Introduce about injection molding supply guide,Qulity,Cost,Supplier,Certification,Market,Tips,FAQ
The injection molding supply guide is a comprehensive resource that provides essential information for anyone involved in the injection molding industry. It covers various aspects such as quality, cost, suppliers, certifications, market trends, tips, frequently asked questions (FAQs), and much more. In a concise manner, this guide aims to equip individuals with the necessary knowledge to make informed decisions and efficiently manage their injection molding processes.
Quality is a crucial factor in injection molding, as it directly impacts the final product’s performance and durability. The guide emphasizes the importance of selecting high-quality materials and implementing rigorous quality control measures throughout the manufacturing process. It also provides insights into inspection techniques and testing procedures to ensure the desired product quality.
Cost is another crucial consideration in injection molding. The guide provides a detailed breakdown of the various cost factors involved, including material costs, tooling expenses, labor expenses, and machine maintenance costs. It offers strategies to optimize costs without compromising on product quality, such as exploring cost-effective materials, minimizing waste, and improving production efficiency.
Suppliers play a vital role in the injection molding supply chain. The guide emphasizes the need for selecting reliable and reputable suppliers who can meet the required specifications, deadlines, and quantities. It provides tips on evaluating potential suppliers, negotiating favorable contracts, and maintaining a healthy supplier relationship.
Certification and compliance with industry standards are essential in the injection molding industry. The guide discusses widely recognized certifications, such as ISO 9001, ISO 13485, and IATF 16949, and their significance in ensuring product quality and customer satisfaction. It also provides guidance on the certification process and the benefits it offers.
The guide covers market trends and insights to help individuals navigate the ever-evolving injection molding industry. It highlights emerging technologies, materials, and market opportunities, enabling businesses to stay competitive and adapt to changing customer demands.
Additionally, the guide offers practical tips and best practices to enhance injection molding processes, troubleshoot common issues, and improve overall efficiency. It includes expertise from industry professionals and addresses frequently asked questions to help readers address specific concerns and challenges they may encounter.
In conclusion, the injection molding supply guide is a valuable resource for individuals seeking a comprehensive and concise overview of the industry. With its focus on quality, cost, suppliers, certifications, market trends, tips, and FAQs, this guide equips readers with the essential knowledge needed for successful injection molding operations.
Types of injection molding supply
Injection molding is a widely-used manufacturing process for producing a variety of plastic parts and products. It involves injecting molten plastic into a mold cavity, allowing it to cool and solidify, and then ejecting the finished product. In order to carry out this process successfully, various supplies and components are required.
1. Mold: The mold is the key component in injection molding. It is typically made of steel or aluminum and consists of two halves, the cavity and the core. The mold is designed according to the desired product shape and is responsible for creating the final product.
2. Plastic Pellets: Injection molding requires plastic material in the form of small pellets or granules. These plastic pellets are fed into the injection molding machine and heated until they melt into a fluid state suitable for injection into the mold.
3. Injection Molding Machine: The injection molding machine is the equipment used to carry out the injection molding process. It consists of a hopper, where the plastic pellets are loaded, and a barrel, where the plastic is melted. The machine also includes an injection unit, which injects the molten plastic into the mold cavity.
4. Cooling System: As the molten plastic is injected into the mold, it needs to cool and solidify to form the final product. A cooling system, such as water channels or cooling plates, is used to dissipate the heat from the molded part and speed up the cooling process.
5. Ejector System: Once the molded part has cooled and solidified, it needs to be ejected from the mold. An ejector system, consisting of ejector pins or sleeves, is used to push the part out of the mold cavity.
6. Mold Release Agents: Mold release agents are substances applied to the mold surface to facilitate the easy removal of the molded part. These agents prevent the plastic from sticking to the mold and help in achieving smooth and defect-free surfaces.
7. Automation and Robotics: In modern injection molding operations, automation and robotics play a crucial role in enhancing efficiency and productivity. These systems can be used for tasks such as part removal, sorting, inspection, and packaging.
The supplies mentioned above are essential for carrying out the injection molding process successfully. Each component contributes to the overall quality and efficiency of the manufacturing process, ensuring the production of high-quality plastic parts and products.
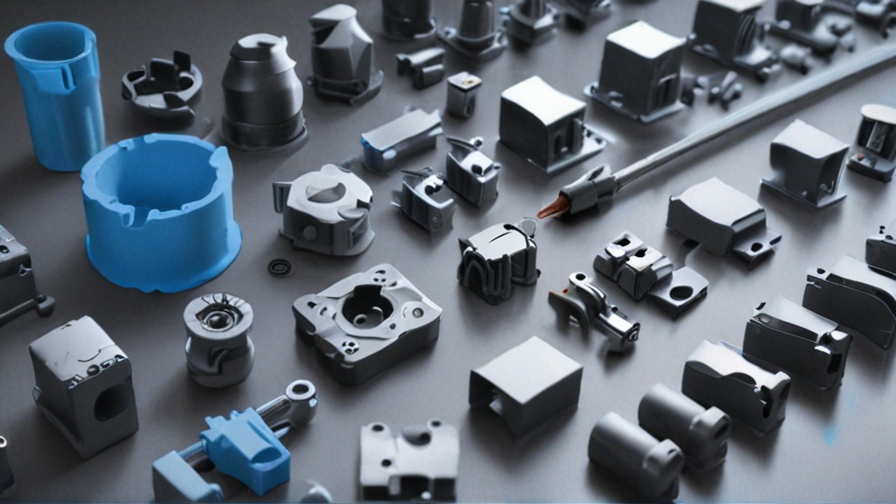
Pros and Cons of Using injection molding supply
Injection molding is a widely used manufacturing process that can produce high-quality, complex plastic parts efficiently. However, there are both pros and cons associated with using injection molding supply. Here are some points to consider:
Pros:
1. Cost-effective: Injection molding is a highly efficient and cost-effective method for large-scale production. It allows for fast production cycles and high output rates, reducing per-unit costs.
2. Versatility: Injection molding can produce parts with intricate designs, complex geometries, and various sizes. It also offers a wide range of materials, including thermoplastics, elastomers, and composites, allowing for versatility in part design and functionality.
3. High accuracy and quality: Injection molding produces precise and consistently high-quality parts with tight tolerances. The process minimizes the need for manual labor, reducing the chances of errors and improving part consistency.
4. Efficiency and speed: Injection molding can produce a large number of parts in a short amount of time. It allows for high-volume production, ensuring quick turnaround times and meeting market demands effectively.
5. Design flexibility: Injection molding offers design flexibility since molds can be customized according to specific requirements. It enables the production of parts with complex shapes, fine details, and multiple components, providing designers with ample leeway for creativity.
