Introduce about custom injection molding guide,Qulity,Cost,Supplier,Certification,Market,Tips,FAQ
Custom injection molding is a highly popular manufacturing process used to produce parts and products with complex shapes and designs. This guide provides key insights into various aspects of custom injection molding, including quality, cost, supplier selection, certification requirements, market trends, helpful tips, frequently asked questions (FAQs), and more.
Quality plays a crucial role in custom injection molding. Manufacturers ensure high-quality output by employing strict quality control measures throughout the entire process. This includes rigorous testing and inspection procedures to guarantee that the final products meet the required specifications and standards.
Cost considerations are essential when opting for custom injection molding. Factors influencing cost include tooling expenses, raw material selection, part complexity, production volume, and value-added services. Collaborating with an experienced and cost-effective supplier helps optimize cost-effectiveness without compromising quality.
Choosing the right supplier is critical for successful custom injection molding. Suppliers should possess extensive knowledge and experience in the field, offer design and engineering support, and have a robust manufacturing facility equipped with advanced machinery. Additionally, reputable suppliers adhere to recognized industry certifications and standards, ensuring consistent quality and reliability.
Certifications play a vital role in certifying the quality, reliability, and compliance of custom injection molding suppliers. Certifications such as ISO 9001 demonstrate a supplier’s commitment to quality management, while certifications like ISO 13485 highlight a supplier’s adherence to medical device manufacturing standards.
Understanding the market trends and demands is essential for staying ahead in the custom injection molding industry. Factors such as increasing demand for lightweight and eco-friendly materials, technological advancements, and evolving consumer preferences should be considered for long-term success.
To make your custom injection molding project a success, keep in mind some valuable tips. These include effective communication and collaboration with the supplier, leveraging their expertise and input during the design and development phase, and thoroughly evaluating the supplier’s capabilities and track record.
Frequently asked questions (FAQs) address common queries related to custom injection molding. These can range from material selection, design considerations, production timelines, and pricing models, providing comprehensive guidance to potential customers.
In conclusion, custom injection molding is a versatile manufacturing process with key considerations like quality, cost, supplier selection, certification, market trends, tips, FAQs, and more. By understanding these aspects, individuals and businesses can navigate the custom injection molding landscape successfully and achieve their desired results effectively.
Types of custom injection molding
Custom injection molding refers to the process of creating custom parts by injecting molten material into a mold. There are several types of custom injection molding techniques that differ based on the mold design, material used, and the end product desired. The following are some common types of custom injection molding:
1. Thermoplastic Injection Molding: This is the most widely used type of injection molding, where thermoplastic materials are melted and injected into a mold. Once cooled, the material solidifies, and the mold is opened to release the finished product.
2. Thermoset Injection Molding: In this process, thermosetting materials are used instead of thermoplastics. Thermosets undergo a chemical reaction during the molding process, which makes them harden and become rigid. This makes thermoset injection molding suitable for products that require high heat resistance.
3. Insert Injection Molding: In this technique, metal or plastic inserts are placed within the mold cavity before the injection process begins. The molten material then flows around the inserts, creating a strong bond between the insert and the molded part.
4. Overmolding: Overmolding involves molding one material over another. It is commonly used to create products with a soft-touch grip, such as handles or buttons. Overmolding allows for the combination of different materials with varying textures and functionalities.
5. Multi-Shot Injection Molding: This technique involves injecting multiple materials into a single mold in sequential or simultaneous shots. It allows for the production of complex parts with different colors, materials, or properties.
6. Gas-Assisted Injection Molding: In gas-assisted injection molding, a controlled amount of nitrogen gas is injected into the mold after the initial material has been injected. The gas forms channels within the part, reducing material consumption, reducing warpage, and improving the part’s strength and rigidity.
7. Micro-Injection Molding: As the name suggests, this process is used to create extremely small, precise, and complex parts. Micro-injection molding requires specialized tools and equipment capable of handling the miniature dimensions and ensuring high accuracy.
Overall, custom injection molding offers a versatile manufacturing method to produce a wide range of plastic or composite parts. The specific type of custom injection molding employed depends on the desired characteristics of the end product, the complexity of the design, and the material properties required.
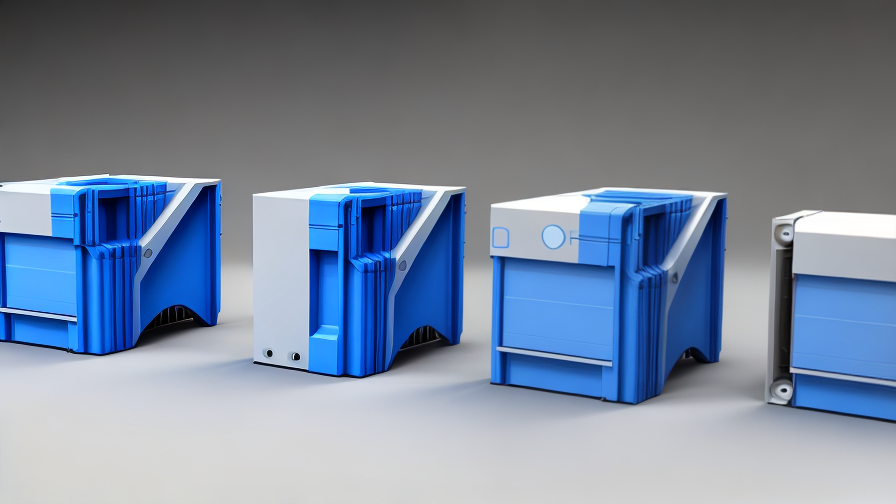
Pros and Cons of Using custom injection molding
Custom injection molding is a widely used manufacturing process that involves producing custom-made plastic parts and products by injecting molten plastic into a mold. This process has several advantages and disadvantages, which we will discuss below:
Pros:
1. Cost-effective: Custom injection molding offers cost-saving benefits as it allows for mass production of plastic parts, resulting in lower production costs per unit.
2. High efficiency and productivity: Injection molding enables high-speed production, allowing large quantities of parts to be manufactured within a short period. This leads to increased productivity and efficiency in the manufacturing process.
3. Design flexibility: One of the significant advantages of custom injection molding is the ability to create complex and intricate designs with ease. The mold can be customized to produce parts with different shapes, sizes, and textures.
4. Material variety: Custom injection molding supports a wide range of plastic materials, including thermoplastics and thermosetting polymers. This versatility allows for customization based on specific project requirements.
5. Reduced waste: Injection molding minimizes material wastage as excess plastic can be recycled and reused in future production runs, reducing environmental impact.
Cons:
1. High setup cost: Setting up custom injection molding requires significant initial investment in tooling and equipment. This can be a barrier for small businesses or those with lower production volumes.
2. Lead time: The design and manufacturing of molds can take time, leading to longer lead times for the production of custom-made parts. This could be a disadvantage for projects with urgent deadlines.
