Introduce about metal parts guide,Qulity,Cost,Supplier,Certification,Market,Tips,FAQ
Metal parts guide provides comprehensive information about various metal parts used in different industries, offering guidance on their selection, manufacturing processes, and applications. This guide encompasses details regarding the quality, cost, suppliers, certifications, market trends, as well as useful tips and frequently asked questions.
Quality is a crucial aspect while considering metal parts. The guide highlights the importance of high-quality materials, precise manufacturing techniques, and stringent quality control measures to ensure superior performance and durability. It provides insights into various quality standards and certifications that metal parts should meet, such as ISO, ASTM, and DIN, ensuring compliance with industry norms.
Cost considerations are another essential aspect addressed in the guide. It includes factors influencing the cost of metal parts, such as material selection, complexity of design, production volume, and finishing requirements. Moreover, it offers cost-saving strategies, like value engineering and optimization of manufacturing processes, enabling businesses to make informed decisions while minimizing expenses.
Finding reliable suppliers is a critical element in the metal parts industry. The guide provides valuable tips on selecting trustworthy suppliers who maintain high standards in terms of quality, timely delivery, and competitive pricing. It also emphasizes the importance of supplier evaluation, including their industry experience, manufacturing capabilities, and customer reviews.
Certification plays a vital role in ensuring the reliability and quality of metal parts. The guide sheds light on various certifications such as RoHS, REACH, and UL, which assure compliance with environmental regulations, safety standards, and product performance requirements. Understanding certification requirements aids businesses in building trust with customers and complying with legal obligations.
Understanding market trends and dynamics is essential to stay competitive in the metal parts industry. The guide covers market analysis, including market size, growth projections, and emerging opportunities. It also provides insights into key market players and their strategies, helping businesses stay updated with the latest industry developments.
The guide offers useful tips and best practices for selecting, specifying, and testing metal parts, facilitating informed decision-making. It addresses frequently asked questions related to material selection, manufacturing processes, finishing techniques, and quality control, providing a comprehensive resource for businesses and individuals.
In conclusion, the metal parts guide serves as a comprehensive resource, covering various aspects such as quality, cost, suppliers, certifications, market trends, tips, and FAQs. It empowers businesses with valuable knowledge to make informed decisions, ensuring the selection of high-quality metal parts that meet their specific requirements.
Types of metal parts
There are several types of metal parts that are commonly used in various industries:
1. Fasteners: Fasteners include screws, bolts, nuts, and washers. They are used to hold components together and provide a secure connection. Fasteners come in different sizes and shapes to suit different applications.
2. Springs: Springs are elastic metal components that store mechanical energy when compressed or stretched and release it when the force is released. They are used in various applications, such as automotive suspensions, mattresses, and toys.
3. Shafts: Shafts are cylindrical metal rods used to transmit rotational motion or torque in machines. They often have keyways or splines to connect with other components, such as gears or pulleys. Shafts are commonly found in engines, pumps, and conveyor systems.
4. Bearings: Bearings are metal parts that support and reduce friction in rotating machinery. They enable smooth movement and facilitate power transmission. Some commonly used types include ball bearings, roller bearings, and plain bearings.
5. Connectors and Fittings: Metal connectors and fittings are utilized to join pipes, tubes, or cables. Examples include couplings, adapters, elbows, tees, and flanges. These parts are crucial for plumbing, HVAC systems, and various industrial applications.
6. Stamped Parts: Stamped parts are metal components produced using a stamping process where a sheet metal is shaped between dies. These parts often have complex shapes and can be found in appliances, automotive components, and electrical equipment.
7. Castings: Castings are metal parts made by pouring molten metal into a mold, allowing it to solidify and take the shape of the mold cavity. Castings are used to create intricate and customized components, such as engine blocks, machine bases, and decorative pieces.
8. Extrusions: Extrusions are metal parts formed by forcing metal through a die to create a cross-sectional shape. This process is commonly used for aluminum and is used in the production of window frames, tubing, and structural components.
9. Brackets and Mounts: Brackets and mounts are metal parts used for supporting and attaching components. They are used in various industries, such as automotive, aerospace, and construction.
10. Electrical Contacts: Electrical contacts are metal parts used to establish electrical connections between conductors. They are found in switches, connectors, relays, and circuit breakers.
These are just a few examples of the many different types of metal parts used in various industries. Each type serves a specific purpose and plays a crucial role in the functioning of different products and systems.
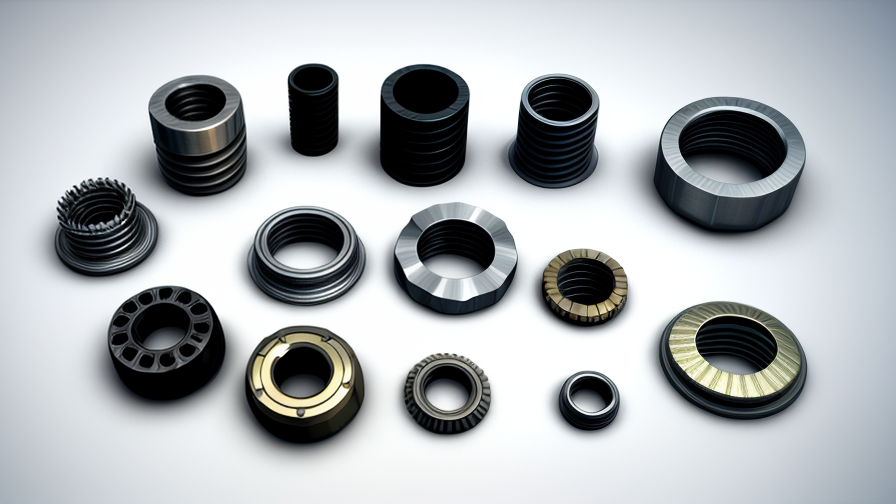
Pros and Cons of Using metal parts
Metal parts are widely used in various industries due to their numerous advantages, but they also have some limitations. Here are some pros and cons of using metal parts:
Pros:
1. Strength and Durability: Metal parts are known for their high strength and durability, making them ideal for applications that require heavy loads and extreme conditions.
2. Resistance to Heat and Corrosion: Metals like stainless steel and titanium exhibit excellent resistance to heat and corrosion, making them suitable for applications in harsh environments.
3. Versatility: Metal parts can be easily fabricated into different shapes and sizes, allowing for customization based on specific requirements. They can also be combined with other materials to create hybrid components.
4. Electrical and Thermal Conductivity: Many metals have good electrical and thermal conductivity, making them essential for applications such as electrical wiring, heat sinks, and circuit boards.
5. Recyclability: Metals can be recycled repeatedly without losing their properties, making them eco-friendly and cost-effective in the long run.
Cons:
1. Weight: Metals are generally heavier compared to other materials such as plastics. This can be a drawback in applications where weight reduction is necessary, such as in the automotive or aerospace industries.
2. Cost: Metal parts are often more expensive to produce than parts made from other materials. The cost of raw materials, manufacturing processes, and specialized equipment results in higher production costs.
3. Corrosion: While some metals have excellent corrosion resistance, others are prone to rust and oxidation when exposed to moisture or certain chemicals. Protective coatings or additional treatments may be required to mitigate this.
4. High Thermal Conductivity: While high thermal conductivity is desirable in many applications, it can be a disadvantage in others, where heat needs to be insulated or transferred in a controlled manner.
