Introduce about filling equipment guide,Qulity,Cost,Supplier,Certification,Market,Tips,FAQ
Filling equipment is essential in various industries to efficiently pack and seal products. This comprehensive guide aims to provide you with valuable information on filling equipment, including its quality, cost, suppliers, certifications, market trends, tips, frequently asked questions (FAQs), and more.
Quality is a critical factor to consider when selecting filling equipment. Reliable and durable machinery ensures accuracy, consistency, and long-term performance, minimizing downtime and maintenance costs. Look for established manufacturers known for their superior craftsmanship and excellent customer reviews to ensure high-quality equipment.
Cost is another crucial aspect to assess. It varies depending on the type and complexity of the filling equipment. Consider your budget and the long-term return on investment (ROI) when choosing the right machinery for your specific needs. While cost is important, prioritize quality, reliability, and customer support to avoid potential issues and disruptions that can be costly in the long run.
Finding a reputable supplier is vital in obtaining top-notch filling equipment. Research and identify trusted suppliers with an extensive product range, excellent customer support, and after-sales service. Engage with supplier representatives who can provide expert advice, customization options, and efficient technical support.
Certification is a key consideration to ensure compliance with industry standards and regulations. Look for filling equipment that has certifications such as ISO, CE, and UL, as they indicate adherence to safety, quality, and environmental standards.
Understanding the market trends and developments in filling equipment is crucial to make informed decisions. Stay updated on innovations, advancements, and emerging technologies that can enhance productivity, reduce waste, and improve efficiency in your operations.
Here are some quick tips to consider:
1. Assess your specific filling requirements before choosing the suitable equipment.
2. Consider scalability to accommodate future growth and diversification.
3. Conduct thorough research and compare different filling equipment options to make an informed decision.
4. Always prioritize safety features to protect your workforce and maintain product integrity.
5. Regularly maintain and service your equipment to ensure optimal performance and longevity.
Frequently asked questions (FAQs) may include queries about equipment capabilities, maintenance practices, troubleshooting, and more. Consult the manufacturer or supplier for comprehensive answers to your specific concerns.
In conclusion, investing in high-quality filling equipment is essential for efficient product packaging. Consider factors like cost, certification, supplier reputation, market trends, and follow the provided tips to make informed decisions. Always seek expert advice and gather comprehensive information when selecting filling equipment for your business.
Types of filling equipment
Filling equipment refers to machines or tools used to efficiently dispense materials into various containers such as bottles, cans, pouches, tubes, or jars. These devices are essential in industries where products need to be measured, weighed, or packaged accurately and quickly. There are various types of filling equipment available, each designed to suit different products and packaging requirements.
1. Piston Fillers: Piston fillers are highly versatile machines that use a piston mechanism to accurately dispense liquids or viscous products into containers. They can handle a wide range of products such as sauces, creams, lotions, gels, and even chunky or solid substances.
2. Gravity Fillers: Gravity fillers are particularly suitable for thin or free-flowing liquids. They work on the principle that the product flows down through a nozzle into the container due to gravity. The filling volume can be adjusted by changing the nozzle size or the time duration of the filling process.
3. Auger Fillers: Auger fillers are commonly used for powders, granules, or other dry products. These machines use a rotating auger to dispense a precise amount of product into the container. Auger fillers are ideal for filling materials such as spices, coffee, flour, or pharmaceutical powders.
4. Overflow Fillers: Overflow fillers are primarily used for filling containers with liquids that have a foaming nature or tend to produce foam during the filling process. These machines ensure that the liquid reaches a consistent level inside the container by allowing the excess liquid to overflow.
5. Volumetric Fillers: Volumetric fillers dispense a predetermined volume of product into each container. They can be used for liquid or semi-liquid products and are popular for their accuracy and reliability. Volumetric fillers can be piston-driven, cup fillers, or even rotary fillers.
6. Net Weight Fillers: Net weight fillers are designed to weigh products accurately before dispensing them into containers. They can be used for a variety of products, including solids, liquids, powders, or granules. These machines weigh the product before and after filling to ensure the correct weight is achieved.
7. Time/Pressure Fillers: Time/pressure fillers are suitable for filling containers with products that require precise filling ratios or specific pressure conditions. They use a combination of timers and pressure controls to regulate the filling process accurately.
These are just a few examples of the many types of filling equipment available on the market. Each filling machine has its own advantages and is designed to cater to specific product and packaging requirements in industries such as food and beverage, pharmaceutical, cosmetics, chemical, and more. Selecting the appropriate filling equipment is crucial to ensure efficient production, accurate measurements, and reduced wastage.
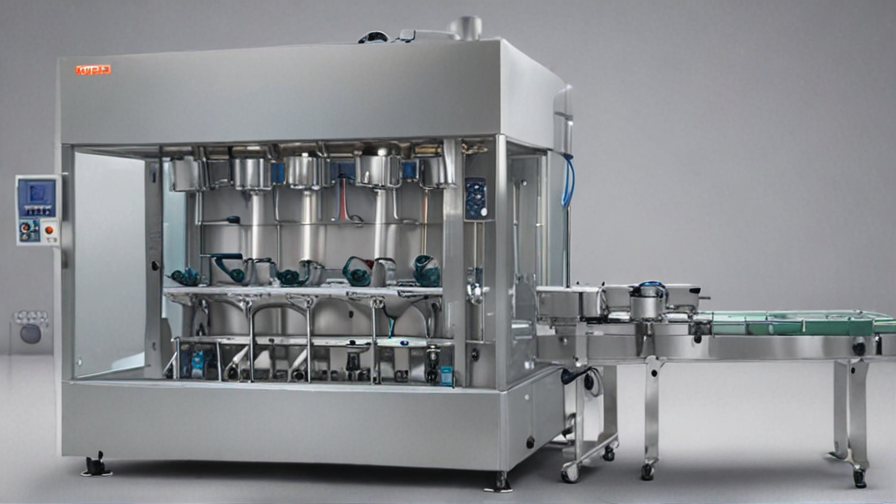
Pros and Cons of Using filling equipment
Filling equipment is widely used in various industries to automate the process of filling containers with liquids, powders, or granular materials. While there are several advantages of using filling equipment, there are also some limitations to consider. Here are the pros and cons of using filling equipment:
Pros:
1. Efficiency: Filling equipment is designed to streamline the filling process, resulting in increased productivity and efficiency. It can fill a large number of containers quickly and accurately, minimizing human errors and reducing the time required for manual filling.
2. Accuracy: Filling equipment is equipped with precise measuring mechanisms that ensure accurate filling volumes. This is particularly important in industries where precise measurements are crucial, such as pharmaceuticals or food and beverages.
3. Consistency: With filling equipment, the filling process is standardized, ensuring consistent product quality. This is especially beneficial in industries where consistency plays a critical role, such as cosmetics, where customers expect uniformity in their products.
4. Cost savings: Although the initial investment in filling equipment can be significant, it can result in long-term cost savings. By automating the filling process, companies can reduce labor costs, improve production efficiency, and minimize waste due to inaccurate or overfilling.
5. Safety and hygiene: Filling equipment is designed with safety features to prevent spillage and contamination. It helps maintain a clean and hygienic filling environment, particularly in industries like pharmaceuticals and food processing.
