Introduce about machining operations guide,Qulity,Cost,Supplier,Certification,Market,Tips,FAQ
A machining operations guide is a comprehensive document that provides valuable information and instructions related to the various elements of machining operations. It serves as a valuable resource for professionals involved in the manufacturing industry, including engineers, technicians, and machinists.
Quality is one of the key aspects covered in a machining operations guide. It outlines the standards and specifications that need to be adhered to in order to ensure the production of high-quality products. This includes information on the selection of appropriate materials, dimensional accuracy, surface finish, and other quality control measures.
Cost considerations play a crucial role in machining operations. The guide offers insights on cost-effective manufacturing techniques, material selection, tooling, and equipment optimization to ensure efficient use of resources and reduce overall costs.
Finding reliable suppliers is essential for successful machining operations. The guide provides guidelines for identifying and evaluating potential suppliers based on factors such as quality, reliability, pricing, and delivery times.
Certification and accreditation are vital aspects of machining operations. The guide can include information on different certifications and standards, such as ISO 9001, which demonstrate a supplier’s commitment to quality management practices.
Understanding the market is crucial to develop an effective machining operation strategy. The guide may provide insights on market trends, customer demands, and emerging technologies to help businesses stay competitive.
The machining operations guide may incorporate tips and best practices learned through experience. These tips can help in overcoming common challenges, improving productivity, and enhancing overall efficiency.
Frequently Asked Questions (FAQs) section in the guide addresses common queries and concerns related to machining operations. This can include information about troubleshooting, tool selection, maintenance, and safety practices.
In conclusion, a machining operations guide is a valuable resource that covers essential aspects of machining operations. It provides guidance on quality, cost, supplier selection, certifications, market insights, tips, and addresses frequently asked questions. By referring to such a guide, professionals can improve their understanding and decision-making in the field of machining operations.
Types of machining operations
Machining operations are processes used to shape and form materials into desired shapes and sizes using various tools and equipment. These operations are widely used across industries like automotive, aerospace, construction, and manufacturing. Here are some common types of machining operations:
1. Turning: Turning is a machining process that involves rotating the workpiece while a cutting tool is applied to remove material and create a cylindrical shape. This operation is commonly used to create cylindrical parts, such as shafts, pins, and valves.
2. Milling: Milling is a versatile machining process that involves rotating a cutting tool while feeding it into the workpiece. This operation is used to remove material from the surface of a workpiece and create complex shapes, slots, holes, and contours.
3. Drilling: Drilling is a machining operation used to create holes in a workpiece. It involves a rotating cutting tool called a drill bit that applies a downward force to remove material and create cylindrical holes.
4. Grinding: Grinding is a precision machining operation used to achieve fine surface finishes and tight tolerances. It involves rotating an abrasive wheel against the workpiece to remove material and create the desired shape or finish.
5. Boring: Boring is a machining process used to enlarge existing holes or create internal cylindrical shapes in a workpiece. It involves rotating a cutting tool while applying axial force to remove material and create accurate internal dimensions.
6. Sawing: Sawing is a cutting process that uses a toothed blade or abrasive disc to cut through materials. It is commonly used to separate workpieces or cut them into desired lengths or shapes.
7. Broaching: Broaching is a machining operation used to create precision slots, keyways, or other irregular shapes in a workpiece. It involves a specialized tool called a broach that is pulled or pushed through the workpiece to remove material gradually.
8. Honing: Honing is a precise machining operation used to achieve highly accurate dimensions, fine surface finishes, and improved roundness in cylindrical parts. It involves rotating an abrasive stone against the workpiece to remove material and enhance its surface quality.
9. Lapping: Lapping is a machining operation used for obtaining high accuracy and surface finish on flat or spherical surfaces. It involves the use of abrasive materials mixed with a lubricant, called lapping compound, to remove material in a rolling-like motion.
10. Electric Discharge Machining (EDM): EDM is a non-traditional machining process that utilizes electrical sparks to remove material from conductive workpieces. It is commonly used for intricate shapes, hard materials, and to achieve precision tolerances.
These are just a few examples of machining operations, and each operation can be further divided into specialized techniques depending on the requirements of different applications.
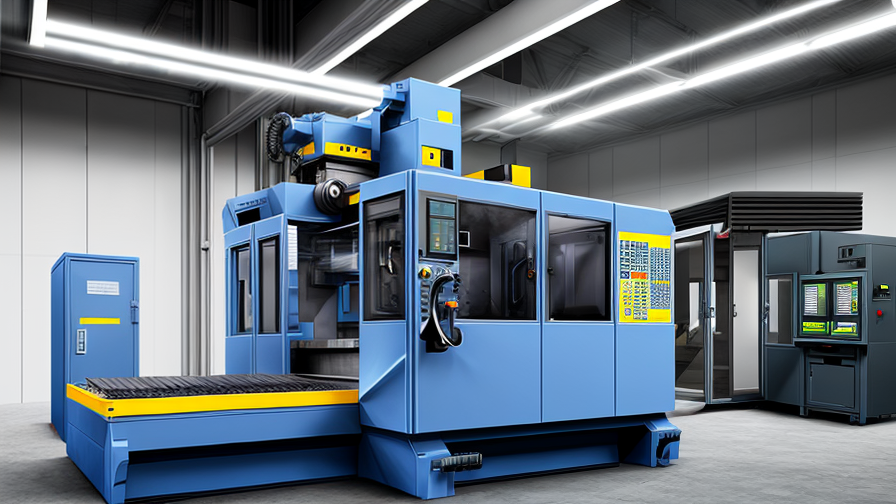
Pros and Cons of Using machining operations
Machining operations refer to a wide range of processes that involve the removal of material from a workpiece to create a desired shape or form. These operations are commonly used in various industries for manufacturing purposes. Here are some pros and cons of using machining operations:
Pros:
1. Accuracy and Precision: Machining operations can achieve high levels of accuracy and precision, making them ideal for producing complex and intricate parts with tight tolerances. This ensures quality and consistency in the manufactured components.
2. Versatility: Machining operations can be used on a wide range of materials, including metals, plastics, and composites. This versatility allows for the production of parts that meet specific requirements, regardless of the material.
3. Surface Finish: Machining operations often result in a superior surface finish compared to other manufacturing methods. This is especially important for applications that require smooth surfaces or parts that will be visible to the end-user.
4. Material Removal: Machining operations are efficient at removing excess material, making them suitable for reducing the weight of components. This can lead to cost savings, especially in industries where lightweight materials are essential, such as aerospace.
5. Customization: Machining operations offer a high degree of customization, allowing manufacturers to produce unique and tailored parts to meet the specific needs of their customers.
Cons:
1. Cost: Machining operations can be expensive due to the equipment, tooling, and skilled labor required. Initial investment costs may be significant, especially for small-scale businesses.
2. Time-consuming: Machining operations can be time-consuming, depending on the complexity of the part and the machining process used. This can result in longer lead times, which may not be desirable for some industries with strict delivery schedules.
