Introduce about cnc machinery manufacturers guide,Qulity,Cost,Supplier,Certification,Market,Tips,FAQ
The CNC machinery manufacturers guide is designed to assist individuals and businesses in the process of selecting, purchasing, and using CNC machinery. This comprehensive guide covers various aspects, including quality, cost, suppliers, certifications, market trends, tips, frequently asked questions (FAQs), and more.
Quality is a crucial factor when choosing CNC machinery. It is important to research and select manufacturers known for their high-quality products. Look for companies that have a reputation for precision, durability, and reliability. Consider factors such as the materials used, engineering expertise, and customer reviews to ensure the machinery meets your quality standards.
Cost is another important aspect to consider. Determine your budget and identify the most cost-effective options that meet your requirements. Look for manufacturers that offer competitive pricing without compromising on quality. Be cautious of overly cheap alternatives, as they may indicate lower quality or a lack of necessary features.
Finding reliable suppliers is essential to ensure a smooth purchasing process and ongoing support. Look for established suppliers with a wide range of CNC machinery options. Consider factors such as their experience, customer support services, and track record.
Certifications play a vital role in validating the quality and reliability of CNC machinery. Look for manufacturers that have obtained relevant certifications, such as ISO 9001 or CE marking. These certifications demonstrate the manufacturer’s commitment to meeting quality standards.
Understanding the market trends is crucial for staying informed about the latest advancements in CNC machinery. Research market reports, industry publications, and attend trade shows or conferences to stay up-to-date with technological advancements, emerging trends, and new product launches.
Tips provided in the guide can help users make informed decisions and maximize the benefits of CNC machinery. These tips may include maintenance recommendations, training suggestions, software compatibility considerations, and more.
The FAQ section addresses common questions and concerns that buyers may have. It provides answers to queries related to installation, troubleshooting, software compatibility, warranty terms, and other relevant topics.
In conclusion, the CNC machinery manufacturers guide is a valuable resource for individuals and businesses looking to invest in CNC machinery. It covers various aspects, such as quality, cost, suppliers, certifications, market trends, tips, and FAQs, providing comprehensive information to aid decision-making.
Types of cnc machinery manufacturers
There are several types of CNC machinery manufacturers that cater to different industries and applications. These manufacturers specialize in various types of CNC machines based on their functionalities and areas of expertise. Some of the common types of CNC machinery manufacturers are:
1. CNC Milling Machine Manufacturers: These manufacturers focus on producing CNC machines that are used for milling operations. CNC milling machines are utilized for cutting and shaping solid materials such as metal or plastic.
2. CNC Lathe Machine Manufacturers: These manufacturers specialize in producing CNC lathe machines. CNC lathes are used for precision turning operations, which involve rotating a workpiece on its axis while a cutting tool shapes it into the desired form.
3. CNC Router Machine Manufacturers: These manufacturers produce CNC machines that are designed specifically for routing applications. CNC routers are used to cut and shape materials like wood, plastic, or composites by following programmed paths.
4. CNC Plasma Cutting Machine Manufacturers: These manufacturers focus on producing CNC machines that utilize plasma torches to cut through electrically conductive materials such as steel, aluminum, or brass.
5. CNC Laser Cutting Machine Manufacturers: These manufacturers specialize in producing CNC machines that use laser beams to cut or engrave various materials with high precision. CNC laser cutting machines are commonly used in industries like automotive, signage, and aerospace.
6. CNC Press Brake Machine Manufacturers: These manufacturers produce CNC machines used for bending and forming sheet metal into desired shapes. CNC press brakes are widely used in the metal fabrication industry.
7. CNC Grinding Machine Manufacturers: These manufacturers focus on producing CNC machines specifically designed for grinding operations. CNC grinding machines are used for precision grinding tasks such as surface grinding, cylindrical grinding, or tool grinding.
8. CNC EDM (Electrical Discharge Machining) Machine Manufacturers: These manufacturers specialize in producing CNC machines used for high-precision machining of electrically conductive materials. CNC EDM machines use electrical discharges to remove material and shape complex parts.
Each type of CNC machinery manufacturer has its own specialization and expertise. They cater to various industries and applications, ensuring that manufacturers in those industries have access to the right CNC machines for their specific machining needs.
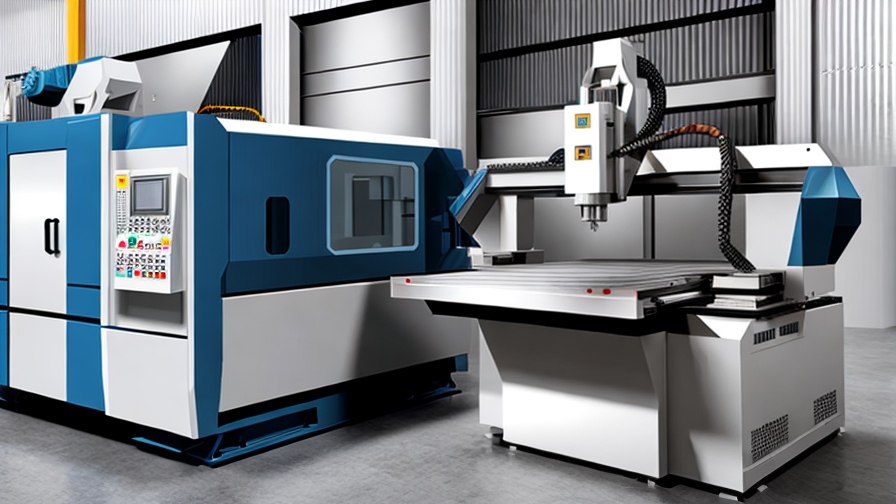
Pros and Cons of Using cnc machinery manufacturers
Using CNC (Computer Numerical Control) machinery manufacturers has several pros and cons that should be considered before making a decision. Here is a summary of some of the key advantages and disadvantages:
Pros:
1. Increased efficiency: CNC machinery can automate and streamline processes, leading to increased productivity and efficiency. It eliminates the need for manual operations and minimizes human error.
2. Precision and accuracy: CNC machines can consistently produce highly accurate and precise parts, which is vital for industries such as aerospace, automotive, and medical where precision is crucial.
3. Flexibility and versatility: CNC machinery manufacturers offer a wide range of machines that can handle various materials and perform different tasks. These machines can be easily reprogrammed to produce different products or make adjustments as needed.
4. Reduced labor costs: By automating tasks that would otherwise require manual labor, CNC machinery can significantly reduce labor costs over the long term.
5. Shorter production time: CNC machines can work continuously without the need for breaks and can produce parts or products much faster than manual operations, resulting in shortened production times.
Cons:
1. High initial cost: CNC machinery can be expensive, especially for small businesses or startups. The cost of purchasing, installing, and maintaining the machines can be a significant investment.
2. Technical expertise required: Operating and programming CNC machines requires specialized skills and training. This can lead to additional costs for training existing employees or hiring skilled operators.
3. Maintenance and repair: CNC machines require regular maintenance and occasional repairs to ensure optimal performance. These maintenance costs should be factored into the overall cost of using CNC machinery manufacturers.
4. Limited flexibility for small quantities: When producing small quantities or prototypes, it may not be cost-effective to use CNC machines as the setup and programming time can be time-consuming and costly.
5. Potential for machine failure: As with any machinery, there is always a risk of machine failure, which can lead to production downtime and additional costs for repairs or replacements.
