Introduce about injection molding processes guide,Qulity,Cost,Supplier,Certification,Market,Tips,FAQ
Injection molding is a widely used manufacturing process that involves injecting molten material into a mold to create a desired shape or product. This comprehensive guide aims to provide information on different aspects of injection molding, such as the process, quality, cost, suppliers, certifications, market, tips, frequently asked questions (FAQs), and more.
The injection molding process involves the following steps: the molten material is injected into a mold cavity, cooled to solidify the product, ejected from the mold, and then ready for further finishing operations. It is a highly versatile process, allowing for the production of complex and intricate parts with high precision.
Quality is a crucial aspect of injection molding. Factors affecting quality include mold design, material selection, machine performance, and process control. A comprehensive quality control system is essential to ensure defect-free products and consistent production.
Cost considerations in injection molding include material costs, mold fabrication expenses, machine and labor costs, and overheads. Optimizing the process and employing efficient manufacturing techniques can help control costs.
Finding a reliable supplier for injection molding services is crucial. Look for experienced and reputable companies that offer a wide range of capabilities, including tool design, mold manufacturing, and post-processing services. Reading customer reviews and checking their certifications and accreditations can aid in selecting the right supplier.
Certifications and accreditations ensure that the supplier adheres to industry standards and best practices. Look for suppliers with certifications like ISO 9001 (quality management), ISO 14001 (environmental management), and ISO 13485 (medical devices) to ensure their commitment to quality and compliance.
The injection molding market is driven by various industries such as automotive, consumer electronics, medical, and packaging. The market is expected to witness steady growth, driven by technological advancements, increasing demand for lightweight and durable products, and the need for eco-friendly materials.
Here are some helpful tips for successful injection molding: optimize the design for manufacturability, select the right material, maintain proper mold temperature, monitor and control process parameters, and conduct regular maintenance of machines and molds.
Frequently Asked Questions (FAQs) about injection molding may include queries about material selection, cycle time, part design guidelines, surface finish options, and cost factors. Get answers regarding common concerns to aid in decision-making and troubleshooting.
In conclusion, this injection molding processes guide covered the key aspects such as the process itself, quality control, cost considerations, supplier selection, certifications, market trends, helpful tips, and frequently asked questions. By understanding these facets, one can make informed decisions and successfully utilize the injection molding process for various manufacturing needs.
Types of injection molding processes
Injection molding is a widely used manufacturing process for producing plastic parts in large volumes. There are several types of injection molding processes, each with its own advantages and applications.
The most common type of injection molding is conventional injection molding, where resin is melted and injected into a mold cavity under high pressure. This process is ideal for producing complex parts with high precision and consistency.
Another type of injection molding is insert molding, where metal or plastic inserts are placed into the mold before the resin is injected. This process is used to create parts with additional features, such as threaded inserts or electronic components.
Overmolding is a type of injection molding where multiple materials are injected into the same mold to create a single part. This process is commonly used for adding soft-touch grips or colored accents to parts.
Blow molding is a variation of injection molding where air is used to inflate a heated plastic tube or parison in a mold cavity to create hollow parts, such as bottles or containers.
Thermoforming is a type of injection molding where a heated sheet of plastic is stretched over a mold cavity and formed using vacuum pressure. This process is ideal for producing large parts with shallow or complex geometries.
Rotational molding is an injection molding process where resin is poured into a heated mold cavity that rotates on multiple axes to evenly distribute the material and create hollow parts, such as tanks or playground equipment.
In conclusion, injection molding is a versatile manufacturing process that can be adapted to a wide range of applications. By choosing the right type of injection molding process, manufacturers can produce high-quality parts efficiently and cost-effectively.
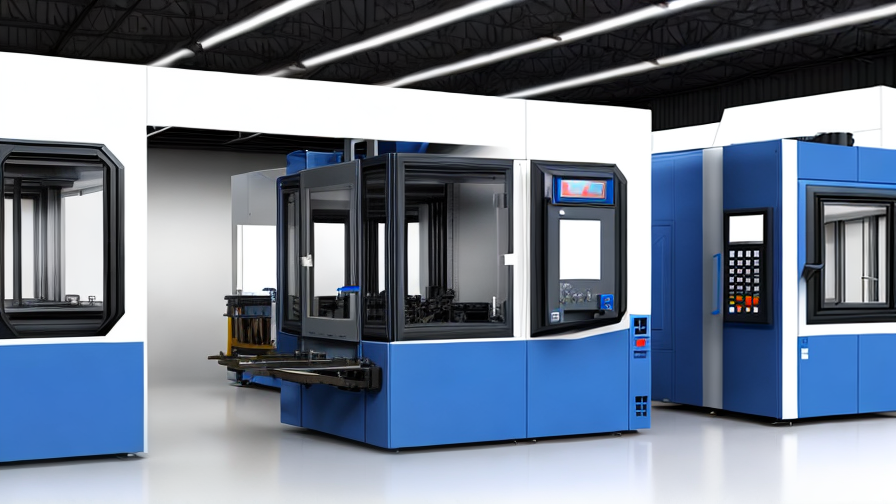
Pros and Cons of Using injection molding processes
Injection molding is a widely used manufacturing process for producing complex and custom plastic parts in large volumes. However, like any other manufacturing technique, it has its own set of pros and cons. Here is a concise analysis of its advantages and disadvantages, within the 300-word limit.
Pros:
1. Cost-effective: Injection molding can be highly cost-effective for larger production runs as it allows for high-volume production with minimal labor costs.
2. High efficiency: The process is highly automated and can achieve high production rates since multiple parts can be produced in a single mold cavity simultaneously.
3. Precision and repeatability: Injection molding offers excellent dimensional accuracy, thereby eliminating the variation seen in manually produced parts. It ensures a consistent quality output.
4. Versatility: Injection molding can produce parts with a wide range of sizes, complexities, and materials, including both thermoplastics and thermosetting plastics, giving manufacturers plenty of options.
5. Wide range of applications: It is suitable for various industries such as automotive, consumer goods, medical, packaging, and more, making it a versatile and widely applicable manufacturing process.
