Introduce about custom injection molds guide,Qulity,Cost,Supplier,Certification,Market,Tips,FAQ
A custom injection mold is a specialized tool that is used in the manufacturing process of producing plastic parts through injection molding. This guide aims to provide valuable information regarding the quality, cost, suppliers, certifications, market, tips, FAQs, and other relevant aspects of custom injection molds.
Quality is of utmost importance when it comes to custom injection molds as it directly affects the final product. High-quality molds ensure consistent and precise manufacturing, resulting in durable and accurate plastic parts.
Cost is another essential factor to consider in custom injection molds. The cost of these molds can vary based on factors like complexity, size, material, and quantity. It is crucial to find a balance between the desired quality and cost to make the production process more efficient and cost-effective.
Finding a reliable supplier for custom injection molds is vital. A reputable and experienced supplier can provide guidance, offer various mold design options, and deliver molds that meet the required specifications.
Certifications play a crucial role in the manufacturing industry. It is important to work with suppliers who possess necessary certifications such as ISO 9001 or other quality management system certifications. These certifications ensure that the supplier follows industry standards and adheres to product quality and safety regulations.
The market for custom injection molds is highly competitive and continuously evolving. It is essential to stay updated with the latest technology advancements, market trends, and customer demands to remain competitive.
Here are a few tips for getting the most out of custom injection molds:
1. Collaborate closely with the mold supplier during the design phase to optimize mold performance.
2. Regularly maintain and clean the molds to ensure consistent quality.
3. Conduct mold trials and adjust parameters to achieve desired outcomes.
4. Consider using insert molding or overmolding techniques to enhance product functionality.
Frequently Asked Questions (FAQs) regarding custom injection molds may include queries about mold lifetime, material selection, lead time, mold maintenance, and cost optimization. It is important to address these questions to help customers make informed decisions.
In summary, understanding the aspects of quality, cost, supplier selection, certifications, market trends, tips, and addressing FAQs in custom injection molds guide will assist manufacturers in making informed decisions and ensuring successful production of plastic parts through injection molding.
Types of custom injection molds
Custom injection molds are tools used in the injection molding process to create a wide range of plastic parts or products. These molds are designed and manufactured according to the specific requirements of the product being produced. There are several different types of custom injection molds utilized in various industries. Here are some common types:
1. Prototype molds: These molds are used for creating prototypes of new products. They are made from less expensive materials and are suitable for short production runs. Prototype molds allow product designers to test and refine their designs before mass production.
2. Production molds: These molds are designed for long-term use in large-scale production. They are made from high-quality materials, such as steel or aluminum, to withstand high pressure and frequent use. Production molds are highly precise and durable, ensuring consistent and efficient manufacturing of plastic parts.
3. Hot runner molds: In a hot runner mold, the plastic is injected directly into the mold cavity through a heated runner system. This eliminates the need for runners to cool and solidify with each shot, resulting in reduced cycle times and material wastage. Hot runner molds are commonly used when high productivity and quality are required.
4. Cold runner molds: Unlike hot runner molds, cold runner molds have channels or runners that are not heated. The plastic material is injected into these channels, which cool down and solidify before the part is ejected. Cold runner molds are more economical but may result in longer cycle times and material wastage due to the presence of runners.
5. Insert molds: These molds are used when a part requires inserts, such as metal or other pre-fabricated components, to be embedded or encapsulated during the injection molding process. Insert molds allow for the efficient production of complex parts with multiple materials or components.
6. Family molds: A family mold is designed to produce multiple parts simultaneously in a single molding cycle. It contains multiple cavities arranged in a way that allows for the production of different parts within a single injection process. Family molds enable higher production volumes and reduced manufacturing costs.
Each type of custom injection mold offers specific advantages and is selected based on factors such as production volume, part complexity, cost-effectiveness, and material requirements. The choice of mold type is crucial in determining the success and efficiency of the injection molding process.
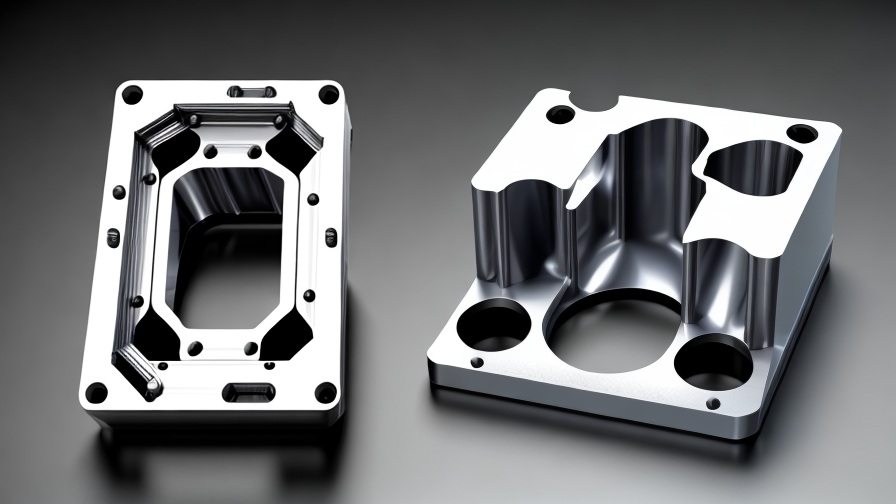
Pros and Cons of Using custom injection molds
Custom injection molds offer several benefits, but they also have certain drawbacks. Let’s explore the pros and cons of using custom injection molds.
One of the key advantages of custom injection molds is their ability to produce complex and precise parts. These molds are designed uniquely for each specific product, ensuring accurate and intricate details. This level of precision is crucial in industries like automotive, medical, and aerospace.
Another benefit of custom injection molds is the potential for cost savings in high-volume production. Once the mold is created, the production costs per part typically decrease as it allows for fast and efficient manufacturing. This makes custom injection molds an attractive option for businesses aiming to reduce production costs in the long run.
The flexibility offered by custom injection molds is also noteworthy. With these molds, manufacturers can easily modify the design or materials used for the parts. Additionally, they can quickly switch to different molds to adapt to changing market demands or to introduce new products. This flexibility enables companies to stay competitive and responsive in dynamic industries.
However, there are certain cons associated with custom injection molds as well. One significant drawback is the high upfront cost and time investment required to create the molds. Designing and manufacturing custom injection molds can be expensive and time-consuming, especially for complex products with intricate details. This cost may pose a barrier for small businesses or startups with limited resources.
Another disadvantage arises from the fact that custom injection molds are typically designed for high-volume production. If a company requires only a small quantity of parts, the cost per unit may become prohibitively high due to the fixed expenses associated with creating custom molds.
Furthermore, changes in design or materials can lead to additional costs and delays in production. Modifying custom injection molds is not always a quick or straightforward process, especially if substantial changes are required. This can slow down production timelines and impact a company’s ability to respond swiftly to market demands.
