Introduce about automatic injection moulding machine guide,Qulity,Cost,Supplier,Certification,Market,Tips,FAQ
Automatic injection molding machines are advanced machines utilized in the manufacturing industry to produce plastic components with precision and efficiency. This guide aims to provide an overview of these machines, focusing on aspects such as quality, cost, suppliers, certification, market, tips, and frequently asked questions (FAQs).
Quality: Automatic injection molding machines boast high-quality components that ensure consistent and precise production. These machines offer tight tolerances, minimal variations, and excellent repeatability, resulting in superior product quality.
Cost: The cost of automatic injection molding machines can vary depending on factors such as machine specifications, size, and features. These machines generally represent a significant investment, but the long-term benefits of enhanced productivity and reduced labor costs outweigh the initial expenditure.
Supplier: Numerous manufacturers specialize in producing and supplying automatic injection molding machines. Renowned suppliers include Arburg, Husky Injection Molding Systems, Engel, Sumitomo (SHI) Demag, etc. Evaluating suppliers based on their reputation, customer reviews, and after-sales service is crucial in selecting a reliable and suitable supplier.
Certification: When purchasing an automatic injection molding machine, it is essential to ensure that the machine meets industry standards and safety regulations. Certification, such as ISO or CE, validates the machine’s quality, safety, and compliance with international standards.
Market: The market for automatic injection molding machines is witnessing steady growth globally, driven by increasing demand for plastic products across various industries such as automotive, packaging, healthcare, electronics, and consumer goods. Emerging economies, like China and India, are experiencing significant expansion in their manufacturing sectors, further fueling the growth of this market.
Tips: Prior to investing in an automatic injection molding machine, it is crucial to assess specific requirements, production volume, material compatibility, and expected return on investment. Consulting with industry experts, conducting thorough research, and considering future scalability are essential tips for making an informed decision.
FAQ: Common FAQs regarding automatic injection molding machines include queries about machine operation, maintenance, troubleshooting, and specific application capabilities. Answers to these FAQs can provide valuable insights for potential buyers and users seeking clarification on various aspects related to these machines.
In summary, automatic injection molding machines offer high-quality production, albeit at a significant cost. Evaluating reliable suppliers, ensuring certification, considering market trends, and adhering to industry tips are essential when considering investment in these machines. Through proper understanding and research, businesses can harness the benefits of automatic injection molding machines for enhanced productivity and product quality.
Types of automatic injection moulding machine
There are several types of automatic injection moulding machines that are commonly used in the manufacturing industry. These machines are designed to produce large quantities of molded plastic parts with minimal manual intervention. The choice of machine depends on various factors such as the type of material being used, the desired end product, and the production volume required.
One common type of automatic injection moulding machine is the hydraulic machine. These machines use hydraulic pressure to clamp the mold and inject the molten plastic into the mold cavity. Hydraulic machines are known for their high clamping force, precision, and versatility. They are suitable for a wide range of plastic materials and can produce parts of different shapes and sizes.
Another type of automatic injection moulding machine is the electric machine. These machines use electrical servo motors to drive the machine functions. Electric machines are known for their energy efficiency, faster cycle times, and high precision. They are often preferred for applications that require high repeatability and tight tolerances.
In recent years, hybrid machines have also become popular. These machines combine the features of hydraulic and electric machines to provide improved performance and energy efficiency. Hybrid machines use electric servo motors for the injection unit and hydraulic systems for the clamping unit. This combination provides the benefits of both technologies, resulting in faster cycles, reduced energy consumption, and improved precision.
In addition to these, there are also specialized types of automatic injection moulding machines such as multi-component machines and multi-color machines. Multi-component machines are used to produce parts with multiple materials or colors in a single shot. They have multiple injection units and can sequentially inject different materials or colors into the mold cavity.
Overall, the choice of automatic injection moulding machine depends on the specific requirements of the production process. Factors such as material type, part complexity, production volume, and cost considerations play a significant role in determining the most suitable machine for a given application.
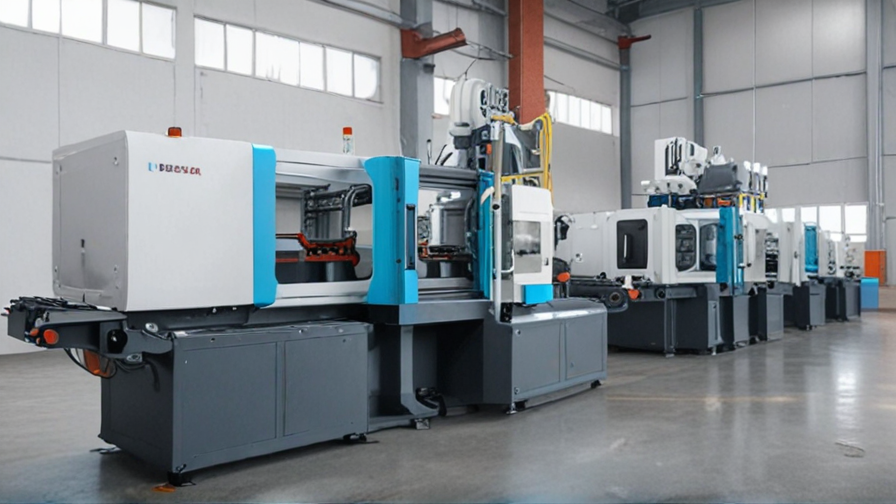
Pros and Cons of Using automatic injection moulding machine
Automatic injection molding machines are widely used in manufacturing industries due to their efficiency and accuracy in producing large quantities of plastic parts. However, like any technology, they come with their own set of pros and cons.
Pros:
1. Increased productivity: Automatic injection molding machines can cycle at a faster rate, allowing for a higher production output. This helps to meet tight deadlines and fulfill customer demands.
2. Consistent quality: These machines offer precise control over variables such as temperature, pressure, and injection speed, ensuring consistent quality in each molded part. This minimizes the chances of defective products and reduces material wastage.
3. Cost-effective: Despite the initial high cost of purchasing an automatic injection molding machine, their long-term benefits outweigh the investment. Higher productivity, reduced labor costs, and minimal scrap rates contribute to overall cost savings.
4. Improved efficiency: With automated functions, such as material feeding, mold clamping, and injection molding, the need for manual intervention is significantly reduced. This leads to increased operational efficiency and reduction in error rates.
Cons:
1. High upfront cost: The initial investment required to purchase an automatic injection molding machine can be substantial, making it a barrier for small businesses or startups.
2. Technical expertise required: Operating and maintaining an automatic injection molding machine requires specialized knowledge and skills. Training the workforce and recruiting skilled technicians can be time-consuming and expensive.
3. Limited flexibility: These machines are designed to manufacture specific types and sizes of parts. If there is a requirement for customization or the production of different products, reconfiguration or investment in additional machinery may be necessary.
4. Downtime and maintenance: Like any mechanical equipment, automatic injection molding machines require regular maintenance and occasional repairs. Downtime during maintenance or breakdowns can disrupt production schedules and lead to delays.
