Introduce about cnc machining parts guide,Qulity,Cost,Supplier,Certification,Market,Tips,FAQ
CNC machining parts guide:
CNC machining, also known as computer numerical control machining, is a manufacturing process that utilizes computerized controls to operate machine tools. It involves the removal of material from a workpiece to create a desired shape and size. CNC machining is widely used in various industries, including aerospace, automotive, medical, and electronics.
Quality:
When it comes to CNC machining parts, quality is of utmost importance. High-quality parts ensure functionality, reliability, and durability. To ensure the quality of CNC machining parts, it is crucial to work with experienced and reputable manufacturers or suppliers who have a proven track record in delivering precision components.
Cost:
The cost of CNC machining parts can vary depending on various factors such as complexity, material, quantity, and turnaround time. While CNC machining can offer cost-effective solutions for producing complex parts, it is important to consider the upfront investment in machinery and programming. However, the precision, efficiency, and repeatability of CNC machining can often outweigh the initial costs.
Supplier:
Choosing the right supplier for CNC machining parts is essential. Look for suppliers with expertise in your industry and a strong reputation for delivering high-quality components on time. It is beneficial to work with a supplier who offers comprehensive manufacturing capabilities, including design assistance, prototyping, and secondary operations.
Certification:
ISO certification is a crucial factor when selecting a supplier for CNC machining parts. ISO 9001 certification ensures adherence to international quality standards, providing assurance that the supplier has established robust quality management systems.
Market:
The market for CNC machining parts is rapidly expanding due to its numerous advantages, such as high precision, efficiency, and flexibility. The demand for CNC machining parts is driven by industries requiring complex and customized components, including aerospace, automotive, medical, and electronics sectors.
Tips:
– Clearly define your requirements and specifications before approaching a supplier to ensure a smooth production process.
– Consider material selection carefully, taking into account desired characteristics, such as strength, durability, and heat resistance.
– Optimize designs to leverage the capabilities of CNC machining, reducing complexity and minimizing costs.
– Request samples or prototypes to evaluate the supplier’s quality, performance, and compatibility with your application.
FAQ:
Q: What materials can be used for CNC machining parts?
A: CNC machining can work with a wide range of materials, including metals (aluminum, steel, titanium) and plastics (ABS, nylon, PEEK).
Q: What is the typical turnaround time for CNC machining parts?
A: Turnaround time can vary depending on the complexity and quantity of parts. Simple parts may be manufactured in days, while more complex projects can take weeks.
Q: Can CNC machining be used for both prototyping and production?
A: Yes, CNC machining is suitable for both prototype development and large-scale production runs.
In conclusion, CNC machining parts offer high-quality, precise, and cost-effective solutions for industries requiring complex and customized components. By carefully selecting reputable suppliers, considering materials and certifications, and optimizing designs, you can ensure the successful production of CNC machining parts for your specific applications.
Types of cnc machining parts
CNC (Computer Numerical Control) machining is a manufacturing process that utilizes computerized controls to operate and manipulate machine tools. It is commonly used in industries such as automotive, aerospace, electronics, and medical equipment manufacturing. CNC machining can produce a wide variety of parts with high precision and accuracy. Here are some common types of CNC machining parts:
1. Prototypes: CNC machining is often used to create prototypes of new products. It allows for quick and accurate production of parts for testing and evaluation before mass production.
2. Mechanical Components: CNC machining can produce a range of mechanical components, such as gears, shafts, couplings, and bearings. These components are essential for the functioning of various machines and equipment.
3. Medical Equipment: CNC machining is extensively used in the manufacturing of medical equipment, including surgical instruments, implants, and prosthetics. These parts require precise dimensions and surface finishes, which CNC machining can provide.
4. Aerospace Components: CNC machining is crucial in the aerospace industry for the production of complex components, such as turbine blades, engine housings, and aircraft structural parts. These parts must adhere to strict tolerances and material specifications to ensure safety and performance.
5. Electronic Enclosures: CNC machining is used to make enclosures for electronic devices like computers, smartphones, and audio/video equipment. The process allows for precise cutting, drilling, and shaping of the enclosure to accommodate various components and ensure proper airflow.
6. Automotive Parts: CNC machining plays a significant role in manufacturing automotive parts, such as engine components, transmission parts, and brake components. The process ensures consistent quality, tight tolerances, and the ability to produce intricate designs for improved performance.
7. Tooling and Fixtures: CNC machining is used to produce tooling and fixtures required for manufacturing processes. These tools and fixtures are necessary to hold and position workpieces accurately during various operations, such as cutting, drilling, and assembly.
8. Customized Parts: CNC machining enables the production of customized parts tailored to specific requirements. This includes unique designs, sizes, and materials that may not be available through standard manufacturing methods.
In conclusion, CNC machining is a versatile manufacturing process capable of producing a wide range of parts across various industries. Its precise control, accuracy, and ability to work with various materials make it an ideal choice for creating complex and customized components.
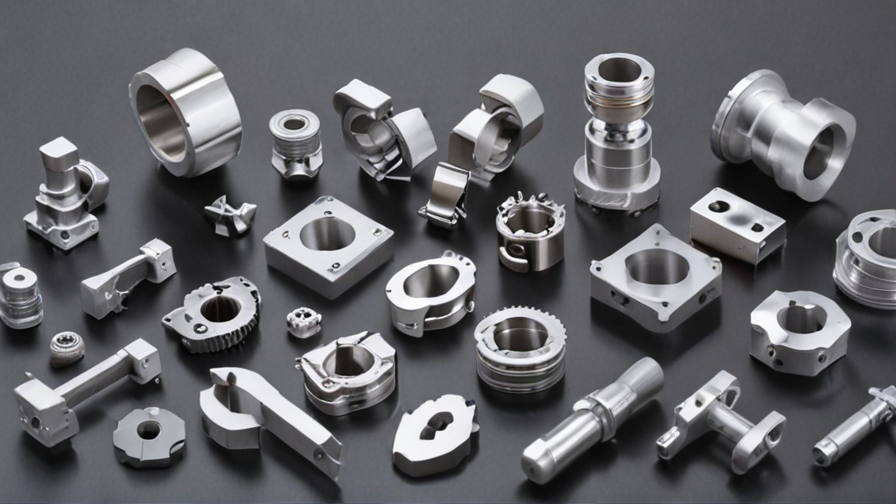
Pros and Cons of Using cnc machining parts
CNC machining parts, which stands for Computer Numerical Control, offer a range of benefits and disadvantages:
Pros of Using CNC Machining Parts:
1. Precision: CNC machines operate with exceptional accuracy, ensuring high-quality parts are produced consistently. They can achieve tolerances as low as 0.001 inches, resulting in precise and reliable components.
2. Efficiency: CNC machines automate the manufacturing process, enabling faster production times and increased productivity. They can work continuously without breaks, reducing the overall time required to manufacture parts.
3. Flexibility: CNC machining can accommodate a wide variety of materials, including metals, plastics, wood, and composites. It can also create complex designs and intricate shapes that would be challenging or impossible to achieve with manual machining.
