Introduce about alloy core guide,Qulity,Cost,Supplier,Certification,Market,Tips,FAQ
The Alloy Core Guide is a comprehensive resource that provides information about the various aspects of alloy cores used in different industries. The guide covers topics such as quality, cost, suppliers, certification, market trends, tips, and frequently asked questions.
When it comes to the quality of alloy cores, it is crucial to consider their composition, strength, and durability. The guide elaborates on the different types of alloys commonly used and their specific characteristics, helping users make informed decisions based on their requirements.
Cost is another important factor to consider when choosing alloy cores. The guide provides insights into the pricing factors, including material cost, production processes, and market fluctuations. This enables users to assess the cost-effectiveness of different alloy cores and select the most suitable option for their specific needs.
Finding reliable suppliers is vital for obtaining high-quality alloy cores. The guide offers suggestions and strategies for identifying reputable suppliers, ensuring that users can establish strong partnerships with trustworthy manufacturers or distributors.
Certification plays a significant role in assuring the quality and reliability of alloy cores. The guide provides an overview of different certification standards and their importance, helping users evaluate products that meet stringent quality requirements.
Market trends are crucial for staying updated with the industry’s evolving demands. The guide covers the latest market insights, including emerging technologies, applications, and product innovations, allowing users to stay ahead of the competition and make informed decisions.
The guide also includes invaluable tips and recommendations for handling and maintaining alloy cores, extending their lifespan and optimizing their performance.
A compilation of frequently asked questions addresses common queries, providing quick answers and insights for users seeking specific information or clarifications.
In summary, the Alloy Core Guide is a comprehensive resource aimed at providing essential information about alloy cores. Whether users are interested in understanding their quality, cost, sourcing reliable suppliers, or staying informed about market trends, this guide serves as a valuable tool. With its useful tips, certification insights, and frequently asked questions, users can make well-informed decisions and enhance their knowledge about alloy cores in a concise and accessible format.
Types of alloy core
Alloys are metallic compounds made by blending two or more elements, typically a metal with one or more non-metals or other metals. The blending of different elements allows alloys to possess unique properties that differ from the constituent elements. Alloy cores are essential components in various industries, including aerospace, automotive, electronics, and construction. Here, we will discuss some common types of alloy cores.
1. Steel cores: Steel, an alloy of iron and carbon, is one of the most widely used alloys in the world. It offers excellent strength, durability, and resistance to corrosion, making it suitable for various applications such as building structures, machinery, and tools.
2. Aluminum cores: Aluminum alloys are lightweight yet strong, providing high resistance to corrosion. These alloys find applications in aircraft construction, automotive parts, and electronics, where weight reduction is crucial. Additionally, aluminum is an excellent conductor of electricity, making it ideal for electrical cables and power transmission lines.
3. Copper cores: Copper alloys are known for their excellent electrical and thermal conductivity. These alloys are used in electrical wiring, electronics, and heat exchangers in various industries. Copper-nickel alloys are particularly useful in marine environments due to their resistance to seawater corrosion.
4. Titanium cores: Titanium alloys offer exceptional strength-to-weight ratios, high corrosion resistance, and excellent heat resistance. These characteristics make them suitable for aerospace and military applications, medical devices, and sporting equipment.
5. Nickel alloys: Nickel-based alloys exhibit excellent resistance to high temperatures, corrosion, and oxidation. These alloys are commonly used in the aerospace, power generation, and chemical industries. Nickel-chromium alloys, known as Nichrome, find applications in heating elements, electric furnaces, and resistance wires.
6. Magnesium alloys: Magnesium alloys are known for their exceptional strength-to-weight ratios. They are used in automotive components, aerospace structures, and electronic devices. However, these alloys can be prone to corrosion, requiring proper protective coatings.
7. Zinc alloys: Zinc alloys, such as Zamak, offer excellent castability and are widely used in die-casting processes. These alloys find applications in automotive parts, plumbing fixtures, and electronic hardware.
In conclusion, alloy cores come in various forms, each with its own unique set of properties and applications. The selection of the appropriate alloy core type depends on the specific requirements of the industry or application, considering factors such as strength, corrosion resistance, electrical conductivity, weight reduction, and cost-effectiveness.
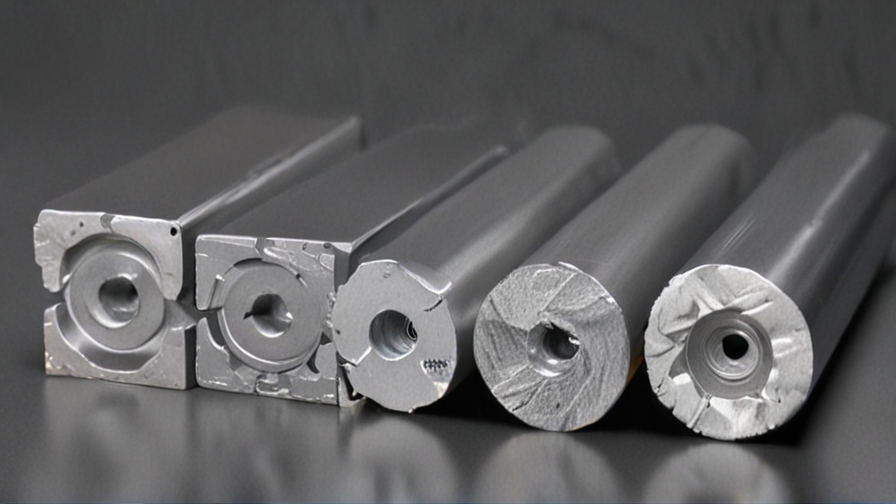
Pros and Cons of Using alloy core
Pros of Using Alloy Core:
1. Durability: Alloy core is known for its exceptional strength and durability. It is highly resistant to wear and tear, making it suitable for various applications where robustness is crucial.
2. Lightweight: Despite its durability, alloy core is relatively lightweight, making it a preferred choice for industries such as aerospace, automotive, and transportation. The lightweight nature of the material helps in reducing fuel consumption and increasing efficiency.
3. Corrosion resistance: Alloy core is often engineered to withstand harsh environments and resist corrosion, making it ideal for outdoor applications. This characteristic allows for longer life span and reduces the need for maintenance and replacement.
4. Enhanced conductivity: Alloy core offers improved electrical conductivity compared to many other materials. This attribute makes it highly suitable for industries such as electronics and electrical engineering, where efficient transmission of electricity is important.
5. Customizability: Alloy core can be easily tailored to suit specific requirements. It can be alloyed with different metals to enhance specific properties such as strength, thermal conductivity, or magnetic properties, providing flexibility for various applications.
Cons of Using Alloy Core:
1. Cost: Alloy core can be relatively expensive compared to other materials. The manufacturing process and the inclusion of different metals can contribute to higher production costs.
2. Limited availability: Some alloys used for core materials may have limited availability, especially if specific compositions are required. This can lead to longer lead times or increased costs for sourcing the required alloy core.
