Introduce about aluminium extrusion process guide,Qulity,Cost,Supplier,Certification,Market,Tips,FAQ
Aluminium extrusion is a manufacturing process used to create complex shapes and profiles with aluminium. This guide provides an overview of the process, including its quality, cost, suppliers, certifications, market trends, tips, and frequently asked questions.
Quality is a critical aspect of aluminium extrusion. The process allows for precision and consistency in creating intricate designs and meeting specific tolerances. High-quality extrusions offer excellent surface finish, dimensional accuracy, and mechanical properties, which are essential for various industries such as automotive, construction, and aerospace.
Cost considerations include factors like design complexity, size, volume, and material choice. Extrusion is often a cost-effective manufacturing method due to reduced material waste, low tooling costs, and efficient production. However, intricate designs or small-scale projects may incur higher costs.
When sourcing aluminium extrusions, it is crucial to choose reliable suppliers with a proven track record. Look for companies with extensive experience in extrusion, knowledgeable engineering teams, and a commitment to quality control. Customer reviews and references can also help evaluate potential suppliers.
Certifications to look for include ISO 9001 (quality management system) and ISO 14001 (environmental management system). These certifications ensure that the supplier follows internationally recognized standards for quality, environmental sustainability, and continuous improvement.
The aluminium extrusion market is witnessing steady growth globally, driven by the increasing demand for lightweight, durable, and corrosion-resistant materials. Industries like construction, automotive, electronics, and renewable energy are major consumers of aluminium extrusions, offering vast market opportunities for suppliers.
Tips for successful aluminium extrusion projects include optimizing designs for extrusion, considering material characteristics, tolerances, and processing limitations. Collaborating closely with the supplier’s engineering team can help streamline the design and production process, ensuring desired outcomes.
Frequently asked questions about aluminium extrusion involve topics such as extrusion capabilities, material options, surface finishes, secondary operations, and delivery times. These FAQs provide insight into the process, helping customers make informed decisions regarding their specific project requirements.
In conclusion, aluminium extrusion is a versatile manufacturing process, offering high-quality, cost-effective solutions for various industries. Choosing reputable suppliers with necessary certifications is vital, considering market trends and employing best practices can lead to successful extrusion projects.
Types of aluminium extrusion process
Aluminium extrusion is a process used to create complex shapes and profiles by forcing heated aluminium through a shaped opening or die. This process is widely used in industries such as construction, automotive, aerospace, and electronics due to the versatility, lightweight, and corrosion resistance of aluminum.
There are several types of aluminium extrusion processes, including:
1. Direct extrusion: This is the most common extrusion process where a heated aluminum billet or log is forced through a die by a ram or hydraulic press. The billet is pushed through the opening in the die, and the desired shape is formed as the aluminum passes through. This process is suitable for simple profiles with a continuous cross-section.
2. Indirect extrusion: In this method, the billet is held stationary, while the die moves towards it, pushing the aluminum through the opening. This process allows for more intricate and complex shapes to be formed, as the die can move in multiple directions.
3. Impact extrusion: Unlike direct or indirect extrusion, impact extrusion involves striking a punch into a heated aluminum billet to force the metal to flow into a die. This process is ideal for creating hollow tubular shapes with thin walls, such as containers or aerosol cans.
4. Hydrostatic extrusion: This technique involves using fluid pressure, typically water or oil, to force the aluminum through the die. Hydrostatic extrusion allows for greater control over the extrusion speed and can produce seamless and uniform profiles.
5. Cold extrusion: In contrast to the aforementioned processes that involve heating the aluminum billet, cold extrusion is performed at or near room temperature. This method is used for producing high-strength components as it preserves the material’s mechanical properties.
Each of these aluminium extrusion processes has its own advantages and limitations and is selected based on the specific requirements of the desired profile. Furthermore, after extrusion, the profiles can undergo further processes such as cutting, machining, bending, and surface finishing to achieve the final desired shape and appearance.
In conclusion, aluminium extrusion is a versatile manufacturing process that allows for the creation of complex and lightweight profiles. The various types of extrusion processes provide different advantages and flexibility, enabling the production of a wide range of aluminium products used in numerous industries.
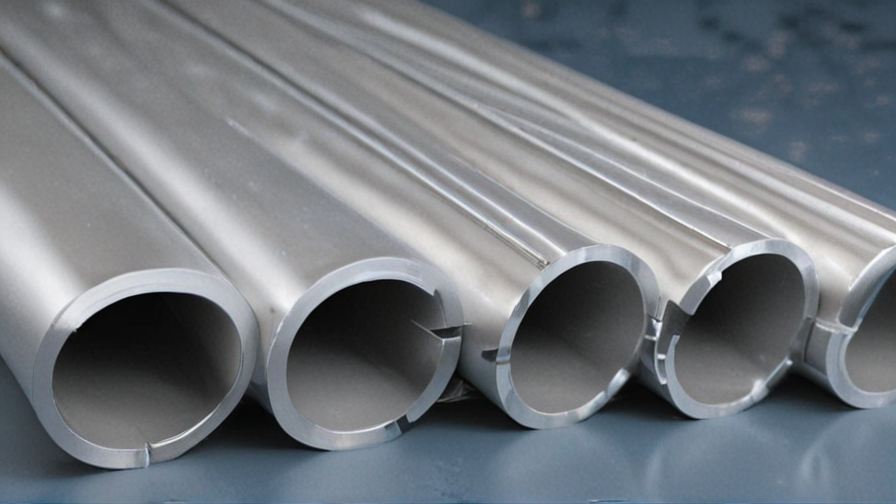
Pros and Cons of Using aluminium extrusion process
Aluminum extrusion is a popular manufacturing process used to create objects with a uniform cross-sectional profile. By forcing heated aluminum through a die to create the desired shape, aluminum extrusion offers several advantages and disadvantages.
Pros:
1. Versatility: Aluminum extrusion allows for the creation of complex cross-sectional shapes. With a wide range of dies available, manufacturers can easily produce customized profiles to meet specific design requirements.
2. Lightweight: Aluminum is known for its lightweight properties, making it an ideal material for applications that require weight reduction, such as the automotive and aerospace industries. The extrusion process further enhances its lightweight nature by removing excess material.
3. Strength: Despite its lightweight nature, aluminum extrusions offer high strength-to-weight ratio compared to other materials. This makes them suitable for applications that require structural integrity and durability.
4. Cost-effective: Aluminum extrusion provides cost advantages compared to other manufacturing processes such as casting or machining. The process is highly efficient, minimizing waste and reducing material and labor costs.
5. Thermal conductivity: Aluminum has excellent thermal conductivity, which is advantageous in applications that require heat dissipation, such as in electronic devices. Extruded aluminum profiles can be further treated to enhance thermal conductivity for specific requirements.
Cons:
1. Limited material options: While aluminum extrusion offers various alloys, the selection is still limited compared to other processes like casting. This limitation can impact applications that require specific material properties not available in aluminum.
2. High tooling costs: The initial tooling costs for aluminum extrusion can be relatively high, especially for complex profiles. These costs may hinder smaller manufacturers with limited budgets from utilizing the extrusion process.
3. Surface finish limitations: Aluminum extrusions typically have a textured or matte surface finish. Achieving a polished or smooth surface can be challenging, requiring additional treatments such as anodizing or powder coating.
4. Limited size constraints: The extrusion process is most suitable for producing profiles with relatively constant cross-sections. Creating extremely large or thick parts can be challenging and may require alternative manufacturing processes.
