Introduce about cnc milling cutter guide,Qulity,Cost,Supplier,Certification,Market,Tips,FAQ
CNC milling cutter guides are essential tools used in the milling process to accurately shape and cut various materials. They provide guidance and support for the milling cutter, ensuring precision and efficiency.
Quality is of utmost importance when selecting a CNC milling cutter guide. The guide should be made from durable materials, such as high-speed steel or carbide, to withstand the rigors of milling. It should also have a precise design to maintain accuracy throughout the machining process.
Cost considerations play a significant role in selecting a milling cutter guide. Factors such as the materials used, design complexity, and brand can affect the price. It’s important to balance the quality and cost to ensure optimal value for money.
When it comes to suppliers, it is advisable to choose reputable and reliable companies. Look for suppliers that have experience in producing milling cutter guides and have positive customer reviews. It is also essential to consider their ability to provide consistent and timely delivery.
Certification is crucial as it ensures that the milling cutter guide meets specific standards set by regulatory bodies. Look for guides that are certified by recognized organizations such as ISO (International Organization for Standardization) to ensure product quality.
In terms of the market, CNC milling cutter guides are widely used in industries such as aerospace, automotive, and manufacturing. The demand for these guides continues to grow as technology advances and more precise machining is required.
Here are some tips when using a CNC milling cutter guide:
1. Ensure proper alignment and secure attachment of the guide to the milling machine.
2. Regularly inspect the guide for any signs of wear or damage and replace if necessary.
3. Use the appropriate cutting speed and feed rate for different materials to achieve optimal results.
4. Apply cutting fluid or lubricant to reduce friction and heat generated during the cutting process.
FAQ:
Q: Can I use a CNC milling cutter guide for different materials?
A: Yes, milling cutter guides are versatile and can be used for various materials such as metal, plastic, and wood.
Q: How long does a milling cutter guide last?
A: The lifespan of a guide depends on factors like the material, usage, and maintenance. However, with proper care, a high-quality guide can last for a long time.
Q: Can I resharpen a worn-out milling cutter guide?
A: It is generally not recommended to resharpen milling cutter guides as it can alter their dimensions and compromise accuracy. It is best to replace them with new ones.
In summary, CNC milling cutter guides are crucial tools for precise and efficient milling operations. Consider factors like quality, cost, supplier reputation, certification, and market demands when selecting a guide. Use these tips and guidelines to maximize the performance and longevity of your milling cutter guide.
Types of cnc milling cutter
CNC milling cutters are tools used in computer numerical control (CNC) milling machines to perform various cutting operations on a workpiece. These cutters come in various types, each designed for specific purposes and materials. Here are some common types of CNC milling cutters:
1. End Mill: End mills are the most common type of milling cutter used in CNC machines. They have cutting edges on both the bottom and the sides, allowing them to remove material both axially and laterally. End mills are versatile and can perform a wide range of cutting operations such as slotting, profiling, and contouring.
2. Ball Nose Cutter: Ball nose cutters have a rounded end that provides a smoother cutting action, reducing the chances of chipping or fracturing the workpiece. They are commonly used for 3D contouring and milling curved surfaces.
3. Face Mill: Face mills have cutting edges on the face and the sides of the cutter. They are ideal for facing large surfaces and creating flat-bottomed cavities. Face mills can remove a significant amount of material quickly.
4. Slab Mill: Slab mills are similar to face mills but have a wider cutting diameter. They are used for heavy-duty machining, removing large amounts of material in a single pass.
5. T-Slot Cutter: T-slot cutters have a T-shaped groove on their cutting surface. They are used to create T-slots in machine tables or other workpiece fixtures.
6. Thread Mill: Thread mills are used to create internal or external threads on a workpiece. They come in various profiles and sizes to match different thread specifications.
7. Shell Mill: Shell mills have a larger diameter compared to end mills. They are used for roughing operations, removing material quickly, and creating flat surfaces.
8. Slitting Cutter: Slitting cutters are used to cut slots, grooves, or slits into the workpiece. They have multiple cutting edges along their circumference.
9. Fly Cutter: Fly cutters have a single cutting edge and are used for shallow milling or facing operations. They are generally large in diameter and operate at high speeds.
10. Woodruff Cutter: Woodruff cutters are used to create keyways, especially in shafts or hubs. They have a disc-shaped cutter with a profiled groove.
These are just a few examples of CNC milling cutters, and there are many more specialized cutters available for specific applications. The selection of the appropriate cutter depends on factors such as the material being machined, the desired surface finish, and the required cutting speed and feed rate.
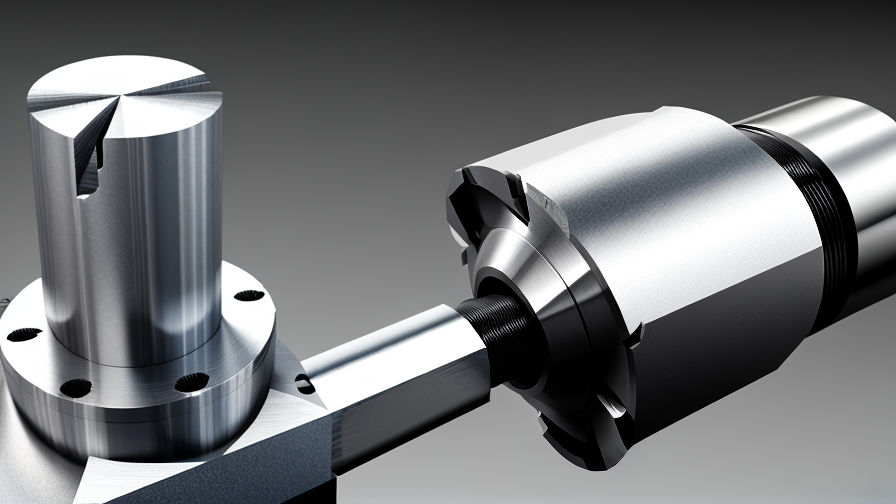
Pros and Cons of Using cnc milling cutter
CNC milling cutters are widely used in various industries for their precision and versatility. They offer several advantages as well as some disadvantages that need to be considered before using them.
Pros:
1. Precision: CNC milling cutters provide extremely high precision and accuracy in cutting and shaping materials. They can achieve tight tolerances and produce complex shapes with ease, ensuring consistent and quality results.
2. Versatility: These cutters can work with a wide range of materials, including metals, plastics, wood, and composites. They can perform various operations such as drilling, contouring, grooving, and slotting, making them suitable for various applications in different industries.
3. Efficiency and productivity: CNC milling cutters are programmable and automated, allowing for higher productivity and efficiency. Once programmed, they can operate continuously and consistently, reducing manual labor and increasing production rates.
4. Cost-effective: Despite the initial investment being relatively high, CNC milling cutters can prove to be cost-effective in the long run. They reduce material wastage, minimize errors, and require less manual labor, leading to cost savings and increased profitability.
5. Complex part production: CNC milling cutters excel in the production of complex parts with intricate details. They can replicate designs accurately and consistently, making them suitable for industries such as aerospace, automotive, and medical where precision is crucial.
Cons:
1. Initial setup and programming: The initial setup and programming of CNC milling cutters can be time-consuming and require skilled operators. It may take some time to optimize the settings and program the cutter for specific tasks.
