Introduce about custom injection mold guide,Qulity,Cost,Supplier,Certification,Market,Tips,FAQ
Custom injection molding is a widely used manufacturing process for creating complex plastic parts efficiently and accurately. It involves the creation of a custom mold that is injected with molten plastic to produce the desired shape. This guide aims to provide an overview of the key aspects related to custom injection molding.
Quality is a crucial factor in custom injection molding. The use of high-quality molds and advanced manufacturing techniques ensures precision, durability, and consistency in the produced parts. Quality control procedures, including inspections and testing, are implemented throughout the process to ensure the highest standards are met.
Cost considerations play a significant role in custom injection molding. Factors such as the complexity of the part, material selection, mold design, and production volume influence the overall cost. When evaluating cost, it is important to consider not only the initial production expense but also the long-term benefits of using injection molding.
Selecting the right supplier is critical for successful custom injection molding. One must choose an experienced and reputable company that can meet specific requirements, provide design and engineering support, and deliver competitive pricing.
Certification is an essential aspect when choosing a custom injection molding supplier. ISO certifications, such as ISO 9001 for quality management systems, demonstrate a company’s commitment to quality, process control, and customer satisfaction. It is advisable to partner with certified manufacturers to ensure reliable and consistent product manufacturing.
The custom injection molding market is expanding rapidly due to its versatility and efficiency. Various industries, including automotive, electronics, medical, and consumer goods, rely on injection molding for the production of a wide range of components. The market demand for custom injection molding is expected to grow further in the coming years.
Here are some tips to consider when embarking on custom injection molding projects: engage in early collaboration with suppliers, optimize part design for manufacturability, select the appropriate material, and plan for prototyping and testing iterations.
Frequently Asked Questions (FAQs) regarding custom injection molding cover topics such as the advantages of injection molding over other manufacturing methods, the limitations of the process, lead times, tooling costs, surface finishes, and material options. Answering these queries helps to provide clarity and ensure a successful injection molding project.
In conclusion, custom injection molding offers a reliable and cost-effective solution for manufacturing complex plastic parts. By considering the aspects of quality, cost, supplier selection, certification, market demand, and following helpful tips and FAQs, businesses can make informed decisions and achieve successful outcomes in their custom injection molding projects.
Types of custom injection mold
There are several types of custom injection molds that are used in the manufacturing industry. These molds are designed to produce specific parts or products by injecting molten material into a mold cavity. Custom injection molds are created based on the specific requirements and specifications of the product and can vary in complexity and design. Here are some of the common types of custom injection molds:
1. Two-Plate Molds: This is the simplest and most common type of custom injection mold. It consists of two plates that are designed to open and close around the mold cavity. The molten material is injected into the cavity through a gate, and once the material has cooled and solidified, the mold opens to release the finished product.
2. Three-Plate Molds: Three-plate molds are similar to two-plate molds but have an additional plate called the stripper plate. The stripper plate helps in removing the product from the mold cavity by separating it from the runner system. This allows for easier ejection of the product and reduces the chances of damage.
3. Hot Runner Molds: In hot runner molds, the molten material is injected directly into the mold cavity through a heated manifold system, eliminating the need for a runner system. This reduces material waste and improves overall productivity. Hot runner molds are commonly used for high-volume production.
4. Family Molds: Family molds are used to produce multiple parts simultaneously. These molds contain multiple cavities, each designed to produce a different part or product. Family molds are used to improve production efficiency and reduce costs.
5. Insert Molds: Insert molds are used when a part requires additional components or inserts. The inserts are placed in the mold cavity before the injection process, and the molten material encapsulates the inserts during the molding process. This allows for the creation of complex and integrated parts.
6. Overmolding: Overmolding involves the injection of multiple materials or colors into a single mold. This technique is used to create products with soft-touch surfaces, multiple colors, or products with handles or grips.
These are just a few examples of the types of custom injection molds used in the manufacturing industry. The choice of mold depends on the specific requirements of the product, production volume, cost considerations, and desired end result. Manufacturers work closely with tooling experts to determine the most suitable type of mold for a given application.
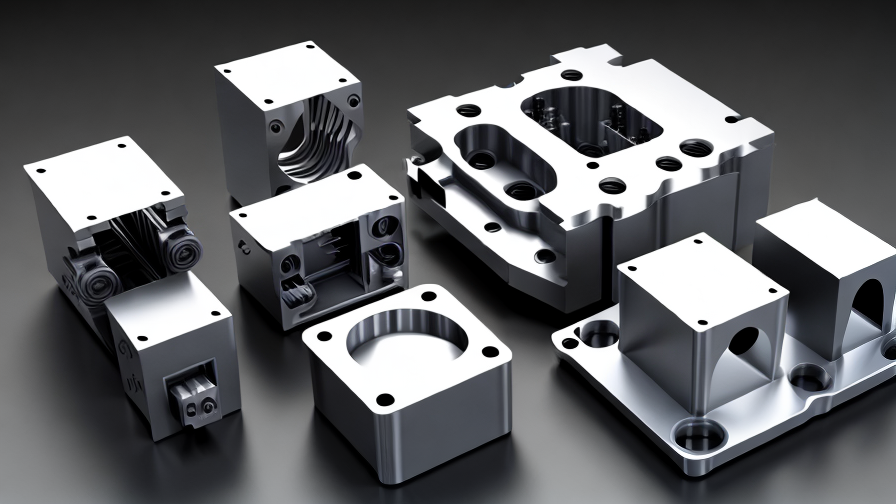
Pros and Cons of Using custom injection mold
Using a custom injection mold has its own set of pros and cons. Here are some of the key advantages and disadvantages:
Pros:
1. Cost-effectiveness: Custom injection molds can be expensive to create initially but are cost-effective in the long run. Once the mold is set, it allows for high-volume production at a significantly lower cost per unit, making it ideal for mass production.
2. Design flexibility: Custom injection molds offer unparalleled design flexibility. They can be customized to produce complex shapes, intricate patterns, and detailed textures. This allows for the creation of unique and visually appealing products that stand out in the market.
3. Fast production: Injection molding is a highly efficient process. Once the custom mold is developed, the production cycle time is relatively short. This results in faster product turnaround and shorter lead times, ensuring timely delivery to meet market demands.
4. High precision and consistency: Injection molding offers precise and accurate production, ensuring consistency in dimensions, shape, and quality across all units. This is particularly beneficial for products where precision and uniformity are critical, such as medical devices or automotive components.
Cons:
1. Initial cost and lead time: Developing a custom injection mold can be costly, especially for small businesses or startups with limited budgets. Additionally, creating the mold can take time, delaying the production process and time to market.
2. Limited design changes: Custom injection molds require significant investment and are designed with specific product specifications in mind. As a result, making design changes to the mold can be expensive and time-consuming. This limitation may restrict the ability to modify or update a product’s design as desired.