5. Design limitations: The extrusion process imposes certain design limitations, such as maintaining uniform wall thicknesses and avoiding sharp inside corners. Designers must consider these constraints to ensure successful extrusion production.
In conclusion, aluminum extrusion offers several significant advantages, including versatility, lightweight properties, and cost-effectiveness. While it may have limitations such as limited material options and high tooling costs, these drawbacks can often be outweighed by the benefits, making aluminum extrusion a viable solution for many industries and applications.
aluminium extrusion process Reference Specifications (varies for different product)
The aluminium extrusion process is a widely used manufacturing method that involves shaping aluminium alloy into various profiles with a constant cross-sectional shape. This process allows for the production of complex shapes, making it highly versatile in many industries.
The first step in the extrusion process is the preparation of the aluminium billet. The billet, typically made from recycled aluminium, is heated to a specific temperature to soften it for extrusion. This temperature varies depending on the aluminium alloy being used and the desired extrusion properties.
Once the billet reaches the required temperature, it is loaded into a chamber of an extrusion press. The billet is then pushed through a die, which determines the shape and size of the extruded profile. The die is a solid steel shape with a hole in the center that matches the desired profile.
As the billet is pushed through the die, it is subjected to immense pressure, ranging from 10,000 to 45,000 pounds per square inch. This pressure forces the softened aluminium to flow through the die, taking on the shape of the profile. The extruded aluminium emerges on the other side of the die as a continuous length of the desired profile.
After extrusion, the aluminium profile undergoes various cooling and straightening processes to ensure dimensional accuracy and stability. It is then cut into the desired lengths and may be further processed, such as machining or surface finishing, depending on the product requirements.
Aluminium extrusion offers numerous advantages. It allows for the creation of lightweight yet strong profiles with excellent corrosion resistance. The process also promotes material efficiency as it utilizes recycled aluminium. Additionally, extruded aluminium profiles can be easily joined, allowing for flexible assembly options.
The specifications for aluminium extrusion vary depending on the product requirements. Factors such as profile shape, alloy composition, surface finish, and dimensional tolerances are carefully defined to meet the intended applications. Specifications may include precise dimensions, mechanical properties, chemical composition, and surface quality, among others.
In conclusion, the aluminium extrusion process is a highly versatile method used to produce complex profiles with a constant cross-sectional shape. By carefully defining the specifications for each product, manufacturers can ensure that extruded aluminium profiles meet the desired requirements for a wide range of applications.
Applications of aluminium extrusion process
The aluminium extrusion process is widely used in various industries due to its versatility and cost-effectiveness. Here are some applications of this process:
1. Construction: Aluminium extrusions are extensively used in the construction industry for the fabrication of structures like doors, windows, curtain walls, and partitions. The lightweight nature of aluminium, combined with its strength and durability, makes it an ideal choice for these applications. Extrusions can be custom-designed to meet specific architectural requirements, resulting in aesthetically pleasing and functional structures.
2. Automotive: The automotive industry utilizes aluminium extrusions for the manufacturing of components like heat sinks, radiator supports, body sections, and structural parts. Aluminium’s low weight helps to improve fuel efficiency, while its corrosion resistance ensures durability in harsh environments. Extrusions also allow for complex shapes, reducing the need for multiple components and simplifying assembly processes.
3. Aerospace: Aluminium extrusions find extensive use in the aerospace industry due to their high strength-to-weight ratio and ability to withstand extreme operating conditions. Extruded aluminum profiles are used for the construction of aircraft frames, wings, fuselages, and other structural components. The use of extrusions helps reduce the weight of the aircraft, leading to fuel efficiency and increased payload capacity.
4. Electronics: The electrical and electronics industry employs aluminium extrusions for the fabrication of heat sinks. These heat sinks dissipate heat generated by electronic components, ensuring their optimal performance and prolonging their lifespan. Aluminium’s excellent thermal conductivity, combined with the flexibility of extrusion design, allows for efficient heat dissipation in electronic devices.
5. Furniture: Aluminium extrusions are widely used in the manufacturing of furniture due to their lightweight nature, strength, and corrosion resistance. They are used for the construction of frames, legs, handles, and decorative elements in chairs, tables, cabinets, and office systems. Extrusions offer design flexibility, allowing for the creation of sleek and modern furniture designs.
6. Renewable Energy: The renewable energy sector extensively utilizes aluminium extrusions for solar panel frames and mounting systems. Extrusions provide the required strength and durability to support solar panels while being lightweight to facilitate easy installation. They also offer the advantage of being easily recyclable, aligning with the sustainability goals of the renewable energy industry.
Overall, aluminium extrusion process finds applications in a wide range of industries due to its versatility, lightweight nature, strength, and cost-effectiveness. Its ability to create custom-designed profiles allows for the production of components with complex shapes, further enhancing its usability in various applications.
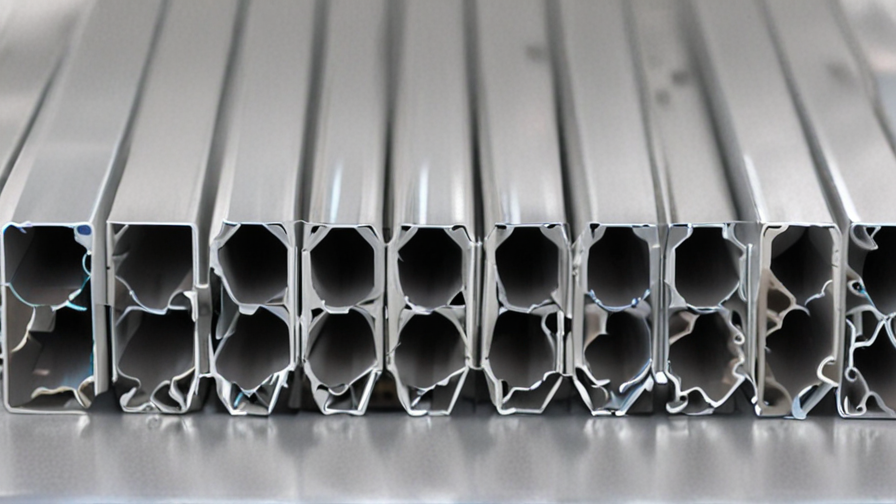
The Work Process and how to use aluminium extrusion process
The work process of aluminum extrusion involves shaping and forming aluminum profiles with various cross-sectional shapes by pushing the material through a die under high pressure. It is a widely used method for manufacturing complex and customized aluminum components and structures.
The first step in the aluminum extrusion process is the preparation of the aluminum billet, which is a cylindrical log of aluminum alloy. The billet is heated to a specific temperature to make it more malleable for extrusion. It is then loaded into the extrusion press.
The extrusion press consists of a container called a cylinder and a piston that fits tightly inside. The billet is placed inside the cylinder, and pressure is applied through the piston to push the aluminum through the die. The die is a specially designed opening that gives the aluminum its desired cross-sectional shape.
As the billet is pushed through the die, it undergoes plastic deformation, taking the shape of the die. This process utilizes tremendous force to shape the aluminum into complex profiles with tight tolerances. Cooling systems are in place to control the temperature of the extruded profile and ensure dimensional stability.
Once the aluminum profile is extruded, it is cut to the desired length and cooled further. Depending on the application, additional steps such as surface treatments, machining, or joining processes may be required.
