Introduce about cnc cut metal guide,Qulity,Cost,Supplier,Certification,Market,Tips,FAQ
CNC cut metal guide refers to a comprehensive handbook that provides information on the process of using CNC (Computer Numerical Control) technology to cut metal materials effectively. This guide serves to assist manufacturers, engineers, and hobbyists who are involved in metal fabrication processes.
When it comes to quality, CNC cut metal offers precise and accurate cuts, ensuring a high level of quality in the end product. The CNC technology allows for intricate designs, complex shapes, and tight tolerances, resulting in a finished product that meets or exceeds industry standards.
Cost-wise, CNC cut metal may have higher initial expenses due to the investment in CNC machines and associated software. However, in the long run, the cost is minimized as the precision and efficiency of CNC cutting reduce material waste and labor requirements, ultimately resulting in cost savings.
Suppliers of CNC cut metal can be found globally. It is essential to identify reputable suppliers who have experience, knowledge, and expertise in the field. Good suppliers offer materials with different specifications, such as different types of metal, thicknesses, and finishes, to cater to various project requirements.
Certification is an important aspect when choosing CNC cut metal suppliers. Suppliers should possess certifications such as ISO 9001, which ensures quality management systems are in place, or ISO 14001, which signifies environmental management standards.
The market for CNC cut metal is extensive, ranging from automotive and aerospace industries to architecture and art. CNC metal cutting is highly sought after for its precision and versatility, making it a popular choice across different sectors.
Tips for working with CNC cut metal involve ensuring proper machine setup, selecting compatible tools and materials, and conducting thorough testing before diving into a large-scale production. Additionally, following safety protocols and maintaining the machine regularly are crucial aspects to consider.
FAQs related to CNC cut metal guide may include questions on material compatibility, machine capabilities, design software, and best practices. A well-rounded guide should address these common queries and provide detailed explanations and solutions.
In summary, a CNC cut metal guide is a valuable resource that covers various aspects related to CNC metal cutting. It highlights the quality and cost advantages, guides the selection of reliable suppliers, emphasizes the importance of certifications, explores market applications, provides tips for effective utilization, and answers frequently asked questions.
Types of cnc cut metal
There are several types of CNC (Computer Numerical Control) cut metal that are commonly used in various industries. These materials include steel, aluminum, brass, copper, titanium, and stainless steel. Each type of metal has its own unique characteristics and applications.
Steel is one of the most widely used metals for CNC cutting due to its strength, durability, and affordability. It is commonly used in the construction, automotive, and aerospace industries. Steel can be cut into various shapes and sizes, making it a versatile material.
Aluminum is another popular choice for CNC cutting due to its lightweight nature, corrosion resistance, and excellent conductivity. It is widely used in the aerospace, automotive, and electronics industries. Aluminum can be easily machined and is often chosen for intricate designs and high-precision components.
Brass is a metal alloy made primarily of copper and zinc. It is known for its excellent corrosion resistance, conductivity, and aesthetics. Brass is commonly used in the manufacturing of decorative items, musical instruments, plumbing fixtures, and electrical connectors.
Copper, like brass, is an excellent conductor of electricity and heat. It is commonly used in electrical applications, plumbing, roofing, and artistic designs. Copper can be CNC cut into intricate shapes and is often chosen for decorative or functional components.
Titanium is a lightweight and strong metal that offers high corrosion resistance. It is commonly used in the aerospace and medical industries. Titanium is more challenging to machine compared to other metals due to its high strength, but its unique properties make it an ideal choice for critical applications.
Stainless steel is a corrosion-resistant alloy that contains a minimum of 10.5% chromium. It is widely used in various industries, including food processing, automotive, and architecture. Stainless steel offers excellent structural integrity, durability, and aesthetics.
In conclusion, the choice of CNC cut metal depends on the specific application requirements and desired characteristics of the finished product. Steel, aluminum, brass, copper, titanium, and stainless steel are commonly used and offer unique properties that make them suitable for a wide range of industries and applications.
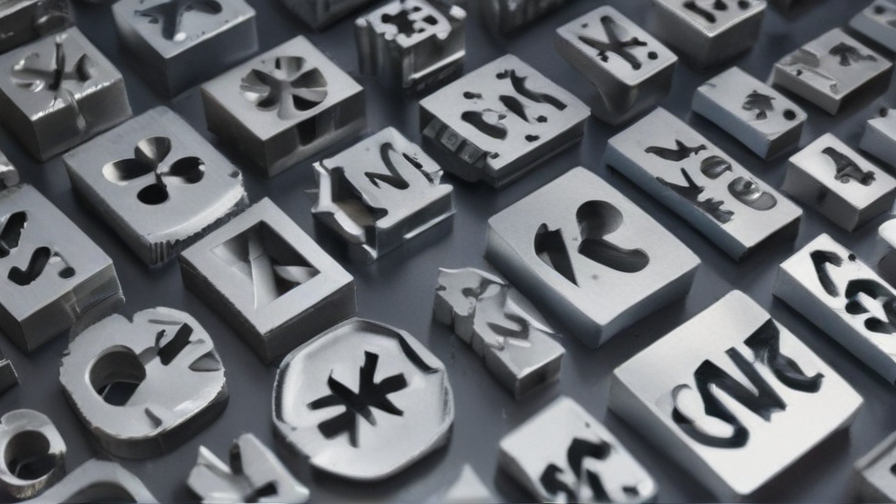
Pros and Cons of Using cnc cut metal
Pros of using CNC cut metal:
1. Precision: CNC machines offer high precision and accuracy, ensuring consistent and reliable results. This is especially advantageous for complex designs and intricate metal cutting requirements.
2. Versatility: CNC cut metal can be used for a wide range of applications, including automotive, aerospace, signage, architecture, and machinery. It can handle various types of metals, such as steel, aluminum, brass, and titanium.
3. Efficiency: CNC machines are capable of fast and efficient metal cutting, reducing manufacturing time and increasing productivity. This is particularly beneficial for bulk production or meeting tight deadlines.
4. Repeatability: CNC cut metal allows for exact reproduction of parts, ensuring consistency throughout the production process. This is crucial for maintaining quality standards and reducing errors.
5. Customization: CNC machines offer high design flexibility, allowing for customization according to specific requirements. This enables the production of unique and personalized metal parts or components.
Cons of using CNC cut metal:
1. Cost: The initial investment in CNC machines can be quite high, making it less feasible for small-scale or low-budget operations. Additionally, the maintenance and repair costs associated with CNC machines can add to the overall expenses.
2. Complexity: Operating CNC machines requires specialized training and expertise. This can be a disadvantage for businesses that do not have skilled personnel, as it may lead to errors or inefficiency.
3. Size limitations: The size of the CNC machine determines the maximum dimensions of the metal that can be cut. Larger or oversized pieces may require alternative cutting methods, which may be more time-consuming and less cost-effective.
4. Material limitations: While CNC machines can work with various metals, there may be limitations on the type or thickness of material that can be cut. Some CNC machines may struggle with cutting harder metals or extremely thin materials.
5. Design restrictions: CNC machines have certain design limitations, such as minimum radius or angle requirements. These restrictions may affect the design possibilities or require additional processes to achieve specific shapes or features.