Cons:
1. Cost: As mentioned earlier, the initial cost of purchasing filling equipment can be substantial, especially for small or start-up businesses. Additionally, there may be ongoing costs for maintenance, repair, and spare parts.
2. Flexibility: Filling equipment is often designed for specific container shapes, sizes, and materials. This lack of flexibility can be a limitation if the containers used in the production process frequently change, requiring additional equipment or adjustments.
3. Complex setup and operation: Filling equipment requires proper installation and calibration, as well as specialized training for operators. This can be time-consuming and may require additional resources, such as expert technicians and training programs.
4. Limited compatibility: Filling equipment may not be compatible with certain products or materials due to their viscosity, foaming properties, or other characteristics. In such cases, alternative filling methods may be required.
5. Maintenance and downtime: Filling equipment needs regular maintenance, which can result in temporary downtime and reduced production. Unscheduled breakdowns or repairs can further disrupt the production process, leading to potential delays and loss of revenue.
In conclusion, filling equipment offers significant advantages in terms of efficiency, accuracy, consistency, cost savings, and safety. However, its limitations include the initial cost, lack of flexibility, complex setup, limited compatibility, and maintenance requirements. Therefore, a thorough analysis of the specific needs and requirements of the industry is essential before investing in filling equipment.
filling equipment Reference Specifications (varies for different product)
When it comes to filling equipment, there are various reference specifications that need to be considered. These specifications may vary depending on the specific product being filled. Here are some essential reference specifications that are commonly used:
1. Fill Volume Range: This refers to the minimum and maximum fill volumes that the equipment can handle. It is crucial to ensure that the filling equipment can accommodate the required fill volume range for the specific product. This specification may vary based on the product’s characteristics and packaging requirements.
2. Filling Speed: The filling speed specification indicates the rate at which the equipment can fill the product into containers. It is essential to match the desired production speed with the filling speed of the equipment to ensure efficient and timely production.
3. Accuracy: Accuracy is a critical specification that determines how precisely the filling equipment dispenses the product. It is crucial, especially for products that require precise filling quantities. Different products may have different accuracy requirements, and the filling equipment should meet those specifications to avoid overfilling or underfilling.
4. Container Compatibility: Filling equipment needs to be compatible with a wide range of containers, such as bottles, jars, cans, or bags. The equipment should be able to accommodate different shapes, sizes, and materials of containers, ensuring versatility in production.
5. Cleanability and Hygiene: Depending on the product being filled, cleanliness and hygiene may be essential factors. Filling equipment should be designed for easy cleaning and maintenance to prevent cross-contamination between different products and maintain product integrity.
6. Product Compatibility: Certain products may require specific materials or features to ensure compatibility and prevent any chemical reactions or contamination. The filling equipment should be made with materials that are compatible with the product being filled to maintain product quality and safety.
7. Automation and Integration: Filling equipment can be manual or fully automated. The level of automation required depends on the production volume and efficiency needs. Additionally, the equipment should be compatible with other packaging machinery, such as capping or labeling machines, to create a seamless production line.
8. Safety Features: Safety is paramount in any manufacturing process. Filling equipment should adhere to safety standards and have features such as emergency stop buttons, safety guards, and alarms to protect operators and prevent accidents.
By considering these reference specifications, manufacturers can select filling equipment that meets the specific requirements of their products, ensuring efficient and high-quality production processes.
Applications of filling equipment
Filling equipment is widely used across various industries for efficiently filling containers or packaging with liquids, powders, or granules. These machines offer numerous advantages such as accuracy, speed, cost-effectiveness, and hygiene, making them essential in many manufacturing processes. Here are some important applications of filling equipment:
1. Food and Beverage Industry: Filling machines are extensively used in the food and beverage industry for filling containers with liquids, sauces, dairy products, oils, and beverages. These machines ensure accurate filling quantities, reduce product wastage, and maintain hygiene standards. They are highly efficient for filling bottles, jars, cans, pouches, and even barrels or drums.
2. Pharmaceutical and Healthcare Sector: Filling equipment plays a critical role in the pharmaceutical and healthcare industry for filling medications, syrups, ointments, creams, gels, and other medical products. These machines are designed to meet stringent safety and sanitary standards, as well as ensure precise dosing and handling of sensitive substances.
3. Cosmetic and Personal Care Products: Filling machines are used in the cosmetic and personal care industry for filling containers with various products such as lotions, creams, shampoo, conditioners, perfumes, and oils. These machines help maintain product consistency, fill containers of varying shapes and sizes, and reduce human error in the filling process.
4. Chemical and Paint Industry: Filling equipment is crucial for the chemical and paint industry where hazardous substances need to be filled into containers. These machines are designed to handle corrosive chemicals, solvents, and paint in a safe and efficient manner. They ensure accurate filling without spillage, which results in significant cost savings and better product quality.
5. Industrial and Automotive Sector: Filling machines find applications in the industrial and automotive sector for filling lubricants, adhesives, sealants, coolant fluids, and other industrial products. These machines are designed for high-volume production, enabling faster filling speeds and maintaining consistency in product quality.
6. Agriculture and Horticulture: Filling equipment is used in the agriculture and horticulture industry for packaging fertilizers, pesticides, insecticides, and other agricultural chemicals. These machines ensure accurate dosing while reducing the risk of exposure to harmful substances.
7. Cleaning and Household Products: Filling machines are commonly used in the cleaning and household product industry for filling containers with detergents, soaps, disinfectants, and other cleaning solutions. They offer precise filling quantity control, ensuring product quality and reducing wastage.
In conclusion, filling equipment is utilized in a wide range of industries to improve productivity, accuracy, and efficiency in the packaging process. These machines are essential for achieving consistent product dosage, minimizing wastage, ensuring hygiene, and meeting safety standards across various sectors.
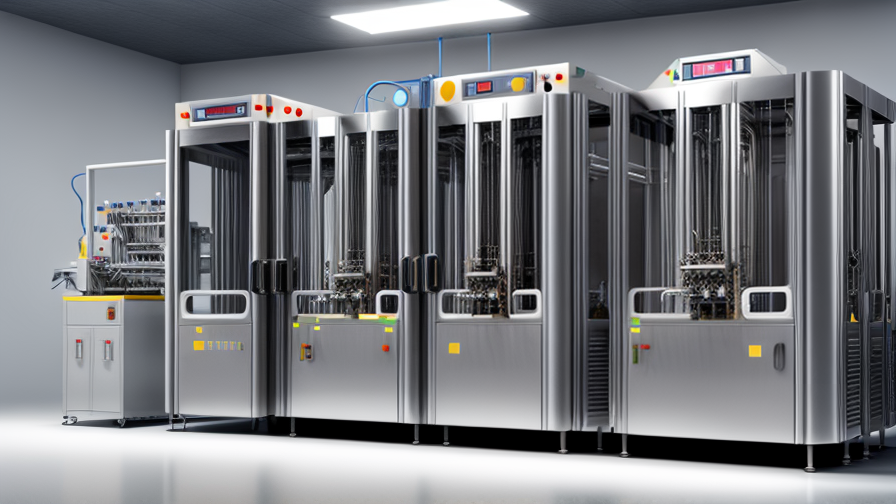
The Work Process and how to use filling equipment
The work process of filling equipment involves several steps to ensure efficient and accurate filling of various products. Here is a brief explanation of the work process:
1. Preparation: Before using the filling equipment, it is important to ensure that it is clean and properly calibrated. Any remnants of previous products should be removed, and the equipment should be set up according to the specific requirements of the product being filled.