5. Difficulty in Fabrication: Some metals, especially those with high melting points like titanium, can be challenging to work with during fabrication processes such as welding or machining.
Overall, the use of metal parts offers significant benefits such as strength, durability, and resistance to heat and corrosion. However, factors like weight, cost, and corrosion susceptibility should be carefully considered based on the specific application to determine if metal parts are the most appropriate choice.
metal parts Reference Specifications (varies for different product)
Metal parts are commonly used in various products across industries such as automotive, aerospace, construction, electronics, and more. These parts play a crucial role in providing strength, durability, and functionality to the final product. Different products require specific reference specifications depending on their design, application, and quality requirements. Here are some common reference specifications for metal parts:
1. Material Composition: The choice of metal alloy used for the part depends on factors like mechanical properties, corrosion resistance, and cost. Common materials include carbon steel, stainless steel, aluminum, brass, and titanium.
2. Dimensions and Tolerances: Accurate dimensions and tight tolerances are critical for proper fit, alignment, and functionality of the parts. Dimensions are usually specified based on height, width, length, or diameter, while tolerances define the acceptable deviation from the exact measurements.
3. Surface Finish: The surface finish of metal parts can affect their appearance, corrosion resistance, and ease of cleaning. Specifications for surface finish may include parameters like roughness average (Ra) values, specific coatings, or plating requirements.
4. Heat Treatment: Depending on the desired mechanical properties, metal parts may require heat treatment processes such as annealing, quenching, or tempering. Specific temperature ranges, cooling rates, and hold times may be specified for each heat treatment process.
5. Strength and Hardness: Components that need high strength or hardness may require specific reference specifications for ultimate tensile strength (UTS), yield strength, or Rockwell Hardness (HRC) values.
6. Mechanical Testing: Metal parts may undergo various mechanical tests to ensure their quality and performance. Common tests include tensile testing, impact testing, fatigue testing, and hardness testing.
7. Welding and Joining Specifications: If the metal parts require welding or joining, specific welding techniques, filler materials, pre-heating temperatures, and post-weld heat treatment (PWHT) processes may be specified.
8. Surface Protection: Metal parts exposed to harsh environments may need protective coatings or treatments to prevent corrosion or wear. Specifications for surface protection may include requirements for galvanizing, powder coating, or plating.
9. Electrical Conductivity: Certain applications, like electrical components, require specific electrical conductivity properties in metal parts. Specifications for electrical conductivity may include resistivity or conductivity values.
10. Regulatory Standards: Depending on the industry or application, metal parts may need to comply with specific international or industry standards such as ISO, ASTM, or ASME.
It is essential to consider these reference specifications during the design, manufacturing, and quality control stages to ensure that the metal parts meet the desired requirements and perform optimally in their respective applications.
Applications of metal parts
Metal parts have a wide range of applications across various industries due to their durability, strength, and versatility. Let’s explore some key applications of metal parts:
1. Automotive Industry: Metal parts are extensively used in vehicles for their structural integrity and ability to withstand high temperatures. They are found in engine components, chassis, body panels, exhaust systems, and suspension systems.
2. Aerospace and Aviation: Metal parts such as titanium, aluminum, and alloys are used in aircraft manufacturing. They provide lightweight strength and resistance to corrosion, making them essential for critical components like the airframe, landing gear, engine parts, and fasteners.
3. Construction: Metal parts like steel beams, columns, and reinforcement bars are widely used in the construction industry. They provide support, structural integrity, and durability to buildings, bridges, and infrastructure projects.
4. Consumer Goods: Metal parts are found in a wide range of consumer goods, including appliances (ovens, refrigerators), electronics (computers, smartphones), furniture (desks, chairs), and kitchenware (utensils, cookware). They offer longevity and stability to these products.
5. Energy Sector: Metal parts are integral to power generation and distribution. They are used in turbines, generators, transformers, transmission lines, and nuclear power plants. Metals like copper and aluminum are especially valuable for their electrical conductivity.
6. Medical Industry: Metal parts find applications in medical devices and equipment due to their biocompatibility and strength. They are used in implants, surgical instruments, prosthetics, and diagnostic equipment.
7. Industrial Equipment: Metal parts are crucial in manufacturing machinery and equipment. They are used in conveyors, press tools, machining tools, pumps, valves, and robots. Metal components withstand heavy loads and provide precision in industrial processes.
8. Defense and Security: Metal parts are essential in the defense sector for their strength and ballistic resistance. They are used in tanks, armored vehicles, ships, aircraft carriers, and firearms.
9. Oil and Gas Industry: Metal parts are used extensively in this sector due to their ability to withstand harsh environments and high-pressure conditions. They are used in drilling rigs, pipelines, valves, and storage tanks.
10. Recycling: Metal parts have a high recycling value and can be easily recycled into new products. Many industries rely on recycled metal parts to reduce environmental impact and conserve resources.
In summary, metal parts have diverse applications across numerous industries, contributing to the development of infrastructure, transportation, manufacturing, energy, healthcare, and more. Their durability, strength, and versatility make them an integral part of modern society.
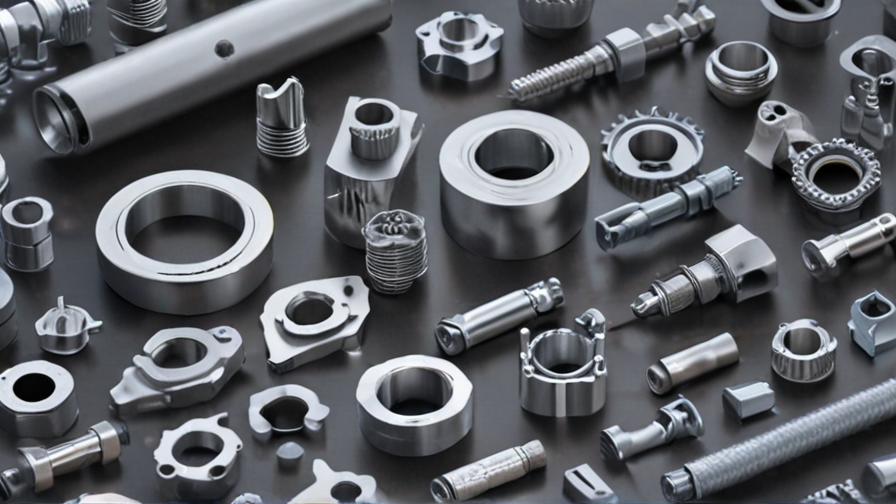
The Work Process and how to use metal parts
The work process of using metal parts involves several steps to ensure the desired outcome. First, the design and engineering phase is crucial, where metal parts are carefully planned and created using computer-aided design (CAD) software. This phase also involves determining the material, dimensions, and specific requirements of the metal parts.
Once the design is finalized, the next step is the fabrication process. This typically involves a variety of methods such as cutting, machining, and forming. Cutting involves using tools like saws or lasers to shape the metal parts according to the design. Machining is the process of removing excess material using techniques like drilling, milling, or turning. Forming involves bending or shaping the metal parts using methods like stamping or forging.
After the fabrication process, the metal parts undergo a finishing process to enhance their appearance, durability, or functionality. This may involve surface treatments like polishing, plating, or coating to protect the metal from corrosion or improve its aesthetics. It may also include processes like heat treatment to enhance strength or hardness.
