Introduce about cnc machining types guide,Qulity,Cost,Supplier,Certification,Market,Tips,FAQ
CNC machining, also known as Computer Numerical Control machining, is a manufacturing process that utilizes computerized controls and precise tools to remove material from a workpiece and create finished products. There are several types of CNC machining processes, each offering specific advantages and applications.
Some common types of CNC machining include milling, turning, drilling, and grinding. Milling involves cutting and shaping materials using a rotating tool, while turning rotates the workpiece to achieve the desired shape. Drilling creates holes, and grinding produces a smooth surface finish. Each type of CNC machining has its own unique set of capabilities and is ideal for specific manufacturing requirements.
When it comes to quality, CNC machining is highly regarded for its precision and accuracy. The computerized controls ensure consistent results, reducing human error and increasing overall product quality. This makes CNC machining popular in industries where tight tolerances and precise specifications are critical, such as aerospace, automotive, and medical.
Regarding cost, CNC machining can be cost-effective for large-scale production runs due to its automation capabilities and reduced labor requirements. The initial setup costs may be higher than other manufacturing processes, but the long-term benefits often outweigh this investment.
Finding a reliable CNC machining supplier is essential to ensure quality and timely delivery. It is crucial to choose a supplier with the right expertise, state-of-the-art equipment, and a proven track record. Additionally, certification and industry standards compliance can further assure the supplier’s capabilities and adherence to quality management processes.
CNC machining has a widespread market presence and is utilized across various industries globally. The demand for CNC machining services continuously grows as technological advancements push for more complex and precise components.
Here are some tips when using CNC machining services:
1. Provide detailed drawings and specifications to convey your requirements accurately.
2. Collaborate with the CNC machining supplier to optimize designs for cost and manufacturability.
3. Regularly communicate with the supplier to stay updated on the progress of your project.
4. Conduct thorough inspections and tests to ensure quality control.
Frequently Asked Questions (FAQs) about CNC machining may include queries about the pricing structure, material compatibility, turnaround time, and post-processing options.
In summary, CNC machining offers a wide range of types and applications, providing high-quality manufacturing solutions. It brings efficiency, precision, and cost-effectiveness to various industries, while ensuring compliance with industry standards. Careful selection of suppliers and effective communication are crucial for successful CNC machining projects.
Types of cnc machining types
CNC (Computer Numerical Control) machining is a process that involves the use of computers and specialized software to control machine tools and perform various manufacturing operations. There are several types of CNC machining, each serving different purposes and offering unique benefits.
1. CNC Milling: CNC milling is one of the most common types of CNC machining. It involves removing material from a workpiece using rotary cutters to create complex shapes and designs. CNC mills can operate either vertically or horizontally and can perform a wide range of operations, including drilling, tapping, and contouring.
2. CNC Turning: CNC turning involves rotating a workpiece while a cutting tool shapes it into the desired form. It is typically used to create cylindrical parts, such as shafts, rods, and tubes. CNC lathes are commonly used for turning operations and can produce high-precision components with excellent surface finishes.
3. CNC Drilling: CNC drilling is a machining process that involves creating holes in a workpiece. It is commonly used in various industries for applications such as creating holes for fasteners or creating holes with specific dimensions and spacing. CNC drilling machines can automate the process and ensure precise hole placements and sizes.
4. CNC Grinding: CNC grinding is a precise machining process that uses an abrasive wheel to remove material from a workpiece. It is commonly used to create high-precision parts with tight tolerances and excellent surface finishes. CNC grinding machines can perform tasks such as surface grinding, ID grinding, and centerless grinding.
5. CNC EDM (Electrical Discharge Machining): CNC EDM is a non-traditional machining process that uses electrical discharges to remove material from a workpiece. It is commonly used for creating complex shapes, intricate details, and sharp edges in parts that are difficult to machine with conventional methods.
6. CNC Laser Cutting: CNC laser cutting is a versatile machining process that uses a high-powered laser beam to cut through materials. It is commonly employed in industries such as automotive, aerospace, and electronics for precision cutting of various materials, including metal, plastic, and wood.
7. CNC Waterjet Cutting: CNC waterjet cutting involves using a high-pressure jet of water mixed with an abrasive material to cut through materials. It offers the advantage of precise and clean cutting without generating heat, making it suitable for materials that are sensitive to high temperatures.
These are just a few examples of the types of CNC machining available. The choice of the right method depends on various factors such as the desired outcome, material type, complexity of the design, and budget. CNC machining has revolutionized manufacturing processes by offering high precision, speed, and automation capabilities, resulting in efficient production of complex parts and components.
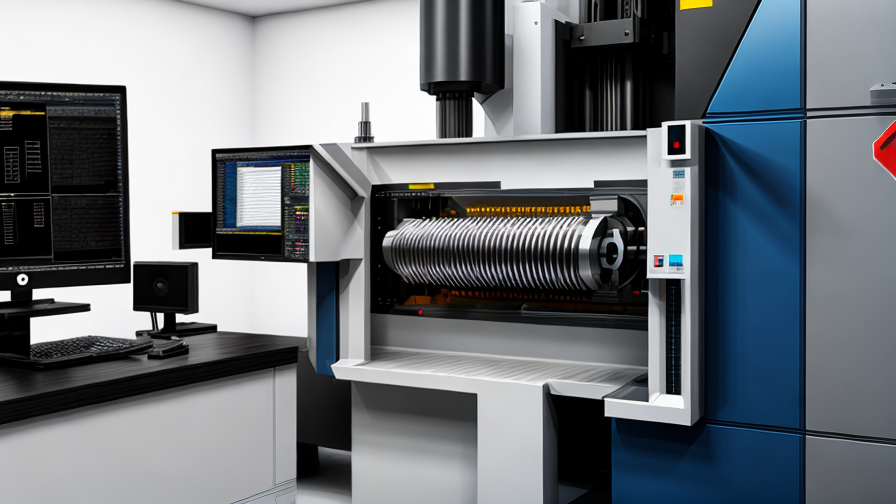
Pros and Cons of Using cnc machining types
CNC (computer numerical control) machining is a process that utilizes computer-controlled machines to produce accurate and precise parts. There are various types of CNC machining, each with its own pros and cons. Here are some of the key advantages and disadvantages to consider:
1. 3-axis CNC machining:
Pros:
– Versatile: Can handle a wide range of parts with simple to moderate complexity.