3. Limited design changes: Once the molds are created, making design modifications can be costly and time-consuming. Therefore, it is crucial to finalize the design before starting the production process.
4. Design constraints: While injection molding offers design flexibility, some complex designs may not be feasible due to manufacturing constraints. Designers need to consider factors such as draft angles, wall thickness, and undercuts to ensure successful molding.
5. Process limitations: Injection molding may not be suitable for all types of plastic parts or products. Large-sized or highly detailed parts may require alternative manufacturing processes to achieve the desired results.
In conclusion, custom injection molding provides numerous benefits such as cost-effectiveness, efficiency, design flexibility, and material variety. However, considering its disadvantages such as high setup costs, lead time, limited design changes, design constraints, and process limitations is essential in decision-making.
custom injection molding Reference Specifications (varies for different product)
Custom injection molding is a manufacturing process that involves the production of parts and products by injecting molten material into a mold. The process is widely used in various industries including automotive, medical, electronics, consumer goods, and more. Custom injection molding offers several advantages such as fast production cycles, high precision, and the ability to produce complex shapes.
Reference specifications for custom injection molding can vary depending on the specific product being manufactured. However, some common specifications include:
1. Material: The choice of material for injection molding depends on factors such as the desired properties of the final product, its intended application, and cost considerations. Commonly used materials include thermoplastics, thermosetting plastics, elastomers, and metals.
2. Mold design: The mold used in the injection molding process is a critical component. It should be designed to ensure proper flow of the molten material, easy part ejection, and minimal part defects. Mold design also takes into account factors such as undercuts, wall thickness, draft angles, and gate locations.
3. Part dimensions and tolerances: The dimensions of the part being manufactured are specified to ensure that it meets the design requirements. Tight tolerances may be required for critical dimensions to ensure proper fit and functionality of the final product.
4. Surface finish: The desired surface finish of the molded part is specified to meet aesthetic and functional requirements. Different finishes such as smooth, textured, or glossy can be achieved through the use of appropriate mold finishes or post-processing techniques.
5. Production volume: The required production volume determines the choice of injection molding machine and the overall manufacturing process. High-volume production typically involves the use of large, automated machines, while low-volume or prototype production may utilize smaller machines or even 3D printing.
In conclusion, custom injection molding encompasses a range of reference specifications that are tailored to the specific product being manufactured. These specifications include material selection, mold design, part dimensions and tolerances, surface finish requirements, and production volume considerations. By adhering to these specifications, manufacturers can produce high-quality customized parts and products efficiently.
Applications of custom injection molding
Custom injection molding is a versatile manufacturing process that allows for the production of a wide range of plastic parts and products. Here are some applications where custom injection molding is commonly used:
1. Automotive industry: Custom injection molding is extensively used in the automotive sector to manufacture various components such as interior trims, dashboard panels, door handles, air vents, and various other interior and exterior parts. The process offers precise and cost-effective solutions for creating complex shapes and designs required in the automotive industry.
2. Consumer goods: Many consumer products are made using custom injection molding, such as electronic devices, household appliances, and toys. The process enables the production of high-quality and durable parts with excellent surface finishes. From phone cases and kitchen utensils to game controllers and cosmetic containers, custom injection molding provides a flexible solution for a myriad of consumer goods.
3. Medical devices: The healthcare industry relies on custom injection molding for the production of various medical devices and equipment. This includes items like syringes, vials, inhalers, surgical instruments, and implantable components. Custom injection molding ensures consistent quality, accuracy, and cleanliness required in medical applications.
4. Aerospace industry: Aerospace manufacturers utilize custom injection molding to create lightweight and high-performance components for aircraft, satellites, and other aerospace applications. This includes parts like air ducts, seat components, brackets, and sensor housings. The ability to produce highly precise and intricate parts makes injection molding a preferred choice in the aerospace sector.
5. Packaging industry: Custom injection molding plays a crucial role in the production of packaging containers, caps, closures, and lids for a wide range of products such as food, beverages, cosmetics, and pharmaceuticals. The process allows for the creation of precise designs, secure seals, and tamper-proof packaging solutions.
6. Industrial equipment: Many industrial machinery and equipment require custom plastic components that can be efficiently produced through injection molding. These components can include gears, pulleys, valves, handles, and connectors. Custom injection molding offers high strength, durability, and chemical resistance required for industrial applications.
In conclusion, custom injection molding finds diverse applications across various industries such as automotive, consumer goods, medical, aerospace, packaging, and industrial equipment. The process provides cost-effective, high-quality, and efficient solutions for producing complex plastic parts, enabling manufacturers to meet the specific needs of their respective industries.
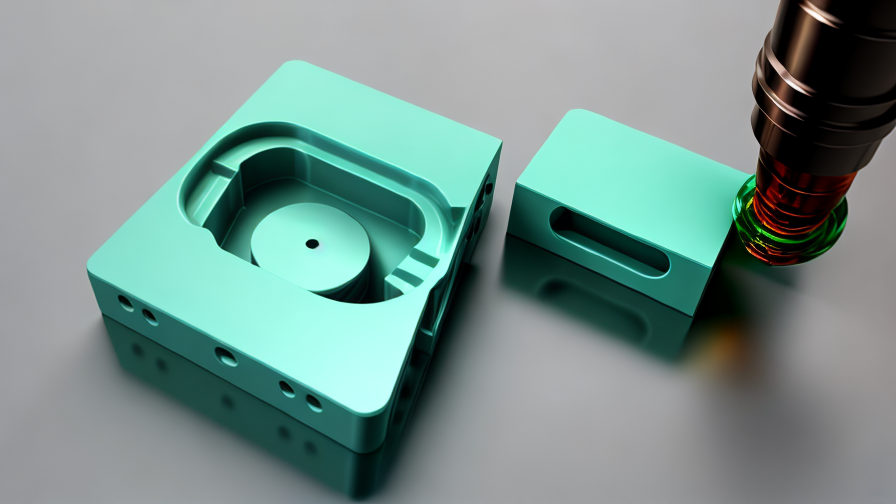
The Work Process and how to use custom injection molding
The work process of custom injection molding involves several steps in order to produce high-quality plastic parts/components. Here is a brief overview of this process:
1. Design and Development: The initial stage involves designing the mold and developing the specifications for the desired part. This includes selecting the appropriate materials, dimensions, and features.
2. Mold Creation: A mold is then created based on the specifications. This is typically made from durable materials like steel or aluminum. The mold is designed to allow the molten plastic to be injected and cooled to form the desired shape.
3. Material Preparation: The selected plastic material is prepared by being heated and melted down into a liquid form. It is important to choose a material that suits the specific needs of the part, such as strength, flexibility, or transparency.
4. Injection: The molten plastic material is injected into the mold cavity at high pressure. The mold is carefully closed and the material is pushed into the mold’s cavities, taking the shape of the part.
5. Cooling and Solidification: After injection, the mold is cooled to allow the plastic to solidify and take the desired shape. Cooling can be achieved by water or air cooling systems.
