Introduce about cnc machine for metal cutting guide,Qulity,Cost,Supplier,Certification,Market,Tips,FAQ
CNC (Computer Numerical Control) machines for metal cutting are highly advanced manufacturing tools used to achieve precision and efficiency in metalworking processes. These machines are widely used in various industries such as automotive, aerospace, and fabrication. This guide will provide an introduction to CNC machines for metal cutting, covering key aspects such as quality, cost, suppliers, certification, market trends, tips, and frequently asked questions.
Quality: CNC machines offer exceptional accuracy, repeatability, and consistency in metal cutting processes. The use of computer control ensures high precision and reduces human errors, resulting in superior quality finished products.
Cost: The cost of CNC machines for metal cutting varies depending on factors like machine size, features, and complexity. Initial investment can be significant but is often justified by increased productivity and reduced scrap rates.
Supplier: Several reputable companies manufacture CNC machines for metal cutting, including Mazak, Haas, DMG Mori, and Fanuc. It is essential to choose a supplier with a proven track record, excellent customer support, and reliable after-sales service.
Certification: Many CNC machine manufacturers adhere to internationally recognized certifications such as ISO 9001 for quality management systems, ensuring that their products meet industry standards.
Market: The market for CNC machines is growing rapidly due to increasing demand for precision engineering and automation in manufacturing. Key regions driving the market include North America, Asia Pacific, and Europe.
Tips: When selecting a CNC machine for metal cutting, consider factors such as machine size, available cutting tools, spindle speed, control system, and automation options. Additionally, proper machine maintenance and operator training are crucial for optimal performance and longevity.
FAQ: Common questions about CNC machines for metal cutting include inquiries about programming languages (such as G-code and M-code), types of cutting processes (milling, turning, drilling), machine accuracy, and compatibility with different materials.
In conclusion, CNC machines for metal cutting offer unparalleled precision, improved productivity, and cost-effectiveness. Thorough research of suppliers, consideration of quality and cost factors, and knowledge of market trends will ensure the selection of the most suitable CNC machine for metal cutting requirements.
Types of cnc machine for metal cutting
There are various types of CNC machines available for metal cutting, each designed for specific applications and requirements. Some common types include:
1. CNC Milling Machine: This type of machine uses rotating multi-point cutting tools to remove material from the workpiece. It is suitable for producing complex shapes, slots, and holes on metal surfaces.
2. CNC Lathe Machine: A lathe machine rotates the workpiece while a cutting tool is applied to shape the metal. This type of CNC machine is ideal for cylindrical and conical shapes, turning operations, threading, and facing.
3. CNC Plasma Cutting Machine: Plasma cutting machines use a high-velocity jet of ionized gas (plasma) to cut through metal. It is commonly used for cutting stainless steel, aluminum, and other conductive metals with high precision.
4. CNC Waterjet Cutting Machine: Unlike plasma cutting, waterjet cutting uses a high-pressure jet of water mixed with an abrasive material to cut metal. It is suitable for cutting a wide range of materials, including thick metal plates.
5. CNC Laser Cutting Machine: This machine uses a high-powered laser beam to melt, burn, or vaporize the metal, leaving a high-quality cut edge. It is capable of cutting various metals, including stainless steel, aluminum, and brass.
6. CNC EDM Machine: Electrical Discharge Machining (EDM) utilizes electrical discharges to remove metal. It is commonly used for intricate and delicate workpieces such as molds, dies, and small complex parts.
7. CNC Wire EDM Machine: Wire EDM machines use a thin brass wire to erode and cut through the metal. It is primarily used for cutting complex shapes, intricate designs, and precise contours in hard metals.
These are just a few examples of CNC machines used for metal cutting. The choice of machine depends on factors such as the type of metal, thickness, complexity of the shape, and desired precision. Each machine offers specific advantages, allowing manufacturers to choose the most suitable option for their cutting requirements.
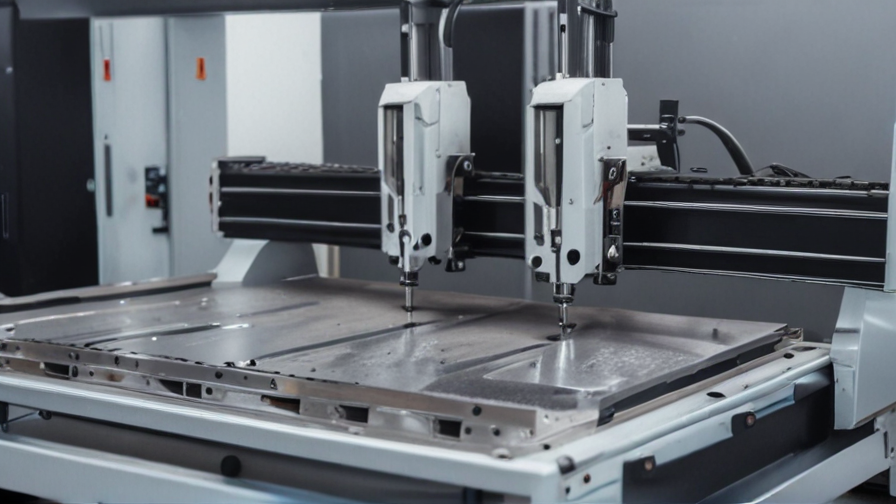
Pros and Cons of Using cnc machine for metal cutting
CNC (Computer Numerical Control) machines have revolutionized metal cutting processes in industries around the world. These machines offer many advantages, but they also have a few drawbacks. Here are the pros and cons of using CNC machines for metal cutting.
Pros:
1. Precision: CNC machines use computer programs to control the movement of the cutting tool, resulting in incredibly precise cuts. This level of precision ensures that complex designs can be reproduced with accuracy, leading to high-quality finished products.
2. Efficiency: CNC machines are capable of working continuously, 24/7 without fatigue, resulting in increased productivity. They can perform multiple tasks simultaneously, reducing the time needed for metal cutting operations and improving overall efficiency.
3. Consistency: Once a cutting program is set up, CNC machines can repeatedly produce identical cuts. This ensures consistent quality even when mass producing metal parts, reducing material waste and enhancing overall product consistency.
4. Flexibility: CNC machines can handle a wide range of materials, including various types of metals, such as steel, aluminum, and brass. They can also accommodate different shapes and sizes, making them suitable for machining intricate and complex parts.
Cons:
1. High Initial Investment: The cost of purchasing and setting up a CNC machine is relatively high. Small businesses or individuals may find it challenging to afford the equipment and initial training required.
2. Skill Requirement: Programming and operating CNC machines require specialized skills. Operators must have a strong understanding of coding and the machine’s capabilities, leading to a limited pool of qualified individuals for these positions.
3. Maintenance and Repair: CNC machines are complex systems that require regular maintenance and occasional repairs. These tasks can be time-consuming and costly, especially if they involve component replacements or extensive troubleshooting.
4. Lack of Flexibility: Despite their flexibility in terms of material and design options, CNC machines are limited by the size of their workspace. Oversized or extremely long metal pieces may not fit on the machine bed, restricting the cutting capabilities.