It is important to weigh these pros and cons while considering the specific needs and requirements of each project or business.
cnc cut metal Reference Specifications (varies for different product)
When it comes to CNC cut metal, there are several reference specifications that can vary depending on the specific product being manufactured. These specifications are crucial in ensuring the quality, precision, and overall performance of the metal components or parts.
One of the key reference specifications for CNC cut metal is the dimensional tolerance. This specification defines the acceptable deviation from the intended dimensions of the metal parts. It ensures that the final products are within the required measurements, allowing for proper fit and functionality when integrated into the larger assembly.
Another important specification is the surface finish requirement. This pertains to the desired smoothness, texture, and appearance of the metal surface after cutting. Different products may have varying surface finish requirements, such as smoothness for aesthetic purposes or roughness for improved grip or friction.
Material specifications are also critical. These include the type of metal to be used, its grade or alloy composition, and thickness requirements. Depending on the application, certain metals may need to possess specific properties, such as high strength, corrosion resistance, or electrical conductivity. The specifications ensure that the correct material is selected to meet the product’s performance criteria.
Moreover, CNC cut metal often requires specific hole sizes, shapes, or patterns. Hole specifications encompass parameters such as diameter, depth, and positional tolerance. These specifications are necessary for proper assembly, allowing for precise alignment and fit with other components.
Additionally, CNC cutting typically involves different types of edges or profiles. The reference specifications outline the required edge conditions, which may include aspects like sharpness, smoothness, or roundness. These specifications ensure that the edges are suitable for their intended purpose, whether it’s for safety reasons or enhanced functionality.
Overall, reference specifications for CNC cut metal are vital for consistent and high-quality production. They provide clear guidelines for dimensional accuracy, surface finish, material selection, hole specifications, and edge conditions. By adhering to these specifications, manufacturers can deliver products that meet or exceed customer expectations while ensuring compatibility and reliable performance in various industries.
Applications of cnc cut metal
CNC (Computer Numerical Control) cutting of metal has become increasingly popular due to its precision, efficiency, and versatility. The technology allows for the creation of complex and intricate designs that would be difficult to achieve with traditional metalworking methods. Below are some of the key applications of CNC cut metal:
1. Prototyping and Rapid Manufacturing: CNC cutting enables the quick and cost-effective production of prototypes and small batches of metal parts. It allows for the efficient testing and refinement of designs before moving to mass production.
2. Industrial Machinery and Equipment: CNC cut metal is extensively used in the manufacturing of industrial machinery and equipment. It facilitates the production of various components, including gears, pulleys, brackets, and frames, which are crucial for machinery functionality.
3. Automotive and Aerospace: Precision parts are vital for the automotive and aerospace industries. CNC cutting ensures the high accuracy required for components such as engine parts, gearbox elements, wing sections, and turbine blades. It improves performance, efficiency, and safety.
4. Architectural and Structural Applications: CNC cut metal finds applications in architectural and structural projects due to its ability to create custom and decorative designs. It is used for the production of gratings, panels, trusses, brackets, and decorative elements, enhancing buildings’ aesthetics and functionality.
5. Electronics and Electrical Components: CNC cutting is used to manufacture precise metal parts required in the electronics and electrical industries. These parts include circuit boards, heat sinks, connectors, enclosures, and antenna mounts.
6. Art and Décor: CNC cut metal provides artists and designers with unlimited possibilities for creating intricate sculptures, art installations, and decorative elements. Its precise cutting capabilities allow for the expression of complex patterns and designs in a variety of metals.
7. Medical Devices and Instruments: CNC cutting is utilized in the production of medical devices and instruments, which requires precision, reliability, and sterility. It is used in manufacturing implants, surgical tools, prosthetics, and other medical equipment.
8. Jewelry and Accessories: CNC cutting has revolutionized the jewelry industry by enabling the creation of intricate and personalized designs. It allows for the precise fabrication of metals like gold, silver, and stainless steel, making it easier for jewelry makers to bring their unique designs to life.
In summary, CNC cut metal has a wide range of applications, from industrial manufacturing to architectural design, art, and even jewelry. Its precision, efficiency, and versatility make it an invaluable tool in various industries that require customization and accuracy in metal fabrication.
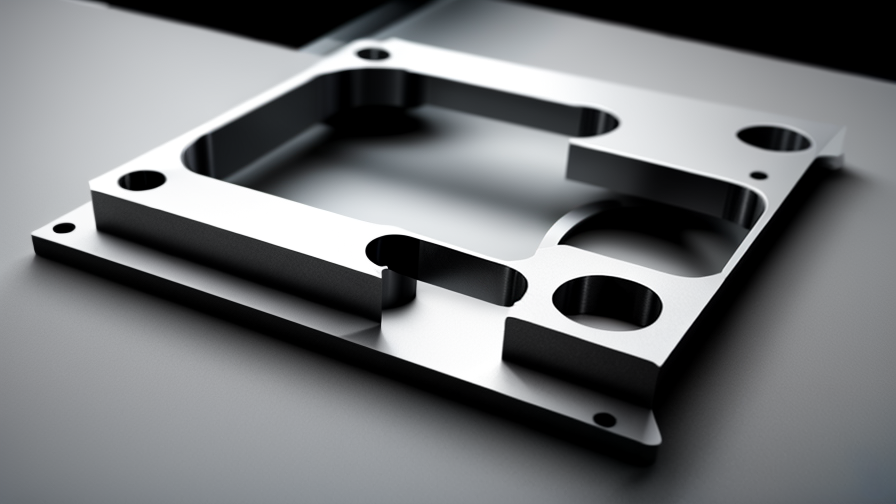
The Work Process and how to use cnc cut metal
CNC (Computer Numerical Control) cutting is a manufacturing process that utilizes computerized control systems to accurately cut and shape metal materials. It offers precise and efficient results, making it a popular choice in various industries.
The work process of CNC cut metal involves several steps. Firstly, a design or CAD (Computer-Aided Design) file of the desired product is created. This file contains all the necessary measurements and specifications for the CNC machine to follow.
Next, the CAD file is loaded into the CNC machine’s software. This software translates the design into code, which the machine follows to accurately cut the metal. The operator sets up the machine by selecting the appropriate cutting tools and materials. This may involve selecting the desired cutting speeds, feed rates, and cutting depths.
Once the machine is set up, it precisely cuts the metal based on the programmed instructions. The CNC machine moves the cutting tool along the specified path, removing excess material and shaping the metal into the desired form. The cutting process may involve various tools such as drills, milling cutters, or lasers depending on the complexity of the design and type of metal being cut.
After the cutting process is complete, the finished product is carefully inspected for quality control. Any imperfections or errors can be corrected and adjustments can be made if necessary. The final product is then ready for use or further processing such as welding, polishing, or painting.
CNC cut metal offers numerous advantages. It allows for fast and accurate cutting, minimizing material waste and reducing production time. It can handle complex designs with intricate details, creating highly precise and consistent results. Moreover, CNC cutting is versatile and can be used with various types of metal including steel, aluminum, brass, and more.
In conclusion, CNC cut metal is an efficient and precise manufacturing process. It involves creating a design, programming the CNC machine, setting it up, cutting the metal, and inspecting the final product. By utilizing CNC cutting, manufacturers can achieve high-quality results in a shorter time frame and with minimal material waste.