2. High initial cost: The cost of acquiring CNC milling cutters can be high, especially for small businesses or individuals. The machines themselves, along with the required software and maintenance, may require a significant investment.
3. Maintenance and tooling costs: CNC milling cutters require regular maintenance and replacement of tools, which can add to the overall operating costs. Proper maintenance and tooling are crucial to ensure the longevity and performance of the cutters.
4. Limited flexibility: While CNC milling cutters are versatile, their capabilities may have limitations. Some designs or materials may be challenging to work with, and certain intricate shapes may require additional setup or specialized cutters.
5. Dependence on power supply: CNC milling cutters rely on a stable power supply, and any power disruptions or failures can cause interruptions in the production process. Backup power options or contingency plans may be required to mitigate these risks.
In conclusion, CNC milling cutters offer precision, versatility, and increased productivity, making them valuable tools for various industries. However, they require an initial investment, skilled operators, and regular maintenance. Considering both the pros and cons will help determine if CNC milling cutters are the right choice for specific applications and budgets.
cnc milling cutter Reference Specifications (varies for different product)
CNC milling cutters are versatile tools used in the machining industry for cutting, shaping, and finishing various materials such as metal, plastic, and wood. These cutters are designed to be used with CNC (Computer Numerical Control) machines to achieve precision and accuracy in the milling process.
The reference specifications of CNC milling cutters may vary depending on the specific product and its intended application. However, some common specifications can be found across different products. Here are some key reference specifications to consider:
1. Material: CNC milling cutters are made from various materials such as high-speed steel (HSS), carbide, or cobalt. The choice of material depends on factors like the type of material being machined, cutting speed, and tool life required.
2. Diameter: The diameter of the milling cutter refers to the width of the cutting edge. It determines the maximum width of the cut and influences the material removal rate. Different diameters are available to accommodate various milling operations.
3. Flute Number: The number of flutes or cutting edges on the milling cutter affects chip evacuation and the surface finish of the machined part. Common options include two, three, or four flutes.
4. Coating: Coatings like titanium nitride (TiN), titanium carbonitride (TiCN), or aluminum titanium nitride (AlTiN) can be applied to the milling cutter to increase tool life, improve cutting performance, and reduce friction and heat.
5. Shank Type: CNC milling cutters come in various shank types, including cylindrical, Weldon, and Morse taper. The shank type should match the machine’s tool-holder system for proper tool clamping.
6. Helix Angle: The helix angle represents the spiral angle of the flutes on the cutter. It influences chip evacuation, cutting forces, and surface finish. Steep helix angles are suitable for high-speed machining, while shallow angles are used for heavy-duty cutting.
7. Cutting Length: The cutting length refers to the part of the milling cutter that is in contact with the workpiece during the cutting process. It determines the maximum depth of cut achievable.
These specifications provide a general understanding of the factors to consider when selecting a CNC milling cutter for a particular application. However, it is important to consult the manufacturer’s specific product documentation for accurate and detailed reference specifications to ensure optimal performance and safety.
Applications of cnc milling cutter
CNC milling cutters are versatile tools used in various industries for a range of applications. Some of the common applications of CNC milling cutters include:
1. Prototyping: CNC milling cutters are widely used in the prototyping stages of product development. They allow engineers and designers to quickly and accurately machine complex shapes and designs from various materials, such as metals, plastics, and composites. This enables rapid iteration and testing of prototypes before moving to the production stage.
2. Aerospace and automotive industry: CNC milling cutters play a critical role in the manufacturing of components for aerospace and automotive applications. They are used to machine precision parts, such as turbine blades, engine blocks, transmission components, and structural elements. The high precision and repeatability of CNC milling cutters ensure that these components meet stringent quality standards and tolerances.
3. Tool and die making: CNC milling cutters are extensively used in tool and die making industries for the production of molds, dies, and other tooling. The ability to machine complex geometries and contours allows for the precise replication of intricate shapes required for production purposes. The use of CNC milling cutters in tool and die making helps to reduce lead times and improve overall manufacturing efficiency.
4. Medical device manufacturing: CNC milling cutters are used in the production of medical devices, such as orthopedic implants, surgical instruments, and prosthetics. The high precision and accuracy of CNC milling cutters ensure that these devices are manufactured to meet specific patient needs and strict regulatory requirements.
5. Electronics and semiconductor industry: CNC milling cutters are utilized in the production of circuit boards, microchips, and other electronic components. They help to create intricate patterns and features on these components, enabling the miniaturization and integration of electronic circuits. CNC milling cutters ensure the precise machining required for high-performance electronic devices.
6. General manufacturing: CNC milling cutters find applications in various general manufacturing industries, including furniture, mold making, jewelry, and consumer goods. They are used to machine parts, molds, and prototypes required for production lines and custom orders. CNC milling cutters provide the flexibility and accuracy required to meet diverse manufacturing needs.
In conclusion, CNC milling cutters are indispensable tools in modern manufacturing processes. Their versatility, precision, and ability to machine various materials make them well-suited for prototyping, aerospace and automotive industries, tool and die making, medical device manufacturing, electronics and semiconductor industry, as well as general manufacturing applications.
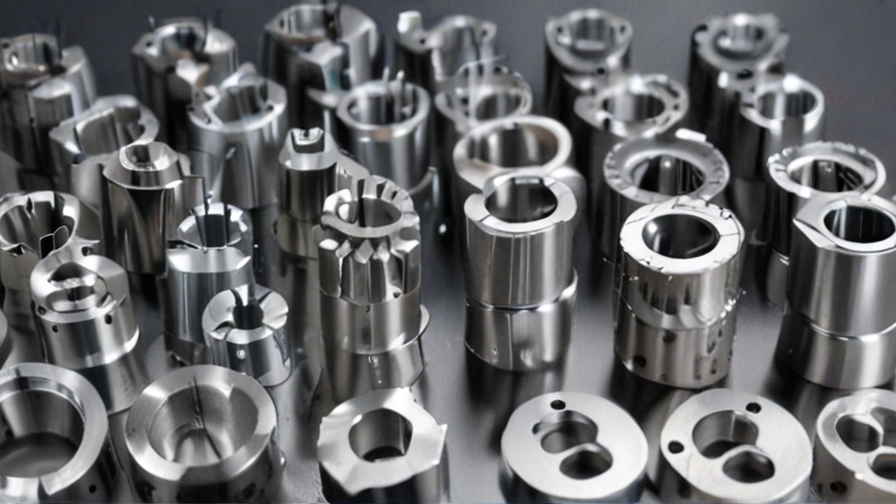
The Work Process and how to use cnc milling cutter
CNC milling is a process that involves the use of computer numerical control (CNC) machines to remove material from a workpiece using rotating multi-point cutting tools, known as milling cutters. Here is a brief overview of the work process and steps involved in using a CNC milling cutter.
1. Design: The first step is to create a design or 3D model of the desired part using computer-aided design (CAD) software. This design is then converted into a CNC program that controls the milling machine.
2. Setup: The workpiece is securely clamped onto the CNC milling machine table. The milling cutter is inserted into the spindle, which is controlled by the CNC program. The cutting tool is carefully selected based on the material being machined and the desired outcome.
