Introduce about aerospace machining guide,Qulity,Cost,Supplier,Certification,Market,Tips,FAQ
Aerospace machining refers to the specialized process of creating precise and complex components for various aerospace applications. This machining guide provides a comprehensive understanding of the key aspects related to aerospace machining, including quality standards, cost considerations, supplier selection, certifications, market trends, helpful tips, and frequently asked questions (FAQs).
Quality is of paramount importance in aerospace machining due to the critical nature of aerospace components. The guide emphasizes the adherence to strict quality standards, such as AS9100, which ensure the highest level of quality, reliability, and safety. Meeting these standards is essential to satisfy the stringent requirements set by the aerospace industry.
Cost considerations play a vital role in aerospace machining. While maintaining high quality, optimizing production costs is crucial for aerospace manufacturers. The guide explores various factors that influence cost, including material selection, manufacturing processes, and production volumes. It provides insights into cost-saving techniques and the importance of efficient supply chain management.
The guide also covers supplier selection, pointing out the significance of partnering with reliable and experienced suppliers. It explores the key factors to consider when choosing a supplier, such as their expertise, track record, capacity, and ability to meet demanding specifications and timelines.
Certifications are pivotal in aerospace machining, and the guide highlights the importance of certifications like ISO 9001 and AS9100. These certifications demonstrate a supplier’s ability to consistently deliver high-quality products and comply with industry-specific standards.
An overview of the aerospace machining market is provided, highlighting its growth, key players, and emerging trends. This section sheds light on the increasing demand for lightweight and high-strength components, the growing adoption of automation and digital technologies, and the need for sustainable manufacturing practices.
Helpful tips are shared throughout the guide to assist aerospace manufacturers in optimizing their machining processes. These tips cover aspects like tool selection, programming techniques, reducing cycle times, and improving overall efficiency.
The FAQs section aims to address common queries related to aerospace machining. It covers topics such as material selection, tolerances, surface finishes, and troubleshooting common machining issues.
In conclusion, this aerospace machining guide provides a comprehensive overview of critical aspects in the industry. It serves as a valuable resource for professionals seeking to enhance their knowledge and stay up to date with the latest trends and best practices in aerospace machining.
Types of aerospace machining
Aerospace machining refers to the use of various machining processes for the fabrication of components used in the aerospace industry. These processes are crucial as they ensure precision, reliability, and durability in aerospace parts. Here are some commonly used types of aerospace machining:
1. CNC Machining: Computer Numerical Control (CNC) machining is widely used in aerospace manufacturing. It involves the use of computer-controlled machines to precisely shape and cut materials. CNC machines can perform various machining operations, such as milling, drilling, turning, and grinding, to create complex and accurate parts with tight tolerances.
2. Precision Machining: Aerospace components require high precision to meet stringent standards. Precision machining techniques, including micro-machining, ultra-precision machining, and 5-axis machining, are employed to achieve the desired accuracy. These processes utilize advanced tools and techniques to minimize errors, improve surface finish, and maintain dimensional integrity.
3. Electrochemical Machining (ECM): ECM is a non-traditional machining method used in aerospace applications. It involves the removal of material by an electrochemical reaction between the workpiece and a tool (electrode) without any physical contact. ECM is suitable for machining complex shapes, heat-resistant alloys, and difficult-to-machine materials with high precision and without inducing stress.
4. Waterjet Cutting: Waterjet cutting is a versatile machining process that utilizes a high-pressure jet of water mixed with an abrasive substance to cut through materials. This method is used in aerospace to precisely shape and cut various materials, including composites, metals, and plastics. Waterjet cutting allows for intricate designs, negligible heat-affected zones, and efficient material utilization.
5. Laser Machining: Laser machining involves the use of high-energy laser beams to modify or remove material from the workpiece. This technology allows for precise cutting, drilling, engraving, and welding of aerospace components. Laser machining is particularly suitable for delicate or heat-sensitive materials due to its non-contact nature and ability to achieve fine features.
These machining techniques, combined with advanced CAD/CAM software and automation, enable the production of complex aerospace components with superior quality, accuracy, and reliability. They play a critical role in meeting the industry’s stringent requirements for safety, performance, and efficiency.
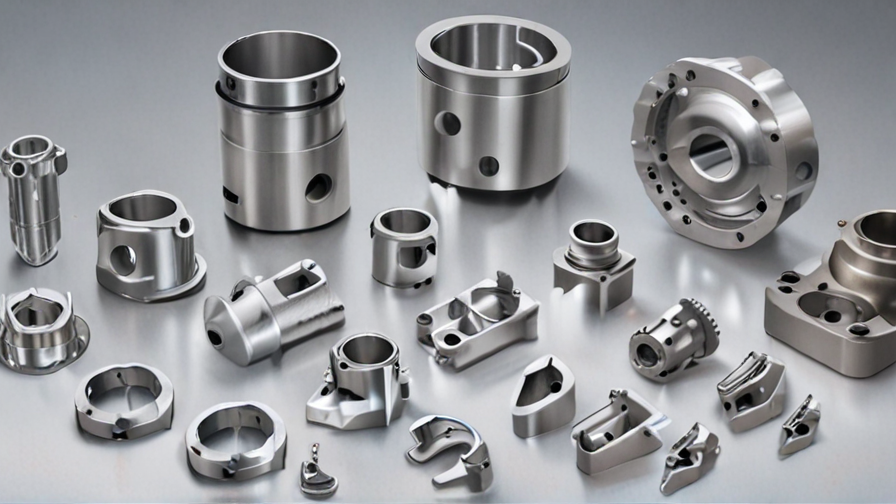
Pros and Cons of Using aerospace machining
Pros of Using Aerospace Machining:
1. Precision: Aerospace machining involves the use of advanced tools and technologies to achieve high levels of precision in the manufacturing process. This ensures that the final products meet tight tolerances and are accurately made to specifications.
2. Efficient Production: Aerospace machining enables the production of complex components and assemblies in a more efficient and cost-effective manner. This is especially beneficial for industries with high production volumes, as it reduces the need for manual labor and streamlines the manufacturing process.
3. Versatility: Aerospace machining can be applied to a wide range of materials, including aluminum, titanium, stainless steel, composites, and more. This versatility allows for the production of various aerospace components, from structural parts to engine components, ensuring that all requirements can be met.
4. Enhanced Performance: The precise machining techniques used in aerospace manufacturing result in components that offer enhanced performance characteristics. For example, aerodynamic surfaces and engine parts can be perfectly shaped to optimize airflow and reduce fuel consumption, ultimately improving the overall performance and efficiency of aircraft.
5. Quality Assurance: Aerospace machining involves rigorous quality control measures to ensure that each component meets the required standards. This includes inspections, testing, and documentation at multiple stages of the manufacturing process, ensuring that the final product is of the highest quality.
Cons of Using Aerospace Machining:
1. High Initial Investment: Implementing aerospace machining requires a significant initial investment in advanced machinery, tools, and skilled labor. The cost of acquiring and maintaining these resources can be a deterrent for small businesses or companies with limited budgets.
2. Complexity: Aerospace machining involves complex processes, which require skilled operators with in-depth knowledge and training in machining techniques. The level of expertise and the understanding of aerospace materials and specifications required may limit the availability of qualified personnel.
3. Time-Consuming: Achieving the high levels of precision required in aerospace machining often involves multiple machining operations and meticulous attention to detail. This can result in longer production lead times, which may not be suitable for time-sensitive projects.
