Introduce about cnc pcb milling guide,Qulity,Cost,Supplier,Certification,Market,Tips,FAQ
CNC PCB milling is a manufacturing process that uses computer-controlled machines to accurately and efficiently fabricate printed circuit boards (PCBs). This guide aims to provide you with information regarding the quality, cost, suppliers, certification, market, tips, and frequently asked questions (FAQs) related to CNC PCB milling.
Quality is an essential consideration in CNC PCB milling as it affects the performance and reliability of the final product. The use of computer-controlled machines ensures precise and consistent results, leading to high-quality PCBs. However, the quality also depends on the expertise of the operator and the materials used.
In terms of cost, CNC PCB milling offers advantages like reduced setup time and flexibility in producing small quantities, making it cost-effective for prototype and small-scale production runs. However, for large-scale production, other methods like etching or stencil printing may be more economical.
Choosing a reliable supplier is crucial to ensure the success of your CNC PCB milling project. Make sure to select a supplier with experience, a good track record, and positive customer reviews. It is also advisable to consider their turnaround time, pricing, and the ability to handle your specific requirements.
Certification is another vital aspect to consider, especially if your PCBs need to meet specific industry standards or regulations. Look for suppliers who have the necessary certifications such as ISO 9001, ISO 14001, or UL listing, depending on your project requirements.
The market for CNC PCB milling is rapidly growing due to increased demand for smaller and more complex electronic devices. Various industries, including consumer electronics, aerospace, medical, automotive, and telecommunications, rely on high-quality PCBs for their products.
Here are some tips to enhance your CNC PCB milling process:
1. Ensure proper machine calibration and maintenance to maintain accuracy and avoid errors.
2. Optimize your file preparation by using appropriate software and considering the tooling requirements.
3. Choose the right tooling materials and parameters for the best results.
4. Consider using a solder mask to improve the durability and compatibility of your PCBs.
Frequently Asked Questions (FAQs):
Q: Can CNC PCB milling be used for multilayer PCBs?
A: Yes, CNC PCB milling can handle multilayer PCBs, but it may be more time-consuming and challenging compared to traditional methods like etching.
Q: What file formats are compatible with CNC PCB milling machines?
A: Commonly used file formats include Gerber, Excellon, and G-code.
Q: Is CNC PCB milling suitable for producing high volumes of PCBs?
A: While CNC PCB milling is cost-effective for small quantities, it may not be the best option for high-volume production due to its relatively slower production speed.
In conclusion, CNC PCB milling provides a viable and efficient option for fabricating high-quality PCBs. Consider factors like quality, cost, supplier reliability, and certifications to ensure success in your CNC PCB milling projects.
Types of cnc pcb milling
There are several types of CNC PCB milling methods that are commonly used in the manufacturing industry. These methods vary in complexity, speed, and precision, and each has its own advantages and disadvantages. Here are some of the most popular types of CNC PCB milling:
1. Mechanical Milling: This is the most common and traditional method of PCB milling. In this method, a rotating tool with sharp edges is used to remove material from the PCB substrate. The tool can be either a drill bit or an end mill, and it is guided by a computer-controlled spindle. Mechanical milling is known for its accuracy and precision, but it can be slow and time-consuming.
2. Laser Milling: Laser milling is a non-contact method of removing material from a PCB substrate using a laser beam. The laser beam is directed by a computer-controlled system and focused on the desired area to remove material. Laser milling is fast and precise, but it is limited by the type of material that can be processed. It is primarily used for non-metallic materials.
3. Chemical Milling: Chemical milling is a method that uses chemical etchants to selectively remove material from the PCB substrate. This method is commonly used for fine and precise patterns. Chemical milling can be faster than mechanical milling, but it requires a controlled environment and careful handling of the chemicals.
4. Electrical Discharge Machining (EDM): EDM is a method that uses electrical energy to remove material from the PCB substrate. A controlled electrical discharge is generated between an electrode and the PCB substrate, which selectively removes material. EDM is fast and precise, but it is mainly used for complex and intricate designs.
5. Ultrasonic Milling: Ultrasonic milling utilizes high-frequency vibrations to remove material from the PCB substrate. An ultrasonic tool is pressed against the PCB substrate, and the vibrations break up the material at the cutting edge. Ultrasonic milling is precise and suitable for delicate materials, but it can be slower compared to other methods.
Each type of CNC PCB milling has its own advantages and disadvantages, and the selection of the method depends on the specific requirements of the PCB design and the desired outcome.
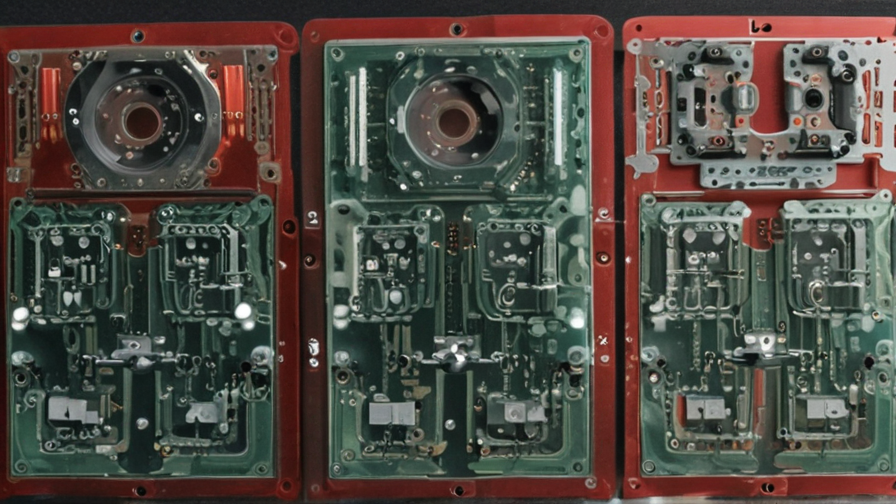
Pros and Cons of Using cnc pcb milling
Pros of Using CNC PCB Milling:
1. Cost-Effective: CNC PCB milling is a cost-effective method compared to traditional PCB manufacturing techniques. It eliminates the need for extensive tooling and reduces material waste, resulting in lower production costs.
2. Faster Turnaround Time: With CNC PCB milling, prototypes and small batches of PCBs can be produced quickly. This reduces the overall time-to-market for electronic products, allowing for faster testing and refinement.
3. Design Flexibility: CNC milling offers great design flexibility as it can create complex and intricate PCB designs with high precision. It allows for the creation of boards with fine traces, tight spacing, and intricate shapes, which may not be possible through other manufacturing techniques.
4. Iterative Prototyping: CNC PCB milling enables rapid iterative prototyping. It allows for quick modifications and design changes to be made, allowing engineers to refine their designs and test multiple iterations before finalizing the PCB layout.
5. DIY Capabilities: CNC mills can be used by DIY enthusiasts and hobbyists to create their own PCBs at home. This empowers individuals to experiment with electronics and develop their own custom circuit boards without the need for expensive outsourcing.
Cons of Using CNC PCB Milling:
1. Limited Material Compatibility: CNC PCB milling is primarily suited for working with rigid materials like FR4. It may not be suitable for certain flexible or specialized materials, such as polyimide or ceramic, which might be required for specific applications.