4. Replicability: CNC machines can replicate parts with exact precision, ensuring consistent quality across multiple production runs. This is particularly beneficial in industries requiring identical or interchangeable components.
5. Reduced labor costs: CNC machining reduces the need for manual labor, minimizing human error and reducing costs associated with operating and training a workforce. This makes it a cost-effective manufacturing solution.
Cons of Using CNC Machining Parts:
1. Initial cost: CNC machines are relatively expensive to purchase and set up. The machinery, software, and infrastructure required for CNC machining can be a significant investment, particularly for small businesses or startups.
2. Maintenance and repair: CNC machines require regular maintenance and occasional repairs to keep them operating at optimal levels. This can result in additional costs, especially if specialized technicians or spare parts are needed.
3. Programming complexity: CNC machines require programming to execute specific instructions. The programming language used, such as G-code, can be complex and time-consuming to learn, requiring skilled operators or programmers to operate the machines effectively.
4. Limited flexibility: While CNC machines offer high flexibility in terms of material choices and design complexity, they may not be suitable for very small or oversized parts. The size limitations of the machine’s workspace may restrict the size and dimensions of the components that can be produced.
5. Lack of human touch: CNC machining removes the artistry and creativity associated with manual machining, which some industries may value. For crafts requiring intricate handwork, CNC machining may not offer the same aesthetic appeal.
In summary, CNC machining parts offer exceptional precision, efficiency, flexibility, replicability, and cost savings. However, the initial cost, maintenance requirements, programming complexity, limited flexibility, and potential lack of human touch are important factors to consider when deciding to use CNC machining.
cnc machining parts Reference Specifications (varies for different product)
CNC machining involves the creation of parts and components using computer numerical control technology. The manufacturing process relies on specifications that guide the machining operations and ensure the desired outcome is achieved. While the reference specifications can vary depending on the specific product being manufactured, there are some common elements that are often included.
Firstly, the reference specifications outline the dimensions and tolerances that the parts need to meet. This includes specifications for length, width, height, and other relevant measurements. Tolerances, which refer to the allowable deviation from the ideal dimensions, are also specified to ensure that the parts are produced with high accuracy.
The material requirements are another important aspect of the reference specifications. The type of material to be used is specified, along with any specific properties that it must possess, such as strength, corrosion resistance, or conductivity. Additionally, surface finish requirements, such as smoothness or hardness, may be specified to ensure the desired functionality and aesthetics of the finished parts.
The reference specifications may also include information on the required mechanical properties of the parts. This can include specifications for hardness, tensile strength, yield strength, and other important characteristics that determine the part’s structural integrity and suitability for its intended application.
In some cases, additional specifications may be included, depending on the product. For example, if the parts are meant to be assembled together, reference specifications may include information on the required mating features or tolerances to ensure proper fit and alignment. If the parts are subjected to specific environmental conditions, such as extreme temperature or pressure, the reference specifications may outline the necessary resistance or endurance requirements.
Overall, reference specifications are crucial in CNC machining as they define the requirements for the manufacturing process and guarantee the quality and functionality of the final parts. By adhering to these specifications, manufacturers can ensure consistency, precision, and the ability to meet customers’ specific needs.
Applications of cnc machining parts
CNC (Computer Numerical Control) machining parts are essential components in various industries and have numerous applications due to their precision, versatility, and efficiency. Here are some applications where CNC machining parts play a crucial role:
1. Automotive Industry: CNC machining parts are widely used in the automotive industry to manufacture components like engine parts, transmission parts, brake systems, suspension parts, and electrical systems. These parts are machined to strict tolerances, ensuring smooth operation and high performance.
2. Aerospace Industry: CNC machining parts are extensively used in the aerospace industry for applications such as manufacturing aircraft engine components, landing gears, wing structures, turbine blades, and various interior components. The precision and reliability of these parts are critical to ensure flight safety.
3. Medical Equipment: The medical industry heavily relies on CNC machining parts for manufacturing complex components with high accuracy. These parts are used for surgical equipment, prosthetics, orthotics, implants, and medical instruments, ensuring precise operation and patient safety.
4. Electronics Industry: CNC machining parts are integral in the manufacturing of electronic devices like smartphones, tablets, computers, and consumer electronics. These parts are vital for the production of circuit boards, connectors, housings, heatsinks, and various other electronic components.
5. Industrial Machinery: CNC machining parts are extensively used in the production of industrial machinery, including manufacturing equipment, automated systems, robotics, and assembly lines. These parts often require complex geometries, high tolerances, and superior durability to withstand rigorous industrial environments.
6. Energy Sector: CNC machining parts are used in the energy sector for producing components used in power generation, including wind turbines, solar panels, hydroelectric infrastructure, and oil extraction equipment. These parts need to be highly precise and durable for efficient and reliable energy production.
7. Defense and Military: The defense industry extensively utilizes CNC machining parts for manufacturing military vehicles, weapons, missile systems, communication equipment, and other defense applications. The precision, strength, and reliability of these parts are crucial for mission-critical operations.
8. Consumer Products: CNC machining parts are used in various consumer products like appliances, furniture, sporting goods, and toys. These parts are responsible for providing structural integrity, smooth functionality, and aesthetic appeal to the end products.
In conclusion, CNC machining parts find applications across a wide range of industries due to their precision, versatility, and durability. Their usage in automotive, aerospace, medical, electronics, industrial machinery, energy, defense, military, and consumer products showcases their essential role in modern manufacturing processes.
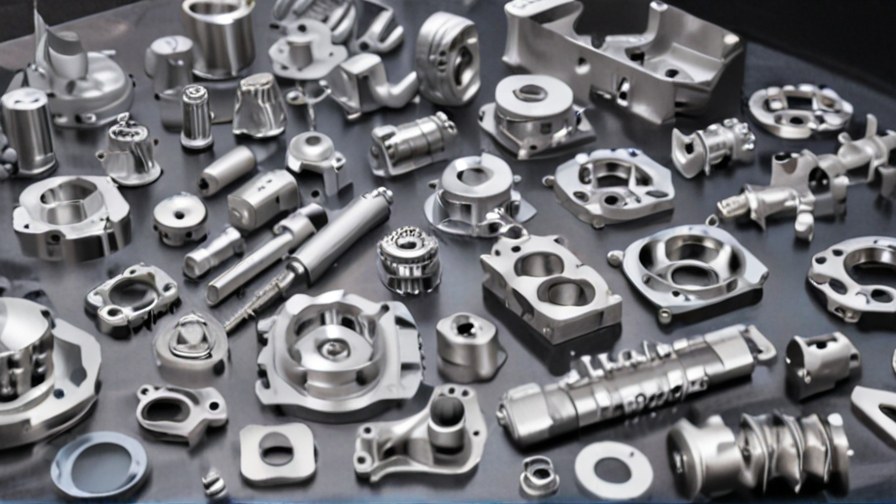
The Work Process and how to use cnc machining parts
CNC machining is a manufacturing process that utilizes computer numerical control (CNC) systems to automate the cutting, shaping, and finishing of various materials to create custom-designed parts. These parts are commonly used in industries such as automotive, aerospace, electronics, and medical.
