Introduce about deep drawn components guide,Qulity,Cost,Supplier,Certification,Market,Tips,FAQ
Introduction:
Deep drawn components are metal or non-metal items that are manufactured through a process known as deep drawing. This process involves transforming flat raw materials into three-dimensional shapes using a deep draw press. This guide aims to provide essential information about deep drawn components, including their quality, cost, suppliers, certifications, market, tips, and frequently asked questions.
Quality:
The quality of deep drawn components is crucial as it determines their durability, performance, and reliability. High-quality components undergo rigorous testing to ensure they meet specified standards and requirements. This includes evaluating material composition, dimensional accuracy, surface finish, and mechanical properties. Quality control measures are implemented throughout the manufacturing process to maintain consistent product quality.
Cost:
The cost of deep drawn components depends on various factors, such as material type, complexity of design, volume of production, and finishing requirements. Generally, deep drawing offers cost advantages as it allows for efficient material usage, precise manufacturing tolerances, and minimal waste generation. Prices may vary among suppliers, so it is advisable to obtain multiple quotes to ensure competitive pricing.
Supplier:
Choosing a reliable supplier is essential to obtain high-quality deep drawn components. It is advisable to source components from suppliers with expertise in deep drawing and a proven track record of delivering exceptional products. Consider factors like their production capabilities, equipment, quality assurance processes, and customer reviews when selecting a supplier.
Certification:
Certification is an important aspect, as it ensures that deep drawn components meet industry-specific standards and regulations. Suppliers with ISO 9001 certification demonstrate their commitment to quality management systems, while those with ISO 14001 certification emphasize environmental management. Other certifications like AS9100 (aerospace), IATF 16949 (automotive), or medical device certifications may be necessary depending on the industry requirements.
Market:
Deep drawn components have a wide range of applications across various industries. They are commonly used in automotive, aerospace, electronics, medical, and household appliance sectors. The market for deep drawn components is expected to grow steadily, driven by advancements in engineering and the demand for lightweight, durable, and cost-effective components.
Tips:
– Engage with your supplier early in the design stage to optimize component manufacturability and reduce costs.
– Provide detailed specifications and requirements to ensure accurate manufacturing and quality compliance.
– Collaborate closely with your supplier to address any challenges and achieve desired outcomes efficiently.
FAQs:
– Q: What materials can be used for deep drawn components?
A: Deep drawn components can be manufactured from various metallic and non-metallic materials, including stainless steel, aluminum, copper, brass, titanium, and certain plastics.
– Q: What are the typical lead times for deep drawn components?
A: Lead times depend on factors like component complexity, volume, and material availability. It is essential to discuss lead times with suppliers to align expectations.
In conclusion, deep drawn components play a vital role in various industries. By considering factors like quality, cost, suppliers, certifications, and market trends, individuals and businesses can make informed decisions when sourcing deep drawn components for their specific needs.
Types of deep drawn components
Deep drawing is a manufacturing process used to make various types of components with cylindrical, box-like, or irregular shapes by forming a flat sheet metal into a desired shape using a die. This technique is commonly employed in industries such as automotive, aerospace, electronics, and household appliances, among others. Here are some examples of deep drawn components:
1. Cups and containers: Deep drawn cups and containers are widely used in the food and beverage industry for packaging liquids, powders, and solid products. These components are also used in the medical field for storing medications, as well as in the automotive industry for fuel tanks and oil reservoirs.
2. Caps and lids: Deep drawn caps and lids are used in various applications such as bottling, sealing, and covering mechanisms. They provide protection for the contents inside the container and can be found in industries including pharmaceuticals, cosmetics, and household products.
3. Enclosures and housings: Deep drawn enclosures and housings are typically used to protect electronic and electrical components. These components ensure the safety and proper functioning of devices such as smartphones, computers, televisions, and control panels.
4. Automotive parts: Deep drawn components find extensive applications in the automotive industry. Examples include oil filters, engine components, exhaust system parts, brake cylinders, and fuel injector housings. These components offer high strength and durability, making them suitable for various car parts.
5. Sinks and bowls: Deep drawn sinks and bowls are commonly used in residential and commercial kitchens, as well as in laboratory settings. The deep drawing process ensures a smooth surface finish, making these components easy to clean and maintain.
6. Lighting fixtures: Deep drawn components are used in the production of lighting fixtures such as lamp covers, reflectors, and shades. These components provide a sleek and aesthetically pleasing design while enhancing the functionality of the lighting system.
7. Filters and screens: Deep drawn filters and screens are utilized in various industries to separate and filter particles, liquids, or gases. They can be found in applications ranging from water filtration systems to industrial air filtration.
In conclusion, deep drawing is a versatile manufacturing process that enables the production of a wide range of components with different shapes and specifications. From cups and containers to automotive parts and lighting fixtures, the possibilities for deep drawn components are virtually endless.
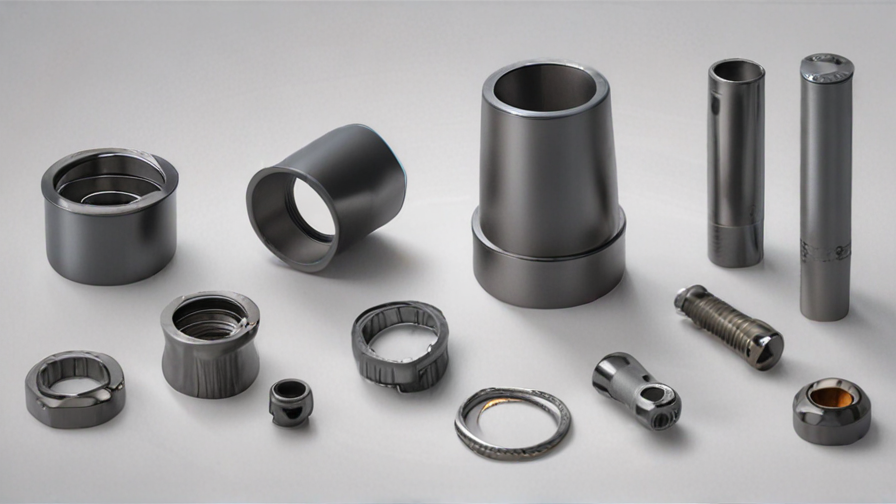
Pros and Cons of Using deep drawn components
Deep drawn components offer several advantages in manufacturing processes. One of the main benefits is their ability to produce complex shapes with high precision and accuracy. This allows for the development of intricate designs that may not be achievable using traditional manufacturing methods. Additionally, deep drawn components are often produced with fewer seams or joints, reducing the likelihood of failure and improving the overall durability of the part.