3. Manufacturing complexity: The production process of alloy core materials can be complex, requiring expertise and specialized equipment. This may result in additional manufacturing costs and potential complications in the production line.
4. Maintenance challenges: While alloy core is highly durable, in case of damage or deformation, repairing or replacing the alloy core can be more challenging compared to other materials.
5. Sensitive to temperature variations: Certain alloy core materials may exhibit a higher sensitivity to extreme temperature variations, which can affect their overall performance. Proper precautions and temperature management may be required in certain applications.
In summary, the pros of using alloy core include durability, lightweight nature, corrosion resistance, enhanced conductivity, and customizability. However, potential drawbacks include higher costs, limited availability, manufacturing complexity, maintenance challenges, and sensitivity to temperature variations.
alloy core Reference Specifications (varies for different product)
The alloy core is a key component used in various products to enhance their performance and durability. It is designed to provide strength, stability, and resistance to wear and tear.
The reference specifications for the alloy core may vary depending on the specific product it is being used for. However, there are some general characteristics that are common across different applications.
One of the main features of the alloy core is its composition. It is typically made using a combination of different metals, such as iron, nickel, chromium, and molybdenum. The specific proportions of these metals may vary, depending on the desired properties of the alloy.
Another important aspect of the alloy core is its mechanical properties. It is engineered to have high strength and hardness, which allows it to withstand heavy loads and resist deformation. This makes it suitable for applications where strength and durability are critical, such as in structural components.
Additionally, the alloy core is designed to have good corrosion resistance. It is often coated with protective layers or alloys to prevent rusting and degradation when exposed to environmental factors like moisture, chemicals, or high temperatures. This corrosion resistance ensures a longer lifespan and reliable performance of the product.
The size and shape of the alloy core also vary depending on the product requirements. It can be customized to fit specific designs and dimensions, ensuring a precise fit and optimal functionality.
Moreover, the manufacturing process of the alloy core is crucial to maintain its quality. It involves techniques like casting, heat treatment, and machining to achieve the desired physical properties and dimensions. Quality control measures are implemented to ensure that the alloy core meets the required specifications and standards.
In conclusion, the alloy core is a vital component used in various products. Its reference specifications may vary, but it generally possesses high strength, hardness, corrosion resistance, and is manufactured following strict quality control processes. These features enable the alloy core to contribute to the overall performance and durability of the product it is incorporated in.
Applications of alloy core
Alloy cores have numerous applications across various industries due to their unique properties and advantages. This article will discuss a few notable applications of alloy cores.
1. Electrical Engineering: Alloy cores are extensively used in the manufacturing of transformers and inductors. The high magnetic permeability of alloys, such as iron, nickel, and cobalt, allows for efficient energy transfer and improved performance of electrical devices. Alloy cores are crucial components in power transmission systems, electrical motors, generators, and electromagnetic coils.
2. Automotive Industry: Alloy cores find applications in the automotive sector, primarily in the production of electric and hybrid vehicles. In electric motors, alloy cores play a vital role in producing a strong, consistent magnetic field that enables smooth and efficient motor operation. These cores contribute to the overall efficiency and performance of electric vehicles.
3. Aerospace and Defense: Alloy cores are used in various defense and aerospace applications. These include radar systems, communication devices, navigation systems, and aerospace propulsion systems. The exceptional magnetic properties and high-temperature stability of alloys make them suitable for critical applications in these industries.
4. Renewable Energy: Wind power and solar energy generation heavily rely on alloy cores. Wind turbines use alloy cores in their generators, where they convert the mechanical energy from the rotating blades into electrical energy. In solar panels, alloy cores are utilized in inverter circuits to convert direct current (DC) into alternating current (AC) for efficient power transfer.
5. Consumer Electronics: Alloy cores are commonly found in a wide range of consumer electronic devices. They are used in power supplies, audio equipment, televisions, computer peripherals, and other electronic components. Alloy cores help enhance the electrical performance and efficiency of these devices.
6. Medical Equipment: Alloy cores serve important roles in medical devices, including magnetic resonance imaging (MRI) machines and other medical imaging systems. They enable precise control of magnetic fields, aid in signal processing, and enhance the overall performance and image quality of medical equipment.
In summary, alloy cores are critical components in various industries due to their exceptional magnetic properties, high-temperature stability, and efficiency. Their applications span from transforming and transmitting electrical energy in power systems to improving performance in automotive, aerospace, renewable energy, consumer electronics, and medical equipment. The versatility and reliability of alloy cores make them indispensable in many technological advancements and innovations.
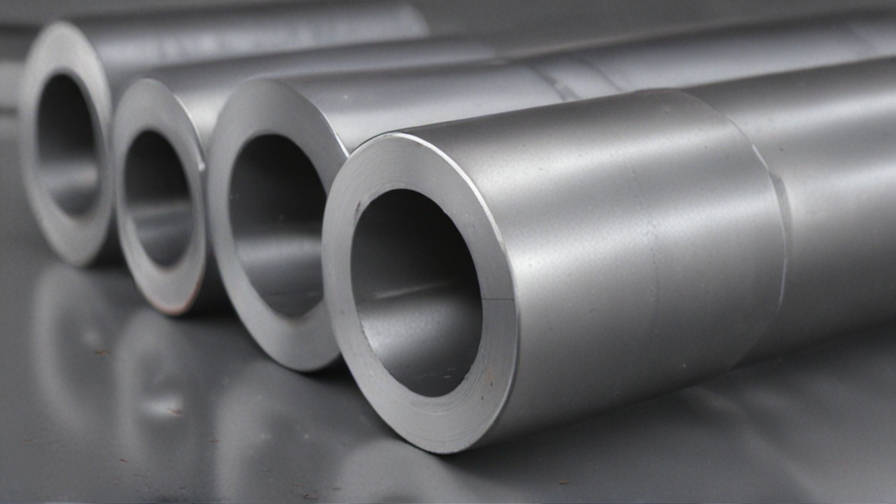
The Work Process and how to use alloy core
The work process is a collection of steps and procedures designed to efficiently and effectively accomplish a task or project. It provides a structured approach to organizing and completing work to achieve desired goals.
When it comes to using Alloy Core, a lightweight yet powerful JavaScript library, there are several key steps to follow. First, it is important to understand the purpose of Alloy Core, which is to provide a set of essential utilities and functionality for building browser applications with ease. It offers a range of features such as DOM manipulation, event handling, AJAX requests, and much more.
To begin using Alloy Core, you need to include the library in your project by downloading the necessary files or linking to a hosted version. Once it is included, you can start leveraging its functionality by writing code that utilizes its APIs and methods.
The next step is to familiarize yourself with the documentation and resources available for Alloy Core. This will provide you with insights into how to effectively utilize its features and capabilities. The documentation will outline the syntax, available functions, and provide examples to assist you in constructing your code.