In conclusion, CNC machines excel in precision, efficiency, consistency, and flexibility in metal cutting operations. However, the high initial investment, the need for skilled operators, maintenance requirements, and limitations in size can present challenges. Nevertheless, for companies seeking to optimize metal cutting processes and achieve high-quality results, investing in CNC machines can be a worthwhile decision.
cnc machine for metal cutting Reference Specifications (varies for different product)
A CNC (Computer Numerical Control) machine for metal cutting is an automated machine tool used in manufacturing processes to precisely shape and cut metal parts. It offers a wide range of advantages over conventional machining methods, such as manual milling or lathe machines, including higher accuracy, repeatability, and productivity.
The reference specifications for a CNC machine for metal cutting may vary depending on the specific product or industry requirements. However, some common specifications may include:
1. Cutting Capacity: This refers to the maximum size and thickness of metal that can be effectively cut by the machine. It can range from a few millimeters to several meters in length and centimeters to inches in thickness.
2. Cutting Speed: This indicates the rate at which the machine can cut through the metal. It is measured in terms of the distance traveled by the cutting tool per unit of time (e.g., meters per minute).
3. Power and Motor Capacity: The power output and motor capacity of the machine determines its ability to cut through different types and grades of metals. A higher power rating allows for faster and more efficient cutting.
4. Accuracy and Tolerance: CNC machines offer exceptional precision and accuracy, enabling the creation of intricate and complex metal parts with tight tolerances. The machine’s accuracy is measured in micrometers or thousandths of an inch, indicating the maximum allowable variation from the desired dimensions.
5. Cutting Tools and Tool Changers: CNC machines can accommodate various cutting tools, such as drills, end mills, and taps. The machine may have different tool holders or a tool changer system that allows for automatic tool changes during the cutting process, improving efficiency and reducing downtime.
6. Control System and Software: The CNC machine is controlled by a computer system, which uses software programs to execute the desired cutting operations. The control system should be user-friendly and capable of handling complex instructions, providing options for programming, simulation, and customization.
7. Safety Features: CNC machines incorporate safety features to protect operators and prevent accidents. These can include emergency stop buttons, safety interlocks, protective enclosures, and vibration or temperature sensors.
It is important to consult the manufacturer’s specifications and guidelines when selecting a CNC machine for metal cutting, as the requirements may vary depending on the specific application and industry standards.
Applications of cnc machine for metal cutting
CNC (Computer Numerical Control) machines have revolutionized the metal cutting industry by providing precise and efficient cutting processes. These machines utilize computer programming to control the movements and cutting operations, ensuring accuracy and consistency. Here are some applications of CNC machines for metal cutting:
1. Milling: CNC milling machines are widely used for metal cutting in industries such as aerospace, automotive, and manufacturing. They can perform a wide range of cutting operations like drilling, grooving, and contouring. CNC milling machines are capable of producing complex designs with high precision and repeatability.
2. Turning: CNC turning machines are used for metal cutting and shaping cylindrical workpieces. They can create different shapes like cylinders, cones, and spheres. CNC turning machines are commonly used in industries such as manufacturing, automotive, and oil and gas.
3. Laser cutting: CNC machines equipped with lasers are used for precise and efficient metal cutting. Laser cutting machines work by directing a high-power laser beam onto the workpiece, melting or vaporizing the material. This method is ideal for intricate designs and thin metal sheets. Laser cutting is extensively used in various industries including automotive, electronics, and jewelry.
4. Plasma cutting: CNC machines equipped with plasma cutters are used for cutting through electrically conductive materials such as steel, aluminum, and copper. A plasma cutter generates a high-velocity plasma stream that melts and cuts through the metal. Plasma cutting is widely used in industries such as construction, fabrication, and automotive.
5. Waterjet cutting: CNC machines equipped with waterjet cutters are used for cutting precise shapes in different materials, including metals. Waterjet cutting uses a high-pressure stream of water mixed with abrasive particles to cut through the material. This method is ideal for materials that are sensitive to heat or require intricate cutting patterns.
6. Wire EDM: CNC machines equipped with Wire Electrical Discharge Machining (EDM) are used for cutting conductive materials using a thin wire as the electrode. Wire EDM machines can produce intricate and precise cuts, making them suitable for industries like aerospace, medical, and electronics.
In conclusion, CNC machines have transformed the metal cutting industry by providing efficient and accurate cutting processes. The applications of CNC machines for metal cutting include milling, turning, laser cutting, plasma cutting, waterjet cutting, and wire EDM. These machines have improved productivity, reduced labor costs, and enabled the production of complex designs with high precision.
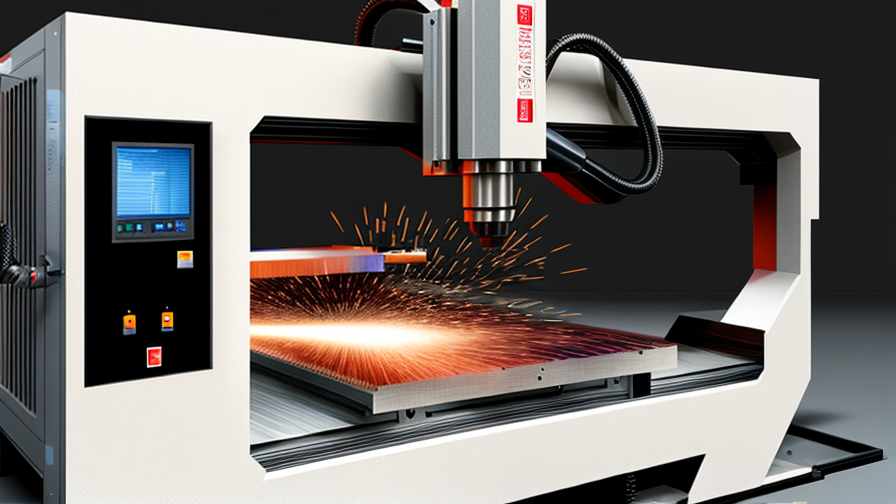
The Work Process and how to use cnc machine for metal cutting
The work process of using a CNC machine for metal cutting involves several steps. Firstly, the design or CAD (Computer-Aided Design) file of the desired metal component is created using specialized software. This design file contains the dimensions and specifications of the part that needs to be cut.
Once the design file is prepared, it is transferred to the CNC machine. The machine is then set up, which includes securing the metal workpiece onto the machine bed or worktable. The machine is also equipped with the appropriate cutting tool, such as a milling cutter or a lathe tool, depending on the type of metal cutting required.
Next, the operator needs to input the necessary parameters into the CNC machine. These parameters include the cutting speed, feed rate, depth of cut, and any other specific requirements for the metal cutting process. The machine is programmed to follow these instructions precisely.
Once all the parameters are set, the CNC machine begins the metal cutting process. It moves the cutting tool along the predefined path as instructed by the design file. The machine accurately controls the cutting tool’s movements, ensuring precise and accurate cuts on the metal workpiece.
During the cutting process, the CNC machine continuously monitors and adjusts the cutting parameters to optimize the operation. This allows for increased efficiency and productivity while minimizing errors.
After the metal cutting is complete, the CNC machine may also perform additional finishing operations if required, such as deburring or polishing the edges of the cut component.