The work process of CNC machining involves several crucial steps. First, a designer or engineer creates a CAD (Computer-Aided Design) model of the desired part using specialized software. The CAD model is then converted into a CNC program that contains precise instructions for the machine to follow.
Once the program is ready, the operator loads the raw material, typically metal or plastic, onto the CNC machine’s worktable or spindle. The machine uses a variety of cutting tools, such as drills, end mills, and lathes, to remove material from the workpiece based on the programmed instructions. This process is repeated until the desired shape and dimensions are achieved.
During the machining process, the CNC machine constantly monitors and adjusts the cutting parameters, such as speed, feed rate, and depth of cut, to ensure accuracy and quality. Additionally, the machine may employ various techniques like coolant or lubrication to enhance the cutting performance and prevent heat buildup.
Once the machining is complete, the finished part is carefully removed from the machine for inspection and post-processing. This may involve deburring, polishing, or applying specialized coatings to enhance the part’s appearance or functionality. Finally, the completed CNC machining parts are ready for assembly or installation into the final product.
To effectively use CNC machining parts, it is essential to have a clear understanding of the required specifications and tolerances. Proper programming of the CNC machine is crucial to achieving precise results. Furthermore, regular maintenance and calibration of the machine are vital to ensure its accuracy and prolong its lifespan.
Overall, CNC machining offers a highly efficient and precise manufacturing process for creating intricate parts. By leveraging the power of computer control, businesses can produce high-quality, customized components that meet the specific requirements of their applications.
Quality Testing Methods for cnc machining parts and how to control the quality
Quality testing methods for CNC machining parts include dimensional inspection, visual inspection, surface finish testing, material property testing, and functional testing.
Dimensional Inspection: This involves using precision measuring instruments like calipers, micrometers, and coordinate measuring machines (CMMs) to verify the dimensions and tolerances of the machined parts. The measurements are compared against the specifications provided in the engineering drawings.
Visual Inspection: Operators visually inspect the machined parts to identify any visible defects such as scratches, dents, or surface irregularities. This is especially important for parts with aesthetic requirements.
Surface Finish Testing: Surface roughness is measured using tools like a profilometer to ensure that the specified surface finish is achieved. This is crucial for parts that require specific smoothness or texture.
Material Property Testing: Material properties like hardness, tensile strength, and material composition (chemical analysis) are tested to ensure compliance with the required specifications. This is particularly important for critical parts that need to withstand specific loads or conditions.
Functional Testing: Machined parts can undergo functional testing to assess their performance based on their intended application. This can include fitting parts together, checking functionality, or simulating real-life conditions to ensure the part’s performance is satisfactory.
To control quality in CNC machining, several measures can be implemented:
– Implementing a robust quality management system that adheres to recognized standards such as ISO 9001. This includes clearly defining quality control processes and responsibilities.
– Regular training and qualification of operators to ensure they have the necessary skills and knowledge to perform their tasks accurately.
– Regular maintenance and calibration of CNC machines and inspection equipment to ensure accuracy and repeatability.
– Established inspection procedures and checklists to ensure that all critical dimensions, surface finishes, and functional requirements are systematically checked.
– Continuous monitoring of key performance indicators (KPIs) such as scrap rate, rejection rate, and customer satisfaction to identify areas for improvement.
– Implementing corrective and preventive actions to address any non-conformities or potential quality issues.
By employing these quality testing methods and implementing effective quality control measures, CNC machining businesses can ensure the production of high-quality parts that meet customer requirements and industry standards.
cnc machining parts Sample Policy and Post-Purchase Considerations for cnc machining parts from China
Sample Policy:
When purchasing CNC machining parts from China, it is important to have a well-defined and comprehensive sample policy to ensure the quality and reliability of the parts. The following sample policy can be implemented:
1. Request for Samples: Before placing a bulk order, it is essential to request samples from the supplier. Specify the desired quantity, material, and specifications of the parts.
2. Inspection and Quality Control: Thoroughly inspect the samples to ensure they meet the required standards. Evaluate the materials used, surface finish, dimensions, and compatibility with the intended application.
3. Quantity and Price Negotiation: Discuss the required quantity and pricing with the supplier based on the quality of the samples. Negotiate for competitive rates without compromising on quality.
4. Communication and Revisions: Clearly communicate any revisions or modifications required in the samples and collaborate with the supplier to ensure these changes are incorporated before finalizing the order.
5. Prototyping: If necessary, consider prototyping services to test the functionality and performance of the CNC machining parts.
6. Agreement and Terms: Draft an agreement with the supplier that specifies the terms of the purchase, including quality standards, inspection procedures, delivery schedule, payment terms, and recourse in case of non-compliance.
Post-Purchase Considerations:
After purchasing CNC machining parts from China, it is important to consider the following aspects:
1. Quality Assurance: Conduct rigorous quality checks upon receiving the bulk order. Inspect a sample from the lot to ensure that the parts meet the approved sample’s specifications.
2. Communication: Maintain open and consistent communication with the supplier. Address any issues promptly and work towards resolving them together.
3. Feedback and Relationship Building: Provide feedback to the supplier regarding the quality, performance, and service rendered. Building a good relationship with the supplier may lead to improved future collaborations.
4. Documentation and Warranty: Keep proper documentation of the transaction, including invoices, shipping documents, and any warranties provided by the supplier. This ensures accountability and facilitates future claims, if necessary.
5. Delivery and Logistics: Monitor the delivery schedule and track the shipment to ensure timely arrival. Coordinate with the supplier and freight forwarders as necessary.
6. Feedback and Recourse: In case of any major discrepancies or non-compliance, report the issue to the supplier immediately. If necessary, explore legal recourse or alternative suppliers for future orders.
By implementing a comprehensive sample policy and considering post-purchase factors, businesses can minimize risks associated with purchasing CNC machining parts from China and maintain high-quality standards.
Sourcing cnc machining parts from China: Opportunities, Risks, and Key Players
Sourcing CNC machining parts from China presents both opportunities and risks for businesses. China is known for its advanced manufacturing capabilities, cost-effective production, and a wide range of suppliers. However, there are also potential challenges and risks that need to be considered.
Opportunities:
1. Cost-effective production: Chinese manufacturers offer competitive pricing due to lower labor costs and economies of scale. This can result in significant savings for businesses.
2. Advanced manufacturing capabilities: China has heavily invested in advanced technologies, including CNC machining. This enables Chinese manufacturers to produce high-quality parts with precision and efficiency.
3. Vast supplier network: China has a large number of suppliers specializing in CNC machining. This provides businesses with a wide range of options to choose from, ensuring availability of different materials, sizes, and specifications.
Risks:
1. Quality control: Maintaining consistent quality can be a challenge when sourcing from China. It is crucial to perform thorough due diligence on suppliers, conduct quality checks, and establish clear communication channels to ensure product quality meets expectations.
2. Intellectual property infringement: China has faced criticism in the past for intellectual property (IP) infringement. Businesses need to protect their designs and patents by implementing legal safeguards and working with reputable suppliers.