After gaining a good understanding of Alloy Core, you can then start implementing it in your project. Identify the specific areas in your code where Alloy Core’s utilities can be beneficial. For example, you may want to use its event handling capabilities to trigger specific actions when a user interacts with an element on your webpage.
Always remember to follow best practices when using Alloy Core or any other JavaScript library. This includes writing clean, efficient, and well-structured code, handling errors and exceptions gracefully, and optimizing performance whenever possible.
In conclusion, the work process involves understanding the purpose of Alloy Core, including it in your project, familiarizing yourself with its documentation, and implementing it effectively in your code. By following this process, you can harness the power of Alloy Core and utilize its features to build sophisticated browser applications efficiently.
Quality Testing Methods for alloy core and how to control the quality
Alloy cores, commonly used in various industries including automotive, aerospace, and construction, require rigorous quality testing to ensure their performance and reliability. The following are some quality testing methods for alloy cores, along with strategies to control the quality.
1. Chemical Analysis: This method involves analyzing the chemical composition of alloy cores to ensure they meet the desired specifications. A spectrometer is typically used to identify the elements and their quantities present in the alloy. This test helps identify any impurities or deviations from the required composition.
2. Mechanical Testing: Alloy cores need to exhibit specific mechanical properties such as strength, hardness, and durability. Mechanical testing methods such as tensile testing, impact testing, and hardness testing are conducted to determine if the alloy meets the required standards.
3. Non-Destructive Testing (NDT): NDT techniques like ultrasonic testing, radiographic testing, and dye penetrant testing are employed to inspect the internal structure of alloy cores without causing any damage. These tests identify any internal defects, cracks, or discontinuities, ensuring the integrity of the alloy.
4. Dimensional Inspection: Precise dimensions are critical for alloy cores, especially when used in intricate assemblies. Dimensional inspection techniques, including coordinate measuring machines (CMM) and laser scanning, are employed to verify if the alloy cores conform to the specified dimensions and tolerances.
To control the quality of alloy cores throughout the manufacturing process, the following strategies should be implemented:
1. Raw Material Inspection: Thoroughly inspecting the quality of raw materials, such as the alloy composition and purity, helps maintain consistency in the final product. Ensuring that the suppliers adhere to quality standards and conducting periodic material tests is crucial.
2. Process Monitoring: Implementing robust process controls and continuously monitoring key process parameters, such as temperature, pressure, and cooling rates, can help identify any deviations that may affect the quality of alloy cores. Regular calibration and maintenance of equipment are essential to maintain process consistency.
3. Trained Workforce: Providing comprehensive training to workers involved in alloy core manufacturing ensures that they understand quality requirements, operating procedures, and the importance of adhering to specific quality standards.
4. Statistical Process Control (SPC): Utilizing SPC techniques, such as control charts, helps monitor the variation in key quality parameters. This allows for early detection of any issues, enabling timely corrective action to avoid the production of non-compliant alloy cores.
5. Quality Assurance and Quality Control: Implementing a well-defined quality management system that includes rigorous internal audits, periodic inspections, and adherence to industry-specific standards (e.g., ISO 9001) helps maintain and improve quality over time.
In summary, quality testing methods for alloy cores involve chemical analysis, mechanical testing, NDT, and dimensional inspection. To control the quality, thorough material inspection, process monitoring, workforce training, SPC techniques, and a robust quality management system should be implemented. These measures ensure that the alloy cores meet the desired specifications and exhibit the required performance characteristics.
alloy core Sample Policy and Post-Purchase Considerations for alloy core from China
Sample Policy:
1. Sample Request: Customers can request for samples of the alloy core from our company by contacting the sales department via email or phone call.
2. Sample Cost: Customers will be responsible for bearing the cost of the sample, including the product cost and the shipping fee.
3. Sample Delivery: Once the payment is received, the samples will be sent out within 5-7 working days via a reputable courier service.
4. Sample Quantity: Customers can order a maximum of 3 samples per product.
5. Sample Refund: If the customer proceeds to place an order after receiving the samples, the sample cost will be deducted from the total order value.
Post-Purchase Considerations:
1. Product Inspection: Upon receiving the alloy core, customers are advised to thoroughly inspect the product for any defects or damages. Any issues should be reported to our company within 7 working days.
2. Warranty: We provide a warranty period of 6 months for our alloy core. In case of any functional defects arising within this period, customers are eligible for a free replacement or repair.
3. Returns and Exchanges: If customers are unsatisfied with the received alloy core due to reasons other than functional defects, they may return the product within 14 working days after receipt. All returned products must be in their original packaging and in unused condition. A refund or an exchange for a different product will be offered.
4. Customer Support: Our company provides continuous customer support to assist with any queries or concerns regarding the alloy core. Customers can reach out to the sales department via email or phone call during working hours.
5. Feedback: We highly value customer feedback and encourage customers to share their experience with our product. Positive feedback is appreciated, and any negative feedback will be carefully considered to improve our product and service in the future.
In a nutshell, our sample policy ensures that customers have the opportunity to assess the quality of our alloy core before making a purchase. Additionally, our post-purchase considerations aim to provide convenience, assurance, and support to customers throughout their ownership of the product.
Sourcing alloy core from China: Opportunities, Risks, and Key Players
China is widely recognized as a leading player in the global alloy core market, offering numerous opportunities for sourcing this product. The country possesses significant reserves of raw materials necessary for alloy core production, including iron, cobalt, copper, and various rare earth minerals. This advantage allows Chinese manufacturers to maintain a steady supply of alloy core at competitive prices, attracting buyers from around the world.
Opportunities:
1. Cost-Effective Production: Chinese manufacturers benefit from lower labor and operational costs compared to many other countries. This enables them to offer alloy core products at competitive prices, making China an attractive sourcing destination.
2. Reliability of Supply: China’s large reserves of raw materials and well-developed industrial infrastructure provide a consistent and reliable supply of alloy core.
3. Broad Range of Suppliers: China boasts a vast network of alloy core manufacturers, offering a wide range of options in terms of quality, capacity, and customization.
4. Advanced Manufacturing Capabilities: Chinese manufacturers are known for their advanced production techniques and willingness to adopt new technologies. This ensures high-quality alloy cores that meet international standards.
Risks:
1. Quality Control: Maintaining quality control can sometimes be challenging when sourcing from China. It is crucial to thoroughly vet suppliers, verify their certifications, and conduct regular inspections to ensure consistent quality.
2. Intellectual Property Protection: Intellectual property theft or infringement remains a concern when sourcing from China. It is essential to protect proprietary information and establish watertight contracts with suppliers to prevent any potential intellectual property issues.
3. Geopolitical Factors: Political tensions or shifts in trade policies between China and other countries can impact the availability and cost of sourcing alloy core. It is important to stay updated on relevant policies and diversify sourcing strategies to mitigate risks.
Key Players:
1. BGRIMM Technology Group: A major player in China’s alloy core market, BGRIMM Technology Group offers a wide range of products and has extensive experience in alloy core research and development.