In conclusion, automatic injection molding machines offer numerous advantages in terms of productivity, quality, and cost-effectiveness. However, the high upfront cost, technical expertise requirement, limited flexibility, and maintenance issues should be carefully considered before making a decision to invest in this technology.
automatic injection moulding machine Reference Specifications (varies for different product)
An automatic injection molding machine is a highly advanced manufacturing tool that is used for large-scale production of plastic products. It is capable of producing a wide range of products, including but not limited to toys, household items, automotive components, and medical devices.
The machine operates by injecting molten plastic material into a mold cavity under high pressure. It consists of several key components, including an injection unit, a clamping unit, and a control system. The injection unit is responsible for melting and injecting the plastic material into the mold, while the clamping unit securely holds the mold in place during the injection process. The control system monitors and regulates various parameters, such as temperature, pressure, and cycle time, to ensure consistent and precise production.
The specifications of an automatic injection molding machine can vary depending on the specific product being manufactured. However, some common reference specifications include:
1. Clamping Force: This refers to the maximum amount of force the machine can exert on the mold to keep it closed during injection. It is typically measured in tons and can range from a few tons to several hundred tons.
2. Injection Capacity: It indicates the maximum volume of molten plastic that the machine can inject into the mold. It is measured in grams or ounces and can vary from a few grams to several kilograms.
3. Injection Speed: This refers to the rate at which the plastic material is injected into the mold. It is typically measured in millimeters per second and can vary depending on the complexity of the product and the type of plastic being used.
4. Mold Size: It specifies the maximum dimensions of the mold that can be accommodated by the machine. This is crucial as it determines the size and shape of the final product that can be produced.
5. Energy Consumption: This indicates the amount of energy required to operate the machine. It is measured in kilowatt-hours (kWh) and varies based on the machine’s design, efficiency, and production capacity.
In summary, an automatic injection molding machine is a versatile and efficient manufacturing tool that offers high-speed production of plastic products. Its reference specifications vary depending on the specific product, but generally include clamping force, injection capacity, injection speed, mold size, and energy consumption.
Applications of automatic injection moulding machine
Automatic injection moulding machines have revolutionized the manufacturing industry due to their efficiency, accuracy, and versatility. Their applications span various sectors, including automotive, electronics, medical, and consumer goods. Here are some key applications of automatic injection moulding machines:
1. Automotive Industry: Automatic injection moulding machines are extensively used in the automotive sector for manufacturing various components such as interior and exterior trims, dashboard panels, door handles, bumpers, engine parts, and more. The machines enable mass production of these components with high precision and consistency.
2. Electronics Industry: Injection moulding machines are widely employed in the electronics industry to manufacture products like computer and laptop components, mobile phone cases, chargers, connectors, keypads, and other small intricate parts. The machines ensure consistent quality and quick production to meet the fast-paced demands of this sector.
3. Medical Industry: Automatic injection moulding machines play a critical role in the medical sector for manufacturing a wide range of products such as syringe barrels, IV connectors, medical device housings, pipette tips, and various surgical instruments. These machines adhere to strict hygiene standards and provide reliable and high-quality products that are essential for the medical field.
4. Consumer Goods Industry: Injection moulding machines are utilized in the consumer goods industry to produce a vast array of items such as plastic bottles, containers, toys, kitchenware, household appliances, and packaging materials. The machines enable cost-effective mass production of these items, meeting the ever-growing demands of consumers.
5. Packaging Industry: Automatic injection moulding machines are extensively used in the packaging industry to manufacture plastic caps, closures, containers, and bottles. These machines offer high production rates, consistent quality, and precise dimensions, making them vital for packaging solutions.
6. Industrial Components: Various industrial components, including gears, bearings, valves, connectors, and housings, are manufactured using automatic injection moulding machines. These machines can produce complex shapes and designs, ensuring a reliable and durable end product.
7. Aerospace Industry: Injection moulding machines find applications in the aerospace sector for manufacturing components such as lightweight interior cabin parts, air ducts, brackets, and connectors. The machines enable the production of components with high strength, thin walls, and intricate designs, meeting the stringent requirements of the aerospace industry.
In conclusion, automatic injection moulding machines have a wide range of applications across industries, including automotive, electronics, medical, consumer goods, packaging, industrial, and aerospace sectors. These machines offer efficient, accurate, and versatile production capabilities, enabling the mass production of high-quality plastic components and products.
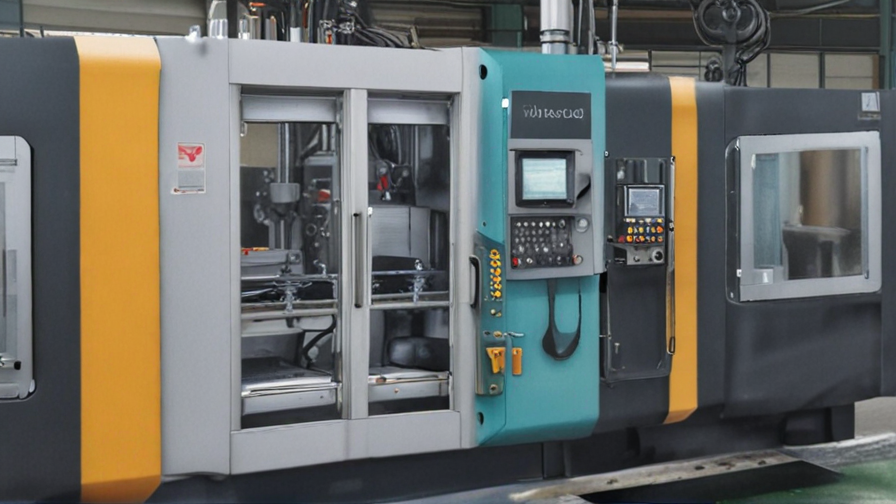
The Work Process and how to use automatic injection moulding machine
The work process of an automatic injection moulding machine involves several steps. Firstly, the raw material, typically in the form of plastic granules, is melted and heated inside the machine’s barrel. The barrel has a rotating screw that helps in mixing and melting the material uniformly. Once the material is molten, the machine injects it into a mould cavity using a nozzle. The mould is a hollow cavity that determines the shape and size of the final product.
After the molten material is injected into the mould, it is left to cool and solidify. This process is known as the cooling phase and can take a few seconds to a few minutes depending on the material and the size of the product. Once the material has solidified, the mould opens, and the finished product is ejected using ejector pins or plates.
To use an automatic injection moulding machine, start by selecting the appropriate mould for your desired product. Clean the mould cavity and install it securely onto the machine. Next, adjust the machine’s settings such as temperature, pressure, and injection speed according to the material being used and the desired product specifications. Ensure that the material hopper is filled with the required amount of raw material.
Once all the necessary adjustments are made, power on the machine and let it heat up to the desired temperature. This may take a few minutes. Once the machine has reached the set temperature, initiate the injection process using the machine’s control panel. The machine will automatically inject the molten material into the mould cavity following the pre-set parameters.
During the cooling phase, regularly monitor the machine and ensure that the cooling system is functioning properly. Once the product has solidified, the machine will automatically open the mould and eject the finished product. Carefully remove the product from the mould and inspect it for any defects or imperfections.