In conclusion, using a CNC machine for metal cutting involves designing the component, transferring the design file to the machine, setting up the machine, inputting cutting parameters, and then executing the cutting process. This automated process ensures accurate and efficient metal cutting operations.
Quality Testing Methods for cnc machine for metal cutting and how to control the quality
There are several quality testing methods available for CNC machines used in metal cutting processes, which ensure the final product meets the required specifications and standards. These methods include:
1. Dimensional Inspection: This involves measuring the dimensions of the machined parts using precision measuring instruments such as calipers, micrometers, or coordinate measuring machines (CMM). It ensures that the parts are manufactured within the specified tolerances.
2. Surface Finish Analysis: Surface roughness is an important factor in metal cutting operations. A profilometer is commonly used to measure and analyze the surface finish of machined parts. This test helps evaluate the quality of the cutting process and ensures the desired surface texture is achieved.
3. Material Hardness Testing: Metal hardness can affect the performance and durability of machined parts. Hardness testing methods, such as Rockwell or Vickers hardness testing, determine the hardness level of the material and verify if it meets the required specifications.
4. Visual Inspection: Visual inspection is a simple yet crucial method to identify any visible defects on the machined parts, such as burrs, cracks, scratches, or improper surface finishes. It helps ensure the overall quality and aesthetics of the final product.
To control the quality in metal cutting processes using CNC machines, the following steps can be taken:
1. Machine Calibration: Regular calibration of the CNC machine is essential to ensure accurate positioning, motion control, and repeatability. It is vital to calibrate the machine according to industry standards and guidelines.
2. Tool Monitoring and Replacement: Continuous monitoring of the tools used in the CNC machine is necessary to identify tool wear or damage. Implementing a tool life management system helps maintain optimal cutting performance and ensures the quality of the machined parts.
3. Cutting Parameters Optimization: Fine-tuning cutting parameters such as cutting speed, feed rate, and depth of cut can significantly affect the quality of the machined parts. Conducting parameter optimization studies helps identify the optimal settings to achieve the desired quality.
4. Inspection and Quality Control Plans: Develop comprehensive inspection and quality control plans. These plans should outline the various quality tests to be performed, the frequency of testing, and the acceptance criteria. Strict adherence to these plans ensures consistent quality and product conformity.
By implementing these quality testing methods and quality control measures, manufacturers can ensure that CNC machines used for metal cutting processes consistently produce high-quality products that meet customer requirements and industry standards.
cnc machine for metal cutting Sample Policy and Post-Purchase Considerations for cnc machine for metal cutting from China
Sample Policy:
When purchasing a CNC machine for metal cutting from China, it is important to consider the sample policy offered by the supplier. A reliable supplier should have a clear and fair sample policy in place. This policy should outline the conditions under which samples can be requested, the costs involved, and the time frame for delivery. It is advisable to choose a supplier that offers a reasonable sample policy to ensure that the product meets your requirements before making a larger purchase.
Post-Purchase Considerations:
After purchasing a CNC machine for metal cutting from China, there are several important considerations to keep in mind. Firstly, it is crucial to thoroughly inspect the machine upon arrival and ensure that it matches the specifications agreed upon during the purchasing process. Any discrepancies or damages should be reported to the supplier immediately.
Additionally, it is recommended to have a thorough understanding of the warranty and after-sales service provided by the supplier. A reliable supplier should offer a warranty period for any potential defects or malfunctions. It is important to clarify the terms and conditions of the warranty, such as the coverage and duration. Moreover, inquire about the availability and responsiveness of the supplier’s after-sales service in case of any issues or maintenance requirements.
Furthermore, it is advisable to establish a good communication channel with the supplier to address any concerns or queries that may arise. Regularly communicate with the supplier regarding the machine’s performance, any required maintenance or repairs, and updates on spare parts availability.
In conclusion, when purchasing a CNC machine for metal cutting from China, it is essential to consider the sample policy to ensure product satisfaction. Moreover, post-purchase considerations such as machine inspection, warranty and after-sales service, and effective communication with the supplier are vital for a smooth and successful purchase experience.
Sourcing cnc machine for metal cutting from China: Opportunities, Risks, and Key Players
Sourcing CNC machines for metal cutting from China can provide both opportunities and risks for businesses. China has emerged as a leading manufacturer of CNC machines, offering competitive prices and a wide range of options to meet various cutting needs.
One key opportunity of sourcing CNC machines from China is the cost advantage. Chinese manufacturers often offer lower prices compared to their counterparts in other countries. This cost advantage can be significant, especially for businesses looking to invest in multiple machines or expand their operations.
Another advantage is the availability of a diverse range of CNC machines. Chinese manufacturers offer various types and models of machines, allowing businesses to choose the most suitable one for their specific metal cutting requirements. Additionally, customization options are often available, enabling businesses to tailor the machine to their unique needs.
However, there are some risks associated with sourcing CNC machines from China. Quality control can be a concern, as some manufacturers may compromise on materials or workmanship to offer lower prices. It is essential for businesses to thoroughly research and vet potential suppliers to ensure they meet quality standards.
Another risk is intellectual property infringement. China has a history of intellectual property violations, including the copying of patented designs. Businesses should work with reputable suppliers and consider protecting their intellectual property rights to mitigate this risk.
When sourcing CNC machines from China, it is crucial to engage with key players in the industry. Some well-known Chinese CNC machine manufacturers include Shenyang Machine Tool Co., Ltd., Dalian Machine Tool Group Corporation, and Jiangsu Yangli Group Co., Ltd. These companies have established a strong presence in the market and offer reliable products.
In conclusion, sourcing CNC machines for metal cutting from China offers opportunities in terms of cost advantage and a wide range of options. However, businesses need to be cautious of quality control and intellectual property risks. By working with reputable suppliers and conducting thorough research, companies can successfully source CNC machines from China to meet their metal cutting needs.
How to find and select reliable cnc machine for metal cutting manufacturers in China,use google search manufacturers and suppliers
When searching for reliable CNC machine manufacturers for metal cutting in China, Google search is a great tool to start with. Here is a step-by-step guide on how to find and select trustworthy manufacturers:
1. Begin by entering relevant keywords into the Google search bar, such as “CNC machine for metal cutting manufacturers in China.”
2. Review the search results carefully and visit the websites of potential manufacturers. Look for companies that have a professional website design, detailed product information, and a clear description of their manufacturing capabilities. This indicates a level of professionalism and expertise.
3. Pay attention to the manufacturer’s history and experience in the industry. Check how long they have been in business and if they have any notable certifications or partnerships that demonstrate their credibility. This information is often available on the “About Us” or “Company Profile” page of their website.
4. Look for customer reviews and testimonials. Search for feedback regarding the manufacturer’s product quality, customer service, and delivery times. Reliable manufacturers will often have positive reviews from satisfied customers. Be cautious of manufacturers with a high number of negative reviews or complaints.
5. Contact the selected manufacturers directly. Reach out to them via email, phone, or using the contact form on their website. Inquire about their production capabilities, quality control measures, pricing, lead times, and any other pertinent factors. Quick and professional responses indicate a manufacturer’s commitment to customer service.