Another advantage of deep drawn components is their cost-effectiveness. The process typically requires minimal tooling and can be completed quickly, resulting in lower production costs. This is particularly beneficial for high volume manufacturing where cost savings can be significant. Deep drawn components also tend to be lightweight, which can lead to savings in material costs and transportation expenses.
Despite their many advantages, there are some limitations to consider when using deep drawn components. One potential drawback is the limited material options available. While deep drawn components can be produced from a variety of materials, certain alloys and thicknesses may not be suitable for the process. Additionally, deep drawn components may have certain limitations in terms of size and depth, which could impact their suitability for certain applications.
Another potential drawback is the need for specialized equipment and skilled operators. Deep drawing requires specific machinery and tooling, as well as a thorough understanding of the process. This can require additional investment in equipment and training, which may not be feasible for all manufacturers.
In conclusion, deep drawn components offer numerous advantages in terms of complexity, precision, and cost-effectiveness. However, it is important to consider the limitations and requirements of the process when evaluating its suitability for a particular application.
deep drawn components Reference Specifications (varies for different product)
Deep drawn components are a type of metal forming process used to create hollow, three-dimensional objects such as cans, cups, and pans. These components are typically made from materials like stainless steel, aluminum, or brass and are commonly used in industries such as automotive, aerospace, and medical.
The reference specifications for deep drawn components vary depending on the specific product being manufactured. However, there are some general guidelines that apply to most deep drawing processes. These specifications include dimensions, tolerances, material thickness, and surface finish.
Dimensions refer to the physical measurements of the deep drawn component, such as its diameter, height, or width. These dimensions are critical to ensuring the part fits and functions as intended. Tolerances, on the other hand, specify the allowable variation in dimensions to ensure the component meets the required specifications.
Material thickness is another important specification for deep drawn components. The thickness of the material used determines the strength and durability of the final product. Thinner materials can be formed into more intricate shapes, while thicker materials offer greater structural integrity.
Surface finish is the final specification that refers to the appearance and texture of the deep drawn component. The desired surface finish can vary depending on the application and aesthetic requirements. Common surface finishes include matte, polished, and textured.
In addition to these general specifications, each product may have specific requirements based on its intended use. For example, deep drawn components used in the medical field may require additional specifications such as biocompatibility or sterilizability.
It is important to note that these reference specifications are subject to variation depending on the production method, equipment, and other factors. Manufacturers must carefully analyze and assess the specific requirements for each deep drawn component to ensure compliance with the desired specifications.
Overall, deep drawn components play a crucial role in various industries, and the reference specifications guide the manufacturing process to ensure consistent and high-quality products.
Applications of deep drawn components
Deep drawn components have various applications across industries due to their unique characteristics and advantages. Some of the key applications include:
1. Automotive Industry: Deep drawn components are widely used in the automotive industry for manufacturing parts such as exhaust system components, fuel tank caps, radiator shells, and engine components. These components are lightweight, durable, and resistant to corrosion, making them ideal for automotive applications.
2. Aerospace Industry: Deep drawn components are crucial for the aerospace industry, where lightweight yet strong materials are vital for aircraft. They are used in the fabrication of complex parts like aircraft engine components, fuel system parts, and satellite housings. Deep drawn components offer high strength-to-weight ratios, ensuring safety and fuel efficiency.
3. Medical Industry: Deep drawn components find extensive use in the medical and healthcare sector for manufacturing surgical instruments, implants, medical device casings, and drug delivery systems. These components can be produced with precise dimensions and tight tolerances, ensuring reliability in critical medical procedures.
4. Electronics Industry: Deep drawn components are essential in the electronics industry for producing various electronic enclosures, connectors, and sensor housings. These components provide excellent electromagnetic shielding and exceptional dimensional stability, ensuring optimal performance and protection of electronic devices.
5. Packaging Industry: Deep drawn components are widely employed in the packaging industry for manufacturing metal cans, containers, and bottles. These components offer excellent resistance to pressure and impact, making them perfect for preserving food, beverages, and other perishable goods.
6. Energy Industry: Deep drawn components are used in the energy sector for manufacturing parts like heat exchangers, solar panel components, and power transmission components. These components possess high thermal conductivity and are resistant to harsh environments, ensuring optimal energy efficiency and durability.
7. Consumer Goods Industry: Deep drawn components are utilized in the production of consumer goods such as metal caps, seals, and closures for bottles, jars, and containers. These components provide airtight and leak-proof seals, preserving the quality and freshness of various consumer products.
In conclusion, deep drawn components find applications across a wide range of industries due to their lightweight, durable, and precise characteristics. From automotive and aerospace to medical and consumer goods, these components play a vital role in enhancing product performance, efficiency, and reliability.
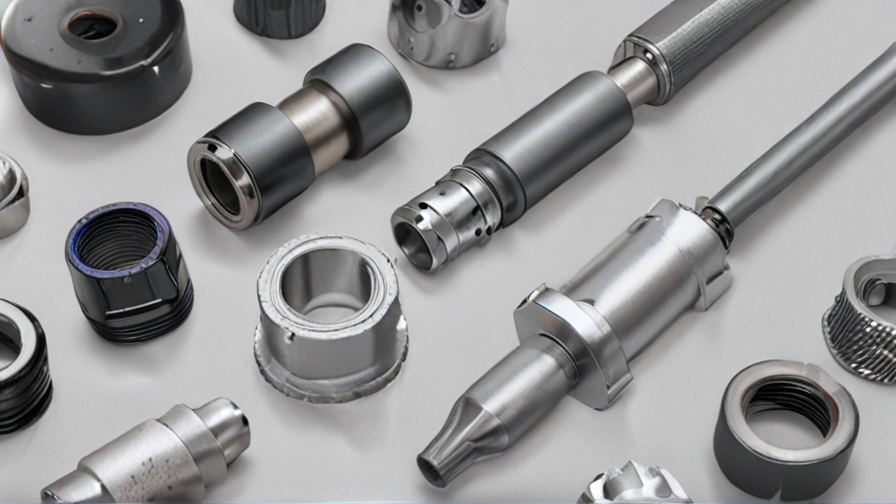
The Work Process and how to use deep drawn components
Deep drawing is a metal forming process used to produce parts with a deeper, more cylindrical shape than typically achievable with conventional stamping or other methods. The process involves a blank of metal being placed over a die, which is then pressed into the die cavity by a punch. The metal is forced to flow into the die cavity, thus taking on the shape of the die.