– Cost-effective: Requires relatively less investment, making it suitable for small-scale manufacturing.
– Familiarity: Widely used, which means there are many skilled operators and readily available tools.
Cons:
– Limited precision: Due to its 3-axis movement, it may struggle to achieve high precision for extremely complex parts.
– Limited flexibility: Can only work on parts that lie on a single plane, limiting the types of geometries that can be produced.
2. 4-axis CNC machining:
Pros:
– Increased complexity: Allows for additional rotary movement, enabling machining of more complex parts.
– Enhanced precision: Improved accuracy due to additional axis control.
– Efficiency: Reduced setup time compared to 3-axis machining.
Cons:
– Higher investment: Requires more advanced machinery and additional training, resulting in higher costs.
– Greater complexity: More complex machinery can be challenging to set up and configure.
3. 5-axis CNC machining:
Pros:
– Maximum versatility: Can handle highly complex parts from multiple angles and planes.
– Superior precision: Allows for intricate detailing and high tolerances.
– Reduced production time: Minimizes the need for multiple setups, thus increasing overall efficiency.
Cons:
– High cost: Requires advanced machinery and extensive operator training, making it expensive.
– Complex programming: More complex geometries require sophisticated programming skills.
Overall, the choice of CNC machining type depends on the specific requirements and budget of the project. While 3-axis machining is more cost-effective and suitable for simpler parts, 4-axis and 5-axis machining offer increased precision and the ability to manufacture more complex geometries. It is essential to weigh these pros and cons to select the best CNC machining type for each specific application.
cnc machining types Reference Specifications (varies for different product)
CNC machining is a versatile manufacturing process that utilizes computer numerical control to efficiently produce complex and precise parts. There are different types of CNC machining that cater to various applications and product requirements. Here are some reference specifications for common CNC machining types:
1. Milling: CNC milling employs rotating cutting tools to remove material from a workpiece. It can accommodate various geometries, such as flat surfaces, curves, and holes. Milling machines offer high precision, exceptional surface finishes, and the ability to create intricate designs. The reference specifications for milling include speed (RPM), feed rate (inches per minute), and cutting depth.
2. Turning: CNC turning is used to create cylindrical parts by rotating a workpiece against a cutting tool. The reference specifications for turning include spindle speed (RPM), feed rate (inches per revolution), and depth of cut. This machining type is often used for producing accurate round parts, such as shafts, pins, and screws.
3. Drilling: CNC drilling is primarily used to create holes in a workpiece. It involves rotating a drill bit against the material to create the desired hole size and shape. The reference specifications for drilling include spindle speed (RPM), feed rate (inches per minute), and drill diameter.
4. Grinding: CNC grinding is suitable for achieving high levels of precision and surface finish. It employs an abrasive wheel to remove material from a workpiece. The reference specifications for grinding include rotational speed (RPM), feed rate (inches per minute), and coolant flow rate.
5. Laser Cutting: CNC laser cutting is a non-contact machining process that uses a high-powered laser to cut through a wide range of materials with high precision. The reference specifications for laser cutting include laser power (watts), cutting speed (inches per minute), and assist gas pressure.
It is essential to note that the reference specifications may vary based on the specific product requirements, such as material type, part complexity, desired tolerances, and desired surface finishes. Manufacturers typically provide detailed guidelines and recommendations for each machining type to ensure optimal performance and desired outcomes.
In conclusion, CNC machining encompasses various types, including milling, turning, drilling, grinding, and laser cutting. Each machining type has its set of reference specifications that need to be considered in the manufacturing process to achieve the desired product characteristics and quality.
Applications of cnc machining types
CNC machining, or Computer Numerical Control machining, is a manufacturing process that utilizes computerized controls to operate machinery and create precise parts and components. There are various types of CNC machining techniques that are used for different applications, each offering its own advantages and capabilities.
One common type of CNC machining is milling, which involves removing material from a workpiece using rotary cutters. Milling machines are highly versatile and can produce a wide range of shapes and sizes, making them suitable for applications such as automotive parts, aerospace components, and molds.
Turning is another type of CNC machining that involves rotating a metal workpiece while a cutting tool removes material to create cylindrical shapes. This technique is commonly used for manufacturing shafts, rods, and other symmetrical components. Turning is known for its high precision and is often utilized in industries such as medical and electronics.
Drilling, as the name suggests, involves creating holes in a workpiece using specialized drill bits. CNC drilling machines can accurately drill holes of varying sizes and depths, making them essential for industries like construction, plumbing, and electrical.
CNC grinding is used for precision machining of hard materials and offers tight tolerances and fine surface finishes. Grinding is employed in automotive, aerospace, and tooling industries for manufacturing components such as dies, molds, and gears.
Wire Electrical Discharge Machining (EDM) uses an electrically charged wire to erode material from a workpiece. CNC wire EDM is particularly useful for creating intricate shapes with tight tolerances and is commonly used in the production of molds, dies, and prototypes.
In summary, CNC machining types have a wide range of applications across various industries. Milling, turning, drilling, grinding, and wire EDM provide precise and efficient manufacturing processes for producing a variety of components used in automotive, aerospace, medical, and many other industries. These CNC machining techniques play a crucial role in the modern manufacturing landscape, enabling the creation of complex and high-quality parts.