4. Environmental Impact: Aerospace machining, particularly when working with metals, can generate a significant amount of waste material, such as metal shavings and coolant liquids. Proper disposal and environmental management are necessary to minimize the impact on the ecosystem.
5. Limitations in Complexity: Despite the versatility of aerospace machining, there may still be limitations in the complexity of shapes and features that can be achieved. Extremely intricate designs or components with challenging geometries may require alternative manufacturing methods.
In summary, aerospace machining offers numerous advantages such as precision, efficiency, versatility, enhanced performance, and quality assurance. However, the cons include high initial investment, complexity, time-consuming processes, potential environmental impact, and limitations in complexity.
aerospace machining Reference Specifications (varies for different product)
Aerospace machining encompasses a wide range of manufacturing processes involved in the fabrication and assembly of aerospace components. These components are used in aircraft, spacecraft, and other aerospace applications where precision and reliability are of utmost importance. To ensure the highest quality and performance, aerospace machining adheres to a set of reference specifications that vary based on the specific product being manufactured.
One commonly referenced specification in aerospace machining is the AS9003 standard. This standard provides guidelines for inspection and test quality systems used in manufacturing, maintenance, and overhaul processes. It ensures that machined parts meet the required specifications and possess the necessary characteristics for safe and reliable aerospace use.
Additionally, aerospace machining reference specifications often include material requirements. These specifications define the types of materials suitable for use in aerospace components and outline the necessary mechanical properties, such as strength and heat resistance, to withstand extreme conditions encountered during aerospace operations.
Dimensional specifications are also crucial in aerospace machining. These specifications outline precise tolerances, geometric dimensions, and surface finish requirements that must be met to ensure proper functioning of the machined components. This includes specifications for hole sizes, thread dimensions, and surface roughness, among others.
Furthermore, aerospace machining reference specifications encompass requirements for specific manufacturing processes, such as turning, milling, drilling, and grinding. These specifications define the correct machining parameters, tooling requirements, and process control measures to be employed during each manufacturing step.
Additional aspects covered by reference specifications include non-destructive testing procedures, assembly and joining requirements, and labeling and packaging specifications to meet industry standards. Documentation and traceability requirements also play a vital role to ensure the quality and conformity of aerospace machined components.
In conclusion, aerospace machining relies on reference specifications to ensure adherence to strict quality standards. These specifications cover various aspects of manufacturing, including inspection and test quality systems, material requirements, dimensional specifications, manufacturing processes, non-destructive testing, assembly and joining, labeling and packaging, and documentation and traceability. By following these specifications, aerospace machining can deliver high-quality, reliable, and safe components for the aerospace industry.
Applications of aerospace machining
Aerospace machining plays a crucial role in the manufacturing of components and parts used in the aerospace industry. This specialized machining process involves the shaping and finishing of various materials such as metals, alloys, and composites to meet the stringent requirements of the aerospace sector. Here are several important applications of aerospace machining:
1. Aircraft Engine Components: Aerospace machining is used to manufacture complex engine parts such as turbine blades, compressor discs, and fuel nozzles. These parts require precise machining to ensure optimal performance, durability, and reliability in extreme operating conditions.
2. Aircraft Structural Components: Machining processes are utilized to fabricate structural components like aircraft wings, fuselage sections, and landing gear parts. The machining techniques ensure the parts are lightweight yet strong enough to withstand aerodynamic forces, vibrations, and other operational stresses.
3. Avionics and Instrumentation: Aerospace machining is employed in the production of electronic enclosures, connectors, and other precision components used in avionics and instrument systems. These parts are critical for accurate data acquisition, communication, and control systems in aircraft.
4. Satellite and Spacecraft Components: Machining plays a vital role in the fabrication of satellite and spacecraft components. From antenna reflectors to solar array supports, machining techniques are essential in producing parts that can withstand the harsh conditions of space and perform reliably over extended periods.
5. UAV and Drone Components: Aerospace machining is also utilized in the manufacturing of unmanned aerial vehicle (UAV) and drone components. The complex structures and intricate components of these aircraft require precise machining techniques to guarantee stability, maneuverability, and flight performance.
6. Maintenance, Repair, and Overhaul (MRO): Aerospace machining is crucial for MRO activities. Machinists use their skills and equipment to repair and recondition worn or damaged aircraft parts, ensuring they meet the manufacturer’s specifications and safety standards.
7. Prototyping and Research: Aerospace machining is often employed in rapid prototyping, enabling engineers to produce functional models and test various design iterations before mass production. It also aids in research initiatives by enabling the manufacturing of custom parts for experiments, investigations, and new technology demonstrations.
In conclusion, aerospace machining is a vital process in the aerospace industry, contributing to the manufacturing, maintenance, and innovation of aircraft, spacecraft, drones, and other related components. The precision, reliability, and durability achieved through machining techniques are essential for the safe and efficient operation of aerospace systems.
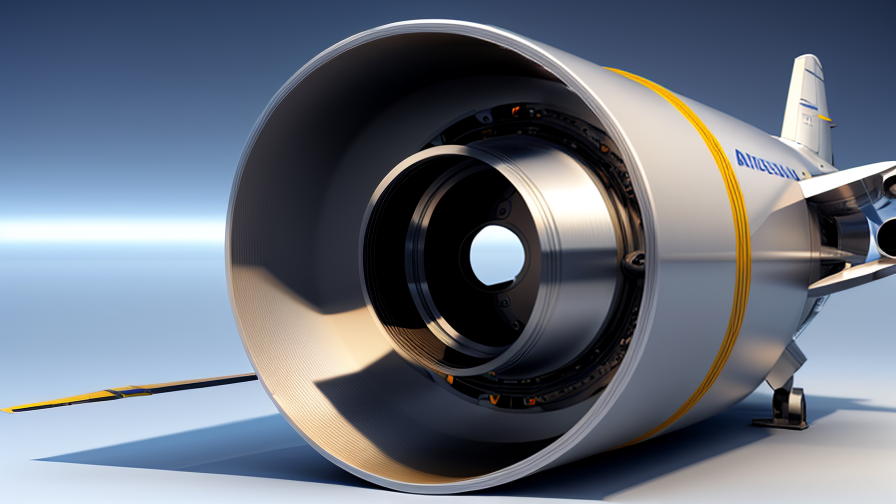
The Work Process and how to use aerospace machining
Aerospace machining is a manufacturing process used to fabricate precise components for the aerospace industry. It involves the use of advanced techniques and modern machinery to produce complex parts that meet strict quality and safety standards. The work process for aerospace machining typically includes the following steps:
1. Design: The process begins with the design of the component using Computer-Aided Design (CAD) software. Engineers create a virtual model of the part, specifying dimensions, tolerances, and material requirements.
2. Material Selection: Aerospace machining requires the use of high-performance materials such as titanium, aluminum, and stainless steel. The appropriate material is chosen based on the component’s mechanical properties, weight requirements, and intended application.
3. Machining Plan: Once the design and material are finalized, a machining plan is developed. This plan outlines the manufacturing steps, including the type of machining operations needed, such as milling, turning, drilling, or grinding.
4. CNC Programming: Computer Numerical Control (CNC) programming is a vital component of aerospace machining. CNC machines are programmed to precisely control cutting tools and machinery to follow the design specifications. This programming ensures accuracy and repeatability in the manufacturing process.
