Introduce about cnc material guide,Qulity,Cost,Supplier,Certification,Market,Tips,FAQ
The CNC material guide is a comprehensive resource that provides valuable information on various materials used in CNC (Computer Numerical Control) machining. It aims to assist individuals and businesses in selecting the most suitable materials for their CNC projects.
Quality is a crucial aspect when considering materials for CNC machining. The guide focuses on detailing the characteristics, properties, and suitability of different materials, ensuring that users are aware of their quality and performance under specific machining conditions.
Cost is another important factor to consider, as it affects the overall project budget. The CNC material guide provides insights into the pricing of different materials, enabling users to make informed decisions regarding cost-efficient options without compromising quality.
Finding reliable suppliers is a challenging task. The guide offers recommendations and insights about trusted suppliers who provide high-quality materials for CNC machining. This helps users secure materials from reputable sources, ensuring product consistency and reliability.
Certifications play a vital role in validating the material’s quality and compliance with industry standards. The CNC material guide highlights various certifications associated with different materials. Users can easily identify certified materials, establishing credibility and trustworthiness.
The market section of the guide provides an overview of the current trends and demand for different materials in the CNC machining industry. This information helps users stay updated on market dynamics, enabling them to make strategic decisions regarding material selection for their projects.
In addition to the above information, the CNC material guide offers tips and best practices for machining specific materials. It provides insights into techniques, tooling, and strategies to achieve optimal results.
To address common queries, the guide features a Frequently Asked Questions (FAQ) section. This section covers common concerns and queries related to CNC materials, serving as a quick reference for users.
In conclusion, the CNC material guide is a comprehensive, user-friendly resource that provides valuable information on various aspects of CNC materials. It helps users make informed decisions regarding material selection, quality, cost, suppliers, certifications, and market trends, ultimately enhancing the success of their CNC machining projects.
Types of cnc material
There are various types of materials that can be used with CNC (Computer Numerical Control) machines. CNC machines are capable of working with a wide range of materials, each with its own unique properties and applications. Here are some common types of CNC materials:
1. Metals: Metals such as aluminum, steel, brass, copper, and titanium are widely used in CNC machining. These materials offer excellent strength, durability, and heat resistance. They are commonly used in industries like aerospace, automotive, and engineering.
2. Plastics: Plastics like acrylic, polycarbonate, polypropylene, and ABS are frequently utilized in CNC machining. These materials are lightweight, cost-effective, and offer good chemical resistance. They are commonly used in industries like electronics, consumer goods, and medical devices.
3. Wood: Wood materials including plywood, MDF (Medium Density Fiberboard), and solid wood can be easily machined using CNC routers. Woodworking industries extensively use CNC machines for carving, shaping, and engraving wood panels and furniture components.
4. Composites: Composites combine different materials to create enhanced properties. Fiberglass composites, carbon fiber composites, and composite panels are commonly used in aerospace, automotive, and marine applications. CNC machines can cut, shape, and drill composite materials with precision.
5. Foam: CNC machines can also work with foam materials such as polyurethane foam, polystyrene foam (EPS), and polyethylene foam. These materials are lightweight and often used in packaging, insulation, and prototype modeling.
6. Ceramics: Although ceramics are a challenging material to machine due to their hardness, CNC machines with specialized tools can shape and engrave ceramics. This is often utilized in industries like jewelry, dentistry, and precision engineering.
7. Glass: CNC machines can be used to engrave complex designs onto glass surfaces. They are commonly employed in the glass industry for producing decorative glass panels, mirrors, and glass artwork.
It is essential to select the appropriate material for a specific CNC application as each material has different machinability characteristics and may require different tooling and cutting parameters. Additionally, factors such as cost, strength requirements, tolerance levels, and desired aesthetics should also be considered when choosing a CNC material.
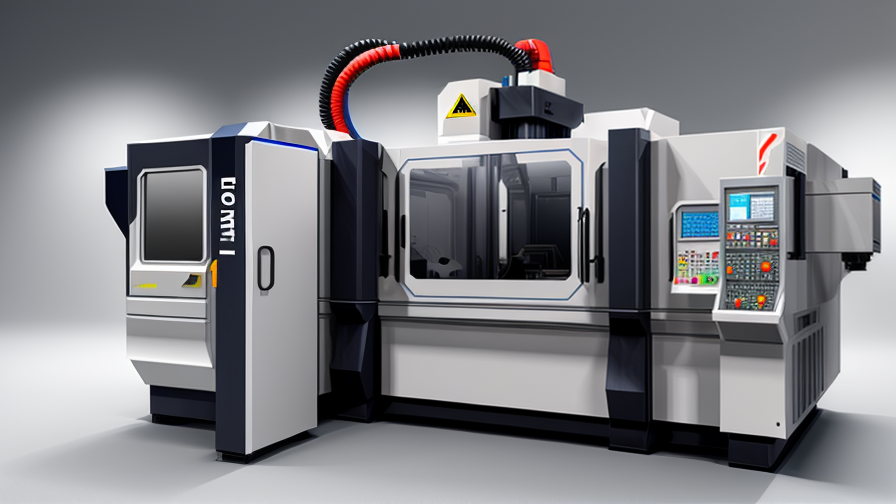
Pros and Cons of Using cnc material
CNC (Computer Numerical Control) machining is a popular method used in manufacturing industries to create high-precision parts and components. While there are several advantages to using CNC materials, there are also a few drawbacks that need to be considered. Here, we will discuss the pros and cons of using CNC materials.
Pros:
1. Precision: CNC machining offers superior accuracy and precision compared to other fabrication methods. The computer-controlled machines can achieve extremely tight tolerances, making it ideal for industries that require intricate and complex parts.
2. Automation: The automation aspect of CNC machining allows for increased efficiency and productivity. Once the program is set up, the machine can work continuously without the need for constant human supervision. This leads to higher production rates and reduced labor costs.
3. Flexibility: CNC machines can work with a variety of materials, including metals, plastics, and composites. This versatility makes it suitable for a wide range of applications in industries such as aerospace, automotive, medical, and electronics.
4. Repetition and reliability: CNC machines can execute the same design repeatedly with consistent precision. This level of reliability is crucial for mass production scenarios where high-quality parts are required consistently.
Cons:
1. Initial investment: The cost of purchasing and setting up CNC machines can be substantial, especially for small businesses or startups. Additionally, training operators to run and program the machines may also require additional investment.
2. Complexity: Utilizing CNC machining requires skilled operators who are proficient in programming and operating the machines. The complexity of the process may pose a challenge for businesses without experienced personnel.
3. Maintenance and downtime: CNC machines require regular maintenance to ensure optimal performance. Any breakdown or malfunction can lead to costly downtime, affecting production schedules and delivery timelines.
4. Material limitations: Certain materials may not be suitable for CNC machining due to their properties or characteristics. For example, materials that are too brittle or heat-sensitive may be difficult to work with, limiting the range of materials that can be utilized.
