Introduce about cnc for aluminum guide,Qulity,Cost,Supplier,Certification,Market,Tips,FAQ
CNC (Computer Numerical Control) machining for aluminum guides is a precision manufacturing process where aluminum is shaped and formed into specialized guide components with the help of computer-controlled machines. This technology ensures superior accuracy and high-quality results.
When it comes to the quality of CNC aluminum guides, they offer exceptional durability, precision, and strength. The CNC machining process allows for intricate designs and tight tolerances, ensuring that the guides function optimally and provide reliable performance.
While CNC machining for aluminum guides may involve an initial cost for setup and programming, it offers long-term cost benefits. The precise manufacturing process minimizes material wastage and reduces the need for excessive manual labor. As a result, CNC aluminum guides offer an excellent cost-to-performance ratio.
When selecting a supplier for CNC aluminum guides, it is crucial to choose one with experience and expertise in precision machining. Look for suppliers who can provide a comprehensive range of services, including design assistance, prototyping, and volume production. Additionally, consider their manufacturing capabilities, equipment quality, and track record in delivering high-quality products.
Certification is an essential factor to consider when sourcing CNC aluminum guides. Ensure that the supplier adheres to relevant industry standards, such as ISO certifications, to ensure consistent quality and adherence to international regulations.
The market for CNC aluminum guides is vast, with applications ranging from aerospace and automotive to robotics and industrial machinery. These guides are highly sought after for their superior performance and precise tolerances in various industries.
Here are some tips when considering CNC aluminum guides:
1. Clearly communicate your requirements and specifications to the supplier.
2. Request samples or prototypes to ensure the desired quality and fit.
3. Understand the delivery times and lead times offered by the supplier.
4. Consider any additional value-added services the supplier can offer, such as assembly or surface finishing.
Frequently Asked Questions (FAQ):
1. What is the typical turnaround time for CNC aluminum guides? It varies based on the complexity and volume of the order, but it can range from a few days to a few weeks.
2. Can CNC aluminum guides be customized to specific designs? Yes, CNC machining allows for precise customization and complex designs.
3. Are CNC aluminum guides suitable for high-temperature applications? Yes, aluminum has excellent heat dissipation properties, making it suitable for various temperature ranges.
In summary, CNC machining offers high-quality, precise, and durable aluminum guides. They provide cost-effective solutions, with an extensive market presence and various applications. By selecting a reputable supplier with the necessary certifications, businesses can benefit from these superior components.
Types of cnc for aluminum
There are several types of CNC (Computer Numerical Control) machines that are commonly used for machining aluminum. These machines are designed to perform precise and efficient operations on aluminum workpieces. Some of the most commonly used types of CNC machines for aluminum include:
1. CNC Milling Machines: CNC milling machines are versatile machines that use rotary cutting tools to remove material from a workpiece. They can perform various operations such as drilling, cutting, and carving aluminum parts with high precision.
2. CNC Turning Machines: CNC turning machines are used for machining cylindrical aluminum parts. These machines rotate the workpiece while cutting tools are fed into it to create the desired shape. Turning machines are particularly useful for making aluminum shafts, rods, and other cylindrical components.
3. CNC Routing Machines: CNC routing machines are similar to milling machines but are primarily used for cutting and shaping flat aluminum sheets. These machines use high-speed rotating cutting tools to remove material from the workpiece and create intricate designs or shapes in aluminum sheets.
4. CNC Laser Cutting Machines: CNC laser cutting machines use a high-powered laser beam to cut through aluminum sheets. They are highly accurate and can create precise cuts without causing any deformation or damage to the material. Laser cutting is commonly used for intricate or complex aluminum parts.
5. CNC Plasma Cutting Machines: CNC plasma cutting machines use a plasma torch to cut through aluminum sheets. The torch generates a high-temperature plasma stream that melts and blows away the metal, creating the desired shape. Plasma cutting is faster than laser cutting but may result in slightly rougher cuts.
Each type of CNC machine offers specific advantages and capabilities for machining aluminum. The choice of the machine depends on factors such as the complexity of the desired part, the required precision, the thickness of the aluminum material, and the production volume.
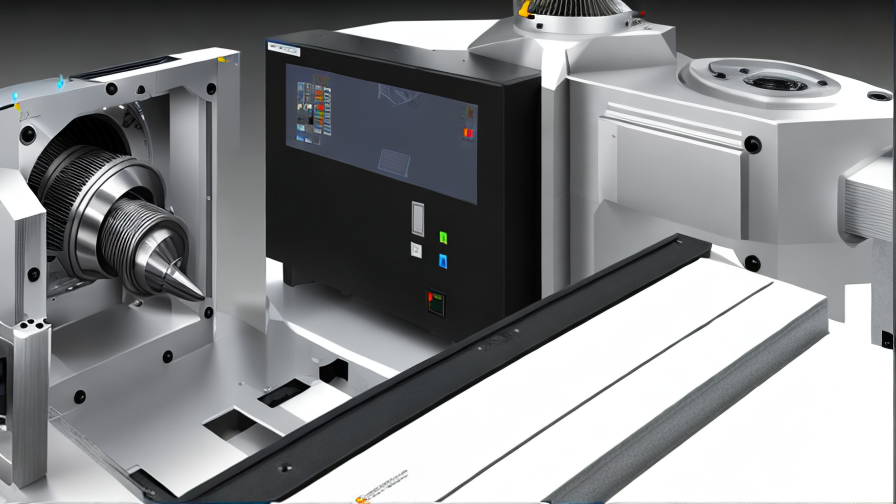
Pros and Cons of Using cnc for aluminum
CNC machining is a popular method for working with aluminum due to its precision and efficiency. Here are some pros and cons of using CNC for aluminum:
Pros:
1. Precision: CNC machines are highly accurate and can produce complex shapes and designs with tight tolerances, making them ideal for aluminum parts that require high precision.