Periodically clean and maintain the automatic injection moulding machine to ensure its optimal performance. This includes regular lubrication, cleaning of the barrel, and checking for any wear or damage.
In conclusion, an automatic injection moulding machine follows a sequential process of melting, injecting, cooling, opening, and ejecting to produce finished plastic products. By understanding and properly adjusting the machine’s settings, one can efficiently use the machine to manufacture high-quality plastic products.
Quality Testing Methods for automatic injection moulding machine and how to control the quality
One of the key quality testing methods for automatic injection moulding machines is the process of validating the moulding parameters. This includes checking the machine settings such as temperature, pressure, and speed, to ensure they meet the required specifications for each specific moulding job. This validation process usually involves running test samples and analyzing them for any defects or inconsistencies.
Another important quality testing method is the inspection of the finished moulded products. This can be done visually, where operators inspect the products for any visible defects such as surface imperfections, flashing, or deformities. Alternatively, automated inspection systems can be employed to detect and analyze any defects more accurately. These systems use techniques such as image processing or sensor-based measurements to identify any deviations from the desired product specifications.
To control the quality of the output, it is essential to establish a robust quality control system. This involves implementing regular checks and audits throughout the entire production process to ensure the equipment is operating within the desired parameters. This can be achieved through periodic calibration and maintenance of the machine, as well as training and monitoring of the operators to ensure they follow the correct procedures.
In addition to these methods, statistical process control techniques can also be used to monitor and control the quality of the injection moulding process. This involves collecting data from various stages of the process and using statistical analysis to identify any trends or deviations. By continuously monitoring and analyzing this data, any potential quality issues can be identified and addressed proactively.
Overall, a combination of validation testing, inspection, quality control systems, and statistical process control can help ensure the quality of products produced by automatic injection moulding machines. By regularly monitoring and adjusting the machine settings and implementing appropriate quality control measures, manufacturers can minimize defects and produce consistent, high-quality moulded products.
automatic injection moulding machine Sample Policy and Post-Purchase Considerations for automatic injection moulding machine from China
Sample Policy:
When purchasing an automatic injection moulding machine from China, it is important to consider certain factors such as quality, pricing, warranty, and after-sales service. Here is a sample policy for your reference:
1. Quality Assurance: Ensure that the supplier follows strict quality control measures and adheres to international standards. Look for certifications like ISO and CE to ensure product quality.
2. Pricing: Compare prices from different suppliers to get the best deal. However, be cautious of significantly lower prices as it may indicate compromised quality.
3. Warranty: Check for the warranty period offered by the supplier. A longer warranty period indicates the supplier’s confidence in their product. Ensure that warranty terms are clearly defined, covering both the machine and its components.
4. After-sales Service: Evaluate the supplier’s after-sales service capabilities such as technical support, spare parts availability, and maintenance services. Prompt and reliable after-sales service is crucial for uninterrupted operation.
5. Customization: If specific requirements are needed, inquire if the supplier can customize the machine accordingly. This could include size, capacity, or specific features.
Post-Purchase Considerations:
After purchasing an automatic injection moulding machine from China, it is essential to take several steps to ensure a smooth operation. Here are some considerations:
1. Installation and Training: Arrange for professional installation and training by qualified technicians to ensure proper setup and efficient operation of the machine.
2. Regular Maintenance: Follow the recommended maintenance schedule provided by the supplier to prolong the machine’s lifespan and prevent unexpected breakdowns.
3. Spare Parts: Keep a stock of commonly used spare parts to minimize downtime in case of any component failures. Check with the supplier regarding the availability and lead time for spare parts.
4. Technical Support: Maintain good communication with the supplier to address any technical issues or concerns promptly. Ensure the supplier can provide remote or on-site technical support when needed.
5. Feedback and Reviews: Provide feedback to the supplier about the machine’s performance, reliability, and any issues faced. This not only helps the supplier improve their products but also helps other potential buyers make informed decisions.
By following this sample policy and post-purchase considerations, you can ensure an efficient and reliable automatic injection moulding machine purchase from China.
Sourcing automatic injection moulding machine from China: Opportunities, Risks, and Key Players
China has emerged as a leading global supplier of injection moulding machines due to its affordable costs, technological advancements, and strong manufacturing capabilities. Sourcing an automatic injection moulding machine from China presents several opportunities, but also risks that should be carefully considered.
Opportunities:
1. Cost advantage: Chinese injection moulding machines are generally more affordable compared to machines from other regions, enabling cost savings for businesses.
2. Technological advancements: China has made significant progress in developing advanced injection moulding machines, offering a wide range of options to meet various production needs.
3. Manufacturing capabilities: China’s vast manufacturing industry ensures a wide availability of machines and parts, facilitating prompt product delivery and after-sales service.
Risks:
1. Quality concerns: In some cases, Chinese manufacturers may prioritize price competitiveness over quality. Vigilance is needed to ensure the chosen machine meets required standards.
2. Intellectual property issues: China has a reputation for inadequate intellectual property protection. There’s a risk of counterfeited or replicated machines, which may lead to patent infringements or compromised machine performance.
3. Communication challenges: Language barriers and cultural differences may pose obstacles when discussing technical specifications, customization requirements, or addressing post-sales support.
Key Players:
1. Haitian International Holding Ltd: A renowned Chinese company specializing in injection moulding machines, offering a wide range of machines with superior performance and energy efficiency.
2. Chen Hsong Holdings Limited: A leading manufacturer of injection moulding machines in China, known for its constant innovation and a global presence.
3. Borch Machinery Co., Ltd: Known for its advanced technology, Borch Machinery offers a comprehensive range of injection moulding machines suitable for various industries.
In conclusion, sourcing an automatic injection moulding machine from China provides opportunities in terms of cost advantage, technological advancements, and manufacturing capabilities. However, risks such as quality concerns, intellectual property issues, and communication challenges should be carefully considered. Key players like Haitian International Holding Ltd, Chen Hsong Holdings Limited, and Borch Machinery Co., Ltd are prominent options to explore within the Chinese market.
How to find and select reliable automatic injection moulding machine manufacturers in China,use google search manufacturers and suppliers
Finding reliable automatic injection moulding machine manufacturers in China can be a daunting task, but with the help of Google search and some key factors to consider, the process can be simplified. Here are some steps to follow in order to find and select a reliable manufacturer:
1. Research and compile a list: Start by conducting a thorough online search using keywords like “automatic injection moulding machine manufacturers in China.” This will generate a list of potential suppliers.
2. Evaluate the company’s website: Go through the websites of each manufacturer on the list. Look for professional design, comprehensive information about their products, certifications, manufacturing capabilities, and any relevant industry affiliations. A well-designed and informative website indicates that the company is serious about their business.
3. Assess manufacturing capabilities: Determine if the manufacturer has the capability to produce automatic injection moulding machines according to your requirements. Look for details about their production processes, machinery, quality control measures, and the size of their factory. It is advisable to choose a manufacturer with a larger factory as they tend to have more experience and resources.