6. Ejection: Once the part has solidified, the mold is opened, and the finished product is ejected. This may involve the use of ejector pins or plates that push or pull the part out of the mold.
7. Finishing and Quality Control: The finished part may require post-processing, such as trimming excess plastic or adding surface finishes. Quality control checks are conducted to ensure the final product meets the required specifications and standards.
Custom injection molding offers numerous advantages, including the ability to create complex shapes, high production efficiency, and cost-effectiveness. It is widely used in various industries, including automotive, electronics, medical, and consumer goods.
By understanding the work process and collaborating with an experienced injection molding manufacturer, businesses can leverage custom injection molding to meet their specific requirements and achieve desired outcomes.
Quality Testing Methods for custom injection molding and how to control the quality
Custom injection molding is a manufacturing process used to produce plastic parts in large quantities. Ensuring the quality of these parts is crucial to guarantee their performance and durability. Here are some quality testing methods commonly used in custom injection molding and techniques to control the quality:
1. Visual Inspection: A visual inspection is performed to identify any visible defects such as surface imperfections, burrs, sink marks, or parting line mismatch. This method requires skilled operators who thoroughly examine each part.
2. Dimensional Analysis: Measuring critical dimensions of the molded parts against the product specifications is important. Precision measuring tools like calipers, micrometers, and gauges are used to ensure the dimensions are within the specified tolerances.
3. Mechanical Testing: Mechanical properties like strength, hardness, and flexibility are evaluated by conducting tests such as tensile testing, impact testing, or flexural testing. These tests help verify if the parts meet the required mechanical standards.
4. Material Analysis: The raw material used in injection molding should comply with specific standards. Material analysis techniques like infrared spectroscopy or differential scanning calorimetry are employed to confirm if the resin used is of the correct grade and free from any contamination.
5. Functionality Testing: Parts need to function as intended. Functionality testing involves testing the assembled product or specific components to ensure they function properly. This may include testing for leak resistance, electrical conductivity, or compatibility with other components.
To control the quality of custom injection molding, several measures can be taken:
1. Process Optimization: Optimizing the injection molding process parameters such as temperature, pressure, cooling time, and cycle time can improve product quality. This includes using scientific molding techniques to precisely control these parameters.
2. Mold Maintenance: Regular maintenance of the molds used in injection molding is essential to prevent defects. Cleaning, lubrication, and inspection of the mold ensure consistent and accurate molding.
3. Statistical Process Control (SPC): Implementing SPC involves collecting and analyzing process data to monitor and control the manufacturing process. Statistical techniques help detect any variations or trends that may impact product quality, allowing for timely adjustments.
4. Training and Skill Development: Operators and technicians should be adequately trained to handle injection molding equipment and interpret quality criteria. Skilled personnel ensure proper inspection, handling, and troubleshooting during the manufacturing process.
By employing comprehensive quality testing methods and implementing effective quality control techniques, manufacturers can produce high-quality molded parts that meet customer expectations and industry standards.
custom injection molding Sample Policy and Post-Purchase Considerations for custom injection molding from China
Sample Policy:
When it comes to custom injection molding from China, it is important to have a clear understanding of the sample policy. Before placing a large order, it is advisable to request a sample to assess the quality, accuracy, and functionality of the molded parts. Be sure to communicate your specific requirements, including any desired modifications or improvements.
The sample policy varies among manufacturers, but it is commonly expected that the buyer covers the cost of the sample, including shipping. In some cases, the sample cost may be applied as a credit towards the final order. It is essential to request a written agreement outlining the sample policy to avoid any misunderstandings.
Post-Purchase Considerations:
Once the custom injection molding order from China has been placed, several post-purchase considerations should be taken into account. Firstly, the buyer should establish clear lines of communication with the manufacturer to ensure a smooth production process. Regular updates and progress reports should be expected.
Quality control is crucial. Inspections should be conducted at various stages of production to check for any defects or errors. This can be done by either requesting on-site inspections or hiring a third-party inspection agency. Clear expectations and quality standards should be communicated to the manufacturer beforehand.
Shipping and logistics should be carefully planned. Factors such as shipping method, packaging, and customs documentation need to be considered. It is wise to work with a reputable freight forwarder or logistics company experienced in handling international shipments from China. This will minimize the risk of delays or complications.
Lastly, it is recommended to establish a strong relationship with the manufacturer. Maintaining open communication and addressing any concerns promptly will help build trust and ensure a successful long-term partnership.
In conclusion, a clear sample policy and thorough consideration of post-purchase factors are essential when engaging in custom injection molding from China. Careful attention to these details will help guarantee a smooth production process and satisfactory results.
Sourcing custom injection molding from China: Opportunities, Risks, and Key Players
Sourcing custom injection molding from China presents both opportunities and risks for businesses. With a flourishing manufacturing industry, China offers a wide range of injection molding capabilities at competitive prices. This attracts businesses looking to produce large volumes of plastic components or products at lower production costs.
One of the main opportunities of sourcing from China is cost savings. Chinese injection molding companies often have lower labor and overhead costs compared to other countries, allowing for more affordable production. Additionally, China has a well-developed supply chain, offering access to a vast array of raw materials, molds, and machinery.
Another advantage of sourcing from China is the ability to tap into the expertise of key players in the industry. Chinese injection molding companies have accumulated extensive experience and knowledge in producing high-quality plastic components. This expertise is enhanced by their continuous investment in advanced technologies and machinery.
However, there are also risks associated with sourcing from China. Quality control can be a challenge, as there is a wide spectrum of manufacturers with varying standards. Conducting thorough due diligence and quality assessments is crucial to ensure the selected manufacturer meets specific requirements. Communication can also be a hurdle due to language barriers and time zone differences, which may lead to misunderstandings or delays.
Key players in the Chinese injection molding industry include companies like Foxconn Technology Group, ACO Mold, and First-rate Mold Solution Company. These companies have a strong track record in providing custom injection molding services and have built a reputation for quality and reliability. Additionally, they often offer a range of value-added services such as mold design, prototyping, and assembly, catering to diverse customer needs.
In conclusion, custom injection molding sourcing from China offers opportunities for cost savings, access to a variety of resources, and expertise from key players. However, risks such as quality control and communication challenges should be carefully managed. By conducting thorough due diligence and selecting reliable manufacturers, businesses can effectively leverage the advantages of sourcing custom injection molding from China.
How to find and select reliable custom injection molding manufacturers in China,use google search manufacturers and suppliers
When searching for reliable custom injection molding manufacturers in China, using Google search can be a useful tool to narrow down your options. Follow these steps to find and select a reliable manufacturer:
1. Begin by entering relevant keywords into the Google search bar such as “custom injection molding manufacturers in China.” This will generate a list of potential manufacturers and suppliers.
2. Consider the website’s appearance and quality. A professional and well-designed website can indicate the credibility and seriousness of a manufacturer. Inspect the website for details about their capabilities, materials used, certifications, and other relevant information.