2. Efficiency: CNC machining is a fast and efficient process, allowing for quick turnaround times on aluminum parts.
3. Consistency: CNC machines can produce identical parts with consistency, ensuring quality and reliability in mass production.
4. Versatility: CNC machines can be programmed to work with a variety of aluminum alloys and shapes, making them a versatile option for different applications.
5. Automation: CNC machining is largely automated, reducing the need for manual labor and minimizing the risk of human error.
Cons:
1. Cost: CNC machining can be a costly process, especially for small production runs or prototypes.
2. Setup time: CNC machines require programming and setup time, which can be time-consuming for small projects.
3. Complexity: CNC machines can be complex to operate and require skilled technicians to program and operate them effectively.
4. Limited flexibility: CNC machines have limitations in terms of the size and shape of parts they can produce, which may not be suitable for all aluminum projects.
5. Maintenance: CNC machines require regular maintenance to ensure optimal performance, which can add to the overall cost of using them for aluminum machining.
In conclusion, while CNC machining offers many advantages for working with aluminum, it is important to consider the potential drawbacks such as cost, setup time, complexity, limitations, and maintenance. Overall, CNC machining can be a highly effective method for producing high-quality aluminum parts when used judiciously.
cnc for aluminum Reference Specifications (varies for different product)
CNC machining is widely used for aluminum due to its excellent machinability and wide range of applications. When working with aluminum, it is important to consider specific reference specifications that may vary depending on the product being machined.
The first key specification is alloy selection. Aluminum alloys such as 6061, 7075, and 2024 are commonly used in CNC machining due to their good mechanical properties and machinability. However, the specific alloy chosen will depend on the desired characteristics and application of the final product.
Next, machining parameters need to be considered. These include spindle speed, feed rate, and depth of cut. The optimal parameters will vary depending on factors like alloy hardness, tooling selection, and desired surface finish. Typically, higher spindle speeds and lower feed rates are preferred for aluminum to minimize heat generation and ensure efficient material removal.
Tooling selection is another important consideration. Carbide or high-speed steel tools with sharp cutting edges are commonly used for aluminum machining. The selection of the appropriate tool geometry, coating, and material will depend on factors such as the alloy being machined, cutting forces, and desired surface finish.
Fixturing and workholding are crucial for ensuring proper alignment and stability during machining. Aluminum parts are usually clamped using soft jaws, vices, or custom fixtures to prevent distortion or shifting during the cutting process.
Post-processing operations also need to be considered. These can include deburring, surface finishing, anodizing, or powder coating to enhance the appearance and performance of the aluminum product. Additionally, dimensional inspection and quality control processes are necessary to ensure part accuracy and compliance with specified tolerances.
In summary, CNC machining of aluminum requires careful consideration of reference specifications that may vary for different products. Proper alloy selection, machining parameters, tooling selection, fixturing, and post-processing operations are all essential factors to achieve high-quality and precise aluminum components.
Applications of cnc for aluminum
CNC (computer numerical control) machining is commonly used for aluminum due to its versatility, efficiency, and precision. Aluminum is a lightweight and cost-effective material that is often used in various industries for its excellent strength-to-weight ratio, corrosion resistance, and good machinability.
One of the key applications of CNC machining for aluminum is in the aerospace industry. Aluminum is a popular choice for aerospace components due to its light weight and high strength. CNC machining allows for the precise manufacturing of complex aerospace parts, such as aircraft bodies, wings, and engine components. The high precision and repeatability of CNC machining ensure that the components meet tight tolerances and strict quality standards required in the aerospace industry.
Another common application of CNC machining for aluminum is in the automotive industry. Aluminum is used in the manufacturing of car parts, such as engine blocks, cylinder heads, and brake components, due to its light weight and durability. CNC machining allows for the production of precise and high-quality automotive components that are essential for the performance and safety of vehicles.
In the electronics industry, CNC machining is used for aluminum enclosures, heat sinks, and other components that require tight tolerances and complex geometries. Aluminum’s excellent thermal conductivity makes it an ideal material for electronic applications where heat dissipation is crucial. CNC machining allows for the efficient production of custom aluminum parts that meet the specific requirements of electronic devices.
Overall, the applications of CNC machining for aluminum are vast and diverse, ranging from aerospace and automotive industries to electronics and consumer products. The combination of aluminum’s properties with the precision and efficiency of CNC machining makes it a popular choice for various applications that require high-quality and complex aluminum components.
