Introduce about cnc metal mill guide,Qulity,Cost,Supplier,Certification,Market,Tips,FAQ
A CNC metal mill guide is a comprehensive manual that provides detailed information and instructions on operating a CNC (Computer Numerical Control) metal milling machine. It covers various aspects such as setup, programming, operation, safety precautions, troubleshooting, and maintenance.
The quality of a CNC metal mill guide is crucial as it directly affects the user’s ability to effectively operate the machine. A high-quality guide will be well-structured, easy to understand, and provide clear illustrations and examples. It should also cover a wide range of topics to cater to both beginners and experienced users.
Cost is an important factor to consider when purchasing a CNC metal mill guide. It should provide good value for money, offering high-quality content at a reasonable price. There are various options available, including free online guides and paid guides that may come with additional resources or support.
When selecting a supplier for a CNC metal mill guide, it is important to choose a reputable and trusted source. Look for suppliers with a proven track record in providing reliable and accurate information. Online reviews and recommendations from other users can be helpful in making the right choice.
Certification is another aspect to consider. A certified CNC metal mill guide ensures that the content has been reviewed and approved by industry experts. This provides added assurance of its accuracy and reliability.
The market for CNC metal mill guides is diverse, catering to different levels of users and specific machine types. Various suppliers offer guides tailored to specific machines or industry applications. Depending on your requirements, you can choose a guide that best fits your needs.
Here are some tips to consider when using a CNC metal mill guide:
1. Read the guide thoroughly before operating the machine.
2. Follow the instructions and safety precautions provided to avoid accidents or damage to the machine.
3. Keep the guide handy for reference during setup, programming, and troubleshooting.
4. Regularly update your knowledge and skills by referring to supplementary resources or attending training courses.
FAQ sections in a CNC metal mill guide often provide answers to commonly asked questions. These questions may include topics like machine setup, tooling selection, troubleshooting common issues, and recommended maintenance practices.
In conclusion, a high-quality CNC metal mill guide is an essential tool for anyone operating a CNC metal milling machine. It provides detailed instructions, tips, and troubleshooting advice to ensure safe and efficient operation. When selecting a guide, consider factors such as quality, cost, supplier reputation, certification, and the specific needs of your machine and industry.
Types of cnc metal mill
There are several types of CNC metal mills that are commonly used in the manufacturing industry. These machines are capable of shaping and machining metal materials with high precision and accuracy. The different types of CNC metal mills can be categorized based on their size, configuration, and specific applications.
1. Vertical CNC Milling Machine: This is the most common type of CNC metal mill, where the spindle axis is vertically oriented. Vertical mills are often used for applications that require milling in a vertical direction, such as drilling or plunge cutting.
2. Horizontal CNC Milling Machine: In contrast to vertical mills, horizontal CNC milling machines have a horizontally oriented spindle axis. These machines are suitable for machining larger workpieces and are often used in industries such as automotive and aerospace.
3. Bed Milling Machine: In bed milling machines, the worktable moves longitudinally along the length of the bed, allowing for the machining of large workpieces. Bed mills are known for their stability and rigidity, making them suitable for heavy-duty applications.
4. Knee Milling Machine: Knee mills are similar to bed mills but have a vertically adjustable knee that allows for greater flexibility in machining operations. These machines are often used for prototyping, small-scale production, and maintenance shops.
5. Turret Milling Machine: Turret mills have a stationary spindle and a worktable that can be moved in multiple directions. They are equipped with a rotating turret that holds multiple cutting tools, enabling faster tool changes and increased productivity.
6. Gantry Milling Machine: Gantry mills are designed for heavy-duty machining of large workpieces, as they have a bridge-like structure that spans the workpiece. These machines are commonly used in the aerospace and marine industries.
7. CNC Swiss Type Lathe: Although technically not a milling machine, a CNC Swiss type lathe is commonly used for metal machining operations. It is designed for high-precision and high-volume production of small, complex parts.
These are just a few examples of CNC metal mills available in the market. Each type has its own advantages and specific applications, and the choice depends on various factors such as the size and complexity of the workpiece, desired accuracy, and production requirements.
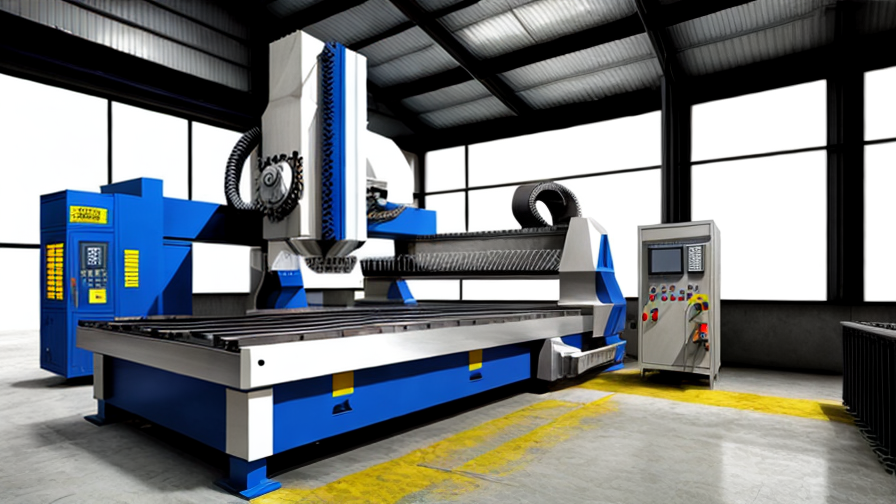
Pros and Cons of Using cnc metal mill
CNC metal mills, also known as CNC machining centers, are widely used in industrial manufacturing processes to shape and carve metal components with precise accuracy. Like any technology, CNC metal mills have their pros and cons. Here are some key points to consider:
Pros:
1. Precision: CNC metal mills can produce highly accurate and repeatable results, ensuring that the finished products meet the required specifications consistently. This level of precision is difficult to achieve with manual machining methods.
2. Efficiency: CNC metal mills can perform various machining operations, such as drilling, milling, turning, and grinding, in a single setup. This reduces the time and effort required for multiple setups and tool changes, resulting in improved productivity.