Finally, the metal parts are assembled or integrated into the desired product or system. This may involve welding, soldering, or mechanical fastening methods like screws or bolts. The assembly process ensures that the metal parts are securely connected and function as intended.
To effectively use metal parts, it is essential to understand their properties, limitations, and proper handling techniques. Different metals have varying strengths, corrosion resistance, and thermal properties. Understanding these properties helps in selecting the appropriate metal for a specific application and ensures that the metal parts will perform optimally under various conditions.
Additionally, it is crucial to follow proper safety precautions when working with metal parts. This includes wearing protective gear like gloves and goggles, using tools and equipment correctly, and handling sharp or hot metal parts with care. It is also important to follow any specific instructions or guidelines provided by manufacturers.
In summary, the work process of using metal parts involves design and engineering, fabrication, finishing, and assembly. Understanding the properties of metals and following proper safety guidelines are essential to effectively utilize metal parts in various applications.
Quality Testing Methods for metal parts and how to control the quality
There are several quality testing methods used for metal parts to ensure their integrity and reliability. These methods help manufacturers maintain control over the quality of their products. Some common quality testing methods for metal parts include:
1. Visual Inspection: This involves inspecting the metal parts visually for any visible defects such as cracks, scratches, or irregular shapes.
2. Dimensional Measurement: The dimensions of metal parts are measured using various equipment like calipers, micrometers, or coordinate measuring machines (CMM). This ensures that the metal parts meet the required specifications.
3. Hardness Testing: A hardness test is performed to determine the hardness of the metal part. This helps assess the material’s strength and resistance to deformation.
4. Chemical Composition Analysis: To ensure the metal part is composed of the correct materials, chemical composition analysis is conducted using techniques like spectroscopy or X-ray fluorescence.
5. Non-Destructive Testing (NDT): NDT methods like ultrasonic testing, magnetic particle inspection, or dye penetrant inspection are employed to detect any hidden flaws, cracks, or defects in the metal parts without damaging them.
To control the quality of metal parts, manufacturers can implement the following measures:
1. Set Clear Specifications: The manufacturer should establish clear specifications and standards that define the required quality of the metal parts. This ensures that the production process is aligned with the desired quality level.
2. Regular Inspection and Testing: Regular inspections and testing must be conducted at different stages of the manufacturing process to identify and correct any quality issues promptly.
3. Employee Training: Proper training programs should be conducted to educate employees about quality standards, testing methods, and the importance of adhering to quality control procedures.
4. Standard Operating Procedures (SOPs): Standard operating procedures should be established to define the correct procedures for manufacturing, testing, and quality control. Adherence to these SOPs facilitates consistency and minimizes errors.
5. Corrective and Preventive Actions: Any quality issues identified during testing or inspection should be documented and addressed through appropriate corrective and preventive actions. This helps prevent reoccurrence of similar issues in the future.
By employing these quality testing methods and implementing stringent quality control measures, manufacturers can ensure the production of reliable and high-quality metal parts.
metal parts Sample Policy and Post-Purchase Considerations for metal parts from China
Sample Policy:
When purchasing metal parts from China, it is crucial to have a comprehensive sample policy in place to ensure the quality and reliability of the products. The following considerations should be taken into account:
1. Sample Requirements: Clearly outline the specifications, dimensions, and material requirements for the metal parts. Provide detailed drawings or samples to the supplier for replication.
2. Sample Approval Process: Establish a systematic process for sample evaluation and approval. This may include conducting rigorous tests, inspections, and assessments to ensure that the metal parts meet the desired standards.
3. Communication with Suppliers: Maintain open and frequent communication with the supplier during the sample development stage. Address any concerns or modifications promptly to avoid delays or misunderstandings.
4. Sample Production Costs: Determine the responsibility for sample production costs. It is common for the buyer to bear these expenses; however, negotiations should be made with the supplier to mitigate potential costs.
Post-Purchase Considerations:
After purchasing metal parts from China, certain considerations should be taken into account to mitigate potential risks and ensure overall satisfaction:
1. Quality Control: Implement strict quality control measures during production and before shipment. Conduct thorough inspections to verify that the metal parts meet the agreed-upon specifications and quality requirements.
2. Testing: Consider conducting independent testing on the received metal parts to validate their quality, performance, and compliance with relevant industry standards.
3. Proactive Feedback: Provide timely and clear feedback to the supplier regarding any issues or concerns encountered during or after purchase. Effective communication can help resolve problems promptly and improve future purchases.
4. Long-Term Relationship: Establish a long-term relationship with reliable suppliers. Building trust and understanding will lead to smoother transactions and better product quality over time.
5. Record Keeping: Maintain detailed records of all transactions, including purchase orders, agreements, communications, and inspection reports. These records can be valuable references for future purchases or resolving disputes if necessary.
By having a well-defined sample policy and considering these factors post-purchase, buyers can increase the likelihood of obtaining high-quality metal parts from China and minimize any potential risks associated with the purchase.
Sourcing metal parts from China: Opportunities, Risks, and Key Players
Sourcing metal parts from China presents a wealth of opportunities for businesses worldwide. China is famously known for its large-scale manufacturing capabilities, technological advancements, and cost-effective production. These factors make it an attractive destination for companies seeking metal parts for various industries, such as automotive, construction, electronics, and machinery.
One major opportunity of sourcing metal parts from China is the extensive range of options available. Chinese manufacturers offer a vast selection of metal parts, including precision components, castings, forgings, and sheet metal parts. This enables businesses to find suitable suppliers that meet their specific requirements, regardless of the complexity or volume of their products.
Moreover, the cost advantages of outsourcing metal parts production to China cannot be ignored. Chinese manufacturers often price their products significantly lower than their counterparts in other countries. This cost-effectiveness is a result of various factors, such as lower labor costs, economies of scale, and government incentives.
However, there are risks associated with sourcing metal parts from China that businesses should be mindful of. Quality control can be a challenge, especially when dealing with numerous suppliers and production facilities. Close monitoring and regular inspections are crucial to ensure adherence to required standards and specifications. Intellectual property protection is another key concern, as unauthorized replication or counterfeiting is a prominent issue in China. Adequate legal protections and confidentiality agreements should be in place to mitigate these risks.
When it comes to key players in the Chinese metal parts industry, a few prominent companies stand out. Examples include Foxconn Technology Group, a major electronics manufacturing company with a significant metal parts division, and China Precision Steel Inc., a leading supplier of precision steel products. Additionally, China International Marine Containers (CIMC) specializes in manufacturing metal parts related to transportation equipment, such as containers and trailers.
In conclusion, sourcing metal parts from China offers considerable opportunities, particularly in terms of the wide range of options available and cost-effectiveness. However, businesses need to be aware of the risks involved, such as quality control and intellectual property protection. By carefully selecting reliable suppliers and implementing stringent quality assurance measures, companies can successfully leverage the advantages that China’s metal parts industry provides.
How to find and select reliable metal parts manufacturers in China,use google search manufacturers and suppliers
Finding reliable metal parts manufacturers in China can be a daunting task, but with the help of Google search, it is possible to identify and select trustworthy manufacturers and suppliers. Here are some steps to follow:
1. Define your requirements: Before starting your search, clearly define the specifications and requirements for the metal parts you need. This will help you in finding manufacturers who specialize in producing the specific parts you require.