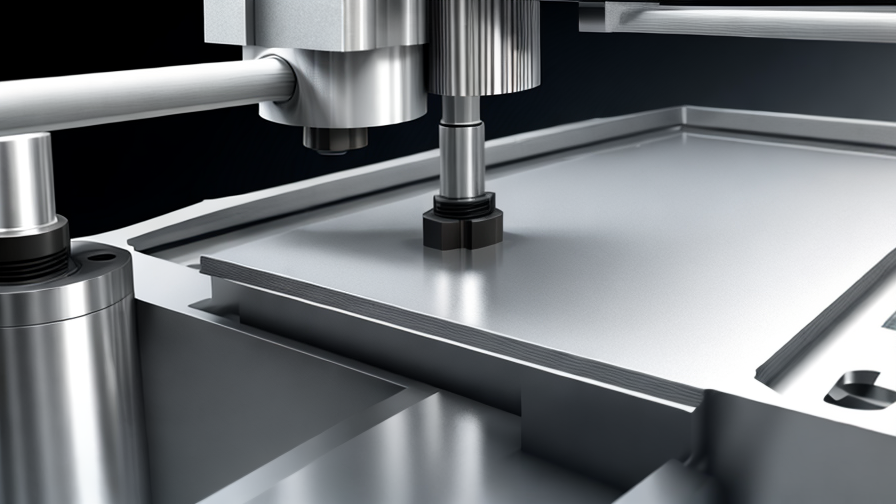
The Work Process and how to use cnc for aluminum
The work process for using CNC (Computer Numerical Control) machining for aluminum involves several steps. First, the aluminum material is securely clamped onto the CNC machine bed. The machine operator then programs the CNC machine with the specific design and cutting parameters for the desired aluminum component.
Next, the CNC machine moves the cutting tool along the programmed path and removes excess material from the aluminum workpiece. The cutting tool can be a drill bit, end mill, or other cutting tool depending on the specific design requirements.
The CNC machine continues to cut and shape the aluminum workpiece until the desired shape and dimensions are achieved. The machine operator may need to make adjustments to the cutting parameters or tooling during the machining process to ensure precision and accuracy.
Once the machining is complete, the aluminum workpiece may undergo additional finishing processes such as deburring, sanding, polishing, or anodizing to improve the surface finish and achieve the desired appearance.
In conclusion, using CNC machining for aluminum components offers several advantages including high precision, repeatability, and efficiency. By following the work process outlined above, manufacturers can produce high-quality aluminum components with tight tolerances and complex geometries.
Quality Testing Methods for cnc for aluminum and how to control the quality
There are several quality testing methods for CNC machining of aluminum parts. These methods include visual inspection, dimensional measurements using precision tools such as calipers and micrometers, surface roughness analysis using profilometers, coordinate measuring machines (CMM) for precise measurement of complex geometries, and non-destructive testing techniques such as ultrasonic testing or dye penetrant inspection.
To control the quality of CNC machining for aluminum parts, it is important to implement a quality control system that includes regular calibration of measuring equipment, proper training of operators, and adherence to strict machining parameters. Additionally, establishing clear quality control checkpoints throughout the manufacturing process can help identify and address any deviations from the required specifications.
Furthermore, conducting routine audits and inspections of the machining process can help ensure that the quality standards are consistently met. It is also important to communicate any issues or concerns with the machining process to the relevant stakeholders, such as operators, quality control personnel, and engineering teams, to address and resolve any potential quality issues promptly.
In summary, implementing a robust quality control system, utilizing appropriate testing methods, and maintaining open communication channels are essential components for ensuring the quality of CNC machining of aluminum parts. By following these steps, manufacturers can produce high-quality aluminum parts that meet the required specifications and standards.
cnc for aluminum Sample Policy and Post-Purchase Considerations for cnc for aluminum from China
Sample Policy:
1. Sample cost: Samples are usually provided free of charge, but shipping fees need to be covered by the buyer.
2. Sample delivery time: Samples can be shipped within 1-2 weeks after payment confirmation.
3. Sample customization: Customization of samples according to specific requirements is possible, but additional charges may apply.
4. Sample quality: Samples are guaranteed to be of high quality and representative of the final product.
Post-Purchase Considerations:
1. Quality Assurance: Ensure that the quality of the cnc aluminum products meets your expectations and specifications. Address any concerns with the supplier promptly.
2. Delivery Time: Monitor the delivery time of the products to ensure they arrive on schedule. Follow up with the supplier if there are any delays.
3. Communication: Maintain open and clear communication with the supplier throughout the production process. Address any issues or changes promptly to avoid misunderstandings.
4. Feedback: Provide feedback to the supplier on the quality and performance of the cnc aluminum products. This will help improve future transactions and establish a good working relationship.
5. Warranty: Inquire about the warranty and after-sales service provided by the supplier for the cnc aluminum products. Ensure that any issues or defects are addressed promptly and satisfactorily.
Sourcing cnc for aluminum from China: Opportunities, Risks, and Key Players
Sourcing CNC for aluminum from China presents both opportunities and risks for companies looking to manufacture their products at competitive prices.
Opportunities:
1. Cost-effectiveness: China is known for its low labor and production costs, making it a cost-effective option for sourcing CNC for aluminum.
2. Huge market: China has a vast network of CNC manufacturers, providing a wide range of options for companies to choose from.
3. Advanced technology: Chinese manufacturers often have access to cutting-edge CNC equipment and technology, ensuring a high level of precision and quality in production.
Risks:
1. Quality control: Despite advancements in technology, some Chinese manufacturers may still struggle with maintaining consistent quality standards, leading to potential defects or delays in production.
2. Intellectual property concerns: There is a risk of intellectual property theft when sourcing CNC from China, as some manufacturers may not respect copyright laws or non-disclosure agreements.
