Introduce about aluminum cnc machine guide,Qulity,Cost,Supplier,Certification,Market,Tips,FAQ
Aluminum CNC machines are cutting-edge tools that are widely used in various industries for precision machining of aluminum components. This guide provides an overview of aluminum CNC machines, covering aspects such as quality, cost, suppliers, certifications, market, tips, and frequently asked questions.
Quality is a vital factor when it comes to CNC machines, as it directly affects the accuracy and efficiency of the machining process. High-quality aluminum CNC machines are designed with robust structures and advanced technologies, ensuring excellent performance, dimensional accuracy, and surface finish. It is essential to choose machines from reputable manufacturers known for their expertise in producing premium CNC equipment.
In terms of cost, aluminum CNC machines can vary significantly depending on their specifications, capabilities, and brand reputation. Entry-level machines may cost a few thousand dollars, while advanced models with sophisticated features can reach several hundred thousand dollars. The cost should be evaluated in accordance with the specific requirements and budget of the user.
When it comes to suppliers, there are numerous companies globally that offer aluminum CNC machines. It is advisable to partner with established suppliers known for their reliability, customer support, and after-sales service. Extensive research should be conducted to compare offerings and make an informed decision.
Certifications play a crucial role in ensuring the quality and safety of aluminum CNC machines. Look for suppliers who comply with international standards such as ISO and CE certifications. These certifications guarantee that the machines meet the necessary requirements and adhere to industry guidelines.
The market for aluminum CNC machines is expanding rapidly due to the growing demand for precise machining in industries such as aerospace, automotive, electronics, and more. The increasing need for lightweight and complex aluminum parts has driven the adoption of CNC machines across various sectors.
Here are a few tips to consider when working with aluminum CNC machines: optimize cutting parameters for aluminum, maintain proper tooling, utilize coolant/lubrication, and regularly inspect and clean the machines to ensure optimal performance and longevity.
Frequently Asked Questions (FAQ):
1. What is the maximum cutting speed of an aluminum CNC machine?
– The cutting speed depends on various factors such as machine power, tooling, and material type. However, aluminum can typically be cut at high speeds compared to other metals.
2. Can aluminum CNC machines be used for other materials?
– Yes, aluminum CNC machines can also work with other materials like steel, brass, plastics, and wood, depending on the machine’s capabilities and appropriate tooling.
3. Is CNC machining suitable for small-scale production?
– Yes, CNC machines are highly versatile and can be utilized for both small-scale prototyping and large-scale production.
In conclusion, aluminum CNC machines are essential tools for precision machining of aluminum components. Consider quality, cost, suppliers, certifications, and market demand when selecting an aluminum CNC machine from reputable suppliers. Take note of the provided tips and refer to the frequently asked questions to enhance knowledge on aluminum CNC machines.
Types of aluminum cnc machine
There are several different types of aluminum CNC machines available, each with its own unique features and capabilities. Here are some of the most common types:
1. CNC Milling Machines: These machines use rotating cutting tools to remove material from a solid block of aluminum. They are capable of producing intricate and precise parts with high accuracy. CNC milling machines can be either vertical or horizontal, depending on the orientation of the cutting tools.
2. CNC Lathes: Lathes are used to shape and cut solid aluminum bars or tubes by rotating them against a cutting tool. CNC lathes can be used to create cylindrical parts, such as screws, bolts, and shafts, with high precision.
3. CNC Plasma Cutters: These machines use a plasma torch to cut through aluminum sheets or plates. The high-velocity plasma stream melts the metal, while a computer-controlled mechanism guides the torch to achieve precise cuts. CNC plasma cutters are ideal for cutting complex shapes and contours.
4. CNC Engraving Machines: As the name suggests, these machines are used for engraving designs or text onto aluminum surfaces. They use a rotating spindle and various cutting tools to create intricate patterns or markings with high precision. CNC engraving machines are commonly used in the signage and jewelry industries.
5. CNC Horizontals: These machines are specifically designed for heavy-duty cutting of aluminum. They have a horizontal spindle and worktable, making them suitable for machining large and bulky aluminum parts. CNC horizontals are commonly used in industries like aerospace and automotive manufacturing.
6. CNC Routers: Routers are versatile machines that use a rotating cutting bit to remove material from aluminum sheets or blocks. They are often used for cutting, shaping, and profiling aluminum parts. CNC routers are popular in industries like woodworking, signage, and prototyping.
It is worth noting that different CNC machines can be equipped with additional features like multiple-axis control, automatic tool changers, and coolant systems, which further enhance their capabilities and productivity. The choice of the right CNC machine for aluminum machining ultimately depends on factors such as part size, complexity, and desired precision.
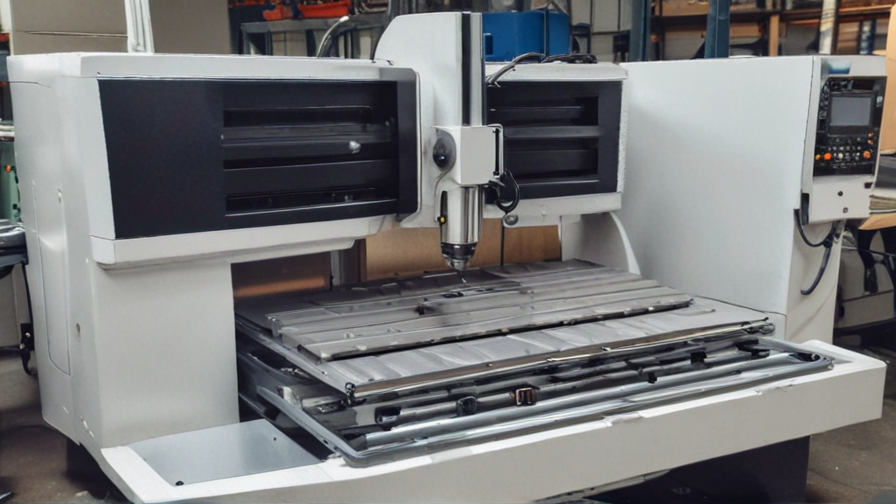
Pros and Cons of Using aluminum cnc machine
Pros:
1. Lightweight and corrosion-resistant: Aluminum is a lightweight material that makes it easy to handle and transport. It is also highly resistant to corrosion, making it suitable for outdoor applications or industries where exposure to moisture or chemicals is a concern.
2. High strength-to-weight ratio: Aluminum alloys provide excellent strength while being relatively light, making them ideal for applications where weight reduction is crucial, such as aerospace and automotive industries.
3. Good thermal conductivity: Aluminum’s high thermal conductivity allows for efficient heat dissipation, making it ideal for heat-sensitive applications like electronics and heat sinks.
4. Machinability: Aluminum has excellent machinability, meaning it can be easily shaped, cut, and fabricated using CNC (Computer Numerical Control) machines. This leads to faster production times, lower costs, and increased efficiency.
5. Versatility: Aluminum can be easily extruded, cast, or machined into various shapes and sizes, allowing for a wide range of applications. It is also highly recyclable, making it an eco-friendly choice.
Cons:
1. Lower wear resistance: Compared to materials like steel, aluminum has lower wear resistance, meaning it is more prone to scratching and deformation over time. This may limit its use in applications where abrasion or heavy loads are involved.