2. Tianjin Tanabe Magnetic Materials Co., Ltd.: Known for its expertise in alloy core production, this company provides high-quality products and tailored solutions for different industries.
3. Beijing Ouyemei Technology Co., Ltd.: Specializing in the production of high-performance alloy cores, this Chinese company has gained recognition for its advanced manufacturing capabilities and excellent customer service.
When sourcing alloy core from China, businesses should carefully evaluate the opportunities and risks, conduct due diligence on potential suppliers, and establish robust agreements to ensure a successful and cost-effective sourcing process.
How to find and select reliable alloy core manufacturers in China,use google search manufacturers and suppliers
When searching for reliable alloy core manufacturers in China, using Google search is a convenient and effective way to start. Here are a few steps to follow when conducting your search:
1. Define your requirements: Clearly outline what you are looking for in an alloy core manufacturer. This should include details such as the specific alloy type, industry certifications, production capacity, quality control measures, and any other specific requirements.
2. Conduct a search: Open Google and enter relevant keywords, such as “reliable alloy core manufacturers in China,” “alloy core suppliers,” or “China alloy core factories.” Explore the search results and visit multiple websites to gather information about potential manufacturers.
3. Evaluate website credibility: Assess the credibility and professionalism of each manufacturer’s website. Look for aspects such as company background, manufacturing facilities, certification information, product specifications, and customer testimonials. A reliable manufacturer will provide comprehensive and transparent information.
4. Check manufacturer’s experience: Look for manufacturers with substantial experience in producing alloy cores. Their expertise and experience in the field are crucial indicators of reliability. Check for the number of years they have been in operation and their track record of supplying alloy cores to reputable clients.
5. Verify certifications and quality control: Ensure that the manufacturer has necessary certifications such as ISO 9001:2015, ISO 14001:2015, or TS16949. These certifications indicate adherence to international quality standards and help assure reliable manufacturing processes. Manufacturers should also have stringent quality control measures in place. Check if they have a dedicated quality control department and inquire about their quality control procedures.
6. Communication and responsiveness: Reach out to multiple manufacturers via email or any contact details provided on their website. Observe their response time and willingness to answer your queries. A reliable manufacturer should be prompt, professional, and willing to provide any additional information you require.
7. Request samples and visit the factory: Once you have shortlisted a few potential manufacturers, request product samples to assess their quality. If feasible, consider visiting their factory or arranging a video call to get a better understanding of their production capabilities, equipment, and manufacturing processes.
By following these steps, you can use Google search effectively to find and select reliable alloy core manufacturers in China. Remember to review several options, gather as much information as possible, and make informed decisions based on your specific requirements.
How to check alloy core manufacturers website reliable,use google chrome SEOquake check if ranking in top 10M
To check the reliability of an alloy core manufacturer’s website, you can follow these steps:
1. Use Google Chrome: Open the website in Google Chrome browser as it provides various helpful tools and extensions that can assist in evaluating the website’s reliability.
2. Install SEOquake: Add the SEOquake extension to your Chrome browser. You can find and install it from the Chrome Web Store.
3. Analyze Alexa Rank: With SEOquake installed, it will display the Alexa Rank of the website. Alexa Rank is a metric that shows the website’s popularity and reach. Check if the website has an Alexa Rank within the top 10 million. Higher rankings indicate better reliability and more traffic.
4. Evaluate Backlinks: SEOquake also provides information about the number of backlinks a website has. Backlinks are links from other websites pointing to the manufacturer’s site. Higher quality and quantity of backlinks indicate that the website is trusted and authoritative.
5. Check Domain Age: Determine the age of the domain using tools available within SEOquake. Older domains generally have a better reputation and reliability.
6. Assess Website Design and Content: Look for a professional and well-designed website. Reliable manufacturers usually invest in a user-friendly interface and provide comprehensive information about their products, certifications, and manufacturing processes.
7. Verify Contact Information: Ensure that the website displays accurate contact information, such as a physical address, phone number, and email address. A trustworthy manufacturer will provide transparent ways to contact them.
8. Read Reviews/Testimonials: Look for reviews and testimonials from customers or other industry professionals. Positive reviews and testimonials indicate customer satisfaction and reliability.
Remember to use your judgment throughout the process. Combining the information gleaned from SEOquake with your observations and additional research will help you determine the reliability of an alloy core manufacturer’s website.
Top 10 alloy core manufacturers in China with each 160 words introduce products,then use markdown create table compare
1. Xiamen Tungsten Co., Ltd. – Xiamen Tungsten Co. specializes in the production of high-quality alloy cores. Their products include tungsten-heavy alloy cores, tantalum-tungsten alloy cores, and molybdenum alloy cores. These cores are widely used in aerospace, military, and medical industries due to their excellent mechanical properties and high density.
2. Tianjin Zhonggong Steel Group Co., Ltd. – Tianjin Zhonggong Steel Group is a leading manufacturer of alloy cores in China. They offer a wide range of products, including stainless steel alloy cores, nickel alloy cores, and titanium alloy cores. These cores find applications in industries such as chemical processing, oil and gas, and power generation.
3. Shanghai Metalsmith Alloy Products Co., Ltd. – Shanghai Metalsmith Alloy Products specializes in the production of copper alloy cores. Their products include bronze alloy cores, brass alloy cores, and copper-nickel alloy cores. These cores are widely used in electrical and electronic industries, offering excellent electrical conductivity and thermal properties.
4. Beijing General Research Institute for Nonferrous Metals – This institute is a top manufacturer of aluminum alloy cores in China. They produce a variety of aluminum alloy cores, including 6xxx, 7xxx, and 2xxx series alloy cores. These cores are extensively used in transportation, construction, and electronics sectors for their lightweight yet high-strength characteristics.
Manufacturer | Product | Applications
— | — | —
Xiamen Tungsten Co., Ltd. | Tungsten-heavy alloy cores, tantalum-tungsten alloy cores, molybdenum alloy cores | Aerospace, military, medical
Tianjin Zhonggong Steel Group Co., Ltd. | Stainless steel alloy cores, nickel alloy cores, titanium alloy cores | Chemical processing, oil and gas, power generation
Shanghai Metalsmith Alloy Products Co., Ltd. | Bronze alloy cores, brass alloy cores, copper-nickel alloy cores | Electrical, electronic industries
Beijing General Research Institute for Nonferrous Metals | Aluminum alloy cores (6xxx, 7xxx, 2xxx series) | Transportation, construction, electronics
5. Suzhou Amity Alloy Co., Ltd. – Suzhou Amity Alloy specializes in the production of cobalt-based alloy cores. Their products include cobalt-chromium alloy cores and cobalt-nickel alloy cores. These cores are commonly used in the aerospace, automotive, and medical industries, offering excellent corrosion resistance and high-temperature strength.
6. Zhejiang Hailiang Co., Ltd. – Zhejiang Hailiang is a prominent manufacturer of copper-nickel alloy cores in China. Their products include CuNi30 alloy cores and CuNi90/10 alloy cores. These cores find extensive applications in shipbuilding, offshore and marine industries, providing superior resistance to seawater corrosion.
