Introduce about custom injection molders guide,Qulity,Cost,Supplier,Certification,Market,Tips,FAQ
The Custom Injection Molders Guide is a comprehensive resource that provides information and guidance on various aspects related to injection molding. It covers topics such as quality, cost, suppliers, certification, market trends, tips, frequently asked questions (FAQ), and more.
Quality is a crucial factor when it comes to injection molding. The guide emphasizes the importance of selecting a reputable and experienced injection molder with a proven track record of delivering high-quality products. It highlights the key factors to consider while evaluating the quality of the molder’s work, such as their quality control processes, adherence to industry standards, and utilization of advanced technologies.
Cost is another significant aspect discussed in the guide. It provides insights on how to effectively manage the costs associated with injection molding projects. This includes tips for optimizing the design for cost-effective manufacturing, selecting suitable materials, and working closely with the injection molder to identify cost-saving opportunities.
The guide offers guidance on finding reliable and reputable suppliers for injection molding projects. It outlines the criteria to evaluate potential suppliers based on their capabilities, experience, capacity, and more. It also emphasizes the importance of establishing strong partnerships with suppliers to ensure successful project outcomes.
Certification is an important consideration while choosing an injection molder. The guide explains the significance of certifications such as ISO 9001, ISO 13485, and IATF 16949 for ensuring compliance with quality management standards and industry-specific requirements.
Market trends and insights are provided to help readers stay updated with the latest developments in the injection molding industry. The guide highlights emerging technologies, materials, and market opportunities to provide a competitive advantage.
Tips and best practices are shared to assist readers in achieving better results in their injection molding projects. These include design considerations, material selection guidelines, process optimization techniques, and more.
The FAQ section addresses common queries and provides answers to help readers understand various aspects of custom injection molding.
In summary, the Custom Injection Molders Guide is a valuable resource that covers a wide range of topics related to injection molding. It provides insights, tips, and guidance to help readers make informed decisions and achieve successful outcomes in their injection molding projects.
Types of custom injection molders
There are several types of custom injection molders that cater to different industries and requirements. These include:
1. Prototype molders: These molders specialize in creating injection molds for prototyping purposes. They often work closely with product designers and engineers to quickly produce low-volume prototypes for testing and validation before mass production begins.
2. Short-run molders: Short-run molders typically focus on small to medium-sized production runs. They are well-equipped to handle batch orders and provide quick turnaround times. This type of molder is suitable for businesses that require flexibility in production quantities or frequently launch new products.
3. High-volume molders: High-volume molders specialize in large-scale production runs, typically in the hundreds of thousands or millions. They employ advanced technologies, such as automation and robotics, to optimize efficiency and productivity. These molders are ideal for industries like automotive, consumer electronics, and packaging.
4. Insert molders: Insert molders use a specialized process that involves placing pre-formed components or inserts into the mold before injecting molten plastic. This technique allows for the production of complex parts with precise positioning of inserts, reducing assembly steps and improving product reliability. Insert molders are commonly utilized in industries such as electronics, medical devices, and automotive.
5. Multi-shot molders: Multi-shot molders enable the production of parts with multiple materials or colors in a single mold. This process involves injecting successive layers of different materials or colors into the mold cavity to form a finished component. Multi-shot molding is often used in industries where aesthetics and material functionality are critical, such as consumer goods, electronics, and medical devices.
6. Micro molders: Micro molders specialize in producing extremely small, intricate plastic parts with micron-level tolerances. They utilize advanced micro molding technologies, including specialized machines and tooling, to achieve high precision. Micro molders cater to industries like medical devices, electronics, telecommunications, and aerospace.
Each type of custom injection molder serves different industries and requirements. Whether it’s for prototyping, short-run production, high-volume manufacturing, specialized processes, or micro molding, understanding the capabilities and specialties of different molders is crucial in choosing the right partner for a specific project.
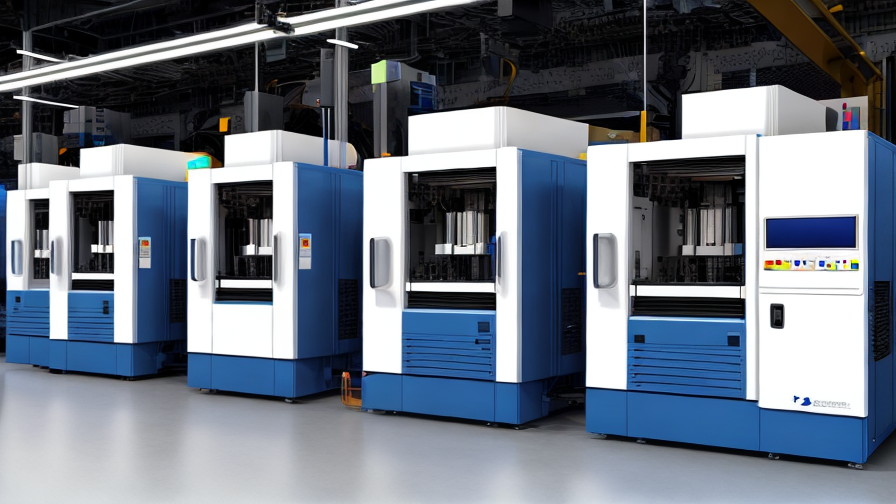
Pros and Cons of Using custom injection molders
Custom injection molding is a manufacturing process in which thermoplastic materials are injected into a mold to produce a wide range of plastic parts and products. When considering using custom injection molders for production, it is essential to weigh the pros and cons associated with this approach.
Pros of using custom injection molders:
1. Design flexibility: Custom injection molders offer significant design flexibility, allowing for complex or intricate part geometries that may not be feasible with other manufacturing processes. This enables businesses to create unique, customized products that meet specific requirements and market demands.
2. Cost-effective for large volumes: Injection molding is most cost-effective for large production volumes. With custom injection molders, businesses can produce a large quantity of identical parts within a shorter timeframe, leading to economies of scale and reduced unit costs.
3. High precision and accuracy: Injection molding processes ensure excellent precision and accuracy, making it suitable for manufacturing small, intricate components. This results in high-quality, reliable products that meet tight tolerances consistently.
4. Materials and surface finishes: Injection molding allows for a wide range of materials to be used, including various resins, elastomers, and thermoplastics. Additionally, custom injection molders can create parts with different surface finishes, such as smooth, textured, or glossy, providing versatility in the final product.
Cons of using custom injection molders:
1. Higher initial investment: Setting up custom injection molding requires substantial initial investment due to the cost of molds, machinery, and tooling. This could be a disadvantage for small businesses or projects with limited budgets.
2. Long lead times: The design and production of molds in custom injection molding can take time, leading to longer lead times compared to other manufacturing processes. This may not be suitable for time-sensitive projects or rapidly changing market demands.
3. Limited design modifications: Once the molds are created, making design modifications becomes challenging and costly. This lack of flexibility can be a drawback if a product requires frequent design changes or customization.
4. Waste generation: Injection molding produces waste material, known as sprues or runners, during the manufacturing process. Proper waste management and recycling processes need to be in place to minimize environmental impact and associated costs.