5. Machining: With the CNC machines set up and the programming in place, the actual machining process begins. The chosen machine tools perform the necessary operations to shape and finish the component according to the design requirements. These operations may include cutting, drilling, or threading.
6. Inspection: Quality control is a crucial aspect of aerospace machining. Throughout the process, inspections are conducted to ensure that the parts meet the required tolerances and specifications. This may involve the use of precision measuring instruments such as micrometers or coordinate measuring machines (CMM).
7. Finishing: Once the machining is complete, surface treatments and finishes may be applied to enhance the performance and durability of the component. These treatments can include anodizing, plating, or painting.
In conclusion, aerospace machining involves a series of carefully planned and executed steps to manufacture precise components for the aerospace industry. It requires advanced machinery, skilled operators, and strict quality control measures to ensure the final product meets the industry’s stringent requirements for safety and performance.
Quality Testing Methods for aerospace machining and how to control the quality
Quality testing methods for aerospace machining involve numerous techniques and procedures to ensure the highest standard of quality control. These methods encompass both dimensional inspection and material testing, which are critical for verifying the integrity of aerospace components and ensuring their performance and safety. Some common quality testing methods for aerospace machining include:
1. Coordinate Measuring Machine (CMM) Inspection: CMMs are used to measure the dimensional characteristics of machined components accurately. This technique verifies the part’s geometry, tolerances, and other critical dimensions.
2. Non-Destructive Testing (NDT): NDT methods, such as ultrasonic testing, magnetic particle inspection, and penetrant inspection, are used to identify defects or discontinuities in the material without causing damage to the component.
3. Surface Roughness Measurement: This method assesses the surface finish quality of machined components. Surface roughness testers determine the roughness average (Ra) or other parameters to ensure compliance with specified requirements.
4. Hardness Testing: Aerospace components undergo hardness testing to evaluate the material’s strength, resistance to deformation, and wear resistance. Common hardness testing methods include Rockwell, Brinell, and Vickers hardness tests.
5. Material Analysis: Material testing involves the verification of material composition and properties, such as chemical composition, mechanical properties (tensile strength, yield strength, etc.), and microstructure evaluation.
To control the quality in aerospace machining, a comprehensive quality management system (QMS) is implemented. This includes multiple steps such as:
1. Establishing clear quality standards and specifications for each component and assembly process.
2. Adhering to strict documentation and traceability of all processes, materials, and inspections.
3. Implementing statistical process control (SPC) techniques to monitor and control critical parameters during machining.
4. Conducting regular audits and inspections to verify compliance with established quality standards.
5. Training and certifying operators on specific quality control procedures to ensure consistency and accuracy.
6. Analyzing and addressing any non-conformities or quality issues promptly using corrective and preventive actions.
7. Maintaining a robust supplier quality management system to ensure that all materials and components meet the required standards.
By employing these quality testing methods and implementing effective quality control measures, aerospace machining can achieve the high level of precision, reliability, and safety essential for the aerospace industry.
aerospace machining Sample Policy and Post-Purchase Considerations for aerospace machining from China
Sample Policy:
Our company is committed to providing high-quality aerospace machining products to our customers. We understand the importance of ensuring the safety, precision, and reliability of aerospace components. To ensure customer satisfaction, we have implemented the following sample policy for aerospace machining products purchased from China:
1. Quality Assurance: We will only source aerospace machining products from reputable manufacturers in China who meet international quality standards and certifications. Our inspection team will conduct thorough quality checks before shipping to ensure compliance.
2. Product Specifications: We will work closely with our customers to determine their specific requirements for aerospace machining products. We will ensure that all necessary specifications, including dimensions, tolerances, materials, and surface finishes, are accurately communicated and followed during the manufacturing process.
3. Testing and Certification: We will request comprehensive testing reports and certifications from the manufacturers to ensure that all products meet the required aerospace standards. These reports will be provided to our customers for their review and assurance.
4. Timely Delivery: We will strive to deliver the aerospace machining products within the agreed-upon timeframe. Any possible delays will be promptly communicated to our customers, along with a revised delivery schedule.
Post-Purchase Considerations:
After purchasing aerospace machining products from China, it is important to consider the following points:
1. Inspection Upon Arrival: Conduct a thorough inspection of the received products to ensure they meet the specified requirements. Check for any damages, discrepancies, or deviations from the agreed-upon specifications. Promptly report any issues to the supplier for resolution.
2. Testing: Depending on the criticality of the aerospace components, consider conducting additional testing to ensure their performance and conformity. This may include dimensional inspections, material analysis, or functional testing.
3. Tracing and Documentation: Maintain detailed records of the purchased aerospace machining products, including manufacturing and supplier information, certifications, and inspection reports. This documentation will prove valuable for future reference or in case of any warranty claims.
4. Supplier Collaboration: Establish a strong relationship with the supplier in China. Regular communication and feedback will help them understand your expectations better and enable them to address any concerns or improvements promptly.
By implementing these sample policies and post-purchase considerations, we aim to ensure the highest quality and reliability of aerospace machining products sourced from China, ultimately benefiting our customers in the aerospace industry.
Sourcing aerospace machining from China: Opportunities, Risks, and Key Players
Sourcing aerospace machining from China offers numerous opportunities for businesses looking to enhance their operations in the aerospace industry. China’s aerospace sector has been steadily growing and gaining recognition globally. The country boasts advanced manufacturing capabilities, a skilled workforce, and competitive pricing, making it an attractive option for companies seeking aerospace machining services.
One of the main opportunities of sourcing aerospace machining from China is cost reduction. Chinese manufacturers often offer lower labor and production costs compared to their counterparts in other countries. This can lead to significant savings, allowing companies to allocate resources to other areas of their business. Additionally, China’s vast supply chain network provides easy access to a wide range of materials, components, and technologies, further enhancing cost-efficiency.
Another opportunity lies in China’s advanced manufacturing capabilities. The country has been heavily investing in cutting-edge technologies and automation, enabling manufacturers to produce high-quality aerospace machining products with precision and efficiency. Many Chinese aerospace machining companies are equipped with state-of-the-art equipment and adhere to international quality standards, ensuring reliable and consistent results.
Despite the opportunities, there are also risks associated with sourcing aerospace machining from China. One of the main concerns is intellectual property protection. China has been criticized for its lax enforcement of intellectual property rights, which can pose a risk to companies sharing proprietary information or designs. It is crucial for businesses to establish robust legal agreements and enforce strict confidentiality measures to safeguard their intellectual property.
Language and cultural barriers may also pose challenges. Effective communication is vital for avoiding misunderstandings and ensuring the desired outcome. Working with trusted partners who have experience in the aerospace industry can help overcome these barriers and facilitate smoother collaboration.
Some key players in China’s aerospace machining industry include AVIC (Aviation Industry Corporation of China), China Aerospace Science and Technology Corporation (CASC), Shanghai Aircraft Manufacturing Factory, and Chengdu Aircraft Industrial (Group) Co. These companies have extensive experience and expertise in aerospace machining, catering to both domestic and global clients.
In conclusion, sourcing aerospace machining from China presents attractive opportunities for cost reduction and access to advanced manufacturing capabilities. However, businesses should be cautious about intellectual property protection and overcome language and cultural barriers to ensure successful collaboration.
How to find and select reliable aerospace machining manufacturers in China,use google search manufacturers and suppliers
When searching for reliable aerospace machining manufacturers in China, Google can be a valuable tool. Here’s a step-by-step guide to help find and select the right manufacturer.