To use deep drawn components, the first step is to design the component and create a tool for the deep drawing process. The material used for deep drawing must be malleable enough to be stretched and molded without cracking or tearing. Common materials used for deep drawing include stainless steel, aluminum, and copper.
The deep drawing process involves several stages, including blanking, drawing, redrawing, and ironing, each of which helps to form the final shape of the component. The process also requires careful control of the material thickness, lubrication, and die clearance to ensure the desired outcome.
Once the deep drawing process is completed, the components may require additional operations such as trimming, deburring, and surface finishing to meet the required specifications.
In summary, the work process for using deep drawn components involves designing the component, creating the necessary tooling, selecting the appropriate material, and executing the deep drawing process, followed by post-processing operations as necessary. Close attention to material properties, tooling design, and process control is essential to produce high-quality deep drawn components.
Quality Testing Methods for deep drawn components and how to control the quality
There are several quality testing methods for deep drawn components that can be used to ensure the products meet the required standards and specifications. Some of the common testing methods include dimensional measurement, material analysis, visual inspection, and leak testing.
Dimensional measurement involves verifying the accuracy of the component’s dimensions using precision measuring tools such as calipers, micrometers, and coordinate measuring machines. This ensures that the components meet the specified tolerances and fitment requirements.
Material analysis is crucial in ensuring the quality of deep drawn components. This can involve using techniques such as material composition analysis, hardness testing, and microstructure analysis to ensure that the material used meets the required standards for strength, durability, and corrosion resistance.
Visual inspection is another important quality testing method for deep drawn components. This involves visually inspecting the components for any surface defects, imperfections, or irregularities that may affect their performance or functionality.
Leak testing is often used for deep drawn components that are intended to hold liquids or gases. This involves pressurizing the component and then checking for any leaks using methods such as bubble testing or tracer gas detection.
In order to control the quality of deep drawn components, it is important to establish clear quality control procedures and standards. This can involve implementing regular inspection and testing protocols at various stages of the manufacturing process, as well as providing adequate training for personnel involved in quality control.
Additionally, using statistical process control methods can help to monitor and maintain the quality of deep drawn components by identifying any variations or discrepancies in the manufacturing process.
Overall, by implementing these quality testing methods and control measures, manufacturers can ensure that deep drawn components meet the required quality standards and specifications, leading to improved product performance and customer satisfaction.
deep drawn components Sample Policy and Post-Purchase Considerations for deep drawn components from China
Policy:
Our company is committed to providing high-quality deep drawn components from China to our customers. We ensure that all our components are manufactured with the highest standards of precision and quality control. Our policy is to work with reliable and reputable suppliers in China, who adhere to strict manufacturing standards and have a proven track record of producing high-quality deep drawn components.
Post-Purchase Considerations:
After purchasing deep drawn components from China, it is important to consider the following factors to ensure a smooth and successful procurement process:
1. Quality Assurance: Upon receipt of the components, it is essential to conduct a thorough inspection to verify the quality and conformity to specifications. Any discrepancies or defects should be reported to the supplier immediately for resolution.
2. Supplier Communication: Maintaining open lines of communication with the supplier is crucial for addressing any issues or concerns that may arise post-purchase. It is important to establish a clear channel for ongoing communication to ensure any potential problems are addressed in a timely manner.
3. Warranty and Return Policy: Understanding the supplier’s warranty and return policy is critical in the event that any components are found to be defective or not meeting the specified requirements. It is important to have clarity on the process for returning products and seeking replacements or refunds.
4. Continuous Improvement: We are committed to continuous improvement and welcome feedback from our customers regarding their experience with our deep drawn components from China. This enables us to address any potential areas for improvement and enhance our overall service to better meet the needs of our customers.
By adhering to these considerations and maintaining a proactive approach to the post-purchase process, we aim to ensure the satisfaction and success of our customers in sourcing deep drawn components from China.
Sourcing deep drawn components from China: Opportunities, Risks, and Key Players
Sourcing deep drawn components from China offers both opportunities and risks for businesses. China is known for its manufacturing capabilities and cost-effectiveness, making it an attractive option for companies looking to reduce production costs. Deep drawing is a manufacturing process used to create complex and precise shapes, making it crucial for industries such as automotive, aerospace, and electronics.
One of the key opportunities of sourcing deep drawn components from China is the potential for cost savings. Chinese manufacturers often offer competitive pricing due to lower labor and material costs. This can significantly reduce production expenses and increase profit margins for businesses.
Additionally, China’s vast manufacturing ecosystem provides access to a wide range of suppliers specializing in deep drawn components. This allows businesses to find the right suppliers that meet their specific requirements and production volumes.
However, there are also risks involved in sourcing from China. Quality control can be a concern, as maintaining consistent product quality may be a challenge for some Chinese suppliers. It is crucial for businesses to conduct thorough due diligence and select reliable and certified manufacturers. Regular inspections and quality checks should be implemented throughout the production process to ensure compliance with standards.
Another risk is the potential for intellectual property (IP) theft. China has been criticized for its lax enforcement of IP protection laws, which can put companies at risk of their designs and technologies being copied or counterfeited. Businesses should take precautions to safeguard their IP, such as using non-disclosure agreements and registering patents or trademarks.
Some key players in the deep drawn components market in China include Chengdu Jingbang Technology Co., Ltd, Luoyang Longding Aluminum Industries Co., Ltd, and Shanghai Hehua Mold Metal Co., Ltd. These companies have a strong presence in the market and offer deep drawing capabilities for various industries.
In conclusion, sourcing deep drawn components from China can provide opportunities for cost savings and access to a wide range of suppliers. However, businesses need to be aware of the potential risks associated with quality control and intellectual property. By selecting reliable suppliers and implementing appropriate safeguards, companies can optimize their sourcing strategies and benefit from China’s manufacturing capabilities.
How to find and select reliable deep drawn components manufacturers in China,use google search manufacturers and suppliers
Finding and selecting reliable deep drawn components manufacturers in China can be a daunting task, but with the help of Google search and a few steps, it is possible to identify trustworthy suppliers. Here’s how to do it:
1. Start by conducting a Google search using relevant keywords such as “deep drawn components manufacturers in China” or “deep drawing suppliers China.” This will help generate a list of potential manufacturers.