Quality Testing Methods for cnc cut metal and how to control the quality
Quality testing methods for CNC cut metal include dimensional inspection, material testing, surface finish evaluation, and visual inspection. Controlling the quality of CNC cut metal involves several measures such as setting clear specifications, monitoring the production process, conducting regular quality audits, and implementing corrective actions.
Dimensional inspection is essential to verify that the CNC cut metal parts meet the required size and shape specifications. This can be done using measuring tools such as calipers, micrometers, or coordinate measuring machines (CMM). Material testing ensures that the metal used meets the required specifications such as tensile strength, hardness, and chemical composition. This can be carried out using destructive or non-destructive testing methods like tensile testing, hardness testing, or spectroscopy.
Surface finish evaluation is critical for CNC cut metal parts that have aesthetic or functional requirements. This can be assessed visually or by using surface roughness testers that measure parameters like Ra (arithmetic average roughness) or Rz (maximum peak-to-valley roughness). Visual inspection is also crucial to identify any visible defects like cuts, burrs, or scratches that may affect the quality of the CNC cut metal.
To control the quality of CNC cut metal, it is important to define clear specifications and communicate them effectively to the production team. This includes providing detailed drawings, material specifications, and any applicable industry standards or regulations. Regular monitoring of the production process is necessary to ensure that the CNC machine is properly calibrated and maintained. This involves checking the machine settings, tool wear, and making adjustments if necessary.
Conducting regular quality audits helps identify any deviations from the specified quality standards and ensures compliance with established procedures. These audits can include both internal checks as well as engaging external quality inspectors or third-party certification bodies. If any defects or non-conformities are identified during the quality audits or inspections, appropriate corrective actions should be taken promptly. This may involve rework, replacing defective parts, adjusting machine settings, or revising production processes to prevent similar issues in the future.
Overall, employing a combination of appropriate quality testing methods and effective quality control measures ensures the production of CNC cut metal that meets the required specifications and satisfies customer expectations.
cnc cut metal Sample Policy and Post-Purchase Considerations for cnc cut metal from China
Sample Policy: When purchasing CNC-cut metal products from China, it is important to inquire about the supplier’s sample policy. Many suppliers offer samples to potential buyers to ensure the quality and accuracy of their products. It is advisable to request samples before placing a bulk order to evaluate the supplier’s capabilities and suitability for your specific needs. However, it is worth noting that some suppliers may charge a fee for samples or shipping, which may be negotiable depending on the potential order size or ongoing business relationship.
Post-Purchase Considerations: After receiving the CNC-cut metal products from China, there are several post-purchase considerations to keep in mind:
1. Quality Inspection: Thoroughly inspect the received products to ensure they meet the expected quality standards. Check for any visible defects, accuracy in dimensions, and proper finishing. Engaging a third-party quality control service may be beneficial to perform a detailed inspection.
2. Communication and Feedback: Establish open channels of communication with the supplier regarding any issues, concerns, or feedback after receiving the products. Promptly notify the supplier if there are any defects or discrepancies from the agreed specifications.
3. Long-term Supplier Relationship: Evaluate the reliability and professionalism of the supplier throughout the entire transaction process. Consider factors such as timely communication, delivery schedules, and willingness to address any concerns or questions regarding the products.
4. Order Volume and Packaging: If satisfied with the initial sample and product quality, discuss future order volumes and packaging requirements with the supplier. Negotiate favorable terms for future orders, including pricing, delivery schedules, and packaging specifications.
5. Documentation and Legal Compliance: Ensure all necessary documentation, such as certificates of origin, compliance with applicable regulations, and warranty terms, are properly obtained from the supplier.
By following these sample policy and post-purchase considerations, you can minimize risks and secure a successful and satisfactory transaction when purchasing CNC-cut metal products from China.
Sourcing cnc cut metal from China: Opportunities, Risks, and Key Players
Sourcing CNC-cut metal from China presents both opportunities and risks for businesses. On one hand, China is known for its vast manufacturing capabilities, cost-effective production, and technological advancements in CNC machining. This provides an opportunity for businesses to obtain high-quality CNC-cut metal at competitive prices.
China’s massive manufacturing infrastructure allows for efficient production and faster turnaround times. The country is home to numerous CNC machining companies that offer a wide range of services, from prototyping to mass production. This enables businesses to find suitable suppliers for their specific metal cutting needs.
However, there are also risks associated with sourcing CNC-cut metal from China. Quality control can be a challenge, as some Chinese suppliers may prioritize quantity over precision. It is essential for businesses to thoroughly vet potential suppliers, request samples, and establish clear communication to ensure the desired quality of the finished products.
Another risk is intellectual property infringement. China has faced criticism for its lax intellectual property enforcement, raising concerns about the protection of proprietary designs or technologies. Businesses should take precautions such as signing non-disclosure agreements and conducting due diligence to protect their intellectual property rights.
Despite the risks, there are key players in the Chinese CNC-cut metal industry that businesses can consider for sourcing. Companies such as Foxron Precision Metal Parts Co., Ltd., Shenzhen Ruiqicheng Precision Hardware Products Co., Ltd., and Shenzhen Tuofa Technology Co., Ltd. have established themselves as reliable suppliers renowned for their precision machining capabilities.
In conclusion, sourcing CNC-cut metal from China offers opportunities for businesses to access cost-effective manufacturing solutions. However, it is crucial to carefully navigate the risks associated with quality control and intellectual property protection. By undertaking proper research, due diligence, and establishing transparent communication, businesses can find reliable suppliers and benefit from China’s CNC machining capabilities.
How to find and select reliable cnc cut metal manufacturers in China,use google search manufacturers and suppliers
To find and select reliable CNC cut metal manufacturers in China, the following steps can be taken:
1. Start with a Google search: Begin by conducting a search using relevant keywords such as “CNC cut metal manufacturers in China” or “CNC machining companies in China.” This will provide you with a list of potential manufacturers.
2. Verify the company’s credibility: Visit the websites of the shortlisted manufacturers to gather information about their capabilities, experience, certifications, and client testimonials. Look for companies that have been in the industry for a considerable period, have a good track record, and are well-established.
3. Assess manufacturing facilities: Look for information on the manufacturer’s production capabilities, equipment, and quality control measures. Ensure that they have modern CNC machining equipment and can handle the specific requirements of your project. Look for certifications such as ISO 9001 which indicates adherence to quality standards.
4. Inquire about material selection: Contact the manufacturers and inquire about the materials they use for CNC cutting. Reliable manufacturers have a wide range of materials available, such as aluminum, steel, stainless steel, and titanium, and can provide guidance in material selection based on your project requirements.
5. Check for customization and design services: Consider whether the manufacturer has the ability to offer design services or work with your custom design. This could be valuable if you require assistance or modifications to your design.
6. Request samples and quotations: Obtain samples of the manufacturers’ previous work and request a detailed quotation for your specific project. Review the quality of the samples and ensure that the quotation includes all the necessary details like material costs, production timelines, and shipping arrangements.
7. Verify communication and customer support: Effective communication is crucial when working with international manufacturers. Consider the responsiveness, language proficiency, and overall professionalism displayed by the manufacturer during your interactions. Good customer support throughout the process can save time and prevent potential issues.