Aluminum extrusions find applications in various industries, including automotive, construction, aerospace, electronics, and many more. The versatility of the extrusion process allows for the creation of customized profiles with specific functionalities to meet the requirements of different applications.
To use the aluminum extrusion process effectively, manufacturers need to consider several factors. These include the design of the die and the subsequent processing steps required to achieve the desired profile. Proper billet preparation, including heating to the right temperature, is crucial for ensuring optimal extrusion quality.
Additionally, maintaining appropriate extrusion press parameters such as pressure, speed, and temperature is essential for achieving consistent and high-quality results. Quality control measures, such as inspecting the extruded profiles for defects and conducting dimensional checks, should also be implemented to ensure the final product meets the required specifications.
In conclusion, the aluminum extrusion process is a versatile and efficient method for shaping and forming aluminum profiles. By understanding the work process and implementing good manufacturing practices, manufacturers can effectively utilize aluminum extrusion to create customized and high-quality aluminum components.
Quality Testing Methods for aluminium extrusion process and how to control the quality
The aluminium extrusion process involves the shaping of aluminium billets or logs into various profiles through a series of steps. To ensure the quality of the extruded aluminium products, several testing methods can be employed:
1. Dimensional Inspection: This includes measuring the dimensions and geometric tolerances of the extruded profile using specialized instruments such as calipers, micrometers, and coordinate measuring machines. It helps in verifying the exactness of the final product as per the desired specifications.
2. Surface Inspection: This involves visually examining the surface finish of the extruded profiles for any defects like scratches, dents, or cracks. It can be done using visual inspection or automated systems with cameras and image processing techniques.
3. Mechanical Testing: Mechanical properties like tensile strength, yield strength, elongation, and hardness determine the strength and reliability of the extruded aluminium. Universal testing machines can be used to conduct these tests as per relevant standards.
4. Chemical Composition Analysis: Checking the chemical composition of the aluminium alloy used is crucial to ensure that it meets the required standards. Techniques like Optical Emission Spectrometry and Inductively Coupled Plasma Analysis are commonly employed for this purpose.
5. Metallurgical Inspection: Microstructural examination using metallographic techniques can reveal the internal structure of the extruded profiles, including grain size, defects, and homogeneity. This inspection helps in assessing the material’s durability and performance.
To control the quality of the aluminium extrusion process, the following steps can be taken:
1. Process Control: Regular monitoring and control of process parameters like temperature, extrusion speed, die design, and lubrication can minimize variations and enhance product consistency.
2. Raw Material Inspection: Regularly inspecting incoming aluminium billets or logs for defects, impurities, and alloy composition ensures the suitability of the raw material for extrusion.
3. Training and Standard Operating Procedures: Proper training and adherence to standardized operating procedures by the workforce reduce human errors and ensure consistent quality.
4. Statistical Process Control: Data-driven techniques like control charts can be applied to monitor key quality parameters and identify any deviations or trends that may affect product quality.
5. Continuous Improvement: Implementing a robust quality management system, performing periodic audits, and addressing customer feedback help in identifying areas for improvement and ensuring overall quality control.
By implementing these quality testing methods and control measures, manufacturers can ensure that their aluminium extrusion process consistently produces high-quality profiles that meet customer requirements and industry standards.
aluminium extrusion process Sample Policy and Post-Purchase Considerations for aluminium extrusion process from China
Sample Policy:
When purchasing aluminium extrusion process from China, it is important to have a clear understanding of the supplier’s policies to ensure a smooth transaction. Here is a sample policy to consider:
1. Product Quality: The supplier must provide high-quality aluminium extrusion products that meet international standards. They should be willing to provide test reports and certifications to validate the quality of their products.
2. Customization: The supplier should offer customization options to meet specific requirements. This includes the ability to provide different shapes, sizes, and finishes of aluminium extrusion profiles.
3. MOQ (Minimum Order Quantity): The supplier should clearly state their MOQ for aluminium extrusion products. It is important to make sure that the required quantity can be met before proceeding with the purchase.
4. Pricing: The supplier should provide competitive pricing for their aluminium extrusion process. This includes transparent pricing with no hidden charges or additional fees.
5. Lead Time: It is crucial to understand the supplier’s lead time for manufacturing and delivering the aluminium extrusion products. This will help in planning production schedules and meeting customer demands.
6. Packaging and Shipping: The supplier should have a proper packaging mechanism to ensure the safe transportation of aluminium extrusion products. They should also offer reliable shipping options and handle all necessary documentation.
Post-Purchase Considerations:
After purchasing aluminium extrusion process from China, the following considerations should be taken into account:
1. Quality Check: Upon receiving the aluminium extrusion products, it is vital to conduct a thorough quality check. This includes inspecting the dimensions, finishes, and overall appearance to ensure that the products meet the required specifications.
2. Communication: Maintaining clear and continuous communication with the supplier is essential. Any issues or concerns should be addressed promptly to resolve them efficiently.
3. Feedback: Providing feedback to the supplier regarding the quality, packaging, and overall service can be valuable. This helps them understand areas of improvement and ensures a better experience for future transactions.
4. Long-term Relationship: If satisfied with the supplier’s products and service, establishing a long-term relationship can be beneficial. This can lead to better pricing, customized solutions, and a smoother procurement process in the future.
By considering these sample policies and post-purchase considerations, one can streamline the procurement of aluminium extrusion process from China and ensure a successful business partnership.
Sourcing aluminium extrusion process from China: Opportunities, Risks, and Key Players
China is a leading global player in the aluminium extrusion industry, offering numerous opportunities for companies looking to source this process. The country’s advanced manufacturing capabilities, large production capacity, and cost-effective solutions make it an attractive option for businesses worldwide. However, there are also risks associated with sourcing aluminium extrusions from China, such as quality control issues and intellectual property concerns.
Opportunities:
1. Cost-Effectiveness: Chinese manufacturers often offer competitive pricing due to lower labor and production costs, enabling businesses to reduce their overall costs and increase profit margins.
2. Wide Range of Products: China’s extensive production capacity allows businesses to choose from a wide range of aluminium extrusion profiles, shapes, and sizes to meet their specific requirements.
3. Advanced Technology: Chinese manufacturers have made significant investments in advanced extrusion technology, ensuring high-quality products with precise dimensions and superior finishes.
4. Supply Chain Efficiency: China’s well-established supply chain networks ensure timely production and delivery, allowing businesses to streamline their operations.
Risks:
1. Quality Control: Selecting reliable suppliers is crucial as some manufacturers may compromise on quality to offer lower prices. Lack of supervision and quality control measures can lead to inferior products.
2. Intellectual Property Concerns: Intellectual property theft is a persistent issue in China. Companies must take necessary precautions to protect their designs, processes, and proprietary information.
3. Language and Communication Barriers: Cultural and language differences can hinder effective communication and lead to misunderstandings or delays in production.
4. Regulatory Compliance: Businesses must ensure that their Chinese suppliers adhere to relevant international standards and comply with environmental regulations to avoid legal complications.
Key Players:
1. China Zhongwang Holdings Limited: Zhongwang is one of the largest aluminium extrusion companies in China, providing comprehensive extrusion solutions for various industries.
2. Xingfa Aluminium Holdings Limited: Xingfa specializes in the production and distribution of high-quality aluminium extrusions, offering a wide range of profiles and surface finishes.
3. Asia Aluminium Holdings Limited: Asia Aluminium is a well-known manufacturer of aluminium extrusion products, renowned for its advanced production facilities and strict quality control.