2. Evaluate the search results and select a few manufacturers that seem promising. Look for established companies with a strong online presence, professional websites, and positive customer reviews. Avoid companies with limited information or negative feedback.
3. Visit the selected manufacturers’ websites and examine their product listings to ensure they specialize in deep drawn components. Look for descriptions, specifications, and examples of their work to determine if they can meet your specific requirements.
4. Check for certifications and quality control measures. Reliable manufacturers will often display certifications such as ISO 9001, indicating adherence to international quality standards. Look for information on their manufacturing processes, quality control procedures, and material sourcing practices.
5. Contact the manufacturers directly through email or phone to inquire about their capabilities, lead times, and pricing. Ask for samples or pictures of previously manufactured deep drawn components to assess the quality of their work.
6. Request references from the manufacturers and contact their previous or existing customers to get feedback on their experiences. This will help validate the manufacturers’ reliability and customer satisfaction.
7. Consider visiting trade shows or exhibitions related to metalworking, manufacturing, or deep drawing in China. This provides the opportunity to meet manufacturers in person, see their products, and assess their capabilities directly.
8. Evaluate multiple manufacturers and compare their offerings, including pricing, quality, lead times, and customer service. Choose a manufacturer that demonstrates reliability, quality craftsmanship, competitive pricing, and good communication.
By utilizing Google search and following these steps, you can identify and select reliable deep drawn components manufacturers in China. Remember to do thorough research, gather information, and consider multiple options before making a final decision.
How to check deep drawn components manufacturers website reliable,use google chrome SEOquake check if ranking in top 10M
To check the reliability of a deep drawn components manufacturer’s website, you can follow these steps:
1. Use Google Chrome: Open the website in Google Chrome, as it provides various tools and extensions to analyze the website’s credibility.
2. Install SEOquake: Install the SEOquake browser extension in Google Chrome. This tool provides a range of SEO-related data about websites, including their rankings.
3. Check Ranking: Once installed, activate SEOquake by clicking on its toolbar icon. It will display a summary of SEO metrics and rankings related to the website you are currently visiting.
4. Top 10M Ranking: Look for the website’s global ranking in the top 10 million. This indicates that the website receives a significant amount of traffic and is considered popular. A higher ranking indicates more reliability.
5. Analyze Other Data: SEOquake provides additional information about the website, such as the number of pages indexed by search engines, the domain age, and the number of backlinks. Analyzing this data can give you a better understanding of the website’s credibility.
6. Compare with Competitors: Consider comparing the ranking and other data with other deep drawn component manufacturers. This analysis can help you determine which websites are more reliable and trustworthy.
7. Keep Word Limit in Mind: When checking multiple websites, limit your analysis to not more than 300 words, so that you can quickly evaluate the reliability of each website.
By following these steps and using tools like SEOquake, you can check the reliability of a deep drawn components manufacturer’s website. However, it’s important to note that rankings and other SEO metrics do not necessarily guarantee the reliability or quality of a website.
Top 10 deep drawn components manufacturers in China with each 160 words introduce products,then use markdown create table compare
1. Ningbo Bold Metalproduct Co.,Ltd
– Specializes in the production of deep drawn components such as stainless steel enclosures, aluminum housings, and metal casings for various industries.
2. Ningbo OEM Industry Manufacturer Ltd.
– Offers deep drawn components such metal covers, enclosures, and casings for electronic and automotive applications with customization options.
3. Zhejiang Balford Mechatronics Co., Ltd.
– Provides deep drawn components including stainless steel tanks, metal shells, and aluminum enclosures for industrial equipment and electrical appliances.
4. Suzhou Shunli Precision Stamping Co., Ltd.
– Produces deep drawn components like metal brackets, housing, and cases for telecommunications, medical, and automotive industries.
5. Shenzhen Gold Lodestar Tool & Die Co., Ltd.
– Specializes in deep drawn components manufacturing precision metal parts, including stainless steel casings, covers, and enclosures for consumer electronics and medical devices.
6. China Acculine Precision Manufacturing Company
– Offers deep drawn components such as metal shells, stainless steel enclosures, and aluminum housings for telecommunications and automotive applications.
7. ChinaSavvy
– Provides deep drawn components including metal cases, enclosures, and housings for consumer electronics, automotive, and industrial equipment.
8. Hongli Metal Products Co., Ltd.
– Specializes in deep drawn components manufacturing metal casings, enclosures, and housings for electrical appliances and industrial machinery.
9. Bossard Group
– Offers deep drawn components such as stainless steel enclosures, metal housings, and aluminum casings for medical and telecommunications industries.
10. J&L Metal Products Co., Ltd.
– Produces deep drawn components including metal covers, enclosures, and casings for automotive and electronic applications with customization options.
| Manufacturer | Products |
|——————————–|————————————–|
| Ningbo Bold Metalproduct Co.,Ltd| Stainless steel enclosures, aluminum housings, metal casings|
| Ningbo OEM Industry Manufacturer Ltd.| Metal covers, enclosures, casings for electronic and automotive applications|
| Zhejiang Balford Mechatronics Co., Ltd.| Stainless steel tanks, metal shells, aluminum enclosures|
| Suzhou Shunli Precision Stamping Co., Ltd.| Metal brackets, housing, cases for telecommunications, medical, and automotive industries|
| Shenzhen Gold Lodestar Tool & Die Co., Ltd.| Precision metal parts, stainless steel casings, covers, enclosures for consumer electronics and medical devices|
| China Acculine Precision Manufacturing Company| Metal shells, stainless steel enclosures, aluminum housings for telecommunications and automotive applications|
| ChinaSavvy| Metal cases, enclosures, housings for consumer electronics, automotive, and industrial equipment|
| Hongli Metal Products Co., Ltd.| Metal casings, enclosures, housings for electrical appliances and industrial machinery|
| Bossard Group| Stainless steel enclosures, metal housings, aluminum casings for medical and telecommunications industries|
| J&L Metal Products Co., Ltd.| Metal covers, enclosures, casings for automotive and electronic applications|
Background Research for deep drawn components manufacturers Companies in China, use qcc.com archive.org importyeti.com
Deep drawn components are highly sought after in various industries such as automotive, aerospace, electronics, and medical. China is a hub for manufacturing deep drawn components, with several reputable companies operating in this sector.
One such company is Shanghai Tengxin Precision Machinery Co., Ltd., which specializes in deep drawn components for the automotive industry. They use advanced technology and state-of-the-art equipment to produce high-quality components for their clients.