8. Consider location and logistics: Evaluate the manufacturer’s location, as it can impact shipping costs and lead times. Located in regions with developed infrastructure, such as coastal cities, may provide better logistics and faster shipping options.
By following these steps, you can find and select reliable CNC cut metal manufacturers in China, ensuring your project is handled by a reputable and capable manufacturer.
How to check cnc cut metal manufacturers website reliable,use google chrome SEOquake check if ranking in top 10M
When checking the reliability of a CNC cut metal manufacturer’s website, using Google Chrome and SEOquake can be quite helpful. Here are a few steps to follow:
1. Install the SEOquake extension on Google Chrome: Firstly, add the SEOquake extension to your Google Chrome browser. This tool provides valuable information about a website’s SEO performance and rankings.
2. Search for the manufacturer’s website: Use Google to search for the CNC cut metal manufacturer’s website. Open the link to their homepage.
3. Activate SEOquake: Once on the manufacturer’s website, click the SEOquake icon at the top-right corner of your browser to activate the tool. A bar will appear at the top of the webpage, showing key metrics.
4. Check their website ranking: Look for the “SEMRush Rank” metric in the SEOquake bar. This provides the website’s ranking among the top 10 million websites on the internet. If a manufacturer’s website is ranked within this range, it indicates a good level of web presence.
5. Verify other metrics: Consider examining additional SEOquake metrics like the number of indexed pages, social media engagement, domain age, and website traffic. These factors can further validate the manufacturer’s website reliability.
6. Assess website design and content: Scrutinize the website’s design for professionalism and user-friendliness. Evaluate the quality of content, images, and product descriptions. A reliable manufacturer usually invests in a well-designed and informative website.
7. Look for certifications and testimonials: Keep an eye out for industry certifications, quality standards, or any acknowledgments that demonstrate the manufacturer’s credibility. Additionally, read any customer testimonials or reviews available on their website to gauge the quality of their products and services.
By following these steps, you can utilize Google Chrome and SEOquake to quickly assess the reliability of a CNC cut metal manufacturer’s website, ensuring you make an informed decision before engaging further with them.
Top 10 cnc cut metal manufacturers in China with each 160 words introduce products,then use markdown create table compare
1. Dongguan Fusheng Precision Technology Co., Ltd. specializes in CNC cutting of metal materials. Their products include custom-made metal parts, precision machining components, and sheet metal fabrication. With advanced CNC machinery and skilled technicians, they provide high-precision and high-quality metal cutting services for a wide range of industries.
2. Guangzhou Hongtai Precision Technology Co., Ltd. offers CNC metal cutting services using advanced equipment like laser cutting machines and waterjet cutters. They provide precise and intricate metal cutting solutions for various materials such as stainless steel, aluminum, brass, and titanium. Their services cater to industries like aerospace, automotive, and electronics.
3. Ningbo Yinzhou Taili Machinery Co., Ltd. specializes in CNC cutting services for stainless steel, carbon steel, aluminum, and other metals. They have a wide range of CNC machinery and can handle large-scale production with accuracy and efficiency. Their metal cutting products include custom sheet metal components, precision machined parts, and structural steel components.
4. Shenzhen Topwell Technology Co., Ltd. is a leading CNC metal manufacturer offering precision cutting services for a variety of metals including steel, aluminum, brass, and copper. They provide customization options for CNC cut parts, ensuring high accuracy and quality. Their products cater to industries like telecommunications, medical devices, and automotive.
5. Suzhou Sutaike Machinery Technology Co., Ltd. focuses on CNC cutting of metal poles, tubes, and profiles. They offer high-precision and high-efficiency solutions for metal cutting and can handle various materials such as stainless steel, copper, and aluminum. Their products are widely used in construction, furniture manufacturing, and decorative applications.
6. Nanjing Precision Engineering Co., Ltd. specializes in CNC cutting of metal components and parts. Their services cover stainless steel, aluminum, brass, and titanium. They provide precision machining, laser cutting, and waterjet cutting services, delivering products that meet tight tolerances and high-quality standards.
7. Hangzhou Hengli Metal Processing Co., Ltd. is known for their CNC cutting services for metal sheets, plates, and profiles. They have advanced cutting equipment and experienced technicians, enabling them to offer precise and efficient cutting solutions. Their products include small to large-scale customized metal parts and components.
8. Beijing Jinda Taigong Technology Co., Ltd. is a CNC cutting manufacturer that produces metal products for various industries. They specialize in cutting stainless steel, aluminum, and titanium. Their cutting services include laser cutting, plasma cutting, and flame cutting, delivering high-quality products with minimal distortion.
9. Shanghai Olimy Co., Ltd. offers CNC metal cutting services for different materials such as stainless steel, aluminum, and brass. They provide precision machining for complex and intricate parts, ensuring high accuracy and quality. Their products are widely used in industries like electronics, telecommunications, and automotive.
10. Kunshan Deshicheng Precision Machinery Co., Ltd. is a reliable CNC metal cutting manufacturer known for their precision and high-quality products. They provide cutting services for various metals, including steel, copper, aluminum, and brass. Their products are widely used in industries such as electronics, telecommunications, and automotive.
| Manufacturer | Products |
|:—————————————————:|:————————————————————-:|
| Dongguan Fusheng Precision Technology Co., Ltd. | Custom metal parts, precision machining components, sheet metal fabrication |
| Guangzhou Hongtai Precision Technology Co., Ltd. | Precise metal cutting solutions for stainless steel, aluminum, brass, titanium |
| Ningbo Yinzhou Taili Machinery Co., Ltd. | Custom sheet metal components, precision machined parts, structural steel components |
| Shenzhen Topwell Technology Co., Ltd. | Precision cutting services for steel, aluminum, brass, copper |
| Suzhou Sutaike Machinery Technology Co., Ltd. | Precision cutting of metal poles, tubes, and profiles |
| Nanjing Precision Engineering Co., Ltd. | CNC cutting of metal components, parts, stainless steel, aluminum, brass, titanium |
| Hangzhou Hengli Metal Processing Co., Ltd. | Cutting services for metal sheets, plates, and profiles |
| Beijing Jinda Taigong Technology Co., Ltd. | Laser cutting, plasma cutting, and flame cutting of stainless steel, aluminum, titanium |
| Shanghai Olimy Co., Ltd. | CNC metal cutting services for stainless steel, aluminum, brass |
| Kunshan Deshicheng Precision Machinery Co., Ltd. | Precision cutting services for steel, copper, aluminum, brass |
These top 10 CNC cut metal manufacturers in China offer a range of products and services for industries such as automotive, aerospace, electronics, and more. Utilizing advanced CNC machinery and skilled technicians, they provide high-precision and high-quality metal cutting solutions to meet diverse requirements. Whether it’s custom-made metal parts, precision machining components, or sheet metal fabrication, these manufacturers offer efficient and accurate cutting services for various metals like stainless steel, aluminum, brass, and titanium. By comparing their expertise, specialties, and product offerings through the table provided above, customers can easily identify the suitable manufacturer based on their specific metal cutting needs.