3. Tooling: The milling cutter is equipped with several cutting edges, called flutes, which vary in number and shape depending on the type of milling operation required. The most common types of milling cutters include end mills, face mills, ball mills, and chamfer mills.
4. Programming: The CNC program is loaded onto the machine’s controller, specifying the tool path, cutting speeds, feed rates, and other parameters. The program guides the machine on how to move the milling cutter in various directions (X, Y, and Z axes) to shape the workpiece.
5. Machining: Once the setup and programming are complete, the CNC milling machine starts removing material from the workpiece. The milling cutter rotates at high speeds, while the workpiece is moved in multiple axes to create the desired shape or features.
6. Finishing: Multiple passes may be required to achieve the desired level of precision, surface finish, and dimensional accuracy. This can involve changing the milling cutter or adjusting the cutting parameters.
7. Inspection: Once the milling process is completed, the finished part is inspected to ensure it meets the required specifications and tolerances. Any necessary adjustments or additional operations can be carried out if needed.
8. Post-processing: Depending on the specific application, the finished part may undergo additional processes such as heat treatment, coating, or assembly before it is deemed complete.
To use a CNC milling cutter effectively, it is essential to have a strong understanding of the machine’s capabilities, cutting parameters, tool selection, and programming. Proper training and experience are necessary to ensure safe operation and optimum results. It is also crucial to regularly maintain and sharpen the milling cutters to maintain their performance and longevity.
Quality Testing Methods for cnc milling cutter and how to control the quality
When it comes to quality testing methods for CNC milling cutters, there are several techniques that can be employed to ensure the desired level of quality. The key is to control the overall quality throughout the manufacturing process.
Firstly, visual inspection is an essential method to assess the external appearance of the milling cutter. Any visible defects such as cracks, dents, or deformations should be identified and rejected to maintain the desired quality.
Dimensional inspection is another important aspect of quality control. It involves measuring critical dimensions of the milling cutter using precise tools such as calipers or micrometers. This ensures that the cutter is produced within the specified tolerance range and maintains the required accuracy.
A hardness test can also be performed to evaluate the hardness of the milling cutter. This test helps determine whether the material used in the cutter meets the desired hardness requirements, which is crucial for the cutter’s performance and longevity.
Additionally, a cutting performance test can be conducted to assess the milling cutter’s efficiency and effectiveness. This involves cutting a material sample using the cutter and analyzing the results in terms of surface finish, precision, and chip formation. This test verifies whether the cutter is capable of producing the desired outcomes.
To control the quality of CNC milling cutters, it is necessary to implement a robust quality management system. This system should include regular inspections at every stage of the manufacturing process, starting from raw material procurement to the final product. Each inspection should be meticulously documented, and non-conforming products should be promptly identified and segregated.
Furthermore, supplier evaluations and audits should be conducted to ensure that only high-quality materials and components are used. Establishing clear specifications and standards for the milling cutters and continuously monitoring and analyzing the manufacturing process are also critical to maintaining quality control.
Regular training of the personnel involved in the manufacturing process is vital to enhance their understanding of quality requirements and to ensure consistent adherence to quality control procedures.
Implementing these quality testing methods and establishing a comprehensive quality management system will help ensure the production of CNC milling cutters that meet the desired standards of quality and performance.
cnc milling cutter Sample Policy and Post-Purchase Considerations for cnc milling cutter from China
Sample Policy:
When purchasing CNC milling cutters from China, it is essential to inquire about the supplier’s sample policy. Some suppliers may offer free samples, while others may charge a sample fee or require the buyer to cover shipping costs. It is advisable to request samples to evaluate the quality, performance, and compatibility of the CNC milling cutter before making a bulk purchase. Additionally, inquire about the lead time for sample production and delivery.
Post-Purchase Considerations:
After purchasing CNC milling cutters from China, there are several post-purchase considerations to keep in mind:
1. Quality Assurance: Ensure that the supplier has a reliable quality control system in place to maintain consistent product quality. Ask for certifications, such as ISO or RoHS, as evidence of their commitment to quality.
2. Performance Evaluation: Thoroughly test the CNC milling cutter in real-world applications to determine its performance, durability, and accuracy. Assess the cutting speed, precision, and surface finish it provides.
3. Warranty Policy: Inquire about the warranty policy provided by the supplier. Be aware of the terms and conditions, such as the duration of the warranty and any limitations or exclusions that may apply.
4. Technical Support: Verify if the supplier offers technical support or assistance with troubleshooting and maintenance. Reliable technical support can help address any issues that may arise during the use of the CNC milling cutter.
5. Delivery and Logistics: Evaluate the efficiency and reliability of the supplier’s shipping and logistics processes. Prompt delivery and proper packaging are crucial to ensure that the CNC milling cutters reach their destination safely and in a timely manner.
6. Price and Payment Terms: Review the pricing structure and payment terms agreed upon. Ensure that both parties are clear on the payment method, currency, and any potential additional costs, such as taxes or import duties.
By considering these aspects, buyers can mitigate risks and ensure a successful purchase of CNC milling cutters from China.
Sourcing cnc milling cutter from China: Opportunities, Risks, and Key Players
China offers many opportunities for sourcing CNC milling cutters due to its large manufacturing capacity, competitive pricing, and technological advancements. Chinese suppliers can provide a wide range of products, from standard to custom-made cutters, catering to different industry needs.
One of the main opportunities lies in cost advantages. China’s lower labor and production cost compared to many other countries allows for competitive pricing. This cost advantage combined with China’s well-established supply chain and infrastructure allows for efficient production and delivery of CNC milling cutters.
Moreover, China is home to numerous key players in the CNC milling cutter industry. Some of the prominent Chinese manufacturers include Sandvik Coromant, ZCCCT, Kyocera, and Mitsubishi Materials. These companies have established themselves as reliable suppliers, providing high-quality products that meet international standards.
However, there are risks associated with sourcing from China. Quality control can be a concern, as not all Chinese suppliers maintain the same level of quality standards. It is crucial to conduct thorough due diligence and select reputable suppliers with a strong track record and certifications, such as ISO 9001.
Another risk is intellectual property (IP) infringement. China has faced criticism in the past for intellectual property violations, including counterfeiting and piracy. To mitigate this risk, companies should ensure they work with suppliers that respect IP rights and employ appropriate legal measures and agreements to safeguard their designs and technologies.
In conclusion, sourcing CNC milling cutters from China offers numerous opportunities, including cost advantages and access to key players in the industry. However, risks such as quality control and IP infringement need to be carefully managed. By selecting reliable suppliers and implementing proper quality control measures, businesses can benefit from China’s manufacturing capabilities while minimizing potential risks.
How to find and select reliable cnc milling cutter manufacturers in China,use google search manufacturers and suppliers
When it comes to finding and selecting reliable CNC milling cutter manufacturers in China, utilizing Google search for manufacturers and suppliers can be an effective approach. Here are some steps to follow:
1. Begin by conducting a search on Google using relevant keywords like “CNC milling cutter manufacturers in China.”
2. Browse through the search results and visit the websites of potential manufacturers. Look for established companies with a good reputation and experience in the industry. Check if they have certifications or accreditations related to quality control and manufacturing standards.
3. Assess the manufacturer’s website for product information, capabilities, and the range of CNC milling cutters they offer. Look for details about their manufacturing processes, technology and equipment used, and their ability to provide custom solutions.