3. Automation: CNC metal mills are fully automated machines that can run continuously and perform complex operations without human intervention. This allows manufacturers to achieve higher production rates, streamline workflows, and reduce labor costs.
4. Flexibility: With CNC programming, manufacturers can easily switch between different product designs and make modifications on the fly. This flexibility enables the production of customized and specialized components, catering to a wide range of customer requirements.
Cons:
1. Initial Investment: CNC metal mills are relatively expensive to purchase and set up, requiring significant upfront investment. The cost includes not only the machine but also the necessary software, tooling, and training for operators.
2. Maintenance and Repair: Like any mechanical system, CNC metal mills require regular maintenance to keep them operating at optimal performance. Failure to perform proper maintenance can lead to breakdowns and costly repairs, as well as downtime in production.
3. Skill and Training: Operating CNC metal mills requires specialized skills and knowledge in programming, machining techniques, and tool selection. This means that operators need to undergo extensive training, which can be time-consuming and costly for manufacturers.
4. Limited Versatility: While CNC metal mills are highly capable machines, they are best suited for high-volume production of similar components. Machining complex shapes or small-scale production runs may be less efficient or require additional setup and programming time.
In conclusion, CNC metal mills offer numerous advantages in terms of precision, efficiency, automation, and flexibility. However, the initial investment, maintenance requirements, training needs, and limited versatility should be carefully considered before implementing this technology in a manufacturing setting.
cnc metal mill Reference Specifications (varies for different product)
CNC metal mills, also known as computer numerical control metal mills, are versatile machining tools used in various industries for milling and shaping metal workpieces. These machines provide high precision and efficiency, allowing manufacturers to produce complex and intricate parts with tight tolerances. While the specific specifications can vary depending on the product being manufactured, there are some general reference specifications commonly associated with CNC metal mills.
One of the key specifications is the maximum workpiece size that the machine can accommodate. This measurement determines the size of the metal parts that can be processed in the mill. CNC metal mills are available in various sizes, ranging from small mills for micro-components to large mills for industrial-scale production.
Another important specification is the spindle speed or the rotational speed of the tool. Typically measured in rotations per minute (RPM), the spindle speed determines the cutting speed and feed rate. Higher spindle speeds are suitable for softer materials that require high-speed machining, while lower speeds are preferred for harder metals that require more cutting force.
The precision and accuracy of CNC metal mills are determined by their positioning and repeatability specifications. Positioning accuracy refers to the ability of the machine to place the tool at the desired position, while repeatability refers to the machine’s ability to consistently return to the same position. These specifications are usually given in microns or thousandths of an inch, indicating the level of precision achievable by the machine.
CNC metal mills also come with various control options, including the number of axes. Common configurations include 3-axis, 4-axis, and 5-axis mills. The number of axes determines the range of motion and the complexity of parts that can be manufactured. More axes allow for simultaneous movement in multiple directions, enabling the production of intricate parts with curved surfaces.
Other specifications to consider include the maximum spindle torque, the tool holder type (such as CAT or BT), the maximum tool diameter, and the maximum tool length. These specifications vary depending on the machine model and are selected based on the specific machining requirements.
In conclusion, CNC metal mills offer a wide range of specifications depending on the desired application. Manufacturers should consider the workpiece size, spindle speed, precision, control options, and other factors when selecting a CNC metal mill to ensure optimal performance and efficiency in their machining operations.
Applications of cnc metal mill
CNC metal mills are versatile machines that are widely used in various industries for manufacturing various metal components. Some common applications of CNC metal mills include:
1. Precision machining: CNC metal mills are used for precise milling, drilling, and cutting of metal components with high accuracy and repeatability. This makes them ideal for producing complex shapes and intricate parts for industries such as aerospace, automotive, and electronics.
2. Prototyping: CNC metal mills are commonly used for prototyping new metal parts or products. They allow engineers and designers to quickly iterate and test different designs before moving into full production, saving time and resources.
3. Custom fabrication: CNC metal mills are used for custom fabrication of metal components for a wide range of applications. Whether it’s a one-off piece or a small batch production, CNC metal mills can efficiently produce custom parts to meet specific requirements.
4. Tool and die making: CNC metal mills are often used in the manufacturing of tooling and dies for stamping, forging, and molding processes. They enable precise machining of metal components, ensuring accurate and consistent results.
5. Mold making: CNC metal mills are used in the production of molds for casting and injection molding processes. They can create complex mold cavities with high precision, allowing for the production of high-quality molds for various applications.
Overall, CNC metal mills are essential tools in modern manufacturing processes, offering precision, efficiency, and versatility for a wide range of metal machining applications. Their ability to produce high-quality components in a cost-effective manner makes them valuable assets in industries such as aerospace, automotive, electronics, and more.
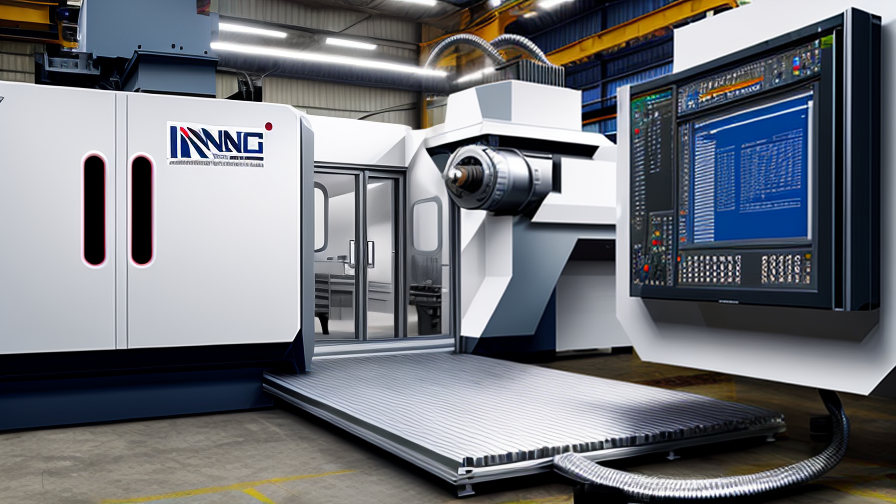
The Work Process and how to use cnc metal mill
A CNC metal mill is a computer-controlled machine that is used to cut and shape metal workpieces. The process of using a CNC metal mill involves several steps:
1. Designing: The first step in using a CNC metal mill is to create a design for the workpiece using computer-aided design (CAD) software. This design will specify the dimensions and shape of the final product.