2. Product handling: The product to be filled is usually stored in bulk containers or tanks. It is important to properly handle and transfer the product to the filling equipment. This may involve using pumps, pipes, or conveyors to transport the product from the storage to the filling area.
3. Filling setup: The filling equipment needs to be adjusted and set up for the specific product and container size. This includes setting the desired fill levels, adjusting conveyor speeds, and ensuring the proper sealing mechanisms are in place.
4. Filling operation: Once the equipment is set up, the filling process can begin. The containers are placed onto the conveyor or held in position manually. The filling equipment fills the containers with the desired volume of product, using techniques such as gravity filling, piston filling, or vacuum filling, depending on the characteristics of the product.
5. Quality control: Throughout the filling process, it is important to monitor the quality of the filled product. This may involve checking the weight or volume of each filled container to ensure it meets the desired specifications.
6. Packaging and labeling: After filling, the containers may need additional packaging or labeling. This can be done using automated labeling machines or manual packaging processes.
Using filling equipment efficiently requires proper training and a good understanding of the specific equipment being used.
1. Familiarize yourself with the equipment: Read the manufacturer’s instructions and guidelines for operating the filling equipment. Understand how each component works and learn about any safety precautions.
2. Prepare the equipment: Clean and sanitize the filling equipment before use. Ensure that all necessary adjustments and calibrations are done accurately.
3. Set up for specific product and container: Adjust the equipment settings according to the specific requirements of the product and containers to be filled. This includes fill levels, conveyor speeds, and any additional settings based on the product’s viscosity, temperature, or other characteristics.
4. Monitor the process: Pay close attention to the filling operation to ensure accuracy and efficiency. Keep an eye on the quality of the filled product, ensuring that the desired fill levels and weights are maintained consistently.
5. Maintain and troubleshoot: Regularly inspect and clean the filling equipment to prevent any potential issues. If any problems arise, follow troubleshooting guidelines provided by the manufacturer.
6. Train operators: Train and educate staff who will be operating the filling equipment. Provide proper instructions on its safe and efficient use, as well as any specific handling protocols for different products.
Using filling equipment efficiently can streamline production processes, improve product quality, and reduce wastage. Proper understanding and adherence to the work process and equipment guidelines are essential for achieving these outcomes.
Quality Testing Methods for filling equipment and how to control the quality
Quality testing methods for filling equipment involve various techniques to ensure that the equipment works efficiently and produces high-quality products. The following are some commonly used methods along with ways to control the quality.
1. Visual Inspection: A visual inspection involves checking the equipment for any visible defects, such as dents, scratches, or misalignments. It is essential to have a standard inspection checklist, and every unit should be inspected before and after use.
2. Functional Testing: Functional testing ensures that the filling equipment is operating as intended. This can involve running a test batch using water or a mock product to check for proper filling, sealing, and labeling. Any deviations from the expected performance should be investigated and resolved.
3. Weight Testing: Weight testing is crucial for accurate filling. It involves weighing multiple randomly selected filled containers to check for consistency. If the weight varies beyond an acceptable range, adjustments need to be made to maintain precision.
4. Leak Testing: Leak testing is essential to prevent product spoilage or contamination. The equipment should undergo rigorous inspections to ensure there are no leaks or faulty seals. This can be done using specialized leak detection equipment or methods like vacuum testing or pressure testing.
5. Cleaning and Sanitization: Proper and regular cleaning is critical to maintaining the quality of filling equipment. Clean-in-place (CIP) systems can automate the cleaning process, ensuring thorough sanitization of all contact surfaces. These systems should be validated to ensure their effectiveness.
To control the quality, the following measures can be implemented:
1. Standard Operating Procedures (SOPs): Develop detailed SOPs for each phase of the filling process, including set-up, operation, cleaning, and maintenance. These SOPs provide guidance on best practices to ensure consistent and reliable equipment performance.
2. Training: Proper training of operators and maintenance personnel is crucial. They should be well-versed in operating the equipment, detecting abnormalities, and troubleshooting potential issues. Regular training sessions can help improve skills and ensure that everyone follows the established procedures.
3. Maintenance and Calibration: Regular maintenance, calibration, and equipment inspections are necessary to identify any potential issues and prevent breakdowns. Develop a maintenance schedule and ensure all equipment is regularly serviced by qualified technicians.
4. Continuous Improvement: Encourage feedback from operators and employees regarding possible process improvements. Regularly review quality control data and identify areas for improvement. Implement corrective actions to address any identified weaknesses or deviations from quality standards.
By employing these testing methods and quality control measures, organizations can ensure that their filling equipment meets the required quality standards and reduces the likelihood of faulty or substandard products.
filling equipment Sample Policy and Post-Purchase Considerations for filling equipment from China
Sample Policy and Post-Purchase Considerations for Filling Equipment from China
1. Sample Policy:
a) Prior to placing a larger order, it is advisable to request samples of the filling equipment from the Chinese supplier. This will allow you to thoroughly evaluate the quality, functionality, and suitability of the equipment for your specific needs.
b) Clearly communicate your requirements and specifications to the supplier to ensure that the samples provided are representative of the final product.
c) Carefully inspect the samples upon receipt for any defects, damages, or inconsistencies. Test the equipment to confirm its performance and compatibility with your production requirements.
d) If the samples meet your expectations, negotiate the terms and conditions of the order with the supplier, including the quantity, delivery schedule, pricing, and any other relevant aspects.
e) In case the samples do not meet your requirements, communicate the issues to the supplier, and discuss possible remedies or alternatives. If necessary, request additional samples or consider sourcing from alternative suppliers.
2. Post-Purchase Considerations:
a) Thoroughly inspect the received filling equipment upon delivery to ensure it matches the specifications agreed upon with the supplier.
b) Test the equipment promptly to identify any functional or performance issues. Engage the supplier to resolve any discrepancies or defects promptly.
c) Conduct a quality control check during the initial operation of the filling equipment to ensure it meets your production requirements, safety standards, and product quality expectations.
d) Establish open lines of communication with the supplier to address any concerns, request technical support, or seek assistance with maintenance or troubleshooting.
e) Maintain a record of all interactions and communications with the supplier, including any complaints, warranty claims, or the resolution of any disputes for future reference.
f) Regularly perform maintenance, inspections, and servicing of the filling equipment, following the supplier’s recommendations and guidelines.
g) Evaluate the overall performance, reliability, and durability of the filling equipment over time to determine if further orders are warranted from the same supplier or if you should explore alternative suppliers in China or other regions.
It is crucial to conduct thorough due diligence while procuring filling equipment from China, ensuring transparency, clear communication, and quality assurance throughout the process.
Sourcing filling equipment from China: Opportunities, Risks, and Key Players
Sourcing filling equipment from China provides ample opportunities for businesses globally, including cost savings and access to a wide range of suppliers. China is known for its robust manufacturing sector, offering a variety of filling equipment options at competitive prices. However, it is essential to consider the associated risks and key players before engaging in the sourcing process.