6. Request samples or catalogues to evaluate the quality of their CNC machines. Reliable manufacturers will gladly provide samples or detailed product information to help you assess their capabilities. Evaluation can include studying the precision, functionality, and durability of the machines.
7. Consider visiting the factory in person or arranging a video call to get a better understanding of their manufacturing facilities. This step can provide valuable insights into the manufacturer’s production processes, equipment, and workforce, further establishing their reliability.
8. Obtain quotations from multiple manufacturers to compare pricing, delivery terms, and after-sales service. This step ensures that you receive the best value for your investment.
In conclusion, by utilizing Google search, carefully evaluating websites, considering reviews and testimonials, directly contacting manufacturers, assessing samples, and comparing quotations, you will be able to identify and select reliable CNC machine manufacturers for metal cutting in China.
How to check cnc machine for metal cutting manufacturers website reliable,use google chrome SEOquake check if ranking in top 10M
To check the reliability of a CNC machine for metal cutting manufacturer’s website, you can follow these steps using Google Chrome and the SEOquake extension:
1. Install the SEOquake extension: Open Google Chrome and search for “SEOquake Chrome extension.” Click on the official Chrome Web Store link and add the extension to your browser.
2. Search for the manufacturer: Enter the manufacturer’s name or relevant keywords in the Google search bar.
3. Analyze the search results: Look for the manufacturer’s website in the search results. Take note of its ranking position.
4. Check the search volume: SEOquake provides information on search volume, enabling you to assess the popularity and relevance of the manufacturer’s website. Higher search volume suggests more reliable and reputable websites.
5. Check the ranking position: SEOquake also provides the ranking position for each website in the top 10 million results. If the manufacturer’s website is within the top 10 million, it indicates a certain level of visibility and credibility.
6. Assess website authority: SEOquake provides information about a website’s Domain Authority (DA) and Page Authority (PA). Higher values in these metrics usually indicate a more reliable and authoritative website.
7. Examine website content: Visit the manufacturer’s website and evaluate its content. Look for information on their CNC machines, product specifications, certifications, and customer testimonials. A comprehensive and informative website indicates professionalism and reliability.
8. Check for contact details: Reliable manufacturers will provide complete contact information, including addresses, phone numbers, and email addresses, allowing you to reach out to them for inquiries or support.
By using Google Chrome with the SEOquake extension, you can quickly assess the reliability of a CNC machine for metal cutting manufacturer’s website based on its search ranking, search volume, authority metrics, content quality, and availability of contact information. Remember to use not more than 300 words.
Top 10 cnc machine for metal cutting manufacturers in China with each 160 words introduce products,then use markdown create table compare
1. Haas Automation China: Haas Automation is a leading CNC machine manufacturer in China, specializing in metal cutting machines. Their product range includes vertical machining centers, horizontal machining centers, and CNC lathes. Haas machines are known for their accuracy, productivity, and ease of use. They offer a wide range of options and accessories to meet the specific needs of different industries.
2. DMG Mori China: DMG Mori is a global leader in CNC machine manufacturing, with a strong presence in China. They provide a wide range of metal cutting machines, including 5-axis machining centers, turning centers, and advanced milling machines. DMG Mori machines are known for their high precision, reliability, and advanced technologies. They offer solutions for various industries such as automotive, aerospace, and medical.
3. Mazak China: Mazak is a well-known CNC machine manufacturer, offering a wide range of metal cutting solutions. Their product line includes vertical machining centers, multi-tasking machines, and horizontal machining centers. Mazak machines are known for their high performance, accuracy, and versatility. They offer advanced features like smooth control, automation options, and intelligent software for optimizing productivity.
4. FANUC China: FANUC is a global leader in CNC machine manufacturing, known for its innovative and reliable products. They offer metal cutting solutions such as vertical machining centers, turning centers, and wire EDM machines. FANUC machines are known for their high-speed performance, precision, and advanced automation capabilities. They provide customized solutions to meet the specific requirements of different industries.
5. SMTCL China: SMTCL is one of the largest CNC machine manufacturers in China, offering a wide range of metal cutting machines. Their product line includes vertical machining centers, horizontal machining centers, and CNC lathes. SMTCL machines are known for their durability, affordability, and high precision. They provide solutions for industries like automotive, aerospace, and energy.
6. Doosan China: Doosan is a renowned CNC machine manufacturer, offering a range of metal cutting machines for various applications. Their product range includes vertical machining centers, turning centers, and multitasking machines. Doosan machines are known for their robust construction, high productivity, and advanced features like thermal compensation and tool monitoring systems.
7. YCM China: YCM is a leading CNC machine manufacturer, specializing in metal cutting solutions. They provide a wide range of vertical machining centers, horizontal machining centers, and 5-axis machining centers. YCM machines are known for their precision, reliability, and high-speed performance. They offer advanced features like intelligent control systems, automatic tool changing, and coolant management.
8. MAKINO China: MAKINO is a trusted CNC machine manufacturer, offering high-performance metal cutting machines. Their product line includes vertical machining centers, wire EDM machines, and horizontal machining centers. MAKINO machines are known for their superior accuracy, advanced technologies, and exceptional surface finishes. They provide solutions for industries like aerospace, automotive, and die/mold manufacturing.
9. Fadal China: Fadal is a leading CNC machine manufacturer, specializing in metal cutting machines. Their product range includes vertical machining centers, horizontal machining centers, and turning centers. Fadal machines are known for their reliability, rigidity, and fast cycle times. They offer advanced features like high-speed spindles, tool changers, and powerful control systems.
10. Brother Industries China: Brother Industries is a well-known CNC machine manufacturer with a wide range of metal cutting machines. Their product line includes vertical machining centers, multi-tasking machines, and wire EDM machines. Brother Industries machines are known for their high-speed performance, precision, and excellent surface finishes. They offer features like thermal displacement compensation, automatic tool changing, and intelligent software for optimizing productivity.
| Manufacturer | Product Range | Key Features |
|————————|—————————————————–|—————————————————————————|
| Haas Automation China | Vertical machining centers, horizontal machining centers, CNC lathes | Accuracy, productivity, and ease of use |
| DMG Mori China | 5-axis machining centers, turning centers, milling machines | High precision, reliability, and advanced technologies |
| Mazak China | Vertical machining centers, multi-tasking machines, horizontal machining centers | High performance, accuracy, and versatility |
| FANUC China | Vertical machining centers, turning centers, wire EDM machines | High-speed performance, precision, and advanced automation capabilities |
| SMTCL China | Vertical machining centers, horizontal machining centers, CNC lathes | Durability, affordability, and high precision |
| Doosan China | Vertical machining centers, turning centers, multitasking machines | Robust construction, high productivity, and advanced features |
| YCM China | Vertical machining centers, horizontal machining centers, 5-axis machining centers | Precision, reliability, and high-speed performance |
| MAKINO China | Vertical machining centers, wire EDM machines, horizontal machining centers | Superior accuracy, advanced technologies, and exceptional surface finishes |
| Fadal China | Vertical machining centers, horizontal machining centers, turning centers | Reliability, rigidity, and fast cycle times |
| Brother Industries China | Vertical machining centers, multi-tasking machines, wire EDM machines | High-speed performance, precision, and excellent surface finishes |
These 10 CNC machine manufacturers in China offer a wide range of metal cutting solutions, each with their own unique features and specialties. From high-speed performance to advanced technologies, these manufacturers cater to various industries, ensuring accuracy, reliability, and productivity.