3. Communication and language barriers: Language and cultural differences can impact communication and understanding between buyers and suppliers. Working with a local agent or interpreter can help bridge this gap and avoid misunderstandings.
Key Players:
1. Foxconn: Foxconn is a major player in the Chinese manufacturing industry, specializing in CNC machining. They provide services to various industries, including electronics, automotive, and medical devices.
2. BYD Company: BYD is a leading manufacturer of CNC-machined parts, particularly for the automotive industry. They are known for their expertise in producing high-quality components with a focus on sustainability.
3. Huawei Technologies: While primarily known for its telecommunications equipment, Huawei also offers CNC machining services. They have established a strong reputation in the industry for delivering reliable and precise parts.
In conclusion, sourcing CNC machining parts from China offers opportunities for cost-effective production, advanced manufacturing capabilities, and a vast supplier network. However, businesses need to remain cautious about quality control, IP protection, and communication barriers. Key players in the Chinese market include Foxconn, BYD Company, and Huawei Technologies.
How to find and select reliable cnc machining parts manufacturers in China,use google search manufacturers and suppliers
Finding and selecting reliable CNC machining parts manufacturers in China can be a daunting task, but with careful research and using Google search effectively, you can simplify the process. Here are some steps to follow:
1. Start with a detailed search: Use specific keywords like “CNC machining parts manufacturers in China” or “reliable CNC machining suppliers in China” to get targeted results.
2. Refine your search results: Look for reputable websites or online directories like Alibaba, Made-in-China, or Global Sources that provide comprehensive information about manufacturers and suppliers. These platforms usually have user reviews and ratings to establish credibility.
3. Evaluate the website: Visit the company’s website and check for essential details like company history, production capacity, certifications, and product range. A well-designed and informative website indicates professionalism and commitment.
4. Contact potential manufacturers: Reach out to multiple manufacturers and inquire about their capabilities, manufacturing processes, quality control measures, certifications, and previous experiences. Clear communication is essential to assess their reliability and suitability for your specific requirements.
5. Request samples: Ask for product samples to assess the quality, precision, and finishing of their CNC machining parts. Reliable manufacturers will readily provide samples and ensure they meet your specifications.
6. Check certifications and compliance: Verify if the manufacturer holds relevant certifications like ISO 9001, ISO 14001, or any specific industry certifications. Compliance with international standards ensures adherence to quality and manufacturing practices.
7. Request references: Ask the manufacturer for references of their previous customers. Contact these references to gain insights into their experiences and satisfaction with the manufacturer’s products and services.
8. Obtain multiple quotes: Request quotations from shortlisted manufacturers to compare pricing, lead time, and services offered. Be cautious of significantly low prices as it may indicate compromised quality.
9. Analyze customer reviews: Search for customer reviews and feedback about the manufacturers you are considering. Online forums, industry-specific websites, or social media platforms can provide valuable insights into their reputation and customer satisfaction levels.
10. Conduct a factory visit: If feasible, plan a visit to the manufacturer’s facility to assess their production capabilities, quality control processes, and overall infrastructure. Direct observation can give you a better understanding of their reliability.
By following these steps and conducting thorough research, you can find and select reliable CNC machining parts manufacturers in China that meet your specific requirements and ensure a successful business partnership.
How to check cnc machining parts manufacturers website reliable,use google chrome SEOquake check if ranking in top 10M
To check the reliability of a CNC machining parts manufacturer’s website, you can follow these steps:
1. Use Google Chrome: Open the website in Google Chrome, as it offers various tools and extensions to analyze websites effectively.
2. Install SEOquake: Add the SEOquake extension to your Google Chrome browser. SEOquake provides valuable insights and metrics about a website’s search engine optimization (SEO) performance.
3. Check the ranking: Use SEOquake to analyze the website’s ranking. Look for the website’s position on search engine result pages (SERPs). If it ranks within the top 10 million, it indicates that the website receives a significant amount of organic search traffic, which can be a positive sign.
4. Analyze other SEO parameters: SEOquake offers additional metrics like the number of indexed pages, domain age, social media engagement, and backlink profile. These factors can provide an overall impression of the website’s reliability. Look for a reasonable number of indexed pages and a healthy backlink profile.
5. Check for professional presentation: Examine the website’s appearance and content. A reliable CNC machining parts manufacturer’s website should have a professional design, clear and detailed product information, and an easy-to-navigate structure. Look for contact information, including a physical address, email, and phone number.
6. Evaluate customer feedback and testimonials: Look for customer reviews and testimonials on the website or third-party review platforms. Genuine positive reviews can indicate that the manufacturer has a good reputation and satisfied customers.
7. Verify certifications and quality standards: Reliable CNC machining parts manufacturers often display certifications and quality standards they adhere to. Verify the validity and relevance of these certifications to ensure compliance with industry standards.
By following these steps and utilizing SEOquake in Google Chrome, you can assess the reliability of a CNC machining parts manufacturer’s website. Remember, this method provides a general overview, and it’s always beneficial to conduct further research or seek recommendations from industry peers.
Top 10 cnc machining parts manufacturers in China with each 160 words introduce products,then use markdown create table compare
1. Foxron Precision Metal Parts Co., Ltd. specializes in CNC machining parts manufacturing, providing a wide range of precision-machined components for various industries such as automotive, aerospace, and electronics. Their products include CNC machined aluminum parts, stainless steel components, and plastic parts, ensuring high accuracy and tight tolerances to meet customers’ specific requirements.
2. Fengying Precision Metal Co., Ltd. offers comprehensive CNC machining solutions, specializing in the production of precision machined parts made of materials like brass, bronze, and stainless steel. Their product range encompasses shafts, gears, connectors, and housings, available in various sizes and finishes.
3. Summit Precision Machining Co., Ltd. prides itself on delivering premium CNC machined parts with exceptional quality and precise dimensions. Their product portfolio includes aluminum, steel, and plastic components, such as brackets, valves, and fittings, suitable for industries like telecommunications, robotics, and automation.
4. Dongguan MQ Precision Hardware Co., Ltd. is a leading manufacturer of CNC machining parts, providing customized solutions for projects requiring high precision and fine finishes. Their product range includes precision-machined metal and plastic parts, including connectors, flanges, and couplings.
5. Realhao Precision specializes in CNC machining services, offering precise and reliable machined parts for industries such as automotive, medical, and lighting. Their product range includes metal components like shafts, valves, and brackets, manufactured to tight tolerances and stringent quality standards.
6. Huaming Machinery Co., Ltd. is a trusted provider of CNC machining parts, offering a comprehensive range of products made from materials like aluminum, stainless steel, and brass. Their product lineup includes precision-machined parts such as housings, fittings, and connectors, suitable for industries like electronics and telecommunications.