In conclusion, custom injection molding offers design flexibility, cost-effectiveness for large volumes, high precision, and material versatility. However, the process requires a significant initial investment, has longer lead times, limited design modifications, and generates waste. It is crucial for businesses to carefully evaluate these aspects and consider their specific production requirements before opting for custom injection molders.
custom injection molders Reference Specifications (varies for different product)
Custom injection molders specialize in manufacturing plastic parts through the injection molding process, providing end-to-end solutions for various industries. These molders are equipped with state-of-the-art facilities and advanced machinery to deliver high-quality, precise, and cost-efficient plastic parts.
Reference specifications may vary depending on the specific product requirements. However, some common specifications include material type, part dimensions, wall thickness, insert type, surface finish, tolerances, and color. Each product requires different specifications to ensure its functionality, durability, and aesthetic appeal.
The material type for injection molding typically includes a wide range of thermoplastics, such as ABS, HDPE, LDPE, polycarbonate, polypropylene, and many more. Each material offers distinct characteristics, including strength, flexibility, heat resistance, chemical resistance, and transparency.
Part dimensions refer to the size and shape of the final product. These specifications play a crucial role in designing the mold and selecting the appropriate injection molding machine. Wall thickness is another essential consideration to ensure the part’s strength, stability, and proper filling during the injection molding process.
Insert type refers to the incorporation of various components, such as metals or other plastic parts, into the final product during the injection molding process. This technique allows for the creation of complex plastic parts with integrated functionality.
Surface finish requirements vary depending on the intended use and aesthetic appeal of the product. Common surface finishes include smooth, textured, glossy, matte, or a specific texture pattern.
Tolerances refer to the allowable deviations from the part’s specified dimensions. These specifications ensure the accuracy and consistency of the produced parts.
Color is a critical aspect for many plastic parts, and custom injection molders offer a wide range of color options. This allows for the creation of parts with specific branding or visual requirements.
In conclusion, custom injection molders require reference specifications for each product to ensure the manufacturing process meets the exact needs and requirements of their clients. These specifications encompass material type, part dimensions, wall thickness, insert type, surface finish, tolerances, and color. By adhering to these specifications, custom injection molders deliver high-quality plastic parts that fulfill the desired functionality, durability, and aesthetic aspects of the client’s product.
Applications of custom injection molders
Custom injection molders are essential in various industries and offer many applications for businesses looking to produce high-quality plastic parts. Here are some key applications of custom injection molders:
1. Automotive Industry: Custom injection molders play a vital role in the automotive industry by producing various plastic components such as interior and exterior trim, dashboard parts, door handles, and electrical connectors. The ability to create complex geometries with precision enables molders to meet the industry’s stringent requirements.
2. Medical Devices: The medical device industry relies heavily on custom injection molders for the production of components like syringes, surgical tools, inhalers, and implantable devices. Molders can ensure the production of parts that meet strict regulatory standards, are biocompatible, and maintain dimensional accuracy.
3. Consumer Goods: Custom injection molders produce a wide range of consumer goods, including electronics enclosures, toys, household items, and packaging. With the ability to create intricate designs, molders can meet the specific requirements of consumer goods manufacturers while ensuring consistent quality and durability.
4. Aerospace: The aerospace industry utilizes custom injection molders to produce lightweight and high-strength plastic components for aircraft interiors and exteriors. These include panels, brackets, ductwork, seating components, and cabin fixtures. Molders can provide parts that meet industry standards for flame retardancy, thermal stability, and resistance to vibration and impact.
5. Electronics: Custom injection molders contribute to the production of electronic devices such as connectors, housings, switches, and keypads. The precision and repeatability of injection molding allow for tight tolerances and integration of features like EMI shielding, snap-fit mechanisms, and circuit board mounting features.
6. Industrial Equipment: Industrial equipment manufacturers rely on custom injection molders to produce parts that withstand harsh environments, have excellent chemical resistance, and provide dimensional stability. These can include gears, seals, knobs, handles, and housings for machinery, pumps, and other industrial equipment.
7. Plumbing and Construction: Custom injection molders are used in the production of plumbing fittings, valves, pipe connectors, and construction-related components. The ability of molders to produce parts with high strength, corrosion resistance, and tight sealing ensures their suitability for plumbing and construction applications.
In conclusion, custom injection molders are widely utilized across various industries for producing high-quality plastic parts. The versatility and precision of injection molding allow manufacturers to meet specific requirements while ensuring consistent quality, durability, and functionality in a broad range of applications.
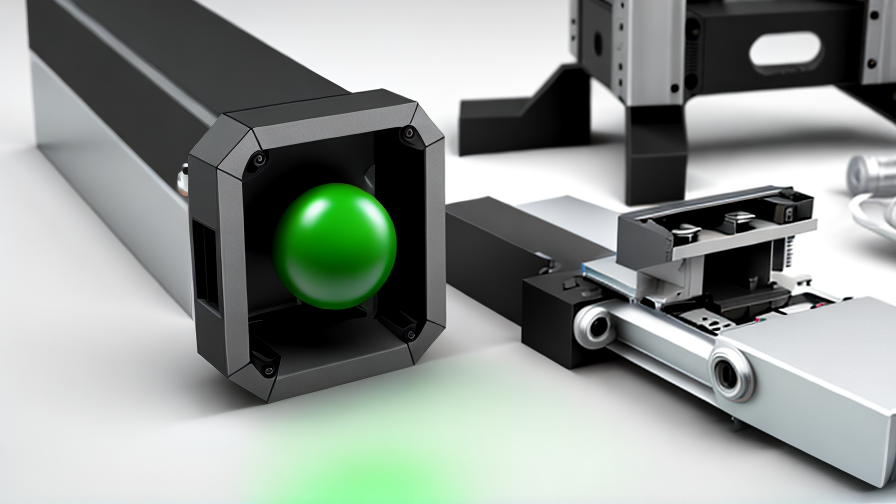
The Work Process and how to use custom injection molders
Custom injection molding is a manufacturing process used to produce large volumes of identical parts. It involves injecting molten plastic into a custom-designed mold or tooling to create high-quality and precise components. Understanding the work process and effectively utilizing custom injection molders can save time, costs, and effort. Here is how it works and how to use them efficiently.
The first step in the process is choosing the right material for the desired part. Different plastics have varying properties, such as durability, flexibility, and temperature resistance. Ensuring the material’s compatibility with the intended application is crucial.
Next, a custom mold is created based on the desired specifications. This mold is typically made from steel or aluminum and can be intricate and complex, depending on the part’s design. The mold is precision engineered to ensure that the injected plastic conforms to the desired shape and dimensions.
Once the mold is ready, the plastic material is melted and injected into the mold cavity under high pressure. The molten plastic fills the entire mold impression, taking the desired shape. Cooling takes place rapidly, solidifying the plastic.
After the plastic has solidified, the mold opens, and the part is ejected from the mold cavity. The final part may require additional post-processing steps, such as trimming excess material or adding surface finishes.
To effectively use custom injection molders, it is essential to communicate your requirements clearly to the molding company. This includes providing detailed design specifications, material selection, and expected quantities. Proper documentation helps avoid misunderstandings and ensures accurate production.