In conclusion, sourcing aluminium extrusion processes from China can offer significant opportunities for businesses due to cost-competitiveness, advanced technology, and ample product options. However, potential risks such as quality control issues, intellectual property concerns, and language barriers need to be carefully considered and mitigated. It is crucial to work with reputable manufacturers and establish robust quality control procedures to ensure that the sourcing process is successful.
How to find and select reliable aluminium extrusion process manufacturers in China,use google search manufacturers and suppliers
When searching for reliable aluminium extrusion process manufacturers in China, utilizing Google search manufacturers and suppliers can be a helpful starting point. However, it is important to use certain strategies to ensure you select the most reliable and suitable manufacturers. Here are some steps you can follow:
1. Keyword search: Begin by inputting relevant keywords in the Google search bar, such as “aluminium extrusion process manufacturers in China” or “reliable aluminium extrusion suppliers.” This will yield a list of potential manufacturers and suppliers.
2. Website assessment: Visit the websites of the manufacturers and suppliers that appear in your search results. Look for information regarding their experience in the industry, their product range, certifications, and any accolades or recognition they have received. A well-designed and comprehensive website can indicate professionalism and reliability.
3. Customer reviews and testimonials: Look for customer reviews and testimonials on the manufacturer’s website or through external review sources. These can provide insights about the company’s reputation, quality of products, and customer service. It is important to consider both positive and negative feedback to get a balanced view.
4. Contact information and communication: Ensure that the manufacturer provides clear and valid contact information on their website. Reach out to them using the provided information and observe their responsiveness and willingness to address your inquiries promptly. This will give you an idea of their customer service and communication standards.
5. Background research: Conduct additional research on the shortlisted manufacturers to gather more information about their reputation, production capabilities, and track record. Online forums, industry websites, and trade platforms can be valuable resources for gathering this information.
6. Request samples and quotations: Once you have narrowed down your options, request samples and quotations from the selected manufacturers. This will allow you to assess the quality of their products and compare pricing. Evaluate the samples for conformance to your requirements and consider whether the pricing is reasonable given the quality offered.
By following these steps, you can find and select reliable aluminium extrusion process manufacturers in China. It is essential to conduct thorough research and consider multiple factors to ensure you choose a manufacturer that meets your specific needs and requirements.
How to check aluminium extrusion process manufacturers website reliable,use google chrome SEOquake check if ranking in top 10M
To check the reliability of an aluminum extrusion process manufacturer’s website, you can follow these steps using Google Chrome and SEOquake:
1. Install SEOquake: Go to the Chrome Web Store and search for “SEOquake.” Click on the “Add to Chrome” button to install the SEOquake extension.
2. Open the manufacturer’s website: Type the web address of the aluminum extrusion process manufacturer’s website into the Google Chrome browser and press Enter.
3. Activate SEOquake: Look for the SEOquake icon on the top right corner of your browser’s toolbar. Click on the icon to activate SEOquake for the website you are viewing.
4. Check website ranking: Once SEOquake is activated, a toolbar will appear below the manufacturer’s website. Look for the “Google index” section and find the value “Rank.” If the rank is within the top 10 million, it indicates that the website receives a decent amount of traffic and is relatively reliable.
5. Evaluate website content: Explore the manufacturer’s website and assess the content provided. Look for comprehensive information about their aluminum extrusion process, such as the manufacturing techniques, certifications, quality control measures, and previous projects. Authentic and detailed content is typically a sign of a reliable manufacturer.
6. Look for customer testimonials: Check if the manufacturer’s website includes customer testimonials or reviews. Positive testimonials demonstrate the manufacturer’s credibility and customer satisfaction.
7. Verify contact information: Ensure that the website provides proper contact information, such as a physical address, phone number, and email address. Reliable manufacturers will usually have multiple channels for communication.
8. Assess website design: A well-designed and professional-looking website indicates that the manufacturer invests in their online presence. A poorly designed or outdated website might raise concerns about their reliability.
Remember to critically evaluate all the information gathered from the manufacturer’s website and consider conducting further research or reaching out to them directly for more details or clarifications.
Top 10 aluminium extrusion process manufacturers in China with each 160 words introduce products,then use markdown create table compare
1. Xingfa Aluminium Holdings Limited: Xingfa Aluminium is one of China’s leading providers of aluminium extrusion solutions. They specialize in manufacturing high-quality aluminium profiles used in various industries such as construction, transportation, and electronics. The company’s products are known for their durability, precision, and versatility.
2. China Zhongwang Holdings Limited: Zhongwang is a prominent manufacturer of aluminium extrusion products in China. They offer a wide range of standard and custom-designed aluminium profiles suitable for architectural, industrial, and aerospace applications. The company focuses on innovation and quality control, ensuring their products meet the highest industry standards.
3. Constellium (Suzhou) Co., Ltd.: Constellium is a global leader in manufacturing advanced aluminium extrusions. Their Suzhou-based facility in China specializes in producing lightweight and high-strength aluminium extruded products for automotive, aerospace, and packaging industries. They are known for their technical expertise and customer-oriented approach.
4. Kaidi Aluminum Industry Co., Ltd.: Kaidi Aluminum is a professional manufacturer of aluminium extrusion profiles in China. They offer a wide range of extruded aluminium profiles suitable for different purposes, including architectural, industrial, and decorative applications. The company emphasizes on product quality, design flexibility, and efficient production processes.
5. Xinxiang Aluminum Co., Ltd.: Xinxiang Aluminum is a trusted manufacturer of aluminium extrusion products in China. They provide high-quality and reliable aluminium profiles used in various industries like construction, transportation, and machinery. Their products are known for their superior strength, resistance to corrosion, and excellent surface finish.
6. Rongde Aluminum Group: Rongde Aluminum Group is a well-established aluminium extrusion manufacturer in China. They offer a diverse range of extruded aluminium profiles suitable for applications in construction, electronics, furniture, and more. The company focuses on product customization, quality control, and timely delivery.
7. China Power Investment Corporation (CPI): CPI is a leading aluminium extrusion process manufacturer in China. They provide top-quality aluminium profiles used in industries such as construction, automotive, and renewable energy. The company’s products are known for their precision, durability, and cost-effectiveness.
8. Guangdong Huachang Aluminum Factory Co., Ltd.: Huachang Aluminum Factory is a reputable manufacturer of aluminium extrusion profiles in China. They offer a wide range of aluminium profiles suitable for construction, industrial, and transportation applications. The company focuses on continuous innovation, product quality, and excellent customer service.
9. Wellste Aluminum Co., Ltd.: Wellste Aluminum is a professional aluminium extrusion manufacturer based in China. They specialize in producing custom-designed aluminium profiles for various applications, including construction, transportation, and electronics. The company emphasizes on precision machining, quality control, and competitive pricing.