Cons:
1. High initial setup costs: Injection molding requires significant upfront investment in the mold design and development. This can make it cost-prohibitive for small production runs or prototypes.
2. Long lead time: The design, fabrication, and validation of injection molds can take weeks or even months, which may delay the production process.
3. Design constraints: The complexity of injection molds means that there are certain design restrictions, such as draft angles, wall thickness, and undercuts. Design modifications may be required to achieve desired results.
4. Limited flexibility for design changes: Once the mold is created, making design changes can be difficult and expensive since it necessitates modifying or creating a new mold.
5. Environmental impact: The process can generate waste in the form of sprues, runners, and defective parts, requiring proper disposal or recycling.
In summary, injection molding offers cost-effectiveness, efficiency, precision, and versatility, making it a popular choice for mass production. However, high initial costs, long lead times, design restrictions, limited design flexibility, and waste generation pose challenges that need to be considered when opting for this manufacturing process.
injection molding processes Reference Specifications (varies for different product)
Injection molding is a widely used manufacturing process for producing plastic products in large quantities. The process involves injecting molten plastic material into a mold cavity, where it cools and solidifies to form the desired shape. There are various specifications that need to be considered when designing and executing an injection molding process.
Firstly, the material used for injection molding should be selected based on the desired properties of the final product, such as strength, flexibility, heat resistance, and color. Common materials used for injection molding include polyethylene, polypropylene, polystyrene, and ABS.
The design of the mold cavity is also crucial in achieving the desired product shape and dimensions. The mold should be carefully designed to allow for proper flow of the molten plastic material and to prevent defects such as warping, sink marks, and voids. The mold should also be designed for easy ejection of the finished product.
Injection molding machines come in various sizes and configurations, depending on the size and complexity of the product being manufactured. The machine should be properly calibrated and set up to ensure consistent and high-quality production.
The injection molding process involves several steps, including clamping the mold, injecting the plastic material, cooling and solidifying the material, and ejecting the finished product. Each step should be carefully controlled to ensure the quality and consistency of the final product.
In conclusion, injection molding is a versatile and efficient manufacturing process that can produce a wide range of plastic products. By considering the appropriate material, mold design, machine setup, and process control, high-quality products can be produced efficiently and cost-effectively.
Applications of injection molding processes
Injection molding is a widely used manufacturing process that involves injecting molten material, typically plastic, into a mold cavity. This process has various applications across a range of industries due to its ability to produce high-quality and complex parts or products with exceptional precision. Here are some of the key applications of injection molding:
1. Automotive Industry: Injection molding is extensively used in the automotive industry to manufacture a wide range of parts, such as dashboards, bumpers, interior trims, door panels, and even entire body panels. The process enables the production of lightweight, durable, and cost-effective components, making it a preferred choice for automobile manufacturers.
2. Consumer Goods: Injection molding is heavily utilized in the production of numerous consumer goods, including kitchen utensils, toys, electronic casings, and packaging materials. The process allows manufacturers to create intricate designs and patterns, ensuring aesthetic appeal and functionality.
3. Medical Equipment: Injection molding plays a crucial role in the manufacturing of medical devices and equipment. It enables the production of items like syringes, IV components, surgical tools, and diagnostic equipment with exceptional accuracy and sterility. The process ensures high-quality and consistent products, meeting the stringent requirements of the healthcare industry.
4. Electronics: Injection molding is commonly employed in the production of various electronic components, such as connectors, housings for electronic devices, switches, and keypads. The process allows for the integration of intricate designs, precise geometries, and custom functionalities required by the electronics industry.
5. Packaging: Injection molding is widely adopted in the packaging industry for the production of containers, caps, closures, and other packaging components. The process enables the creation of lightweight, durable, and appealing packaging solutions that enhance product protection and visual appeal.
6. Aerospace and Defense: Injection molding is used in the aerospace and defense sectors for manufacturing components that require high strength, heat resistance, and dimensional stability. These include aircraft interior parts, cockpit instruments, missile components, and protective gear.
7. Construction: Injection molding is employed in the construction industry for producing a variety of components including pipes, cable conduits, fittings, and insulation materials. The process enables the manufacturing of durable, weather-resistant, and cost-effective construction products.
In conclusion, injection molding finds applications in a diverse range of industries like automotive, consumer goods, medical equipment, electronics, packaging, aerospace and defense, and construction. Its versatility, precision, and ability to produce complex parts make it an indispensable manufacturing process for a multitude of products used in our daily lives.
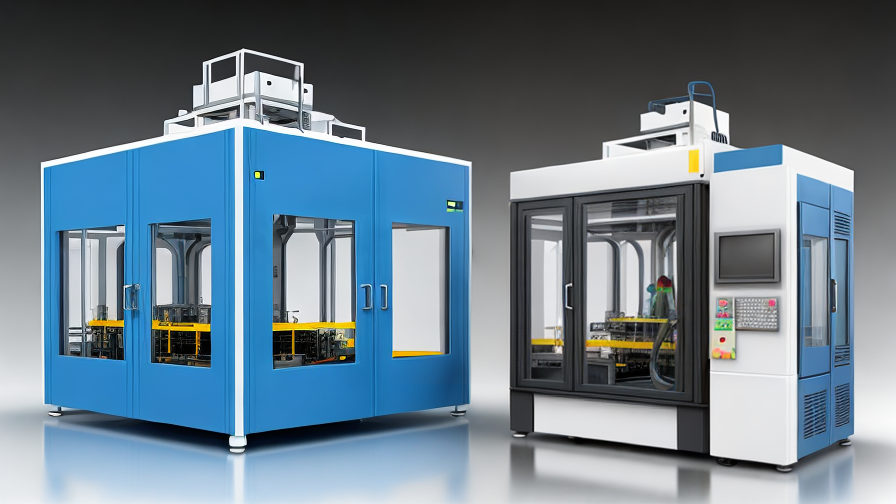
The Work Process and how to use injection molding processes
Injection molding is a manufacturing process used to produce parts and products by injecting molten material, usually plastic, into a mold cavity. This process is widely employed due to its versatility, efficiency, and cost-effectiveness.