2. Lower stiffness: While aluminum is strong for its weight, it is generally less stiff than materials like steel. This can lead to potential issues with precision and stability in applications requiring high rigidity or tight tolerances.
3. Lower melting point: Aluminum has a relatively low melting point compared to other metals, which can limit its application in high-temperature environments.
4. Higher cost: Although aluminum is readily available, the cost of aluminum CNC machines and tools can be higher compared to those used for other materials like wood or plastic.
5. Material limitations: While aluminum is versatile, it may not be suitable for all applications. Some industries require materials with specific properties not provided by aluminum, such as high strength or conductivity.
In conclusion, aluminum CNC machines offer several advantages such as lightweight, corrosion resistance, high strength-to-weight ratio, and good thermal conductivity. However, they also have drawbacks such as lower wear resistance and stiffness, higher cost, and material limitations in certain applications.
aluminum cnc machine Reference Specifications (varies for different product)
The specifications of an aluminum CNC machine can vary depending on the specific product. However, there are key reference specifications that are commonly found in such machines.
Firstly, the machine should have a sturdy and durable construction, typically made of high-quality materials like cast iron or steel. This ensures stability and precision during the machining process.
A key specification to consider is the machine’s worktable size. It should provide adequate space for holding and securing the aluminum workpiece firmly. The table may feature T-slots or other clamping mechanisms to facilitate the fixation of the material.
Another important specification is the machine’s spindle power and speed. CNC machines typically have high-speed spindles capable of rotating at varying speeds. The power of the spindle determines the machine’s cutting capabilities, with higher power allowing for more efficient machining.
The machine’s precision and accuracy are crucial factors. Look for specifications regarding the positioning accuracy and repeatability of the machine, typically measured in microns. The machine should be capable of consistently achieving tight tolerances to produce precise aluminum parts.
Additionally, the machine should provide multiple-axis control for complex machining operations. Three-axis machines are more common, allowing movement in the X, Y, and Z directions. More advanced machines may offer additional rotational axes, such as a fourth or fifth axis, for enhanced versatility.
Control systems are also important considerations. CNC machines are typically equipped with advanced computer-based controls that allow for precise programming and operating of the machine. Look for specifications regarding the type of control system, such as Fanuc or Siemens, and ensure it meets your specific requirements.
Other relevant specifications may include the machine’s tool capacity, coolant system, chip evacuation system, and overall footprint.
It is important to note that the specific reference specifications for an aluminum CNC machine can vary depending on the manufacturer, model, and intended application. Therefore, it is advisable to consult the machine’s user manual or reach out to the manufacturer for detailed information.
Applications of aluminum cnc machine
Aluminum CNC machines are widely used in various industries due to their versatility, precision, and efficiency. Here are some applications where aluminum CNC machines are commonly used:
1. Automotive industry: Aluminum is widely used in the automotive industry for making components such as engine blocks, pistons, cylinder heads, and transmission parts. CNC machines can precisely and accurately mill, drill, and shape aluminum, ensuring high-quality and durable automotive parts.
2. Aerospace industry: Aluminum CNC machines are extensively used in the aerospace industry for manufacturing aircraft components. Aluminum alloys offer excellent strength-to-weight ratio, making them ideal for fabricating parts like fuselage panels, wings, landing gears, and interior components with the help of CNC machines.
3. Electronics industry: Aluminum CNC machines are used in the electronics industry to produce enclosures and housings for various electronic devices, including smartphones, tablets, laptops, and televisions. CNC machines can create intricate and precise designs on aluminum surfaces that provide protection and aesthetics to electronic devices.
4. Signage industry: Aluminum CNC machines are utilized in the signage industry for producing custom signs and letters. CNC machines can accurately carve and engrave aluminum sheets, allowing for intricate and detailed designs. These signs are weather-resistant and long-lasting, making them suitable for outdoor applications.
5. Furniture industry: Aluminum is widely used in the furniture industry due to its lightweight, durability, and modern aesthetic. CNC machines help in shaping and machining aluminum for designing furniture pieces like tables, chairs, shelves, and frames with intricate patterns and designs.
6. Construction industry: Aluminum CNC machines find application in the construction industry for creating architectural components like windows, doors, curtain walls, and structural profiles. CNC machines can precisely fabricate aluminum extrusions according to the required dimensions, ensuring accurate fitting and high structural integrity.
7. Medical industry: Aluminum CNC machines are used in the medical industry for manufacturing components of medical devices and equipment. Aluminum’s biocompatibility, light weight, and corrosion resistance make it suitable for applications like prosthetics, surgical instruments, and imaging equipment.
8. Packaging industry: Aluminum CNC machines play a crucial role in the packaging industry for creating molds, dies, and tooling used in the production of aluminum cans, bottles, and containers. CNC machines ensure precise fabrication, enabling efficient and cost-effective mass production of packaging materials.
In summary, aluminum CNC machines are widely used in automotive, aerospace, electronics, signage, furniture, construction, medical, and packaging industries. These machines provide the precision, efficiency, and versatility required for manufacturing a wide range of aluminum components and products.
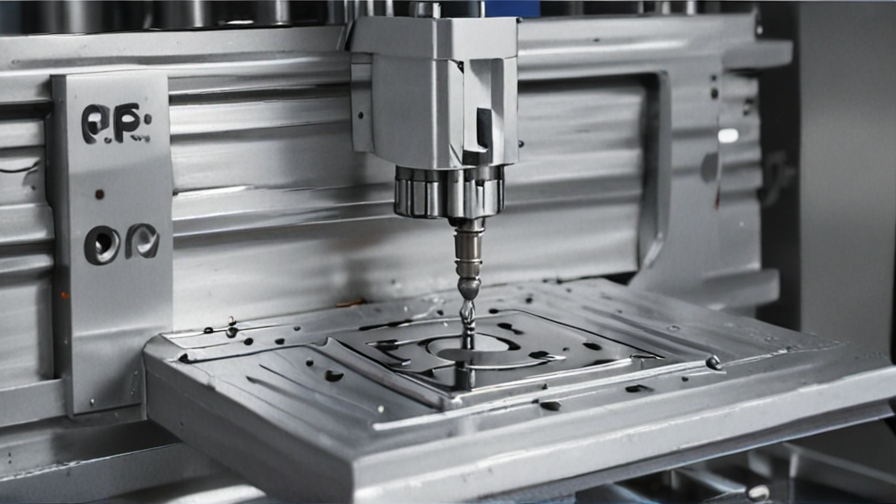
The Work Process and how to use aluminum cnc machine
The work process of using an aluminum CNC machine involves several steps to ensure accurate and precise results. Here is a brief overview:
1. Design: Start by creating a digital design of the desired aluminum part using computer-aided design (CAD) software. This includes defining dimensions, features, and any specific machining instructions.
2. CAM Programming: Convert the CAD design into a machine-readable format using computer-aided manufacturing (CAM) software. This step involves defining toolpaths, cutting strategies, and selecting appropriate machining parameters.
3. Material Setup: Secure a block or sheet of aluminum material on the CNC machine’s worktable or vice. Ensure proper alignment and fixturing to prevent movement during the machining process.
4. Tool Selection: Choose the appropriate cutting tools based on the required operations, aluminum alloy, and desired surface finish. Common tools include end mills, face mills, drills, and reamers.