10. Zhongfu Industrial Co., Ltd.: Zhongfu Industrial is a leading manufacturer of aluminium extrusion products in China. They offer a wide range of standard and custom aluminium profiles suitable for architectural, industrial, and transportation sectors. The company focuses on technological advancement, environmentally friendly practices, and customer satisfaction.
| Manufacturer | Product Range | Customization Capability | Quality Control |
|—————————————|————————————————————————————————|—————————————|————————————————————————————————————|
| Xingfa Aluminium Holdings Limited | Aluminium profiles for construction, transportation, electronics | Yes | Stringent quality control measures ensure durability and precision of profiles. |
| China Zhongwang Holdings Limited | Aluminium profiles for architectural, industrial, aerospace applications | Yes, with innovative designs | High-quality extrusions adhere to global industry standards. |
| Constellium (Suzhou) Co., Ltd. | Lightweight and high-strength aluminium extrusions for automotive, aerospace, packaging sectors | Yes, specialized applications | Advanced technical expertise guarantees top-notch product quality. |
| Kaidi Aluminum Industry Co., Ltd. | Aluminium profiles for architectural, industrial, decorative applications | Yes, with design flexibility | Efficient production processes result in reliable and cost-effective products. |
| Xinxiang Aluminum Co., Ltd. | Aluminium profiles for construction, transportation, machinery | Yes | Superior strength and corrosion resistance make their products highly reliable. |
| Rongde Aluminum Group | Aluminium profiles for construction, electronics, furniture | Yes | Custom profiles undergo thorough quality checks for optimum performance. |
| China Power Investment Corporation | Aluminium profiles for construction, automotive, renewable energy applications | Yes, for specific requirements | Precision manufacturing ensures high-quality products that meet industry standards. |
| Guangdong Huachang Aluminum Factory | Aluminium profiles for construction, industrial, transportation | Yes | Continuous innovation leads to product advancements suiting various applications. |
| Wellste Aluminum Co., Ltd. | Custom-designed aluminium profiles for construction, transportation, electronics | Yes, with machining capabilities | Rigorous quality control ensures the delivery of superior profiles at competitive prices. |
| Zhongfu Industrial Co., Ltd. | Aluminium profiles for architectural, industrial, transportation sectors | Yes, for specific needs or projects | Technological advancement enables the production of environmentally friendly profiles with precision. |
In conclusion, China offers a wide range of aluminium extrusion process manufacturers, each providing unique products and customization capabilities. These manufacturers maintain strict quality control measures to ensure the durability, precision, and compliance of their aluminium profiles. Whether for architectural, industrial, or transportation applications, customers can find reliable and innovative solutions from these top Chinese manufacturers.
Background Research for aluminium extrusion process manufacturers Companies in China, use qcc.com archive.org importyeti.com
When it comes to aluminium extrusion process manufacturers in China, there are various companies that can be found through platforms such as qcc.com, archive.org, and importyeti.com. These platforms provide information about different businesses operating in the Chinese market.
Qcc.com is a Chinese website that offers comprehensive data on companies in China. It provides details about a company’s registration information, financial status, social contributions, and legal history. By using qcc.com, one can easily find a list of aluminium extrusion process manufacturers in China, along with their contact details and other relevant information.
Archive.org, on the other hand, is an internet archive that allows users to access past versions of websites, documents, and other media. It can be used to track the history and evolution of aluminium extrusion process manufacturers’ websites in China. It can be helpful in gauging a company’s growth and development over time, as well as understanding their product offerings and manufacturing capabilities.
Importyeti.com is a platform that provides import and export data for shipments to and from China. It can be used to search for aluminium extrusion process manufacturers in China and gain insights into their import and export activities. This information can be valuable for understanding a company’s global reach and market competitiveness.
In conclusion, by utilizing qcc.com, archive.org, and importyeti.com, one can conduct background research on aluminium extrusion process manufacturers in China. These platforms offer comprehensive data on companies’ registration information, financial status, historical website data, and import/export activities. This information enables potential buyers or partners to make informed decisions when considering aluminium extrusion manufacturers in China.
Leveraging Trade Shows and Expos for aluminium extrusion process Sourcing in China
Trade shows and expos are excellent platforms for sourcing aluminium extrusion processes in China. These events provide an opportunity to connect with numerous suppliers, manufacturers, and industry experts under one roof, making it easier to find reliable and cost-effective sourcing options.
Attending trade shows allows for direct interaction with suppliers, fostering personal relationships and building trust. It also provides a chance to see and evaluate the quality of products firsthand, ensuring they meet the required standards for aluminium extrusion processes.
Furthermore, trade shows provide a platform for exploring new technologies and innovations in the aluminium extrusion industry. This can lead to discovering more efficient and sustainable processes, allowing businesses to stay competitive and meet evolving market demands.
Expos also offer an opportunity to network with industry professionals and engage in knowledge-sharing sessions. This can result in gaining valuable insights into the latest market trends, regulations, and best practices. Being aware of such information enables businesses to make informed decisions and select the most suitable suppliers for their aluminium extrusion process sourcing needs.
To maximize the benefits from attending trade shows and expos, it is essential to thoroughly research and plan in advance. Identifying the specific exhibitors that specialize in aluminium extrusion processes will help streamline the sourcing process and minimize time wasted on irrelevant suppliers. It is also crucial to prepare a list of requirements and questions in advance to ensure productive discussions with potential suppliers.
In conclusion, trade shows and expos provide a valuable opportunity for businesses to source aluminium extrusion processes in China. By directly interacting with suppliers, exploring new technologies, and networking with industry professionals, companies can find reliable and cost-effective sourcing options that meet their specific requirements.
The Role of Agents and Sourcing Companies in Facilitating aluminium extrusion process Purchases from China
Agents and sourcing companies play a crucial role in facilitating aluminium extrusion process purchases from China. These intermediaries act as a bridge between buyers and Chinese manufacturers, thereby simplifying the purchasing process and ensuring a smooth transaction.
One of the primary functions of agents and sourcing companies is to identify reliable and reputable aluminium extrusion process manufacturers in China. They have extensive knowledge of the market and can leverage their network to find manufacturers that meet the specific requirements of the buyers. This eliminates the need for buyers to spend significant time and resources in research and supplier identification.
Agents and sourcing companies also assist in negotiating favorable terms and conditions with the Chinese manufacturers. They have experience in dealing with local suppliers and are well-versed in Chinese business practices and customs. This helps in ensuring that buyers get the best prices, payment terms, and delivery schedules for their aluminium extrusion process purchases.
Furthermore, agents and sourcing companies provide quality control services to ensure that the purchased products meet the required standards. They conduct factory audits, perform inspections before shipment, and take corrective actions if any non-compliance is identified. This helps buyers mitigate the risk of receiving substandard or defective aluminium extrusion products.
Additionally, agents and sourcing companies handle all the documentation and logistics involved in the purchasing process. They coordinate with the manufacturers for product samples, prepare and review contracts, arrange for shipping, and handle customs clearance. This streamlines the entire procurement process and saves buyers from the complexities and hassles of international trade.
Overall, agents and sourcing companies act as trusted partners for buyers who want to purchase aluminium extrusion process products from China. Their expertise, knowledge, and local presence enable buyers to find reliable manufacturers, negotiate favorable terms, ensure quality control, and streamline the entire purchasing process.
Price Cost Research for aluminium extrusion process manufacturers Companies in China, use temu.com and 1688.com
When it comes to researching the price cost for aluminium extrusion process manufacturers in China, two popular platforms that can be utilized are temu.com and 1688.com. These websites provide a wealth of information on suppliers, prices, and specifications, making it easier to obtain accurate data.
Firstly, temu.com is a comprehensive platform that offers a vast range of suppliers and manufacturers in China. It allows users to search for specific products, such as aluminium extrusion, and filter the search results based on various criteria such as price, location, and certifications. This makes it easier to narrow down options and find manufacturers that align with specific requirements and budget.