2. Start with a Google search: Begin by performing a Google search using relevant keywords such as “metal parts manufacturers in China” or “reliable metal parts suppliers.” This will yield a list of potential manufacturers who have websites and online presence.
3. Evaluate the websites: Visit the websites of the manufacturers that appear in your search results. Look for information about their history, production capabilities, certifications, quality control processes, and customer reviews/testimonials. A well-designed and informative website can indicate a more professional and reliable manufacturer.
4. Check company details: Verify the company details provided on their website, such as their physical address, contact information, and business licenses. Valid and transparent contact details increase the credibility of the manufacturer.
5. Review product samples: Request product samples or catalogues from potential manufacturers. Reliable manufacturers should be willing to provide samples for quality evaluation. Examine the quality, finishing, and precision of the samples to assess their manufacturing capabilities.
6. Online presence and reputation: Search for the manufacturer’s name on various online platforms and forums to check for reviews and feedback from their existing or past customers. Evaluate their reputation based on the feedback received and any positive or negative experiences shared.
7. Communication and responsiveness: Contact the potential manufacturers and assess their responsiveness and communication skills. Prompt and clear responses to your queries indicate their professionalism and commitment to customer service.
8. Request for quotations: Finally, shortlist a few manufacturers and request quotations for your specific metal parts. Compare their prices, lead times, and payment terms. Choose the manufacturer who offers competitive pricing along with their reliability and quality.
In conclusion, while using Google search to find metal parts manufacturers in China, it is crucial to conduct thorough research, evaluate their websites, check for reviews and feedback, review product samples, and communicate with the shortlisted manufacturers to find a reliable supplier that best meets your needs.
How to check metal parts manufacturers website reliable,use google chrome SEOquake check if ranking in top 10M
One way to check the reliability of a metal parts manufacturers website is by using Google Chrome’s SEOquake extension. This handy tool allows you to check the website’s ranking in the top 10 million websites globally based on its Alexa traffic rank. Here’s how you can use it:
1. Install the SEOquake extension: Open the Google Chrome browser, go to the Chrome Web Store, search for “SEOquake,” and click on the “Add to Chrome” button to download and install the extension.
2. Visit the metal parts manufacturer’s website: Go to the website of the metal parts manufacturer you want to check.
3. Activate SEOquake: Once the website loads, click on the SEOquake icon in the Chrome toolbar to activate it. The icon looks like a magnifying glass with the letter “SQ” on it.
4. Check the Alexa rank: After activating SEOquake, a toolbar will appear on the top of the website. Look for the “Alexa Rank” section. If the website’s ranking is within the top 10 million sites globally, it indicates a certain level of popularity and reliability.
By using SEOquake and checking the Alexa ranking, you can get a rough idea of the website’s reliability and popularity. However, it is important to note that this ranking should not be the sole determinant of reliability. Other factors, such as customer reviews, certifications, and years of experience, should also be considered.
Remember to exercise caution when assessing the reliability of a metal parts manufacturer’s website and consider multiple factors before making a decision.
Top 10 metal parts manufacturers in China with each 160 words introduce products,then use markdown create table compare
1. Foxron Precision Metal Parts Co., Ltd. is a leading metal parts manufacturer in China. They specialize in producing high precision metal components such as aluminum extrusions, CNC machined parts, die casting parts, and sheet metal parts. Their products are widely used in industries like electronics, automotive, medical, and telecommunications.
2. Dongguan Thriving Metal Parts Co., Ltd. offers a comprehensive range of metal parts including CNC machined parts, stamping parts, die casting parts, and screws. They focus on providing customized solutions to meet specific customer requirements. Their products are known for their high precision, durability, and excellent finishing.
3. Ningbo OEM Industry Manufacturer Ltd. is a well-established metal parts manufacturer in China. They provide a wide range of metal products such as CNC machined parts, stamping parts, and die casting parts. Their products are used in various industries including automotive, electronics, and machinery.
4. Shanghai M-HE Mechanical Equipment Co., Ltd. specializes in manufacturing precision metal parts for industries such as automotive, aerospace, and electronics. Their products include CNC machined parts, stamping parts, and die casting parts. They are known for their strict quality control measures and on-time delivery.
5. Xiamen Rising Mechanical Import & Export Co., Ltd. is a leading manufacturer of metal parts in China. They offer a wide range of products including CNC machined parts, stamping parts, and sheet metal fabrication. Their products are known for their high precision, excellent performance, and competitive prices.
6. Hangzhou Aunov Tech Co., Ltd. specializes in manufacturing metal parts such as aluminum profiles, CNC machined parts, and sheet metal fabrication. Their products are widely used in industries such as construction, electronics, and automotive. They are committed to delivering high-quality products and providing excellent customer service.
7. Suzhou Kairlo Machinery & Electronics Co., Ltd. is a professional metal parts manufacturer in China. They offer a wide range of products including CNC machined parts, stamping parts, and sheet metal fabrication. Their products are known for their precision, durability, and cost-effectiveness.
8. Shenzhen Arvin Industries Co., Ltd. is a leading metal parts manufacturer in China. They specialize in producing high-quality CNC machined parts, die casting parts, stamping parts, and sheet metal fabrication. Their products are widely used in industries like electronics, telecommunications, and automotive.
9. Wuxi Baide Precision Machinery Co., Ltd. is a renowned metal parts manufacturer in China. They provide a wide range of products including CNC machined parts, sheet metal fabrication, and stamping parts. Their products are highly appreciated for their precision, durability, and competitive prices.
10. Guangzhou Shengcheng Metal Products Co., Ltd. is a reliable manufacturer of metal parts in China. They offer a comprehensive range of products including CNC machined parts, die casting parts, and stamping parts. Their products are widely used in industries such as automotive, electronics, and machinery.
| Manufacturer | Specializations | Key Features |
|————-|—————–|—————-|
| Foxron Precision Metal Parts Co., Ltd. | Aluminum extrusions, CNC machined parts, die casting parts, sheet metal parts | High precision, wide industry usage |
| Dongguan Thriving Metal Parts Co., Ltd. | CNC machined parts, stamping parts, die casting parts, screws | Customized solutions, high precision |
| Ningbo OEM Industry Manufacturer Ltd. | CNC machined parts, stamping parts, die casting parts | Wide industry application, customization |
| Shanghai M-HE Mechanical Equipment Co., Ltd. | CNC machined parts, stamping parts, die casting parts | Quality control, on-time delivery |
| Xiamen Rising Mechanical Import & Export Co., Ltd. | CNC machined parts, stamping parts, sheet metal fabrication | High precision, competitive prices |
| Hangzhou Aunov Tech Co., Ltd. | Aluminum profiles, CNC machined parts, sheet metal fabrication | Wide industry usage, excellent customer service |
| Suzhou Kairlo Machinery & Electronics Co., Ltd. | CNC machined parts, stamping parts, sheet metal fabrication | Precision, cost-effectiveness |
| Shenzhen Arvin Industries Co., Ltd. | CNC machined parts, die casting parts, stamping parts, sheet metal fabrication | High-quality production, wide industry usage |
| Wuxi Baide Precision Machinery Co., Ltd. | CNC machined parts, sheet metal fabrication, stamping parts | Precision, competitive prices |
| Guangzhou Shengcheng Metal Products Co., Ltd. | CNC machined parts, die casting parts, stamping parts | Wide industry usage, reliability |
In conclusion, these top 10 metal parts manufacturers in China offer a diverse range of products including CNC machined parts, stamping parts, die casting parts, and sheet metal fabrication. They cater to various industries and are known for their precision, durability, and competitive pricing. Whether it’s automotive, electronics, or machinery, these manufacturers provide customized solutions and excellent customer service to meet specific requirements. With their strict quality control measures and commitment to on-time delivery, these metal parts manufacturers are trusted partners in the global market.
