Introduce about cnc turning and milling machine guide,Qulity,Cost,Supplier,Certification,Market,Tips,FAQ
CNC turning and milling machines, also known as CNC lathes or machining centers, are innovative and advanced tools used in various industries for precision manufacturing. These machines enable automated and precise cutting, shaping, and drilling of materials like metal, plastic, wood, and composites.
Quality is essential when considering a CNC turning and milling machine. Look for machines with robust structures, high precision capabilities, and reliable components to ensure accuracy and long-term durability. Opt for machines equipped with features like automatic tool changers, advanced control systems, and high spindle speeds for enhanced efficiency and productivity.
Cost is a significant factor to consider while purchasing CNC machines. The price range varies depending on the size, specifications, and brand of the machine. It is recommended to research and compare prices from different suppliers to find one that offers a competitive price without compromising on quality.
Finding a reliable supplier is crucial for obtaining high-quality CNC turning and milling machines. Look for suppliers with a good reputation in the industry, positive customer reviews, and after-sales support. Consider suppliers that offer comprehensive warranties, training, and technical assistance to maximize machine performance.
Certification is another important aspect to consider. Look for machines that comply with industry standards, such as ISO 9001 for quality management. Certification ensures that the machine has undergone rigorous testing and meets the necessary safety and performance requirements.
The market for CNC turning and milling machines is growing rapidly due to the increasing demand for precision manufacturing. These machines are widely used across industries such as automotive, aerospace, electronics, and medical device manufacturing. The market is driven by the need for high accuracy, efficiency, and automation in manufacturing processes.
Here are some quick tips to consider when purchasing a CNC turning and milling machine:
1. Assess your specific manufacturing needs and requirements.
2. Research and compare different machine models, brands, and suppliers.
3. Consider the machine’s capabilities, features, and specifications.
4. Evaluate the supplier’s reputation, customer reviews, and after-sales support.
5. Compare prices and negotiate for the best deal.
6. Ensure proper training and support for machine operation and maintenance.
Frequently Asked Questions (FAQ):
1. What materials can be processed with CNC turning and milling machines?
CNC machines can process various materials, including metals (steel, aluminum, brass), plastics, wood, and composites.
2. Can CNC machines perform complex and intricate operations?
Yes, CNC machines are highly capable of performing complex operations, including 3D contouring, thread milling, and multi-axis machining.
3. How long does it take to become proficient in operating a CNC turning and milling machine?
The learning curve depends on your prior experience and the complexity of the machine. Basic proficiency can be achieved within a few weeks of training, while mastering all functionalities may take several months of practice.
In conclusion, CNC turning and milling machines are vital tools in precision manufacturing, enabling automated and precise cutting and shaping processes. Selecting a high-quality machine from a reliable supplier is crucial for efficient and accurate production. Consider market trends, certifications, and compare prices to make an informed decision.
Types of cnc turning and milling machine
There are various types of CNC turning and milling machines used in the manufacturing industry. These machines are designed to automate and enhance the precision and speed of the turning and milling processes. Here are some common types of CNC machines used for turning and milling:
1. CNC Lathe: A CNC lathe is one of the most common types of turning machines. It uses computer numerical control to rotate a workpiece while a cutting tool removes material from the surface. CNC lathes are used for producing cylindrical or conical shapes, such as shafts, rods, and tubes.
2. CNC Swiss-Type Lathe: Swiss-type lathes (also known as sliding headstock lathes) are used for small, intricate parts. These machines have a guide bushing that supports the bar stock during machining, resulting in excellent precision. CNC Swiss-type lathes are commonly used in the medical, watchmaking, and electronics industries.
3. CNC Vertical Turning Center: A vertical turning center (VTC) is a machine that rotates a workpiece vertically while a cutting tool removes material. VTCs are used for machining large, heavy workpieces with a vertical orientation. These machines are commonly used in industries such as aerospace and automotive for manufacturing components like turbine discs and brake rotors.
4. CNC Horizontal Machining Center: A horizontal machining center (HMC) is a milling machine with a horizontally oriented spindle. HMCs are known for their versatility and are used for high-precision milling, drilling, and tapping operations. They are used in a wide range of industries including automotive, aerospace, and mold-making.
5. CNC Vertical Machining Center: A vertical machining center (VMC) is a milling machine with a vertically oriented spindle. VMCs are widely used in industries like automobile manufacturing, aerospace, and tool and die making. They are suitable for producing complex shapes, such as gears, molds, and precision parts.
6. CNC 5-Axis Machine: A 5-axis CNC machine can perform complex machining operations with five different axes of movement. These machines allow for greater flexibility and the ability to produce complex shapes or surfaces. 5-axis machines are commonly used in the aerospace, automotive, and medical industries for manufacturing intricate components.
In conclusion, these are just a few types of CNC turning and milling machines used in the manufacturing industry. Each machine has its own unique capabilities and applications, enabling manufacturers to produce a wide range of precision components efficiently.
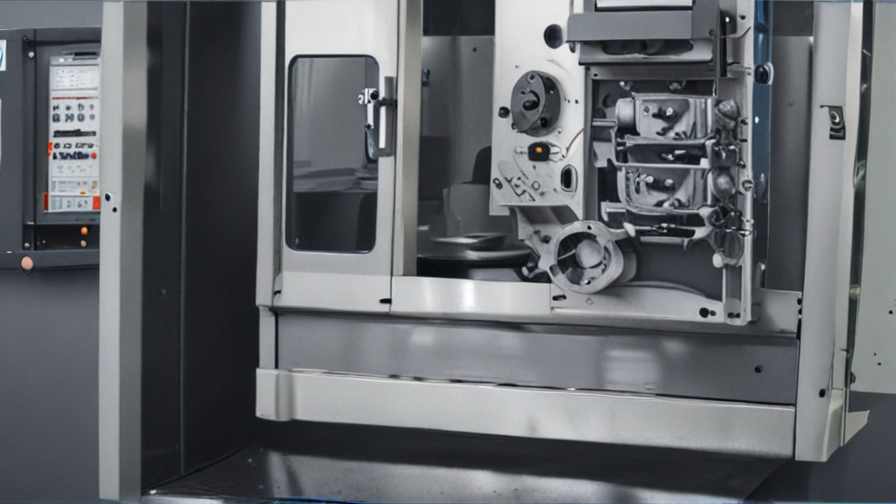
Pros and Cons of Using cnc turning and milling machine
CNC turning and milling machines are advanced and versatile tools that offer numerous advantages, but they also have a few drawbacks. Understanding these pros and cons can help individuals and businesses decide whether these machines are suitable for their needs.
Pros of CNC Turning and Milling Machines:
1. Precision: CNC machines offer exceptional precision, allowing for highly accurate and consistent results. They can achieve tolerances as small as 0.0001 inches, enabling the creation of complex and intricate components.
2. Efficiency: These machines are highly efficient, capable of performing multiple operations without manual intervention. They can automatically change tools, adjust cutting speeds, and optimize processes, resulting in increased productivity and reduced production time.
3. Automation: CNC machines are fully automated, reducing the need for extensive human supervision. This frees up operators to attend to other tasks and allows for uninterrupted production runs.