Regular communication with the molding company is also necessary throughout the process. It allows for updates, feedback, and addressing any concerns promptly. This collaboration helps identify potential design or production issues early, minimizing costly revisions or delays.
Working closely with the molding company can further optimize the production process. They can provide valuable insights on material selection, mold design, and process optimization, resulting in more cost-effective and efficient manufacturing.
In conclusion, custom injection molding is a versatile process used to mass-produce plastic parts. Understanding the work process and effectively using custom injection molders involve selecting the right material, designing a precise mold, and maintaining clear communication with the molding company. By embracing collaboration and regular communication, the production of high-quality custom parts can be achieved efficiently.
Quality Testing Methods for custom injection molders and how to control the quality
Quality testing methods for custom injection molders are essential to ensure that the products meet the required standards. Below are some commonly used quality testing methods for custom injection molders:
1. Visual Inspection: This method involves examining the products visually to detect any defects such as surface imperfections, dimensional inaccuracies, or color variations.
2. Dimensional Measurement: Precise measurement techniques, such as using calibrated gauges or coordinate measuring machines (CMM), are employed to ensure the accuracy of critical dimensions.
3. Functional Testing: Functional testing involves verifying the product’s performance by subjecting it to various usage scenarios. For example, an automotive component may undergo simulated wear and tear tests or performance tests under different temperature conditions.
4. Material Property Testing: It is crucial to test the material properties, such as tensile strength, impact resistance, and chemical resistance, to ensure that the material used for injection molding is suitable for the application.
5. Mold Flow Analysis: By using specialized software, mold flow analysis simulates the injection molding process to identify potential issues like air entrapment, weld lines, or insufficient filling. This analysis helps optimize the molding process before production.
6. Statistical Process Control (SPC): SPC involves continuously monitoring and controlling the production process using statistical methods to detect any variations and maintain consistency in quality. SPC can involve monitoring parameters such as temperature, time, pressure, or cycle time during injection molding.
To control the quality of custom injection molding, several measures can be implemented. These include:
1. Establishing Quality Standards: Clearly define the quality standards and specifications that the molded parts must meet. This ensures that expectations are communicated effectively to all stakeholders.
2. Documenting Processes: Documenting all aspects of the injection molding process, including parameters, materials, and tooling, enables repeatability and traceability. This documentation can help identify potential issues and ensure consistent quality.
3. Training and Skills Development: Providing comprehensive training to operators and quality control personnel is crucial to ensure that they have the required skills and knowledge to detect and address quality issues effectively.
4. Regular Maintenance and Calibration: Proper maintenance of machinery and regular calibration of measuring equipment are essential to ensure accurate and consistent results.
5. Continuous Improvement: Implementing a culture of continuous improvement encourages feedback, analysis of quality data, and the implementation of corrective actions to enhance the overall quality of the custom injection molding process.
By utilizing appropriate quality testing methods and implementing robust quality control measures, custom injection molders can ensure that their products meet the required quality standards consistently.
custom injection molders Sample Policy and Post-Purchase Considerations for custom injection molders from China
Sample Policy:
When purchasing custom injection molders from China, it is important to establish clear sample policies to ensure the quality of the product. The following sample policy can be considered:
1. Sample Approval: Before placing a full order, it is recommended to request samples from the manufacturer. These samples should accurately represent the final product and undergo rigorous testing and inspection to ensure they meet the required specifications.
2. Sample Cost: Manufacturers may charge for samples, including the product cost and shipping fees. It is important to clarify the sample cost with the supplier and negotiate potential refunds or discounts if a bulk order is later placed.
3. Sample Delivery Time: Discuss and agree upon the expected delivery time of the samples with the manufacturer. Timely arrival of samples allows for prompt evaluation and decision-making.
4. Sample Revisions: If the initial samples do not meet the desired specifications, it is essential to communicate the necessary revisions to the manufacturer. Clear instructions and effective communication can help achieve the desired results in subsequent samples.
Post-Purchase Considerations:
After the purchase of custom injection molders from China, some crucial considerations should be taken into account:
1. Inspection upon Arrival: Conduct a thorough inspection of the received products to ensure they match the approved samples and meet the required standards. Promptly report any discrepancies or quality issues to the manufacturer to seek appropriate resolutions.
2. Quality Assurance: Establish a quality assurance system to monitor the manufactured products consistently. This may include regular inspections, performance testing, and feedback communication with the manufacturer.
3. Communication: Maintain regular and open communication channels with the manufacturer to address any concerns promptly. Active engagement can help resolve potential issues, facilitate troubleshooting, and foster a healthy business relationship.
4. Warranty and Returns: Discuss and establish warranty terms with the manufacturer. Clarify the procedures for returns or replacements in the case of defective or substandard products.
5. Feedback and Evaluation: Provide feedback to the manufacturer about the overall experience, product quality, and service. This not only helps them improve their processes but also assists future buyers in making informed decisions.
It is crucial to review and customize these policies and considerations based on individual requirements and preferences.
Sourcing custom injection molders from China: Opportunities, Risks, and Key Players
Sourcing custom injection molders from China offers both opportunities and risks for businesses. China has emerged as a global manufacturing hub, providing cost-effective production solutions, including injection molding. The country’s vast industrial infrastructure, skilled workforce, and large-scale production capabilities make it an attractive destination for companies seeking custom injection molders.
Opportunities:
1. Cost-Effectiveness: China’s lower labor and production costs compared to Western countries allow for cost-effective manufacturing arrangements.
2. Wide Range of Materials: Chinese custom injection molders offer access to a wide range of materials, including traditional plastics, specialized polymers, and composites.
3. Scalability: With its massive production capacity, China can handle large orders, making it ideal for businesses requiring high-volume production.
4. Technological Advancements: Many Chinese custom injection molders utilize advanced machinery and technologies, ensuring precision, efficiency, and high-quality products.
5. Market Expertise: China has a well-established manufacturing ecosystem that provides expertise in various industries, enabling customized molders tailored to specific product requirements.
Risks:
1. Quality Control: Ensuring consistent quality can be challenging due to the sheer number of suppliers in China and potential differences in production standards.
2. Intellectual Property Protection: China’s reputation for lax intellectual property laws raises concerns about the risk of product replication or unauthorized use of patented designs.
3. Communication and Cultural Differences: Language barriers and cultural nuances may lead to misunderstandings, affecting timely communication, and project management.
4. Logistics and Shipping: Longer lead times and potential delays in shipping and transportation can pose challenges when sourcing from China.
Key Players:
1. Hutchinson Technology Inc.: A leading Chinese injection molder specializing in precision injection molding for various industries, including automotive, electronics, and medical devices.
2. Lee&Wong Plastic Products Co., Ltd.: This custom injection molder offers comprehensive manufacturing services involving mold design, production, and finishing for international clients.
3. Jet Mold Products Co., Ltd.: Specializing in high-quality tooling and injection molding, Jet Mold provides custom solutions for clients in industries like automotive, electronics, and consumer goods.
4. Tech Mold Inc.: Known for its advanced manufacturing techniques, Tech Mold offers design, engineering, and custom injection molding services to global clients.
