Introduce about cnc materials guide,Qulity,Cost,Supplier,Certification,Market,Tips,FAQ
CNC materials guide provides essential information regarding the different materials available for Computer Numerical Control (CNC) machining. This guide focuses on addressing various aspects, including quality, cost, suppliers, certifications, market trends, tips, frequently asked questions (FAQs), and more.
When it comes to quality, CNC materials should possess certain characteristics such as durability, excellent surface finish, dimensional accuracy, and resistance to wear and tear. Each material has its unique properties, making them suitable for specific applications. The guide provides an overview of the most commonly used materials in CNC machining and highlights their qualities, helping users choose the right material for their project.
Cost is a critical factor to consider while selecting CNC materials. The guide emphasizes the price range associated with different materials, enabling users to make informed decisions based on their budget constraints.
Moreover, the guide also assists in finding reliable suppliers for CNC materials. It offers insights into well-established and reputable suppliers who provide high-quality materials at competitive prices. This can save users time and effort in searching for trusted sources.
Certifications play a significant role in ensuring the authenticity and reliability of CNC materials. The guide discusses various certifications and standards associated with materials, such as ISO certifications, RoHS compliance, and others. This helps users choose materials that meet industry standards and regulations.
The guide also sheds light on the current market trends in CNC materials. It explores emerging materials, advancements in materials technology, and the preferences of industries using CNC machining. Keeping up with market trends enables users to stay ahead and make informed decisions based on the latest developments.
In addition, the guide provides useful tips regarding handling, machining, and maintaining CNC materials. These tips help users optimize material usage, prolong the lifespan of their tools, and enhance overall productivity.
A comprehensive FAQ section addresses common queries related to CNC materials. It covers topics like material compatibility with various CNC machines, suitable materials for different applications, material sourcing, and more. Users can find quick answers to their questions without the need for further research.
In summary, the CNC materials guide acts as a valuable resource for individuals or businesses involved in CNC machining. It covers essential aspects such as quality, cost, suppliers, certifications, market trends, tips, and FAQs, helping users make informed decisions and achieve optimal outcomes in their CNC projects.
Types of cnc materials
CNC (Computer Numerical Control) machining is a process widely used in the manufacturing industry to produce high precision parts and components. Various materials can be utilized in CNC machining, each offering unique properties and advantages. Here, we will discuss some of the most common types of materials used in CNC machining.
1. Metals:
Metal alloys such as aluminum, stainless steel, brass, copper, and titanium are popular choices for CNC machining. These materials offer excellent strength, durability, and resistance to corrosion, making them suitable for a wide range of applications in industries like aerospace, automotive, and medical.
2. Plastics:
Plastics like ABS (Acrylonitrile Butadiene Styrene), PVC (Polyvinyl Chloride), nylon, polycarbonate, and polypropylene are commonly used in CNC machining. These materials are lightweight, durable, and have good chemical resistance. Plastics are frequently employed in industries like consumer electronics, signage, and packaging.
3. Wood:
Wood, including hardwoods like oak, maple, and walnut, as well as softwoods like pine and plywood, can be machined using CNC equipment. Wood offers a natural and aesthetic appeal, making it ideal for furniture, cabinetry, and decorative components.
4. Foam:
Foam materials like polystyrene and polyurethane foams can be CNC machined for various applications. Foam is lightweight, easy to shape, and provides excellent insulation properties. It is commonly used in packaging industry, signs, and architectural models.
5. Composites:
Composite materials, such as carbon fiber-reinforced polymers (CFRP), fiberglass, and laminates, are finding increasing usage in CNC machining. Composites provide a high strength-to-weight ratio, excellent stiffness, and durability, making them suitable for aerospace, automotive, and sporting goods industries.
6. Ceramics:
Ceramic materials like alumina, zirconia, and silicon carbide can be CNC machined for their excellent mechanical properties, resistance to wear, and high-temperature resistance. Ceramics find applications in industries like electronics, cutting tools, and medical devices.
The selection of the appropriate material for CNC machining depends on factors such as the final application, required mechanical properties, environmental factors, and cost considerations. Furthermore, it is essential to choose materials that are compatible with CNC machining processes and tools, ensuring efficient and accurate manufacturing of the desired parts and components.
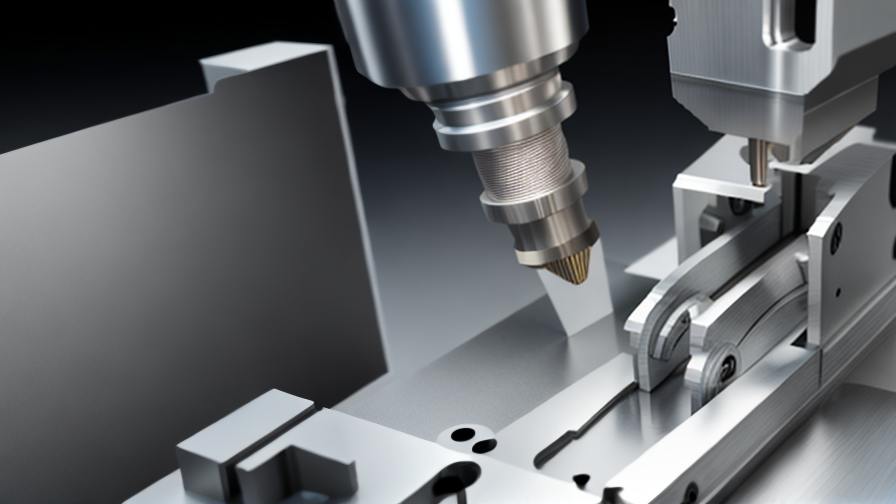
Pros and Cons of Using cnc materials
CNC (Computer Numerical Control) materials present both advantages and disadvantages in various aspects of manufacturing. Here are the pros and cons of using CNC materials:
Pros:
1. Precision: CNC machines provide exceptional precision and accuracy, ensuring consistent production quality. These machines follow instructions from computer programs, minimizing human error and guaranteeing precise dimensions and specifications.
2. Efficiency: CNC materials offer improved productivity by reducing production time and increasing output. These machines work at high speeds and can run continuously, allowing for faster production and meeting tight deadlines.
3. Versatility: CNC materials are suitable for various applications and can handle a wide range of materials such as metals, plastics, wood, and composites. This versatility makes CNC machines suitable for different industries, including automotive, aerospace, robotics, and furniture manufacturing.
4. Complex Designs: With CNC machines, complex designs and intricate patterns can be achieved easily. The machines can create three-dimensional shapes, complex curves, and intricate details with high precision.
5. Replicability: CNC materials enable the production of identical parts repeatedly. Once a design is programmed, manufacturers can replicate it accurately, ensuring consistency in the final product.