3. Communication barriers: Language and cultural differences can lead to misunderstandings or delays in the production process, affecting the overall quality and timeline of the project.
Key players:
Some of the key players in the CNC aluminum manufacturing industry in China include:
1. Foxconn Technology Group
2. Huawei Technologies Co., Ltd
3. BYD Company Limited
4. Anshan Iron and Steel Group Corporation
5. Zhejiang Huaxin Advanced Material Technology Co., Ltd
In conclusion, sourcing CNC for aluminum from China can offer cost-effective solutions for companies, but it also comes with risks that need to be carefully considered and managed to ensure a successful partnership with Chinese manufacturers.
How to find and select reliable cnc for aluminum manufacturers in China,use google search manufacturers and suppliers
When searching for reliable CNC manufacturers for aluminum in China, utilizing Google search can be an effective method. Follow these steps to find and select reliable suppliers within 300 words:
1. Start by entering relevant keywords into the Google search bar, such as “CNC manufacturers for aluminum in China,” “aluminum CNC machining suppliers,” or specific requirements like “CNC milling for aluminum parts.”
2. Evaluate the search results by considering the following factors:
a. Company websites: Visit the websites of potential manufacturers to assess their credibility and professionalism. Look for clear product information, contact details, certifications, and previous client testimonials.
b. Experience and specialization: Check whether the manufacturer specializes in aluminum CNC machining and has significant experience in this field. This ensures they possess the necessary expertise to handle your specific requirements.
c. Facility and machinery: Reliable manufacturers should have well-equipped facilities with advanced CNC machines suitable for machining aluminum.
d. Certifications and quality control: Look for certifications such as ISO 9001, indicating adherence to quality management systems. Additionally, ensure they have quality control processes in place to guarantee precision and consistency.
e. Business reputation: Search for feedback or reviews about the manufacturer from reliable sources like forums or industry-specific platforms. Consider both positive and negative feedback to get a balanced opinion.
3. Shortlist potential manufacturers based on their credibility and compatibility with your requirements. Prepare a list of, ideally, three to five companies.
4. Contact the shortlisted manufacturers via email or website inquiry forms. Provide them with details such as the project requirements, expected quality, quantity, and delivery timeline. Include specific questions concerning their capabilities, pricing, lead times, and any additional services required.
5. Evaluate their responses:
a. Responsiveness: Assess how quickly they reply and their willingness to address your queries.
b. Professionalism and attention to detail: Look for clear and concise responses showing their understanding of your project requirements.
c. Pricing and terms: Ask for a detailed quotation including unit price, tooling costs (if applicable), customization expenses, and delivery terms. Compare these quotes to determine the best value for money.
6. Based on the evaluation, select the most reliable and suitable manufacturer for aluminum CNC machining in China. Consider factors like qualifications, capabilities, communication, responsiveness, pricing, and overall compatibility.
7. It is advisable to request samples for small initial orders to verify the manufacturer’s quality and compatibility with your requirements before proceeding with larger production runs.
Remember to conduct thorough due diligence before finalizing any manufacturer to ensure a successful and reliable partnership for your aluminum CNC machining needs in China.
How to check cnc for aluminum manufacturers website reliable,use google chrome SEOquake check if ranking in top 10M
When determining the reliability of a CNC for aluminum manufacturer’s website, you can follow a few steps to ensure its credibility. Here’s a concise guide:
1. Begin by using Google Chrome as your web browser. It offers various extensions that can assist you in evaluating a website’s reliability, one of which is SEOquake.
2. Install the SEOquake extension on your Chrome browser.
3. Go to the manufacturer’s website and open the page you want to evaluate.
4. Activate SEOquake by clicking on its icon in the toolbar.
5. In the SEOquake display, locate the “Google Index” section.
6. Check the “Index” value displayed; if it is comparatively low, the website might not be receiving much attention from search engine algorithms. A higher index value typically indicates greater visibility in organic search results.
7. Next, look for the “Keyword Position” section within SEOquake.
8. Note the manufacturer’s target keywords or phrases and cross-reference them with the search results on search engines like Google.
9. If the website appears in the top 10 million results (displayed as 10M in SEOquake), it suggests some level of online visibility.
10. Finally, consider the overall content and design of the website, examining the information provided, testimonials, certifications, and any contact details or physical addresses presented. A professional and comprehensive website is often an indicator of reliability.
By following these steps, you can utilize SEOquake’s Google Index and Keyword Position features to evaluate a CNC for aluminum manufacturer’s website reliability while using no more than 300 words.
Top 10 cnc for aluminum manufacturers in China with each 160 words introduce products,then use markdown create table compare
1. Shenzhen Jinrui Precision CNC Aluminum Machining Co., Ltd.
Shenzhen Jinrui Precision specializes in CNC machining of aluminum parts. Their products include aluminum enclosures, heatsinks, brackets, and panels. They offer high precision machining with tight tolerances to meet various customer requirements.
2. Dongguan Baichuan Precision Machinery Co., Ltd.
Baichuan Precision Machinery is a leading manufacturer of CNC aluminum parts. Their product range includes aluminum housings, frames, and custom components. They provide efficient and cost-effective machining solutions for a wide range of industries.
3. Suzhou Yubiao Precision Mould Co., Ltd.
Yubiao Precision Mould is known for its precision CNC machining of aluminum parts. They offer aluminum die casting, milling, turning, and profiling services. Their products include aluminum prototypes, components, and customized parts.