3. Waste and Efficiency: Machining operations produce waste in the form of chips or shavings from the material removal process. Managing and disposing of this waste can be challenging and may require additional resources.
4. Limited Geometry: Machining operations have certain limitations when it comes to creating parts with intricate geometries, such as internal features, curved surfaces, or undercuts. These may require additional operations or alternative manufacturing methods.
5. Skill and Knowledge: Machining operations require skilled operators who possess knowledge of the machinery, software, and materials. This can lead to challenges in finding qualified personnel and increased training requirements.
In summary, machining operations offer accuracy, versatility, surface finish, material removal, and customization benefits. However, they may have drawbacks in terms of cost, time, waste management, limited geometry possibilities, and the need for skilled personnel.
machining operations Reference Specifications (varies for different product)
Machining operations are a crucial part of the manufacturing process, utilized to shape and form various materials into desired products. These operations are performed using machine tools such as lathes, milling machines, grinders, and drilling machines. The reference specifications for machining operations vary depending on the specific product being manufactured.
In general, machining operations involve the removal of material from a workpiece to achieve the desired shape, size, and finish. This material removal is achieved through cutting, shearing, and grinding actions. The reference specifications for machining operations include parameters such as cutting speed, feed rate, depth of cut, and tool geometry.
Cutting speed refers to the speed at which the workpiece material is being removed by the cutting tool. It is typically measured in surface feet per minute (SFPM) or meters per minute (m/min). The cutting speed is determined by factors like the material being machined, the type of tool, and the desired finish.
Feed rate, on the other hand, refers to the distance the cutting tool moves relative to the workpiece per unit of time. It is usually measured in inches per minute (IPM) or millimeters per minute (mm/min). The feed rate affects the material removal rate and the quality of the machined surface.
Depth of cut is the distance between the uncut surface of the workpiece and the final machined surface. It determines the amount of material that will be removed with each pass of the cutting tool. The depth of cut affects the cutting forces, tool life, and surface finish.
Tool geometry includes parameters such as cutting edge angle, rake angle, and clearance angle. These angles are designed to ensure efficient material removal, proper chip formation, and reduced cutting forces.
In addition to these reference specifications, there are various other factors to consider in machining operations, such as coolant application, tool material selection, and machine tool rigidity. These factors impact the performance, accuracy, and efficiency of the machining process.
Overall, machining operations require careful adherence to reference specifications to achieve the desired product quality and meet customer requirements. The selection and optimization of these specifications depend on the specific material, product geometry, and machining tool being employed.
Applications of machining operations
Machining operations play a crucial role in various industries, including manufacturing, aerospace, automotive, medical, and more. Here are some key applications of machining operations:
1. Manufacturing: Machining operations are extensively used in manufacturing processes, such as milling, turning, drilling, and grinding. These operations shape raw materials into finished products with high precision and accuracy, meeting quality standards and specific requirements.
2. Automotive: Machining operations are employed in the production of automotive parts like engine components, transmission parts, suspension systems, and braking systems. CNC (Computer Numerical Control) machines perform cutting, drilling, and shaping operations on materials like steel, aluminum, and composites, ensuring the desired specifications are met.
3. Aerospace: The aerospace industry relies heavily on machining operations. Materials used in aerospace applications, including titanium, stainless steel, and other alloys, require precise shaping and drilling. Machining operations ensure critical components like turbine blades, engine parts, and structural components meet stringent safety and performance standards.
4. Medical: In medical industries, machining operations are crucial for producing instruments, implants, and prosthetics. CNC machines create intricate medical components from materials like stainless steel, cobalt-chrome alloys, and polymers. These operations ensure high accuracy, superior surface finish, and proper fitment for medical devices.
5. Electronics: Machining operations aid in the production of precise electronic components, circuit boards, and connectors. High-speed drilling and milling operations are conducted on materials like fiberglass-reinforced epoxy laminates, aluminum housings, and copper sheets to create intricate designs, enabling efficient electronics assembly.
6. Energy: Machining operations are used in the energy sector to manufacture components for power generation, such as turbines, generators, and valves. The machining processes ensure critical components are precisely shaped, resulting in improved efficiency and durability.
7. Mold-making: In industries like plastic injection molding or casting, machining operations are employed to produce molds and dies. The accuracy and precision of these operations directly impact the final product’s quality, tolerances, and dimensional stability.
8. Defense: Machining operations are crucial in defense applications, including the production of firearms, artillery, military vehicles, and aircraft components. The accuracy and consistency achieved through machining operations contribute to the reliability and safety of these defense systems.
Overall, machining operations find applications in a wide range of industries, enabling the production of high-quality components, improving performance, and ensuring safety standards are met. The continual advancements in machining technology further enhance its capabilities and expand its applications in various sectors.
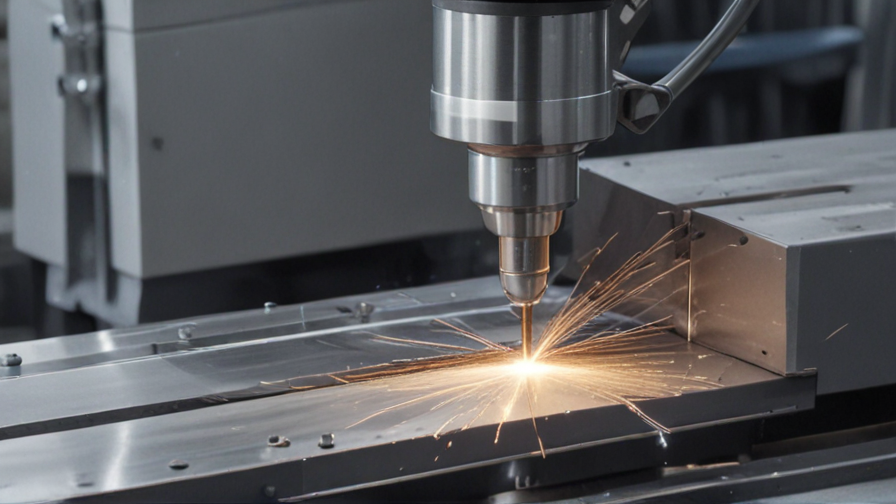
The Work Process and how to use machining operations
The work process in machining operations involves a series of steps to transform raw materials into finished products. It typically begins with the selection of the appropriate material for the desired product. Factors such as durability, strength, and cost are considered during this stage. Once the material is chosen, it is then cut into the required size and shape using cutting tools and techniques like sawing, shearing, or milling.
After the initial shaping, the workpiece undergoes various machining operations such as drilling, turning, grinding, and boring. Drilling involves creating holes in the workpiece using a rotating drill bit, while turning involves rotating the workpiece against a cutting tool to remove excess material and create different shapes. Grinding is a process that uses abrasive wheels to smooth the surface of the workpiece, and boring is used to enlarge existing holes.
These machining operations can be performed manually or using computer numerical control (CNC) machines. Manual machining requires skilled operators who use their hands and tools to carry out the operations, while CNC machining involves programming the machine to execute the desired operations automatically. CNC machines offer higher precision and efficiency, especially for complex shapes and large-scale production.