In conclusion, sourcing custom injection molders from China provides significant opportunities in terms of cost-effectiveness, materials availability, scalability, and advanced technologies. However, businesses should remain cautious of risks related to quality control, intellectual property protection, communication barriers, and logistics challenges. Identifying and collaborating with reputable key players can help mitigate potential risks and ensure successful partnerships.
How to find and select reliable custom injection molders manufacturers in China,use google search manufacturers and suppliers
When looking for reliable custom injection molders manufacturers in China, one effective approach is to use Google search to find manufacturers and suppliers. Here is a step-by-step guide on how to do this:
1. Use relevant keywords: Start by using keywords such as “custom injection molders manufacturers in China” or “plastic injection molding companies in China.” This will help narrow down the search results to manufacturers that specifically specialize in injection molding.
2. Scan the search results: Go through the search results and look for reputable websites of manufacturers or suppliers. It is important to choose websites that appear professional, provide detailed information about their services, and have valid contact information.
3. Check certifications and quality standards: Once you have shortlisted a few manufacturers, dig deeper to see if they have any certifications or adhere to specific quality standards. ISO 9001 certification is a good indicator of a manufacturer’s commitment to quality.
4. Read customer reviews or testimonials: Look for customer reviews or testimonials on the manufacturer’s website or search for reviews on external platforms. This can provide insights into the manufacturer’s reliability, product quality, and customer satisfaction level.
5. Contact the manufacturer directly: After narrowing down your options to a few potential manufacturers, reach out to them directly. Ask for more information about their capabilities, production processes, lead times, and pricing. A reliable manufacturer will be prompt, transparent, and willing to answer all your queries.
6. Request samples or visit the factory: If possible, ask for product samples or visit the manufacturer’s factory to assess the quality of their work firsthand. This can help you make an informed decision about their reliability and suitability for your specific requirements.
Remember to exercise due diligence when selecting a manufacturer by verifying their credentials, conducting thorough research, and comparing multiple options. This process will assist you in finding a reliable custom injection molders manufacturer in China.
How to check custom injection molders manufacturers website reliable,use google chrome SEOquake check if ranking in top 10M
To check the reliability of a custom injection molders manufacturer’s website, you can follow these steps:
1. Use Google Chrome: Open the website in Google Chrome browser for a seamless experience with various helpful browser extensions.
2. Install SEOquake: SEOquake is a free browser extension available for Google Chrome. Install it from the Chrome Web Store and enable it for your browser.
3. Check the website’s ranking: Once SEOquake is installed, go to the manufacturer’s website and activate the SEOquake extension by clicking on its icon in your browser’s toolbar. It will display a sidebar with various SEO-related information.
4. Look for visibility scores: In the SEOquake sidebar, check the Alexa Rank score. If the website ranks within the top 10 million, it signifies a certain level of visibility and popularity.
5. Analyze backlinks: SEOquake also provides backlink data. Click on the “Backlinks” tab in the sidebar to see the number of backlinks pointing to the website. A higher number of quality backlinks suggests a reliable website.
6. Assess on-page optimization: SEOquake also provides an SEO Audit feature. Click on “Diagnosis” in the sidebar to get an overview of the website’s on-page optimization. Look for factors such as meta tags, page speed, and mobile optimization.
7. Read customer reviews and testimonials: Look for customer reviews or testimonials on the website to get an idea of the manufacturer’s reliability, customer satisfaction, and product quality.
8. Verify contact information: A reliable manufacturer will have proper contact information listed on their website. Check for a physical address, phone number, and email address. You can further verify their legitimacy by giving them a call or reaching out via email.
By following these steps and analyzing the information using SEOquake, you can gain valuable insights into the reliability and trustworthiness of the custom injection molders manufacturer’s website.
Top 10 custom injection molders manufacturers in China with each 160 words introduce products,then use markdown create table compare
**1. Longxiang Group Co., Ltd.** is a prominent custom injection molder manufacturer in China. With years of experience, they specialize in the production of high-quality plastic injection molds. Their product range includes household appliances, automotive parts, medical equipments, electronic products, and more. Longxiang Group is known for their advanced manufacturing processes and state-of-the-art machinery, ensuring precision and reliability in their products.
**2. Taizhou Huangyan JMT Mould Co., Ltd.** is renowned for their expertise in injection molding. They offer customized molds for various industries including automotive, home appliances, packaging, and more. JMT Mould is committed to providing excellent quality products and services with their highly skilled team and advanced manufacturing equipment.
**3. Sino Mould Co., Ltd.** is a leading injection molder manufacturer in China. They specialize in producing custom injection molds for industries such as automotive, packaging, household appliances, and more. Sino Mould offers comprehensive solutions, from mold design and manufacturing to product development and production.
**4. Focare Mold Co., Ltd.** is an established custom injection molder manufacturer in China. They provide high-quality injection molds for various industries including medical, electronics, automotive, and more. Focare Mold is known for their efficient production processes and attention to detail, ensuring the success of their clients’ projects.
**5. ENGEL Machinery (Changzhou) Co., Ltd.** is a trusted manufacturer of custom injection molds in China. They offer a wide range of solutions for different industries including automotive, packaging, telecommunications, and more. ENGEL Machinery is dedicated to providing innovative products with their advanced technology and expertise.
**6. Shenzhen RYD Technology Co., Ltd.** specializes in custom injection molds production for electronics, medical, and automotive industries. With their state-of-the-art facilities and highly skilled team, they deliver top-notch quality products and excellent customer service.
**7. Xiamen Better Silicone Rubber Co., Ltd.** is a leading custom injection molder manufacturer in China. They specialize in silicone injection molding for industries such as healthcare, automotive, and consumer electronics. Better Silicone Rubber offers high-quality products with precise tolerances and excellent material properties.
**8. Dongguan AE MOULD Products Co., Ltd.** is a well-known injection molder manufacturer in China. They provide custom molds for various industries including automotive, electronics, household appliances, and more. AE MOULD Products is committed to delivering high-quality products and efficient services to their clients.
**9. Ningbo Beilun Juxing Mould Co., Ltd.** offers customizable injection molds for industries such as automotive, packaging, and home appliances. With their advanced technology and stringent quality control, they ensure the production of reliable and durable molds.
**10. Shanghai Elue Industrial Co., Ltd.** is a trusted manufacturer of custom injection molds in China. They specialize in precision mold design and manufacturing for industries including automotive, medical, and electronics. Elue Industrial provides one-stop solutions, from initial concept design to final production, catering to the specific needs of their clients.
| Manufacturer | Industries Served | Specializations |
| ————————————– | ——————————————————– | —————————————- |
| Longxiang Group Co., Ltd. | Household appliances, automotive parts, medical equipment, electronic products, and more | Advanced manufacturing processes |
| Taizhou Huangyan JMT Mould Co., Ltd. | Automotive, home appliances, packaging, and more | Highly skilled team, advanced equipment |
| Sino Mould Co., Ltd. | Automotive, packaging, household appliances, and more | Comprehensive solutions |
| Focare Mold Co., Ltd. | Medical, electronics, automotive, and more | Efficient production processes |
| ENGEL Machinery (Changzhou) Co., Ltd. | Automotive, packaging, telecommunications, and more | Advanced technology and expertise |
| Shenzhen RYD Technology Co., Ltd. | Electronics, medical, and automotive industries | State-of-the-art facilities and expertise |
| Xiamen Better Silicone Rubber Co., Ltd. | Healthcare, automotive, and consumer electronics | High-quality silicone products |
| Dongguan AE MOULD Products Co., Ltd. | Automotive, electronics, household appliances, and more | High-quality custom molds |
| Ningbo Beilun Juxing Mould Co., Ltd. | Automotive, packaging, home appliances | Advanced technology and quality control |
| Shanghai Elue Industrial Co., Ltd. | Automotive, medical, electronics | Precision mold design and manufacturing |
These top 10 custom injection molders in China offer a wide range of services to cater to various industries. The table provides a quick comparison of their key industries served and specializations, highlighting their unique strengths.