2. Programming: Once the design is complete, the next step is to program the CNC machine with the necessary instructions to create the workpiece. This involves specifying the cutting tools, cutting speeds, and cutting paths.
3. Setting up: Before the CNC metal mill can be used, the workpiece must be securely attached to the machine’s worktable. The cutting tools must also be properly installed and aligned.
4. Testing: Once everything is set up, the CNC machine can be tested to ensure that the program is functioning correctly. This may involve running a test cut on a scrap piece of metal to verify the accuracy of the program.
5. Cutting: With everything in place, the CNC metal mill can now be used to cut and shape the workpiece according to the programmed instructions. The machine will move the cutting tools along the specified paths to remove material and create the final product.
6. Finishing: After the cutting process is complete, the workpiece may require additional finishing processes such as deburring or polishing to achieve the desired surface finish.
In conclusion, using a CNC metal mill involves designing the workpiece, programming the machine, setting up the workpiece and machine, testing the program, cutting the workpiece, and finishing the final product. It is important to follow these steps carefully to ensure accurate and efficient production of metal components.
Quality Testing Methods for cnc metal mill and how to control the quality
Quality testing methods for CNC metal mills involve several steps to ensure the accuracy and precision of the machined parts. These methods include:
1. Visual Inspection: This involves visually examining the machined parts for any visible defects, such as scratches, burrs, or surface irregularities. Operators or quality inspectors check for any deviations from the specified dimensions and make necessary adjustments.
2. Dimensional Inspection: Dimensional inspection involves using precision instruments like calipers, micrometers, and coordinate measuring machines (CMM) to measure and verify the dimensional accuracy of the machined parts. The measurements are compared against the design specifications to ensure that the parts meet the required tolerances.
3. Surface Finish Analysis: For CNC metal mills, it is crucial to maintain the desired surface finish. Surface roughness testers or profilometers are used to measure the smoothness of the machined surfaces. The measurements are compared against specified surface finish parameters to ensure compliance.
4. Functional Testing: In some cases, functional testing is performed on CNC machined parts to ensure that they meet the required performance criteria. This may involve testing the assembled components to check their fit, movement, or mating with other parts.
To control the quality of CNC metal mills, it is essential to implement proper processes and procedures. Here are some key steps:
1. Process Documentation: Documenting all the processes and parameters used during machining operations is necessary to have a standardized approach to quality control. This includes recording machine settings, tooling details, machining parameters, and any deviations from the standard process.
2. Regular Maintenance: Routine maintenance and calibration of CNC metal mills are crucial to ensure their proper functioning and accuracy. Regular checks on machine conditions, tooling, and lubrication systems should be carried out to prevent any issues that may affect quality.
3. Operator Training: Conducting comprehensive training programs for operators helps in developing their skills and knowledge related to machine setup, programming, and quality control techniques. This ensures that the operators can detect any deviations from the specified quality parameters and take necessary actions.
4. Statistical Process Control (SPC): Monitoring and analyzing process variation through SPC techniques can help control quality. Collecting and analyzing data from production runs enables identifying trends, detecting potential issues, and making proactive improvements to maintain quality standards.
By adopting these quality testing methods and implementing effective quality control measures, the CNC metal mill can consistently produce high-quality machined parts while reducing the risk of defects and deviations.
cnc metal mill Sample Policy and Post-Purchase Considerations for cnc metal mill from China
Sample Policy:
1. Minimum Order Quantity: Our minimum order quantity for cnc metal mill is 1 set.
2. Sample Availability: Samples can be provided upon request. Sample cost and shipping fees will be borne by the customer.
3. Payment Terms: We accept payment through T/T, L/C, and Western Union. Payment terms will be discussed and agreed upon before order confirmation.
4. Shipping: We can arrange shipping for your cnc metal mill order. Shipping costs will be determined based on the destination and shipping method.
5. Warranty: We offer a 12-month warranty for all our cnc metal mills. Any defects or issues arising during this period will be repaired or replaced free of charge.
Post-Purchase Considerations:
1. Installation and Training: We can provide installation and training services for your cnc metal mill. Our technicians will guide you on how to set up and operate the machine effectively.
2. Technical Support: Our team of technical experts is available to provide support and assistance with any issues or questions you may have regarding your cnc metal mill.
3. Maintenance: Regular maintenance is essential to ensure the optimal performance and longevity of your cnc metal mill. We can provide guidance on maintenance procedures and schedules.
4. Spare Parts: We stock a range of spare parts for our cnc metal mills. In case of any part replacements or repairs, we can supply the necessary components promptly.
5. Feedback and Reviews: Your feedback is valuable to us. We appreciate reviews and suggestions on how we can improve our product and service to better meet your needs.
Sourcing cnc metal mill from China: Opportunities, Risks, and Key Players
China is considered one of the leading global players in the manufacturing industry and has emerged as a major source for CNC metal mills. There are several opportunities, risks, and key players associated with sourcing CNC metal mills from China.
Opportunities:
1. Cost Advantage: China offers a significant cost advantage due to lower labor and manufacturing costs. This makes CNC metal mills sourced from China highly competitive in terms of pricing.
2. Wide Range of Suppliers: There is a wide range of suppliers in China providing CNC metal mills with various specifications and capabilities, giving buyers a wide selection to choose from.
3. Technology and Innovation: China has made significant advancements in CNC technology and machinery, offering more advanced and efficient CNC metal mills compared to other regions.
4. Manufacturing Capacity: China has a high manufacturing capacity, enabling fast production and delivery times for CNC metal mills, especially when compared to other countries.
Risks:
1. Quality Control: One of the major risks when sourcing CNC metal mills from China is the issue of quality control. Some suppliers may compromise on quality to reduce costs, leading to potential performance and reliability issues.