3. Volume requirements: Custom injection molds are most cost-effective for high-volume production. If the production quantity is low, the high initial cost of mold creation may not be feasible, making it more appropriate to use other manufacturing methods.
4. Complexity and expertise: Developing a custom injection mold requires expertise in design and engineering. The complex nature of injection molding necessitates skilled professionals and specialized equipment. Small businesses or those without experienced personnel might face difficulties in handling the process efficiently.
In conclusion, while custom injection molds offer cost-effectiveness, design flexibility, fast production, precision, and consistency, they require a significant initial investment, have limitations in design changes, volume requirements, and complexities in implementation. Careful consideration of these pros and cons is essential when deciding whether to use a custom injection mold for a specific product.
custom injection mold Reference Specifications (varies for different product)
Custom Injection Mold Reference Specifications:
The specifications for custom injection mold can vary depending on the specific product being manufactured. However, there are some general guidelines that need to be followed to ensure a successful mold design and production process. The following reference specifications provide an overview of key considerations:
1. Mold Material: The selection of mold material is crucial as it directly impacts the mold’s durability, heat resistance, and dimensional stability. Commonly used materials include hardened steel, aluminum alloys, and pre-hardened steels. The specific material choice depends on factors like production volume, budget, and product requirements.
2. Mold Base and Cavity: The mold base should be designed to accommodate the required number of cavities, ensuring optimal productivity while maintaining structural integrity. The cavity layout and design should consider the product’s shape, dimensions, and any additional features like ribs, bosses, or inserts.
3. Cooling System: An efficient cooling system is essential for maintaining consistent mold temperature and ensuring high-quality part production. The cooling channel design should ensure uniform cooling and avoid hot spots, warpage, or sink marks. Proper placement of cooling lines is critical to minimize cycle time.
4. Ejection System: The ejection system aids in the removal of molded parts from the mold. It typically consists of ejector pins or sleeves, which need to be designed to avoid part distortion or damage. The ejection system design should consider the part’s shape, draft angles, and any surface finish requirements.
5. Venting: Adequate venting is necessary to prevent trapped air or gases, which can lead to defects like burns, voids, or gas traps. Vent locations and sizes need to be strategically placed to facilitate air escape during the injection molding process.
6. Draft Angles: Incorporating draft angles in the design helps in the smooth ejection of parts from the mold. The ideal draft angle may vary depending on the material, part complexity, and demolding requirements. It is essential to consider draft angles early in the design process to avoid rework or increased manufacturing costs.
7. Surface Finish: The desired surface finish of the molded parts dictates the selection of mold material and surface treatment processes. Polishing, texturing, or other surface treatments may be needed for aesthetic or functional purposes, such as enhancing release properties or adding texture.
8. Tolerances: The mold design should consider the product’s required tolerances, which can vary depending on the material, part dimensions, and quality requirements. Designing the mold with appropriate clearances and fits ensures the desired part accuracy and functionality.
In summary, these reference specifications provide a glimpse into the considerations involved in the custom injection mold design process. It is important to note that the specifications will vary for different products and industries. Collaborating with experienced mold designers and manufacturers can help to optimize the mold design and ensure efficient production of high-quality injection molded parts.
Applications of custom injection mold
Custom injection molding is a versatile manufacturing process that involves the production of complex and precise plastic parts in large quantities. This technology has numerous applications across various industries due to its ability to create customized components with consistent quality and high production efficiency, making it a popular choice for many manufacturers.
One of the primary applications of custom injection molding is in the automotive industry. It is used to produce a wide range of parts, such as dashboards, interior and exterior trims, bumpers, and engine components. Custom injection molding allows for intricate designs, precise dimensions, and superior surface finishes, ensuring the production of durable and aesthetically appealing automotive parts.
The electronics and telecommunications industry also extensively utilizes custom injection molding to manufacture components like phone casings, connectors, and switches. These parts often require high precision and excellent dimensional stability to ensure the proper functioning of electronic devices. Custom injection molding enables the production of these parts with tight tolerances and exceptional repeatability, meeting the specific requirements of the industry.
The medical industry benefits significantly from custom injection molding, as it enables the production of precision components used in medical devices and equipment. From syringes and catheters to surgical tools and implantable devices, custom injection molding ensures the production of sterile, biocompatible, and high-quality medical products.
Consumer products, such as household appliances, toys, and packaging, also rely on custom injection molding. The process allows for the creation of products with intricate designs and various colors, enhancing their visual appeal. Additionally, custom injection molding offers cost-effective production for high-volume consumer goods, making it an ideal choice for manufacturers in this sector.
Industrial applications, including aerospace, construction, and energy, also benefit from custom injection molding. The ability to produce complex and durable plastic parts is crucial in these sectors, as they often require components that can withstand harsh operating conditions and heavy loads. Custom injection molding meets these requirements by producing parts with high structural integrity and exceptional resistance to environmental factors.
In conclusion, custom injection molding is a versatile technology with myriad applications across different industries. From automotive and electronics to medical and consumer products, this manufacturing process offers a cost-effective and efficient solution for producing complex, precise, and high-quality plastic parts.
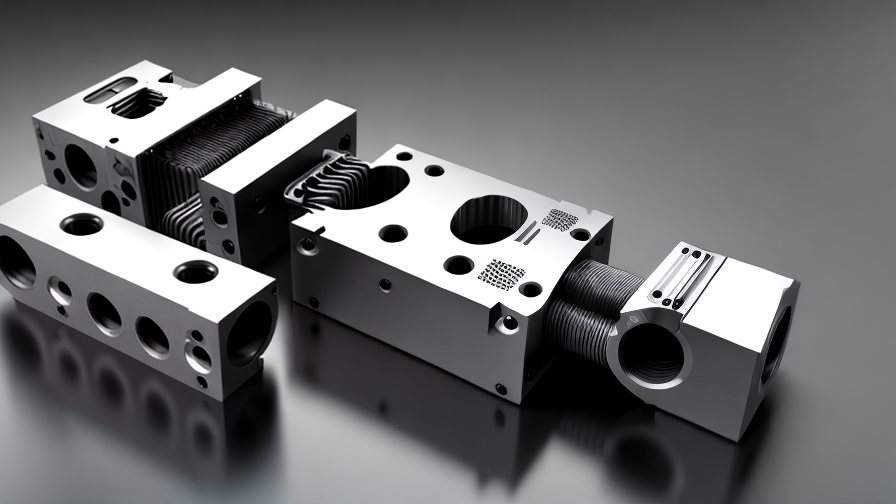
The Work Process and how to use custom injection mold
The work process of custom injection molding involves several steps to achieve the desired end product. It begins with the design phase, where engineers create a 3D model using design software. This step ensures that the mold and part geometry are accurately represented.
Once the design is finalized, it is converted into machine code that can be understood by the injection molding machine. The mold material, typically steel or aluminum, is then selected based on the specific requirements of the project, such as part complexity or anticipated production volume.