4. Product quality and certifications: Check if the manufacturer has the necessary certifications like ISO 9001, CE, or other relevant standards for manufacturing automatic injection moulding machines. These certifications ensure that the manufacturer follows quality standards and provides reliable products.
5. Customer reviews and testimonials: Look for customer reviews and testimonials on the manufacturer’s website or other trusted review platforms. Positive feedback from previous customers is a good indication of the manufacturer’s reliability and product quality.
6. Communication and support: Evaluate the manufacturer’s responsiveness and ability to communicate effectively in English. Prompt and clear communication is crucial for a successful manufacturing partnership. Additionally, check if they offer technical support and after-sales service.
7. Request samples and visit the facility: If possible, request samples of the manufacturer’s automatic injection moulding machines to assess the quality firsthand. You may also consider visiting the manufacturer’s facility in China, which will provide a deeper understanding of their capabilities and production processes.
By following these steps and conducting thorough research, you can find and select a reliable automatic injection moulding machine manufacturer in China. Take your time to ensure that the chosen manufacturer meets your specific requirements and can provide high-quality machines.
How to check automatic injection moulding machine manufacturers website reliable,use google chrome SEOquake check if ranking in top 10M
To ensure the reliability of an automatic injection molding machine manufacturer’s website, you can follow these steps:
1. Use Google Chrome: Open the website using the Google Chrome browser. This browser is popularly used and offers various tools and extensions that can help evaluate the reliability of a website.
2. Install SEOquake: Install the SEOquake extension on your Google Chrome browser. This extension provides valuable insights and metrics about a website’s performance and credibility.
3. Check the website ranking: Activate the SEOquake extension by clicking on the icon in the browser toolbar. Once activated, a small SEOquake bar will appear below the website address. Click on the “Rank” tab, and it will display the website’s current ranking within the top 10 million websites. A higher ranking indicates better reliability.
4. Evaluate other factors: While checking the website’s ranking is a good indication of credibility, it’s also essential to consider other factors. Assess the overall website design, user experience, relevant content, and information provided. Look for clear contact information, product details, and an established company profile.
5. Read reviews and testimonials: Look for reviews and testimonials from other customers or industry experts regarding the manufacturer’s products and services. These reviews can provide valuable insights into the reliability and credibility of the manufacturer.
6. Word of mouth and recommendations: Seek recommendations or feedback from others who have previously dealt with the manufacturer. This firsthand information can help you to determine the reliability of their website and products.
Remember that ranking in the top 10 million does not guarantee reliability, but it can be a good starting point for evaluation. It is essential to consider multiple factors and utilize various tools to assess the trustworthiness and reliability of an automatic injection molding machine manufacturer’s website.
Top 10 automatic injection moulding machine manufacturers in China with each 160 words introduce products,then use markdown create table compare
1. Haitian International Holdings Ltd. (Haitian) is one of the leading manufacturers of automatic injection moulding machines in China. Their machines are known for their high efficiency, reliability, and precision in producing high-quality plastic products. Haitian offers a wide range of machines, including the Mars Series, Jupiter Series, and ZE Series, catering to various moulding needs.
2. Chen Hsong Holdings Limited (Chen Hsong) is another prominent manufacturer in China. They have an extensive product portfolio ranging from small to large machines, suitable for diverse applications. Chen Hsong’s machines are known for their energy efficiency, stability, and high-performance capabilities. They offer the JM-SVP/2 Series, SuperMaster Series, and MK Series, among others.
3. Ningbo Haida Plastic Machinery Co., Ltd. (Haida) specializes in the production of automatic injection moulding machines and auxiliary equipment. Their machines are designed for high-speed and high-precision moulding, ensuring consistent and reliable production. Haida offers the HDX Series, HDJS Series, and HDJL Series, providing a comprehensive range to meet various customer requirements.
4. Yizumi Group is a well-known manufacturer offering a full range of automatic injection moulding machines to meet diverse industrial needs. Yizumi’s machines are equipped with advanced technologies and innovative features, ensuring high efficiency and accuracy. Their product range includes the UN series, DP series, and A5 series, among others.
5. Borch Machinery Co., Ltd. specializes in the production of automatic injection moulding machines with a focus on providing advanced solutions for various industries. Borch’s machines are known for their energy-saving capabilities, stability, and high-speed production. They offer the BU series, BS series, and BM series, catering to different moulding requirements.
6. Engel Machinery (Changzhou) Co., Ltd. is a subsidiary of the Austrian-based Engel Group. They manufacture automatic injection moulding machines with a strong emphasis on precision, speed, and energy efficiency. Engel’s machines are equipped with advanced control systems, ensuring optimal performance. Their product range includes the e-cap series, e-motion series, and e-victory series.
7. Arburg (Shanghai) Machinery Trading Co., Ltd. belongs to the German-based Arburg Group and produces automatic injection moulding machines utilizing advanced technologies. Arburg’s machines are known for their flexibility, precision, and reliability. They offer the Allrounder series, which caters to various industries and applications.
8. Guangdong Yizumi Precision Machinery Co., Ltd. (Yizumi) specializes in the production of high-quality automatic injection moulding machines. Yizumi’s machines are designed for precision moulding, ensuring consistent and accurate production. Their product range includes the A5 series, FE series, and M series, providing versatility and reliability.
9. Sumitomo (SHI) Demag Plastics Machinery (Ningbo) Co., Ltd. is a joint venture between Japanese-based Sumitomo Heavy Industries and Germany-based Demag Plastics Group. They manufacture automatic injection moulding machines known for their precision, efficiency, and reliability. Sumitomo (SHI) Demag offers the Systec series, El-Exis series, and Evolution series, providing advanced solutions for various industries.
10. Dakumar Machinery Co., Ltd. specializes in the production of automatic injection moulding machines and auxiliary equipment. Dakumar’s machines are characterized by their energy efficiency, stability, and user-friendly operation. They offer the DKM series and DE series, catering to different moulding requirements.
| Manufacturer | Notable Product Series | Key Features |
|—————————————————|—————————|—————————————————–|
| Haitian International Holdings Ltd. (Haitian) | Mars Series, Jupiter Series, ZE Series | High efficiency, reliability, precise moulding |
| Chen Hsong Holdings Limited (Chen Hsong) | JM-SVP/2 Series, SuperMaster Series, MK Series | Energy efficiency, stability, high-performance |
| Ningbo Haida Plastic Machinery Co., Ltd. (Haida) | HDX Series, HDJS Series, HDJL Series | High-speed, high-precision moulding |
| Yizumi Group | UN series, DP series, A5 series | Advanced technologies, high efficiency |
| Borch Machinery Co., Ltd. | BU series, BS series, BM series | Energy-saving, stability, high-speed |
| Engel Machinery (Changzhou) Co., Ltd. | e-cap series, e-motion series, e-victory series | Precision, speed, energy efficiency |
| Arburg (Shanghai) Machinery Trading Co., Ltd. | Allrounder series | Flexibility, precision, reliability |
| Guangdong Yizumi Precision Machinery Co., Ltd. | A5 series, FE series, M series | Precision moulding, consistent production |
| Sumitomo (SHI) Demag Plastics Machinery (Ningbo) Co., Ltd. | Systec series, El-Exis series, Evolution series | Precision, efficiency, reliability |
| Dakumar Machinery Co., Ltd. | DKM series, DE series | Energy efficiency, stability, user-friendly |
In this markdown table, the top 10 automatic injection moulding machine manufacturers in China are compared based on their notable product series and key features. The table provides a concise overview of each manufacturer, making it easier for readers to compare their offerings.