Background Research for metal parts manufacturers Companies in China, use qcc.com archive.org importyeti.com
When it comes to metal parts manufacturers in China, there are several reliable sources that can provide extensive background research on companies in this industry. Websites such as qcc.com, archive.org, and importyeti.com offer valuable information and insights about metal parts manufacturers in China.
Qcc.com is a trusted Chinese business information platform that provides comprehensive company profiles, including basic business information, registration details, industry classification, and financial data. It also offers insights into a company’s management, shareholders, and operating status. By searching for specific metal parts manufacturers on qcc.com, researchers can gather relevant information to assess a company’s credibility and capabilities.
Archive.org is a popular internet archive platform that allows users to access historical versions of websites and web pages. This can be particularly helpful in understanding a company’s evolution, growth trajectory, and any significant changes it might have undergone over time. Researchers can explore past versions of a company’s website on archive.org to gather information about its history, achievements, product range, and other essential details.
Importyeti.com is a comprehensive tool for sourcing intelligence that provides data on import and export activities conducted by companies worldwide. It allows users to search for specific products, such as metal parts, and identifies the companies involved in these trade activities. Researchers can gain insights into a metal parts manufacturer’s export capabilities, customer base, and market presence by utilizing the importyeti.com database.
In summary, qcc.com, archive.org, and importyeti.com are valuable resources for conducting background research on metal parts manufacturers in China. By utilizing these platforms, researchers can gather comprehensive information about a company’s background, financials, historical records, and global trade activities, enabling them to make informed decisions about potential business partnerships or collaborations.
Leveraging Trade Shows and Expos for metal parts Sourcing in China
Trade shows and expos in China are valuable platforms for sourcing metal parts due to their ability to connect buyers with a wide range of suppliers in a concentrated time and space. These events provide numerous benefits that can greatly enhance the sourcing process for metal parts.
Firstly, trade shows and expos offer an extensive selection of suppliers under one roof. This allows buyers to efficiently compare multiple options and choose the best fit for their specific requirements. Exhibitors showcase their products, capabilities, and expertise, enabling buyers to assess quality, reliability, and compatibility.
Additionally, attending trade shows and expos provides an opportunity for face-to-face interactions with suppliers. This facilitates the establishment of personal relationships and fosters trust, which are crucial for successful long-term partnerships. Buyers can discuss specific product details, negotiate pricing and terms, and gain a better understanding of the supplier’s capabilities and processes.
Trade shows and expos in China also serve as a platform for discovering new trends, technologies, and innovations in the metal parts industry. Exhibitors often display the latest advancements, allowing buyers to stay informed and remain competitive in their market. By attending these events, buyers can identify new products or techniques that may improve their own manufacturing processes or differentiate their products.
In addition, trade shows and expos enable buyers to stay updated on industry regulations and certifications. Many exhibitors display their compliance with international standards, giving buyers confidence in the supplier’s commitment to quality and compliance. This is particularly important for metal parts, as they often require rigorous testing and certifications to ensure safety and reliability.
To make the most of trade shows and expos in China, buyers should carefully plan their visit, identifying specific suppliers of interest and scheduling appointments in advance. It is also crucial to conduct thorough research beforehand to understand the market, industry trends, and potential suppliers. By leveraging these events effectively, buyers can optimize their sourcing process and find reliable and qualified suppliers for their metal parts needs.
The Role of Agents and Sourcing Companies in Facilitating metal parts Purchases from China
Agents and sourcing companies play a crucial role in facilitating metal parts purchases from China. With their expertise and local knowledge, they provide a range of valuable services to buyers looking to procure metal parts from Chinese manufacturers.
Firstly, agents and sourcing companies act as intermediaries between buyers and Chinese manufacturers. They assist in identifying suitable suppliers based on the buyer’s specific requirements, such as production capacity, quality standards, and pricing. This helps buyers save time and effort in searching for reliable manufacturers themselves.
Secondly, agents and sourcing companies help with communication and language barriers. They effectively bridge the gap between foreign buyers and Chinese manufacturers by providing translation services and ensuring clear communication. This minimizes misunderstandings and enhances the efficiency of the procurement process.
Furthermore, agents and sourcing companies offer quality control and inspection services. They conduct factory audits, inspect samples, and monitor the production process to ensure that the metal parts meet the buyer’s specifications and quality standards. This reduces the risk of receiving substandard or non-compliant products.
Agents and sourcing companies also assist with logistics and shipping arrangements. They have experience in handling international shipments and can coordinate the transportation of metal parts from Chinese manufacturers to the buyer’s location. This includes customs clearance, freight forwarding, and tracking of the shipment, simplifying the entire procurement process for the buyer.
Lastly, agents and sourcing companies provide valuable market insights and expertise. They stay updated on the latest market trends, pricing fluctuations, and regulatory changes in China’s metal parts industry. This knowledge helps buyers make informed decisions and navigate the complexities of the Chinese market effectively.
In summary, agents and sourcing companies play a crucial role in facilitating metal parts purchases from China. By acting as intermediaries, providing communication support, quality control, logistics assistance, and market expertise, they enable buyers to source metal parts efficiently and effectively from Chinese manufacturers.
Price Cost Research for metal parts manufacturers Companies in China, use temu.com and 1688.com
When conducting price cost research for metal parts manufacturers in China, two websites that can be utilized are Temu.com and 1688.com. These platforms provide comprehensive information regarding suppliers, products, and pricing, allowing potential buyers to make informed decisions.
Temu.com is an online platform that specializes in connecting buyers and suppliers in the manufacturing industry. It offers a wide range of metal parts manufacturers in China, allowing buyers to compare different suppliers and their pricing. The website provides detailed company profiles, product catalogs, and customer reviews, facilitating thorough research before making a final purchase decision.
1688.com, often referred to as “Alibaba China,” is a popular platform exclusively for the Chinese market. It is an effective tool for finding metal parts manufacturers in China and comparing their prices. With millions of suppliers listed, 1688.com offers a vast selection of products accessible at competitive prices. The website also provides supplier ratings and customer feedback, ensuring buyers have a good understanding of the supplier’s reputation and product quality.
When researching prices on both platforms, it is important to consider various factors that may affect cost. These factors include the type of metal used, design complexity, manufacturing technique, quantity ordered, and shipping options. Additionally, it is common practice to negotiate prices with suppliers to find the most favorable terms.
In conclusion, conducting price cost research for metal parts manufacturers in China can be efficiently done using Temu.com and 1688.com. These platforms provide access to a wide range of suppliers, their product catalogs, and pricing information, allowing buyers to make well-informed decisions. By considering various factors and negotiating prices, buyers can secure the best deal for their metal parts requirements.