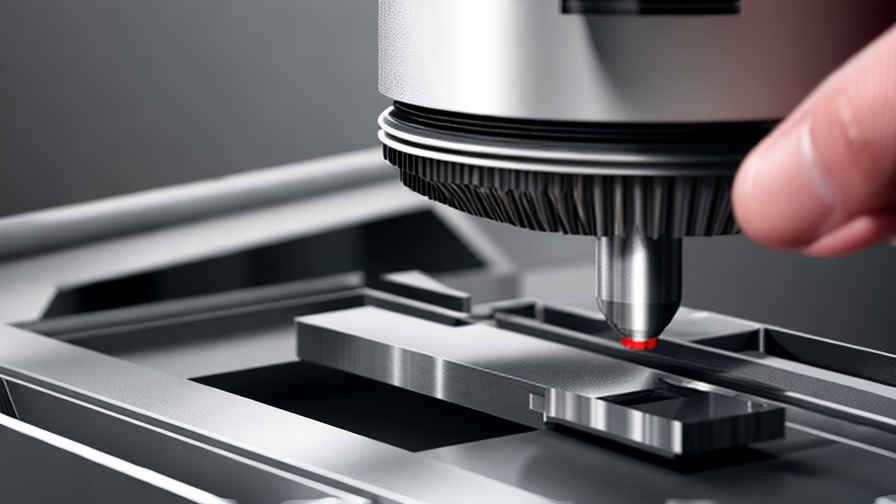
The Work Process and how to use cnc machining types
CNC machining is a process that involves using computer numerical control (CNC) machines to automatically execute precise manufacturing tasks. There are various types of CNC machining, including milling, turning, drilling, and grinding. Each type utilizes different tools and techniques to create the desired final product.
The work process of CNC machining involves several steps. First, a 3D design of the part or component is created using computer-aided design (CAD) software. This design is then converted into a format that can be understood by the CNC machine using computer-aided manufacturing (CAM) software.
Once the design is ready, the material to be machined is selected, such as metal, plastic, or wood. The material is then loaded onto the CNC machine, and the necessary cutting tools are installed. The CNC machine is programmed with the instructions needed to perform the specific machining operation, such as milling, turning, or drilling.
When everything is set up, the CNC machine begins the machining process. It moves the cutting tools along the programmed path, removing excess material and shaping the workpiece according to the design specifications. The machine operates with high precision and accuracy, ensuring consistent and repeatable results.
Throughout the machining process, the CNC machine continuously monitors and adjusts various parameters, such as cutting speed, feed rate, and tool position. This ensures that the machining operation remains within the desired tolerances and prevents any errors or inconsistencies.
Once the machining is complete, the finished part or component is inspected for quality assurance. Any necessary finishing operations, such as polishing or deburring, may also be carried out at this stage. The final product is then ready for use or further assembly.
In summary, CNC machining is a versatile and efficient manufacturing process that utilizes different types of machines to create precise parts and components. By following a structured work process and leveraging the capabilities of CNC machines, manufacturers can achieve high-quality results while optimizing production time and costs.
Quality Testing Methods for cnc machining types and how to control the quality
There are several quality testing methods that can be utilized for CNC machining types to ensure the end product meets the required standards.
1. Dimensional testing: This involves measuring the dimensions of the machined part using tools such as calipers, micrometers, or coordinate measuring machines (CMMs). This helps ensure that the part has been machined accurately according to the design specifications.
2. Surface finish testing: Surface roughness testers can be used to measure the surface finish of the machined part. This is important as the surface finish can affect the functionality and appearance of the part.
3. Hardness testing: Hardness testing can be performed to measure the hardness of the material after machining. This is crucial as the hardness of the material can affect its strength and durability.
4. Visual inspection: Visual inspection can be used to detect any visible defects or imperfections on the machined part. This can include checks for burrs, cracks, or incomplete machining.
To control the quality of CNC machining, it is essential to implement various quality control measures. This includes regularly calibrating and maintaining CNC machines, as well as ensuring that operators are properly trained and adhere to standard operating procedures. Additionally, implementing quality control checks at different stages of the machining process can help identify and address any issues early on. This can include using statistical process control techniques and conducting regular audits to monitor the quality of the machined parts. By implementing these measures, manufacturers can ensure that the CNC machining process consistently produces high-quality parts that meet the required standards.
cnc machining types Sample Policy and Post-Purchase Considerations for cnc machining types from China
Sample Policy:
When purchasing cnc machining types from China, it is important to consider the following post-purchase considerations:
1. Quality Assurance: Ensure that the supplier provides high-quality cnc machining types that meet your specifications and standards. Request samples or inspect the products before placing a bulk order.
2. Communication: Maintain open and clear communication with the supplier throughout the ordering process. Confirm delivery times, costs, and any other details to avoid misunderstandings.
3. Payment Terms: Clarify payment terms with the supplier before making a purchase. Negotiate a secure payment method that protects both parties involved.
4. Shipping and Handling: Discuss shipping and handling arrangements with the supplier to ensure that your cnc machining types arrive safely and on time. Confirm packaging materials and methods to prevent damage during transit.
5. Warranty and Returns: Inquire about the supplier’s warranty and return policies for cnc machining types. Understand the terms and conditions for defective products or potential issues with your order.
6. Customization Options: If you require customized cnc machining types, discuss your specifications with the supplier and confirm that they can fulfill your requirements. Ensure that any modifications meet your quality standards.
7. Compliance and Regulations: Verify that the supplier complies with all relevant regulations and certifications for cnc machining types. Confirm that the products meet industry standards and are safe for use.
By considering these post-purchase considerations, you can make a successful purchase of cnc machining types from China and ensure customer satisfaction.
Sourcing cnc machining types from China: Opportunities, Risks, and Key Players
China offers a wide variety of CNC machining types, including milling, turning, grinding, drilling, and EDM. The country’s vast manufacturing capabilities and competitive pricing make it an attractive sourcing destination for businesses looking to produce high-quality parts and components.
