining design
Machining design refers to the process of creating mechanical parts and components through various machining methods. It involves designing the optimal shape, size, and features of a workpiece, which are then manufactured using tools such as lathes, mills, drills, and grinders. There are several types of machining design, each suited for different materials, applications, and desired outcomes. Some popular types include:
1. Turning: Turning is a machining method where a workpiece rotates on a spindle, while a cutting tool removes unwanted material to create the desired shape. It is commonly used to produce cylindrical components such as shafts, rods, and bolts.
2. Milling: Milling involves rotating multiple cutting tools to remove material from a workpiece, resulting in complex shapes and features. It can be performed in horizontal or vertical orientations, allowing for versatility in creating slots, pockets, and contours.
3. Drilling: Drilling is the process of creating holes in a workpiece using a rotating cutting tool. It is often combined with other machining methods to produce accurate holes of various sizes, depths, and angles.
4. Grinding: Grinding utilizes abrasive wheels to remove material and create a smooth surface finish or precise dimensions. It is commonly used for applications requiring high precision, such as tool and die making or finishing hardened steel components.
5. Shaping: Shaping involves removing material in a linear motion to form flat surfaces and straight edges. It is typically performed using a reciprocating cutting tool, such as in planing or shaping machines, and is effective for creating large, flat workpieces.
6. Boring: Boring is the process of enlarging an existing hole or creating internal features in a workpiece. It is often used to achieve high accuracy and smooth surface finish, especially in cylindrical components.
7. CNC Machining: Computer Numerical Control (CNC) machining refers to the use of computer-controlled machines that follow pre-programmed instructions to execute machining operations. It offers greater precision, repeatability, and automation compared to traditional machining methods.
8. Wire EDM: Wire Electrical Discharge Machining (EDM) uses a thin, electrically charged wire to erode material and produce complex shapes with tight tolerances. It is commonly used for intricate parts and difficult-to-machine materials.
Each type of machining design excels in specific applications, and choosing the most appropriate method depends on factors such as material type, part geometry, required tolerances, production volume, and cost considerations. By selecting the right machining design, manufacturers can efficiently fabricate high-quality parts for a wide range of industries.
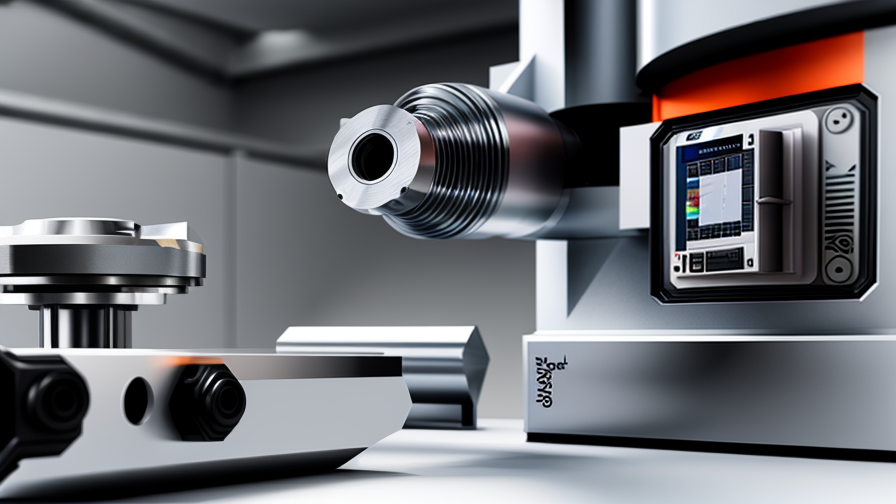
Pros and Cons of Using machining design
Machining design involves the use of machine tools and computer-aided design (CAD) software to create precise, custom parts and components. This process offers numerous benefits, as well as some limitations, which can be analyzed through a list of pros and cons:
Pros:
1. Precision: Machining design allows for the creation of highly precise and accurate parts, meeting tight tolerances and specifications. This level of precision is difficult to achieve with other manufacturing methods.
2. Versatility: Machining design can be used to create a wide range of parts, from simple to complex geometries. It is applicable to various materials such as metals, plastics, and composites, making it a versatile manufacturing process.
3. Customization: Machining design enables the production of custom parts tailored to specific requirements. It offers the flexibility to modify designs easily and produce prototypes before mass production, reducing the risk of expensive mistakes.
4. Efficiency: With the use of CAD software, machining design reduces the need for manual calculations and measurements, saving time and improving overall efficiency. CAD also allows for quick adjustments and modifications, streamlining the design process.
5. Cost-effectiveness: Although machining design can involve high initial costs due to machinery and software investment, it can be cost-effective in the long run. As designs can be modified digitally, errors and material waste are reduced, ultimately reducing production costs.
Cons:
1. Time-consuming: Machining design can be a time-consuming process, particularly for complex parts. Each part may require multiple machining operations, leading to longer production times compared to other manufacturing methods.
2. High initial investment: The equipment and software required for machining design can be costly, especially for small businesses or individuals. Purchasing, installing, and maintaining the machinery and software can be a significant investment.
3. Material limitations: While machining design is versatile, it is not suitable for all materials. Some materials may pose challenges due to their hardness, brittleness, or heat sensitivity. Additionally, certain complex geometries may be difficult to machine effectively.
4. Waste generation: Machining design can generate waste in the form of excess material and chips from the machining process. This waste must be properly managed and disposed of, which adds to production costs and environmental concerns.
5. Skills and expertise required: Effective machining design requires skilled operators with knowledge of CAD software, machining techniques, and material properties. Training and expertise are essential to achieve precise and accurate results.
In summary, machining design offers highly accurate and versatile manufacturing capabilities with customization options. However, it requires a significant initial investment, can be time-consuming, and may have limitations with certain materials and complex geometries. Overall, weighing the pros and cons can help determine the suitability of machining design for specific manufacturing needs.
machining design Reference Specifications (varies for different product)
When it comes to machining design, there are several reference specifications that should be considered. These specifications may vary for different products, depending on their nature and intended use. The following are some common reference specifications that can guide the machining design process:
1. Dimensional Tolerances: Dimensional tolerances ensure that the final product meets the required size and shape specifications. These tolerances may be expressed as a range or limit for various dimensions, such as length, width, and height.
2. Surface Finish: Surface finish specifications define the texture or smoothness of the machined surface. The surface finish is crucial for functional and aesthetic purposes, as it can affect the product’s performance and appearance.
3. Material Specifications: The choice of materials for machining design largely depends on the product’s requirements. Material specifications include factors like material composition, hardness, toughness, and corrosion resistance. These specifications ensure that the chosen material can withstand the anticipated loads and environmental conditions.
4. Machining Processes: Machining design also requires specifications for the specific machining processes to be used, such as turning, milling, drilling, or grinding. These specifications include parameters like cutting speed, feed rate, depth of cut, and tooling requirements.
5. Assembly Requirements: For products requiring assembly, specifications for part fit, clearance, and tolerances need to be considered. These specifications ensure that the machined parts can be properly assembled and function as intended.
6. Safety Considerations: Machining design should adhere to safety regulations and standards. This includes considering specifications for safety features like guards, emergency stops, and interlocks to prevent accidents during machining operations.