7. Shenzhen Rollyu Precision Machining Co., Ltd. focuses on the production of CNC machined parts with high precision and excellent surface finishes. Their product catalog comprises metal and plastic components, including gears, shafts, and housings, accommodating various industries such as automotive, aerospace, and electronics.
| Manufacturer | Specialization | Notable Products |
| ———————- | ————————– | ————————— |
| Foxron Precision Metal Parts Co., Ltd. | CNC machining of aluminum, stainless steel, plastic parts | Precision-machined components for automotive, aerospace, and electronics |
| Fengying Precision Metal Co., Ltd. | CNC machining of brass, bronze, stainless steel parts | Shafts, gears, connectors, and housings |
| Summit Precision Machining Co., Ltd. | CNC machining of aluminum, steel, plastic components | Brackets, valves, fittings for telecommunications, robotics, and automation |
| Dongguan MQ Precision Hardware Co., Ltd. | Customized CNC machined metal and plastic parts | Connectors, flanges, couplings |
| Realhao Precision | CNC machining of metal parts | Shafts, valves, brackets for automotive, medical, lighting industries |
| Huaming Machinery Co., Ltd. | CNC machining of aluminum, stainless steel, brass parts | Housings, fittings, connectors for electronics and telecommunications |
| Shenzhen Rollyu Precision Machining Co., Ltd.| CNC machining of metal and plastic parts | Gears, shafts, housings for automotive, aerospace, and electronics industries |
These are just a few of the top CNC machining parts manufacturers in China, each excelling in their specialization and delivering precision-machined components for various industries.
Background Research for cnc machining parts manufacturers Companies in China, use qcc.com archive.org importyeti.com
When it comes to finding CNC machining parts manufacturers in China, there are several websites that can be used for background research. Three popular platforms are qcc.com, archive.org, and importyeti.com. These websites provide valuable information and insights into different manufacturers, helping you make an informed decision.
Qcc.com is a comprehensive business database in China that allows users to search for specific companies, including CNC machining parts manufacturers. The platform provides company profiles, contact information, registered capital, and company size, among other details. This information provides a glimpse into a company’s background and allows you to assess their capabilities and reliability.
Archive.org is a website that allows users to access archived versions of various web pages. This tool can be useful when researching CNC machining parts manufacturers, as it enables you to view historical data and track changes in a company’s online presence. By analyzing archived versions of a manufacturer’s website, you can gain insights into their history, past projects, and any changes they may have undergone over time.
Importyeti.com is an online business directory specifically tailored for importers looking for suppliers in China. The platform provides information about manufacturers, including their specialization, location, and products. Additionally, you can find factory audit reports, quality certifications, and customer reviews through this website. This information is crucial for evaluating a manufacturer’s credibility and the quality of their CNC machining parts.
In conclusion, qcc.com, archive.org, and importyeti.com are three valuable resources for conducting background research on CNC machining parts manufacturers in China. These platforms can provide insights into a company’s profile, online presence, historical data, and customer reviews, helping you make an informed decision when selecting a supplier.
Leveraging Trade Shows and Expos for cnc machining parts Sourcing in China
Trade shows and expos are excellent platforms for sourcing CNC machining parts in China. These events provide a unique opportunity to connect with numerous suppliers and manufacturers under a single roof, saving both time and effort in the sourcing process.
Attending trade shows and expos focused on CNC machining parts in China allows buyers to directly interact with exhibitors, understand their capabilities, and evaluate the quality of their products. It also enables face-to-face negotiations, fostering better communication and relationship building with potential suppliers.
Moreover, these events give buyers a chance to stay updated on the latest trends, technologies, and innovations in the industry. By observing the showcased products and engaging in discussions with industry experts, buyers gain valuable insights that can contribute to making informed decisions regarding their sourcing strategy.
To maximize the effectiveness of trade show and expo visits, buyers should thoroughly research and identify the events that align with their sourcing needs. By focusing on specific shows where CNC machining parts suppliers in China are prominently featured, buyers can ensure they are targeting the right suppliers and increasing their chances of finding suitable partners.
To further enhance the sourcing process, buyers should come prepared with a clear understanding of their requirements, including specific part specifications, quantity, and quality standards. This will enable them to engage in productive conversations with suppliers and make accurate comparisons between different offerings.
Furthermore, buyers should utilize their time at trade shows and expos to gather as much information as possible. This includes collecting brochures, catalogues, and samples from potential suppliers, as well as exploring additional services they may offer, such as design assistance or logistical support.
In conclusion, trade shows and expos are advantageous for sourcing CNC machining parts in China. These events provide a platform for direct interaction with suppliers, knowledge acquisition, and informed decision-making. By utilizing these opportunities effectively, buyers can identify reliable partners, access competitive pricing, and ensure high-quality CNC machining parts for their needs.
The Role of Agents and Sourcing Companies in Facilitating cnc machining parts Purchases from China
Agents and sourcing companies play a crucial role in facilitating CNC machining parts purchases from China. They act as intermediaries between buyers and Chinese manufacturers, working to streamline the sourcing and procurement process. Here are some key aspects of their role:
1. Supplier identification and assessment: Agents and sourcing companies have extensive networks and databases of reliable and experienced Chinese manufacturers. They help buyers identify suitable suppliers based on their specific requirements, such as quality standards, production capacity, and cost effectiveness. They also assess the credibility and reliability of these suppliers through background checks, on-site visits, and client testimonials.
2. Negotiation and price management: One of the main advantages of working with agents and sourcing companies is their expertise in negotiation. They negotiate with suppliers on behalf of the buyers to secure competitive prices and favorable terms. Their knowledge of the local market and industry standards allows them to ensure that buyers receive fair pricing for CNC machining parts.
3. Quality control and inspection: Agents and sourcing companies understand the importance of quality control in the manufacturing process. They implement a stringent quality control system to ensure that the CNC machining parts meet the buyers’ specifications and standards. They conduct regular inspections during production and before shipment to detect and rectify any quality issues, ensuring that only high-quality parts are delivered.
4. Logistics management and shipping: Another essential role of agents and sourcing companies is managing the logistics and shipping process. They coordinate the transportation of the purchased CNC machining parts from the Chinese supplier to the buyer’s location. This includes arranging documentation, customs clearance, and delivery logistics. Their expertise in shipping practices and regulations ensures a smooth and efficient delivery process.
5. Language and cultural barriers: Agents and sourcing companies bridge the gap between buyers and Chinese manufacturers by overcoming language and cultural barriers. They are fluent in both English and Chinese, facilitating clear communication and effective collaboration between the buyer and the supplier. This understanding of Chinese business customs and practices helps avoid misunderstandings and facilitates successful transactions.
In summary, agents and sourcing companies streamline the process of purchasing CNC machining parts from China by identifying reliable suppliers, negotiating competitive prices, ensuring quality control, managing logistics, and overcoming language and cultural barriers. Their expertise and knowledge help buyers save time, reduce risks, and ensure a successful procurement experience.
Price Cost Research for cnc machining parts manufacturers Companies in China, use temu.com and 1688.com
When it comes to CNC machining parts manufacturers, China is known for its vast number of companies offering competitive prices. Two popular platforms for finding such manufacturers are Temu.com and 1688.com. These platforms provide a wide range of options and allow users to filter their search based on various parameters such as price, quantity, and location.