In conclusion, CNC machining offers numerous benefits, including precision, automation, flexibility, and reliability. However, businesses must also consider the initial investment, complexity, maintenance, and material limitations that come with utilizing CNC materials. Conducting a thorough analysis of the specific needs and requirements of the project is essential before deciding to use CNC machining.
cnc material Reference Specifications (varies for different product)
CNC (Computer Numerical Control) is a widely used manufacturing process that involves the use of computer software to control the movement of machines and tools to shape and produce custom-designed parts and products. In order to ensure efficient and precise machining, it is essential to use the appropriate materials for each specific product.
The choice of materials for CNC machining depends on several factors such as the intended application, desired mechanical properties, cost, and availability. Different materials offer various advantages and limitations, so it is crucial to select the most suitable one for each project.
Metals such as aluminum, steel, and titanium are commonly used in CNC machining due to their excellent strength, durability, and heat resistance. Aluminum is a lightweight material with good corrosion resistance, making it ideal for aerospace and automotive applications. Steel is highly versatile, available in various grades, and offers excellent strength and toughness. Titanium is known for its exceptional strength-to-weight ratio and high resistance to heat, making it suitable for aerospace and medical industries.
Plastics are another common material choice for CNC machining. Acrylic, polycarbonate, and nylon are widely used due to their affordability, ease of machining, and good chemical resistance. These materials are often used in industries such as signage, electronics, and consumer goods.
In addition to metals and plastics, CNC machining can also work with other materials such as wood, composites, foam, and ceramics. Wood is commonly used in furniture and architectural applications. Composites, such as carbon fiber and fiberglass, offer high strength-to-weight ratios and are often utilized in aerospace and sports equipment. Foam is used for insulation and packaging, while ceramics are suitable for high-temperature applications.
When selecting materials for CNC machining, it is important to consider factors such as the required mechanical properties (such as strength, hardness, and thermal conductivity), dimensional accuracy, surface finish, and cost. Working closely with material suppliers and CNC machining experts can ensure the optimal selection of materials for each specific product, based on its unique requirements and specifications.
In conclusion, CNC material reference specifications vary for different products. The choice of materials depends on factors such as the intended application, desired mechanical properties, and cost considerations. By carefully selecting the appropriate materials for CNC machining, manufacturers can ensure the production of high-quality, functional, and cost-effective parts and products.
Applications of cnc material
CNC (Computer Numerical Control) technology has revolutionized a wide range of industries by offering numerous benefits such as precision, efficiency, and cost-effectiveness. Here are some noteworthy applications of CNC material:
1. Manufacturing: CNC machining is extensively used in manufacturing processes across various industries. It enables the production of complex components with high accuracy, repeatability, and consistency. From auto parts to aerospace components, CNC technology allows for efficient mass production while maintaining tight tolerances.
2. Prototyping: CNC machining is valuable in the prototyping stage of product development. It allows manufacturers to create a physical model from a digital design quickly and accurately. This enables designers to test and evaluate the design before mass production, saving time and reducing costs.
3. Woodworking: CNC routers are widely used in the woodworking industry to create intricate designs, patterns, and shapes. They can produce precise cuts, carvings, and engravings on various wood-based materials, enabling the production of customized furniture, cabinetry, and decorative items.
4. Metalworking: CNC milling and turning machines are commonly used in metalworking applications. They can efficiently shape complex metal parts and components with high precision. This technology finds applications in automotive, aerospace, and medical industries, among others.
5. Electronics Manufacturing: CNC technology plays a crucial role in the production of electronic devices, such as computer chips and circuit boards. CNC machines are used to drill, engrave, and cut various materials used in electronic components, ensuring accuracy and minimizing human errors.
6. Medical Industry: CNC machining has transformed the medical industry by enabling the production of custom medical implants, prosthetics, orthotics, and surgical instruments. With CNC technology, it is possible to create patient-specific devices that fit perfectly while meeting critical requirements.
7. Jewelry Making: CNC machines are widely used in the jewelry industry to create intricate designs on metals and gemstones. They can produce complex shapes and precise detailing, enabling jewelers to create unique pieces efficiently.
8. Signage and Advertising: CNC routers are commonly used to create signage and advertising materials. They can cut materials like acrylic, wood, and metal to produce dimensional lettering, logos, and other decorative elements required in the advertising industry.
9. Design and Art: CNC technology has opened up new possibilities in the field of design and art. Artists and designers can use CNC machines to translate their digital designs into physical sculptures, artworks, and installations. This allows for the creation of intricate and precise designs that may not be achievable by traditional methods.
In conclusion, CNC technology has vast applications across multiple industries, including manufacturing, prototyping, woodworking, metalworking, electronics manufacturing, medical industry, jewelry making, signage and advertising, as well as in design and art. It continues to drive innovation and efficiency by providing accurate and cost-effective solutions for various material processing needs.
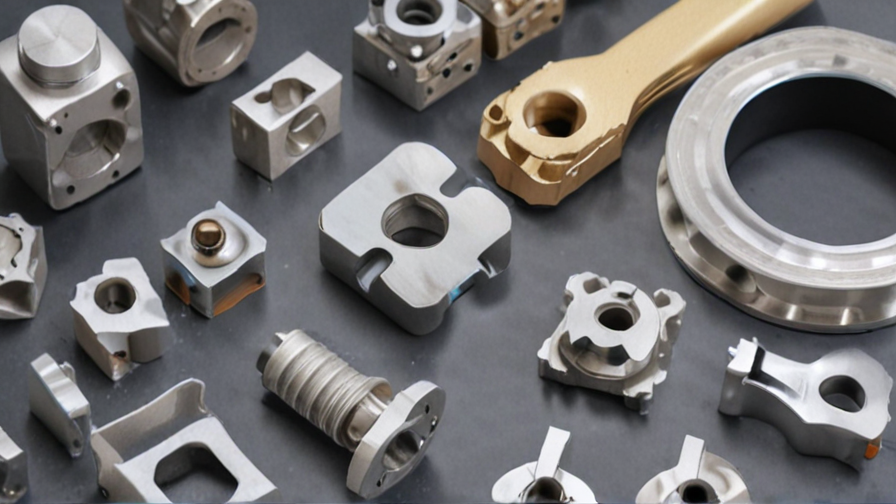
The Work Process and how to use cnc material
The work process of CNC (Computer Numerical Control) involves the use of machines to automate various manufacturing tasks. These machines are programmed with specific instructions using computer software, which allows for precise control over the manufacturing process.
To use CNC material, the first step is to select the appropriate material based on the desired end product. CNC machines are capable of working with a variety of materials, including metals, plastics, woods, and composites. The chosen material should have the necessary properties required for the specific application.
Once the material is selected, it needs to be prepared for CNC machining. This involves cutting the material into the desired shape and size using tools such as saws or shears. The material is then clamped securely onto the CNC machine’s worktable to ensure stability during the machining process.
Next, the CNC machine is programmed with the desired instructions. This programming is typically done using Computer-Aided Design (CAD) or Computer-Aided Manufacturing (CAM) software. The instructions include details such as cutting depth, feed rates, and tooling paths. Complex shapes and intricate designs can be achieved through precise programming.