Background Research for automatic injection moulding machine manufacturers Companies in China, use qcc.com archive.org importyeti.com
Automatic injection molding machines are essential in the manufacturing industry as they streamline the process of injecting molten material into molds to create a variety of plastic products. China, being one of the world’s prominent manufacturing hubs, is home to numerous manufacturers specializing in automatic injection molding machines. Some notable companies in this field include:
1. Haitian International Holdings Limited: With over 50 years of experience, Haitian is the world’s largest supplier of plastic injection molding machines. They offer a wide range of machinery, including servo-hydraulic and all-electric models, catering to different production needs.
2. Ningbo Haixing Plastic Machinery Manufacturing Co., Ltd.: Founded in 2003, Haixing specializes in the production of precision plastic injection molding machines. They are known for their advanced technology, high-quality products, and excellent customer service.
3. Chen De Plastics Machinery Co., Ltd.: Established in 1986, Chen De is a leading manufacturer of injection molding machines in China. They offer a comprehensive range of machinery, including standard and customized models, to meet specific production requirements.
4. Guangdong Yizumi Precision Machinery Co., Ltd.: Yizumi is known for its innovative and technologically advanced injection molding machines. They focus on intelligent equipment and offer a wide range of products, including high-speed, multi-component, and hybrid models.
5. Zhejiang Sound Machinery Manufacture Co., Ltd.: Sound Machinery has been manufacturing injection molding machines since 1983. They provide a diverse lineup of machines, including hydraulic, electric, and hybrid models, with a focus on energy efficiency and precision.
These companies have a strong presence in the global market and supply their machines to various industries, such as automotive, packaging, electronics, and medical devices. They are known for their reliable performance, advanced technology, and competitive pricing.
To gather more information about these manufacturers, qcc.com, archive.org, and importyeti.com could be useful resources. These platforms provide company profiles, product catalogs, customer reviews, and historical data on these manufacturers. By utilizing these sources, researchers can gain insights into the manufacturing capabilities, product quality, certifications, and global customer base of these companies.
Leveraging Trade Shows and Expos for automatic injection moulding machine Sourcing in China
Trade shows and expos offer a valuable opportunity for sourcing automatic injection moulding machines from China. These events facilitate direct interaction with suppliers, enabling businesses to assess product quality, negotiate prices, and establish partnerships.
China boasts several prominent trade shows and expos that focus specifically on machinery and manufacturing, including the China International Plastic Rubber Industry Exhibition and the China International Import Expo. These events attract a wide range of exhibitors, including manufacturers, distributors, and industry experts.
Attending trade shows and expos provides businesses with access to a variety of automatic injection moulding machine suppliers in one location. This saves time and effort compared to researching and contacting potential suppliers individually. Moreover, face-to-face meetings allow for a more personal and detailed discussion, allowing businesses to better understand the capabilities, specifications, and features of each machine.
Trade shows and expos also provide a platform for businesses to evaluate the quality of the machines being showcased. By physically examining the machines and observing live demonstrations, buyers can assess the build, functioning, and overall performance. This firsthand experience helps ensure that the machines meet the required standards and specifications.
Negotiating prices and establishing partnerships is another key advantage of attending trade shows and expos. Suppliers often offer special discounts or promotions during these events to attract potential buyers. Moreover, face-to-face negotiations provide businesses with more leverage to discuss terms and conditions, seek customization options, and explore long-term cooperation.
In conclusion, trade shows and expos in China offer a valuable opportunity for businesses to source automatic injection moulding machines. They provide a centralized location to meet suppliers, evaluate product quality, negotiate prices, and establish partnerships. By tapping into these events, businesses can streamline the sourcing process and find the most suitable suppliers for their requirements.
The Role of Agents and Sourcing Companies in Facilitating automatic injection moulding machine Purchases from China
Agents and sourcing companies play a crucial role in facilitating the purchase of automatic injection moulding machines from China. These professionals act as intermediaries between buyers and manufacturers, simplifying the entire process and ensuring a smooth transaction.
Firstly, agents and sourcing companies carry out market research and identify reliable manufacturers in China that specialize in automatic injection moulding machines. They have extensive knowledge of the industry and are well-connected with manufacturers, allowing them to find the most suitable options for buyers.
Once potential manufacturers are identified, agents and sourcing companies act as representatives for buyers during negotiations. They have the language skills and cultural understanding necessary to communicate effectively with Chinese manufacturers, ensuring that all parties are on the same page and requirements are clearly understood.
Agents and sourcing companies also have a deep understanding of the Chinese market and can negotiate favorable terms and prices on behalf of buyers. They are experts in the local business culture and can navigate any potential language and cultural barriers, facilitating a successful transaction.
Furthermore, agents and sourcing companies provide important quality control services. They can inspect the injection moulding machines before shipping to ensure that they meet the buyer’s specifications and quality standards. This helps to minimize the risk of receiving faulty or substandard equipment.
Additionally, agents and sourcing companies take care of logistics and shipping arrangements, handling all necessary paperwork and ensuring that the machines are delivered safely and on time. They act as a single point of contact for buyers, simplifying the process and reducing the overall stress of international trade.
In summary, agents and sourcing companies play a vital role in facilitating the purchase of automatic injection moulding machines from China. They simplify the process by researching and identifying reliable manufacturers, negotiating favorable terms, providing quality control services, and managing logistics. Their expertise and local knowledge are essential in ensuring a smooth and successful transaction.
Price Cost Research for automatic injection moulding machine manufacturers Companies in China, use temu.com and 1688.com
When it comes to researching the price costs of automatic injection molding machine manufacturers in China, two reliable sources to consider are Temu.com and 1688.com. These platforms offer a comprehensive range of manufacturers and suppliers to choose from.
Starting with Temu.com, it provides a user-friendly interface to search and compare prices of automatic injection molding machines. The website displays detailed information about the manufacturers, including their product range, specifications, and pricing. This platform ensures transparency by allowing customers to directly communicate with the manufacturers for further inquiries and negotiations. Temu.com assists in obtaining competitive prices for automatic injection molding machines.
Alternatively, 1688.com is a popular wholesale marketplace in China. It offers a wide selection of automatic injection molding machine manufacturers at competitive prices. This website provides comprehensive product descriptions, customer reviews, and supplier ratings. It also lists relevant contact information to facilitate communication with the manufacturers.
When conducting price research on these platforms, several factors should be considered. These include the machine’s specifications, production capacity, and auxiliary equipment. Additionally, customers should assess the manufacturers’ reputation, certifications, and after-sales support to ensure a reliable and trustworthy partnership.