7. Cost and Time Constraints: In addition to technical specifications, machining design should also account for cost and time constraints. This involves optimizing the design for efficient machining, reduced material waste, and minimized production time.
Overall, these reference specifications play a crucial role in guiding the machining design process. They ensure the final product meets the required quality, performance, and cost criteria. By following these specifications, designers can create machined components that align with the intended design and functional requirements.
Applications of machining design
Machining design has various applications across different industries, including automotive, aerospace, electronics, medical, and many others. Here are some key applications of machining design:
1. Manufacturing of complex components: Machining design plays a vital role in the manufacturing of complex components with high precision and accuracy. This includes parts for engines, turbines, robots, medical devices, electronic devices, and much more. The design ensures that the components can be produced with the desired dimensions and tolerances.
2. Prototyping: Machining design is used in rapid prototyping to create functional prototypes before mass production. Using computer-aided machining (CAM) software, designers can convert digital designs into manufacturing instructions for CNC machines, which can quickly produce parts for testing and validation.
3. Tool and die making: Machining design is crucial in the production of tools and dies used in various manufacturing processes. These tools and dies are essential in shaping and forming raw materials into final products. Machining design helps optimize the tool and die geometry, ensuring efficiency and reliability during the production process.
4. Packaging machinery design: Machining design is extensively used in the design and production of packaging machinery. From food packaging to pharmaceutical packaging, the components and systems of packaging machinery are manufactured using machining processes. Design optimization ensures precise movement, alignment, and sealing, leading to efficient and reliable packaging operations.
5. Automotive industry: Machining design is indispensable in the automotive industry, where it is used to manufacture engine components, transmission parts, chassis components, and much more. The design of these components ensures adherence to strict quality and performance standards, leading to reliable and safe vehicles.
6. Aerospace industry: The aerospace industry relies heavily on machining design for the production of critical components for aircraft, rockets, and satellites. Machining design ensures the production of lightweight components with high strength and precision, contributing to the overall performance and safety of aerospace systems.
7. Medical devices: Precision machining design is crucial in the production of medical devices like surgical instruments, implants, and prosthetics. The design ensures the manufacturing of biocompatible and highly precise components, enabling advancements in medical treatments and procedures.
Overall, machining design finds applications in various industries, contributing to the efficient production of complex components, machinery, and tools. It enables manufacturers to meet stringent quality standards, achieve high precision, and ensure the reliability and functionality of the final products.
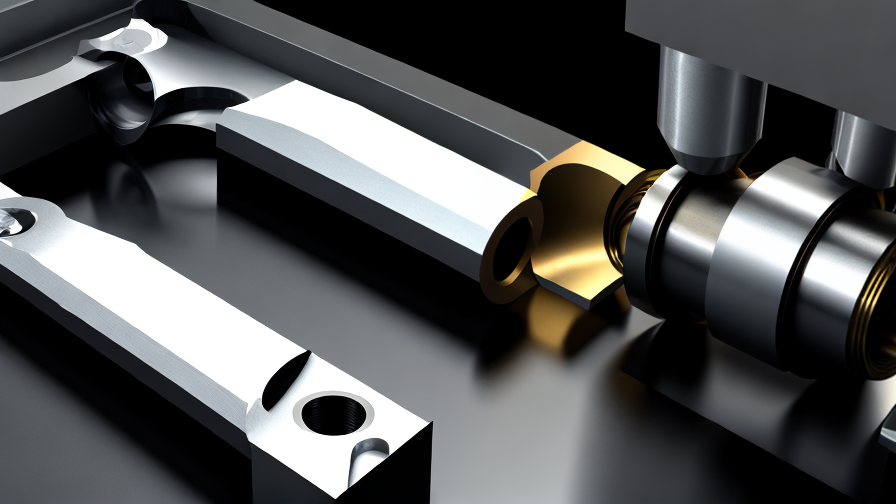
The Work Process and how to use machining design
The work process of machining design involves several steps and considerations. It begins with understanding the specific requirements of the project and gathering necessary information such as material specifications, dimensions, and desired tolerances. Once the requirements are clear, the designer proceeds to create a concept or initial design.
In machining design, computer-aided design (CAD) software is commonly used to create a detailed 3D model of the part or component. This model helps visualize the design, identify potential issues, and perform virtual tests before the actual machining process begins.
Once the design is finalized, the next step is to select the appropriate machining techniques and processes. This involves determining the suitable cutting tools, fixturing, and machining parameters such as cutting speed, feed rate, and tool paths. The designer needs to consider factors like material properties, desired surface finish, and the complexity of the part.
During the machining process, the designer should closely monitor the progress and make adjustments as needed. This may involve measuring and inspecting the part using various metrology techniques to ensure that it meets the specified requirements and tolerances.
Regular communication and collaboration with machinists, engineers, and other stakeholders are crucial throughout the work process. They can provide valuable insights, suggest improvements, and help address any challenges that may arise during the design and machining stages.
In summary, the work process of machining design entails understanding project requirements, creating a detailed 3D model using CAD software, selecting suitable machining techniques, closely monitoring the machining process, and collaborating with all relevant stakeholders. Efficient and effective machining design can lead to precise and high-quality machined parts or components.
Quality Testing Methods for machining design and how to control the quality
When it comes to quality testing methods for machining design, there are several approaches that can be adopted to ensure control and adherence to desired quality standards. These methods involve both in-process and post-process inspections, aiming to identify any deviations or defects in the machined parts. Here are some commonly used quality testing methods for machining design:
1. Visual Inspection: Visual inspection involves visually examining the machined parts for any surface defects, such as cracks, scratches, burrs, or uneven finishes. This method is relatively quick and inexpensive, helping to identify obvious defects.
2. Dimensional Inspection: This method focuses on measuring the dimensional accuracy of machined parts using a variety of tools like calipers, micrometers, depth gauges, or coordinate measuring machines (CMMs). It ensures that the parts meet the specified tolerances.
3. Hardness Testing: This method assesses the hardness of a machined part, which is critical for determining its durability and suitability for the intended application. Techniques like hardness testing provide valuable insights into the material’s strength.
4. Non-Destructive Testing (NDT): NDT techniques like ultrasonic testing, magnetic particle testing, or liquid penetrant testing are used to detect internal or hidden defects in machined parts without causing damage. These methods help ensure the integrity of the parts.
5. Performance Testing: In some cases, the machined parts may undergo performance testing to validate their functionality under real-world conditions. This can include testing for factors like load capacity, vibration resistance, or temperature tolerance.
To control the quality of machining design, several strategies can be implemented:
1. Design for Manufacturing (DFM): Ensure that the design is optimized for the machining process, minimizing the likelihood of errors or defects. Collaborating with machinists during the design phase is crucial to identify any potential manufacturing challenges or limitations.
2. Process Optimization: Continuously analyze and improve the machining process, considering factors like tooling, cutting parameters, coolant application, or workpiece clamping. Optimizing these elements can help enhance product quality.
3. Statistical Process Control (SPC): Implement SPC techniques to monitor the machining process, gathering data on critical process variables and using statistical analysis to identify any variations or trends that might affect product quality. Statistical tools like control charts can be utilized for better process control.
4. Training and Skill Development: Invest in training programs for machinists to enhance their skills and knowledge. Well-trained personnel can better understand the requirements, operate the machinery accurately, and detect and rectify any quality issues promptly.