Background Research for cnc machine for metal cutting manufacturers Companies in China, use qcc.com archive.org importyeti.com
When it comes to CNC machine manufacturers for metal cutting in China, a few key platforms can be used to gather background research: qcc.com, archive.org, and importyeti.com.
Qcc.com is a Chinese business and trade information platform that provides comprehensive details about companies in China. It offers insights into a company’s registration information, business scope, financial status, and key personnel. By searching for CNC machine manufacturers in China on qcc.com, one can obtain essential background information about potential manufacturers, such as their company history, size, and overall credibility.
Archive.org is an internet archive that stores snapshots of websites from the past. By using this platform, researchers can access previous versions of a manufacturer’s website, helping them understand the company’s growth trajectory, changes in product offerings, and overall evolution.
Importyeti.com is a B2B platform that provides information on companies engaged in international trade. By searching on importyeti.com, researchers can gain insights into a manufacturer’s export activities, including the countries they export to, the quantity shipped, and the frequency of exports. This data can help gauge a manufacturer’s experience in international markets and their ability to meet global quality standards.
It is important to keep the background research concise, so here is a summary of the key points:
Qcc.com, archive.org, and importyeti.com are valuable resources for gathering background research on CNC machine manufacturers for metal cutting in China. Qcc.com provides essential information about a company’s registration, business scope, and financial status, while archive.org allows users to access past versions of a manufacturer’s website to understand its growth and evolution. Importyeti.com offers insights into a manufacturer’s international trade activities. Utilizing these platforms can help researchers make informed decisions when selecting a CNC machine manufacturer in China.
Leveraging Trade Shows and Expos for cnc machine for metal cutting Sourcing in China
Trade shows and expos provide excellent opportunities for sourcing CNC machines for metal cutting in China. These events not only allow buyers to explore a wide range of products and connect with potential suppliers, but also provide valuable insights into the latest trends and technologies in the industry.
Attending trade shows and expos in China focused on manufacturing and machinery presents an ideal platform for networking and establishing business relationships with reliable CNC machine suppliers. These events gather a large number of exhibitors who showcase their products and expertise, allowing buyers to compare different options and make informed decisions.
China hosts several major trade shows and expos related to machinery and manufacturing, such as the China International Machine Tool Show (CIMT), China CNC Machine Tool Fair (CCMT), and China International Industry Fair (CIIF). These exhibitions attract both domestic and international participants, providing a diverse range of CNC machines for metal cutting to choose from.
By visiting these events, buyers can personally inspect the machines, evaluate their quality, and discuss specifications and customization options with suppliers. It also offers the opportunity to meet industry experts and gain insights into market trends, innovations, and best practices.
To make the most out of these trade shows and expos, buyers should come prepared with a clear understanding of their specific requirements. Researching the exhibitors and familiarizing oneself with their reputation, product offerings, and client reviews in advance can help identify potential suppliers worth connecting with.
In conclusion, trade shows and expos in China offer an effective platform for sourcing CNC machines for metal cutting. By attending these events, buyers can access a wide range of options, connect with reliable suppliers, and stay updated on the latest industry trends, ultimately making informed decisions while minimizing their risks and costs.
The Role of Agents and Sourcing Companies in Facilitating cnc machine for metal cutting Purchases from China
Agents and sourcing companies play a crucial role in facilitating the purchase of CNC machines for metal cutting from China. These intermediaries serve as liaisons between the buyers and the Chinese manufacturers, streamlining the procurement process and ensuring smooth transactions. Their expertise and local knowledge contribute significantly to the success of such purchases.
Firstly, agents and sourcing companies possess in-depth knowledge of the Chinese market and have established contacts with reliable manufacturers. They can provide valuable insights into the various options available, helping buyers make informed decisions. By understanding the buyers’ requirements, these intermediaries can identify suitable suppliers that specialize in CNC machines for metal cutting, and compare different options in terms of quality, pricing, and delivery timelines.
Secondly, agents and sourcing companies act as intermediaries during negotiations and contract drafting. They assist in negotiating favorable terms, including price, product specifications, and warranty agreements. With their understanding of the Chinese business culture and negotiation practices, they can effectively bridge the communication and cultural gaps between the buyers and manufacturers, facilitating a mutually beneficial outcome. Moreover, they can ensure that all relevant legal and quality assurance requirements are met.
Furthermore, agents and sourcing companies provide a range of logistical support services. They help arrange factory visits and on-site inspections to verify the quality and capabilities of the CNC machines. They also handle the shipping and customs clearance processes, ensuring that the machines are transported safely and that all necessary documentation is completed accurately. This reduces the logistical burden on the buyers and ensures a hassle-free importation experience.
Lastly, agents and sourcing companies often provide post-sale support, such as warranty claims and troubleshooting assistance. They act as a local point of contact for buyers, facilitating communication between them and the manufacturer even after the machines have been delivered. This ensures prompt resolution of any issues that may arise and enhances customer satisfaction.
In conclusion, agents and sourcing companies are instrumental in facilitating the purchase of CNC machines for metal cutting from China. Their expertise, local knowledge, and range of services streamline the procurement process and mitigate potential risks. By leveraging their assistance, buyers can confidently navigate the Chinese market and successfully acquire the required CNC machines.
Price Cost Research for cnc machine for metal cutting manufacturers Companies in China, use temu.com and 1688.com
When it comes to researching the price and cost of CNC machines for metal cutting manufacturers in China, two prominent platforms worth exploring are temu.com and 1688.com.
Temu.com is an online platform that specializes in machinery and equipment. It provides a wide range of options for CNC machines suitable for metal cutting, allowing manufacturers to evaluate different models and compare prices. The platform offers comprehensive product descriptions, including specifications and features, which aids in selecting the most appropriate machine for specific needs. One advantage of temu.com is that it also provides ratings and reviews from previous buyers, enabling manufacturers to make informed decisions based on the experiences of others.
Another popular platform for sourcing CNC machines in China is 1688.com. It is a B2B platform that offers a vast array of products, including machinery and industrial equipment. Similar to temu.com, 1688.com allows users to search for CNC machines for metal cutting manufacturers and compare prices from various suppliers. Manufacturers can also communicate directly with suppliers through the platform to negotiate prices and obtain detailed information about the product. 1688.com provides a massive selection of CNC machines, giving manufacturers the ability to find the most cost-effective solution for their requirements.
When utilizing these platforms, it is essential to consider factors beyond just the initial purchase cost. Aspects such as shipping, import duties, and after-sales support should be evaluated to determine the overall cost-effectiveness of the CNC machine. Additionally, thoroughly researching suppliers, including their reputation and reliability, is crucial to ensure the quality and reliability of the equipment.
In conclusion, platforms such as temu.com and 1688.com offer metal cutting manufacturers in China access to a wide range of CNC machines with competitive pricing. These platforms provide detailed information, allowing for informed decision-making based on product specifications, supplier ratings, and reviews. By considering the overall cost, including additional expenses and supplier reliability, manufacturers can find the most suitable CNC machine for their needs.