2. Intellectual Property Protection: China has faced criticism for intellectual property rights violations. Companies must ensure that their designs, patents, and proprietary technology are adequately protected when sourcing CNC metal mills from Chinese suppliers.
3. Communication and Language Barrier: Language barriers and potential miscommunication can pose challenges when interacting with Chinese suppliers. Clear communication and specifications are crucial to ensure the desired product is received.
4. Supply Chain Disruptions: The global supply chain is vulnerable to disruptions, such as political instability, natural disasters, and trade conflicts. These disruptions can affect the timely delivery of CNC metal mills sourced from China.
Key Players:
1. Fanuc Corporation: A Japanese company with manufacturing operations in China, known for its high-quality CNC metal mills.
2. DMG Mori: A German-Japanese joint venture that operates production facilities in China, offering advanced CNC metal mills.
3. Haas Automation: An American company with manufacturing facilities in China, providing a range of CNC metal mills for various applications.
4. Shenyang Machine Tool Corporation: A major Chinese player in the CNC metal mill industry, offering a wide range of machines.
In conclusion, sourcing CNC metal mills from China provides several opportunities such as cost advantages, a wide range of suppliers, and advanced technology. However, it also involves risks related to quality control, intellectual property protection, communication barriers, and supply chain disruptions. Key players in this industry include companies like Fanuc Corporation, DMG Mori, Haas Automation, and Shenyang Machine Tool Corporation.
How to find and select reliable cnc metal mill manufacturers in China,use google search manufacturers and suppliers
When searching for reliable CNC metal mill manufacturers in China, using Google search is a great starting point. Here’s a simple guide on how to find and select the right manufacturer while keeping the description within 300 words.
1. Start by searching relevant keywords on Google, such as “CNC metal mill manufacturers in China” or “CNC machining suppliers in China.”
2. Analyze the search results and visit the websites of manufacturers that appear on the first few pages. Look for companies with professional websites, informative product descriptions, and a credible online presence.
3. Pay attention to the manufacturer’s experience and specialization. Look for companies that have been in the industry for several years and have a solid track record of producing CNC metal mills. It’s best to choose manufacturers specializing in CNC metal milling rather than those offering a wide range of unrelated products.
4. Check if the manufacturer has the necessary certifications and quality control processes. Look for certifications such as ISO 9001, which ensure that the manufacturer follows international quality standards. This is crucial to receive reliable and high-quality CNC metal milling machines.
5. Look for customer reviews and testimonials on the manufacturer’s website or other platforms. Positive feedback indicates the manufacturer’s reliability and customer satisfaction. Additionally, consider reaching out to their existing customers for references or recommendations.
6. Contact potential manufacturers directly. Inquire about their production capabilities, customization options, lead times, pricing structure, and after-sales services. A reliable manufacturer should respond promptly and provide detailed and helpful information.
7. It’s also advisable to visit trade shows or exhibitions in China related to CNC machining or metalworking. This gives an opportunity to meet manufacturers in person, examine their products, and discuss specific requirements.
8. Lastly, compare multiple manufacturers based on their product quality, pricing, lead times, after-sales service, and overall reputation. By evaluating all these factors, you can make an informed decision and select a reliable CNC metal mill manufacturer in China.
Remember to conduct due diligence, carefully assess each manufacturer’s capabilities, and consider factors beyond just price. Building a long-term relationship with a trustworthy manufacturer will ensure consistent quality and reliable supply in the future.
How to check cnc metal mill manufacturers website reliable,use google chrome SEOquake check if ranking in top 10M
One way to check if a CNC metal mill manufacturer’s website is reliable is by using Google Chrome’s SEOquake tool to see if the website ranks in the top 10 for relevant keywords. This can give an indication of the website’s visibility and credibility within the industry.
In addition to checking the website’s ranking, you can also look for other indicators of reliability such as customer reviews, certifications, and industry affiliations. A reputable manufacturer will typically have positive reviews from customers and be affiliated with industry organizations or associations.
It’s also important to look for information on the website such as a physical address, contact information, and detailed product specifications. A reliable manufacturer will have a professional-looking website with clear and accurate information about their products and services.
By doing these checks and taking the time to research the manufacturer, you can ensure that you are working with a reputable and reliable CNC metal mill manufacturer.
Top 10 cnc metal mill manufacturers in China with each 160 words introduce products,then use markdown create table compare
1. Haas Automation: Haas Automation is a renowned CNC metal mill manufacturer in China. They offer a wide range of products, including vertical machining centers, horizontal machining centers, turnkey solutions, and rotary products. Their machines are known for their high performance, reliability, and precision.
2. DMG Mori: DMG Mori is a leading CNC metal mill manufacturer known for their innovative and technologically advanced products. They offer a diverse portfolio, including 5-axis machining centers, multi-axis turning machines, and automated systems. The company focuses on delivering high-quality machines that provide efficient and accurate milling solutions.
3. Mazak: Mazak specializes in CNC metal mills that cater to various industries, such as automotive, aerospace, and medical. Their range of products includes vertical machining centers, horizontal machining centers, and multi-tasking machines. Mazak machines are known for their advanced technology, productivity, and exceptional accuracy.
4. Fanuc: Fanuc is a global leader in CNC metal mill manufacturing, offering a comprehensive range of solutions for machining applications. They provide vertical machining centers, horizontal machining centers, and high-speed milling machines. Fanuc machines are renowned for their reliability, robustness, and cutting-edge automation capabilities.
5. Okuma: Okuma is a well-established CNC metal mill manufacturer that offers a wide range of products designed for precision and productivity. Their portfolio includes vertical machining centers, horizontal machining centers, and double-column machining centers. Okuma machines are known for their high-speed cutting, advanced automation features, and exceptional accuracy.
6. Haas Automation SM: Haas Automation SM is a subsidiary of Haas Automation and specializes in small to medium-sized CNC metal mills. They offer vertical machining centers, toolroom mills, and compact mills. Haas Automation SM machines are known for their affordability, compact size, and user-friendly interface.