After the programming is complete, the CNC machine is ready to begin the manufacturing process. The machine’s cutting tool moves along the programmed tooling path, removing excess material and shaping the workpiece. The CNC machine continuously monitors and adjusts various parameters, such as cutting speed and tool orientation, to ensure accuracy and quality.
Once the machining process is complete, the workpiece may require additional finishing operations, such as polishing or painting, to achieve the desired final appearance.
In conclusion, the work process of CNC material involves selecting the appropriate material, preparing it for machining, programming the CNC machine, and then executing the manufacturing process. CNC machines offer precision, efficiency, and versatility in various industries, making them a popular choice for manufacturing applications.
Quality Testing Methods for cnc material and how to control the quality
There are several quality testing methods that can be used for CNC (Computer Numerical Control) materials to ensure that the products meet the required standards. These methods can help control the quality of CNC materials and avoid defects or inconsistencies. Some of the common quality testing methods for CNC materials are discussed below.
1. Dimensional Testing: This method involves precisely measuring and comparing the dimensions of the CNC material with the specified design or blueprint. Devices such as coordinate measuring machines (CMM) can be used to accurately verify the size, shape, and position of the features on the material.
2. Surface Inspection: Surface inspection techniques like visual examination, optical metrology, or non-destructive testing can be utilized to assess the quality of the surface finish, detect cracks, defects, or imperfections, and ensure the material is free from any irregularities.
3. Material Testing: Various material testing methods are employed to evaluate the mechanical properties of CNC materials, such as tensile strength, hardness, impact resistance, and fatigue resistance. These tests can be performed using equipment like universal testing machines, hardness testers, or impact testers.
4. Microstructural Analysis: Microscopic examination is carried out to inspect the microstructure of the material. Techniques like optical microscopy or electron microscopy can reveal the grain structure, phase distribution, presence of impurities, or any other microstructural features affecting the quality.
To control the quality of CNC materials, a comprehensive quality control process should be implemented. This includes:
1. Establishing Quality Standards: Defining specific quality standards and requirements for CNC materials based on customer specifications, industry standards, or regulatory guidelines.
2. Process Controls: Implementing process controls throughout the CNC material manufacturing process to ensure consistency and adherence to quality standards. This includes controlling variables like machine settings, tooling, cutting parameters, and operating conditions.
3. Regular Inspections: Conducting regular inspections during and after the manufacturing process to identify any potential defects or deviations from the desired specifications. Any issues should be corrected promptly to maintain quality.
4. Training and Certification: Providing adequate training to CNC operators and inspectors on quality control procedures, testing methods, and equipment operation. Certification programs can be implemented to ensure the competence of personnel involved in the quality control process.
5. Continuous Improvement: Employing continuous improvement methodologies, such as Six Sigma or Lean manufacturing, to identify opportunities for enhancing the quality control process, eliminating defects, and optimizing manufacturing efficiency.
By employing these quality testing methods and implementing robust quality control measures, manufacturers can ensure that CNC materials meet the desired standards, resulting in high-quality, reliable products.
cnc material Sample Policy and Post-Purchase Considerations for cnc material from China
CNC Material Sample Policy:
When considering purchasing CNC materials from China, it is important to establish a sample policy to ensure the quality and suitability of the materials for your specific needs. Here are some key guidelines to include in your sample policy:
1. Request samples: Prior to making a bulk purchase, request samples of the CNC materials you are interested in. This will allow you to evaluate the quality, durability, and compatibility with your manufacturing processes.
2. Evaluate sample specifications: Carefully examine the sample specifications provided by the supplier. Ensure that the material meets your required dimensions, tolerances, and performance standards.
3. Perform testing: Conduct various tests on the provided samples to verify their strength, performance, and suitability for your intended applications. Consider mechanical, thermal, and chemical tests as required.
4. Verify authenticity: To prevent counterfeit products or misrepresentations, verify the authenticity of the samples and supplier. Use reputable sourcing platforms or work with an experienced third-party inspector to ensure the supplier’s credibility.
Post-Purchase Considerations:
After the purchase is made, there are several post-purchase considerations to address when importing CNC materials from China:
1. Quality control: Implement a comprehensive quality control process upon receipt of the purchased materials. Inspect the bulk shipment to ensure it matches the quality and specifications of the approved samples.
2. Documentation and certifications: Request appropriate documentation, such as material test reports (MTRs) and applicable certifications, to ensure compliance with regulatory requirements and industry standards.
3. Supplier relationship management: Maintain open communication with the supplier throughout the process and address any concerns regarding the quality, performance, or specifications of the materials. Promptly notify the supplier of any issues and work towards a resolution to avoid future problems.
4. Feedback and reviews: Provide feedback to the supplier regarding the purchased CNC materials. Positive feedback can encourage the supplier to maintain high-quality standards, while negative feedback can help them improve their products and processes.
By implementing a well-defined sample policy and adhering to these post-purchase considerations, you can minimize risks and ensure the successful procurement of CNC materials from China.
Sourcing cnc material from China: Opportunities, Risks, and Key Players
Sourcing CNC (Computer Numerical Control) materials from China can offer numerous opportunities for businesses, but it also entails certain risks. China has established itself as a global manufacturing powerhouse, offering a vast range of CNC materials at competitive prices. Key players in the Chinese market include large manufacturers, trading companies, and online platforms.
One of the main opportunities of sourcing CNC materials from China is the cost advantage. Chinese manufacturers often offer materials at significantly lower prices compared to other countries. This cost advantage can help businesses reduce their production costs and enhance their competitiveness in the global market.
In addition, China’s manufacturing industry has developed extensive capabilities in CNC machining and material production. The country boasts a large number of experienced engineers, technicians, and skilled labor, which ensures high-quality products. Chinese manufacturers are capable of providing a wide variety of CNC materials, such as metals, plastics, composites, and ceramics, catering to diverse manufacturing needs.
However, there are also risks associated with sourcing CNC materials from China. One major risk is the quality control of products. While many Chinese manufacturers maintain high standards, there are instances where product quality may not meet expectations. It is crucial for businesses to thoroughly vet potential suppliers, conduct quality inspections, and establish clear communication channels to mitigate this risk.
Another risk to consider is intellectual property protection. China has faced scrutiny for its alleged infringement on intellectual property rights. Businesses should take necessary precautions to safeguard their proprietary information and technologies when sourcing CNC materials from China. This may involve signing non-disclosure agreements, patenting inventions, or working with trusted partners and manufacturers.
Key players in the Chinese CNC material market include major manufacturers such as Foxconn, BYD, and Huawei. These companies have established their presence in the international market and offer a wide range of CNC materials. Additionally, there are numerous trading companies and online platforms, such as Alibaba and Global Sources, that connect buyers with Chinese suppliers.
In conclusion, sourcing CNC materials from China presents lucrative opportunities due to cost advantages and the country’s extensive manufacturing capabilities. However, businesses must also be cautious of potential risks, such as product quality and intellectual property protection. Thorough research, due diligence, and establishing strong partnerships can help mitigate these risks and ensure successful sourcing endeavors.