Cons:
1. High initial cost: The creation of molds for injection molding can be expensive, especially for complex parts. This initial investment may not be feasible for small-scale or custom production runs.
2. Long lead time: The design and manufacture of molds can take time, leading to longer lead times before production can begin. This delay may not be favorable for time-sensitive projects or market demands.
3. Limited material options: While injection molding offers a wide range of materials, it may not be suitable for all types of plastics. Certain materials with unique properties, such as high-temperature resistance or biodegradability, may not be compatible with the injection molding process.
4. Design constraints: Injection molding has certain design limitations due to the materials used and the molding process itself. This includes draft angles, parting lines, and uniform wall thickness requirements, which can restrict design possibilities for certain applications.
5. Waste and environmental impact: Plastic waste generated during the injection molding process can be a concern, especially as environmental consciousness grows. Proper waste management and recycling practices are crucial to minimize the environmental impact.
In conclusion, injection molding supply offers numerous advantages such as cost-effectiveness, versatility, high accuracy, efficiency, and design flexibility. However, it comes with particular drawbacks, including high initial costs, long lead times, limited material options, design constraints, and potential environmental concerns.
injection molding supply Reference Specifications (varies for different product)
Injection molding is a widely used manufacturing process in which molten material, usually thermoplastic or thermosetting polymers, is injected into a mold cavity. The material then cools and solidifies, resulting in the formation of a finished product. The process requires the use of various equipment and supplies to ensure successful and efficient molding.
One crucial aspect in injection molding is the selection of the appropriate raw materials. The specifications for these materials can vary depending on the desired properties of the final product. Factors such as strength, flexibility, heat resistance, and dimensional stability need to be considered when choosing the material. Additionally, additives like colorants, lubricants, and flame retardants may be included to enhance the properties of the molded product.
Another important component in the injection molding supply chain is the mold itself. The mold consists of two halves, a cavity and a core, which are precision machined to form the desired shape of the final product. The specifications for the mold depend on the complexity and size of the part. Factors like mold material, runners and gates design, cooling system, and ejection mechanisms are carefully considered to ensure the quality and efficiency of the molding process.
To facilitate the injection molding process, auxiliary equipment is also required. This includes injection molding machines, which vary in size and capacity depending on the volume of production. The machines consist of a hopper, where the raw material is fed, an injection unit, which melts and injects the material into the mold, a clamping unit, which holds the mold securely, and a control system to monitor and regulate the process parameters.
To avoid any defects or inconsistencies in the final product, quality control measures are implemented throughout the injection molding supply chain. This includes regular inspection of raw materials, monitoring of process parameters such as temperature and pressure, and thorough inspection of the molded parts.
In conclusion, injection molding supply reference specifications vary depending on the product requirements. The selection of raw materials, mold design, auxiliary equipment, and quality control measures all play crucial roles in ensuring the success of the injection molding process. By carefully considering these specifications and implementing appropriate measures, manufacturers can produce high-quality molded products efficiently.
Applications of injection molding supply
Injection molding, as a manufacturing process, plays a crucial role in various industries due to its numerous applications and advantages. Here, we will highlight some key applications of injection molding and their significance:
1. Automotive Industry: Injection molding is extensively used in the automotive sector for manufacturing components such as car bumpers, dashboards, interior trims, and other plastic parts. This process enables the production of complex geometries with high precision, durability, and cost-effectiveness, thereby enhancing the overall performance and aesthetics of automobiles.
2. Medical Devices: Injection molding is widely employed in the medical field to produce a diverse range of products, including syringes, IV catheters, surgical instruments, and medical-grade components. The ability to maintain strict tolerances and produce sterile, single-use items makes injection molding a preferred method in the medical industry.
3. Packaging Industry: Injection molding is vital for manufacturing various packaging materials, such as bottles, caps, closures, and containers. It enables the production of lightweight, durable, and visually appealing packaging solutions that enhance product safety, shelf life, and consumer appeal.
4. Electronics Industry: Injection molding plays a significant role in the production of electronic components like connectors, housings, and casings. It ensures precise encapsulation, protection against environmental factors, and efficient production of high volumes, meeting the demands of the electronics sector.
5. Consumer Goods: Injection molding is extensively used in the production of consumer goods like toys, kitchenware, and appliances. Its versatility allows for the cost-effective manufacturing of intricate shapes, textures, and designs, meeting the diverse demands of the consumer market.
6. Aerospace and Defense: Injection molding finds applications in the aerospace and defense industries for producing lightweight components like interior panels, brackets, and housings. Injection molding’s ability to utilize advanced materials and adhere to strict quality standards ensures the reliability and performance required in these sectors.
7. Construction Industry: Injection molding is utilized in the construction industry to manufacture pipe fittings, door and window frames, insulation panels, and other building components. Its capability to produce durable, weather-resistant, and corrosion-resistant products contributes to the longevity and sustainability of construction projects.
In summary, injection molding is a highly versatile and efficient manufacturing process with vast applications in automotive, medical, packaging, electronics, consumer goods, aerospace, defense, and construction industries. The process enables the production of complex geometries, offers material versatility, ensures high precision, and allows for cost-effective mass production.
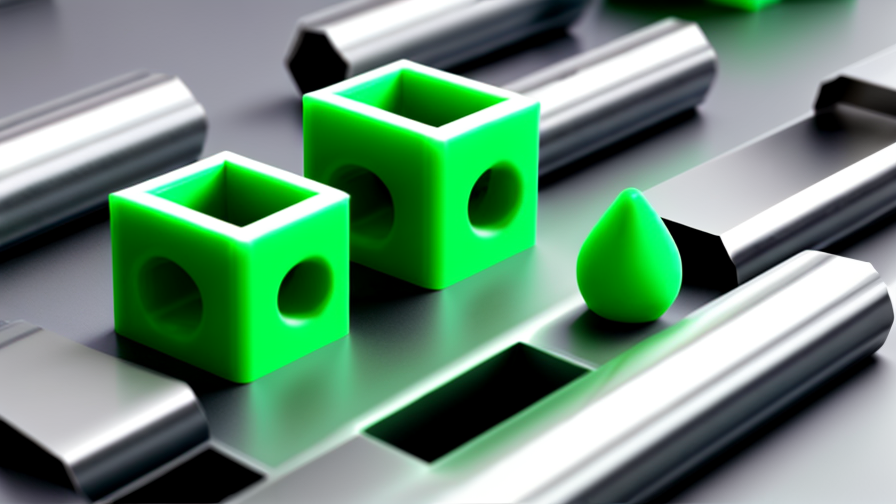
The Work Process and how to use injection molding supply
Injection molding is a widely used manufacturing process in which molten thermoplastic material is injected into a mold, then cooled and solidified to obtain a desired shape. The process involves several steps and requires the use of various supplies.