Background Research for cnc cut metal manufacturers Companies in China, use qcc.com archive.org importyeti.com
When searching for CNC cut metal manufacturers in China, three useful online resources are Qcc.com, Archive.org, and Importyeti.com. These platforms provide valuable information about companies operating in the metal manufacturing industry in China.
Qcc.com is a comprehensive database that contains information about businesses in China. It offers detailed company profiles, including contact information, registration status, financial data, and more. By searching for “CNC cut metal manufacturers” on Qcc.com, one can gather a list of companies in the industry and obtain relevant details to assess their capabilities.
Archive.org is an online platform that archives web pages, allowing users to access previous versions of websites. This tool can be beneficial when researching CNC cut metal manufacturers in China. By entering the website addresses or names of specific manufacturers found on Qcc.com, for example, one can potentially view archived versions of their websites to gather additional information such as their product range, equipment, certifications, and past projects.
Importyeti.com is a platform that provides import and export data, offering insights into companies’ shipment records. By examining trade activities related to CNC cut metal manufacturers in China, one can identify their customers, markets, and product portfolio. This data can be used to evaluate the manufacturing capabilities, market reach, and reputation of potential suppliers in China.
In conclusion, Qcc.com, Archive.org, and Importyeti.com are valuable resources for conducting background research on CNC cut metal manufacturers in China. Utilizing these platforms can help gather essential information about companies’ registration status, financial data, past projects, equipment, trade activities, and more. These insights are crucial for making informed decisions when selecting suitable manufacturers for CNC cut metal products.
Leveraging Trade Shows and Expos for cnc cut metal Sourcing in China
Trade shows and expos are valuable platforms for sourcing CNC cut metal in China. These events provide an opportunity for businesses to connect with reputable suppliers, explore new products, and stay updated on the latest industry trends. By leveraging these trade shows and expos, businesses can efficiently source CNC cut metal and gain a competitive edge in the market.
Attending trade shows and expos in China allows businesses to directly interact with numerous suppliers under one roof. This saves time and effort compared to searching for suppliers individually. Exhibitors at these events showcase their CNC cut metal products, providing businesses with a firsthand look at the quality, variety, and capabilities offered.
Trade shows and expos also foster face-to-face communication between buyers and suppliers. This direct interaction allows businesses to establish relationships, negotiate prices, discuss technical specifications, and address any concerns. Building strong connections with suppliers is crucial for long-term partnerships and ensures smooth operations.
Furthermore, trade shows and expos serve as a platform for businesses to stay updated on the latest advancements in CNC cut metal technology. Manufacturers showcase their innovative techniques, machinery, and materials, allowing businesses to stay ahead of the competition by adopting cutting-edge solutions. They can also obtain product samples, compare different suppliers, and assess their capabilities before making purchasing decisions.
To make the most out of trade shows and expos, businesses should thoroughly research and plan their visit in advance. They should identify specific shows related to CNC cut metal sourcing in China and create a list of potential suppliers to visit. Researching exhibitors and their products beforehand enables businesses to prioritize and optimize their time at the event.
In conclusion, trade shows and expos present an efficient and effective means of sourcing CNC cut metal from China. These events provide businesses with the opportunity to explore a wide range of suppliers, establish relationships, negotiate prices, and stay updated on the latest industry advancements. By leveraging trade shows and expos, businesses can streamline their sourcing process and enhance their competitiveness in the market.
The Role of Agents and Sourcing Companies in Facilitating cnc cut metal Purchases from China
Agents and sourcing companies play a crucial role in facilitating CNC cut metal purchases from China. These entities act as intermediaries between buyers and manufacturers, assisting in the procurement process and ensuring smooth transactions.
One of the main benefits of using agents or sourcing companies is their extensive network and knowledge of the Chinese market. With their expertise and understanding of the local industry, they can connect buyers with reputable CNC cut metal manufacturers who meet their specific requirements. This saves buyers valuable time and effort in searching for suitable suppliers themselves.
Agents and sourcing companies also help buyers overcome language and cultural barriers. Communication can be challenging when dealing directly with Chinese manufacturers, as language differences can lead to misinterpretations or misunderstandings. Agents act as translators, ensuring clear and accurate communication between both parties. They also bridge any cultural gaps that may arise, ensuring smooth business relationships.
Furthermore, agents and sourcing companies assist buyers in negotiating favorable terms and prices. They have established relationships with manufacturers and are equipped with market insights, allowing them to negotiate competitive pricing, favorable payment terms, and potentially even exclusive deals. This can result in cost savings for buyers and increase their profitability.
In addition, these entities handle logistical matters, including shipping, customs clearance, and quality control. They have the resources and expertise to navigate complex international shipping processes, ensuring that the purchased CNC cut metal products reach the buyer on time and in excellent condition. They also conduct quality control inspections to ensure that the products meet the specified standards and avoid any potential quality issues.
Overall, agents and sourcing companies simplify the process of purchasing CNC cut metal from China. Their industry knowledge, language proficiency, and logistical expertise make them invaluable in sourcing reliable suppliers, negotiating favorable terms, and ensuring the smooth delivery of high-quality products.
Price Cost Research for cnc cut metal manufacturers Companies in China, use temu.com and 1688.com
When conducting price cost research for CNC cut metal manufacturers in China, two popular websites that can be utilized are temu.com and 1688.com. These platforms offer a wide range of suppliers and manufacturers, making it easier to compare prices and find the best deals.
Temu.com is a business-to-business (B2B) online sourcing platform that connects buyers and suppliers in various industries. It provides a comprehensive database of CNC cut metal manufacturers in China, allowing users to search for specific products and obtain price quotations. With temu.com, buyers can directly communicate with manufacturers, negotiate prices, and make informed purchasing decisions based on their specific requirements.
Another valuable resource for price cost research is 1688.com, a popular Chinese-language website owned by Alibaba Group. It serves as a wholesale marketplace, offering a vast selection of products, including CNC cut metal services. 1688.com provides detailed information about suppliers and their products, allowing users to compare pricing, minimum order quantities, and other relevant details. However, it’s important to note that the website is primarily in Chinese, so translation tools or assistance may be required for non-Chinese speakers.
To maximize the efficiency of price cost research on these platforms, it is advisable to follow some best practices. Firstly, always provide clear requirements and specifications to ensure accurate quotations from manufacturers. Secondly, consider the overall production capacity and capabilities of the manufacturer to ensure they can meet your demands. Additionally, it’s essential to consider factors such as quality control, shipping options, and any additional services provided by the manufacturer.
In conclusion, by utilizing online platforms like temu.com and 1688.com, buyers can efficiently conduct price cost research for CNC cut metal manufacturers in China. These websites offer extensive supplier databases, enabling users to compare prices, negotiate deals, and make informed purchasing decisions. However, it’s important to thoroughly evaluate manufacturers based on their capabilities and other factors beyond just pricing.
Shipping Cost for cnc cut metal import from China
The shipping cost for importing CNC cut metal from China will depend on various factors such as the weight, dimensions, destination, mode of transportation, and any additional services required. Generally, there are two commonly used modes of shipping: air freight and sea freight.
Air freight offers faster transit times but is relatively more expensive compared to sea freight. The cost will be calculated based on either the dimensional weight or the actual weight, whichever is higher. Additional charges may include fuel surcharges, security fees, handling fees, and customs clearance charges. It is also worth noting that air freight is more suitable for smaller quantities or urgent shipments.