Opportunities in sourcing CNC machining from China include cost savings, access to advanced technology, and quick turnaround times. Chinese manufacturers have the expertise and resources to handle complex projects and large production volumes, making them suitable partners for businesses in various industries.
However, there are risks associated with sourcing CNC machining from China, including quality control issues, communication barriers, intellectual property concerns, and logistical challenges. It is essential for businesses to conduct thorough due diligence, visit potential suppliers, and establish clear agreements to mitigate these risks.
Key players in the Chinese CNC machining industry include Foxconn, Huawei Technologies, and BYD Company Limited. These companies have extensive experience in producing precision parts for electronics, automotive, aerospace, and other industries. By partnering with established manufacturers, businesses can benefit from their technical expertise, quality control processes, and efficient production capabilities.
Overall, sourcing CNC machining from China can be a rewarding endeavor for businesses seeking cost-effective solutions and access to advanced manufacturing technologies. By carefully evaluating suppliers, addressing potential risks, and fostering strong partnerships, companies can leverage the benefits of China’s thriving machining industry to meet their production needs effectively.
How to find and select reliable cnc machining types manufacturers in China,use google search manufacturers and suppliers
Finding and selecting reliable CNC machining types manufacturers in China can be a crucial task for businesses wanting to outsource their manufacturing needs. One of the most effective ways is to use Google search to identify potential manufacturers and suppliers. Here are some key steps to follow:
1. Start by entering relevant keywords such as “CNC machining types manufacturers in China” or specific requirements like “CNC milling manufacturers in China.”
2. Review the search results and visit the websites of manufacturers that appear reputable and relevant to your needs. Carefully examine their product offerings, manufacturing capabilities, certifications, and experience.
3. Look for information about the company’s history, including when it was established and how long it has been operating. Longevity can be an indication of a reliable and established manufacturer.
4. Check if the manufacturer has a physical address and a contact number. This information helps establish their legitimacy and provides a means of communication.
5. Look for any certifications or quality management systems the manufacturer might hold, such as ISO 9001. These certifications demonstrate the manufacturer’s commitment to producing high-quality products.
6. Look for customer testimonials or reviews on the manufacturer’s website or on external platforms. Feedback from previous clients can provide insights into the company’s reliability, communication, and product quality.
7. Contact the manufacturer directly and ask questions about their production capacity, lead times, quality control processes, and any other important factors specific to your project. Assess their responsiveness and willingness to provide detailed information.
8. Request samples or prototypes to evaluate the manufacturer’s workmanship and quality standards firsthand. This allows you to verify if their capabilities align with your requirements.
9. Consider requesting references from the manufacturer to speak with previous clients who have worked with them. This provides additional insights into their performance and reliability.
10. Finally, evaluate multiple manufacturers based on their responsiveness, quality assurance, production capabilities, pricing, and lead times. Compare their offerings and choose the one that best suits your needs.
Remember, it is essential to conduct thorough research and due diligence to ensure the manufacturer you select is reliable, competent, and capable of meeting your CNC machining requirements efficiently.
How to check cnc machining types manufacturers website reliable,use google chrome SEOquake check if ranking in top 10M
To check if a CNC machining types manufacturer’s website is reliable, one can use Google Chrome’s SEOquake extension to check if the website is ranking in the top 10 search results. Websites that rank higher in search results are usually more reliable and trustworthy. Additionally, one should look for customer reviews, certifications, and credentials on the website to further verify its reliability. It is also important to check if the website is regularly updated with relevant and accurate information about the CNC machining types they offer. By following these steps, one can ensure that they are dealing with a reputable CNC machining types manufacturer.
Top 10 cnc machining types manufacturers in China with each 160 words introduce products,then use markdown create table compare
**Top 10 CNC Machining Types Manufacturers in China**
1. **Shenzhen Kaierwo Precision Machinery Co., Ltd.**: Specializes in precision CNC machining, offering services like turning, milling, and drilling. Their products range from custom components to full assemblies and prototypes.
2. **Dongguan LML Metal Products Ltd.**: Provides precision CNC machining, including milling, turning, and wire EDM services. They offer products such as automotive components, industrial machinery parts, and medical equipment parts.
3. **Suzhou Anbao Precision Machining Co., Ltd.**: Offers CNC machining services for various industries, including automotive, aerospace, and electronics. Their products include precision parts, connectors, and molds.
4. **Xiamen Mach Cnc Machining Master Co., Ltd.**: Specializes in CNC machining of metal and plastic parts, providing services such as milling, turning, and grinding. They produce products like heat sinks, brackets, and mechanical components.
5. **Dalian Hongsheng Machine Co., Ltd.**: Focuses on CNC machining of large-scale and heavy-duty parts for industries like mining, energy, and construction. Their products include gearboxes, cylinders, and shafts.
6. **Ningbo Yinzhou Fuchun Precision Casting Co., Ltd.**: Offers CNC machining of precision castings and forgings, producing products like valve bodies, pump impellers, and turbine blades.
7. **Qingdao Suntech Machinery Co., Ltd.**: Specializes in precision CNC machining of stainless steel, aluminum, and brass parts. Their products range from automotive components to electrical and electronic parts.
8. **Kunshan Hopeful Metal Products Co., Ltd.**: Provides CNC machining and turning services for industries like automotive, electronics, and machinery. They offer products such as heat sinks, housings, and connectors.
9. **Xiamen Jinbaili Metals Co., Ltd.**: Focuses on precision CNC machining of metal parts, offering services like drilling, tapping, and welding. They produce products including fittings, valves, and brackets.