Shipping Cost for metal parts import from China
Importing metal parts from China can incur various shipping costs depending on several factors such as weight, volume, transportation mode, and destination. Let’s explore some common shipping methods and their associated costs.
1. Air Freight: Air shipping is the fastest method but also the most expensive. Costs are usually calculated based on the actual or volumetric weight, whichever is higher. For example, shipping a 100 kg metal parts package from China to the United States via air freight can range from $4 to $10 per kilogram, resulting in a total cost of $400 to $1000.
2. Sea Freight: Sea shipping is slower but economical for larger shipments. It is typically charged based on container size, weight, and shipping distance. For instance, transporting a 20-foot full container load (FCL) of metal parts from China to Europe can cost around $1000 to $4000, depending on the destination port.
3. LCL (Less than Container Load): If your shipment doesn’t fill an entire container, you can opt for LCL shipping. This method combines several consignments into one container and charges based on the volume occupied. LCL rates range from $30 to $60 per cubic meter, with additional handling fees and destination charges.
4. Incoterms: The International Commercial Terms (Incoterms) determine the division of shipping costs and responsibilities between the buyer and the seller. Common shipping terms like Ex Works (EXW), Cost and Freight (CFR), or Free on Board (FOB) can influence the final shipping cost.
5. Customs and Duties: Importing metal parts from China may attract customs duties, taxes, and fees imposed by the importing country. These costs can vary based on the metal parts’ classification and country-specific regulations.
It is crucial to request quotes from freight forwarders or shipping agents who can provide accurate cost estimations based on your specific requirements. Additionally, consider insurance, documentation, and potential customs brokerage fees when calculating the overall shipping cost.
Compare China and Other metal parts Markets: Products Quality and Price,Visible and Hidden Costs
China is known for its dominance in the metal parts market and is often compared to other markets in terms of product quality, price, and visible and hidden costs. One of the key factors that have contributed to China’s success in this industry is the relatively low cost of labor, allowing for competitive prices of metal parts.
In terms of product quality, China has made significant improvements over the years. While in the past, Chinese metal parts were often associated with lower quality, the situation has changed as manufacturers invested in advanced equipment and improved their production processes. Many Chinese manufacturers have also obtained ISO certifications and adhere to rigorous quality control measures. However, it is important to note that variances in product quality can still exist, especially among different manufacturers. Other metal parts markets may also have their own set of quality standards and certifications, which can be a determining factor in the overall product quality.
When comparing prices, China often offers competitive rates due to economies of scale and low labor costs. Chinese manufacturers can produce metal parts in large quantities, resulting in reduced production costs. Additionally, the lower cost of labor allows for cost savings, which are then passed on to customers. However, other metal parts markets may have their own cost advantages, such as proximity to raw materials or access to specialized expertise, which can affect pricing. It is crucial for buyers to consider both the initial price and the long-term value provided by the metal parts.
Visible costs in the metal parts market primarily include the purchase price, transportation costs, and import duties. China’s manufacturing capabilities and infrastructure enable efficient production and shipping, resulting in competitive visible costs. However, other markets may have advantages in terms of transportation costs, especially for local or regional buyers.
Hidden costs, on the other hand, can include quality control inspections, intellectual property protection, lead times, and communication challenges. These costs are often underestimated or overlooked. Chinese manufacturers have made efforts to address hidden costs by improving communication and offering services such as quality inspections. However, other metal parts markets may have advantages in terms of faster lead times or better protection of intellectual property rights, which can reduce hidden costs for buyers.
In summary, while China has emerged as a dominant player in the metal parts market, its product quality and pricing competitiveness have significantly improved over time. However, other markets may offer their own advantages in terms of quality standards, pricing, visible costs, and hidden costs. Buyers should carefully assess their specific requirements and consider all factors when choosing a metal parts market.
Understanding Pricing and Payment Terms for metal parts: A Comparative Guide to Get the Best Deal
When it comes to procuring metal parts, understanding pricing and payment terms is crucial in order to get the best deal. This guide aims to provide a comparative analysis of different pricing and payment factors to help you make informed decisions.
1. Pricing Factors:
– Material Costs: The cost of raw materials plays a significant role in determining the price of metal parts. Factors like the type of metal, its availability, and market demand can affect material costs.
– Manufacturing Processes: The complexity and scale of manufacturing processes influence pricing. Machining, casting, forging, or stamping methods require different levels of expertise, equipment, and time, affecting the price.
– Quantity: Larger order quantities generally lead to lower per-unit pricing. Manufacturers often offer volume-based discounts or economies of scale.
– Customization: Any special requirements or customized features can impact pricing. Additional tooling or setup costs might be incurred to meet unique specifications.
– Market Competition: Competitive markets encourage manufacturers to offer more competitive prices. Researching multiple suppliers and obtaining quotes can help you negotiate better deals.
2. Payment Terms:
– Payment Methods: Different suppliers may offer various payment options such as credit cards, bank transfers, or payment platforms. Evaluate the available methods based on convenience, security, and associated fees.
– Payment Schedule: Determine the payment schedule that suits your budget and cash flow. Some suppliers may require a down payment before production starts, with the remaining amount payable upon completion or delivery.
– Trade-offs: Some manufacturers offer lower prices but longer lead times, while others might have higher prices with faster delivery. Consider your priorities and production timeline to choose the right balance.
– Currency and Exchange Rates: If dealing with international suppliers, be aware of currency fluctuations and their potential impact on pricing. Consider hedging options or negotiate fixed rates for stability.
– Contract Terms: Ensure that all payment terms, delivery schedules, quality requirements, and liability clauses are clearly defined and documented to avoid any conflicts or misunderstandings.
Ultimately, finding the best deal for metal parts involves considering various pricing factors and negotiating favorable payment terms. By understanding these aspects and conducting thorough research, you can make informed decisions that align with your budget, quality requirements, and production timeline.
Chinese Regulations and Industry Standards Certifications for metal parts,Import Regulations and Customs for metal parts from China
China has various regulations and industry standards certifications for metal parts. These certifications ensure the quality and safety of metal parts produced in the country. Some of the important certifications and regulations are:
1. China Compulsory Certification (CCC): This certification is mandatory for various products, including certain metal parts. It ensures that the product meets the specified safety requirements and quality standards.
2. ISO 9001: This international quality management system certification guarantees that a company follows stringent quality control measures in its production processes for metal parts.
3. GB Standards: China has a set of national standards known as GB standards. These standards cover various aspects of metal parts production, including design, manufacturing, and testing methods.
4. RoHS: The Restriction of Hazardous Substances (RoHS) directive restricts the use of certain hazardous substances, such as lead, mercury, and cadmium, in metal parts. Compliance with RoHS is essential for exporting metal parts to many countries.
When importing metal parts from China, it is crucial to understand the import regulations and customs procedures. Some key points to consider are:
1. Import Tariffs: Check the applicable import tariffs for metal parts in your country. These tariffs vary depending on the type of metal parts and can impact the overall cost of importing.
2. Customs Documentation: Ensure that you have all the necessary customs documentation, such as commercial invoices, packing lists, and certificates of origin, to facilitate smooth customs clearance.
3. Customs Classification: Determine the correct customs classification for your metal parts. The Harmonized System (HS) codes are used to classify products, and choosing the right code is important for accurate customs declaration.