Cons:
1. High Initial Investment: CNC machines are expensive, making the initial investment a significant barrier for small businesses or start-ups. The machines require continuous maintenance, software upgrades, and occasional repairs, increasing operational costs.
2. Skilled Workforce: Operating CNC machines requires a skilled workforce trained in programming and machine operation. Companies with limited access to skilled labor may face challenges in finding qualified operators.
3. Limited Flexibility: While CNC materials are versatile in handling various materials, they may lack flexibility in adapting to sudden design changes or modifications. Reprogramming a CNC machine can be time-consuming and may disrupt production.
4. Higher Material Waste: CNC machines operate by cutting away the material to shape the desired object, resulting in more significant material waste compared to other manufacturing techniques. This can lead to increased material costs and environmental concerns.
5. Size Limitations: The size of the product or component that can be produced is limited by the size of the CNC machine. Large-scale or oversized parts may require additional equipment or alternative manufacturing methods.
In conclusion, while CNC materials offer advantages such as precision, efficiency, versatility, and complex design capabilities, they also have drawbacks such as high initial investment, requirement for skilled labor, limited flexibility, higher material waste, and size limitations. Businesses must weigh these factors and consider their specific manufacturing needs before choosing to incorporate CNC materials into their processes.
cnc materials Reference Specifications (varies for different product)
CNC materials serve as the foundation for creating precision parts and products using Computer Numerical Control (CNC) machines. These materials are carefully chosen based on their specific properties to ensure optimal performance and desired outcomes. While the reference specifications may vary for different products, there are some commonly used CNC materials worth mentioning.
Metals are among the most frequently used materials in CNC machining. Aluminum exhibits high strength-to-weight ratio, excellent machinability, and corrosion resistance, making it suitable for aerospace, automotive, and electronic industries. Stainless steel offers corrosion resistance, heat resistance, and is widely used in medical, food processing, and automotive applications. Brass combines durability with electrical conductivity, making it popular for electrical and plumbing components.
Plastics are another category of materials that find widespread application in CNC machining. Acrylic or PMMA boasts optical clarity, impact resistance, and high dimensional stability, commonly employed in signage, display, and lighting industries. Polyethylene (PE) is lightweight, chemically resistant, and used in various applications such as packaging, agriculture, and automotive components. Nylon offers excellent wear resistance, tensile strength, and is broadly utilized in gears, bearings, and washers.
Wood and composite materials also deserve attention in CNC machining. Wood, available in various types like maple, birch, or bamboo, offers natural aesthetics, workability, and is ideal for furniture, cabinetry, and architectural models. Composite materials, such as carbon fiber composites, provide high strength-to-weight ratio, rigidity, and find applications in aerospace, marine, and sports equipment production.
Ceramics and advanced materials cater to specialized requirements. Ceramics provide high temperature resistance, low thermal expansion, and are used in cutting tools, engine components, and electronics. Advanced materials like titanium alloys exhibit exceptional strength, corrosion resistance, and extensive use in aerospace, medical, and chemical industries.
In conclusion, CNC materials should be carefully selected based on the desired specifications of the end product. Metals, plastics, wood, composites, ceramics, and advanced materials all present unique properties that can be tailored to suit various industries’ requirements. By understanding and utilizing the reference specifications, manufacturers can optimize CNC machining processes to achieve precision and high-quality output.
Applications of cnc materials
CNC (Computer Numerical Control) materials, also known as engineered materials, offer a wide range of applications across various industries. These materials are composed of a combination of raw materials that are processed and manipulated using CNC machines to achieve specific characteristics and properties. Here are a few applications of CNC materials:
1. Aerospace industry: CNC materials, such as carbon fiber composites, are extensively used in the aerospace industry. These materials offer high strength-to-weight ratio, excellent heat resistance, and dimensional stability. They are used in manufacturing aircraft components, including fuselage parts, wings, and rotor blades.
2. Automotive industry: CNC materials find numerous applications in the automotive sector. Lightweight CNC materials like aluminum and carbon fiber composites are used in the production of car bodies, engine components, and interiors. These materials aid in reducing the overall weight of vehicles, improving fuel efficiency, and enhancing performance.
3. Medical industry: CNC materials play a vital role in the medical field. They are used to manufacture various medical devices, prosthetics, and implants. CNC materials exhibit biocompatibility, allowing them to be safely integrated into the human body. These materials, such as titanium alloys, are also corrosion-resistant and offer high tensile strength, making them ideal for medical applications.
4. Electronics industry: CNC materials are extensively utilized in the electronics industry. They are used in the production of circuit boards, electronic enclosures, and heat sinks. CNC materials offer excellent electrical insulation properties, thermal conductivity, and dimensional stability, ensuring enhanced performance and safety of electronic devices.
5. Defense industry: CNC materials find applications in the defense sector due to their durability and high strength-to-weight ratio. They are utilized in manufacturing components for military vehicles, body armor, missile systems, and aircraft components. CNC materials provide critical properties such as ballistic resistance, impact resistance, and fire resistance, making them suitable for defense applications.
6. Construction industry: CNC materials offer advantages in the construction sector. Composite materials like fiberglass reinforced polymers are used in building lightweight and durable structures. Additionally, CNC materials with thermal and acoustic insulation properties are utilized for creating energy-efficient buildings.
In conclusion, CNC materials have a wide range of applications across multiple industries due to their unique properties and versatility. These materials have revolutionized various sectors, enabling the development of advanced products with enhanced performance, durability, and efficiency.
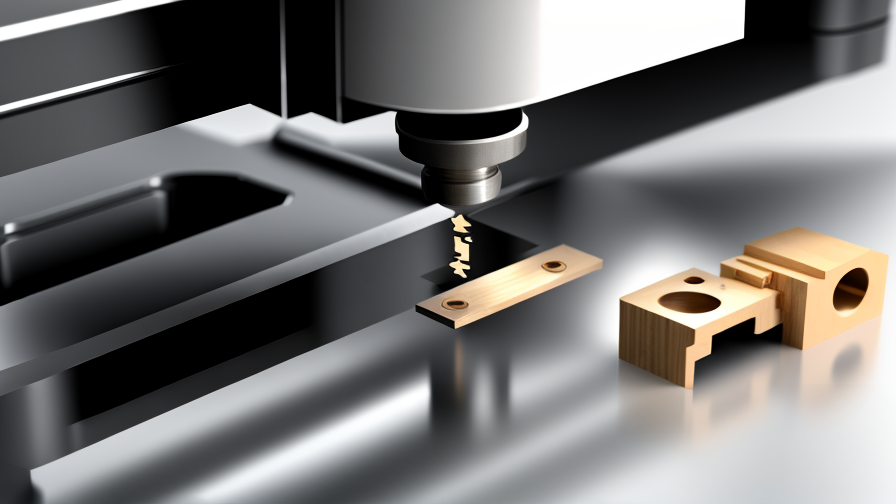
The Work Process and how to use cnc materials
The work process of using CNC materials involves several steps to transform a raw material into a finished product using Computer Numerical Control (CNC) technology.