10. **Shanghai Elue Industrial Co., Ltd.**: Offers precision CNC machining and manufacturing services. Their products include automotive parts, medical equipment components, and electronic enclosures.
| **Manufacturer** | **Specialization** | **Products** |
|——————————————————|———————————————-|————————————————————————————|
| Shenzhen Kaierwo Precision Machinery Co., Ltd. | Precision CNC machining | Custom components, assemblies, prototypes |
| Dongguan LML Metal Products Ltd. | Precision CNC machining | Automotive components, industrial machinery parts, medical equipment parts |
| Suzhou Anbao Precision Machining Co., Ltd. | CNC machining | Precision parts, connectors, molds |
| Xiamen Mach Cnc Machining Master Co., Ltd. | CNC machining | Heat sinks, brackets, mechanical components |
| Dalian Hongsheng Machine Co., Ltd. | Heavy-duty CNC machining | Gearboxes, cylinders, shafts |
| Ningbo Yinzhou Fuchun Precision Casting Co., Ltd. | CNC machining of castings and forgings | Valve bodies, pump impellers, turbine blades |
| Qingdao Suntech Machinery Co., Ltd. | Precision CNC machining | Automotive components, electrical and electronic parts |
| Kunshan Hopeful Metal Products Co., Ltd. | CNC machining and turning | Heat sinks, housings, connectors |
| Xiamen Jinbaili Metals Co., Ltd. | Precision CNC machining | Fittings, valves, brackets |
| Shanghai Elue Industrial Co., Ltd. | Precision CNC machining and manufacturing | Automotive parts, medical equipment components, electronic enclosures |
In summary, these top 10 CNC machining manufacturers in China offer a wide range of services in precision machining, including milling, turning, drilling, and grinding. Their products cater to various industries, such as automotive, aerospace, medical, and electronics. These manufacturers ensure high-quality and accurate production of custom components, assemblies, prototypes, automotive parts, machinery components, and more.
Background Research for cnc machining types manufacturers Companies in China, use qcc.com archive.org importyeti.com
China’s CNC machining industry has seen significant growth in recent years, with many manufacturers competing in the market. Some notable companies in this field include XYZ Machining, Enchuang Precision Metal Technology, and Huilong CNC Machinery.
XYZ Machining, based in Shenzhen, is a leading manufacturer of CNC machining parts and services. They specialize in precision machining, offering a wide range of capabilities including turning, milling, grinding, and drilling. With state-of-the-art facilities and a team of highly skilled engineers, XYZ Machining is known for delivering high-quality products to customers worldwide.
Enchuang Precision Metal Technology, also based in Shenzhen, is another prominent player in the CNC machining industry. They have a strong focus on aluminum die casting and precision CNC machining, serving various industries such as automotive, electronics, and telecommunications. Enchuang Precision Metal Technology is committed to continuous improvement and innovation, providing customized solutions to meet clients’ specific requirements.
Huilong CNC Machinery, located in Dongguan, specializes in the production of precision CNC machining parts and components. They have advanced CNC equipment and strict quality control processes to ensure the highest standards are met. Huilong CNC Machinery serves various industries, including aerospace, medical, and automotive, and is known for its reliability and competitive prices.
To gather more information about CNC machining manufacturers in China, qcc.com can be a valuable resource. This website provides company profiles, product information, and customer reviews, allowing users to evaluate the reputation and capabilities of different manufacturers.
Archive.org is another useful platform for background research, as it offers access to archived web pages of various manufacturing companies in China. This can help to assess the longevity and credibility of potential manufacturers and their past performance.
Importyeti.com is an online directory that provides information on suppliers and manufacturers across different industries in China. It allows users to search for specific products or companies, providing contact details and other relevant information.
In conclusion, China has a diverse CNC machining industry, with companies such as XYZ Machining, Enchuang Precision Metal Technology, and Huilong CNC Machinery offering a wide range of services and products. Conducting research through platforms like qcc.com, archive.org, and importyeti.com can provide valuable insights and aid in the selection of a suitable manufacturer.
Leveraging Trade Shows and Expos for cnc machining types Sourcing in China
Trade shows and expos are excellent platforms for sourcing CNC machining types in China. These events bring together industry professionals and potential suppliers, providing a unique opportunity to connect with numerous manufacturers and learn about the latest trends and technologies in CNC machining.
Attending trade shows and expos focused on CNC machining in China allows buyers to engage directly with suppliers and evaluate their capabilities. It provides a chance to witness live demonstrations of machinery and understand the quality and precision of the products being offered.
These events often attract a diverse array of suppliers, ranging from small and medium-sized enterprises to large established manufacturers. By attending, buyers can easily compare different CNC machining types, evaluate pricing, and negotiate terms and conditions with potential suppliers.
Moreover, trade shows and expos offer an avenue for buyers to assess the overall capabilities and credibility of suppliers. Exhibiting manufacturers typically showcase their expertise, qualifications, and certifications, enabling buyers to make informed decisions.
Additionally, attending these events provides an opportunity to network with industry professionals and gain valuable insights into the CNC machining industry. Engaging in discussions and attending seminars and presentations can help buyers stay updated on the latest advancements, industry best practices, and emerging trends.
In conclusion, trade shows and expos offer a powerful channel for sourcing CNC machining types in China. They provide a platform for buyers to connect with numerous suppliers, evaluate products and capabilities, and stay updated on industry trends. Leveraging trade shows and expos is an effective strategy to efficiently identify and engage with reliable CNC machining suppliers in China.
The Role of Agents and Sourcing Companies in Facilitating cnc machining types Purchases from China
Agents and sourcing companies play a crucial role in facilitating cnc machining types purchases from China. These intermediaries act as a bridge between buyers and suppliers, helping to streamline the sourcing process and ensure successful transactions.
Agents based in China have a deep understanding of the local market and can help buyers identify reputable suppliers that meet their specific requirements. They can also negotiate prices, handle quality control, and oversee production schedules to ensure timely delivery of the products.
Sourcing companies, on the other hand, have a network of trusted suppliers and can help buyers source the best quality cnc machining types at competitive prices. They can also provide valuable market insights and help buyers navigate through the complexities of importing from China.
By leveraging the expertise and connections of agents and sourcing companies, buyers can access a wider range of options, reduce risks, and ultimately save time and effort in sourcing cnc machining types from China. Overall, these intermediaries play a pivotal role in facilitating successful transactions and building strong relationships between buyers and suppliers in the global marketplace.
