Types and Applications of carbide roller
Carbide rollers are high-performance rollers that are made from a type of ceramic material called carbide. Carbide rollers offer high wear resistance, durability, corrosion resistance, and excellent toughness, making them ideal for a variety of industrial applications. Carbide rollers can be used in various industries, including steel wire and tube, printing, paper, textile, and food packaging.
There are different types of carbide rollers, including:
1. Tungsten carbide rollers: These are the most popular type of carbide rollers due to their high wear resistance, durability, and toughness. They are widely used in wire and tube drawing processes, printing and paper processing industries.
2. Silicon carbide rollers: These rollers exhibit excellent thermal properties that make them ideal for use in high-temperature applications such as glass production and heat-treating metals.
3. Titanium carbide rollers: These carbide rollers offer high resistance to wear, even at high speeds, so they are commonly used in metalworking industries.
The applications of carbide rollers include:
1. Wire Drawing: Carbide rollers are widely used in wire drawing processes where they provide high wear resistance, toughness and durability, making them ideal for processing steel, copper and aluminium wires.
2. Textile Industry: Carbide rollers are used in the textile industry to produce high-quality fabrics through the process of calendering, a method of ironing and smoothing out fabrics.
3. Printing and paper Industry: Carbide rollers are used in printing and paper industries to produce high-quality prints and paper by maintaining consistent levels of pressure and temperature.
4. Food packaging: Carbide rollers are also used in food packaging to create tightly sealed packages using heat sealing.
In conclusion, carbide rollers are recognised for their high wear resistance, durability and toughness, making them ideal for several industrial applications such as wire drawing, printing and paper industry, textile industry, and food packaging. The different types of carbide rollers include tungsten carbide, silicon carbide and titanium carbide rollers, each suited for different industrial applications.
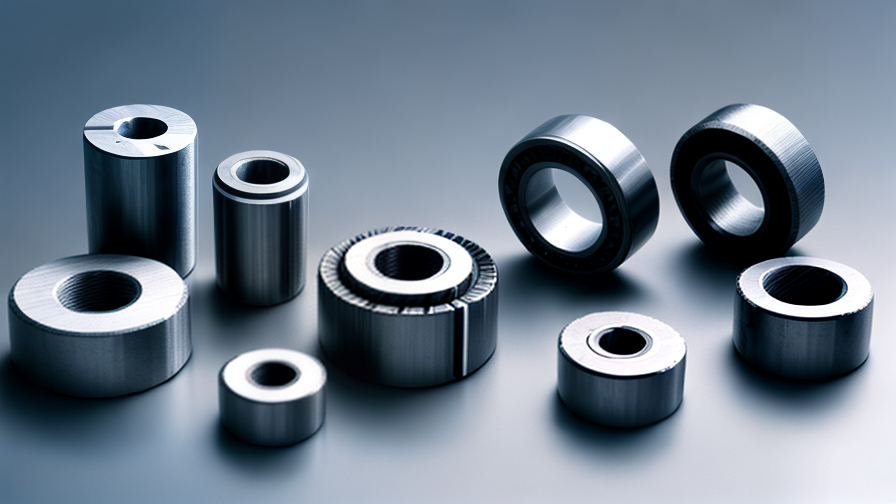
Benefits and Feature of Utilizing carbide roller
Carbide rollers are widely used in several industries such as the automotive industry, food industry, and metalworking industry. These rollers are advantageous because of their durability, wear resistance, and precision. Below are some of the benefits and features that businesses can achieve from utilizing carbide rollers.
1. Durability – Carbide rollers have a high resistance to wear and tear compared to other materials such as steel or rubber. This makes them ideal for use in harsh environments that require continuous operation and exposure to extreme temperatures, chemicals, and wear.
2. Precision – Carbide rollers have excellent roundness and straightness, making them ideal for applications that require precision and accuracy such as in the manufacturing of electronic components.
3. Corrosion resistance – Carbide rollers are resistant to corrosion, which makes them ideal for use in environments where they are in contact with corrosive substances.
4. Versatility – Carbide rollers are suitable for use in a range of industries, making them a versatile option for several applications.
5. Low maintenance – Carbide rollers require less maintenance compared to other materials, which helps to reduce downtime and increase productivity.
6. Cost-effectiveness – Although carbide rollers might be more expensive initially, their durability and longevity help to reduce replacement and maintenance costs in the long run.
In conclusion, utilizing carbide rollers provides several benefits and features that businesses can harness for increased efficiency and productivity. These rollers are durable, precise, corrosion-resistant, versatile, and cost-effective, making them an ideal choice for several industries.
The Process of carbide roller
Carbide rollers are used in a variety of applications, such as wire flattening, drawing, and forming. They are made up of tungsten carbide and cobalt and are highly resistant to wear and tear. The production process for carbide rollers involves the following steps:
1) Preparing the raw material – The raw material used for carbide rollers is tungsten carbide powder and cobalt powder. These materials are weighed in the correct proportions and mixed together by using a ball mill.
2) Compression- The mixture of tungsten carbide and cobalt powder is then compressed into the desired shape. This is done by using a hydraulic press that applies immense pressure to the mixture, resulting in compacted carbide blocks.
3) Cutting – The compacted carbide blocks are then cut into smaller sizes using either diamond or abrasive saws.
4) Grinding – The carbide blocks are then ground using a grinder to produce the desired dimensions and surface finish.
5) Sintering – The ground carbide blocks are then placed in a sintering furnace where they are heated to a temperature of around 1500°C in a controlled atmosphere. This process enables the carbide to become fully consolidated.
6) Machining – The sintered carbide blocks are then machined into the final product according to the required specifications. This process involves drilling, grinding, and polishing the carbide to produce the final shape and surface finish.