The mold is created using precision machining techniques like milling or CNC machining. Mold cavities and cores are carefully crafted to match the part design, allowing for the injection of molten material to form the desired shape. Mold components like cooling channels and ejection systems are also incorporated during this stage.
Next, the injection molding machine is prepared by installing the mold and connecting it to the machine’s heating and cooling systems. The machine is preheated to the specified temperature, and the molten material is loaded into the machine’s hopper. The material is then melted and injected into the mold under high pressure using a reciprocating screw or plunger.
After the material fills the mold cavities, it is allowed to cool and solidify. Cooling time can vary based on factors such as material type and part thickness. Once the part has solidified, the mold is opened, and the part is ejected using an ejection system.
The part is then inspected for defects or imperfections, and any necessary post-processing operations like trimming or surface finishing are performed. Finally, the part is packaged and prepared for shipment to the customer.
To use a custom injection mold effectively, it is essential to communicate the specific requirements and expectations to the mold manufacturer. This includes details like desired part dimensions, material properties, and expected production volumes. A thorough understanding of the end-use application can help in selecting the appropriate mold material and design features.
Regular maintenance and cleaning of the mold are crucial to prolong its lifespan and ensure consistent part quality. This includes periodic inspection for wear or damage, cleaning of cooling channels, and lubrication of moving parts.
By following these steps and considering important factors, custom injection molds can be used to efficiently produce high-quality plastic parts for various industries like automotive, medical, or consumer goods.
Quality Testing Methods for custom injection mold and how to control the quality
Quality testing for custom injection molds is crucial to ensure the production of high-quality parts. Several methods can be employed to control the quality of these molds:
1. Visual inspection: Thorough visual inspection should be conducted to identify any visible defects, such as surface imperfections, scratches, or uneven texture. This can help ensure that the mold is free from any obvious defects that may affect the quality of the final product.
2. Dimensional measurement: Precise measurements of critical dimensions are essential to verify that the mold meets the required specifications. This can be achieved using measurement tools like calipers, micrometers, or coordinate measuring machines (CMMs). A meticulous assessment of dimensional accuracy helps to ensure the production of parts with the correct dimensions.
3. Mold functionality testing: Functional testing is performed to validate the proper functioning of the custom injection mold. This involves examining the mold’s ability to perform actions such as opening and closing smoothly, ejecting parts correctly, and aligning properly with other components. Functional testing helps to ensure the mold’s reliability during production runs.
4. Mold material testing: The material used for the custom injection mold should be tested to verify its quality and suitability. Material testing may involve checking for the correct hardness, chemical composition, and mechanical properties. This can help identify any material defects that might impact the mold’s performance and longevity.
5. Sampling and production testing: Regular sampling and production testing should be conducted to assess the quality of the parts produced using the custom injection mold. This involves inspecting the produced parts for any defects, such as warping, sink marks, or surface imperfections. Statistical process control techniques can also be implemented to monitor and control the quality of the parts during production.
To control the quality of custom injection molds effectively, it is essential to establish robust quality control processes throughout the manufacturing cycle. This includes implementing proper design controls, using high-quality materials, conducting regular inspections and testing, and maintaining accurate documentation of all quality activities.
By employing these quality testing methods and establishing comprehensive quality control practices, manufacturers can maintain the highest standards for custom injection molds, ensuring the production of consistent and defect-free parts.
custom injection mold Sample Policy and Post-Purchase Considerations for custom injection mold from China
When it comes to sourcing custom injection molds from China, it is crucial to have a clear understanding of the sample policy and post-purchase considerations. These factors can significantly impact the success of your project. Here is a concise guide summarizing important points in less than 300 words:
Sample Policy:
1. Requesting samples: Before placing a bulk order, it is advisable to request a sample from the supplier. This allows you to assess the quality, design, and functionality of the custom injection mold.
2. Cost and lead time: Inquire about the cost of obtaining samples, including shipping charges. Additionally, clarify the lead time required to produce and deliver the samples.
3. Modifications and revisions: Discuss whether the supplier allows modifications and revisions based on your feedback on the sample. Determine whether there are any extra charges associated with these modifications.
4. Quality assurance: Ensure that the sample provided matches the quality standards you expect for your final product. Inspect for defects, accuracy, and durability.
5. Communication: Maintain clear and open communication with the supplier during the sample evaluation process. Address any concerns promptly to improve the chances of meeting your expectations.
Post-Purchase Considerations:
1. Manufacturing process oversight: Engage in regular communication with the supplier to monitor the manufacturing process. Obtain updates, production status, and inspection reports to ensure quality control.
2. Quality inspections: Conduct rigorous quality inspections throughout the production process, including inspecting raw materials, molds, and finished products. This helps identify and rectify any arising issues.
3. Payment terms and conditions: Clearly outline the payment terms to avoid any misunderstandings. Negotiate fair terms and discuss payment milestones based on the progress of the production.
4. Shipping and logistics: Collaborate with the supplier to determine the most suitable shipping method and ensure proper packaging and labeling to prevent damage during transit.
5. Legal considerations: Familiarize yourself with the legalities involved in importing custom injection molds, such as customs regulations, documentation requirements, and intellectual property protection.
By adhering to the sample policy and considering post-purchase factors, you can mitigate risks and ensure a successful outcome when procuring custom injection molds from China.
Sourcing custom injection mold from China: Opportunities, Risks, and Key Players
Sourcing custom injection molds from China presents several opportunities for businesses. One key advantage is cost-effectiveness, as China offers competitive prices due to lower manufacturing expenses. This makes it an attractive option for companies seeking to reduce production costs without compromising on quality. Additionally, China has a well-established manufacturing industry with advanced technology and skilled labor, enabling businesses to access a wide range of expertise and product capabilities.
However, there are also risks associated with sourcing injection molds from China. Quality control can be a concern, as there may be variations in the manufacturing process, resulting in inconsistent product quality. To mitigate this risk, thorough due diligence is crucial, including verifying the manufacturer’s certifications and requesting samples or visiting the factory to assess their capabilities and production standards. Communication and language barriers can also pose challenges, leading to misunderstandings and delays, so clear and effective communication channels should be established.
Several key players in China specialize in producing custom injection molds. Some prominent companies include Hanking Mould Engineering Ltd., which has over 15 years of experience and offers comprehensive mold making services. JM Mold Precision Technology Co., Ltd. is another established player, known for its high-quality and precise mold manufacturing. Sino Mold Tooling Co., Ltd. is recognized for its expertise in custom mold design and engineering. These companies have a solid track record and are trusted by many businesses worldwide.
In conclusion, sourcing custom injection molds from China can provide opportunities for cost savings and access to advanced manufacturing expertise. However, businesses should be aware of the associated risks and take necessary precautions to ensure product quality and effective communication. Selecting reputable suppliers, conducting proper due diligence, and establishing clear communication channels are crucial steps for successful sourcing from China.