4. Customs Duties and Taxes: Familiarize yourself with the customs duties and taxes levied on imported metal parts. These charges may include customs duties, value-added tax (VAT), and other applicable fees.
To avoid any potential issues with Chinese regulations and customs, it is advisable to work with a reputable supplier who is well-versed in international trade practices and can provide the necessary certifications and documentation for metal parts export.
Sustainability and Environmental Considerations in metal parts Manufacturing
Sustainability and environmental considerations are vital in metal parts manufacturing to mitigate the negative impacts on the environment and promote sustainable practices. These considerations encompass various aspects, including resource conservation, waste reduction, energy efficiency, and emissions control.
One crucial aspect of sustainability in metal parts manufacturing is resource conservation. This involves minimizing the use of raw materials, such as metals, to reduce depletion and ensure their long-term availability. Implementing efficient production processes that optimize material usage, minimize scrap generation, and promote recycling can help conserve resources and minimize waste.
Waste reduction is another essential element in sustainable metal parts manufacturing. By implementing waste management strategies, such as proper segregation, recycling, and reusing, manufacturers can minimize the amount of waste generated and avoid its direct disposal to the environment. Additionally, exploring alternative materials or production techniques that generate less waste can further contribute to waste reduction.
Energy efficiency is of utmost importance as it directly impacts both the environmental and economic aspects of metal parts manufacturing. Manufacturers can adopt energy-efficient technologies and processes to minimize energy consumption and associated greenhouse gas emissions. Optimizing equipment, streamlining production processes, and utilizing renewable energy sources are effective strategies to achieve energy efficiency goals.
Controlling emissions is another key consideration in sustainable metal parts manufacturing. Industries emitting pollutants, such as volatile organic compounds (VOCs), particulate matter, or greenhouse gases, should implement suitable emission control technologies or practices to minimize their environmental impact. This may include using air filtration systems, catalytic converters, or implementing carbon capture and storage (CCS) techniques.
Moreover, sustainable metal parts manufacturing involves fostering collaboration among stakeholders. Manufacturers can engage in partnerships with suppliers, customers, and other relevant parties to jointly develop and promote sustainable practices throughout the supply chain. Information sharing, knowledge transfer, and regular audits can help ensure compliance and continuous improvement in sustainability performance.
In conclusion, sustainability and environmental considerations play a significant role in metal parts manufacturing. By implementing strategies such as resource conservation, waste reduction, energy efficiency, emissions control, and stakeholder collaboration, manufacturers can mitigate their environmental footprint and contribute to a more sustainable future.
List The Evolution history of “metal parts”
The evolution of metal parts, also known as the history of metalworking, spans thousands of years and has seen remarkable advancements. The development of metal parts can be broadly categorized into several key periods.
1. Ancient Times (Prehistory-500 BCE): The earliest known metalworking techniques emerged during this period. Copper was among the first metals to be used for crafting tools and decorative items. Bronze, an alloy of copper and tin, was also developed during this time, giving rise to the Bronze Age.
2. Classical Era (500 BCE-500 CE): This era witnessed the rise of ironworking. Iron, being more abundant and durable than bronze, became a widely-used metal in various applications such as tools, weapons, and construction materials. Techniques such as forging and casting were refined during this time.
3. Medieval Period (500-1500 CE): The Middle Ages saw incremental improvements in metalworking techniques. Blacksmiths started incorporating water-powered hammers and bellows, making the production of metal parts more efficient. The increased demand for armor and weaponry during this time further drove advancements in metalworking.
4. Industrial Revolution (18th-19th centuries): The Industrial Revolution brought about a revolutionary transformation in metalworking. The invention of steam-powered machinery, including rolling mills and powered hammers, enabled mass production of metal parts. This led to drastic improvements in the manufacturing capabilities and accessibility of metal components.
5. Modern Era (20th century-present): The 20th century witnessed tremendous progress in metalworking technologies. The development of electric arc furnaces and other advanced manufacturing processes allowed for the production of alloys with specific properties. Precision machining techniques such as CNC (Computer Numerical Control) machining further refined the production of metal parts, increasing accuracy and reducing human labor.
6. Contemporary Trends: The present era is characterized by the rapid integration of digital technologies into metalworking processes. Additive manufacturing, commonly known as 3D printing, has gained popularity as it allows for complex geometries and rapid prototyping. Materials such as titanium alloys and superalloys are now widely used in aerospace and other high-performance industries.
In conclusion, the evolution of metal parts has progressed from using copper in ancient times to the widespread use of iron, the industrialization of metalworking during the Industrial Revolution, and the modern advancements in precision machining and digital manufacturing techniques. These developments have transformed the production and application of metal parts, contributing to the technological progress and development of various industries.
The Evolution and Market Trends in metal parts Industry
The metal parts industry has witnessed significant evolution and market trends over the years. From traditional manufacturing techniques to advanced technology-driven production methods, the industry has experienced notable developments.
One of the key evolutions in the metal parts industry is the shift towards precision manufacturing. With the advent of computer-aided design (CAD) and computer-aided manufacturing (CAM), manufacturers can now achieve higher accuracy and precision in their metal parts. This has led to improved product quality and reduced production time, resulting in increased efficiency and cost savings.
Another important evolution is the adoption of advanced materials in the metal parts industry. Traditional metals such as steel, iron, and aluminum are still widely used, but newer materials like titanium, nickel alloys, and composites have also gained popularity. These materials offer enhanced strength, durability, and resistance to corrosion, expanding the range of applications for metal parts in various industries.
One of the prominent market trends in the metal parts industry is the growing demand for lightweight components. As industries such as aerospace, automotive, and consumer electronics focus on improving fuel efficiency and reducing emissions, the need for lightweight metal parts has surged. This has led manufacturers to develop innovative techniques such as metal injection molding and additive manufacturing to produce lightweight components without compromising on strength and performance.
Additionally, sustainability has become a crucial market trend in the metal parts industry. With increasing environmental concerns, manufacturers are adopting eco-friendly practices and materials. Recycling and reusing metal parts, reducing waste generation, and implementing energy-efficient manufacturing processes are some of the initiatives undertaken to achieve sustainability in the industry.
Furthermore, the industry is experiencing a shift towards automation and robotics. With the aim of improving productivity, reducing labor costs, and ensuring consistent quality, companies are increasingly investing in automated machinery and robots for metal parts production. This trend is expected to continue as technology advances and labor costs continue to rise in many parts of the world.
In conclusion, the metal parts industry has undergone significant evolution, driven by advancements in technology, materials, and manufacturing techniques. Market trends such as precision manufacturing, lightweight components, sustainability, and automation have shaped the industry and will continue to influence its future trajectory.
Custom Private Labeling and Branding Opportunities with Chinese metal parts Manufacturers
Chinese metal parts manufacturers offer a wide range of custom private labeling and branding opportunities for businesses looking to enhance their product offerings. By collaborating with these manufacturers, companies can create unique and customized metal parts that can be branded with their own logo, design, and packaging.
One of the key advantages of working with Chinese metal parts manufacturers is their ability to provide cost-effective solutions without compromising on quality. These manufacturers typically have advanced technologies, modern machinery, and well-trained workforce, ensuring the production of high-quality metal parts that meet international standards.
Moreover, Chinese manufacturers have an extensive supply chain network and access to a variety of raw materials. This enables them to offer a diverse range of metal parts and finishes, including stainless steel, aluminum, brass, and more. Businesses can take advantage of this wide selection to create customized metal parts that meet specific requirements and quality standards.