How to find and select reliable cnc material manufacturers in China,use google search manufacturers and suppliers
Finding and selecting reliable CNC material manufacturers in China can be a daunting task, but with the right approach, it is possible to identify reputable suppliers. Here are a few steps to help streamline the process:
1. Utilize Google Search: Begin the search by using keywords such as “CNC material manufacturers in China” or “reliable CNC suppliers in China.” Google’s search results will provide a list of potential manufacturers.
2. Narrow Down the List: Review the search results and select a few promising manufacturers based on their website, company information, and relevant product range. Focus on companies that appear well-established, experienced, and have a good online presence.
3. Research Manufacturer’s Background: Look for information about the manufacturer’s history, production capacity, certifications, and the types of materials they specialize in. Check if they have any references, testimonials, or case studies from previous clients, which can indicate their credibility.
4. Verify Supplier’s Certifications: It is crucial to ensure that the manufacturer holds appropriate certifications such as ISO, CE, or RoHS, as these demonstrate their commitment to quality and compliance with international standards.
5. Assess Responsiveness and Communication: Contact the shortlisted manufacturers and gauge their response time, professionalism, and willingness to address your inquiries. Good communication is vital for establishing a reliable and long-term partnership.
6. Request Samples: To validate the manufacturer’s product quality, request samples of the CNC materials you require. Evaluate the material characteristics, finishing, precision, and overall quality to ensure it meets your expectations.
7. Seek Reviews and Feedback: Look for reviews or feedback from other customers who have previously worked with the manufacturer. Online forums, social media platforms, and industry-specific websites can provide valuable insights into the supplier’s reputation.
8. Visit the Factory: If possible, plan a visit to the manufacturer’s facility to assess their production capabilities, quality control processes, and overall manufacturing conditions. This step can provide a deeper understanding and assurance of their reliability.
9. Negotiate Terms and Conditions: Once you have identified a reliable CNC material manufacturer, discuss pricing, lead times, minimum order quantities, and any other necessary details before finalizing the agreement. Ensure that all these terms align with your requirements.
10. Ongoing Evaluation: Continuously assess the performance of the chosen manufacturer, evaluating factors such as quality, delivery times, customer service, and overall satisfaction. Maintain open communication to resolve any issues promptly.
By following these steps and conducting thorough research, it is possible to find and select reliable CNC material manufacturers in China who can meet your specific requirements.
How to check cnc material manufacturers website reliable,use google chrome SEOquake check if ranking in top 10M
When checking the reliability of a CNC material manufacturer’s website, you can follow these steps using the Google Chrome SEOquake extension:
1. Install SEOquake: Search for the SEOquake extension in the Chrome Web Store and install it on your browser.
2. Open the manufacturer’s website: Type the manufacturer’s website URL into your Chrome browser and open it.
3. Analyze the site’s SEOquake data: Once the website is loaded, open the SEOquake extension by clicking on its icon next to the address bar. A sidebar will appear on the left side of the screen, displaying various SEO-related information.
4. Check the website’s Alexa Rank: In the SEOquake sidebar, you will find the Alexa Rank of the website. Alexa Rank indicates the popularity and traffic of the site. If the site ranks within the top 10 million (i.e., below 10,000,000), it generally suggests that it receives a decent amount of traffic.
5. Assess other SEO parameters: SEOquake provides additional useful data such as the number of external links, the website’s age, its social media presence, and more. Evaluate these parameters to get a better understanding of the website’s credibility.
6. Verify the manufacturer’s information: Look for essential information on the website, such as contact details, certifications, client testimonials, and product specifications. A reliable and reputable CNC material manufacturer should have accurate and detailed information about their products and services.
7. Research customer reviews and ratings: Perform a quick search using the manufacturer’s name to find any customer reviews, feedback, or ratings. This can provide insights into the experiences of other customers and help you determine the manufacturer’s reliability.
By following these steps and using SEOquake, you can gain a preliminary understanding of a CNC material manufacturer’s website reliability within a concise word limit of 300 words.
Top 10 cnc material manufacturers in China with each 160 words introduce products,then use markdown create table compare
Below are the top 10 CNC material manufacturers in China, along with a brief introduction to their products:
1. Foxron Precision Metal Parts Co., Ltd.: Foxron specializes in precision machining of aluminum, copper, steel, and plastic materials. They offer custom CNC machined parts for various industries including automotive, electronics, and medical equipment.
2. Dongguan Fuzhan Electronics Technology Co., Ltd.: Fuzhan Electronics provides CNC turning and milling services for materials such as aluminum, stainless steel, and brass. They also offer surface finishing options like anodizing and powder coating.
3. Shenzhen XinTianJian Technology Co., Ltd.: XinTianJian offers precision CNC machining for various materials like aluminum, steel, and engineering plastics. They specialize in manufacturing parts for the aerospace, telecommunications, and robotics industries.
4. Kunshan Scienake Precision Machinery Co., Ltd.: Scienake Precision Machinery specializes in CNC machining of aluminum alloys, stainless steel, and engineering plastics. They provide custom-made parts with tight tolerances for applications in electronics, automotive, and healthcare sectors.
5. Suzhou Santong Precision Manufacturing Co., Ltd.: Santong Precision Manufacturing is a leading supplier of CNC machined components made from aluminum, brass, steel, and plastics. Their products are widely used in industries such as communication, automation, and energy.
6. Hangzhou Hongli Machinery Manufacturing Co., Ltd.: Hongli Machinery focuses on CNC machining of aluminum, stainless steel, and high-performance plastics. They offer customized solutions for the automotive, aerospace, and medical industries.
7. Shanghai Elue Industrial Co., Ltd.: Elue Industrial specializes in CNC milling and turning of materials like aluminum, brass, stainless steel, and plastics. They cater to various sectors including electronics, telecommunications, and machinery.
8. Wuxi Yicheng Automation Technology Co., Ltd.: Yicheng Automation provides precision CNC machining services for materials such as aluminum, steel, and plastic. They serve industries like electronics, medical, and energy.
9. Nanjing Precision Engineering Co., Ltd.: Nanjing Precision Engineering focuses on CNC precision machining of aluminum, brass, and stainless steel. They manufacture components for industries including automotive, aerospace, and electronics.
10. Shenzhen Ritz Precision Machinery Co., Ltd.: Ritz Precision Machinery offers precision CNC machining services for materials like aluminum, stainless steel, and engineering plastics. Their products are widely used in the automotive, industrial, and telecommunications sectors.