How to find and select reliable custom injection mold manufacturers in China,use google search manufacturers and suppliers
When it comes to finding and selecting reliable custom injection mold manufacturers in China, utilizing Google search is one effective approach. To efficiently narrow down your options, follow these steps:
1. Identify relevant keywords: Use specific keywords such as “custom injection mold manufacturers in China” or “reliable injection mold suppliers in China” to generate relevant results.
2. Evaluate search results: Carefully review the search results and visit the websites of potential manufacturers. Look for information about their capabilities, experience, certifications, production processes, equipment, and customer feedback. Pay attention to companies that offer comprehensive and detailed information, as it reflects their professionalism and transparency.
3. Check the company’s credibility: Important factors to consider include the manufacturer’s track record, their years in business, and their reputation in the industry. Look for customer reviews, testimonials, case studies, or any other indicators of their reliability.
4. Verify their certifications: Check if the manufacturer holds any relevant certifications, such as ISO 9001:2015 for quality management systems or ISO 13485 for medical device manufacturing. This assures that they adhere to international standards and practices.
5. Communication channels: Assess their accessibility and responsiveness. Prompt and clear communication channels can help address your concerns and needs effectively.
6. Request for sample products: Ask for sample products to evaluate the quality, functionality, and durability of their injection molds. This will give you firsthand information and help you make a better decision.
7. Inquire about their manufacturing process: Learn about their design capabilities, prototyping processes, quality control measures, and customization options. Understanding their complete manufacturing process will help you assess their expertise and suitability for your project.
8. Pricing and negotiation: Collect quotes from multiple manufacturers and compare them. Keep in mind that the cheapest option may not always be the best. Evaluate the quotes in conjunction with their capabilities, quality, and track record. Negotiate terms and conditions, ensuring clarity on lead times, minimum order quantities, and payment methods.
9. Visit their facilities: If possible, schedule a visit to their manufacturing facilities. Personally observing their infrastructure, equipment, and production lines can provide valuable insights.
By employing these steps in your search for reliable custom injection mold manufacturers in China, you will increase your chances of finding a suitable partner who meets your requirements and delivers high-quality products.
How to check custom injection mold manufacturers website reliable,use google chrome SEOquake check if ranking in top 10M
When looking for a reliable custom injection mold manufacturers’ website, you can follow a few steps to ensure its credibility. One approach is to use Google Chrome’s SEOquake extension, which helps you assess the website’s ranking and other factors. Here is how you can proceed:
1. Install SEOquake: Open Google Chrome web browser and go to the Chrome Web Store. Search for “SEOquake” and click on the appropriate extension. Click “Add to Chrome” and follow the installation prompts.
2. Activate SEOquake: Once installed, you will notice a small SEOquake icon among your Chrome extensions. Click on it to activate the tool.
3. Set Parameters: After activation, you can choose the parameters you want to assess. To determine a reliable website, focus on the website ranking. For this, select the “Google Index” option under the “SEMRush” tab. It provides the website’s current ranking among the top 10 million websites.
4. Search: Now, enter the custom injection mold manufacturer’s website URL in the search bar or simply visit the website you want to evaluate.
5. Analyze the Ranking: After the website loads, SEOquake will display the Google Index ranking for that particular website. If the website ranks within the top 10 million, it indicates a reasonably well-established site.
It’s important to note that while SEOquake can help you assess a website’s ranking, it does not provide a full analysis of reliability or quality. Thus, consider other aspects as well, such as customer reviews, certifications, product information, company background, and contact details.
In summary, using Google Chrome’s SEOquake extension to check if a custom injection mold manufacturers’ website ranks within the top 10 million websites can be a helpful step to evaluate its reliability. However, it’s essential to consider other factors to ensure the credibility and suitability of the manufacturer for your specific requirements.
Top 10 custom injection mold manufacturers in China with each 160 words introduce products,then use markdown create table compare
1. ACO Mold
ACO Mold is a professional injection mold manufacturer in China, specializing in custom plastic injection molding. They offer a wide range of services including mold design, mold manufacturing, injection molding, prototype services, and more. With advanced equipment and highly skilled technicians, ACO Mold has the capability to deliver high-quality injection molds and molded products. Their portfolio includes automotive parts, electronic components, medical devices, and consumer products.
2. FOW Mold
FOW Mold is a leading injection mold manufacturer in China, providing custom design and manufacturing solutions. They have extensive experience in producing molds for various industries such as automotive, electronics, and household appliances. FOW Mold focuses on delivering precision molds with strict quality control measures. Their range of products includes plastic injection molds, die-casting molds, and injection molding services.
| Company | Products | Industry |
|———|———-|———-|
| ACO Mold | Plastic injection molds, prototype services, injection molding | Automotive, electronics, medical devices, consumer products |
| FOW Mold | Plastic injection molds, die-casting molds, injection molding | Automotive, electronics, household appliances |
3. Mingling Industrial Automation Technology
Mingling Industrial Automation Technology specializes in custom injection molds for various industries, including automotive, electronics, and home appliances. They offer a complete range of services from mold design to manufacturing and molding. Mingling Industrial Automation Technology focuses on providing cost-effective solutions without compromising on quality and timely delivery.
4. JasonMould Industrial Company
JasonMould Industrial Company specializes in plastic injection molding and mold manufacturing. They have an extensive range of products including precision molds, household molds, and automotive molds. With advanced equipment, a skilled team, and strict quality control, JasonMould Industrial Company ensures the production of high-quality injection molds and molded products.
5. SINCERE TECH Plastic Mold
SINCERE TECH Plastic Mold is a leading injection mold manufacturer in China, known for its expertise in the automotive industry. They offer custom injection molding services for automotive parts, including interior and exterior parts, electronics, and more. SINCERE TECH Plastic Mold focuses on delivering precision molds and molded products with excellent surface finishes.
6. Wintech Rapid Prototyping
Wintech Rapid Prototyping specializes in custom injection mold design and manufacturing. They offer a wide range of services including 3D printing, rapid prototyping, and mold manufacturing. Wintech Rapid Prototyping caters to various industries such as automotive, electronics, medical devices, and consumer products.
7. Deep Mould Co., Ltd.
Deep Mould Co., Ltd. is a reputable injection mold manufacturer in China, specializing in custom mold design and production. They offer a comprehensive range of services including mold making, injection molding, and rapid prototyping. Deep Mould Co., Ltd. serves industries such as automotive, electronics, and home appliances.
8. ACO Mold Technology Co., Ltd.
ACO Mold Technology Co., Ltd. is committed to providing high-quality injection molds and molded products. With advanced equipment and a skilled team, they offer a wide range of injection molding services. ACO Mold Technology Co., Ltd. caters to industries like automotive, electronics, medical devices, and consumer products.
9. Sun On Plastic Moulding Limited
Sun On Plastic Moulding Limited specializes in custom injection mold manufacturing for various industries, including automotive, electronics, and consumer products. They have a strong focus on quality control and use advanced technologies to deliver precision molds and molded products.