Chinese metal parts manufacturers also value customization and offer a range of branding options. Companies can choose to imprint their logo or brand name on the products using methods such as laser engraving, etching, or embossing. Additionally, manufacturers can collaborate with businesses to develop custom packaging solutions that reflect their brand identity and appeal to their target market.
Working with Chinese manufacturers not only provides businesses with access to a wide variety of metal parts but also offers an opportunity for businesses to establish long-term partnerships. These manufacturers often have dedicated sales teams that can assist in product development, ensuring that the final metal parts align with the client’s specific branding and quality requirements.
In conclusion, Chinese metal parts manufacturers offer custom private labeling and branding opportunities that enable businesses to differentiate their products in the market. With their cost-effective solutions, extensive supply chain network, and willingness to collaborate on customization, these manufacturers are ideal partners for businesses seeking to enhance their product offerings with high-quality metal parts.
Tips for Procurement and Considerations when Purchasing metal parts
When procuring metal parts, it is essential to consider a few key factors to ensure the best quality and cost-effectiveness. Here are some tips and considerations to keep in mind:
1. Define the Requirements: Clearly define the specifications, functionality, and quality standards for the metal parts you require. Consider factors such as size, material, finish, tolerance levels, and any specific industry regulations.
2. Choose the Right Supplier: Partner with a reputable and experienced supplier capable of delivering quality metal parts. Look for a supplier with a proven track record, technological capabilities, and appropriate certifications. Request and review samples, testimonials, and references to assess their capabilities.
3. Material Selection: Selecting the right type of metal is crucial. Consider the intended application, environmental factors, and required strength and durability. Common metals include aluminum, stainless steel, carbon steel, brass, and copper. Ensure the supplier offers a variety of materials and is transparent about their sourcing methods and quality control.
4. Quality Assurance: Implement stringent quality control measures to ensure the received metal parts adhere to your specifications. This can include conducting regular inspections, testing samples, and reviewing certificates of compliance. Establishing quality standards minimizes the risk of receiving faulty or subpar parts.
5. Pricing: Obtain detailed quotes from multiple suppliers to evaluate pricing options. Be cautious of exceptionally low prices as they may indicate compromised quality. Consider the total cost of ownership over time, including factors like maintenance, durability, and potential replacement costs.
6. Lead Time: Ensure the supplier can meet your production timeline. Discuss the lead time for manufacturing, packaging, and shipping, and verify their reliability in delivering on time. Timely procurement is crucial to avoid project delays.
7. Communication and Collaboration: Maintain open lines of communication with the supplier throughout the procurement process. Clearly articulate your requirements, address any concerns promptly, and foster a collaborative relationship. Regular updates and clear communication help avoid misunderstandings and ensure a smooth procurement experience.
8. Packaging and Shipping: Discuss packaging requirements to protect the metal parts during transportation. Consider factors like bulk packaging, individual labeling, and any special handling instructions to minimize the risk of damage.
By considering these tips and factors when procuring metal parts, you can make informed decisions that result in reliable, high-quality components while optimizing costs and minimizing potential risks.
FAQs on Sourcing and Manufacturing metal parts in China
1. Why should I consider sourcing and manufacturing metal parts in China?
Sourcing and manufacturing metal parts in China offer several advantages, including cost-effectiveness, high production capacity, and a wide range of materials and manufacturing processes. Chinese manufacturers often provide competitive pricing due to lower labor costs and economies of scale. Moreover, China’s extensive industrial infrastructure allows for large-scale production and quick turnaround times.
2. How can I find reliable metal part suppliers in China?
To find reliable suppliers, you can start by conducting online research and utilizing popular B2B platforms like Alibaba or Global Sources. It is essential to thoroughly vet potential suppliers by reviewing their company profiles, product quality certifications, and customer reviews. Additionally, requesting samples and conducting factory visits can help to evaluate the supplier’s capabilities and ensure they align with your requirements.
3. Are there any risks in sourcing from China?
While sourcing from China offers significant advantages, there are some risks to consider. Quality control can be a challenge, so it is crucial to establish clear product specifications and conduct regular inspections during production. Additionally, intellectual property protection can be a concern, so it is advisable to utilize non-disclosure agreements (NDAs) and protect your designs through patents or trademarks.
4. Can Chinese manufacturers handle customizable or complex metal parts?
Yes, Chinese manufacturers have extensive expertise in producing customizable and complex metal parts. From simple components to intricate assemblies, Chinese factories can handle a wide array of production requirements. However, it is vital to communicate your specifications clearly and work closely with the manufacturer to ensure the desired outcome.
5. How can I ensure quality control during manufacturing?
Implementing rigorous quality control measures is essential to ensure consistency and reliability. Conducting initial sample inspections, implementing in-process quality checks, and performing final pre-shipment inspections are advisable steps. Hiring third-party quality control inspectors or engaging professional sourcing agents can help facilitate this process and ensure adherence to international quality standards.
6. What are the common manufacturing processes used in China for metal parts?
China offers various manufacturing processes for metal parts, including casting, forging, stamping, machining, and fabrication. These processes can achieve precise dimensions, excellent surface finishes, and meet a wide range of functional requirements. The choice of manufacturing process depends on the complexity of the part, material suitability, and desired production volume.
In summary, sourcing and manufacturing metal parts in China can be a cost-effective and efficient solution due to the country’s industrial capabilities and competitive pricing. However, it is crucial to conduct thorough research, establish clear specifications, and implement robust quality control measures to mitigate any potential risks.
Why contact sourcifychina.com get free quota from reliable metal parts suppliers?
Sourcifychina.com is able to obtain a free quota from reliable metal parts suppliers due to several reasons. Firstly, Sourcifychina.com has built a strong network and partnerships with numerous reputable metal parts suppliers in China. Suppliers are willing to offer a free quota to Sourcifychina.com as a demonstration of their commitment to building a long-term business relationship.
Secondly, Sourcifychina.com has established itself as a reliable and trusted sourcing platform. It has a track record of successfully connecting buyers with high-quality suppliers, ensuring efficient communication and smooth transaction processes. This reputation attracts suppliers to collaborate with Sourcifychina.com and provide a free quota as a gesture of goodwill.
Thirdly, Sourcifychina.com brings a significant volume of business to these metal parts suppliers. By sourcing metal parts for multiple buyers, it consolidates orders and enables suppliers to achieve economies of scale, thus reducing their production costs. Offering a free quota to Sourcifychina.com is seen as a strategic move by suppliers to secure a steady stream of business and gain a competitive advantage in the market.
Moreover, Sourcifychina.com employs a rigorous supplier qualification process. It conducts thorough assessments and due diligence to ensure that the suppliers it partners with meet stringent quality standards and can deliver high-quality metal parts. This quality assurance factor attracts suppliers to work with Sourcifychina.com and provide a free quota, as it guarantees their products will be marketed to potential buyers who value quality.
In conclusion, Sourcifychina.com receives a free quota from reliable metal parts suppliers due to its strong network, reputation as a trusted sourcing platform, high volume of business, and commitment to quality assurance. This advantageous position allows Sourcifychina.com to connect buyers with reliable suppliers while providing the opportunity for suppliers to expand their customer base and elevate their market presence.