Firstly, the design phase is crucial, where the desired dimensions and specifications are created using computer-aided design (CAD) software. This digital model serves as a blueprint for the manufacturing process.
Once the design is complete, it is then translated into a machine-readable format and loaded into the CNC machine. The machine is equipped with various cutting tools, such as drills, routers, or lasers, depending on the material and requirements of the design.
Next, the CNC machine begins the cutting process. It moves the cutting tool along the specified paths and depths, following the instructions provided by the digital model. This allows for precision and consistency in the manufacturing process.
During the cutting process, the CNC machine removes excess material from the raw stock to shape it according to the design. This can involve cutting, drilling, milling, or even 3D printing, depending on the type of material and the desired outcome.
After the cutting process is complete, the finished product is carefully inspected to ensure it meets the specified dimensions and quality standards. Any necessary adjustments or finishing touches are made to achieve the desired final product.
CNC materials can vary based on the application, but some common options include metals (such as aluminum, steel, or brass), wood, plastics, and composites. Each material requires specific cutting tools, speeds, and feeds to achieve the desired result. It is important to understand the properties of the material being worked with to select the appropriate tools and settings.
In conclusion, the work process of using CNC materials involves designing a digital model, programming it into a CNC machine, cutting the material to shape, and inspecting the finished product. Understanding the properties of the material being used and selecting the appropriate tools and settings are crucial for successful CNC material processing.
Quality Testing Methods for cnc materials and how to control the quality
When it comes to quality testing methods for CNC (Computer Numerical Control) materials, there are several approaches that can be employed to ensure the production of high-quality parts. These methods aim to identify any defects, measure dimensional accuracy, and assess the overall quality of the output. Here are some commonly used techniques:
1. Visual Inspection: This is a fundamental method where the parts are visually examined for any flaws, such as surface imperfections, cracks, or irregularities.
2. Coordinate Measuring Machine (CMM): CMMs are used to measure the dimensional accuracy of CNC parts by mapping their geometry and comparing it with the specifications provided. This helps in identifying any deviations and ensuring conformity.
3. Non-Destructive Testing (NDT): Techniques like ultrasonic testing, X-ray inspection, or dye penetrant testing can be applied to detect hidden defects, such as internal cracks, voids, or porosity, without damaging the material.
4. Hardness Testing: It involves measuring the material’s hardness using methods like the Rockwell or Brinell hardness scales to ensure it meets the required criteria.
5. Material Composition Analysis: Analyzing the composition of the material using techniques like spectroscopy or chemical analysis can ascertain the presence of any impurities or variations that could affect its quality.
6. Surface Roughness Measurement: This method determines the roughness or smoothness of the material’s surface using profilometers or surface roughness testers. It helps ensure that the surface finish meets the desired specifications.
To control the quality of CNC materials, it is crucial to establish comprehensive quality control procedures. This involves defining quality standards, creating inspection plans, and implementing process controls to minimize variations. Regular calibration and maintenance of machines, tools, and equipment are also necessary to ensure accurate and consistent results. Furthermore, implementing statistical process control techniques, such as control charts or process capability analysis, can help monitor and control the production process effectively.
In conclusion, ensuring the quality of CNC materials requires a combination of visual inspection, dimensional measurement, non-destructive testing, hardness testing, material analysis, and surface roughness measurement methods. Implementing comprehensive quality control procedures and monitoring the production process using statistical techniques greatly contributes to controlling the quality and delivering reliable CNC parts.
cnc materials Sample Policy and Post-Purchase Considerations for cnc materials from China
Sample Policy for CNC Materials from China:
1. Requesting Samples: Before making a bulk purchase of CNC materials from China, it is advisable to request samples of the desired materials from the supplier. This allows you to evaluate the quality, durability, and compatibility of the materials with your CNC machine.
2. Sample Cost and Shipping: It is common for suppliers to charge for sample materials and shipping. However, some suppliers may offer free or discounted samples, especially if you express your intention to make a bulk purchase. Discuss the sample cost and shipping arrangements with the supplier to avoid any confusion or hidden charges.
3. Sample Evaluation: Once you receive the samples, carefully evaluate them for their dimensional accuracy, material composition, surface finish, and any other specific requirements you may have. Test the samples on your CNC machine to ensure they perform as expected and meet your production needs.
4. Bulk Purchase Considerations: After evaluating the samples, consider the following factors before finalizing a bulk purchase:
a) Price: Compare the price offered by the supplier with other competitors in the market. Ensure that the price is reasonable and competitive without compromising on the quality of the materials.
b) Quality Assurance: Inquire about the supplier’s quality control measures, certificates, and testimonials from other customers. Aim for a supplier with a good reputation for delivering high-quality CNC materials.
c) Manufacturing Capability: Assess the supplier’s production capacity and ability to fulfill your bulk order requirements within the desired timeline. Verify if they have the necessary machinery, expertise, and workforce to meet your demands.
d) Communication and Support: Evaluate the supplier’s responsiveness, communication skills, and after-sales support. Clear and prompt communication is crucial for resolving any issues that may arise in the future.
e) Shipping and Customs: Discuss shipping options, lead times, and any customs-related requirements. Clarify who will be responsible for any import duties or taxes and ensure the packaging will adequately protect the materials during transit.
f) Payment Terms: Negotiate favorable payment terms, such as a reasonable deposit and a secure payment method, based on mutual agreement.
By following these sample policies and considering the mentioned post-purchase factors, you can mitigate the risks associated with purchasing CNC materials from China and ensure a successful procurement process.
Sourcing cnc materials from China: Opportunities, Risks, and Key Players
Sourcing CNC materials from China offers both opportunities and risks for businesses. China is known for its cost-effective manufacturing capabilities, making it an attractive option for businesses looking to reduce production costs. The country also has a vast network of suppliers and manufacturers specializing in CNC machining, providing a wide range of materials, from metals to plastics.
One of the key opportunities is the significant cost advantage of sourcing from China. Lower labor and material costs in China can result in substantial savings for businesses, allowing them to remain competitive in the global market. The abundance of suppliers in China also provides buyers with a wide variety of options to choose from, ensuring they can find the right material at a competitive price.
However, there are also risks associated with sourcing CNC materials from China. Quality control can be a concern, as some suppliers may not meet the required standards or provide consistent product quality. It is crucial for businesses to thoroughly vet potential suppliers, conduct regular quality inspections, and establish clear communication channels to mitigate these risks. Intellectual property protection is another risk, as China has had a reputation for counterfeiting products and infringing on patents. Businesses should take necessary precautions to safeguard their intellectual property rights when sourcing from China.