Ultimately, the decision to use CNC machinery manufacturers should be based on careful consideration of the specific needs and capabilities of the business. While there are clear advantages in terms of efficiency, precision, and productivity, it is essential to weigh these against the potential costs and limitations associated with CNC machinery.
cnc machinery manufacturers Reference Specifications (varies for different product)
When it comes to CNC (Computer Numerical Control) machinery, various manufacturers provide different reference specifications based on the specific product. These reference specifications serve as guidelines for customers to understand the capabilities, features, and limitations of the CNC machinery. Here are some key reference specifications commonly provided by CNC machinery manufacturers.
1. Machine Type: Manufacturers specify the type of CNC machine, such as CNC milling machines, CNC lathes, CNC routers, or CNC plasma cutters. This helps customers determine which machine is suitable for their specific application.
2. Dimensions and Working Area: The physical dimensions of the machine, including length, width, and height, are mentioned. Additionally, the working area or table size specifies the maximum dimensions of the material that can be processed.
3. Axis Configuration: The number of axes determines the machine’s movement capabilities. Common axis configurations include 3-axis, 4-axis, and 5-axis machines. This specification influences the complexity and range of shapes that can be produced.
4. Spindle Speed and Power: The rotational speed of the spindle and its power rating are crucial references. Higher spindle speeds enable faster machining, while greater power is required for cutting hard materials or heavy-duty operations.
5. Tool Capacity: Manufacturers specify the number of tools that can be loaded in the machine’s tool changer. This determines the machine’s versatility and ability to perform complex operations without manual tool changes.
6. Accuracy and Repeatability: Precision is a fundamental aspect of CNC machinery. Accuracy refers to the machine’s ability to achieve the desired position, while repeatability ensures consistent results after multiple cycles. Manufacturers provide reference values for these parameters, often in microns or fractions of millimeters.
7. Control System: CNC machinery manufacturers indicate the control system used, such as Fanuc, Siemens, or Haas. Knowing the control system helps customers understand the programming requirements and compatibility with existing software or processes.
8. Connectivity and Automation: Some CNC machines offer advanced connectivity options like Ethernet or USB ports for data transfer, as well as integration with other automated systems like robotic loaders or bar feeders. These features enhance productivity and workflow integration.
9. Safety Features: Reference specifications often mention safety features like emergency stop buttons, enclosed work areas, safety interlocks, and protective covers. These features ensure operator safety and comply with industry standards.
10. Additional accessories and options: Manufacturers may provide a list of optional accessories and features available for customization, such as coolant systems, chip conveyors, probing systems, or automatic tool measuring.
It is important to note that these reference specifications may vary depending on the manufacturer, model, and intended application. Customers should carefully review and consider these specifications to ensure they meet their specific requirements before purchasing CNC machinery.
Applications of cnc machinery manufacturers
CNC machinery manufacturers play a pivotal role in various industries, offering a wide range of applications and benefits. Here are a few key areas where CNC machinery is extensively used:
1. Aerospace: CNC machinery is crucial in the aerospace industry for manufacturing high-precision components like turbine blades, engine parts, and airframes. The ability of CNC machines to produce complex shapes with tight tolerances ensures the safety and reliability of aircraft components.
2. Automotive: CNC machines are extensively employed in the automotive industry for manufacturing components like engine blocks, transmission parts, and steering systems. The accuracy and repeatability of CNC machines enable mass production while maintaining high precision, reducing costs, and improving efficiency.
3. Electronics: CNC machinery is widely used in the electronics industry for the production of printed circuit boards (PCBs) and electronic components. CNC machines offer precise drilling, routing, and cutting capabilities, ensuring the accuracy and quality of electronic devices.
4. Medical: CNC machining plays a vital role in the medical industry for producing orthopedic implants, surgical tools, and dental prosthetics. With CNC machinery, complex shapes and intricate designs can be manufactured with high precision, meeting the stringent requirements of the medical field.
5. Furniture and Woodworking: CNC machinery is extensively used in the furniture and woodworking industry for cutting, carving, and shaping various materials like wood, plastic, and composites. CNC machines enhance workflow efficiency, reduce waste, and enable customization in furniture production.
6. Prototyping and Rapid Manufacturing: CNC machinery is widely utilized in prototyping and rapid manufacturing processes. CNC machines allow for quick and precise fabrication of prototypes and low-volume production, saving time and costs compared to traditional manufacturing methods.
7. Jewelry Making: CNC machinery has revolutionized the jewelry industry, enabling intricate and detailed designs to be manufactured with ease. CNC machines can carve, mill, and engrave precious metals and gemstones, providing precise and consistent results.
8. Packaging and Printing: CNC machinery is employed in the packaging and printing industry for the production of custom packaging materials, labels, and signage. CNC machines offer a quick and accurate way to cut, engrave, and shape various materials, enhancing branding and packaging customization.
In conclusion, CNC machinery manufacturers serve a diverse range of industries and provide numerous applications. From aerospace and automotive to electronics and medical, CNC machines offer precision, efficiency, and flexibility, enabling manufacturers to meet the demands of a competitive market.
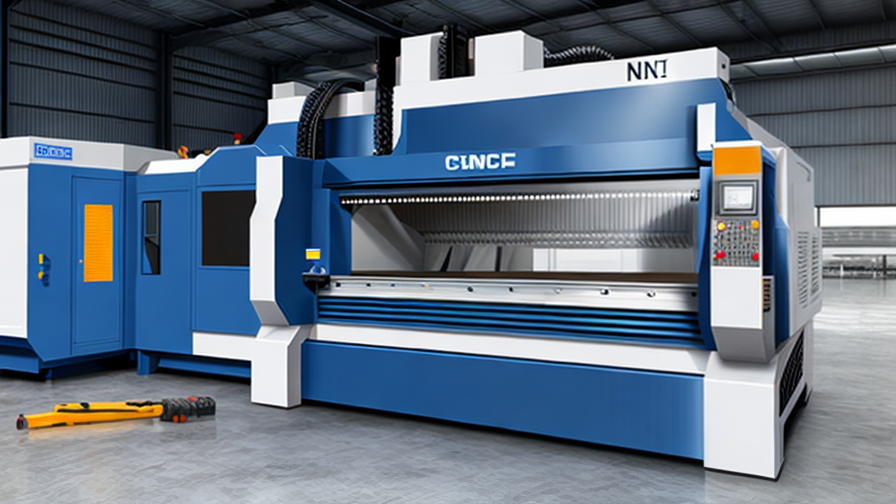
The Work Process and how to use cnc machinery manufacturers
The work process of CNC machinery involves several steps that are followed to design and manufacture various products. Here is a brief description of how to use CNC machinery manufacturers.
1. Design: The first step in the work process is to design the product using computer-aided design (CAD) software. The design is created in 2D or 3D, specifying the dimensions, geometries, and features of the product.
2. Programming: Once the design is complete, the next step is to program the CNC machine. This involves writing a set of instructions, known as G-code, which dictates the movement of the machine’s tools and the cutting path.
3. Material setup: The material to be machined is prepared and set up on the CNC machine. This involves securing the material onto a worktable or fixture using clamps or vises.
4. Tool setup: The appropriate cutting tools are selected and installed into the machine’s tool holder. The tools are chosen based on the requirements of the design and the material being machined.
5. Machine setup: The CNC machine is prepared for operation by powering it on, initializing the machine, and loading the program. The machine’s axes and tool offsets may need to be calibrated before starting the machining process.
6. Machining: Once everything is set up, the machining process begins. The CNC machine follows the programmed instructions to move the cutting tools along the specified paths, removing material from the workpiece to create the desired shape and features.