Another leading manufacturer is Tianjin Rongtai Deep Drawn Technology Co., Ltd., which caters to a wide range of industries including electronics, telecommunications, and medical. They are known for their precision and expertise in producing complex deep drawn components.
Yuyao Jingyi Metal Co., Ltd. is also a prominent player in the deep drawn components market, offering a comprehensive range of products for the automotive and electrical industries. They are known for their innovative solutions and commitment to delivering high-quality components to their customers.
These companies can be found on qcc.com, archive.org, and importyeti.com, which provide valuable information about their products, services, and contact details. With their extensive experience and dedication to quality, these manufacturers are trusted by clients around the world for their deep drawn component needs.
Leveraging Trade Shows and Expos for deep drawn components Sourcing in China
Trade shows and expos are excellent opportunities for sourcing deep drawn components in China. These events bring together a wide range of suppliers, manufacturers, and industry experts, making them ideal platforms for networking, learning about the latest technologies and trends, and connecting with potential partners and suppliers.
When attending trade shows and expos in China, it’s important to have a clear understanding of your sourcing needs and objectives. Researching the event beforehand and identifying the exhibitors who specialize in deep drawn components will help you make the most of your time and resources. It’s also beneficial to schedule meetings with potential suppliers in advance to ensure that you have dedicated time to discuss your specific requirements and explore potential collaboration opportunities.
Furthermore, trade shows and expos provide the opportunity to conduct on-site inspections of suppliers’ capabilities, products, and quality control processes. This hands-on approach can give you valuable insights into a supplier’s reliability and their ability to meet your deep drawn components sourcing needs.
In addition to sourcing potential suppliers, trade shows and expos in China also offer the chance to stay updated on industry developments and best practices. Attending seminars, workshops, and networking events can provide valuable knowledge and insights that can help inform your sourcing decisions and strategies.
Overall, leveraging trade shows and expos for deep drawn components sourcing in China can be a highly effective way to connect with potential suppliers, stay informed about industry trends, and make informed sourcing decisions. By approaching these events with a clear plan and objectives, you can maximize the value of your attendance and strengthen your supply chain for deep drawn components.
The Role of Agents and Sourcing Companies in Facilitating deep drawn components Purchases from China
Agents and sourcing companies play a crucial role in facilitating the purchase of deep drawn components from China. These entities act as intermediaries between buyers and suppliers, helping to streamline the procurement process and ensure efficient and cost-effective sourcing.
One of the key advantages of using agents and sourcing companies is their extensive knowledge and experience in the Chinese market. They have a deep understanding of the local manufacturing landscape, including the capabilities, expertise, and quality standards of various suppliers. This knowledge enables them to identify the most suitable suppliers for deep drawn components, ensuring the best match for the buyer’s requirements.
Agents and sourcing companies also help buyers overcome language and cultural barriers that may exist when dealing directly with Chinese suppliers. They act as translators, ensuring effective communication between the buyer and supplier. Additionally, they are well-versed in the negotiation process and can secure better pricing and contract terms on behalf of the buyer.
Moreover, these entities have established relationships with a network of reliable and trusted suppliers. They have already vetted these suppliers for quality and reliability and can provide the buyer with a shortlist of pre-qualified options. This saves the buyer time and effort in researching and verifying potential suppliers.
Furthermore, agents and sourcing companies assist with quality control and inspection processes. They can conduct factory audits, product inspections, and quality control checks to ensure that the purchased deep drawn components meet the buyer’s specifications and standards. This reduces the risk of receiving substandard or defective products and helps to maintain consistent quality.
In summary, agents and sourcing companies play a vital role in facilitating the purchase of deep drawn components from China. Their expertise in the local market, ability to overcome language and cultural barriers, established relationships with suppliers, and quality control assistance make the sourcing process smoother, more efficient, and more reliable for buyers.
Price Cost Research for deep drawn components manufacturers Companies in China, use temu.com and 1688.com
China is a hub for deep drawn components manufacturers, and two popular platforms for sourcing such manufacturers are temu.com and 1688.com. Both platforms offer a wide range of options for buyers looking to procure deep drawn components.
temu.com is an online trade platform that connects buyers with verified suppliers in China. It provides a user-friendly interface where buyers can search for deep drawn component manufacturers by various categories such as industry, product type, and location. It also offers a secure payment system, ensuring a smooth and secure transaction process. temu.com allows buyers to compare prices from different manufacturers and negotiate directly with suppliers to get the best deal.
1688.com, on the other hand, is a leading online wholesale marketplace in China. It is similar to Alibaba.com, but primarily caters to the domestic Chinese market. Buyers can find numerous reliable manufacturers and suppliers of deep drawn components on this platform. It provides a vast database and a range of filters to narrow down the search process. Buyers can directly communicate with suppliers through the platform’s messaging system to discuss price, specifications, and other details.
When conducting price-cost research on these platforms, it is advisable to follow a systematic approach. Start by searching for manufacturers that specialize in deep drawn components and have a good reputation. Evaluate their product quality, production capability, and certifications. Request quotes from multiple suppliers to compare prices, keeping in mind factors like minimum order quantity, lead time, and payment terms.
It is crucial to use caution while selecting suppliers solely based on price. Consider factors like quality, reliability, and responsiveness as well. Cross-check supplier details, read customer reviews, and if possible, request samples before making a final decision.
In conclusion, temu.com and 1688.com are valuable platforms for conducting price-cost research for deep drawn components in China. Their extensive databases and user-friendly interfaces, combined with comprehensive search filters, make it easier for buyers to find suitable manufacturers. However, buyers should consider multiple factors and exercise due diligence before finalizing any supplier.
Shipping Cost for deep drawn components import from China
When importing deep drawn components from China, the shipping cost can vary depending on several factors. The main determinants of shipping cost are the weight and volume of the components, the mode of transportation, and the distance between the origin and destination.
For smaller shipments, air freight is usually the preferred option due to its speed and reliability. The cost of air freight is calculated based on the weight and dimensions of the shipment, with additional charges for any special handling or documentation requirements. It is important to note that air freight costs can be relatively high compared to other modes of transportation.
For larger shipments, sea freight is often more cost-effective. The shipping cost is determined by the volume of the goods, measured in cubic meters or cubic feet. Sea freight charges also depend on factors such as the type of container used (standard or specialized), the shipping route, and any additional services required, such as insurance or customs clearance.