4. Look for customer testimonials or reviews on the manufacturer’s website or through other reliable sources. This can give you insights into their reputation, product quality, and customer satisfaction.
5. Check if the manufacturer has any partnerships or collaborations with reputed industry organizations or associations. This indicates their commitment to quality and continuous improvement.
6. Contact the manufacturers that meet your requirements and request additional information. Inquire about their production capacity, lead times, pricing, and quality control measures.
7. Ask for samples or visit their manufacturing facilities if possible. This can help you evaluate their production capabilities firsthand and assess the quality of their CNC milling cutters.
8. Consider reaching out to other industry professionals or associations for recommendations on reliable CNC milling cutter manufacturers in China.
9. Lastly, compare the shortlisted manufacturers based on factors such as product quality, price, delivery time, after-sales support, and overall reliability. Make a well-informed decision based on your specific requirements and preferences.
It is crucial to carry out due diligence and extensive research before finalizing any manufacturer. Examining multiple options, reading reviews, and gathering as much information as possible will help ensure you select a reliable CNC milling cutter manufacturer in China.
How to check cnc milling cutter manufacturers website reliable,use google chrome SEOquake check if ranking in top 10M
To ensure the reliability of a CNC milling cutter manufacturer’s website, you can follow the steps below:
1. Use Google Chrome: Start by opening the website in Google Chrome, which offers a variety of features and extensions to enhance your browsing experience.
2. Install SEOquake Extension: Install the SEOquake extension on your Google Chrome browser. This tool provides valuable insights about a website’s SEO performance, such as its overall ranking and organic visibility.
3. Check Ranking: After installing SEOquake, you can use it to determine the website’s ranking. Enter the desired keyword or keyphrase related to CNC milling cutters, and SEOquake will display the website’s current position in the search engine results pages (SERPs).
4. Top 10M Ranking: Pay attention to whether the website appears within the top 10 million search results. This indicates a relatively high level of visibility and authority for the manufacturer.
5. Analyze Results: Evaluate the SEOquake results in conjunction with other factors. A website’s ranking alone does not guarantee its reliability, so consider additional aspects such as customer reviews, certifications, product information, and presence on industry directories.
6. Trustworthy Manufacturers: Look for CNC milling cutter manufacturers that are well-established, recognized in the industry, and have a strong reputation for delivering quality products. Consider collaborating with manufacturers that have been in the business for a significant period, as they have likely gained the trust of customers over time.
7. Avoid Suspicious Websites: Be cautious of websites that have poor designs, broken links, excessive pop-ups, or a significant number of negative reviews. These are potential red flags indicating an unreliable or untrustworthy manufacturer.
By following these steps and conducting thorough research, you can identify reliable CNC milling cutter manufacturers and make informed decisions for your needs. Remember to consider factors beyond just website ranking to ensure you choose a manufacturer that aligns with your requirements.
Top 10 cnc milling cutter manufacturers in China with each 160 words introduce products,then use markdown create table compare
1. Jiangsu Soodtools Co., Ltd. – With over 20 years of experience, Jiangsu Soodtools is a leading manufacturer of CNC milling cutters in China. Their product range includes solid carbide end mills, indexable milling cutters, and drills. These tools are known for their high precision, excellent cutting performance, and long tool life. Their end mills are widely used in industries such as automotive, aerospace, and mold and die making.
2. Shenzhen ZLY Diamond Tool Co., Ltd. – Specializing in the production of diamond-coated tools, Shenzhen ZLY Diamond Tool is a renowned manufacturer of CNC milling cutters in China. Their products include diamond end mills, diamond abrasive cutters, and diamond chamfering tools. These tools are suitable for machining materials like graphite, composites, and ceramics. They offer excellent tool life, various cutting geometries, and high precision, making them ideal for applications in the electronics and aerospace industries.
3. ZCCCT Carbide Tools Co., Ltd. – ZCCCT Carbide Tools is a leading manufacturer of cemented carbide cutting tools in China. Their CNC milling cutter product range includes solid carbide end mills, ball nose mills, and indexable milling cutters. These precision tools offer high cutting speeds, excellent surface finishes, and improved productivity. ZCCCT’s milling cutters are widely used in industries such as automotive, aerospace, and general engineering.
4. Inmind Tools Co., Ltd. – Established in 2006, Inmind Tools is a prominent manufacturer of CNC milling cutters in China. Their product portfolio includes solid carbide end mills, drill bits, and reamers. With advanced production technology and strict quality control, Inmind Tools guarantees the performance and reliability of their milling cutters. Their tools are widely used in industries ranging from automotive to mold and die making.
| Manufacturer | Product Range | Key Features |
|————————-|———————————|———————————————–|
| **Jiangsu Soodtools** | Solid carbide end mills, indexable milling cutters, drills | High precision, excellent cutting performance, long tool life. |
| **Shenzhen ZLY Diamond Tool** | Diamond end mills, diamond abrasive cutters, diamond chamfering tools | Suitable for machining graphite, composites, ceramics. High precision, excellent tool life. |
| **ZCCCT Carbide Tools** | Solid carbide end mills, ball nose mills, indexable milling cutters | High cutting speeds, excellent surface finishes, improved productivity. |
| **Inmind Tools** | Solid carbide end mills, drill bits, reamers | Advanced production technology, strict quality control, wide application range. |
5. Suzhou Sunrix Precision Tools Co., Ltd. – Known for their precision and durability, Suzhou Sunrix Precision Tools is a major manufacturer of CNC milling cutters in China. Their product line includes ball nose end mills, corner radius end mills, and flat end mills. These tools are made from high-quality materials to ensure optimal performance and precision. Sunrix milling cutters find extensive application in aerospace, medical equipment, and electronics industries.
6. Chengdu Diamond Tools Co., Ltd. – Chengdu Diamond Tools specializes in producing high-quality polycrystalline diamond (PCD) and cubic boron nitride (CBN) tools. Their range of CNC milling cutters includes PCD end mills, CBN ball nose cutters, and CBN indexable inserts. These tools offer exceptional wear resistance and are suitable for machining non-ferrous materials, hardened steels, and superalloys. Chengdu Diamond Tools serves industries like automotive, aerospace, and precision engineering.
7. Dongguan Dohre Tool Co., Ltd. – Dongguan Dohre Tool is a well-established manufacturer of CNC milling cutters in China. Their product portfolio comprises solid carbide end mills, roughing end mills, and high-speed cutting tools. These tools feature high precision, excellent chip evacuation, and extended tool life. Dohre milling cutters are widely used in industries like automotive, mold and die making, and general machining.
8. Zhuzhou Sant Cutting Tools Co., Ltd. – Zhuzhou Sant Cutting Tools is a reputable manufacturer of cemented carbide cutting tools in China. Their CNC milling cutter range includes solid carbide end mills, carbide rotary burrs, and CNC router bits. These tools are widely utilized for milling, drilling, and grooving operations on various materials. Sant milling cutters offer exceptional stability, wear resistance, and precise chip evacuation.
9. Hangzhou Fengchi Import and Export Co., Ltd. – Hangzhou Fengchi is a leading supplier of cutting tools, especially CNC milling cutters, in China. Their product catalog includes solid carbide end mills, carbide corner radius cutters, and carbide T-slot cutters. These tools are designed to deliver high performance, excellent surface finishes, and increased productivity. Fengchi milling cutters cater to industries such as automotive, aerospace, and mold and die making.