2. Complexity for Multi-layer Boards: While CNC milling can handle single or double-sided PCBs well, it becomes more challenging and time-consuming when producing multi-layer boards. The alignment and accuracy required for multiple layers can be difficult to achieve using milling alone.
3. Environmental Impact: CNC PCB milling generates significant waste material, especially when using subtractive methods. The disposal of waste materials, such as copper dust and FR4 particles, needs to be managed carefully to minimize the environmental impact.
4. Skill and Knowledge Required: CNC PCB milling requires expertise in PCB design software and knowledge of the milling process. It may require a learning curve for individuals who are new to the technology, especially for complex and precise designs.
5. Initial Investment: Setting up a CNC milling machine can involve a significant upfront cost, especially for high-quality machines capable of producing complex PCBs. This cost may be a barrier for smaller businesses or hobbyists who have budget constraints.
In conclusion, CNC PCB milling offers cost savings, faster turnaround time, design flexibility, and DIY capabilities. However, it has limitations related to material compatibility, complexity for multi-layer boards, environmental impact, skill requirements, and initial investment.
cnc pcb milling Reference Specifications (varies for different product)
CNC (Computer Numerical Control) PCB (Printed Circuit Board) milling is a process used to manufacture prototype or small-scale production circuit boards. It involves the use of specialized milling machines to remove copper and other materials from a non-conductive substrate, creating the desired circuitry.
The reference specifications for CNC PCB milling may vary depending on the specific product being manufactured. However, some common requirements include:
1. Material: The substrate material used for PCB milling is typically a non-conductive material such as FR-4 fiberglass or aluminum. The choice of material depends on factors like the application, required durability, and cost.
2. Copper thickness: The copper on the PCB surface is responsible for carrying electrical signals. The reference specifications often specify the required thickness of the copper layer, which can range from 1oz (35µm) to higher values like 2oz (70µm) or more. Thicker copper layers provide better conductivity and heat dissipation but result in higher manufacturing costs.
3. Trace width and spacing: The reference specifications define the minimum trace width and spacing requirements. This determines how close traces can be placed to each other and ensures proper insulation between them. Smaller trace width and spacing allow for denser circuitry but may pose manufacturing challenges, especially with higher copper thicknesses.
4. Hole sizes: PCBs often have holes for component mounting or interconnecting layers. The reference specifications specify the required hole sizes and tolerances. Different products may have different hole size requirements based on the components used, such as through-hole or surface-mount devices.
5. Tolerances: As with any manufacturing process, tolerances are crucial in CNC PCB milling. The reference specifications define the acceptable tolerance levels for various parameters like trace width, hole size, and board dimensions. Tighter tolerances ensure higher precision but may increase manufacturing costs.
In summary, CNC PCB milling reference specifications outline the material, copper thickness, trace width and spacing, hole sizes, and tolerances required for manufacturing a specific product. Adhering to these specifications is essential to achieve the desired functionality, durability, and manufacturability of the printed circuit boards.
Applications of cnc pcb milling
CNC PCB milling is a manufacturing process that utilizes computer-controlled milling machines to create printed circuit boards (PCBs). This technology has revolutionized the PCB fabrication industry, offering various applications and advantages over traditional methods such as etching.
One significant application of CNC PCB milling is rapid prototyping. Engineers and designers can quickly turn their ideas into physical PCBs by uploading the design file to the CNC milling machine. This allows them to test the functionality and performance of the circuit before mass production, ensuring the design is error-free and optimized.
Another application is in the production of small batches or customized PCBs. CNC PCB milling enables efficient and cost-effective production of small quantities of PCBs, eliminating the need for expensive setup processes involved in large-scale manufacturing. This makes it ideal for small businesses, hobbyists, and research institutions.
CNC PCB milling also offers superior precision and accuracy compared to traditional etching methods. The milling machine follows the design file with high precision, resulting in intricate and precisely designed PCBs. This is especially beneficial for complex circuit designs that require tight tolerances and miniaturization.
Furthermore, CNC PCB milling allows for the use of various materials. Unlike etching, which primarily works with copper-clad boards, CNC milling machines can handle a wide range of materials such as FR-4, aluminum, and even flexible substrates. This versatility expands the possibilities in PCB design and opens doors for novel applications.
Additionally, CNC PCB milling facilitates the production of multi-layered PCBs. With precise milling, the machine can drill and route intricate patterns to create multiple layers, enabling the integration of complex circuits and connections in a compact space. This is particularly advantageous in the development of advanced electronic devices with high-density circuitry.
Overall, CNC PCB milling provides a fast, low-cost, and precise method for prototyping and manufacturing PCBs. Its wide range of applications makes it an indispensable tool for various industries, including electronics, aerospace, automotive, robotics, and telecommunications. The technology continues to evolve, enabling further innovations in electronic design and manufacturing processes.
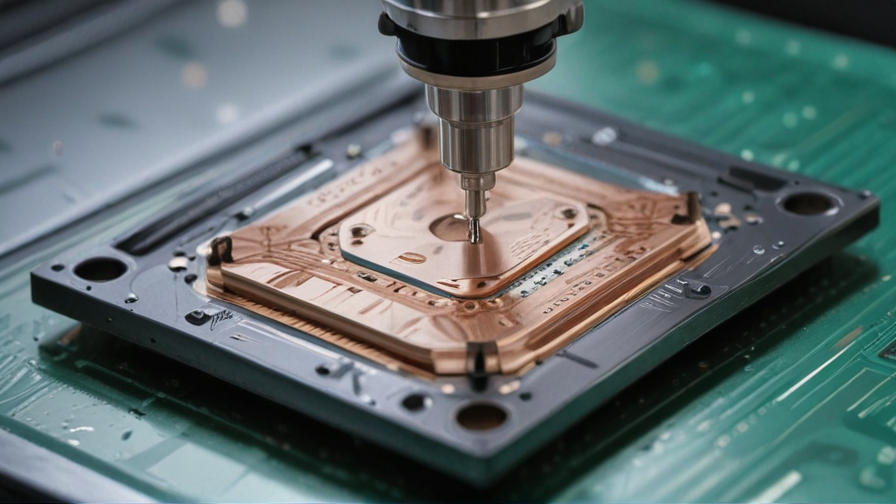
The Work Process and how to use cnc pcb milling
CNC PCB milling is a process that involves using a computer-controlled machine to mill or engrave printed circuit boards (PCBs). This method is commonly used in the electronics industry to create prototypes or small production runs of PCBs.
The work process for CNC PCB milling typically involves the following steps:
1. Designing the PCB: The first step is to create a digital design of the PCB using CAD (Computer-Aided Design) software. This design specifies the circuit layout, component placement, and the traces that will be milled onto the PCB.
2. Generating the machine instructions: Once the design is complete, the CAD software generates the machine instructions or G-code that the CNC milling machine will use to mill the PCB. This G-code contains information about the tool paths, speeds, and depths of cut.
3. Preparing the machine: The milling machine is set up by attaching a milling bit to the spindle and securing the PCB to the machine’s worktable. The machine is then calibrated to ensure precise movement in the X, Y, and Z axes.
4. Loading the G-code: The generated G-code is loaded into the CNC milling machine’s controller. This code serves as a set of instructions for the machine to follow during the milling process.
5. Milling the PCB: The milling process begins with the machine moving the milling bit over the surface of the PCB, following the tool paths specified in the G-code. The milling bit removes the excess copper from the board, leaving behind the desired circuit traces. This process may involve multiple passes with different tools and depth settings.