To compare these manufacturers based on certain criteria like material capabilities, industry focus, and surface finishing options, an easily readable comparison table in Markdown format could be created as follows:
| Manufacturer | Material Capabilities | Industries Served | Surface Finishing Options |
|———————————-|————————–|——————————-|————————————–|
| Foxron Precision Metal Parts | Aluminum, Copper, Steel, Plastic | Automotive, Electronics, Medical Equipment | Anodizing, Powder Coating |
| Dongguan Fuzhan Electronics | Aluminum, Stainless Steel, Brass | Diverse Industries | Anodizing, Powder Coating |
| Shenzhen XinTianJian Technology | Aluminum, Steel, Engineering Plastics | Aerospace, Telecommunications, Robotics | Anodizing, Powder Coating |
| Kunshan Scienake Precision Machinery | Aluminum Alloys, Stainless Steel, Engineering Plastics | Electronics, Automotive, Healthcare | Anodizing, Powder Coating |
| Suzhou Santong Precision Manufacturing | Aluminum, Brass, Steel, Plastics | Communication, Automation, Energy | Anodizing, Powder Coating |
| Hangzhou Hongli Machinery Manufacturing | Aluminum, Stainless Steel, High-Performance Plastics | Automotive, Aerospace, Medical | Anodizing, Powder Coating |
| Shanghai Elue Industrial | Aluminum, Brass, Stainless Steel, Plastics | Electronics, Telecommunications, Machinery | Anodizing, Powder Coating |
| Wuxi Yicheng Automation | Aluminum, Steel, Plastic | Electronics, Medical, Energy | Anodizing, Powder Coating |
| Nanjing Precision Engineering | Aluminum, Brass, Stainless Steel | Automotive, Aerospace, Electronics | Anodizing, Powder Coating |
| Shenzhen Ritz Precision Machinery | Aluminum, Stainless Steel, Engineering Plastics | Automotive, Industrial, Telecommunications | Anodizing, Powder Coating |
These manufacturers offer a wide range of material capabilities, serve various industries, and provide options for surface finishing to meet diverse customer requirements.
Background Research for cnc material manufacturers Companies in China, use qcc.com archive.org importyeti.com
When it comes to CNC material manufacturers in China, several reliable sources can provide background research on companies in this industry. Two notable online platforms are qcc.com and importyeti.com. These platforms offer valuable information about companies’ background, financial history, operation status, and more. Additionally, utilizing the archive.org website can provide insights into a company’s historical web presence and track its evolution over time.
Qcc.com is a comprehensive business information platform that provides details on Chinese companies, including CNC material manufacturers. It offers company profiles, registration information, legal status, financial data, and key personnel. This platform is a useful resource for conducting company background checks, verifying legal compliance, and assessing a company’s credibility.
Importyeti.com is another online database that focuses on import and export data. It provides information on companies engaged in international trade, including CNC material manufacturers in China. Importyeti.com can offer insights into a company’s import and export activities, key markets, major customers, and suppliers. This data can be valuable for assessing a company’s international business capabilities and identifying potential partners or competitors.
In addition to these platforms, using archive.org can provide access to a company’s historical website snapshots. By entering a company’s web address, archive.org displays saved versions of the website dating back to its inception. This feature allows researchers to trace a company’s online presence, track changes in product offerings, observe its growth trajectory, and assess its digital marketing strategies.
By utilizing qcc.com, importyeti.com, and archive.org, individuals seeking information on CNC material manufacturers in China can gain valuable insights into a company’s background, financial history, international trade activities, and online presence.
Leveraging Trade Shows and Expos for cnc material Sourcing in China
Trade shows and expos in China present excellent opportunities for businesses to source CNC materials. These events serve as a platform for manufacturers, suppliers, and industry professionals to showcase their products and services. By attending trade shows and expos, businesses can gain valuable insights into the latest trends, technologies, and innovations in CNC material sourcing.
One major benefit of attending these events is the ability to meet face-to-face with potential suppliers. This direct interaction allows businesses to evaluate the quality of products, negotiate prices, and build long-term relationships. Meeting suppliers in person also provides the opportunity to discuss specific needs and requirements, ensuring a customized solution for CNC material sourcing.
Trade shows and expos bring together a wide range of manufacturers and suppliers under one roof, making it easier for businesses to compare different offerings. By reviewing various options, businesses can identify the most suitable suppliers in terms of cost, quality, and reliability. In addition, attending these events allows businesses to stay updated with the latest CNC material sourcing trends, as exhibitors often showcase new materials and technologies.
For businesses looking to source CNC materials in China, trade shows and expos offer an array of benefits. They provide a platform for direct interaction with suppliers, making it easier to assess product quality, negotiate prices, and establish trust. These events also enable businesses to explore different offerings and stay up-to-date with the latest trends in CNC material sourcing.
In conclusion, businesses can leverage trade shows and expos in China to effectively source CNC materials. By attending these events, businesses can meet potential suppliers, assess product quality, foster long-term partnerships, and stay updated with industry trends, ultimately enhancing their CNC material sourcing strategies.
The Role of Agents and Sourcing Companies in Facilitating cnc material Purchases from China
Agents and sourcing companies play a crucial role in facilitating CNC material purchases from China. These entities act as intermediaries between buyers and manufacturers, streamlining the procurement process and ensuring a smooth transaction.
First and foremost, agents and sourcing companies have extensive knowledge about the Chinese market and industry. They are well-versed in local regulations, logistics, and customs procedures, which helps buyers navigate the complex landscape of international trade. By leveraging their expertise, agents and sourcing companies can assist buyers in finding suitable suppliers that meet their specific CNC material requirements.
Moreover, agents and sourcing companies act as quality control inspectors. They visit factories and conduct thorough inspections to ensure compliance with international standards. They assess the manufacturing capabilities, equipment, worker skills, and overall production quality to guarantee that the CNC materials being purchased meet the buyer’s specifications. This helps prevent any potential quality issues and ensures that buyers receive materials that meet their expectations.
Agents also play a crucial role in negotiating prices with suppliers on behalf of buyers. They have extensive market knowledge, allowing them to compare prices, identify competitive rates, and secure favorable deals. Agents leverage their relationships with manufacturers to obtain the best possible prices, ensuring that buyers can procure CNC materials at competitive rates.
Furthermore, sourcing companies assist with logistics and shipping arrangements. They help organize the transportation of the purchased CNC materials from China to the buyer’s desired location. This involves coordinating shipping methods, customs clearance, and managing any documentation or paperwork required for international trade. By taking care of these logistics, agents and sourcing companies simplify the purchasing process and save buyers valuable time and resources.
In summary, agents and sourcing companies play a significant role in facilitating CNC material purchases from China. Their understanding of the Chinese market, quality control inspections, negotiation expertise, and logistics support streamline the buying process and ensure that buyers receive high-quality materials at competitive prices.
Price Cost Research for cnc material manufacturers Companies in China, use temu.com and 1688.com
When it comes to conducting price cost research for CNC material manufacturers in China, Temu.com and 1688.com are two popular websites that can be utilized for this purpose. These platforms serve as comprehensive online marketplaces, offering a wide variety of products and services from many different manufacturers.
Temu.com is a B2B website that facilitates trade between businesses. It provides access to a vast database of suppliers and manufacturers, including CNC material manufacturers in China. Users can search for specific products or suppliers and compare prices, specifications, and other relevant information.
1688.com, on the other hand, is a popular B2B platform owned by Alibaba Group. It is widely recognized as the largest wholesale marketplace in China, connecting buyers with suppliers. The site offers a massive range of products, including CNC materials, at competitive prices. 1688.com allows users to browse through suppliers, view their product catalogs, and negotiate prices directly.