Secondly, 1688.com, an Alibaba-owned platform, is widely used within China for conducting business-to-business transactions. This platform enables users to access a wide range of suppliers and get direct quotes from them. Additionally, it provides valuable information on product specifications, minimum order quantities, and quality certifications. Users can also compare prices from different suppliers, facilitating the identification of cost-effective options.
To effectively conduct price cost research using these platforms, it is important to follow a few key steps. Firstly, accurately define the specific requirements and specifications for the aluminium extrusion process. This will ensure that the search results on these platforms are relevant. Secondly, carefully analyze the product offerings, pricing, and quality certifications provided by different suppliers. It is crucial to consider factors such as manufacturing capabilities, delivery options, and payment terms.
Additionally, users should reach out to suppliers directly to request quotations and negotiate pricing, especially when dealing with large orders. This will help in getting a comprehensive understanding of the cost structure and pricing variations between different manufacturers. By using these platforms in combination with effective communication, it is possible to gather comprehensive price cost information for aluminium extrusion process manufacturers in China.
In conclusion, temu.com and 1688.com are valuable resources for researching pricing and costing information for aluminium extrusion process manufacturers in China. By utilizing these platforms, users can efficiently collect data, assess supplier options, and find cost-effective solutions for their requirements.
Shipping Cost for aluminium extrusion process import from China
The shipping cost for importing aluminium extrusion process from China can vary depending on multiple factors. Firstly, the distance and weight of the shipment play a significant role in determining the cost. Shipping by sea is the most common method for such heavy goods, and the charges are usually calculated based on the volume or weight of the consignment. However, it is important to note that there might be additional costs associated with shipping, such as port fees, customs duties, and handling charges.
Another crucial factor that influences shipping costs is the shipping method chosen. There are typically two options: FCL (Full Container Load) and LCL (Less than Container Load). If the quantity of goods is substantial, opting for FCL can be more cost-effective, as it involves the exclusive use of a container. On the other hand, LCL shipping is suitable for smaller quantities, but the charges may be higher due to consolidation and deconsolidation.
Additionally, the shipping company chosen also impacts the cost. Different carriers have varying pricing structures, transit times, and quality of services. It is important to research and compare quotes from multiple freight forwarders or shipping lines to get the best deal.
Lastly, it is advisable to consider any potential ancillary costs associated with the shipping process, such as insurance, customs brokerage, inland transportation, and any additional requirements or documentation needed for the importation.
To summarize, when importing aluminium extrusion process from China, the shipping cost varies based on factors such as distance, weight, shipping method (FCL or LCL), chosen carrier, and additional costs like insurance and customs fees. It is essential to conduct thorough research and compare different options to ensure cost-effectiveness and a smooth import process.
Compare China and Other aluminium extrusion process Markets: Products Quality and Price,Visible and Hidden Costs
China and other aluminium extrusion process markets can be compared in terms of product quality, price, and the visible and hidden costs involved.
Product quality is a crucial factor when considering aluminium extrusion processes. Chinese manufacturers have significantly improved their product quality over the years and are now producing extrusions that meet international standards. However, other markets such as Europe, North America, and Japan are still considered to have higher quality standards in terms of dimensional accuracy, surface finish, and tight tolerances. These markets often use more advanced technologies and have stricter quality control measures in place.
Price is another important aspect to consider when comparing the aluminium extrusion process markets. China has been known for its competitive pricing, offering lower prices compared to other markets. This is mainly due to lower labor and production costs in China. On the other hand, markets such as Europe and North America might have higher prices due to higher labor costs, stricter environmental regulations, and higher quality standards. However, it is important to note that pricing may vary depending on the complexity of the extrusion design and the quantity ordered.
Visible costs, such as material costs, labor costs, and energy costs, can significantly impact the pricing of aluminium extrusions in different markets. China, with its lower labor and production costs, can offer lower visible costs compared to other markets. However, hidden costs such as transportation and logistics, import tariffs, and quality control inspections can also affect the overall cost. For example, if the aluminium extrusions need to be shipped from China to a distant market, transportation costs can increase the final price.
In conclusion, China and other aluminium extrusion process markets can vary in terms of product quality, price, and visible and hidden costs. While China has improved its product quality and offers competitive pricing due to lower labor and production costs, other markets such as Europe, North America, and Japan are still considered to have higher quality standards. Additionally, hidden costs such as transportation and import tariffs can impact the overall pricing in different markets. Ultimately, the decision on which market to choose for aluminium extrusion processes may depend on the specific requirements of the project and the balance between quality and price considerations.
Understanding Pricing and Payment Terms for aluminium extrusion process: A Comparative Guide to Get the Best Deal
When it comes to understanding pricing and payment terms for the aluminium extrusion process, it is important to have a comparative guide in order to secure the best deal possible. This guide aims to provide insights into the factors that influence pricing and payment terms, enabling buyers to make informed decisions.
The pricing of aluminium extrusion varies based on several key factors. Firstly, the complexity and size of the extruded profile play a significant role. More intricate designs and larger sizes often result in higher prices due to the increased level of expertise, time, and material required. Additionally, the chosen alloy and its availability can affect pricing, as some alloys may be more expensive or harder to source than others.
Quality requirements also impact pricing as higher tolerances and strict quality control measures can lead to higher costs. Surface treatments, finishes, and additional services like cutting, machining, or fabrication may also increase the overall price. Therefore, it is crucial to outline the desired specifications and qualities beforehand to avoid any misunderstanding or unexpected costs.
Payment terms in the aluminium extrusion industry can differ depending on various factors such as order volume, frequency, and buyer-seller relationship. Generally, initial payments or deposits are required to start the production process, with the remaining balance due upon completion or before shipping. Large-volume orders may allow for more flexible payment terms, such as installments or a letter of credit.
Negotiating payment terms can be beneficial for buyers, especially for long-term relationships or significant orders. Supplier financing or trade credit options may be available, allowing buyers to spread their payments over a set period of time. However, it is essential to ensure that such financing options do not result in significantly higher overall costs due to interest or fees.
To find the best deal, it is advisable to obtain quotes from multiple suppliers and compare their pricing and payment terms. However, it is important to consider not only the price, but also the supplier’s reputation, quality control measures, response time, and delivery capabilities. Engaging in detailed discussions with potential suppliers can help clarify any uncertainties regarding pricing or payment terms.
In conclusion, understanding pricing and payment terms for the aluminium extrusion process requires thorough analysis and comparison. Factors such as profile complexity, alloy selection, quality requirements, and additional services can influence pricing. Payment terms can be negotiated based on order volume and buyer-seller relationship, with options ranging from deposits to trade credit. Considering multiple suppliers and key criteria beyond price is crucial for securing the best deal possible.
Chinese Regulations and Industry Standards Certifications for aluminium extrusion process,Import Regulations and Customs for aluminium extrusion process from China
Chinese Regulations and Industry Standards Certifications for the aluminium extrusion process:
China has implemented various regulations and industry standards certifications to ensure the quality and safety of aluminium extrusion processes. These include:
1. National Standards: China has established national standards for aluminium extrusion processes, such as GB/T 5237, which specifies the technical requirements for aluminium alloy extrusions used in construction.
2. Quality Management Systems: Chinese aluminium extrusion manufacturers often adhere to the ISO 9001 quality management system, which ensures that the extrusion process meets international quality standards.
3. Environmental Standards: Chinese regulations, including the Law on the Prevention and Control of Atmospheric Pollution, impose environmental requirements on aluminium extrusion processes to reduce emissions and promote sustainable manufacturing.