6. Inspecting and cleaning: Once the milling process is complete, the PCB is inspected for any defects or errors. Any excess dust or debris is cleaned off the PCB using compressed air or a brush.
7. Drilling and finishing: Depending on the design, holes may need to be drilled into the PCB for component placement. This can be done manually or using a separate drilling machine. The PCB may also undergo additional processes such as solder mask application and surface finish application.
By using CNC PCB milling, designers and manufacturers can achieve precise and repeatable results, thereby saving time and effort compared to traditional methods. Additionally, this process allows for rapid prototyping and customization, making it ideal for small-scale production or testing new designs.
Quality Testing Methods for cnc pcb milling and how to control the quality
Quality testing methods for CNC PCB milling involve various techniques to ensure that the milled PCBs meet the required quality standards. Here are some commonly used methods:
1. Visual Inspection: This involves visually examining the milled PCBs for any visible defects such as uneven traces, improper hole sizes, or delamination.
2. Electrical Testing: Electrical tests are performed to verify the conductivity and integrity of the traces and circuitry. For example, the continuity test checks if all connections are properly established.
3. Impedance Testing: This test measures the impedance of the transmission lines on the PCB. It ensures that the impedance values are within the specified range, which is critical for signal integrity.
4. Dimensional Inspection: This involves measuring various dimensions of the PCB, such as hole diameters, trace widths, and board thickness, to ensure they comply with the design specifications.
5. Solderability Testing: Solderability tests assess the ability of the PCB to accept solder. This is done by performing a wetting and spreading test on the surface of the PCB’s pads.
To control the quality of CNC PCB milling, the following steps can be undertaken:
1. Implement Strict Design Guidelines: Clearly define PCB design guidelines to ensure that the design is optimized for the milling process. This includes spacing considerations, trace width limitations, and constraints on hole sizes.
2. Calibration and Maintenance: Regularly calibrate and maintain the milling machine to ensure accurate and precise milling operations. This includes monitoring and adjusting feed rates, spindle speed, and tooling conditions.
3. Process Documentation: Develop comprehensive documentation for the milling process, including tooling specifications, milling parameters, and standard operating procedures. This helps to maintain consistency and repeatability.
4. Training and Skill Development: Invest in workforce training to ensure the operators are familiar with the milling process and capable of executing it correctly. This includes training on machine operation, tooling handling, and quality control techniques.
5. Statistical Process Control (SPC): Implement SPC techniques to continuously monitor and control the milling process. This involves collecting data, analyzing process variations, and taking corrective actions whenever necessary.
By combining these testing methods and quality control measures, manufacturers can ensure that CNC PCB milling consistently produces high-quality PCBs that meet the requirements of the intended applications.
cnc pcb milling Sample Policy and Post-Purchase Considerations for cnc pcb milling from China
Sample Policy for CNC PCB Milling from China:
When purchasing CNC PCB milling services from China, it is advisable to request samples from potential suppliers before placing a bulk order. Sample policy can vary between suppliers, but generally, they may charge for the sample and shipping cost. However, some suppliers may offer free samples, especially for large orders. It is important to clarify the sample policy with the supplier beforehand to avoid any misunderstandings.
Post-Purchase Considerations for CNC PCB Milling from China:
1. Quality Control: Once the samples have been received and approved, it is crucial to ensure consistency in quality for future orders. Conduct thorough inspections of the delivered PCBs to identify any defects or inconsistencies. Communicate any issues with the supplier to resolve them and maintain high-quality standards.
2. Communication: Effective and consistent communication is key. Ensure the supplier is responsive and prompt in addressing any queries or concerns. Clear communication helps in maintaining a good working relationship and ensures that all specifications are met.
3. Lead Time and Delivery: Discuss the lead time required for production and shipping with the supplier. Timely delivery is crucial, so establish clear expectations and make sure they can meet your required timeframe.
4. Packaging and Shipping: PCBs are delicate and need proper packaging to avoid damage during transit. Discuss packaging requirements with the supplier to ensure the PCBs are adequately protected. Additionally, consider any customs regulations or import duties that may apply and clarify responsibilities with the supplier in terms of shipping arrangements.
5. Payment Terms: Negotiate and clarify payment terms with the supplier, including methods, currency, and the agreed-upon timeline. Ensure the chosen payment method is secure and reliable.
6. Sample Revisions: If any modifications or adjustments are required after receiving the initial samples, clearly communicate your feedback to the supplier. Request revised samples if necessary to ensure the final product meets your requirements.
By following these post-purchase considerations, you can establish a successful partnership with a Chinese supplier for CNC PCB milling and ensure the consistent delivery of high-quality PCBs.
Sourcing cnc pcb milling from China: Opportunities, Risks, and Key Players
Sourcing CNC PCB milling from China presents both opportunities and risks. On the opportunity side, China is an established manufacturing hub with a highly skilled workforce and advanced technology. The country has a solid infrastructure in place to support the production of printed circuit boards (PCBs) using computer numerical control (CNC) milling techniques. This allows for efficient and cost-effective manufacturing processes, making China an attractive option for PCB milling.
One of the key opportunities of sourcing CNC PCB milling from China is the potential for cost savings. Chinese manufacturers often offer competitive pricing due to lower labor costs and economies of scale. This can provide significant savings, especially for large-volume productions.
Additionally, China offers a wide range of options when it comes to PCB milling. The country has numerous specialized manufacturers and suppliers that focus on CNC PCB milling. This means that buyers have access to a large pool of potential suppliers, allowing them to choose the most suitable partner based on their specific requirements and preferences.
However, sourcing from China also comes with risks that need to be considered. Quality control can be a challenge, as not all Chinese manufacturers adhere to the same standards. It is crucial to thoroughly vet potential suppliers and conduct regular quality checks to ensure that the PCBs meet the desired specifications.
Another risk is intellectual property (IP) protection. China has a reputation for IP infringement, and there have been cases of counterfeit PCBs being produced and sold. Companies must take precautions to protect their designs and IP through non-disclosure agreements (NDAs) and other legal measures.
Despite these risks, there are several key players in the Chinese market that have established themselves as reliable manufacturers of CNC-milled PCBs. Some of the well-known players include Shenzhen JLCPCB, ChinaPCBOne, and Shenzhen Grande Electronics. These companies have a track record of delivering high-quality products and have built a reputation as trustworthy suppliers.
In summary, sourcing CNC PCB milling from China offers opportunities for cost savings, a wide supplier base, and access to advanced manufacturing capabilities. However, risks such as quality control and IP protection should be carefully managed. By working with reputable suppliers and implementing robust quality assurance processes, businesses can leverage the advantages of sourcing from China while mitigating potential risks.
How to find and select reliable cnc pcb milling manufacturers in China,use google search manufacturers and suppliers
When searching for reliable CNC PCB milling manufacturers in China, Google search can be an effective tool. Here’s a step-by-step guide to find and select the right manufacturer for your needs:
1. Start your search: Open Google and enter relevant keywords like “CNC PCB milling manufacturers in China” or “reliable PCB manufacturers in China.” This will generate a list of potential manufacturers and suppliers.
2. Evaluate the search results: Go through the search results and visit the websites of various manufacturers. Look for information on their expertise, capabilities, and experience. Check if they specialize in PCB milling and if they have an established presence in the industry.