4. Versatility: CNC machines can perform both turning and milling operations, eliminating the need for separate machines. This versatility allows for a wide range of applications, from simple cylindrical parts to complex 3D shapes.
5. Flexibility: These machines can easily accommodate changes in design or specifications without requiring extensive setup time. Operators can quickly reprogram and adjust parameters, allowing for agile and flexible manufacturing processes.
Cons of CNC Turning and Milling Machines:
1. Cost: CNC machines are generally more expensive than traditional manual machines. The initial purchase cost, as well as maintenance and repair expenses, can be significant for small businesses or individuals.
2. Complexity: CNC machines require specialized training and expertise to operate effectively. Learning the programming language and understanding machine operations may require a considerable investment of time and resources.
3. Limited Manual Control: While automation is advantageous, it can limit the operator’s ability to make manual adjustments on the fly. This lack of control can be problematic in certain situations that may require immediate adjustments or modifications.
4. Maintenance and Downtime: CNC machines are complex systems that require regular maintenance and occasional repairs. When breakdowns occur, production can come to a halt, resulting in costly downtime until the issue is resolved.
5. Initial Setup: Setting up CNC machines for production requires careful planning and preparation. This includes fixture design, tool selection, and programming, which can be time-consuming and may slow down the initial production.
In conclusion, CNC turning and milling machines offer precision, efficiency, automation, versatility, and flexibility. However, they come with a higher upfront cost, require specialized training, offer limited manual control, require regular maintenance, and have a setup period. Businesses and individuals should carefully evaluate these pros and cons to determine if the benefits outweigh the drawbacks in their specific manufacturing context.
cnc turning and milling machine Reference Specifications (varies for different product)
CNC (Computer Numerical Control) turning and milling machines are versatile tools used in the manufacturing industry for various purposes. These machines have revolutionized the way precision components are produced, offering higher accuracy, efficiency, and productivity compared to traditional manual machines.
The specifications of CNC turning and milling machines vary based on the specific product requirements and applications. However, there are some common reference specifications that are frequently encountered in these machines.
One important specification is the maximum machining diameter. This refers to the largest workpiece diameter that can be accommodated by the machine. The maximum machining length is another crucial specification, determining the maximum length of the workpiece that can be machined.
The spindle speed is a significant specification that refers to the rotational speed of the machine’s spindle. It greatly influences the cutting speed and material removal rate during the machining process. Another critical specification is the spindle motor power, which determines the machine’s capability to handle different types of materials and machining operations.
The number of axes is an essential specification, indicating the machine’s ability to move and position the cutting tool in different directions. Common configurations include 2-axis, 3-axis, and 5-axis machines, with each axis adding more flexibility and complexity to the machining process.
The rapid traverse rate is the speed at which the machine moves between different machining positions. It affects the overall machining time and productivity. The tool magazine capacity specifies the number of tools that can be stored in the machine simultaneously, allowing for automatic tool changes and reducing downtime.
Additionally, it is essential to consider the CNC control system specifications. Examples include the type of control system (e.g., Fanuc, Siemens), the programming language supported (e.g., G-code), and any additional features offered for advanced operations like threading or contouring.
In conclusion, CNC turning and milling machines are key players in the manufacturing industry. While specific product requirements may lead to variations in specifications, some common reference specifications apply to these machines. It is crucial to consider factors such as maximum machining diameter, spindle speed and power, number of axes, rapid traverse rate, tool magazine capacity, and CNC control system specifications when selecting a CNC turning and milling machine for a specific application.
Applications of cnc turning and milling machine
CNC (Computer Numerical Control) turning and milling machines are integral to modern manufacturing processes. These machines are capable of producing complex and precise components for various industries. Here, we discuss some of the key applications and benefits of CNC turning and milling machines within this word limit.
1. Aerospace industry: CNC turning and milling machines play a crucial role in the production of aerospace components, such as landing gears, engine parts, and turbine blades. These machines can efficiently shape and machine high-strength materials like titanium and aluminum alloys, ensuring accuracy and consistency of the parts.
2. Automotive industry: CNC machines are widely used in the automotive sector for producing engine components, suspension parts, and gearbox elements. These machines can efficiently handle the large production volumes required by automotive manufacturers, while maintaining high precision and quality.
3. Medical industry: CNC turning and milling machines are used in the production of medical devices and implants with complex geometries. These machines can manufacture components from biocompatible materials like stainless steel and titanium, ensuring the necessary precision and sterilization requirements.
4. Electronics industry: CNC machines are utilized to produce a wide range of electronic components like enclosures, connectors, and circuit boards. They offer high precision and repeatability, allowing for the creation of intricate features required in the electronics industry.
5. Prototyping and rapid production: CNC turning and milling machines are also widely used for rapid prototyping and small-scale production runs. They enable quick and accurate production of prototypes and finished parts, reducing lead times and costs associated with traditional machining methods.
6. General manufacturing: CNC machines find applications in various other manufacturing industries, including defense, energy, and consumer goods. These machines can efficiently produce a diverse range of complex components, meeting tight tolerances and quality requirements.
The advantages of CNC turning and milling machines include increased productivity, precise and repeatable manufacturing, reduced labor costs, and the ability to handle a wide variety of materials. CNC machines also offer flexibility, as they can be programmed for different tasks, allowing for faster setup times and improved overall efficiency.
In summary, CNC turning and milling machines have extensive applications across multiple industries, ranging from aerospace and automotive to medical and electronics. These machines provide precise and efficient manufacturing solutions, contributing to the advancement of technology and innovation in various sectors.
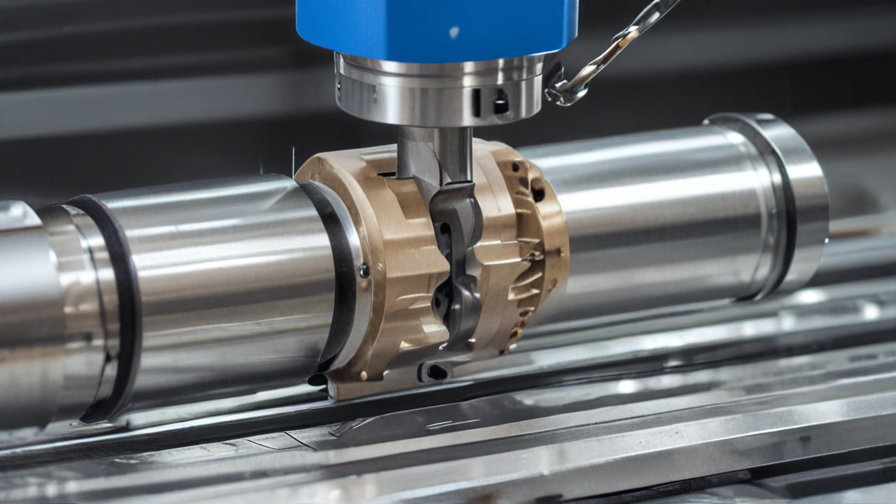
The Work Process and how to use cnc turning and milling machine
CNC turning and milling machines are versatile tools commonly used in manufacturing industries to produce high-quality precision parts. The work process involves several steps, starting from the preparation of the machine to the completion of the final part. Here is a brief overview of the work process for using a CNC turning and milling machine.