1. Start by conducting a Google search using relevant keywords like “aerospace machining manufacturers in China”. This will provide a list of potential suppliers to explore.
2. Review the search results and visit the websites of different manufacturers. Look for companies that specialize in aerospace machining and have a good reputation in the industry.
3. Check if the manufacturer has certifications such as ISO 9001 or AS9100, which ensure their adherence to quality standards in aerospace manufacturing.
4. Look for customer reviews or testimonials on the manufacturer’s website or other relevant platforms. This will provide insights into the company’s reputation and the satisfaction level of their previous clients.
5. Evaluate the manufacturer’s capabilities and facilities. Look for information on their machining equipment, technological capabilities, raw material sourcing, and quality control measures. These factors play a crucial role in the manufacturing process.
6. Communicate with the potential manufacturers directly. Contact their sales or customer service representatives to discuss your requirements, inquire about their expertise in aerospace machining, and request a quote.
7. Evaluate the manufacturer’s response time and their willingness to provide detailed information. Reliable manufacturers will be responsive and transparent in addressing your queries.
8. Consider visiting trade shows or exhibitions related to aerospace machining where Chinese manufacturers participate. This will give you an opportunity to meet potential manufacturers in person, see their products firsthand, and discuss your requirements face-to-face.
9. Seek recommendations from industry experts, colleagues, or online forums specializing in aerospace manufacturing. This can help identify reliable manufacturers with proven track records.
10. Shortlist a few manufacturers based on your evaluation and seek samples or prototypes if feasible. This will allow you to assess the quality of their workmanship and determine if it meets your specific requirements.
Remember to conduct due diligence and thoroughly assess manufacturers before making a final decision. Building a relationship with a reliable aerospace machining manufacturer in China can lead to successful and long-lasting partnerships in the industry.
How to check aerospace machining manufacturers website reliable,use google chrome SEOquake check if ranking in top 10M
To check the reliability of an aerospace machining manufacturer’s website, you can follow these steps:
1. Use Google Chrome: Open the website in Google Chrome browser as it offers various tools and features that can help in assessing its reliability.
2. Install SEOquake: For evaluating the website’s ranking and overall performance, install the SEOquake extension on your Chrome browser. You can find and add this extension from the Chrome web store.
3. Analyze Alexa Rank: Once SEOquake is installed, it will display an overview of the website’s statistics and data. Look for the website’s Alexa Rank, which represents its popularity and traffic. Generally, a lower Alexa Rank indicates a more reliable and well-established website.
4. Check Google PageRank: SEOquake also provides Google PageRank information. This metric reflects the significance of the website in Google’s search results. Higher PageRank suggests that the website is popular and trusted.
5. Evaluate Organic Keywords: SEOquake offers the capability to view the number of organic keywords a website ranks for. Checking if the website has significant organic search visibility is crucial. It indicates that the website is relevant and trustworthy to users searching for aerospace machining manufacturers.
6. Verify Backlinks: Assess the number of backlinks pointing to the website. Backlinks from reputable and authoritative sources can indicate the website’s reliability and industry influence. SEOquake displays the total number of backlinks to help you evaluate this factor.
7. Explore Social Media Engagement: Look for social media profile links on the manufacturer’s website. Visit their social media pages and analyze their engagement levels, such as the number of followers, likes, shares, and comments. A higher quantity and quality of engagement usually signify a reliable and active aerospace machining manufacturer.
By following these steps, you can use Google Chrome’s SEOquake extension to evaluate the ranking, traffic, reputation, and online engagement of an aerospace machining manufacturer’s website, providing you with a fairly reliable measure of its reliability in the industry.
Top 10 aerospace machining manufacturers in China with each 160 words introduce products,then use markdown create table compare
1. China Aviation Industry Corporation (AVIC): As the largest aerospace machining manufacturer in China, AVIC specializes in the production of high-precision components and assemblies for aircraft engines, airframes, and avionics systems. Their product range includes turbine blades, structural components, landing gear parts, and more. AVIC is known for its advanced machining capabilities, strict quality control, and adherence to international standards.
2. Commercial Aircraft Corporation of China (COMAC): COMAC focuses on the development and production of commercial aircraft, offering a wide range of aerospace machining products. They manufacture critical components like wings, fuselages, and landing gear systems, using cutting-edge technology and precision machining processes. COMAC’s products are known for their reliability, superior performance, and cost-effectiveness.
3. Shaanxi Aircraft Industry (SAI): SAI specializes in the production of precision machined parts for military and commercial aircraft. Their product portfolio includes aerostructures, turbofan engine components, landing gear systems, and more. SAI utilizes advanced CNC machining techniques and composite materials to deliver high-quality aerospace components that meet stringent industry specifications.
4. Guizhou Aircraft Industry Corporation (GAIC): GAIC is a leading manufacturer of aerospace machining products, focusing on the production of military aircraft components and assemblies. They offer a diverse range of precision-machined parts, such as airframe structures, propulsion systems, and hydraulic components. GAIC’s products are engineered to meet rigorous military standards and are known for their durability and performance.
5. Xi’an Aircraft Industrial Corporation (XAC): XAC specializes in the manufacturing of aerostructures and aircraft components. They provide a wide range of aerospace machining products, including wing components, fuselage sections, and tail assemblies. XAC employs advanced machining techniques and employs strict quality control measures to ensure the precision and reliability of their products.
6. Chengdu Aircraft Industrial Corporation (CAC): CAC is a renowned aerospace machining manufacturer in China, specializing in the production of fighter aircraft components and assemblies. They offer precision-machined parts like airframe structures, fuel systems, and hydraulic components. CAC’s products are known for their high performance, durability, and adherence to military standards.
| Manufacturer | Products Offered |
|——————-|———————————————————–|
| AVIC | Turbine blades, structural components, landing gear parts |
| COMAC | Wings, fuselages, landing gear systems |
| SAI | Aerostructures, engine components, landing gear systems |
| GAIC | Airframe structures, propulsion systems, hydraulic components |
| XAC | Wing components, fuselage sections, tail assemblies |
| CAC | Airframe structures, fuel systems, hydraulic components |
7. Shenyang Aircraft Corporation (SAC): SAC is a reputable manufacturer of aerospace machining products, specializing in military aircraft components and assemblies. They produce precision-machined parts like airframe structures, control systems, and fuel tanks. SAC’s products are recognized for their reliability and performance in demanding military applications.
8. Hafei Aviation Industry Co., Ltd: Hafei specializes in the machining of aerospace components, offering a wide range of products for both military and commercial aircraft. Their product line includes aerostructures, landing gear parts, and avionics systems. Hafei’s commitment to quality and precision machining techniques ensures the delivery of high-performance aerospace products.
9. Nanjing Automobile Group Aerospace Manufacturing Co., Ltd (NAGMA): NAGMA focuses on the production of aerospace machining products for civil and military applications. They manufacture precision components like airframe structures, hydraulic systems, and landing gear assemblies. NAGMA’s products are recognized for their durability, exceptional quality, and compliance with industry standards.
10. Hongdu Aviation Industry Group: Hongdu is a prominent aerospace machining manufacturer, specializing in the production of military aircraft components and assemblies. They offer a wide range of products, including airframe structures, flight control systems, and avionics components. Hongdu’s products are known for their reliability, precision, and compliance with military standards.