To begin, a mold is designed and fabricated based on the desired product specifications. The mold consists of two halves – a cavity and a core – that fit together to form the desired shape. These molds are typically made of steel or aluminum to withstand the high temperatures and pressures involved in the process.
Once the mold is ready, the next step is the injection phase. Granular or powdered thermoplastic material, known as resin, is melted and injected into the mold under high pressure. The injection molding machine, equipped with a screw mechanism, forces the molten resin into the mold cavity.
After injection, the mold is cooled to allow the resin to solidify. Cooling can be facilitated by various methods, including water or air cooling. The cooling time is determined based on the material used and the size and complexity of the product. Once the resin is solidified, the mold opens, and the finished product is ejected.
Injection molding supplies include the raw material (resin), the mold, and the injection molding machine. The choice of resin depends on the specific requirements of the product, such as strength, flexibility, and resistance to heat or chemicals. Commonly used resins include polypropylene, polystyrene, polyethylene, and nylon.
The mold plays a crucial role in the injection molding process, as it determines the final shape and details of the product. The mold must be accurately designed and manufactured to ensure proper filling, cooling, and ejection of the product.
The injection molding machine is the device that exerts the necessary pressure to inject the molten resin into the mold. It consists of a hopper, where the resin is fed, a heating unit to melt the resin, and a clamping unit to hold the mold in place. The machine also involves various control systems to monitor and adjust the parameters of the process.
In conclusion, injection molding is a versatile manufacturing process that allows for the mass production of high-quality plastic products. By following the work process and utilizing essential supplies like resin, molds, and injection molding machines, manufacturers can efficiently produce a wide range of products with consistent quality and precision.
Quality Testing Methods for injection molding supply and how to control the quality
Injection molding is a widely used manufacturing process for producing plastic parts. To ensure the quality of the molded parts, several testing methods are employed during the production process. These methods include:
1. Visual Inspection: This is the most basic method where the parts are visually checked for any visible defects such as surface imperfections, color variations, and dimensional discrepancies.
2. Dimensional Measurement: Parts are measured using various instruments like micrometers, calipers, and coordinate measuring machines to ensure they meet the specified tolerances.
3. Load Testing: This method involves applying a specified load or pressure to the molded part to evaluate its strength and durability. It helps identify any structural weaknesses or deformation issues.
4. Gauge and Functional Testing: Specialized gauges and fixtures are used to test the functionality and fit of the molded parts in assembly or mating components. This ensures that the parts meet the required design criteria.
5. Leak and Flow Testing: For parts such as containers or valves, leak testing is conducted to verify their sealing capability. Flow testing analyzes the flow characteristics of the molded parts, helping to optimize their design for enhanced performance.
To control the quality of injection molded parts, several measures can be implemented:
1. Process Monitoring: Continuous monitoring of operating parameters like injection pressure, temperature, and cycle time ensures consistency in quality. Any deviation from set parameters can be quickly identified and corrected.
2. Statistical Process Control (SPC): SPC techniques, such as control charts and process capability analysis, enable the identification of process variations and trends. This helps in taking corrective actions before defects occur.
3. Mold Maintenance: Regular maintenance and cleaning of molds prevent issues such as flash, sink marks, or warpage. Proper lubrication and cleaning of molds also improve part quality and extend mold life.
4. Material Control: Ensuring the quality and consistency of raw materials is crucial. Material testing, storage in controlled environments, and proper drying procedures prevent material-related defects.
5. Employee Training: Training operators on injection molding principles, proper machine handling, and quality control techniques enhances their understanding of the process, minimizing errors and defects.
By employing these testing methods and quality control measures, the injection molding supply can consistently produce high-quality parts while minimizing defects and customer complaints.
injection molding supply Sample Policy and Post-Purchase Considerations for injection molding supply from China
Sample Policy and Post-Purchase Considerations for Injection Molding Supply from China:
When sourcing injection molding supplies from China, it is crucial to establish clear guidelines and considerations to ensure a smooth purchasing process and satisfactory product quality. Below is a sample policy that can help you navigate the procurement journey:
Sample Policy:
1. Supplier Evaluation: Conduct a rigorous evaluation of potential suppliers based on factors such as their manufacturing experience, certification, quality management system, and customer reviews.
2. Product Specifications: Clearly communicate your requirements regarding product specifications, including materials, dimensions, colors, tolerances, finishes, and packaging. Provide detailed drawings or samples for reference.
3. Sample Approval: Request pre-production samples from the supplier to assess the product’s quality, functionality, and compliance with your specifications. Only proceed after obtaining sample approval.
4. Quality Assurance: Establish quality control measures for the injection molding process. This may include on-site inspections during production, as well as statutory quality certifications and tests for the finished products.
5. Delivery Timeframes: Set realistic delivery deadlines with the supplier, considering factors such as production capacity, shipping distance, and any potential delays. Ensure that the supplier is capable of meeting your required timeframes.
Post-Purchase Considerations:
1. Shipping and Customs: Ensure that all necessary shipping arrangements are made, including packaging, labeling, and proper documentation for customs clearance in your country. Clarify responsibilities and cost allocations with the supplier.
2. Communication: Maintain regular and effective communication with the supplier regarding the production progress, shipment tracking, and any potential issues that may arise. Promptly address any concerns and seek resolution.
3. After-Sales Support: Clarify the supplier’s after-sales policies and support. Inquire about warranties, return policies, and possible defective product handling procedures. Ensure prompt and satisfactory resolution of any post-purchase issues.
4. Supplier Relationship: Foster a positive and collaborative relationship with the supplier, as it may play a crucial role in addressing challenges and facilitating future orders. Provide feedback on product quality and service.
5. Continuous Improvement: Continuously review your sourcing and procurement process, seeking areas for improvement. Identify opportunities to optimize product quality, minimize costs, and enhance overall efficiency.
By implementing a robust policy before purchasing and considering vital post-purchase factors, you can minimize risks and maintain favorable relationships when sourcing injection molding supplies from China within a limited word count.
Sourcing injection molding supply from China: Opportunities, Risks, and Key Players
Sourcing injection molding supply from China presents both opportunities and risks for businesses. China is known for its large and advanced manufacturing industry, making it a cost-effective option for companies looking for injection molding services. Additionally, China offers a wide range of suppliers with diverse capabilities, allowing businesses to find the right partner for their specific needs.
The most significant advantage of sourcing injection molding supply from China is the potential cost savings. Chinese manufacturers often offer competitive pricing due to lower labor and production costs. This can result in significant savings for businesses, especially for high-volume production runs.