3. Assess their website: A reputable manufacturer will have a professional-looking website that provides comprehensive information about their services, certifications, machinery, and customer feedback. Look for manufacturers with detailed product descriptions and clear contact information.
4. Supplier directories: Apart from standard Google search, you can also explore supplier directories like Alibaba, Made-in-China, or Global Sources. These platforms provide a list of manufacturers with verified credentials and customer reviews, helping you find reliable options.
5. Customer reviews and testimonials: Look for testimonials or reviews from previous customers. This helps gauge the manufacturer’s reputation and reliability. Pay attention to both positive and negative feedback to have a balanced understanding of their strengths and weaknesses.
6. Contact the shortlisted manufacturers: Make a shortlist of potential manufacturers and reach out to them for further evaluation. Inquire about their product quality, production capacity, lead time, pricing, and any specific requirements you might have. Prompt and professional responses indicate reliability.
7. Request samples: If feasible, request samples of their PCB milling work. This will give you firsthand experience of the quality and precision they offer. Evaluate the samples based on your specific requirements and quality standards.
8. Certifications and compliance: Check if the manufacturer holds relevant certifications like ISO 9001, ISO 14001, or UL certification. Compliance with international standards ensures adherence to quality and environmental guidelines.
9. OEM/ODM capability: If you have unique design requirements or need customization, ensure that the manufacturer has the capability to provide OEM (Original Equipment Manufacturer) or ODM (Original Design Manufacturer) services. This flexibility can be crucial when it comes to fulfilling your specific needs.
10. Competitive pricing: Compare the pricing of different manufacturers while considering factors like quality, expertise, and additional services offered. Remember that the cheapest option may not always provide the desired quality, while the most expensive does not guarantee the best outcome.
By carefully analyzing potential manufacturers through Google search, exploring supplier directories, reviewing customer feedback, and contacting them for further inquiry, you can find and select reliable CNC PCB milling manufacturers in China that align with your specific requirements.
How to check cnc pcb milling manufacturers website reliable,use google chrome SEOquake check if ranking in top 10M
When it comes to checking the reliability of a CNC PCB milling manufacturer’s website, you can follow a few simple steps:
1. Use Google Chrome: Start by using a web browser like Google Chrome, as it has numerous built-in features and extensions that can assist in evaluating a website.
2. Install SEOquake: Add the SEOquake extension to your Google Chrome browser. SEOquake provides essential metrics that can give you a better understanding of a website’s credibility and overall performance.
3. Check the website ranking: Use SEOquake to check the website’s ranking in the top 10 million (top 10M). This metric indicates the website’s popularity and visibility online. Websites with higher rankings are generally more reliable and trustworthy.
4. Analyze the website’s statistics: SEOquake provides additional metrics such as a website’s Alexa Rank, Google Index, and the number of backlinks it has. These metrics can indicate the website’s authority, search engine visibility, and overall credibility.
5. Consider user reviews and testimonials: Look for user reviews or testimonials on the website itself or search for external reviews on forums or social media platforms. Genuine positive reviews and testimonials from satisfied customers can give you confidence in the manufacturer’s reliability.
6. Verify the company’s information: Check the website for comprehensive information about the manufacturer, including their contact details, address, and customer support. A reliable manufacturer will have transparent and easily accessible company information.
7. Look for certifications and affiliations: Reliable manufacturers often showcase certifications, affiliations, or partnerships with industry organizations or standardization bodies. These indicate their commitment to quality and compliance with industry standards.
Remember, while using SEOquake can provide valuable insights, it’s important to consider other factors such as the manufacturer’s reputation, experience, and the quality of their products and services.
Top 10 cnc pcb milling manufacturers in China with each 160 words introduce products,then use markdown create table compare
1. Bantam Tools: Bantam Tools is a leading manufacturer in China, specializing in CNC PCB milling machines. Their machines are designed for precision, offering high-speed milling capabilities, as well as quick setup and easy usability. The Bantam Tools CNC milling machines are suitable for various materials, including FR-1, FR-4, aluminum, and brass. With a compact design, their machines are perfect for small-scale production and rapid prototyping.
2. MITS Electronics: MITS Electronics is known for producing high-quality CNC PCB milling machines in China. Their machines are equipped with advanced features like automatic tool changers, precise positioning systems, and adjustable spindles. MITS Electronics’ machines offer excellent precision, enabling the production of intricate PCB designs. These machines are suitable for various materials, such as FR-4, aluminum, and copper clad laminates.
3. LPKF Laser & Electronics: LPKF is a well-established manufacturer of CNC PCB milling machines based in China. They offer a wide range of machines suitable for both prototyping and production applications. LPKF machines utilize high-quality spindles and advanced control systems for precise milling operations. Their machines can handle various materials, including FR-4, PTFE, and flexible PCBs.
4. Shenzhen Sinoamigo Technology: Sinoamigo Technology specializes in CNC PCB milling machines with a focus on user-friendly operation and high precision. Their machines are equipped with advanced control systems, allowing for efficient and accurate milling. Sinoamigo’s machines are suitable for various materials, such as FR-4, CEM-1, and aluminum-clad laminates.
5. Wintech PCB Technology: Wintech PCB Technology is a leading manufacturer of CNC PCB milling machines based in China. Their machines are designed for high-speed and high-precision milling operations. Wintech PCB machines are suitable for various materials, including FR-4, aluminum, and copper.
| **Manufacturer** | **Product Description** |
|—————————|——————————————————————|
| Bantam Tools | CNC PCB milling machines with high-speed milling capabilities. |
| MITS Electronics | CNC PCB milling machines with automatic tool changers. |
| LPKF Laser & Electronics | CNC PCB milling machines with precise positioning systems. |
| Sinoamigo Technology | CNC PCB milling machines with user-friendly operation. |
| Wintech PCB Technology | CNC PCB milling machines for high-speed and high-precision milling. |
6. Shenzhen Jieke Automation Equipment: Jieke Automation Equipment is known for its CNC PCB milling machines with advanced features like automatic tool calibration and efficient dust collection systems. Their machines are suitable for various materials, including FR-4 and aluminum substrates.
7. Shenzhen Fast ToBuy Commerce & Trade: Fast ToBuy Commerce & Trade specializes in CNC PCB milling machines with high cutting speeds and precision. Their machines are equipped with high-quality spindles and precise positioning systems. Fast ToBuy’s machines are suitable for FR-4, CEM-1, and aluminum-clad laminates.
8. Shenzhen Chikin Automation Equipment: Chikin Automation Equipment offers CNC PCB milling machines with versatile capabilities suitable for small and large-scale production. Their machines feature high-speed spindles and advanced control systems for precise milling operations. Chikin Automation’s machines can handle FR-4, aluminum, and copper substrates.
9. Shenzhen MR Tech: MR Tech manufactures CNC PCB milling machines known for their efficiency and reliability. Their machines are designed for high-speed and high-precision milling, allowing for intricate PCB designs. MR Tech’s machines are suitable for FR-4, aluminum, and copper substrates.