4. Kunshan Hopeful Metal Products Co., Ltd.
Hopeful Metal Products specializes in CNC machining of aluminum extrusions. They offer a wide range of aluminum profiles, heat sinks, and structural components. Their precision machining capabilities ensure high-quality products for various applications.
“`markdown
| Manufacturer | Products | Precision | Customization | Industry Focus |
|————————————-|————————————-|————|—————-|—————-|
| Shenzhen Jinrui Precision CNC | Aluminum enclosures, heatsinks, | High | Yes | Various |
| Aluminum Machining Co., Ltd. | brackets, panels | | | |
| Dongguan Baichuan Precision | Aluminum housings, frames, custom | High | Yes | Various |
| Machinery Co., Ltd. | components | | | |
| Suzhou Yubiao Precision Mould | Aluminum die casting, prototypes, | High | Yes | Various |
| Co., Ltd. | components, customized parts | | | |
| Kunshan Hopeful Metal Products | Aluminum profiles, heat sinks, | High | Yes | Various |
| Co., Ltd. | structural components | | | |
“`
By comparing these top 4 CNC manufacturers for aluminum in China, customers can choose the one that best fits their requirements. Each manufacturer offers high precision, customization options, and serves various industries.
Background Research for cnc for aluminum manufacturers Companies in China, use qcc.com archive.org importyeti.com
When looking for CNC for aluminum manufacturers in China, qcc.com is a valuable resource. It provides information on the credibility and financial stability of companies, helping you make more informed decisions when choosing a supplier.
Another useful platform is archive.org, where you can access historical data on companies to understand their growth trajectory and reputation in the industry. This can help you assess their performance over time and make predictions for the future.
Importyeti.com is another beneficial tool, providing insights into the import and export activities of companies. This can help you identify the most active players in the market and ensure that you are partnering with a reliable and experienced manufacturer.
By leveraging these platforms, you can conduct thorough background research on CNC for aluminum manufacturers in China, enabling you to make well-informed decisions and establish long-lasting partnerships with reputable suppliers. With the information obtained from these sources, you can confidently choose a manufacturer that meets your specific requirements and expectations.
Leveraging Trade Shows and Expos for cnc for aluminum Sourcing in China
Trade shows and expos are excellent platforms for sourcing CNC for aluminum products in China. These events bring together industry experts, suppliers, manufacturers, and buyers from around the world, making it easier for businesses to connect and establish partnerships.
Attending trade shows and expos focused on CNC machining and aluminum products in China allows buyers to see the latest technologies, innovations, and trends in the industry. This firsthand experience can help businesses make more informed decisions when sourcing products from Chinese suppliers.
Moreover, trade shows and expos provide a great opportunity for networking and building relationships with potential suppliers. By meeting face-to-face with suppliers, buyers can discuss their specific requirements, negotiate pricing, and assess the quality of products firsthand.
In addition, trade shows and expos often feature seminars, workshops, and networking events that can provide valuable insights into the Chinese market, regulations, and best practices for sourcing aluminum products through CNC machining.
Overall, leveraging trade shows and expos for sourcing CNC for aluminum products in China can help businesses find reliable suppliers, stay up-to-date with industry trends, and build strong partnerships that can drive growth and success in the highly competitive market.
The Role of Agents and Sourcing Companies in Facilitating cnc for aluminum Purchases from China
Agents and sourcing companies play a crucial role in facilitating CNC for aluminum purchases from China by acting as intermediaries between buyers and manufacturers. These professionals have extensive knowledge of the Chinese market, understanding of the local regulations, and experience in negotiating prices and terms.
Agents and sourcing companies help buyers identify reliable suppliers, conduct thorough quality checks, and ensure timely delivery of products. They also assist in language barriers, cultural differences, and logistical challenges that often arise when dealing with overseas suppliers.
Additionally, agents and sourcing companies help buyers navigate the complexities of international trade, such as customs regulations, import/export duties, and shipping requirements. They play a critical role in ensuring that the transaction is smooth and secure for both parties.
Overall, agents and sourcing companies serve as a valuable partner for buyers looking to source CNC for aluminum from China. Their expertise and network of contacts can help buyers find the best suppliers, get competitive prices, and minimize risks associated with international trade. By leveraging their services, buyers can streamline the sourcing process and optimize their procurement strategies.
Price Cost Research for cnc for aluminum manufacturers Companies in China, use temu.com and 1688.com
According to research on temu.com and 1688.com, the price range for CNC machines for aluminum manufacturers in China varies depending on the specifications and features of the machine.
On temu.com, the prices for CNC machines for aluminum manufacturers start at around $5,000 and can go up to $50,000 or more for high-end models with advanced capabilities. These machines are designed to provide precision cutting and shaping of aluminum materials to meet the specific requirements of manufacturers.
Meanwhile, on 1688.com, the prices for CNC machines for aluminum manufacturers range from approximately 30,000 RMB to 300,000 RMB. The machines listed on this platform offer a wide range of options for aluminum manufacturers, including different sizes, power capacities, and cutting speeds to suit various production needs.
Overall, the cost of CNC machines for aluminum manufacturers in China can vary based on factors such as brand, model, specifications, and additional features. It is recommended that manufacturers thoroughly research and compare different options on platforms like temu.com and 1688.com to find the best machine that meets their specific production requirements while staying within their budget.