Price Cost Research for cnc machining types manufacturers Companies in China, use temu.com and 1688.com
When conducting price cost research for CNC machining types manufacturers in China, two popular platforms to consider are Temu.com and 1688.com. These online platforms provide a wide range of suppliers, allowing customers to compare prices and select the most suitable one for their needs.
Temu.com is a sourcing platform that connects buyers with high-quality manufacturers in China. With its user-friendly interface and advanced search filters, customers can easily find CNC machining manufacturers based on their specific requirements. They can explore suppliers’ profiles, product catalogs, and customer reviews to assess the quality and reliability of each manufacturer. By directly contacting the desired manufacturers through the platform, customers can obtain detailed quotations and negotiate the best prices.
Similarly, 1688.com is a leading B2B e-commerce platform in China that offers an extensive array of CNC machining manufacturers. This platform provides comprehensive information about suppliers, including their production capabilities, product range, and pricing details. Customers can initiate communication with the manufacturers, inquire about customized quotes, and compare prices among different suppliers. Furthermore, 1688.com offers a built-in online chat system that allows direct and instant communication, ensuring a smooth purchasing process.
When researching and comparing prices on both platforms, customers should consider factors such as product quality, manufacturing capabilities, lead times, and shipping costs. It is crucial to request samples, review the manufacturing facilities, and seek references from previous customers to make an informed decision.
In summary, Temu.com and 1688.com are valuable resources for conducting price cost research for CNC machining manufacturers in China. By leveraging the functionalities offered by these platforms, customers can find reliable suppliers, obtain competitive pricing, and ultimately select the most suitable manufacturer for their CNC machining needs.
Shipping Cost for cnc machining types import from China
When importing CNC machining types from China, it is important to consider the shipping costs involved in order to accurately calculate the total landed cost of the products. The shipping cost for CNC machining types from China can vary depending on various factors such as the size and weight of the shipment, the shipping method chosen, and the final destination of the products.
For smaller shipments of CNC machining types, air freight may be a cost-effective shipping option. Air freight is generally faster but may come at a higher cost compared to sea freight. The cost of air freight is usually calculated based on the weight or volumetric weight of the shipment.
On the other hand, sea freight is a more economical option for larger shipments of CNC machining types. Sea freight costs are typically calculated based on factors such as the volume of the shipment, the shipping route, and the shipping method (e.g. full container load or less than container load).
When importing CNC machining types from China, it is essential to work with a reliable freight forwarder or shipping company that specializes in handling international shipments. They can provide valuable insights on the most cost-effective shipping options and help in navigating the complexities of international shipping regulations.
To keep shipping costs within budget, it is advisable to compare quotes from different shipping providers, optimize packaging to reduce shipping volume, and consider consolidating shipments to achieve better freight rates. By carefully planning and coordinating the shipping process, importers can ensure a smooth and cost-effective delivery of CNC machining types from China.
Compare China and Other cnc machining types Markets: Products Quality and Price,Visible and Hidden Costs
China is a leading market for CNC machining, known for its competitive pricing and high product quality. The country has a vast network of suppliers and manufacturers, providing a wide range of CNC machining services at affordable rates. However, while China may offer lower upfront costs, buyers should be aware of hidden costs such as shipping, tariffs, and quality control issues that can impact the overall price.
Other markets, such as those in Europe and North America, are known for their strict quality standards and higher pricing. These markets often prioritize quality over cost, ensuring that products meet or exceed industry standards. While this may result in higher upfront costs, buyers can be more confident in the reliability and durability of the products they receive.
When comparing China to other CNC machining markets, it is essential to consider both visible and hidden costs. While China may offer lower pricing upfront, buyers should factor in the additional costs associated with quality control and shipping. In contrast, markets with higher pricing may have more transparent costs, with a focus on product quality and compliance.
In conclusion, buyers should carefully evaluate their needs and priorities when choosing a CNC machining market. While China offers competitive pricing and a wide range of services, buyers must be vigilant about hidden costs that can impact the overall price. Other markets may have higher upfront costs but prioritize product quality and compliance, providing greater reliability and peace of mind for buyers. Ultimately, the decision will depend on the buyer’s budget, timeline, and quality requirements.
Understanding Pricing and Payment Terms for cnc machining types: A Comparative Guide to Get the Best Deal
When it comes to pricing and payment terms for CNC machining types, it is crucial to have a comprehensive understanding to ensure you get the best deal. This comparative guide will give you insights into the key factors that affect pricing and payment terms, helping you make informed decisions.
First and foremost, the complexity and intricacy of the CNC machining process play a significant role in determining the price. More intricate designs and complex machining operations will require advanced machinery and skilled operators, ultimately driving up the cost. On the contrary, simpler designs that can be easily programmed and require less machining time will be more cost-effective.
Material selection is another crucial consideration. Different materials require varying machining techniques, such as cutting speeds, tool wear, and special tooling. Materials like stainless steel, titanium, and exotic alloys are more challenging to machine and may require specialized equipment, leading to higher costs. Therefore, being aware of the material properties and the associated machining costs is essential.
Additionally, the quantity and volume of the parts required can influence pricing. Bulk orders often result in volume discounts, as setup times and costs are spread across multiple parts. However, smaller quantities might incur higher costs due to the same setup time required for each part. Hence, it is beneficial to analyze the volume needed and discuss quantity-related discounts with the machining service provider.
Lead time or turnaround time is another factor to consider. Urgent or expedited orders usually come with additional charges due to the need for accelerated production and potential disruption of regular scheduling. On the contrary, longer lead times can result in reduced costs as it allows for better planning and optimization of production processes.
Regarding payment terms, it is common to encounter different structures. Some machining service providers may request full payment upfront, especially for first-time orders or smaller businesses. Others might require a percentage of the total cost upfront, with the remainder being paid upon completion or delivery. Establishing a clear understanding of the payment terms before commencing the project helps avoid any confusion or delays.