Temu.com is a sourcing website dedicated to connecting global buyers with Chinese manufacturers. It offers a user-friendly interface and reliable supplier recommendations. The website provides transparency in pricing by allowing buyers to compare quotes from different suppliers. This feature enables users to select the most cost-effective option for their CNC machining parts requirements.
1688.com, on the other hand, is a popular online marketplace in China. With millions of suppliers, the platform offers a vast array of CNC machining parts at competitive prices. It also has a built-in translation feature, making it accessible to non-Chinese speakers. Buyers can browse through numerous product listings and communicate directly with the suppliers to negotiate pricing and other details.
When conducting price cost research on these platforms, it is essential to focus on certain factors to ensure a successful transaction. Firstly, buyers should clearly define their product requirements, including specifications, materials, quantity, and delivery schedules. This information allows suppliers to provide accurate pricing. Secondly, buyers should compare multiple quotations to identify the best value for money. It is advisable to consider factors such as quality, lead time, and supplier reliability in addition to price.
To summarize, Temu.com and 1688.com are reliable online platforms for conducting price cost research on CNC machining parts manufacturers in China. By utilizing these platforms, buyers can explore numerous suppliers, compare prices, and negotiate effectively to find the most suitable option for their specific requirements.
Shipping Cost for cnc machining parts import from China
When importing CNC machining parts from China, the shipping cost can vary depending on several factors. These factors include the size and weight of the parts, the distance between the two countries, the shipping method chosen, and any additional services or requirements.
For small and lightweight CNC machining parts, air freight is a popular and cost-effective option. Air freight is faster than sea freight and can be more suitable for time-sensitive orders. However, it can be relatively expensive, especially for larger and heavier parts.
Sea freight, on the other hand, is a more affordable option for shipping larger and heavier CNC machining parts. It is generally slower than air freight but can save costs if the delivery timeline is not urgent. Sea freight prices are influenced by shipping routes, container sizes, and any additional services such as customs clearance and delivery to the final destination.
To determine the exact shipping cost for CNC machining parts from China, it is recommended to obtain quotes from multiple freight forwarders or shipping carriers. They will consider the specific dimensions and weight of the parts, the shipping method, any additional services required, and the destination country.
It is worth noting that the shipping cost is just one aspect to consider when importing CNC machining parts from China. Other factors such as import duties, customs clearance fees, and any potential additional charges should also be taken into account.
In conclusion, the shipping cost for CNC machining parts import from China can vary depending on several factors such as size, weight, shipping method, distance, and additional services. Obtaining quotes from freight forwarders or shipping carriers is the best way to accurately determine the shipping cost for your specific requirements.
Compare China and Other cnc machining parts Markets: Products Quality and Price,Visible and Hidden Costs
China is widely known as a global manufacturing hub, including for CNC machining parts. When comparing China to other CNC machining parts markets, there are several aspects to consider: product quality, price, visible and hidden costs.
In terms of product quality, China has made significant strides over the years. Many Chinese manufacturers have invested in advanced CNC machining technology and quality control measures, leading to improved product quality. However, it is important to note that while China has made progress, it still faces challenges in consistently achieving the same level of quality as some developed countries. Markets such as Germany, Japan, and the United States are typically associated with higher quality standards due to their long-standing expertise and focus on precision engineering.
When it comes to price, China has a distinct advantage. The country’s lower labor and overhead costs allow Chinese manufacturers to offer competitive pricing for CNC machining parts. This advantage becomes particularly significant for high-volume production orders. In comparison, other markets with higher labor and operational costs may struggle to compete on price.
Visible costs, such as the cost of production and shipping, are generally competitive in China. The country’s well-developed logistics infrastructure and efficient supply chain management contribute to relatively low visible costs. However, hidden costs can sometimes arise when working with Chinese manufacturers. These can include language and communication barriers, intellectual property concerns, and lead time variations. These hidden costs should be carefully considered and addressed to minimize potential risks.
In summary, China offers competitive pricing and has significantly improved its product quality in the CNC machining parts market. However, other markets known for their precision engineering, such as Germany and Japan, still retain a reputation for higher quality standards. China’s advantage lies in its lower labor and overhead costs, resulting in more competitive prices. While visible costs in China are generally competitive, hidden costs like communication barriers or intellectual property concerns should be taken into account when evaluating Chinese manufacturers. Thus, buyers must carefully assess their priorities in terms of cost, quality, and associated risks when deciding between China and other CNC machining parts markets.
Understanding Pricing and Payment Terms for cnc machining parts: A Comparative Guide to Get the Best Deal
When it comes to CNC machining parts, understanding pricing and payment terms is crucial to secure the best deal for your business. This comparative guide aims to provide insights into these aspects, helping you make informed decisions while keeping the content concise within 300 words.
Pricing for CNC machining parts can vary based on several factors, including the complexity of the part, material choice, quantity ordered, and manufacturing processes involved. It is essential to obtain quotes from multiple suppliers to compare prices effectively. Ensure that the quotes include all relevant costs, such as material costs, tooling charges, and any additional manufacturing processes required.
When reviewing pricing, it is essential to strike a balance between cost and quality. Opting for the lowest-priced supplier may compromise the quality of the parts, impacting your end product. Look for suppliers who offer competitive pricing without compromising on material quality, precision, and adherence to specifications.
Payment terms are another crucial aspect to consider. Suppliers generally have various payment options, such as upfront payment, partial payment, or payment upon delivery. Negotiate payment terms that align with your cash flow requirements and offer the most favorable terms for your business.
Consider discussing long-term agreements with suppliers to establish a stable partnership. This can help secure better pricing and payment terms, as well as guarantee a steady supply of CNC machining parts for your business.
Additionally, evaluating a supplier’s track record and reputation is essential. Look for reviews, references, or case studies to assess their reliability, quality of work, and ability to meet deadlines. A trustworthy and reputable supplier should be able to provide clear communication channels and excellent customer service to facilitate a smooth transaction process.
In conclusion, obtaining competitive pricing and favorable payment terms for CNC machining parts is vital. Comparing quotes from multiple suppliers, considering the balance between cost and quality, negotiating payment terms, and establishing long-term partnerships can help you secure the best deal and ensure the success of your manufacturing operations.
Chinese Regulations and Industry Standards Certifications for cnc machining parts,Import Regulations and Customs for cnc machining parts from China
Chinese Regulations and Industry Standards Certifications for CNC Machining Parts:
In China, the primary regulatory body for CNC machining parts is the Standardization Administration of China (SAC). The SAC is responsible for developing and enforcing standards and certifications to ensure the quality and safety of CNC machining parts. The main certification for CNC machining parts is the China Compulsory Certification (CCC) mark. The CCC mark is mandatory for many products, including CNC machining parts, that are sold in the Chinese market. It indicates that the product meets the minimum requirements defined by Chinese regulations.
Additionally, CNC machining parts may also need to comply with industry-specific standards and certifications. For example, the China Machinery Industry Federation (CMIF) has established various standards for CNC machining parts, covering aspects such as design, performance, and manufacturing processes. Adhering to these industry standards can enhance the credibility and competitiveness of CNC machining parts in the Chinese market.