Opportunities for sourcing filling equipment from China are primarily driven by cost advantages. Chinese manufacturers benefit from low labor and production costs, resulting in more affordable filling equipment compared to other countries. This cost advantage enables businesses to save significantly on their procurement expenses, allowing for increased profitability or competitive pricing in the market.
Additionally, China offers a vast network of suppliers specializing in filling equipment. This availability provides buyers with various options, facilitating customization and the ability to meet specific requirements. From small-scale manual filling machines to fully automated production lines, China’s manufacturing capabilities cater to diverse needs across industries.
However, along with opportunities, there are risks associated with sourcing from China. Quality control can be a concern as the market is vast and diverse. While many reputable suppliers adhere to international quality standards, there is a risk of encountering substandard or counterfeit products. Conducting thorough due diligence, including product inspections and supplier verifications, is crucial to mitigate these risks.
Another risk to consider is intellectual property protection. China has faced criticism in the past for intellectual property infringements. When sourcing filling equipment, businesses must ensure supplier compliance with intellectual property rights and confidentiality agreements to safeguard proprietary technologies.
Key players in the Chinese filling equipment industry include well-established manufacturers like Shanghai JOYGOAL Packaging Machinery Co., Ltd., Zhangjiagang King Machine Co., Ltd., and Guangzhou Jinfeng Light Industry Machinery Co., Ltd. These companies have a track record of supplying filling equipment globally and often offer a wide range of options suitable for different applications.
In summary, sourcing filling equipment from China presents significant opportunities, particularly in terms of cost savings and access to a diverse supplier network. However, businesses must navigate potential risks related to quality control and intellectual property protection. By conducting thorough due diligence and engaging with reputable suppliers, businesses can capitalize on the benefits offered by the Chinese market.
How to find and select reliable filling equipment manufacturers in China,use google search manufacturers and suppliers
Finding and selecting reliable filling equipment manufacturers in China can be a daunting task, but by following a few steps, you can start your search effectively.
1. Utilize Google Search: Begin your search by typing relevant keywords like “filling equipment manufacturers in China” or “reliable filling equipment suppliers” into the Google search engine. This will generate a list of potential manufacturers and suppliers.
2. Refine your search: Narrow down your options by adding more specific keywords related to your requirements, such as the type of filling equipment you need (e.g., liquid filling machines, powder filling machines, etc.), industry-specific terms, or any specific features or certifications.
3. Evaluate the website: Once you have identified some potential manufacturers or suppliers, visit their websites to assess their credibility. Look for clear and professional websites that provide detailed information about their products, company history, manufacturing capabilities, and contact details.
4. Verify their legitimacy: Check if the manufacturer has valid certifications, such as ISO 9001, which ensures adherence to quality management systems. Look for any industry associations or memberships that might add to their credibility.
5. Assess their experience: Look for established manufacturers with a track record of supplying filling equipment. Check how long they have been in operation, their client base, and if they have supplied equipment to companies similar to yours.
6. Compare product range and customization options: Evaluate the manufacturer’s product range and ensure that they offer the specific type and capacity of filling equipment you require. Additionally, check if they can provide customization options to meet your individual needs.
7. Read reviews and testimonials: Search for online reviews or testimonials from their previous customers to get an understanding of the company’s reputation. Look for positive feedback related to product quality, after-sales service, and prompt delivery.
8. Contact the shortlisted manufacturers: Finally, get in touch with the shortlisted manufacturers to discuss your requirements, request quotes, and ask any questions you may have. Evaluate their responsiveness, willingness to provide detailed information, and their ability to understand and meet your specific needs.
During this process, it is essential to exercise due diligence by conducting thorough research, asking for samples, and seeking recommendations from industry professionals or colleagues to ensure you select a reliable filling equipment manufacturer in China that aligns with your requirements.
How to check filling equipment manufacturers website reliable,use google chrome SEOquake check if ranking in top 10M
When looking to check the reliability of a filling equipment manufacturer’s website, you can take a few steps to ensure credibility. Here’s a method using Google Chrome and SEOquake extension:
1. Install Google Chrome: Start by downloading and installing the Google Chrome web browser if you haven’t already.
2. Add SEOquake Extension: Visit the Chrome Web Store and search for the SEOquake extension. Install it to your browser.
3. Open the Manufacturer’s Website: Go to the website of the filling equipment manufacturer that you want to evaluate.
4. Use SEOquake: With the website open, click on the SEOquake icon in your browser’s toolbar. This tool provides a wide range of SEO-related information about a website.
5. Check Global Rank: Once SEOquake is activated, look for the “Global Rank” information. This indicates the website’s rank out of the top 10 million websites globally. A lower rank suggests higher traffic and potentially higher reliability.
6. Analyze Additional Metrics: Explore other metrics provided by SEOquake, such as PageRank, Alexa Rank, and the number of indexed pages. These can provide additional insights into the website’s reliability and popularity.
7. Gather More Information: While SEOquake offers valuable information, it’s important to gather further evidence. Look for customer reviews, testimonials, industry certifications, and partnerships displayed on the website. These can help establish the manufacturer’s reputation and reliability.
By using this method, you can get a preliminary understanding of the website’s reliability based on its ranking and various SEO metrics. However, it’s crucial to combine this analysis with other factors like customer feedback and industry reputation to make a fully informed decision.
Top 10 filling equipment manufacturers in China with each 160 words introduce products,then use markdown create table compare
1. Aseptic Solutions Co. Ltd: Aseptic Solutions specializes in manufacturing a wide range of filling equipment, including aseptic bag fillers, aseptic pouch fillers, and aseptic bottle fillers. Their products are known for their high accuracy, efficiency, and reliability.
2. Newamstar Packaging Machinery Co. Ltd: With over 30 years of experience, Newamstar is a leading manufacturer of filling equipment. They offer a comprehensive range of products, including water filling machines, juice filling machines, carbonated beverage filling machines, and more.
3. Jiangsu Jinrong Machinery Co. Ltd: Jinrong Machinery is known for its expertise in manufacturing dairy beverage packaging machinery. They provide various filling equipment, such as carton packers, bottle sterilizers, cup filling machines, and more.
4. Guangzhou Techgen Packaging Machinery Co. Ltd: Techgen Packaging Machinery specializes in the production of automatic liquid filling machines. Their products range from small-scale fillers to high-speed rotary fillers, suitable for various industries such as food and beverage, pharmaceuticals, and cosmetics.
5. Shanghai Jimei Food Machinery Co. Ltd: Jimei Food Machinery offers a wide range of filling equipment, including liquid filling machines, juice filling machines, milk filling machines, and more. Their products are renowned for their accuracy, efficiency, and flexibility.
| Manufacturer | Products Offered | Notable Features |
|—————|——————|——————|
| Aseptic Solutions Co. Ltd | Aseptic bag fillers, aseptic pouch fillers, aseptic bottle fillers | High accuracy and reliability |
| Newamstar Packaging Machinery Co. Ltd | Water filling machines, juice filling machines, carbonated beverage filling machines | Extensive experience in the industry |
| Jiangsu Jinrong Machinery Co. Ltd | Carton packers, bottle sterilizers, cup filling machines | Specializes in dairy beverage packaging |
| Guangzhou Techgen Packaging Machinery Co. Ltd | Automatic liquid filling machines | Range from small-scale to high-speed fillers |
| Shanghai Jimei Food Machinery Co. Ltd | Liquid filling machines, juice filling machines, milk filling machines | Known for accuracy, efficiency, and flexibility |
6. Zhangjiagang Proman Machine Co. Ltd: Proman Machine focuses on manufacturing water filling machines, including PET bottle filling machines, bottle rinsing machines, and bottle capping machines. They provide customized solutions for different production needs.