1. Preparation: Begin by selecting the appropriate cutting tools, materials, and fixturing devices for the job at hand. Load the tools into the tool turret or tool changer of the machine and secure the workpiece in the clamps or chuck.
2. Programming: Use computer-aided design (CAD) software to create a 3D model of the part or import an existing design. Transfer the design to computer-aided manufacturing (CAM) software to generate the machine instructions (G-code) needed for CNC operation. Program the machine by inputting the desired cutting paths, speeds, and feeds.
3. Machine setup: Power up the machine and load the CNC program into the control unit. Perform tool offset measurements and calibration to ensure precise machining. Set up any additional features like coolant systems or tool monitors as required.
4. Operation: Start the machining process by initiating the program and closely monitoring the machine’s progress. The machine will automatically execute the programmed actions, including tool changes, spindle speed adjustments, and tool positioning.
5. Quality control: Regularly inspect the part during production to ensure accuracy and dimensions. Use precision measuring tools like calipers, micrometers, or coordinate measuring machines (CMMs) to verify the part’s compliance with the design specifications.
6. Finishing: Apply finishing operations such as deburring, polishing, or surface treatment to enhance the part’s aesthetic appeal and functionality.
7. Post-processing: Remove the finished part from the machine and clean the machine and work area. Store the programming file and tooling data for future reference or modifications.
By following these steps, manufacturers can efficiently utilize CNC turning and milling machines to produce intricate and precise parts. The CNC technology offers numerous advantages, including reduced labor costs, improved productivity, and consistency in part quality, making it an indispensable tool in modern manufacturing processes.
Quality Testing Methods for cnc turning and milling machine and how to control the quality
Quality testing methods for CNC turning and milling machines are essential to ensure that the produced components meet the required specifications. There are several common methods to control the quality of these machines:
1. Dimensional Inspection: This involves using measurement equipment like calipers, micrometers, or coordinate measuring machines (CMMs) to check if the finished components have the correct dimensions. This helps identify any deviations from the intended specifications.
2. Surface Finish Evaluation: Surface roughness testers are employed to measure the smoothness of the surfaces produced by the machine. This ensures that the surface finish meets the required standards, especially for applications where friction or appearance is crucial.
3. Tolerance Verification: Gauge blocks and plug gauges are used to verify whether the machined parts meet the specified tolerance limits. This helps ensure that the parts will fit together correctly during assembly.
4. Performance Testing: CNC turning and milling machines can be subjected to performance tests to determine the accuracy and repeatability of the machine’s movements and positioning. This involves running test programs and comparing the actual outputs to the expected results.
To control the quality of CNC machines effectively, certain measures can be implemented:
1. Regular Maintenance: Maintaining CNC machines regularly helps prevent unexpected breakdowns and ensures that the machine operates within its designed specifications. Lubrication, cleaning, and calibration should be done on a scheduled basis.
2. Operator Training: Providing comprehensive training to machine operators helps them understand the machine’s capabilities, know the correct operating procedures, and recognize any signs of potential issues. Well-trained operators can contribute significantly to maintaining machine quality.
3. Standard Operating Procedures (SOPs): Developing and implementing clear SOPs for setup, programming, and machining processes promotes consistency and eliminates errors. SOPs should include checklists and guidelines for quality control measures.
4. Quality Control Inspections: Conducting regular inspections at various stages of the manufacturing process enables early detection of any deviations from quality standards. Inspections should cover raw materials, setup processes, in-progress checks, and final inspections.
In conclusion, quality testing methods for CNC turning and milling machines play a crucial role in ensuring the produced components are of high quality. Implementing regular maintenance, providing operator training, adhering to SOPs, and conducting quality control inspections are all essential to control the quality efficiently.
cnc turning and milling machine Sample Policy and Post-Purchase Considerations for cnc turning and milling machine from China
Sample Policy for CNC Turning and Milling Machine from China:
When purchasing a CNC turning and milling machine from China, it is essential to consider the following sample policy:
1. Product Quality: Ensure that the supplier provides machines with high-quality standards and precision. Request detailed product specifications, including the type of materials used and the tolerances achieved.
2. Warranty: Check if the supplier offers a warranty for the machine. It is advisable to opt for a supplier who provides a reasonable warranty period covering any manufacturing defects or malfunctioning parts.
3. After-Sales Service: Inquire about the availability of a technical support team that can help with installation, maintenance, and troubleshooting. A prompt and reliable after-sales service is crucial for ensuring uninterrupted operation of the machine.
4. Spare Parts and Availability: Confirm that the supplier can provide readily available spare parts for the machine. The ability to easily source spare parts locally or from the supplier is essential to minimize downtime in case of component failure.
5. Price and Payment Terms: Compare prices from different suppliers, ensuring that the offered price aligns with the quality of the machine. Negotiate reasonable payment terms, such as partial payment upon order confirmation and the remaining balance upon machine inspection and acceptance.
Post-Purchase Considerations for CNC Turning and Milling Machine:
After the purchase, the following post-purchase considerations can ensure a successful implementation of the CNC turning and milling machine from China:
1. Installation and Calibration: Engage a professional technician to install and calibrate the machine according to the manufacturer’s instructions. Proper calibration is vital for accurate and precise machining operations.
2. Training and Operator Skill Development: Provide adequate training to the machine operators to ensure they are proficient in using the equipment safely and efficiently. This can be arranged through the supplier or by hiring a qualified trainer familiar with the specific machine model.
3. Regular Maintenance and Cleaning: Follow the manufacturer’s recommended maintenance schedule to prolong the machine’s lifespan and prevent unexpected breakdowns. Regularly cleaning the machine and removing swarf and debris is essential to maintain its optimal performance.
4. Upgrades and Software Updates: Keep track of any available upgrades or software updates provided by the manufacturer. These updates may enhance the machine’s functionality or address any identified issues, improving overall performance.
5. Performance Evaluation: Periodically assess the machine’s performance and output quality to ensure it meets the expected standards. Identify any recurring issues and communicate them to the supplier for resolution or consultation.
By considering these policies and post-purchase considerations, buyers can maximize the value and performance of their CNC turning and milling machine from China while minimizing potential issues and risks.
Sourcing cnc turning and milling machine from China: Opportunities, Risks, and Key Players
China is a leading global manufacturing hub, known for its reliable and cost-effective production capabilities. When it comes to CNC turning and milling machines, sourcing from China can offer numerous opportunities.
Firstly, Chinese manufacturers have a strong expertise in producing CNC machines, including turning and milling machines. They have a wide range of models and configurations to suit diverse customer needs. Additionally, Chinese manufacturers often offer competitive prices due to lower labor and production costs.
Sourcing CNC turning and milling machines from China also provides access to a vast supply chain network. Chinese manufacturers have well-established relationships with component suppliers, ensuring a steady supply of parts and minimizing production delays. Moreover, China’s developed transportation infrastructure enables efficient logistics and delivery of machinery to global destinations.