On the other hand, sea freight is more cost-effective for larger quantities or bulk shipments. It is charged based on the volume of goods (CBM – cubic meters) or the weight (TEU – twenty-foot equivalent unit) of the cargo. Sea freight requires longer transit times, typically varying from a few weeks to a couple of months.
To provide a rough estimate, the shipping cost for a small package of CNC cut metal via air freight from China to the United States can range between $5 to $15 per kilogram. Keep in mind that air freight rates are subject to fluctuations and often depend on various factors like the volume of shipments, fuel prices, and demand.
In contrast, sea freight rates can range from $500 to $1500 per CBM (cubic meter) for a shipment from China to the United States. It is important to note that these rates may vary depending on the shipping line, destination port, current conditions, and additional services such as insurance, customs clearance, and delivery to the final destination.
It is advisable to obtain shipping quotes from multiple freight forwarders or shipping agents to compare prices and services. Ultimately, the best shipping method will depend on the urgency, budget, and specific requirements of the CNC cut metal import from China.
Compare China and Other cnc cut metal Markets: Products Quality and Price,Visible and Hidden Costs
China is one of the leading markets for CNC cut metal products globally. When comparing China with other CNC cut metal markets in terms of product quality and price, as well as visible and hidden costs, several key factors emerge.
In terms of product quality, China has made significant advancements in recent years. While there are many reliable and high-quality CNC cut metal manufacturers in the country, the overall perception of Chinese products still varies. The quality of Chinese products can range from excellent to poor, depending on the supplier. Other CNC cut metal markets, such as Germany, Switzerland, and the United States, are known for their consistently high-quality products due to their strict quality control standards.
Price is often a significant factor when comparing CNC cut metal markets. Chinese manufacturers generally offer competitive prices due to lower labor and production costs compared to other markets. The lower costs are mainly attributed to China’s large labor force and economies of scale. Other markets, especially those in Western countries, often have higher labor costs, which can result in higher product prices. However, it is important to consider that price alone does not determine product quality.
Visible costs, such as material costs, labor costs, and transportation costs, are relatively straightforward to assess. Chinese manufacturers may offer lower visible costs due to their efficient supply chains and large production capacities. However, other markets may have higher visible costs due to higher labor and material costs. It is essential to carefully analyze these costs as they impact the final price of CNC cut metal products.
Hidden costs, on the other hand, may not be immediately apparent and can vary between different markets. One significant hidden cost associated with Chinese manufacturers is the risk of intellectual property infringement. Companies outsourcing CNC cut metal production to China might face the potential theft of their proprietary designs or unauthorized production of their products. Other markets, especially those with stringent intellectual property laws, may offer greater protection against such risks.
In conclusion, China’s CNC cut metal market offers competitive prices and has improved product quality in recent years, although concerns about consistency remain. Other markets, particularly in Western countries, are known for consistently high-quality products but may come at a higher price due to labor and material costs. Visible costs, such as labor and material costs, can be lower in China due to economies of scale, while hidden costs, such as intellectual property risks, may be higher. Ultimately, businesses should carefully evaluate their priorities and requirements when deciding between different CNC cut metal markets.
Understanding Pricing and Payment Terms for cnc cut metal: A Comparative Guide to Get the Best Deal
When it comes to pricing and payment terms for CNC cut metal, it is vital to understand the factors that influence costs and negotiate the best deal. This comparative guide aims to provide insights into the key considerations involved in pricing and payment terms for CNC cut metal, helping you secure the most favorable agreement.
Firstly, the complexity and intricacy of the design significantly impact the pricing. More intricate designs require additional time, labor, and tooling, which typically result in higher costs. It is crucial to provide the supplier with detailed specifications and drawings to enable accurate quoting.
The material selection is another critical factor affecting pricing. Different metals have varying costs and difficulty levels in the cutting process. Understand the characteristics of the metal needed for your project and analyze its availability and price fluctuations in the market.
Batch size and production volume also play a crucial role in determining pricing. Bulk orders often lead to economies of scale, offering potential discounts. Discuss your volume requirements with suppliers and negotiate quantity-based pricing models.
Furthermore, suppliers may consider the estimation of machine time required for cutting the metal. The number of CNC machines and their capabilities at the supplier’s facility will determine their production capacity. This information can aid you in negotiating lead times and ensuring timely delivery.
When it comes to payment terms, several options are commonly available. Traditional methods include full payment upfront or a percentage of the payment upfront. However, it is essential to evaluate the trustworthiness and reputation of the supplier before committing a significant sum in advance.
Alternatively, some suppliers offer progress payments, where payment is made in stages based on completed milestones. This option reduces risk, but staying diligent in monitoring progress is crucial.
Lastly, consider the impact of shipping and additional costs such as packaging and taxes. Clarify with the supplier if these expenses are included in the pricing or if they are to be borne separately.
In conclusion, ensure that pricing discussions include factors such as design complexity, material selection, volume requirements, and machine time estimation. Negotiate payment terms that balance your financial security and the supplier’s trustworthiness. Also, consider additional costs and logistics involved to accurately evaluate the total expenditure involved in purchasing CNC cut metal. By utilizing this comparative guide, you can navigate the pricing and payment terms to secure the best deal for your CNC cut metal needs.
Chinese Regulations and Industry Standards Certifications for cnc cut metal,Import Regulations and Customs for cnc cut metal from China
Chinese Regulations and Industry Standards Certifications for CNC Cut Metal:
In China, the production and sale of CNC cut metal products are subject to various regulations and industry standard certifications. These regulations aim to ensure the quality and safety of the products, as well as promote fair trade practices. The following are some key regulations and certifications relevant to the CNC cut metal industry in China.
1. Manufacturing License: CNC cut metal manufacturers in China are required to obtain a manufacturing license issued by the relevant authorities. This license confirms that the manufacturer meets the necessary quality and safety standards.
2. ISO 9001: This internationally recognized certification ensures that a company has implemented an effective quality management system. It demonstrates that the manufacturer has standardized processes in place to consistently deliver products that meet customer requirements.
3. ISO 14001: This certification focuses on environmental management systems. It ensures that CNC cut metal manufacturers in China are committed to minimizing their environmental impact and implementing sustainable practices.
4. GB/T Standards: China has developed a series of national standards known as GB/T standards. These standards cover various aspects of CNC cut metal production, including dimensional tolerances, material properties, and testing methods. Manufacturers need to comply with these standards to ensure product quality and compatibility.
Import Regulations and Customs for CNC Cut Metal from China:
When importing CNC cut metal products from China, importers need to comply with certain regulations and customs procedures. These procedures are in place to facilitate trade while ensuring product safety and fair competition. The following are some key regulations and customs requirements when importing CNC cut metal from China.
1. Customs Declarations: Importers are required to declare accurate and detailed information about the imported CNC cut metal products to the customs authorities. This includes product descriptions, quantities, values, and other relevant details.
2. Import Duties and Taxes: Importers need to pay applicable duties and taxes on imported CNC cut metal products based on the customs valuation. The rates vary depending on factors such as the product category and country of origin.