7. Beijing Meckey Engineering Co. Ltd: Meckey Engineering specializes in the production of filling equipment for various industries, such as food, beverage, pharmaceuticals, and chemicals. They offer a wide range of products, including liquid filling machines, powder filling machines, and paste filling machines.
8. Shanghai Joylong Industry Co. Ltd: Joylong Industry is a prominent manufacturer of liquid filling machines, including beverage filling machines, milk filling machines, and yogurt filling machines. Their products are designed for high productivity and operational efficiency.
9. Langfang Best Crown Packing Machinery Co. Ltd: Best Crown Packing Machinery manufactures a comprehensive range of filling equipment, such as water filling machines, juice filling machines, and carbonated beverage filling machines. Their products are known for their advanced technology and stable performance.
10. Guangzhou Babel Information Technology Co. Ltd: Babel Information Technology focuses on providing high-quality filling equipment for the pharmaceutical industry. They offer a wide range of products, including powder filling machines, liquid filling machines, and granule filling machines, with a focus on precision and hygiene.
In summary, China’s top filling equipment manufacturers offer a diverse range of products to meet the needs of various industries. With their advanced technology, reliability, and efficiency, these manufacturers continue to contribute to the growth of the packaging and filling sector.
Background Research for filling equipment manufacturers Companies in China, use qcc.com archive.org importyeti.com
When it comes to filling equipment manufacturers in China, several online platforms can provide valuable information. Qcc.com, archive.org, and importyeti.com are three such platforms that can assist in conducting background research.
Qcc.com is a popular database website focused on providing information about Chinese companies. It can help identify filling equipment manufacturers by searching for relevant keywords or using specific filters such as location or industry. The platform provides general company information, including contact details, registered capital, and key personnel. This information can be crucial in shortlisting potential manufacturers for further research.
Archive.org, also known as the Wayback Machine, is a digital archive of websites. It can be useful for tracking the historical development of filling equipment manufacturers’ websites and understanding their evolution over time. By analyzing past versions of websites, researchers can gather insights about product offerings, partnerships, and overall business growth.
Importyeti.com is a platform that specializes in providing data on import and export activities. It can be utilized to discover filling equipment manufacturers that have a track record of exporting their products. The platform offers shipment details, including suppliers, buyers, and product descriptions. This information helps gain an understanding of a manufacturer’s production capabilities, target markets, and potential competitors.
By utilizing these platforms, researchers can efficiently gather relevant information about filling equipment manufacturers in China. They can identify potential companies, explore their historical growth, and assess their international business activities. This targeted background research will provide insights to facilitate the sourcing and selection process for filling equipment manufacturers in China.
Leveraging Trade Shows and Expos for filling equipment Sourcing in China
Trade shows and expos can be extremely beneficial for businesses looking to source equipment from China. These events provide a unique opportunity for companies to meet and connect with suppliers, gather market intelligence, and establish mutually beneficial relationships.
One of the main advantages of attending trade shows and expos is the ability to see and physically inspect the equipment. This allows businesses to evaluate the quality, functionality, and suitability of the products before making a purchasing decision. It also provides a platform for businesses to compare multiple suppliers and their offerings in one location, saving time and effort.
Additionally, trade shows and expos often attract a wide range of suppliers, including small and medium-sized enterprises (SMEs) that may not have a strong online presence. This gives businesses the opportunity to discover new and niche suppliers who might not be easily found through other channels.
Another significant advantage of trade shows and expos is the opportunity to establish direct relationships with suppliers. Meeting face-to-face enables businesses to establish trust, negotiate better pricing, discuss customization options, and address any concerns or queries in real-time. These direct relationships can prove invaluable in the long run, as they often result in increased product quality, improved communication, and faster response times.
Furthermore, trade shows and expos are an excellent platform for networking and learning from industry experts. Seminars, workshops, and presentations at these events can provide valuable insights into industry trends, regulations, and best practices. Engaging with experts and peers can help businesses refine their sourcing strategies, overcome challenges, and stay ahead of the competition.
In conclusion, trade shows and expos offer an efficient and effective way to source equipment from China. They provide an opportunity for businesses to physically evaluate products, discover new suppliers, establish direct relationships, and gain industry intelligence. By leveraging these events, companies can streamline their sourcing process, mitigate risks, and foster long-term partnerships with reliable suppliers.
The Role of Agents and Sourcing Companies in Facilitating filling equipment Purchases from China
Agents and sourcing companies play a crucial role in facilitating filling equipment purchases from China. With their expertise and knowledge of the Chinese market, they act as intermediaries between buyers and manufacturers, streamlining the entire sourcing and purchasing process.
One of the main advantages of using agents and sourcing companies is their ability to identify reliable and reputable manufacturers in China. They have extensive networks and relationships with trusted suppliers, ensuring that buyers are connected with quality manufacturers who can meet their specific requirements. Agents also have an in-depth understanding of local regulations, standards, and industry practices, helping buyers navigate any potential challenges.
Agents and sourcing companies provide comprehensive services throughout the procurement process. They assist buyers in identifying suitable equipment based on their specific needs and budget constraints. They provide valuable guidance during factory visits, ensuring that buyers have a thorough understanding of the manufacturing capabilities and quality control procedures of potential suppliers.
Furthermore, agents are proficient in negotiating favorable terms and conditions on behalf of buyers. They have extensive experience in price negotiation, helping buyers secure competitive prices and favorable payment terms. Sourcing companies can also assist with quality control inspections, ensuring that the equipment meets the required standards before shipment.
Another key role of agents and sourcing companies is logistics management. They coordinate the transportation, customs clearance, and delivery of the purchased equipment, ensuring a smooth and timely process. This expertise in logistics eliminates any potential headaches and allows buyers to focus on their core business operations.
In summary, agents and sourcing companies act as indispensable partners when purchasing filling equipment from China. Their extensive knowledge of the Chinese market, connections with reputable manufacturers, negotiation skills, and logistics management expertise streamline the entire purchasing process and ensure a successful and efficient procurement experience for the buyers.
Price Cost Research for filling equipment manufacturers Companies in China, use temu.com and 1688.com
When it comes to filling equipment manufacturers in China, two popular websites for price cost research are temu.com and 1688.com. These platforms offer a wide range of products and suppliers, making it convenient for businesses to find the best deals.
temu.com is a comprehensive platform that connects buyers with Chinese manufacturers. With a user-friendly interface, it allows users to search for filling equipment manufacturers specifically. By utilizing filters such as production capacity, location, and product type, businesses can narrow down their search and find the most suitable suppliers. The website also provides detailed information about each manufacturer, including their product range, certifications, and customer reviews. This allows buyers to assess the quality and reliability of the manufacturers before making a purchase.