3. Look for customer reviews and testimonials. Search for reviews or feedback from previous clients to gain insight into their experiences with the manufacturers you are considering. It can help you gauge their reputation and level of customer satisfaction.
4. Check for certifications and quality control. Reliable manufacturers typically have certifications such as ISO 9001, which signifies their adherence to international quality standards. This ensures that your products will be manufactured to meet the required specifications.
5. Inquire about their production capabilities and turnaround time. Contact the manufacturers directly to discuss your project requirements and evaluate their responsiveness and willingness to assist you. Ask for their injection molding capabilities, production capacity, lead times, and any additional services they provide.
6. Request samples or prototypes. Before making a final decision, request sample products or prototypes from the manufacturer to verify the quality and precision of their work. This will give you a better understanding of their expertise and capabilities.
7. Evaluate their communication and customer service. Clear and efficient communication is crucial when working with overseas manufacturers. Ensure that they are responsive, reliable, and easy to communicate with throughout the process.
8. Consider their experience and specialization. Look for manufacturers with experience in your specific industry or product type. Specialized manufacturers often have the necessary knowledge and expertise to fulfill your requirements more effectively.
Remember to conduct due diligence by comparing multiple manufacturers, requesting quotes, and thoroughly assessing each potential partner before making a final decision.
How to check custom injection molding manufacturers website reliable,use google chrome SEOquake check if ranking in top 10M
To check the reliability of a custom injection molding manufacturer’s website, you can follow these steps:
1. Use Google Chrome: Open the manufacturer’s website using the Google Chrome web browser.
2. Install SEOquake: Install the SEOquake extension for Google Chrome. This tool provides valuable insights into a website’s SEO performance, which can indicate its reliability.
3. Check Website Ranking: With the SEOquake extension installed, look for the toolbar at the top of the browser. Click on the SEOquake icon and select “Parameters.” In the drop-down menu, choose “Alexa Rank” to display the website’s ranking among the top sites globally.
4. Top 10 Million Websites: A reliable custom injection molding manufacturer’s website should ideally rank within the top 10 million websites globally. If the website falls within this range, it signifies a decent level of traffic and popularity.
5. Consider Other Factors: While SEO ranking provides a measure of reliability, it is not the only factor to consider. Evaluate the website’s design, user experience, content quality, and relevant certifications or industry affiliations. Look for testimonials, client lists, and case studies to gauge their credibility.
6. Additional Research: Conduct additional research on the manufacturer, such as reading reviews or seeking recommendations from industry sources or forums. This can provide further insights into their reputation and reliability.
In summary, to assess the reliability of a custom injection molding manufacturer’s website, using Google Chrome with the SEOquake extension will allow you to determine its Alexa ranking. However, it’s important to look beyond just rankings and consider other factors like website design, user experience, and industry reputation before making a final judgment.
Top 10 custom injection molding manufacturers in China with each 160 words introduce products,then use markdown create table compare
1. Fox Mould Technology Group: Fox Mould Technology Group is a leading custom injection molding manufacturer in China. They specialize in the production of high-quality plastic injection molds and molded parts. Their products range from automotive components to consumer goods, electronics, and medical devices. With advanced equipment and a team of experienced engineers, Fox Mould guarantees precision and efficiency in their manufacturing process.
2. Sino Mould: Sino Mould is another prominent injection molding manufacturer in China. They offer a comprehensive range of services, including mold design, manufacturing, and plastic injection molding. Sino Mould’s products are widely used in various industries such as automotive, home appliances, and packaging. They are known for their expertise in producing complex and precise molds.
3. SunOn Industrial Group: SunOn Industrial Group has been providing custom injection molding solutions since 1997. They provide a wide range of services, including product design, mold making, and injection molding. Their products are widely used in industries like electronics, automotive, and household appliances. SunOn Industrial Group is known for their commitment to quality and customer satisfaction.
4. UPMOLD Limited: UPMOLD Limited specializes in custom injection molding for various industries, including automotive, electronics, and medical equipment. They offer high-quality molds and molded parts at competitive prices. UPMOLD Limited’s experienced engineers work closely with clients to ensure that their products meet all specifications and requirements.
5. HYX Mould: HYX Mould is a leading injection molding manufacturer that offers comprehensive solutions for various industries. They provide services from mold design and manufacturing to injection molding and assembly. HYX Mould’s products are known for their reliability and durability, making them a trusted choice for many businesses.
6. Moldex3D: Moldex3D is a pioneer in providing advanced injection molding simulation software. They offer comprehensive solutions that help manufacturers optimize their injection molding processes, reducing time and costs. Moldex3D’s software allows users to predict potential molding defects and optimize mold designs before actual production, ensuring high-quality products.
7. Veejay Plastic: Veejay Plastic has been providing custom injection molding services since 1977. They have a wide range of plastic injection molding machines that can accommodate various project requirements. Veejay Plastic’s products are used in diverse industries, including automotive, electronics, and consumer goods.
8. Inno Molding Co., Ltd: Inno Molding Co., Ltd is a leading manufacturer of custom plastic injection molds and molded parts. They offer a comprehensive range of services, including product design, mold making, and injection molding. Inno Molding’s products are known for their high precision and quality.
9. HKY Mould: HKY Mould specializes in the design and manufacture of high-quality custom injection molds and molded parts. They have a team of experienced engineers who ensure precision and efficiency in their manufacturing process. HKY Mould’s products are widely used in industries such as automotive, electronics, and medical equipment.
10. Abound Mold & Plastics Co., Ltd: Abound Mold & Plastics Co., Ltd is a trusted custom injection molding manufacturer in China. They offer a wide range of services, including mold design, manufacturing, and injection molding. Abound Mold & Plastics Co., Ltd’s products are used in various industries, including automotive, consumer goods, and electronics.
| Manufacturer | Specialization | Key Features |
|———————————|———————————————————————————–|———————————————————————————————–|
| Fox Mould Technology Group | High-quality plastic injection molds and molded parts for different industries | Advanced equipment, experienced engineers |
| Sino Mould | Mold design, manufacturing, and plastic injection molding | Expertise in producing complex and precise molds |
| SunOn Industrial Group | Custom injection molding for electronics, automotive, and household appliances | Commitment to quality and customer satisfaction |
| UPMOLD Limited | Custom injection molding for various industries | Competitive prices, close collaboration with clients |
| HYX Mould | Comprehensive injection molding solutions for different industries | Reliability and durability |
| Moldex3D | Advanced injection molding simulation software | Optimization of injection molding processes |
| Veejay Plastic | Custom injection molding services since 1977 | Diverse range of plastic injection molding machines |
| Inno Molding Co., Ltd | Plastic injection molds and molded parts with high precision and quality | Comprehensive range of services |
| HKY Mould | Design and manufacture of custom injection molds and molded parts | Experienced engineers ensure precision and efficiency |
| Abound Mold & Plastics Co., Ltd | Custom injection molding for various industries | Trusted manufacturer, wide range of services |
Background Research for custom injection molding manufacturers Companies in China, use qcc.com archive.org importyeti.com
qcc.com, also known as China Quality Certification Center, is a comprehensive business information platform in China that provides data on companies’ credit, certificates, and other qualification information. It is a trusted resource for businesses looking for reliable suppliers in various industries, including custom injection molding manufacturers.