7. Inspection and finishing: After the machining is complete, the finished product is inspected for accuracy and quality. Any necessary adjustments or finishing operations, such as deburring or polishing, may be performed at this stage.
8. Repeat or iterate: The process can be repeated for producing multiple identical parts. If modifications are required, the design or program can be revised, and the machining process can be repeated to create a new version of the product.
Using CNC machinery manufacturers involves having a clear understanding of the design requirements, good programming skills, material and tool knowledge, and proficiency in operating the CNC machine. Regular maintenance and calibration of the machine are also essential to ensure its optimal performance. Taking proper safety precautions while working with CNC machinery is crucial to avoid accidents and injuries.
Quality Testing Methods for cnc machinery manufacturers and how to control the quality
Quality testing methods for CNC machinery manufacturers include the following:
1. Dimensional Inspection: This involves using precision measuring tools to check the accuracy and consistency of a component’s dimensions. This ensures that the machine parts are manufactured according to the required specifications.
2. Surface Finish Assessment: Surface roughness and finish evaluation are important for determining the quality of machined surfaces. This can be done using tools like a profilometer to measure the surface roughness or visual inspection for any visible defects.
3. Functionality Testing: This involves conducting tests to ensure that the CNC machinery performs its intended functions correctly. For example, testing the movements, speeds, and accuracy of the machine’s axes and examining the behavior of the machine under different operating conditions can be performed.
4. Material Testing: Assessing the quality of the materials used in the machine’s construction is crucial. This includes checking the hardness, tensile strength, and other mechanical properties of materials to ensure they meet the required standards.
5. Durability Testing: Subjecting the CNC machine to simulated operating conditions helps evaluate its long-term durability. This can involve running the machine continuously for an extended period or testing its resistance to vibrations, shocks, and other environmental factors.
To control quality, manufacturers can implement the following measures:
1. Standard Operating Procedures (SOPs): Clearly defined SOPs ensure consistency in manufacturing processes and help minimize variations in product quality.
2. Quality Control Inspections: Regular inspections at various stages of manufacturing help identify and rectify any issues early on. This includes inspection of raw materials, intermediate components, and finished products.
3. Training and Qualification: Ensuring that employees are trained and qualified to operate CNC machinery effectively contributes to maintaining consistent quality.
4. Calibration and Maintenance: Regular calibration and maintenance of machinery and testing equipment guarantee that they are functioning accurately, leading to reliable quality testing results.
5. Statistical Process Control (SPC): Employing SPC techniques helps monitor and control the manufacturing process. This involves collecting and analyzing data, identifying trends, and implementing necessary corrective actions to maintain consistent quality.
By employing these testing methods and control measures, CNC machinery manufacturers can ensure that their products meet the expected quality standards, leading to customer satisfaction and increased competitiveness in the market.
cnc machinery manufacturers Sample Policy and Post-Purchase Considerations for cnc machinery manufacturers from China
Sample Policy:
1. Quality Assurance: Our company ensures that all CNC machinery manufactured in China meets high-quality standards. We provide comprehensive quality control inspections at various stages of production to ensure the accuracy and precision of our machines. In case of any defects or malfunctions, we offer a warranty period for repairs or replacements.
2. Customization: We understand that different customers may have specific requirements for CNC machinery. We offer customization options to cater to individual needs, such as special tooling, additional features, or modifications to the machine’s design. Our team works closely with customers to understand their unique requirements and provides tailored solutions.
3. Technical Support: We provide timely technical support and assistance to customers before, during, and after the purchase of CNC machinery. Our knowledgeable technicians are available to address any queries, provide training, and offer troubleshooting solutions remotely or on-site.
4. Spare Parts and Maintenance: We ensure the availability of genuine spare parts for our CNC machinery. In addition, we offer maintenance contracts or service agreements to ensure regular upkeep of the machines, prolonging their lifespan and maintaining optimal performance.
Post-Purchase Considerations:
1. Installation and Testing: Upon delivery, our team of experts assists with the installation and setup of the CNC machinery. We conduct thorough testing to ensure all components are functioning correctly and offer training to customers on machine operation and maintenance.
2. Documentation and Manuals: We provide comprehensive user manuals and documentation in English or the customer’s preferred language, including machine specifications, safety guidelines, troubleshooting procedures, and maintenance instructions.
3. Technical Support and Training: Our technical support team remains available to assist customers with any queries or issues that may arise during CNC machinery operation. We offer training programs for operators and maintenance personnel to optimize their understanding of the machine and enhance productivity.
4. Warranty and After-Sales Service: We offer a warranty period for our CNC machinery, covering repairs or replacements in case of any manufacturing defects. Beyond the warranty period, we provide affordable after-sales service, including routine maintenance, repairs, and spare parts supply.
5. Feedback and Continuous Improvement: We value customer feedback and suggestions. We encourage customers to provide their insights and recommendations to help us further improve our products and services. Our aim is to constantly enhance the performance, reliability, and customer satisfaction associated with our CNC machinery.
Note: The above sample policy and post-purchase considerations are for illustration purposes only and may vary among different CNC machinery manufacturers in China.
Sourcing cnc machinery manufacturers from China: Opportunities, Risks, and Key Players
China is known for being a leading global manufacturer of various products, including machinery and equipment. When it comes to sourcing CNC (Computer Numerical Control) machinery manufacturers, China offers both opportunities and risks.
Opportunities:
1. Cost Advantage: Chinese manufacturers can often offer lower prices compared to manufacturers in other countries. This cost advantage is primarily due to factors such as lower labor and production costs in China.
2. Wide Range of Suppliers: China has a vast network of CNC machinery manufacturers, providing buyers with a wide range of options to choose from. This extensive supplier base allows buyers to find manufacturers that best meet their specific requirements.
3. Advanced Technology: Chinese CNC machinery manufacturers have significantly improved their technological capabilities over the years. Many companies in China now produce state-of-the-art CNC machinery with advanced features and superior quality.
Risks:
1. Quality Concerns: While the quality of CNC machinery manufactured in China has improved, there can still be variations in quality across different suppliers. Buyers need to carefully assess the reputation, certifications, and track record of potential manufacturers to ensure they meet the required quality standards.
2. Intellectual Property Risks: China has faced criticism in the past for intellectual property (IP) violations. There have been cases of counterfeit or copied CNC machinery originating from China. Buyers should be cautious to protect their IP and work with reputable manufacturers with strong IP protection measures.
3. Communication and Cultural Differences: Effective communication can sometimes be challenging due to language barriers and cultural differences. Buyers need to ensure that they can clearly convey their requirements and expectations to the manufacturer to avoid misunderstandings and potential issues.
Key Players:
Some of the prominent CNC machinery manufacturers in China include:
1. Shenyang Machine Tool Co., Ltd.
2. Jinan Bodor CNC Machine Co., Ltd.
3. Dalian Machine Tool Group Corporation
4. Taizhou Hitech NC Machine Tool Co., Ltd.
5. Beijing No.1 Machine Tool Plant
6. Jiangsu Dongfang Hydraulic Co., Ltd.
7. Jinan Firm CNC Equipment Co., Ltd.
These manufacturers have a good market reputation, offer a wide range of CNC machinery products, and have experience in serving international clients.
In summary, when sourcing CNC machinery manufacturers from China, buyers can benefit from the cost advantage, wide supplier base, and advanced technology. However, they should also be aware of the potential risks associated with quality, intellectual property, and communication. Engaging with reputable manufacturers will mitigate these risks and ensure a successful sourcing process.