Import Regulations and Customs for CNC Machining Parts from China:
Importing CNC machining parts from China to other countries requires compliance with the regulations and customs requirements of the destination country. Firstly, it is essential to determine the tariff classification of the CNC machining parts in accordance with the Harmonized System (HS) code used by the destination country. This code determines the import duties and taxes applicable to the product.
In addition to import duties, the importing country may impose other regulatory requirements, such as product certification or testing. For instance, some countries may require specific certifications or compliance with relevant international standards in order to ensure product quality and safety.
Customs procedures for importing CNC machining parts will vary based on the destination country’s regulations. It is important to prepare the necessary documents, such as commercial invoices, packing lists, and certificates, and declare accurate product information to customs authorities. It is advisable to work with a freight forwarder or customs broker who can provide guidance on customs procedures and ensure compliance with import regulations.
In summary, Chinese regulations for CNC machining parts include certifications such as the China Compulsory Certification mark, as well as industry standards established by organizations like the CMIF. Importing CNC machining parts from China to other countries requires compliance with destination country regulations, including tariff classification, certifications, and customs procedures.
Sustainability and Environmental Considerations in cnc machining parts Manufacturing
Sustainability and environmental considerations are increasingly important in the manufacturing industry, including the production of CNC machining parts. CNC (Computer Numerical Control) machining is a widely used manufacturing process that involves the automated removal of material from a workpiece to create a desired shape or product.
To ensure sustainability, manufacturers are adopting various practices that minimize environmental impact throughout the entire CNC machining process. These include:
1. Material Selection: Opting for sustainable materials, such as recyclable or biodegradable metals and alloys, can help reduce the environmental footprint of CNC machining parts manufacturing. Additionally, manufacturers can prioritize using materials that require less energy or water during processing.
2. Waste Reduction: CNC machining generates waste in the form of excess material, swarf (metal chips), and coolant. Employing efficient cutting strategies, such as minimizing cutting depths and optimizing tool paths, can help reduce the amount of waste generated. Furthermore, implementing recycling and reuse programs for materials and coolant can significantly minimize waste disposal.
3. Energy Efficiency: CNC machines consume substantial amounts of energy during operation. To enhance energy efficiency, manufacturers can invest in advanced CNC machines that incorporate energy-saving features and technologies. These may include servo motor systems, variable speed drives, and energy recovery systems that capture and reuse energy.
4. Impact of Coolants/Lubricants: Coolants and lubricants are crucial for CNC machining as they ensure efficient cutting and extend tool life. However, some of these fluids can be harmful to the environment if not properly managed. Implementing closed loop or minimal fluid systems, which recirculate fluids and minimize consumption, can help reduce the environmental impact of coolants and lubricants.
5. Recycling and Disposal: Proper disposal of waste materials, including excess metal, swarf, and coolant, is essential for environmental sustainability. Manufacturers can work with specialized recycling facilities or adopt sustainable waste management practices to ensure the responsible disposal or reuse of these materials.
In conclusion, sustainability and environmental considerations in CNC machining parts manufacturing involve selecting sustainable materials, reducing waste generation, enhancing energy efficiency, managing coolants and lubricants, and implementing responsible recycling and disposal practices. By incorporating these measures, manufacturers can significantly reduce their environmental footprint in CNC machining operations.
List The Evolution history of “cnc machining parts”
CNC (Computer Numerical Control) machining parts have come a long way since their inception. The evolution of this technology can be traced back to the early 1950s when the first computer-controlled machine tool was introduced. This early version was developed for the US Air Force to produce complex contours for jet engine parts.
During the 1960s and 70s, the use of CNC machining parts expanded into various industries, including automotive, aerospace, and electronics. The machines became more sophisticated, incorporating advanced features like automatic tool changers, which allowed for increased productivity and versatility.
In the 1980s, the introduction of CAD (Computer-Aided Design) and CAM (Computer-Aided Manufacturing) software revolutionized CNC machining. These programs allowed engineers to design and simulate parts before manufacturing them, minimizing errors and maximizing efficiency.
The 1990s saw further advancements in CNC machining parts, such as the integration of 3D printing technologies. This enabled the production of complex shapes and intricate designs that were not feasible with traditional machining techniques.
In the early 2000s, the focus shifted towards enhancing the precision and accuracy of CNC machining parts. High-speed machining techniques were introduced, increasing the spindle speeds and feed rates, resulting in faster production times and improved surface finishes.
In recent years, there has been a growing emphasis on automation and robotics in CNC machining. CNC machines are now equipped with sensors and monitoring systems that enable real-time data collection and analysis, optimizing production processes and reducing downtime.
Additionally, advancements in computer software and connectivity have made it possible to remotely monitor and control CNC machines, allowing for increased flexibility and remote operation.
Looking ahead, the future of CNC machining parts seems promising. Developments in artificial intelligence and machine learning are expected to further improve efficiency and optimize machining processes.
In conclusion, the evolution of CNC machining parts has undergone significant transformations over the past several decades. From the early computer-controlled machines to the integration of advanced software and automation, these advancements continue to enhance precision, productivity, and versatility in various industries.
The Evolution and Market Trends in cnc machining parts Industry
CNC machining parts industry has undergone significant evolution and witnessed several market trends over the years. The industry has experienced remarkable advancements in technology, which have greatly enhanced the precision and efficiency of machining processes.
One of the major developments in the CNC machining parts industry is the introduction of computer numerical control (CNC) systems. This technology has revolutionized the industry by automating the manufacturing process, eliminating the need for manual operations, and reducing human error. CNC systems have also enabled complex designs and shapes to be easily machined, resulting in high-quality finished products.
Another notable trend in the CNC machining parts industry is the use of advanced materials. With the increasing demand for products with excellent mechanical properties and improved performance, manufacturers have started utilizing materials like titanium, composites, and alloys. These materials offer superior strength, lightness, and resistance to heat, making them ideal choices for applications in aerospace, automotive, and medical industries.
Furthermore, the market has witnessed a shift towards miniaturization. The demand for smaller and more intricate parts has increased with the advancements in industries such as electronics and telecommunications. CNC machining parts industry has adapted to this trend by developing state-of-the-art machinery and techniques to produce complex micro-components. Miniaturization has not only allowed for the production of smaller devices but also increased their functionality and convenience.
Additionally, industry players have been focusing on sustainability and eco-friendliness. The use of green manufacturing practices and energy-efficient technologies has gained prominence, as businesses strive to reduce their carbon footprint. This includes the optimization of machining processes to minimize waste, recycling of materials, and adoption of renewable energy sources.
In terms of market trends, there has been a growing demand for customized products. Customers now seek tailored solutions that meet their specific requirements. This trend has led to the emergence of niche markets and the need for flexible CNC machining capabilities to accommodate varying design specifications.
Overall, the CNC machining parts industry continues to evolve in response to technological advancements, market demands, and sustainability goals. The future looks promising with further improvements expected in precision, efficiency, and customization capabilities of CNC machining processes.