Moreover, China’s extensive manufacturing infrastructure allows for quick production turnarounds, enabling companies to meet tight deadlines and respond to market demands efficiently. The country’s large pool of skilled workers and advanced technology contribute to faster production times and high-quality output.
However, there are also risks associated with sourcing injection molding supply from China. Language and cultural barriers may lead to miscommunication or misunderstandings, potentially affecting product quality and delivery schedules. Ensuring clear communication and understanding of specifications and requirements is crucial to minimize these risks.
Intellectual property protection is another concern when sourcing from China. To mitigate this risk, businesses should carefully select their suppliers, conduct due diligence, and enforce strong contract agreements to protect their intellectual property rights.
When it comes to key players in the Chinese injection molding industry, some notable manufacturers include:
1. Foxconn Technology Group: Known for their extensive capabilities in electronics manufacturing, Foxconn also offers injection molding services.
2. BYD Company: Specializing in electric vehicles, BYD is a leading player in plastic injection molding and related industries.
3. Haier Group: A prominent home appliance manufacturer, Haier has a strong presence in injection molding for producing various plastic components used in appliances.
4. Midea Group: With expertise in consumer electronics and home appliances, Midea is another key player in the Chinese injection molding industry.
In summary, sourcing injection molding supply from China offers opportunities for cost savings, diverse supplier options, and quick production turnaround times. However, risks related to communication, intellectual property, and quality control should be carefully managed. Businesses should consider key players such as Foxconn, BYD, Haier, and Midea when seeking reliable injection molding suppliers in China.
How to find and select reliable injection molding supply manufacturers in China,use google search manufacturers and suppliers
When searching for reliable injection molding supply manufacturers in China, Google can be a valuable tool to help identify potential suppliers. Here are a few steps to follow:
1. Start by conducting a search using relevant keywords on Google. For example, you can search for “injection molding supply manufacturers in China” or “reliable injection molding suppliers in China.” This will provide you with an initial list of potential manufacturers.
2. Browse through the search results and visit the websites of the manufacturers or suppliers. Look for indications of credibility, such as certifications, years of experience, customer testimonials, and a professional website design. These factors can give you insights into their reliability and expertise.
3. Pay attention to their product range, manufacturing capabilities, and production capacity. Ensure that the manufacturer specializes in injection molding and has the ability to meet your specific requirements in terms of size, material, and complexity.
4. Check if the manufacturer has any quality control certifications, such as ISO 9001, which demonstrate their commitment to maintaining high manufacturing standards. This is crucial to ensure that the products you receive meet your expectations and requirements.
5. Look for manufacturers with extensive experience in exporting their products. This indicates that they are familiar with international trade regulations, packaging, and shipping procedures, which can contribute to smoother transactions.
6. It is also beneficial to check if the supplier has a responsive and professional customer service team. They should be prompt in addressing your inquiries and providing necessary documentation, such as specifications, pricing details, and lead times.
7. Another useful factor to consider is the supplier’s proximity to major logistics hubs or seaports. This can provide advantages in terms of shipping times and costs.
8. To further evaluate the manufacturer’s reliability, you can search for reviews or feedback from other customers. This will help you understand their reputation and the experiences of other businesses who have worked with them.
Remember, thoroughly researching and evaluating potential suppliers is crucial in ensuring that you work with a reliable injection molding supply manufacturer in China.
How to check injection molding supply manufacturers website reliable,use google chrome SEOquake check if ranking in top 10M
To check the reliability of an injection molding supply manufacturer’s website, you can follow these steps:
1. Use Google Chrome: Open the manufacturer’s website using the Google Chrome browser. Chrome offers various extensions that can assist in analyzing the website’s reliability.
2. Install SEOquake: Install the SEOquake extension for Google Chrome. This tool provides valuable insights and metrics about websites, including their ranking and popularity.
3. Check Ranking: Activate SEOquake and observe the toolbar that appears beneath the website’s URL. Look for the numeric value labeled “Rank” to determine the website’s position. If the website ranks within the top 10 million, it signifies a higher level of popularity.
– If the ranking is below 10 million, it indicates that the website attracts a good amount of traffic and is relatively reliable.
– However, if the ranking is above 10 million, it suggests that the website might not be as popular or trusted.
4. Additional Factors: While SEOquake provides a ranking metric, it’s crucial to consider other factors as well. Look for website features such as user-friendly design, comprehensive product information, contact details (phone number, address, email), certifications or affiliations, customer reviews or testimonials, and clear return or refund policies. These factors contribute to the overall reliability of the manufacturer.
5. Limit Word Count: It is important to keep the information concise and limit the word count to 300 words or less.
By utilizing Google Chrome and the SEOquake extension, you can quickly evaluate the reliability of an injection molding supply manufacturer’s website. Remember to consider other factors besides ranking, including website features and customer feedback, to make an informed decision.
Top 10 injection molding supply manufacturers in China with each 160 words introduce products,then use markdown create table compare
1. Foxnum Technology Co., Ltd. has established itself as one of the top injection molding supply manufacturers in China. With a wide range of products including plastic parts, precision molds, and injection molding machines, Foxnum Technology caters to diverse industrial needs. Their plastic parts are meticulously produced using high-quality materials, ensuring durability and precision. Moreover, they specialize in providing customized molds tailored to specific client requirements, allowing for efficient and cost-effective production.
2. Zhongde Moulds is renowned for its comprehensive range of injection molding supplies. Their products are meticulously designed and manufactured with cutting-edge technology and high-quality materials. The company offers a variety of plastic molds, injection molding machines, and plastic parts to meet diverse industrial needs. Customers can benefit from their customization options, as the company specializes in producing molds tailored to specific requirements.
3. JI-TECH Precision Mold Co., Ltd. excels in providing high-precision injection molding supplies to industries worldwide. Their products include plastic molds, injection molding machines, and plastic parts that are manufactured with meticulous attention to detail. The company is known for its commitment to delivering products that meet the highest industry standards. With their state-of-the-art technology and skilled workforce, JI-TECH Precision Mold ensures consistent quality and performance.
| Manufacturer | Products Offered |
|——————————-|————————————————|
| Foxnum Technology Co., Ltd. | Plastic parts, precision molds, injection molding machines |
| Zhongde Moulds | Plastic molds, injection molding machines, plastic parts |
| JI-TECH Precision Mold Co., Ltd. | Plastic molds, injection molding machines, plastic parts |
These leading injection molding manufacturers in China offer diverse product portfolios to cater to various industrial needs. Each company emphasizes quality, precision, and customization options, enabling customers to achieve efficient and cost-effective production.
Background Research for injection molding supply manufacturers Companies in China, use qcc.com archive.org importyeti.com
When it comes to injection molding supply manufacturers in China, there are several reputable platforms that can be utilized for background research. Some of the notable platforms include qcc.com, archive.org, and importyeti.com.