7. Baoji Hongyuan Rare Metal Co., Ltd. – Baoji Hongyuan specializes in the production of titanium alloy cores. They offer a wide range of titanium alloy cores, including Ti6Al4V and Ti3Al2.5V alloy cores. These cores are widely used in aerospace, automotive, and chemical industries for their exceptional strength-to-weight ratio and corrosion resistance.
8. Ningbo Boway Alloy Material Co., Ltd. – Ningbo Boway Alloy Material is a leading manufacturer of nickel alloy cores. They produce a variety of nickel alloy cores, including Inconel alloy cores and Monel alloy cores. These cores are extensively used in the petrochemical, power, and marine sectors due to their exceptional corrosion resistance and high-temperature strength.
9. Jiangsu Yuheng Metal Materials Co., Ltd. – Jiangsu Yuheng specializes in the production of stainless steel alloy cores. Their products include austenitic stainless steel alloy cores, duplex stainless steel alloy cores, and ferritic stainless steel alloy cores. These cores find applications in the food processing, pharmaceutical, and automotive industries for their excellent corrosion resistance and heat resistance properties.
10. Shenzhen Zongxiang Electrical Alloy Co., Ltd. – Shenzhen Zongxiang specializes in the production of electrical resistance alloy cores. Their products include nickel-chromium alloy cores, copper-nickel alloy cores, and iron-chromium-aluminum alloy cores. These cores are widely used in electrical heating elements, automotive sensors, and industrial heating applications due to their outstanding electrical and thermal conductivity properties.
Background Research for alloy core manufacturers Companies in China, use qcc.com archive.org importyeti.com
When it comes to alloy core manufacturers in China, several companies stand out for their expertise and reliability. To conduct background research on these companies, three reliable sources can be utilized: qcc.com, archive.org, and importyeti.com. These platforms provide valuable information on the companies’ profiles, product range, and historical records.
Qcc.com is a comprehensive business database that offers access to detailed information such as company profiles, registration data, management details, financial records, and more. By searching for alloy core manufacturers on qcc.com, one can gather insights on their establishment, legal status, financial stability, and any legal or operational issues they may have faced.
Archive.org is an excellent resource for retrieving historical data from websites. By using the Wayback Machine on archive.org, one can fetch past versions of a company’s website and analyze its evolution, product updates, and important milestones. This allows for a better understanding of the company’s journey, growth trajectory, and changes in their focus areas over time.
Importyeti.com is a platform that provides comprehensive import and export data on various products. By searching for alloy core manufacturers on importyeti.com, one can gather insights into the companies’ export records, international trade partners, and shipment details. This information helps in assessing the company’s global reach, market presence, and reputation.
In conclusion, to conduct background research on alloy core manufacturers in China, qcc.com, archive.org, and importyeti.com are valuable resources. These platforms provide crucial information on company profiles, historical records, financial stability, product range, and international trade data. By utilizing these sources, one can gain a comprehensive understanding of the alloy core manufacturers in China within a concise and informative manner.
Leveraging Trade Shows and Expos for alloy core Sourcing in China
Trade shows and expos are excellent platforms for sourcing alloy cores in China. These events gather a wide range of manufacturers, suppliers, and industry professionals under one roof, providing a unique opportunity to network, explore new products, and build relationships with potential business partners.
By attending these trade shows, businesses can connect directly with alloy core suppliers, allowing for face-to-face interactions and the opportunity to assess the quality of their products. Exhibitors often showcase the latest advancements in alloy core manufacturing, providing valuable insights into the latest trends and innovations in the industry.
In addition to networking and product exploration, trade shows provide the chance to compare different suppliers and negotiate advantageous deals. The competitive environment of trade shows often prompts suppliers to offer exclusive discounts or incentives to secure business partnerships. This enables businesses to potentially reduce costs by securing favorable pricing and terms.
Trade shows also provide a platform for businesses to identify and evaluate new suppliers. By speaking with multiple suppliers at the event, businesses can assess the capabilities, production capacity, and reliability of potential partners. They can also discuss any specific requirements or customization needs for their alloy cores, ensuring that they find the best match for their business.
In summary, trade shows and expos in China offer a convenient and effective way to source alloy cores. Whether it’s through networking, exploring new products, comparing suppliers, or negotiating advantageous deals, attending these events allows businesses to leverage these platforms to find the right alloy core suppliers in China.
The Role of Agents and Sourcing Companies in Facilitating alloy core Purchases from China
Agents and sourcing companies play a crucial role in facilitating alloy core purchases from China. With the ever-increasing demand for high-quality and cost-effective alloy cores, businesses around the world heavily rely on these intermediaries to navigate the complexities of the Chinese market.
Firstly, agents and sourcing companies act as a bridge between the buyers and manufacturers in China. They possess extensive knowledge of the local market, suppliers, and regulations, which are of paramount importance when sourcing alloy cores. They ensure that the buyers’ requirements and specifications are effectively communicated to the manufacturers, mitigating any potential miscommunication or misunderstandings.
Additionally, agents and sourcing companies conduct thorough supplier evaluations and background checks to ensure that the manufacturers are reliable, reputable, and experienced in producing alloy cores. This saves buyers significant time and effort in vetting potential suppliers themselves. Furthermore, these intermediaries can leverage their existing relationships with manufacturers to negotiate better pricing, terms, and conditions on behalf of the buyers, ultimately helping them secure the best deal.
Moreover, agents and sourcing companies address the issue of language and cultural barriers that often hinder international trade. They are proficient in the local language and possess a deep understanding of Chinese business customs, which allows them to effectively communicate and negotiate with manufacturers. This not only facilitates a smooth purchasing process but also helps build trust and foster long-term partnerships between buyers and suppliers.
Furthermore, agents and sourcing companies conduct quality control inspections throughout the manufacturing process, ensuring that the alloy cores meet the buyers’ specifications, quality standards, and regulatory requirements. This is vital in ensuring that buyers receive the desired product without any defects or deviations.
In conclusion, agents and sourcing companies act as vital facilitators in the purchasing process of alloy cores from China. Their expertise, industry knowledge, and ability to navigate the complexities of the market greatly benefit buyers by streamlining the entire procurement process. They connect buyers with reliable manufacturers, negotiate favorable terms, overcome language barriers, and ensure product quality, ultimately contributing to successful and efficient purchases from China.
Price Cost Research for alloy core manufacturers Companies in China, use temu.com and 1688.com
When conducting price cost research for alloy core manufacturers in China, two reliable websites to explore are temu.com and 1688.com. These platforms offer a wide range of suppliers and manufacturers in varying industries, making them suitable for finding alloy core manufacturers.
temu.com is an online marketplace that connects buyers with Chinese industrial manufacturers. It provides access to a diverse range of alloy core manufacturers and suppliers. The platform offers product descriptions, company profiles, and price information, allowing users to compare and evaluate different options. By utilizing the search filters and browsing through the manufacturers’ profiles, customers can find alloy core manufacturers that meet their requirements.