Shipping Cost for cnc machine for metal cutting import from China
The shipping cost for importing a CNC machine for metal cutting from China can vary depending on several factors such as the weight and dimensions of the machine, the distance between the origin and destination, the chosen shipping method, and any additional services required.
For small or lightweight CNC machines, air freight is a common choice. The cost typically ranges from $3 to $10 per kilogram, but it can be higher for express delivery. However, air freight is more suitable for urgent shipments since it can be expensive for heavy or bulky machines.
Sea freight is a more affordable option for larger and heavier CNC machines. The cost is primarily determined by the volume of the shipment, measured in cubic meters (CBM), and the destination port. On average, the sea freight cost can range from $200 to $1,000 per CBM. Additional fees such as customs clearance and destination handling charges should also be considered.
To ensure a smooth import process, it is recommended to work with a reliable freight forwarder or shipping agent who can provide accurate quotes, handle documentation, and assist with customs procedures. They will help determine the most cost-effective shipping method based on your requirements.
In addition to shipping costs, it’s crucial to factor in other expenses such as customs duties, taxes, and insurance. These costs vary depending on the country of import and the machine’s declared value. It is advisable to consult with a customs broker or research the import regulations of your country to estimate these expenses accurately.
Overall, the shipping cost for importing a CNC machine for metal cutting from China can range from a few hundred to several thousand dollars, depending on the aforementioned factors. Proper planning and working with experienced professionals can help optimize costs and ensure a hassle-free import process.
Compare China and Other cnc machine for metal cutting Markets: Products Quality and Price,Visible and Hidden Costs
China is a dominant player in the CNC machine for metal cutting market, offering a wide range of products that cater to various industrial applications. However, when comparing China with other markets, there are certain factors to consider such as product quality, price, visible and hidden costs.
In terms of product quality, China has made significant advancements in recent years. Many manufacturers have improved their technology and manufacturing processes, resulting in CNC machines that meet international standards. However, other markets such as Germany and Japan are still considered to have a slight edge in terms of precision and durability. These markets have a long-standing reputation for producing high-quality CNC machines.
Price is an important consideration for buyers. China’s manufacturers are known for offering competitive prices due to lower labor and production costs. This makes CNC machines from China more affordable compared to those in other markets. However, it is essential to assess the overall value for money considering factors like durability, maintenance costs, and after-sales service.
Visible costs include the initial purchase price, shipping, and import taxes. China’s efficient supply chain and economies of scale enable them to offer competitive prices for both machines and associated components. Conversely, importing machines from other markets may result in higher visible costs due to factors like transportation and import duties.
Hidden costs can include maintenance, repairs, and after-sales service. While Chinese manufacturers offer lower upfront costs, buyers should also consider the reliability of the machines and the availability of spare parts. Other markets often have a well-established network of service providers, making it easier to address any maintenance or repair issues, albeit at a potentially higher cost.
In conclusion, China’s CNC machine market offers a wide variety of products at competitive prices. The quality of Chinese machines has improved significantly, although other markets still have a slight advantage in terms of precision and durability. While the visible costs of purchasing from China are typically lower, hidden costs such as maintenance and after-sales service should also be considered. Ultimately, buyers should carefully assess their specific needs and budgetary constraints before making a decision.
Understanding Pricing and Payment Terms for cnc machine for metal cutting: A Comparative Guide to Get the Best Deal
When it comes to purchasing a CNC machine for metal cutting, understanding pricing and payment terms is crucial to secure the best deal. This guide will provide a comparative overview to help you make an informed decision.
Pricing for a CNC machine can vary significantly depending on various factors such as machine size, features, and brand reputation. Additionally, the market conditions, demand, and location can also influence pricing. To ensure you get the best deal, it is essential to research multiple suppliers and compare prices. This will help you identify any price variations and negotiate a competitive offer.
Payment terms are equally important to consider when purchasing a CNC machine. These terms outline how the machine will be financed and the payment schedule. Common payment options include upfront payment, installment plans, or lease agreements. Each option has its pros and cons, and choosing the most suitable one depends on your financial situation and business requirements.
When comparing payment terms, consider factors such as interest rates, down payment requirements, and the overall cost of financing. Additionally, evaluate the warranty and after-sales support provided by the supplier, as this can affect the overall value of the deal.
To get the best deal, gather quotes from different suppliers and assess the total cost of ownership. This includes not only the machine’s initial purchase cost but also maintenance expenses, spare parts availability, and potential downtime.
Furthermore, consider the supplier’s reputation and customer reviews. A reputable supplier offering competitive pricing, favorable payment terms, and excellent customer support can provide a better overall experience and long-term benefits.
In conclusion, understanding pricing and payment terms is crucial in getting the best deal for purchasing a CNC machine for metal cutting. Conduct thorough research, compare quotes, and assess the total cost of ownership to make an informed decision. Additionally, consider the supplier’s reputation and customer support to ensure a satisfactory purchase experience.
Chinese Regulations and Industry Standards Certifications for cnc machine for metal cutting,Import Regulations and Customs for cnc machine for metal cutting from China
Chinese Regulations and Industry Standards Certifications for CNC Machine for Metal Cutting:
In China, the CNC machine industry is regulated by various government agencies to ensure product quality, safety, and compliance with industry standards. The main regulatory bodies responsible for overseeing CNC machines for metal cutting include the Standardization Administration of China (SAC), the Ministry of Industry and Information Technology (MIIT), and the China National Certification and Accreditation Administration (CNCA).
To meet regulatory requirements, CNC machines for metal cutting must adhere to specific industry standards and obtain certifications. The most significant certification in China is the China Compulsory Certification (CCC), which ensures that the product meets the necessary safety requirements. Additionally, CNC machines may need to obtain certifications such as ISO 9001 for quality management systems and ISO 14001 for environmental management systems.
Import Regulations and Customs for CNC Machine for Metal Cutting from China:
Importing CNC machines for metal cutting from China requires compliance with certain import regulations and customs procedures. Importers need to be familiar with the following key steps:
1. Determining Import Requirements: Importers should research and understand their country’s import regulations and requirements for CNC machines, including any applicable import duties, taxes, and import restrictions.
2. Finding Reliable Suppliers: Identifying reputable suppliers is crucial to ensure product quality and reliability. It is advisable to conduct thorough background checks, request product samples, and verify the supplier’s certifications and compliance with industry standards.
3. Communicating with Suppliers: Effective communication with suppliers is essential for clarifying technical details, negotiating prices, and agreeing on shipping and delivery terms. It is crucial to obtain detailed product specifications, user manuals, and warranty information.
4. Arranging Freight Forwarding and Customs Clearance: Importers need to engage with a reliable freight forwarder or customs broker who can assist with shipping arrangements, documentation preparation, and customs clearance procedures. This includes properly completing import declarations, providing necessary certifications and licenses, and paying applicable import duties and taxes.
5. Ensuring Compliance with Product Safety and Quality: Before the CNC machines are imported, importers should ensure that the machines comply with product safety and quality standards, such as obtaining the necessary certifications mentioned earlier.