When using these platforms for price cost research, it is essential to conduct thorough searches and analyze multiple suppliers to get a comprehensive understanding of the market. Comparative analysis of prices, product quality, certifications, and customer reviews can help in making an informed decision.
Additionally, it is crucial to communicate directly with potential suppliers to confirm details and negotiate prices. Effective communication in English may require patience, and it is recommended to use concise and precise language while using translation tools if needed.
In conclusion, Temu.com and 1688.com are valuable resources for conducting price cost research for CNC material manufacturers in China. By utilizing these platforms, comparing prices, analyzing product specifications, and engaging in direct communication with suppliers, businesses can make informed decisions based on their specific requirements. Remember, utilizing these platforms can require time and effort, but it can ultimately lead to finding the right CNC material manufacturers at competitive prices.
Shipping Cost for cnc material import from China
The shipping cost for importing CNC materials from China can vary depending on several factors. Firstly, the weight and dimensions of the package play a significant role in determining the shipping cost. Generally, heavier and larger packages will incur higher shipping costs.
Secondly, the distance between the port of origin in China and the destination port also affects the shipping cost. Longer distances typically result in higher shipping fees.
Additionally, the shipping method chosen greatly impacts the cost. There are various options available, including air freight, sea freight, and express courier services. Air freight is the quickest but usually the most expensive option. Sea freight is generally more affordable, but it takes longer to arrive. Express courier services such as DHL or UPS offer a balance between speed and cost.
Customs duties and taxes may also add to the shipping cost. It is essential to be aware of the import regulations and any additional charges that may be levied by customs authorities in the destination country.
To get a specific shipping cost, it is advisable to contact shipping companies or freight forwarders who can provide detailed quotes based on the specific requirements of the CNC materials to be imported. They will take into account factors such as weight, dimensions, shipping method, and destination to provide an accurate cost estimate.
In conclusion, the shipping cost for importing CNC materials from China can vary depending on factors such as weight, dimensions, distance, shipping method, and customs duties. To get an accurate estimate, it is recommended to consult with shipping companies or freight forwarders who can provide detailed quotes based on specific requirements.
Compare China and Other cnc material Markets: Products Quality and Price,Visible and Hidden Costs
China is known for being a major player in the global CNC material market. However, it is crucial to compare it with other markets in terms of product quality and price, as well as visible and hidden costs.
In terms of product quality, China has made significant progress over the years. Many Chinese CNC material manufacturers have adopted advanced technology and equipment to improve the precision and consistency of their products. However, it is important to note that the quality of CNC materials in China can vary significantly depending on the manufacturer. Some companies prioritize cost-cutting measures, resulting in lower quality products. On the other hand, other markets, such as Germany and Japan, are renowned for their exceptional product quality in the CNC material market. They have a long-standing tradition of precision engineering and strict quality control measures, ensuring that their products meet the highest standards.
Price is another crucial factor to consider when comparing China to other CNC material markets. Chinese manufacturers often offer competitive pricing due to lower labor and production costs. This makes their products more affordable compared to those from other countries, such as Germany or Japan. However, it is important to consider the trade-off between price and quality. While Chinese products may be more cost-effective, they may not necessarily offer the same level of quality and longevity as their higher-priced counterparts from other markets.
When considering both visible and hidden costs, China has some advantages and disadvantages. The visible costs, such as the initial purchase price, tend to be relatively lower in China due to its lower manufacturing costs. However, hidden costs, such as import duties, shipping fees, and potential quality issues, can add up and impact the overall cost. For example, importing CNC materials from China may incur higher transportation costs, longer lead times, and potential delays due to customs clearance procedures. Additionally, the quality control process may require additional time and resources to ensure the products meet the desired specifications.
In conclusion, China is a significant player in the CNC material market, offering competitive pricing and improving product quality. However, when comparing it to other markets, such as Germany and Japan, there are differences in terms of product quality and price. While Chinese products may be more affordable, they may not always meet the same level of quality and reliability. Furthermore, careful consideration of both visible and hidden costs is necessary to accurately assess the overall cost-effectiveness of sourcing CNC materials from China.
Understanding Pricing and Payment Terms for cnc material: A Comparative Guide to Get the Best Deal
When it comes to purchasing CNC materials, understanding pricing and payment terms is crucial to securing the best deal. This comparative guide aims to help you navigate the complexities of pricing and payment in the CNC material industry.
Pricing of CNC materials can vary significantly depending on several factors. The first consideration is the material itself. Different materials, such as aluminum, steel, or plastics, possess unique characteristics and production costs. Suppliers might price materials differently based on availability, demand, and fluctuations in raw material prices.
Additionally, the quantity and quality of the CNC materials impact pricing. Bulk orders often enjoy discounts as economies of scale come into play. Higher-quality materials, which undergo additional processing and quality control steps, generally command premium prices.
When comparing prices, it is vital to consider associated costs beyond the material itself. These may include shipping, handling, and taxes. Some suppliers offer free or discounted shipping for large orders, which can significantly affect the final price.
Payment terms also play a crucial role in obtaining the best deal. Common payment options in the CNC material industry include cash, credit cards, bank transfers, and trade credit.
Cash payments are immediate and can potentially fetch discounts. However, this might not be a feasible option for all buyers, depending on their financial situation. Credit cards provide convenience but may come with additional fees.
Bank transfers are a preferred payment method for many businesses, as they offer security and transparency. Establishing a good relationship with your supplier may also lead to the possibility of trade credit, allowing you to receive materials upfront and pay within an agreed-upon timeframe.
Negotiating terms is a key strategy to obtain favorable pricing and payment conditions. Suppliers may offer discounts for bulk orders, loyal customers, or extended payment periods. Comparing quotes from different suppliers and discussing these with each party may result in better deals.
In conclusion, understanding pricing factors, associated costs, and evaluating payment terms are essential to secure the best deal when purchasing CNC materials. By considering these factors, negotiating with suppliers, and conducting thorough comparisons, you can make informed decisions and optimize your procurement process.
Chinese Regulations and Industry Standards Certifications for cnc material,Import Regulations and Customs for cnc material from China
China has established a comprehensive regulatory framework and industry standards for CNC (Computer Numerical Control) materials. The primary regulations governing the production and certification of CNC materials in China include:
1. Chinese National Standards (CNS): CNS standards ensure the quality control and safety of CNC materials, such as metals, plastics, and composites. These standards cover various aspects, including dimensional accuracy, mechanical properties, surface finish, and tolerances.
2. China Compulsory Certification (CCC): CCC certification is a mandatory requirement for certain CNC materials and products. It is issued by the Chinese government to ensure compliance with safety, health, and environmental protection standards. The CCC mark indicates that the product meets these requirements before entering the Chinese market.
3. Industrial Standards: China has industry-specific standards for CNC materials, established by organizations such as the China Machinery Industry Federation (CMIF) and the China Machine Tool & Tool Builders’ Association (CMTBA). These standards cover areas such as CNC machine performance, cutting tools, machining processes, and overall production standards.
When importing CNC materials from China, several regulations and customs procedures should be considered:
1. Import Tariffs: Different CNC materials may be subject to various import duties and taxes imposed by the importing country. Importers should consult the customs authorities to determine the applicable tariffs.