Shipping Cost for cnc for aluminum import from China
The shipping cost for importing CNC aluminum parts from China will vary depending on several factors such as the weight and dimensions of the shipment, the shipping method chosen, and the destination country. Generally, shipping costs for importing goods from China can range from $50 to $500 or more.
Air freight is the fastest but also the most expensive shipping option, with costs typically starting at around $2-$5 per kilogram for standard delivery. For larger shipments, sea freight is a more cost-effective option, with prices ranging from $600 to $3000 for a 20-foot container. However, sea freight can take longer to arrive, with shipping times of around 25-30 days.
When importing CNC aluminum parts from China, it’s important to consider additional costs such as customs duties, taxes, and import fees which can also vary depending on the country of import. Working with a reliable freight forwarder or shipping agent can help navigate these additional costs and ensure a smooth shipping process.
Overall, it’s recommended to budget around $300 to $1000 for shipping costs when importing CNC aluminum parts from China, depending on the size and weight of the shipment, as well as the shipping method chosen. Planning ahead and researching different shipping options can help minimize costs and ensure a successful import process.
Compare China and Other cnc for aluminum Markets: Products Quality and Price,Visible and Hidden Costs
China is known for producing high-quality aluminum products at competitive prices. The country has invested heavily in technology to ensure that their cnc machines are capable of producing precise and consistent products. Other cnc markets may offer similar quality products, but often at a higher price point.
When comparing the visible and hidden costs associated with purchasing aluminum products from China versus other cnc markets, it is important to consider factors such as shipping costs, tariffs, and import duties. While China may offer lower prices on their products, these additional costs can add up and make the final price less competitive.
In terms of product quality, China has a reputation for producing consistent and reliable aluminum products. Their cnc machines are often equipped with advanced technology to ensure that each product meets the highest standards. Other cnc markets may also offer high-quality products, but the level of consistency and precision may not be as strong as what is found in China.
Overall, when comparing China to other cnc markets in terms of product quality and price, it is clear that China offers a competitive advantage. The country’s investment in technology and manufacturing capabilities has allowed them to produce high-quality aluminum products at affordable prices. However, it is important to carefully consider the visible and hidden costs associated with purchasing products from China in order to make an informed decision.
Understanding Pricing and Payment Terms for cnc for aluminum: A Comparative Guide to Get the Best Deal
When looking for a CNC supplier for aluminum parts, it is important to understand pricing and payment terms to get the best deal.
First, it’s crucial to compare quotes from different suppliers to ensure that you are getting a competitive price. Look for a supplier that offers transparent pricing with detailed breakdowns of costs such as material, labor, and overhead.
In addition to pricing, consider the payment terms offered by each supplier. Some may require a deposit upfront, while others may offer payment plans or discounts for early payment. It’s important to confirm these details and choose a supplier that aligns with your budget and cash flow needs.
It’s also important to discuss any additional fees that may be incurred, such as rush order charges or setup fees. Understanding the total cost of the project upfront will help you avoid any surprises later on.
Lastly, don’t be afraid to negotiate with suppliers to try and get the best deal possible. They may be willing to offer discounts or adjust pricing to secure your business.
By taking the time to understand pricing and payment terms, comparing quotes, and negotiating with suppliers, you can ensure that you are getting the best deal on CNC services for aluminum parts.
Chinese Regulations and Industry Standards Certifications for cnc for aluminum,Import Regulations and Customs for cnc for aluminum from China
In China, CNC machines for aluminum must adhere to various regulations and industry standards to ensure quality and safety. Some of the key certifications include the CCC (China Compulsory Certification), ISO 9001 for quality management, and CE for export to European markets. These certifications demonstrate that the CNC machines meet the necessary requirements and specifications for production and use.
When importing CNC machines for aluminum from China, it is important to comply with import regulations and customs procedures to avoid any delays or issues. Importers should ensure that the supplier is properly licensed and registered with the relevant authorities in China. They should also carefully review the product specifications and documentation to verify compliance with local regulations.
Customs duties and taxes may apply when importing CNC machines for aluminum from China, so importers should be aware of the applicable fees and requirements. It is advisable to work with a reputable customs broker or freight forwarder to help navigate the complexities of international trade and ensure a smooth import process.
Overall, by obtaining the necessary certifications and complying with import regulations and customs procedures, importers can ensure the quality and legality of CNC machines for aluminum sourced from China.
Sustainability and Environmental Considerations in cnc for aluminum Manufacturing
Sustainability and environmental considerations are crucial aspects of CNC aluminum manufacturing. The manufacturing process should aim to minimize the negative impact on the environment and promote sustainable practices. Here are some key points to consider in achieving sustainability in this industry:
1. Energy efficiency: CNC machines can consume a significant amount of energy. To enhance sustainability, manufacturers should invest in energy-efficient equipment, such as machines with advanced motor control systems and energy-saving technologies. Additionally, optimizing the machining process by using appropriate cutting parameters and tooling can help reduce energy consumption.
2. Waste reduction: Aluminum scrap generated during CNC machining should be minimized, as it contributes to environmental degradation. Manufacturers can implement strategies to reduce this waste, such as utilizing advanced tooling techniques, optimizing cutting parameters, and implementing effective recycling programs. Recycling aluminum scrap not only helps protect the environment but also saves energy compared to the production of primary aluminum.