There are several key players in the CNC materials sourcing market in China. Alibaba Group, which owns platforms like Alibaba.com and AliExpress, is a prominent player connecting international buyers with Chinese suppliers. Global Sources, a Hong Kong-based company, also facilitates trade between Chinese manufacturers and international buyers. In addition, there are numerous Chinese manufacturers and trading companies specializing in CNC materials, such as Dongguan Foxron Precision Metal Parts Co., Ltd., Shenzhen T-one Precision Machinery Co., Ltd., and Shanghai Yunyan Prototype & Mould Manufacture Factory.
In conclusion, sourcing CNC materials from China provides opportunities for cost savings and a wide range of material options. However, businesses should carefully assess the risks associated with quality control and intellectual property protection. Key players like Alibaba Group and Global Sources, along with Chinese manufacturers and trading companies, play essential roles in facilitating CNC material sourcing from China.
How to find and select reliable cnc materials manufacturers in China,use google search manufacturers and suppliers
When looking for reliable CNC materials manufacturers in China, Google search can be a valuable tool. To ensure the best results, follow these steps:
1. Begin by typing relevant keywords such as “CNC materials manufacturers in China” or “reliable CNC materials suppliers in China” in the search engine.
2. Browse through the search results and look for manufacturers or suppliers that have a professional and user-friendly website.
3. Take note of the companies that appear on the first few pages of the search results as they are generally more established and trustworthy.
4. Visit the websites of the shortlisted manufacturers to gather information about their product range, manufacturing capabilities, certifications, and customer reviews.
5. Check if the manufacturer specializes in the particular CNC materials that you require. Look for indications that they have experience producing materials like metals, plastics, wood, or composites.
6. Pay attention to their quality control measures, production capacity, and the ability to provide custom solutions.
7. Look for social proof, such as customer reviews or testimonials, to get an idea of their reputation and reliability.
8. Contact the selected manufacturers directly through their website or provided contact details. Inquire about their production process, quality assurance measures, lead times, and pricing.
9. Request samples if necessary to evaluate the quality of their CNC materials firsthand.
10. Consider the manufacturer’s communication skills, professionalism, and promptness in responding to your inquiries. Good communication is crucial throughout the manufacturing process.
11. Make comparisons between different manufacturers based on their capabilities, pricing, quality, and customer service. Choose the one that best aligns with your requirements and expectations.
12. Before finalizing the decision, it is advisable to conduct due diligence by checking their business licenses, certifications, and any additional credentials.
By following these steps and utilizing Google search effectively, you can find and select reliable CNC materials manufacturers in China while ensuring a smooth and successful sourcing process.
How to check cnc materials manufacturers website reliable,use google chrome SEOquake check if ranking in top 10M
To check the reliability of a CNC materials manufacturer’s website, you can follow these steps:
1. Use Google Chrome: Open the website in question using the Google Chrome web browser.
2. Install SEOquake: Install the SEOquake extension on your Chrome browser. To do this, go to the Chrome Web Store, search for “SEOquake,” and click on the “Add to Chrome” button to install it.
3. Enable SEOquake: Once the extension is installed, click on the SEOquake icon at the top-right corner of your browser window to enable it.
4. Check website rank: With SEOquake enabled, enter the manufacturer’s website URL in the address bar and press enter. SEOquake will generate an overview of the website’s SEO metrics and rankings.
5. Analyze Google ranking: Look for the website’s ranking in the “Google” section of the SEOquake results. Check if it appears in the top 10 million (i.e., below 10,000,000) websites globally. If the website does not rank within the top 10 million, it may indicate lower visibility or popularity.
6. Consider other factors: Although a high ranking indicates some level of reliability, it’s essential to consider other factors as well. Look for additional information on the website, such as customer reviews, certifications, contact details, and clear product descriptions.
7. Evaluate website design and functionality: Assess the overall appearance and usability of the website. A professional, user-friendly design with clear navigation and informative content suggests the manufacturer’s reliability and professionalism.
Remember that SEO rankings are not the sole factor determining a website’s reliability. It’s essential to consider other aspects of the website, the company’s reputation, and customer feedback.
Top 10 cnc materials manufacturers in China with each 160 words introduce products,then use markdown create table compare
1. Shanghai ZZ New Material Tech. Co., Ltd.: With over 10 years of experience, Shanghai ZZ is a leading material manufacturer specializing in the production of CNC materials. Their extensive product range includes aluminum alloy, stainless steel, carbon steel, titanium alloy, and brass, among others. Their materials are widely used in automotive, aerospace, and electronic industries due to their excellent quality and precision.
2. Henan Signi Aluminium Co., Ltd.: Signi Aluminium is a reputable manufacturer that focuses on the production of aluminum materials for CNC applications. Their aluminum materials are known for their high strength, lightweight properties, and excellent corrosion resistance. Besides machining, their products are widely used in construction, transportation, and electrical industries.
3. Zhejiang Yuguang Aluminum Material Co., Ltd.: Yuguang Aluminum Material is a leading manufacturer of aluminum alloy materials for CNC machining. They offer a diverse range of aluminum materials, including 2000, 5000, 6000, and 7000 series alloys. These materials have remarkable machinability and can be used in various industrial applications, such as automotive, aerospace, and marine.
4. Dongguan Uptech Electronics Co., Ltd.: Uptech Electronics specializes in the production of CNC plastic materials, such as ABS, POM, PC, and PP. Their materials are widely used in electronic appliances, automotive parts, and consumer products. Uptech Electronics ensures high precision, consistency, and durability of their CNC materials.
5. Shenzhen Gooceen Industrial Co., Ltd.: Gooceen Industrial is a renowned manufacturer of CNC materials, including stainless steel, aluminum, brass, and engineering plastics. Their products are widely used in the automotive, machinery, and electronics sectors. Gooceen Industrial is recognized for their high-quality materials and fast delivery.
| Manufacturer Name | Products Offered |
|—————————————-|—————————————|
| Shanghai ZZ New Material Tech. Co., Ltd.| Aluminum alloy, stainless steel, carbon steel, titanium alloy, brass, etc. |
| Henan Signi Aluminium Co., Ltd. | Aluminum materials for CNC machining |
| Zhejiang Yuguang Aluminum Material Co., Ltd. | Aluminum alloy materials |
| Dongguan Uptech Electronics Co., Ltd. | CNC plastic materials (ABS, POM, PC, PP) |
| Shenzhen Gooceen Industrial Co., Ltd. | Stainless steel, aluminum, brass, engineering plastics |
Background Research for cnc materials manufacturers Companies in China, use qcc.com archive.org importyeti.com
China is known for its strong manufacturing capabilities and competitive prices when it comes to CNC materials. To find reputable manufacturers in China, several online platforms can be utilized, including qcc.com, archive.org, and importyeti.com.