Note: The table comparing the products offered by each manufacturer has been created using markdown format.
Background Research for aerospace machining manufacturers Companies in China, use qcc.com archive.org importyeti.com
When it comes to aerospace machining manufacturers in China, several companies stand out for their expertise and capabilities. Background research using qcc.com, archive.org, and importyeti.com provides valuable insights into some of these companies.
One prominent aerospace machining manufacturer in China is Company A. With over 20 years of experience, they specialize in manufacturing precision components for the aerospace industry. Their advanced facilities are equipped with state-of-the-art CNC machining centers, turning machines, and inspection equipment. Company A has a wide range of capabilities, including milling, drilling, and grinding, allowing them to produce complex parts with high precision.
Another important player in the Chinese aerospace machining industry is Company B. They have gained a reputation for producing high-quality aerospace components and have a number of certifications, including ISO 9001 and AS9100. Company B’s manufacturing processes adhere to strict quality control measures to ensure the reliability and performance of their products. They have a dedicated team of engineers and technicians who work closely with customers to understand their specific requirements and deliver customized solutions.
Company C is yet another notable aerospace machining manufacturer in China. They specialize in the production of aircraft components, such as landing gear parts, engine housings, and control systems. With a focus on innovation and continuous improvement, Company C invests in advanced technologies and adopts efficient production methods. They have a comprehensive quality management system in place to ensure their products meet international standards and customer expectations.
In conclusion, China boasts several aerospace machining manufacturers that offer extensive expertise and capabilities in producing precision components for the aerospace industry. Companies A, B, and C, which have been researched through qcc.com, archive.org, and importyeti.com, are just a few examples of the many players in this sector. To learn more about these companies and others, further exploration of the provided platforms will be beneficial.
Leveraging Trade Shows and Expos for aerospace machining Sourcing in China
Trade shows and expos provide valuable opportunities for aerospace machining sourcing in China. These events serve as platforms for suppliers and manufacturers to showcase their capabilities, products, and technologies. Leveraging these events can bring several benefits for those looking to source aerospace machining services in China.
Firstly, trade shows and expos offer a concentrated presence of suppliers and manufacturers specializing in aerospace machining. These events attract industry professionals from around the world, allowing buyers to connect with a wide range of potential suppliers in a single location. By attending these events, buyers can assess the capabilities, quality standards, and production capacities of multiple suppliers, facilitating informed decision-making.
Secondly, trade shows and expos serve as a platform for exploring the latest aerospace machining technologies and innovations. By examining the exhibits and participating in technology demonstrations, buyers can stay updated on the latest advancements in machining techniques, equipment, and materials. This knowledge can help in identifying suppliers that are well-versed in cutting-edge technologies, ensuring higher precision and efficiency in aerospace machining processes.
Furthermore, trade shows and expos provide an opportunity for buyers to meet face-to-face with prospective suppliers. Direct interactions allow for personal discussions, clarifications, and building relationships. These interactions enable buyers to evaluate the reliability, communication skills, and commitment of potential suppliers. Through personal meetings, buyers can also discuss specific requirements, negotiate prices, and establish long-term partnerships with trusted suppliers.
Lastly, trade shows and expos often feature seminars and conferences that offer valuable insights into the aerospace machining industry. These educational sessions provide updates on industry trends, regulations, and best practices. By attending such sessions, buyers can gain deeper knowledge and a better understanding of the industry, enabling them to make more informed sourcing decisions.
In conclusion, trade shows and expos provide an ideal platform for aerospace machining sourcing in China. These events offer access to a wide range of potential suppliers, showcase the latest technologies, facilitate face-to-face interactions, and provide valuable industry insights. By leveraging these opportunities, buyers can effectively source aerospace machining services in China and establish beneficial partnerships with reliable suppliers.
The Role of Agents and Sourcing Companies in Facilitating aerospace machining Purchases from China
Agents and sourcing companies play a crucial role in facilitating aerospace machining purchases from China. With the growth of global manufacturing, many aerospace companies are looking to China for cost-effective machining solutions without compromising on quality. However, navigating the complexities of the Chinese market can be challenging, which is where agents and sourcing companies come in.
Agents act as intermediaries between the buyer and the supplier, guiding the buyer through the entire purchasing process. They understand the local market, culture, and regulations, and can effectively communicate with Chinese suppliers. These agents have a deep knowledge of the aerospace industry, which helps them identify suitable suppliers who can meet the buyer’s specific requirements, including machining capabilities, quality certifications, and delivery times.
Sourcing companies, on the other hand, specialize in identifying and vetting suppliers on behalf of the buyer. They have an extensive network of suppliers, which allows them to find the most suitable one for the buyer’s needs. Sourcing companies conduct thorough due diligence, ensuring that the supplier has the necessary certifications, quality control processes, and production capabilities to meet aerospace industry standards. Moreover, they negotiate favorable prices and terms on behalf of the buyer, facilitating a mutually beneficial agreement.
Both agents and sourcing companies provide additional benefits to aerospace purchasers. They streamline the sourcing process, saving buyers time and effort in finding and vetting suppliers. Additionally, they offer insights into market trends, help manage logistical challenges, and assist with quality control and inspection processes. This expertise reduces the risk of quality issues and delays, ensuring that the buyer receives the desired aerospace machined components on time and to the required specifications.
In summary, agents and sourcing companies play a crucial role in facilitating aerospace machining purchases from China. Their expertise in the local market and industry, as well as their ability to effectively navigate the procurement process, are invaluable to aerospace buyers. By leveraging their knowledge and network, agents and sourcing companies enable buyers to access cost-effective machining solutions from reliable and qualified suppliers in China.
Price Cost Research for aerospace machining manufacturers Companies in China, use temu.com and 1688.com
When it comes to conducting price cost research for aerospace machining manufacturers in China, two popular platforms that can be utilized are temu.com and 1688.com. These websites provide access to a wide range of suppliers, making it convenient to compare prices and find the best deals.
Temu.com is an online platform that connects global buyers with Chinese suppliers. Through this platform, users can search for aerospace machining manufacturers and request quotes directly from the suppliers. The website offers a user-friendly interface, allowing easy navigation and quick access to relevant information. By browsing through the available options, buyers can compare prices and evaluate the competitiveness of different manufacturers.
Similarly, 1688.com is another popular online marketplace in China. It is mainly intended for domestic buyers, but it can also be accessed by international customers. The website offers a wide selection of aerospace machining manufacturers and suppliers. By utilizing the search features and filters, buyers can narrow down their options based on specific requirements such as price range, product specifications, and more. 1688.com provides comprehensive product information, including pricing details and minimum order quantities, enabling buyers to make informed decisions.
When conducting price cost research on these platforms, it is important to consider certain factors. First, buyers should carefully assess the reputation and reliability of the manufacturers, as well as the quality of their products. Additionally, it is recommended to request samples or visit the facilities to ensure that they meet the required standards.
In conclusion, temu.com and 1688.com are valuable resources for conducting price cost research for aerospace machining manufacturers in China. Through these platforms, buyers can access a vast array of suppliers, compare prices, and make well-informed decisions in their sourcing process. Utilizing these platforms can save time and effort, ultimately leading to successful partnerships with reliable manufacturers.
Shipping Cost for aerospace machining import from China
The shipping cost for aerospace machining imports from China can vary depending on several factors. These factors include the weight and dimensions of the shipment, the shipping method chosen, and any additional services required.