How to find and select reliable cnc machinery manufacturers manufacturers in China,use google search manufacturers and suppliers
When looking for reliable CNC machinery manufacturers in China, it is essential to conduct thorough research and consider several factors. Here is a step-by-step guide on how to find and select reliable manufacturers using Google search:
1. Start by conducting a basic Google search using keywords like “reliable CNC machinery manufacturers in China” or “CNC machinery suppliers in China.” This will provide you with a list of potential manufacturers.
2. Go through the search results and visit the websites of different manufacturers. Look for information about their company history, production capacity, quality control processes, and certifications. Reliable manufacturers will often have well-developed websites that showcase their products and provide detailed information.
3. Check for customer reviews and feedback. Look for independent websites, forums, or platforms where customers share their experiences with the manufacturer. This will give you insights into the manufacturer’s reputation and customer satisfaction.
4. Verify the manufacturer’s credentials and certifications. Look for certifications such as ISO 9001:2015, CE, or any relevant quality management certifications. These certifications indicate that the manufacturer follows quality assurance processes and meets international standards.
5. Assess the manufacturer’s production capabilities. Look for information about their facilities, machinery, and technological capabilities. A reliable manufacturer should have modern machinery, well-equipped production facilities, and a skilled workforce capable of meeting your specific requirements.
6. Check for their exporting experience. Reliable manufacturers should have experience exporting their products to different countries. Look for affiliations with international trade organizations or previous partnerships with companies outside of China.
7. Contact the shortlisted manufacturers and request product catalogs, specifications, and quotations. By comparing the information you receive, you can evaluate their responsiveness, willingness to provide information, and attention to detail.
8. Consider visiting the manufacturer’s premises. If feasible, arrange a visit to evaluate their production facilities, quality control processes, and meet their team in person. This will help establish a stronger relationship and provide confidence about their capabilities.
9. Seek recommendations. Consult with industry professionals, sourcing agents, or other businesses that have experience working with CNC machinery manufacturers in China. Their insights and recommendations can help you narrow down your options and make an informed decision.
It is important to conduct due diligence when selecting CNC machinery manufacturers in China to ensure product quality, reliability, and long-term partnerships.
How to check cnc machinery manufacturers manufacturers website reliable,use google chrome SEOquake check if ranking in top 10M
To ensure the reliability of a CNC machinery manufacturer’s website, you can follow these steps using Google Chrome and the SEOquake extension:
1. Install SEOquake: Add the SEOquake extension to your Google Chrome browser. This tool provides valuable information about a website’s ranking and credibility.
2. Search for the manufacturer: Use a search engine to find the manufacturer’s website. Type in the relevant keywords like “CNC machinery manufacturer” followed by the company name.
3. Check the website’s ranking: Once on the search results page, look for the manufacturer’s website link and click on it. With SEOquake activated, you will see a toolbar at the top of the page displaying various metrics.
4. Analyze the Alexa Rank: On the SEOquake toolbar, focus on the “Alexa Rank” metric. Alexa Rank determines a website’s popularity and credibility. Ensure that the manufacturer’s website has a rank within the top 10 million. Avoid websites with a very high or no rank as they may be less reliable.
5. Inspect other SEOquake metrics: SEOquake provides additional metrics like Google Index, Pages Indexed, and Backlinks. Consider these metrics as well to evaluate the website’s reliability.
6. Explore the website: Check the website’s design, user interface, and content. Look for comprehensive information about the CNC machinery, their manufacturing process, certifications, and customer testimonials. A reliable manufacturer’s website should have clear and well-presented information.
7. Look for contact information: A trustworthy manufacturer should provide multiple methods of contact, such as phone numbers, email addresses, and physical address. Check if these details are readily available on their website.
8. Verify manufacturing certifications: Check if the manufacturer mentions any certifications on their website, such as ISO or CE. Reliable manufacturers often display their certifications to establish trustworthiness.
By following these steps, you can assess the reliability of a CNC machinery manufacturer’s website using Google Chrome with the assistance of the SEOquake extension. Remember to utilize these tools, metrics, and observations to make an informed decision before engaging with the manufacturer.
Top 10 cnc machinery manufacturers manufacturers in China with each 160 words introduce products,then use markdown create table compare
1. Jingdiao Technology Co., Ltd. specializes in the design and manufacturing of high-precision CNC machining centers, wire EDM machines, and injection molding machines. Their CNC machinery offers excellent precision, stability, and efficiency, making them ideal for industries such as aerospace, automotive, and electronic manufacturing.
2. Shenyang Machine Tool Co., Ltd. is a leading manufacturer of CNC machine tools, including turning centers, milling machines, and grinding machines. They offer a wide range of products suitable for different applications, such as heavy-duty machining, precision machining, and high-speed cutting.
3. DMG Mori Seiki Co., Ltd. is a global leader in the production of CNC machine tools, including milling machines, lathes, and multi-axis machines. Their products are known for their advanced technology, high-performance capabilities, and reliability, making them suitable for various industries, including aerospace, energy, and medical.
4. Chiron Group SE is a renowned manufacturer of CNC vertical machining centers and turnkey solutions for metal processing. Their machines are characterized by their high accuracy, speed, and flexibility, allowing for efficient and precise machining of various components.
5. Yawei Machine Tool Co., Ltd. specializes in the production of CNC press brakes, shearing machines, and laser cutting machines. Their CNC press brakes offer excellent bending precision and versatility, making them suitable for a wide range of sheet metal processing applications.
6. Jinan Bodor CNC Machine Co., Ltd. manufactures high-quality laser cutting machines, fiber laser marking machines, and laser welding machines. Their laser cutting machines provide high cutting speed, precision, and stability, effectively meeting the demands of industries like metal fabrication, shipbuilding, and automobile manufacturing.
7. Han’s Laser Technology Industry Group Co., Ltd. is a leading manufacturer of CNC laser cutting machines, welding machines, and engraving machines. Their CNC laser cutting machines are widely used in industries such as sheet metal processing, electronics, and signage making.
8. Ruijie Mechanical Equipment Co., Ltd. specializes in the production of CNC routers, laser cutting engraving machines, and plasma cutting machines. Their CNC routers offer high precision and efficiency, making them suitable for various industries including woodworking, advertising, and mold making.
9. Quick CNC Machine Co., Ltd. designs and manufactures CNC routers, plasma cutting machines, and laser cutting machines. Their CNC routers are known for their high precision, reliability, and user-friendly operation, making them ideal for industries such as woodworking, prototyping, and signage.