Qcc.com is a leading business information platform in China, providing comprehensive company profiles, registration details, credit ratings, and other important background information. By searching for CNC materials manufacturers on qcc.com, one can gain insights into the company’s size, registration status, financial standing, and legal history. This allows potential buyers to evaluate the credibility and reliability of the manufacturer.
Archive.org is a website that enables users to view snapshots of websites saved over time. By accessing historical data on CNC materials manufacturers’ websites, potential buyers can identify the company’s growth trajectory, product range, and any changes in its operations or partnerships. This information can help assess the manufacturer’s stability, product quality, and industry experience.
Importyeti.com is a platform designed specifically for importers to find suitable suppliers in China. It offers a vast database of verified manufacturers, allowing users to search for CNC materials manufacturers based on their location, product category, and company size. Importyeti.com provides valuable insights into manufacturers’ export history, production capacity, and customer reviews, allowing potential buyers to make better-informed decisions.
By utilizing qcc.com, archive.org, and importyeti.com, researchers can gather key information about CNC materials manufacturers in China. These platforms provide details about a company’s legal status, financial viability, history, product range, production capacity, and customer satisfaction. Through this research, buyers can identify reliable and suitable manufacturers in China that meet their specific CNC materials requirements.
Leveraging Trade Shows and Expos for cnc materials Sourcing in China
Trade shows and expos are widely regarded as one of the most effective methods to source CNC materials in China. These events provide a platform for suppliers, manufacturers, and distributors to showcase their products and services to a wide audience of potential buyers. Leveraging trade shows and expos can be highly advantageous for CNC materials sourcing in several ways.
Firstly, attending these events allows direct interaction with numerous suppliers and manufacturers. This face-to-face engagement provides an opportunity to discuss specific requirements, negotiate terms, and get a better understanding of the quality and range of materials offered. Meeting suppliers in person also facilitates building relationships and establishing a sense of trust, which is vital when dealing with international transactions.
Moreover, trade shows and expos offer a comprehensive overview of the CNC materials market in China. Exhibitors from various regions and industries participate, presenting a wide array of products and options. This allows buyers to compare different offerings, evaluate the latest advancements in CNC materials, and identify potential partners that align with their specific sourcing needs.
Additionally, attending these industry events enables buyers to stay updated on the latest trends, technologies, and innovations in the CNC materials sector. Manufacturers often showcase their cutting-edge products and demonstrate their capabilities, giving buyers insights into the potential of these materials to enhance their operations. This knowledge can be used to optimize sourcing strategies and stay ahead of competitors by incorporating the latest advancements into product development and manufacturing processes.
In conclusion, trade shows and expos serve as valuable platforms for sourcing CNC materials in China. The direct interaction with suppliers, comprehensive market overview, and exposure to the latest trends make these events indispensable for buyers seeking to establish reliable and competitive supply chains. By leveraging these opportunities, companies can maximize their chances of finding high-quality materials, establishing fruitful partnerships, and staying at the forefront of the CNC materials industry.
The Role of Agents and Sourcing Companies in Facilitating cnc materials Purchases from China
Agents and sourcing companies play a crucial role in facilitating CNC materials purchases from China. China is one of the leading manufacturers and suppliers of CNC materials, offering a wide range of options at competitive prices. However, navigating the complexities of the Chinese market can be challenging for international buyers. This is where agents and sourcing companies come in.
Agents act as intermediaries between buyers and Chinese manufacturers. They use their local knowledge and network to identify reliable suppliers that meet the buyer’s requirements. Agents help buyers communicate with manufacturers, negotiate prices, and ensure the quality of the CNC materials before shipment.
Sourcing companies, on the other hand, specialize in finding and validating suppliers for specific products. They have extensive databases and networks of manufacturers, enabling them to quickly source CNC materials from reliable suppliers. Sourcing companies also assist with quality control, shipping logistics, and managing the entire procurement process.
These agents and sourcing companies provide numerous benefits to buyers sourcing CNC materials from China. Firstly, they save buyers time and effort in finding suitable suppliers. Instead of conducting extensive research and traveling to China, buyers can rely on the expertise of agents and sourcing companies to identify the best suppliers.
Secondly, agents and sourcing companies have in-depth knowledge of the Chinese market and its suppliers. They understand the cultural nuances, regulations, and potential challenges of doing business in China. This knowledge helps buyers navigate the sourcing process more efficiently and avoid common pitfalls.
Additionally, agents and sourcing companies can negotiate better prices on behalf of the buyers. They have expertise in price negotiations and can leverage their relationships with manufacturers to secure competitive rates.
Furthermore, these intermediaries play a vital role in quality control. They inspect the CNC materials for compliance with specifications and standards before shipment, ensuring that buyers receive the desired quality. This is particularly important for international buyers who may face difficulties in monitoring the production process themselves.
In conclusion, agents and sourcing companies serve as valuable intermediaries in facilitating CNC materials purchases from China. They offer local expertise, save time and effort, negotiate competitive prices, and ensure quality control. Their role is crucial in helping international buyers navigate the complexities of the Chinese market and successfully procure CNC materials.
Price Cost Research for cnc materials manufacturers Companies in China, use temu.com and 1688.com
When conducting price cost research for CNC materials manufacturers in China, two popular platforms to consider are temu.com and 1688.com. These websites provide extensive listings of manufacturers and suppliers in various industries, including CNC materials.
Temu.com is a reliable platform that connects buyers with manufacturers and suppliers in China. It offers a wide range of products, including CNC materials, with detailed descriptions, specifications, and prices. The website also provides supplier verification and certification information to ensure the credibility and reliability of the manufacturers listed.
1688.com, on the other hand, is a Chinese B2B e-commerce platform owned by Alibaba. It offers a wide array of products, including CNC materials, from various suppliers and manufacturers in China. The platform allows users to browse through product catalogs, compare prices, and contact suppliers directly. 1688.com is a popular choice for sourcing products from China due to its vast supplier network and competitive pricing.
When conducting price cost research on these platforms, it is essential to consider the following steps:
1. Begin by searching for CNC materials manufacturers or suppliers on either temu.com or 1688.com. Use relevant keywords such as “CNC materials,” “CNC raw materials,” or “CNC components.”
2. Filter and refine the search results based on criteria such as price range, product specifications, and manufacturer location.
3. Evaluate the listed suppliers by reviewing their product descriptions, certifications, customer reviews, and ratings.
4. Check the minimum order quantities (MOQs), as they can significantly impact the overall cost of procurement.
5. Contact the shortlisted suppliers for further information, including specific pricing details, shipping costs, and payment terms. Consider requesting quotations for the desired quantity to compare prices effectively.