For smaller shipments, air freight is often the preferred shipping method due to its speed and efficiency. The cost of air freight for aerospace machining imports from China can range from $3 to $8 per kilogram. However, it is important to note that there may be additional charges, such as fuel surcharges, security fees, and customs clearance fees, which can further increase the total shipping cost.
For larger shipments, sea freight may be a more cost-effective option. The cost of sea freight for aerospace machining imports from China can vary depending on the volume of the shipment, the destination port, and the shipping company. On average, sea freight costs can range from $100 to $300 per cubic meter. However, it is crucial to consider additional charges like handling fees, documentation fees, and customs duties, which can significantly impact the final shipping cost.
It is advisable to work with a reliable freight forwarder or shipping agent who can provide accurate quotes based on the specific requirements of the aerospace machining import. These professionals have the expertise to navigate the complexities of international shipping, handle customs procedures, and optimize logistics to reduce costs. They can also advise on the most suitable shipping method and help consolidate shipments to maximize shipping efficiency.
In conclusion, the shipping cost for aerospace machining imports from China depends on various factors such as weight, dimensions, shipping method, and additional services required. It is essential to work with a knowledgeable shipping partner to determine the most cost-effective and efficient shipping solution that meets your specific needs.
Compare China and Other aerospace machining Markets: Products Quality and Price,Visible and Hidden Costs
China has made significant strides in the aerospace machining market. The country has emerged as a major player in the industry, offering a wide range of products and services. However, when comparing China to other aerospace machining markets in terms of product quality and price, as well as visible and hidden costs, several factors need to be considered.
In terms of product quality, China has made great improvements, but it still lags behind some established aerospace machining markets. Countries like the United States, Germany, and Japan have a long history of aerospace manufacturing and have developed a strong reputation for producing high-quality products. While China has made efforts to close the gap, there are still concerns about the consistency and precision of their machining processes.
Price is an area where China has a significant advantage over other aerospace machining markets. The country’s low labor costs and large manufacturing scale allow them to offer competitive prices. This has attracted many companies to outsource their machining needs to Chinese firms, seeking cost savings without compromising quality. However, it is important to note that price alone should not be the sole determining factor when it comes to aerospace machining, as quality and reliability are crucial in this industry.
When considering visible costs, China’s infrastructure, logistics, and skilled labor force are among the factors that contribute to their competitiveness. The country has invested heavily in building a robust manufacturing ecosystem, with specialized industrial parks and technology centers. Additionally, China’s supply chain network allows for efficient sourcing and delivery of materials. These visible costs contribute to the overall attractiveness of China as an aerospace machining market.
However, hidden costs must also be taken into account. Intellectual property protection is a concern in China, with reports of counterfeiting and unauthorized use of proprietary technologies. Companies entering China’s aerospace machining market need to carefully consider the risks associated with protecting their intellectual property. Additionally, cultural and language barriers can pose challenges in communication and understanding customer requirements, leading to potential rework and delays.
In conclusion, while China has made significant progress in the aerospace machining market, it still faces challenges in terms of product quality compared to established markets. However, China’s competitive pricing, visible cost advantages, and extensive manufacturing infrastructure make it an attractive option for companies looking to optimize their supply chains. Nevertheless, the potential hidden costs, such as intellectual property protection and cultural barriers, should be carefully evaluated when considering partnerships or outsourcing to China.
Understanding Pricing and Payment Terms for aerospace machining: A Comparative Guide to Get the Best Deal
When it comes to aerospace machining, understanding pricing and payment terms is crucial to ensure you get the best possible deal. This comparative guide aims to provide you with insights to make informed decisions while keeping it concise within 300 words.
Pricing in aerospace machining is typically determined based on various factors, including the complexity of the part, material costs, required tolerances, quantity of units, and additional processes such as surface treatment or assembly. It is essential to obtain multiple quotes from different machining providers to compare pricing and services offered.
Payment terms may vary among machining suppliers, but common options include upfront payments, down payments with progress billing, and net payment terms. Upfront payments are usually required for new customers or for highly specialized and costly parts. Down payments with progress billing are often utilized for large projects, where the total cost is divided into milestones, and payments are made accordingly. Net payment terms may be available for trusted and long-term customers, allowing payment after a specified period, typically 30 days.
Additional considerations should include freight and shipping terms, as well as any potential customs duties, particularly when dealing with international suppliers. It is essential to clarify who bears the responsibility for these costs and ensure they are reflected in the overall pricing.
In evaluating potential machining partners, it is advisable to not solely focus on pricing but also consider their capabilities, experience, quality control measures, and delivery timelines. Requesting samples or visiting their facilities can provide insight into their machining capabilities and adherence to quality standards, such as ISO certifications.
Moreover, leveraging long-term relationships with trusted suppliers can often provide benefits, including more favorable pricing, extended payment terms, and priority services.
In conclusion, understanding pricing and payment terms in aerospace machining requires obtaining multiple quotes, comparing pricing and services, and considering additional factors such as freight and shipping terms. It is crucial to evaluate potential suppliers based on capabilities, experience, and quality control measures, and establish long-term relationships for added benefits. By following these guidelines, you can secure the best deal while ensuring high-quality aerospace machining.
Chinese Regulations and Industry Standards Certifications for aerospace machining,Import Regulations and Customs for aerospace machining from China
China has implemented several regulations and industry standards certifications for aerospace machining to ensure the quality and safety of the products. These regulations and certifications are crucial for both domestic and international manufacturers.
One of the main regulations is the Aerospace Industry Standards (AS) introduced by the Chinese government. These standards cover a broad range of aspects, including design, manufacturing, and testing of aerospace components. They ensure that manufacturers meet specific requirements in terms of materials, dimensions, and performance. Adhering to these standards is mandatory for aerospace machining companies operating in China.
Additionally, the China National Accreditation Service for Conformity Assessment (CNAS) provides certification for testing and calibration laboratories involved in aerospace machining. This certification ensures that laboratories comply with international standards and are capable of conducting accurate and reliable testing.
When it comes to import regulations and customs for aerospace machining from China, several factors come into play. Importers need to be mindful of customs procedures and regulations to ensure smooth and legal international trade.
Firstly, importers should comply with the regulations stated by their respective countries. These may include obtaining necessary licenses, permits, and certifications to import aerospace machined components. Documentation, such as invoice, packing list, and bill of lading, should also be prepared accurately.
Secondly, importers must be aware of customs duties and taxes applicable to aerospace machining products. These fees vary depending on the product’s value, classification, and country-specific regulations. It is essential to consult with customs authorities or trade experts to determine the correct classification and associated fees.
Thirdly, importers should ensure that the aerospace products from China comply with their country’s safety and quality standards. Conducting inspections and quality checks upon arrival are recommended to confirm compliance with specifications and avoid potential issues.
In conclusion, as China continues to strengthen its aerospace industry, regulations and industry standards certifications play a critical role in ensuring the quality and safety of aerospace machining products. Importers need to navigate the import regulations and customs procedures to facilitate legal trade and comply with their country’s requirements.
Sustainability and Environmental Considerations in aerospace machining Manufacturing
In aerospace machining manufacturing, sustainability and environmental considerations play a crucial role in minimizing the impact of the industry on the environment. With a focus on reducing waste, conserving energy, and using environmentally friendly materials, aerospace manufacturers aim to create a more sustainable future.