Qcc.com is a comprehensive business information database that provides detailed information about Chinese companies. It offers access to company profiles, financial data, management information, and other essential details that can aid in the evaluation of injection molding supply manufacturers. By using qcc.com, researchers can gain insights into a company’s background, registration status, key personnel, and their market presence.
Archive.org is a digital library that stores snapshots of websites over time. Researchers can leverage this platform to view historical data and track the development and changes of injection molding supply manufacturers’ websites. This can be particularly useful in understanding a company’s growth trajectory, product offerings, and market positioning over the years.
Importyeti.com is an import database that provides information on international shipments entering China. Researchers can utilize this platform to track the import records of injection molding supplies and identify the suppliers involved. Importyeti.com offers insights into the shipment volume, port of entry, destination, and other pertinent details that can enhance the understanding of China’s injection molding supply manufacturers’ import/export activities.
By combining the information obtained from qcc.com, archive.org, and importyeti.com, researchers can gain a holistic view of injection molding supply manufacturers in China. This comprehensive research approach enables them to identify reputable companies, track their performance over time, understand their product offerings, and evaluate their import/export activities.
Leveraging Trade Shows and Expos for injection molding supply Sourcing in China
Trade shows and expos offer a unique opportunity for businesses to source injection molding supplies in China efficiently and effectively. These events bring together a wide range of suppliers, manufacturers, and industry professionals under one roof, providing a platform for networking, knowledge sharing, and discovering new trends and innovations in the field of injection molding.
Attending trade shows and expos in China allows businesses to connect with a large number of potential suppliers from all over the country. This enables them to compare and evaluate different options, negotiate deals, and ultimately select the most suitable partner for their supply needs. By meeting suppliers face-to-face and discussing requirements in detail, businesses can establish a personal connection and gain a better understanding of the supplier’s capabilities, quality standards, and responsiveness.
Trade shows and expos also provide a chance to witness live demonstrations and evaluate the performance of different injection molding machines and technologies. This hands-on experience allows businesses to assess the quality, reliability, and efficiency of the equipment, helping them make informed decisions when selecting suppliers.
Moreover, these events offer valuable networking opportunities, allowing businesses to connect not only with suppliers but also with industry experts, consultants, and other potential partners. By engaging in conversations and attending seminars and workshops, businesses can gain industry insights, gather market intelligence, and stay updated on the latest trends and technologies.
To maximize the benefits of attending trade shows and expos, it is essential for businesses to plan and prepare in advance. Prior research and identification of key suppliers, as well as a clear understanding of specific sourcing requirements, will help focus efforts and make the most of the limited time available. It is also crucial to establish clear objectives and develop a strategy for engaging with suppliers, including collecting relevant information, setting up meetings, and arranging samples and prototypes for evaluation.
In conclusion, trade shows and expos offer a valuable platform for businesses to source injection molding supplies in China. Through networking, live demonstrations, and knowledge sharing, businesses can connect with potential suppliers, evaluate equipment and technologies, and gain industry insights, ultimately making informed decisions and forging successful partnerships in the injection molding supply chain.
The Role of Agents and Sourcing Companies in Facilitating injection molding supply Purchases from China
Agents and sourcing companies play a crucial role in facilitating injection molding supply purchases from China. These professionals act as intermediaries between buyers and manufacturers, helping to streamline the procurement process and ensure successful transactions.
One of the primary responsibilities of agents and sourcing companies is to identify reliable injection molding suppliers in China. They have extensive knowledge and contacts within the industry, allowing them to locate manufacturers that meet the buyer’s specific requirements in terms of quality, capacity, and price. By conducting thorough supplier audits, they also ensure that the chosen manufacturers comply with international quality standards and can deliver on the buyer’s expectations.
Furthermore, agents and sourcing companies handle negotiations on behalf of the buyers. They leverage their knowledge of market prices, manufacturing capabilities, and industry practices to secure the best possible deals. This includes negotiating favorable prices and payment terms, as well as ensuring that the buyer’s intellectual property rights are protected throughout the process.
Agents and sourcing companies also play a critical role in managing the logistics and shipping of injection molding supplies from China to the buyer’s location. They liaise with freight forwarders, handle customs documentation, and track the progress of the shipment to ensure timely delivery. This expertise in international logistics eliminates potential headaches and ensures a smooth supply chain.
Additionally, agents and sourcing companies act as a bridge between the buyer and the manufacturer, facilitating communication and resolving any issues that may arise during the procurement process. They serve as a point of contact for both parties, addressing concerns, clarifying requirements, and helping to build trusting relationships between the buyer and the supplier.
In conclusion, agents and sourcing companies play a vital role in facilitating injection molding supply purchases from China. Their knowledge, experience, and network within the industry streamline the procurement process, ensuring that buyers can access high-quality products at competitive prices while eliminating potential risks and challenges associated with international trade.
Price Cost Research for injection molding supply manufacturers Companies in China, use temu.com and 1688.com
When conducting price cost research for injection molding supply manufacturers in China, two valuable platforms to utilize are temu.com and 1688.com. With a cap of 300 words, let’s delve into the details.
temu.com is an online sourcing platform that connects businesses to Chinese injection molding suppliers. It provides a comprehensive database of manufacturers, allowing users to browse through various options, compare prices, and assess the quality of products. temu.com also facilitates direct communication with suppliers, which is crucial for negotiating deals and gathering additional information. Through this platform, one can request free quotations, samples, and even visit factories if needed.
1688.com, on the other hand, is a popular B2B e-commerce website owned by Alibaba Group. It caters specifically to the Chinese market, providing a vast range of products, including injection molding supplies. Similar to temu.com, 1688.com allows users to search for manufacturers, compare prices, and communicate directly with suppliers. The website’s extensive product listings and user reviews make it an excellent resource to gauge the market and make informed decisions.
When utilizing both platforms, it is essential to follow a systematic approach to price cost research. Begin by searching for injection molding supply manufacturers on temu.com and shortlist potential suppliers based on their pricing, quality, and customer reviews. From there, cross-reference these suppliers on 1688.com to ensure a comprehensive evaluation. By alternating between the two platforms, one can gather more data and make well-informed decisions.
In summary, temu.com and 1688.com are useful platforms to conduct price cost research for injection molding supply manufacturers in China. Utilizing their extensive databases and direct communication features can help businesses find reliable suppliers, compare prices, and negotiate better deals.
Shipping Cost for injection molding supply import from China
The shipping cost for importing injection molding supplies from China depends on various factors, including the weight and volume of the goods, the shipping method chosen, and the destination port. Here is an overview of the options available:
1. Express Delivery: If you require fast shipping, express delivery services like DHL, FedEx, or UPS can be used. While this option is quick, it is also the most expensive. The cost per kilogram typically ranges from $15 to $30, and an additional fee may be applicable for customs clearance.