5. Continuous Improvement: Encourage a culture of continuous improvement by actively seeking feedback from customers, conducting regular audits, and implementing corrective actions to address any quality concerns that arise.
By combining these quality testing methods and control strategies, manufacturers can ensure the production of high-quality machined parts that meet the required specifications and customer expectations.
machining design Sample Policy and Post-Purchase Considerations for machining design from China
Sample Policy and Post-Purchase Considerations for Machining Design from China
At [Company Name], we understand the critical role machining design plays in the manufacturing process. To ensure a smooth and successful partnership with our Chinese suppliers, we have established the following sample policy and post-purchase considerations:
Sample Policy:
1. Initial Communication: Prior to placing an order, we encourage open communication with the supplier to discuss design specifications, materials, lead times, and quality standards.
2. Sample Evaluation: It is advisable to request samples for evaluating the supplier’s capabilities and verifying their adherence to design requirements before proceeding with mass production.
3. Quality Control Measures: During the manufacturing process, regular quality inspections, random sample checks, and on-site visits should be conducted to ensure compliance with desired specifications.
4. Intellectual Property Protection: Our company firmly protects intellectual property rights. We recommend signing an NDA (Non-Disclosure Agreement) with the supplier to safeguard proprietary design information.
Post-Purchase Considerations:
1. Quality Assurance: After receiving the products, thorough inspections should be performed to verify the quality and performance. If any discrepancies are found, promptly communicate the issue with the supplier for resolution.
2. Packaging and Shipping: Pay close attention to packaging to prevent damage during transportation. Collaborate with the supplier to ensure appropriate packaging and reliable shipping methods are used.
3. Communication and Feedback: Staying in constant communication with the supplier is crucial. Provide clear feedback on the products received, addressing both positive aspects and areas for improvement. Timely feedback helps establish a stronger relationship and improves future orders.
4. Continuous Improvement: It is important to evaluate the supplier’s performance periodically. Identify areas that require improvement and provide constructive feedback. Encourage continuous improvement to maintain a successful partnership.
By adhering to this sample policy and post-purchase considerations, we aim to ensure a seamless and successful machining design procurement process from our Chinese suppliers.
Sourcing machining design from China: Opportunities, Risks, and Key Players
Sourcing machining design from China offers various opportunities and benefits for businesses. One of the primary advantages is the lower labor and production costs compared to many other countries. China’s vast industrial infrastructure and skilled workforce make it a competitive player in the machining design industry. This allows businesses to access high-quality machining services at a reduced cost, thereby increasing their profit margins.
Moreover, China has an extensive supply chain network, providing a wide array of machining design options to choose from. Whether it is metal fabrication, CNC machining, or precision machining, China offers a diverse range of services to cater to different business needs. The country also has a large pool of experienced designers and engineers who can provide innovative and customized solutions.
However, there are certain risks associated with sourcing machining design from China. One of the key concerns is intellectual property protection. China has been notorious for intellectual property infringements in the past, and this remains a significant risk for businesses. Unauthorized use or replication of designs and proprietary information can result in substantial losses for companies.
Another risk is the potential for communication and language barriers. Effective communication is crucial in machining design to avoid misunderstandings and ensure precise specifications are met. Thus, companies need to choose suppliers who have proficient English speakers and can provide clear documentation and instructions.
When it comes to key players in machining design in China, some notable names include Foxconn Technology Group, BYD Co., Ltd., and Huawei Technologies Co., Ltd. These companies have established themselves as leaders in the field and can provide comprehensive machining design services. Additionally, there are numerous smaller, specialized firms that cater to specific machining requirements.
In conclusion, sourcing machining design from China presents significant opportunities for businesses due to its cost-effectiveness, diverse range of services, and skilled workforce. However, companies must carefully assess the risks associated with intellectual property protection and communication barriers. By choosing reliable suppliers and implementing proper safeguards, businesses can leverage the advantages offered by China’s machining design industry.
How to find and select reliable machining design manufacturers in China,use google search manufacturers and suppliers
When searching for reliable machining design manufacturers in China, you can follow a few key steps to ensure you find and select the right one for your needs. Utilizing Google search can be a valuable tool in this process. Here’s how you can go about it:
1. Create a list of requirements: Before starting your search, clearly define your machining design requirements. Consider factors such as the specific type of machining needed, materials required, quantity, budget, and desired lead time.
2. Conduct a Google search: Start by searching for “machining design manufacturers in China” or similar keywords. Visit the websites of the manufacturers that appear in the search results. Look for those that specialize in your specific industry or product requirements.
3. Check their website: Evaluate the credibility and professionalism of the manufacturer by thoroughly examining their website. Look for comprehensive information about their services, capabilities, certifications, infrastructure, and past projects. This will give you an initial impression of their expertise and reliability.
4. Company background check: Look for relevant information about the manufacturer, such as the year of establishment, manufacturing experience, and customer testimonials or reviews. Consider the company’s reputation, certifications, and any awards or industry recognition they may have received.
5. Product quality: To ensure reliable machining, check if the manufacturer has quality control systems in place, such as ISO 9001 certification. Look for evidence of their commitment to maintaining high-quality standards and adherence to international quality assurance protocols.
6. Request for quotations: Contact shortlisted manufacturers and provide them with detailed specifications and requirements of your machining design project. Request quotations including costs, lead time, payment terms, and any other necessary information.
7. Communication and responsiveness: Pay attention to the manufacturer’s response time and communication effectiveness. Prompt and clear communication is essential for a reliable partnership.
8. Quality assurance: Inquire about their quality control procedures, inspection processes, and whether they can provide material certifications or test reports. A reliable manufacturer should be able to assure you of product quality throughout the manufacturing process.
9. Sample or trial order: Ask for a small sample order or trial production run to assess the manufacturer’s capabilities, product quality, and their ability to meet your requirements.
10. Proximity to your location: Consider the location and proximity of the manufacturer to your own facility. This can impact shipping and logistics costs, lead time, and overall convenience.
By following these steps and conducting thorough research, you can find and select reliable machining design manufacturers in China that meet your specific needs and standards.
How to check machining design manufacturers website reliable,use google chrome SEOquake check if ranking in top 10M
When determining the reliability of a machining design manufacturer’s website, you can follow these steps:
1. Use Google Chrome: Start by opening the website in Google Chrome. This browser has various useful tools and extensions to evaluate website reliability.
2. Install SEOquake: Install the SEOquake extension for Google Chrome. SEOquake is a tool that provides an overview of a website’s SEO performance, including its ranking among the top 10 million sites.
3. Analyze the website: With SEOquake activated, navigate to the website you want to evaluate. The extension will display a summary of key SEO metrics, including the website’s Alexa Rank.
4. Check Alexa Rank: Pay attention to the website’s Alexa Rank. If the website is ranked within the top 10 million sites, it generally indicates decent traffic and credibility. Websites with higher traffic are typically more reliable.
5. Assess website design: Determine if the website’s design appears professional and well-maintained. Look for clear navigation, up-to-date information, and a user-friendly interface. A well-designed website often reflects the reliability and professionalism of the manufacturer.
6. Verify contact information: Look for valid and easily accessible contact information, such as a physical address, phone number, and email address. Legitimate businesses usually provide multiple ways to get in touch.