To use machining operations effectively, it is important to have a clear understanding of the desired outcome and the capabilities of the machines and tools being used. Proper planning and measurement are crucial to ensure accurate results. It is also important to follow safety protocols when operating machinery and to regularly maintain and inspect the equipment to ensure optimal performance.
In conclusion, the work process in machining operations involves selecting the appropriate material, cutting and shaping the workpiece, and then performing various machining operations. These operations can be done manually or using CNC machines. Understanding the desired outcome, the capabilities of the machines and tools, and following safety protocols are key to using machining operations effectively.
Quality Testing Methods for machining operations and how to control the quality
Quality testing methods for machining operations are crucial to ensure that the manufactured parts meet the desired specifications and standards. Several different techniques can be employed to control the quality of machining processes. Some of the commonly used methods are:
1. Dimensional Inspection: This involves measuring the machined parts using various tools such as calipers, micrometers, and coordinate measuring machines (CMMs). By comparing the measured dimensions with the design specifications, any deviations can be identified and addressed.
2. Surface Roughness Testing: Surface roughness is an important aspect of machined components. Specialized instruments like profilometers or surface roughness testers are used to measure and analyze the texture of the surface to ensure it meets the required standards.
3. Hardness Testing: Machined components often require specific hardness levels to ensure durability and performance. Methods like Rockwell or Brinell hardness testing are employed to evaluate the hardness of the material after machining.
4. Metallurgical Analysis: This is used to examine the microstructure of the machined part. Metallographic techniques such as microscopic examination and etching can reveal any defects or inconsistencies in the material.
5. Non-destructive Testing: Techniques like ultrasonic testing, dye penetrant inspection, or magnetic particle testing are used to detect surface or subsurface defects without damaging the final product. This is particularly useful for critical components where structural integrity is paramount.
To control the quality of machining operations, the following practices can be implemented:
1. Establishing clear quality standards and specifications for machined parts.
2. Regularly calibrating and maintaining inspection equipment to ensure accurate measurements.
3. Implementing statistical process control (SPC) techniques to monitor machining processes, identify trends, and take corrective actions before defects occur.
4. Conducting regular audits to assess the effectiveness of quality control measures and identify areas for improvement.
5. Training and educating machine operators about quality requirements, proper machine setup, and the importance of following standardized procedures.
6. Implementing a robust feedback loop system to track and address any quality issues that arise during machining operations.
By employing these quality testing methods and control measures, manufacturers can ensure that their machining operations consistently produce parts that meet the desired specifications and adhere to high-quality standards, ultimately resulting in customer satisfaction and the success of their business.
machining operations Sample Policy and Post-Purchase Considerations for machining operations from China
Sample Policy:
Our company has a strict policy when it comes to machining operations from China. This policy ensures that we receive high-quality products while adhering to ethical and environmental standards. Our policy includes the following:
1. Supplier Selection: We carefully select suppliers based on their reputation, experience, and ability to meet our specific machining requirements. We consider factors such as quality certifications, production capacity, delivery schedule, and financial stability.
2. Quality Assurance: We require our suppliers to have quality control systems in place to ensure that all products meet our specifications. This includes inspection procedures, traceability of materials, and testing protocols. We may conduct regular audits to ensure compliance.
3. Environmental Standards: We prioritize suppliers who are committed to sustainable practices and have appropriate environmental certifications. We aim to minimize the impact of our operations on the environment and expect our suppliers to share this commitment.
4. Intellectual Property Protection: We strictly enforce intellectual property rights and require our suppliers to respect and protect our proprietary designs and information. Non-disclosure agreements and contracts are essential when dealing with machining operations from China.
Post-Purchase Considerations:
After purchasing machining operations from China, it is important to consider the following:
1. Quality Inspection: Conduct a thorough inspection of the received products to ensure they meet the required specifications. If any issues are discovered, notify the supplier immediately and initiate appropriate actions as outlined in the purchase agreement.
2. Communication and Feedback: Establish open lines of communication with the supplier to address any concerns or queries promptly. Regular feedback on product quality, delivery, and overall satisfaction can help build a stronger business relationship.
3. Document and Record Keeping: Maintain detailed records of all transactions, including invoices, inspection reports, and communication records. These documents serve as evidence and may be essential in case of any disputes or future reference.
4. Continual Evaluation: Periodically assess the supplier’s performance based on key performance indicators such as product quality, delivery time, and customer service. Consider making adjustments to the supplier selection if necessary to optimize results.
It is crucial to establish a comprehensive policy and consider post-purchase factors when dealing with machining operations from China. Following these guidelines will help ensure a smooth and successful procurement process while maintaining high-quality standards.
Sourcing machining operations from China: Opportunities, Risks, and Key Players
China has become a favored destination for sourcing machining operations due to its abundant resources, low labor costs, and technological advancements. The country boasts a strong manufacturing sector and a wide range of skilled machinists. However, there are opportunities, risks, and key players that businesses must consider when sourcing machining operations from China.
Opportunities: One of the major advantages of sourcing machining operations from China is its cost-effectiveness. China’s lower labor costs compared to Western countries enable businesses to save significantly on production expenses. Moreover, China’s vast supply chain and extensive network of suppliers make it easier to source raw materials at competitive prices. Additionally, China’s massive machining capabilities cater to various industries, offering a wide array of machining services such as turning, milling, grinding, and more.
Risks: Despite the opportunities, there are inherent risks to consider when sourcing machining operations from China. Quality control is one primary concern as ensuring consistent and high-quality products can be challenging due to varying levels of expertise and standards across different suppliers. Intellectual property theft is another significant risk, as China has been criticized for lax enforcement of intellectual property laws. Protecting proprietary designs and innovations requires careful consideration and contractual agreements.
Key Players: China has several key players in the machining industry. Some of the established and reputable players include Foxconn, BYD Precision Manufacture, and Geely Group. These companies have a solid track record in producing machined parts for various industries, including automotive, electronics, and machinery. Additionally, there are numerous smaller and specialized machining companies that cater to specific industries or offer niche services.
In conclusion, sourcing machining operations from China presents both opportunities and risks for businesses. Cost-effectiveness, diversified supply chains, and extensive machining capabilities serve as key advantages. However, ensuring consistent quality and protecting intellectual property should be top priorities. Considering the vast number of players in the Chinese machining industry, careful selection of suppliers is necessary to mitigate risks and maximize the opportunities provided by China’s machining prowess.
How to find and select reliable machining operations manufacturers in China,use google search manufacturers and suppliers
Finding and selecting reliable machining operations manufacturers in China can be achieved using Google search. Here are some steps to follow:
1. Start by typing relevant keywords into the Google search bar, such as “reliable machining operations manufacturers in China” or “high-quality machining suppliers China.”
2. Review the search results and visit the websites of manufacturers that appear in the top search results. Look for manufacturers that have a professional website with detailed information about their products, services, and manufacturing capabilities.