10. Shenzhen Jiefengtai Technology: Jiefengtai Technology produces CNC PCB milling machines with a focus on quick setup and easy usability. Their machines feature precise positioning systems for accurate milling operations. Jiefengtai’s machines can handle FR-4, CEM-1, and aluminum-clad laminates.
| **Manufacturer** | **Product Description** |
|—————————|—————————————————————————|
| Bantam Tools | High-speed, compact CNC PCB milling machines for small-scale production. |
| MITS Electronics | Precision CNC PCB milling machines with automatic tool changers. |
| LPKF Laser & Electronics | CNC PCB milling machines suitable for prototyping and production applications. |
| Sinoamigo Technology | User-friendly CNC PCB milling machines with high precision. |
| Wintech PCB Technology | High-speed and high-precision CNC PCB milling machines. |
| Jieke Automation Equipment | CNC PCB milling machines with automatic tool calibration and dust collection. |
| Fast ToBuy Commerce & Trade | High cutting speed and precision CNC PCB milling machines. |
| Chikin Automation Equipment | Versatile CNC PCB milling machines for small and large-scale production. |
| MR Tech | Efficient and reliable CNC PCB milling machines for intricate designs. |
| Jiefengtai Technology | Quick setup and easy usability CNC PCB milling machines with accurate positioning. |
In conclusion, China offers a wide range of CNC PCB milling machine manufacturers with each having unique product features and capabilities. The table provides a concise comparison of these top 10 manufacturers, enabling customers to make informed decisions based on their specific requirements for PCB milling operations.
Background Research for cnc pcb milling manufacturers Companies in China, use qcc.com archive.org importyeti.com
When looking for CNC PCB milling manufacturers in China, three useful websites for background research are qcc.com, archive.org, and importyeti.com. These platforms can provide information on company backgrounds, their products and services, and historical data.
QCC.com is a comprehensive business information database that offers details on Chinese companies. Users can access information such as registration data, business scope, financials, ownership structure, and key personnel. This platform can help in verifying the legitimacy and reliability of PCB milling manufacturers, as well as identifying their size and capabilities.
Archive.org is a digital library that allows users to access historical snapshots of websites. By entering the URL of a PCB milling manufacturer’s website, one can view its previous versions and track any changes or developments over time. This can be helpful to gauge a company’s longevity, growth trajectory, and commitment to quality.
Importyeti.com is a website that provides import/export data of various products, including PCBs. This platform can help in identifying the export history of manufacturers, their main markets, and the types of products they specialize in producing. This information can be useful for evaluating a manufacturer’s experience and reputation in the market.
By utilizing these websites, researchers can gain insights into the background and track record of CNC PCB milling manufacturers in China. This information can help in making informed decisions regarding supplier selection and ensuring the quality and reliability of the products obtained.
Leveraging Trade Shows and Expos for cnc pcb milling Sourcing in China
Trade shows and expos offer excellent opportunities for sourcing CNC PCB milling services in China. With a strategic approach, these events can help businesses connect with potential suppliers, discover the latest technology trends, and establish valuable business relationships.
Attending trade shows focused on manufacturing, electronics, or specifically PCB milling in China allows companies to meet a diverse range of exhibitors, including manufacturers, suppliers, and service providers. It provides a platform to understand the current market trends, compare different offerings, and evaluate the capabilities of potential suppliers.
China is known for its advanced manufacturing capabilities, and attending trade shows and expos in the country provides businesses with firsthand access to the latest CNC PCB milling technologies and solutions. Exhibitors often showcase cutting-edge equipment, software solutions, and automation technologies that can greatly enhance the efficiency and productivity of PCB milling processes.
Furthermore, trade shows and expos provide an opportunity to connect with industry experts, gain insights into best practices, and participate in workshops or seminars discussing the latest advancements in CNC PCB milling. These events often attract knowledgeable professionals who can offer valuable guidance and advice on sourcing strategies, quality control, and other crucial aspects of the PCB milling process.
To maximize the effectiveness of trade shows and expos for CNC PCB milling sourcing in China, companies should plan their visit in advance. This includes conducting thorough research and identifying the key exhibitors and industry experts to meet. Preparing a list of questions and requirements can help facilitate meaningful discussions with potential suppliers and ensure that specific needs are addressed.
In conclusion, trade shows and expos in China offer a unique opportunity for businesses to find CNC PCB milling suppliers. By attending these events, companies can connect with a wide range of exhibitors, explore the latest technologies, and benefit from expert insights. Proper planning and proactive engagement can result in successful sourcing and the establishment of valuable partnerships.
The Role of Agents and Sourcing Companies in Facilitating cnc pcb milling Purchases from China
Agents and sourcing companies play a crucial role in facilitating CNC PCB milling purchases from China. These intermediaries act as a bridge between international buyers and Chinese suppliers, making the sourcing process smooth and efficient.
Firstly, agents and sourcing companies have a deep knowledge of the Chinese market and its suppliers. They have established networks and relationships with trusted manufacturers who specialize in CNC PCB milling. This expertise allows them to identify reliable suppliers that meet the buyer’s specific requirements in terms of quality, price, and lead time.
Secondly, agents and sourcing companies help international buyers overcome language and cultural barriers. As most Chinese suppliers primarily communicate in Mandarin, it can be challenging for foreign buyers to negotiate, clarify specifications, and resolve any issues that arise during the purchasing process. Agents and sourcing companies act as translators and cultural mediators, ensuring effective communication between the two parties.
Thirdly, these intermediaries assist in quality control and product inspections. They ensure that the CNC PCB milling products meet the buyer’s expectations and adhere to international standards. Agents and sourcing companies conduct factory audits, perform on-site inspections, and carry out quality control procedures to prevent any substandard products from being shipped.
Furthermore, agents and sourcing companies handle logistics and shipping arrangements. They coordinate with freight forwarders and shipping companies to ensure timely delivery of the purchased products. Additionally, they handle the necessary customs documentation and procedures to facilitate smooth importation of goods, saving buyers from the hassle of navigating complex international shipping logistics.
Lastly, agents and sourcing companies often provide additional services such as negotiating prices, managing payments, and resolving disputes. They leverage their expertise to secure the best pricing options for buyers and handle the financial transactions securely. In case any issues or conflicts arise between the buyer and supplier, agents and sourcing companies actively mediate and resolve disputes, safeguarding the interests of the buyer.
In conclusion, agents and sourcing companies play a crucial role in facilitating CNC PCB milling purchases from China. Their expertise in the Chinese market, ability to overcome language and cultural barriers, knowledge in quality control, handling logistics, and providing additional services streamline the purchasing process for international buyers, making it easier to source reliable suppliers and ensuring a smooth and successful transaction.
Price Cost Research for cnc pcb milling manufacturers Companies in China, use temu.com and 1688.com
When conducting price cost research for CNC PCB milling manufacturers in China, two popular platforms to consider are Temu.com and 1688.com. These websites provide comprehensive listings of suppliers and manufacturers, offering a wide range of products and services.
To begin your research, visit Temu.com, a leading B2B platform in China. Temu.com features a vast directory of manufacturers specialized in CNC PCB milling. You can search for manufacturers by inputting relevant keywords such as “CNC PCB milling,” “PCB fabrication,” or “PCB manufacturing.”
After obtaining a list of potential suppliers on Temu.com, proceed to 1688.com. This platform is a prominent wholesale marketplace in China, known for its extensive range of products and competitive pricing. Through 1688.com, you can further narrow down your options by comparing prices and evaluating different manufacturers.