7. Research the manufacturer: Conduct additional research on the manufacturing company. Look for customer reviews, testimonials, and information on their reputation. This can provide valuable insights into their reliability.
8. Check for certifications: Verify if the manufacturer holds any certifications or memberships in recognized industry organizations. This can indicate their commitment to quality standards and professionalism.
Remember, it is always prudent to exercise your judgment and cross-reference information from multiple sources when evaluating the reliability of a manufacturing website.
Top 10 machining design manufacturers in China with each 160 words introduce products,then use markdown create table compare
1. Foxron Precision Metal Parts Co., Ltd. (160 words)
Foxron Precision Metal Parts Co., Ltd. is a leading machining design manufacturer in China. They specialize in the production of precision metal parts for various industries, including automotive, electronics, and aerospace. With advanced CNC machining capabilities and a team of experienced engineers, Foxron delivers high-quality products that meet international standards. Their product range includes CNC machined components, aluminum extrusions, die castings, and sheet metal parts. They utilize cutting-edge technology to ensure accurate and efficient manufacturing processes, providing cost-effective solutions for clients worldwide. Foxron’s commitment to quality, reliability, and on-time delivery has earned them a solid reputation in the industry.
| **Company** | **Products** |
| ————- | ————— |
| Foxron | CNC machined components, aluminum extrusions, die castings, sheet metal parts |
2. Sinotech (Suzhou) Precision Products Co., Ltd. (160 words)
Sinotech (Suzhou) Precision Products Co., Ltd. is a renowned machining design manufacturer in China. They specialize in the production of precision machined parts for various industries, including automotive, medical, and telecommunications. With state-of-the-art facilities and a highly skilled workforce, Sinotech ensures the highest level of precision and quality in their products. They offer a wide range of services, including CNC milling, turning, and grinding, as well as surface finishing and assembly. Sinotech’s dedicated engineering team provides tailored solutions to meet specific customer requirements, ensuring customer satisfaction and long-term partnerships.
| **Company** | **Products** |
|————————–|——————-|
| Sinotech (Suzhou) | Precision machined parts, CNC milling, turning, grinding, surface finishing, assembly |
3. Dongguan Sengtor Precision Mold Co., Ltd. (160 words)
Dongguan Sengtor Precision Mold Co., Ltd. is a leading machining design manufacturer based in China. They specialize in the production of precision molds and plastic injection parts. With a strong focus on innovation and advanced technology, Sengtor delivers high-quality products that meet the stringent requirements of various industries, including consumer electronics, automotive, and medical. Their experienced team of engineers utilizes advanced CAD/CAM software and CNC machining equipment to ensure precise and efficient manufacturing processes. Sengtor’s commitment to quality assurance and customer satisfaction has made them a trusted partner for international clients seeking reliable machining design solutions.
| **Company** | **Products** |
|—————————|———————————————|
| Dongguan Sengtor Precision | Precision molds, plastic injection parts, CNC machining |
4. Shenzhen Quickmachine Technology Co., Ltd. (160 words)
Shenzhen Quickmachine Technology Co., Ltd. is a renowned machining design manufacturer in China, specializing in the production of precision machined components. They have a wide range of capabilities, including CNC milling, turning, grinding, and wire EDM. With a strong focus on quality and commitment to customer satisfaction, Quickmachine ensures efficient production processes and delivers high-quality products that meet international standards. Their precise and reliable services cater to various industries, including automotive, aerospace, and electronics. Quickmachine’s dedication to continuous improvement and advanced technology makes them a preferred choice for global clients seeking superior machining design solutions.
| **Company** | **Products** |
|————————-|—————————————————–|
| Shenzhen Quickmachine | Precision machined components, CNC milling, turning, grinding, wire EDM |
5. Precision CNC Machining Co., Ltd. (160 words)
Precision CNC Machining Co., Ltd. is a well-established machining design manufacturer in China, specializing in providing precision engineering solutions for clients worldwide. They have extensive experience in CNC machining, surface treatment, and assembly. With a commitment to quality and customer satisfaction, Precision CNC Machining delivers high-quality products that meet international standards. Their comprehensive range of services caters to different industries, including automotive, aerospace, and medical. From prototypes to mass production, their team of experts ensures accurate and timely delivery of customized solutions. Precision CNC Machining’s dedication to precision, reliability, and efficient production processes sets them apart in the industry.
| **Company** | **Products** |
|—————————|—————————————————–|
| Precision CNC Machining | Precision engineering solutions, CNC machining, surface treatment, assembly |
6. Bomei Precision Hardware Co., Ltd. (160 words)
Bomei Precision Hardware Co., Ltd. is a leading machining design manufacturer based in China, specializing in the production of precision metal parts and components. With state-of-the-art facilities and a skilled workforce, they offer comprehensive services, including CNC machining, sheet metal fabrication, and surface treatment. Bomei Precision Hardware caters to various industries, including automotive, electronics, and telecommunications. They prioritize quality control at every stage of production, ensuring that their products meet the highest standards. With a focus on customer satisfaction, Bomei Precision Hardware provides efficient solutions that meet specific requirements. Their commitment to continuous improvement and competitive pricing makes them a reliable partner for global clients.
| **Company** | **Products** |
|—————————|—————————————————–|
| Bomei Precision Hardware | Precision metal parts, CNC machining, sheet metal fabrication, surface treatment |
7. Shanghai Elue Industrial Co., Ltd. (160 words)
Shanghai Elue Industrial Co., Ltd. is a reputable machining design manufacturer in China, specializing in the production of custom precision machined parts. They offer a diverse range of services, including CNC milling, drilling, turning, and surface finishing. With a well-equipped facility and a team of experienced engineers, Elue Industrial ensures high-quality products that meet customer specifications. They serve various industries, including automotive, aerospace, and medical. With a customer-centric approach, Elue Industrial offers cost-effective solutions and efficient project management. Their dedication to quality, reliability, and timely delivery has made them a preferred choice for international clients seeking machining design expertise.
| **Company** | **Products** |
|————————-|——————————————————–|
| Shanghai Elue Industrial| Custom precision machined parts, CNC milling, turning, drilling, surface finishing |
8. Dongguan Zhiyan Mold Co., Ltd. (160 words)
Dongguan Zhiyan Mold Co., Ltd. is a leading machining design manufacturer based in China. They specialize in the production of precision molds and plastic injection parts for various industries, including automotive, electronic, and consumer goods. With advanced equipment and a team of skilled technicians, Zhiyan Mold ensures the highest levels of accuracy and quality in their products. Their comprehensive services include mold design, development, and manufacturing, as well as plastic injection molding. Zhiyan Mold’s commitment to innovation, continuous improvement, and customer satisfaction has established them as a trusted provider of reliable and cost-effective machining design solutions globally.
| **Company** | **Products** |
|————————-|———————————————————-|
| Dongguan Zhiyan Mold | Precision molds, plastic injection parts, mold development |
9. Fortuna Precision Mold Co., Ltd. (160 words)
Fortuna Precision Mold Co., Ltd. is a reputable machining design manufacturer in China, specializing in precision mold manufacturing and injection molding services. With a strong emphasis on quality control and innovative solutions, Fortuna delivers high-quality products for various industries, such as automotive, electronics, and medical. They offer a wide range of services, including mold design, development, testing, and production. Fortuna’s experienced team of engineers utilizes advanced CNC machining equipment and software to ensure accurate and efficient manufacturing processes. Their commitment to customer satisfaction, competitive pricing, and timely delivery makes Fortuna a reliable partner for global clients seeking machining design expertise.