Background Research for custom injection molders manufacturers Companies in China, use qcc.com archive.org importyeti.com
When it comes to sourcing custom injection molders manufacturers in China, several online platforms can provide valuable information and insights. Websites like qcc.com, archive.org, and importyeti.com are effective tools for conducting background research on these companies.
QCC.com is a comprehensive platform that focuses on providing business information on Chinese companies. It allows users to search for manufacturers by industry, location, and company name. The platform provides details such as company profiles, registration information, key personnel, financial reports, and contact information. This enables buyers to evaluate the credibility and legitimacy of potential injection molders manufacturers in China.
Archive.org is an online archive that allows users to access historical versions of websites. This can be helpful in understanding a manufacturer’s past performance, capabilities, quality control measures, and certifications. By analyzing a company’s website over a period of time, buyers can gain insights into their evolution, stability, and consistency.
Importyeti.com is a supplier sourcing platform that provides shipment data for import-export activities. It allows users to search for specific products or companies and gain access to shipment records, including supplier names, shipment dates, port of origin, and port of destination. This data can help buyers identify injection molders manufacturers in China that have a proven track record of successfully exporting their products.
It is important to note that these platforms should serve as starting points for research, and further due diligence is required by contacting the manufacturers directly. This can involve conducting factory audits, requesting product samples, and discussing specific requirements and expectations.
In conclusion, by utilizing platforms like qcc.com, archive.org, and importyeti.com, buyers can gather essential information about custom injection molders manufacturers in China. With the insights gained from these platforms, buyers can make informed decisions when selecting the right supplier for their injection molding needs.
Leveraging Trade Shows and Expos for custom injection molders Sourcing in China
Trade shows and expos provide an excellent platform for custom injection molders to source suppliers in China. These events offer a unique opportunity to meet multiple suppliers under one roof, giving businesses a chance to establish direct contacts and evaluate potential partnerships.
One key advantage of attending trade shows and expos in China is the ability to witness firsthand the capabilities and quality of different injection molding suppliers. Exhibitors often showcase samples of their products, allowing molders to assess the supplier’s expertise in terms of design, tooling, and manufacturing. This hands-on experience helps in making informed decisions about potential partnerships.
Furthermore, trade shows and expos provide a platform for networking and building relationships with suppliers. Face-to-face interactions enable better communication, fostering trust and credibility. These events also create a conducive environment for discussing specific project requirements, negotiating pricing terms, and understanding supplier capabilities in terms of production capacity and lead time.
To maximize the benefits of attending trade shows and expos, custom injection molders should come prepared. This includes conducting thorough research on the event and its exhibitors, making appointment arrangements with shortlisted suppliers in advance, and compiling a list of requirements and questions to ask potential partners. It is crucial to allocate sufficient time for thorough discussions and negotiations during the event.
In addition, custom injection molders can leverage social media platforms and online groups to connect with suppliers before and after the trade show. Engaging in industry-specific online communities can help in establishing contacts, gathering insights, and staying updated on the latest trends and technologies in injection molding.
In conclusion, trade shows and expos present an efficient and effective way for custom injection molders to source suppliers in China for their specific requirements. By leveraging such events, molders can evaluate potential suppliers, establish direct contacts, negotiate pricing terms, and build long-term partnerships based on trust and credibility.
The Role of Agents and Sourcing Companies in Facilitating custom injection molders Purchases from China
Agents and sourcing companies play a crucial role in facilitating custom injection molders’ purchases from China. These entities act as intermediaries between the buyer and the manufacturer, ensuring a smooth and efficient procurement process.
One of the primary responsibilities of agents and sourcing companies is to identify reputable and reliable injection molding manufacturers in China. They have extensive networks and knowledge of the local market, allowing them to connect buyers with suitable suppliers. These sources have expertise in conducting due diligence and quality assessments of potential manufacturers, ensuring that the buyer selects a reputable supplier capable of meeting their specific requirements.
Agents and sourcing companies also provide valuable assistance in negotiating pricing and contract terms. They have in-depth knowledge of the local industry landscape, including market trends and competitive pricing. Thus, they can negotiate favorable terms on behalf of the buyer, ensuring cost-effectiveness and value for money.
In addition to supplier selection and negotiation, agents and sourcing companies help facilitate communication and ensure effective coordination throughout the purchasing process. They act as intermediaries between the buyer and the supplier, bridging any language or cultural barriers and resolving any miscommunications or issues that may arise. This ensures a streamlined and efficient purchasing experience, minimizing delays and misunderstandings.
Moreover, agents and sourcing companies typically have a thorough understanding of import/export regulations, customs procedures, and logistics. They provide guidance and assistance in navigating these complexities, ensuring compliance with relevant laws and regulations. This expertise helps prevent potential pitfalls or delays in the shipping and delivery process.
Overall, agents and sourcing companies play a crucial role in facilitating custom injection molders’ purchases from China by identifying reputable suppliers, negotiating favorable terms, ensuring effective communication, and providing guidance on import/export regulations. Their expertise and services greatly simplify the procurement process, ultimately benefiting buyers by minimizing risks, enhancing efficiency, and optimizing value for money.
Price Cost Research for custom injection molders manufacturers Companies in China, use temu.com and 1688.com
When conducting price cost research for custom injection molders manufacturers in China, two popular platforms to utilize are temu.com and 1688.com. These platforms serve as online marketplaces that connect buyers with suppliers, enabling users to source products at competitive prices. By leveraging these platforms, one can obtain information on pricing and manufacturing capabilities of custom injection molders in China.
Temu.com is a leading platform for businesses seeking suppliers in China. It offers a wide range of products and services, including custom injection molding. By searching for custom injection molders on temu.com, users can access profiles of various manufacturers, along with their pricing details and manufacturing capabilities. The platform also provides contact information for direct communication with suppliers, enabling users to negotiate prices or request additional information.
Similarly, 1688.com is a popular wholesale marketplace in China that allows users to source products directly from manufacturers. It features a comprehensive directory of custom injection molders and offers insights into their prices and manufacturing capabilities. On 1688.com, users can browse through product listings, view supplier profiles, compare prices, and read customer reviews. The platform also facilitates communication between buyers and sellers, making it convenient for users to seek clarification or negotiate better pricing.