The work process of injection molding involves several steps. Firstly, the mold is prepared, which consists of two halves that fit together and form a cavity into which the molten material is injected. The mold is typically made of steel and is precision-machined to produce the desired shape of the final product.
The next step is the preparation of the material. Plastic pellets or granules are fed into a hopper, which then transfers the material to a heated barrel. Inside the barrel, the material is melted by the heat generated from electric heaters and the friction caused by a rotating screw. The molten plastic is then injected into the mold cavity under high pressure.
Once the cavity is filled with the molten material, it is allowed to cool and solidify. This solidification process can be accelerated by cooling the mold with water or by using a special mold material that rapidly dissipates heat. After solidification, the mold is opened, and the part is ejected using ejector pins or plates.
The final step involves post-processing, such as trimming excess material, removing any imperfections, and adding finishing touches like surface textures or logos. These post-processing steps ensure that the final product meets the required specifications and quality standards.
To utilize injection molding effectively, there are certain considerations. Designing the mold and part for manufacturability is crucial. Mold design should optimize the flow of molten material and minimize cooling time, which affects production efficiency. Part design should consider the material’s shrinkage and warpage tendencies and incorporate features like draft angles and proper wall thickness to ensure successful molding.
Additionally, selection of the right material is essential. Properties like melt flow rate, flexibility, and durability should be evaluated based on the intended application of the final product. Material selection affects the process parameters, such as melt temperature and injection pressure.
Lastly, maintaining and operating the injection molding machine and mold properly is vital for consistent and high-quality production. Regular maintenance, calibration, and monitoring of key process variables like temperature and pressure help ensure the process is stable and repeatable.
In summary, injection molding is a versatile manufacturing process that involves preparing the mold, melting the material, injecting it into the mold cavity, allowing it to cool and solidify, and then finishing the part. To use this process effectively, considerations should be given to mold and part design, material selection, and proper machine and mold maintenance.
Quality Testing Methods for injection molding processes and how to control the quality
Quality testing methods for injection molding processes include:
1. Dimensional testing: Measure the dimensions of the molded parts using calipers, gages, and coordinate measuring machines to ensure they meet the specified tolerances.
2. Visual inspection: Examine the surface of the molded parts for defects such as flash, burn marks, sink marks, and bubbles. Use cameras and magnifying tools for detailed inspection.
3. Material testing: Analyze the material properties of the molded parts, such as tensile strength, impact resistance, and thermal stability. This can be done through mechanical testing, thermal analysis, and spectroscopy.
4. Injection molding process monitoring: Monitor key process parameters during injection molding, such as temperature, pressure, fill rate, and cooling time. Use sensors and data acquisition systems to track and analyze process variations.
To control the quality of injection molding processes, follow these steps:
1. Set clear quality standards and specifications for the molded parts, including dimensional tolerances, surface finish requirements, and material properties.
2. Implement a robust quality management system, including standard operating procedures, work instructions, and process controls.
3. Conduct regular training and competency assessments for operators and technicians involved in the injection molding process.
4. Perform regular maintenance and calibration of injection molding machines, molds, and auxiliary equipment to ensure consistent performance.
5. Establish a comprehensive quality control plan with defined inspection points, sampling procedures, and acceptance criteria.
By employing these quality testing methods and implementing effective quality control measures, manufacturers can ensure that injection molded parts meet the desired quality standards and performance requirements.
injection molding processes Sample Policy and Post-Purchase Considerations for injection molding processes from China
Sample Policy:
Our company aims to provide our customers with high-quality injection molding processes from China. To ensure a smooth and efficient purchasing experience, we have established the following policies:
1. Quality Assurance: We understand the importance of product quality. Our experienced team conducts strict quality control inspections throughout the manufacturing process to ensure that all products meet the required standards and specifications.
2. On-Time Delivery: We value your time and strive to deliver your products within the agreed-upon timeframe. Our production team works diligently to meet deadlines and ensure that your order arrives on schedule.
3. Competitive Pricing: We offer competitive pricing for our injection molding processes without compromising on the quality of the final product. We believe in providing value for money and aim to establish long-term partnerships based on mutual trust and benefit.
4. Flexibility: We understand that customer requirements may change over time. Our company is flexible and open to accommodating any modifications or adjustments to your order. We aim to provide a personalized experience, tailored to your specific needs.
Post-Purchase Considerations:
After successfully purchasing injection molding processes from China, it is important to consider the following points:
1. Product Inspection: Upon receiving your order, inspect the products thoroughly to ensure they meet your quality standards. Any discrepancies or issues should be communicated to us immediately, allowing us to address them promptly.
2. Feedback and Communication: Your feedback is essential to us. Please share your experience with us, including any suggestions for improvement. We value open communication and are committed to addressing any concerns or queries you may have.
3. Long-Term Collaboration: If you are satisfied with our products and services, we encourage you to consider a long-term collaboration. Establishing a stable partnership allows us to better understand your requirements and deliver even better results.
4. Continuous Improvement: We constantly strive to improve our injection molding processes. Your feedback plays a crucial role in our ongoing efforts to enhance our production techniques, quality control measures, and overall customer experience.
In summary, our company is dedicated to providing high-quality injection molding processes from China. Our sample policy ensures adherence to strict quality standards, on-time delivery, competitive pricing, and flexibility. We encourage post-purchase considerations such as product inspection, feedback, long-term collaboration, and continuous improvement to foster a mutually beneficial relationship.
Sourcing injection molding processes from China: Opportunities, Risks, and Key Players
China is a leading destination for sourcing injection molding processes due to its competitive pricing, advanced technology, and extensive experience in the manufacturing industry. The country offers a wide range of opportunities for businesses looking to produce high-quality plastic parts at a lower cost.
However, there are also risks associated with sourcing injection molding processes from China. These include quality control issues, intellectual property concerns, communication barriers, and potential delays in production and shipping. It is essential for businesses to conduct thorough research and choose reliable and reputable manufacturers to mitigate these risks.