4. Safety Considerations: Occupational safety regulations, such as the Law on Safety Production, aim to ensure the safety of workers involved in the aluminium extrusion process. This includes guidelines on equipment safety, worker protection, and emergency response.
Import Regulations and Customs for aluminium extrusion process from China:
When importing aluminium extrusion products from China, it is essential to comply with import regulations and customs requirements to avoid any legal complications. Key considerations include:
1. Customs Documentation: Proper documentation is crucial for importing aluminium extrusion products from China. This includes commercial invoices, packing lists, bill of lading/airway bills, and certificates of origin.
2. Import Duties and Taxes: Importing aluminium extrusion products may attract customs duties and taxes, depending on the country of importation. Importers should be aware of the applicable customs tariff codes and assess the costs involved accurately.
3. Product Compliance: Imported aluminium extrusion products must comply with the destination country’s standards and regulations. Compliance with local building codes, fire safety standards, and other relevant regulations should be ensured before importation.
4. Certification and Testing: Some countries may require specific certifications or testing to ensure the quality and safety of imported aluminium extrusion products. These certifications can include ISO certifications, product testing reports, or other relevant industry-specific certifications.
Complying with Chinese regulations and industry standards certifications, as well as adhering to import regulations and customs requirements, is crucial when engaging in aluminium extrusion process imports from China.
Sustainability and Environmental Considerations in aluminium extrusion process Manufacturing
The aluminium extrusion process is widely used in various industries for its versatility, strength, and lightweight properties. However, it is essential to consider sustainability and environmental factors during the manufacturing process to minimize its ecological impact.
Firstly, the production of aluminium involves extracting bauxite, which is a resource-intensive process. To ensure sustainability, manufacturers should strive to use recycled aluminium as much as possible. Recycling aluminium requires significantly less energy and resources compared to primary production, reducing carbon emissions and conserving natural resources.
Furthermore, energy consumption during the extrusion process should be optimized to reduce environmental impact. Adopting energy-efficient technologies and practices, such as using energy-efficient machinery and implementing process improvements, can minimize energy consumption. Additionally, utilizing renewable energy sources for powering the extrusion process can further enhance sustainability.
Water usage is another crucial consideration. While the extrusion process typically requires minimal water, manufacturers should still implement water-saving measures to conserve this valuable resource. This can include implementing closed-loop water systems, recycling and reusing process water, and reducing water wastage through efficient cooling systems.
Waste management is an integral part of sustainable manufacturing. Implementing waste reduction strategies, such as optimizing raw material usage and recycling scrap aluminium, can minimize waste generation. Additionally, manufacturers can promote the use of sustainable packaging materials and adopt responsible disposal practices to minimize the environmental impact of their operations.
To enhance sustainability in aluminium extrusion, manufacturers can also focus on improving their supply chain management. This includes working closely with suppliers to ensure they adhere to sustainable practices and sourcing raw materials from responsible and environmentally conscious suppliers.
In summary, sustainability and environmental considerations in aluminium extrusion process manufacturing play a critical role in reducing the ecological impact of this versatile manufacturing process. By utilizing recycled aluminium, optimizing energy consumption, conserving water, managing waste effectively, and promoting responsible sourcing, manufacturers can minimize their environmental footprint and contribute to a more sustainable future.
List The Evolution history of “aluminium extrusion process”
The history of the aluminum extrusion process dates back to the late 18th century when Sir Humphry Davy, an English chemist, first isolated the metal. However, it was not until the early 20th century that the extrusion process for aluminum began to develop.
The first commercial aluminum extrusion press was built in 1904 by Alexander Dick at a factory in Scotland. This press used hydraulic cylinders to push aluminum billets through a die to create various shapes. The process was initially used for creating simple profiles such as rods and bars.
In the 1920s, extrusion technology advanced further with the introduction of hot extrusion. This process involved heating the aluminum billets before extrusion, which increased the metal’s malleability and allowed for the production of more complex profiles. Hot extrusion also improved the surface finish of the extruded products.
The 1950s brought about significant improvements in extrusion techniques. The introduction of induction heating and improved hydraulic systems allowed for faster extrusion speeds and greater control over the process. This led to a wider range of complex shapes being produced, including those with hollow sections.
Further advancements in extrusion technology occurred in the second half of the 20th century. The development of computer-controlled systems, such as programmable logic controllers (PLCs), enabled precise control over temperature, speed, and pressure during extrusion. These advancements greatly enhanced the quality and consistency of extruded aluminum products.
In recent years, the focus has shifted towards energy efficiency and environmental sustainability. Aluminium extrusion manufacturers have adopted various strategies to reduce energy consumption and waste during the extrusion process. These include using recycled aluminum and optimizing extrusion dies.
Additionally, advancements in extrusion design software and simulation tools have allowed for better product development and optimization. The ability to quickly prototype and test different designs has resulted in more efficient and lighter extruded aluminum components, finding applications in industries such as automotive, aerospace, and construction.
In conclusion, the evolution of the aluminum extrusion process has been a continuous journey of technological advancements and improvements. From simple profiles to complex shapes, the process has evolved to offer greater control, precision, and sustainability. The future of aluminum extrusion holds promising possibilities as technology continues to propel the industry forward.
The Evolution and Market Trends in aluminium extrusion process Industry
The aluminium extrusion process industry has witnessed significant evolution and market trends over the years. This process involves the shaping of aluminium by forcing it through a die to create complex profiles for various industries such as construction, automotive, and aerospace.
One of the major trends in the aluminium extrusion process industry is the increasing demand for lightweight materials in various sectors. Aluminium extrusions are preferred due to their high strength-to-weight ratio, making them ideal for applications that require durability without adding excessive weight. This trend has been driven by the need for fuel-efficient vehicles, sustainable construction materials, and lightweight aircraft components.
Moreover, advancements in technology have played a crucial role in the evolution of the aluminium extrusion process. Computer-aided design (CAD) software has made it easier to create intricate and precise extrusion profiles. This has opened up opportunities for innovative designs and customized solutions, thereby expanding the market for aluminium extrusions.
Another notable trend is the growing popularity of sustainable and eco-friendly manufacturing processes. Aluminium extrusion is considered a sustainable method as it enables the efficient use of raw materials with minimal waste. Additionally, aluminium is highly recyclable, which aligns with the global emphasis on reducing environmental impact.
In terms of market growth, the aluminium extrusion process industry has witnessed steady expansion. The construction industry has been a major driver, utilizing extruded aluminium profiles for window frames, curtain walls, and structural components. The automotive sector has also embraced aluminium extrusions for lightweight components, contributing to the market growth.
Furthermore, market trends have been influenced by regional dynamics. Emerging economies, such as China and India, have experienced rapid industrialization, leading to increased demand for aluminium extrusion products. Developed regions, like North America and Europe, have focused on technological advancements and product innovation to cater to diverse industry needs.
In conclusion, the aluminium extrusion process industry has evolved significantly, driven by trends such as lightweight materials, technological advancements, and sustainability. These trends have contributed to the market growth, with the construction and automotive sectors being major contributors. As the industry continues to evolve, manufacturers are expected to focus on innovation, sustainability, and fulfilling the demands of various industries.
Custom Private Labeling and Branding Opportunities with Chinese aluminium extrusion process Manufacturers
Chinese aluminium extrusion process manufacturers offer excellent opportunities for custom private labeling and branding. With their advanced technology, superior quality products, and competitive prices, these manufacturers can help businesses establish their own unique brand identity in the market.