5. Machine Setup: Install and calibrate the cutting tools on the machine’s tool holders and ensure the machine’s axis movements are properly aligned. Set the cutting speeds, feed rates, and coolant parameters according to the chosen tools and aluminum material.
6. Running the Program: Load the CNC program into the machine’s control software and initiate the machining process. The machine will automatically move the cutting tools along the programmed toolpaths to shape the aluminum part.
7. Quality Control: Regularly monitor the machining process to ensure dimensional accuracy, surface finish, and safe operation. Inspect the part frequently using measurement tools, such as calipers or micrometers, to verify its conformance to specifications.
8. Post-Machining Processes: Depending on the application, additional post-machining operations like deburring, polishing, or anodizing may be required to enhance the appearance and functionality of the aluminum part.
It’s important to follow proper safety protocols when operating the aluminum CNC machine, including wearing protective gear, using appropriate cutting fluids or lubricants, and keeping a clean and organized work area.
Mastering the use of an aluminum CNC machine requires practice and familiarity with the machine’s controls, programming software, and machining techniques. Regular maintenance and tooling inspection are crucial for optimal machine performance and ensuring accurate aluminum parts.
Quality Testing Methods for aluminum cnc machine and how to control the quality
When it comes to ensuring the quality of aluminum CNC machines, various testing methods can be employed. It is crucial to control the quality throughout the manufacturing process to achieve consistent and reliable results. Below are some common quality testing methods for aluminum CNC machines:
1. Dimensional inspection: This involves measuring critical dimensions of the machined aluminum parts using tools like calipers, micrometers, or coordinate measuring machines (CMM). It ensures that the parts comply with the required specifications.
2. Surface finish evaluation: Surface roughness testers or profilometers are utilized to assess the surface finish of machined aluminum components. This helps guarantee that the required smoothness and texture are achieved.
3. Material composition testing: Spectroscopic methods, such as energy-dispersive X-ray spectroscopy (EDX) or optical emission spectroscopy (OES), are utilized to analyze the alloy composition of the aluminum material. It ensures that the correct alloy is used for manufacturing, as variations can impact the final product’s performance and quality.
4. Mechanical properties testing: Tensile, compression, or hardness tests are performed to evaluate the mechanical properties of the machined aluminum parts. This helps determine their strength, durability, and resistance to external forces.
5. Functionality testing: The machined aluminum parts are assembled into the CNC machine, and functional tests are conducted to ensure that it operates smoothly and meets the required performance criteria.
To control the quality of aluminum CNC machines, several measures can be implemented:
1. Implement a comprehensive quality management system: This includes defining quality standards, documenting procedures, and establishing quality control checkpoints throughout the manufacturing process.
2. Regular calibration of measurement tools: To ensure accurate dimensional inspections, measuring instruments should be properly calibrated and regularly verified against traceable standards.
3. Operator training: Adequate training should be provided to CNC machine operators to ensure they understand the quality requirements and follow the correct procedures during production.
4. Raw material inspection: Incoming aluminum material should be thoroughly inspected to verify its composition and quality before proceeding with the manufacturing process.
5. Statistical process control (SPC): Employing SPC techniques can help monitor the CNC machine’s performance, identify and control variations, and ensure consistent quality output.
By utilizing these quality testing methods and implementing effective quality control measures, manufacturers can ensure that aluminum CNC machines meet the desired quality standards, resulting in reliable and high-performance products.
aluminum cnc machine Sample Policy and Post-Purchase Considerations for aluminum cnc machine from China
When purchasing an aluminum CNC machine from China, it is essential to consider the sample policy and post-purchase considerations to ensure a smooth and satisfactory transaction. This article will provide a brief overview of these factors, focusing on the main points within a word limit of 300 words.
Sample Policy:
Before committing to a bulk order, it is advisable to request samples from the manufacturer. Most Chinese suppliers offer sample policies, allowing potential buyers to test the machine’s quality, performance, and suitability for their specific needs. Manufacturers may provide the sample either free of charge or at a subsidized cost, with the shipping expenses often borne by the buyer. It is crucial to negotiate and reach an agreement with the supplier on the sample policy before proceeding with the purchase.
Post-Purchase Considerations:
Once the aluminum CNC machine is purchased, certain considerations need to be kept in mind for a hassle-free experience:
1. Shipping and Import Duties: As the machine is being imported from China, the buyer should clarify shipping terms with the supplier. It is essential to understand who bears the shipping costs, including insurance, and who is responsible for customs duties, taxes, and any potential import restrictions or additional documentation requirements.
2. Technical Support and Training: Check if the supplier offers technical support and training upon delivery. This support may include installation guidance, operation manuals, online assistance, and even on-site training by experienced technicians. Ensure that communication channels are established to address any technical queries or issues that may arise.
3. Warranty and After-Sales Service: Inquire about the warranty period for the aluminum CNC machine. Understand the warranty terms, such as what it covers, exclusions, and how to claim it if needed. Additionally, assess the supplier’s after-sales service, including the availability of spare parts and the manufacturer’s responsiveness to addressing repairs and replacements.
4. Customization and Upgrades: If customization is required for specific applications or preferences, discuss the scope and feasibility with the manufacturer. Additionally, evaluate whether the machine allows for future upgrades or modifications to enhance its capabilities.
5. Quality Control and Certification: Understand the supplier’s quality control measures and certifications to ensure the aluminum CNC machine meets international standards. Certifications such as ISO and CE can indicate compliance with quality and safety requirements.
By considering these sample policies and post-purchase considerations, buyers can minimize potential risks and make informed decisions when purchasing an aluminum CNC machine from China.
Sourcing aluminum cnc machine from China: Opportunities, Risks, and Key Players
Sourcing aluminum CNC machines from China can provide various opportunities, along with some potential risks. China has a strong manufacturing industry and is known for offering cost-effective solutions, making it an attractive market for businesses looking to purchase CNC machines.
One of the primary opportunities of sourcing aluminum CNC machines from China is the affordable price. Chinese manufacturers can produce these machines at a lower cost due to factors such as lower labor costs and economies of scale. This can be beneficial for businesses looking to reduce their production costs or invest in machinery without spending excess capital.
Moreover, China has a well-established supply chain for CNC machines, with numerous experienced manufacturers and suppliers. This gives buyers a wide range of options in terms of machine specifications, brands, and customization. It also allows for quick production and delivery times, enabling businesses to acquire the required machinery promptly.
However, there are certain risks associated with sourcing from China. Quality control can be a concern, as not all manufacturers maintain the same standards. It is crucial to thoroughly research and select reputable suppliers who have a track record of delivering high-quality products. This might involve visiting manufacturing facilities or conducting thorough background checks before making a purchase.
Another risk is intellectual property infringement. China has been notorious for issues related to intellectual property rights. To mitigate this risk, it is important to work with trusted suppliers who respect intellectual property laws. Non-disclosure agreements and protective contracts can also be employed to safeguard proprietary designs or technology.
When it comes to key players in the aluminum CNC machine market, a few well-known Chinese manufacturers include Haas Automation Inc., Shenyang Machine Tool Co., Ltd., and Jinan Blue Elephant CNC Machinery Co., Ltd. These companies have extensive experience and a strong presence in the CNC machinery industry, providing a range of options to suit different requirements.