However, there are certain risks associated with sourcing from China. Quality control can be a concern, as some Chinese manufacturers may not adhere to stringent international standards. It is essential to conduct thorough due diligence and select reputable suppliers who have a proven track record of delivering high-quality products.
Intellectual property risks can be another challenge when sourcing from China. Protecting proprietary designs and technology is crucial, and companies must engage in careful contractual negotiations and ensure proper safeguards to safeguard their IP rights.
Several key players in the Chinese market manufacture CNC turning and milling machines. Some notable companies include Shenyang Machine Tool Group, DMG Mori, Haas Automation, and Jinan Bodor CNC Machine Co., Ltd. These companies have extensive experience in producing and exporting CNC machines, offering a wide range of options for buyers.
In conclusion, sourcing CNC turning and milling machines from China presents opportunities such as cost-effectiveness, a wide range of options, and a well-established supply chain. However, risks related to quality control and intellectual property protection should be carefully managed. By selecting reputable suppliers and implementing adequate safeguards, businesses can capitalize on the benefits offered by Chinese manufacturers in this sector.
How to find and select reliable cnc turning and milling machine manufacturers in China,use google search manufacturers and suppliers
When searching for reliable CNC turning and milling machine manufacturers in China, Google search can be a useful tool. Here are some steps to follow within 300 words:
1. Start by entering keywords related to your requirement, such as “CNC turning and milling machine manufacturers in China.” This search will provide you with an initial list of potential suppliers.
2. Take a closer look at the search results and explore the websites of different manufacturers/suppliers. Look for those that specialize in CNC turning and milling machines, as they are more likely to have the necessary expertise and experience.
3. The credibility and reliability of a manufacturer can be assessed by various factors. Look for detailed information on their website, including the number of years they have been in business, their manufacturing facilities, quality control processes, certifications, and customer testimonials or reviews.
4. Check if the manufacturer has the necessary certifications, such as ISO 9001, which signifies adherence to quality standards. Additionally, certifications like CE, RoHS or UL compliance may also be important, depending on your specific requirements.
5. Look for information on their production capacity and technical capabilities. It is crucial to ensure that the manufacturer can handle the volume and complexity of your CNC turning and milling machine requirements.
6. Seek out suppliers with a strong research and development (R&D) team and an ability to offer customized solutions. This indicates that they can understand and meet your specific needs while keeping up with technological advancements.
7. Use business directories and online platforms, such as Alibaba or Global Sources, to find additional manufacturers. These platforms often provide detailed information on suppliers, including their product range, certifications, and customer ratings.
8. Once you have shortlisted a few potential suppliers, contact them directly to discuss your requirements, request quotations, and ask for additional information. Clear communication and prompt responses are indicators of a reliable manufacturer.
9. Ideally, you should request samples or visit the manufacturer’s facility to assess their production capabilities and quality control processes firsthand. However, this might not always be feasible due to geographical constraints or time limitations.
By following these steps, you can identify and select reliable CNC turning and milling machine manufacturers in China, ensuring a smooth and successful business relationship.
How to check cnc turning and milling machine manufacturers website reliable,use google chrome SEOquake check if ranking in top 10M
To check the reliability of CNC turning and milling machine manufacturers’ websites, you can follow these steps:
1. Open Google Chrome: Start by launching the Google Chrome web browser on your computer.
2. Install SEOquake: SEOquake is a browser extension that provides valuable SEO data about websites. To install it, open a new tab in Chrome, go to the Chrome Web Store, search for “SEOquake,” and click on the “Add to Chrome” button to install the extension.
3. Search for CNC Turning and Milling Machine Manufacturers: In the Chrome address bar, type in the relevant keywords related to CNC turning and milling machine manufacturers. Press Enter to perform the search.
4. Analyze Search Results: Once the search results page appears, scroll down to examine the top 10 million ranking websites. SEOquake will display various metrics, such as the Google PageRank, Alexa Rank, number of indexed pages, etc. Ensure that the manufacturer’s website is listed in the top 10M for it to be considered reliable.
5. Visit the Manufacturer’s Website: Click on the link to the manufacturer’s website in the search results. This will open their website in a new tab.
6. Evaluate Features and Information: Take your time to explore the manufacturer’s website, paying attention to factors like website design, user-friendliness, product information, customer testimonials, certifications, contact details, and available support.
7. Verify Company Background: Look for an “About Us” or “Company Profile” page to gain insights into the manufacturer’s history, experience, expertise, and any industry associations.
8. Check Product Catalog and Specifications: Navigate through the product pages to ensure they offer CNC turning and milling machines that meet your requirements. Assess the detailed specifications, technical data, and any available documentation or downloadable resources.
9. Seek Customer Reviews and Feedback: Look for customer reviews, testimonials, or case studies on the manufacturer’s website or other reputable platforms to determine the satisfaction levels of their customers.
10. Contact the Manufacturer: If you find the website reliable based on the aforementioned criteria, consider reaching out to the manufacturer through their provided contact information. You can inquire about additional details, pricing, availability, or any other queries you might have.
By following these steps, you can effectively assess the reliability of CNC turning and milling machine manufacturers’ websites within a limit of 300 words.
Top 10 cnc turning and milling machine manufacturers in China with each 160 words introduce products,then use markdown create table compare
1. Haas Automation Inc.:
As one of the leading CNC turning and milling machine manufacturers in China, Haas Automation Inc. offers a wide range of high-quality machines. Their product lineup includes CNC lathes, vertical machining centers, horizontal machining centers, and rotary tables. Haas machines are known for their reliability, accuracy, and advanced technology, making them a popular choice among manufacturers.
2. DMG Mori Co., Ltd.:
DMG Mori Co., Ltd. is a global player in the machine tool industry, with a strong presence in China. They manufacture CNC turning and milling machines that cater to various industrial sectors. Their product range comprises multi-axis turning centers, vertical and horizontal machining centers, and flexible manufacturing systems. DMG Mori focuses on delivering smart, versatile, and high-performance machines to customers.
3. Mazak Corporation:
For over a century, Mazak Corporation has been at the forefront of CNC machine manufacturing. Their Chinese division offers a comprehensive range of CNC turning and milling machines, including vertical and horizontal machining centers, turning centers, and multitasking machines. Mazak machines are renowned for their precision, durability, and cutting-edge technology.
4. YCM (Yeong Chin Machinery Industries Co., Ltd.):
Specializing in CNC machine tool manufacturing, YCM provides advanced turning and milling solutions. Their product line includes CNC lathes, vertical machining centers, and horizontal machining centers. YCM machines are designed to optimize productivity, accuracy, and operational efficiency, making them suitable for a wide range of applications.