In conclusion, custom injection molds offer precise and complex part production, cost savings in high-volume manufacturing, and flexibility for design changes. However, their high upfront cost, limited suitability for small-scale production, and potential delays in modifying molds must also be considered. Ultimately, businesses must carefully evaluate their specific needs and production requirements to determine if custom injection molds are the right choice for them.
custom injection molds Reference Specifications (varies for different product)
In the world of manufacturing, custom injection molds play a crucial role in bringing products to life. These molds are specifically designed and fabricated to create intricate and precise shapes for various products, ranging from automotive parts to consumer goods.
When it comes to creating custom injection molds, it is important to follow specific reference specifications. These specifications can vary depending on the product being manufactured, but they typically include detailed guidelines that dictate the design, material, and tolerance requirements.
The reference specifications for custom injection molds outline the dimensions, surface finish, and particular features of the intended product. This ensures that the mold is tailored to meet the exact requirements of the final product, resulting in consistent and high-quality output.
Design is a critical component of the reference specifications for custom injection molds. It provides information on the parting line, gating, and runner systems, which are essential for proper material flow throughout the mold cavity. Additionally, the design specifications may include provisions for the ejection system, cooling channels, and other necessary features to facilitate efficient manufacturing processes.
Material selection is another critical consideration in custom injection mold specifications. The reference specifications outline the appropriate type of material to be used, taking into account factors such as the product’s function, durability, and dimensional stability requirements. The chosen material should be compatible with the injection molding process and able to withstand the demands of production.
Tolerance requirements are also an integral part of custom injection mold specifications. These specifications define the allowable variations in dimensions, ensuring that the molded products meet the required precision and fitment standards. Tolerance specifications contribute to the overall quality and functionality of the final product by minimizing dimensional errors.
In summary, reference specifications for custom injection molds are essential in manufacturing products with precision and consistency. These specifications provide guidelines for the design, material selection, and tolerance requirements necessary to produce high-quality molded parts. By adhering to these specifications, manufacturers can ensure that their custom injection molds are optimized for the specific products they are producing.
Applications of custom injection molds
Custom injection molds are widely used in various industries to produce unique and specialized products. These molds are specifically designed to meet the requirements and specifications of a particular product, ensuring efficiency and precision in the production process. Here are some key applications of custom injection molds:
1. Automotive Industry: Custom injection molds play a crucial role in the automotive industry, where complex and intricate components are required. From interior parts like dashboards and door panels to exterior parts like bumpers and grills, injection molds enable the production of high-quality, durable, and precise automotive components.
2. Medical and Healthcare Industry: Injection molding is extensively used in the medical field for manufacturing a wide range of equipment, devices, and disposable products. Custom molds enable the production of medical components such as syringes, IV catheters, surgical instruments, and prosthetics with medical-grade materials, ensuring strict adherence to quality and safety standards.
3. Consumer Goods: Many consumer goods rely on custom injection molds for their production. This includes items such as kitchen appliances, toys, electronic enclosures, packaging containers, and cosmetic products. The flexibility of custom molds allows for the creation of intricate designs and shapes, meeting the aesthetic and functional requirements of consumer goods.
4. Aerospace Sector: The aerospace industry demands precision-engineered components that can withstand extreme conditions. Custom injection molds are used to produce lightweight yet strong aerospace parts like aircraft interiors, engine components, and structural frames. These molds ensure the production of parts that are durable, cost-effective, and meet the strict standards set by the aerospace industry.
5. Electronics Industry: Custom injection molds are vital for the efficient production of various electronic components. This includes parts like connectors, switches, circuit boards, and casings for electronic devices. Molds designed specifically for the electronics industry enable the production of intricate and compact parts, ensuring the proper functioning of electronic devices.
In summary, custom injection molds offer a wide range of applications in various industries. From automotive and medical sectors to consumer goods and electronics industries, these molds allow for the production of high-quality, precise, and specialized components. They play a vital role in enhancing production efficiency, meeting industry standards, and fulfilling unique product requirements.
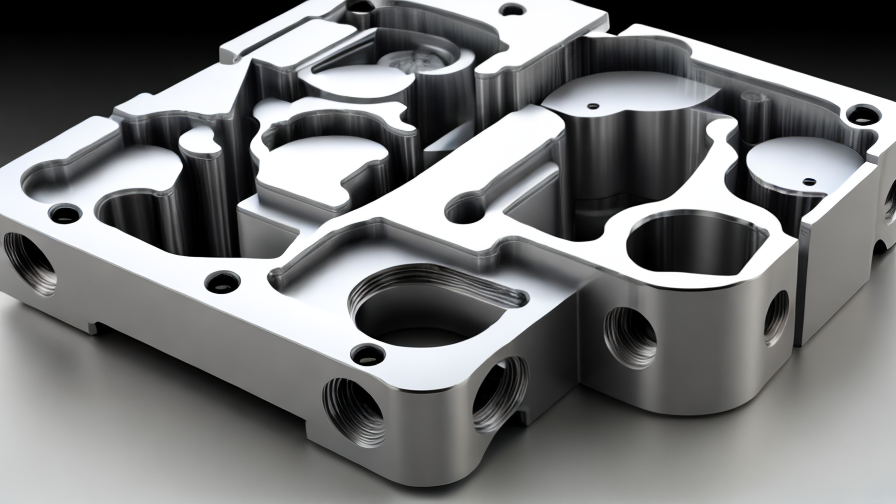
The Work Process and how to use custom injection molds
The work process of using custom injection molds involves several steps, starting from the design phase and culminating in the production of the desired product. Here is a brief overview of the process:
1. Design: The first step involves creating a design for the product that needs to be manufactured using injection molding. This design is usually created using computer-aided design (CAD) software.
2. Mold Creation: Once the design is finalized, a mold is created based on the design specifications. The mold is usually made from steel or aluminum and consists of two halves, known as the core and cavity.
3. Mold Preparation: Before the injection process begins, the mold needs to be prepared. This typically involves cleaning the mold and ensuring that it is free from any debris or contaminants.
4. Injection: The injection molding machine is set up, and the appropriate plastic material, known as the resin, is fed into the machine. The resin is heated until it reaches its melting point.
5. Injection Molding: Once the resin is melted, it is injected into the mold cavity under high pressure using a reciprocating screw. The pressure is maintained for a specific period to allow the resin to cool and solidify.
6. Ejection: After the resin has solidified, the mold is opened, and the product is ejected. Ejection can be achieved through various methods, such as using ejector pins or air blasts.
7. Finishing: The final step involves removing any excess material, such as flash or sprue, from the finished product. This may require additional trimming or polishing.
Using custom injection molds offers several advantages, including high production efficiency, repeatability, and cost-effectiveness for large quantities. The molds can be customized according to specific product requirements, allowing for the production of complex shapes and intricate details.
In conclusion, the work process of using custom injection molds involves designing the product, creating the mold, preparing the mold, injecting the resin, ejecting the product, and finishing. Custom injection molds provide a reliable and efficient method for manufacturing various plastic products.