It is recommended to use the services of a freight forwarder who can negotiate the best shipping rates and handle all logistical aspects of the import process. They can provide quotes based on the specific requirements and assist with the necessary documentation, ensuring a smooth and efficient shipping process.
Additionally, it is crucial to consider other costs associated with importing from China, such as customs duties, taxes, and any potential import restrictions or regulations. These costs may vary depending on the country of import and the nature of the components.
To summarize, the shipping cost for deep drawn components imported from China will depend on the weight, volume, mode of transportation, and distance involved. It is advisable to consult with a freight forwarder to obtain accurate quotes and ensure a cost-effective and hassle-free import process.
Compare China and Other deep drawn components Markets: Products Quality and Price,Visible and Hidden Costs
China is one of the leading players in the deep drawn component market. However, when compared to other markets, there are certain differences in terms of product quality, price, visible and hidden costs.
In terms of product quality, China has made significant progress over the years. Chinese manufacturers have invested heavily in technology and equipment, allowing them to produce high-quality deep drawn components that meet international standards. However, other markets such as Germany and Japan are still considered to have an edge in terms of precision and consistency in product quality. These markets have been known for their exceptional craftsmanship and attention to detail, resulting in superior product quality.
When it comes to pricing, China has a competitive advantage due to its low labor and operational costs. Chinese manufacturers are able to offer deep drawn components at relatively lower prices compared to other markets. This cost advantage has made China a preferred sourcing destination for companies looking for cost-effective solutions. However, it is important to note that the price advantage comes with certain trade-offs, such as compromises in product quality or lead times.
In terms of visible costs, China may have certain advantages. The country has a robust manufacturing infrastructure with a wide array of suppliers and production capabilities. This allows for economies of scale, resulting in lower costs for raw materials and production processes. On the other hand, other markets may have higher visible costs due to factors like higher labor costs or stricter environmental regulations.
When considering hidden costs, other markets may have an advantage. Hidden costs include factors beyond the initial purchase price such as quality defects, delivery delays, or intellectual property risks. China has been known to face challenges in terms of intellectual property protection, with counterfeit products being prevalent. Other markets, with stricter intellectual property laws, may offer more security and protection against such risks, resulting in lower hidden costs in the long run.
In conclusion, while China offers competitive pricing and has improved product quality in the deep drawn components market, other markets like Germany and Japan still maintain an advantage in terms of overall product quality and lower hidden costs. However, China’s cost advantage and well-established manufacturing capabilities make it a significant player in the global market. Companies should carefully evaluate their requirements and consider the trade-offs when choosing between China and other markets for deep drawn components.
Understanding Pricing and Payment Terms for deep drawn components: A Comparative Guide to Get the Best Deal
When it comes to sourcing deep drawn components, understanding pricing and payment terms is crucial in order to secure the best deal. Here’s a comparative guide to help you navigate this process and get the most value for your money.
First and foremost, it’s essential to understand the different pricing models that deep drawn component suppliers may use. These can include cost-plus pricing, fixed pricing, and market-based pricing. It’s important to compare quotes from multiple suppliers to ensure that you are getting a competitive price for the components you need.
In addition to comparing pricing, it’s also important to consider the payment terms that each supplier offers. This can include factors such as payment method, payment schedule, and any discounts for early payment. Some suppliers may offer more favorable payment terms than others, so it’s important to weigh these factors when making a decision.
Another important consideration is the total cost of ownership. This includes not only the initial price of the components, but also factors such as shipping costs, lead times, and any potential maintenance or replacement costs down the line. By considering the total cost of ownership, you can make a more informed decision about which supplier offers the best overall value.
Lastly, don’t be afraid to negotiate. Many suppliers are willing to work with customers to find a pricing and payment arrangement that works for both parties. By being open to negotiation, you may be able to secure a better deal than the initial quote.
In conclusion, understanding pricing and payment terms is essential when sourcing deep drawn components. By comparing pricing, considering payment terms, evaluating the total cost of ownership, and being willing to negotiate, you can ensure that you are getting the best deal possible for the components you need.
Chinese Regulations and Industry Standards Certifications for deep drawn components,Import Regulations and Customs for deep drawn components from China
Chinese Regulations and Industry Standards Certifications:
In China, the deep drawn components industry is subject to regulations and industry standards certifications to ensure the quality and safety of the products. One of the key regulations is the Compulsory Certification (CCC), which is required for certain products to be sold in the Chinese market. However, deep drawn components do not fall under the CCC certification scope.
Instead, deep drawn components are expected to comply with various industry standards certifications to ensure their quality and functionality. The industry standard for deep drawn components in China is governed by the Chinese National Standard (GB) system. For example, GB/T 31113-2014 specifies the dimensions and technical requirements for deep drawn components.
It is important for manufacturers and suppliers of deep drawn components to adhere to these industry standards certifications. This helps in building trust among customers and ensuring the products meet the necessary quality requirements.
Import Regulations and Customs for deep drawn components from China:
When importing deep drawn components from China, there are certain import regulations and customs procedures to be followed. Firstly, the importing company must comply with the import customs clearance process, which involves submitting the necessary documents, such as commercial invoice, packing list, and bill of lading, to the customs authorities.
Additionally, importers may need to obtain import licenses or permits depending on the specific requirements of the destination country. These licenses ensure compliance with local regulations and facilitate smooth customs clearance.
Furthermore, it is advisable to verify and comply with any applicable import tariffs or duties imposed by the importing country. These tariffs may vary depending on the product and the country of importation.
To ensure a seamless import process, it is recommended to work with a reliable logistics provider or freight forwarder who can assist with customs documentation, import regulations, and customs clearance. This ensures that all import requirements are met, reducing the risk of delays or penalties during the importation of deep drawn components from China.
In summary, Chinese deep drawn components adhere to industry standards certifications rather than the Compulsory Certification. Importing these components from China requires compliance with import customs clearance procedures, obtaining necessary licenses or permits, and ensuring compliance with import tariffs or duties specific to the destination country.
Sustainability and Environmental Considerations in deep drawn components Manufacturing
Sustainability and environmental considerations play a crucial role in the manufacturing of deep drawn components. Deep drawing is a metal forming process that involves shaping a flat sheet metal into a three-dimensional component using a stamping press. Here are some key points regarding sustainability and environmental aspects in deep drawn components manufacturing:
1. Material selection: Choosing sustainable materials is vital to reduce the environmental impact. Opting for recyclable or recycled materials not only reduces waste but also conserves natural resources. Additionally, using lightweight materials can result in energy savings during production and transport.