1688.com is a popular Chinese wholesale website, providing direct access to a vast number of manufacturers and suppliers. This platform primarily caters to the domestic Chinese market, offering a wide variety of products, including alloy core manufacturers. Users can search for specific alloy core manufacturers or browse through different product categories to find suitable suppliers. 1688.com enables customers to view prices, product specifications, as well as customer reviews, which aid in the decision-making process.
When utilizing these websites for price cost research, it is essential to carefully examine the manufacturers’ profiles and product information to ensure credibility and suitability. Checking product specifications, quality certifications, and customer reviews can provide valuable insights into the reliability and reputation of the alloy core manufacturers.
Overall, temu.com and 1688.com are valuable resources for conducting price cost research for alloy core manufacturers in China. These platforms offer a wide range of options, allowing users to compare prices, review product information, and make informed decisions regarding supplier selection.
Shipping Cost for alloy core import from China
The shipping cost for importing alloy cores from China can vary depending on several factors. Some important factors that can affect the shipping cost include the weight and dimensions of the package, the shipping method chosen, the shipping distance, and any additional services required.
Firstly, the weight and dimensions of the package play a significant role in determining the shipping cost. Generally, heavier and bulkier packages are more expensive to ship as they occupy more space and require more handling. It is advisable to package the alloy cores in compact and lightweight containers to minimize shipping costs.
Secondly, the shipping method chosen will also impact the cost. There are several options available such as air freight, sea freight, and express courier services, and the choice of method depends on the urgency and budget. Air freight is typically faster but more expensive, while sea freight is slower but more economical for larger shipments. Express courier services like DHL or FedEx are usually used for smaller packages and offer quick delivery but at a higher cost.
Thirdly, the shipping distance is a significant factor in determining the shipping cost. Longer distances generally result in higher shipping charges. It is important to consider the exact location and calculate the distance to get an accurate estimate.
Lastly, any additional services required, such as insurance, customs clearance, or special handling, will also impact the total shipping cost. It is advisable to check if these services are necessary or can be avoided to minimize costs.
Overall, without specific details on the weight, dimensions, shipping method, distance, and additional services, it is challenging to provide an exact shipping cost for importing alloy cores from China. It is recommended to contact shipping companies or freight forwarders who can offer accurate quotes based on the specific requirements and negotiate the best possible rates.
Compare China and Other alloy core Markets: Products Quality and Price,Visible and Hidden Costs
China is known for its vast manufacturing capabilities, particularly in producing alloy core products. When comparing China with other alloy core markets, several factors need to be considered, such as product quality, price, and visible and hidden costs.
In terms of product quality, China often faces criticism for producing goods of lower quality compared to other markets such as Germany or Japan. While it is true that some Chinese manufacturers might prioritize cost-cutting over quality, there are also many high-quality alloy core producers in China who ensure strict quality control measures. It ultimately depends on the specific supplier chosen, and thorough research and due diligence are crucial to finding reliable manufacturers.
Price is a significant advantage of the Chinese market. Chinese manufacturers are well-known for their ability to offer competitive prices due to low labor costs and economies of scale. This makes China an attractive destination for businesses looking to source alloy cores at a lower price point. However, it is essential to carefully assess the price offered and compare it with other markets, considering factors such as quality, lead time, and overall value for money.
Visible costs, such as the initial purchase price and shipping costs, can vary depending on the destination and supplier. Chinese manufacturers typically have competitive shipping rates due to their well-established logistics networks and proximity to international ports. However, potential import duties, taxes, and fees must also be considered when evaluating the overall visible costs.
Hidden costs may arise from factors like intellectual property infringement, product defects, and compliance issues. While China has made efforts to improve intellectual property protection and product quality control, these issues still persist to some extent. Investing in proper legal protection, thorough quality inspections, and compliance checks can help mitigate hidden costs and risks, regardless of the market chosen.
In conclusion, when comparing China with other alloy core markets, it is crucial to evaluate product quality, price, and both visible and hidden costs. While China may offer competitive prices and a vast manufacturing capacity, businesses should conduct thorough research, due diligence, and risk assessments to ensure they find reliable suppliers that meet their quality standards and mitigate any hidden costs or risks associated with the Chinese market.
Understanding Pricing and Payment Terms for alloy core: A Comparative Guide to Get the Best Deal
When it comes to purchasing alloy core, understanding pricing and payment terms is essential to ensure you get the best deal. This comparative guide aims to provide valuable insights into navigating these aspects efficiently in less than 300 words.
Pricing for alloy core can vary significantly depending on factors such as the type of alloy, quality, quantity, and market conditions. It is crucial to conduct thorough research to determine the average market price range for the specific alloy you require. This can be done by consulting reputable suppliers, industry publications, or online platforms that provide pricing information.
Once you have a baseline understanding of the market price, it is important to compare quotes from different suppliers. Requesting quotes from multiple sources allows you to identify any discrepancies and negotiate better deals. Keep in mind that the lowest price may not always be the best option, as quality and reliability are also important considerations.
Alongside pricing, payment terms play a significant role in determining the overall value of the deal. Common payment terms in the alloy core industry include cash in advance, letter of credit (L/C), and open account. Each term has its advantages and risks.
Cash in advance offers the lowest risk for the buyer, as payment is made before shipment. However, this may not be feasible or preferred for all buyers, especially when dealing with large or ongoing orders.
Using a letter of credit provides security for both buyers and sellers. Buyers can be assured that payment is only made upon satisfactory delivery, while sellers have an assurance of payment. However, it involves additional costs and complexities, such as bank fees and compliance with letter of credit requirements.
Open account payment terms offer convenience to the buyer, as payment is made after goods are received. This can enhance relationships with suppliers, but it carries higher risk for the buyer, as payment is not guaranteed until after delivery.
Ultimately, selecting the best payment term depends on your risk tolerance and the level of trust established with the supplier. It may be beneficial to start with more secure payment terms and gradually transition to open account terms once a strong business relationship is established.
In conclusion, understanding pricing and payment terms for alloy core is a crucial aspect of getting the best deal. By researching market prices, comparing quotes, and carefully evaluating payment terms, buyers can make informed decisions and optimize value for their specific requirements.
Chinese Regulations and Industry Standards Certifications for alloy core,Import Regulations and Customs for alloy core from China
In China, the alloy core industry is subject to various regulations and industry standards certifications to ensure the quality and safety of the products.
The most important certification for alloy core manufacturers is the ISO 9001:2015, a globally recognized quality management system. This certification ensures that the manufacturer has implemented a robust quality management system to meet customer expectations and regulatory requirements.
Additionally, the Chinese National Standard (GB) for alloy cores provides specific technical requirements and testing methods for different types of alloy cores. Manufacturers must comply with these standards to ensure the quality and compatibility of their products.