3. Product Inspections: Imported CNC cut metal products may be subject to inspections by customs authorities to ensure compliance with safety and quality standards. These inspections aim to prevent the entry of substandard or non-compliant products into the market.
4. Documentation Requirements: Importers must provide the necessary documentation, including commercial invoices, packing lists, bills of lading, and certificates of origin, to facilitate customs clearance. Compliance with customs documentation requirements is crucial to avoid delays or rejection of the shipment.
In conclusion, Chinese regulations and industry standards certifications ensure the quality and safety of CNC cut metal products. When importing CNC cut metal from China, importers need to comply with customs regulations and documentation requirements, as well as pay applicable duties and taxes.
Sustainability and Environmental Considerations in cnc cut metal Manufacturing
Sustainability and environmental considerations in CNC cut metal manufacturing play a crucial role in ensuring a greener and more responsible approach to production. CNC (Computer Numerical Control) technology enables precise and customizable metal cutting, resulting in reduced waste and enhanced efficiency. However, it is essential to address sustainability aspects throughout the entire manufacturing process to minimize environmental impact.
One of the primary sustainability considerations in CNC cut metal manufacturing is material selection. Opting for environmentally friendly materials, such as recycled or responsibly sourced metals, can significantly reduce the carbon footprint associated with metal production. Additionally, recycling and reusing metal scraps and remnants generated during the cutting process mitigates waste and conserves valuable resources.
Energy consumption is another critical area for sustainability. CNC machines require electricity to operate, and using energy-efficient machinery can help minimize the environmental footprint. Employing power-saving features and optimizing the cutting process can reduce energy consumption, resulting in lower greenhouse gas emissions. Furthermore, sourcing electricity from renewable sources or investing in on-site renewable energy generation can contribute to a more sustainable manufacturing process.
Waste management and disposal practices also deserve attention in CNC cut metal manufacturing. Proper segregation and recycling of waste materials, such as coolant or lubricant fluids, help prevent pollution and promote a circular economy approach. Implementing stringent waste management protocols can minimize the release of harmful substances into the environment, ensuring compliance with environmental regulations.
Transportation is another aspect to consider in terms of sustainability. Reducing the distance traveled during the supply chain for raw materials and finished products can decrease carbon emissions. Local sourcing of materials and utilizing efficient logistic strategies, such as consolidating shipments, can contribute to sustainability efforts.
Collaboration with suppliers is crucial in achieving sustainable CNC cut metal manufacturing. Prioritizing partnerships with suppliers committed to environmental responsibility and encouraging sustainable practices throughout the entire supply chain can have a significant positive impact.
In summary, sustainability and environmental considerations in CNC cut metal manufacturing encompass material selection, energy efficiency, waste management, transportation, and supplier collaboration. By addressing these aspects, manufacturers can achieve a more sustainable and responsible approach, aligning with global efforts to protect the environment and conserve resources.
List The Evolution history of “cnc cut metal”
The evolutionary history of CNC cut metal can be traced back to the early 1950s when Computer Numerical Control (CNC) technology was first introduced. At that time, CNC machines were primarily used for the automation of various manufacturing processes, including metal cutting.
The first CNC machines utilized punched tape cards to program the desired instructions for metal cutting. These instructions were interpreted by the machine, which controlled the movement and rotation of cutting tools to shape the metal material based on the programmed design. This technology revolutionized metal cutting processes by providing increased accuracy and repeatability compared to manual methods.
As computer technology advanced, so did CNC machining capabilities. In the 1970s and 1980s, the development of microprocessors and miniaturization of electronics enabled the integration of computers directly into CNC machines. This eliminated the need for punched tape cards and allowed for the use of computer-aided design (CAD) software to generate cutting instructions.
In the 1990s, the introduction of CAD/CAM software further enhanced the capabilities of CNC machining. CAD/CAM software enabled engineers to create intricate and complex designs that could be directly translated into cutting instructions for CNC machines. This opened up new possibilities for the cutting of metal, allowing for the fabrication of more intricate and customized components with greater precision.
In recent years, advancements in CNC technology have focused on improving automation and efficiency. These advancements include the use of robotics for material handling, laser scanning for 3D modeling, and adaptive machining to optimize cutting processes in real-time.
Additionally, the availability of a wide range of cutting tools, such as plasma cutters, waterjets, and lasers, has expanded the applications of CNC cut metal. These tools offer different advantages in terms of precision, speed, and cost-effectiveness.
Today, CNC cut metal is widely used in various industries, including aerospace, automotive, and construction. Its ability to produce highly accurate and complex parts has made it an essential tool in the manufacturing sector, driving innovation and pushing the boundaries of what can be achieved in metal fabrication.
The Evolution and Market Trends in cnc cut metal Industry
The CNC cut metal industry has experienced significant evolution and market trends over the years. With advancements in technology and automation, CNC (Computer Numerical Control) machines have transformed the metal cutting process, leading to increased precision, productivity, and efficiency.
One important trend in the CNC cut metal industry is the adoption of multi-axis machining. Traditional CNC machines typically operate on three axes (X, Y, and Z). However, with the demand for complex shapes and intricate designs, manufacturers now utilize machines capable of operating on five or more axes. This enables the production of more intricate and precise metal cuts for various industries such as aerospace, automotive, and medical devices.
Furthermore, there has been a shift towards the use of high-speed cutting techniques. Manufacturers are investing in CNC machines capable of achieving higher cutting speeds while maintaining accuracy. This trend has resulted in reduced production times and increased productivity. High-speed cutting also allows for the processing of different types of materials, including heat-sensitive alloys and hardened steels.
Another noticeable trend is the integration of CNC machines with advanced software and automation technologies. Program optimization, digital simulations, and real-time monitoring have become essential tools in the metal cutting industry. Automation features such as tool changes, material handling, and quality control not only improve overall productivity but also ensure consistent part quality.
The market for CNC cut metal has been expanding due to various factors. One of the primary drivers is the growth in the aerospace and automotive industries. These sectors demand high-quality precision parts, which can be efficiently produced using CNC machines. The rapid growth of the medical device industry has also contributed to the increased demand for CNC cut metal components, as they often require intricate designs and precision machining.
Moreover, the rise of additive manufacturing technologies like 3D printing has influenced the CNC cut metal industry. While additive manufacturing offers unique capabilities, CNC machining remains crucial for post-processing, finishing, and achieving tight tolerances. The integration of 3D printing and CNC machining has created a hybrid manufacturing approach, offering more design freedom and production flexibility.
In conclusion, the CNC cut metal industry has evolved significantly, driven by technological advancements and market demands. The adoption of multi-axis machining, high-speed cutting techniques, and automation has revolutionized the metal cutting process. The market trends reflect the growing demand for precision parts in sectors such as aerospace, automotive, and medical devices. Additionally, the integration of additive manufacturing and CNC machining has paved the way for hybrid manufacturing approaches, offering new possibilities in terms of design and production.
Custom Private Labeling and Branding Opportunities with Chinese cnc cut metal Manufacturers
Chinese CNC cut metal manufacturers offer excellent opportunities for custom private labeling and branding. With their advanced technologies and competitive pricing, these manufacturers can meet various customization needs of businesses seeking to establish their own unique brand identities.