2. Customs Documentation: Importers must provide essential documentation, including commercial invoices, packing lists, bill of lading/airway bill, and a certificate of origin. These documents help customs officials assess the value, quantity, and origin of the imported CNC materials.
3. Product Safety and Testing: Importers should ensure that the CNC materials meet the safety standards and regulations of their country. They may be required to conduct product testing and obtain relevant certification before importation.
4. Import Restrictions: Some countries impose restrictions or bans on the importation of specific CNC materials due to quality, safety, or environmental concerns. Importers should review these restrictions before initiating any imports.
5. Labeling and Marking: Imported CNC materials must be labeled and marked appropriately, indicating the product’s country of origin, manufacturer, material composition, and safety warnings if applicable. These markings help customs officials in ensuring compliance with local regulations.
Importers should also engage reputable suppliers who comply with Chinese regulations and industry standards. Conducting due diligence on suppliers’ credentials and quality management systems is crucial to ensure the importation of high-quality CNC materials that meet the required standards.
Sustainability and Environmental Considerations in cnc material Manufacturing
Sustainability and environmental considerations in CNC material manufacturing have become increasingly important in recent years. As the global focus on environmental protection and sustainable practices grows, it is crucial for CNC manufacturing industries to adopt eco-friendly approaches to mitigate their environmental impact.
One key aspect of sustainability in CNC material manufacturing is the choice of materials used. Traditional materials like plastics and metals often have harmful effects on the environment throughout their lifecycle, from extraction to disposal. Therefore, manufacturers are now exploring alternative materials such as biodegradable plastics, plant-based composites, and recycled materials. These options help reduce carbon emissions, waste generation, and dependence on non-renewable resources.
Furthermore, reducing energy consumption during the manufacturing process is essential for sustainability. CNC machines that are energy-efficient and utilize renewable energy sources can significantly contribute to reducing carbon footprints. Implementing design improvements, such as optimizing toolpaths and reducing material waste, can also result in energy and resource savings. Additionally, recycling and reusing machining byproducts, such as chips and coolant fluids, help minimize environmental harm.
Water management is another critical consideration. CNC material manufacturing often involves the use of coolants and lubricants that can pose risks to water resources if not properly managed. Implementing water treatment and recycling systems ensures that these harmful substances are removed before the water is discharged. Moreover, integrating water-saving technologies and practices can minimize water usage, reducing strain on local water supplies.
Lastly, proper waste management and disposal are vital components of sustainable CNC material manufacturing. Implementing recycling programs, including the responsible disposal of hazardous materials and reducing waste sent to landfills, helps minimize environmental harm. Adopting circular economy principles, such as reusing and repurposing materials, is also beneficial.
In conclusion, sustainability and environmental considerations in CNC material manufacturing play a crucial role in protecting the environment and conserving resources. Adopting materials with a lower environmental impact, reducing energy consumption, managing water resources, and implementing proper waste management practices collectively contribute to a more sustainable manufacturing process. By prioritizing these considerations, CNC material manufacturers can contribute to a greener future.
List The Evolution history of “cnc material”
The evolution of CNC material has seen a significant transformation over the years, starting from traditional materials to more advanced and sophisticated options. The following provides a brief overview of the evolution history of CNC materials, tracing their development and advancements in different industries.
Initially, CNC machines were primarily used for processing metals such as steel and aluminum. These materials were favorable due to their durability and ease of machining. CNC milling and turning centers allowed for precise and efficient metal cutting, forming the foundation of CNC material processing.
As technology progressed, CNC machines began to incorporate new materials such as plastics. This development expanded the applications of CNC machining, allowing for the production of a wide range of plastic components used in various industries. Plastics offered advantages such as lightweight, flexibility, and cost-effectiveness.
With the rise of composite materials, CNC machines further evolved to accommodate their processing. Composite materials, consisting of a mixture of different elements, became popular due to their high strength-to-weight ratios. CNC machining played a crucial role in shaping and cutting composite materials, enabling the production of complex and intricate structures used in aerospace, automotive, and other advanced industries.
Another significant development in CNC material technology was the inclusion of ceramics. Ceramics possess unique properties like high heat resistance, electrical insulation, and hardness, making them ideal for specific applications in fields like electronics and medical devices. CNC machines equipped with specialized tools enabled precise cutting and shaping of these brittle materials.
The latest advancement in CNC material evolution revolves around additive manufacturing or 3D printing. This technology allows for the production of intricate parts by adding material layer by layer. With the integration of CNC machining with 3D printing, complex geometries and hybrid structures can be achieved, opening up new possibilities in prototyping, customization, and small-scale production.
In summary, the evolution history of CNC material has witnessed a progression from traditional metals to plastics, composites, ceramics, and additive manufacturing. As advancements continue, the scope of materials that can be processed by CNC machines will likely expand even further, enabling novel applications in diverse industries.
The Evolution and Market Trends in cnc material Industry
The CNC (Computer Numerical Control) material industry has witnessed significant evolution and market trends over the years. Initially, CNC machines were primarily used in metal manufacturing, but now they are extensively used in a wide range of industries, including automotive, aerospace, healthcare, and electronics, among others.
One major evolution in the CNC material industry is the adoption of advanced technologies and software. CNC machines have become highly efficient, precise, and versatile due to advancements in computer-aided design (CAD) and computer-aided manufacturing (CAM) software. These advancements have enabled the industry to produce complex and intricate designs, reducing human error and increasing overall productivity.
Another evolution is the increasing use of non-metal materials in CNC machining. While metals still dominate the industry, materials like plastics, composites, ceramics, and wood are gaining traction. This is driven by the need for lightweight components, improved functionality, and cost-effectiveness in various applications. CNC machines are now capable of processing these materials efficiently, offering a broader range of options for manufacturers.
Market trends in the CNC material industry point towards automation and integration of smart technologies. The industry is witnessing a rise in the adoption of Industry 4.0 technologies, such as the Internet of Things (IoT), artificial intelligence, and robotics. This integration allows for real-time monitoring, predictive maintenance, and enhanced manufacturing capabilities, leading to improved efficiency and reduced downtime.
Additionally, customization and on-demand manufacturing are becoming increasingly important market trends. CNC machines can produce highly customized products with minimal setup time and cost, making them ideal for small-scale or niche manufacturing. The ability to quickly adapt to changing customer demands and manufacturing requirements provides a competitive edge in today’s market.
Overall, the CNC material industry has undergone significant evolution and is constantly influenced by market trends. Advancements in technology, the adoption of non-metal materials, and the integration of smart technologies have revolutionized the industry. The emphasis on automation, customization, and on-demand manufacturing are key factors shaping the future of the CNC material industry.
Custom Private Labeling and Branding Opportunities with Chinese cnc material Manufacturers
Chinese CNC material manufacturers offer a plethora of custom private labeling and branding opportunities for businesses looking to establish their own identity in the market. With a wide range of CNC materials available, businesses can personalize their products to meet their specific branding requirements.