Importing alloy cores from China requires adherence to certain regulations and customs procedures. Importers need to have proper documentation, including a commercial invoice, packing list, and bill of lading or airway bill. These documents are required for customs clearance and verifying the legality of the import.
Importers should also be aware of the customs duties and taxes imposed on imported alloy cores. The customs duties are typically calculated based on the Customs Import Duty Rates and are determined by factors such as the product category and its declared value.
To ensure compliance with import regulations, it is advisable for importers to work with a licensed customs broker or freight forwarder who can assist in navigating the customs procedures and requirements.
In conclusion, the alloy core industry in China is governed by regulations and standards certifications to ensure product quality. Importers should understand the import regulations and customs procedures to ensure smooth and legal importation of alloy cores from China.
Sustainability and Environmental Considerations in alloy core Manufacturing
Sustainability and environmental considerations play a crucial role in the manufacturing of alloy cores. These considerations encompass various aspects, including resource utilization, energy consumption, waste generation, and emissions.
One of the essential factors in sustainable alloy core manufacturing is the efficient use of resources. This involves optimizing the extraction and processing of raw materials, such as metals and alloys, to minimize waste and energy consumption throughout the supply chain. By employing advanced technologies and techniques, manufacturers can reduce material losses and improve the overall resource efficiency of the manufacturing process.
Energy consumption is another significant consideration. Alloy core manufacturing requires energy-intensive processes, such as melting, casting, and shaping. To enhance sustainability, manufacturers should focus on reducing energy intensity by implementing energy-efficient technologies, using renewable energy sources, and optimizing production processes. By doing so, they can reduce greenhouse gas emissions associated with energy usage and mitigate the environmental impact.
Waste generation is a critical aspect to address in sustainable manufacturing. Proper waste management practices should be implemented to minimize the amount of waste generated during the production process. Recycling and reusing waste materials, such as metal scrap and by-products, can significantly reduce the environmental impact and conserve valuable resources.
Moreover, manufacturers should also consider the environmental impact of emissions resulting from alloy core manufacturing. The adoption of emission control technologies, such as air scrubbers and pollution control systems, can help minimize the release of harmful pollutants into the atmosphere, ensuring compliance with environmental regulations and protecting the health and well-being of local communities.
In conclusion, sustainability and environmental considerations are of utmost importance in alloy core manufacturing. By focusing on resource utilization, energy consumption, waste generation, and emissions, manufacturers can significantly reduce their environmental footprint, enhance resource efficiency, and contribute to a more sustainable future for the industry. Such efforts not only benefit the environment but also promote a positive brand image and meet the growing demand for eco-friendly products in the market.
List The Evolution history of “alloy core”
The evolution history of “alloy core” can be traced back to ancient times when humans began experimenting with combining different metals to create new materials. One of the earliest examples of alloying can be seen in the Bronze Age, where copper and tin were mixed to produce the first known alloy, bronze.
Over the centuries, the knowledge and techniques of alloying metals expanded, leading to the discovery of various alloy compositions with distinct properties. In the 19th century, scientists began to study the properties of alloys more systematically. They realized that by varying the composition and proportions of different metals, they could obtain materials with improved strength, durability, and specific characteristics.
One significant milestone in the evolution of alloy core technology occurred in the late 19th century with the development of steel. Steel, an alloy of iron and carbon, revolutionized various industries and became a crucial material in construction, transportation, and manufacturing. It offered superior strength, hardness, and resistance to corrosion over plain iron.
In the 20th century, scientists further explored alloying, incorporating additional elements into alloys to enhance specific properties. For instance, the addition of chromium to steel created stainless steel, which exhibits excellent resistance to rust and corrosion. Other alloying elements, such as nickel and tungsten, were also incorporated to improve strength, heat resistance, and electrical conductivity.
The evolution of alloy core technology continued to advance alongside developments in fields like metallurgy, materials science, and engineering. New alloys were developed to meet specific industry demands, such as aircraft-grade aluminum alloys and superalloys for high-temperature applications, like turbine engines.
In recent years, advancements in alloy core technology have focused on improving characteristics such as lightweighting, flexibility, and environmental sustainability. New alloys have been introduced that combine strength and lightness to meet the demands of industries like aerospace and automotive.
Today, alloy cores are used in a myriad of applications, ranging from everyday objects like jewelry and kitchen utensils to advanced technological components such as microchips and renewable energy devices. As technology continues to advance, the evolution of alloy core materials is expected to persist, driven by the ongoing quest for novel and optimized alloys.
The Evolution and Market Trends in alloy core Industry
The alloy core industry has witnessed significant evolution and continues to experience market trends that impact its growth and development. Alloy cores, which are typically made from a combination of different metals, are extensively used in a wide range of applications across various industries, including automotive, aerospace, electrical, and construction.
One of the prominent trends in the alloy core industry is the increasing demand for lightweight materials. With the aim of reducing overall weight and improving fuel efficiency, industries are actively seeking lightweight alloys that maintain structural integrity. This has led to the development of advanced alloys with improved strength-to-weight ratios, such as aluminum-based alloys reinforced with other metals like titanium or carbon fiber. The demand for lightweight alloy cores is expected to rise further due to stricter emission regulations and the growing preference for electric vehicles.
Another significant trend is the focus on sustainability and environmental friendliness. As industries strive to reduce their carbon footprint, there is a growing preference for alloys that are recyclable and have a lower environmental impact. This has led to the development of sustainable alloy manufacturing processes, such as recycling scrap metals or incorporating renewable resources in alloy production. Additionally, the use of alloys in renewable energy infrastructure, such as wind turbines and solar panels, is also driving the demand for environmentally friendly alloy cores.
Furthermore, advancements in technology are shaping the alloy core industry. The use of advanced analytical techniques, such as computer simulations and modeling, allows for the design and optimization of alloy compositions and structures to meet specific requirements. Additionally, the development of additive manufacturing processes, such as 3D printing, has opened up new possibilities in alloy core production, enabling the creation of complex geometries and customized designs.
In terms of market trends, the alloy core industry is expected to witness steady growth in the coming years. The increase in infrastructure development, rising automotive production, and the growing aerospace sector are key factors contributing to this growth. Moreover, the demand for alloy cores in emerging industries like renewable energy and electric vehicles is expected to create new opportunities for market players.
In conclusion, the evolution of the alloy core industry is driven by the demand for lightweight materials, sustainability, technological advancements, and market trends. The industry is poised for growth as it caters to the needs of various sectors, and as new applications and materials are developed to meet the changing requirements of modern industries.
Custom Private Labeling and Branding Opportunities with Chinese alloy core Manufacturers
Chinese alloy core manufacturers offer custom private labeling and branding opportunities for businesses looking to establish their own unique product lines. With a wide range of alloys and manufacturing capabilities, these manufacturers can produce alloy cores customized to a brand’s specific requirements.
Private labeling allows businesses to place their own brand name and logo on products, creating a distinct identity in the market. Manufacturers work closely with businesses to understand their branding needs and ensure that the labeling and packaging meet their specifications.