Quality Testing Methods for custom injection molds and how to control the quality
Quality testing methods for custom injection molds are essential to ensure that the molds meet the required standards and specifications. Controlling the quality of these molds is crucial to prevent defects and ensure overall product quality. Some commonly used methods for quality testing of custom injection molds include:
1. Visual Inspection: This involves visually examining the mold for any visible defects such as cracks, scratches, or improper surface finishes. It helps identify any visible abnormalities that may affect the mold’s performance.
2. Dimensional Analysis: This method involves measuring critical dimensions of the mold components using calibrated tools such as calipers, micrometers, or CNC machines. It helps ensure that the mold components are within the specified tolerance limits.
3. Mold Flow Analysis: This involves using specialized software to simulate the injection molding process. It helps identify potential flow-related issues such as air traps, weld lines, or excessive pressure variations. Mold flow analysis allows for design optimizations to improve part quality and mold performance.
4. Mechanical Testing: This method involves conducting mechanical tests on mold materials, such as hardness testing or tensile testing. These tests help ensure that the materials used in the mold construction meet the required mechanical properties and can withstand the stresses of the injection molding process.
5. Sample Production and Verification: Producing a limited number of sample parts using the mold helps evaluate the overall quality and functionality of the mold. These sample parts are then verified against the required specifications, including dimensional accuracy, surface finish, and functionality.
To control the quality of custom injection molds, several measures can be implemented:
1. Thorough Design Review: Conducting a comprehensive design review can help identify potential design flaws or areas for improvement before manufacturing the molds.
2. Material Selection: Choosing high-quality and appropriate materials for mold construction is vital to ensure durability and performance during the injection molding process.
3. Regular Maintenance: Regularly inspecting and maintaining the molds throughout their lifetime helps prevent wear and tear, ensuring consistent and reliable performance.
4. Process Monitoring: Implementing process monitoring techniques such as statistical process control (SPC) helps identify any process variations or deviations that may affect the mold quality. It enables timely corrective actions to maintain consistent quality.
5. Documentation and Traceability: Maintaining detailed documentation throughout the mold’s lifecycle, including design changes, maintenance records, and testing results, ensures traceability and facilitates quality control.
By employing these quality testing methods and implementing effective quality control measures, manufacturers can ensure the production of high-quality custom injection molds that meet the required specifications, minimizing defects, and ensuring overall product quality.
custom injection molds Sample Policy and Post-Purchase Considerations for custom injection molds from China
Sample Policy:
When purchasing custom injection molds from China, it is common for suppliers to provide sample products before finalizing the order. The purpose of this sample policy is to ensure that the molds meet the buyer’s requirements and specifications. Here are some key points to consider:
1. Sample cost: Buyers may be required to cover the cost of the sample molds, including the tooling and manufacturing costs. However, some suppliers may offer a discount or waive the sample cost if the buyer proceeds with the order.
2. Sample lead time: Suppliers in China usually require a certain lead time to produce the samples. This lead time includes the time for mold design, tooling, molding, and shipping. It is important for the buyer to discuss and agree upon the sample lead time with the supplier.
3. Sample approval: Once the samples are received, the buyer should thoroughly evaluate them to ensure that they meet the desired specifications. It is essential to communicate any necessary modifications or improvements to the supplier. If the samples are approved, the buyer can proceed with the order.
Post-Purchase Considerations:
After the purchase of custom injection molds from China, several considerations should be kept in mind for a smooth production process. Here are a few important points:
1. Quality control: It is critical to establish a robust quality control system to ensure consistent and reliable mold production. This can include regular inspections, testing, and the monitoring of production processes. Collaborating closely with the supplier during production can help address any quality issues promptly.
2. Effective communication: Timely and clear communication with the supplier is essential in addressing concerns or changes during the production process. This includes providing detailed specifications, design revisions, and production updates. Regular communication can help prevent misunderstandings and potential delays.
3. Shipping and logistics: Coordinating shipping and logistics should be discussed and agreed upon with the supplier. This includes determining the shipping method, freight forwarder, and any necessary import/export documentation. Proper planning will help ensure the molds arrive on time and in good condition.
In conclusion, when purchasing custom injection molds from China, it is important to follow a sample policy to ensure the molds meet requirements. Additionally, maintaining effective communication and implementing quality control measures are crucial post-purchase considerations for a successful production process.
Sourcing custom injection molds from China: Opportunities, Risks, and Key Players
Sourcing custom injection molds from China presents both opportunities and risks for businesses. On one hand, China is known for its cost-efficient manufacturing capabilities, making it an attractive option for companies looking to produce injection molds at a lower cost. Additionally, China has a vast network of experienced mold makers and manufacturers, providing a wide range of options for custom molds.
However, there are also risks associated with sourcing from China. Quality control can be a concern, as there have been instances of substandard molds being produced. Language and communication barriers may also pose challenges, as effective communication is crucial for ensuring the desired specifications and requirements are met.
Despite the risks, several key players have emerged in the Chinese market for custom injection molds. One such player is Taizhou Huangyan Jmt Mould, a leading manufacturer with expertise in producing high-quality molds for various industries. Jmt Mould has a strong reputation for its precision molds and offers comprehensive services, including mold design, manufacturing, and inspection.
Another reputable player is Sino Mould, which specializes in manufacturing injection molds for a wide range of applications, such as automotive parts, home appliances, and medical equipment. Sino Mould has a strong emphasis on quality control and has implemented strict inspection processes to ensure the molds meet international standards.
Additionally, Dongguan Yuansheng Plastic Co., Ltd., is a notable manufacturer known for its expertise in producing molds for the electronics industry. With a focus on precision and high-quality molds, Yuansheng Plastic has established long-standing partnerships with clients worldwide.
While these are just a few examples, it is crucial for businesses to thoroughly research and evaluate potential mold manufacturers in China before making a final decision. Conducting due diligence, including requesting samples and conducting factory audits, can help mitigate risks and ensure a successful sourcing experience.
How to find and select reliable custom injection molds manufacturers in China,use google search manufacturers and suppliers
When searching for reliable custom injection molds manufacturers in China, utilizing Google search can be a valuable tool. Here’s a step-by-step guide to help you find and select the right manufacturers:
1. Start by typing relevant keywords into the search bar on Google, such as “custom injection molds manufacturers China” or “reliable injection molds suppliers in China.” This will generate a list of potential manufacturers to explore.
2. Visit the websites of the manufacturers that appear on the search results page. Look for information about their experience, expertise, capabilities, certifications, and customer reviews. Focus on manufacturers with a good reputation and extensive experience in producing high-quality injection molds.
3. Check if the manufacturer provides comprehensive product details, including the types of materials they can work with, production capacity, lead times, and quality control processes.
4. Look for any industry certifications or affiliations that signify the manufacturer’s commitment to quality. These could include ISO certifications, memberships in trade associations, or compliance with international standards.