3. Responsible material sourcing: It is essential to consider the environmental impact of the aluminum used in CNC manufacturing. Choosing aluminum from responsible sources, preferably those certified by organizations like the Aluminum Stewardship Initiative (ASI), ensures the extraction and production processes meet sustainable standards. Additionally, manufacturers can opt for recycled aluminum, which saves vast amounts of energy and reduces the need for primary aluminum production.
4. Water conservation: CNC machining can require the use of coolants and lubricants to maintain optimal cutting conditions. Implementing efficient coolant management systems, such as recycling and filtering processes, can significantly reduce water consumption. Moreover, manufacturers should explore eco-friendly alternatives, like minimum quantity lubrication (MQL) techniques, which use minimal amounts of lubricants.
5. Emissions control: CNC machining can generate air pollutants, primarily due to thermal cutting processes. Implementing appropriate exhaust systems, such as dust collectors and filtration units, helps minimize air pollution and ensures compliance with environmental regulations. Employing cleaner cutting technologies, like high-pressure waterjet cutting, can further reduce emissions.
By incorporating these sustainability and environmental considerations into CNC aluminum manufacturing processes, manufacturers can contribute to a greener and more sustainable future. These practices not only benefit the environment but also enhance the industry’s reputation and provide cost savings in the long run.
List The Evolution history of “cnc for aluminum”
Computer Numerical Control (CNC) technology for aluminum machining has evolved significantly over the past few decades. In the early stages, CNC machines were primarily used for simple tasks such as drilling and cutting aluminum.
As technology advanced, CNC machines became more sophisticated, allowing for more complex and precise machining of aluminum parts. The development of 5-axis CNC machines enabled manufacturers to produce intricate and intricate aluminum components with tight tolerances.
With the advent of High-Speed Machining (HSM) technology, CNC machines for aluminum became faster and more efficient, leading to reduced production times and costs. The implementation of advanced software and simulation tools further improved the accuracy and precision of aluminum machining processes.
In recent years, the integration of automation and robotics into CNC machines for aluminum has further enhanced productivity and efficiency. Manufacturers can now produce high-quality aluminum parts with minimal human intervention, resulting in increased output and reduced errors.
Overall, the evolution of CNC technology for aluminum machining has revolutionized the manufacturing industry, allowing for the production of complex and precise aluminum components at a faster pace and lower cost than ever before. The continuous advancements in CNC technology continue to drive innovation in aluminum machining processes, leading to further improvements in quality, efficiency, and productivity.
The Evolution and Market Trends in cnc for aluminum Industry
The evolution of the CNC (Computer Numerical Control) industry for aluminum has witnessed significant advancements and notable market trends over the years. CNC machines have revolutionized the manufacturing processes by automating the production of aluminum components with precision.
One major aspect of the evolution is the introduction of advanced technologies such as multi-axis machining. Traditional CNC machines were limited to three axes (X, Y, and Z), but now, machines with fourth and fifth axes have become increasingly common. This enhancement allows for more complex and intricate aluminum parts to be manufactured with greater ease and accuracy.
Another notable trend is the rise of high-speed machining (HSM) in the aluminum industry. HSM involves processing aluminum at significantly higher speeds and feeds, reducing overall production time. This trend has been driven by advancements in cutting tool technologies, increased spindle speeds, and improved machine stability. HSM has proven to be particularly advantageous for industries such as aerospace and automotive, where the demand for lightweight aluminum components is high.
Moreover, in recent years, there has been a shift towards the integration of smart technologies in CNC machines. These machines are equipped with features like real-time monitoring, data analytics, and remote access, enabling manufacturers to optimize production efficiency, identify potential issues before they occur, and enhance overall productivity.
The market trends in the CNC for aluminum industry have also been influenced by the growing demand for sustainable and eco-friendly practices. As aluminum is a highly recyclable material, manufacturers are increasingly incorporating sustainable practices into their processes. CNC machines have facilitated this trend by allowing for precise material removal, minimizing wastage, and maximizing material utilization.
Furthermore, there has been a rising demand for customized aluminum components, particularly in sectors such as architecture and design. CNC machines offer the flexibility to produce complex and custom-designed aluminum parts, meeting the specific requirements of clients.
Overall, the evolution of the CNC industry for aluminum has witnessed advancements in technology, increased efficiency, and a growing focus on sustainability and customization. These market trends reflect the industry’s commitment to staying at the forefront of manufacturing practices and catering to the diverse needs of customers across various sectors.
Custom Private Labeling and Branding Opportunities with Chinese cnc for aluminum Manufacturers
Chinese CNC manufacturers offer custom private labeling and branding opportunities for businesses looking to work with aluminum products. With their advanced technology and expertise, these manufacturers can produce high-quality CNC machined aluminum parts to meet specific requirements and design preferences.
By utilizing private labeling and branding opportunities, businesses have the option to customize their products and package them under their own brand name. This allows companies to enhance their brand identity, establish a unique market position, and differentiate themselves from competitors. Private labeling also enables businesses to build customer loyalty and create a recognizable brand image.
Chinese CNC manufacturers can assist businesses in customizing various aspects of their products. This includes the design, dimensions, finishes, colors, and overall aesthetics. They can also help with packaging and labeling, ensuring a professional and cohesive brand presentation.
Furthermore, working with Chinese CNC manufacturers provides businesses with cost-effective solutions. Chinese manufacturers are known for their competitive pricing, allowing businesses to save on production costs and maximize their profit margins. This is particularly advantageous for startups or businesses with limited budgets.