10. Changzhou Accurate Cutting Tools Co., Ltd. – As a professional manufacturer of cutting tools, Changzhou Accurate Cutting Tools offers a wide range of CNC milling cutters in China. Their product range comprises solid carbide end mills, roughing end mills, and ball nose cutters. These tools are manufactured with precision and stringent quality control to meet the demanding requirements of industries such as automotive, aerospace, and general machining.
In conclusion, China boasts numerous reputable manufacturers known for producing CNC milling cutters with varying features and applications. From prominent companies like Jiangsu Soodtools and ZCCCT Carbide Tools to specialized manufacturers like Shenzhen ZLY Diamond Tool and Chengdu Diamond Tools, customers can access a wide range of high-quality tools to suit their specific machining needs.
Background Research for cnc milling cutter manufacturers Companies in China, use qcc.com archive.org importyeti.com
China is one of the leading manufacturers of CNC milling cutters in the world, with numerous companies specializing in their production. To gather background research on these manufacturers, several online platforms can be utilized, such as qcc.com, archive.org, and importyeti.com.
Qcc.com is a Chinese business data platform that provides information on various companies, including their registration details, financial status, and key personnel. This platform allows researchers to identify and gather information on Chinese CNC milling cutter manufacturers, such as their company names, contact details, and registered capital. Additionally, the platform may provide insights into the company’s history, size, and distribution networks.
Archive.org is a web archive platform that allows researchers to access and explore historical versions of websites. By utilizing this platform, researchers can retrieve data from the websites of CNC milling cutter manufacturers that might have been updated or removed in the present. This can be useful for obtaining past product catalogs, company profiles, and other relevant information that might not be readily available on current websites.
Importyeti.com is an import export data platform that offers valuable insights into global trade activities, including detailed records of companies involved in import/export transactions. Researchers can use this platform to identify Chinese CNC milling cutter manufacturers that have been exporting their products to other countries. The platform provides information on the company name, address, trade volume, and destination countries, enabling researchers to gain a comprehensive understanding of a manufacturer’s global presence and market reach.
To summarize, qcc.com, archive.org, and importyeti.com are valuable resources for conducting background research on CNC milling cutter manufacturers in China. While qcc.com provides company registration details, archive.org enables access to historical website data, and importyeti.com offers import/export records for manufacturers engaged in global trade. By utilizing these platforms, one can gather relevant information within the given word limit.
Leveraging Trade Shows and Expos for cnc milling cutter Sourcing in China
Trade shows and expos are an excellent platform for sourcing CNC milling cutters in China. These events offer a unique opportunity for companies to connect directly with manufacturers, consider various options, and make informed decisions. Here’s how to maximize the benefits of trade shows and expos when sourcing CNC milling cutters in China:
1. Research and select relevant trade shows: Identify trade shows and expos that specifically cater to the machinery industry or CNC tools. Look for events that attract a large number of suppliers and manufacturers specializing in CNC milling cutters.
2. Plan ahead: Before attending the event, determine your sourcing requirements by considering factors such as cutter specifications, material preferences, quantity, and budget. This will help you narrow down your search and focus on relevant exhibitors.
3. Identify potential suppliers: Study the exhibitor list and determine which companies align with your sourcing needs. Prioritize and create a list of potential suppliers to visit during the event.
4. Network and establish contacts: Trade shows provide an opportunity to meet face-to-face with potential suppliers and build relationships. Engage in meaningful conversations, exchange business cards, and gather relevant contact information for future correspondence.
5. Evaluate product offerings: Thoroughly evaluate the range of CNC milling cutters on display. Assess their quality, precision, durability, and suitability for your specific machining requirements. Seek samples, product literature, and pricing information from exhibitors to compare and make informed decisions.
6. Discuss customization options: If your milling cutter requirements entail customization, discuss possibilities with suppliers at the event. Evaluate their capabilities, flexibility, and willingness to accommodate your specific needs.
7. Business negotiations and contracts: Engage in negotiations with shortlisted suppliers and discuss pricing, delivery timelines, and payment terms. Assess the supplier’s reliability, production capacity, and ability to meet your volume requirements. Once satisfied, consider signing a contract to formalize the agreement.
8. Follow-up after the event: Maintain communication with potential suppliers post-event. Engage in further discussions, request additional samples or information, and present any necessary documentation. This will help solidify relationships and ensure a smooth sourcing process.
Attending trade shows and expos in China provides a comprehensive platform to source CNC milling cutters, connect with manufacturers, evaluate options, and facilitate successful business partnerships. By leveraging this avenue effectively, companies can find reliable suppliers and ensure quality CNC milling cutters for their operations.
The Role of Agents and Sourcing Companies in Facilitating cnc milling cutter Purchases from China
Agents and sourcing companies play a crucial role in facilitating CNC milling cutter purchases from China. These entities act as intermediaries between buyers and suppliers, streamlining the sourcing process and ensuring smooth transactions.
Firstly, agents and sourcing companies have an in-depth knowledge of the Chinese market and an extensive network of reliable suppliers. They can identify the most suitable manufacturers or distributors based on the buyer’s specific requirements, such as the desired quality, price range, and delivery time. By leveraging their expertise and connections, agents can provide buyers with access to a wide range of CNC milling cutter options that meet their needs.
Secondly, agents and sourcing companies act as a bridge for communication and negotiation. They possess language skills and cultural understanding that facilitate effective communication between buyers and suppliers. This is particularly crucial when it comes to discussing product specifications, pricing, and shipping arrangements. By serving as a mediator, agents ensure that both parties understand each other’s expectations and reach mutually beneficial agreements.
Furthermore, agents and sourcing companies also play a significant role in quality control and inspection. They can conduct factory audits, verify certifications, and conduct on-site product inspections to ensure that the CNC milling cutters meet the agreed-upon standards and specifications. This helps to mitigate risks and avoid potential quality issues, ensuring that buyers receive products of the highest quality.
Lastly, agents and sourcing companies handle logistics and shipping arrangements. They coordinate the transportation of the purchased CNC milling cutters, including documentation, customs clearance, and freight forwarding. By taking care of these logistical aspects, agents save buyers time and effort, allowing them to focus on their core business activities.
In summary, agents and sourcing companies are instrumental in facilitating CNC milling cutter purchases from China. They provide buyers with access to a wide range of suppliers, streamline communication and negotiation, ensure quality control, and handle logistics. By availing their services, buyers can navigate the complexities of international trade more efficiently and effectively.
Price Cost Research for cnc milling cutter manufacturers Companies in China, use temu.com and 1688.com
When it comes to CNC milling cutter manufacturers in China, two popular platforms for price and cost research are “temu.com” and “1688.com”. These platforms offer a wide range of suppliers and products, making them ideal for finding competitive pricing options.
Temu.com is an online marketplace where manufacturers, wholesalers, and individuals can offer their products directly to buyers. It features a user-friendly interface, allowing users to search for CNC milling cutter manufacturers based on specific parameters such as price range, location, and other relevant filters. By comparing prices from different suppliers, users can find the best deals that suit their budget and requirements.