1688.com, a subsidiary of Alibaba, is another popular website for price cost research in China. It is primarily in Mandarin, but with the help of translation tools, users can navigate through its vast database of suppliers. Similar to temu.com, it offers various filters to help businesses find the right filling equipment manufacturers. The platform provides a wide range of products at competitive prices, making it a preferred choice for buyers looking for cost-effective solutions.
When conducting price cost research on temu.com and 1688.com, it is important to have a clear understanding of the specific requirements and quality standards needed for filling equipment. Buyers should compare prices, manufacturers’ credibility, and any additional services offered. It is also recommended to communicate directly with the suppliers to negotiate prices, inquire about customization options, and discuss shipping and payment terms.
In conclusion, temu.com and 1688.com are valuable platforms for price cost research when searching for filling equipment manufacturers in China. By utilizing these websites, businesses can find cost-effective solutions while ensuring quality and reliability.
Shipping Cost for filling equipment import from China
The shipping cost for importing filling equipment from China depends on various factors such as weight, dimensions, shipping method, and location. Typically, there are two main shipping methods: air freight and sea freight.
For air freight, the cost is usually higher but provides faster delivery. The price is calculated based on the volumetric or actual weight of the equipment. Volumetric weight is calculated by multiplying the length, width, and height of the package and dividing it by a volumetric factor. The cost also includes additional charges such as fuel surcharges, handling fees, customs clearance, and delivery to the final destination. On average, air freight costs can range from $4-$10 per kilogram.
On the other hand, sea freight is a more affordable option for shipping larger and heavier equipment. The cost is calculated based on the cubic meter (CBM) or cubic foot (CFT) of the cargo. Shipping companies offer either Full Container Load (FCL) or Less than Container Load (LCL) services. FCL is suitable if the equipment occupies a whole container, while LCL is ideal for smaller shipments. The cost includes sea freight charges, documentation fees, customs clearance, local charges, and inland transportation. On average, sea freight costs can range from $800 to $1500 per cubic meter.
It’s important to note that these costs are estimates and can vary based on factors such as the shipping company, seasonality, fuel prices, and any additional services required. To get an accurate shipping cost, it is recommended to request quotes from multiple shipping companies and compare their offers. Additionally, it is advisable to work with a freight forwarder or a shipping agent who can help you navigate the import process, handle documentation, and provide guidance on the most cost-effective shipping method.
Compare China and Other filling equipment Markets: Products Quality and Price,Visible and Hidden Costs
China and other filling equipment markets vary in terms of product quality and price as well as visible and hidden costs.
In terms of product quality, China has made significant progress in recent years. Chinese manufacturers have improved their production processes and invested in technologies to enhance the quality of their filling equipment. However, there is still a perception that products from certain other countries, such as Germany or Japan, have higher quality standards. This perception is mainly due to the long-established reputation of these countries for producing reliable and durable industrial machinery.
When it comes to price, Chinese filling equipment often offers a competitive advantage. China’s manufacturing capabilities and lower labor costs enable its manufacturers to offer their products at more affordable prices compared to other countries. This price advantage has made China an attractive option for businesses seeking cost-effective filling equipment solutions.
Visible costs, such as the initial purchase price and transportation costs, are generally lower for Chinese filling equipment. However, hidden costs can arise due to factors such as longer lead times for Chinese manufacturers, which can delay production schedules. Additionally, warranty and aftersales service may differ between Chinese manufacturers and manufacturers from other countries, and this can impact the overall cost of ownership.
In summary, while China has made advancements in product quality, some customers may still prefer filling equipment from other countries due to their longstanding reputation for higher quality. Chinese filling equipment often has a competitive advantage in terms of price, but hidden costs such as longer lead times and differing aftersales service should be taken into consideration when evaluating the total cost of ownership. Ultimately, the choice between China and other filling equipment markets will depend on the specific requirements and priorities of each customer.
Understanding Pricing and Payment Terms for filling equipment: A Comparative Guide to Get the Best Deal
When it comes to purchasing filling equipment, understanding pricing and payment terms is crucial to ensure you get the best deal. This comparative guide will help you navigate these aspects efficiently and make an informed decision.
Determining the pricing of filling equipment involves evaluating several factors. First, consider the equipment’s technical specifications, such as its capacity, speed, and functionality. Higher capacity or advanced features may result in a higher price. Additionally, the brand reputation and quality of the equipment also influence the pricing. Established brands often charge a premium for their reliable and durable products.
Comparing different suppliers is key to getting the best deal. Request quotes from multiple vendors and extensively study the inclusions and exclusions in their prices. Look out for hidden costs such as installation fees or warranty charges, as they can significantly impact the total cost. Understanding the comprehensive breakdown of prices will allow you to make an accurate comparison between different suppliers.
Payment terms are another vital aspect to consider. Suppliers may offer various options, including upfront payment, installment plans, or leasing agreements. Each option has its benefits and considerations. While upfront payment provides immediate ownership and potentially lower prices, installment plans offer flexibility in managing cash flow. Leasing can be a cost-effective solution for short-term projects or when equipment upgrades are frequent.
It is crucial to carefully review the terms and conditions associated with different payment options. Consider factors such as interest rates, repayment periods, penalties for late payments, and ownership transfer clauses. Ensure that the chosen payment terms align with your business objectives and financial capabilities.
Moreover, negotiate whenever possible to secure better pricing or more favorable payment terms. Highlighting your commitment to a long-term partnership or emphasizing a bulk order could provide leverage during negotiations.
Finally, do not overlook the importance of after-sales support and warranty when evaluating pricing. A comprehensive warranty and prompt technical assistance can save you from potential losses and downtime in case of any equipment malfunction.
In conclusion, understanding pricing and payment terms is integral to obtaining the best deal for filling equipment. Evaluate the pricing based on technical specifications, compare quotes from different suppliers, and consider hidden costs. Analyze payment options and negotiate for better terms when feasible. Don’t forget to assess after-sales support and warranty provisions. By following these guidelines, you can make a well-informed decision and secure the ideal filling equipment for your business.
Chinese Regulations and Industry Standards Certifications for filling equipment,Import Regulations and Customs for filling equipment from China
Chinese regulations and industry standards certifications for filling equipment are crucial for ensuring the quality and safety of such equipment. One of the key certifications required is the China Compulsory Certificate (CCC). This certification is mandatory for many products, including filling equipment, and is regulated by the Certification and Accreditation Administration of China (CNCA). It ensures that the equipment meets certain safety and quality standards and is fit for use in China.
In addition to the CCC, filling equipment may also need to comply with industry-specific standards such as the China Food and Drug Administration (CFDA) standards for food and drug filling equipment. These standards are designed to ensure that the equipment used in the food and pharmaceutical industries meets specific hygiene and safety requirements.
Importing filling equipment from China requires compliance with import regulations and customs procedures. Importers are required to provide necessary documentation during the import process. This includes a commercial invoice, packing list, bill of lading or airway bill, and any other relevant certificates or permits. It is important to note that customs duties, import taxes, and other fees may be applicable, and importers need to be aware of these costs.
Importers may need to work with a customs agent or freight forwarder who can assist in navigating the customs clearance process. This includes ensuring that all required documentation is in order and that any necessary payments are made.