In conclusion, conducting price cost research for automatic injection molding machine manufacturers in China is accessible through Temu.com and 1688.com. With their extensive database and comprehensive information, these platforms enable customers to compare prices, evaluate manufacturers, and make informed purchasing decisions. It is crucial to consider the specific requirements, quality, and reputation of the manufacturer to ensure a successful business collaboration.
Shipping Cost for automatic injection moulding machine import from China
The shipping cost for importing an automatic injection molding machine from China can vary based on several factors. The shipping method, distance, weight, and dimensions of the machine will all contribute to the final cost.
There are generally two main shipping methods for importing goods from China: ocean freight and air freight. Ocean freight is typically more cost-effective but slower, while air freight is faster but pricier. For a heavy and bulky machine like an injection molding machine, ocean freight is commonly chosen due to lower rates.
The distance between the origin and destination ports also affects the shipping cost. Longer distances require more fuel and time, resulting in higher costs. Additionally, the size and weight of the machine play a significant role. The larger and heavier the machine, the more it will cost to ship.
Other factors that might influence shipping costs include customs duties, taxes, and fees imposed by both the exporting and importing countries. These charges must be considered when calculating the total cost.
To obtain an accurate estimate, it is advisable to contact a freight forwarder or shipping agent who specializes in importing machinery from China. They will consider all the aforementioned factors and provide you with a comprehensive breakdown of the shipping costs, including any additional fees or taxes.
It is crucial to keep in mind that shipping costs are just one aspect to consider when importing an automatic injection molding machine. Other expenses like import duties, insurance, customs brokerage charges, and inland transportation must be factored in as well to determine the overall cost.
Compare China and Other automatic injection moulding machine Markets: Products Quality and Price,Visible and Hidden Costs
China is one of the leading players in the automatic injection molding machine market, offering a wide range of products at competitive prices. However, when comparing China to other markets, several factors should be considered including product quality and price, as well as visible and hidden costs.
In terms of product quality, China has made significant advancements in recent years. Chinese manufacturers have improved their manufacturing processes and technologies to produce high-quality automatic injection molding machines. The machines produced in China are now comparable to those from other developed markets, such as Europe and the United States.
Price is another crucial factor when comparing different markets. China has a cost advantage due to its relatively low labor and production costs, allowing manufacturers to offer their products at competitive prices. This cost advantage makes Chinese-made automatic injection molding machines more attractive to buyers who are looking for cost-effective solutions.
However, it is important to consider visible and hidden costs when evaluating different markets. Visible costs include the initial purchase price of the machine, transportation, and import duties. Chinese manufacturers often offer competitive prices for their machines, providing cost savings for buyers. Additionally, China’s well-established logistics infrastructure ensures efficient transportation of the machines domestically and internationally.
Hidden costs, on the other hand, may arise from factors such as maintenance, spare parts, and customer support. While Chinese manufacturers have made substantial improvements in product quality, there can still be concerns regarding the availability of spare parts and the quality of after-sales support. Buyers should carefully evaluate the reputation and reliability of the manufacturer to ensure that hidden costs are minimized.
In conclusion, China’s automatic injection molding machine market offers competitive prices and improved product quality, making it a strong player in the global market. However, buyers should carefully consider visible and hidden costs to make an informed decision. Conducting thorough research, analyzing the reputation and reliability of manufacturers, and considering long-term support can help buyers make the best choice for their specific needs.
Understanding Pricing and Payment Terms for automatic injection moulding machine: A Comparative Guide to Get the Best Deal
When looking to purchase an automatic injection molding machine, it is essential to have a clear understanding of pricing and payment terms to secure the best deal. This comparative guide aims to provide key insights into these aspects within a concise 300-word limit.
Pricing for automatic injection molding machines can vary significantly depending on various factors, including machine size, capacity, and brand reputation. Smaller machines typically range from $10,000 to $50,000, while larger and more advanced machines can cost upwards of $100,000. It is crucial to consider the specific requirements of your production needs and select a machine that offers the best value for money.
In addition to the machine price, it is vital to consider the overall cost of ownership. This includes maintenance, spare parts, energy consumption, and potential upgrades. Some manufacturers may offer discounted or bundle packages for comprehensive after-sales support, which can help reduce long-term expenses.
Payment terms for automatic injection molding machines can vary based on the supplier and individual agreement. The most common methods include upfront payment, installments, or lease/finance options. While upfront payment may offer cash discounts, it may not be suitable for businesses with restricted budgets. Installment plans spread the cost over time, making the investment more manageable. Lease or finance options allow businesses to acquire the machine while paying in regular installments, often with the possibility of upgrading to newer models in the future.
When negotiating the payment terms, it is essential to consider the warranty and service provided. Comprehensive warranties can offer peace of mind, ensuring that any issues or malfunctions are resolved promptly without additional charges.
To get the best deal on an automatic injection molding machine, it is crucial to research and compare different suppliers, assessing their reputation, customer reviews, and technical support. Requesting multiple quotations and discussing payment terms can help negotiate favorable terms and secure the most cost-effective solution.
In conclusion, understanding pricing and payment terms is vital when purchasing an automatic injection molding machine. Careful consideration of machine price, overall costs of ownership, and available payment options can help businesses make informed decisions to obtain the best deal possible.
Chinese Regulations and Industry Standards Certifications for automatic injection moulding machine,Import Regulations and Customs for automatic injection moulding machine from China
Chinese Regulations and Industry Standards Certifications for automatic injection moulding machine
In China, the production and sale of automatic injection moulding machines are subject to several regulations and industry standards. The primary regulations governing the manufacturing and operation of these machines are:
1. China Compulsory Certification (CCC): The CCC mark is mandatory for products entering the Chinese market, including automatic injection moulding machines. It ensures that the products meet the specified safety, quality, and environmental requirements.
2. Machinery Industry Standard (MIS): MIS provides guidelines and standards for the design, manufacturing, safety, and testing of automatic injection moulding machines in China. Compliance with MIS is essential for manufacturers to ensure their machines meet the industry requirements.
3. Safety Regulation of Special Equipment: Automatic injection moulding machines are considered special equipment in China, and they need to comply with specific safety regulations. These safety regulations aim to prevent workplace accidents and ensure the equipment’s safe operation.
4. Environmental Protection Standards: China has strict environmental protection standards that automatic injection moulding machines must adhere to. Machines should meet the requirements for energy efficiency, emissions, and waste management to minimize their impact on the environment.
Import Regulations and Customs for automatic injection moulding machine from China
When importing automatic injection moulding machines from China, it is crucial to understand the import regulations and customs procedures. Some of the key aspects to consider are:
1. Import Duties and Taxes: Importing automatic injection moulding machines into most countries attracts customs duties and taxes. Importers should familiarize themselves with the specific duties and taxes applicable in their respective countries to ensure compliance.
2. Customs Documentation: Importers need to provide various documents to clear customs, including packing lists, commercial invoices, bill of lading, and certificates of origin. These documents help customs authorities verify the authenticity and legality of the imported machines.