5. HAITEC CNC (China) Co., Ltd.:
With a strong focus on innovation, HAITEC CNC manufactures precision CNC turning and milling machines. Their product portfolio features CNC lathes, machining centers, turning centers, and vertical grinding machines. HAITEC CNC machines are known for their high precision, rigidity, and compact design, enabling manufacturers to achieve excellent machining results.
| Manufacturer | Products Offered |
|————————-|——————————————–|
| Haas Automation Inc. | CNC lathes, vertical and horizontal machining centers, rotary tables |
| DMG Mori Co., Ltd. | Multi-axis turning centers, vertical and horizontal machining centers, flexible manufacturing systems |
| Mazak Corporation | Vertical and horizontal machining centers, turning centers, multitasking machines |
| YCM (Yeong Chin Machinery Industries Co., Ltd.) | CNC lathes, vertical and horizontal machining centers |
| HAITEC CNC (China) Co., Ltd. | CNC lathes, machining centers, turning centers, vertical grinding machines |
These top CNC turning and milling machine manufacturers in China offer a range of products to cater to diverse machining needs. From Haas Automation Inc.’s reliable and advanced technology to DMG Mori Co., Ltd.’s smart and versatile machines, manufacturers can find suitable solutions for their requirements. Mazak Corporation’s precision and durability, YCM’s focus on productivity and efficiency, and HAITEC CNC’s high precision and rigidity make them prominent players in the Chinese market. Choose a manufacturer that aligns with your machining needs to enhance productivity and achieve superior machining results.
Background Research for cnc turning and milling machine manufacturers Companies in China, use qcc.com archive.org importyeti.com
When it comes to CNC turning and milling machine manufacturers in China, several companies stand out for their high-quality products and extensive experience in the industry. Here, we provide a brief background on some of the notable manufacturers:
1. Qiqihar Heavy CNC Equipment Co., Ltd.: Qiqihar Heavy CNC Equipment is recognized as one of the leading manufacturers in China, specializing in CNC turning and milling machines. With a history dating back to 1949, the company has accumulated vast knowledge and expertise in the field. They offer a wide range of machines suitable for various industries, including aerospace, automotive, and energy.
2. Shenyang Machine Tool Co., Ltd.: Shenyang Machine Tool, founded in 1947, is one of the oldest machine tool manufacturers in China. The company has a strong presence in the CNC turning and milling machines market, offering a diverse range of products. They are known for their advanced technology and innovative solutions that cater to the needs of different industries.
3. Dalian Machine Tool Group Corporation: Dalian Machine Tool Group is a renowned manufacturer in China, specializing in the production of CNC turning and milling machines. With over 70 years of experience, the company has established a strong reputation for its high precision and reliable machines. Their products find applications in various sectors, such as automotive, aerospace, and industrial machinery.
To gather further information about these companies, several sources can be utilized. QCC.com, an online business directory, provides comprehensive company profiles and information about the products and services they offer. Archive.org, an internet archive, allows access to previous versions of websites, enabling researchers to gather historical data about the companies. Importyeti.com provides data on import and export activities, allowing researchers to gain insights into the companies’ international presence and collaborations.
These sources, coupled with others available, offer a wealth of information to study and understand the background, capabilities, and reputation of CNC turning and milling machine manufacturers in China.
Leveraging Trade Shows and Expos for cnc turning and milling machine Sourcing in China
Trade shows and expos provide excellent opportunities for sourcing CNC turning and milling machines in China. These events bring together a wide range of suppliers and manufacturers from the industry, allowing buyers to explore different options, compare prices, and evaluate the quality of products.
By attending trade shows and expos, buyers can gain firsthand experience of the machines on display. They can witness live demonstrations, ask questions to the exhibitors, and even try out the machines themselves. This allows buyers to assess the performance, functionalities, and overall build quality of the CNC machines. It also provides an opportunity to discuss specific requirements with suppliers and obtain personalized solutions.
In addition to evaluating the machines, trade shows and expos also offer networking opportunities. Buyers can meet and connect with multiple suppliers, manufacturers, and industry experts. These connections can be valuable for building long-term relationships, obtaining references, and staying updated with the latest trends and technologies in the CNC turning and milling machine industry.
Furthermore, trade shows and expos often have special discounts and promotions for attendees. By purchasing directly from the event, buyers can negotiate better deals and save on costs. They can also benefit from exclusive offers or bundle deals when purchasing CNC machines and related accessories.
To make the most of trade shows and expos for CNC turning and milling machine sourcing in China, buyers should come well-prepared. They should research the participating exhibitors, identify their specific needs, and have a list of questions ready to ask. Buyers should also take notes and collect brochures, catalogues, and contact information to facilitate follow-up communication after the event.
In conclusion, trade shows and expos provide an effective platform for sourcing CNC turning and milling machines in China. By attending these events, buyers can evaluate machines, connect with suppliers, and negotiate favorable deals, ultimately enabling them to find the right CNC machines for their business needs.
The Role of Agents and Sourcing Companies in Facilitating cnc turning and milling machine Purchases from China
Agents and sourcing companies play a vital role in facilitating CNC turning and milling machine purchases from China. These entities act as intermediaries between buyers and manufacturers, ensuring a smooth and efficient purchasing process. Their expertise and local knowledge of the Chinese market help buyers overcome language barriers, cultural differences, and logistical challenges.
One of the primary responsibilities of agents and sourcing companies is to identify reliable manufacturers that specialize in CNC turning and milling machines in China. They have comprehensive databases and networks that allow them to shortlist and validate credible suppliers. This saves buyers valuable time and effort in finding suitable suppliers, as they can rely on the expertise of these intermediaries.
Agents and sourcing companies also help negotiate with suppliers on behalf of the buyers. They have a deep understanding of local market prices, industry standards, and negotiation tactics, which enable them to secure the best possible deals for their clients. They ensure that the quality, specifications, and pricing of the CNC machines meet the buyer’s requirements and expectations.
Furthermore, these intermediaries assist in conducting factory audits and quality inspections to ensure that the CNC machines are manufactured in compliance with international standards. They also help arrange sample shipments for buyers to assess the product’s quality before placing bulk orders.
In terms of logistics, agents and sourcing companies coordinate the shipping and handling of CNC machines from China to the buyer’s desired location. They handle customs documentation, packaging, and internal transportation, ensuring that the machines are delivered safely and on time.
Overall, agents and sourcing companies play a crucial role in simplifying the process of purchasing CNC turning and milling machines from China. Their expertise, local knowledge, and network of suppliers streamline the sourcing process, negotiate favorable terms, assure quality standards, and manage logistics. By utilizing these intermediaries, buyers can access a wider range of options, save time and resources, and have a smoother purchasing experience.
Price Cost Research for cnc turning and milling machine manufacturers Companies in China, use temu.com and 1688.com
When conducting a price cost research for CNC turning and milling machine manufacturers in China, two popular platforms to consider are Temu.com and 1688.com. These platforms can provide valuable insights into the pricing of various CNC machine manufacturers in the Chinese market.
Temu.com is a leading online marketplace that specifically caters to the manufacturing industry. It offers a wide range of products, including CNC machines. Utilizing its search function, users can easily locate CNC turning and milling machine manufacturers within China. The platform also provides pertinent information such as product specifications, company profiles, and customer reviews. By analyzing multiple listings, one can gain an understanding of the average price range and specific product features offered by different manufacturers.
Another widely-used platform for price cost research is 1688.com. Operated by Alibaba Group, 1688.com is a Chinese B2B marketplace, offering a vast array of products, including CNC machines. The platform provides comprehensive search filters based on product requirements, supplier location, and price range. Users can find detailed product descriptions, images, and company profiles to evaluate potential manufacturers. Additionally, being a B2B platform, 1688.com often offers direct communication channels with suppliers, allowing for further negotiation and better understanding of pricing.