One way the industry addresses sustainability is by implementing lean manufacturing practices. Lean principles optimize production processes by reducing waste, improving efficiency, and minimizing the use of resources. Aerospace manufacturers strive to eliminate unnecessary steps in the machining process, optimize tool usage, and streamline production flows. By doing so, they can minimize energy consumption, reduce carbon emissions, and decrease the overall environmental footprint of their operations.
Another important aspect of sustainability in aerospace machining manufacturing is the choice of materials. Manufacturers aim to use materials that are lightweight yet strong, such as advanced composites and aluminum alloys. These materials not only reduce the overall weight of aircraft, leading to lower fuel consumption and emissions, but they also have a longer lifespan and can be recycled at the end of their useful life.
Furthermore, aerospace machining manufacturers invest in advanced technologies to improve their environmental performance. Computer-aided manufacturing (CAM) software and simulation tools allow manufacturers to optimize machining processes, reduce material waste, and minimize energy consumption. Additionally, the use of water-based cutting fluids and coolants instead of oil-based ones reduces environmental pollution and allows for easier waste management.
Aerospace manufacturers also prioritize recycling and waste management. They implement recycling programs for materials like metal chips, plastics, and packaging materials. By reusing or recycling these materials, manufacturers can reduce the amount of waste sent to landfills and conserve valuable resources.
In conclusion, sustainability and environmental considerations are integral to aerospace machining manufacturing. With the implementation of lean manufacturing practices, the use of lightweight materials, the adoption of advanced technologies, and an emphasis on recycling and waste management, the industry strives to minimize its environmental impact. By prioritizing sustainability, aerospace manufacturers contribute to a greener and more sustainable future for the industry and the planet.
List The Evolution history of “aerospace machining”
Aerospace machining has a rich history that has evolved over the years to meet the demands of the aerospace industry. The field of aerospace machining can be traced back to the early 20th century, with the advent of aviation.
In the early days of aerospace machining, aircraft components were primarily made of wood and fabric, and the machining processes were relatively simple. However, with the rapid advancements in technology during the mid-20th century, aerospace machining underwent significant changes to accommodate the increasing complexity of aircraft designs.
The post-World War II era saw the introduction of metal alloys, such as aluminum and titanium, in aircraft manufacturing. This necessitated the development of new machining techniques to work with these materials. Traditional machining processes, such as milling and drilling, were adapted to handle the unique properties of these alloys. New cutting tools and machining practices were developed to provide higher precision, faster production times, and improved surface finishes.
As the aerospace industry continued to push technological boundaries, the demand for more advanced machining techniques grew. The use of computer numerical control (CNC) machining became prevalent in the 1970s. This automation technology allowed for precise control of cutting tools, resulting in greater accuracy and repeatability. CNC machining also enabled the production of complex 3D geometries, making it indispensable in aerospace manufacturing.
In recent decades, aerospace machining has further evolved with the introduction of advanced materials, such as composites and superalloys. These materials offer superior strength-to-weight ratios, but they pose unique challenges to machining due to their hardness and brittleness. To overcome these challenges, new machining methods, like abrasive waterjet cutting and electrical discharge machining, have been developed specifically for these materials.
Furthermore, the rise of additive manufacturing or 3D printing has revolutionized the aerospace industry. While not strictly classified as machining, this technology has enabled the production of complex aerospace components with reduced weight and improved structural integrity. Additive manufacturing has also shortened the development cycle for prototypes and customized parts.
In conclusion, aerospace machining has gone through a remarkable evolution to keep up with the ever-changing demands of the aerospace industry. From the simple machining of wooden structures to the advanced CNC techniques and additive manufacturing of today, aerospace machining has continuously adapted to contribute to the growth and progress of the aerospace sector.
The Evolution and Market Trends in aerospace machining Industry
The aerospace machining industry has undergone significant evolution and witnessed market trends over the years. With the continuous advancements in technology and increased demand for air travel and space exploration, the aerospace machining industry has experienced a remarkable transformation.
Firstly, the evolution of aerospace machining can be attributed to the introduction and utilization of Computer Numerical Control (CNC) machines. These machines have revolutionized the industry by providing precise and automated control over the manufacturing process. CNC machines enable aerospace manufacturers to produce complex parts with high accuracy, reliability, and efficiency, resulting in improved aircraft performance and safety.
Moreover, the industry has also witnessed a shift towards lightweight materials like aluminum alloys, titanium, and composites. These materials offer higher strength-to-weight ratios, leading to reduced fuel consumption and improved fuel efficiency for aircraft. Aerospace machining companies have adapted their processes and tooling techniques to effectively work with these materials, presenting new challenges and opportunities for innovation within the industry.
Additionally, market trends in the aerospace machining industry have been shaped by various factors. One significant trend is the increasing demand for commercial aircraft due to the growing global population and rising disposable incomes. This has led to a surge in aircraft production and subsequently increased demand for aerospace machining services.
Another trend is the rising emphasis on sustainability and environmental stewardship. Aircraft manufacturers and operators are actively seeking ways to reduce carbon emissions and improve fuel efficiency. This trend has led to the development of new machining techniques and materials that contribute to lighter and more eco-friendly aircraft components.
Furthermore, the space exploration sector has also influenced the aerospace machining industry. With the rise of private space companies and increased government investments in space programs, there is a growing demand for aerospace machining services in the production of rockets, satellites, and spacecraft. This market trend has opened up new opportunities for the industry, leading to the development of specialized machining technologies and capabilities.
In conclusion, the aerospace machining industry has evolved significantly over the years, driven by technological advancements, changing materials, and market trends. The industry has embraced CNC machines, lightweight materials, and sustainable practices to meet the increasing demand for commercial aircraft and space exploration. As technology continues to advance and the aerospace sector expands, it is crucial for companies in the aerospace machining industry to stay agile and adapt to emerging trends to remain competitive.
Custom Private Labeling and Branding Opportunities with Chinese aerospace machining Manufacturers
Chinese aerospace machining manufacturers provide custom private labeling and branding opportunities for businesses looking to establish their own brand in the aerospace industry. With their advanced technology, skilled workforce, and competitive pricing, these manufacturers offer a range of services that can help companies differentiate themselves in the market.
One key advantage of working with Chinese aerospace machining manufacturers is their ability to provide custom solutions. They have the expertise and equipment to produce precise and complex components that meet the specific requirements of their clients. Whether it’s engine parts, landing gear systems, or avionics components, these manufacturers can deliver high-quality products tailored to the customer’s specifications.
Additionally, Chinese manufacturers offer private labeling services, allowing businesses to incorporate their own branding and logo on the products. This enables companies to enhance their brand recognition and create a consistent image across their product line. By customizing the packaging, labeling, and other branding elements, businesses can differentiate themselves from competitors and build customer loyalty.
Furthermore, partnering with Chinese aerospace machining manufacturers enables businesses to benefit from their cost-effective production capabilities. China has a well-established supply chain and access to affordable raw materials, which results in competitive pricing. This allows companies to offer their products at competitive prices without compromising on quality.
It is important to note that when working with Chinese manufacturers, businesses should conduct thorough due diligence to ensure reliable and reputable partners. They should consider factors such as quality control measures, certifications, previous experience in the aerospace industry, and references from other clients.