7. Sodick: Sodick specializes in CNC metal mills with a focus on electrical discharge machining (EDM). They offer high-precision wire EDM machines, sinker EDM machines, and vertical machining centers. Sodick machines are known for their exceptional accuracy, reliability, and advanced EDM technologies.
8. Kent CNC: Kent CNC manufactures a diverse range of CNC metal mills, including vertical machining centers, double-column machining centers, and turning centers. Their machines are designed to provide high-speed milling, exceptional rigidity, and optimal precision. Kent CNC focuses on delivering cost-effective solutions for various industries.
9. Shenyang Machine Tool Co., Ltd.: Shenyang Machine Tool is a leading CNC metal mill manufacturer in China, offering a wide range of products, including horizontal machining centers, vertical machining centers, and gantry-type milling machines. Their machines are designed for high-productivity operations and provide excellent precision and stability.
10. Chiron: Chiron specializes in CNC metal mills for high-speed cutting and precision machining. They offer vertical machining centers, horizontal machining centers, and mill-turn centers. Chiron machines are known for their dynamic performance, exceptional speed, and advanced technology.
| Manufacturer | Products |
| ————————- | —————————————————- |
| Haas Automation | Vertical and horizontal machining centers |
| DMG Mori | 5-axis machining centers, multi-axis turning machines |
| Mazak | Vertical and horizontal machining centers |
| Fanuc | Vertical and horizontal machining centers |
| Okuma | Vertical and horizontal machining centers |
| Haas Automation SM | Vertical machining centers and compact mills |
| Sodick | Wire and sinker EDM machines, vertical machining centers |
| Kent CNC | Vertical machining centers, turning centers |
| Shenyang Machine Tool Co. | Horizontal and vertical machining centers |
| Chiron | Vertical and horizontal machining centers, mill-turn centers |
In conclusion, China has several top CNC metal mill manufacturers offering a wide range of machines catering to different industries and requirements. These manufacturers are known for their advanced technology, reliability, precision, and productivity. Whether you require vertical or horizontal machining centers, EDM machines, or specialized mill-turn centers, the Chinese market offers a variety of options to meet your machining needs.
Background Research for cnc metal mill manufacturers Companies in China, use qcc.com archive.org importyeti.com
When looking for CNC metal mill manufacturers in China, it is essential to conduct background research on potential companies to ensure quality and reliability. QCC.com is a valuable resource that provides information on the quality of products and services offered by manufacturers. This platform allows users to access reviews and ratings from customers, helping to gauge the reputation of a company before making a decision.
Archive.org is another useful tool for researching CNC metal mill manufacturers in China. This website archives past versions of web pages, providing insight into the company’s history, previous products, and any issues that may have occurred. By reviewing historical data on a manufacturer, potential customers can make more informed decisions about working with them.
Importyeti.com is a comprehensive database that tracks import and export data, including information on CNC metal mill manufacturers in China. By analyzing data on shipments, pricing, and other factors, importyeti.com can help identify reliable manufacturers and highlight any potential red flags to consider.
By utilizing these resources, customers can conduct thorough background research on CNC metal mill manufacturers in China to ensure that they select a reputable and trustworthy partner for their machining needs. These platforms provide valuable information to help customers make informed decisions and avoid potential risks associated with working with unreliable manufacturers.
Leveraging Trade Shows and Expos for cnc metal mill Sourcing in China
Trade shows and expos provide an excellent opportunity to source CNC metal mills in China, allowing businesses to explore a wide range of options and make informed decisions. These events bring together manufacturers, suppliers, and industry professionals, offering a platform to showcase and demonstrate their products and services.
When attending trade shows and expos, it is crucial to prepare beforehand. Researching and identifying specific events that focus on CNC metal mills in China will help businesses target the right exhibitors. Utilizing online resources, such as industry directories and event websites, can provide details about the participating companies and their products.
Prioritizing networking is key at these events. Engaging in face-to-face discussions with suppliers enables businesses to gain a deeper understanding of their capabilities, production processes, and quality standards. It also facilitates building relationships, which can be beneficial for long-term partnerships.
During the trade show or expo, businesses should be prepared to ask relevant questions to understand the supplier’s expertise, product range, pricing, and lead times. Requesting samples, product demonstrations, and technical specifications can help evaluate the quality and suitability of the CNC metal mills for specific requirements.
To maximize the effectiveness of sourcing efforts at trade shows and expos, it is crucial to take notes, collect business cards, and gather brochures or catalogs from potential suppliers. This information will be valuable for later comparison, evaluation, and negotiations.
Post-event, reviewing the gathered information and researching the shortlisted suppliers using trusted sources is essential. This step helps verify their reputation, production facilities, and customer feedback before proceeding with any agreements. Contacting references or previous customers can provide insight into the supplier’s reliability and customer service.
In conclusion, trade shows and expos offer an ideal platform for sourcing CNC metal mills in China, as businesses can interact with numerous suppliers, compare products, and build relationships. By careful preparation, active networking, and follow-up research, businesses can leverage these events to find reliable and suitable suppliers for CNC metal mills.
The Role of Agents and Sourcing Companies in Facilitating cnc metal mill Purchases from China
Agents and sourcing companies play a crucial role in facilitating CNC metal mill purchases from China. These professionals have an in-depth understanding of the Chinese market, suppliers, and manufacturing processes. They have established relationships with reliable suppliers and can negotiate better prices on behalf of their clients.
Agents and sourcing companies help in vetting suppliers to ensure they meet quality standards and have the capacity to fulfill orders. They also assist in verifying the credibility of suppliers through background checks and visits to manufacturing facilities. This minimizes the risk of working with unreliable suppliers and receiving subpar products.
Additionally, agents and sourcing companies help in managing communication between the buyer and supplier, ensuring that all requirements are clearly understood and met. They can also navigate language and cultural barriers, as well as handling logistics and shipping arrangements.
Overall, agents and sourcing companies provide a valuable service in simplifying the buying process, reducing risks, and ensuring a successful purchase of CNC metal mills from China. Their expertise and industry knowledge can help buyers make informed decisions and secure the best possible deal.