5. Contact the manufacturers directly to request more information, such as their product catalog, samples, and pricing. Pay attention to their response time and willingness to assist you. Prompt and professional communication is an important indicator of reliability.
6. Ask for references from the manufacturer’s existing clients or inquire if they can provide case studies that demonstrate their capabilities and successful projects. This will help you gauge their track record and customer satisfaction.
7. Consider visiting trade shows or exhibitions related to injection molding to meet manufacturers in person, gather more information, and assess the quality of their products firsthand.
8. Evaluate multiple manufacturers and compare their offerings, pricing, lead times, and customer support. It’s essential to have several options to make an informed decision.
9. Lastly, before finalizing your choice, consider visiting the facilities of your shortlisted manufacturers if feasible. This will give you an opportunity to assess their manufacturing processes, quality control measures, and overall capability.
By following these steps and utilizing Google search, you can find and select reliable custom injection molds manufacturers in China. Remember to choose manufacturers with a proven track record, excellent customer reviews, comprehensive product information, and clear communication channels to ensure a successful partnership.
How to check custom injection molds manufacturers website reliable,use google chrome SEOquake check if ranking in top 10M
When evaluating the reliability of a custom injection molds manufacturer’s website, you can follow these steps:
1. Use Google Chrome: Open the manufacturer’s website using Google Chrome browser as it offers useful extensions for conducting website analysis.
2. Install SEOquake: Install the SEOquake extension from the Chrome Web Store. It is a powerful tool that provides a range of metrics and insights about a website’s performance.
3. Conduct a search: Go to Google and search for the manufacturer’s specific keywords or phrases to see if their website ranks among the top 10 million websites.
4. Evaluate the results: Once the search results appear, SEOquake will display key metrics like the Alexa Rank, Google Index, and SEMrush Rank for the manufacturer’s website. If the website ranks within the top 10 million, it shows that it receives a decent amount of traffic and is likely more reliable.
5. Look for other trust indicators: Also, consider other trust indicators like customer reviews, testimonials, certifications, or industry affiliations mentioned on the website. These elements can provide additional insights into the manufacturer’s reputation and reliability.
By following these steps and utilizing the SEOquake extension in Google Chrome, you can quickly assess the reliability of a custom injection molds manufacturer’s website. Remember to take into account any other available trust indicators to make a well-informed decision.
Top 10 custom injection molds manufacturers in China with each 160 words introduce products,then use markdown create table compare
1. Yuyao Yuanda Mould Co., Ltd.: Specializing in the development and production of custom injection molds, Yuyao Yuanda Mould Co., Ltd. offers a wide range of products such as bottle caps, medical equipment components, and automotive parts. With over 20 years of experience, they provide high-quality molds that are known for their precision and durability.
2. Taizhou Huangyan Deying Mould Co., Ltd.: Deying Mould Co., Ltd. is a well-established manufacturer of custom injection molds in China. They offer a diverse range of products, including household appliances, office supplies, and industrial components. With advanced manufacturing techniques and strict quality control processes, they consistently deliver molds that meet or exceed customer expectations.
3. Higrade Mold Group: Higrade Mold Group is a leading manufacturer of custom injection molds in China, catering to various industries such as automotive, electronics, and medical. Their products include precision molds for intricate parts, multi-cavity molds for mass production, and hot runner molds for high efficiency. They prioritize customer satisfaction and ensure the timely delivery of quality molds.
4. Bait Mold Industrial Limited: Bait Mold Industrial Limited specializes in producing custom injection molds for fishing lures. With comprehensive design capabilities and advanced manufacturing equipment, they offer a wide variety of fishing lure molds, including soft bait molds, hard bait molds, and jigging spoon molds. Their molds are highly sought after by fishing enthusiasts and professionals worldwide.
5. Huida Plastic Mould Factory: Huida Plastic Mould Factory is a renowned manufacturer of custom injection molds in China, mainly serving the automotive industry. They specialize in producing molds for automotive interior and exterior parts, such as bumpers, dashboard components, and door panels. With a strong focus on precision and efficiency, they have gained a reputation for delivering high-quality molds.
| **Manufacturer** | **Specialization** | **Products** | **Key Features** |
|—|—|—|—|
| Yuyao Yuanda Mould Co., Ltd. | Custom injection molds | Bottle caps, medical equipment components, automotive parts | Precision and durability |
| Taizhou Huangyan Deying Mould Co., Ltd. | Custom injection molds | Household appliances, office supplies, industrial components | Advanced manufacturing techniques |
| Higrade Mold Group | Custom injection molds | Automotive, electronics, medical | Precision molds, multi-cavity molds, hot runner molds |
| Bait Mold Industrial Limited | Fishing lure molds | Soft bait molds, hard bait molds, jigging spoon molds | Comprehensively designed fishing lures |
| Huida Plastic Mould Factory | Custom injection molds | Automotive interior, exterior parts | Focus on precision and efficiency |
6. Dongguan Yixun Industrial Co., Ltd.: Dongguan Yixun Industrial Co., Ltd. is recognized for its custom injection molds used in the electronics industry. They provide molds for components such as connectors, switches, and housings. With their advanced technology and expertise, they ensure the precise molding of intricate electronic parts.
7. Focare Mould Co., Ltd.: Focare Mould Co., Ltd. is a leading manufacturer of custom injection molds for the medical industry. They specialize in producing molds for medical devices, such as syringes, vials, and IV components. Quality and cleanroom standards are prioritized to ensure the safety and reliability of the final products.
8. Shiny Tool & Mould Co., Ltd.: Shiny Tool & Mould Co., Ltd. offers high-quality custom injection molds for the automotive industry. They provide molds for various automotive parts, including interior trims, door handles, and mirror covers. Their molds are designed to meet stringent industry standards and can withstand high production volumes.
9. Runma Injection Molding Robot Arm Co., Ltd.: Runma Injection Molding Robot Arm Co., Ltd. specializes in the development and manufacturing of injection molding robot arms. Their products include single-axis robot arms, double-axis robot arms, and multi-axis robot arms. These robot arms are designed to enhance the automation and efficiency of injection molding processes.
10. Shanghai Siage Precision Mould Made Co., Ltd.: Shanghai Siage Precision Mould Made Co., Ltd. focuses on producing high-precision custom injection molds for electronic products. They manufacture molds for components such as connectors, sensors, and PCBs. With their state-of-the-art equipment and expertise, they deliver molds that meet exact specifications and ensure precise product assembly.
| **Manufacturer** | **Specialization** | **Products** | **Key Features** |
|—|—|—|—|
| Dongguan Yixun Industrial Co., Ltd. | Custom injection molds | Electronic components | Precise molding of intricate parts |
| Focare Mould Co., Ltd. | Custom injection molds | Medical devices | Quality and cleanroom standards |
| Shiny Tool & Mould Co., Ltd. | Custom injection molds | Automotive parts | Meets industry standards, withstands high production volumes |
| Runma Injection Molding Robot Arm Co., Ltd. | Injection molding robot arms | Single-axis, double-axis, multi-axis robot arms | Enhances automation and efficiency |
| Shanghai Siage Precision Mould Made Co., Ltd. | Custom injection molds | Electronic components | High precision, meets exact specifications |
In conclusion, these top 10 custom injection molds manufacturers in China cover an extensive array of industries and applications. They provide high-quality molds with specialized features that cater to the unique needs of each sector. Whether it’s automotive, medical, electronics, or fishing, these manufacturers offer reliable and efficient solutions to their clients.