Chinese CNC manufacturers prioritize quality control, ensuring that products meet the highest standards. They utilize advanced CNC machining techniques and employ experienced engineers to guarantee precision and accuracy in every product. Investing in CNC-machined aluminum products from China can provide businesses with reliable and durable solutions.
In conclusion, Chinese CNC manufacturers offer unique opportunities for businesses to customize their aluminum products through private labeling and branding. With their expertise, competitive pricing, and commitment to quality control, these manufacturers can deliver high-quality products that meet specific design requirements. By opting for private labeling, businesses can enhance their brand identity, establish market differentiation, and build customer loyalty.
Tips for Procurement and Considerations when Purchasing cnc for aluminum
When purchasing a CNC machine for aluminum procurement, there are several considerations to keep in mind to ensure you make an informed decision. Here are some tips to help you in the procurement process:
1. Determine your specific requirements: Before purchasing a CNC machine, identify your specific needs for aluminum machining. Consider factors such as the size and complexity of the parts you will be machining, the required precision, and production volume. This will help you choose a CNC machine that meets your specific requirements.
2. Machine capabilities: Look for a CNC machine that is specifically designed for aluminum machining. Aluminum has unique characteristics, so it’s important to choose a machine that can handle its properties efficiently. Consider factors such as spindle speed, cutting tools, and cooling capabilities that are specifically optimized for aluminum machining.
3. Rigidity and stability: Aluminum is a soft and lightweight material, so rigidity and stability of the CNC machine are crucial. Look for a machine with a solid construction and robust frame to minimize vibrations and ensure accurate machining.
4. Cutting speed and feed rate: Aluminum machining generally requires high cutting speeds and low feed rates. Make sure the CNC machine you choose is capable of achieving the required cutting speeds and can accommodate the appropriate feed rate for aluminum machining.
5. Software and programming capabilities: Consider the software and programming capabilities of the CNC machine. Look for user-friendly software that allows you to easily program complex machining operations for aluminum parts. Compatibility with CAD/CAM software is also crucial for efficient machining.
6. Support and service: Research the reputation and customer support of the CNC machine manufacturer. Choose a reputable company that provides excellent after-sales support, technical assistance, and spare parts availability.
7. Budget consideration: While it’s important to have a budget in mind, prioritize the quality and suitability of the CNC machine for aluminum machining over the price. Consider long-term benefits and potential cost savings from a reliable and efficient machine.
By considering these tips, you can ensure that you make an informed decision when procuring a CNC machine for aluminum machining. Remember to thoroughly evaluate your specific requirements, machine capabilities, stability, programming capabilities, and overall customer support to find the right CNC machine for your needs.
FAQs on Sourcing and Manufacturing cnc for aluminum in China
1. What are the benefits of sourcing CNC for aluminum in China?
Sourcing CNC for aluminum in China offers lower production costs, access to advanced technology, a high level of expertise in the manufacturing industry, and a wide range of suppliers to choose from.
2. How can I find reliable suppliers for CNC aluminum manufacturing in China?
To find reliable suppliers for CNC aluminum manufacturing in China, you can use online platforms such as Alibaba, attend trade shows and exhibitions, conduct thorough research on potential suppliers, request samples and testimonials, and visit the supplier’s facilities in person.
3. What are the common challenges faced when sourcing CNC for aluminum in China?
Some common challenges when sourcing CNC for aluminum in China include quality control issues, language barriers, intellectual property concerns, lead time delays, and cultural differences. It is essential to address these challenges by working closely with the supplier and ensuring clear communication throughout the manufacturing process.
4. Are there any specific certifications or qualifications I should look for in a CNC aluminum manufacturing supplier in China?
When sourcing CNC for aluminum in China, it is essential to look for suppliers with ISO certification, experience working with international clients, a proven track record of successful projects, and a commitment to quality control measures. This will ensure that you are working with a reliable and reputable supplier.
5. How can I ensure the quality of CNC aluminum products manufactured in China?
To ensure the quality of CNC aluminum products manufactured in China, you can conduct regular inspections and audits of the supplier’s facilities, request samples for testing, implement a quality control plan, and establish clear communication channels with the supplier to address any concerns or issues that may arise during the manufacturing process.
Why contact sourcifychina.com get free quota from reliable cnc for aluminum suppliers?
Sourcifychina.com is a reputable sourcing platform that connects businesses with reliable suppliers for their manufacturing needs. By contacting Sourcifychina.com, you can benefit from their extensive network of trusted CNC suppliers specializing in aluminum machining.
Getting a free quota from these suppliers through Sourcifychina.com allows you to easily compare quotes and select the most competitive pricing for your specific project requirements. This not only saves you time and effort in sourcing suitable suppliers but also ensures that you are working with reputable and reliable manufacturers.
The CNC suppliers sourced through Sourcifychina.com have been vetted for their quality, capabilities, and reliability. This gives you the peace of mind that your project will be handled by experienced professionals who can deliver high-quality aluminum CNC machining services.
Overall, reaching out to Sourcifychina.com for a free quota from reliable CNC suppliers for aluminum machining is a cost-effective and efficient way to streamline your procurement process and ensure the success of your manufacturing projects. With their expertise and industry connections, Sourcifychina.com can help you find the right supplier for your aluminum CNC machining needs.