Price Cost Research for cnc metal mill manufacturers Companies in China, use temu.com and 1688.com
When conducting price cost research for CNC metal mill manufacturers in China, two popular online platforms to consider are temu.com and 1688.com. These websites provide a wide range of suppliers and manufacturers offering CNC metal mills at competitive prices.
To begin the research process, visit temu.com and 1688.com and use keywords such as “CNC metal mill manufacturers in China” to search for relevant suppliers. Take note of the different manufacturers and their products, specifications, and prices.
Compare the prices offered by different manufacturers to get an idea of the average cost of CNC metal mills in China. Keep in mind that prices may vary based on factors such as quality, brand, and features.
Contact a few manufacturers directly to request for a detailed quotation, including information on pricing, payment terms, and shipping costs. Be sure to inquire about any additional fees or charges that may apply.
Consider factors such as the manufacturer’s reputation, production capacity, and after-sales service when making your decision. It is also advisable to ask for samples or visit the manufacturer’s facility if possible to ensure the quality of the products.
By conducting thorough research on temu.com and 1688.com and comparing prices from different manufacturers, you can make an informed decision when purchasing CNC metal mills from China.
Shipping Cost for cnc metal mill import from China
The shipping cost for importing a CNC metal mill from China will vary depending on several factors such as the size and weight of the machine, the shipping method chosen, the distance between China and the destination country, and any additional services required.
Typically, the cost of shipping a CNC metal mill from China to another country can range from a few hundred dollars to over a thousand dollars. The most common shipping methods include air freight, sea freight, and courier services. Air freight is usually the fastest but also the most expensive option, while sea freight is slower but more cost-effective for larger and heavier shipments.
When calculating the shipping cost, it is important to consider additional expenses such as customs duties, taxes, insurance, and any necessary documentation fees. It is recommended to work with a reputable freight forwarder or shipping company to ensure a smooth and cost-effective shipping process.
To keep the shipping cost within budget, it is advisable to compare quotes from multiple shipping providers, optimize packaging to reduce weight and dimensions, and plan the shipment well in advance to avoid rush charges. Additionally, consider consolidating multiple items into one shipment to save on overall shipping costs.
Overall, the shipping cost for importing a CNC metal mill from China can be significant, but with careful planning and organization, it is possible to keep the cost within a reasonable budget.
Compare China and Other cnc metal mill Markets: Products Quality and Price,Visible and Hidden Costs
China is known as the world’s largest market for CNC metal mills, offering a wide range of products at competitive prices. However, when comparing China with other CNC metal mill markets in terms of product quality and price, as well as visible and hidden costs, several factors need to be considered.
In terms of product quality, China has made great strides in improving its manufacturing capabilities. Many CNC metal mills in China now produce high-quality products that meet international standards. However, it is important to note that product quality can vary significantly depending on the manufacturer and price range. Other CNC metal mill markets, such as Germany and Japan, are renowned for their precision engineering and superior product quality. As a result, these markets may have a slight advantage over China in terms of overall product quality.
When it comes to price, China has a strong competitive edge. Chinese manufacturers are able to offer CNC metal mills at relatively lower prices compared to other markets. This is largely due to lower labor costs and economies of scale resulting from the vast manufacturing infrastructure in China. In comparison, CNC metal mills from markets like Germany and Japan tend to have higher price points due to their focus on quality and precision.
Visible costs, such as the initial purchase price of CNC metal mills, may be relatively lower in China. However, it is crucial to consider the hidden costs associated with purchasing from China. Import duties, shipping costs, and potential expenses related to quality control and after-sales service can significantly impact the overall cost of acquiring CNC metal mills from China. On the other hand, other markets may have higher visible costs, but these markets often provide more comprehensive after-sales support and superior customer service, potentially offsetting hidden costs.
In conclusion, China’s CNC metal mill market offers a wide range of products at competitive prices. While the country has made significant improvements in terms of product quality, other markets known for their precision engineering may have an edge in this aspect. It is essential to consider visible and hidden costs when comparing China with other CNC metal mill markets, as these factors can significantly impact the overall cost of ownership and the level of after-sales support received.
Understanding Pricing and Payment Terms for cnc metal mill: A Comparative Guide to Get the Best Deal
When it comes to acquiring a CNC metal mill, understanding pricing and payment terms is crucial to ensure you get the best deal. Here is a comparative guide to help you navigate through this process.
Pricing for CNC metal mills can vary significantly based on factors like brand, size, features, and functionality. It’s essential to research different manufacturers and suppliers to compare prices. Online platforms, industry trade shows, and contacting suppliers directly can provide valuable information. Additionally, consulting with industry professionals or peers can offer insights into market rates.
Payment terms for CNC metal mills usually involve a combination of upfront payment and financing options. Many suppliers require a deposit or partial payment before the machine is manufactured or delivered. The remaining balance is typically due upon completion or delivery.
Understanding the financing options available is essential, especially for larger investments. Some suppliers offer in-house financing or installment plans, allowing you to pay in stages over an agreed-upon period. Others may partner with external financing companies, offering leasing or loan options. Researching these alternatives can help you determine which option best suits your financial circumstances.
It is crucial to consider additional costs beyond the machine’s price. These include shipping, installation, training, ongoing maintenance, and potential future upgrades. Requesting detailed quotations from suppliers can help evaluate the total cost of ownership.
Negotiation is an integral part of securing the best deal. Comparing quotes from different suppliers can give you leverage when negotiating the price or payment terms. Consider factors like the reputation of the supplier, warranty or service agreements, and the availability of spare parts. Some suppliers may be willing to be flexible on pricing or offer added benefits to win your business.
Finally, it is essential to review the supplier’s reputation and customer reviews before finalizing your purchase. Checking for testimonials, feedback, or ratings can provide insights into the supplier’s reliability, product quality, and after-sales support.
In summary, understanding pricing and payment terms for CNC metal mills requires thorough research and comparison. Gathering information from multiple suppliers and financing options allows you to negotiate effectively and secure the best deal for your needs.