10. Shenzhen DNE Laser Equipment Co., Ltd. produces laser cutting machines, laser welding machines, and laser marking machines. Their laser cutting machines provide excellent cutting quality, speed, and precision, meeting the requirements of industries like metal fabrication, electrical appliances, and automotive manufacturing.
| Manufacturer | Products Offered | Key Features |
|——————————|————————————————|————————————————————————————————————————————————–|
| Jingdiao Technology Co., Ltd. | CNC machining centers, wire EDM machines, injection molding machines | Excellent precision, stability, efficiency |
| Shenyang Machine Tool Co., Ltd. | Turning centers, milling machines, grinding machines | Suitable for heavy-duty machining, precision machining, high-speed cutting |
| DMG Mori Seiki Co., Ltd. | Milling machines, lathes, multi-axis machines | Advanced technology, high-performance capabilities, reliability |
| Chiron Group SE | CNC vertical machining centers, turnkey solution | High accuracy, speed, flexibility |
| Yawei Machine Tool Co., Ltd. | CNC press brakes, shearing machines, laser cutting machines | Excellent bending precision, versatility |
| Jinan Bodor CNC Machine Co., Ltd. | Laser cutting machines, fiber laser marking machines, laser welding machines | High cutting speed, precision, stability |
| Han’s Laser Technology Industry Group Co., Ltd. | CNC laser cutting machines, welding machines, engraving machines | Widely used in sheet metal processing, electronics, signage making |
| Ruijie Mechanical Equipment Co., Ltd. | CNC routers, laser cutting engraving machines, plasma cutting machines | Ideal for woodworking, advertising, mold making |
| Quick CNC Machine Co., Ltd. | CNC routers, plasma cutting machines, laser cutting machines | High precision, reliability, user-friendly operation |
| Shenzhen DNE Laser Equipment Co., Ltd. | Laser cutting machines, laser welding machines, laser marking machines | Excellent cutting quality, speed, precision |
Background Research for cnc machinery manufacturers manufacturers Companies in China, use qcc.com archive.org importyeti.com
There are several CNC machinery manufacturers companies in China that can be explored for background research purposes. Two useful websites to gather information from are qcc.com and importyeti.com.
QCC.com is a Chinese business data search platform that provides comprehensive company information, including details about their registration, contact information, legal representative, shareholders, and financial data. It is helpful in researching the background of CNC machinery manufacturers companies in China, as it allows users to find important information about the companies, such as their establishment date, registered capital, and business scope. Additionally, QCC.com provides information about the company’s branches, subsidiaries, shareholders, and related companies, which is useful to understand the industry network and associations.
Importyeti.com is another valuable resource to explore. It is a platform that collects data from customs authorities, providing information about import and export activities of companies. By searching for CNC machinery manufacturers in China on this platform, one can get insights into their export history, including the volumes, destinations, and countries they are exporting to. This information can be helpful in understanding the company’s market reach and customer base.
In conducting background research, it is important to keep the description within 300 words. Utilizing platforms like qcc.com and importyeti.com assists in gathering essential information about CNC machinery manufacturers companies in China, such as their financial status, establishment history, and export activities. Such research helps to establish a basic understanding of the company’s background, enhancing the decision-making process and providing a solid foundation for further investigation if needed.
Leveraging Trade Shows and Expos for cnc machinery manufacturers Sourcing in China
Trade shows and expos can be a crucial platform for CNC machinery manufacturers sourcing in China to leverage. These events provide opportunities for manufacturers to connect with potential suppliers, gain industry insights, and showcase their products. In a limited 300-word response, here are some key ways manufacturers can benefit from these trade shows and expos:
1. Sourcing Opportunities: Trade shows and expos bring together a diverse range of suppliers, including CNC machinery manufacturers, under one roof. Manufacturers seeking suppliers for CNC machinery can explore multiple options, compare offerings, and negotiate deals face-to-face. This direct interaction allows for better evaluation of suppliers, their capabilities, and their products. It also facilitates building relationships, which can lead to long-term partnerships.
2. Industry Insights: Trade shows and expos offer a wealth of industry knowledge and expertise. Seminars, workshops, and presentations are often organized alongside the exhibition, providing insights on the latest trends, technologies, and developments in the CNC machinery industry. Manufacturers can gain valuable knowledge on the current and future market conditions, enabling them to make informed decisions regarding their sourcing strategies in China.
3. Product Showcasing: Exhibiting at trade shows and expos allows CNC machinery manufacturers to showcase their products and highlight their capabilities to potential buyers. Live demonstrations, product displays, and interactive sessions can attract the attention of interested buyers and generate leads. Manufacturers can use these platforms to build brand awareness and establish themselves as trusted suppliers in the industry.
4. Networking Opportunities: Trade shows and expos attract professionals from all sectors of the industry, including suppliers, buyers, distributors, and even competitors. Attending these events opens up networking opportunities for CNC machinery manufacturers to meet key players in the industry, exchange information and contacts, and form strategic partnerships. Building a strong network can enhance business opportunities and access to reliable suppliers in China.
5. Market Intelligence: By participating in trade shows and expos, CNC machinery manufacturers gain invaluable market intelligence. They can observe competitors’ product offerings, pricing strategies, and market positioning. This insight allows manufacturers to adapt their own sourcing and marketing strategies accordingly, ensuring their competitiveness in the market.
In conclusion, trade shows and expos provide CNC machinery manufacturers with sourcing opportunities, industry insights, product showcasing, networking opportunities, and market intelligence. Leveraging these events can immensely benefit manufacturers sourcing in China, enabling them to connect with reliable suppliers, stay updated with industry trends, and strengthen their market presence.
The Role of Agents and Sourcing Companies in Facilitating cnc machinery manufacturers Purchases from China
Agents and sourcing companies play a crucial role in facilitating CNC machinery manufacturers’ purchases from China. With their extensive knowledge of the local market and their network of suppliers, they simplify the buying process and ensure smooth transactions.
One of the main responsibilities of agents and sourcing companies is to identify suitable suppliers for their clients. They conduct thorough research, evaluate potential suppliers based on factors like quality, price, and reliability, and select the most appropriate ones. This saves CNC machinery manufacturers valuable time and effort in finding reliable suppliers themselves.
Agents and sourcing companies also act as a bridge between CNC machinery manufacturers and Chinese suppliers. They facilitate communication and negotiations, ensuring that the manufacturers’ requirements are clearly understood and met. This helps prevent misunderstandings and promotes a smoother purchasing process.
Another crucial role of agents and sourcing companies is quality control. They inspect the products before shipment to ensure that they meet the manufacturers’ specifications and standards. This reduces the risk of receiving defective or subpar products and gives the manufacturers peace of mind.
Furthermore, agents and sourcing companies handle logistics and shipping arrangements. They coordinate with freight forwarders and customs agents to ensure that the purchased products are delivered promptly and without any customs or regulatory issues. This saves CNC machinery manufacturers the hassle of dealing with complex international shipping procedures.
Lastly, agents and sourcing companies also provide valuable support in negotiating favorable terms and pricing. They leverage their knowledge of the local market and their negotiation skills to secure the best possible deals for their clients. This helps CNC machinery manufacturers save costs and increase their competitiveness in the global market.
In summary, agents and sourcing companies play a vital role in facilitating CNC machinery manufacturers’ purchases from China. They simplify the buying process, identify suitable suppliers, ensure quality control, handle logistics, and negotiate favorable terms. Their expertise and services contribute to a more efficient and successful sourcing experience for CNC machinery manufacturers.
Price Cost Research for cnc machinery manufacturers manufacturers Companies in China, use temu.com and 1688.com
When conducting price cost research for CNC machinery manufacturers in China, two popular platforms to consider are temu.com and 1688.com. These platforms provide a wide range of information regarding manufacturers and their respective pricing, allowing buyers to make informed decisions.
Temu.com, a B2B platform, specializes in connecting international buyers with Chinese manufacturers. By exploring the website, users can easily find a variety of CNC machinery manufacturers and obtain information such as price ranges, product specifications, and contact details. The platform also allows users to directly communicate with manufacturers to negotiate prices and discuss specific requirements. Temu.com offers a user-friendly interface and filters, making it convenient to search for CNC machinery manufacturers based on specific needs.
1688.com, on the other hand, is a leading Chinese B2B platform that caters primarily to domestic buyers. While the website is primarily in Mandarin, it offers an extensive range of CNC machinery manufacturers and product options. The platform enables users to search for manufacturers based on various factors, including price range, location, and product specialization. Additionally, 1688.com provides detailed product descriptions, customer reviews, and supplier ratings, aiding in the decision-making process. Users also have the option to contact the manufacturers directly through the platform or through other means to inquire about pricing and negotiate deals.