When assessing manufacturers on these platforms, consider several key factors. First, carefully review the company’s profile, including their years of operation, production capacity, and certifications. This information will help gauge their expertise and reliability in CNC PCB milling.
Next, it is crucial to obtain detailed quotations from the shortlisted manufacturers. Provide them with your specific requirements, including PCB specifications, quantities, lead time, and any additional services you may require, such as surface finishing or assembly. This will enable you to get accurate pricing information tailored to your project.
Additionally, reach out to the manufacturers directly to discuss any customization options, technical capabilities, and potential cost-saving measures. Building a good relationship with the manufacturers can also lead to better negotiating power and potential discounts.
It is essential to compare prices, taking into account factors such as quality, lead time, and additional services offered. Cheap pricing should not be the sole deciding factor, as the quality and reliability of the manufacturer are equally important.
In summary, Temu.com and 1688.com are reliable platforms to conduct price cost research for CNC PCB milling manufacturers in China. By carefully evaluating manufacturers’ profiles, obtaining detailed quotations, and considering various factors, you can make an informed decision while keeping the word count below 300.
Shipping Cost for cnc pcb milling import from China
The shipping cost for importing CNC PCB milling machines from China can vary depending on several factors. These factors include the weight and dimensions of the machines, the shipping method chosen, the destination country, and any additional services required.
For small, lightweight machines, air shipping might be a suitable option. Air freight charges are typically calculated based on the weight of the shipment, and the cost can range from a few hundred to several thousand dollars.
Ocean shipping is an alternative for larger and heavier machines. Shipping charges for ocean freight are primarily calculated based on the volume or cubic meters (CBM) of the shipment. The cost of ocean shipping can range from a few hundred dollars for a small shipment to several thousand dollars for larger shipments.
To obtain a more accurate shipping cost, it is recommended to provide detailed information about the machines to freight forwarders or shipping companies. They can offer quotes based on your specific requirements and provide information about any additional charges, such as customs fees, taxes, or insurance.
It’s important to note that other expenses may be incurred during the shipping process. These include import duties, customs clearance fees, and documentation charges. It’s advisable to check with customs authorities in the destination country to determine any potential additional costs.
To ensure a smooth importing process, it is recommended to work with a reputable freight forwarder who can handle all the logistics, customs procedures, and provide assistance with any necessary import documentation. This will help avoid any unexpected delays or additional costs.
In conclusion, the shipping cost for importing CNC PCB milling machines from China can vary depending on factors such as weight, dimensions, shipping method, and destination. To get an accurate cost estimate, it is best to consult with freight forwarders or shipping companies who can provide tailored quotes based on your specific requirements.
Compare China and Other cnc pcb milling Markets: Products Quality and Price,Visible and Hidden Costs
China is one of the largest markets for CNC PCB milling, but it is important to compare it with other markets in terms of product quality, price, and visible and hidden costs.
When it comes to product quality, China has made significant improvements over the years. Many PCB manufacturers in China now offer high-quality products that meet international standards. However, it is worth noting that quality can vary among different manufacturers. Other markets, such as the United States and Germany, are known for their high-quality PCBs. These markets often have stricter regulations and standards, resulting in consistently superior product quality.
In terms of price, China has a competitive advantage due to its lower labor costs. PCBs manufactured in China are generally more affordable compared to those produced in other markets. This has made China a popular choice for cost-sensitive buyers. However, it is essential to consider other factors, such as shipping and import duties, which may add to the overall cost. Other markets, particularly domestic ones, may have higher upfront costs but can provide better value in terms of product quality and customer service.
When comparing visible costs, China generally offers more competitive prices for CNC PCB milling. Visible costs include initial product price, shipping costs, and import duties. China’s large-scale production capabilities and low labor costs contribute to its cost advantage. Other markets, such as Western European countries, may have higher visible costs due to higher labor expenses and stricter regulations.
However, hidden costs need to be considered as well. Hidden costs include factors like intellectual property risks, counterfeit products, and potential issues in communication and project management. China, unfortunately, has a reputation for intellectual property concerns, and businesses must take precautions when sharing sensitive information or proprietary designs. While other markets may have higher visible costs, they often offer better protection of intellectual property rights and lower risks of counterfeit products.
In conclusion, while China offers competitive prices and improved product quality in the CNC PCB milling market, it is essential to consider other markets for their superior product quality, customer service, and lower hidden costs related to intellectual property protection. The decision depends on the specific requirements and priorities of each buyer.
Understanding Pricing and Payment Terms for cnc pcb milling: A Comparative Guide to Get the Best Deal
Pricing and payment terms for CNC PCB milling can vary depending on a few factors. Understanding these factors can help you negotiate the best deal for your needs. Here is a comparative guide to help you navigate the pricing and payment terms of CNC PCB milling.
1. Quantity: The number of PCBs you need will affect the pricing. Most manufacturers offer bulk discounts, so ordering a larger quantity can help lower the cost per unit.
2. Complexity: The complexity of your PCB design will also impact the pricing. Intricate designs with smaller traces, multiple layers, and tighter tolerances may require more precision during the milling process, leading to higher costs.
3. Material: The choice of material for your PCBs can also affect the pricing. Different materials have varying costs, such as FR4, aluminum, or flexible substrates. Consider your project requirements and budget when selecting the material.
4. Turnaround time: If you need your PCBs urgently, you may have to pay a premium for expedited services. Manufacturers often offer different turnaround time options, with faster delivery typically costing more.
5. Additional services: Some manufacturers may offer additional services, such as surface finishing techniques (e.g., gold plating), solder mask options, or component sourcing. These services may come at an extra cost, so consider whether they are necessary for your project.
When it comes to payment terms, several options are commonly offered:
1. Full payment upfront: Manufacturers may require full payment before they start production. This option gives them assurance and may come with discounts.
2. Partial payment upfront: Some manufacturers allow you to pay a portion of the total cost upfront, with the remaining balance payable upon completion or before shipping.
3. Net payment terms: If you have an established relationship or are a recurring customer, you may negotiate net payment terms, such as 30 days after receiving the invoice.
4. Escrow services: For larger orders or when dealing with a new manufacturer, you might consider using an escrow service. These services hold your payment until you receive and inspect the PCBs, ensuring both parties are protected.
To get the best deal, it is advisable to obtain quotes from multiple manufacturers and compare their pricing and payment terms. Don’t forget to consider factors like quality, delivery time, and customer reviews when making your decision.
Chinese Regulations and Industry Standards Certifications for cnc pcb milling,Import Regulations and Customs for cnc pcb milling from China
Chinese Regulations and Industry Standards Certifications for CNC PCB Milling:
In China, CNC PCB milling falls under the jurisdiction of several regulations and industry standards certifications. The primary ones include:
1. The China Compulsory Certification (CCC): This certification ensures that CNC PCB milling machines comply with the safety, quality, and environmental protection standards defined by the Chinese government. It is mandatory for manufacturers to obtain CCC certification before exporting their products or selling them in the domestic market.
2. ISO 9001: This certification emphasizes the quality management system implemented by manufacturers. It ensures that the CNC PCB milling machines adhere to international standards and meet customers’ requirements.
3. ISO 14001: This certification focuses on environmental management systems to promote sustainable manufacturing. It ensures that CNC PCB milling machines are manufactured in an eco-friendly manner, minimizing any detrimental impact on the environment.