1688.com, on the other hand, is a business-to-business (B2B) platform owned by Alibaba Group, specifically tailored for the Chinese market. It hosts a vast number of suppliers, including CNC milling cutter manufacturers. Users can search for products, filter results by price, and even negotiate prices directly with the manufacturers to further optimize costs.
Both platforms provide detailed product descriptions, including specifications and images, enabling users to make informed decisions about the quality and suitability of the CNC milling cutters offered. Additionally, they offer contact information so that users can communicate directly with the suppliers to clarify any queries or negotiate pricing.
In summary, temu.com and 1688.com are valuable resources for conducting price and cost research for CNC milling cutter manufacturers in China. These platforms facilitate efficient product comparisons, enabling users to find competitive pricing options while ensuring the desired quality and specifications. By utilizing these platforms appropriately, users can make cost-effective purchasing decisions, ultimately benefiting their businesses.
Shipping Cost for cnc milling cutter import from China
The shipping cost for importing CNC milling cutters from China can vary depending on several factors. Firstly, the weight and dimensions of the package play a significant role in determining the cost. Heavier or bulkier packages will generally incur higher shipping charges. Secondly, the shipping method chosen can impact the cost. There are several options available, including air freight, sea freight, express courier services, or a combination of these. Each option comes with different costs and delivery times. It is advisable to compare prices from various shipping providers to find the most cost-effective solution.
Another factor to consider is customs duties and taxes. When importing goods from China, the destination country may impose these charges based on the value of the products. It is important to research and understand the import regulations of the destination country to avoid any surprise costs.
Additionally, any special requirements or additional services such as insurance, packaging, or warehousing can contribute to the overall shipping cost.
To estimate the shipping cost, it is recommended to provide the shipping provider with the weight, dimensions, value, and destination of the package. They can then provide a quote based on the chosen shipping method. Online shipping calculators can also be useful tools for estimating costs.
Ultimately, importing CNC milling cutters from China involves careful consideration of shipping options, customs duties, and additional services to ensure a cost-efficient and smooth process.
Compare China and Other cnc milling cutter Markets: Products Quality and Price,Visible and Hidden Costs
China is known for its exceptional manufacturing capabilities and its vast market for CNC milling cutters. When comparing China’s CNC milling cutter market with other markets globally, several factors need considering, including product quality, price, and visible and hidden costs.
In terms of product quality, China has made significant progress over the years. Many Chinese manufacturers have invested in advanced technology and quality control processes to improve the consistency and reliability of their products. However, it is important to note that not all Chinese manufacturers uphold the same quality standards. While some offer high-quality CNC milling cutters that can compete globally, others may compromise on quality to offer lower-priced products.
Speaking of price, China has a competitive advantage due to its lower labor and production costs. Chinese CNC milling cutters tend to be more affordable compared to those from other markets, such as Europe or the United States. This cost advantage often attracts buyers who are looking for budget-friendly options without compromising their requirements. However, it is crucial to evaluate the price-quality trade-off and ensure that the desired level of quality is maintained despite lower prices.
When it comes to visible costs, China’s CNC milling cutter market offers great savings through economies of scale. Due to its vast manufacturing capabilities and large domestic market, Chinese manufacturers can produce CNC milling cutters in large quantities, reducing production costs and making their products more cost-effective.
However, hidden costs can be a concern for buyers in the Chinese market. One of the major hidden costs is the risk of intellectual property theft or counterfeiting. China has been notorious for intellectual property rights infringements, and the risk of counterfeit or substandard products is higher compared to some other markets. Buyers need to be cautious and choose reputable manufacturers with a strong track record to mitigate these risks.
In summary, China’s CNC milling cutter market offers a combination of competitive prices and improving product quality. However, buyers should be aware of potential hidden costs, such as intellectual property risks. Careful evaluation of manufacturers and their quality control processes is crucial to ensure that the desired level of quality is upheld while taking advantage of the cost benefits offered by the Chinese market.
Understanding Pricing and Payment Terms for cnc milling cutter: A Comparative Guide to Get the Best Deal
When it comes to purchasing CNC milling cutters, understanding the pricing and payment terms is crucial to ensure you get the best deal. A comparative guide can help you navigate the market and make an informed decision. Here are some key points to consider while keeping the description within 300 words.
1. Pricing: The price of CNC milling cutters can vary significantly depending on various factors such as brand reputation, quality, and specifications. The comparative guide should provide a price range for different types and sizes of milling cutters available in the market. It should offer insights into the average price and highlight any exceptional deals or discounts that may be available.
2. Quality: The guide should emphasize the importance of quality when purchasing CNC milling cutters. Lower-priced cutters may seem appealing, but they might not provide the durability and precision required for efficient machining. The guide should recommend investing in high-quality cutters from reputable manufacturers, even if they come at a slightly higher price.
3. Payment Terms: Understanding the payment terms is crucial to avoid any surprises or hidden costs. The guide should outline common payment options such as upfront payment, installment plans, or leasing options. It should also highlight any additional charges like shipping fees, import duties, or taxes that might be applicable.
4. Warranty and After-Sales Support: A good comparative guide should emphasize the importance of warranty and after-sales support. It should suggest choosing suppliers who offer reliable warranty coverage and responsive customer service. This ensures that any manufacturing defects or issues can be addressed promptly without incurring additional expenses.
5. Reviews and Feedback: The guide should recommend checking reviews and feedback from other customers to gauge the reliability and performance of different brands and models. It should provide information on reputable sources where such reviews can be found, helping buyers make an informed decision.
By providing valuable information on pricing, payment terms, quality, warranty, and customer reviews, a comparative guide can assist buyers in selecting the best CNC milling cutter for their needs. Remember, prioritizing quality and long-term performance is more important than solely focusing on price when it comes to such an essential tool in machining operations.
Chinese Regulations and Industry Standards Certifications for cnc milling cutter,Import Regulations and Customs for cnc milling cutter from China
In China, there are several regulations and industry standards certifications for CNC milling cutters that manufacturers must comply with. The most significant ones are as follows:
1. GB/T 23809-2009: This is the national standard for CNC milling cutters in China. It specifies the technical requirements, testing methods, and marking requirements for these products.
2. ISO 9001: This is an internationally recognized certification for quality management systems. Chinese manufacturers producing CNC milling cutters often obtain this certification to demonstrate their commitment to quality control.
3. RoHS: This certification ensures that CNC milling cutters do not contain restricted substances, such as lead, mercury, cadmium, and certain flame retardants. Compliance with RoHS is important for exporting products to many countries.
4. CE: The CE certification indicates that CNC milling cutters comply with European Union safety, health, and environmental protection standards. Although it is not mandatory for products sold within China, many manufacturers choose to obtain this certificate for export purposes.
When importing CNC milling cutters from China, it is essential to be aware of the import regulations and customs procedures. These include:
1. Customs Declaration: Importers need to provide accurate information on the customs declaration form, including the product description, value, country of origin, and Harmonized System (HS) code for CNC milling cutters.
2. Tariffs and Duties: Importers may be subject to customs duties, value-added tax (VAT), and other import taxes levied by their country’s customs authority. The import duty rates for CNC milling cutters can vary depending on the country and its trade agreements with China.
3. Trade Documentation: Importers should ensure that all necessary trade documents, such as the commercial invoice, packing list, bill of lading, and certificates of origin, are correctly prepared and submitted to the customs authorities.