It is essential for importers to familiarize themselves with the specific regulations and requirements of their country of import, as these may vary. Engaging a professional to ensure compliance with customs and import regulations is recommended to avoid any issues or delays in the importing process.
In conclusion, ensuring compliance with Chinese regulations and industry standards certifications is vital for importing filling equipment from China. Additionally, importers must be aware of the import regulations and customs procedures of their country to facilitate a smooth importing process.
Sustainability and Environmental Considerations in filling equipment Manufacturing
Sustainability and environmental considerations play a crucial role in the manufacturing of filling equipment. Filling equipment is used in various industries, such as food and beverage, pharmaceuticals, and cosmetics, to fill products into containers. Here are some key aspects to consider for sustainable filling equipment manufacturing:
1. Energy Efficiency: Manufacturers need to focus on designing filling equipment that minimizes energy consumption. This can be achieved by using efficient motors, implementing energy-saving technologies, and reducing power wastage during operation. By reducing energy usage, manufacturers can lower their carbon footprint and contribute to a more sustainable manufacturing process.
2. Material Selection: Opting for eco-friendly materials in equipment construction is essential. The use of sustainable materials reduces environmental impact, such as the emission of greenhouse gases during the production phase and waste generation. Manufacturers should seek materials that are recyclable, biodegradable, or made from renewable resources to ensure minimal environmental impact.
3. Waste Reduction: Implementing waste reduction approaches is crucial in filling equipment manufacturing. This involves minimizing material wastage during production, optimizing processes to reduce scrap or rework, and ensuring proper disposal of waste materials. Recycling and reusing materials wherever possible can also significantly reduce the environmental impact of manufacturing.
4. Water Management: Efficient water management is vital to minimize resource consumption and protect water bodies. Manufacturers should strive to install equipment that reduces water usage during cleaning and operation. Innovative solutions, such as the use of closed-loop systems or water recycling technologies, can help conserve water and reduce the overall environmental impact.
5. Emissions Control: Manufacturers should focus on controlling emissions from filling equipment to reduce air pollution. This includes implementing emission control technologies, such as filters or catalytic converters, to minimize harmful pollutants released into the atmosphere during the manufacturing process.
6. Product Life Cycle Assessment: Assessing the overall environmental impact of filling equipment throughout its life cycle is crucial. Manufacturers should evaluate the energy consumption, raw material usage, waste generation, and emissions associated with their equipment from production to disposal. This assessment helps identify areas for improvement and informs decisions regarding eco-design and end-of-life management.
By incorporating sustainability and environmental considerations into filling equipment manufacturing, manufacturers can contribute to a greener and more environmentally responsible industry. This not only benefits the planet but also enhances the brand image and competitiveness of the manufacturer in the market.
List The Evolution history of “filling equipment”
Filling equipment has evolved greatly over time, with advancements in technology and the changing demands of various industries. From simple manual methods to complex automated systems, here is a brief overview of the evolution history of filling equipment.
1. Manual Filling: The earliest form of filling equipment involved manual methods, utilizing containers such as buckets or pitchers to transfer liquids or granular materials. This crude method required a labor-intensive process and lacked accuracy.
2. Gravity Filling: Gravity filling systems emerged as an improvement over manual methods. These systems utilized gravity to fill containers. Examples include pouring liquid from a container into bottles or barrels. Although still a manual process, gravity filling enabled more precise measurement and reduced spillage.
3. Piston Filling: Piston filling machines were introduced in the early 20th century, revolutionizing the packaging industry. These machines used a piston to draw product from a container and dispensed it into bottles or other containers. Piston fillers provided increased accuracy and speed compared to previous methods.
4. Vacuum Filling: In the mid-20th century, vacuum filling machines were introduced. These machines employed vacuum pressure to both draw the product into the filling chamber and dispense it into containers. Vacuum fillers offered enhanced accuracy and controlled filling levels.
5. Time-Flow Filling: As the demand for automation grew, time-flow filling machines were invented. These machines regulated the filling process by controlling the flow rate and timing, improving accuracy and consistency. Time-flow fillers were widely adopted in various industries.
6. Liquid Level Filling: Liquid level filling machines emerged, further improving accuracy by measuring the liquid level in containers. These machines ensured consistent fill levels by monitoring the container’s liquid level and adjusting the filling process accordingly.
7. Volumetric Filling: Volumetric filling machines marked a significant advancement in filling technology. Using positive displacement techniques, these machines accurately measured and dispensed precise volumes of liquids or granular materials, regardless of the product consistency or viscosity.
8. Modern Automated Systems: With the advent of computer-controlled technology, fully automated filling systems have become prevalent. These systems utilize sophisticated sensors, programmable logic controllers (PLCs), and human-machine interfaces (HMIs) to automate the filling process. They offer high efficiency, accuracy, and flexibility to cater to diverse industry requirements.
In conclusion, the evolution history of filling equipment showcases a progression from manual methods to advanced automated systems. Each step forward has brought increased accuracy, efficiency, and consistency, enabling industries to meet their filling needs effectively.
The Evolution and Market Trends in filling equipment Industry
The filling equipment industry has witnessed significant evolution and market trends over the years. With advancements in technology and changing consumer demands, filling equipment has become more efficient and versatile.
One major evolution in the industry has been the shift towards automation. Manual filling processes have been replaced by automated machinery that offers higher accuracy, precision, and speed. This has resulted in increased productivity and reduced labor costs for companies. Furthermore, automation has enabled the integration of filling equipment with other production systems, enhancing overall operational efficiency.
Another important market trend is the demand for flexibility in filling equipment. Companies are now looking for machinery that can handle different types of products, containers, and volumes. This trend has led to the development of multi-purpose filling equipment that can adapt to various requirements. Manufacturers are investing in innovative technologies and software that allow quick and easy changeovers between different products and packaging formats.
Moreover, the filling equipment industry is witnessing a rise in demand for sustainability and environmentally friendly solutions. Consumers and regulatory bodies now emphasize the use of biodegradable materials and reduction of waste. As a result, filling equipment manufacturers are developing eco-friendly solutions such as reduced packaging sizes, recyclable materials, and efficient product recovery systems.
Additionally, the global market for filling equipment is expanding due to increasing industrialization in emerging economies. The growth of industries such as food and beverage, pharmaceuticals, and personal care in countries like China, India, and Brazil has created a significant demand for filling equipment. Manufacturers are capitalizing on this trend by expanding their product offerings and establishing a strong presence in these regions.
In conclusion, the filling equipment industry has evolved significantly to meet the changing needs of consumers and advancements in technology. Automation, flexibility, sustainability, and global expansion are major trends driving the market. As companies focus on efficiency, versatility, and environmental consciousness, the filling equipment industry is expected to continue its growth and innovation in the coming years.
Custom Private Labeling and Branding Opportunities with Chinese filling equipment Manufacturers
Chinese filling equipment manufacturers offer custom private labeling and branding opportunities for businesses looking to establish their own unique product identity. These manufacturers provide the option to incorporate custom labels and branding elements onto their filling equipment, allowing businesses to showcase their brand’s logo, images, and colors.