Custom Private Labeling and Branding Opportunities with Chinese cnc machining parts Manufacturers
Chinese CNC machining parts manufacturers offer a wide range of custom private labeling and branding opportunities for businesses looking to establish their own brand identity. With expertise in precision machining and manufacturing, these manufacturers can produce high-quality, customized parts according to specific design requirements.
Private labeling allows businesses to create their own unique brand by placing their logo, company name, or any other desired branding elements on the products. Chinese CNC machining parts manufacturers understand the importance of branding and provide the flexibility to imprint branding elements on the parts using various techniques such as laser engraving, etching, or screen printing.
Moreover, these manufacturers can also assist businesses in designing and producing customized packaging for their products. This includes designing and printing labels, boxes, and other packaging materials with the company’s brand aesthetics, enhancing the overall brand experience for customers.
By collaborating with Chinese CNC machining parts manufacturers, businesses can ensure that the final products meet their specific quality standards. These manufacturers often have advanced machining equipment and follow stringent quality control procedures to guarantee the accuracy, precision, and durability of the machined parts.
Additionally, partnering with Chinese manufacturers offers cost-effective solutions without compromising on quality. China’s competitive manufacturing industry ensures competitive pricing for custom private labeling and branding services, making it an attractive option for businesses of all sizes.
In conclusion, Chinese CNC machining parts manufacturers provide ample opportunities for businesses to establish their own brand identity through customized private labeling and branding. With their expertise in precision manufacturing, attention to detail, and cost-effective solutions, businesses can confidently rely on these manufacturers to bring their brand vision to life.
Tips for Procurement and Considerations when Purchasing cnc machining parts
1. Clearly define your requirements: Before purchasing CNC machining parts, it is essential to clearly define your requirements. This includes determining the specific dimensions, materials, tolerances, and finishes needed for the parts.
2. Research potential suppliers: Conduct thorough research to identify potential suppliers of CNC machining parts. Consider factors such as their experience, reputation, quality control processes, certifications, and customer reviews.
3. Request for quotes: Once you have shortlisted a few suppliers, request quotes for the required CNC machining parts. Ensure that the quotes are comprehensive and include all relevant information such as pricing, lead time, shipping costs, and any additional charges.
4. Assess quality control measures: Look for suppliers who have robust quality control measures in place. This includes inspection processes to ensure the parts meet the specified requirements and adherence to industry standards.
5. Evaluate communication and customer service: Effective communication is crucial when working with suppliers. Assess their responsiveness, ability to understand your requirements, and willingness to provide regular updates on the progress of your order.
6. Consider production capacity: Evaluate the production capacity of the supplier to ensure they can handle your required quantity of CNC machining parts within the desired timeframe.
7. Review sample parts: Request sample parts from the supplier to assess their quality, accuracy, and finish. This will help you make an informed decision about whether the supplier meets your expectations.
8. Pricing and payment terms: Consider pricing and payment terms before finalizing a supplier. Compare quotes from different suppliers while considering factors such as volume discounts, bulk order pricing, and any additional costs such as tooling charges.
9. Consider lead time: Evaluate the lead time provided by the supplier to ensure it aligns with your project timeline. Discuss any potential delays or expedited options if required.
10. Contract and legal considerations: Before finalizing the purchase, ensure all the terms and conditions are documented in a contract. This includes specifications, pricing, delivery schedule, dispute resolution mechanisms, and any applicable warranties or guarantees.
By following these tips and considerations, you can ensure a smooth procurement process when purchasing CNC machining parts.
FAQs on Sourcing and Manufacturing cnc machining parts in China
1. Why should I consider sourcing and manufacturing CNC machining parts in China?
China is known for its strong manufacturing industry, including CNC machining. The country offers competitive pricing, a vast network of suppliers, and advanced manufacturing capabilities. Chinese manufacturers often have experience working with international clients and can provide high-quality products at a lower cost compared to other countries.
2. How can I find a reliable supplier for CNC machining parts in China?
There are several methods to find reliable suppliers in China. You can utilize online platforms, such as Alibaba or Global Sources, which provide a directory of verified manufacturers and allow you to communicate directly with potential suppliers. Additionally, attending trade shows in China, like the Canton Fair, is an excellent way to establish connections and meet potential suppliers face-to-face.
3. How can I ensure the quality of CNC machining parts manufactured in China?
To ensure the quality of CNC machining parts, consider the following steps:
– Conduct thorough research on the supplier’s reputation, certifications, and client feedback.
– Request samples or prototypes to evaluate the quality before proceeding with bulk orders.
– Establish clear quality control requirements, specifications, and standards in your contract.
– Conduct regular inspections and quality checks during production and before shipment.
– Utilize a third-party quality inspection agency to conduct inspections on your behalf.
4. How long does it typically take to manufacture CNC machining parts in China?
The lead time for manufacturing CNC machining parts in China can vary based on the complexity of the parts, quantity, and the manufacturer’s production capacity. However, it is common for the lead time to range from 2-8 weeks, including the time required for production, quality control, and shipping.
5. Can I customize CNC machining parts according to my specific requirements?
Yes, Chinese manufacturers are generally open to customization and can produce CNC machining parts according to your specific design and requirements. It is essential to provide comprehensive technical drawings, specifications, and detailed instructions to the manufacturer to ensure accurate customization.
In conclusion, sourcing and manufacturing CNC machining parts in China can offer cost-effective solutions with reliable suppliers, extensive manufacturing capabilities, and the ability to customize products. However, it is crucial to conduct due diligence, ensure quality control, and establish clear communication and expectations with the chosen supplier.
Why contact sourcifychina.com get free quota from reliable cnc machining parts suppliers?
Sourcifychina.com offers free quotas from reliable CNC machining parts suppliers to provide customers with a convenient and efficient sourcing experience. There are several reasons why Sourcifychina.com provides this service:
1. Building Trust and Confidence: By offering free quotas from reliable suppliers, Sourcifychina.com helps build trust and confidence in their sourcing platform. Customers can be assured that they are dealing with reputable suppliers who meet the required quality standards.
2. Cost Savings: By obtaining free quotas, customers can save on the initial cost of sourcing and supplier vetting. It eliminates the need for customers to search for suitable suppliers themselves, saving them time and resources.
3. Supplier Verification: Sourcifychina.com ensures that all the suppliers listed on their platform are thoroughly vetted and verified. By obtaining free quotas from trusted suppliers, customers can rely on Sourcifychina.com’s evaluation and verification process to connect them with high-quality suppliers.
4. Quick and Efficient Sourcing: The free quotas from reliable suppliers streamline the sourcing process for customers. Instead of extensive research and negotiation, customers can easily compare quotes and select the best supplier based on their requirements.
5. Customized Solutions: Sourcifychina.com considers customers’ specific needs and requirements while sourcing CNC machining parts. By obtaining free quotas, customers can communicate their project details and receive tailored solutions accordingly, ensuring a more efficient sourcing process.
In conclusion, Sourcifychina.com offers free quotas from reliable CNC machining parts suppliers to build trust, save costs, provide verified suppliers, offer quick sourcing, and deliver customized solutions. This service aims to simplify the sourcing process and connect customers with reliable suppliers for their CNC machining part requirements.