2. Energy efficiency: Implementing energy-efficient practices and technologies can significantly reduce the carbon footprint of deep drawn component manufacturing. This includes using energy-efficient equipment, optimizing production processes, and implementing renewable energy sources wherever possible.
3. Waste reduction and recycling: Minimizing waste generation is essential to achieve sustainability. Implementing lean manufacturing principles such as reducing scrap material, reusing offcuts, and recycling waste products can help in conserving resources and reducing landfill waste.
4. Water conservation: Deep drawing processes often involve the use of coolants or lubricants, which can result in water consumption. Implementing water conservation practices, such as using closed-loop systems or water recycling technologies, can minimize water usage and prevent pollution of water bodies.
5. Emissions control: Deep drawn component manufacturing may involve the use of hazardous substances or emit pollutants during the manufacturing process. Implementing effective emission control measures, such as proper ventilation systems and the use of eco-friendly lubricants, can reduce the environmental impact.
6. Product life cycle assessment: Considering the entire life cycle of deep drawn components, including raw material extraction, manufacturing, usage, and disposal, can help identify opportunities for improvement in terms of sustainability and environmental considerations.
7. Compliance with regulations and standards: Adhering to regional and international environmental regulations and standards is crucial for sustainable manufacturing practices. This ensures that the manufacturing processes do not harm the environment and meet the required environmental performance criteria.
Overall, incorporating sustainable practices in deep drawn component manufacturing can lead to reduced environmental impact, resource conservation, and a more sustainable future for the industry and the planet.
List The Evolution history of “deep drawn components”
Deep drawing is a manufacturing process used to produce components with complex shapes from flat sheet metal. The evolution of deep drawn components can be traced back to ancient times when basic techniques of metalworking were developed. However, significant advancements have been made over the centuries, leading to the sophisticated deep drawing techniques used today.
1. Ancient Metalworking:
Early civilizations, such as the Egyptians and Romans, were primarily involved in simple metalworking processes like forging and casting. These techniques laid the foundation for metal shaping but did not involve deep drawing as we know it.
2. Industrial Revolution (18th – 19th century):
The Industrial Revolution marked a crucial turning point in deep drawing evolution. The invention of mechanical presses and the steam engine allowed for more precise, large-scale metal forming. Deep drawing began to be used for producing simple cylindrical components like cans and cups.
3. Material Advancements:
During the late 19th and early 20th centuries, advancements in metallurgy greatly impacted deep drawing. The introduction of new, more malleable metals like aluminum and its alloys expanded the possibilities of forming more intricate shapes.
4. World Wars and Automotive Industry:
The two World Wars played a significant role in the development of deep drawn components. The increased demand for materials and parts led to advancements in manufacturing processes. Deep drawing rapidly evolved in the automotive industry, where components like engine cylinders and body parts became common.
5. Modern Technology:
In the latter half of the 20th century, the introduction of computer-aided design (CAD) and computer-aided manufacturing (CAM) revolutionized deep drawing. These technologies enabled precise modeling, improved tooling, and increased efficiency in production.
6. Automation and Robotics:
The advent of automation and robotics in the 21st century brought further enhancements to deep drawing. Computer numerical control (CNC) machines and robotic systems improved accuracy, reduced lead times, and increased productivity. The integration of artificial intelligence and machine learning also contributed to optimization and process control.
7. Sustainable Practices:
Recent years have seen a growing emphasis on sustainable practices, leading to developments in deep drawing. The focus on reducing material waste and energy consumption has led to the utilization of lightweight materials and improved die design techniques.
In summary, deep drawn components have evolved significantly from basic metalworking techniques in ancient times to advanced computer-controlled processes used today. Material advancements, industrial demands, technological innovations, and sustainability considerations have all played a crucial role in shaping the evolution of deep drawing.
The Evolution and Market Trends in deep drawn components Industry
The deep drawn components industry has undergone significant evolution and witnessed various market trends in recent years. Deep drawing is a metal forming technique used to create a wide array of hollow components such as cans, cylinders, and other complex shapes. These components find applications in numerous industries such as automotive, aerospace, electronics, and household appliances.
One of the key trends in the deep drawn components industry is the increased demand for lightweight materials. As industries strive to improve fuel efficiency and reduce emissions, the need for lightweight components has become paramount. Deep drawn components made from lightweight materials like aluminum and high-strength steels are gaining popularity as they offer a perfect balance between strength, durability, and weight reduction.
Furthermore, the growing focus on sustainability and environmentally friendly manufacturing processes has led to the adoption of sustainable materials in the deep drawn components industry. For instance, the use of recycled materials and bio-based plastics is on the rise, as they offer similar properties to traditional materials while reducing the carbon footprint.
Another significant trend in the deep drawn components industry is the integration of advanced technologies such as robotics and automation. These innovations have streamlined the production process, ensuring higher precision, improved consistency, and faster manufacturing times. Robotic systems equipped with artificial intelligence and machine learning capabilities can optimize the deep drawing process, enhance quality control, and increase productivity.
Moreover, with the advent of Industry 4.0 technologies, the deep drawn components industry is witnessing the implementation of smart factories. Internet of Things (IoT) devices and data analytics are being employed to monitor and optimize the production process, predict maintenance needs, and improve overall operational efficiency. This digitalization of the industry offers real-time insights and facilitates seamless communication between different stages of production.
In conclusion, the deep drawn components industry is evolving to cater to the demands of lightweight materials, sustainability, and advanced technologies. With the adoption of innovative manufacturing processes and the integration of smart factories, the industry is well-positioned to meet current market trends and ensure continued growth and development.
Custom Private Labeling and Branding Opportunities with Chinese deep drawn components Manufacturers
If you are looking for custom private labeling and branding opportunities with Chinese deep drawn components manufacturers, you have come to the right place. Our partners in China have extensive experience in producing high-quality deep drawn components for various industries, and they are ready to work with you to create custom branding and labeling solutions for your products.
With our partners’ expertise in deep drawn component manufacturing, you can be confident that your products will be made to the highest standards of quality and precision. Whether you are looking to add your brand logo to existing components or create entirely new custom designs, our partners have the capabilities and resources to meet your needs.
In addition to their technical capabilities, our partners in China also have a strong understanding of international branding and labeling requirements. They can work with you to ensure that your custom branding and labeling solutions comply with all relevant regulations and standards, so you can confidently market your products in any market around the world.