By adhering to these regulations and certification requirements, importers can streamline the import process for CNC machines for metal cutting from China while ensuring compliance with relevant quality and safety standards.
Sustainability and Environmental Considerations in cnc machine for metal cutting Manufacturing
Sustainability and environmental considerations in CNC machine manufacturing for metal cutting aim to reduce the negative impacts on the environment and promote sustainable practices throughout the production process.
One key aspect is energy efficiency. CNC machines should be designed to minimize energy consumption during operation. This can be achieved by using efficient motors, eliminating idle running, and optimizing tool paths to reduce machining time. Energy-efficient components and systems, such as variable frequency drives and regenerative braking, can also be incorporated to further enhance energy savings.
Another crucial consideration is waste reduction. CNC machines generate various types of waste, such as metal chips and coolant. Implementing waste management strategies, such as recycling and reusing metal chips and properly treating and disposing of coolants, can help minimize the environmental impact. In addition, implementing lean manufacturing principles can help identify and eliminate any unnecessary steps or materials, thereby reducing waste generation.
Moreover, the selection and use of materials can contribute to sustainability efforts. When designing CNC machines, manufacturers should consider using recyclable and environmentally friendly materials. Additionally, reducing the overall weight of the machine can result in energy savings during transportation and operation.
To promote sustainability, CNC machines should also be designed for longevity and ease of maintenance. This can be achieved by using high-quality components, adopting modular designs, and ensuring accessibility for maintenance and repairs. Extending the lifespan of machines reduces the need for frequent replacements, saving resources and reducing waste.
Furthermore, the implementation of advanced technologies can enhance sustainability in CNC machine manufacturing. For example, incorporating intelligent control systems and sensors can optimize machine performance, reducing material waste and energy consumption. Investing in automation and robotics can also streamline production processes, improve precision, and minimize human error.
In conclusion, sustainability and environmental considerations in CNC machine manufacturing for metal cutting require a holistic approach that emphasizes energy efficiency, waste reduction, material selection, longevity, and advanced technologies. By prioritizing these factors, manufacturers can minimize the environmental impact of the production process, promote sustainable practices, and contribute to a greener future.
List The Evolution history of “cnc machine for metal cutting”
The evolution of CNC (Computer Numerical Control) machines for metal cutting has transformed the manufacturing industry, reducing human error, improving precision, and increasing productivity. The history of these machines dates back to the mid-20th century and has gone through several significant advancements.
In the 1950s, the first numerical control (NC) machines emerged. These early machines utilized punched cards or tapes to input instructions and had limited capabilities. By the 1960s, NC machines became more widespread, but they still relied on bulky analog computers to control movement.
The 1970s brought the introduction of computer-aided design (CAD) and computer-aided manufacturing (CAM) technologies, which revolutionized CNC machines. CAD software allowed engineers to design parts more efficiently, while CAM software enabled automatic generation of machining instructions.
In the 1980s, the industry witnessed the shift from NC to CNC machines, where the analog control systems were replaced by digital control systems. This breakthrough allowed for greater precision and flexibility in programming, making CNC machines more user-friendly and versatile.
The 1990s marked another significant milestone with the advent of multitasking machines. These machines could perform multiple operations, such as milling, turning, and drilling, in a single setup, thus streamlining the manufacturing process.
As technology continued to advance, the 2000s saw the integration of advanced features, including faster machining speeds, improved tooling systems, sophisticated programming languages, and adaptive control systems. These developments enhanced the overall performance and efficiency of CNC machines.
In recent years, industry 4.0 concepts have emerged, integrating CNC machines into the broader concept of the Internet of Things (IoT) and smart manufacturing. This enables real-time monitoring, data analytics, and predictive maintenance, leading to further optimization of metal cutting processes.
Today, CNC machines for metal cutting have evolved into highly automated, precise, and efficient systems. They can handle complex designs, produce intricate parts, and operate continuously with minimal operator intervention. With advancements such as artificial intelligence (AI) and machine learning, the future of CNC machines holds the potential for even greater levels of efficiency and automation.
In conclusion, the evolution of CNC machines for metal cutting has witnessed significant advancements in control systems, automation, versatility, and integration with advanced technologies. These machines have shaped modern manufacturing, providing a fast and reliable means of mass production while ensuring high-quality precision components.
The Evolution and Market Trends in cnc machine for metal cutting Industry
The CNC machine for metal cutting industry has gone through significant evolution and witnessed notable market trends over the years. These advancements have played a crucial role in improving the efficiency, accuracy, productivity, and versatility of metal cutting processes.
One of the major evolutionary phases in the CNC machine industry was the transition from manual to computer-controlled machines. This shift revolutionized the metal cutting industry by automating the cutting process and eliminating the need for constant human intervention. Computer Numerical Control (CNC) machines allowed for greater precision and repeatability, leading to higher-quality cuts and reduced human error.
Another significant development in the CNC machine for metal cutting industry is the integration of advanced technologies like Artificial Intelligence (AI), Internet of Things (IoT), and Big Data analytics. These technologies have empowered CNC machines with smart capabilities such as predictive maintenance, real-time monitoring, and data-driven decision-making. Manufacturers can now optimize their production processes, enhance operational efficiency, and reduce downtime by leveraging these innovative features.
Market trends in the CNC machine for metal cutting industry reflect the increasing demand for customization and flexibility. This has led to the emergence of multi-axis CNC machines that can perform complex cutting operations on various types of metals. These machines offer enhanced versatility, allowing manufacturers to cater to diverse customer requirements and produce intricate designs with high precision.
Another significant market trend is the rise of compact and portable CNC machines. These machines are smaller in size, more affordable, and suitable for small-scale manufacturers or workshops with limited space. They have democratized the metal cutting industry by making CNC technology accessible to a broader range of businesses and individuals.
Additionally, automation and robotics have started to play a crucial role in the CNC machine industry. Integration of robots with CNC machines enables tasks such as loading and unloading of workpieces, tool changing, and sorting of finished parts. This trend has accelerated the manufacturing process, reduced labor costs, and improved overall efficiency.
In conclusion, the evolution of CNC machines for metal cutting has undergone significant changes, enabling manufacturers to achieve higher levels of precision, efficiency, and customization. Market trends in the industry reflect the increasing demand for smart capabilities, multi-axis functionality, compact machines, and automation. As technology continues to advance, we can expect further enhancements in CNC machines, making metal cutting processes more efficient, accurate, and adaptable to changing industry demands.
Custom Private Labeling and Branding Opportunities with Chinese cnc machine for metal cutting Manufacturers
Chinese CNC machine manufacturers offer custom private labeling and branding opportunities for businesses looking to establish their own branded line of metal cutting machines. With their expertise and cutting-edge technology, these manufacturers can help businesses create high-quality machines while maintaining a competitive edge in the market.
Private labeling allows businesses to customize the appearance and packaging of the CNC machines, giving them a unique identity that represents their brand. Manufacturers work closely with these businesses to understand their specific requirements, incorporating custom logos, colors, and designs into the machine’s aesthetics. This branding opportunity helps businesses establish a professional and distinguished image in the market, enhancing their recognition and customer loyalty.