Chinese Regulations and Industry Standards Certifications for cnc metal mill,Import Regulations and Customs for cnc metal mill from China
In China, the regulations and industry standards for CNC metal mills are overseen by the National standards bodies, including the Ministry of Industry and Information Technology (MIIT) and the China Machinery Industry Federation (CMIF). The key certification for CNC metal mills in China is the China Compulsory Certification (CCC), which is required for products that are sold in the Chinese market.
Additionally, CNC metal mills may also need to comply with industry standards such as the GB/T standards for machinery and equipment safety. It is important for manufacturers and exporters to ensure that their products meet these regulations and standards in order to avoid any legal complications or issues with customs when exporting to China.
When importing CNC metal mills from China, exporters need to be aware of the import regulations and customs procedures in place. This includes providing the necessary documentation, such as the CCC certificate and other relevant certifications, to customs authorities. It is also important to ensure that the products comply with Chinese quality and safety standards to avoid any delays or problems with customs clearance.
Overall, it is essential for exporters to adhere to Chinese regulations and industry standards certifications when exporting CNC metal mills to China in order to successfully navigate the import process and ensure compliance with local laws and regulations.
Sustainability and Environmental Considerations in cnc metal mill Manufacturing
In the manufacturing industry, sustainability and environmental considerations play a crucial role in minimizing the negative impact on the environment. This also holds true for CNC metal mill manufacturing, where efforts are made to adopt sustainable practices and minimize the carbon footprint.
One key aspect of sustainability in CNC metal mill manufacturing lies in resource utilization. This involves optimizing the use of energy, raw materials, and water during the production process. Manufacturers are increasingly investing in energy-efficient machines and technologies to reduce energy consumption. Additionally, waste management practices, such as recycling and reusing materials, are employed to minimize the environmental impact of production.
Another important consideration is the reduction of greenhouse gas emissions. CNC metal mill manufacturers are adopting greener alternatives like electric or hybrid machines, which significantly decrease emissions compared to traditional combustion engines. Furthermore, the implementation of efficient waste management systems, such as proper collection and disposal of hazardous materials, ensures the safe handling of chemicals and reduces the risk of environmental pollution.
The sustainability approach also extends to the entire supply chain. Manufacturers are increasingly seeking out suppliers who prioritize eco-friendly practices and materials. This includes using materials that are responsibly sourced and have a lower environmental impact. Moreover, companies are promoting sustainable packaging solutions to minimize waste generation and encourage recycling.
To promote a sustainable approach, CNC metal mill manufacturers are also investing in research and development to improve the recycling capabilities of metal waste. This involves developing advanced techniques for recycling metal chips and scraps, which can then be reused in the production process. By reducing the need for fresh raw materials, this practice helps conserve resources and further minimizes the environmental impact.
Overall, through various initiatives and practices, sustainability and environmental considerations in CNC metal mill manufacturing aim to minimize energy consumption, reduce waste generation, and decrease greenhouse gas emissions. By adopting these principles, manufacturers can align their operations with environmentally-friendly practices and contribute to a greener future.
List The Evolution history of “cnc metal mill”
The evolution history of CNC metal mills can be traced back to the early 1950s when computer numerical control (CNC) technology was first introduced. At that time, the mills were primarily operated manually, requiring skilled machinists to operate them. However, the emergence of CNC technology revolutionized the machining industry.
In the 1960s, the first CNC metal mills started to appear. These machines were controlled by punch cards or magnetic tapes. The introduction of numerical control allowed for greater precision and repeatability in metal milling operations. This technology was rapidly adopted by the automotive, aerospace, and defense industries.
During the 1970s and 1980s, advancements in computer technology led to the development of more sophisticated CNC metal mills. The introduction of computer-aided design (CAD) and computer-aided manufacturing (CAM) software allowed for the creation of complex designs and efficient programming of the machines. This increased the versatility and productivity of metal milling operations.
In the 1990s, CNC metal mills underwent further improvements with the advent of multitasking machines. These machines combined milling, turning, drilling, and other operations into a single unit, reducing setup time and improving overall efficiency. Additionally, the integration of real-time monitoring systems enhanced the accuracy and reliability of the machining process.
In recent years, CNC metal mills have continued to evolve with the integration of advanced technologies such as artificial intelligence and machine learning. These technologies enable self-optimization, adaptive control, and predictive maintenance, allowing for increased productivity and reduced downtime.
Today, CNC metal mills are equipped with state-of-the-art features like high-speed spindles, advanced tooling systems, and automatic tool changers. They can handle a wide range of materials, from soft metals to hard alloys, with unparalleled precision. Furthermore, the use of robotics and automation has further enhanced the efficiency and productivity of these machines, reducing the need for manual intervention.
In conclusion, the evolution of CNC metal mills has seen the transformation of manual milling operations to advanced, fully automated systems. These machines have greatly improved productivity, precision, and versatility, making them essential tools in various industries, including automotive, aerospace, and manufacturing.
The Evolution and Market Trends in cnc metal mill Industry
The CNC metal mill industry has witnessed significant evolution and market trends over the years. CNC (Computer Numerical Control) technology has revolutionized the metal milling process, enabling higher precision, efficiency, and productivity.
One major evolution in the CNC metal mill industry is the transition from manually operated mills to automated CNC machines. Previously, operators had to manually control the milling process, which was time-consuming and prone to human error. With CNC machines, the entire process is automated, eliminating the need for human intervention and reducing the possibility of errors. This has resulted in higher quality products, faster production times, and reduced labor costs.
Another significant evolution is the integration of advanced software and systems into CNC metal mills. Today, CNC mills are equipped with sophisticated software that allows for precise control and programming of the machines. This software enables operators to create complex 3D designs, import digital models, and simulate the milling process before production. This not only streamlines the workflow but also enhances the overall accuracy and efficiency of the milling process.
In terms of market trends, there has been a growing demand for CNC metal mills in various industries, such as automotive, aerospace, electronics, and medical devices. The need for precision-engineered components and parts has driven the adoption of CNC metal mills by these industries. Additionally, the ability of CNC machines to work with a wide range of materials, including aluminum, steel, and titanium, has further expanded their market potential.