4. Product Compliance: Importers should verify that the CNC milling cutters comply with the applicable regulations, certifications, and standards of their country. It is advisable to work with reputable suppliers who can provide necessary documentation and ensure product compliance.
In summary, manufacturers of CNC milling cutters in China must adhere to national standards and certifications, such as GB/T 23809-2009 and ISO 9001. Importers should be familiar with import regulations, customs declaration requirements, and product compliance standards when importing CNC milling cutters from China.
Sustainability and Environmental Considerations in cnc milling cutter Manufacturing
Sustainability and environmental considerations are increasingly important in all manufacturing processes, including CNC milling cutter manufacturing. These considerations aim to minimize the negative impacts on the environment and promote the efficient use of resources. Several key aspects are crucial in this regard.
Firstly, material selection plays a vital role in ensuring sustainability. Manufacturers should select materials that are environmentally friendly, renewable, and have a low carbon footprint. Utilizing recycled or recyclable materials in CNC milling cutter manufacturing can significantly reduce the extraction of new resources and minimize waste generation.
Secondly, energy consumption is another important consideration. CNC milling machines require a significant amount of energy to operate. Implementing energy-efficient practices, such as using renewable energy sources like solar or wind power and optimizing the machine’s motor efficiency, can reduce the carbon emissions associated with the manufacturing process.
Thirdly, waste reduction and recycling should be an integral part of the manufacturing process. CNC milling cutter manufacturers should strive to minimize waste generation and establish efficient recycling systems for both metal and non-metal wastes. Recycling reduces the need for extracting new materials and helps conserve resources.
Moreover, the disposal of hazardous materials and chemicals used in the manufacturing process should be carefully managed. Implementing effective waste management systems, employing proper disposal methods, and ensuring compliance with regulatory standards are essential to prevent environmental pollution.
Furthermore, the product’s lifespan and end-of-life considerations are important aspects of sustainability. Designing CNC milling cutters with durability, reliability, and the ability to be repaired or refurbished extends their lifespans. Additionally, incorporating end-of-life strategies such as take-back programs and proper disposal techniques for worn-out or obsolete cutters can reduce the environmental impact.
Finally, the implementation of eco-friendly practices throughout the supply chain is crucial for a sustainable manufacturing process. Working with suppliers who adhere to sustainable principles, promoting sustainable packaging, and optimizing transportation routes to reduce carbon emissions are significant steps towards a greener CNC milling cutter manufacturing industry.
In conclusion, sustainability and environmental considerations in CNC milling cutter manufacturing revolve around material selection, energy efficiency, waste reduction and recycling, proper hazardous material disposal, product lifespan, and eco-friendly supply chain practices. By adopting sustainable practices, manufacturers can contribute to a healthier environment and a more sustainable future.
List The Evolution history of “cnc milling cutter”
The evolution of CNC milling cutters can be traced back to the early days of numerical control (NC) machines in the 1940s. Initially, these machines used manual programming and operated on punch cards. Milling cutters for these machines were basic, consisting of simple end mills and face mills.
In the 1960s, the industry witnessed a major breakthrough with the introduction of computer numerical control (CNC) machines. These machines utilized computer programs to control the cutting process, allowing for more complex machining operations. As a result, the demand for more sophisticated milling cutters grew.
To meet this demand, manufacturers started developing high-speed steel (HSS) milling cutters with advanced geometries. These cutters featured increased rigidity and heat resistance, enabling faster and more efficient machining. However, their limited durability led to the development of carbide-tipped milling cutters in the 1970s. With carbide inserts, these cutters delivered enhanced tool life and could be used at higher cutting speeds.
The 1980s ushered in the era of solid carbide milling cutters. Made entirely of carbide, these cutters offered exceptional hardness and wear resistance. They became popular for machining challenging materials such as stainless steel and hardened steels.
In the 1990s, the advent of advanced coatings further improved the performance of CNC milling cutters. Titanium nitride (TiN) coatings provided higher resistance to wear, while titanium aluminum nitride (TiAlN) and other similar coatings significantly increased tool life and productivity.
The 21st century has witnessed continuous advancements in CNC milling cutters. Companies have developed new tool geometries, specialized coatings, and innovative cutting edge designs to improve the efficiency and precision of milling operations. Furthermore, the integration of artificial intelligence and machine learning has enabled CNC milling cutters to adapt to changing machining conditions automatically.
In recent years, there has been a growing focus on sustainability, leading to the development of eco-friendly cutting tools. These green milling cutters minimize tool waste and energy consumption during production.
Today, CNC milling cutters are available in a wide range of designs, materials, and coatings, each tailored to specific applications and materials. With ongoing technological innovations, the future of CNC milling cutters holds untapped potential in terms of performance, durability, and environmental sustainability.
The Evolution and Market Trends in cnc milling cutter Industry
The CNC milling cutter industry has undergone significant evolution and witnessed various market trends in recent years. The introduction of computer numerical control (CNC) technology has revolutionized the milling process, enabling precise and efficient cutting operations with a higher level of automation.
One of the key market trends in the CNC milling cutter industry is the increasing demand for customization. As industries strive to meet the specific requirements of their customers, there is a growing need for CNC milling cutters that can produce complex and unique designs. This has led to the development of specialized tools and cutters that can handle a wide range of materials and geometries, allowing manufacturers to offer customized solutions.
Another prominent trend is the integration of advanced technologies in CNC milling cutters. For instance, the incorporation of artificial intelligence (AI) and machine learning algorithms has enhanced the capabilities of these tools. AI-driven systems can optimize the cutting process by adjusting speed, feed rates, and tool paths in real-time, resulting in improved efficiency and reduced material waste.
Moreover, there is an increasing focus on sustainability and environmental consciousness in the CNC milling cutter industry. Manufacturers are now developing eco-friendly cutting tools that minimize energy consumption and waste generation. Efforts are being made to incorporate sustainable materials and coatings, reducing the environmental impact of the milling process.
The market for CNC milling cutters is also witnessing a shift towards digitalization and connectivity. Industry 4.0 technologies are being integrated into milling machines, allowing real-time monitoring and remote control of the cutting process. This enables manufacturers to optimize production, reduce downtime, and enhance overall efficiency.
In conclusion, the CNC milling cutter industry has evolved significantly, driven by the demand for customization, technological advancements, sustainability, and digitalization. These market trends have led to the development of more advanced and efficient tools, offering manufacturers improved productivity and flexibility in their milling operations. With the constant evolution of technology and changing market demands, it is expected that the CNC milling cutter industry will continue to expand and innovate in the coming years.
Custom Private Labeling and Branding Opportunities with Chinese cnc milling cutter Manufacturers
Chinese CNC milling cutter manufacturers offer custom private labeling and branding opportunities for businesses looking to enhance their product offering. With their advanced production capabilities and competitive pricing, these manufacturers are a popular choice for companies seeking to establish their own brand in the market.
The private labeling service allows businesses to have their logos, packaging designs, and other unique features on the CNC milling cutters. This enables them to create a distinct identity for their products and stand out from competitors. Additionally, companies can tailor the product specifications, sizes, and materials to meet their specific requirements.