With the advancements in technology and manufacturing capabilities, Chinese filling equipment manufacturers can efficiently and accurately apply custom labels onto the equipment. This includes labeling on various parts of the filling machines, such as control panels, dials, and front panels. By having customized equipment, businesses can enhance their brand recognition and create a sense of exclusivity.
Private labeling and branding opportunities with Chinese filling equipment manufacturers not only help businesses showcase their brand identity but also have many practical benefits. Firstly, it allows the equipment to blend seamlessly with existing production lines or machinery, ensuring a cohesive and unified appearance. This is particularly important for businesses that prioritize a consistent and professional brand image.
Additionally, private labeling and branding on filling equipment enables businesses to enhance their product packaging. By incorporating matching colors and designs on both the packaging and equipment, businesses can create a visually appealing and aesthetically pleasing product presentation.
Furthermore, custom private labeling and branding can also serve as a marketing tool. As the equipment is often on display in the production area, custom labeling can attract attention from customers, suppliers, and stakeholders, acting as a subtle form of advertising. This can be particularly beneficial when the equipment is used in trade shows or exhibitions.
In conclusion, Chinese filling equipment manufacturers provide businesses with the opportunity for custom private labeling and branding. By incorporating their brand identity onto the equipment, businesses can enhance their product packaging, create a consistent brand image, and utilize the equipment as a marketing tool. These advantages make private labeling and branding with Chinese filling equipment manufacturers a sought-after option for companies looking to establish a unique product identity.
Tips for Procurement and Considerations when Purchasing filling equipment
When it comes to procurement and purchasing filling equipment, there are several key tips and considerations that can help ensure a successful and efficient process. These include:
1. Define your requirements: Clearly identify your needs and specifications for the filling equipment. Consider factors such as the type of products to be filled, expected production capacity, required fill accuracy, and any specific features or functionalities needed.
2. Research suppliers: Conduct thorough research to identify reputable and experienced suppliers of filling equipment. Look for suppliers who have a proven track record, positive customer reviews, and offer reliable after-sales support.
3. Request quotes: Contact multiple suppliers and request detailed quotes that include not only the equipment cost but also additional expenses such as installation, training, maintenance, and spare parts. Analyze and compare these quotes to ensure you are getting the best value for your investment.
4. Consider long-term costs: Evaluate the total cost of ownership beyond the initial purchase price. This includes ongoing maintenance, energy consumption, repair costs, and the availability of spare parts. Choosing equipment with high efficiency and durability can save you money in the long run.
5. Test equipment quality: If possible, request a demonstration or visit the supplier’s facility to see the filling equipment in action. This will help you assess its quality, performance, and ease of use. Additionally, ask for references from other customers who have purchased similar equipment.
6. Evaluate compatibility: Consider the compatibility of the filling equipment with your existing production line and processes. Ensure that it can seamlessly integrate and communicate with other machinery and software systems.
7. Check safety and compliance: Verify that the filling equipment complies with relevant safety standards and regulations. Look for certifications such as CE, UL, or ISO to ensure the equipment meets industry requirements.
8. Support and training: Inquire about the level of technical support and training that the supplier provides. Adequate training will help your staff understand and utilize the equipment effectively, minimizing downtime and maximizing efficiency.
9. Warranty and service agreements: Review the warranty terms offered by the supplier and understand what it covers. Additionally, discuss service agreements and after-sales support options to ensure prompt assistance in case of any issues or breakdowns.
10. Budget and financing: Establish a realistic budget for the purchase of the filling equipment and explore financing options if necessary. Consider leasing or financing arrangements that can help spread out the costs and ease the financial burden.
By following these tips and considerations, you can make a well-informed procurement decision when purchasing filling equipment, ensuring it meets your needs while providing long-term efficiency, reliability, and value for your investment.
FAQs on Sourcing and Manufacturing filling equipment in China
Q: Why should I consider sourcing and manufacturing filling equipment in China?
A: China is known for its manufacturing capabilities and is considered the world’s factory. It offers cost-effective solutions due to lower labor and production costs, allowing for competitive prices for filling equipment. With a vast network of suppliers and manufacturers, China can provide a wide range of filling equipment options to cater to various industries and production needs.
Q: How do I find suitable suppliers and manufacturers for filling equipment in China?
A: There are several ways to find reputable suppliers and manufacturers in China. Online B2B platforms like Alibaba, Made-in-China, and Global Sources have extensive databases of suppliers and manufacturers of filling equipment. Trade shows, industry exhibitions, and networking events in China are another effective way to connect with potential suppliers. Additionally, engaging with sourcing agents or consulting firms that have expertise in the Chinese market can help streamline the supplier selection process.
Q: What are the factors to consider when selecting a supplier or manufacturer for filling equipment in China?
A: Several factors should be considered when selecting a supplier or manufacturer in China, including product quality, production capacity, pricing, lead time, certifications, and after-sales service. It is crucial to conduct thorough due diligence, including requesting samples, visiting the manufacturer’s facilities, and checking references before finalizing a partnership.
Q: Are there any challenges associated with sourcing and manufacturing filling equipment in China?
A: While sourcing and manufacturing in China offer numerous benefits, there can be challenges that need to be addressed. Language and communication barriers can sometimes arise during negotiations and production processes. Intellectual property protection is another concern, so it is crucial to ensure the use of proper contracts and non-disclosure agreements. Logistics and transportation can also pose challenges, requiring careful planning to ensure timely delivery and minimize potential disruptions.
Q: Are there any specific regulations or standards to consider when sourcing filling equipment from China?
A: When sourcing filling equipment from China, it is essential to understand and comply with local regulations and industry standards. Depending on the specific product and destination market, certifications such as CE, FDA, ISO, or UL may be required. Conducting product testing and verification to ensure compliance is recommended.
In conclusion, sourcing and manufacturing filling equipment in China offers cost-effectiveness, a vast supplier network, and a wide range of options. However, it is essential to carefully select suppliers, consider challenges, and comply with regulations to ensure a successful partnership.
Why contact sourcifychina.com get free quota from reliable filling equipment suppliers?
Sourcifychina.com is able to get free quota from reliable filling equipment suppliers for several reasons. Firstly, Sourcifychina.com has built a strong reputation and relationship with these suppliers through years of collaboration. This reputation is built on trust, professionalism, and successful business partnerships.
Secondly, Sourcifychina.com has proven its ability to consistently provide these suppliers with high-quality customers who are serious about purchasing filling equipment. They have a track record of connecting suppliers with genuine buyers, which is valuable to the suppliers as it maximizes their chances of making profitable sales.
Furthermore, Sourcifychina.com has a wide network of potential customers from various industries who are actively seeking reliable filling equipment suppliers. By leveraging this network, Sourcifychina.com can attract large numbers of potential buyers to these suppliers, increasing their exposure and sales opportunities.
Lastly, the free quota offered by reliable filling equipment suppliers to Sourcifychina.com can be viewed as an investment. By providing a certain number of quota, the suppliers are able to showcase their products and services to a targeted audience of potential buyers. This can lead to long-term business relationships and increased sales in the future.
In summary, Sourcifychina.com receives free quota from reliable filling equipment suppliers due to their strong reputation, ability to connect suppliers with genuine buyers, wide network of potential customers, and the potential for long-term business partnerships.