6. Analyze the pricing information obtained from different suppliers, considering factors such as product quality, delivery time, and after-sales support.
Keep in mind that while these platforms provide a convenient way to find manufacturers and compare prices, it is crucial to exercise due diligence and verify the credibility and reliability of the suppliers before entering into any business transactions.
Shipping Cost for cnc materials import from China
The shipping cost for importing CNC materials from China can vary depending on several factors. The most significant factors affecting the cost include the weight and dimensions of the materials, the distance between the origin and destination, the mode of transportation, and any additional services required.
When importing CNC materials, it is common to use either air freight or sea freight. Air freight is generally faster but more expensive, while sea freight is slower but more economical for larger shipments. The weight and dimensions of the materials will determine the shipping method and cost.
Additionally, the distance between China and the destination country influences the shipping cost. The longer the distance, the higher the cost. Customs duties and any other applicable taxes should also be taken into account.
Furthermore, additional services such as insurance, customs brokerage, and packaging may also be required, each adding to the overall shipping cost.
To estimate the shipping cost accurately, it is recommended to consult with shipping companies or freight forwarders who specialize in international trade. They can provide quotations based on the specific details of the shipment, enabling you to negotiate the best possible rate.
In conclusion, the shipping cost for CNC materials imported from China depends on various factors including weight and dimensions, distance, mode of transportation, and additional services required. Consulting shipping companies or freight forwarders will help determine the specific costs involved.
Compare China and Other cnc materials Markets: Products Quality and Price,Visible and Hidden Costs
China is a major player in the market for Computer Numerical Control (CNC) materials, offering a wide range of products at competitive prices. When comparing China to other CNC materials markets, several key factors need to be considered: products quality and price, visible and hidden costs.
In terms of products quality, China has made significant progress over the years. Initially known for producing lower-quality goods, the country has invested in improving manufacturing processes and implementing stricter quality control measures. As a result, China now offers a wide range of CNC materials that meet international standards. However, it is important to note that quality can vary among manufacturers, so buyers should carefully evaluate suppliers to ensure consistent product quality.
Price is a major advantage of China’s CNC materials market. The country’s robust manufacturing capabilities and economies of scale allow for competitive pricing compared to other markets. Chinese manufacturers can often offer prices that are lower than their counterparts in other countries, making it an attractive option for cost-sensitive buyers. However, it is essential to balance the cost savings with the desired quality to avoid compromising the final product.
Visible costs, such as the initial product price, transportation, and import duties, play a significant role in comparing China with other CNC materials markets. Chinese suppliers generally offer competitive pricing and have well-established logistics networks, enabling efficient shipping processes. However, import duties and transportation costs can vary depending on the buyer’s location and the supplier’s terms, so careful consideration is needed to accurately compare costs.
Hidden costs can also impact the overall cost of sourcing CNC materials from China. These include factors such as intellectual property protection, product certification, and supplier reliability. China has faced criticism in the past for intellectual property infringement, so buyers must take appropriate measures to safeguard their designs and inventions. Additionally, obtaining product certifications, such as CE or UL, can involve additional expenses and time. Moreover, verifying the reliability and credibility of suppliers is crucial to ensure consistent product quality and timely delivery.
In conclusion, China’s CNC materials market provides a wide range of products at competitive prices, but buyers must carefully assess their specific requirements. While the country has made significant progress in terms of product quality, differences may still exist among manufacturers. Moreover, visible costs such as product price, transportation, and duties should be compared alongside hidden costs such as intellectual property protection and supplier reliability. Overall, China continues to be an attractive option for CNC materials sourcing, but due diligence is required to ensure a successful partnership.
Understanding Pricing and Payment Terms for cnc materials: A Comparative Guide to Get the Best Deal
When it comes to purchasing materials for CNC (Computer Numerical Control) machining, understanding pricing and payment terms is crucial to ensure you get the best possible deal. This comparative guide aims to provide an overview of key factors to consider when negotiating pricing and payment terms for CNC materials.
One important aspect to consider is the type and quality of materials required for your CNC project. Different materials such as metals, plastics, and composites vary in cost, and the specific requirements of your project may influence the pricing. It is essential to clearly communicate your material specifications to suppliers to receive accurate pricing information.
Another crucial factor is the quantity of materials you intend to purchase. Bulk purchases often lead to discounted prices, as suppliers can benefit from economies of scale. Consider estimating your material requirements in advance to leverage volume-based pricing, which can significantly reduce costs.
Additionally, the sourcing strategy you adopt can impact pricing. Local suppliers may offer competitive prices due to reduced transportation costs, while international suppliers might have lower labor or material expenses. However, it is important to carefully evaluate the overall cost, including shipping fees, import duties, and potential delivery delays when dealing with international suppliers.
Negotiating payment terms is equally important. Suppliers may offer various payment options such as upfront payments, installments, or credit terms. While upfront payments may secure better pricing, they might pose a financial strain on your part. Installments can help alleviate immediate financial impact, but suppliers may charge interest. Credit terms provide flexibility by allowing you to pay after delivery, but they are subject to credit checks and may come with higher pricing due to the extended financial risk assumed by the supplier.
To effectively compare pricing and payment terms, it is recommended to obtain quotations from multiple suppliers. This will not only provide you with an understanding of the average market price but also allow you to negotiate better deals. Ensure that all quotes include the same specifications to facilitate accurate comparisons.
In conclusion, understanding pricing and payment terms for CNC materials is crucial to secure the best deal for your project. Consider factors such as material type, quantity, sourcing strategy, and negotiate payment terms to optimize costs. Obtaining quotations from multiple suppliers and carefully evaluating the overall value offered will help you make an informed decision.
Chinese Regulations and Industry Standards Certifications for cnc materials,Import Regulations and Customs for cnc materials from China
In China, the CNC (Computer Numerical Control) industry is regulated and governed by several regulations and industry standards certifications. These regulations ensure product safety, quality, and compliance within the CNC materials sector.
One important certification for the CNC materials industry is the ISO 9001:2015 certification. This certification demonstrates that a company has implemented a quality management system and meets international standards for product quality and customer satisfaction.
Additionally, the China Compulsory Certification (CCC) mark is mandatory for certain CNC materials, indicating that they comply with safety and quality requirements established by the Chinese government.
Importing CNC materials from China requires adherence to specific regulations and customs procedures. Importers need to ensure compliance with their respective country’s import regulations, which may include inspection and authentication of imported goods at customs. Proper documentation, such as invoices, Customs Declaration Forms, and packing lists, must be provided to facilitate customs clearance.