3. Check if the manufacturer has appropriate certifications, such as ISO 9001:2015, which ensures adherence to quality management standards. This certification indicates the manufacturer’s commitment to quality and reliability.
4. Look for customer testimonials or reviews on the manufacturer’s website or third-party platforms. Positive feedback from previous customers can validate the reliability of their services.
5. Engage in online industry forums or communities to seek recommendations and feedback from other professionals who have experience working with Chinese machining manufacturers. Their insights and recommendations can be valuable in selecting reliable suppliers.
6. Consider reaching out to industry associations or trade organizations that specialize in machining operations. They may have a list of recommended manufacturers or can provide guidance in finding reliable suppliers.
7. Obtain multiple quotes from shortlisted manufacturers to compare prices, lead times, and quality assurance measures they offer. This step will help you make an informed decision on which manufacturer best aligns with your requirements.
8. Consider visiting the facility or conducting video calls with the shortlisted manufacturers to get a better understanding of their manufacturing capabilities, equipment, and quality control processes.
9. Lastly, verify the manufacturer’s legal status by checking if they are a registered company, holding valid licenses and permits, both locally and nationally.
By following these steps and conducting thorough research, you can identify and select reliable machining operations manufacturers in China.
How to check machining operations manufacturers website reliable,use google chrome SEOquake check if ranking in top 10M
To determine the reliability of machining operations manufacturers’ websites, you can follow these steps:
1. Use Google Chrome: This web browser offers various extensions that can help assess the credibility of a website. One such extension is SEOquake.
2. Install SEOquake: Go to the Chrome Web Store and search for the SEOquake extension. Install it on your Google Chrome browser.
3. Open the manufacturer’s website: Visit the website of the machining operations manufacturer you want to evaluate.
4. Activate SEOquake: Click on the SEOquake extension button in your browser’s toolbar to activate it.
5. Check the website’s ranking: SEOquake will provide you with multiple statistics about the website, including its Alexa Rank. Alexa Rank is a global ranking system that measures a website’s popularity. If the website falls within the top 10 million websites, it generally indicates a significant level of traffic and reliability.
6. Evaluate other factors: While the website’s ranking is a good starting point, it’s also essential to assess other aspects. Look for clear and comprehensive information about the manufacturer’s products, services, policies, contact information, and customer reviews if available. A well-designed and professionally maintained website usually indicates a more reliable manufacturer.
7. Use your judgment: Remember that a website’s ranking and appearance can provide initial insights, but they should not be the sole basis for determining reliability. Consider the manufacturer’s reputation, years of operation, certifications, industry affiliations, and customer feedback to form a more comprehensive assessment.
In summary, use Google Chrome and SEOquake to check if a machining operations manufacturer’s website ranks within the top 10 million websites. However, remember to consider other factors and use your judgment to ensure reliability.
Top 10 machining operations manufacturers in China with each 160 words introduce products,then use markdown create table compare
1. BYD Precision Manufacture Co., Ltd.: BYD specializes in precision machining operations and offers a wide range of products, including CNC machining, milling, grinding, drilling, and turning. Their state-of-the-art facilities ensure high-quality production for industries like automotive, electronics, and medical equipment.
2. Foxconn Technology Group: Foxconn is a renowned manufacturer that provides machining operations and solutions for a wide range of products, including computer peripherals, consumer electronics, and telecommunications devices. Their cutting-edge facilities enable high-precision machining with minimal tolerances.
3. China Baowu Steel Group Corporation Limited: Baowu Steel Group offers comprehensive machining operations for steel products. With advanced equipment and skilled technicians, they provide services such as CNC milling, cutting, and welding. Their products find applications in various industries, including construction, automotive, and aerospace.
4. Huawei Technologies Co., Ltd.: Huawei is a leading manufacturer of telecommunications equipment and consumer electronics. They offer machining operations for their products, including CNC milling, turning, and drilling. Huawei’s precise machining capabilities ensure the production of high-quality components for their devices.
5. Geely Automobile Holdings Ltd.: Geely is a prominent automotive manufacturer that offers machining operations for their vehicles. They utilize advanced CNC machining techniques for processes like milling, grinding, and turning. Geely’s skilled workforce ensures the precision and quality of their machined components.
6. GREE Electric Appliances Inc.: GREE specializes in manufacturing air conditioners and home appliances. They provide machining operations for their products, including CNC milling, drilling, and turning. GREE’s precise machining processes guarantee the performance and durability of their appliances.
7. Lenovo Group Limited: Lenovo is a renowned manufacturer of computers, laptops, and mobile devices. They offer machining operations for their products, including CNC milling, drilling, and turning. Lenovo’s high-precision machining ensures the production of reliable and efficient electronic components.
8. ZTE Corporation: ZTE is a leading telecommunications equipment manufacturer. They provide machining operations for their products, including CNC milling, drilling, and turning. ZTE’s precise machining capabilities contribute to the quality and performance of their telecommunications devices.
9. Sinosteel Corporation: Sinosteel specializes in the production of steel products and offers machining operations for various industries. Their services include CNC milling, cutting, and welding. Sinosteel’s high-quality machining processes ensure the reliability and functionality of their steel components.
10. Haier Group Corporation: Haier is a leading consumer electronics and home appliances manufacturer. They provide machining operations for their products, including CNC milling, turning, and drilling. Haier’s precision machining guarantees the performance and longevity of their appliances.
| Manufacturer | Products | Machining Operations |
| ————————————- | ——————— | ——————————————– |
| BYD Precision Manufacture Co., Ltd. | CNC machining | Milling, grinding, drilling, turning |
| Foxconn Technology Group | Computer peripherals | CNC machining with minimal tolerances |
| China Baowu Steel Group Corporation | Steel products | CNC milling, cutting, welding |
| Huawei Technologies Co., Ltd. | Telecommunications | CNC milling, turning, drilling |
| Geely Automobile Holdings Ltd. | Vehicles | CNC milling, grinding, turning |
| GREE Electric Appliances Inc. | Air conditioners, appliances | CNC milling, drilling, turning |
| Lenovo Group Limited | Computers, mobile devices | CNC milling, drilling, turning |
| ZTE Corporation | Telecommunications | CNC milling, drilling, turning |
| Sinosteel Corporation | Steel products | CNC milling, cutting, welding |
| Haier Group Corporation | Consumer electronics, appliances | CNC milling, turning, drilling |
Background Research for machining operations manufacturers Companies in China, use qcc.com archive.org importyeti.com
When it comes to machining operations manufacturers in China, there are several resources that can provide valuable background research. Two websites that can be particularly useful are qcc.com and importyeti.com. Another useful resource is archive.org, which is a digital library of internet sites and other cultural artifacts.
Qcc.com is a Chinese website that provides comprehensive business information on companies across various industries. It offers details such as company profiles, contact information, financials, legal issues, and more. By searching for machining operations manufacturers on qcc.com, one can gather important details about companies, such as their size, location, production capabilities, and customer base.