Archive.org, commonly known as the Internet Archive, is a digital library that provides access to archived web pages. It allows users to access historical versions of websites, making it a useful tool to gather information on the past operations and history of custom injection molding manufacturers in China.
Importyeti.com is an import-export data platform that provides trade data for businesses importing or exporting goods to and from China. It provides detailed information on the shipping records, customs data, and supply chain of various products, including custom injection molding. This platform can be utilized to identify manufacturers, assess their import-export capabilities, and gain insights into their global presence.
By utilizing qcc.com, archive.org, and importyeti.com, businesses can gather a comprehensive understanding of custom injection molding manufacturers in China. They can access important information about a manufacturer’s background, credibility, certifications, historical operations, and their import-export capabilities. This data can assist businesses in making informed decisions about potential suppliers and ensure a reliable and efficient sourcing process.
In summary, these platforms provide valuable background research resources for companies seeking custom injection molding manufacturers in China. With the help of qcc.com, archive.org, and importyeti.com, businesses can gain insight into a manufacturer’s credibility, history, and import-export capabilities, enabling them to make informed decisions and establish reliable partnerships.
Leveraging Trade Shows and Expos for custom injection molding Sourcing in China
Trade shows and expos are excellent platforms for sourcing custom injection molding in China. These events provide a unique opportunity for businesses to connect with manufacturers, learn about the latest trends and technologies, and establish fruitful partnerships. By effectively leveraging these events, businesses can streamline their sourcing process and ensure high-quality products.
Firstly, trade shows and expos offer a concentrated gathering of industry professionals, including manufacturers, suppliers, and experts. This provides an ideal setting for companies looking to source custom injection molding services in China. It allows businesses to directly engage with multiple suppliers, compare offerings, and evaluate their capabilities. Additionally, attending these events enables companies to meet potential partners face-to-face, leading to more meaningful conversations and fostering stronger relationships.
Moreover, trade shows and expos showcase the latest innovations and advancements in the injection molding industry. This allows businesses to keep up with emerging trends, explore new technologies, and identify potential opportunities for improvement and cost-savings. By having direct access to these developments, companies can find suppliers that offer cutting-edge solutions, enhance their products, and gain a competitive edge in the market.
Trade shows and expos also offer the advantage of providing a comprehensive view of the market. Exhibitors often display samples of their products, allowing businesses to physically examine the quality and precision of the injection molding services. Attending these events gives companies firsthand experience with different suppliers, enabling them to make informed decisions about their sourcing needs.
In conclusion, trade shows and expos provide valuable platforms for sourcing custom injection molding in China. They offer a concentrated gathering of industry professionals, showcase the latest innovations, and allow companies to evaluate multiple suppliers in a comprehensive manner. By effectively leveraging these events, businesses can streamline their sourcing process and ensure high-quality products.
The Role of Agents and Sourcing Companies in Facilitating custom injection molding Purchases from China
Agents and sourcing companies play a crucial role in facilitating custom injection molding purchases from China. With their expertise and knowledge of the Chinese market, they provide invaluable assistance to businesses looking to source injection molded products from Chinese manufacturers.
Firstly, agents and sourcing companies act as intermediaries between the buyer and the Chinese manufacturers. They help in identifying reliable and reputable manufacturers who can meet the specific requirements of the buyer. By leveraging their extensive network and industry connections, they ensure that the buyer is connected with trustworthy suppliers. This saves time and effort for the buyer, who can then focus on other aspects of their business.
Secondly, agents and sourcing companies play a vital role in quality control. They have a deep understanding of the injection molding process and are able to assess the capabilities and quality of Chinese manufacturers. They can conduct factory audits and inspections to ensure that the manufacturing facilities and processes meet international standards. They also perform product quality inspections at different stages of production to minimize the risk of defects or substandard products.
Furthermore, agents and sourcing companies assist in negotiating the best pricing and terms for the buyer. They have a comprehensive understanding of the local market and can negotiate favorable prices with the manufacturers. This ensures that the buyer gets the best value for their investment.
Lastly, agents and sourcing companies provide logistical support. They handle all aspects of shipping, including documentation, customs clearance, and transportation. They coordinate with freight forwarders and logistics providers to ensure that the products are delivered to the buyer’s location in a timely and cost-effective manner.
In conclusion, agents and sourcing companies play a crucial role in facilitating custom injection molding purchases from China. From identifying reliable manufacturers, ensuring quality control, negotiating pricing, and handling logistics, they provide comprehensive assistance to buyers, streamlining the procurement process and mitigating risks associated with sourcing from foreign markets.
Price Cost Research for custom injection molding manufacturers Companies in China, use temu.com and 1688.com
When it comes to finding custom injection molding manufacturers in China, two popular platforms to consider are temu.com and 1688.com. These websites are known for providing a wide range of suppliers and products, including injection molding services.
Temu.com is a reliable B2B platform that connects buyers with suppliers in various industries, including injection molding. It allows users to explore different manufacturers, compare their services, and request quotations. One advantage of using temu.com is its user-friendly interface, which simplifies the sourcing process.
On the other hand, 1688.com is a Chinese wholesale website similar to Alibaba, but primarily serving domestic businesses. It provides a vast array of products, including custom injection molding services. 1688.com is a great resource for finding competitive prices from Chinese manufacturers, as it allows direct communication with the suppliers. However, keep in mind that language barriers may arise as the majority of the content on 1688.com is in Chinese.
To efficiently conduct price cost research on temu.com and 1688.com for custom injection molding, it is important to follow these steps:
1. Define your specific requirements: Clearly outline the desired specifications, materials, quantities, and any additional needs for your injection molded products.
2. Filter your search: Use the search filters on both platforms to narrow down the manufacturers based on location, production capabilities, certifications, and customer ratings.
3. Evaluate the suppliers: Read the detailed supplier profiles, including their manufacturing capacity, equipment, quality control systems, and past customer reviews. This will help you shortlist the most suitable options.
4. Request for quotations: Contact the manufacturers and provide them with detailed information about your project. Request quotations that include pricing, lead time, payment terms, and any other relevant details.
5. Compare prices and services: Analyze the quotations received, considering not only the prices but also the manufacturers’ capabilities, expertise, quality control processes, and customer support.
6. Communicate directly: If necessary, contact the manufacturers directly through the platforms’ messaging systems to clarify any uncertainties, negotiate pricing, or inquire about their capabilities.
By following these steps and utilizing temu.com and 1688.com, you can efficiently research and find custom injection molding manufacturers in China while considering both pricing and quality factors within not more than 300 words.