10. Ecomolding Co., Ltd.
Ecomolding Co., Ltd. is an experienced injection mold manufacturer in China. They offer a range of services including mold design, manufacturing, and injection molding. Ecomolding Co., Ltd. serves industries such as automotive, electronics, and household appliances, providing custom mold solutions with a high level of precision.
Background Research for custom injection mold manufacturers Companies in China, use qcc.com archive.org importyeti.com
When searching for custom injection mold manufacturers in China, several useful resources can provide background research on potential companies. These include qcc.com, archive.org, and importyeti.com.
QCC.com is a comprehensive business information database in China that provides information on company profiles, industry analysis, and credit reports. It is a valuable resource for conducting background checks on potential injection mold manufacturers. The platform allows users to access information such as company registration details, shareholding information, financial indicators, and legal records to ensure the credibility and reliability of the chosen manufacturers.
Archive.org is a website that allows users to access archived versions of web pages. This tool can be used to review previous iterations of a company’s website, enabling researchers to assess the manufacturer’s history, product offerings, and any changes in their business model. By analyzing archived web pages, potential customers can gain insights into a manufacturer’s capabilities, past projects, certifications, and partnerships, which can help in making informed decisions.
Importyeti.com is a platform specifically designed to provide information on import and export activities of companies. It allows users to search for specific suppliers and provides details such as shipment history, trade data, and contact information. By inputting the name of a custom injection mold manufacturer or related keywords, users can access information related to a company’s imports and exports, including which countries they trade with, the volume of trade, and the types of products they specialize in.
By utilizing these resources, potential customers can gather crucial information about custom injection mold manufacturers in China. Conducting background research on these platforms can help verify a manufacturer’s reliability, track record, and capabilities, aiding in the decision-making process.
Leveraging Trade Shows and Expos for custom injection mold Sourcing in China
Trade shows and expos are excellent opportunities for businesses seeking custom injection mold sourcing in China. These events provide a platform for direct interaction with numerous suppliers, allowing companies to gather information, compare offerings, and establish potential partnerships.
Attending trade shows in China dedicated to the plastics and manufacturing industry offers several advantages. Firstly, it provides a chance to meet suppliers face-to-face and build personal relationships, which is crucial for effective communication and problem-solving. It also allows for a hands-on examination of product samples, ensuring quality and suitability for specific project requirements.
Trade shows and expos facilitate networking opportunities, enabling businesses to connect with multiple suppliers at once. This can significantly reduce the time and effort required to identify suitable partners. Moreover, these events offer valuable market insights, showcasing the latest trends, technologies, and best practices in the industry.
To make the most out of trade shows and expos, businesses can follow certain strategies. They should thoroughly research and shortlist potential suppliers based on their specialization, experience, and reliability. Prioritizing suppliers with proven track records and positive customer feedback can minimize risks and improve the likelihood of successful partnerships.
During trade shows, companies should engage in detailed discussions with suppliers to understand their capabilities, production processes, and quality control measures. It is essential to inquire about certifications, ensure transparency in pricing and payment terms, and clarify intellectual property protection measures.
Additionally, companies should seize the opportunity to seek referrals or testimonials from existing clients of potential suppliers. This can provide valuable insights into their performance and customer satisfaction levels.
Finally, businesses must be prepared to negotiate contracts and agreements on-site to capitalize on potential discounts or special offers. It is important to establish clear expectations regarding product specifications, lead times, and quality standards to avoid misunderstandings in the future.
In summary, trade shows and expos are invaluable platforms for businesses seeking custom injection mold sourcing in China. They offer direct interaction with multiple suppliers, networking opportunities, and market insights. By adequately preparing, businesses can maximize the value derived from these events and establish successful partnerships with reliable Chinese suppliers.
The Role of Agents and Sourcing Companies in Facilitating custom injection mold Purchases from China
Agents and sourcing companies play a crucial role in facilitating custom injection mold purchases from China. These entities act as intermediaries between the buyer and the manufacturer, providing expertise, guidance, and support throughout the purchasing process.
One of the key roles of agents and sourcing companies is to identify suitable manufacturers that can meet the specific requirements of the buyer. They have a comprehensive network of suppliers and extensive knowledge of the Chinese market, enabling them to find reliable and reputable mold manufacturers. This saves buyers time and effort in searching for suitable suppliers themselves.
Agents and sourcing companies also help buyers with the negotiation and communication process. They have a deep understanding of the Chinese business culture and are skilled in negotiating favorable terms and prices on behalf of the buyer. They act as a bridge between the buyer and the manufacturer, translating any language barriers and ensuring clear communication of requirements and expectations.
Moreover, these entities provide quality control services to ensure that the manufactured molds meet the buyer’s specifications and standards. They conduct regular factory inspections, monitor the production processes, and perform quality checks on the finished products. This helps to minimize the risk of product defects and ensures that the buyer receives high-quality molds.
Additionally, agents and sourcing companies handle logistics and shipping arrangements, making the purchasing process more convenient for the buyer. They coordinate the transportation of the molds from the manufacturer’s facility in China to the buyer’s location, handling all the necessary paperwork and customs procedures. This ensures a smooth and efficient delivery of the products.
Overall, agents and sourcing companies play a vital role in facilitating custom injection mold purchases from China. They provide valuable expertise, streamline the purchasing process, ensure quality control, and handle logistics. Their involvement helps buyers navigate the complexities of sourcing from overseas and enhances the overall purchasing experience.
Price Cost Research for custom injection mold manufacturers Companies in China, use temu.com and 1688.com
When conducting price cost research for custom injection mold manufacturers in China, two popular platforms to explore are temu.com and 1688.com. These platforms provide valuable insights into the pricing and offerings of various manufacturers.
Temu.com is a sourcing platform specifically designed for buyers seeking custom manufacturing services. It offers a user-friendly interface that allows users to connect with suppliers and obtain competitive quotes. By utilizing temu.com, one can easily navigate through a vast network of injection mold manufacturers in China and compare prices, quality, and production capabilities. This platform also provides tools for collaboration and efficient communication with suppliers to ensure a smooth purchasing process.
Another widely used platform is 1688.com, which is a subsidiary of Alibaba Group. 1688.com is primarily targeting domestic Chinese buyers, but it is also accessible to international users. With an extensive supplier database, it enables users to search for custom injection mold manufacturers and evaluate their prices, manufacturing capabilities, and product quality. While the platform is in Chinese, online translation tools can help non-Chinese speakers navigate the website and understand the information provided.
To maximize the effectiveness of price cost research, it is crucial to consider various factors. These include product specifications, mold complexity, material requirements, lead times, and any additional services needed. It is advisable to request detailed quotes and engage in direct communication with prospective manufacturers to ensure accurate pricing information that aligns with your specific requirements.
In summary, temu.com and 1688.com are valuable platforms for conducting price cost research on custom injection mold manufacturers in China. By utilizing these platforms and communicating directly with suppliers, one can effectively evaluate pricing, quality, and capabilities to make an informed decision.