To optimize the price cost research, it is recommended to use some additional strategies. Firstly, compare the prices of similar CNC turning and milling machines across multiple listings on both platforms. This will help identify price trends and potential cost-saving options. Secondly, reach out to the manufacturers directly through communication channels provided on the platforms. This will enable more precise negotiation and customization of the machine, potentially resulting in better pricing and added benefits.
In summary, Temu.com and 1688.com are reliable platforms for conducting price cost research for CNC turning and milling machine manufacturers in China. By leveraging their search functions, product information, and communication channels, users can gather valuable insights into the pricing landscape and find suitable manufacturers within their budgetary requirements.
Shipping Cost for cnc turning and milling machine import from China
When it comes to importing a CNC turning and milling machine from China, the shipping cost is a crucial consideration. Several factors affect the shipping cost, including the size and weight of the machine, the shipping method chosen, and the destination country.
The size and weight of the CNC machine play a significant role in determining the shipping cost. Generally, larger and heavier machines require specialized handling and may incur higher freight charges. It is essential to have the precise dimensions and weight of the machine before obtaining shipping quotes. Additionally, some carriers have weight and size restrictions, which can affect the shipping method and cost.
The shipping method chosen also influences the cost. The two most common options are air freight and sea freight. Air freight is generally faster but more expensive compared to sea freight. It is suitable for urgent and smaller shipments. On the other hand, sea freight is slower but more cost-effective for larger and heavier machines. It is crucial to assess the delivery timeline and budget to determine the most suitable shipping method.
The destination country also impacts the shipping cost. Different countries have varying import duties, taxes, and customs clearance fees. Import duties and taxes are typically based on the value of the machine and may significantly contribute to the overall shipping cost. Customs clearance fees are charged by the destination country and depend on the complexity of the clearance process.
To accurately estimate the shipping cost, it is advisable to contact freight forwarders or shipping companies that specialize in international shipments. They can provide quotes based on the specific requirements and guide through the necessary paperwork and regulations.
In conclusion, the shipping cost for importing a CNC turning and milling machine from China depends on factors such as size and weight of the machine, shipping method chosen, and destination country. It is essential to consider these factors and consult with shipping experts to ensure a smooth and cost-effective importing process.
Compare China and Other cnc turning and milling machine Markets: Products Quality and Price,Visible and Hidden Costs
China has established itself as a key player in the global CNC turning and milling machine market, competing with other major markets such as the United States, Germany, Japan, and South Korea. When comparing China with these markets in terms of product quality and price, as well as visible and hidden costs, several factors come into play.
Product Quality:
China initially gained a reputation for producing lower-quality machines compared to more established markets. However, over the years, China has made significant strides in improving the quality of its CNC machines. Many Chinese manufacturers have invested in research and development, technology, and skilled labor, resulting in the production of high-quality machines that can compete with those from other markets.
Price:
One of China’s main advantages in the global market is its ability to offer CNC turning and milling machines at a much lower price compared to its competitors. Chinese manufacturers benefit from lower production costs, including labor and raw materials, allowing them to offer cost-effective solutions to customers worldwide. However, it should be noted that lower prices do not always mean compromised quality, as Chinese manufacturers have been successful in maintaining a balance between cost and quality.
Visible Costs:
Visible costs mainly include the initial purchase price of the CNC machines. Chinese manufacturers often provide competitive pricing, allowing customers to acquire the required machinery at a lower cost compared to other markets. However, it is worth considering other factors such as after-sales service, maintenance costs, and spare parts availability, which may vary between China and other markets.
Hidden Costs:
Hidden costs encompass factors that are not immediately apparent but can impact the overall cost of owning and operating CNC turning and milling machines. These costs may include transportation fees, import duties, taxes, and potential delays in obtaining spare parts when dealing with foreign manufacturers. It is essential to consider these hidden costs to make an informed decision.
In conclusion, China has made remarkable progress in terms of product quality and offers competitive pricing in the global CNC turning and milling machine market. While China is known for its cost advantage, other factors such as product quality, after-sales service, and hidden costs should also be considered when comparing China with other markets.
Understanding Pricing and Payment Terms for cnc turning and milling machine: A Comparative Guide to Get the Best Deal
When it comes to purchasing a CNC turning and milling machine, understanding the pricing and payment terms is crucial to ensure that you get the best deal. This comparative guide provides insights into the factors that affect pricing and payment, helping you make an informed decision while keeping the word count under 300 words.
1. Machine Specifications:
The price of a CNC turning and milling machine depends on various factors such as machine size, power, accuracy, and additional features. Higher specifications and capabilities often result in a higher price tag. It is essential to assess your specific requirements to determine the appropriate specifications suitable for your needs.
2. Machine Brand and Quality:
Different brands offer CNC machines with varying quality levels. Reputable brands typically offer machines with better durability, accuracy, and reliability. While these machines may come at a higher price, they often provide better long-term value due to reduced maintenance and improved performance.
3. New vs. Used Machines:
New machines usually come with a higher price compared to used ones. However, they offer the advantage of having the latest technology and potentially longer lifespan. On the other hand, used machines can be a more budget-friendly option, but thorough inspection and assessment of the machine’s condition are essential to avoid unforeseen maintenance or repair costs.
4. Payment Methods:
Payment terms for CNC machines can vary depending on the supplier. Common payment options include upfront payment, installment plans, or leasing options. Evaluate your financial situation and determine the most suitable payment method for your business. Consider factors such as cash flow, budget, and long-term requirements.
5. Supplier Negotiations:
When finalizing a deal, it is always beneficial to negotiate with the supplier. Try to negotiate the price, payment terms, warranty, and other factors that can potentially lower the overall cost or improve the deal. Demonstrate your willingness to commit to a long-term partnership to increase your chances of obtaining a more favorable offer.
In conclusion, understanding pricing and payment terms is an essential aspect of purchasing a CNC turning and milling machine. By considering machine specifications, brand and quality, new vs. used options, payment methods, and supplier negotiations, you can make an informed decision and secure the best deal that aligns with your business’s needs and budget.
Chinese Regulations and Industry Standards Certifications for cnc turning and milling machine,Import Regulations and Customs for cnc turning and milling machine from China
China has a well-established system of regulations and industry standards for CNC turning and milling machines. The key certification that manufacturers need to obtain is the China Compulsory Certification (CCC) mark, also known as the 3C mark. This mark is mandatory for all products to be sold on the Chinese market, including CNC machines. To obtain the 3C mark, manufacturers must undergo a series of tests and inspections to ensure the quality and safety of their products.
In addition to the CCC mark, there are various industry standards that manufacturers can choose to comply with, such as the GB/T 16855.1-2018 standard for CNC machine tools. This standard specifies the requirements for safety and performance of CNC turning and milling machines.
When importing CNC turning and milling machines from China, it is important to be aware of the import regulations and customs procedures. Importers need to provide the necessary documentation, including the commercial invoice, packing list, bill of lading or airway bill, and a copy of the CCC certificate. It is also essential to ensure that the machines comply with the applicable regulations and standards of the destination country.