Importyeti.com is another valuable resource for researching Chinese manufacturers. This website specializes in providing information about Chinese suppliers and manufacturers, making it a useful tool for conducting market research. Importyeti.com provides data on company backgrounds, product portfolios, trade activities, and even shipment information, which can help identify potential machining operations manufacturers in China.
Lastly, archive.org is a website that acts as a digital library, preserving snapshots of webpages over time. By searching for machining operations manufacturers in China on archive.org, one can access historical versions of company websites, thus gaining insight into a company’s evolution, product offerings, and customer interactions over time.
Overall, utilizing qcc.com, importyeti.com, and archive.org can provide comprehensive background research on machining operations manufacturers in China. These resources offer valuable information about a company’s profile, trade activities, financial status, production capabilities, and historical records.
Leveraging Trade Shows and Expos for machining operations Sourcing in China
Trade shows and expos are excellent opportunities for machining operations sourcing in China. These events bring together numerous suppliers and manufacturers under one roof, providing a platform for direct communication and interaction. Leveraging trade shows and expos allows businesses to efficiently source and select machining operations in China.
Firstly, these events provide a vast range of options and enable businesses to explore a wide variety of machining suppliers in one place. By attending these shows, companies can evaluate the quality, capabilities, and pricing of different suppliers, facilitating an informed decision-making process. The ability to compare and contrast suppliers side by side is invaluable for finding the most suitable machining partner.
Secondly, trade shows and expos in China bring together suppliers from across the country, including both well-established manufacturers and emerging companies. This diversity allows businesses to tap into a broader pool of machining operations. As China is known for its expertise in manufacturing, attending such events ensures access to the latest technological advancements and innovative solutions.
Furthermore, trade shows often include live demonstrations and exhibits, enabling businesses to observe and assess the performance of machining equipment firsthand. This is particularly important when sourcing machining operations from China, as it helps validate the supplier’s claims regarding their capabilities and machinery.
In addition to sourcing opportunities, trade shows and expos provide a platform for networking and building relationships with suppliers. Face-to-face interactions foster trust and create a foundation for future collaborations. Physical presence at these events also allows businesses to negotiate pricing, discuss customization options, and establish partnerships beneficial for long-term success.
In conclusion, trade shows and expos offer machining operations sourcing in China a unique advantage. These events provide access to a wide range of suppliers, facilitate comparison and evaluation, showcase the latest technological advancements, and create opportunities for networking and relationship-building. By leveraging trade shows and expos, companies can enhance their sourcing efforts and find the most suitable machining partners in China.
The Role of Agents and Sourcing Companies in Facilitating machining operations Purchases from China
Agents and sourcing companies play a crucial role in facilitating machining operations purchases from China. These entities act as intermediaries and assist companies in sourcing appropriate suppliers, negotiating prices, managing quality control, and handling logistics. Their main objective is to streamline the purchasing process and minimize risk for their clients.
One of the key benefits of utilizing agents or sourcing companies is their local knowledge and expertise. They have an in-depth understanding of the Chinese market, including its industrial landscape, regulatory environment, and business practices. This knowledge allows them to identify suitable suppliers who can meet the specific requirements of the machined components or parts needed.
Moreover, agents and sourcing companies can leverage their established relationships with Chinese suppliers to negotiate favorable prices and terms on behalf of their clients. They have experience in price benchmarking and can advise on whether the quoted prices are reasonable or if there is room for further negotiation.
Quality control is another critical aspect of machining operations purchases. Agents and sourcing companies ensure that the products meet the required specifications and quality standards. They conduct factory audits, inspect product samples, monitor production processes, and perform pre-shipment inspections. This comprehensive quality control process helps to minimize the risk of receiving substandard or defective products.
Furthermore, agents and sourcing companies handle the logistics and shipping arrangements, ensuring a smooth and efficient delivery of the machined components. They have a network of trusted logistics providers who can handle international freight forwarding and customs clearance processes. This saves time and resources for the purchasing companies and allows them to focus on their core business operations.
In summary, agents and sourcing companies facilitate machining operations purchases from China by utilizing their local knowledge, expertise, and network. They assist in finding suitable suppliers, negotiating favorable prices, managing quality control, and handling logistics, ultimately streamlining the entire purchasing process and reducing risks for the buyers.
Price Cost Research for machining operations manufacturers Companies in China, use temu.com and 1688.com
When it comes to price cost research for machining operations manufacturers in China, two reliable platforms to consider are temu.com and 1688.com.
temu.com is an online marketplace that connects buyers with suppliers from various industries. It provides a platform for both domestic and international users to find and negotiate deals. To conduct price cost research on temu.com, one can search for machining operation manufacturers in China and browse through the products and services they offer. The platform usually provides details such as prices, certifications, and customer reviews, which can help in comparing options and making informed decisions.
1688.com, on the other hand, is a popular Chinese e-commerce website. It is mainly in Chinese language and caters to domestic market needs. For international users, translating tools or assistance may be required to navigate through the platform. 1688.com hosts a vast range of suppliers, including those specializing in machining operations. Buyers can explore different listings, product specifications, and pricing information to understand the cost structure of machining operations manufacturers in China.
To effectively utilize temu.com and 1688.com for price cost research, it is advisable to narrow down the search by filtering for specific machining operations, such as CNC machining, precision machining, or metal fabrication. This will help in finding suppliers who specialize in the required services. Additionally, contacting multiple manufacturers to request for detailed quotations and specifications can aid in comparing prices and negotiating better deals.
In conclusion, temu.com and 1688.com are valuable online platforms for conducting price cost research on machining operations manufacturers in China. While temu.com serves as an international marketplace, 1688.com is more focused on the domestic market. Utilizing these platforms, buyers can explore various suppliers, compare prices, and find the most suitable option for machining operations while keeping the description within 300 words.
Shipping Cost for machining operations import from China
The shipping costs for importing machining operations from China can vary depending on various factors including the weight and dimensions of the products, the shipping method chosen, and the final destination.
There are several shipping methods available for importing goods from China including express couriers, air freight, and sea freight. Express courier services like DHL, UPS, and FedEx are generally faster but more expensive, while air freight and sea freight options are typically slower but more cost-effective.
For lightweight and smaller packages, express courier services are commonly used and can range from around $20 to $100 per kilogram, depending on the urgency of delivery. Air freight is suitable for medium-sized shipments, and the cost can be estimated around $5 to $15 per kilogram. However, it’s important to note that there may be additional charges for customs clearance, documentation, and handling fees.
Sea freight is the most economical option for large and heavy shipments. The cost is typically calculated based on the volume or weight of the cargo, known as freight tonnage. The average sea freight shipping cost from China to major ports around the world can range from $500 to $2000 per container (20ft or 40ft), depending on the distance and specific port fees.
It’s also advisable to consider additional costs such as insurance, import duties, taxes, and potential customs fees when calculating the total shipping cost. These costs can vary depending on the country’s regulations and trade agreements between China and the importing country.
To ensure accurate cost estimation, it’s recommended to consult with professional freight forwarders or shipping agents who can provide tailor-made solutions and negotiate competitive rates. They will take into consideration all the necessary factors and help in selecting the most suitable shipping method for your specific requirements, making the import process smoother and cost-effective.