Background Research for custom injection molds manufacturers Companies in China, use qcc.com archive.org importyeti.com
When looking for custom injection mold manufacturers in China, it is essential to conduct thorough background research on potential companies to ensure their credibility, reliability, and ability to meet your requirements. Several online platforms can facilitate this research, such as qcc.com, archive.org, and importyeti.com.
Qcc.com is a Chinese business directory that provides comprehensive company information. By utilizing this platform, you can obtain valuable insights into a manufacturer’s registration details, legal status, financial records, and key personnel. These details can help you gauge a company’s reputation and longevity within the industry.
Archive.org is a digital archive that allows you to access historical versions of websites. This can be a useful tool to track a manufacturer’s online presence over time and check for consistency in their claims and offerings. By reviewing older versions of a manufacturer’s website, you can gain insights into their evolution, growth, and any changes in their product portfolio or services.
Importyeti.com is an online platform that provides import and export data for various products. By utilizing this platform, you can gather valuable information on a manufacturer’s export history, including their key markets, shipment volumes, and customers. This data can help you ascertain a company’s experience in exporting and their success in serving international clients.
When conducting background research, it is crucial to consider multiple sources and cross-validate the information to ensure its accuracy and reliability. Utilizing platforms like qcc.com, archive.org, and importyeti.com can provide a comprehensive understanding of a custom injection mold manufacturer’s background, reputation, and capabilities in China.
Leveraging Trade Shows and Expos for custom injection molds Sourcing in China
Trade shows and expos can be incredibly valuable for sourcing custom injection molds in China. These events provide a unique opportunity to connect with a wide range of manufacturers, suppliers, and industry experts all in one place. Here’s how you can leverage trade shows and expos to find the right partner for your custom injection molds sourcing needs:
1. Extensive Supplier Network: Trade shows and expos attract a diverse range of suppliers and manufacturers specializing in various industries. By attending these events, you can explore a large number of potential sourcing partners in a short period. This allows you to compare different options and find the most suitable custom injection mold supplier according to your specific requirements.
2. Face-to-Face Interaction: Meeting suppliers face-to-face offers numerous advantages. It enables you to establish personal connections, ask detailed questions, and evaluate their capabilities and expertise. You can discuss your project in-depth, provide samples, and receive immediate feedback. This direct interaction can significantly save time and ensure better alignment between your needs and the capabilities of the injection mold supplier.
3. Quality Control: When sourcing custom injection molds, quality is of utmost importance. Trade shows and expos often showcase manufacturers with a proven track record of producing high-quality molds. By inspecting their product displays and discussing their manufacturing processes, you can assess the suppliers’ quality control measures and ensure adherence to your standards.
4. Innovation and Technology: Trade shows and expos are hubs of innovation and technological advancements. Attending these events allows you to stay updated on the latest trends and advancements in the injection molding industry. You can explore new materials, technologies, and techniques that can enhance the quality, efficiency, and cost-effectiveness of your custom mold production.
5. Industry Insights: In addition to the product displays, trade shows and expos also host presentations, seminars, and discussions on industry-related topics. Attending these sessions can provide valuable insights into the injection molding industry, market trends, and potential challenges. These insights can inform your decision-making and help you make informed choices when selecting a supplier.
In conclusion, trade shows and expos offer a valuable platform for sourcing custom injection molds in China. They provide access to a wide range of suppliers, facilitate face-to-face interactions, enable quality control assessment, showcase innovative technologies, and offer industry insights. By leveraging these events, you can find the right partner for your custom injection molds sourcing needs efficiently.
The Role of Agents and Sourcing Companies in Facilitating custom injection molds Purchases from China
Agents and sourcing companies play a crucial role in facilitating custom injection molds purchases from China. They act as a bridge between overseas buyers and Chinese manufacturers, ensuring a smooth and efficient procurement process.
One of the primary responsibilities of agents and sourcing companies is to identify reputable manufacturers in China that specialize in injection molding. They have extensive networks and partnerships with various suppliers, enabling them to match the specific requirements of buyers with the capabilities of manufacturers. This saves time and effort for buyers who may otherwise struggle to find suitable suppliers independently.
Agents and sourcing companies also provide valuable assistance in negotiating prices and terms. They have in-depth knowledge of the market and are skilled in navigating the complexities of doing business in China. This allows them to secure competitive prices and ensure that buyers receive the best value for their money.
Additionally, agents and sourcing companies help facilitate communication between buyers and manufacturers. They act as translators, ensuring that all specifications and requirements are accurately conveyed to the manufacturers. This eliminates misunderstandings that could arise due to language and cultural barriers.
Quality control is another critical aspect that agents and sourcing companies handle. They have experience in assessing and inspecting the manufacturing processes and final products to ensure that they meet the desired standards. This helps buyers avoid potential quality issues and minimize the risk of receiving subpar injection molds.
Furthermore, agents and sourcing companies offer logistical support. They can assist with arranging shipping and customs clearance, ensuring that the products are delivered to the buyers’ location in a timely manner. This simplifies the entire procurement process and allows buyers to focus on their core business activities.
In summary, agents and sourcing companies play a crucial role in facilitating custom injection molds purchases from China. They provide a range of services, including identifying suitable manufacturers, negotiating prices, facilitating communication, conducting quality control, and handling logistics. Their expertise and knowledge of the Chinese market help streamline the procurement process and ensure successful outcomes for buyers.
Price Cost Research for custom injection molds manufacturers Companies in China, use temu.com and 1688.com
When it comes to finding custom injection mold manufacturers in China, two popular platforms to explore are temu.com and 1688.com. These online marketplaces offer a vast array of suppliers that cater to different industries and product needs. Conducting price and cost research on these platforms can help you make informed decisions about your manufacturing requirements.
Temu.com, a global B2B platform, allows users to source custom injection mold manufacturers from China. It provides a comprehensive search system that enables you to filter results based on your specific criteria, such as mold type, material, quantity, and more. Through this platform, you can directly communicate with manufacturers and negotiate prices to ensure the best deal for your project.
1688.com, on the other hand, is a Chinese B2B marketplace and a subsidiary of Alibaba Group. While the site is predominantly available in Chinese, it offers a wide range of suppliers specializing in custom injection molds. It features detailed product descriptions, customer reviews, and pricing information on various mold manufacturers. By utilizing translation tools or seeking assistance, you can navigate and communicate effectively on this platform to find suitable solutions for your injection molding needs.