When conducting price cost research, it is essential to consider various factors, including the complexity of the injection mold, desired quantity, and the level of customization required. It is advisable to reach out to multiple suppliers to request quotes and assess their prices, production capabilities, quality control measures, and lead times. Thoroughly analyzing pricing, customer feedback, and the expertise of the manufacturers is crucial in making informed decisions and selecting the most suitable custom injection molder for your requirements.
In summary, temu.com and 1688.com are valuable platforms for price cost research when seeking custom injection molders in China. By utilizing these platforms, users can access a wide range of manufacturers, compare pricing, assess manufacturing capabilities, and initiate direct communication with suppliers. It is important to thoroughly evaluate these factors to ensure the selection of a reliable and cost-effective custom injection molder in China.
Shipping Cost for custom injection molders import from China
Shipping cost for importing custom injection molders from China can vary depending on various factors such as the size and weight of the molds, shipping method, distance, and any additional services required.
Generally, when importing from China, there are two main shipping methods: air freight and ocean freight. Air freight is a faster but more expensive option, while ocean freight is slower but more cost-effective.
For smaller custom injection molders weighing less than 150 kg, air freight is usually the preferred option. The cost can range from $2 to $5 per kilogram. However, this cost can increase if additional services like express shipping or customs clearance are required.
For larger custom injection molders weighing more than 150 kg, ocean freight is the more suitable option. The cost is calculated based on the volume or weight (whichever is higher) of the shipment, and the distance traveled. It can range from $1,000 to $5,000 for a full container load (FCL). However, if the molds are small and can be shipped as less than container load (LCL), the cost can be lower, usually around $100 to $500 per cubic meter.
In addition to the shipping cost, other expenses need to be considered. These may include export fees, customs duties, import taxes, port fees, and any additional services such as insurance or packaging. These charges can vary depending on the specific details of the shipment and should be factored into the total shipping cost.
To get an accurate estimate, it is recommended to reach out to shipping agents or freight forwarders who can provide specific quotations based on the details of your shipment. They can also assist with handling all the necessary paperwork and logistics to ensure a smooth import process.
Compare China and Other custom injection molders Markets: Products Quality and Price,Visible and Hidden Costs
China:
China is known for its vast manufacturing capabilities and has a reputation for producing products at a lower cost compared to other countries. The custom injection molding market in China is no exception. Chinese molders offer a wide range of products, from simple to complex parts, to cater to the needs of various industries.
In terms of product quality, Chinese molders have made significant improvements over the years. Many companies have invested in advanced technology and equipment, enabling them to produce high-quality molds. However, there are still concerns regarding consistency and precision, which can sometimes affect the final product quality.
Price is one of the key advantages of the Chinese custom injection molding market. China’s lower labor costs and larger production scale allow for competitive pricing. This attracts businesses from around the world seeking cost-effective solutions for their injection molding needs. However, it is important to consider the hidden costs that may arise when dealing with Chinese manufacturers, such as import duties, shipping, and communication challenges.
Other Markets:
Other custom injection molding markets, such as those in countries like the United States, Germany, and Japan, are known for their longstanding reputation for high-quality products. These markets have strict standards and regulations in place to ensure product consistency, precision, and reliability.
While the prices offered by these markets may be higher compared to China, businesses often prioritize the assurance of premium product quality. The higher costs are justified by the confidence in the durability and performance of the final product, which is crucial in industries demanding precision and reliability.
When it comes to visible and hidden costs, the situation may vary depending on the specific country and manufacturer. However, in general, other markets may have more transparent pricing structures and fewer hidden costs, making it easier for businesses to estimate their expenses accurately.
In summary, China offers competitive prices and has improved product quality over the years, making it a popular choice for businesses seeking cost-effective solutions. However, concerns remain regarding consistency and precision. Other custom injection molding markets, renowned for their high-quality products, may have higher prices but offer assurance in terms of durability and performance. These markets might have more transparent pricing structures and fewer hidden costs. Businesses need to carefully evaluate their priorities and requirements before choosing a custom injection molding market.
Understanding Pricing and Payment Terms for custom injection molders: A Comparative Guide to Get the Best Deal
When it comes to custom injection molding, understanding the pricing and payment terms is crucial to getting the best deal. This comparative guide will provide insights on how to navigate the complex landscape of pricing structures and payment options offered by custom injection molders.
The pricing structure for custom injection molding typically consists of two main components: tooling costs and production costs. Tooling costs refer to the expenses involved in creating the molds required for the manufacturing process. It includes design, engineering, and manufacturing costs. Production costs, on the other hand, encompass the actual production of the parts or products using the molds.
Different custom injection molders may have varying approaches to pricing these two components. Some molders may offer a lower upfront cost for tooling while increasing the per-part production cost. Others may have a higher tooling cost but lower production costs. It is essential to evaluate the overall cost based on your specific production requirements and expected volumes. Analyzing multiple quotes from various molders will help identify the most cost-effective option.
Aside from pricing, understanding the payment terms offered by custom injection molders is vital. Payment terms may vary depending on the size of the project, the relationship with the molder, and other factors. Common payment options include upfront payments, milestone-based payments, and net payment terms.
Upfront payments require paying a percentage of the total cost before production begins. This option may be suitable for smaller projects or when working with a new molder. Milestone-based payments involve making payments at specific stages of the project, such as after tooling design approval or part sample acceptance. This payment method provides some flexibility and ensures quality control at each stage. Net payment terms allow for payment after the completion of the project within a specified period, typically 30 days. It is essential to negotiate favorable terms that align with your cash flow and financial capabilities.
To get the best deal, it is advisable to not solely focus on price but also consider factors like quality, customer service, lead times, and track record. Assess the expertise, experience, and reputation of the molders to ensure they can meet your expectations and deliver high-quality products consistently.
In conclusion, understanding the pricing and payment terms offered by custom injection molders is crucial to securing the best deal. Evaluating the pricing structure, comparing quotes, and negotiating favorable payment terms are key aspects of the process. Additionally, considering factors beyond price is necessary to ensure a successful partnership with a reliable and capable custom injection molder.
Chinese Regulations and Industry Standards Certifications for custom injection molders,Import Regulations and Customs for custom injection molders from China
Chinese Regulations and Industry Standards Certifications for custom injection molders:
Custom injection molders in China need to adhere to specific regulations and industry standards to ensure the quality and safety of their products. One important regulation is the Implementation Rules for the Compulsory Certification of Plastic Injection Molds. This regulation mandates that injection molds intended for manufacturing plastic products must undergo compulsory certification. It ensures that the molds meet the required quality standards and specifications.
The certification process involves evaluation of the mold’s design, structure, material, and manufacturing process. The certification body conducts factory inspections and tests the molds to assess their performance, durability, and reliability. Once the molds pass all the criteria, they are issued the Compulsory Certification Mark.
Furthermore, custom injection molders should also comply with industry standards such as ISO 9001:2015. This international standard ensures that the molders have an effective quality management system in place. It involves processes for monitoring and improving quality, managing customer feedback, and ensuring continuous improvement.
Import Regulations and Customs for custom injection molders from China:
When importing custom injection molds from China, it is crucial to comply with import regulations and customs requirements. First and foremost, one needs to research and identify the specific import regulations of their country. These regulations may include product-specific standards, labeling requirements, and documentation procedures.