Compare China and Other machining operations Markets: Products Quality and Price,Visible and Hidden Costs
China is currently one of the biggest players in the machining operations market, competing with other countries such as the United States, Germany, and Japan. When it comes to products quality and price, China has been able to offer competitive rates due to its low labor costs and large manufacturing capabilities. Chinese manufacturers have improved their product quality over the years and are now able to meet international standards in many cases. However, it is important to note that not all Chinese manufacturers offer the same level of quality, and some still struggle to meet certain specifications.
Other machining operations markets, such as those in the United States, Germany, and Japan, are known for their high-quality products but often come at a higher price. These countries have stricter regulations and higher labor costs, which can impact the pricing of their products. However, customers can generally expect better quality control and precision from manufacturers in these countries.
In terms of visible and hidden costs, China often has a price advantage due to its lower labor and operating costs. However, it is important for buyers to consider potential hidden costs such as shipping expenses, import duties, and the risk of intellectual property theft. These factors can increase the overall costs of sourcing products from China.
Other machining operations markets may have higher upfront costs, but they often have fewer hidden costs. Shipping and transportation expenses may be lower if the buyer is located in the same country or region as the manufacturer. Additionally, customers may have more legal recourse in the event of any issues, as regulations and intellectual property protection are typically stronger in these markets.
In conclusion, China offers competitive prices and improved product quality in the machining operations market. However, customers should be aware of potential hidden costs and quality variations across different Chinese manufacturers. Other markets may provide higher-quality products but come at a higher price. Ultimately, customers need to analyze their specific needs and consider factors such as quality, price, visible and hidden costs, and legal protections before choosing a manufacturing source.
Understanding Pricing and Payment Terms for machining operations: A Comparative Guide to Get the Best Deal
Pricing and payment terms for machining operations can vary significantly among different manufacturers and suppliers. Understanding these factors is crucial to ensuring that you get the best deal for your machining requirements while also managing your payment obligations effectively. Here is a comparative guide to help you navigate this process:
1. Price Structure: Compare the pricing structures offered by different machining service providers. Some may charge based on the overall complexity of the job or the time required for completion. Others may have fixed rates for specific services or charge based on materials used. Determine which pricing structure suits your needs and budget.
2. Additional Costs: Inquire about any additional costs that may be associated with your machining project. These could include charges for tooling, setup, programming, or any required post-processing. Understanding these additional costs will help you avoid any unexpected expenses.
3. Volume Discounts: If you have a larger machining project or require ongoing services, ask if the supplier offers volume discounts. Some manufacturers may provide reduced pricing for larger orders, which can result in significant savings for your business.
4. Payment Terms: Discuss the payment terms with the machining service provider. Common options include paying on delivery, partial payments at different project milestones, or setting up a credit account. Negotiate terms that align with your financial capabilities and cash flow requirements.
5. Payment Methods: Inquire about the accepted payment methods. Some suppliers may accept bank transfers, credit cards, or other electronic payment options. Clarify these details to ensure a smooth payment process.
6. Flexibility: Assess the flexibility of the machining service provider regarding changes to the project scope or timeline. Discuss any potential penalties or additional costs associated with such changes to avoid surprises down the line.
7. Quality Assurance: Consider the quality assurance processes implemented by the machining service provider. This includes checking for certifications, inspection procedures, and warranties offered. Ensure that their quality standards align with your expectations.
8. Lead Time: Understand the lead time required for your machining project. Compare this among different suppliers, considering any urgency you may have. Balancing lead time with pricing can help you make an informed decision.
By carefully analyzing these factors, you can make an informed decision when selecting a machining service provider, ensuring that you get the best deal for your requirements while managing your payment obligations effectively.
Chinese Regulations and Industry Standards Certifications for machining operations,Import Regulations and Customs for machining operations from China
Chinese Regulations and Industry Standards Certifications for machining operations:
In China, machining operations are governed by several regulations and industry standards to ensure product quality, safety, and environmental standards. The most prominent certification for machining operations is the ISO 9001:2015 standard, which focuses on the quality management systems of organizations. This certification ensures that machining operations follow specific procedures and meet customer requirements consistently. ISO 14001:2015 is another significant certification that focuses on environmental management systems, ensuring that machining operations align with environmental regulations and mitigate their impact.
Other industry standards specific to machining operations include GB/T 6414-2007, which lays out the measurements and tolerances for machined parts, and GB/T 1804-2000, which specifies the precision grades and tolerances for machines. These standards ensure that the machined parts meet specific dimensional requirements.
Import Regulations and Customs for machining operations from China:
When importing machining operations from China, various regulations and customs procedures must be considered. Importers must comply with the regulations set by their home country as well as those imposed by China. The import process generally involves the following steps:
1. Custom Duties and Taxes: Importers need to determine the customs duties, taxes, and fees applicable to the imported machining operations. This can vary depending on the type of product, its value, and the destination country.
2. Import Licenses: Depending on the nature of the machining operations, importers may need to obtain specific licenses or permits from the respective authorities in their home country.
3. Customs Documentation: Importers must provide accurate and complete documentation, including commercial invoices, packing lists, bill of lading/airway bill, and a certificate of origin.
4. Inspection and Compliance: Imported machining operations may be subject to inspection by the customs authorities to ensure compliance with import regulations, standards, and specifications.
5. Trade Barriers and Restrictions: Importers must stay up to date with any trade barriers or restrictions imposed by their home country or China, such as quotas, embargoes, or trade sanctions.
It is crucial for importers to work with reputable suppliers and utilize the services of freight forwarders who have experience in handling customs procedures for machinery and equipment imports.
Overall, importers must thoroughly research and understand the regulations and customs procedures specific to their home country and China to ensure a smooth and compliant import process.
Sustainability and Environmental Considerations in machining operations Manufacturing
Sustainability and environmental considerations play a crucial role in machining operations manufacturing. Machining involves the use of various tools and processes to shape and form materials into desired components. However, these operations can have significant environmental impacts if not managed properly.
One important aspect of sustainability in machining operations is the efficient use of resources. This includes minimizing material waste and energy consumption. Machining processes often generate a substantial amount of waste material, which can have negative environmental implications if not properly managed. To address this, manufacturers employ strategies such as optimizing cutting parameters, using appropriate cutting tools, and implementing effective chip evacuation systems to reduce material waste. Additionally, advancements in cutting tool technology, such as the development of high-performance coatings, have resulted in increased tool life and reduced energy usage.
Furthermore, the choice of materials in machining operations can have implications for sustainability. Manufacturers are increasingly opting for materials that have a lower environmental impact, such as recycled or sustainable materials. For instance, the use of aluminum or composite materials instead of traditional metals can reduce energy consumption and greenhouse gas emissions during machining processes.