Customs duties and taxes may apply when importing CNC turning and milling machines from China. The specific rates vary depending on the country of import and the classification of the machines. Importers should consult with their local customs authorities to determine the applicable rates and procedures.
In summary, China has established regulations and industry standards for CNC turning and milling machines, with the CCC mark being the key certification required. Importing these machines from China requires compliance with the applicable import regulations and customs procedures of the destination country.
Sustainability and Environmental Considerations in cnc turning and milling machine Manufacturing
Sustainability and environmental considerations in CNC turning and milling machine manufacturing are essential for minimizing the industry’s impact on the environment. Several strategies can be implemented to achieve sustainability goals.
Firstly, manufacturers can focus on energy efficiency. CNC machines consume a significant amount of energy during operation. By selecting energy-efficient components and adopting technologies such as regenerative braking, energy usage can be reduced. Additionally, implementing automated shutdown mechanisms when machines are not in use can further minimize energy consumption.
Secondly, the choice of materials in machine manufacturing is crucial for sustainability. Opting for recyclable and low-impact materials helps reduce the carbon footprint. Manufacturers can also explore alternatives to traditional manufacturing materials, such as using bio-based polymers or incorporating recycled materials in machine parts.
Another important consideration is waste reduction and management. Manufacturers should implement efficient processes to minimize material waste during production. Implementing recycling programs and finding innovative ways to reuse or repurpose waste materials can further contribute to sustainability efforts.
Furthermore, promoting the circular economy is vital. By designing machines for disassembly and facilitating component reuse or recycling, manufacturers can ensure that products have a longer lifespan. This approach reduces the need for new materials and minimizes waste generation.
Sustainable transportation and logistics should also be prioritized. Manufacturers can optimize shipping routes and adopt cleaner transportation methods to reduce greenhouse gas emissions associated with machine deliveries.
Lastly, manufacturers should strive for continuous improvement. Regular monitoring and assessment of environmental performance can identify areas for improvement. Engaging employees in sustainability initiatives and fostering a culture of environmental responsibility throughout the organization can also contribute to long-term sustainability goals.
In conclusion, sustainability and environmental considerations play a crucial role in CNC turning and milling machine manufacturing. By focusing on energy efficiency, material selection, waste reduction, circular economy principles, sustainable transportation, and continuous improvement, manufacturers can minimize the industry’s environmental impact and contribute to a more sustainable future.
List The Evolution history of “cnc turning and milling machine”
The evolution of CNC turning and milling machines can be traced back to the late 1940s and early 1950s, when the concept of numerical control was first introduced. Initially, machines were controlled by punched tape systems and used primarily in manufacturing industries for repetitive tasks.
In the 1960s, the development of minicomputers revolutionized the industry by enabling real-time control of machines. Major advancements in computer technology allowed for the creation of digital control systems, which significantly improved the precision, flexibility, and productivity of CNC machines.
The 1970s saw the introduction of multitasking machines that combined turning and milling capabilities in a single unit. These machines allowed for the integration of various operations, reducing setup time and increasing efficiency.
In the 1980s and 1990s, the miniaturization of computers and advancements in software and hardware led to the development of more compact and powerful CNC machines. These machines incorporated features like automatic tool changers, improved spindle speeds, and advanced programming capabilities that further enhanced productivity and accuracy.
The early 2000s witnessed the emergence of 5-axis machining, allowing for the simultaneous control of multiple axes and enabling the production of complex parts with high precision. This advancement played a crucial role in industries such as aerospace and automotive, where intricate components are frequently required.
Additionally, continued advancements in software and networking technologies led to the introduction of computer-aided design (CAD) and computer-aided manufacturing (CAM) systems. These systems streamlined the design-to-production process, allowing for seamless integration of CAD/CAM software with CNC machines.
More recent developments have focused on automation and robotics. Robotic arms and automated loading/unloading systems have been integrated into CNC machines, minimizing human intervention and increasing production efficiency.
In summary, the evolution history of CNC turning and milling machines can be characterized by significant advancements in control systems, integration of multiple operations, miniaturization of computers, introduction of multitasking machines, and incorporation of automation and robotics. These advancements have revolutionized the manufacturing industry, making CNC machines fundamental for precision machining applications.
The Evolution and Market Trends in cnc turning and milling machine Industry
The CNC (Computer Numerical Control) turning and milling machine industry has undergone significant evolution and witnessed several market trends over the years. These machines have become a crucial part of various industries, including automotive, aerospace, electronics, and medical, due to their high precision, efficiency, and productivity.
One of the key market trends in this industry is the increased demand for multi-axis CNC machines. The need for complex and intricate parts in industries such as aerospace and automotive has resulted in the popularity of multi-axis machines, which can perform multiple machining operations in a single setup. This trend has driven the development and adoption of advanced CNC turning and milling machines that offer greater flexibility and improved productivity.
Another market trend is the integration of automation and robotics in CNC machines. With the rise of Industry 4.0 and the focus on smart manufacturing, manufacturers are increasingly implementing automation solutions to enhance production efficiency and reduce downtime. This integration allows for seamless communication and coordination between CNC machines and other manufacturing processes, leading to higher accuracy, faster turnaround times, and reduced labor costs.
Furthermore, the industry has witnessed advancements in machine design and software technology. CNC turning and milling machines are becoming more compact, ergonomic, and energy-efficient. Improved machine design ensures better rigidity, stability, and vibration damping, resulting in higher machining accuracy. Moreover, the development of advanced software technologies, such as CAD/CAM (Computer-Aided Design/Computer-Aided Manufacturing) systems, has simplified programming and increased the capabilities of CNC machines.
The global market for CNC turning and milling machines has been experiencing steady growth, driven by the expanding manufacturing sector, increasing demand for precision components, and advancements in technology. Asia-Pacific region, particularly China and Japan, dominate the market due to the presence of prominent manufacturers and robust industrial infrastructure. However, North America and Europe also hold a significant market share, owing to their focus on technological innovation and adoption.
In conclusion, the evolution of CNC turning and milling machines has been characterized by the adoption of multi-axis machines, integration of automation and robotics, and advancements in machine design and software technology. These trends have resulted in increased productivity, efficiency, and accuracy in the machining industry. The market for CNC machines is witnessing steady growth globally, with Asia-Pacific leading the market.
Custom Private Labeling and Branding Opportunities with Chinese cnc turning and milling machine Manufacturers
If you are searching for custom private labeling and branding opportunities with Chinese CNC turning and milling machine manufacturers, you are in luck. China has become a powerhouse in the manufacturing industry, offering a wide range of high-quality machinery at competitive prices. By tapping into this market, you have the chance to establish your own brand and take advantage of the growing demand for precision machining equipment.
Chinese CNC turning and milling machine manufacturers are well-equipped to cater to the specific needs of your business. They possess the technical expertise, advanced machinery, and vast production capabilities to customize machines according to your specifications. Whether you require specific features, dimensions, or branding elements, they can meet your requirements.