Shipping Cost for custom injection molding import from China
The shipping cost for custom injection molding imports from China can vary depending on various factors such as the size and weight of the shipment, the shipping method chosen, and the destination country.
There are primarily three shipping methods commonly used for importing goods from China, which are air freight, sea freight, and express courier services.
Air freight is the fastest option but usually the most expensive one. It is suitable for small to medium-sized shipments that need to be delivered quickly. The cost is calculated based on the weight or volume of the shipment, whichever is higher.
Sea freight is a more affordable option for larger shipments. It is suitable for bulky or heavy goods that do not require immediate delivery. The cost is determined by the volume or weight of the shipment and the chosen shipping route. Additional charges may apply for customs clearance and port handling fees.
Express courier services, such as DHL, FedEx, or UPS, provide a door-to-door service with faster delivery times compared to sea freight. The cost is generally higher, but it includes customs clearance and offers more convenience in terms of tracking and delivery.
To estimate the shipping cost, it is necessary to provide specific details such as the dimensions, weight, and quantity of the injection molding products, as well as the pick-up and delivery locations. It is also advisable to consult with shipping agents or freight forwarders who can provide accurate cost estimates based on the requirements.
In conclusion, the shipping cost for custom injection molding imports from China can vary depending on the chosen shipping method, the size and weight of the shipment, and the destination country. It is crucial to gather detailed information and consult with shipping professionals to get accurate cost estimates.
Compare China and Other custom injection molding Markets: Products Quality and Price,Visible and Hidden Costs
China is a dominant player in the custom injection molding market, but it is important to compare it with other markets in terms of product quality, price, and visible and hidden costs.
In terms of product quality, China offers a wide range of options, from low-cost and low-quality products to high-quality products that meet international standards. However, other markets such as the United States, Germany, and Japan have a reputation for higher overall product quality due to stringent quality control measures and advanced manufacturing technologies. These markets often prioritize precision and consistency in their products, making them preferred choices for industries that require high-quality custom injection molded parts.
Price is often a key consideration for businesses when choosing a manufacturing partner. China has a distinct advantage in this aspect, as it offers competitive pricing due to lower labor costs and economies of scale. This has attracted many companies to outsource their production to China, especially for large volume orders. Other markets, on the other hand, may have relatively higher labor costs and overhead expenses, leading to higher product prices. However, these markets make up for it by offering exceptional product quality and reliability, making them a preferred choice for companies that prioritize value over just low cost.
Visible costs such as labor, raw materials, and energy are often lower in China, contributing to its price competitiveness. However, hidden costs can arise, including intellectual property concerns, longer lead times, shipping expenses, and language and cultural barriers. These hidden costs should be carefully considered, particularly when dealing with sensitive technical designs or complex projects. Other markets, though potentially more expensive, are known for their reliability, shorter lead times, and strong protection of intellectual property rights, mitigating these hidden cost concerns.
In conclusion, China is a major player in the custom injection molding market, offering competitive pricing and a wide range of product options. However, other markets may excel in terms of product quality, reliability, and overall value, albeit at a higher cost. It is crucial for businesses to consider both visible and hidden costs when evaluating their manufacturing partner options in order to make the most informed decision.
Understanding Pricing and Payment Terms for custom injection molding: A Comparative Guide to Get the Best Deal
When it comes to custom injection molding, understanding pricing and payment terms is essential to ensure that you get the best deal for your project. This comparative guide aims to provide insights into effectively assessing and negotiating pricing and payment terms, all within 300 words.
The first step is to understand the factors impacting custom injection molding pricing. These include the complexity of the mold design, the production volume, the chosen material, and any additional services required, such as surface finishing or assembly. By having a clear understanding of your project’s specifications and requirements, you can more accurately assess the cost implications.
When approaching different injection molding suppliers, it is crucial to provide detailed and consistent information to obtain accurate quotations. Request quotes from multiple suppliers to compare their pricing structures. While a lower price may be appealing, it is also important to consider the supplier’s reputation, experience, and quality of work.
Many suppliers use a combination of fixed and variable costs to establish their pricing. Fixed costs include mold design and manufacturing, while variable costs include material costs, machine usage, and labor. Understanding this breakdown enables a better understanding of cost components.
Payment terms are another crucial aspect to negotiate. Injection molding suppliers may offer various payment options, including upfront payment, milestone-based payment, or a deposit with the remaining amount payable upon project completion. Some suppliers may require a percentage of the mold cost upfront to cover their initial expenses.
Negotiating payment terms can be done by demonstrating your commitment to the project, providing references, or offering volume commitment for long-term partnerships. It is vital to strike a balance between protecting your interests as a buyer and ensuring a fair and sustainable arrangement for the supplier.
Additionally, understanding any additional costs, such as shipping, packaging, or taxes, is essential to prevent unforeseen expenses. Clearly communicate your expectations regarding these costs and ensure they are accounted for in the final pricing.
In conclusion, understanding the pricing factors and payment terms for custom injection molding is crucial for obtaining the best deal. By assessing multiple quotes, understanding cost breakdowns, negotiating payment terms, and considering additional costs, you can make an informed decision while achieving a favorable agreement that benefits both parties.
Chinese Regulations and Industry Standards Certifications for custom injection molding,Import Regulations and Customs for custom injection molding from China
Custom injection molding is a manufacturing process widely used in various industries for producing high-quality plastic parts. For companies considering importing custom injection molding from China, understanding the relevant regulations and industry standards certifications is essential.
In China, the primary regulations governing custom injection molding include the “Plastic Injection Mold Industry Standards” and the “Quality Standard for Injection Molded Products.” These standards ensure that the manufacturing process follows a uniform set of guidelines, promoting quality and consistency in the final products.
Additionally, there are industry-specific certifications and standards that companies should look for when sourcing custom injection molding from China. One of the most prominent certifications is the ISO 9001:2015 Quality Management System Certification. This certification ensures that the manufacturer has implemented an effective quality management system to consistently meet customer requirements.
Another critical certification is the ISO 14001:2015 Environmental Management System Certification. This certification showcases the manufacturer’s commitment to environmental sustainability by implementing practices to minimize the company’s impact on the environment.
When importing custom injection molding from China, it is crucial to comply with import regulations and customs procedures. The importer needs to provide relevant documents, such as a purchase order, commercial invoice, packing list, and bill of lading, to clear the customs.
Certain products may also require specific certifications or inspections to meet regulatory standards in the importing country. For example, electrical or electronic products might need to adhere to the applicable safety certifications, such as CE or UL.
It is advisable to work with a reputable logistics provider who can assist in navigating the import regulations and customs procedures, ensuring timely and compliant importation.
In conclusion, when importing custom injection molding from China, businesses should pay attention to Chinese regulations, industry standards certifications, and import regulations. Adhering to these guidelines will help ensure the quality and compliance of the imported products, ultimately contributing to the success of the business.