Reducing the environmental footprint of machining operations also involves minimizing the use of harmful substances. Cutting fluids, which are commonly used in machining to lubricate and cool the cutting tool, can contain hazardous components. Proper management of cutting fluids, including recycling and proper disposal, is essential to prevent pollution and ensure worker safety. Moreover, the adoption of sustainable alternatives, such as minimal quantity lubrication (MQL) systems, can significantly reduce the use of cutting fluids, further minimizing environmental impacts.
Lastly, implementing sustainable manufacturing practices involves the adoption of advanced technologies. The use of computer numerical control (CNC) machines, for example, allows for more precise control and optimization of cutting parameters, resulting in reduced material waste and energy usage. Additionally, the integration of smart manufacturing systems can enable real-time monitoring and optimization of machining processes, leading to increased resource efficiency and reduced environmental impact.
In conclusion, sustainability and environmental considerations are integral to machining operations manufacturing. Through the efficient use of resources, proper waste management, the choice of sustainable materials, the reduction of harmful substances, and the adoption of advanced technologies, manufacturers can minimize their environmental footprint and contribute to a more sustainable future.
List The Evolution history of “machining operations”
Machining operations have evolved significantly over time, from simple manual processes to highly advanced computer-controlled systems. The history of machining can be divided into several key periods, each marked by significant technological advancements.
1. Pre-Industrial Revolution (Ancient to 18th century): Machining operations can be traced back to ancient civilizations such as Egypt, Greece, and China, where basic hand tools like chisels, files, and drills were used for shaping and cutting materials. This period saw the development of various manual machining techniques.
2. Industrial Revolution (18th to 19th century): The invention of the steam engine and the rise of the machine tool industry led to the mechanization of machining operations. Water-powered mills and steam-powered machines, such as lathes and planers, were introduced. This period saw the birth of the industrial machining era.
3. Early 20th century: The introduction of electricity and mass production techniques revolutionized machining operations. Electrical motors replaced steam engines, providing more precise and controllable power. This period also saw the emergence of specialized machines for specific tasks, such as milling machines and grinding machines.
4. Post-WWII era: This period witnessed rapid advancements in machining technology. Numerical Control (NC) machines, which used punched cards to control machining movements, were developed. This primitive form of computer-aided machining paved the way for Computer Numerical Control (CNC) machines.
5. Late 20th century: CNC machines became increasingly popular, as computer technology improved. CNC machining offered greater precision, repeatability, and the ability to automate complex operations. CAD/CAM (Computer-Aided Design/Computer-Aided Manufacturing) software further enhanced machining capabilities by facilitating design and programming processes.
6. Present: Today, machining operations have advanced to include high-speed machining, robotics, and additive manufacturing technology. Modern CNC machines are integrated with advanced sensors, monitoring systems, and simulation software for optimal efficiency and quality control. The industry is moving towards Smart Manufacturing, where machining operations are interconnected with data-driven technologies like the Internet of Things (IoT) and Artificial Intelligence (AI).
In conclusion, machining operations have come a long way from manual techniques to highly automated and computer-controlled processes. Technological advancements have enabled higher precision, efficiency, and the ability to work with a wide range of materials, transforming various industries and shaping the modern world.
The Evolution and Market Trends in machining operations Industry
The machining operations industry has undergone significant evolution and witnessed various market trends in recent years. These changes have been driven by advancements in technology, increased efficiency requirements, and shifting consumer demands.
One of the significant advancements that have revolutionized machining operations is the use of computer numerical control (CNC) machines. CNC machines have allowed for greater precision, repeatability, and automation in machining processes. These machines can interpret digital designs and instructions, resulting in higher accuracy and faster production times. The adoption of CNC machines has led to increased productivity and reduced costs for manufacturers.
Another trend in the machining operations industry is the growing emphasis on sustainability and environmental consciousness. As awareness about the impact of industrial processes on the environment increases, manufacturers are implementing eco-friendly practices. This includes the use of environmentally friendly materials, energy-efficient machinery, waste reduction strategies, and recycling initiatives. The integration of sustainability practices has not only attracted environmentally conscious consumers but also resulted in cost savings and improved brand reputation for manufacturers.
Additionally, the demand for customized and complex components has surged in recent years. Consumers expect products tailored to their specific needs and preferences, driving manufacturers to offer more customization options. To meet this demand, machining operations have become more versatile and flexible. The industry is now equipped with advanced tools and software that can handle intricate designs and intricate geometries. This trend has also been supported by the decreasing costs of prototyping and low-volume production, making customization more financially viable.
Moreover, the rise of the Internet of Things (IoT) has had a significant impact on the machining operations industry. IoT technology enables real-time data collection and analysis, allowing for predictive maintenance, quality control, and process optimization. By connecting machines and equipment to the internet, manufacturers can gather valuable insights and improve operational efficiency. The integration of IoT technology also facilitates remote monitoring and control, enabling manufacturers to streamline their processes and increase overall productivity.
In conclusion, the machining operations industry has evolved significantly due to technological advancements, sustainability initiatives, customization demands, and the integration of IoT technology. These trends have not only transformed the way manufacturers operate but also influenced consumer expectations and market dynamics. To stay competitive in this evolving industry, companies must embrace these trends and continually update their processes and technologies.
Custom Private Labeling and Branding Opportunities with Chinese machining operations Manufacturers
There are numerous opportunities for custom private labeling and branding with Chinese machining operations manufacturers. China is well-known for its expertise in manufacturing and has a vast network of suppliers that offer diverse machining capabilities.
Private labeling allows businesses to customize products with their own branding elements, such as the company logo, tagline, or packaging design. This creates a distinct identity for the product, helping to establish a unique brand in the market. Chinese machining operations manufacturers offer flexible private labeling options, allowing businesses to easily incorporate their brand identity into the final product.
Additionally, Chinese manufacturers provide extensive customization opportunities. They can tailor products to meet specific requirements, such as different materials, sizes, or finishes. This level of customization allows businesses to create unique products that resonate with their target audience and differentiate them from competitors.
Working with Chinese machining operations manufacturers also offers cost advantages. China has a robust manufacturing infrastructure and can often offer competitive pricing due to economies of scale. This cost-effectiveness allows businesses to maintain a competitive edge in the market while still delivering high-quality products.
Furthermore, Chinese manufacturers have a reputation for efficiency and timely production. They can meet large volume orders within tight deadlines, ensuring businesses can efficiently fulfill customer demands.
To tap into these opportunities, businesses should establish strong partnerships with Chinese manufacturers. It is crucial to conduct thorough research, ensuring the manufacturer aligns with the desired quality standards and has experience in the specific machining operations required. Effective communication is also vital to convey brand requirements accurately.
In summary, custom private labeling and branding opportunities with Chinese machining operations manufacturers offer businesses the chance to create unique products while enjoying cost advantages and efficient production. With careful research and collaboration, businesses can establish successful partnerships to capitalize on the potential of Chinese manufacturing capabilities.
Tips for Procurement and Considerations when Purchasing machining operations
When it comes to procurement and purchasing machining operations, there are several considerations and tips to keep in mind to ensure a successful and cost-effective process.