One of the key advantages of working with Chinese manufacturers is the freedom to implement your brand’s identity into the machines. Private labeling allows you to showcase your company’s logo, colors, and other branding elements on the equipment. This not only helps in promoting your brand but also creates a sense of trust and familiarity among your customers.
Moreover, Chinese manufacturers often offer flexible solutions for customization. This means that you can modify the machines based on your target market’s preferences or industry-specific requirements. From adding specific software functions to incorporating different language options, Chinese manufacturers can tailor the machines to suit your customers’ needs.
Collaborating with Chinese manufacturers also gives you the opportunity to benefit from cost-effective production. Chinese factories have access to abundant resources, efficient supply chains, and skilled labor, allowing them to offer competitive pricing. This enables you to maximize your profit while providing high-quality machinery to your customers.
In conclusion, working with Chinese CNC turning and milling machine manufacturers opens doors to custom private labeling and branding opportunities. By leveraging their technical expertise, production capabilities, and cost advantages, you can establish your own brand identity and meet the specific needs of your target market. Make the most out of this manufacturing powerhouse and take your business to new heights.
Tips for Procurement and Considerations when Purchasing cnc turning and milling machine
When purchasing a CNC turning and milling machine, there are several key considerations that should be taken into account to ensure a successful procurement process.
1. Machine specifications: It is crucial to thoroughly evaluate the machine specifications and capabilities to ensure they align with your specific requirements. Consider factors such as maximum turning and milling diameters, spindle speed, tool capacity, and overall machine dimensions.
2. Cost: Set a realistic budget and evaluate the cost of the machine, including any additional accessories or software required. Consider the long-term operational costs, such as maintenance, repairs, and energy consumption. It is essential to strike a balance between cost and quality to avoid compromising on machine performance.
3. Supplier reputation and support: Research and choose a reputable supplier that offers quality machines and excellent customer support. Consider factors such as the supplier’s experience, customer reviews, and after-sales service. A reliable supplier will provide technical support, training, and spare parts availability to ensure smooth machine operation.
4. Machine interface and programming: Review the machine’s user interface and programming capabilities. Ensure that the machine is equipped with user-friendly software and supports standard programming languages such as G-code. Compatibility with CAD/CAM software should also be considered for seamless integration into your existing manufacturing processes.
5. Machine accuracy and repeatability: Evaluate the machine’s accuracy and repeatability to ensure precise and consistent machining results. Consider factors such as positioning accuracy, spindle runout, and tool changing accuracy. Opting for a machine with higher precision levels can greatly enhance the overall quality and efficiency of your machining operations.
6. Customization options: Determine if the machine can be customized or adapted to meet your unique requirements. Some suppliers may offer additional features or machine configurations tailored to specific machining needs. Assess if these customizations are necessary and whether they align with your budget and long-term objectives.
7. Safety features: Prioritize machines that incorporate advanced safety features to ensure operator protection. Consider features like emergency stop buttons, safety interlocks, and protective enclosures. Adequate safety measures are crucial to prevent accidents and comply with regulatory guidelines.
By carefully considering these factors, you can make an informed decision and procure a CNC turning and milling machine that effectively meets your production needs while ensuring long-term operational success.
FAQs on Sourcing and Manufacturing cnc turning and milling machine in China
Q1: Why should I consider sourcing and manufacturing CNC turning and milling machines in China?
A1: China has emerged as a global manufacturing hub, offering cost-effective solutions for various industries. Sourcing CNC turning and milling machines from China can provide substantial cost savings due to lower labor and production costs compared to many western countries. Additionally, China has a vast network of suppliers and manufacturers, ensuring a wide range of options for customization and scalability.
Q2: How do I find reliable suppliers or manufacturers in China?
A2: Researching and selecting reliable suppliers or manufacturers is crucial. Start by conducting extensive online research, utilizing platforms like Alibaba or Global Sources to find potential suppliers. Verify their credibility by checking their certifications, past customer reviews, and years of experience. It is highly recommended to visit the facility in person or send a representative to assess their capabilities and production processes.
Q3: What are the potential challenges in sourcing and manufacturing CNC machines from China?
A3: Language and cultural barriers can be challenging, so it is essential to communicate clearly and ensure both parties are on the same page regarding specifications, quality standards, and delivery schedules. Logistics and shipping can also be complex, so partnering with a reputable freight forwarder can help streamline the process and minimize any potential delays or complications.
Q4: Is quality control a concern when sourcing from China?
A4: Quality control is a crucial aspect of sourcing from China. To mitigate risks, consider hiring third-party quality inspection services to monitor production, conduct random checks, and ensure adherence to specified requirements. Establishing clear quality control protocols and having open communication with the supplier can help maintain high standards.
Q5: What is the typical lead time for manufacturing CNC turning and milling machines in China?
A5: Lead times may vary depending on the complexity and specifications of the CNC machines being manufactured. On average, the lead time ranges from 4 to 8 weeks for standard models. However, it is essential to factor in additional time for customization, quality control inspections, and shipping.
Q6: How do I handle intellectual property protection when sourcing from China?
A6: Intellectual property protection should be a top priority when sourcing from China. Start by safeguarding your designs, inventions, or technology through patents, trademarks, or copyrights. It is advisable to work with suppliers who have a strong track record of respecting intellectual property rights. Additionally, signing confidentiality agreements and monitoring production processes can help mitigate risks.
In conclusion, sourcing and manufacturing CNC turning and milling machines in China can offer cost-effective solutions, but require thorough research, clear communication, quality control measures, and intellectual property protection to ensure a smooth and successful procurement process.
Why contact sourcifychina.com get free quota from reliable cnc turning and milling machine suppliers?
Sourcifychina.com is able to obtain a free quota from reliable CNC turning and milling machine suppliers due to the following reasons:
1. Established Partnerships: Sourcifychina.com has built strong and longstanding relationships with various CNC turning and milling machine suppliers over the years. Through these partnerships, the website has gained trust and credibility, enabling them to negotiate free quotas for their clients.
2. Volume of Orders: Being a popular platform for sourcing machinery, Sourcifychina.com handles a significant volume of orders for CNC turning and milling machines. The high demand generated by the website allows them to leverage their purchasing power and negotiate deals with suppliers, including free quotas.
3. Increased Exposure: By connecting reliable suppliers with prospective buyers, Sourcifychina.com acts as a valuable marketing and sales channel for suppliers. Suppliers understand that offering a free quota allows them to showcase their products to a wide customer base, ultimately leading to increased exposure and potential future business opportunities.
4. Customer Acquisition: Offering a free quota enables suppliers to attract potential customers who are interested in CNC turning and milling machines but may be hesitant to make a financial commitment initially. By removing the upfront cost, suppliers can effectively capture leads and convert them into paying customers in the long run.
5. Competitive Advantage: In a highly competitive industry, suppliers are constantly looking for ways to stand out and gain an advantage over their competitors. By offering free quotas through Sourcifychina.com, suppliers can attract more potential customers and differentiate themselves from other suppliers who may charge for their quotes.
In summary, Sourcifychina.com obtains free quotas from reliable CNC turning and milling machine suppliers by leveraging their established partnerships, handling a large volume of orders, providing increased exposure to suppliers, acquiring new customers, and offering a competitive advantage in the market.