When you choose to work with our partners in China, you can expect personalized service, attention to detail, and a commitment to delivering exceptional results. They will work closely with you throughout the process to understand your specific branding and labeling requirements and to ensure that the final products meet your expectations.
Take advantage of the custom private labeling and branding opportunities with Chinese deep drawn components manufacturers and elevate your products to the next level of professionalism and marketability. Contact us today to learn more about how we can help you create custom branding and labeling solutions for your products.
Tips for Procurement and Considerations when Purchasing deep drawn components
When purchasing deep drawn components, there are several considerations and tips that can help ensure a successful procurement process. These components are commonly used in industries such as automotive, aerospace, and medical, and it’s important to choose the right supplier for your specific needs.
1. Quality: The quality of deep drawn components is crucial for ensuring the overall performance and safety of the final product. When sourcing these components, it’s important to thoroughly assess the supplier’s quality control processes and certifications.
2. Material selection: Deep drawn components can be made from a variety of materials, including stainless steel, aluminum, copper, and brass. The material selection should be based on the specific application and performance requirements. It’s important to work closely with the supplier to determine the most suitable material for your needs.
3. Design and engineering support: Working with a supplier that offers design and engineering support can be highly beneficial. They can help optimize the design of the components for manufacturability, cost-effectiveness, and performance.
4. Production capabilities: Assess the supplier’s production capabilities, including the equipment and technologies they have in place for deep drawing. It’s important to ensure that the supplier has the capacity to meet your production requirements and timelines.
5. Cost considerations: While cost is an important factor, it’s also crucial to consider the overall value that the supplier can provide. This includes factors such as quality, reliability, delivery times, and customer support.
6. Regulatory compliance: Depending on the industry and application, deep drawn components may need to meet certain regulatory standards and certifications. It’s essential to partner with a supplier that is well-versed in these requirements and can ensure compliance.
7. Communication and partnership: Building a strong partnership with your supplier is essential for a successful procurement process. Clear and open communication, as well as a collaborative approach, can help ensure that the deep drawn components meet your specific needs and expectations.
Overall, when purchasing deep drawn components, it’s important to carefully evaluate suppliers based on their quality, capabilities, and overall ability to meet your specific requirements. By considering these factors and tips, you can make an informed decision and ensure a successful procurement process.
FAQs on Sourcing and Manufacturing deep drawn components in China
Q: What are deep drawn components?
Deep drawn components are metal parts or components that are created through the process of deep drawing. Deep drawing involves using a metal blank or disc and forming it into a desired shape by applying pressure. This results in a seamless, three-dimensional part with high precision.
Q: Why should I consider sourcing and manufacturing deep drawn components in China?
Sourcing and manufacturing deep drawn components in China can offer several advantages. China has a well-established and efficient manufacturing industry with access to a vast range of materials and advanced production technologies. Chinese manufacturers often have extensive experience in deep drawing and can offer competitive pricing due to lower labor and production costs. Additionally, China has a large number of specialized suppliers and can easily scale production to meet any demand.
Q: How do I find suitable suppliers in China for deep drawn components?
To find suitable suppliers in China for deep drawn components, you can utilize various methods. Online platforms such as Alibaba, Made-in-China, and Global Sources provide databases of manufacturers and suppliers. These platforms allow you to search for deep drawn component manufacturers and contact them directly. Additionally, attending trade shows and exhibitions related to metalworking and manufacturing in China can provide opportunities to connect with potential suppliers face-to-face.
Q: What considerations should I keep in mind when sourcing deep drawn components from China?
When sourcing deep drawn components from China, several considerations are important. Firstly, it’s crucial to thoroughly assess the potential suppliers’ capabilities, quality control processes, and certifications. Requesting samples or conducting factory visits can help evaluate their capabilities accurately. Communication is also vital, so ensure that the supplier has a good command of English to avoid miscommunication. Negotiating clear pricing, lead times, and payment terms is essential to establish a mutually beneficial relationship.
Q: How can I ensure the quality of deep drawn components manufactured in China?
To ensure the quality of deep drawn components manufactured in China, it’s best to implement several strategies. Conducting factory audits, quality inspections, and product testing at different stages of production can help identify any potential issues. It is advisable to work with a third-party inspection company specializing in quality control. Maintaining regular communication with the supplier and providing detailed specifications, drawings, and quality requirements is also necessary to minimize any misunderstandings and ensure consistent quality.
Q: What are the typical lead times for manufacturing deep drawn components in China?
Lead times for manufacturing deep drawn components in China can vary depending on factors such as complexity, order quantity, and suppliers’ production capacity. However, on average, lead times usually range from four to eight weeks. It is essential to discuss and agree on realistic lead times with the supplier before commencing production to avoid any unexpected delays.
In conclusion, sourcing and manufacturing deep drawn components in China offer advantages such as cost-effectiveness, a wide range of supplier options, and access to advanced manufacturing technologies. However, careful supplier selection, thorough quality control, and effective communication are necessary to ensure a successful partnership and high-quality products.
Why contact sourcifychina.com get free quota from reliable deep drawn components suppliers?
Sourcifychina.com provides a platform for businesses to connect with reliable deep drawn components suppliers in China. In order to encourage businesses to use their services and connect with these suppliers, Sourcifychina.com offers a free quota for contacting suppliers.
There are several reasons why Sourcifychina.com offers this free quota. Firstly, it allows businesses to test the platform and experience the benefits of connecting with reliable suppliers for their deep drawn components needs. By offering a free quota, businesses can explore the platform without any financial commitment.
Secondly, by offering a free quota, Sourcifychina.com aims to attract businesses to their platform and increase their user base. This benefits both the businesses and the suppliers as it provides a larger pool of potential clients. By expanding their user base, Sourcifychina.com can create a more competitive marketplace, offering businesses a wider range of options for deep drawn components suppliers.
Thirdly, offering a free quota helps Sourcifychina.com gather feedback and improve their platform. Businesses who use the free quota can provide valuable insights and suggestions for enhancements, allowing Sourcifychina.com to continuously improve and optimize their services.
Lastly, by providing a free quota, Sourcifychina.com aims to establish itself as a trusted and reliable platform for businesses looking for deep drawn components suppliers in China. Offering a free quota demonstrates their confidence in the quality and reliability of the suppliers they connect businesses with.
In conclusion, Sourcifychina.com offers a free quota to businesses to encourage them to use their platform and connect with reliable deep drawn components suppliers in China. This strategy helps attract businesses to the platform, gather feedback for improvement, and establish Sourcifychina.com as a trusted marketplace.