Shipping Cost for custom injection mold import from China
The shipping cost for importing a custom injection mold from China can vary depending on several factors. These factors include the size and weight of the mold, the shipping method chosen, the distance between China and the destination country, and any additional services required.
One common shipping method for large and heavy items like injection molds is sea freight. Sea freight offers a cost-effective option, especially for large shipments. The cost is usually calculated based on the volume or weight of the mold and the distance it needs to travel. It is important to note that sea freight can take longer compared to air freight, with shipping times ranging from a few weeks to several months.
Air freight is a faster but more expensive shipping option. It is suitable for smaller and lightweight molds or when time is of the essence. The cost is calculated based on the weight and dimensions of the mold and the distance it needs to be transported. Air freight can take anywhere from a few days to a couple of weeks for delivery.
In addition to the shipping method, other costs may come into play. These can include customs duties, fees for shipping documentation, insurance, and destination charges. It is essential to check the import regulations and requirements of the destination country to determine if any extra costs are applicable.
To get an accurate shipping cost estimate, it is recommended to contact shipping providers or freight forwarders. They can provide detailed quotes based on the specific requirements and dimensions of the custom injection mold, as well as the preferred shipping method. Comparing different quotes will help in finding the most cost-effective shipping solution within the desired budget.
Compare China and Other custom injection mold Markets: Products Quality and Price,Visible and Hidden Costs
China is one of the leading manufacturing hubs for custom injection molds, competing with other markets such as the United States, Germany, Japan, and South Korea. When comparing China to other markets, several factors need to be considered, including product quality and price, visible and hidden costs.
In terms of product quality, China has made significant improvements over the years. Chinese manufacturers have invested in advanced technology and enhanced their quality control systems to ensure the production of high-quality molds. However, other markets like Germany, Japan, and the United States still hold a reputation for superior precision and craftsmanship in their products. While China’s quality has improved, it may still lag behind these markets in terms of intricate designs and complex molds.
When it comes to pricing, China offers a competitive advantage. The cost of production in China is generally lower compared to other markets due to lower wages and overhead expenses. This cost advantage makes China an attractive option for businesses looking for cost-effective custom injection molds. However, it is important to note that pricing can vary within China itself, with some manufacturers offering low prices but potentially compromising on quality.
In terms of visible costs, China may have an edge over other markets as it benefits from economies of scale. The vast manufacturing infrastructure in China allows for efficient production processes, resulting in cost savings that can be passed on to customers. Additionally, the abundance of materials and suppliers in China provides a wider range of options and lower material costs.
However, hidden costs in China cannot be overlooked. One such cost is the potential distance and logistical challenges faced when working with Chinese manufacturers, especially for customers located outside of Asia. Long shipping times, language barriers, and cultural differences can impact communication and lead to delays or misunderstandings. Moreover, intellectual property concerns and the need for stricter quality control measures may result in additional costs for customers.
In conclusion, China’s custom injection mold market offers a balance between product quality and price. While China has made significant strides in improving product quality, it may still lag behind other markets known for superior craftsmanship. However, China’s cost advantage, economies of scale, and diverse supplier network make it a competitive option. It is crucial for businesses to consider both visible and hidden costs when choosing between China and other custom injection mold markets.
Understanding Pricing and Payment Terms for custom injection mold: A Comparative Guide to Get the Best Deal
When it comes to getting custom injection molds, understanding pricing and payment terms is essential to ensure that you get the best deal possible. This comparative guide aims to provide an overview of the factors that influence pricing and payment terms for injection molds, helping you make informed decisions.
Firstly, it is important to consider the complexity and size of the mold. Larger and more intricate molds require higher manufacturing costs and materials, leading to higher prices. The number of cavities in the mold also affects the price, as more cavities increase production capacity but also raise costs.
Material selection is another crucial factor. Different materials have varying costs, with high-performance polymers being more expensive than traditional plastics. The choice of material depends on the requirements of the final product and can impact the mold price.
The lead time for mold production also influences pricing. Urgent orders often incur additional fees due to expedited manufacturing processes. Planning ahead and allowing for a longer lead time can help reduce costs.
Additionally, the choice of manufacturer plays a significant role in pricing. Different manufacturers have varying overheads, labor costs, and quality standards. Researching and obtaining quotes from multiple manufacturers allows for a better understanding of the market prices and helps negotiate competitive prices.
Payment terms can differ between manufacturers, and understanding them is crucial. Some manufacturers require a deposit upfront, with the balance payable upon completion, while others may offer installment plans. It is important to clarify the payment terms and ensure they align with your financial capabilities.
Negotiating is key to obtaining the best deal. Comparing prices, asking for discounts, and discussing alternative payment arrangements can potentially reduce costs. Building a long-term relationship with the manufacturer can also lead to more favorable pricing and payment terms in the future.
In conclusion, understanding the factors influencing pricing and payment terms for custom injection molds allows for informed decision-making when seeking the best deal. Considering factors such as mold complexity, material selection, lead time, manufacturer choice, and negotiating effectively can help achieve cost-effective solutions while maintaining quality.
Chinese Regulations and Industry Standards Certifications for custom injection mold,Import Regulations and Customs for custom injection mold from China
Chinese Regulations and Industry Standards Certifications for Custom Injection Mold
China has several regulations and industry standards certifications for custom injection mold manufacturing to ensure product quality and safety. Here are some of the important ones:
1. GB/T 14486-2016: This is the national standard for the design and manufacture of plastic injection molds in China. It covers various aspects including mold materials, dimensional tolerances, surface treatment, and quality inspection requirements.
2. ISO 9001: This is an international standard for quality management systems. Many injection mold manufacturers in China obtain this certification to demonstrate their commitment to producing high-quality products.
3. ISO 14001: This certification focuses on environmental management systems, ensuring that manufacturers comply with environmental regulations and minimize their impact on the environment during the production process.
4. ISO/TS 16949: Particularly important for automotive industry customers, this certification addresses quality management systems specific to the automotive sector. It ensures that manufacturers meet the strict quality requirements for producing injection molds used in automotive parts.
5. RoHS: Restriction of Hazardous Substances Directive, commonly known as RoHS, restricts the use of certain hazardous substances in electrical and electronic equipment. Injection mold manufacturers in China need to comply with the RoHS directive if the molds are used in such products.
Import Regulations and Customs for Custom Injection Mold from China
When importing custom injection molds from China, it is essential to comply with import regulations and go through the customs process smoothly. Here are some key points to consider:
1. Import Duties: Importing custom injection molds may attract import duties or tariffs. Importers should be aware of the specific rates applicable in their country and factor in these costs while planning the purchase.
2. Customs Documentation: Proper documentation is necessary for smooth customs clearance. This typically includes a commercial invoice, packing list, bill of lading or airway bill, and any required certifications or licenses.
3. Customs Valuation: The customs value of the injection molds is determined based on various factors such as the transaction value, adjustments for certain expenses, and any applicable royalties or license fees. Importers should ensure accurate valuation for customs purposes.