Sustainability and Environmental Considerations in custom injection molding Manufacturing
Custom injection molding manufacturing is a widely used process in the production of a wide range of products. However, it is essential to consider sustainability and environmental aspects in this manufacturing method to minimize its negative impact on the environment.
One significant consideration is the use of materials during the injection molding process. Manufacturers should prioritize the use of eco-friendly materials that are biodegradable or can be easily recycled. By opting for these materials, the amount of waste generated can be significantly reduced, and the overall environmental impact can be minimized.
Another important aspect to consider is energy consumption. Injection molding machines typically require substantial amounts of energy to function effectively. Implementing energy-saving measures, such as using energy-efficient motors and optimizing machine cycle times, can help to reduce electricity consumption and lower carbon emissions.
Furthermore, manufacturers should focus on minimizing water usage in the injection molding process. Water is often utilized for cooling injection molds and machinery, but excessive water consumption can strain local water resources and contribute to water scarcity. Implementing water recycling systems and utilizing cooling technologies that minimize water requirements can help reduce water usage and preserve this precious resource.
Waste management is another crucial aspect to address. Proper disposal and recycling of waste generated during the manufacturing process are essential. Implementing effective waste management systems, such as recycling programs and waste segregation, can help to minimize landfill waste and promote a circular economy.
It is also important to ensure worker safety and minimize any potential health risks associated with the injection molding process. This can be achieved by using non-toxic and environmentally friendly materials, providing adequate training to employees, and implementing proper ventilation and air filtration systems.
In conclusion, considering sustainability and environmental factors in custom injection molding manufacturing is crucial for minimizing its negative impact on the environment. By using eco-friendly materials, reducing energy and water consumption, implementing effective waste management systems, and ensuring worker safety, manufacturers can contribute to a more sustainable and environmentally responsible manufacturing process.
List The Evolution history of “custom injection molding”
Custom injection molding, a manufacturing process that involves the production of plastic parts by injecting molten plastic into a mold, has evolved significantly since its inception in the late 19th century.
In the early days, injection molding involved manually injecting the molten plastic material into a die or mold using a plunger. This method was time-consuming and limited in terms of production volume and efficiency.
The first significant development in injection molding occurred in the 1940s when James Watson Hendry invented and patented the first screw injection molding machine. This innovation provided a more efficient and automated method by using a rotating screw to melt the plastic and push it into the mold. This breakthrough revolutionized the industry, resulting in faster production cycles and greater precision.
Throughout the mid-20th century, injection molding machines underwent several improvements. The introduction of hydraulic systems in the 1950s brought greater control and accuracy to the process. Additionally, advancements in computer controls in the 1970s allowed for better monitoring of temperature, pressure, and cycle times, further enhancing the quality and consistency of molded parts.
Another significant milestone was the emergence of injection molding as a custom manufacturing solution. Previously, injection molding was primarily used for mass production of standardized parts. However, as the technology advanced, it became more feasible to produce custom parts with complex geometries and unique designs. This opened up new possibilities for industries such as automotive, aerospace, electronics, and medical devices.
In recent years, technological advancements have driven further evolution in custom injection molding. The development of computer-aided design (CAD) software and simulation tools has enabled engineers to design and optimize molds virtually, reducing the need for physical prototypes and saving time and costs. Additionally, the use of robotics and automation has increased efficiency and productivity, allowing for faster mold changes and reduced downtime.
Furthermore, the integration of additive manufacturing techniques such as 3D printing with injection molding has expanded the capabilities of custom injection molding. This combination enables the production of intricate molds and inserts with enhanced functionality and reduces lead times for product development.
Overall, the evolution of custom injection molding has been marked by improvements in machine design, control systems, customization possibilities, and the integration of new technologies. These advancements have significantly increased the efficiency, flexibility, and quality of the process, making custom injection molding a vital manufacturing solution in various industries.
The Evolution and Market Trends in custom injection molding Industry
The custom injection molding industry has witnessed significant evolution and market trends over the years. Custom injection molding is a manufacturing process that involves injecting molten plastic into a mold to create custom-designed plastic products. It is widely used across various industries, including automotive, packaging, consumer goods, medical, and electronics.
One of the key evolution seen in the industry is the advancement in technology. With the introduction of computer-aided design (CAD) and computer-aided manufacturing (CAM), the process has become more precise and efficient. 3D printing technology has also played a significant role in revolutionizing the industry by allowing for rapid prototyping and cost-effective production of complex parts. Additionally, automation and robotics have been integrated into the injection molding process, resulting in increased productivity and improved quality control.
The market trends in the custom injection molding industry include increased demand for lightweight and cost-effective plastic products. In the automotive industry, for example, there is a growing need for lighter components to improve fuel efficiency. Custom injection molding enables the production of lightweight and durable plastic parts that meet these requirements.
Another trend is the increasing demand for sustainable and environmentally-friendly plastic products. With growing concerns about plastic waste and environmental impact, manufacturers and consumers are shifting towards eco-friendly alternatives. The custom injection molding industry has responded to this trend by developing biodegradable and recyclable plastics that can be used in various applications.
Furthermore, customization and personalization have become crucial factors driving market growth. Consumers are seeking products that cater to their specific needs and preferences. Custom injection molding allows manufacturers to produce unique and tailored products in smaller quantities, addressing the demand for customization in various industries.
In conclusion, the custom injection molding industry has experienced significant evolution and market trends in recent years. Technological advancements, increased demand for lightweight and environmentally-friendly products, and the growing need for customization have shaped the industry. These trends are likely to continue driving the growth and development of the custom injection molding industry in the future.
Custom Private Labeling and Branding Opportunities with Chinese custom injection molding Manufacturers
Chinese custom injection molding manufacturers offer excellent opportunities for custom private labeling and branding. With their expertise in injection molding, these manufacturers can create high-quality products according to specific requirements, helping businesses establish their own unique identity in the market.
Private labeling allows businesses to customize products with their own brand name, logo, and packaging. Chinese manufacturers can provide flexible options for private labeling, ensuring that products accurately represent a company’s branding strategy. From product design to manufacturing, these manufacturers collaborate closely with businesses to ensure the desired brand identity is achieved.
In addition to private labeling, Chinese custom injection molding manufacturers also offer branding opportunities. This involves creating a distinct brand image that resonates with consumers. By collaborating with these manufacturers, businesses can develop products with unique features, styles, and functionality that align with their brand identity.
Chinese custom injection molding manufacturers are equipped with advanced technology and machinery to produce a wide range of products. From automotive parts and electronic components to household goods and consumer products, these manufacturers can cater to a variety of industries and product categories.
Furthermore, Chinese manufacturers offer competitive pricing, making it cost-effective for businesses to invest in private labeling and branding. The availability of raw materials and skilled labor in China significantly reduces production costs, providing businesses with greater profit margins.