2. Air Freight: Air freight is a popular choice for medium-sized shipments. Transportation costs for air freight range from $4 to $8 per kilogram. However, there may be additional charges for handling, documentation, and customs clearance. It usually takes 3-7 days for the goods to reach the destination.
3. Sea Freight: For large and heavy shipments, sea freight is the most cost-effective option. The cost is charged per cubic meter (CBM) or per 20ft/40ft container. On average, sea freight costs around $300 to $800 per CBM, but prices can vary depending on the specific route and shipping company. It usually takes 20-40 days for the shipment to arrive.
It’s important to consider that these amounts are only estimates, and additional expenses such as insurance, customs duties, and local charges may also apply. To get accurate shipping quotes, it is advisable to contact freight forwarders or shipping companies who can provide personalized quotes based on your specific requirements.
In conclusion, when importing injection molding supplies from China, selecting the appropriate shipping method according to your budget and timeline is crucial. Comparing prices, evaluating transit times, and considering any additional fees will help ensure a successful and cost-effective importation process.
Compare China and Other injection molding supply Markets: Products Quality and Price,Visible and Hidden Costs
China has become a major player in the injection molding supply market, and comparing it to other markets is crucial. One aspect that stands out is the product quality. Generally, China offers a wide range of products, but the quality can be variable. Some Chinese manufacturers prioritize low costs over quality, resulting in potential quality issues. On the other hand, other markets, such as Europe or the United States, tend to prioritize quality, resulting in more reliable products.
The price of injection moldings is another critical factor for comparison. China is well-known for its competitive pricing, offering relatively low prices compared to other markets. This is primarily due to low labor and manufacturing costs. Conversely, other markets may have higher prices due to various factors, including higher labor costs or more stringent quality control standards. It is essential to consider the budget requirements and product value when deciding which market to source injection moldings from.
Visible and hidden costs need to be taken into consideration as well. China may offer low upfront costs, but it can come with hidden costs such as additional shipping expenses, longer lead times, potential quality issues, and language barriers. These factors can increase the overall cost of sourcing injection moldings from China. On the other hand, other markets may have higher upfront costs but can provide better customer service, shorter lead times, and fewer hidden expenses, resulting in reduced overall costs.
In conclusion, when comparing China to other injection molding supply markets such as Europe or the United States, several factors need to be considered. China offers a wide range of products with varying quality levels, whereas other markets prioritize quality. China’s competitive pricing is advantageous, but hidden costs may arise. Understanding product quality, price, visible and hidden costs is crucial in making an informed decision on which market to source injection moldings from.
Understanding Pricing and Payment Terms for injection molding supply: A Comparative Guide to Get the Best Deal
When looking to source injection molding supplies, understanding the pricing and payment terms is essential to ensure you get the best deal. This comparative guide aims to provide you with key information so that you can make an informed decision.
Pricing for injection molding supplies typically depends on several factors:
1. Quantity: The larger the quantity of supplies you order, the lower the per-unit cost is likely to be. Manufacturers often offer volume discounts, so it’s crucial to determine your required quantity before seeking quotes.
2. Material: Different materials have varying costs. Factors such as the type of plastic, its composition, and grade can affect the price. Discuss your specific material requirements and potential alternatives with suppliers to find the most cost-effective solution.
3. Complexity: The complexity of the design and manufacturing process can impact pricing. Intricate molds or parts may require additional steps or specialized equipment, leading to higher costs. Discuss design complexity with suppliers to better assess its impact on pricing.
4. Tooling: Tooling costs are associated with the creation of molds for injection molding. These costs include design, manufacturing, and maintenance. Tooling costs are typically a one-time expense, but they can significantly affect the overall pricing of supplies.
Regarding payment terms, common options include:
1. Upfront payment: Suppliers may require payment in full before production begins. This method is often used for new customers or small orders.
2. Deposit and balance: A deposit is paid upfront, and the remaining balance is settled upon completion of manufacturing. The payment terms for the balance can vary, so negotiate a timeframe that suits your needs.
3. Payment upon delivery: Some suppliers allow for payment after delivery. This option provides you the opportunity to inspect the supplies before making the final payment. However, suppliers may require a certain level of trust or may limit this option to established customers.
4. Credit terms: This option is more common for frequent buyers or established relationships. Suppliers offer credit with defined payment terms, such as “net 30” or “net 60,” allowing you to pay after a certain period from the invoice date.
In conclusion, understanding the factors affecting pricing, such as quantity, material, complexity, and tooling, is crucial when sourcing injection molding supplies. Additionally, familiarizing yourself with various payment terms can help you negotiate favorable terms and secure the best deal possible.
Chinese Regulations and Industry Standards Certifications for injection molding supply,Import Regulations and Customs for injection molding supply from China
Chinese Regulations and Industry Standards Certifications for injection molding supply focus on ensuring the quality and safety of products manufactured in the country. These regulations and certifications play a crucial role in maintaining industry standards and facilitating international trade.
One of the key regulations for injection molding supply in China is the GB/T Standard, which stands for the Guobiao Standard. This standard is a set of mandatory national standards that cover various aspects of injection molding, such as materials, dimensions, performance, and testing methods. Compliance with GB/T standards is essential to ensure the quality and consistency of injection molded products.
In addition to the GB/T Standard, there are also various industry-specific certifications that manufacturers can obtain to demonstrate their adherence to specific quality and safety requirements. For example, the ISO 9001 certification focuses on quality management systems, while the ISO 14001 certification addresses environmental management systems. These certifications provide reassurance to buyers that the manufacturer follows rigorous quality control processes and meets international standards.
When importing injection molding supplies from China, it is important to comply with the relevant import regulations and customs procedures. The first step is to determine the import category and the applicable trade regulations for the specific product. This includes identifying the harmonized system (HS) code, which classifies products for customs purposes.
Importers must also be aware of any specific regulations associated with the product, such as certifications, labeling requirements, or restrictions on certain materials. It is advisable to work closely with a customs broker or freight forwarder who has expertise in handling imports from China to ensure compliance with all applicable regulations.
Customs duty and taxes are also important considerations when importing from China. Importers should be familiar with the customs valuation methods, which determine the total value of the import shipment for duty calculation purposes. In some cases, customs authorities may require additional documentation, such as a commercial invoice, packing list, or certificate of origin.
To summarize, injection molding supply in China is subject to various regulations and industry standards certifications to ensure product quality and safety. Importers should familiarize themselves with the relevant import regulations, customs procedures, and duties to ensure compliance and a smooth import process.