The CNC cut metal manufacturing process allows for precise and intricate designs to be translated onto metal surfaces, making it ideal for customization and branding purposes. Manufacturers in China have extensive experience in working with diverse metals such as aluminum, stainless steel, brass, and copper, ensuring flexibility in material selection for different branding requirements.
Private labeling enables businesses to display their own logos, company names, or other custom designs on the products they manufacture. It helps to enhance brand recognition, strengthen customer loyalty, and differentiate products from competitors. Chinese manufacturers understand the significance of private labeling and have the capability to incorporate such specifications into their CNC cutting processes.
In addition to private labeling, Chinese CNC cut metal manufacturers offer branding opportunities through custom packaging and labeling. Businesses can work closely with these manufacturers to create packaging designs that align with their brand image, ensuring a cohesive and professional look for their products. Customized labeling can also be added to packages, providing important product information or conveying the brand’s unique selling points.
Furthermore, Chinese manufacturers often offer low minimum order quantities, making it feasible for businesses of all sizes to take advantage of these branding opportunities. This allows startups and small businesses with limited budgets to establish their own custom branded products without significant upfront investments.
To summarize, Chinese CNC cut metal manufacturers present enticing opportunities for custom private labeling and branding. Their expertise in metalworking, ability to work with various metals, and flexibility in customization make them ideal partners for businesses seeking to create unique and recognizable products in the market.
Tips for Procurement and Considerations when Purchasing cnc cut metal
When it comes to purchasing CNC cut metal, there are several considerations that need to be taken into account. Here are some tips for procurement and important factors to consider:
1. Specifications: Clearly define the specifications required for the CNC cut metal, including dimensions, material type, thickness, and any special requirements such as tolerance levels or surface finish. This ensures that the supplier can provide you with accurate quotes and meet your specific needs.
2. Quality and Certification: Ensure that the supplier has the necessary certifications and quality control processes in place to meet your standards. Look for suppliers who are ISO certified or have other relevant industry certifications.
3. Supplier Selection: Research and evaluate potential suppliers before making a decision. Consider their experience, reputation, capabilities, and production capacity. Request samples or references to assess the quality of their work.
4. Price and Lead Time: Obtain quotes from multiple suppliers to compare prices and lead times. However, be cautious of choosing the lowest priced option as it could compromise quality. Ensure that the lead time aligns with your project timeline.
5. Supplier Capacity: Confirm that the supplier has the capacity to handle your order volume. Assess their production capabilities, machinery, and workforce to avoid delays or quality issues.
6. Communication and Support: Effective communication with the supplier throughout the procurement process is crucial. Ensure that they can provide ongoing support, address any concerns, and provide timely updates on the progress of your order.
7. Packaging and Shipping: Discuss packaging requirements and shipping options with the supplier to ensure that the CNC cut metal arrives in good condition. Consider factors such as protective packaging, insurance coverage, and shipping methods.
8. Payment Terms: Clarify the payment terms with the supplier, including deposit requirements, milestone payments, or payment upon delivery. Establish a payment schedule that is mutually beneficial and consider negotiating discounts for bulk or repeat orders.
9. Contract and Legal Considerations: Have a written contract in place that clearly outlines the terms and conditions of the purchase, including specifications, pricing, delivery date, and any penalties for non-compliance. Seek legal advice if necessary.
10. Continuous Evaluation: Regularly assess the performance of the supplier to ensure they consistently meet your expectations. Consider factors such as quality, delivery reliability, and customer service to maintain a reliable supply chain.
By following these tips and considering the important factors for procurement, you can ensure a successful purchase of CNC cut metal that meets your requirements and expectations.
FAQs on Sourcing and Manufacturing cnc cut metal in China
Q: What is CNC cut metal?
A: CNC stands for Computer Numerical Control, which is a technology that utilizes computer programs to control the movements of machine tools and process raw materials into finished products according to precise specifications. CNC cut metal refers to the process of using computer-controlled machines to precisely cut and shape metal materials.
Q: Why source and manufacture CNC cut metal in China?
A: China is known for its cost-effective manufacturing capabilities, which make it an attractive destination for sourcing and manufacturing CNC cut metal. The country has a vast number of metal fabrication facilities equipped with advanced CNC machinery and skilled labor. Additionally, China has a wide range of metal suppliers and stable supply chains that can provide raw materials at competitive prices.
Q: What types of CNC cut metal can be sourced and manufactured in China?
A: China offers a wide range of CNC cut metal options, including but not limited to:
1. Sheet metal: Flat pieces of metal that can be cut and shaped into various forms.
2. Tubing: Cylindrical or hollow metal structures that can be cut, bent, and welded to create different products.
3. Extrusions: Metal profiles that are created by forcing molten metal through a shaped opening.
4. Machined parts: Precise metal components that are shaped through CNC milling, turning, or drilling processes.
Q: What considerations should be made when sourcing and manufacturing CNC cut metal in China?
A: When sourcing and manufacturing CNC cut metal in China, it is important to consider the following factors:
1. Quality control: Ensure that the chosen manufacturer has proper quality control systems in place to meet your desired standards.
2. Communication: Effective communication is essential to avoid misunderstandings and ensure manufacturing specifications are met.
3. Intellectual property protection: Take necessary steps to protect your designs and avoid intellectual property infringement.
4. Logistics and shipping: Plan for transportation and shipping arrangements to minimize any delays or issues with delivery.
Q: How can I find reliable manufacturers for CNC cut metal in China?
A: To find reliable manufacturers, you can:
1. Research online: Utilize sourcing platforms, directories, and forums to identify potential manufacturers and read reviews from other buyers.
2. Attend trade shows: Participate in industry-specific exhibitions and trade shows in China to meet manufacturers directly and evaluate their capabilities.
3. Get referrals: Seek recommendations from industry experts, colleagues, or business contacts who have experience sourcing CNC cut metal from China.
Note: The above FAQs provide a basic overview of sourcing and manufacturing CNC cut metal in China and should not be considered exhaustive. Additional research and due diligence should be undertaken to fully understand the complexities of sourcing and manufacturing in China.
Why contact sourcifychina.com get free quota from reliable cnc cut metal suppliers?
Sourcifychina.com offers free quota from reliable CNC cut metal suppliers for a few reasons. Firstly, by providing a free quota, Sourcifychina.com aims to attract potential customers and showcase the quality of their supplier network. This allows businesses to assess the capabilities and pricing of different suppliers without incurring any costs upfront.
Furthermore, Sourcifychina.com understands that finding reliable and high-quality suppliers for CNC cut metal can be challenging. By offering a free quota, they aim to simplify the sourcing process and make it more convenient for businesses. This saves time and effort for businesses that may otherwise have to search and vet multiple suppliers on their own.
Additionally, Sourcifychina.com has established partnerships with reliable suppliers in China who meet their stringent quality standards. These suppliers have been thoroughly assessed and verified, guaranteeing the reliability and consistency of their products and services. By offering a free quota from these trusted suppliers, Sourcifychina.com instills confidence in businesses that their sourcing needs will be met effectively.
In conclusion, Sourcifychina.com offers a free quota from reliable CNC cut metal suppliers to attract potential customers, simplify the sourcing process, and ensure the quality and reliability of the sourced products. This approach aims to provide businesses with a hassle-free sourcing experience and help them find suitable suppliers from their extensive network.