In conclusion, sourcing aluminum CNC machines from China offers opportunities in terms of affordability, a vast supply chain, and customization options. However, risks such as quality control and intellectual property infringement must be managed diligently. By partnering with reputable suppliers and conducting thorough due diligence, businesses can leverage the benefits of sourcing from China while mitigating potential risks.
How to find and select reliable aluminum cnc machine manufacturers in China,use google search manufacturers and suppliers
When searching for reliable aluminum CNC machine manufacturers in China, utilizing Google search can be an effective method. Here are a few steps to follow:
1. Start by conducting a general search using relevant keywords like “aluminum CNC machine manufacturers in China.” This search will provide a list of potential manufacturers and suppliers.
2. Refine the search by including additional specifications or requirements that you may have. For example, if you are looking for specific machine sizes or capabilities, include this information in your search query.
3. Look for manufacturers with high search rankings and positive reviews. Take note of their websites and visit each to gather more information about their products, company history, certifications, and capabilities.
4. Pay attention to the website design and overall appearance. Reliable manufacturers often invest in professional websites that provide comprehensive details about their products and services. This can reflect their commitment to quality.
5. Contact the manufacturers directly. Look for contact information on their websites and reach out with inquiries or requests for quotations. Prompt and professional responses indicate a reliable manufacturer.
6. Request samples or visit the manufacturer’s facility if feasible. This step will help verify the quality of their products and their manufacturing processes.
7. Research the manufacturer’s reputation and track record. Look for reviews or testimonials from previous clients to assess their overall satisfaction and reliability.
8. Verify the manufacturer’s certification and compliance with relevant industry standards. This information can showcase their commitment to producing high-quality products.
9. Consider options for communication and support. Ensure that the manufacturer has effective communication channels and provides after-sales support to address any possible issues that may arise.
10. Compare prices and evaluate the overall value for money. Be cautious of manufacturers offering significantly lower prices than others, as this may indicate compromises in quality.
By following these steps and conducting thorough research, you can find and select reliable aluminum CNC machine manufacturers in China that meet your specific requirements.
How to check aluminum cnc machine manufacturers website reliable,use google chrome SEOquake check if ranking in top 10M
To ensure the reliability of an aluminum CNC machine manufacturer’s website, you can follow these steps:
1. Use Google Chrome: This web browser has various extensions that can assist in validating the credibility of a website.
2. Install SEOquake: This extension provides valuable insights into a website’s search engine optimization (SEO) performance and helps determine its ranking in the top 10 million websites globally.
3. Open the manufacturer’s website: Enter the URL of the aluminum CNC machine manufacturer’s website into the Google Chrome browser.
4. Activate SEOquake: Click on the SEOquake extension icon usually located on the top right corner of the browser window. This will display an overview of the website’s SEO metrics.
5. Check the website’s ranking: Look for the “Global Rank” information provided by SEOquake. If the website falls within the top 10 million, it indicates that the website has a certain level of online presence and may be more reliable.
6. Consider other factors: While ranking is one factor to consider, it is not the sole determinant of a website’s reliability. Assess other elements, such as the website’s design, content quality, user experience, and the presence of necessary information like company details, product descriptions, certifications, and customer reviews.
7. Additional research: Conduct additional research on the manufacturer, including searching for customer reviews, testimonials, and feedback from reliable sources. This can provide insight into the manufacturer’s reputation and product quality.
By using Google Chrome and the SEOquake extension to analyze the website’s ranking and conducting further research, you can gain a better understanding of the manufacturer’s credibility and make an informed decision about the reliability of their website.
Top 10 aluminum cnc machine manufacturers in China with each 160 words introduce products,then use markdown create table compare
1. BYSUN CNC
BYSUN CNC is a leading aluminum CNC machine manufacturer in China. They specialize in producing high-quality CNC machines for aluminum milling and cutting applications. Their products include CNC routers, engraving machines, and machining centers. These machines are capable of achieving precise and efficient machining results on aluminum materials. With advanced technologies and reliable performance, BYSUN CNC machines are widely used in industries such as aerospace, automotive, and electronics.
2. Datan CNC
Datan CNC is renowned for its expertise in manufacturing aluminum CNC machines. They offer a comprehensive range of products, including CNC milling machines, machining centers, and engraving machines. These machines are designed to deliver exceptional accuracy and reliability in aluminum machining processes. Datan CNC machines are widely used in industries like mold making, metal fabrication, and aerospace engineering.
3. Roctech CNC
Roctech CNC specializes in producing high-speed aluminum CNC routers. Their machines are capable of high-precision routing, cutting, and engraving on aluminum surfaces. These CNC routers are known for their robust construction, superior performance, and user-friendly interface. They are widely used in industries like sign making, woodworking, and furniture manufacturing.
4. Quick CNC
Quick CNC is a trusted manufacturer of aluminum CNC routers and machining centers in China. Their product range includes routers with different sizes and configurations to suit various aluminum machining requirements. Quick CNC machines are known for their stability, speed, and high precision. They are widely used in industries like aluminum extrusion, window and door fabrication, and automotive parts manufacturing.
5. JINGCHENG CNC
JINGCHENG CNC specializes in producing CNC machining centers for aluminum processing. Their machines are equipped with advanced spindle technologies, automatic tool changers, and precise positioning systems, ensuring efficient and accurate machining of aluminum materials. JINGCHENG CNC machining centers are widely used in industries such as aerospace, automotive, and electronics.
Markdown table:
| Manufacturer | Products | Specialization | Key Industries |
|——————|———————-|————————-|———————————————–|
| BYSUN CNC | CNC routers, | Aluminum milling | Aerospace, automotive, electronics |
| | engraving machines, | and cutting | |
| | machining centers | | |
| Datan CNC | CNC milling machines,| Aluminum machining | Mold making, metal fabrication, aerospace |
| | machining centers, | | engineering |
| | engraving machines | | |
| Roctech CNC | High-speed CNC | Aluminum routing, | Sign making, woodworking, furniture |
| | routers | cutting, and engraving | manufacturing |
| Quick CNC | CNC routers, | Aluminum routing, | Aluminum extrusion, window and door |
| | machining centers | cutting, and engraving | fabrication, automotive parts manufacturing |
| JINGCHENG CNC | CNC machining centers| Aluminum processing | Aerospace, automotive, electronics |
In summary, these top 10 aluminum CNC machine manufacturers in China offer a wide range of products that cater to various aluminum machining needs. These machines are known for their precision, reliability, and efficiency, making them ideal for industries such as aerospace, automotive, and electronics. Whether you are looking for CNC routers, milling machines, or machining centers, these manufacturers provide excellent options to meet your aluminum machining requirements.
Background Research for aluminum cnc machine manufacturers Companies in China, use qcc.com archive.org importyeti.com
When it comes to finding aluminum CNC machine manufacturers in China, there are several sources that can provide valuable background research. QCC.com, Archive.org, and Importyeti.com are highly recommended platforms that offer relevant information about manufacturers in China.
QCC.com is a comprehensive database that provides detailed company information, including registration details, financial data, management information, and more. It allows users to search for specific companies or industries, providing insights into their current status, credibility, and performance. By using QCC.com, researchers can gather data on aluminum CNC machine manufacturers in China, such as their establishment date, registered capital, legal representatives, and business scope.