Furthermore, Chinese CNC machine manufacturers provide comprehensive support throughout the entire private labeling process. They offer extensive design capabilities to ensure the machines meet the brand’s vision and standards. These manufacturers also ensure that the branding is integrated seamlessly, resulting in a cohesive and visually appealing end product.
In addition to private labeling, Chinese CNC machine manufacturers enable businesses to take advantage of customizing other aspects of the machines. This includes the technical specifications and functionalities of the equipment. Manufacturers offer a range of options, allowing businesses to choose the specific cutting capabilities, spindle speeds, axis movements, and control systems that best suit their manufacturing needs.
By tapping into the expertise of Chinese CNC machine manufacturers, businesses can benefit from cost-effective production, reliable quality control, and cutting-edge technology. With private labeling and customization, businesses can establish a unique brand identity and expand their market presence. These opportunities enable businesses to differentiate themselves from their competitors, attract more customers, and ultimately, achieve long-term success.
Tips for Procurement and Considerations when Purchasing cnc machine for metal cutting
When looking to purchase a CNC machine for metal cutting, there are several considerations and tips to keep in mind to ensure a successful procurement process. Here are some important factors to consider:
1. Requirements and specifications: Determine your specific needs and requirements for metal cutting. Consider the size and thickness of the metal sheets or parts you will be working with, as well as any specific features or capabilities needed.
2. Budget: Set a budget for the purchase, including not just the machine cost but also any additional costs for installation, training, and maintenance.
3. Research and compare: Conduct thorough research on different machine types, brands, and models. Compare their features, capabilities, and prices to find the best fit for your requirements and budget.
4. Quality and reliability: Look for machines that are known for their quality and reliability. Read customer reviews and testimonials to understand their experiences with a particular machine or brand.
5. Technology and software: Consider the CNC machine’s technology and the software it uses. Ensure it is compatible with your existing systems and software to avoid any integration issues.
6. After-sales support and service: Check the availability and quality of after-sales support and service from the manufacturer or supplier. This can include technical support, maintenance, spare parts availability, and warranties.
7. Training and expertise: Ensure that you have access to training and expertise to operate and maintain the CNC machine effectively. The supplier should provide proper training to your staff or recommend reliable training resources.
8. Scalability and future requirements: Consider your future requirements and growth plans. Select a machine that can accommodate potential increases in production volume or any additional capabilities you may require in the future.
9. Safety features: Prioritize machines with appropriate safety features, such as emergency stop buttons, safety guards, and safety interlocks, to protect operators and prevent accidents.
10. Environmental impact: Consider the environmental impact of the machine and its operations, such as energy consumption and waste generation. Opt for machines that are energy-efficient and environmentally friendly.
Remember to consult with experts, such as machine operators and procurement professionals, to gather their insights and recommendations based on their experience. With careful consideration of these tips, you can make an informed decision and procure the right CNC machine for metal cutting.
FAQs on Sourcing and Manufacturing cnc machine for metal cutting in China
1. Why should I source CNC machines for metal cutting in China?
Sourcing CNC machines for metal cutting in China offers several advantages. Firstly, China is known for its large manufacturing capacity and cost-effective production capabilities. This translates to lower production costs and potential cost savings for buyers. Secondly, Chinese manufacturers are often highly experienced and skilled in the production of CNC machines, ensuring product quality and reliability. Lastly, China has a well-established supply chain and infrastructure, making it easier to source and transport the machines efficiently.
2. How can I find reputable manufacturers of CNC machines in China?
To find reputable manufacturers in China, you can start by researching and compiling a list of potential suppliers. Online platforms such as Alibaba and Global Sources are commonly used to search for CNC machine manufacturers. Look for suppliers with high ratings, positive reviews, and extensive experience in producing metal cutting CNC machines. It is also recommended to engage in direct communication with the manufacturers to understand their capabilities, obtain product samples, and request necessary certifications to ensure quality standards are met.
3. Can I customize the CNC machines to meet my specific requirements?
Yes, most manufacturers in China offer customization services to meet individual requirements. However, it is important to communicate your exact specifications and needs clearly during the initial stages of negotiation. Discuss your specific requirements, including cutting capacity, accuracy, speed, and any specific functionalities required. Manufacturers will then work with you to develop and produce a machine that meets your requirements.
4. How can I ensure product quality and reliability?
To ensure product quality and reliability, it is crucial to conduct thorough due diligence before finalizing a supplier. Request samples or visit the manufacturer’s facilities if possible to assess their production processes and quality control measures. Additionally, ensure that the manufacturer holds relevant certifications, such as ISO 9001, which assures adherence to quality management standards. Requesting a warranty for the CNC machine is also recommended to secure post-sales support and maintenance services.
5. What is the typical lead time for manufacturing and delivery?
Lead times for manufacturing and delivery may vary depending on the complexity and customization of the CNC machines. On average, it takes around 4 to 8 weeks for a manufacturer to complete the production process after receiving the order confirmation. Shipping time will depend on the chosen method, whether by air, sea, or land. It is important to factor in these lead times when planning your procurement and production timelines.
In summary, sourcing CNC machines for metal cutting in China offers advantages such as cost savings, reliable manufacturers, and an efficient supply chain. To ensure successful sourcing, thoroughly research potential suppliers, communicate your requirements clearly, and conduct due diligence to ensure product quality and reliability. Planning for lead times is also crucial to effectively manage your procurement timeline.
Why contact sourcifychina.com get free quota from reliable cnc machine for metal cutting suppliers?
Sourcifychina.com may receive a free quota from reliable CNC machine for metal cutting suppliers for several reasons.
Firstly, Sourcifychina.com is an established and trusted platform that connects suppliers and buyers in the manufacturing industry. By offering a free quota, suppliers can increase their visibility and reach a wider audience through the platform. This can potentially result in more business opportunities and customer acquisitions.
Secondly, Sourcifychina.com has a rigorous vetting process for suppliers, ensuring that only reliable and high-quality suppliers are featured on the platform. By providing a free quota, suppliers can showcase their capabilities and demonstrate their expertise in CNC machine for metal cutting. This can help build trust with potential buyers who are looking for trustworthy and reputable suppliers.
Additionally, offering a free quota allows suppliers to showcase their competitive pricing and services. Buyers often compare multiple suppliers before making a purchasing decision, and a free quota enables suppliers to highlight their cost-effectiveness and unique selling points. This can be particularly advantageous for smaller or lesser-known suppliers who are looking to attract new customers and compete with larger competitors.
Furthermore, Sourcifychina.com understands the importance of providing a seamless and efficient experience for both buyers and suppliers. By offering a free quota, suppliers can demonstrate their commitment to customer satisfaction and showcase their ability to meet deadlines and specifications. This can be especially beneficial for buyers who are looking for reliable and responsive suppliers for their CNC machine needs.
In summary, Sourcifychina.com offers a free quota to reliable CNC machine for metal cutting suppliers to help them increase their visibility, build trust, showcase their capabilities, and provide a seamless experience for buyers. This mutually beneficial arrangement allows suppliers to attract new customers and buyers to find trustworthy and qualified suppliers for their manufacturing needs.