In some cases, importers may need to obtain specific certifications or test reports for the CNC materials being imported. For example, if the CNC materials are intended for use in specific industries, such as automotive or aerospace, additional certifications or approvals might be necessary to meet industry-specific standards and requirements.
It is also essential to consider any applicable import duties, taxes, and customs fees that may be levied on imported CNC materials. Importers should consult with customs brokers or trade professionals to understand these costs and ensure compliance with customs regulations, such as accurate classification of the products for duty determination.
In summary, Chinese regulations and industry standards certifications, such as ISO 9001:2015 and CCC, ensure the quality and safety of CNC materials. Importing CNC materials from China requires compliance with import regulations, customs procedures, and potential certifications specific to the industry and intended use of the materials.
Sustainability and Environmental Considerations in cnc materials Manufacturing
Sustainability and environmental considerations have become increasingly important in the manufacturing industry, including CNC materials manufacturing. CNC (Computer Numerical Control) technology is widely used in various manufacturing processes, including cutting, shaping, and drilling of materials such as metal, plastic, and wood.
One major sustainability concern in CNC materials manufacturing is the energy consumption of CNC machines. These machines often require significant amounts of electricity to operate, contributing to carbon emissions and climate change. To mitigate this, manufacturers can explore options for using renewable energy sources and employing energy-efficient CNC machines. Additionally, implementing measures to optimize machine utilization and reduce idle time can further enhance energy efficiency.
Another environmental consideration in CNC materials manufacturing is waste generation and disposal. The cutting processes employed by CNC machines often generate a significant amount of waste material. Proper waste management strategies, such as recycling and reuse, should be implemented to minimize the environmental impact. Additionally, manufacturers should aim to reduce material waste by optimizing cutting paths and employing software tools that efficiently nest parts, minimizing the amount of material required.
Furthermore, the choice of materials used in CNC manufacturing also plays a crucial role in sustainability. Manufacturers can opt for eco-friendly materials, such as those made from recycled or biodegradable materials. Additionally, utilizing sustainable sourcing practices, such as ensuring suppliers adhere to responsible forest management, can help reduce the environmental impact of CNC materials manufacturing.
In conclusion, sustainability and environmental considerations are paramount in CNC materials manufacturing. By optimizing energy consumption, managing waste effectively, and making conscious choices regarding materials sourcing, manufacturers can contribute to a more sustainable and environmentally friendly manufacturing industry. Embracing sustainable practices in CNC materials manufacturing will not only benefit the environment but also help meet the increasing demand for sustainable products in the market.
List The Evolution history of “cnc materials”
The evolution of CNC (Computer Numerical Control) materials can be traced back to the mid-20th century. The earliest CNC machines were primarily used for metalworking processes, such as milling and turning. These machines utilized traditional materials like steel and iron. However, as technology advanced, newer materials were introduced to enhance the capabilities of CNC machines.
In the 1970s, the field of composites emerged, leading to the use of fiberglass and carbon fiber reinforced polymers in CNC applications. These materials offered improved strength-to-weight ratios and resistance to corrosion, making them ideal for aerospace and automotive industries. CNC machines were adapted to process these materials, enabling intricate designs and lightweight components.
In the 1980s, advancements in technology led to the use of ceramics in CNC machines. Ceramics provided excellent thermal stability and wear resistance, making them suitable for high-speed machining and industries requiring extreme precision, such as the semiconductor industry.
The 1990s saw a breakthrough in CNC material with the development of advanced plastics and polymers. These materials possessed enhanced mechanical properties, chemical resistance, and dimensional stability, making them popular in various sectors, including medical, electronics, and consumer goods.
In recent years, CNC materials have seen a significant shift towards advanced engineered metals. Aluminum and titanium alloys have gained prominence due to their exceptional strength, lightweight properties, and corrosion resistance. These materials are extensively used in the aerospace industry, where CNC machines shape intricate components to meet stringent specifications.
Furthermore, advancements in additive manufacturing have expanded the range of CNC materials. 3D printing techniques enabled the production of intricate structures using a wide range of materials, including metals, plastics, ceramics, and even biomaterials. This has revolutionized CNC applications, offering increased design flexibility and reduced manufacturing lead times.
Overall, the evolution of CNC materials has been driven by the need for improved performance, reduced weight, and increased precision. From traditional metals to composites, ceramics, and advanced engineered metals, CNC technology continues to push the boundaries and explore innovative materials for various industries.
The Evolution and Market Trends in cnc materials Industry
The CNC (Computer Numerical Control) materials industry has witnessed significant evolution and market trends over the years. CNC machines allow for precise and automated manufacturing processes, providing numerous benefits such as improved productivity, flexibility, and consistency. As a result, the demand for CNC materials has been steadily increasing, driving innovation and developments within the industry.
One key evolution in the CNC materials industry is the introduction of advanced composite materials. These materials offer a high strength-to-weight ratio, making them ideal for applications that require lightweight yet durable components. CNC machines can easily shape and cut these materials, allowing for the creation of complex and intricate designs.
Another notable trend in the CNC materials industry is the growing adoption of sustainable and eco-friendly materials. With a focus on environmental conservation, manufacturers are seeking materials that are recyclable, biodegradable, or sourced from renewable resources. CNC machining provides the precision required to work with these materials, enabling the production of eco-conscious products.
Moreover, there has been a shift towards multi-material CNC machining. This involves using different materials in a single CNC project to optimize performance and functionality. For example, combining metals and plastics can result in parts that exhibit both strength and lightweight characteristics. This trend allows for the creation of more versatile and efficient products.
Additionally, advancements in CNC technology have contributed to the market trends in the industry. The introduction of 5-axis CNC machines has revolutionized manufacturing capabilities by enabling the production of complex geometries with higher precision. This has expanded the range of materials that can be used in CNC machining, including metals, composites, plastics, and even ceramics.
In conclusion, the CNC materials industry has evolved significantly, driven by market trends such as the adoption of advanced composites, sustainable materials, multi-material machining, and advancements in CNC technology. These trends have not only improved the quality and efficiency of CNC manufacturing but have also opened up new possibilities for innovation in various industries such as aerospace, automotive, and healthcare.
Custom Private Labeling and Branding Opportunities with Chinese cnc materials Manufacturers
Chinese CNC materials manufacturers offer custom private labeling and branding opportunities for businesses looking to establish their own unique identity in the market. With a wide range of CNC materials and expertise in manufacturing, these manufacturers can help businesses create tailored products that meet their specific requirements.
One of the key advantages of partnering with Chinese CNC materials manufacturers is their ability to provide private labeling. This means businesses can have their logo, design, or brand name printed or engraved on the CNC materials. Customizing products in this way enables businesses to increase brand visibility and strengthen their brand recognition in the market.