| **Company** | **Products** |
|————————|————————————————|
| Fortuna Precision Mold | Precision molds, injection molding services, mold design and development |
10. Ningbo Sylue Machine Co., Ltd. (160 words)
Ningbo Sylue Machine Co., Ltd. is a renowned machining design manufacturer based in China. They specialize in the production of precision CNC machined parts and components. Sylue Machine offers a wide range of services, including CNC milling, turning, drilling, and surface treatment. With a strong focus on quality and customer satisfaction, Sylue Machine delivers high-quality products that meet international standards. They cater to diverse industries, including automotive, aerospace, and telecommunications. Sylue Machine’s advanced machinery and skilled technicians ensure the efficient production of customized solutions, meeting unique requirements of clients worldwide. Their commitment to continuous improvement and competitive pricing has made them a preferred choice for machining design solutions.
| **Company** | **Products** |
|———————–|———————————————————–|
| Ningbo Sylue Machine | Precision CNC machined parts, CNC milling, turning, drilling, surface treatment |
Background Research for machining design manufacturers Companies in China, use qcc.com archive.org importyeti.com
When searching for machining design manufacturers in China, several resources can be utilized to gather relevant background information. The following three websites – qcc.com, archive.org, and importyeti.com – are reliable sources to conduct research on such companies.
Qcc.com is an online platform that provides comprehensive business data in China. It offers company profiles, financial information, and legal records, making it a valuable resource for researching machining design manufacturers. By searching for specific company names or industry keywords, one can access information on their registration status, capital, shareholders, and other relevant details.
Archive.org is a digital library that provides access to archived web pages. This platform can be used to retrieve historical information about a company’s website. By entering the URL of a specific manufacturer’s website, one can view its past versions and track its development, enabling researchers to assess the company’s evolution, product range, and customer base over time.
Importyeti.com is a supplier sourcing platform that allows users to search for manufacturers and suppliers globally. By using specific keywords such as “machining design” or related terms, one can narrow down the search to Chinese manufacturers. Importyeti.com provides information on the export history, shipment details, and buyer reviews of these manufacturers, aiding in the evaluation of their reliability and product quality.
Combining information from these three resources, researchers can gain comprehensive insights into the background and credibility of machining design manufacturers in China. This approach enables informed decision-making when selecting a suitable manufacturer for one’s specific requirements.
Leveraging Trade Shows and Expos for machining design Sourcing in China
Trade shows and expos can be incredibly valuable for sourcing machining design services in China. These events provide a unique opportunity to connect with a wide range of suppliers, discover new technologies, and build relationships within the industry.
When attending trade shows and expos in China, it is essential to have a clear strategy in place to maximize the benefits. Here are some tips for leveraging these events effectively:
1. Pre-event Research: Before attending the trade show, conduct thorough research on the participating exhibitors and their specialties. Identify potential machining design suppliers that align with your requirements and target audience.
2. Schedule Appointments: Contact the shortlisted suppliers in advance and schedule one-on-one meetings or demonstrations during the event. This will ensure dedicated time to discuss your requirements and address any concerns.
3. Attend Seminars and Presentations: Trade shows often host seminars and presentations on various industry topics. Attend these sessions to gain insights into the latest advancements in machining design technology, market trends, and supplier capabilities.
4. Network with Industry Experts: Engage in conversations with industry experts, including engineers, designers, and manufacturers. They can offer valuable advice, share their experiences, and provide referrals to reliable machining design suppliers in China.
5. Request Samples and Catalogs: Don’t hesitate to ask for product samples, catalogs, or brochures from the suppliers you are interested in. These materials will help you assess the quality of their work and determine their suitability for your project.
6. Negotiate Contracts and Pricing: Trade shows often offer opportunities for negotiation and special discounts. Use this to your advantage and secure favorable terms and pricing from the machining design suppliers you are considering.
7. Follow Up: After the event, follow up with potential suppliers to solidify any agreements made, clarify any remaining questions, and establish a timeline for further discussions or project milestones.
By leveraging trade shows and expos in China, you can access a vast network of machining design suppliers, gain insights into emerging technologies, and build valuable relationships within the industry. With careful preparation and planning, these events can significantly contribute to successful sourcing efforts.
The Role of Agents and Sourcing Companies in Facilitating machining design Purchases from China
Agents and sourcing companies play a crucial role in facilitating machining design purchases from China. These entities act as intermediaries between the buyers and Chinese manufacturers, simplifying the procurement process, and enabling businesses to access cost-effective and high-quality machining design solutions.
Agents and sourcing companies have extensive knowledge and experience in the Chinese market. They are well-versed in the local manufacturing landscape, including the capabilities, expertise, and specialties of various manufacturers. This knowledge allows them to identify the most suitable suppliers for specific machining design requirements.
One of the key roles of agents and sourcing companies is to handle communication and negotiation on behalf of the buyer. They bridge the language and cultural gap between the two parties, helping to ensure smooth and effective communication. Agents are fluent in both English and Chinese, which allows them to accurately convey the buyer’s requirements to the manufacturer and facilitate effective collaboration throughout the design and production process.
Agents and sourcing companies also provide valuable assistance in the sourcing and qualification of suppliers. They conduct thorough supplier evaluations, including factory visits, quality control assessments, and verification of relevant certifications, to ensure that the suppliers meet the required standards. This vetting process helps to mitigate the risks associated with sourcing from unknown or unqualified manufacturers.
Furthermore, agents and sourcing companies assist buyers in negotiating favorable pricing and terms with the suppliers. Their expertise in local market dynamics enables them to navigate the pricing structure and negotiate competitive pricing on behalf of the buyers. They also help buyers in understanding the market dynamics, including factors such as currency exchange rates, production costs, and industry trends, which can impact pricing decisions.
Overall, agents and sourcing companies simplify the purchasing process and alleviate the potential challenges and risks associated with sourcing machining designs from China. Their expertise, local knowledge, and strong supplier networks enable businesses to access cost-effective and high-quality machining solutions, ensuring successful transactions with Chinese manufacturers.
Price Cost Research for machining design manufacturers Companies in China, use temu.com and 1688.com
When it comes to finding machining design manufacturers in China, two popular platforms to consider are temu.com and 1688.com. By utilizing these platforms, one can effectively conduct price cost research in order to find the most suitable manufacturers for their needs.
Temu.com is a reliable and user-friendly online platform that connects buyers with Chinese manufacturing suppliers. It provides access to a wide range of product categories, including machining design. Utilizing temu.com, buyers can browse through a vast catalog of manufacturers and request quotes based on their specific requirements. The platform allows users to compare prices, quality, and manufacturing capabilities, helping them make informed decisions.
Similarly, 1688.com is one of the largest online wholesale marketplaces in China. It offers a comprehensive range of products, making it an ideal platform for finding machining design manufacturers. However, it is important to note that this platform is primarily in Chinese, so it may be necessary to use translation tools, such as Google Translate, to navigate the website effectively.