Some key players in the injection molding industry in China include
– Haitian International Holdings Limited
– Cosmos Machinery Enterprises Limited
– Tederic Machinery Co., Ltd.
– Ningbo HAITAI Industry & Trade Co., Ltd.
– Zhejiang Sound Machinery Manufacture Co., Ltd.
Overall, sourcing injection molding processes from China can be a lucrative opportunity for businesses looking to cut costs and expand their operations. However, it is crucial to consider the risks involved and take necessary precautions to ensure a successful partnership with Chinese manufacturers.
How to find and select reliable injection molding processes manufacturers in China,use google search manufacturers and suppliers
1. Start by utilizing Google search to find a list of injection molding processes manufacturers in China. Use keywords such as “injection molding processes manufacturers China” or “injection molding suppliers China” to narrow down the search.
2. Visit the websites of the manufacturers and suppliers that appear in the search results. Look for information about the company’s history, experience, and the range of services they offer.
3. Check the company’s certifications and qualifications to ensure that they meet the necessary industry standards. Look for certifications such as ISO 9001, ISO 14001, or IATF 16949.
4. Read reviews and testimonials from previous customers to gauge the reliability and quality of the manufacturer’s services. Websites like Alibaba, Made-in-China, and Global Sources can provide valuable insights from other customers.
5. Contact the manufacturers directly to inquire about their manufacturing process, lead times, pricing, and quality control measures. Ask for samples or a factory tour to assess the quality of their products firsthand.
6. Obtain quotes from multiple manufacturers and compare their pricing, lead times, and quality standards. Choose a manufacturer that offers competitive pricing, reliable lead times, and high-quality products.
7. Consider visiting trade shows and exhibitions in China to meet with potential suppliers in person and establish a more personal relationship. This can provide a better understanding of their capabilities and commitment to quality.
By following these steps and conducting thorough research, you can find and select a reliable injection molding processes manufacturer in China that meets your specific requirements and quality standards.
How to check injection molding processes manufacturers website reliable,use google chrome SEOquake check if ranking in top 10M
To check the reliability of an injection molding processes manufacturer’s website, you can follow these steps:
1. Use Google Chrome: Start by opening the website you want to evaluate in the Google Chrome browser. Chrome offers various useful features and extensions for analyzing websites.
2. Install SEOquake: Install the SEOquake extension on your Google Chrome browser. This tool provides a comprehensive SEO analysis of websites, including important ranking factors and metrics.
3. Check the Alexa Rank: With SEOquake enabled, you will generally see a toolbar at the top of your browser with various SEO information. Look for the Alexa Rank, which indicates a website’s traffic rank on a global scale. If the manufacturer’s website has an Alexa Rank within the top 10 million, it implies a decent level of popularity and reliability.
4. Analyze other important SEO metrics: SEOquake provides additional metrics like the number of indexed pages, domain age, backlinks, and social media shares. Investigate these metrics to determine the website’s overall authority and online presence.
5. Evaluate website design and content: Assess the website’s design, user-friendliness, and content quality. A reliable manufacturer typically invests in a professional and informative website that reflects their commitment to providing quality products and services.
6. Look for certifications and industry affiliations: Check if the website mentions any certifications or industry affiliations that demonstrate the manufacturer’s credibility and adherence to quality standards.
7. Browse customer reviews and testimonials: Look for customer reviews and testimonials on the manufacturer’s website or external platforms. Positive feedback and satisfied customer experiences indicate reliability and customer satisfaction.
By following these steps and using SEOquake to analyze the manufacturer’s website, you can get a good idea of their reliability and reputation. Remember to consider multiple factors while evaluating a manufacturer to ensure a comprehensive assessment.
Top 10 injection molding processes manufacturers in China with each 160 words introduce products,then use markdown create table compare
1. Foxconn Technology Group: Foxconn is a leading injection molding process manufacturer in China, offering a wide range of high-quality products. They specialize in precision molding of complex components for various industries such as automotive, electronics, and medical equipment. Their advanced technology and strict quality control ensure precise and durable products.
2. Haier Group: Haier Group provides innovative injection molding solutions for the consumer electronics industry. With their state-of-the-art facilities and expertise, they cater to the global market by producing high-quality plastic components for appliances like refrigerators, air conditioners, and washing machines.
3. Midea Group: Midea specializes in the manufacturing of injection molded products for home appliances and HVAC systems. Their extensive product range includes parts for air conditioners, water heaters, and kitchen appliances. Midea is known for its advanced manufacturing processes and environmentally friendly practices.
4. BYD Auto: BYD Auto is a prominent manufacturer of electric vehicles and supplier of injection molded components in China. They produce high-quality automotive parts like consoles, panels, and dashboards using cutting-edge injection molding techniques.
5. Changhong Group: Known for its expertise in the electronics industry, Changhong Group manufactures a wide range of plastic molded products including TV casings, remote controllers, and home entertainment systems. They pride themselves on delivering products of excellent quality and reliability.
6. Gantrail: Gantrail is a leading manufacturer of injection molded railway components. They provide innovative solutions for the construction and maintenance of railway tracks, including rail clips, rail pads, and rail fastening systems. Gantrail’s products are known for their durability and precision.
7. Gree Electric Appliances: Gree Electric Appliances specializes in injection molding for the air conditioning industry. They produce a wide range of parts such as air conditioner covers, fans, and control panels using high-performance thermoplastics. Gree’s products are known for their efficiency and reliability.
| Manufacturer | Specialization | Key Products |
|————————|—————————–|—————————————————|
| Foxconn Technology Group| Precision molding | Complex components for automotive, electronics, etc.|
| Haier Group | Consumer electronics | Plastic components for appliances |
| Midea Group | Home appliances | Parts for air conditioners, water heaters, etc. |
| BYD Auto | Electric vehicles | Automotive parts like consoles, panels, etc. |
| Changhong Group | Electronics | Plastic molded products for TVs, entertainment systems|
| Gantrail | Railways | Rail clips, rail pads, and rail fastening systems |
| Gree Electric Appliances | Air conditioning | Air conditioner covers, fans, control panels, etc. |
8. Haitian International Holdings: Specializing in injection molding machines, Haitian International Holdings offers a diverse range of machinery for various industries. Their machines are known for their high performance, energy efficiency, and robust construction.