Customs may require certain documents for the importation of injection molds, such as commercial invoices, packing lists, and bills of lading or airway bills. These documents provide information about the product, its value, and its origin.
It is also advisable to work with a reliable freight forwarder or customs broker. They have expertise in handling customs clearance procedures, ensuring compliance with import regulations, and facilitating smooth transportation.
Importers should be aware of any taxes, duties, or tariffs that may apply to imported injection molds. They need to consider these additional costs when budgeting for the importation.
In conclusion, custom injection molders in China must comply with regulations and industry standards certifications to ensure the quality of their products. Importers of custom injection molds from China should familiarize themselves with import regulations and customs requirements, ensuring proper documentation and compliance with applicable taxes and duties.
Sustainability and Environmental Considerations in custom injection molders Manufacturing
Sustainability and environmental considerations play a crucial role in the manufacturing process of custom injection molders. These considerations focus on minimizing the negative impact on the environment and promoting sustainable practices throughout the production cycle.
Firstly, the selection of materials used in injection molders greatly impacts sustainability. Manufacturers strive to use materials that are environmentally friendly, such as biodegradable or recycled plastics. This not only reduces the consumption of natural resources but also decreases waste generation and the carbon footprint associated with production.
Additionally, energy consumption is a significant factor in manufacturing custom injection molders. Implementing energy-efficient technologies and processes can significantly reduce energy consumption, resulting in lower greenhouse gas emissions. Companies can achieve this by utilizing energy-efficient machinery, optimizing manufacturing processes, and adopting renewable energy sources.
Waste management practices are another essential aspect to consider. Implementing effective waste reduction and recycling programs can minimize the amount of waste generated during the manufacturing process. This includes properly separating and recycling materials, reusing excess materials, and disposing of hazardous waste in an environmentally responsible manner.
Water conservation is another critical consideration. Custom injection molding processes often require water for cooling and lubrication purposes. By implementing water-efficient techniques, such as recycling and reusing water, companies can minimize water consumption and reduce their environmental impact.
Furthermore, manufacturers can improve sustainability by focusing on product design and longevity. Designing injection molders that are durable, long-lasting, and easily repairable promotes a circular economy in which products are utilized for a more extended period. This reduces the need for frequent replacements and minimizes waste generation.
In conclusion, sustainability and environmental considerations in custom injection molder manufacturing involve selecting eco-friendly materials, reducing energy consumption, managing waste effectively, conserving water, and designing products for longevity. By prioritizing these considerations, manufacturers can contribute to a more sustainable and environmentally friendly manufacturing industry.
List The Evolution history of “custom injection molders”
Custom injection molding has undergone significant evolution and advancements since its inception. The history of custom injection molders can be traced back to the mid-19th century when John Wesley Hyatt developed the first injection molding machine in 1872. Initially, this process was primarily used for producing billiard balls, but it laid the foundation for future developments.
In the early 20th century, improvements were made to the injection molding process. The introduction of thermoplastics as a molding material in the 1930s revolutionized the industry. This breakthrough enabled the production of more diverse and durable products, leading to increased demand for custom injection molders.
Advancements continued throughout the 20th century. In the 1950s, the introduction of control systems improved the accuracy and precision of injection molding machines. These machines became more efficient, allowing for higher production rates and increased complexity in molded products.
The 1970s saw the emergence of computer numerical control (CNC) technology, which further enhanced the capabilities of custom injection molders. CNC controllers enabled more precise control over the process, ensuring consistent results and reducing manufacturing errors.
In the 1980s and 1990s, the industry witnessed the integration of computer-aided design (CAD) and computer-aided manufacturing (CAM) systems. This integration streamlined the design and production processes, reducing the time and cost required to create molds and produce customized parts.
The turn of the 21st century marked the integration of robotics and automation in custom injection molding. Robotics allowed for increased process automation, which led to higher production rates and improved overall efficiency. Additionally, advancements in material sciences led to the development of new and enhanced polymers, expanding the range of products that could be produced through injection molding.
In recent years, the focus has shifted towards sustainable manufacturing practices and the use of eco-friendly materials. Custom injection molders are adopting more energy-efficient machines and exploring the use of bioplastics and recycled materials to meet the growing demand for sustainable products.
In conclusion, the evolution of custom injection molders has been characterized by continuous improvements in machinery, material selection, precision, automation, and sustainability. These advancements have played a pivotal role in shaping the industry and meeting the increasing demands of various sectors, from automotive to healthcare and consumer goods.
The Evolution and Market Trends in custom injection molders Industry
The custom injection molders industry has undergone significant evolution and witnessed various market trends over the years. This industry primarily involves the manufacturing of custom injection molds used in various industries such as automotive, electronics, medical, packaging, and consumer goods. Let’s explore the evolution and market trends that have shaped this industry.
Evolution:
The custom injection molders industry has evolved from traditional mold making processes to highly advanced computer-aided design (CAD) and computer-aided manufacturing (CAM) techniques. The adoption of these technologies has greatly improved the precision, speed, and efficiency of mold making, resulting in higher quality products and reduced production time.
Market Trends:
1. Increasing demand for complex and intricate mold designs: As industries strive for product differentiation and improved functionalities, there is a growing need for intricate and complex mold designs. Custom injection molders are now required to meet these demands by utilizing advanced machining technologies and intricate mold making techniques.
2. Growing adoption of automation: The industry is witnessing a significant transition towards automation and robotics in mold making processes. This trend is driven by the need for improved precision, productivity, and cost-effectiveness. Automated systems enable custom injection molders to streamline their operations, reduce human errors, and enhance overall production efficiency.
3. Emphasis on sustainability: With increasing environmental concerns, there is a rising demand for sustainable mold making processes. Custom injection molders are incorporating eco-friendly practices by utilizing recyclable materials, optimizing energy consumption, and reducing waste generation. This trend is driven by both regulatory requirements and consumer preferences for environmentally responsible products.
4. Shift towards additive manufacturing: Additive manufacturing, commonly known as 3D printing, is increasingly being utilized in the custom injection molders industry. This technology offers new design possibilities, shorter lead times, and cost advantages for prototyping and low-volume production. While traditional mold making processes still dominate high-volume production, additive manufacturing is expected to gain further traction in the industry.
5. Global market expansion: The custom injection molders industry is experiencing global market expansion, driven by the growth of end-use industries across emerging economies. As these economies continue to industrialize, the demand for custom injection molds is expected to rise. Manufacturers in this industry are therefore actively expanding their global presence through partnerships, acquisitions, and setting up production facilities in new regions.
In conclusion, the custom injection molders industry has evolved with the adoption of advanced technologies and witnessed market trends such as complex mold designs, automation, sustainability, additive manufacturing, and global expansion. These trends are shaping the industry and enabling custom injection molders to meet the changing demands of diverse industries.
Custom Private Labeling and Branding Opportunities with Chinese custom injection molders Manufacturers
Chinese custom injection molders offer great opportunities for custom private labeling and branding. With their advanced manufacturing capabilities, they can produce high-quality products according to specific requirements. This allows businesses to build their own unique brand image and expand their customer base.
One advantage of partnering with Chinese custom injection molders is the cost-effectiveness. Manufacturing in China typically provides access to lower labor and production costs, resulting in competitive pricing for custom products. This allows businesses to offer attractive price points to their customers while maintaining profitability.