3. Product Inspection and Testing: Some countries may require imported automatic injection moulding machines to undergo inspections and testing to ensure compliance with local regulations and standards. Importers should be prepared to facilitate such inspections, which may include electrical safety testing and conformity assessments.
4. Import Licensing and Permits: Depending on the destination country, importing automatic injection moulding machines may require obtaining import licenses or permits. Importers should check with the appropriate authorities in their country to determine the specific requirements.
In conclusion, compliance with Chinese regulations and industry standards certifications is crucial for the manufacturing and sale of automatic injection moulding machines. Importers must also adhere to import regulations and customs procedures to successfully bring these machines from China while ensuring compliance with local requirements.
Sustainability and Environmental Considerations in automatic injection moulding machine Manufacturing
Automatic injection moulding machines play a vital role in the manufacturing industry. However, their production and operation should also consider sustainability and environmental factors. Several considerations can be made to minimize their impact on the environment.
Firstly, the materials used in the manufacturing of automatic injection moulding machines should be carefully chosen. Sustainable materials like recycled plastics and metals can be utilized to reduce the overall carbon footprint. Additionally, the production process should aim for minimal waste generation by implementing efficient material handling and recycling systems.
Energy efficiency is another key aspect to consider. Automatic injection moulding machines should be designed to consume minimal energy during their operation. This can be achieved through the use of energy-efficient electric motors, optimized heating and cooling systems, and advanced control algorithms. Moreover, integrating renewable energy sources like solar or wind power could further reduce the machines’ environmental impact.
Water conservation is also important in the manufacturing process. Injection moulding machines typically require water for cooling purposes. Implementing closed-loop cooling systems and water treatment technologies can help minimize water consumption and reduce the strain on local water resources. Efforts should also be made to ensure proper disposal of wastewater generated during the production process.
Lastly, end-of-life considerations are crucial. Automatic injection moulding machines should be designed with recyclability and reusability in mind. Implementing easy disassembly and separation of materials will facilitate recycling at the end of their lifecycle. Proper disposal plans should be in place to avoid machines ending up in landfills.
In conclusion, sustainability and environmental considerations should be integrated throughout the lifecycle of automatic injection moulding machines. Material choice, energy efficiency, water conservation, and end-of-life management are key areas to focus on. By optimizing these aspects, manufacturers can minimize the environmental impact of these machines and contribute to a more sustainable manufacturing industry.
List The Evolution history of “automatic injection moulding machine”
The evolution of automatic injection molding machines has been a fascinating journey that spans over several decades. It all began in the late 1800s when the first manually operated injection molding machines were introduced. These machines were rudimentary and required significant human intervention throughout the manufacturing process.
The early 20th century marked the emergence of semi-automatic injection molding machines. These machines incorporated basic automation features such as automatic material feeding and ejection mechanisms, which reduced the need for constant manual labor. However, operators were still required to manually open and close the mold and initiate the injection process.
By the 1960s, fully automatic injection molding machines became a reality. These machines leveraged hydraulic power to automate the entire manufacturing process. They featured automatic mold opening and closing, injection, and ejection systems. With these advancements, operators only needed to load the molds and initiate the machine, allowing for a higher level of productivity and efficiency.
Throughout the 1970s and 1980s, the demand for faster and more precise injection molding led to significant advancements in the technology. Microprocessor control systems were integrated into automatic injection molding machines, allowing for greater accuracy and repeatability. Additionally, hydraulic systems were improved to provide better control over the injection speed, pressure, and temperature, resulting in higher quality molded parts.
In the 1990s, the introduction of electric injection molding machines revolutionized the industry. These machines replaced the traditional hydraulic system with electric servo motors, enabling more precise control over the entire injection process. Electric machines offered faster cycle times, reduced energy consumption, and decreased maintenance requirements.
In recent years, the evolution of automatic injection molding machines has focused on further enhancing precision, speed, and energy efficiency. Advancements in robotics and automation have resulted in the integration of robotic arms for part removal and assembly, reducing the need for additional labor. Furthermore, the development of advanced sensor technology and data analytics allows for real-time monitoring and optimization of the injection process, ensuring consistent quality and minimal waste.
Overall, the evolution of automatic injection molding machines is a testament to human ingenuity and technological progress. From manual labor-intensive machines to highly automated and precise systems, the industry continues to push boundaries to meet the growing demands of the manufacturing world.
The Evolution and Market Trends in automatic injection moulding machine Industry
The automatic injection molding machine industry has seen significant evolution and market trends over the years. Initially, injection molding machines required manual operation, which was time-consuming and had limitations in precision and efficiency. However, with advancements in technology and automation, automatic injection molding machines have become the preferred choice in various industries.
One major evolution in the industry is the integration of robotics and artificial intelligence (AI) into automatic injection molding machines. This has brought a paradigm shift in the way these machines operate. The use of robots allows for increased precision, faster cycle times, and improved repeatability. AI features enable the machines to self-optimize and adapt to changing production needs, resulting in enhanced productivity and reduced waste.
Another market trend is the growing demand for energy-efficient and environmentally friendly automatic injection molding machines. With the increasing focus on sustainability, manufacturers are developing machines that reduce energy consumption and minimize material waste. These machines incorporate advanced technologies such as servo motors, variable pump drives, and energy recovery systems, resulting in improved energy efficiency and cost savings for the users.
Moreover, the automatic injection molding machine industry is witnessing a rise in the adoption of smart manufacturing techniques. Manufacturers are integrating IoT (Internet of Things) capabilities with automatic injection molding machines to enable real-time monitoring and data analysis. This facilitates predictive maintenance, quality control, and process optimization, leading to improved overall equipment effectiveness and production efficiency.
In terms of market trends, the Asia-Pacific region has emerged as a dominant player in the automatic injection molding machine industry. This can be attributed to the rapid industrialization and manufacturing growth in countries like China and India. The demand for consumer goods, packaging, automotive components, and electronics in this region has contributed to the increased adoption of automatic injection molding machines.
Overall, the evolution of automatic injection molding machines towards automation, robotics, AI, energy efficiency, and smart manufacturing has revolutionized the industry. These advancements have resulted in higher production rates, improved product quality, reduced costs, and enhanced sustainability. With the Asia-Pacific region leading the market, the future of the automatic injection molding machine industry looks promising and dynamic.
Custom Private Labeling and Branding Opportunities with Chinese automatic injection moulding machine Manufacturers
China is known as a manufacturing powerhouse, producing a wide range of products for the global market. When it comes to automatic injection molding machines, Chinese manufacturers offer competitive advantages in terms of cost, customization, and private labeling opportunities.
Chinese automatic injection molding machine manufacturers are experienced in producing high-quality machines that meet international standards. They have advanced manufacturing facilities and employ skilled engineers and technicians, ensuring the production of reliable and efficient machines. The cost advantage is significant, as China’s manufacturing capabilities allow for lower labor and production costs compared to many other countries.
One of the key opportunities Chinese manufacturers provide is customization. They can tailor automatic injection molding machines according to specific requirements, such as the injection volume, mold size, and machine dimensions. This flexibility allows businesses to efficiently meet their specific manufacturing needs.