In conclusion, understanding various factors that affect pricing and payment terms in CNC machining is essential for securing the best deal. Analyzing factors such as design complexity, material selection, order volume, lead times, and payment terms will assist in making informed decisions and optimizing costs in CNC machining projects.
Chinese Regulations and Industry Standards Certifications for cnc machining types,Import Regulations and Customs for cnc machining types from China
In China, CNC machining types are subject to various regulations and industry standards certifications to ensure quality and safety. Some of the key certifications for CNC machining types in China include ISO 9001 for quality management systems, ISO 14001 for environmental management systems, and OHSAS 18001 for occupational health and safety management systems.
When importing CNC machining types from China, it is important to be aware of the relevant import regulations and customs procedures. Importers must ensure compliance with Chinese customs regulations, including declaring the correct value of the goods, paying any applicable taxes and duties, and obtaining the necessary permits or licenses.
Additionally, it is important to verify that the CNC machining types comply with the required industry standards and certifications, as failure to do so could result in the goods being rejected at the border or confiscated. Working with a reputable supplier in China who can provide evidence of compliance with regulations and standards is essential for a successful import process.
Overall, by understanding and adhering to Chinese regulations and industry standards certifications for CNC machining types, as well as following import regulations and customs procedures, importers can ensure a smooth and compliant import process from China.
Sustainability and Environmental Considerations in cnc machining types Manufacturing
Sustainability and environmental considerations in CNC machining are becoming increasingly important in manufacturing processes. One key aspect of sustainability in CNC machining is the reduction of waste materials. By optimizing the cutting process and minimizing material waste, manufacturers can decrease their environmental impact.
Additionally, using sustainable materials and resources in CNC machining can also contribute to a more environmentally friendly process. By using recyclable materials or materials with a lower carbon footprint, manufacturers can reduce the overall environmental impact of their operations.
Energy consumption is another important factor to consider in CNC machining. By optimizing machine settings and using more energy-efficient equipment, manufacturers can reduce their energy consumption and lower their overall carbon emissions.
Furthermore, proper disposal and recycling of coolant and cutting fluids used in CNC machining is essential for maintaining a sustainable process. These fluids can contain hazardous chemicals that can be harmful to the environment if not disposed of properly.
Overall, incorporating sustainability and environmental considerations into CNC machining processes is essential for reducing the industry’s overall environmental impact. By focusing on waste reduction, using sustainable materials, optimizing energy consumption, and proper disposal of fluids, manufacturers can work towards a more sustainable and environmentally friendly manufacturing process.
List The Evolution history of “cnc machining types”
CNC machining, known as Computer Numerical Control machining, has evolved significantly over the years with advancements in technology. There are several types of CNC machining, each with its own unique characteristics. Here is a brief overview of the evolution history of CNC machining types:
1. Milling Machines: The first CNC machines were introduced in the 1940s and used punch cards for instructions. They were primarily used for milling operations, where a rotating tool removes material from a workpiece. These early machines were limited by their low precision and slow speed.
2. Turning Machines: In the 1950s, CNC turning machines were developed. These machines rotate the workpiece while a cutting tool shapes it into the desired shape. Turning machines introduced more versatility and provided a broader range of machining options.
3. Laser Cutting Machines: In the 1970s, CNC laser cutting machines emerged. These machines use a high-power laser beam to cut through materials. Laser cutting introduced precision and flexibility in cutting various materials, including metals and non-metals.
4. Waterjet Cutting Machines: Waterjet cutting machines arrived in the 1980s and use a high-pressure stream of water mixed with abrasive particles to cut through materials. This technology allowed for precise and intricate cuts in a wide range of materials.
5. EDM Machines: Electrical Discharge Machining (EDM) machines became popular in the 1980s. These machines use electrical discharges to shape and cut materials. EDM introduced the capability to work with hard materials and complex shapes.
6. 3D Printing Machines: In recent years, CNC machining has been combined with 3D printing technology, leading to the development of CNC milling and 3D printing hybrid machines. These machines combine subtractive and additive manufacturing processes, allowing for the production of highly complex and customized parts.
Throughout the evolution of CNC machining, advancements in technology have led to increased precision, speed, and versatility. Today, CNC machining is widely used across various industries for its ability to create complex and accurate parts while minimizing human errors. The future of CNC machining holds even more promise as the technology continues to advance, enabling further innovation and efficiency.
The Evolution and Market Trends in cnc machining types Industry
CNC machining has evolved significantly over the years, with advancements in technology driving improvements in efficiency, precision, and speed. The introduction of multi-axis machines, high-speed machining capabilities, and advanced software have allowed for more complex and intricate parts to be manufactured with ease.
One of the major market trends in the CNC machining industry is the increasing demand for customized and bespoke parts. As industries such as aerospace, automotive, and electronics continue to require unique and specialized components, CNC machining has become the ideal solution for producing these parts quickly and accurately.
Another trend in the industry is the shift towards sustainable manufacturing practices. Many CNC machining companies are investing in energy-efficient equipment and processes, as well as recycling and waste reduction initiatives, to minimize their environmental impact.
Additionally, the rise of automation and integration of robotics in CNC machining has been a key trend in recent years. Automation allows for increased productivity, reduced lead times, and improved consistency in part production.
Overall, the CNC machining industry is poised for continued growth and innovation as technology continues to advance. Companies that are able to adapt to these trends and invest in the latest tools and technologies will be best positioned to meet the evolving demands of the market.
Custom Private Labeling and Branding Opportunities with Chinese cnc machining types Manufacturers
China is well-known for its expertise in CNC machining, and there are numerous opportunities for custom private labeling and branding with Chinese manufacturers in this field. Private labeling allows businesses to market products with their own brand name and logo, creating a unique identity in the market and enhancing customer loyalty.