9. ABB Group: ABB Group manufactures plastic molded components for the electrical equipment industry. Their products include switchgear casings, circuit breaker panels, and electrical enclosures. ABB’s injection molded components are known for their reliability and superior insulation properties.
10. Auto Injection Molding: Auto Injection Molding is a leading manufacturer of precision plastic parts and components for the automotive industry. Their products include interior and exterior components such as bumpers, dashboard panels, and door handles. They utilize advanced injection molding technologies to ensure precise and durable products.
| Manufacturer | Specialization | Key Products |
|—————————|———————-|—————————————————-|
| Haitian International Holdings | Injection molding machines | Diverse range of machinery |
| ABB Group | Electrical equipment | Switchgear casings, circuit breaker panels, etc. |
| Auto Injection Molding | Automotive | Precision plastic parts and components for vehicles |
Using markdown, we have created a comparison table above to summarize the key specializations and products offered by the top 10 injection molding process manufacturers in China.
Background Research for injection molding processes manufacturers Companies in China, use qcc.com archive.org importyeti.com
When it comes to injection molding processes, China is considered a major player in the global market, with numerous manufacturers specializing in this field. Some key sources for researching and identifying injection molding companies in China include qcc.com, archive.org, and importyeti.com.
Qcc.com is a Chinese business information platform that provides comprehensive company data, including information about injection molding manufacturers. This platform allows users to search for specific companies, view their business profiles, and access details such as company introduction, registration information, contact details, and certificates.
Archive.org is a digital library that captures snapshots of web pages and websites over time. This platform can be useful for accessing historical information or previous versions of company websites, allowing users to track the evolution of injection molding manufacturers’ online presence and activities.
Importyeti.com is an online directory and database platform that focuses on facilitating international trade, including the import and export of goods. Users can search for specific products or suppliers, allowing them to find injection molding manufacturers in China. Importyeti.com provides company profiles, contact information, export history, and a verification system for suppliers.
By utilizing these platforms, individuals and businesses can conduct thorough research on injection molding manufacturers in China. This research can involve checking the credibility and reputation of companies, assessing their capabilities and expertise, and comparing their product portfolios and pricing. Additionally, it can help identify manufacturers that adhere to industry standards, hold relevant certifications, and have a history of successful partnerships or projects.
In conclusion, qcc.com, archive.org, and importyeti.com are valuable sources for conducting background research on injection molding manufacturers in China. Through these platforms, users can gather crucial information about companies’ profiles, history, capabilities, and credibility, enabling them to make informed decisions when selecting potential manufacturing partners for injection molding processes.
Leveraging Trade Shows and Expos for injection molding processes Sourcing in China
Trade shows and expos are excellent platforms for sourcing injection molding processes in China. These events bring together a wide range of industry professionals, suppliers, and manufacturers, providing a comprehensive overview of the latest technologies, trends, and innovations in the field.
One of the key advantages of attending trade shows and expos is the opportunity to meet face-to-face with potential suppliers and manufacturers. This allows for direct communication, negotiation, and the chance to examine samples and prototypes in person. Additionally, trade shows often feature live demonstrations and workshops, providing valuable insights into the capabilities and quality of various suppliers.
Trade shows and expos also offer a great opportunity to network with other industry professionals and gain a better understanding of the competitive landscape in the injection molding industry. By connecting with other attendees, you can learn about their experiences with different suppliers, gather recommendations, and identify potential partners for collaboration.
Furthermore, trade shows and expos provide a platform for staying up-to-date on industry trends, new technologies, and emerging market opportunities. By attending seminars, panel discussions, and presentations, you can gain valuable insights into the latest developments in injection molding processes, helping you make informed decisions when sourcing suppliers in China.
In conclusion, leveraging trade shows and expos for sourcing injection molding processes in China can be highly beneficial. By taking advantage of the networking opportunities, direct communication with suppliers, and access to industry insights, you can streamline your sourcing process, identify reliable partners, and stay ahead of the competition.
The Role of Agents and Sourcing Companies in Facilitating injection molding processes Purchases from China
Agents and sourcing companies play a crucial role in facilitating injection molding process purchases from China. These intermediaries act as a bridge between buyers and manufacturers, ensuring smooth communication, quality control, and timely delivery of products. Here is how they facilitate the entire process:
1. Supplier Identification: Agents and sourcing companies have extensive networks and connections in China’s manufacturing industry. They can identify reliable and suitable Chinese injection molding manufacturers based on the buyer’s specific requirements, such as desired materials, production capacity, and quality standards.
2. Negotiation and Contracts: These intermediaries help negotiate prices, terms, and conditions with manufacturers on behalf of the buyers. They have in-depth knowledge of local market norms, ensuring favorable contracts for their clients. Agents and sourcing companies also ensure that the necessary legal documentation is in place, protecting the interests of both parties involved.
3. Quality Control: One of the key roles of agents and sourcing companies is to monitor and ensure quality control throughout the production process. They conduct regular visits to the manufacturer’s facility, inspecting materials, molds, and finished products to meet the buyer’s specifications. They can also arrange for third-party quality inspections to provide an unbiased evaluation of the products.
4. Logistic Support: Agents and sourcing companies assist with logistics and shipping arrangements. They have expertise in international freight, customs clearance, and documentation requirements. This ensures that the injection molded products reach the buyer’s location on time and without any hassles.
5. Communication and Language Support: Effective communication is vital for successful collaboration between buyers and manufacturers. Agents and sourcing companies act as interpreters, translating technical specifications, design modifications, and other requirements between the parties involved. This reduces miscommunication and fosters better understanding and problem-solving.
6. Risk Management: Doing business internationally comes with inherent risks such as fraud, poor quality, or delayed deliveries. Agents and sourcing companies mitigate these risks by conducting due diligence on manufacturers, verifying their credentials, and maintaining strong relationships with trusted suppliers.