Moreover, Chinese custom injection molders often have extensive experience working with international clients. They understand the importance of quality control and product consistency to meet the branding objectives of their customers. They can produce products that adhere to high standards while incorporating unique designs and features requested by the brand.
Chinese manufacturers also offer a wide range of materials and manufacturing techniques, giving brands the flexibility to create custom products that align with their target market’s preferences. This versatility enables businesses to differentiate themselves from competitors and cater to specific customer needs.
Additionally, Chinese custom injection molders often provide packaging and labeling services, allowing businesses to directly brand their products. This includes customizing packaging designs, adding logos, and using specific color schemes that represent the brand identity. Such branding efforts create a cohesive and recognizable product line, which can enhance brand loyalty and recognition.
However, when exploring private labeling and branding opportunities with Chinese custom injection molders, businesses should ensure appropriate intellectual property protection measures. This can involve signing non-disclosure agreements, safeguarding product designs, and conducting thorough due diligence to select reputable manufacturers.
Overall, partnering with Chinese custom injection molders offers businesses a cost-effective and versatile solution for private labeling and branding. By leveraging their manufacturing capabilities and expertise, companies can create unique products that stand out in the market and establish a strong brand presence.
Tips for Procurement and Considerations when Purchasing custom injection molders
When purchasing custom injection molders for procurement, there are several considerations to keep in mind:
1. Determine your specific requirements: Before purchasing a custom injection molder, define your needs. Consider factors like the size, type, and complexity of the part you need to produce, the required production volume, and the materials to be used. Having a clear understanding of your requirements will help you find the right machine.
2. Quality and reliability: Look for a reputable manufacturer with a track record of producing high-quality injection molders. Focus on the machine’s precision, durability, and overall performance. Consider reading customer reviews and testimonials to assess the reliability of the equipment.
3. Capacity and production volume: Evaluate the production capacity of the injection molder. Ensure that it can meet your production volume needs without compromising on quality.
4. Cost: Compare prices from different suppliers to ensure you get the best value for your investment. However, do not compromise on quality for price. Cheap equipment may lead to poor performance and higher maintenance costs in the long run.
5. Technical support and after-sales service: Check the manufacturer’s reputation for customer support. Ensure they provide timely assistance, spare parts availability, and comprehensive training to your operators.
6. Energy efficiency: Consider the energy consumption of the injection molder. Opting for energy-efficient machines can help reduce operating costs and minimize environmental impact.
7. Adaptability and customization: Determine the customization options offered by the supplier. It is crucial to have a molder that can adapt to your changing production needs and accommodate future expansion.
8. Compliance with safety standards: Ensure that the custom injection molder complies with all relevant safety standards and regulations. Look for certifications like CE or UL to ensure the equipment’s safety and reliability.
9. Warranty and maintenance: Review the warranty terms and conditions provided by the supplier. Understand the maintenance requirements and consider the availability of a local service network for easier troubleshooting and repairs.
10. Supplier’s expertise and reputation: Research the supplier’s experience and expertise in the injection molding industry. Look for a supplier with a good reputation, knowledgeable staff, and a strong support system.
By considering these factors, you can make an informed decision that meets your specific requirements, ensuring a successful procurement of custom injection molders.
FAQs on Sourcing and Manufacturing custom injection molders in China
1. What is injection molding?
Injection molding is a manufacturing process used to produce high volumes of identical parts by injecting molten material, typically plastic, into a custom-designed mold. The molten material solidifies and takes the shape of the mold, allowing for the mass production of parts with high precision and accuracy.
2. Why source and manufacture custom injection molders in China?
China has become a popular destination for sourcing and manufacturing custom injection molders due to several reasons: lower labor and production costs, vast manufacturing capabilities, a wide selection of suppliers, and a well-established infrastructure supporting the injection molding industry. These factors make China an attractive option for businesses looking to reduce production costs and access high-quality molds.
3. How can I find reliable injection molding suppliers in China?
To find reliable injection molding suppliers in China, it is crucial to conduct extensive research and due diligence. Online platforms, such as Alibaba and Global Sources, provide comprehensive lists of injection molders in China. However, it is advisable to verify the supplier’s credibility by checking their certifications, visiting their facilities, and requesting samples or references from previous clients. Working with a sourcing agent or a manufacturing consultant with expertise in China can also help ensure a smooth and reliable sourcing process.
4. Can I customize my injection molders in China?
Yes, most injection molders in China offer customization services. They typically work closely with clients to understand their specific requirements, including the desired material, shape, size, and functionality of the molders. The supplier will then create a custom mold design based on these specifications. It is essential to provide clear and detailed requirements to achieve the desired customization accurately.
5. How can I ensure the quality of injection molders manufactured in China?
While quality control can be a concern when sourcing from China, there are several ways to ensure the quality of injection molders. One way is to work with reputable suppliers who have a proven track record and positive feedback from previous clients. Additionally, implementing a comprehensive quality control process that includes inspections throughout the production cycle can help identify and address any potential quality issues. Conducting third-party inspections or hiring a quality control specialist can also provide an extra layer of assurance.
6. How long does it take to manufacture custom injection molders in China?
The time required to manufacture custom injection molders in China depends on various factors, including the complexity of the design, the size of the mold, and the supplier’s production capacity. Generally, the process can take anywhere from a few weeks to several months. It is essential to communicate the desired timeframe with the supplier and consider factors like mold design revisions and shipping time when planning for production.
It is important to note that while these FAQs provide a brief overview, sourcing and manufacturing custom injection molders in China requires careful consideration, thorough research, and effective communication to ensure a successful and cost-effective outcome.
Why contact sourcifychina.com get free quota from reliable custom injection molders suppliers?
Contacting sourcifychina.com can provide the benefit of obtaining a free quota from reliable custom injection molders suppliers. Sourcifychina.com is a sourcing platform that connects businesses with trusted manufacturers and custom injection molders in China. By using their services, businesses can gain access to a network of pre-vetted suppliers who have a proven track record of delivering high-quality products.
The availability of a free quota allows businesses to get a clear picture of their potential costs and requirements before committing to a supplier. This helps in evaluating the feasibility of the project and ensures transparency from the beginning. By receiving a quotation, businesses can assess whether the supplier meets their specific needs in terms of price, quality, lead time, and production capacity.
Sourcifychina.com has established relationships with reliable custom injection molders in China who have undergone a rigorous screening process. They have been vetted based on their certifications, manufacturing capabilities, quality control measures, and client feedback. This ensures that businesses can find trusted suppliers who can deliver consistent results.
By utilizing sourcifychina.com’s sourcing platform, businesses can save time and effort in searching for suitable suppliers. The platform provides a streamlined process where businesses can submit their project requirements and receive multiple quotations from reputable custom injection molders. This eliminates the need for businesses to individually reach out to different suppliers, reducing the time and costs involved in sourcing.
Overall, contacting sourcifychina.com offers the advantage of accessing a network of reliable custom injection molders in China and obtaining a free quota. This allows businesses to evaluate potential suppliers, compare prices, and select the most suitable partner for their injection molding needs.