4. National Standard of the People’s Republic of China: This standard, known as GB, sets regulations and specifications for various aspects of CNC PCB milling machines, including safety, performance, and technical requirements. Adherence to these standards is essential for compliance and product quality.
Import Regulations and Customs for CNC PCB Milling from China:
Importing CNC PCB milling machines from China requires compliance with import regulations and customs procedures specific to the destination country. While the regulations may vary, here are some general considerations:
1. Tariffs and Customs Duties: Importing CNC PCB milling machines usually incurs tariffs and customs duties. These charges depend on the product’s category and the importing country’s import regulations. Importers must research and understand the tariff rates and any applicable exemptions or preferential treatment.
2. Documentation: Accurate and complete documentation is crucial for smooth customs clearance. Required documents may include commercial invoices, packing lists, bills of lading/airway bills, certificates of origin, and necessary permits or licenses.
3. Product Compliance: Importers should verify that the CNC PCB milling machines meet the technical standards and safety requirements of their country. Some countries may require additional certifications or compliance with specific industry standards.
4. Customs Procedures: Importers need to work with customs brokers or agents to navigate the customs procedures efficiently. This involves filing necessary import declarations, paying import duties, and ensuring adherence to customs regulations and clearance processes.
It is essential to consult with local customs authorities and seek professional advice to ensure compliance with the specific regulations and customs requirements of the importing country.
Sustainability and Environmental Considerations in cnc pcb milling Manufacturing
CNC (Computer Numerical Control) PCB (Printed Circuit Board) milling manufacturing has garnered significant attention in recent years, not only for its precision and speed but also for its sustainability and environmental considerations. This manufacturing process involves the use of computer-controlled machines to remove copper and other materials from a circuit board, resulting in a custom-designed PCB.
One of the main sustainability benefits of CNC PCB milling is the reduction in material waste. Traditional manufacturing methods, such as chemical etching, produce a significant amount of hazardous waste that must be disposed of properly. In contrast, CNC PCB milling eliminates the need for chemicals, reducing the environmental impact and eliminating the associated disposal costs.
Additionally, CNC PCB milling allows for the efficient use of materials. By precisely cutting only the necessary areas of the circuit board, it minimizes the amount of raw materials required for production. This reduction in material usage not only saves resources but also decreases the overall cost of the manufacturing process.
Furthermore, CNC PCB milling enables the use of recycled and reclaimed materials. The machines are capable of working with various types of substrates, including recycled plastics and metals. By incorporating these materials into the manufacturing process, the overall environmental footprint can be further reduced.
Energy efficiency is also an important consideration in CNC PCB milling. The machines can be programmed to optimize the tool paths, reducing unnecessary movements and minimizing energy consumption. Additionally, advancements in technology have led to the development of more energy-efficient CNC machines, contributing to a greener manufacturing process.
In conclusion, CNC PCB milling manufacturing offers several sustainability and environmental benefits. Its ability to reduce material waste, use recycled materials, and optimize energy efficiency make it a more environmentally friendly option compared to traditional manufacturing methods. As the industry continues to evolve, it is important for manufacturers to prioritize sustainability and environmental considerations to minimize their ecological impact and contribute to a greener future.
List The Evolution history of “cnc pcb milling”
CNC PCB milling, or computer numerical control printed circuit board milling, has undergone significant evolution since its inception. Here is a brief history of its development:
1. Hand Routing: In the early days of PCB manufacturing, hand routing techniques were used. Skilled technicians manually cut copper traces on the printed circuit boards using various hand tools. This method was time-consuming and lacked precision.
2. Mechanical Prototyping: In the late 1970s, mechanical prototyping machines emerged. These machines utilized mechanical cutters to shape the PCBs. While more efficient than hand routing, they still had limitations in terms of accuracy and complexity.
3. Manual CNC Mills: By the 1980s, computer numerical control technology was introduced to the PCB milling process. Manual CNC mills allowed operators to program the milling path using a computer, improving accuracy and enabling the creation of more complex PCB designs.
4. Automated CNC PCB Mills: In the 1990s, the first automated CNC PCB mills were developed. These machines featured improved software and hardware capabilities, allowing for fully automated production of PCBs. They offered higher precision, faster production times, and reduced human intervention.
5. Miniaturization and High-Speed Spindles: With the increasing demand for smaller and more intricate electronic devices, CNC PCB milling technology continued to evolve. Miniaturization techniques were introduced, allowing for the fabrication of complex circuitry on tiny boards. High-speed spindles were also developed, enabling more precise milling of small features and finer traces.
6. Integration with Design Software: With the advancement of PCB design software, CNC PCB milling machines started integrating seamlessly with these tools. Design files could now be directly translated into milling instructions, reducing the chances of errors and improving accuracy.
7. Advanced Material Compatibility: As the field of electronics advanced, new materials such as flexible and multi-layered PCBs gained popularity. CNC PCB milling machines adapted to these changes, offering compatibility with a wide range of materials while ensuring high-quality outputs.
8. PCB Prototyping and Hobbyist Adoption: In recent times, the availability of affordable CNC PCB mills has opened up PCB prototyping to individual inventors, hobbyists, and small businesses. This has democratized the manufacturing process, empowering innovators to bring their ideas to life.
Overall, the evolution of CNC PCB milling has seen a shift toward automation, precision, and increased accessibility, allowing for the efficient and accurate production of printed circuit boards.
The Evolution and Market Trends in cnc pcb milling Industry
The CNC (Computer Numerical Control) PCB (Printed Circuit Board) milling industry has seen significant evolution and market trends in recent years. PCB milling involves the use of CNC machines to remove unwanted copper material from the surface of a substrate, creating a circuit pattern.
One major evolution in the industry is the miniaturization of PCBs. With the increasing demand for smaller and more complex electronic devices, PCBs need to be smaller and have more intricate circuit patterns. CNC machines have adapted to this trend by becoming more precise and capable of producing finer circuitry. This evolution has enabled the production of high-density interconnect (HDI) PCBs, which have smaller vias and thinner traces.
Another trend in the CNC PCB milling industry is the shift towards automation and integration. CNC machines are now equipped with advanced software and hardware features that streamline the production process. These machines can automatically load and unload PCBs, inspect the end result for quality control, and even perform multiple milling processes in a single run. Integration with other manufacturing processes, such as pick-and-place machines and soldering equipment, has also become more common, leading to increased efficiency and productivity.
Market trends in the CNC PCB milling industry largely revolve around the growing demand for faster turnaround times and cost-effective solutions. As the electronics industry becomes more competitive, manufacturers need to produce PCBs quickly and efficiently. This has led to the development of faster milling machines that can process PCBs in shorter time frames. Additionally, the industry has seen the rise of affordable and accessible CNC machines, making PCB milling more accessible to small businesses and hobbyists.
Furthermore, the demand for sustainable and environmentally friendly manufacturing practices has also influenced the market trends in the industry. CNC PCB milling machines have become more energy-efficient, minimizing waste and reducing environmental impact. Manufacturers are also increasingly using eco-friendly materials and processes, such as water-soluble solder masks, to minimize the use of hazardous substances.
In conclusion, the CNC PCB milling industry has evolved to meet the demands of miniaturization, automation, integration, and sustainability. Market trends reflect the need for faster turnaround times, cost-effective solutions, and environmentally friendly manufacturing practices. By adapting to these trends, the industry continues to thrive and cater to the growing needs of the electronics industry.