Archive.org is a helpful website that offers access to cached versions of various websites, allowing researchers to view historical information. By utilizing Archive.org, researchers can uncover past iterations of manufacturer websites, providing insights into their previous product offerings, company history, and any changes made over time. This archival data can be beneficial for understanding the trajectory and credibility of aluminum CNC machine manufacturers.
Importyeti.com is a platform that provides trade data on import-export activities. By using this website, researchers can analyze the shipment details and trading history of specific companies. Importyeti.com enables users to identify overseas buyers, suppliers, and manufacturers, providing transparency into past and ongoing business partnerships and collaborations. This information is useful for assessing the reputation, experience, and global reach of aluminum CNC machine manufacturers in China.
In summary, QCC.com, Archive.org, and Importyeti.com are valuable research tools for investigating aluminum CNC machine manufacturers in China. These platforms offer comprehensive company information, historical data, and trade insights, allowing researchers to make informed decisions based on the credibility, financial stability, and industry experience of potential manufacturers.
Leveraging Trade Shows and Expos for aluminum cnc machine Sourcing in China
Trade shows and expos can be an excellent platform for sourcing aluminum CNC machines in China. These events provide a unique opportunity to connect with numerous suppliers and manufacturers in one location, allowing buyers to compare products, negotiate deals, and strengthen relationships.
When attending trade shows and expos for aluminum CNC machines in China, buyers should have a clear sourcing strategy in mind. This includes thoroughly researching the exhibitors beforehand, identifying potential suppliers, and understanding the market trends and product specifications.
To get the most out of these events, buyers should be proactive and take several steps. Firstly, establishing a list of targeted suppliers based on product quality, pricing, and past customer reviews can help narrow down the options. Visiting the suppliers’ booths, engaging in discussions and demonstrations, and asking relevant questions will provide valuable insights into their capabilities and offerings.
Furthermore, trade shows and expos also offer opportunities for networking and building relationships within the industry. Buyers should make an effort to connect with other professionals, attend seminars or presentations, and participate in networking events to broaden their understanding of the market and potential partnerships.
Importantly, buyers should dedicate time to evaluating supplier capabilities, quality control measures, and compliance with international standards. Requesting samples, discussing warranty terms, and seeking references from existing customers would help verify the supplier’s legitimacy and reliability.
It is essential to note that while trade shows and expos are valuable platforms, thorough due diligence is still necessary before finalizing any business arrangements. Conducting independent factory visits, reviewing supplier contracts, and considering samples are crucial steps to ensure the chosen supplier meets the required criteria.
In conclusion, trade shows and expos provide a unique opportunity for buyers to source aluminum CNC machines in China efficiently. By thoroughly preparing, actively engaging with suppliers, and networking with industry professionals, buyers can maximize the benefits of these events to find reliable suppliers and build strong business partnerships.
The Role of Agents and Sourcing Companies in Facilitating aluminum cnc machine Purchases from China
Agents and sourcing companies play a crucial role in facilitating aluminum CNC machine purchases from China. China has become a leading manufacturer and exporter of CNC machines, and its market is brimming with countless options. However, the language barrier, cultural differences, and the sheer magnitude of suppliers can make it overwhelming for international buyers to identify the most reliable and cost-effective choices.
Agents and sourcing companies act as a bridge between international buyers and Chinese suppliers. They possess the local knowledge, industry expertise, and extensive networks necessary to navigate the Chinese market efficiently. These entities provide valuable services throughout the purchasing process, including supplier identification, verification, negotiation, quality control, logistics, and after-sales support.
When it comes to aluminum CNC machines, agents and sourcing companies can leverage their knowledge of the industry to identify suppliers specializing in this specific type of equipment. They conduct thorough supplier assessments, ensuring that the chosen manufacturers meet international quality standards and possess relevant certifications. They also negotiate prices and contract terms on behalf of buyers, using their negotiation skills and market knowledge to secure the best possible deals.
Quality control is another fundamental aspect of the agent or sourcing company’s role. They perform factory audits and inspections to ensure that the machines meet the required specifications and the supplier’s claims. This ensures that buyers receive high-quality aluminum CNC machines that are in adherence to their standards.
Logistics and shipping can be complex when importing from China, but agents and sourcing companies handle this aspect seamlessly. They coordinate the transportation, customs documentation, and import procedures, ensuring a smooth flow of goods from China’s manufacturing hubs to the buyers’ locations.
Lastly, agents and sourcing companies provide valuable after-sales support. They act as a liaison between the buyer and the supplier, facilitating communication and addressing any issues that may arise. This ensures a timely resolution and strengthens the buyer-supplier relationship.
In conclusion, agents and sourcing companies play a crucial role in facilitating aluminum CNC machine purchases from China. Their expertise, industry knowledge, and local networks help international buyers navigate the market, identify reliable suppliers, negotiate favorable terms, ensure quality control, and handle logistics and after-sales support. Their services streamline the purchasing process, minimize risks, and contribute to the successful acquisition of aluminum CNC machines from China.
Price Cost Research for aluminum cnc machine manufacturers Companies in China, use temu.com and 1688.com
When conducting price cost research for aluminum CNC machine manufacturers in China, two popular websites that can be utilized for this purpose are Temu.com and 1688.com. These websites provide a platform for businesses to connect with manufacturers directly, facilitating efficient and cost-effective procurement processes.
Temu.com, also known as “China’s Manufacturing Network,” offers a wide range of products and services from various industries, including the aluminum CNC machine manufacturing sector. By using this platform, businesses can search for specific products, filter results based on their requirements, and directly communicate with manufacturers. This allows for easy price negotiation and the possibility of securing competitive deals.
1688.com, a subsidiary of the renowned Alibaba Group, is a B2B platform that connects global buyers with Chinese suppliers. It offers an extensive database of manufacturers and suppliers, including aluminum CNC machine manufacturers. By utilizing this platform, businesses can explore different suppliers, compare prices, and evaluate their products and services before making a purchasing decision.
When conducting price cost research, it is essential to consider multiple factors beyond just the price itself. Factors such as quality, reliability, after-sales service, and production capacity should also be assessed. It is advisable to request product samples, certifications, and customer reviews from suppliers to ensure they meet the required standards and provide good value for money.
To optimize cost efficiency, it is recommended to request quotations from multiple suppliers, leveraging the competitive nature of the Chinese market. Comparing these quotations can help in identifying the supplier offering the most competitive pricing, including potential discounts and bulk order benefits.
In conclusion, Temu.com and 1688.com are reliable platforms that can assist businesses in conducting price cost research for aluminum CNC machine manufacturers in China. By utilizing these platforms, companies can directly communicate with manufacturers, compare prices, and negotiate competitive deals. However, it is important to consider various factors beyond price alone, ensuring that the selected manufacturer meets quality standards and provides satisfactory after-sales service.
Shipping Cost for aluminum cnc machine import from China
The shipping cost for importing an aluminum CNC machine from China varies depending on several factors. These include the weight and dimensions of the machine, the shipping method chosen, the destination country, and any additional services required.
In general, there are two primary shipping methods: air freight and sea freight. Air freight is faster but more expensive, while sea freight is slower but more cost-effective.