Sustainability and Environmental Considerations in injection molding supply Manufacturing
Injection molding is a widely used manufacturing process in various industries, and it’s important to consider sustainability and environmental factors during the production of plastic parts. Here are some key considerations in injection molding supply manufacturing:
1. Material Selection: Choosing eco-friendly materials is crucial in minimizing the environmental impact of injection molding. Using biodegradable or recycled materials reduces the consumption of limited resources and decreases waste generation. Additionally, opting for materials with lower carbon footprints during their production further contributes to sustainability.
2. Energy Efficiency: Injection molding is an energy-intensive process, and manufacturers should strive to reduce energy consumption. Implementing energy-efficient machines and technologies, such as high-performance electric injection molding machines, can significantly decrease energy usage. Additionally, optimizing production schedules and reducing idle times can further improve energy efficiency.
3. Waste Management: Proper waste management is essential to minimize the environmental impact. This includes implementing recycling programs for waste generated during the injection molding process. Post-production waste, such as scrapped parts or runners, should be recycled or reused whenever possible. By reducing waste sent to landfills, the industry can contribute to sustainable practices.
4. Mold Design and Tooling: Optimal mold design and tooling can lead to significant environmental benefits. By reducing the weight of molds and utilizing design techniques that minimize material waste, manufacturers can decrease material consumption and carbon emissions associated with the production process.
5. Transportation and Logistics: Minimizing the carbon footprint associated with transportation and logistics is crucial. Reducing shipping distances, maximizing truckload efficiency, and utilizing alternative transportation methods like rail or sea can help reduce greenhouse gas emissions.
6. Life Cycle Assessment: Conducting a comprehensive life cycle assessment helps identify potential environmental hotspots throughout the entire product life cycle. This assessment includes evaluating raw material extraction, manufacturing processes, product use, and disposal. Identifying areas for improvement allows manufacturers to make informed decisions to enhance sustainability.
In summary, injection molding supply manufacturing should prioritize sustainability and environmental considerations. By selecting eco-friendly materials, optimizing energy efficiency, implementing waste management programs, improving mold design, and addressing transportation emissions, the industry can contribute to a more sustainable future.
List The Evolution history of “injection molding supply”
Injection molding supply has come a long way since its inception, evolving with advancements in technology and material sciences. The history of injection molding supply can be traced back to the 19th century when the first attempts to mold materials using an injection process were made.
In the late 1800s, John Wesley Hyatt and his brother Isaiah devised a method to mimic the natural material celluloid, which ultimately became the first thermoplastic material. They used a plunger-style injection molding machine to mold celluloid into various shapes, marking the birth of injection molding.
As time progressed, injection molding began to gain popularity and was used mainly for manufacturing small, intricate objects such as buttons and hair combs. It was during World War II that injection molding gained significant traction due to the increasing demand for mass production of items like syringe barrels and manufacturing parts for war machinery.
In the 1950s, the discovery of new thermoplastic materials, such as polypropylene and polyethylene, expanded the possibilities for injection molding. This led to the development of more advanced injection molding machines capable of higher production rates and greater precision.
The 1970s saw the introduction of computer numerical control (CNC) systems, enabling automation and enhancing the accuracy of injection molding processes. This, coupled with the use of computer-aided design (CAD), revolutionized the industry by allowing for complex designs and reducing human error.
In the 1990s, innovations in software and robotics further improved the efficiency and precision of injection molding. The integration of computer-controlled robotics into the manufacturing process enabled faster mold changes and enhanced productivity.
Today, injection molding supply continues to advance with the advent of 3D printing, allowing for rapid prototyping and customization of molds. Materials like biodegradable plastics and liquid silicone rubber have also gained popularity in recent years, meeting the demand for more sustainable and versatile products.
Overall, the evolution of injection molding supply has been marked by technological breakthroughs, expanded material options, increased automation, and higher efficiency. With ongoing advancements, injection molding continues to play a pivotal role in an array of industries, including automotive, aerospace, medical, and consumer goods.
The Evolution and Market Trends in injection molding supply Industry
The injection molding supply industry has witnessed significant evolution and market trends over the years. Injection molding is a widely used manufacturing process that involves the production of parts and products by injecting molten material into a mold.
One of the key evolutions in the injection molding supply industry is the development of advanced technologies and materials. Modern injection molding machines now incorporate computer controls and automation, leading to increased precision, efficiency, and productivity in the manufacturing process. Additionally, new materials, such as bio-based and biodegradable plastics, have emerged to meet the growing demand for environmentally friendly products.
Another important trend is the increased customization and personalization of injection molded products. As technology advancements allow for more complex molds and intricate designs, manufacturers can now cater to individual customer requirements with greater flexibility. This trend has been especially evident in industries like automotive and medical, where product customization is essential.
Additionally, sustainability has become a significant focus in the injection molding supply industry. Manufacturers are increasingly adopting measures to reduce the environmental impact of their operations. This includes using recyclable materials, optimizing energy consumption, and implementing waste reduction strategies.
Furthermore, the injection molding supply industry has witnessed globalization. With the opportunity to access a wider customer base, many injection molding suppliers have expanded their operations globally. This expansion has led to the establishment of manufacturing facilities in regions with lower labor costs, such as Asia, resulting in increased competitiveness and market presence.
Moreover, the COVID-19 pandemic has brought certain challenges and opportunities to the industry. While the initial disruption in supply chains affected production and led to a decline in demand, the industry quickly adapted to the changing market conditions. Injection molding suppliers shifted their focus towards producing essential medical supplies, such as face shields and ventilator parts, contributing to the battle against the virus.
In conclusion, the injection molding supply industry has evolved significantly in recent years, driven by advancements in technology, increased customization, sustainability, globalization, and the impact of the COVID-19 pandemic. These trends have shaped the market, providing opportunities for growth and innovation in the injection molding supply sector.
Custom Private Labeling and Branding Opportunities with Chinese injection molding supply Manufacturers
When it comes to custom private labeling and branding opportunities with Chinese injection molding supply manufacturers, there are several options available. Chinese manufacturers have extensive experience in injection molding and can help create custom products according to specific brand requirements.
Private labeling allows businesses to create their own brand identity by imprinting their logo, company name, or design on the products. Chinese manufacturers often offer private labeling services, which enable businesses to present products as their own, giving them a competitive advantage in the market.
Moreover, branding opportunities extend further with Chinese injection molding supply manufacturers. They can work closely with businesses to develop custom molds that meet their unique specifications. This enables businesses to create products that are tailor-made to their brand, enhancing their brand recognition and market position.
Chinese manufacturers also offer branding services such as custom packaging and product inserts. These additional branding opportunities allow businesses to package their products in a way that aligns with their brand image, helping to create a cohesive brand experience for customers.