When utilizing these platforms, it is advisable to keep the following tips in mind:
1. Clearly define requirements: Before starting the search process, make sure to have a clear understanding of the specific CNC machinery requirements. This will help narrow down the search and find suitable manufacturers more efficiently.
2. Compare prices and offerings: Explore various manufacturers on both platforms to compare prices, quality, after-sales service, and additional factors that are important to the buying decision.
3. Communicate with manufacturers: Initiate conversations with selected manufacturers to negotiate prices, discuss customization options, and clarify any doubts or questions.
4. Verify manufacturer credentials: Ensure that the selected manufacturers have appropriate certifications and credentials that adhere to industry standards.
Overall, using temu.com and 1688.com can provide valuable insights and access to a wide range of CNC machinery manufacturers in China. By following the suggested tips, buyers can make well-informed decisions regarding pricing and other related factors.
Shipping Cost for cnc machinery manufacturers import from China
The shipping cost for CNC machinery manufacturers importing from China can vary depending on various factors. These factors include the size and weight of the machinery, the delivery distance, the shipping method chosen, and any additional services required.
There are primarily two main shipping methods used for importing machinery from China: sea freight and air freight. Sea freight is usually the more economical option for shipping large and heavy machinery as it offers lower shipping rates compared to air freight. However, it also has a longer transit time, typically ranging from a few weeks to several months, depending on the destination.
Air freight, on the other hand, is faster but more expensive. It is suitable for urgent shipments or when the machinery is relatively small and lightweight. The cost for air freight is usually calculated based on a combination of weight and volume, whichever is higher.
Apart from the shipping method, additional costs that manufacturers need to consider include customs duties, import taxes, and any import documentation fees. These costs can vary depending on the country of import, the value of the machinery, and any applicable trade agreements or regulations.
To get an accurate estimate of the shipping cost, manufacturers need to provide details about the dimensions and weight of the machinery, the desired delivery location, and any specific shipping requirements. They can then request quotes from shipping companies or freight forwarders who specialize in machinery transportation.
In summary, the shipping cost for importing CNC machinery from China involves considering factors such as the size, weight, shipping method, and additional services required. Manufacturers should gather all necessary information and obtain quotes from reliable shipping providers to ensure a cost-effective and efficient import process.
Compare China and Other cnc machinery manufacturers Markets: Products Quality and Price,Visible and Hidden Costs
China is widely recognized as one of the leading manufacturers of CNC machinery globally. However, it is important to weigh the products’ quality and price while considering both visible and hidden costs when comparing the Chinese market with other CNC machinery manufacturers.
In terms of product quality, China has made significant advancements over the years. Many Chinese manufacturers produce CNC machinery that meets international standards, with some even offering high precision and advanced features. However, it is essential to conduct thorough research and select reputable manufacturers to ensure quality assurance.
Price is a significant advantage for China when compared to other CNC machinery manufacturers. China’s extensive supply chain and large production volumes allow for economies of scale, resulting in lower production costs. As a result, Chinese CNC machinery can often be more affordable compared to products from other countries. However, the price should not be the sole determining factor when considering CNC machinery, as quality and reliability are crucial in these capital-intensive investments.
Visible costs, such as the initial purchase price, are relatively transparent and easy to compare. Chinese CNC machinery manufacturers often offer competitive prices, which can be appealing. However, it is essential to consider hidden costs such as shipping, customs duties, and taxes when importing machinery from China. These costs can significantly impact the overall price, depending on the destination country.
Furthermore, after-sales service and support should be considered as a hidden cost. While some Chinese manufacturers provide excellent service, language barriers and distance can sometimes pose challenges for overseas customers. It is essential to determine the level of support offered by manufacturers, including spare parts availability and technical assistance, to avoid unexpected costs and delays in case of breakdowns or maintenance needs.
In conclusion, China’s CNC machinery market offers competitive prices and improved product quality. However, thorough research and due diligence are necessary to choose reputable manufacturers and consider potential visible and hidden costs. Ultimately, buyers should evaluate their specific requirements, product specifications, and long-term investment plans to make an informed decision about CNC machinery procurement.
Understanding Pricing and Payment Terms for cnc machinery manufacturers: A Comparative Guide to Get the Best Deal
When purchasing CNC machinery, understanding the pricing and payment terms is crucial to ensure you get the best deal possible. This comparative guide aims to provide an overview of the key factors to consider and tips to negotiate favorable terms.
1. Price Comparison: Start by researching multiple CNC machinery manufacturers to compare prices. Consider factors such as machine capabilities, quality, warranty, and after-sales support. Obtaining quotes from several manufacturers will give you a better understanding of market prices and help you negotiate.
2. Customization Costs: CNC machinery can be customized to meet specific requirements. Be aware that customization may increase the price. Understand the customization options available and the associated costs. Compare these costs among different manufacturers to ensure you get the best price for the desired features.
3. Payment Terms: Manufacturers may offer different payment terms. Common options include full upfront payment, partial upfront payment with the remaining amount upon delivery, or financing options. Consider your cash flow and financial capabilities when choosing the most suitable payment terms. Negotiating flexible payment terms may be possible, especially for larger orders.
4. Warranty and After-sales Support: Understand the warranty offered by the manufacturer. A longer warranty period can provide peace of mind and potentially save on future repair costs. Additionally, inquire about after-sales support, including technical assistance, spare parts availability, and maintenance services. All these factors contribute to the overall value and should be considered when comparing prices.
5. Bargaining Room: Don’t hesitate to negotiate the price and payment terms. Engage in discussions with manufacturers to find common ground. Highlight your potential as a repeat customer or consider placing a larger order to strengthen your negotiation position. Emphasize factors such as long-term partnership, potential referrals, or global exposure if applicable.
6. Consider Value rather than merely price: While price is an essential consideration, don’t solely focus on it. Evaluate the overall value provided by the manufacturer, including product quality, service reputation, customer reviews, and delivery time frame. A lower-priced machine may end up costing more if it lacks reliability or requires frequent repairs.
In conclusion, when understanding pricing and payment terms for CNC machinery manufacturers, comparing prices, considering customized options, exploring payment terms, warranty, after-sales support, bargaining, and evaluating overall value are essential. This guide serves as a starting point to help you get the best deal possible.
Chinese Regulations and Industry Standards Certifications for cnc machinery manufacturers,Import Regulations and Customs for cnc machinery manufacturers from China
Chinese Regulations and Industry Standards Certifications for CNC Machinery Manufacturers:
In China, CNC machinery manufacturers must adhere to various regulations and industry standards to ensure their products meet quality and safety requirements. One of the key regulations is the “China Compulsory Certification” (CCC) which is administered by the Certification and Accreditation Administration of China (CNCA). This certification is mandatory for a wide range of products, including CNC machinery, and demonstrates compliance with national safety and quality standards. Manufacturers must undergo testing and evaluation to obtain the CCC mark, indicating their products meet the specified requirements.
Additionally, CNC machinery manufacturers need to comply with industry-specific standards. The “National Standard of the People’s Republic of China – CNC Machine Tools” provides guidelines related to safety performance, technical characteristics, and testing methods for CNC machinery. Manufacturers must ensure their products adhere to these standards to ensure product quality and compatibility with other related equipment.