When conducting price cost research on these platforms, it is advisable to keep the description concise and specific to the machining design requirements. Including details about quantities, materials, dimensions, and other crucial specifications will help in obtaining accurate and relevant quotes.
While searching for suitable manufacturers, be sure to consider factors beyond just the price. Assessing the reliability and quality of the manufacturers is equally important. Proper due diligence, such as reading reviews, checking certifications, and communicating directly with the manufacturers, will help in selecting the most suitable supplier.
In summary, temu.com and 1688.com are valuable platforms for conducting price cost research for machining design manufacturers in China. By utilizing the features offered by these platforms and considering various factors beyond just the price, buyers can find reliable suppliers for their manufacturing needs.
Shipping Cost for machining design import from China
The shipping cost for importing machining designs from China depends on various factors such as the weight and size of the package, the shipping method chosen, and the destination country. However, there are generally two common shipping methods for importing goods from China: air freight and sea freight.
Air freight is usually a faster but more expensive option. The cost is typically calculated based on the weight and volume of the package. For small and lightweight packages, there are shipping services such as DHL, FedEx, and UPS, which offer door-to-door delivery with tracking services. The shipping cost for air freight from China to most countries ranges from $5 to $20 per kilogram, but it may vary based on the volume and urgency of the delivery.
Sea freight is a more affordable option for larger and heavier shipments. The cost is calculated based on the volume and type of goods, as well as the destination port. Shipping via sea freight is usually done using containers, and fees may include customs clearance, documentation, and handling charges. The shipping cost for sea freight from China to most countries ranges from $500 to $2000 per container, depending on the size and weight of the shipment.
It is important to note that additional costs may be incurred, such as customs duties, taxes, and import fees, which vary from country to country. These charges are typically determined by the customs authorities of the importing country and are the responsibility of the buyer.
To minimize shipping costs, it is advisable to plan ahead and consolidate orders to maximize the use of container space and minimize the number of shipments. Additionally, choosing a reliable and experienced freight forwarder or shipping agent can help navigate the complex logistics process and potentially negotiate better shipping rates.
Overall, the shipping cost for importing machining designs from China can vary widely based on multiple factors. It is recommended to obtain quotes from different shipping companies and consider the specific requirements of the shipment to determine the most cost-effective shipping option.
Compare China and Other machining design Markets: Products Quality and Price,Visible and Hidden Costs
China is renowned as one of the world’s manufacturing powerhouses, particularly in the realm of machining design. When comparing China to other machining design markets, several factors need to be considered, including product quality and price, visible and hidden costs.
Product quality in China has improved significantly over the years, with many Chinese manufacturers offering products that meet international standards. However, there is still a perception that products from other machining design markets like Japan, Germany, or the United States may offer higher quality. These markets have a long-standing reputation for precision engineering and attention to detail. Conversely, China is often associated with mass production and cost-cutting measures, leading some to question the overall quality of their products.
Price is where China truly stands out. Chinese manufacturers have a competitive edge when it comes to pricing due to lower labor and production costs. This has made China an attractive option for many businesses looking to reduce manufacturing expenses. In contrast, other machining design markets, such as Japan or Germany, tend to have higher labor costs, leading to comparatively higher price tags on their products.
Visible costs refer to the expenses that are evident when procuring products or services. In this aspect, China’s manufacturing advantage becomes even more apparent as they offer lower visible costs compared to other markets. The competitive pricing from Chinese manufacturers is primarily due to economies of scale and a well-established supply chain. This allows businesses to save money when purchasing from China, making it a cost-effective choice.
Hidden costs, on the other hand, can arise from various factors such as logistics, quality control, and intellectual property protection. China has faced criticism for potential hidden costs, including issues like supply chain disruptions, inconsistent quality control, and intellectual property infringement. However, other machining design markets are not immune to hidden costs either. They may have higher labor costs, complex import/export regulations, or stringent quality standards that can drive up expenses throughout the supply chain.
In summary, when comparing China to other machining design markets, there are trade-offs between product quality and price. China offers competitive prices due to their lower labor and production costs, making it an enticing choice for many businesses. However, other markets like Japan or Germany may have a stronger reputation for product quality and precision engineering. The visible costs from China are generally lower, thanks to economies of scale and an established supply chain. However, hidden costs such as logistical challenges, quality control issues, and intellectual property concerns are factors that need to be considered when sourcing from any market.
Understanding Pricing and Payment Terms for machining design: A Comparative Guide to Get the Best Deal
When it comes to machining design, understanding pricing and payment terms is essential to ensure you get the best deal. This comparative guide will provide insights into the factors that influence pricing and payment terms, enabling you to make informed decisions while minimizing costs.
Firstly, the complexity and intricacy of the design play a significant role in determining the price. Designs with intricate details or demanding specifications require more time, resources, and expertise, thus resulting in higher costs. Consider the level of complexity and detail required for your project and communicate it clearly to potential machining design providers.
The material being used is another important factor. Different materials have varying machining properties and costs. For example, metals like aluminum and brass are generally less expensive to machine compared to titanium or stainless steel. Understand the material requirements for your design and inquire about the associated costs.
Batch size or quantity also affects pricing. Machining design providers often offer volume discounts for larger production runs. It is advisable to evaluate your project’s requirements and determine the most cost-effective batch size. Sometimes splitting the project into smaller batches might be more economical.
Another crucial aspect is lead time. Tight deadlines or rush orders might incur additional charges due to expedited production or overtime costs. Planning ahead and allowing ample lead time will not only help you avoid extra charges but also ensure better quality.
Payment terms vary among machining design providers. Common payment options are upfront payment in full, progressive payments based on project milestones, or installment payments. Evaluate your financial capabilities and choose a payment option that aligns with your needs and cash flow.
Seek quotes from multiple machining design providers to compare prices and payment terms. However, keep in mind that quality should not be compromised for the sake of lowering costs. Ensure that the providers you consider have a track record of delivering high-quality work.
In conclusion, understanding the factors influencing pricing and payment terms for machining design is crucial for obtaining the best deal. Carefully evaluate the complexity of the design, material requirements, batch size, lead time, and available payment options. By analyzing quotes from multiple providers, you can make an informed decision that balances cost-efficiency and quality.
Chinese Regulations and Industry Standards Certifications for machining design,Import Regulations and Customs for machining design from China
Chinese Regulations and Industry Standards Certifications for machining design ensure the quality and safety of machined products. The main certification for machining design in China is the China Compulsory Certification (CCC) system. This system, implemented by the Certification and Accreditation Administration of China (CNCA), requires certain products, including some machining equipment, to undergo testing and certification before they can be sold in the Chinese market.
To meet the CCC requirements, machining designs must adhere to relevant standards set by the Standardization Administration of China (SAC). SAC has established a series of standards such as GB/T, GB, and JB to regulate different aspects of machining design, including performance, safety, and quality control.
Importing machining designs from China requires compliance with customs regulations. The China Customs Authority oversees imports and enforces certain regulations to ensure smooth trade and protect domestic industries. Importers need to be aware of the following aspects:
1. Customs Declarations: Importers must accurately declare the details of the imported machinery, including the purpose, specifications, and intended usage.