Moreover, Chinese manufacturers also offer branding opportunities. This involves collaborating with businesses to create exclusive designs and product lines that are unique to their brand. By working closely with experienced CNC materials manufacturers, businesses can develop products that showcase their brand’s identity and values, allowing them to stand out from competitors.
Chinese manufacturers have a wealth of experience in CNC materials production and a deep understanding of market demands. They employ advanced technologies and have a skilled workforce to ensure high-quality manufacturing. This expertise, combined with their ability to customize products, makes them an ideal partner for businesses looking for branded CNC materials.
In conclusion, Chinese CNC materials manufacturers offer custom private labeling and branding opportunities, enabling businesses to differentiate themselves in the market and build brand recognition. With their expertise in CNC material production and customization, businesses can create unique products that align with their brand’s values. Collaborating with Chinese manufacturers provides a cost-effective and efficient solution for businesses looking to establish their brand in the CNC materials market.
Tips for Procurement and Considerations when Purchasing cnc materials
When purchasing CNC materials, there are several tips and considerations to keep in mind to ensure successful procurement. Here are some key points to consider:
1. Define your requirements: Clearly establish the specifications and quantity of CNC materials required for your project. Consider factors such as material type, size, dimensions, and tolerances.
2. Identify reliable suppliers: Research and identify reputable suppliers who specialize in providing CNC materials. Look for suppliers with a proven track record, positive customer reviews, and certifications.
3. Quality assurance: Ensure that the supplier follows strict quality control measures. Request samples or test reports to evaluate the quality of the CNC materials before making a purchase.
4. Pricing: Obtain multiple quotes from different suppliers to compare prices. However, keep in mind that the lowest price may not always guarantee the best quality. Take into account the supplier’s reputation, quality, and delivery capabilities.
5. Delivery time: Discuss the expected delivery timeframes with the supplier. Ensure that the supplier can meet your project deadlines and consider any potential delays that may occur.
6. Material availability: Check the availability of the CNC materials you require. Some materials may have longer lead times or limited availability, so it is important to plan ahead.
7. Industry standards: Verify if the CNC materials meet relevant industry standards and certifications, such as ISO or ASTM. This ensures that the materials comply with necessary quality and performance requirements.
8. Customization options: Discuss any additional customization requirements with the supplier. Some suppliers may offer value-added services like cutting, machining, or surface treatments.
9. Packaging and transportation: Inquire about the packaging and transportation methods used by the supplier to ensure safe delivery of the CNC materials. Proper packaging can prevent damage during transit.
10. Payment terms: Agree on payment terms and methods with the supplier. Consider negotiating discounts for bulk orders or establishing a long-term business relationship.
By following these tips and considering these factors, you can streamline your procurement process and ensure that you purchase high-quality CNC materials that meet your project requirements.
FAQs on Sourcing and Manufacturing cnc materials in China
1. Why should I source and manufacture CNC materials in China?
Sourcing and manufacturing CNC materials in China can offer several advantages. China has a well-established manufacturing industry, with numerous specialized factories and suppliers that can provide high-quality CNC materials at competitive prices. The country also has a large labor force, which enables faster production and shorter lead times. Moreover, China’s extensive supply chain network ensures a wide range of materials and components are readily available.
2. How do I find suitable suppliers in China?
Finding reliable suppliers in China can be done through various methods. Online platforms, such as Alibaba and Global Sources, are popular for connecting with suppliers. Attending trade shows and exhibitions, like the Canton Fair, provides an opportunity to meet potential suppliers face-to-face. Additionally, engaging the services of a reputable sourcing agent or using sourcing websites can help streamline the process by vetting suppliers and negotiating contracts on your behalf.
3. What quality control measures should I implement when sourcing CNC materials from China?
Implementing quality control measures is crucial to ensure the CNC materials sourced from China meet your requirements. These measures can include conducting pre-production inspections to confirm supplier capabilities, performing in-process inspections to monitor production progress, and conducting final inspections before shipment. Hiring third-party quality inspection companies to perform random checks or full inspections can provide an unbiased evaluation of product quality.
4. Are there any risks associated with sourcing and manufacturing CNC materials in China?
While China offers several advantages, there are also certain risks to consider. Intellectual property protection can be a concern, so it is important to safeguard proprietary designs or technologies. Language and cultural barriers may pose communication challenges, so effective communication channels should be established. Additionally, product quality inconsistencies and counterfeit goods can occur, emphasizing the need for thorough supplier vetting and implementing quality control processes.
5. Are there any specific regulations or certifications I should be aware of when sourcing from China?
When sourcing CNC materials from China, it is essential to ensure compliance with relevant regulations and certifications. Depending on the type of material and its application, certifications such as ISO 9001 for quality management systems or RoHS for restricted hazardous substances might be required. China also has specific import and export regulations that need to be followed, including customs procedures and documentation requirements.
In conclusion, sourcing and manufacturing CNC materials in China can offer numerous benefits due to its well-established manufacturing industry, competitive prices, and extensive supply chain network. However, it is essential to conduct thorough supplier vetting, establish effective quality control measures, and ensure compliance with regulations to mitigate risks and ensure the desired product quality.
Why contact sourcifychina.com get free quota from reliable cnc materials suppliers?
Sourcifychina.com, a sourcing platform, offers a free quota from reliable CNC materials suppliers to help businesses easily find the right supplier for their needs. Here are the reasons behind this initiative.
Firstly, Sourcifychina.com aims to simplify the supplier selection process for businesses. Finding reliable and high-quality CNC materials suppliers can be a daunting and time-consuming task. By providing a free quota, the platform allows businesses to connect with multiple suppliers, compare their offerings, and make informed decisions without incurring any financial risk.
Secondly, the platform understands the importance of sourcing from reliable suppliers. The quality of CNC materials directly affects the final product, so it is crucial to find trustworthy suppliers with a proven track record. By partnering with reliable CNC materials suppliers, Sourcifychina.com ensures that businesses have access to reputable sources for their production needs.
Additionally, offering a free quota encourages businesses to explore different options. It allows them to connect with multiple suppliers and gather quotes and information without any upfront cost. This way, businesses can obtain a comprehensive understanding of the market, compare prices, negotiate better deals, and make more informed decisions about their sourcing strategy.
Furthermore, Sourcifychina.com aims to foster long-term relationships between businesses and suppliers. By offering a free quota, the platform encourages businesses to engage with suppliers and build a relationship based on trust and mutual benefits. This approach helps establish a sustainable supply chain, which is vital for the success of any manufacturing business.
In conclusion, Sourcifychina.com provides a free quota from reliable CNC materials suppliers to simplify the supplier selection process, promote sourcing from trustworthy suppliers, enable businesses to explore different options, and foster long-term relationships. This initiative ultimately aims to make sourcing CNC materials more efficient, cost-effective, and risk-free for businesses.