In conclusion, agents and sourcing companies provide invaluable support in the procurement process of injection molding from China. Their expertise in supplier identification, negotiation, quality control, logistics, communication, and risk management ensures a smooth and successful purchasing experience for buyers, helping them access cost-effective and high-quality injection molded products.
Price Cost Research for injection molding processes manufacturers Companies in China, use temu.com and 1688.com
When looking for injection molding processes manufacturers in China, two potential resources to consider are temu.com and 1688.com. These platforms provide a wide range of options for companies looking for injection molding services in China.
By conducting research on these websites, businesses can compare the prices and costs of different manufacturers to find the best fit for their needs and budget. They can also read reviews and ratings from previous customers to get a better idea of the quality of service provided by each manufacturer.
It is important to note that prices for injection molding processes in China can vary depending on factors such as the complexity of the design, the materials used, and the quantity of parts being produced. By using these websites, companies can easily compare prices and costs to find a manufacturer that meets their specific requirements at a competitive price.
In conclusion, temu.com and 1688.com are valuable resources for companies looking for injection molding processes manufacturers in China. By conducting thorough research on these platforms, businesses can find a reliable and affordable manufacturer to meet their injection molding needs.
Shipping Cost for injection molding processes import from China
Shipping costs for importing injection molding processes from China can vary depending on several factors. These factors include the size and weight of the shipment, the shipping method chosen, and the destination country.
There are generally two main methods for shipping goods from China: air freight and sea freight. Air freight is typically faster but more expensive, while sea freight is slower but more cost-effective for larger shipments.
For smaller shipments or urgent orders, air freight is often preferred. The shipping cost for air freight is calculated based on the weight or volumetric weight of the shipment, whichever is higher. Volumetric weight calculation takes into account both the weight and dimensions of the package. Air freight rates from China to other countries can range from $3 to $15 per kilogram, depending on the carrier and destination.
On the other hand, sea freight is the preferred option for large-volume shipments. The shipping cost for sea freight is typically calculated based on the volume or weight of the cargo, known as a freight ton. Sea freight rates from China to other countries can range from $200 to $2000 per freight ton, depending on factors such as the destination, shipping line, and type of container used.
In addition to the shipping cost, importers should also consider other charges such as customs duties, import taxes, and destination handling fees. These charges vary depending on the regulations and policies of the destination country.
To reduce shipping costs, importers can consider consolidating their orders to maximize container space utilization, choosing a more economical shipping route, or negotiating with the freight forwarder for better rates.
It’s important to note that the shipping costs mentioned here are estimates and can vary significantly based on the specific requirements of each shipment. Therefore, it is recommended to consult with a reputable freight forwarder or shipping agent to get accurate and up-to-date shipping cost information for your specific scenario.
Compare China and Other injection molding processes Markets: Products Quality and Price,Visible and Hidden Costs
China is widely known as one of the largest global players in the injection molding industry. Its market is characterized by a wide range of products, high competition, and relatively low prices. Comparing China’s injection molding market with other markets, such as those in Europe or the United States, reveals differences in product quality, pricing, and both visible and hidden costs.
In terms of product quality, China’s injection molding market has made significant improvements over the years. Many Chinese manufacturers have implemented advanced technologies, quality control processes, and are ISO certified, ensuring that their products meet international standards. However, it is worth noting that the quality consistency and precision may not match the level achieved by some Western countries’ manufacturers. Western markets, particularly Europe and the United States, have long-standing reputations for stringent quality control and precision engineering, resulting in highly reliable and durable products.
When it comes to pricing, China’s injection molding market holds a competitive advantage due to its lower labor and manufacturing costs. This cost advantage allows Chinese manufacturers to offer products at a more affordable price compared to their Western counterparts. However, lower pricing does not necessarily guarantee poor quality. Chinese manufacturers’ ability to achieve economies of scale and a vast supplier network contribute to cost-efficiency, allowing them to offer competitive prices without compromising on product quality.
Visible costs, such as labor, materials, and manufacturing expenses, play a crucial role in determining the overall cost of injection molded products. China’s lower labor costs contribute significantly to lowering the visible costs, making their products more price-competitive. However, there are also hidden costs associated with the Chinese market. Importing products from China may entail additional costs such as shipping fees, customs duties, and time required for transportation. It is important to consider these hidden costs when comparing the overall costs of sourcing from China versus other markets.
In conclusion, China’s injection molding market offers a wide range of products and has improved its product quality over the years. Its competitive advantage lies in lower pricing due to lower labor and manufacturing costs. While Chinese manufacturers have been able to match international quality standards, Western markets still hold a reputation for higher precision and reliability. Additionally, it is crucial to consider not only the visible costs but also the hidden costs associated with sourcing products from China. Overall, the choice of market ultimately depends on the specific requirements, budget, and preferences of the buyer.
Understanding Pricing and Payment Terms for injection molding processes: A Comparative Guide to Get the Best Deal
When it comes to pricing and payment terms for injection molding processes, it is essential to understand the various factors that can influence the overall cost and ensure you are getting the best deal possible.
First and foremost, it is crucial to consider the complexity of the part being molded. More complex parts with intricate designs or features will generally require more time and resources to produce, leading to a higher overall cost. Additionally, the material being used can also impact the pricing, with some materials being more expensive than others.
It is also important to carefully review the pricing structure offered by different injection molding providers. Some companies may charge a flat fee for the entire project, while others may charge based on the number of parts produced or the complexity of the design. Understanding these pricing models can help you compare quotes and determine which provider offers the best value for your specific needs.
In terms of payment terms, it is common for injection molding providers to require a deposit upfront before work can begin. This deposit can vary depending on the size and scope of the project, so it is important to clarify these terms before signing any contracts. Additionally, it is essential to establish a timeline for payments throughout the project to ensure smooth and timely payment procedures.
By understanding these key factors and comparing quotes from different injection molding providers, you can ensure you are getting the best deal and the highest quality results for your injection molding project.