Furthermore, there is a growing trend towards miniaturization and lightweight designs, especially in the aerospace and electronics sectors. This has resulted in the demand for CNC metal mills that can produce intricate and complex components with high precision. Manufacturers are constantly innovating to develop CNC machines with higher spindle speeds, improved tooling options, and enhanced control systems to meet these requirements.
In conclusion, the CNC metal mill industry has evolved significantly, leveraging advancements in technology and software to improve productivity and precision. Market trends indicate a growing demand for CNC metal mills in various industries, driven by the need for high-quality components and the push towards miniaturization. As technology continues to advance, it is expected that CNC metal mills will continue to play a vital role in the manufacturing sector.
Custom Private Labeling and Branding Opportunities with Chinese cnc metal mill Manufacturers
If you are looking for custom metal milling services with private labeling and branding opportunities, Chinese CNC metal mill manufacturers can offer you a range of options. With state-of-the-art technology and skilled technicians, these manufacturers can provide precision metal milling services to meet your specific requirements.
With private labeling and branding opportunities, you can showcase your brand on the finished products and establish a strong presence in the market. Chinese manufacturers can work closely with you to understand your branding needs and incorporate your logo, colors, and design elements into the products. This customized approach allows you to create a unique and distinctive product line that reflects your brand identity.
Whether you need metal components, parts, or prototypes, Chinese CNC metal mill manufacturers can deliver high-quality products with fast turnaround times. By partnering with a reliable manufacturer, you can ensure consistent quality, competitive pricing, and reliable supply chain management.
In conclusion, partnering with Chinese CNC metal mill manufacturers for custom private labeling and branding opportunities can help you differentiate your products in the market and enhance your brand visibility. With their expertise and capabilities, you can create customized metal milling solutions that meet your exact specifications and branding requirements. Consider exploring these opportunities with Chinese manufacturers to leverage their experience and resources for your business success.
Tips for Procurement and Considerations when Purchasing cnc metal mill
When purchasing a CNC metal mill, there are several key considerations to keep in mind to ensure you are making the right investment for your business.
First, consider the size and capacity of the CNC metal mill. Make sure it can handle the size and type of metal you will be working with.
Secondly, look at the precision and accuracy of the machine. A high-quality CNC metal mill will provide consistent and precise results, which is essential for producing high-quality metal parts.
Additionally, consider the speed and efficiency of the machine. Look for a CNC metal mill that can operate quickly and efficiently to maximize productivity.
Another important factor to consider is the machine’s durability and reliability. You want a CNC metal mill that is built to last and can withstand heavy use in a production environment.
It’s also important to consider the software and controls that come with the CNC metal mill. Make sure the machine is compatible with your existing software and that the controls are user-friendly for your operators.
Lastly, consider your budget and shop around for the best price. Compare different brands and models to find a CNC metal mill that offers the best value for your money.
Overall, taking the time to research and consider these factors will help you make an informed decision when purchasing a CNC metal mill for your business.
FAQs on Sourcing and Manufacturing cnc metal mill in China
1. How do I find a reputable manufacturer for CNC metal mills in China?
One way to find a reputable manufacturer for CNC metal mills in China is to conduct thorough research and due diligence. You can start by searching online directories, attending trade shows, and seeking recommendations from industry professionals. It is crucial to verify the manufacturer’s credentials, such as certifications and customer testimonials, before making a decision.
2. What factors should I consider when sourcing a CNC metal mill from China?
When sourcing a CNC metal mill from China, consider factors such as the manufacturer’s reputation, production capacity, quality control measures, pricing, and lead times. It is essential to communicate clearly with the manufacturer about your specific requirements and expectations to ensure a successful partnership.
3. How can I ensure quality control and oversight of the manufacturing process for my CNC metal mill in China?
To ensure quality control and oversight of the manufacturing process for your CNC metal mill in China, you can consider visiting the manufacturer’s facilities, conducting inspections, and implementing strict quality control measures. It is advisable to have a detailed contract outlining quality standards, inspection procedures, and dispute resolution mechanisms to mitigate any potential risks.
4. Can I customize my CNC metal mill design when sourcing from China?
Yes, many manufacturers in China offer customization services for CNC metal mills to meet the specific needs and requirements of their clients. You can work closely with the manufacturer to design a custom CNC metal mill that aligns with your production goals, budget, and technical specifications.
5. What are the advantages of sourcing a CNC metal mill from China?
Sourcing a CNC metal mill from China can offer cost savings, access to advanced manufacturing technologies, a wide range of product options, and a large pool of skilled labor. Additionally, China’s robust supply chain and infrastructure can facilitate efficient production and timely delivery of CNC metal mills to customers worldwide.
Why contact sourcifychina.com get free quota from reliable cnc metal mill suppliers?
Sourcifychina.com is able to acquire a free quota from reliable CNC metal mill suppliers for several reasons. Firstly, Sourcifychina.com has built a strong network and relationships with these suppliers over time. This enables the platform to negotiate favorable terms and discounts on behalf of their clients.
Additionally, Sourcifychina.com acts as a trusted intermediary between businesses and suppliers. Due to their established reputation and experience in the industry, suppliers are more willing to offer incentives such as free quotas to earn the business of Sourcifychina.com’s clients.
Furthermore, Sourcifychina.com brings a consistent volume of business to these suppliers. By aggregating the demand from multiple clients, Sourcifychina.com is able to consolidate orders and negotiate better deals, including the provision of free quotas.
The platform’s expertise in sourcing and production management also contributes to the acquisition of free quotas. Sourcifychina.com assists clients in optimizing their product designs, improving cost-efficiency, and ensuring smooth production processes. This makes the suppliers more willing to offer free quotas as a part of strengthening their mutually beneficial partnership.
Finally, the reputation and track record of Sourcifychina.com play a crucial role. By consistently delivering high-quality products and maintaining good relationships with suppliers, the platform has gained trust and credibility within the industry. This enhances their ability to secure free quotas from reliable CNC metal mill suppliers.
In conclusion, Sourcifychina.com receives free quotas from reliable CNC metal mill suppliers due to their strong network, established reputation, ability to aggregate demand, expertise in sourcing, and trustworthiness within the industry.