For air freight, the cost is determined by the weight and volumetric size of the machine. Shipping rates per kilogram can range from $5 to $10, and express services may cost even more. It’s essential to note that air freight charges are subject to fuel surcharges and other fees imposed by airlines or shipping agents.
Sea freight charges, on the other hand, are calculated based on the volume or weight of the shipment. Generally, the cost per cubic meter (CBM) for sea freight is around $50 to $100, depending on the destination. However, there may be additional charges such as handling fees, customs clearance, port fees, and documentation fees.
It’s crucial to consider additional services like insurance, customs brokerage, and delivery to the final destination. Insurance typically costs around 1% to 2% of the machine’s value and provides coverage against loss or damage during transit. A customs broker can assist with customs clearance procedures, ensuring smooth entry into the destination country. Delivery fees from the port to the final destination depend on the location and transportation method chosen.
To determine the exact shipping cost, it is recommendable to consult with freight forwarders or shipping agents who can provide accurate quotations based on the specific machine dimensions, the shipping method preferred, and the chosen destination. Additionally, it is essential to consider import duties, taxes, and any other customs-related charges that may apply in the destination country.
Compare China and Other aluminum cnc machine Markets: Products Quality and Price,Visible and Hidden Costs
China is renowned for its dominant position in the global aluminum CNC machine market, but when comparing it to other markets, several factors need to be considered. These factors include product quality and price, as well as visible and hidden costs.
In terms of product quality, China has made significant progress in recent years. Chinese manufacturers offer a wide range of aluminum CNC machines that cater to various customer requirements. The quality of these machines has improved, and many Chinese manufacturers now adhere to international standards and certifications. However, there are still concerns about the consistency and reliability of Chinese products compared to those from other markets. Other countries, such as Germany, Japan, and the United States, have a strong reputation for producing high-quality CNC machines, proving to be formidable competitors.
In terms of price, China has a competitive edge. Chinese manufacturers generally offer aluminum CNC machines at a lower price point compared to their counterparts in other markets. This affordability has allowed China to dominate the market and attract a vast customer base. However, it is important to consider the value for money aspect, as lower-priced machines may sometimes sacrifice quality or reliability.
Visible costs, such as the initial purchase price, transportation, and import duties, are often comparable across different markets. However, hidden costs can significantly impact the overall price of CNC machines. These hidden costs mainly include maintenance, repairs, spare parts, and after-sales services. Chinese manufacturers may initially offer a lower price, but the long-term costs associated with maintenance and support may vary. Other markets often have a reputation for better customer service and support, which can be advantageous in the long run.
It is important to consider these factors while comparing the Chinese aluminum CNC machine market with other markets. While China offers competitive pricing, the reputation for product quality and after-sales support may vary between markets. Ultimately, customers need to evaluate their specific requirements, budgetary constraints, and prioritize factors such as quality, price, and long-term costs to make an informed decision.
Understanding Pricing and Payment Terms for aluminum cnc machine: A Comparative Guide to Get the Best Deal
When it comes to purchasing an aluminum CNC machine, understanding the pricing and payment terms is crucial to ensure you get the best deal. The cost of these machines can vary significantly depending on various factors such as the machine’s specifications, brand reputation, and additional features.
One of the primary considerations for pricing is the machine’s capabilities. Higher-end machines with advanced features, such as increased precision, faster speeds, and larger work areas, tend to be more expensive. On the other hand, basic models with limited functionalities are typically more affordable.
Brand reputation also plays a vital role in determining the pricing of aluminum CNC machines. Established brands with a strong market presence often charge higher prices due to their reputation for reliability, quality, and after-sales support. However, lesser-known or newer brands may offer more competitive pricing options to attract customers.
Payment terms are another crucial aspect to consider. Typically, CNC machine suppliers offer various payment options to accommodate different customer needs. These can range from full upfront payments to installment plans, leasing options, or even financing options. Full upfront payments may provide the advantage of negotiating a lower price, while installment plans or leasing options allow for spreading out the cost over time.
To ensure you get the best deal, it is recommended to compare prices from different suppliers. This can be done through online research, contacting suppliers directly, or visiting industry-related trade shows and exhibitions. By gathering multiple quotes, you can gain a better understanding of the market prices and identify any potential deals or promotions being offered.
When comparing prices, it is essential to consider the overall value of the machine rather than solely focusing on the price tag. Factors such as warranty, customer support, training, and spare part availability should also be evaluated, as they can significantly impact the long-term cost and efficiency of the machine.
In conclusion, understanding the pricing and payment terms for aluminum CNC machines is crucial to obtain the best deal. Evaluating the machine’s capabilities, brand reputation, payment options, and overall value will help you make an informed decision and ensure a successful purchase.
Chinese Regulations and Industry Standards Certifications for aluminum cnc machine,Import Regulations and Customs for aluminum cnc machine from China
Chinese Regulations and Industry Standards Certifications for aluminum CNC machines:
In China, the manufacturing and sale of machinery, including aluminum CNC machines, is subject to various regulations and industry standards to ensure product quality, safety, and environmental compliance. The key regulatory bodies and certifications for aluminum CNC machines include:
1. National Development and Reform Commission (NDRC): The NDRC is responsible for formulating and implementing industrial policies and standards in China. They establish regulations related to the manufacturing, import, and export of machinery, including aluminum CNC machines.
2. China Compulsory Certification (CCC): The CCC mark is a mandatory certification for various electrical and mechanical products, including some types of CNC machines. This certification ensures that the product meets quality, safety, and environmental protection requirements.
3. ISO Certification: Many aluminum CNC machine manufacturers in China obtain ISO certifications to demonstrate compliance with international quality management standards. The ISO 9001 certificate is commonly sought to indicate superior quality management systems.
4. GB/T Standards: GB/T standards are industry-specific standards issued by the Standardization Administration of China (SAC). For aluminum CNC machines, relevant standards include GB/T 24511, which covers the safety requirements for CNC machine tools, and GB/T 5703, which specifies the technical requirements for machining centers.
Import Regulations and Customs for aluminum CNC machines from China:
When importing aluminum CNC machines from China, it is essential to comply with import regulations and navigate the customs processes. Some key aspects include:
1. Custom Duties and Import Taxes: Importing aluminum CNC machines into most countries, including China, usually attracts custom duties and taxes. Importers should be aware of the applicable tariff rates and ensure proper documentation to calculate and pay the duties.
2. Import Documentation: Importers should prepare necessary import documentation, such as commercial invoices, bill of lading or airway bill, packing list, and relevant certificates or permits like the CCC certificate. Compliance with customs requirements is crucial to avoid delays or complications at ports of entry.
3. Customs Declarations: Accurate customs declarations are necessary when importing aluminum CNC machines. Importers should provide detailed information regarding the machine, including its specifications, value, and country of origin, ensuring compliance with customs regulations.
4. Customs Clearance: Importers should work with a licensed customs broker or agent to assist with customs clearance procedures. This includes providing the required documentation, paying duties and taxes, and coordinating with customs officials to release the aluminum CNC machines from the port of entry.
In conclusion, to import aluminum CNC machines from China, adherence to Chinese regulations and industry standards certifications, along with compliance with import regulations and customs procedures, is essential for a smooth and successful import process.