Private labeling opportunities are also available, enabling businesses to create their own brand identity. Chinese manufacturers can incorporate the desired logo, design, and aesthetics into the machine’s appearance, providing a branded product that stands out in the market. This enhances brand recognition and customer loyalty, paving the way for increased sales and business growth.
Moreover, Chinese manufacturers are known for their comprehensive after-sales services, including technical support, spare parts availability, and warranty services. These post-sales services offer peace of mind to businesses, ensuring the smooth operation of their injection molding machines.
In conclusion, Chinese automatic injection molding machine manufacturers offer attractive opportunities for businesses looking to customize and private label their products. With competitive pricing, high-quality manufacturing, customization capabilities, and comprehensive after-sales services, partnering with Chinese manufacturers can be a strategic choice for businesses seeking to maximize their market presence and profitability.
Tips for Procurement and Considerations when Purchasing automatic injection moulding machine
When purchasing an automatic injection molding machine, there are several factors and considerations that one should keep in mind. Here are some tips and considerations for procurement:
1. Determine the production requirement: Assess your production needs and determine the required production capacity of the machine. Consider factors such as the type and volume of products to be manufactured.
2. Research different machine options: Conduct thorough research on various automatic injection molding machine suppliers and models available in the market. Look for reputable suppliers known for their quality and reliability.
3. Consider the machine’s specifications: Evaluate the machine’s specifications, including clamping force, injection weight, injection pressure, and mold thickness range. Ensure that the machine’s capabilities align with your production requirements.
4. Quality and durability: Look for machines made from high-quality materials that can withstand the rigors of continuous use. Check the machine’s components, such as the injection unit, mold clamping system, and control system, to ensure their durability.
5. Energy efficiency: Consider machines that offer energy-saving features. Look for models that use servo motor systems, as they can significantly reduce energy consumption when compared to traditional hydraulic systems.
6. Training and technical support: Inquire about the training and technical support provided by the supplier. Ensure that they offer training for machine operation, maintenance, and troubleshooting. A reliable supplier should also provide prompt technical assistance when needed.
7. Cost-effectiveness: Compare prices from different suppliers while considering the machine’s quality and features. Look for a machine that provides the best value for your investment in terms of productivity, efficiency, and durability.
8. Warranty and after-sales service: Check the warranty period offered by the supplier and inquire about their after-sales service. A reliable supplier should offer a comprehensive warranty and provide timely assistance for any issues that may arise.
9. Consider future expansion: If you anticipate future growth or diversification, consider machines that allow for flexibility and expansion. Look for models that allow for easy integration with automated systems or additional modules.
10. Safety features: Look for machines that come with advanced safety features such as emergency stop buttons, safety doors, and automatic fault detection systems to ensure operator safety.
By considering these tips and factors, you can make an informed decision when purchasing an automatic injection molding machine that meets your production requirements and offers long-term value.
FAQs on Sourcing and Manufacturing automatic injection moulding machine in China
1. Why should I source automatic injection moulding machines from China?
China is widely recognized as a global manufacturing hub, especially for plastic injection moulding machines. It offers cost advantages, a vast supplier base, and advanced manufacturing capabilities. Chinese manufacturers often maintain high-quality standards and have expertise in producing automatic injection moulding machines.
2. How can I find reliable manufacturers in China?
There are several ways to identify reputable manufacturers in China. One approach is to use online platforms like Alibaba, which enable you to browse through a wide range of suppliers, compare prices, and read customer reviews. Additionally, attending trade shows in China, such as the Chinaplas exhibition, allows you to personally meet manufacturers and gain insights into their production capabilities.
3. How do I ensure the quality of automatic injection moulding machines from Chinese suppliers?
To ensure quality, it is crucial to conduct thorough due diligence. Research the manufacturer’s reputation, request samples, and ask for certifications, such as ISO 9001, which signifies adherence to quality management standards. It is also advisable to visit the supplier’s manufacturing facilities to assess their production processes and equipment.
4. Can I customize the automatic injection moulding machines according to my specific requirements?
Chinese manufacturers often offer customization options to meet diverse customer needs. You can discuss your requirements with the manufacturer and determine if they can accommodate your customization requests. Before finalizing an order, make sure the manufacturer is capable of delivering the desired specifications.
5. What is the typical lead time for manufacturing and delivery?
The lead time may vary depending on factors such as order quantity, customization requirements, and the manufacturer’s production schedule. Generally, it is advisable to inquire about lead times during the initial communication with the supplier. This information will help you plan your procurement process accordingly.
6. How can I handle logistics and shipping?
Chinese manufacturers are experienced in exporting products worldwide, and they can assist you in handling logistics and shipping. They can provide guidance on the best shipping methods, arrange transportation, and ensure proper packaging to prevent any damage. Communicate your shipping needs with the manufacturer to establish a smooth delivery process.
7. What about after-sales support and technical assistance?
Reliable Chinese manufacturers usually provide comprehensive after-sales support and technical assistance. This may include product warranty, troubleshooting, spare parts availability, and remote assistance. Discuss these aspects with the manufacturer before making a purchase to ensure you can access support whenever needed.
In summary, sourcing and manufacturing automatic injection moulding machines in China offers cost advantages, a wide supplier base, and advanced manufacturing capabilities. Conducting due diligence, ensuring quality, and discussing customization options are essential steps in the sourcing process. Additionally, clarifying lead times, handling logistics, and ensuring after-sales support are crucial considerations for a successful procurement experience.
Why contact sourcifychina.com get free quota from reliable automatic injection moulding machine suppliers?
Sourcifychina.com, a reputed sourcing company, may get a free quota from reliable automatic injection molding machine suppliers for several reasons.
Firstly, suppliers often provide free quotas to reputable sourcing companies as a way to promote their products and expand their customer base. By offering a free quota to Sourcifychina.com, suppliers can showcase their automatic injection molding machines to potential buyers and increase their chances of securing future orders.
Additionally, suppliers may view Sourcifychina.com as a valuable partner in the sourcing process. As a well-established and trusted sourcing company, Sourcifychina.com has a vast network of clients looking for injection molding machines. Providing a free quota allows suppliers to forge a mutually beneficial relationship with Sourcifychina.com, potentially leading to long-term partnerships and increased sales.
Furthermore, offering a free quota to Sourcifychina.com helps suppliers establish credibility and trust among buyers. By demonstrating their confidence in the quality and performance of their machines, suppliers can attract more buyers through Sourcifychina.com’s platform.
This arrangement also benefits Sourcifychina.com and its clients. The free quota allows Sourcifychina.com to access and evaluate the quality, pricing, and specifications of the automatic injection molding machines without any financial commitment or risk. It enables Sourcifychina.com to provide its clients with comprehensive information and recommendations based on first-hand experience, ensuring that clients can make informed decisions.
In conclusion, reliable automatic injection molding machine suppliers may offer Sourcifychina.com a free quota to increase their market reach, establish partnerships, and build a reputation for quality and credibility. This mutually beneficial arrangement allows Sourcifychina.com to assess the products more effectively and provide valuable insights to its clients.