When conducting price and cost research on both platforms, it is essential to consider several factors. These include the complexity of the mold design, the type and quality of materials used, production quantities, customization requirements, and any additional services offered, such as mold maintenance or repair.
By requesting quotes and evaluating multiple manufacturers, you can compare their prices, services, and capabilities to identify the most cost-effective and reliable supplier for your custom injection mold project.
In summary, leveraging temu.com and 1688.com allows you to access a wide array of custom injection mold manufacturers in China. By conducting thorough price and cost research, considering factors specific to your project, and comparing quotes, you can find a suitable manufacturer that meets your budget and quality requirements.
Shipping Cost for custom injection molds import from China
The shipping cost for custom injection molds imported from China can vary based on several factors. These factors include the size and weight of the molds, the shipping method chosen, and the destination country.
Generally, there are two ways to ship injection molds from China: air freight and ocean freight. Air freight is the faster option but can be more expensive. On the other hand, ocean freight is more cost-effective but takes longer.
For smaller molds or urgent shipments, air freight is usually the preferred option. The cost of air freight can range from $4 to $10 per kilogram, depending on the carrier and other factors such as the volume of the shipment. Additionally, there may be additional charges for customs clearance, handling fees, and insurance.
For larger molds or non-urgent shipments, ocean freight is more suitable. The cost of ocean freight is typically calculated based on the volume or cubic meters (CBM) of the shipment. On average, ocean freight can range from $500 to $1,500 per CBM, depending on the shipping line, season, and destination. Similarly, additional charges such as customs clearance and handling fees may apply.
It is important to note that these costs are approximate and can vary depending on various factors. Working with a reliable freight forwarder or shipping agent can help in obtaining accurate shipping quotes and managing the logistics efficiently. Additionally, ensuring proper packaging and documentation for customs clearance can help avoid any potential delays or extra costs.
In conclusion, the shipping cost for custom injection molds imported from China depends on factors such as size, weight, shipping method, and destination. Estimating the shipping cost accurately can help in budgeting and planning the import process effectively.
Compare China and Other custom injection molds Markets: Products Quality and Price,Visible and Hidden Costs
China is one of the largest players in the global custom injection molds market, and it competes with other countries like the United States, Germany, and Japan. When comparing China with other markets, several factors come into play, including product quality and price, visible and hidden costs.
In terms of product quality, China has made significant strides over the years. Many Chinese manufacturers now offer high-quality custom injection molds that meet international standards. However, it is crucial to note that quality can vary among different suppliers. Other market players like the United States, Germany, and Japan also have a reputation for producing top-quality products. In terms of strict quality control, these countries may have an edge over China. However, China’s focus on continuous improvement and technology adoption has gradually closed this gap.
Price is a significant factor for many buyers, and China often offers lower prices compared to other markets. The manufacturing cost in China is relatively lower due to factors such as lower labor costs and a vast industrial base. This cost advantage enables Chinese suppliers to offer competitive prices for custom injection molds. Other markets like the United States, Germany, and Japan tend to have higher manufacturing costs, which can reflect in higher prices for their products.
Visible costs, such as production and transportation costs, are relatively easy to compare between different markets. However, hidden costs need careful consideration. China’s hidden costs primarily involve intellectual property protection and supply chain risks. Intellectual property theft is still a concern in China, and buyers need to take measures to protect their product designs and proprietary information. Additionally, supply chain risks, such as delays and quality issues, can be more prevalent in China due to its complex network of suppliers.
In summary, China’s custom injection molds market offers a combination of competitive prices and improving product quality. It has become a strong contender against other market players like the United States, Germany, and Japan. However, buyers need to assess visible and hidden costs to make informed decisions. While China may have advantages in terms of cost, other markets may have an edge in product quality and intellectual property protection. Ultimately, buyers should carefully evaluate their specific requirements and assess the strengths and weaknesses of each market before making a decision.
Understanding Pricing and Payment Terms for custom injection molds: A Comparative Guide to Get the Best Deal
Pricing and payment terms for custom injection molds can vary significantly depending on several factors, including the complexity of the design, the size and quantity of the mold, and the materials used. It is crucial to negotiate the best deal to ensure a cost-effective and successful injection molding project. Here is a comparative guide to understanding pricing and payment terms for custom injection molds:
1. Design Complexity: The more intricate and complex the design, the higher the cost. Mold manufacturers will consider factors such as part complexity, undercuts, and tight tolerances when determining the price.
2. Mold Size and Quantity: Larger molds and higher quantities generally command higher prices due to increased material and production costs. However, some manufacturers offer discounts for larger orders or long-term partnerships.
3. Material Selection: Different mold materials, such as steel or aluminum, have varying costs. Steel molds are more durable but expensive, whereas aluminum molds are cheaper but have a shorter lifespan. Consider the expected production volume and part requirements when selecting mold materials.
4. Mold Maintenance and Repairs: Inquire about the manufacturer’s warranty, maintenance, and repair services. Some manufacturers offer free or discounted mold maintenance to ensure prolonged mold life and consistent part quality.
5. Payment Terms: Understand the payment structure proposed by mold manufacturers. Typically, a down payment is required to start mold production, followed by installment, milestone-based payments, or a lump sum upon completion. Negotiate payment terms that offer flexibility while protecting your interests.
6. Additional Costs: Inquire about any additional costs not included in the initial quote, such as shipping, taxes, or packaging. These costs can significantly impact the overall project budget.
7. Comparing Multiple Quotes: Obtain quotes from multiple mold manufacturers and compare them carefully. Ensure that all quotes are providing similar specifications and quality standards for an accurate price comparison. Evaluate the reputation, experience, and customer references of each manufacturer as well.
In conclusion, understanding the pricing and payment terms for custom injection molds is essential to secure the best deal. Consider design complexity, mold size and quantity, material selection, maintenance services, payment terms, and additional costs. Be diligent in comparing multiple quotes to make an informed decision and maximize the value of your investment in custom injection molds.
Chinese Regulations and Industry Standards Certifications for custom injection molds,Import Regulations and Customs for custom injection molds from China
When it comes to custom injection molds, China has certain regulations and industry standards certifications in place to ensure the quality and safety of these products.
One of the key regulations is the GB/T 19001-2016/ISO 9001:2015 certification, which focuses on quality management systems. This certification demonstrates that the manufacturer has implemented a set of standardized processes and practices to consistently deliver high-quality custom injection molds.
In addition, the GB/T 19022-2016/ISO 14001:2015 certification addresses environmental management systems. It ensures that the manufacturer has effective procedures in place to minimize environmental impacts during the production and disposal of injection molds.
Chinese industry standards related to custom injection molds encompass various aspects, such as design, materials, dimensions, performance, and testing methods. Some prominent standards include GB/T 14486-2016, which specifies the requirements for injection molds used in thermoplastic molding, and GB/T 19658-2015, which focuses on the design and manufacturing requirements for large-scale injection molds.