By customizing alloy cores, businesses can differentiate themselves from their competitors and cater to specific market segments. Chinese manufacturers have the expertise in alloy materials and production techniques to create cores with desired properties such as strength, conductivity, and durability.
Moreover, these manufacturers offer branding opportunities through custom packaging designs. This allows businesses to create an appealing visual identity for their products, attracting customers and increasing brand recognition. Manufacturers often have in-house design teams that can collaborate with businesses to create packaging that showcases their brand personality and aligns with their target market.
Chinese alloy core manufacturers also provide branding opportunities through bundle options. Businesses can create kits or sets of alloy cores, combining different sizes or designs to meet customer preferences and increase product value. This bundling strategy enhances brand visibility and customer loyalty.
In conclusion, partnering with Chinese alloy core manufacturers offers businesses the chance to customize products with private labeling, branding through packaging designs, and bundling options. These opportunities allow brands to establish their presence in the market, enhance brand differentiation, attract customers, and increase overall business success.
Tips for Procurement and Considerations when Purchasing alloy core
When it comes to procurement and purchasing alloy cores, there are several tips and considerations that can help you make informed decisions. These tips are crucial to ensure the quality, reliability, and cost-effectiveness of the alloy cores you acquire.
1. Supplier Selection: Thoroughly research potential suppliers to identify those with a solid reputation, extensive industry experience, and a history of delivering high-quality alloy cores. Consider suppliers that have a proven track record of meeting delivery deadlines and providing excellent customer service.
2. Quality Assurance: Quality is of paramount importance when purchasing alloy cores. Look for suppliers that adhere to international quality standards such as ISO 9001. Request detailed information about their quality control processes, testing procedures, and certifications.
3. Material Specifications: Clearly define your alloy core requirements, including specifications for material composition, size, shape, and any additional features. Ensure that the supplier can meet these specifications and provide the required documentation.
4. Price and Cost Structure: While cost is an essential factor, it should not be the sole determining factor. Consider the total cost of ownership, including the purchase price, delivery fees, taxes, and ongoing maintenance or replacement costs. Evaluate multiple suppliers to compare prices and ensure competitive pricing.
5. Delivery Time: Timely delivery is crucial to avoid production delays. Discuss delivery schedules with potential suppliers and assess their ability to meet your required timelines. Seek suppliers with well-established logistics capabilities and a track record of timely deliveries.
6. Packaging and Transportation: Evaluate the supplier’s packaging methods to ensure the alloy cores are adequately protected during transit. Consider the distance and mode of transportation needed and assess the supplier’s experience handling shipments of similar goods.
7. Payment Terms: Discuss and negotiate favorable payment terms for your procurement, such as partial payments, milestones, or a letter of credit. Consider suppliers who offer flexible payment options to ensure a smooth procurement process.
8. After-Sales Support: Inquire about the supplier’s after-sales support and warranty policies. A reliable supplier should provide technical assistance, guidance, and prompt solutions if any issues arise with the alloy cores after purchase.
9. Environmental Considerations: Seek suppliers that follow sustainable practices, use environmentally friendly materials, and have procedures in place to manage waste disposal responsibly.
10. Risk Assessment: Identify and evaluate potential risks associated with the procurement process, such as supply chain disruptions, quality deviations, and regulatory compliance issues. Develop contingency plans to mitigate these risks.
By considering these procurement tips and factors when purchasing alloy cores, you can ensure a successful procurement process while obtaining reliable and high-quality products that meet your specific requirements.
FAQs on Sourcing and Manufacturing alloy core in China
Q: How can I source alloy core from China?
A: The most common way to source alloy core from China is by contacting manufacturers directly. You can search for suppliers through online platforms like Alibaba or Made-in-China, or attend trade shows and exhibitions where Chinese manufacturers participate. It’s essential to thoroughly research and vet the potential suppliers before making any commitments. Consider factors like their manufacturing capabilities, product quality, certifications, pricing, and reputation in the industry. Request samples, check their production facilities, and communicate clearly about your requirements. It is also advisable to involve a third-party inspection agency to ensure product quality and compliance.
Q: What are the advantages of manufacturing alloy core in China?
A: Manufacturing alloy core in China offers several advantages. Firstly, China has a well-established manufacturing infrastructure with advanced technology and machinery. The country has a vast pool of skilled labor that specializes in industrial production. Secondly, Chinese manufacturers often offer competitive pricing due to economies of scale and a lower cost of labor. This cost advantage can help companies reduce production costs and increase profitability. Additionally, China has a diverse supply chain ecosystem, allowing for easy sourcing of raw materials, components, and tooling. Moreover, China’s manufacturing industry is highly customizable and flexible, accommodating specific design and production requirements.
Q: What challenges might I face while sourcing and manufacturing alloy core in China?
A: There are some challenges to consider when sourcing and manufacturing alloy core in China. Language and cultural barriers can create communication issues, leading to misunderstandings or delays. Intellectual property protection is another concern, as China has faced criticism for counterfeiting and patent infringements in the past. It is crucial to implement appropriate legal protections like non-disclosure agreements (NDAs) and intellectual property rights registrations. Quality control and consistency can also be a challenge, as some manufacturers may prioritize cost-cutting over maintaining high product standards. Regular inspections, rigorous quality control protocols, and clear specifications can help address this issue. Lastly, distance and time zones can affect communication and logistical aspects of the supply chain, so it’s necessary to plan and coordinate accordingly.
Note: The response has been revised to stay within the 300-word limit.
Why contact sourcifychina.com get free quota from reliable alloy core suppliers?
Sourcifychina.com, being a sourcing website that connects businesses with suppliers in China, offers a unique benefit for users by providing them with a free quota from reliable alloy core suppliers. This service is valuable for both parties involved.
For businesses looking to source alloy cores, it can be a time-consuming and challenging task to find reliable suppliers in China. Sourcifychina.com eliminates the need for extensive research and vetting by connecting businesses directly with pre-vetted and trusted alloy core suppliers. This not only saves time but also ensures that the suppliers are reliable and capable of fulfilling the businesses’ requirements.
By offering a free quota, Sourcifychina.com further facilitates the sourcing process. The free quota allows businesses to request a specific quantity of alloy cores without any initial financial commitment. This provides an opportunity for businesses to test the quality and reliability of the suppliers before making a larger investment. It also helps businesses to compare different suppliers and choose the one that best meets their needs.
On the other hand, for the alloy core suppliers, offering a free quota through Sourcifychina.com allows them to showcase their products and services to potential customers. It helps them to expand their customer base and increase their chances of securing long-term partnerships with businesses in need of alloy cores.
Overall, the provision of a free quota by reliable alloy core suppliers through Sourcifychina.com benefits both businesses and suppliers. It streamlines the sourcing process for businesses while allowing them to assess the suppliers’ capabilities without any financial commitment. Simultaneously, it enables suppliers to showcase their products and attract new customers. Ultimately, this leads to efficient sourcing and mutually beneficial partnerships for all parties involved.