2. Documentation: Importers need to provide necessary documentation, such as commercial invoice, packing list, bill of lading or airway bill, and any relevant certifications or licenses.
3. Import Duties and Taxes: Customs duties, value-added tax (VAT), and consumption tax may be levied on imported machining designs. Importers should be aware of these costs and factor them into pricing considerations.
4. Customs Clearance: Imported machining designs must go through customs clearance procedures, which involve inspections, document verification, and payment of any applicable duties and taxes.
Importers should work closely with their freight forwarders or customs agents to ensure compliance with import regulations and a smooth customs clearance process.
In summary, machining design in China must meet the requirements of the CCC certification system and adhere to relevant industry standards. Importers should be familiar with Chinese customs regulations and complete all necessary documentation and declaration processes for a successful import.
Sustainability and Environmental Considerations in machining design Manufacturing
Sustainability and environmental considerations in machining design manufacturing are crucial aspects that need to be integrated into the overall product development process. With the increasing focus on environmental protection and the need to minimize the impact of manufacturing activities, incorporating sustainability principles and practices has become a priority for many industries.
One of the key elements in sustainable machining design manufacturing is the efficient use of resources. This involves optimizing the use of energy, raw materials, and water throughout the manufacturing process. The selection of materials that have a lower environmental impact, such as recycled or renewable materials, can also contribute to sustainability goals.
Reducing waste generation is another important aspect of sustainable machining design manufacturing. This can be achieved by implementing strategies such as lean manufacturing techniques, which aim to minimize waste by optimizing production processes and eliminating unnecessary steps. Recycling and proper disposal of waste materials are also essential to minimize the environmental impact.
Moreover, the integration of renewable energy sources in machining design manufacturing can significantly reduce the carbon footprint. Utilizing solar panels or wind turbines to power manufacturing facilities can help lower greenhouse gas emissions. Similarly, implementing energy-efficient equipment and machinery can contribute to energy conservation and sustainability goals.
Additionally, sustainability considerations should extend beyond the manufacturing process to the entire product life cycle. Considering the end-of-life aspects of a product, such as recyclability or ease of disassembly, can facilitate proper disposal and minimize waste accumulation.
Lastly, incorporating environmentally friendly practices in machining design manufacturing requires collaboration and communication among stakeholders. This includes working closely with suppliers to ensure the use of sustainable materials, engaging employees to promote sustainability practices, and involving customers to encourage responsible product use and disposal.
Overall, sustainability and environmental considerations in machining design manufacturing are essential not only to meet regulatory requirements but also to address the growing consumer demand for environmentally friendly products. By integrating sustainable practices, manufacturers can contribute to a greener future while also achieving economic benefits through resource efficiency and waste reduction.
List The Evolution history of “machining design”
Machining design has undergone significant evolution throughout history, driven by advancements in technology and the need for more efficient and precise manufacturing processes. Here is a brief overview of the key milestones in the evolution of machining design:
1. Early Machining Techniques (Ancient times – 18th century): The earliest forms of machining date back to ancient civilizations, such as the Egyptians and Greeks, who used primitive tools like chisels and saws to shape materials. Over time, simple machines like lathes and mills emerged, enabling more advanced machining operations.
2. Industrial Revolution (Late 18th – 19th century): The invention of the steam engine and the development of interchangeable parts in the late 18th century triggered a manufacturing revolution. This period saw significant improvements in the precision and speed of machining, with the introduction of machine tools like the lathe, milling machine, and planer.
3. Numerical Control (NC) Systems (Mid-20th century): The development of numerical control systems in the mid-20th century marked a major milestone in machining design. These systems replaced the reliance on manual control, allowing the automation of machine tools through punched cards or magnetic tapes. NC systems enhanced precision, repeatability, and productivity.
4. Computer Numerical Control (CNC) (1960s – 1980s): The integration of computers into machine tool control gave rise to CNC machining. CNC allowed for greater control and programming flexibility, making complex machining operations feasible. With CNC, machining design became more streamlined, precise, and capable of handling intricate geometric shapes.
5. Advanced CAD/CAM Integration (1990s – Present): The integration of computer-aided design (CAD) and computer-aided manufacturing (CAM) systems revolutionized machining design further. CAD/CAM provides engineers and designers with advanced tools for modeling, simulation, and optimization of machining processes. This integration enables faster prototyping, reduced errors, and increased efficiency in production.
6. 3D Printing and Additive Manufacturing (21st century): The advent of 3D printing and additive manufacturing techniques has disrupted traditional machining design practices. While not strictly classified as machining, these processes offer new possibilities for rapid manufacturing of complex geometries, customization, and reduced material waste.
Overall, the evolution of machining design has been characterized by a gradual shift from manual techniques to computer-controlled processes, with a continuous focus on enhancing precision, efficiency, and flexibility. Today, machining design benefits from advanced technologies like CNC, CAD/CAM integration, and additive manufacturing, driving innovation in various industries.
The Evolution and Market Trends in machining design Industry
The machining design industry has undergone significant evolution over the years, driven by advancements in technology and changing market trends. Machining design refers to the process of developing and optimizing the design of components and parts to be manufactured using machining techniques.
One of the most notable trends in the machining design industry is the increasing adoption of computer-aided design (CAD) and computer-aided manufacturing (CAM) software. These tools have revolutionized the design process by enabling engineers to create complex and precise 3D models that can be directly translated into machine instructions. CAD/CAM software not only enhances design capabilities but also improves efficiency and reduces the time required for prototyping and production.
Another major trend in the machining design industry is the growing use of advanced machining technologies such as multi-axis machining, high-speed machining, and additive manufacturing. Multi-axis machining allows for increased flexibility and the ability to produce intricate geometries, while high-speed machining enables faster production rates and improved surface finishes. Additive manufacturing, also known as 3D printing, has the potential to transform the industry by enabling the production of complex parts with reduced lead times and material waste.
Furthermore, the machining design industry is also experiencing a shift towards sustainability and eco-friendly practices. There is an increasing demand for lightweight components and reduced material usage, leading to the adoption of optimization techniques and advanced materials. Manufacturers are also focusing on implementing energy-efficient machining processes and recycling strategies to minimize environmental impact.
In terms of market trends, there is a growing demand for customized and highly specialized machining designs. Industries such as aerospace, automotive, medical, and electronics require components with unique specifications, leading to a need for tailored machining design solutions. This trend has led to the emergence of specialized machining design firms that cater to specific industries or applications.
Additionally, globalization has had a significant impact on the machining design industry. With the rise of outsourcing and international competition, manufacturers are facing pressure to reduce costs while maintaining high-quality standards. This has led to the adoption of lean manufacturing principles, automation, and the integration of digital technologies to optimize processes and improve efficiency.
In conclusion, the machining design industry has evolved to meet the demands of advancing technology and changing market trends. The adoption of CAD/CAM software, advanced machining technologies, and sustainable practices have transformed the industry. Furthermore, the demand for customization, specialization, and cost optimization has driven the need for tailored machining design solutions. As technology continues to progress, the machining design industry will likely continue to evolve and adapt to meet the ever-changing market demands.
Custom Private Labeling and Branding Opportunities with Chinese machining design Manufacturers
Chinese machining design manufacturers offer custom private labeling and branding opportunities for businesses looking to establish their own unique identity in the market. These manufacturers can create products that are tailored to meet the specific needs and requirements of the brand, while also incorporating their own design and branding elements.