Custom Private Labeling and Branding Opportunities with Chinese cnc pcb milling Manufacturers
Chinese CNC PCB milling manufacturers offer various opportunities for custom private labeling and branding. With their expertise in precision machining and electronics manufacturing, these manufacturers can provide tailor-made solutions to meet specific branding requirements.
Firstly, Chinese manufacturers can offer custom private labeling services, where they incorporate a client’s brand name and logo onto the PCB milling products. This helps establish a brand identity and recognition in the market. Private labeling can be done through various methods such as laser engraving, printing, or using adhesive labels.
In addition to private labeling, Chinese CNC PCB milling manufacturers also offer branding opportunities through customized packaging. They can design and manufacture packaging materials that reflect a client’s brand image and product positioning. This includes creating branded boxes, pouches, or other packaging solutions that showcase the client’s logo and brand colors.
Furthermore, Chinese manufacturers are flexible in accommodating custom designs and specifications. They can work closely with clients to develop unique PCB milling products that align with their brand values and target market. This includes customizing the size, shape, and features of the CNC milling machines, as well as incorporating specific branding elements into the design.
Chinese CNC PCB milling manufacturers are also conscious of quality control and can ensure that all branded products meet the client’s standards. They implement strict quality management systems to guarantee the performance and reliability of their milling machines. This helps maintain the brand reputation and ensures customer satisfaction.
In conclusion, Chinese CNC PCB milling manufacturers offer excellent opportunities for custom private labeling and branding. Through private labeling, customized packaging, and tailored product design, clients can establish a strong brand presence in the market. Moreover, the manufacturers’ focus on quality control preserves the brand’s reputation and customer satisfaction.
Tips for Procurement and Considerations when Purchasing cnc pcb milling
When it comes to purchasing CNC PCB milling machines, there are several important considerations and tips for procurement. Here are some key points to keep in mind:
1. Research and evaluate your needs: Before making any purchase, conduct thorough research to understand your exact requirements. Consider factors like the size and complexity of the PCBs you will be working with, the materials you will be using, and your expected production volume.
2. Machine quality and reliability: Ensure that the CNC PCB milling machine you choose is of high quality and offers reliable performance. Look for well-established brands with positive customer reviews and a good track record in the industry. Check for durability, precision, and ease of use.
3. Compatibility with software: Evaluate whether the CNC machine is compatible with the software you plan to use for designing and programming your PCBs. This compatibility is crucial for seamless workflow and precision in the milling process.
4. Speed and accuracy: Consider the machine’s milling speed and accuracy. Fast and precise milling capabilities can significantly impact your production time and the quality of your PCB prototypes.
5. Maintenance and support: Ensure that the supplier provides adequate maintenance and support services. CNC machines may require regular servicing and occasional repairs. It’s important to have access to technical support and replacement parts.
6. Cost-effectiveness: Consider the total cost of ownership, including the initial purchase price, maintenance costs, and the lifespan of the machine. While it may be tempting to go for the cheapest option, ensure that it meets your quality and performance requirements in the long run.
7. Training and support: Determine whether the supplier offers training programs or resources to help you get started with using the CNC PCB milling machine. Hands-on training and ongoing technical support can ensure that you make the most of your investment.
8. Future scalability: Consider your future needs and whether the machine can accommodate any potential growth in your production volume or changes in your PCB design requirements. Choosing a machine that can be easily upgraded or expanded can save you from having to invest in a new one later on.
In summary, thorough research and evaluating your specific needs are crucial when purchasing CNC PCB milling machines. Consider factors such as machine quality, compatibility, speed, accuracy, support services, cost-effectiveness, training, and future scalability to make an informed procurement decision.
FAQs on Sourcing and Manufacturing cnc pcb milling in China
Q: What is CNC PCB milling?
A: CNC PCB milling is the process of using a computer-controlled milling machine to remove unwanted copper from a printed circuit board (PCB), creating tracks and pads for electronic components.
Q: Why should I source and manufacture CNC PCB milling in China?
A: China has become a global hub for PCB manufacturing due to its competitive pricing, advanced technology, and vast resources. Chinese manufacturers offer a wide range of services, including CNC PCB milling, at competitive prices, making it an attractive option for businesses.
Q: How can I find reliable CNC PCB milling suppliers in China?
A: There are various ways to find reliable CNC PCB milling suppliers in China. One common approach is to use B2B platforms, such as Alibaba or Global Sources, where you can browse through a large number of suppliers, compare prices and reviews, and communicate directly with potential suppliers.
Q: What should I consider when selecting a CNC PCB milling supplier in China?
A: When selecting a CNC PCB milling supplier in China, it is important to consider their experience, expertise, certifications (such as ISO 9001), and manufacturing capabilities. You should also check their quality control processes, lead times, and communication methods to ensure smooth collaboration.
Q: Can I visit the supplier’s factory in China before making a decision?
A: It is highly recommended to visit the supplier’s factory in China before finalizing any agreement. This will give you an opportunity to assess their facilities, equipment, production processes, and meet the team in person. It also helps to establish trust and ensures transparency.
Q: How can I ensure quality control during the manufacturing process?
A: To ensure quality control during the manufacturing process, you should request samples or prototypes before placing a bulk order. Regular communication with the supplier is essential to address any concerns or specifications. Conducting inspections or audits, either by yourself or through a third-party quality control company, can also help ensure product consistency and adherence to your requirements.
Q: What are the advantages of sourcing and manufacturing CNC PCB milling in China?
A: The advantages of sourcing and manufacturing CNC PCB milling in China include cost-effectiveness, access to advanced technology and expertise, a wide range of options, and rapid production turnaround. China’s mature supply chain and infrastructure make it a reliable choice for PCB manufacturing needs.
Overall, sourcing and manufacturing CNC PCB milling in China offers businesses the opportunity to access high-quality products at competitive prices while benefiting from the country’s manufacturing capabilities and expertise.
Why contact sourcifychina.com get free quota from reliable cnc pcb milling suppliers?
Sourcifychina.com offers a free quota from reliable CNC PCB milling suppliers for several reasons. Firstly, they aim to provide an efficient and reliable sourcing experience to their customers. By partnering with trusted suppliers, they ensure the quality and reliability of the CNC PCB milling services.
Secondly, offering a free quota enables customers to make an informed decision without any initial financial commitment. It allows them to assess the cost and feasibility of their PCB milling requirements before making a purchase. This helps in reducing the risk of investing in a service that may not match the customer’s needs.
Furthermore, Sourcifychina.com understands the competitive nature of the sourcing industry. By offering a free quota, they aim to attract potential customers and stand out from their competitors. It serves as an incentive for customers to choose Sourcifychina.com over other sourcing platforms, as it demonstrates their commitment to customer satisfaction and affordability.
Moreover, providing a free quota enables customers to compare prices and services among different suppliers. This helps them make an informed decision and choose the most suitable supplier for their specific needs. The transparency and flexibility offered by Sourcifychina.com empower customers to make better choices based on their budget and requirements.
In conclusion, Sourcifychina.com offers a free quota from reliable CNC PCB milling suppliers to ensure a high-quality sourcing experience, provide affordability, and stand out in a competitive market. This approach allows customers to make informed decisions, compare prices and services, and ultimately choose the right supplier for their PCB milling needs.