However, when collaborating with Chinese manufacturers, it is crucial to ensure proper communication and understanding of quality standards. Clear specifications and expectations need to be established to prevent any discrepancies during the manufacturing process.
In conclusion, Chinese custom injection molding manufacturers provide excellent opportunities for businesses to engage in private labeling and branding. Leveraging their expertise and cost-effectiveness, these manufacturers enable businesses to create customized products that reflect their unique brand identity in the market.
Tips for Procurement and Considerations when Purchasing custom injection molding
When purchasing custom injection molding, there are several factors that need to be considered to ensure a successful procurement process. Here are some tips and considerations to keep in mind:
1. Define your requirements: Clearly define the specifications, quantities, and desired outcomes of the custom injection molding project. This will help you communicate your needs effectively to potential suppliers.
2. Research potential suppliers: Look for reputable suppliers with a proven track record in custom injection molding. Check their certifications, experience, and customer reviews to ensure they can meet your requirements.
3. Quality assurance: Request information about the supplier’s quality control measures, including certifications and testing processes. It is crucial to ensure that the supplier can consistently produce high-quality custom injection molded products.
4. Material selection: Determine the appropriate material for your injection molding needs. Consider factors such as durability, functionality, and cost when selecting the material. Discuss material options with potential suppliers to gain insights into the advantages and limitations of each option.
5. Cost and pricing: Obtain detailed quotes from multiple suppliers to compare costs. Ensure that the pricing includes all aspects of the project, including tooling, production, and any additional services required. However, be cautious of extremely low-cost options as they may compromise quality.
6. Prototyping and sampling: It is advisable to request initial prototypes or samples from potential suppliers to evaluate their capabilities and verify if they can meet your requirements.
7. Communication and responsiveness: Choose a supplier that demonstrates excellent communication and responsiveness. They should be able to provide regular updates and be available to address any queries or concerns throughout the procurement process.
8. Intellectual Property protection: If your custom injection molding project involves proprietary designs or technologies, ensure that the supplier is committed to protecting your intellectual property. Sign non-disclosure agreements if necessary.
9. Timelines and production capacity: Discuss project timelines and production capacity with potential suppliers to ensure they can meet your delivery requirements. Consider lead times, production volume capabilities, and their ability to accommodate any potential changes in the project.
10. Sustainability considerations: If sustainability is a priority for your organization, inquire about the supplier’s environmental practices and certifications. This may include their waste management processes, use of eco-friendly materials, or compliance with relevant regulations.
By following these tips and considerations, you can streamline the procurement process for custom injection molding and make an informed decision while selecting a supplier.
FAQs on Sourcing and Manufacturing custom injection molding in China
Q1: Why should I consider sourcing and manufacturing custom injection molding in China?
China has become a popular destination for sourcing and manufacturing custom injection molding due to several reasons. Firstly, China offers lower production costs compared to many other countries, making it an attractive option for cost-sensitive businesses. Additionally, the country has a well-established manufacturing infrastructure and a vast network of suppliers, allowing for quick turnaround times and large production capacity. The Chinese market also boasts a wide range of materials, technologies, and machinery, ensuring that businesses can find the right solution for their specific requirements. Finally, China has a pool of skilled labor and experienced engineers, contributing to the ability to produce high-quality custom injection molded products.
Q2: How can I source a reliable custom injection molding supplier in China?
Finding a reliable custom injection molding supplier in China may seem daunting, but it can be done with proper research and due diligence. Start by leveraging online platforms and directories that connect businesses with Chinese suppliers, such as Alibaba or Global Sources. Look for suppliers with a good track record, positive customer reviews, and relevant certifications. It is also recommended to request samples or visit the supplier’s facilities to assess their capabilities and quality standards. When communicating with potential suppliers, ask detailed questions about their manufacturing process, quality control measures, and their experience with similar projects. Finally, consider working with a reputable sourcing agent or partner who has an established network of trusted suppliers and can provide additional support in navigating language and cultural barriers.
Q3: Are there any potential challenges or risks associated with sourcing custom injection molding in China?
While sourcing custom injection molding in China can be advantageous, there are some challenges and risks to consider. One common concern is intellectual property protection, as China has been notorious for intellectual property infringements in the past. To mitigate this risk, it is crucial to establish clear confidentiality agreements and engage in thorough due diligence when selecting a supplier. Language and cultural barriers can also pose challenges during communication and negotiations. Working with a reliable sourcing agent who possesses language skills and local knowledge can help overcome these challenges. Finally, it is essential to conduct proper quality inspections and have a robust quality control process in place to ensure that the final products meet the required standards and specifications.
Q4: What are the payment terms and logistics considerations when sourcing custom injection molding from China?
Payment terms and logistics considerations vary depending on the supplier. Generally, suppliers in China prefer a deposit or initial payment upfront, followed by the balance payment upon completion or before shipment. It is crucial to establish clear payment terms and milestones in the contract to protect both parties’ interests. In terms of logistics, consider the packaging, transportation, and import duties associated with the shipment. Discuss with the supplier and logistics provider to determine the most cost-effective and efficient shipping method, such as air freight or sea freight, and ensure compliance with the necessary import regulations and documentation.
In conclusion, sourcing and manufacturing custom injection molding in China can offer cost advantages, a wide range of options, and large production capacity. However, it is essential to carefully research and select reliable suppliers, address potential challenges related to intellectual property protection and communication, and establish clear payment terms and logistics considerations for a successful partnership.
Why contact sourcifychina.com get free quota from reliable custom injection molding suppliers?
Sourcifychina.com offers a free quota from reliable custom injection molding suppliers for several reasons. Firstly, by providing a free quota, Sourcifychina.com aims to attract potential customers and encourage them to explore the services offered by their platform. This allows customers to assess the reliability and quality of custom injection molding suppliers without incurring any additional costs.
Secondly, Sourcifychina.com understands that finding and vetting reliable custom injection molding suppliers can be a time-consuming and challenging process. By offering a free quota, the platform simplifies this process for customers by connecting them directly with trusted suppliers. This saves customers the effort of conducting extensive research and vetting, ensuring that they only work with reliable suppliers from the outset.
Thirdly, providing a free quota allows customers to compare quotes from different custom injection molding suppliers. This helps them in making informed decisions based on factors such as pricing, manufacturing capabilities, lead times, and quality standards. By offering this service, Sourcifychina.com facilitates a transparent and competitive marketplace, enabling customers to secure the most cost-effective and suitable options for their custom injection molding needs.
Moreover, the free quota from reliable custom injection molding suppliers ensures that customers have access to high-quality manufacturing services at competitive prices. Sourcifychina.com has established relationships with trusted suppliers who have a proven track record of delivering exceptional results. This ensures that customers can have peace of mind, knowing that they are working with reputable suppliers who can meet their specific requirements.
In conclusion, Sourcifychina.com provides a free quota from reliable custom injection molding suppliers to attract customers, simplify the supplier selection process, facilitate comparison, and ensure access to high-quality and competitively priced manufacturing services.