4. Customs Duties and Taxes: Apart from import duties, importers may be subject to other customs fees, taxes, or VAT (Value Added Tax), depending on the regulations of their country. It is crucial to understand these additional costs to avoid surprises.
5. Customs Broker: Working with a licensed customs broker can simplify the customs clearance process. They can assist with documentation, compliance, and ensure that all customs requirements are met.
In summary, understanding Chinese regulations and industry standards certifications for custom injection molds, as well as complying with import regulations and customs procedures, is crucial for a successful and hassle-free import process from China.
Sustainability and Environmental Considerations in custom injection mold Manufacturing
Sustainability and environmental considerations are becoming increasingly important in the manufacturing industry, including custom injection mold manufacturing. Companies are recognizing the need to reduce their environmental impact and adopt sustainable practices to ensure long-term success. Here are some key considerations in this regard.
Material Selection: Choosing the right materials for custom injection molds is crucial. Opting for recycled or biodegradable materials can help reduce the overall carbon footprint of the manufacturing process. Additionally, using materials with longer lifespan and durability can minimize the need for frequent replacements, thereby reducing waste generation.
Energy Efficiency: Custom injection mold manufacturing often involves the use of energy-intensive machinery. Implementing energy-efficient equipment, such as high-performance mold machines and energy-saving technologies, can significantly reduce energy consumption and associated greenhouse gas emissions. Regular maintenance and optimizing production processes also play a vital role in maximizing energy efficiency.
Waste Reduction and Recycling: Minimizing waste generation and promoting recycling are essential in sustainable manufacturing. Companies can implement recycling programs to handle plastics and other waste materials generated during the injection molding process. Furthermore, implementing waste-reducing practices like optimizing the mold design to reduce scrap and reusing excess materials can help in reducing environmental impact and cutting costs.
Water Conservation: Water is a valuable resource, and conserving it is crucial in sustainable manufacturing. Implementing water management systems and using closed-loop cooling systems can significantly reduce water consumption. Additionally, adopting effective water treatment and filtration methods can prevent pollution and ensure responsible water discharge.
Carbon Footprint Reduction: Manufacturing processes can contribute to carbon emissions. Implementing carbon reduction strategies such as using renewable energy sources, optimizing transportation logistics, and adopting energy-efficient practices can help reduce the carbon footprint of custom injection mold manufacturing.
Overall, integrating sustainability and environmental considerations into custom injection mold manufacturing can lead to benefits such as cost savings, improved brand reputation, and a healthier planet. By making conscious choices regarding material selection, energy efficiency, waste reduction, water conservation, and carbon footprint reduction, manufacturers can contribute to a greener and more sustainable future.
List The Evolution history of “custom injection mold”
The evolution of custom injection mold can be traced back to the late 19th century when the first injection molding machine was patented by John Wesley Hyatt. Initially, these machines used a plunger to inject material into a mold cavity, but they were limited in terms of precision and efficiency.
In the early 20th century, the injection molding process gained popularity as advancements were made in machine design and material development. The introduction of hydraulic systems allowed for better control of the injection process, resulting in more consistent and accurate parts.
During the mid-20th century, the development of thermoplastics and the advent of automated injection molding machines revolutionized the industry. These machines featured screw systems that replaced the plunger, providing more uniform and controlled material distribution. The use of thermoplastics also expanded the possibilities for diverse applications and product designs.
In the 1970s and 1980s, computerized numerical control (CNC) technology was integrated into injection molding machines, enabling precise control of variables such as injection speed, pressure, and temperature. This advancement led to improved part quality, reduced waste, and increased production efficiency.
The 1990s saw the emergence of computer-aided design (CAD) and computer-aided manufacturing (CAM) software, which further enhanced the customization and complexity of injection molds. This software allowed for rapid prototyping and simulation, enabling manufacturers to test and refine their molds before production.
In recent years, the evolution of custom injection mold has been driven by advancements in robotics, automation, and 3D printing technologies. Robotics have made it possible to automate repetitive tasks, streamline production, and improve precision. 3D printing, or additive manufacturing, has expanded the possibilities for rapid mold prototyping and low-volume production, reducing lead times and costs.
Today, custom injection molds are essential in various industries, including automotive, medical, consumer goods, and electronics. Continuous advancements in materials, machine technology, and software continue to push the limits of customization, precision, and efficiency in the injection molding process.
The Evolution and Market Trends in custom injection mold Industry
The custom injection mold industry has witnessed significant evolution and market trends over the years. Injection molding is a manufacturing process that involves injecting molten material into a mold to produce precise and intricate parts or products. This process has gained immense popularity due to its cost-effectiveness, efficiency, and ability to produce complex geometries.
One of the key trends in the custom injection mold industry is the adoption of advanced technologies. With the advent of computer-aided design (CAD) and computer-aided manufacturing (CAM), manufacturers are able to design and produce highly complex molds with improved accuracy and efficiency. This has resulted in reduced lead times and enhanced overall quality.
Another significant trend in the industry is the increased demand for sustainability. Manufacturers are now focusing on using eco-friendly materials and processes to reduce their environmental footprint. This includes the use of biodegradable or recyclable materials and the implementation of energy-efficient manufacturing practices.
Furthermore, the custom injection mold market has experienced a shift towards smaller batch sizes and higher product customization. As consumers demand more personalized and unique products, manufacturers are adapting their processes to accommodate this trend. This has led to the development of technologies such as rapid prototyping and 3D printing, which allow for faster and more cost-effective production of custom molds.
In terms of market dynamics, the custom injection mold industry is witnessing a steady growth due to the expanding automotive, packaging, and medical sectors. These industries require high-quality molds to meet the increasing demand for their products. Additionally, the rise of e-commerce has resulted in an increased need for packaging solutions, boosting the demand for custom injection molds.
In summary, the custom injection mold industry has evolved to embrace advanced technologies, sustainability, smaller batch sizes, and customization. These trends have been driven by the need for faster production, improved product quality, and reduced environmental impact. With the continued growth of key industries and the rise of e-commerce, the custom injection mold market is expected to expand further in the coming years.
Custom Private Labeling and Branding Opportunities with Chinese custom injection mold Manufacturers
Chinese custom injection mold manufacturers offer excellent opportunities for custom private labeling and branding. With their vast experience, cutting-edge technology, and competitive pricing, these manufacturers provide businesses with the ability to create unique and high-quality products tailored to their specific requirements.
The process of custom private labeling and branding begins with collaborating closely with the manufacturer to understand the customer’s vision and specifications. Chinese manufacturers utilize advanced injection molding techniques to transform these ideas into tangible products, ensuring precise dimensions and intricate details.
One of the key advantages of working with Chinese manufacturers is their ability to offer cost-effective solutions without compromising on quality. These manufacturers leverage economies of scale, advanced machinery, and skilled labor to deliver products at competitive prices. This allows businesses to benefit from higher profit margins while maintaining a competitive edge in the market.