Chinese Regulations and Industry Standards Certifications for injection molding processes,Import Regulations and Customs for injection molding processes from China
China is known as a prominent hub for manufacturing and exporting various products, including injection molding processes. However, the Chinese government has implemented certain regulations and industry standards certifications for these processes to ensure quality control and safety measures. Additionally, there are import regulations and customs that need to be considered when importing injection molding processes from China.
One of the key regulations in China for injection molding processes is the China Compulsory Certification (CCC) system. This certification is mandatory for certain products and aims to safeguard the quality and safety of these products. Manufacturers must comply with CCC requirements and obtain the certification before exporting their products, including injection molding processes.
In addition to the CCC certification, there are also industry-specific standards that companies must adhere to. For injection molding processes, the most commonly followed standards are the ISO 9001 Quality Management System and ISO 14001 Environmental Management System. These standards ensure that the manufacturing processes meet international quality and environmental standards.
When importing injection molding processes from China, it is essential to comply with import regulations and customs. Importers must provide necessary documentation, such as commercial invoices, packing lists, and bills of lading, to clear customs. Additionally, the import of certain products may require specific licenses or permits from regulatory authorities.
Importers should also be aware of customs duties and taxes levied on importing injection molding processes from China. These charges vary depending on the product classification and its declared value. It is advisable to work with a customs broker or freight forwarder to navigate through the customs clearance process smoothly and ensure compliance with import regulations.
In summary, injection molding processes exported from China must comply with Chinese regulations and industry standards certifications, such as CCC, ISO 9001, and ISO 14001. Importers should be familiar with import regulations and customs procedures to smoothly import these processes and comply with necessary documentation, licenses, and duties.
Sustainability and Environmental Considerations in injection molding processes Manufacturing
Injection molding is a popular manufacturing process known for its efficiency and high production volumes. However, sustainability and environmental considerations are crucial factors that should be incorporated into injection molding processes to reduce their impact on the environment.
One key consideration is the choice of materials used in the injection molding process. Using sustainable and eco-friendly materials, such as biodegradable plastics or recycled materials, can significantly reduce the carbon footprint associated with production. These materials can be sourced from renewable resources, reducing the dependency on fossil fuels and minimizing energy consumption during production.
Another aspect to consider is energy efficiency. Injection molding machines require significant amounts of energy to operate, mainly in the form of electricity. Implementing energy-saving measures, such as using servo motors and optimizing the heating and cooling processes, can help reduce energy consumption. Additionally, incorporating energy-efficient technologies like LED lighting and high-efficiency motors in the manufacturing facility can further minimize the environmental impact.
Waste management is also a vital aspect of sustainability in injection molding processes. Implementing a robust recycling program within the manufacturing facility can ensure that plastic waste generated during the process is properly sorted and recycled. Additionally, reducing scrap rates by optimizing process parameters and utilizing advanced molds with minimal waste can further minimize waste generation. Proper disposal of any hazardous byproducts or chemicals used in the process is essential to prevent environmental pollution.
Furthermore, water conservation is an important consideration. Injection molding processes require water for cooling and maintaining temperature control. Implementing water-recycling systems and optimizing the cooling process can reduce water consumption and the potential for water pollution from chemical additives.
Lastly, the transportation of goods should also be evaluated for sustainability. By optimizing shipping routes, using more efficient transportation methods, and minimizing packaging waste, the overall environmental impact of the injection molding process can be reduced.
In conclusion, incorporating sustainability and environmental considerations into injection molding processes is essential to minimize the environmental impact of manufacturing. By choosing sustainable materials, optimizing energy efficiency, managing waste effectively, conserving water, and evaluating transportation methods, injection molding can become a more environmentally friendly manufacturing process.
List The Evolution history of “injection molding processes”
Injection molding processes have evolved significantly since its invention in the 19th century. Originally developed as a method to produce celluloid products, injection molding was later used to manufacture plastic buttons and combs. In the 1950s, the process saw a major breakthrough with the introduction of the first screw injection molding machine, improving efficiency and accuracy.
Throughout the 20th century, advancements in materials science and technology led to the development of new resins, allowing for more complex and durable products to be produced through injection molding. The introduction of computer-aided design (CAD) and computer-aided manufacturing (CAM) further revolutionized the process, making it faster, more precise, and cost-effective.
In recent years, the adoption of additive manufacturing technologies, such as 3D printing, has further expanded the capabilities of injection molding processes. These technologies have enabled the production of custom and complex geometries, as well as the use of sustainable materials in injection molding.
Furthermore, the industry has seen the integration of automation and robotics, leading to increased production speeds, reduced labor costs, and improved quality control in injection molding processes. Advancements such as real-time monitoring and predictive maintenance have also enhanced the efficiency and reliability of injection molding operations.
Overall, the evolution of injection molding processes has been marked by a constant drive towards innovation and optimization, making it a versatile and indispensable manufacturing technique in various industries today.
The Evolution and Market Trends in injection molding processes Industry
Injection molding processes have evolved significantly over the years, with advancements in technology and materials leading to improved efficiency and quality. The introduction of computer-aided design (CAD) and computer-aided manufacturing (CAM) software has allowed for more precise and complex designs to be produced with high accuracy.
Market trends in the injection molding industry include a shift towards the use of sustainable and bio-based materials, as well as the integration of automation and robotics to streamline production processes. Additionally, the demand for lightweight and durable products in industries such as automotive, electronics, and medical devices has driven the adoption of advanced materials and technologies in injection molding.
Another key trend in the injection molding industry is the increasing focus on customization and personalization, with manufacturers offering bespoke solutions to cater to the unique needs of individual customers. This trend is driven by the growing demand for personalized products in various sectors, such as consumer goods and healthcare.
Overall, the injection molding industry is experiencing rapid growth and innovation, driven by technological advancements and changing market demands. Manufacturers are constantly seeking ways to improve efficiency, quality, and sustainability in their processes, while also meeting the evolving needs of customers in a competitive global market.
Custom Private Labeling and Branding Opportunities with Chinese injection molding processes Manufacturers
Chinese injection molding processes manufacturers offer custom private labeling and branding opportunities for businesses looking to create their own unique products. With advanced technology and expertise in producing high-quality plastic products, these manufacturers can help businesses develop custom molds and produce products that meet their specifications.