By partnering with a Chinese machining design manufacturer, businesses have the flexibility to design and develop products that align with their brand aesthetic and values. Whether it is customizing the product shape, color, material, or incorporating branding elements such as logos or labels, these manufacturers have the capabilities to bring the brand’s vision to life.
Furthermore, Chinese machining design manufacturers have extensive experience in dealing with different industries and markets, making them well-versed in understanding the target audience and market trends. They can provide valuable insights and suggestions to help optimize the product design and branding strategy.
In addition to customization options, these manufacturers often offer private labeling services. This means that businesses can have their brand name, logo, and other identifying information displayed on the products, creating a cohesive and professional image for the brand.
Private labeling and branding opportunities with Chinese machining design manufacturers can be a cost-effective solution for businesses looking to streamline their supply chain. By working directly with manufacturers, businesses can eliminate intermediaries, reducing costs and production lead times.
In conclusion, partnering with Chinese machining design manufacturers presents businesses with the opportunity to create custom products that reflect their brand identity and values. With their expertise in customizing designs and offering private labeling services, these manufacturers can help businesses establish a unique and marketable brand presence.
Tips for Procurement and Considerations when Purchasing machining design
When it comes to procurement of machining designs, there are several important considerations that need to be taken into account. Here are some tips and considerations to keep in mind:
1. Define your requirements: Before starting the procurement process, clearly define your requirements and expectations. Consider factors such as the type of machining design you need, specific features, tolerances, materials, and any other specific requirements.
2. Conduct a thorough market analysis: Research and identify potential suppliers or vendors that specialize in machining designs. Evaluate their experience, expertise, reputation, and track record. This will help you shortlist reliable and reputable suppliers who can meet your requirements.
3. Quality assurance: Quality is crucial when it comes to machining designs. Ensure that your chosen supplier has implemented quality control measures and complies with industry standards. Ask for certifications or quality assurance processes to gain confidence in their capabilities.
4. Cost-effectiveness: While cost should not be the sole consideration, it is important to find the right balance between quality and affordability. Request quotes from several suppliers and compare them, taking into account factors like warranty, maintenance costs, and potential additional charges.
5. Technical support and after-sales service: Check if the supplier offers technical support and after-sales service. This includes timely troubleshooting, maintenance, and repair assistance. This will ensure smooth operation and minimize downtime in case of any issues.
6. Capacity and lead time: Evaluate the supplier’s capacity to handle your project and meet your deadlines. Check if they have the necessary resources, equipment, and expertise to fulfill your order within the desired timeframe.
7. Communication and collaboration: Effective communication is vital for successful procurement. Establish clear lines of communication with your supplier and maintain a collaborative approach throughout the process. This will help in resolving any potential issues and ensuring the machining design meets your expectations.
8. Intellectual property protection: If your machining design is unique or proprietary, ensure that the supplier can guarantee intellectual property protection. Sign non-disclosure agreements or secure appropriate patents to safeguard your designs.
9. Environmental and ethical considerations: Consider the supplier’s commitment to environmental sustainability and ethical practices. Ensure they adhere to regulations and standards related to waste management, energy consumption, and labor rights.
By considering these tips and factors while procuring machining designs, you can enhance the chances of obtaining high-quality designs that meet your specific requirements while ensuring a smooth and efficient procurement process.
FAQs on Sourcing and Manufacturing machining design in China
1. Why should I consider sourcing and manufacturing machining design in China?
Sourcing and manufacturing machining design in China offers numerous advantages, such as cost-effectiveness due to low labor and production costs, a vast network of suppliers and manufacturers, and advanced technology and machinery. China has emerged as a global manufacturing hub, providing high-quality products and services at competitive prices. The country’s extensive manufacturing experience and capabilities make it an ideal choice for machining design projects.
2. What types of machining design can be sourced and manufactured in China?
China’s machining design industry covers a wide range of products, including complex precision components, CNC machining parts, die casting components, injection molding products, and much more. From simple to intricate designs, China-based manufacturers have the expertise and capabilities to handle various machining requirements.
3. How can I find reliable suppliers and manufacturers in China for machining design?
To ensure reliable sourcing and manufacturing in China, it is essential to conduct thorough research and due diligence. Utilizing online platforms and directories like Alibaba, Global Sources, or Made-in-China can be a good starting point. It is recommended to request quotes from multiple suppliers, assess their capabilities and quality control measures, and verify their certifications and industry reputation. Visiting trade shows and exhibitions, or engaging with sourcing agents or consulting firms specialized in China manufacturing can also aid in finding reputable partners.
4. How can I ensure quality control and product consistency in manufacturing machining design in China?
Quality control is crucial when sourcing and manufacturing in China. It is imperative to establish clear specifications, quality standards, and inspection protocols in collaboration with the chosen supplier. Regular communication with the manufacturer throughout the production process, providing detailed feedback, and conducting on-site inspections or third-party quality control inspections can help ensure product consistency and adherence to requirements.
5. Can China-based manufacturers handle customized machining design projects?
Yes, China-based manufacturers are capable of handling customized machining design projects. With access to advanced technology and skilled engineers, they can work closely with customers to design, prototype, and produce machined components according to specific requirements. It is essential to provide detailed drawings, specifications, and samples to facilitate accurate reproduction and customization.
In conclusion, sourcing and manufacturing machining design in China offer various advantages, including cost-effectiveness, a vast range of manufacturing capabilities, and high-quality products. Conducting thorough research, finding reliable suppliers, emphasizing quality control, and leveraging customization options are crucial steps to ensure successful sourcing and manufacturing projects in China.
Why contact sourcifychina.com get free quota from reliable machining design suppliers?
Sourcifychina.com is a platform that connects businesses with reliable machining design suppliers in China. This platform offers a unique opportunity for businesses to get a free quota from these suppliers for a variety of reasons.
Firstly, the suppliers on Sourcifychina.com are carefully vetted and selected based on their track record of delivering high-quality machining design services. These suppliers have proven themselves to be reliable and trustworthy, ensuring that businesses can confidently seek their services.
Secondly, by offering a free quota, Sourcifychina.com allows businesses to assess the capabilities and pricing of different suppliers without any financial commitment. This is particularly beneficial for businesses that are in the initial stage of exploring manufacturing options or are looking to switch suppliers. By getting a free quota, businesses can easily compare and evaluate the offerings of different suppliers, enabling them to make informed decisions.
Moreover, Sourcifychina.com understands that businesses often have specific requirements or custom designs that need to be incorporated into the machining process. By offering a free quota, the platform encourages businesses to communicate their design needs with the suppliers upfront. This helps in reducing misunderstandings and streamlining the manufacturing process, ultimately leading to better outcomes.
Furthermore, providing a free quota allows businesses to estimate the cost and feasibility of their machining design projects accurately. This eliminates the risk of unexpected expenses or delays during the manufacturing process, ensuring smoother operations and better cost management.
In conclusion, Sourcifychina.com offers a free quota from reliable machining design suppliers to enable businesses to assess, compare, and communicate their design requirements without any financial commitment. This ensures that businesses can make informed decisions, optimize their manufacturing processes, and achieve successful outcomes.