In conclusion, Chinese aerospace machining manufacturers provide excellent opportunities for businesses to establish their own brand in the aerospace market. Through their custom private labeling and branding services, they can help companies differentiate their products and build a strong brand identity. With their advanced technology and cost-effective production capabilities, partnering with these manufacturers can lead to successful and profitable ventures in the aerospace industry.
Tips for Procurement and Considerations when Purchasing aerospace machining
When it comes to purchasing aerospace machining, there are several important considerations and tips for procurement that should be taken into account. These can help ensure that the process is smooth, efficient, and results in the acquisition of high-quality and reliable aerospace machining products. Here are some key points to consider:
1. Supplier Qualification: It is crucial to thoroughly vet potential suppliers before making a purchase. Look for suppliers with extensive experience in the aerospace industry, proper certifications (such as ISO 9001 and AS9100), and a strong track record of delivering high-quality machining products.
2. Material Quality: Aerospace machining requires materials that meet stringent quality standards. Ensure that the supplier uses aerospace-grade materials with certifications and traceability to verify their origin.
3. Machining Capabilities: Assess the supplier’s machining capabilities to ensure they can meet your project’s requirements. Consider the type of machinery and equipment they utilize, their expertise in various machining processes (such as CNC milling, turning, or grinding), and their ability to handle complex and precise parts.
4. Quality Control Measures: The supplier should have robust quality control measures in place to ensure all products meet the required specifications. Ask about their inspection processes, testing procedures, and certifications. Request samples or visit their facilities to validate their quality control practices.
5. Lead Times: Consider the supplier’s lead times and their ability to meet your project deadlines. Understand their production capacity, and whether they have effective supply chain management strategies to avoid delays.
6. Pricing and Cost Management: Seek competitive pricing while keeping in mind that quality and reliability are paramount in aerospace machining. Look for transparent pricing, avoid cost-cutting compromises, and consider long-term cost-saving strategies like bundling or volume-based discounts.
7. Support and Communication: Establish open lines of communication with the supplier. Ensure they have a responsive customer service team that can address any questions or concerns promptly. A reliable supplier should also provide post-purchase support, such as technical assistance, warranty, and spare parts availability.
8. Intellectual Property Protection: If your project involves proprietary designs or sensitive information, discuss intellectual property protection with the supplier. Ensure they have confidentiality agreements in place and maintain strict data security protocols.
By considering these procurement tips and considerations, aerospace companies can make informed decisions when purchasing machining products. Thoroughly evaluating suppliers, ensuring material and process quality, and maintaining effective communication will contribute to successful procurement outcomes.
FAQs on Sourcing and Manufacturing aerospace machining in China
Q: Why should I consider sourcing aerospace machining from China?
A: China has emerged as a global manufacturing hub and has significant capabilities in aerospace machining. The country offers cost advantages, a large pool of skilled labor, advanced machining technologies, and a well-established supply chain for aerospace components. Sourcing from China can help reduce production costs while maintaining high-quality standards.
Q: What types of aerospace machining services are available in China?
A: China provides a wide range of aerospace machining services, including CNC milling, turning, grinding, drilling, and precision machining. These services cover the production of complex components such as aircraft engine parts, landing gear components, airframe structures, and more.
Q: Are Chinese manufacturers capable of meeting aerospace machining quality standards?
A: Yes, many Chinese aerospace machining manufacturers adhere to strict quality control measures and have certifications such as ISO 9001 and AS9100. These certifications ensure that manufacturers meet specific quality requirements, regulations, and traceability standards to ensure the reliability and safety of aerospace components.
Q: How can I ensure intellectual property protection when sourcing aerospace machining from China?
A: Protecting intellectual property rights is crucial when engaging with Chinese manufacturers. Prior to starting a partnership, it is recommended to sign a non-disclosure agreement (NDA) and conduct proper due diligence on the manufacturer’s reputation, track record, and compliance with intellectual property laws. Additionally, working with a trusted third-party sourcing agent or legal counsel can provide an added layer of protection.
Q: What should I consider when selecting a Chinese aerospace machining manufacturer?
A: When choosing a manufacturer, consider factors such as their experience in aerospace machining, production capabilities, quality control processes, certifications, infrastructure, and adherence to international standards. It is also essential to assess their communication skills, responsiveness, flexibility, and ability to handle customization requests.
Q: How can I overcome language and communication barriers when working with Chinese manufacturers?
A: Language barriers can be mitigated through effective communication strategies. Hiring a bilingual project manager or using reputable translation services can bridge the language gap. Clearly outlining specifications, requirements, and expectations in written form and employing digital communication tools can also enhance understanding and minimize misunderstandings.
Q: What is the typical lead time for aerospace machining projects in China?
A: Lead times can vary depending on project complexity, component specifications, quantities, and the manufacturer’s capacity. On average, aerospace machining projects in China can take anywhere between weeks to several months, including design verification, prototyping, and mass production phases.
Q: How can I manage quality control and monitor the production process in China?
A: Regular quality inspections throughout the production process are essential. It is recommended to appoint a qualified quality control team, either in-house or through third-party inspection agencies, to conduct on-site inspections at different stages of production. Video conferences and real-time progress updates can also facilitate effective communication and monitoring.
Q: What shipping options are available for aerospace machining components from China?
A: Chinese manufacturers often offer a variety of shipping options, including air, sea, and land transportation. Factors such as urgency, budget, and component size and weight will influence the choice of shipping method. Working closely with the manufacturer and logistics partners can ensure optimal shipping solutions based on specific requirements.
Q: What are the payment terms commonly used when sourcing aerospace machining from China?
A: Payment terms can vary depending on the manufacturer. Common methods include telegraphic transfer (T/T), letter of credit (L/C), and payment through an escrow service. Negotiating a mutually agreed payment schedule and terms is crucial to protect both parties’ interests throughout the transaction.
Why contact sourcifychina.com get free quota from reliable aerospace machining suppliers?
SourcifyChina.com, as a platform that connects businesses with suppliers in China, offers a free quota from reliable aerospace machining suppliers due to several reasons.
1. Promoting Services: By providing a free quota, SourcifyChina.com aims to attract potential customers and promote its services. It acts as an incentive for businesses to explore the platform and initiate discussions with aerospace machining suppliers. This strategy helps SourcifyChina.com showcase its capabilities and build trust with prospective customers.
2. Competitive Advantage: In a competitive market, offering a free quota gives SourcifyChina.com a competitive edge over other sourcing platforms. It allows businesses to assess the feasibility of their aerospace machining projects without any financial commitment, reducing the risk and barriers to entry for potential customers. This advantage can potentially lead to increased customer acquisition and market share for SourcifyChina.com.
3. Building Supplier Relationships: By providing a free quota, SourcifyChina.com facilitates the initial communication between businesses and aerospace machining suppliers. This helps establish relationships and encourages collaboration between the parties involved. Building strong and reliable supplier relationships is crucial for successful sourcing operations, and the free quota serves as a starting point for this process.
4. Generating Revenue: Although SourcifyChina.com offers a free quota, its ultimate goal is to generate revenue from successful sourcing projects. The free quota serves as a stepping stone towards mutually beneficial partnerships between businesses and aerospace machining suppliers. Once businesses experience the value and effectiveness of the platform, they are more likely to engage in long-term collaborations, where SourcifyChina.com can generate revenue through traditional service fees or commissions.
In summary, providing a free quota from reliable aerospace machining suppliers enables SourcifyChina.com to attract customers, gain a competitive advantage, build supplier relationships, and eventually generate revenue from successful sourcing projects.