Import Regulations and Customs for CNC Machinery Manufacturers from China:
Importing CNC machinery from China requires compliance with import regulations and customs procedures of the destination country. It is crucial for CNC machinery manufacturers to understand these requirements to facilitate smooth importation. Some key considerations include:
1. Import Duties and Taxes: Importers should be aware of the applicable import duties and taxes levied by their country of importation. These costs should be factored into the overall pricing strategy.
2. Customs Documentation: Accurate and complete customs documentation is essential for efficient customs clearance. This includes commercial invoices, packing lists, bills of lading, and any other relevant documents required by the destination country’s customs authority.
3. Product Compliance: The imported CNC machinery must comply with the safety and quality standards of the destination country. Importers should ensure that the machinery meets the necessary certifications, such as the CCC mark, to avoid any issues during customs inspection.
4. Customs Tariff Classification: Importers must determine the correct customs tariff classification of the CNC machinery. This classification helps determine the applicable import duties and helps customs authorities assess the product’s eligibility for importation.
To ensure a smooth import process, CNC machinery manufacturers from China should consult with import agents or freight forwarders who have expertise in handling customs procedures and regulations. These professionals can provide guidance on the specific requirements of the destination country, helping manufacturers navigate the complexities of international trade.
Sustainability and Environmental Considerations in cnc machinery manufacturers Manufacturing
In recent years, sustainability and environmental considerations have become an increasingly important aspect in the manufacturing industry, including CNC machinery manufacturers. There is a growing recognition of the need to prioritize environmental responsibility and reduce the impact of manufacturing processes on the planet.
One significant way in which CNC machinery manufacturers are addressing sustainability is by adopting more energy-efficient practices. This includes the use of advanced technologies, such as high-efficiency motors and smart energy management systems, which help to reduce energy consumption. By optimizing energy usage, manufacturers can not only lower their carbon footprint but also achieve considerable cost savings.
Moreover, many CNC machinery manufacturers are adopting environmentally friendly materials and production techniques. This involves utilizing materials with lower carbon footprints, such as recycled or sustainable materials, and reducing the use of hazardous substances. Additionally, manufacturers can develop closed-loop systems that enable the recycling, reuse, or recovery of materials, thus minimizing waste generation and promoting a circular economy.
Furthermore, the implementation of lean manufacturing principles can significantly contribute to sustainability efforts. By reducing waste, optimizing production processes, and improving overall efficiency, CNC machinery manufacturers can minimize their environmental impact. This includes eliminating unnecessary steps in production, reducing scrap rates, and improving product quality and durability.
The sustainability of CNC machinery manufacturers is not limited to their production processes. It also encompasses packaging and logistics. Adopting eco-friendly packaging materials and optimizing transportation routes helps to reduce emissions and waste throughout the supply chain, contributing to overall sustainability goals.
Lastly, manufacturers are increasingly taking responsibility for the end-of-life of their products. This involves designing machinery with easily recyclable components and providing avenues for proper disposal or recycling. By considering the entire lifecycle of their products, CNC machinery manufacturers can reduce environmental impacts and adopt a more sustainable approach.
In conclusion, sustainability and environmental considerations are crucial for CNC machinery manufacturers. By adopting energy-efficient practices, using eco-friendly materials, implementing lean manufacturing principles, optimizing packaging and logistics, and taking responsibility for end-of-life processes, manufacturers can reduce their environmental impact and contribute to a more sustainable future.
List The Evolution history of “cnc machinery manufacturers”
CNC machinery manufacturers have played a crucial role in the evolution of the manufacturing industry over the years. Here is a concise overview of their evolution history:
1. Early Origins: The concept of numerical control (NC) originated in the mid-20th century, where early machines were controlled manually using punched tape. In the 1950s, the aerospace and automotive industries began to adopt these machines for precision and repetitive tasks.
2. Computer Aided Manufacturing (CAM): In the 1960s, the integration of computers into NC machines led to the birth of Computer Aided Manufacturing (CAM). This advancement allowed for the automation of machine tasks, reducing human error and increasing accuracy.
3. Introduction of CNC: The 1970s marked the transition from NC to Computer Numerical Control (CNC). CNC technology utilized computer systems to control various machine functions, including tool movement, spindle speed, and feed rate. This development dramatically improved precision and productivity.
4. Machining Center Innovations: In the 1980s, CNC machinery manufacturers introduced machining centers that combined several machining operations into one unit. This innovation reduced the need for multiple machines, increased efficiency, and facilitated complex part manufacturing.
5. Integration of CAD/CAM: With the rise of Computer Aided Design (CAD) and CAM systems, CNC machinery manufacturers began integrating these technologies into their machines in the 1990s. This amalgamation allowed for seamless communication between design and manufacturing, enabling faster production and easier prototyping.
6. High-Speed Machining: Advancements in control systems and cutting tools introduced high-speed machining capabilities in the early 2000s. CNC machinery manufacturers implemented faster tool changes, improved spindle speeds, and enhanced control algorithms, enabling rapid material removal and reduced cycle times.
7. Automation and Robotics: In recent years, CNC machinery manufacturers have focused on incorporating automation and robotics into their systems. This integration has led to the development of flexible manufacturing cells and lights-out manufacturing, where machines can operate without human intervention, maximizing productivity and reducing labor costs.
Today, CNC machinery manufacturers continue to push the boundaries of technology. They are exploring concepts like artificial intelligence, internet of things (IoT), and additive manufacturing to further enhance the capabilities and efficiency of their machines. As the manufacturing industry evolves, CNC machinery manufacturers remain at the forefront, driving innovation and revolutionizing production processes.
The Evolution and Market Trends in cnc machinery manufacturers Industry
The CNC machinery manufacturers industry has evolved significantly over the years, keeping pace with technological advancements and market trends. The industry experienced a major shift with the introduction of Computer Numerical Control (CNC) technology, which revolutionized the manufacturing process. This technology enabled manufacturers to automate various tasks, resulting in increased productivity and precision.
One of the most prominent trends in the industry is the integration of advanced technologies like Artificial Intelligence (AI) and Internet of Things (IoT) into CNC machinery. This integration allows for real-time monitoring and control, predictive maintenance, and data analytics, leading to optimized performance and reduced downtime. Manufacturers are constantly striving to incorporate these technologies to stay competitive in the market.
Another trend in the CNC machinery manufacturers industry is the development of multi-axis machines. These machines offer increased flexibility and versatility, allowing manufacturers to produce complex and intricate parts with ease. Additionally, advancements in materials and cutting technologies have led to improved cutting speeds and quality, further enhancing the capabilities of CNC machinery.
The market for CNC machinery has also witnessed significant growth over the years. Increased demand for customized and complex components, particularly in sectors such as aerospace, automotive, and electronics, has driven the market expansion. Moreover, the adoption of CNC machinery by small and medium-sized enterprises (SMEs) has increased, as machines have become more affordable and user-friendly.
Another market trend is the rise of additive manufacturing, commonly known as 3D printing. While CNC machinery has traditionally been used for subtractive manufacturing processes, such as cutting and shaping, the advent of 3D printing has provided manufacturers with new opportunities. Many CNC machinery manufacturers are now offering hybrid machines that combine both additive and subtractive capabilities, catering to the growing demand for 3D-printed parts.
In conclusion, the CNC machinery manufacturers industry has witnessed significant evolution and market trends. Integration of advanced technologies, development of multi-axis machines, and the rise of additive manufacturing are some of the key factors that have shaped the industry. With the continued advancements in technology and increasing market demand, the CNC machinery manufacturers industry is expected to experience further growth in the future.