Importing custom injection molds from China involves adhering to certain regulations and customs procedures. Importers need to provide the necessary documentation, including a commercial invoice, packing list, and bill of lading or airway bill. Customs authorities will inspect these documents to ensure compliance with import regulations and proper valuation of the goods.
It’s important to note that importers may also need to comply with additional regulations depending on the specific characteristics of the injection molds, such as product safety certifications or conformity assessments.
In conclusion, Chinese regulations and industry standards certifications play a crucial role in ensuring the quality and safety of custom injection molds. Importers should familiarize themselves with the required documentation and customs procedures to successfully import these products from China.
Sustainability and Environmental Considerations in custom injection molds Manufacturing
Sustainability and environmental considerations play a crucial role in the manufacturing of custom injection molds. By implementing environmentally friendly practices, manufacturers can reduce their environmental impact, improve energy efficiency, and promote sustainability.
One key aspect of sustainable custom injection mold manufacturing is the choice of materials. Manufacturers are encouraged to opt for eco-friendly and recyclable materials for their molds. Using materials that have a minimal environmental footprint and can be recycled or reused at the end of their life cycle reduces waste and conserves resources.
Additionally, manufacturers need to adopt energy-efficient manufacturing processes. By implementing measures such as optimizing machine settings, using energy-efficient equipment, and minimizing energy consumption during production, manufacturers can significantly reduce their carbon footprint. Investing in modern and energy-efficient machinery can also ensure better resource utilization, resulting in cost savings and reduced environmental impact.
Another important factor to consider is waste management. Effective waste management practices involve reducing, reusing, and recycling waste generated throughout the manufacturing process. For instance, manufacturers can implement recycling programs to process plastic waste or recondition molds for reuse. Additionally, they can explore options for composting organic waste to minimize environmental harm.
Furthermore, custom injection mold manufacturers can foster sustainability by implementing lean manufacturing principles. By streamlining production processes, reducing unnecessary material usage, and optimizing workflows, manufacturers can minimize waste, improve efficiency, and reduce their overall environmental impact.
It is also essential for manufacturers to prioritize research and development to explore innovative techniques and materials that are more sustainable and environmentally friendly. By collaborating with experts and investing in research, manufacturers can discover novel solutions that maximize resource utilization, minimize waste generation, and promote long-term sustainability.
In conclusion, sustainability and environmental considerations in custom injection mold manufacturing are critical for minimizing environmental impact, reducing waste, and promoting long-term sustainability. By choosing eco-friendly materials, optimizing energy consumption, adopting efficient waste management practices, implementing lean manufacturing principles, and investing in research and development, manufacturers can make significant strides towards a greener and more sustainable future.
List The Evolution history of “custom injection molds”
Custom injection molds have a rich and fascinating history that has evolved significantly over time. Understanding the evolution of these molds helps us appreciate the advancements in manufacturing techniques that have revolutionized the process.
The history of custom injection molds dates back to the mid-19th century when the process of injection molding was first experimented with. Initially, molds were simple and made of metal or wood, limiting their application to basic shapes. The molds were manually operated and required time-consuming adjustments for each product. This method was labor-intensive and had limited efficiency.
In the early 20th century, the introduction of thermoplastics opened up new possibilities for custom injection molds. This led to the development of more complex molds that could be used repeatedly for manufacturing products with greater precision. The advent of plastic injection molding machines in the 1940s further revolutionized the process by automating the injection of molten plastic into the molds, improving both speed and accuracy.
As technology advanced, the materials used to manufacture custom injection molds also evolved. Steel became the preferred material due to its durability and resistance to wear and tear. Additionally, with the introduction of computer-aided design (CAD) and computer numerical control (CNC) machining in the 1970s, the precision and detail of custom injection molds reached new heights.
In recent decades, the widespread adoption of 3D printing has ushered in a new era for custom injection molds. The ability to create molds quickly and inexpensively using 3D printing technology has dramatically reduced lead times and costs associated with mold production. With advancements in materials, including high-performance thermoplastics, custom injection molds can now withstand higher temperatures and pressures, enabling the production of more complex and durable products.
Furthermore, developments in mold design software and simulation tools have allowed manufacturers to optimize mold designs for cost-efficiency and product quality. Additive manufacturing techniques, such as conformal cooling, have also been incorporated into custom injection molds, improving cycle times and reducing part defects.
Today, custom injection molds play a crucial role in a wide range of industries, including automotive, aerospace, medical, and consumer goods. With ongoing advances in materials, technology, and design capabilities, the future of custom injection molds holds the promise of even greater efficiency, cost-effectiveness, and versatility.
The Evolution and Market Trends in custom injection molds Industry
The custom injection molds industry has undergone significant evolution and experienced several market trends in recent years. This industry plays a critical role in manufacturing various consumer products by producing custom-designed molds for injection molding processes. Here, we explore some key aspects of the industry’s evolution and market trends.
One of the significant evolutions in the custom injection molds industry is the adoption of advanced technologies. With the advancement in 3D printing, computer-aided design (CAD), and computer-aided manufacturing (CAM), manufacturers can now create intricate and complex molds with high precision and efficiency. This has resulted in improved product quality and reduced lead times, leading to increased customer satisfaction.
Another evolution in this industry is the growing emphasis on sustainability. As environmental concerns continue to rise, manufacturers are increasingly focusing on producing molds that are more eco-friendly. This includes using recyclable materials and adopting energy-efficient manufacturing processes, thereby reducing the industry’s carbon footprint.
In terms of market trends, there is a growing demand for miniaturization in various industries. As consumer electronics and medical devices become smaller and more compact, the need for precision molds capable of producing tiny components has risen. This trend has led to the development of micro-injection molding techniques and the demand for highly accurate and intricate molds.
Furthermore, the custom injection molds industry has witnessed a shift towards regionalization. The globalization of trade has resulted in increased competition, making time-to-market a critical factor for manufacturers. To reduce lead times and transportation costs, companies are opting for local mold manufacturers, allowing them to have closer collaboration and faster response times.
Lastly, the industry is experiencing a shift towards automation and robotics. Manufacturers are increasingly incorporating automation into the injection molding process to improve efficiency, reduce labor costs, and enhance quality control. This trend enables faster production cycles and reduces the risk of human error.
In conclusion, the custom injection molds industry has seen remarkable evolution and market trends. The adoption of advanced technologies, increased focus on sustainability, demands for miniaturization, regionalization, and automation have all shaped the industry’s current landscape. Moving forward, we can expect further advancements in technology and continued market adaptation to meet the ever-changing needs of manufacturers and consumers.
Custom Private Labeling and Branding Opportunities with Chinese custom injection molds Manufacturers
Chinese custom injection molds manufacturers offer a range of opportunities for custom private labeling and branding. With their expertise and advanced technology, they can help businesses create products that stand out in the market.