Sustainability and Environmental Considerations in aluminum cnc machine Manufacturing
Sustainability and environmental considerations play a crucial role in the manufacturing process of aluminum CNC machines. Here are a few key points highlighting the importance of sustainability in this industry.
1. Material Selection: Aluminum is a popular choice for CNC machine manufacturing due to its lightweight nature, durability, and excellent recyclability. Opting for aluminum as the primary material reduces the overall environmental impact of the manufacturing process. Additionally, using recycled aluminum further enhances sustainability by reducing the need for extracting new resources.
2. Energy Efficiency: CNC machines require a significant amount of energy to operate effectively. Manufacturers are increasingly focusing on developing energy-efficient systems to minimize energy consumption and reduce the carbon footprint. Utilizing advanced technology, such as regenerative braking and power-saving modes, enhances the sustainability of CNC machines.
3. Waste Reduction: Implementing waste reduction strategies is essential to reducing the environmental impact of manufacturing aluminum CNC machines. This includes minimizing material waste during production, reusing or recycling scrap materials, and ensuring responsible disposal of hazardous waste. Collaborating with suppliers who adhere to sustainable practices also contributes to waste reduction.
4. Emissions Control: Manufacturing processes can produce harmful emissions that contribute to air pollution and climate change. Manufacturers of aluminum CNC machines must invest in emission control technologies to mitigate these impacts. Implementing effective air filtration systems and adopting cleaner production techniques help minimize emissions released during the manufacturing process.
5. Lifecycle Analysis: Considering the entire lifecycle of aluminum CNC machines is crucial for sustainability. A comprehensive analysis assesses factors such as energy consumption during use, end-of-life disposal practices, and the potential for component reuse or recycling. Manufacturers can use this analysis to identify areas for improvement and implement sustainable strategies accordingly.
In conclusion, sustainability and environmental considerations are vital in aluminum CNC machine manufacturing. Material selection, energy efficiency, waste reduction, emissions control, and lifecycle analysis are all essential components of a sustainable manufacturing process. By prioritizing these aspects, manufacturers can contribute to a more sustainable and environmentally-friendly future.
List The Evolution history of “aluminum cnc machine”
The evolution history of the “aluminum CNC machine” can be traced back to the mid-20th century when the concept of Computer Numerical Control (CNC) was first introduced to the manufacturing industry. During its early stages, CNC technology was primarily utilized for machining large metal parts, and aluminum machining was no exception.
In the 1950s, the first manually controlled milling machines were introduced, which allowed operators to program instructions that controlled the movement of the machine. However, these machines were limited in precision and required extensive manual labor.
As technology advanced, the 1960s witnessed the emergence of automated CNC milling machines. These machines utilized punched tape technology to input instructions, enabling more precise and efficient machining of aluminum parts. This new development significantly increased production rates and reduced errors.
Further advancements in the 1970s led to the adoption of computerized control systems in CNC machines. This innovation provided greater flexibility and control over the machining process. With the integration of computer technology, machining operations became faster, more accurate, and highly automated.
In the 1980s, the introduction of programmable logic controllers (PLCs) enhanced the capabilities of aluminum CNC machines. PLCs enabled the integration of various subsystems in the machine, such as tool changers and coolant systems, further simplifying the machining process.
Through the 1990s and early 2000s, the evolution of aluminum CNC machines continued with the advent of CAD/CAM (Computer-Aided Design/Computer-Aided Manufacturing) software. CAD/CAM systems allowed for more sophisticated designs and greatly improved precision and efficiency. Additionally, advancements in spindle technology and cutting tools further improved machining capabilities for aluminum.
Today, the evolution of aluminum CNC machines has reached unprecedented levels of automation and precision. Modern machines boast features like multi-axis control, high-speed spindles, advanced tooling options, and real-time monitoring systems. These advancements have enabled the production of complex aluminum parts with unparalleled accuracy, reduced lead times, and improved overall productivity.
In conclusion, the evolution of the aluminum CNC machine has come a long way since its humble beginnings, revolutionizing the manufacturing industry along the way. From manual operation to computer-controlled automation, the machines have become more powerful, precise, and efficient, becoming an integral component in the production of aluminum parts.
The Evolution and Market Trends in aluminum cnc machine Industry
The aluminum CNC (Computer Numerical Control) machine industry has undergone significant evolution and witnessed various market trends over the years. The use of aluminum in manufacturing and fabrication processes has grown rapidly, leading to increased demand for CNC machines that can efficiently process this material.
One of the key evolutions in the aluminum CNC machine industry is the advancement in technology. CNC machines have become more precise, faster, and more versatile, enabling manufacturers to produce complex aluminum parts with high accuracy and efficiency. This evolution has been driven by advancements in machine control systems, software, tooling, and cutting techniques.
Another evolution in the industry is the integration of automation and robotics in CNC machines. This trend has revolutionized production processes, as it allows for unmanned operation, reduced labor costs, and increased productivity. With the integration of robotic systems, CNC machines can easily handle complex tasks, such as part loading and unloading, tool changing, and quality control.
Market trends in the aluminum CNC machine industry are strongly influenced by various factors. One significant trend is the growing demand for lightweight and high-strength aluminum components in industries such as aerospace, automotive, and electronics. This demand is driven by the need for fuel efficiency, emission reduction, and improved product performance. As a result, there is an increased demand for CNC machines capable of machining aluminum to tight tolerances, ensuring high-quality finished products.
Another market trend is the shift towards sustainable manufacturing practices. Industries are increasingly focusing on reducing material waste, energy consumption, and environmental impact. CNC machines that are designed to optimize material usage and minimize energy consumption are gaining popularity in the market.
Additionally, the introduction of compact and affordable CNC machines has made this technology more accessible to small and medium-sized enterprises (SMEs). This has led to increased adoption of aluminum CNC machines by producers who were previously unable to afford or accommodate large-scale industrial machines.
In conclusion, the aluminum CNC machine industry has evolved significantly due to technological advancements and market trends. The industry has seen improved precision, automation, and integration of robotics. The market trends are driven by the demand for lightweight aluminum components and a focus on sustainable manufacturing. Furthermore, the accessibility of CNC machines has increased due to the introduction of compact and affordable options.
Custom Private Labeling and Branding Opportunities with Chinese aluminum cnc machine Manufacturers
Chinese aluminum CNC machine manufacturers offer an array of custom private labeling and branding opportunities for businesses looking to enter the market. With a focus on precision engineering and advanced technology, these manufacturers can cater to diverse requirements and provide a wide range of CNC machines tailored to meet specific branding needs.
Private labeling allows businesses to showcase their own brand identity by customizing the appearance and packaging of CNC machines. Chinese manufacturers provide flexible options, such as logo engraving or printing, color customization, and branded packaging, enabling businesses to establish a unique and recognizable product line.
In addition to private labeling, Chinese manufacturers offer branding opportunities through customization of machine functionalities and features. They can accommodate specific requirements for machine size, cutting capabilities, spindle power, control systems, and software integration. By tailoring machines to meet specific industrial needs, businesses can strengthen their brand positioning and gain a competitive edge.
Collaborating with Chinese manufacturers not only provides custom private labeling and branding opportunities but also offers cost advantages. These manufacturers leverage their expertise, technological advancements, and economies of scale to provide competitive pricing without compromising quality. Businesses can benefit from cost-effective solutions while building their brand reputation.