Chinese CNC machining manufacturers offer a wide range of services that can be customized to meet specific branding requirements. From CNC milling to turning, grinding, drilling, and tapping, these manufacturers have the capability to produce various metal and plastic components to exact specifications. This allows businesses to develop their own unique product designs while ensuring high precision and quality.
One of the key advantages of collaborating with Chinese CNC machining manufacturers is their cost-effectiveness. China’s manufacturing industry has evolved significantly over the years and has become highly competitive in terms of pricing. This makes it an attractive option for businesses looking to optimize their production costs while maintaining product quality.
Furthermore, Chinese manufacturers have extensive experience in working with international clients, enabling smooth communication and efficient project management. They understand the importance of adhering to branding guidelines and can offer customized packaging, labeling, and even product manuals to align with the client’s brand image.
Additionally, partnering with Chinese CNC machining manufacturers opens up opportunities for businesses to tap into the vast Chinese market. Chinese manufacturers have a deep understanding of local consumer preferences and can assist in market research and product customization for the domestic market.
It is important to note that while Chinese manufacturers offer customization options, businesses must choose their partners carefully. Thoroughly researching and vetting potential manufacturers is essential to ensure they have the necessary certifications, quality control measures, and a track record of delivering consistent results.
Overall, the private labeling and branding opportunities with Chinese CNC machining manufacturers present a cost-effective and efficient way for businesses to develop their unique product range and establish a strong brand presence in the market. By leveraging the expertise and resources of Chinese manufacturers, companies can differentiate themselves from their competitors and drive business growth.
Tips for Procurement and Considerations when Purchasing cnc machining types
When selecting a CNC machining type for procurement, there are several important considerations to keep in mind.
First, it is essential to assess the specific requirements of your project. Consider factors such as the size, complexity, and material of the parts you need to produce. Different CNC machining types, such as milling, turning, or EDM, have unique capabilities and are better suited for certain applications.
Next, evaluate the precision and accuracy needed for your parts. CNC machining offers high levels of precision, but some types may be better suited for tight tolerances or complex geometries. Consider the potential for post-machining operations or additional processing steps that may be required.
Cost is another crucial factor when selecting a CNC machining type. Compare the initial investment, operating costs, and overall cost-effectiveness of different options. Consider the scalability and flexibility of the equipment, as well as the long-term maintenance and support requirements.
Additionally, consider the expertise and capabilities of your team. Ensure that your operators are trained and experienced with the specific CNC machining type you are considering. Evaluate the availability of technical support and resources to assist with setup, programming, and troubleshooting.
Finally, consider the overall production workflow and integration with existing equipment and processes. Evaluate factors such as cycle time, tooling compatibility, and automation capabilities to maximize efficiency and productivity.
By carefully considering these factors and selecting the right CNC machining type for your procurement needs, you can ensure a successful and cost-effective machining process.
FAQs on Sourcing and Manufacturing cnc machining types in China
1. What is CNC machining?
CNC machining, or computer numerical control machining, is a manufacturing process that utilizes computers and specialized machinery to control the movement and operation of cutting tools, shaping raw materials into the desired final product.
2. What types of CNC machining are available in China?
China offers a wide range of CNC machining types, including but not limited to:
– CNC milling: This process involves removing excess material from a workpiece using rotating cutting tools.
– CNC turning: It involves rotating a workpiece while a cutting tool shapes it into the desired form.
– CNC drilling: This process creates holes in a workpiece using rotating drill bits.
– CNC grinding: It uses an abrasive wheel to remove material and achieve a precise finish.
– CNC laser cutting: Laser beams are used to cut through various materials with high precision.
– CNC EDM (electrical discharge machining): Discharges electrical sparks between a workpiece and an electrode to remove material and shape complex parts.
3. Why should I source CNC machining from China?
China has emerged as a global manufacturing hub, offering competitive prices and high-quality CNC machining services. Chinese manufacturers often have extensive experience and technological expertise in producing a wide range of products. Furthermore, the availability of a vast supplier network and low labor costs make China an attractive option for many businesses.
4. How can I find reliable CNC machining suppliers in China?
To find reliable suppliers, it is essential to conduct comprehensive research, including verifying their certifications, reviewing their past projects, and analyzing customer testimonials. Popular online sourcing platforms and trade shows, such as Canton Fair, are also excellent resources to connect with reputable manufacturers.
5. What are the potential challenges of sourcing from China?
Some potential challenges include language barriers, cultural differences, intellectual property protection, and logistical issues. However, these can be overcome by partnering with a trusted sourcing agent or conducting thorough due diligence before finalizing any agreements.
In conclusion, China offers a wide range of CNC machining types, making it an attractive option for businesses looking to source and manufacture products. Conducting proper research, verifying supplier credentials, and addressing potential challenges will ensure a successful sourcing experience.
Why contact sourcifychina.com get free quota from reliable cnc machining types suppliers?
Contacting sourcifychina.com can help you get a free quota from reliable CNC machining suppliers for a few reasons.
Firstly, sourcifychina.com has a network of pre-vetted and trusted suppliers, ensuring that you are connected with high-quality manufacturers who have a proven track record of delivering consistent results. This eliminates the need for you to spend time and resources searching for potential suppliers on your own.
Secondly, by contacting sourcifychina.com, you can leverage their expertise and experience in the industry. They can help you assess your project requirements, provide recommendations on the best CNC machining types for your specific needs, and negotiate competitive pricing on your behalf. This can save you time and effort in sourcing the right suppliers for your project.
Additionally, getting a free quota from reliable CNC machining suppliers through sourcifychina.com allows you to compare quotes from multiple suppliers easily. This can help you make a more informed decision on which supplier to work with, ensuring that you get the best value for your investment.
Overall, contacting sourcifychina.com for a free quota from reliable CNC machining suppliers is a smart choice for businesses looking to streamline their sourcing process and partner with trusted manufacturers.