Custom Private Labeling and Branding Opportunities with Chinese cnc machinery manufacturers Manufacturers
Chinese cnc machinery manufacturers offer great opportunities for custom private labeling and branding. These manufacturers have extensive experience and expertise in producing high-quality cnc machinery, making them ideal partners for businesses looking to establish their own brand in the market.
One of the key advantages of working with Chinese manufacturers is their ability to provide custom private labeling. This means that businesses can have their own brand name, logo, and design incorporated into the products they order. This helps to create a unique identity for the brand, making it easily recognizable in the market. By having their own custom branding, businesses can effectively differentiate themselves from competitors and build customer loyalty.
Furthermore, Chinese manufacturers also offer custom branding opportunities in terms of product packaging. Businesses can work closely with the manufacturers to design packaging that aligns with their brand design and ethos. Custom packaging not only enhances brand recognition but also improves the perceived value of the products in the eyes of customers.
In addition, collaborating with Chinese cnc machinery manufacturers provides businesses with the advantage of cost-effectiveness. Chinese manufacturers are known for their competitive pricing due to their access to low-cost labor and resources. This allows businesses to obtain high-quality custom-branded products at a fraction of the cost compared to manufacturing domestically.
Furthermore, many Chinese manufacturers are experienced in exporting products to international markets. They are well-versed in complying with different certification requirements and industry standards, ensuring that the custom-branded products meet all necessary regulations in the target market. This saves businesses from the hassle and potential legal issues that may arise from non-compliant products.
To conclude, working with Chinese cnc machinery manufacturers presents excellent opportunities for custom private labeling and branding. By collaborating with these manufacturers, businesses can establish their own unique brand identity, increase customer loyalty, and avail cost-effective solutions, all while ensuring compliance with industry standards.
Tips for Procurement and Considerations when Purchasing cnc machinery manufacturers
When it comes to purchasing CNC machinery from manufacturers, there are several factors and considerations that should be taken into account. These include machine specifications, reliability, manufacturer reputation, after-sales service, and costs.
Firstly, it is important to thoroughly research and compare the specifications of different CNC machinery models. Consider factors such as the machine’s capabilities, such as the maximum workload it can handle, the number of axes, and the precision it can achieve. Understanding your specific needs and requirements will help determine which machine is the best fit for your business.
Reliability is another crucial aspect to consider. Look for a manufacturer with a proven track record of producing reliable and durable machinery. Read customer reviews and testimonials to gauge the machine’s performance and reliability over time.
Manufacturer reputation plays a significant role in determining the quality of the machinery and service. Choose a reputable manufacturer that has been in the industry for a while and has a positive reputation. This ensures that you are purchasing from a reliable source that is likely to deliver on their promises.
After-sales service is equally important. Find a manufacturer that provides comprehensive support, including technical assistance, maintenance, and repair services. Ideally, opt for a manufacturer that has a local service center or authorized dealers in your region to ensure quick and efficient support whenever needed.
Lastly, cost considerations are a crucial factor in any procurement decision. While price should not be the sole determining factor, it is essential to balance the cost with the machine’s quality and capabilities. Consider the long-term return on investment (ROI) of the machinery and evaluate whether it aligns with your budget and business goals.
In conclusion, when purchasing CNC machinery from manufacturers, it is essential to thoroughly research and consider machine specifications, reliability, manufacturer reputation, after-sales service, and costs. By taking these factors into consideration, you can make an informed decision and select the most suitable CNC machinery for your business needs.
FAQs on Sourcing and Manufacturing cnc machinery manufacturers in China
Q: Why should I source CNC machinery from China?
A: China is a leading manufacturer of CNC machinery globally due to its competitive prices, extensive manufacturing infrastructure, and skilled labor force. Chinese manufacturers offer a wide range of options and customization capabilities, making it a cost-effective choice for many businesses.
Q: How can I find reliable CNC machinery manufacturers in China?
A: There are multiple ways to find reliable manufacturers in China. Online platforms like Alibaba and GlobalSources provide a vast database of suppliers to choose from. It is crucial to thoroughly research the manufacturer by checking their company profile, product range, customer reviews, and certifications. Engaging with manufacturers at trade shows and exhibitions can also provide an opportunity to meet them in person and establish a trustworthy relationship.
Q: What factors should I consider before selecting a CNC machinery manufacturer?
A: When selecting a CNC machinery manufacturer, factors to consider include their reputation, industry experience, manufacturing capabilities, quality control processes, certifications, price competitiveness, and after-sales service. It is advisable to request samples or visit the manufacturer’s premises to assess their facilities and ensure they meet your requirements.
Q: How can I ensure the quality of CNC machinery manufactured in China?
A: To ensure quality, reputable Chinese manufacturers often have international certifications such as ISO and CE. Prioritize choosing manufacturers that implement strict quality control processes, conduct inspections at various production stages, and have a well-established testing facility. Requesting samples, product specifications, and detailed product warranties will also help assess the manufacturer’s commitment to ensuring quality.
Q: How do I handle communication and language barriers with Chinese manufacturers?
A: Communication can be challenging but can be overcome through various means. Many Chinese manufacturers have English-speaking sales representatives or hire interpreters to assist in the negotiation process. Clarify all specifications, technical requirements, and terms of the agreement in writing to minimize misunderstandings. Using visual aids like drawings or diagrams can also aid in conveying information accurately.
Q: What about shipping and logistics?
A: Chinese manufacturers often have experience with international shipping and can provide assistance with customs documentation and shipping arrangements. They may have existing relationships with shipping companies and can offer competitive rates. Alternatively, you can work with freight forwarders to handle the logistics, ensuring your machinery reaches its destination smoothly.
In conclusion, sourcing CNC machinery from China offers cost-effective options, but due diligence in vetting manufacturers is essential. Consider reputation, experience, quality control measures, certifications, price, and after-sales service when selecting a manufacturer. Effective communication and understanding shipping and logistics processes will contribute to a successful sourcing experience.
Why contact sourcifychina.com get free quota from reliable cnc machinery manufacturers suppliers?
Sourcifychina.com offers a unique opportunity to obtain free quota from reliable CNC machinery manufacturers and suppliers for several reasons.
Firstly, Sourcifychina.com has established strong long-term relationships with a network of reputable CNC machinery manufacturers and suppliers in China. These manufacturers and suppliers have been thoroughly vetted and selected based on their track record of quality products, reliable production capabilities, and adherence to international standards.
Secondly, Sourcifychina.com acts as a trusted intermediary between the buyers and manufacturers/suppliers. By leveraging their extensive industry knowledge and expertise, Sourcifychina.com ensures seamless communication and negotiation process. They assist in facilitating direct contact with the CNC machinery manufacturers, aiding in the exchange of information, and addressing any concerns that may arise during the procurement process.
Thirdly, Sourcifychina.com operates on a commission basis whereby they receive a percentage of the total order value from the manufacturers/suppliers. This commission-based model enables Sourcifychina.com to offer their customers a free quota without any additional charges. By bearing the commission fees, Sourcifychina.com aims to build strong client relationships and contribute to their clients’ success.
Lastly, Sourcifychina.com understands the importance of easing the financial burden on businesses. By providing a free quota, they enable potential buyers to assess the cost and feasibility of their CNC machinery requirements without any upfront expenses. This allows businesses to make informed decisions before committing to larger orders and investments.
In summary, Sourcifychina.com offers a free quota from reliable CNC machinery manufacturers and suppliers as a result of their extensive network, trusted intermediary services, commission-based model, and commitment to supporting businesses in making well-informed purchasing decisions without financial constraints.