One major advantage of partnering with Chinese manufacturers is their expertise in customizations. They possess advanced machinery and technology that enable them to achieve intricate designs and precision in manufacturing. Whether it is engraving, cutting, or embossing logos and branding elements, Chinese manufacturers can easily handle the customization process.
Furthermore, Chinese manufacturers also offer flexible options for private labeling. Businesses can collaborate with manufacturers to design and create custom labels that reflect their unique brand identity. From choosing the material, color, size, and placement of labels, manufacturers can accommodate various customization preferences.
Additionally, Chinese CNC material manufacturers usually provide OEM (Original Equipment Manufacturer) and ODM (Original Design Manufacturer) services. This means that businesses can not only request customized labeling and branding but also have the option to design their own unique products. Manufacturers can guide businesses through the entire production process, from initial product design to the finished result.
It is worth noting that partnering with Chinese manufacturers for private labeling and branding also offers cost advantages. The competitive pricing in China allows businesses to achieve their desired customizations without straining their budget.
In conclusion, Chinese CNC material manufacturers provide diverse opportunities for businesses to customize products with private labels and branding elements. Their expertise in advanced machinery, flexibility in private labeling, and cost advantages make them an ideal choice for businesses looking to establish their own unique identity in the market.
Tips for Procurement and Considerations when Purchasing cnc material
When it comes to procurement and purchasing CNC materials, there are several important tips and considerations to keep in mind:
1. Identify your specific requirements: Before purchasing CNC materials, clearly define your project requirements such as material type, size, shape, and quantity. This will help you choose the most suitable material for your project.
2. Research and evaluate suppliers: Look for reputable suppliers with a track record of delivering quality CNC materials. Consider factors such as the supplier’s experience, reviews, certifications, and their ability to provide materials within your required time frame.
3. Material quality and specifications: Ensure that the CNC materials meet the required quality standards and specifications. Consider factors such as material strength, durability, tolerance, and other mechanical properties necessary for your project. Request material samples or certifications if needed.
4. Price and cost-effectiveness: Compare prices from multiple suppliers to get the best value for your money. However, be cautious of extremely low prices as they could indicate substandard quality. Consider other factors such as shipping costs, payment terms, and discounts offered.
5. Supply chain and logistics: Consider the supplier’s location and shipping capabilities. Opt for suppliers who can deliver the materials on time and efficiently, minimizing any potential disruptions to your project’s timeline.
6. Customer support and after-sales service: Choose a supplier who offers reliable customer support and assistance throughout the procurement process. Consider factors such as their responsiveness to inquiries, willingness to address concerns, and their ability to provide technical guidance when needed.
7. Sustainability and ethical practices: Consider the supplier’s commitment to sustainability and ethical practices. This includes factors such as their adherence to environmental regulations, responsible sourcing of materials, and their efforts to minimize waste.
8. Long-term supply partnerships: Building long-term relationships with trusted suppliers can provide stability and consistent quality in the procurement process. Consider suppliers who are willing to work closely with you, understand your evolving needs, and offer competitive pricing for future projects.
By considering these tips and factors when purchasing CNC materials, you can ensure that you make informed decisions that meet the requirements of your project, while also optimizing cost-effectiveness and quality.
FAQs on Sourcing and Manufacturing cnc material in China
1. Why should I consider sourcing and manufacturing CNC material in China?
Sourcing and manufacturing CNC material in China offers several advantages. China is known for its low manufacturing costs, abundance of raw materials, and a vast network of suppliers and manufacturers. The country also has a skilled labor force and advanced manufacturing capabilities, ensuring high-quality products at competitive prices. Moreover, China’s manufacturing industry has a well-established supply chain, allowing for efficient production and delivery times.
2. How do I find reliable suppliers and manufacturers in China for CNC material?
To find reliable suppliers and manufacturers in China, it is crucial to conduct thorough research. Utilize online platforms and directories that connect buyers with suppliers, such as Alibaba or Global Sources. Read customer reviews and ratings to gauge the reputation and reliability of potential suppliers. Additionally, consider attending trade shows and exhibitions in China to meet suppliers face-to-face and establish direct relationships.
3. How can I ensure quality control when sourcing CNC material from China?
To ensure quality control, it is essential to partner with reputable suppliers and manufacturers who prioritize quality. Conduct factory audits or inspections to assess their production capabilities, equipment, and quality control processes. Request product samples or prototypes to evaluate the material’s quality and functionality. Implement strict quality control measures, including pre-shipment inspections, to avoid receiving substandard products.
4. What are the common challenges when sourcing and manufacturing CNC material in China?
Language barriers and cultural differences can pose challenges when sourcing and manufacturing CNC material in China. Miscommunication may lead to misunderstandings or errors in product specifications. Time zone differences can also affect communication and response times. Import/export regulations, customs procedures, and logistics should also be considered when shipping materials from China.
5. How can I protect my intellectual property when sourcing and manufacturing CNC material in China?
To protect your intellectual property, consider working with a reputable legal advisor who specializes in international trade and intellectual property laws. Apply for patents, trademarks, or copyrights in China to establish legal protections. When working with suppliers, sign non-disclosure agreements (NDAs) and ensure they have strict confidentiality policies in place. Monitor and conduct regular audits to detect any unauthorized use of intellectual property.
Overall, sourcing and manufacturing CNC material in China can be a cost-effective and efficient option, but proper research, due diligence, and the implementation of quality control measures are essential for a successful partnership.
Why contact sourcifychina.com get free quota from reliable cnc material suppliers?
Sourcifychina.com, being a platform connecting businesses with reliable CNC material suppliers in China, offers a free quota to its users for various reasons.
Firstly, the free quota allows businesses to experience the services and benefits of Sourcifychina.com without any financial commitment. By providing a limited number of inquiries for free, businesses can explore the platform’s functionality, interface, and the responsiveness of the suppliers before committing to a paid plan. This trial period helps build trust and confidence in the platform’s effectiveness.
Secondly, by offering a free quota, Sourcifychina.com attracts potential customers who might otherwise be hesitant to try the platform. For businesses considering sourcing from Chinese suppliers, the fear of scams, unreliable partners, and language barriers can be significant hurdles. Providing a free quota reduces the initial financial risk associated with trying a new sourcing platform, making it more appealing for businesses to give it a try.
Moreover, offering a free quota gives Sourcifychina.com an opportunity to showcase the quality and reliability of their network of CNC material suppliers. By connecting businesses with trustworthy and vetted suppliers, the platform aims to establish itself as a reliable intermediary. The free quota allows businesses to experience the high caliber of suppliers available, leading to potential long-term partnerships and paid subscription plans.
Lastly, providing a free quota helps Sourcifychina.com gather valuable market feedback and data. Through the trial period, the platform can collect insights on user preferences, pain points, and potential areas of improvement. This feedback allows continuous refinement and enhancement of the platform’s functionality and services, ensuring the best user experience for businesses.
In conclusion, Sourcifychina.com offers a free quota to businesses in order to facilitate trial and provide a risk-free experience, attract customers who may have reservations, demonstrate the quality of their supplier network, and gather market feedback for continuous improvement.