1. Define your requirements: Clearly identify your specific machining needs, including the type of operations required, desired materials, quantities, and delivery timeline. This will help you communicate your requirements effectively and receive accurate quotes.
2. Conduct market research: Research the market to identify potential suppliers who have expertise in your desired type of machining operations. Look for companies with a proven track record, positive customer reviews, and certifications relevant to your industry.
3. Request for proposals (RFPs): Prepare a detailed Request for Proposal (RFP) document that outlines your requirements, including technical specifications, quality expectations, delivery schedule, and any special considerations. Send this document to multiple suppliers to get competitive bids.
4. Evaluate supplier capabilities: Review the bids received and assess suppliers based on various criteria such as cost, quality, delivery time, technical expertise, capacity, and reliability. Visit their facilities if possible to evaluate their infrastructure and equipment.
5. Quality assurance: Ensure that the machining supplier has established quality control processes in place. Request their quality certifications and protocols to ensure that the parts or components produced meet your specifications and meet industry standards.
6. Cost analysis: Consider the overall cost, including not just the machining cost but also transportation, taxes, packaging, and any additional charges. Compare quotes from different suppliers to find the one that offers the best balance of quality and cost.
7. Risk management: Assess the supplier’s financial stability and reputation to minimize the risk of project delays or disruptions. Perform due diligence by checking references, certifications, and financial records to ensure their reliability.
8. Communication and collaboration: Establish clear lines of communication with the chosen supplier to ensure effective collaboration throughout the project. Regularly communicate your expectations, provide feedback, and address any issues that arise promptly.
9. Contract management: Draft a comprehensive contract that covers all aspects of the machining project, including timelines, quality requirements, intellectual property rights, liability, and payment terms.
10. Continuous improvement: Once the machining operations are underway, maintain open communication with the supplier to address any quality or performance issues. Encourage feedback and suggest improvements to ensure ongoing efficiency and effectiveness.
By following these tips and considerations, you can enhance your procurement process and ensure a successful partnership with a machining supplier.
FAQs on Sourcing and Manufacturing machining operations in China
1. Why should I consider sourcing machining operations in China?
China has become a global manufacturing hub due to its cost-effective labor, extensive industrial infrastructure, and large pool of skilled technicians. Sourcing machining operations from China can significantly reduce costs without compromising quality.
2. What are the common machining operations available in China?
China offers a wide range of machining operations, including CNC milling, turning, grinding, drilling, tapping, and wire EDM. These operations can produce parts with high precision and complex geometries.
3. How do I find reliable manufacturing suppliers in China?
To find reliable suppliers, it is recommended to utilize online platforms like Alibaba, Made-in-China, or Global Sources. These platforms allow you to browse through companies, review their profiles, customer ratings, certifications, and contact them directly for further discussions. Additionally, conducting background checks, requesting samples, and visiting their facilities can help ensure their reliability.
4. What are the factors to consider when selecting a machining operation supplier in China?
When choosing a supplier, consider factors like their experience in producing similar parts, production capacity, quality control measures, communication skills, lead times, and pricing. It is also essential to inquire about their ability to handle customization, meet quality standards (e.g., ISO 9001), and provide post-sales support.
5. Will language and cultural barriers affect the sourcing and manufacturing process in China?
Language and cultural barriers can pose challenges initially but can be overcome through effective communication. Many Chinese suppliers have multilingual staff, and the use of translators or working with sourcing agents can bridge the language gap. Building strong relationships with suppliers and understanding their business culture helps to establish effective communication channels.
6. Are there any quality concerns when sourcing machining operations from China?
Quality concerns can arise when sourcing from any country, but in China, it is important to vet suppliers rigorously to ensure their commitment to quality. This can be achieved through factory audits, certifications, requesting samples, and conducting regular inspections during production.
7. How can I ensure intellectual property protection when sourcing from China?
To protect intellectual property (IP), it is vital to work with suppliers who respect and prioritize IP rights. Signing non-disclosure agreements (NDAs), patents, and trademarks can add legal protection. Additionally, utilizing confidentiality agreements and working with trusted third-party logistics providers can help safeguard IP during shipping and customs clearance.
8. What are the potential challenges in sourcing and manufacturing machining operations in China?
Some challenges include language barriers, cultural differences, quality control, logistics management, lead times, and intellectual property protection. However, with thorough research, due diligence, proper communication, and building strong relationships with suppliers, these challenges can be effectively addressed.
9. What are the payment terms when sourcing from China?
Payment terms vary between suppliers. Commonly used methods include bank transfers, letters of credit (LC), and secure payment platforms like PayPal or Alibaba’s Trade Assurance. Negotiating favorable payment terms, such as a 30% deposit and 70% upon completion or LC payments, can help ensure trust and reduce financial risks.
10. Is it possible to visit the manufacturers in China before finalizing the sourcing agreement?
Visiting the manufacturers in China is highly recommended, especially for larger orders or complex projects. It allows you to assess the supplier’s facilities, quality control measures, production capabilities, and build a strong business relationship. Face-to-face meetings also improve communication and facilitate problem-solving.
In summary, sourcing and manufacturing machining operations in China can provide cost advantages and access to a vast array of skilled suppliers. However, thorough supplier vetting, effective communication, quality control measures, and IP protection strategies are crucial to ensure successful outcomes.
Why contact sourcifychina.com get free quota from reliable machining operations suppliers?
Sourcifychina.com is able to provide free quota from reliable machining operations suppliers for a variety of reasons.
Firstly, Sourcifychina.com has established long-standing partnerships and relationships with a network of reliable machining operations suppliers. These suppliers have been carefully vetted and have a proven track record of delivering high-quality products and services. The trust built through these relationships allows Sourcifychina.com to negotiate favorable terms, including free quota, for their clients.
Secondly, Sourcifychina.com operates on a large scale, sourcing a wide range of products and services from suppliers in China. By aggregating the requirements of multiple clients, Sourcifychina.com is able to leverage their purchasing power and negotiate advantageous terms with suppliers. The suppliers, in return, can benefit from the increased volume of business and the opportunity to establish long-term relationships with reliable clients.
Additionally, Sourcifychina.com acts as an intermediary between clients and suppliers, providing a range of services including sourcing, quality control, logistics, and payment management. By streamlining the procurement process and providing expert guidance, Sourcifychina.com helps to reduce the risk and uncertainty for both clients and suppliers. As a result, suppliers are more inclined to offer free quota to attract new clients and secure ongoing business through Sourcifychina.com.
Furthermore, Sourcifychina.com has developed a strong reputation within the industry for reliability, transparency, and professionalism. Their commitment to ensuring client satisfaction and delivering high-quality products has earned them the trust of both clients and suppliers. This reputation allows Sourcifychina.com to negotiate favorable terms with suppliers who are eager to collaborate with a reputable and reliable sourcing partner.
In conclusion, Sourcifychina.com is able to obtain free quota from reliable machining operations suppliers due to their established relationships, large-scale operations, intermediary services, and strong reputation. These factors enable Sourcifychina.com to provide their clients with cost-effective sourcing solutions while ensuring the quality and reliability of the products received.