Chinese manufacturers are renowned for their expertise in CNC machining technology. They employ modern equipment and skilled workers, ensuring high precision and quality in the manufacturing process. This, coupled with their extensive experience in serving international clients, makes them a reliable partner for businesses seeking to enhance their product lineup.
Another advantage of collaborating with Chinese CNC milling cutter manufacturers is their cost-efficiency. Due to competitive labor and material costs, companies can achieve significant cost savings by manufacturing with these suppliers. This allows businesses to offer their branded products at competitive prices, attracting more customers and increasing market share.
Businesses seeking custom private labeling and branding solutions can easily find Chinese CNC milling cutter manufacturers through various online platforms and trade directories. These suppliers typically have extensive product catalogs and readily provide samples for evaluation. Communication is often facilitated through English-speaking representatives who understand international market demands and ensure a smooth collaboration.
In conclusion, Chinese CNC milling cutter manufacturers provide custom private labeling and branding opportunities for businesses seeking to differentiate their products. Their advanced technology, cost-efficiency, and experience in serving international markets make them a reliable choice for companies aiming to establish their own brand and expand their market presence.
Tips for Procurement and Considerations when Purchasing cnc milling cutter
When it comes to procuring CNC milling cutters, there are several key considerations that businesses should keep in mind. These tips can help ensure that you make an informed purchasing decision while staying within your budget.
1. Define your requirements: Start by identifying the specific requirements for your CNC milling operations. Consider factors such as the type of material to be machined, desired surface finish, tolerance levels, and the complexity of the desired cuts. This will help you determine the appropriate cutter type, size, and coating.
2. Research suppliers: Look for reputable suppliers of CNC milling cutters and compare their offerings. Consider factors such as product quality, pricing, and customer reviews. Don’t hesitate to ask for samples or reach out to other customers to get feedback on the products and services provided.
3. Quality and durability: Choose suppliers that offer high-quality cutters made from durable materials. These factors will impact the tool’s lifespan, cutting performance, and overall efficiency. Look for manufacturers with a proven track record and certifications that demonstrate their commitment to producing reliable products.
4. Tool design: Assess the design features of the CNC milling cutter, including the number of flutes, flute length, and helix angle. These aspects should align with your requirements to ensure optimal performance. Consider whether you need a specialized cutter for specific applications or if a general-purpose one will suffice.
5. Coating options: Check if the cutters are coated with protective materials such as TiN, TiCN, or TiAlN. These coatings enhance the tool’s hardness, lubricity, and heat resistance. Understanding the type of coating required for your machining operations is crucial for achieving precise and consistent results.
6. Price considerations: While cost is an essential factor to consider, it should not be the sole deciding factor. Balancing quality, performance, and cost is crucial. Look for suppliers that offer competitive pricing without compromising on the required specifications and performance.
7. Support and warranty: Ensure that the supplier provides adequate technical support and after-sales service. This can include assistance with tool selection, troubleshooting, and guidance on optimizing tool life. Additionally, inquire about the warranty or guarantees offered.
By following these tips, businesses can make informed decisions when purchasing CNC milling cutters, ensuring they meet their machining needs while staying within their budget. Remember to consider the specific requirements, research suppliers, assess quality and durability, evaluate tool design and coating options, consider pricing while maintaining quality, and ensure support and warranty provisions from the supplier.
FAQs on Sourcing and Manufacturing cnc milling cutter in China
1. Why should I consider sourcing CNC milling cutters from China?
China is known for its competitive manufacturing capabilities and low production costs. With a vast number of specialized factories and a mature supply chain, China offers a wide range of options for CNC milling cutter sourcing. Moreover, Chinese manufacturers have gained expertise in producing high-quality tools, making them a popular choice for businesses looking for cost-effective solutions.
2. How do I find a reliable CNC milling cutter manufacturer in China?
To find a reliable manufacturer, consider conducting thorough research and due diligence. Start by searching for reputable companies through online directories, industry trade shows, or professional networks. Look for manufacturers with a proven track record, positive customer reviews, and certifications (such as ISO 9001). Request samples, communicate openly about your requirements, and evaluate their manufacturing capabilities and quality control processes. Additionally, consider engaging the services of a sourcing agent or third-party inspection company to ensure the legitimacy and reliability of the supplier.
3. What factors should I consider when sourcing CNC milling cutters in China?
When sourcing CNC milling cutters, several factors need to be considered. These include the manufacturer’s production capacity, lead times, pricing, quality control processes, and post-sales support. It is crucial to understand their manufacturing capabilities, machinery, and quality inspection procedures to ensure that the products meet your specifications. Additionally, discussing intellectual property concerns, negotiating favorable terms, and establishing clear communication channels are essential for a successful sourcing process.
4. How can I ensure the quality of CNC milling cutters sourced from China?
Ensuring quality when sourcing CNC milling cutters from China requires a proactive approach. Before placing bulk orders, request samples for testing and verify if they meet your specific requirements. Conduct on-site visits or enlist the help of a third-party inspection company to assess the manufacturer’s facilities, equipment, and quality control procedures. Asking for relevant certifications and adhering to transparent communication with the supplier throughout the production process can also help maintain product quality.
5. What are the potential challenges in sourcing CNC milling cutters from China?
Some potential challenges in sourcing CNC milling cutters from China include language barriers, cultural differences, intellectual property concerns, logistics, and inconsistent quality control. It is important to address these challenges by ensuring effective communication, using legal contracts, protecting intellectual property rights, staying updated on import regulations, and conducting regular inspections or audits. Working with an experienced sourcing agent or partnering with trusted manufacturers can help overcome these obstacles and ensure a smooth sourcing process.
In conclusion, sourcing CNC milling cutters from China can offer cost-effective solutions, but due diligence, careful supplier selection, and quality control measures are necessary to ensure a successful sourcing experience.
Why contact sourcifychina.com get free quota from reliable cnc milling cutter suppliers?
Sourcifychina.com may get free quotas from reliable CNC milling cutter suppliers for several reasons. Firstly, as a platform that connects buyers and suppliers, Sourcifychina.com plays a crucial role in facilitating business transactions. By bringing potential buyers to suppliers, the platform helps suppliers increase their sales volume and expand their customer base.
In order to attract buyers and encourage them to use the platform, Sourcifychina.com may negotiate with CNC milling cutter suppliers to provide free quotas. These free quotas enable buyers to access a certain number of milling cutters without any initial cost or commitment. This allows buyers to test the products, evaluate their quality and performance, and build trust with the suppliers before making larger orders.
For CNC milling cutter suppliers, offering free quotas through Sourcifychina.com can be beneficial as well. It allows them to showcase their products to a wider audience and gain exposure to potential customers who might not have discovered their offerings otherwise. By providing free quotas, suppliers can generate interest and attract potential long-term buyers, leading to increased sales in the future.
Furthermore, Sourcifychina.com aims to establish itself as a reliable and trustworthy platform. By partnering with reliable CNC milling cutter suppliers, they can ensure that the products available on their platform meet quality standards. This enhances the credibility and reputation of Sourcifychina.com, building trust among buyers and encouraging them to use the platform for their sourcing needs.
By offering free quotas from reliable CNC milling cutter suppliers, Sourcifychina.com creates a win-win situation for both buyers and suppliers. Buyers can access quality products without any initial investment or risk, while suppliers can expand their customer base and benefit from increased sales opportunities.