Furthermore, Chinese custom injection mold manufacturers offer customization options in terms of colors, materials, designs, and finishes. This level of customization enables businesses to create products that align with their brand image and appeal to their target market. Manufacturers can even emboss logos or brand names onto the products, ensuring brand visibility and enhancing brand recognition.
Additionally, Chinese manufacturers comply with international quality standards such as ISO 9001, ensuring consistent quality control throughout the manufacturing process. This ensures that the final products meet the highest standards and are of exceptional quality.
By collaborating with a Chinese custom injection mold manufacturer, businesses can benefit from a streamlined production process, enhanced product quality, competitive pricing, and the ability to create unique and branded products. These opportunities enable businesses to differentiate themselves in the market, attract new customers, and build a strong brand presence.
In conclusion, Chinese custom injection mold manufacturers offer excellent opportunities for businesses looking to leverage custom private labeling and branding. From concept to production, these manufacturers provide the necessary expertise, technology, and cost-effective solutions to help businesses create unique and high-quality products.
Tips for Procurement and Considerations when Purchasing custom injection mold
When purchasing a custom injection mold, there are several important considerations to keep in mind to ensure a successful procurement process. Here are some essential tips and factors to consider:
1. Define your requirements: Clearly articulate your specific needs and requirements for the custom injection mold. Consider factors such as size, shape, material, complexity, and desired production quantity.
2. Choose a reputable supplier: Research and identify reliable suppliers who specialize in custom injection molds. Look for their experience, expertise, and reputation in the market. Check if they have a proven track record of delivering quality molds on time.
3. Quality assurance: Ensure that the supplier has a robust quality control process in place. Inquire about material testing, dimensional accuracy, and mold durability. Request samples or visit their facility to assess the quality of their work and inspect their manufacturing equipment.
4. Cost and value: Obtain detailed quotes from multiple suppliers to compare costs and value. Consider not only the initial purchase price but also factors such as delivery time, ongoing maintenance costs, and warranty terms. Look for a balance between quality and cost-effectiveness.
5. Compatibility and adaptability: Confirm that the injection mold will work seamlessly with your existing manufacturing processes and machinery. Discuss any necessary modifications or adjustments to ensure compatibility and avoid costly production delays.
6. Communication and collaboration: Establish a strong communication channel with the supplier. Regular and effective communication is crucial throughout the procurement process to clarify requirements, address concerns, and ensure timely updates.
7. Intellectual property protection: Discuss intellectual property rights and confidentiality agreements with the supplier, especially if you require unique or proprietary designs. Ensure that your designs and information are adequately protected.
8. Maintenance and support: Inquire about after-sales services, maintenance, and technical support provided by the supplier. A reliable supplier should offer assistance in case of any issues with the mold or if modifications are needed.
9. Delivery timeline: Confirm the lead time required for the production and delivery of the custom injection mold. Discuss any considerations for expedited delivery or flexibility in the schedule.
10. Consider long-term partnerships: If you anticipate requiring future molds or modifications, consider building a long-term relationship with the supplier. A trusted partnership can lead to better pricing, priority support, and a more seamless procurement process.
By following these tips and considering the key factors involved in the procurement of a custom injection mold, you can ensure a successful purchase that meets your specific requirements and delivers long-term value.
FAQs on Sourcing and Manufacturing custom injection mold in China
1. Why should I source custom injection molds from China?
China is known for its competitive manufacturing industry, particularly in the field of injection mold production. Chinese manufacturers offer cost-effective solutions, high-quality products, and quick turnaround times. By sourcing injection molds from China, you can benefit from competitive pricing and access to advanced manufacturing technology.
2. How can I find a reliable injection mold manufacturer in China?
Finding a reliable manufacturer in China requires thorough research and due diligence. You can start by searching online directories, attending trade shows, or leveraging professional networks. It is crucial to verify the manufacturer’s experience, certifications, and customer reviews before proceeding with any orders.
3. Is it possible to customize injection molds to my specific requirements?
Yes, Chinese manufacturers are experienced in providing customized injection molds based on clients’ specific requirements. They can work closely with you to understand your product design, materials, dimensions, and any other specifications needed for the mold production.
4. What is the typical turnaround time for manufacturing injection molds in China?
The manufacturing time for injection molds in China varies depending on the complexity and size of the molds. However, on average, it can take around 4 to 8 weeks from the initial design and prototyping stage to the final production of the injection molds.
5. What are the quality standards of injection molds manufactured in China?
Chinese manufacturers adhere to international quality standards, such as ISO 9001, to ensure the production of high-quality injection molds. Reputable manufacturers also conduct quality control inspections at every stage of the manufacturing process to maintain consistency and accuracy.
6. Can I visit the manufacturer’s facility in China before placing an order?
Yes, it is possible to visit the manufacturer’s facility in China before placing an order. It is often recommended to establish a direct relationship with the manufacturer and assess their capabilities, production processes, and quality control measures personally.
7. Are there any risks associated with sourcing injection molds from China?
There are inherent risks associated with any offshore manufacturing, including language barriers, intellectual property protection, and potential communication issues. It is crucial to address these concerns by working with reputable manufacturers, utilizing legal contracts, and protecting your intellectual property rights through patents and non-disclosure agreements.
In conclusion, sourcing custom injection molds from China provides cost-effective solutions, access to advanced technology, and competitive pricing. However, it is essential to conduct thorough research, select a reliable manufacturer, and address any potential risks before initiating the manufacturing process.
Why contact sourcifychina.com get free quota from reliable custom injection mold suppliers?
Sourcifychina.com offers a free quota from reliable custom injection mold suppliers for a few reasons. Firstly, by partnering with these suppliers, Sourcifychina.com can provide a reliable and trustworthy sourcing solution to its customers. These suppliers have a proven track record of delivering high-quality custom injection molds, ensuring that customers receive products that meet their specifications and standards.
Secondly, offering a free quota allows Sourcifychina.com to attract potential customers who may be hesitant to invest in sourcing services. By eliminating the upfront cost of obtaining a quota, customers can explore the services provided by Sourcifychina.com without any financial commitment, making it more accessible and risk-free.
Furthermore, the free quota helps Sourcifychina.com build relationships with customers and gain their trust. By showcasing the expertise and reliability of its network of custom injection mold suppliers, Sourcifychina.com can demonstrate that it is committed to delivering exceptional sourcing services to its clients.
Lastly, by providing a free quota, Sourcifychina.com can better understand its customers’ requirements and tailor its solutions accordingly. This initial consultation enables Sourcifychina.com to gather vital information about the project scope, specifications, and budget, allowing them to provide an accurate quotation and ensure customer satisfaction.
In summary, offering a free quota from reliable custom injection mold suppliers benefits Sourcifychina.com by providing customers with a trustworthy sourcing solution, attracting potential customers, building relationships, and capturing essential project details for an accurate quotation.