Working with Chinese injection molding supply manufacturers provides businesses with cost-effective solutions. The competitive pricing of Chinese manufacturers combined with their expertise in injection molding ensures high-quality products at a competitive price.
However, while exploring these opportunities, it is important to conduct thorough research and due diligence to find reliable and reputable manufacturers. This can be achieved by checking their certifications, requesting samples, and engaging in open communication to ensure a successful partnership.
Overall, businesses have numerous opportunities for custom private labeling and branding with Chinese injection molding supply manufacturers. These partnerships allow businesses to create unique products that align with their brand identity while benefiting from the cost-effectiveness and expertise provided by Chinese manufacturers.
Tips for Procurement and Considerations when Purchasing injection molding supply
When it comes to procurement of injection molding supplies, there are several considerations that need to be taken into account. Here are some tips to guide you through the process:
1. Identify your requirements: Before making any purchases, clearly define your requirements such as the type and quantity of injection molding supplies needed. Consider the specific materials, sizes, and dimensions required for your production process.
2. Quality assurance: Ensure that the supplier can provide high-quality injection molding supplies. Look for certifications such as ISO 9001 to ensure they meet the necessary quality standards. Request samples or conduct tests to assess the quality of the supplies before making a bulk purchase.
3. Cost-effectiveness: While it’s important to ensure quality, also consider the overall cost of the supplies. Compare prices from different suppliers and negotiate for competitive pricing. However, don’t compromise on quality to save costs, as inferior supplies may impact the production process and result in defects or waste.
4. Supplier reliability: Evaluate the supplier’s reputation in the industry. Check for references, customer reviews, and the supplier’s financial stability. A reliable supplier should have a track record of timely deliveries, responsive customer service, and the ability to handle any issues that may arise.
5. Lead times and inventory management: Consider the lead times required by the supplier to deliver the injection molding supplies. Assess your inventory needs and determine if you require just-in-time deliveries or if it’s feasible to maintain stock in-house. Inquire about the supplier’s stock availability and their ability to meet your specific delivery requirements.
6. Environmental considerations: In today’s eco-conscious world, it’s important to consider the environmental impact of your purchases. Look for suppliers who offer sustainable and eco-friendly materials. This could include recycled or biodegradable options that align with your company’s sustainability goals.
7. After-sales support: Inquire about the supplier’s after-sales support and warranty policies. Understand how they handle returns, replacements, or any issues that may arise with the injection molding supplies. A supplier with good after-sales support will ensure that your concerns are addressed promptly and efficiently.
Overall, carefully assessing your requirements, quality assurance, cost-effectiveness, supplier reliability, lead times, environmental considerations, and after-sales support are all essential when purchasing injection molding supplies. By following these tips, you can make informed decisions and ensure a smooth procurement process.
FAQs on Sourcing and Manufacturing injection molding supply in China
1. Why should I consider sourcing and manufacturing injection molding supply in China?
China is known for its cost-effective manufacturing solutions, offering competitive pricing for injection molding supplies. The country has a well-established manufacturing infrastructure, with a vast network of suppliers and manufacturers capable of handling large production volumes. Additionally, China’s skilled labor force and technological advancements contribute to high-quality manufacturing output.
2. How can I find reliable suppliers and manufacturers in China?
To find reliable suppliers and manufacturers in China, it is recommended to conduct thorough research and due diligence. Utilize online platforms and directories, attend trade shows, and engage in business-to-business networking to identify potential partners. It is crucial to request samples, review certifications, and conduct factory audits to ensure quality and compliance.
3. What are the risks associated with sourcing and manufacturing in China?
There are several risks associated with sourcing and manufacturing in China, including language barriers, intellectual property theft concerns, complex supply chains, and varying quality standards. To mitigate these risks, adopt proper contract management, protect intellectual property through patents and agreements, and establish clear communication channels with suppliers.
4. How can I ensure quality control in manufacturing?
Implementing a robust quality control system is critical to maintaining consistency in manufacturing. This involves conducting regular inspections, implementing strict quality standards, and monitoring production processes throughout the manufacturing cycle. Regular communication with suppliers and overseeing the production process helps in identifying and fixing any issues promptly.
5. What about logistics and shipping?
China has a well-developed logistics infrastructure, ensuring efficient shipping of goods worldwide. Work with logistics providers who specialize in international shipping and have experience delivering goods from China. It is crucial to plan and coordinate shipments well in advance, considering factors like lead times, customs regulations, and transportation modes.
6. Are there any legal and compliance considerations?
China has specific regulations and compliance requirements for sourcing and manufacturing. Ensure you adhere to these regulations, such as product safety certifications, import/export permits, and compliance with labor laws. Consulting legal professionals and utilizing third-party inspection services can help navigate the legal landscape.
7. How do I handle quality issues or defects in manufactured products?
In case of quality issues or defects, it is essential to have open lines of communication with suppliers. Promptly address any problems, discuss potential solutions, and establish clear expectations for corrective actions. Maintaining a professional and collaborative approach is key to resolving issues effectively.
Overall, sourcing and manufacturing injection molding supply in China can offer cost-effective solutions, but it requires careful supplier selection, quality control measures, and legal compliance to ensure successful operations.
Why contact sourcifychina.com get free quota from reliable injection molding supply suppliers?
Sourcifychina.com is a platform that helps businesses find reliable injection molding supply suppliers in China. The website offers a unique benefit of providing free quotas to its users. There are a few reasons why Sourcifychina.com offers this feature:
1. Building Trust: By offering free quotas from reliable suppliers, Sourcifychina.com aims to establish trust with its users. It demonstrates their confidence in their network of suppliers and assures businesses that they are dealing with trustworthy partners.
2. Cost Savings: Sourcing suppliers for injection molding can be a time-consuming and costly process. By offering free quotas, Sourcifychina.com allows businesses to save money on supplier sourcing and negotiation services, helping them reduce sourcing costs.
3. Simplifying the Sourcing Process: Sourcing injection molding suppliers in China can be challenging, especially for businesses unfamiliar with the market. Sourcifychina.com aims to simplify the process by connecting businesses directly with reliable suppliers, eliminating the need for extensive research and vetting on the part of the businesses.
4. Encouraging Usage: Offering free quotas for injection molding supplies encourages businesses to use Sourcifychina.com as their go-to platform for supplier sourcing. By providing this benefit, the platform can attract more users and increase its user base, thus expanding its network of suppliers as well.
In conclusion, Sourcifychina.com offers free quotas from reliable injection molding supply suppliers to build trust with users, save costs, simplify the sourcing process, and encourage businesses to use their platform. By providing this unique benefit, they aim to become a preferred sourcing platform for businesses looking for injection molding suppliers in China.