7) Quality control – Once the carbide rollers are finished, they are subjected to a series of tests to ensure that they meet the required standards. These tests include measuring the dimensions, surface roughness, and hardness of the rollers.
In conclusion, the process of making carbide rollers involves mixing tungsten carbide and cobalt powder, compressing and cutting the material, grinding it, sintering it in a furnace using a controlled atmosphere, machining it to the required shape and finish, and finally subjecting it to quality control tests to ensure its quality.

How to use carbide roller
Carbide roller is a tool used to shape and form hard materials such as steel, aluminum, and other metals. It is commonly used in metalworking industries where precision is crucial. Here are the steps on how to use carbide roller:
1. Prepare the carbide roller and the metal to be worked on. Lubricate the carbide roller to minimize friction and wear.
2. Determine the desired shape or form of the metal. Decide on the pressure required and the direction of rolling.
3. Position the metal on the carbide roller. Adjust the pressure of the roller to the desired amount.
4. Apply gradual pressure on the metal using the carbide roller. Roll the metal back and forth until the desired shape is attained.
5. Inspect the metal to ensure that it has been achieved the required shape. Repeat the rolling process if necessary.
6. Remove the metal from the carbide roller and clean both the carbide roller and the metal.
7. Store the carbide roller in a dry and safe place.
It is essential to use the correct carbide roller for specific industrial operations. It is also vital to handle them with care to avoid damage or breakage during use. Follow all safety guidelines and precautions when using carbide rollers to prevent accidents and injuries.
carbide roller Manufacturer,Supplier and Wholesale
Carbide rollers are an essential component in many manufacturing processes such as printing, papermaking, steel processing, and other heavy industries. They are used to give support to the web materials and offer a high level of wear resistance, durability, and reduced maintenance costs.
As a carbide roller manufacturer, supplier, and wholesale distributor, we offer a wide range of products to meet our customer’s requirements. Our carbide rollers are made from premium quality tungsten carbide, cobalt-based alloy, or chrome carbide, making them resistant to corrosion and oxidization.
Our manufacturing process includes the use of advanced technology and machinery that ensures precise dimensions, uniformity of shape, and smooth surface finishing. We specialize in producing various types of carbide rollers such as printing rollers, guide rollers, pinch rollers, and steel rollers.
Our team of experts ensures that each carbide roller is checked thoroughly for quality and performance before dispatching it to our customers. We also offer customized solutions that cater to the specific needs of our customers.
As a supplier and wholesale distributor, we supply carbide rollers to various industries and ensure timely delivery of the products. Our competitive pricing and high-quality products have made us a reliable partner to our customers worldwide.
In conclusion, as a trusted carbide roller manufacturer, supplier, and wholesale distributor, we offer a comprehensive range of products that meet the highest industry standards. Our commitment to quality, innovation, and customer satisfaction has made us a preferred partner for various heavy industries.

carbide roller Price
The price of carbide rollers varies depending on the size, shape, and quality of the roller. Carbide rollers are made from a hard and durable material known as tungsten carbide, which makes them ideal for various industrial applications. The manufacturing process also plays a crucial role in determining the price of carbide rollers.
A small-sized carbide roller will typically cost between $50 to $200, while a larger and more complex one may cost up to several thousand dollars. The price also depends on the degree of precision that is required in the manufacturing process. Some high-precision carbide rollers may require extensive quality control measures, which can drive up the price.
Carbide rollers are used in various industries, including metalworking, plastic and rubber, paper and printing, and textile manufacturing. They are used in different stages of the production process to deliver high-quality and efficient outcomes. Carbide rollers are known for their longevity, wear-resistance, and low maintenance requirements, making them a cost-effective investment in the long run.
In conclusion, the price of carbide rollers varies depending on the size, complexity, and precision required in the manufacturing process. Given their durability and longevity, carbide rollers are a cost-effective investment for industries that require high-quality and efficient production outcomes.
FAQ sourcing carbide roller manufacturer from China with multiple answers
1) What is carbide roller and what are its applications?
Carbide roller is made of tungsten carbide, which is a hard and wear-resistant material. It is widely used in various industries as an important component in the manufacturing process of products such as wire, tube, and rods. The roller is used to provide a smooth surface and precise shape to the products.
2) What are the advantages of sourcing carbide roller from China?
China is known for its production of high-quality carbide rollers at competitive prices, making it an attractive option for buyers. In addition, Chinese carbide roller manufacturers have advanced equipment and technology, which allows them to produce rollers that have long-lasting high wear resistance and dimensional stability.
3) How to identify high-quality carbide roller manufacturers in China?
Buyers should consider the manufacturer’s production experience and qualifications, as well as their reputation in the industry. Visiting the manufacturer’s factory and inspecting the quality of their products is also a reliable way of identifying high-quality carbide roller manufacturers.
4) What is the production lead time for carbide roller from China?
The production lead time for carbide roller from China varies depending on the manufacturer’s production capacity and the buyer’s order quantity. Typically, the lead time ranges from 4 to 8 weeks.
5) How do Chinese carbide roller manufacturers ensure quality control?
Chinese carbide roller manufacturers typically have strict quality control measures in place, including testing the materials and finished products to ensure they meet the required standards. Manufacturers also have quality control personnel who monitor the entire production process to minimize the chances of defects or errors.
6) What are the payment terms typically offered by Chinese carbide roller manufacturers?
Manufacturers typically offer payment terms such as T/T (telegraphic transfer) or L/C (letter of credit). Buyers should discuss payment terms with the manufacturer before placing an order to ensure they are mutually agreed upon.
7) What are the shipping options for carbide roller from China?
Shipping options include air freight, sea freight, or courier services. The buyer should discuss shipping options with the manufacturer to ensure the most efficient and cost-effective shipping method is selected.