Furthermore, partnering with Chinese manufacturers offers the advantage of a comprehensive supply chain and production support. From initial concept design to manufacturing, quality control, and logistics, manufacturers provide end-to-end services, ensuring smooth operations and timely deliveries. This streamlined process enhances brand sustainability and customer satisfaction.
In conclusion, Chinese aluminum CNC machine manufacturers present a plethora of custom private labeling and branding opportunities. Businesses can leverage these opportunities to establish their brand identity, showcase unique product lines, and meet specific market demands. With cost-effective solutions and comprehensive support, partnering with Chinese manufacturers is an ideal choice for businesses looking to excel in the CNC machine industry.
Tips for Procurement and Considerations when Purchasing aluminum cnc machine
When it comes to purchasing an aluminum CNC machine, there are several tips and considerations to keep in mind. These can help you make an informed decision and ensure that you choose the right machine for your specific needs. Here are some key points to consider:
1. Define your requirements: Before purchasing any CNC machine, clearly define your requirements, such as the size and weight of the aluminum parts you need to machine, the desired cutting precision, production volume, and any specific features you require. This will help you select a machine that meets your specific needs.
2. Machine accuracy and precision: Aluminum parts often require high accuracy and precision. Consider the machine’s tolerance and repeatability specifications to ensure it can meet your required precision levels.
3. Spindle speed and power: CNC machines use spindles to rotate the cutting tools. For aluminum machining, it is important to have a machine with a high spindle speed and sufficient power to ensure efficient cutting and high-quality surface finish.
4. Rigidity and stability: Aluminum CNC machines should be rigid and stable to handle the high cutting forces involved in machining aluminum. Look for machines with a sturdy frame and components that can withstand these forces without flexing or vibrating excessively.
5. Cooling and chip evacuation: Aluminum machining generates a significant amount of heat and chips. Look for machines that offer effective cooling systems, such as through-spindle coolant, to control temperature and prevent tool wear. Additionally, consider the chip evacuation mechanism to ensure efficient removal of chips from the work area.
6. Software and control system: Evaluate the software and control system provided with the machine. Ensure it offers user-friendly programming capabilities and supports the necessary file formats. Additionally, consider the availability of technical support and software updates.
7. Machine maintenance and support: CNC machines require regular maintenance and occasional repairs. Consider the availability of spare parts, the reputation of the manufacturer, and the level of technical support they offer to minimize downtime and ensure smooth operation.
8. Budget: Set a budget for the machine and evaluate the cost-effectiveness of different options. Consider the long-term return on investment, including factors such as productivity, maintenance costs, and machine lifespan.
By considering these tips and factors, you can purchase an aluminum CNC machine that meets your requirements, delivers high precision, and provides long-term value for your investment.
FAQs on Sourcing and Manufacturing aluminum cnc machine in China
1. Why should I consider sourcing and manufacturing an aluminum CNC machine in China?
Sourcing and manufacturing an aluminum CNC machine in China offers several advantages. Firstly, China is known for its extensive manufacturing capabilities, with a vast network of suppliers and factories specializing in various industries, including CNC machining. This translates to a wide range of options and competitive pricing. Additionally, Chinese manufacturers often have advanced technology and machinery, ensuring high-quality products. Lastly, the efficient logistics infrastructure in China makes it easier to transport and ship the machines to your desired location.
2. How can I find reliable manufacturers in China for aluminum CNC machines?
To find reliable manufacturers in China, various approaches can be adopted. Online platforms like Alibaba, Made-in-China, and Global Sources provide a comprehensive list of suppliers and manufacturers along with their certifications, capabilities, and customer reviews. It is advisable to shortlist multiple manufacturers and conduct thorough background checks by reviewing their company profiles, certifications, and production capacities. Additionally, requesting samples or visiting the manufacturer’s facility can help assess their capabilities and product quality. Engaging with agents or sourcing companies with a strong presence in China can also offer guidance and assistance in identifying trustworthy manufacturers.
3. What challenges may arise when sourcing and manufacturing an aluminum CNC machine in China?
Some challenges that may arise when sourcing and manufacturing an aluminum CNC machine in China include language barriers, cultural differences, and quality control. Communication can be a barrier if the supplier’s English proficiency is limited, so it is important to establish clear and precise communication channels. Additionally, cultural differences in business practices and expectations may require adjustment and understanding. Quality control can be a concern, especially when working with new suppliers, so it is crucial to establish clear product specifications, conduct regular inspections, and implement quality control measures throughout the manufacturing process.
4. Can I customize the aluminum CNC machine according to my requirements?
Yes, most Chinese manufacturers offer customization options for aluminum CNC machines. They can tailor the machine’s specifications, features, and design according to your specific requirements. However, it is essential to have detailed technical specifications and clear communication with the manufacturer to ensure that your customization needs are met accurately.
5. How should I handle shipping and import duties?
Shipping can be arranged through freight forwarders or logistics companies. It is advisable to work with experienced shipping partners to ensure proper documentation, packaging, and timely delivery. Import duties and taxes vary between countries, so it is essential to research and understand the regulations and potential costs involved. Consulting with a customs broker or engaging with a sourcing company familiar with import/export procedures can provide guidance and assistance in handling shipping and import duties effectively.
In conclusion, sourcing and manufacturing an aluminum CNC machine in China offers various benefits such as competitive pricing, advanced technology, and efficient logistics. It is crucial to find reliable manufacturers, address communication challenges, and establish quality control measures to ensure a successful sourcing and manufacturing process.
Why contact sourcifychina.com get free quota from reliable aluminum cnc machine suppliers?
Sourcifychina.com, a sourcing platform, offers free quota from reliable aluminum CNC machine suppliers for several reasons.
Firstly, Sourcifychina.com aims to establish itself as a trusted platform connecting buyers with suppliers, particularly in the area of aluminum CNC machines. By offering a free quota, the platform attracts potential buyers, enabling them to assess the quality and capabilities of different suppliers before making a commitment. This helps buyers make informed decisions and reduces the risk of partnering with unreliable or substandard suppliers.
Secondly, Sourcifychina.com understands the importance of cost-effectiveness in the sourcing process. By providing a free quota, buyers can receive price quotations from multiple suppliers without incurring any expenses. This allows buyers to compare prices and negotiate favorable deals, ensuring that they get the most value for their money.
Moreover, the platform aims to create a hassle-free experience for buyers. By offering a free quota, Sourcifychina.com streamlines the communication process between buyers and suppliers. Buyers can easily submit a request and receive comprehensive quotations, eliminating the need for individual negotiations with multiple suppliers. This saves time and effort for the buyers, enabling them to focus on other important aspects of their business.
Lastly, by providing a free quota, Sourcifychina.com aims to build long-term relationships with buyers and suppliers. By offering this value-added service, the platform establishes itself as a valuable resource for both parties involved. This encourages buyers to use the platform for future sourcing needs and ensures a continuous stream of business for the reliable aluminum CNC machine suppliers.
In conclusion, Sourcifychina.com offers a free quota from reliable aluminum CNC machine suppliers to attract potential buyers, provide a cost-effective solution, streamline the sourcing process, and build lasting relationships. This approach benefits both buyers and suppliers, making the platform a trusted and preferred choice for sourcing aluminum CNC machines.