One advantage of working with Chinese aluminium extrusion process manufacturers is the flexibility they offer in terms of customization. These manufacturers have the capability to produce aluminium extrusion products in various shapes, sizes, and finishes, according to the specific requirements of the brand. This allows businesses to create customized products that align with their brand image and meet the demands of their target market.
Another benefit is the ability to private label the products. Chinese manufacturers understand the importance of branding and provide options for businesses to put their own logo, labels, and packaging on the products. This enables companies to build brand recognition and loyalty among customers.
Chinese aluminium extrusion process manufacturers also have the expertise to provide assistance throughout the branding process. They can offer design recommendations, create prototypes, and provide samples for testing and evaluation. This ensures that the final product meets the brand’s specifications and quality standards.
In addition to customization and private labeling, Chinese manufacturers offer cost-effective solutions. Their efficient production techniques and access to raw materials enable them to offer competitive prices compared to manufacturers in other regions. This allows businesses to maximize their profit margins while still delivering high-quality branded products to their customers.
Overall, partnering with Chinese aluminium extrusion process manufacturers presents businesses with unique opportunities for custom private labeling and branding. These manufacturers’ ability to customize products, provide private labeling options, and offer competitive prices make them a compelling choice for brands looking to establish their presence in the market.
Tips for Procurement and Considerations when Purchasing aluminium extrusion process
When purchasing aluminum extrusion process equipment, there are several key considerations to keep in mind. Here are some tips to help guide your procurement process:
1. Identify your needs: Determine the specific requirements of your project, such as desired extrusion shapes, dimensions, and production capacity. This will help you select the most suitable equipment.
2. Quality assurance: Look for reputable suppliers known for their quality products. Consider certifications, industry awards, and customer reviews to ensure the equipment meets your standards.
3. Customization options: Check if the supplier offers customization services to meet your specific requirements. This could include specialized die designs, surface finishes, or integrated product handling systems.
4. Equipment durability: Aluminum extrusion equipment is a long-term investment. Therefore, ensure that the machinery is robust, reliable, and built using high-quality materials to withstand continuous operation.
5. Technology and innovation: Stay updated with the latest advancements in aluminum extrusion technology. Look for suppliers who offer cutting-edge features like advanced controls, automation, or energy-efficient processes to enhance productivity and reduce costs.
6. Training and support: Choose a supplier that provides comprehensive training programs for operators, maintenance staff, and management. Also, ensure they offer reliable after-sales support, including spare parts availability and technical assistance.
7. Cost-efficiency: While price is a significant factor, don’t compromise on quality or service just to save money. Consider the overall value and long-term benefits rather than short-term cost.
8. Environmental sustainability: Consider the supplier’s commitment to sustainability. Look for equipment that incorporates eco-friendly practices such as energy-efficient processes, waste reduction, or use of recycled materials.
9. Supplier reputation: Research the supplier’s track record and market reputation. Consider factors like their experience in the industry, customer satisfaction, and financial stability to ensure a reliable partnership.
10. Long-term partnership: Establish a strong relationship with the supplier, as this will be beneficial for future upgrades, additional equipment needs, or ongoing support.
By considering these factors, you can make an informed procurement decision for your aluminum extrusion process equipment, ensuring smooth operations, optimal productivity, and high-quality output.
FAQs on Sourcing and Manufacturing aluminium extrusion process in China
1. What is the aluminium extrusion process?
The aluminium extrusion process involves shaping aluminium alloy into a desired cross-sectional profile by forcing it through a shaped die. This process allows for the creation of complex shapes and designs, making it suitable for a wide range of applications.
2. Why consider sourcing and manufacturing aluminium extrusions in China?
China is one of the largest producers of aluminium extrusions in the world. It offers a cost-effective solution for sourcing and manufacturing due to its abundant supply of raw materials and relatively lower labor costs. Additionally, Chinese manufacturers often have advanced extrusion equipment and technologies, ensuring high-quality products.
3. How to find reliable aluminium extrusion manufacturers in China?
To find reliable manufacturers, it is crucial to conduct thorough research and due diligence. Online platforms like Alibaba, Made-in-China, and Global Sources provide a wide range of supplier options. It is advisable to verify a manufacturer’s credentials, certifications, customer reviews, and request samples before making a final decision.
4. What quality measures should be considered?
Quality control is essential when sourcing and manufacturing aluminium extrusions in China. Look for manufacturers with ISO certifications, such as ISO 9001:2015, as it ensures proper quality management systems. Additionally, requesting factory audits or certifications specific to your industry or application can provide further reassurance.
5. How can I ensure timely delivery?
Timely delivery can be ensured by clearly communicating your production requirements and deadlines with the manufacturer. Establishing a detailed production timeline and agreeing on penalties for delays can also help to enforce punctuality. Regular communication and monitoring progress throughout the manufacturing process are important as well.
6. Are there any restrictions when importing aluminium extrusions from China?
Importing aluminium extrusions from China may be subject to certain regulations, such as customs duties, import taxes, and compliance with quality standards in the destination country. It is important to familiarize yourself with the import regulations of your country and work with a reliable customs agent to ensure compliance.
7. Do Chinese aluminium extrusion manufacturers offer customization options?
Chinese manufacturers often provide extensive customization options to meet specific design requirements. They have the capability to fabricate extrusions in various profiles, sizes, and finishes, enabling customers to obtain tailor-made solutions.
In conclusion, sourcing and manufacturing aluminium extrusions in China can be cost-effective and of high quality, given the country’s expertise in this industry. However, it is important to perform thorough research, ensure quality control, and comply with import regulations to ensure a successful partnership with Chinese manufacturers.
Why contact sourcifychina.com get free quota from reliable aluminium extrusion process suppliers?
Sourcifychina.com is a sourcing service that connects businesses with reliable aluminum extrusion process suppliers in China. As part of their effort to promote their services and build a trustworthy relationship with clients, Sourcifychina.com offers free quota to interested businesses.
There are several reasons why Sourcifychina.com provides this free quota from reliable aluminum extrusion process suppliers:
1. Building trust: By offering a free quota, Sourcifychina.com aims to build trust with potential clients. This allows businesses to experience the quality of their services before committing to a long-term partnership.
2. Cost-effective solution: The free quota enables businesses to evaluate the pricing and quality of the aluminum extrusion process without investing any capital upfront. This cost-effective approach helps companies minimize risks and make informed decisions.
3. Access to reliable suppliers: Sourcifychina.com has a network of reliable aluminum extrusion process suppliers in China. By offering the free quota, they provide businesses with access to these trusted suppliers, ensuring quality products and services.
4. Supplier verification: Sourcifychina.com thoroughly vetted and screened all their suppliers to ensure reliability and adherence to industry standards. The free quota allows businesses to verify the credibility and capabilities of these suppliers firsthand.
5. Customized solutions: Sourcifychina.com understands that each business has unique requirements. By providing a free quota, they can tailor their solutions to meet the specific needs of clients, ensuring a seamless and satisfactory sourcing experience.
In conclusion, Sourcifychina.com offers a free quota from reliable aluminum extrusion process suppliers to build trust, provide cost-effective solutions, grant access to verified suppliers, and offer customized solutions. This demonstrates their commitment to helping businesses connect with trustworthy suppliers in China, facilitating successful sourcing ventures.