Through private labeling, businesses can have their logo, brand name, and other branding elements printed or embossed on the products, creating a unique and professional look. This allows businesses to promote their brand and stand out in the market, increasing brand recognition and customer loyalty.
Additionally, Chinese manufacturers can provide packaging services, allowing businesses to have their products packaged in custom branded packaging, further enhancing their brand image and marketing efforts.
With competitive pricing and fast turnaround times, Chinese injection molding processes manufacturers offer cost-effective solutions for businesses looking to create custom products. By partnering with these manufacturers, businesses can access a wide range of customization options and produce high-quality products that meet their specific needs.
Overall, private labeling and branding opportunities with Chinese injection molding processes manufacturers provide businesses with a unique way to differentiate their products in the market and build a strong brand presence.
Tips for Procurement and Considerations when Purchasing injection molding processes
When purchasing injection molding processes, there are several key considerations that should be taken into account to ensure that you are getting the best value for your investment. Here are some tips to keep in mind:
1. Define your requirements: Before you start the procurement process, clearly define your requirements in terms of the type of parts you need to produce, the quantity, the quality standards, and any specific materials or finishes that are required.
2. Research suppliers: Look for reputable suppliers with a track record of providing high quality injection molding processes. Check online reviews and ask for references from past clients to ensure that the supplier has a good reputation.
3. Consider cost: While cost is an important factor, it should not be the only consideration when purchasing injection molding processes. Look for suppliers who offer a competitive price while also providing high quality products and services.
4. Quality standards: Make sure that the supplier you choose adheres to industry quality standards and has relevant certifications to demonstrate their commitment to quality.
5. Technology and capabilities: Consider the supplier’s technology and capabilities in terms of the type of molding processes they offer, the range of materials they can work with, and their ability to deliver complex or customized parts.
6. Communication and customer service: Choose a supplier who is responsive to your inquiries, communicates effectively, and provides excellent customer service. This will help to ensure a smooth procurement process and ongoing support after the purchase.
By keeping these tips in mind and conducting thorough research before making a decision, you can ensure that you are getting the best injection molding processes for your specific requirements.
FAQs on Sourcing and Manufacturing injection molding processes in China
Q: What is injection molding?
A: Injection molding is a manufacturing process used to produce parts in large quantities by injecting molten material into a mold.
Q: What are the advantages of sourcing and manufacturing injection molding in China?
A: There are several advantages to sourcing and manufacturing injection molding in China. Firstly, China has a well-established supply chain and a vast number of experienced manufacturers. This means that finding suitable suppliers and manufacturers for your specific needs is generally easier and more cost-effective. Additionally, manufacturing costs in China are usually lower compared to other countries, making it an attractive option for businesses seeking cost savings. China also offers a wide range of material options and can handle various part sizes and complexities.
Q: What are the challenges of sourcing and manufacturing injection molding in China?
A: One of the main challenges of sourcing and manufacturing injection molding in China is the language and cultural barrier. Communication with suppliers and manufacturers may require extra effort and attention to avoid misunderstandings and ensure quality control. It is crucial to find reliable partners who can effectively bridge this gap. Additionally, there can be longer lead times due to shipping distances, especially if your business is located in a different region. Quality control can be another concern, as not all manufacturers in China may meet the required standards. Extensive supplier research and due diligence must be undertaken to ensure product quality and reliability.
Q: How can I find suitable manufacturers for injection molding in China?
A: To find suitable manufacturers for injection molding in China, you can utilize various sourcing methods. Online platforms, such as Alibaba or Global Sources, provide access to a wide range of manufacturers and suppliers. Industry trade shows and exhibitions also offer opportunities to connect with potential partners. It is crucial to conduct thorough background checks, request samples, and visit facilities if possible before finalizing any partnerships. Working with a sourcing agent or a manufacturing consultant familiar with the Chinese market can also simplify the process and provide valuable insights.
Q: What should I consider when sourcing and manufacturing injection molding in China?
A: Several factors should be considered, including the supplier’s reputation, production capabilities, quality control measures, pricing, and communication abilities. It is essential to have clear production specifications and quality requirements documented in a detailed agreement. Intellectual property protection should also be addressed through non-disclosure agreements (NDAs) and other legal measures.
In conclusion, sourcing and manufacturing injection molding in China can offer significant advantages in terms of cost savings, access to a vast supplier network, and manufacturing capabilities. However, challenges such as language barriers, quality control, and longer lead times must be carefully managed to ensure a successful partnership.
Why contact sourcifychina.com get free quota from reliable injection molding processes suppliers?
Sourcifychina.com offers free quotas from reliable injection molding processes suppliers for several reasons. Firstly, it allows customers to evaluate and compare different suppliers before making a final decision. By receiving multiple quotes, clients can ensure they are receiving competitive pricing and find the best partner for their project.
Secondly, offering free quotas from reliable suppliers assists customers in saving time and effort. Instead of individually reaching out to multiple suppliers and negotiating pricing, Sourcifychina.com streamlines the process by providing access to various suppliers through a single platform. This helps to expedite the sourcing process and allows clients to focus on other aspects of their project.
Another benefit of receiving free quotas is the ability to gauge the capabilities and expertise of different suppliers. Each supplier may have unique specialties or strengths in certain areas. By collecting quotes from various sources, customers can gain insight into which suppliers have the necessary skills and experience to meet their specific requirements.
Furthermore, the free quotas from reliable suppliers ensure transparency and trust in the sourcing process. Sourcifychina.com carefully selects and vets suppliers to ensure they meet the necessary quality standards. This helps to minimize the risk of partnering with unreliable or subpar suppliers, providing customers with peace of mind.
In conclusion, by offering free quotas from reliable injection molding processes suppliers, Sourcifychina.com facilitates the sourcing process for customers. It allows for evaluation and comparison of different suppliers, saves time and effort, provides insights into supplier capabilities, and ensures transparency and trust in the sourcing process.