One of the main advantages of collaborating with Chinese injection molds manufacturers is their ability to provide custom manufacturing solutions. They can produce molds according to specific requirements and designs provided by businesses. This allows companies to create unique and personalized products that align with their branding strategies.
Additionally, Chinese manufacturers offer private labeling services, enabling businesses to establish their brand identity. They can customize the products with business logos, brand names, and other branding elements, helping to enhance brand recognition and customer loyalty. This is particularly beneficial for businesses looking to build a strong brand presence in the market and maintain a consistent image across their product line.
Working with Chinese suppliers also offers cost advantages. Chinese injection molds manufacturers generally have lower production costs, making them a cost-effective solution for businesses. This enables businesses to invest in custom branding and labeling without significantly increasing their overall production costs.
Furthermore, Chinese manufacturers have extensive experience in international trade and have established reliable logistics networks. This ensures efficient and timely delivery of products, making it easier for businesses to access the global market.
In conclusion, partnering with Chinese custom injection molds manufacturers presents various opportunities for custom private labeling and branding. Their ability to customize molds and products, along with their cost advantages and efficient logistics, make them a suitable choice for businesses looking to create unique and branded products.
Tips for Procurement and Considerations when Purchasing custom injection molds
When purchasing custom injection molds for procurement, there are several essential tips and considerations to keep in mind. These can help ensure that you choose the best molds that meet your specific requirements and expectations:
1. Clearly Define your Needs: Before approaching mold manufacturers, have a thorough understanding of your project’s requirements, including material type, product dimensions, and production quantity. This will help you communicate your needs effectively.
2. Research Mold Manufacturers: Take time to explore different mold manufacturers, review their reputation, experience, and customer feedback. Look for a company that has expertise in your industry and a proven track record of delivering high-quality molds.
3. Assess Mold Materials: Discuss with manufacturers the type of materials they use for injection molds. Ensure that the materials are of high quality and suitable for your specific application. Consider factors such as durability, temperature resistance, and cost when choosing the right material.
4. Quality Assurance and Testing: Inquire about the manufacturer’s quality control processes and certifications. A reputable manufacturer should provide testing and inspection reports to ensure the molds meet industry standards.
5. Cost Optimization: While cost is a critical factor, it should not compromise the quality of the mold. Look for a balance between price and quality, ensuring that the mold will meet your production needs and have a longer lifespan.
6. After-sales Support: Inquire about the warranty period and after-sales support provided by the manufacturer. Having reliable customer support is essential in case any issues arise or modifications are required.
7. Production Capacity: Evaluate the manufacturer’s production capacity and lead times. Ensure they can deliver molds within your desired timeframe without compromising on quality.
8. Communication and Collaboration: Establish open and clear communication channels with the manufacturer throughout the procurement process. Regular updates and collaboration will help achieve the desired results efficiently.
Remember, purchasing custom injection molds is a crucial investment for your business. Taking time to research, assess, and communicate effectively with the manufacturer will ensure the molds meet your expectations and contribute to the success of your production processes.
FAQs on Sourcing and Manufacturing custom injection molds in China
Q: Why are many companies sourcing and manufacturing custom injection molds in China?
A: Many companies choose to source and manufacture custom injection molds in China due to factors such as lower production costs, a vast manufacturing infrastructure, and access to a skilled labor force. China’s advanced manufacturing capabilities and large pool of mold-making experts make it an attractive option for companies looking to produce molds more efficiently and cost-effectively.
Q: How can I find a reliable supplier for custom injection molds in China?
A: To find a reliable supplier, you can start by conducting thorough research and due diligence. Utilize online platforms, such as Alibaba or Global Sources, to search for mold manufacturers in China. Pay attention to their years of experience, certifications, and customer reviews. It is highly recommended to request samples, visit the manufacturing facilities, and communicate directly with supplier representatives to assess their reliability and capabilities before making a decision.
Q: How important is quality control when sourcing injection molds from China?
A: Quality control is crucial when sourcing injection molds from China. Working with a reputable manufacturer that has stringent quality control processes is essential to ensure the molds meet your specifications. Conducting regular inspections and audits throughout the manufacturing process is recommended to identify and rectify any potential issues before mass production. Utilizing methods like first article inspection, quality assurance plans, and ensuring adherence to international standards like ISO 9001 can help maintain the quality of injection molds.
Q: How long does it typically take to manufacture custom injection molds in China?
A: The manufacturing lead time for custom injection molds in China varies depending on the complexity of the mold, the quantity required, and the manufacturing capabilities of the supplier. Generally, it can range from a few weeks to several months. Factors like design revisions, tooling production, and quality control inspections can also impact the overall lead time.
Q: What are the payment terms commonly used when sourcing injection molds from China?
A: Payment terms are typically agreed upon between the buyer and the supplier. However, it is common to negotiate a deposit (usually 30-50%) upfront at the time of order confirmation, with the balance payment due upon completion and inspection of the molds. However, the specific payment terms can vary depending on the supplier’s policies and the relationship established between the buyer and the supplier.
Q: How can I ensure intellectual property protection when sourcing injection molds from China?
A: Intellectual property protection is a crucial concern when sourcing injection molds from China. Companies can protect their designs and molds by signing non-disclosure agreements (NDAs) with suppliers. It is also recommended to work with reputable manufacturers with good track records in respecting and protecting intellectual property rights. Additionally, registering your intellectual property in China can provide legal protection in case of infringement.
In conclusion, sourcing and manufacturing custom injection molds in China offer various benefits, including cost-effectiveness and access to a skilled workforce. By ensuring quality control, finding reliable suppliers, and protecting intellectual property rights, companies can successfully navigate this process.
Why contact sourcifychina.com get free quota from reliable custom injection molds suppliers?
Sourcifychina.com offers a free quota from reliable custom injection molds suppliers for several reasons. Firstly, by providing a free quota, they aim to attract potential clients and establish themselves as a trusted platform for sourcing injection molds from reliable suppliers in China. This helps them build their reputation and gain credibility in the market.
Secondly, providing a free quota allows clients to understand the cost implications and make informed decisions about their sourcing needs. It gives them an opportunity to compare quotes from different suppliers and evaluate the pricing and quality of the molds. This helps clients make efficient and cost-effective choices for their businesses.
Furthermore, the free quota service offers clients the convenience of accessing multiple suppliers without individually contacting each one. Sourcifychina.com serves as a centralized platform where clients can submit their requirements and receive multiple quotes from reliable suppliers. This saves time and effort for clients who may otherwise have to research and communicate with various suppliers individually.
Additionally, by partnering with reliable custom injection mold suppliers, Sourcifychina.com ensures that clients receive high-quality molds that meet their specifications. The platform verifies the credentials, expertise, and production capabilities of the suppliers beforehand, ensuring that clients can trust the quality and reliability of the molds they receive.
In conclusion, offering a free quota from reliable custom injection mold suppliers benefits Sourcifychina.com by attracting potential clients, establishing credibility, facilitating informed decision-making, offering convenience, and ensuring the delivery of high-quality molds.